materials and qualification procedures for ships 9-1
Process Check List
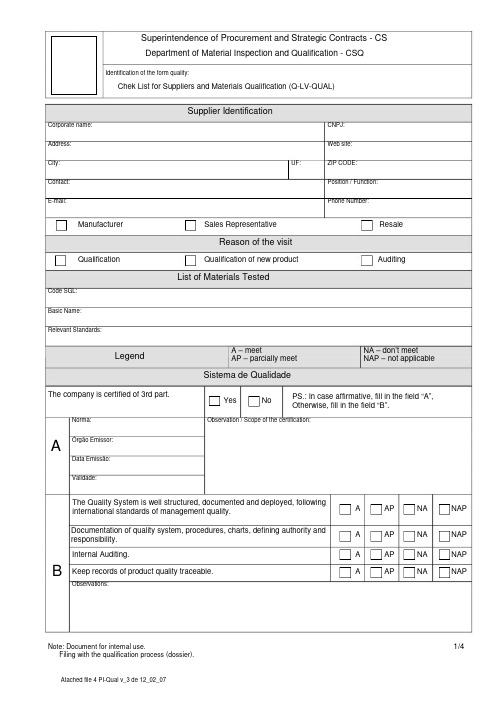
Documentation of quality system, procedures, charts, defining authority and responsibility. Internal Auditing.Chek List for Suppliers and Materials Qualification (Q-LV-QUAL)Supplier IdentificationCorporate name:Address:City:Contact:E-mail:UF:CNPJ:Web site:ZIP CODE:Position / Function:Phone Number:ManufacturerSales RepresentativeResaleReason of the visitQualificationQualification of new productAuditingList of Materials TestedCode SGL:Basic Name:Relevant Standards:LegendA – meetAP – parcially meetNA – don’t meet NAP – not applicableSistema de QualidadeThe company is certified of 3rd part.Norma:Yes NoPS.: In case affirmative, fill in the field “A”, Otherwise, fill in the field “B”.Observation / Scope of the certification:AÓrgão Emissor:Data Emissão:Validade:The Quality System is well structured, documented and deployed, following international standards of management quality.A A A AAP AP AP APNA NA NA NANAP NAP NAP NAPBKeep records of product quality traceable.Observations:1/4Chek List for Suppliers and Materials Qualification (Q-LV-QUAL)PlantIndustrial area / inventoryGeneral facilitiesCleaning and organizationSafety standards and physical assets LaboratoriesTechnology usedObservations:AAAAAAAPAPAPAPAPAPNANANANANANANAPNAPNAPNAPNAPNAP Production ProcessProduction Capacity (equipment and manpower) Documentation involving the production process Selection criteria for suppliersPreparation and orientation of the manpower Specific procedure in obtaining inputsStorage planningStorage and identification of raw material used in production.Maintenance planning.Storage and packaging of finished product. Transportation and distribution logistics Observations:AAAAAAAAAAAPAPAPAPAPAPAPAPAPAPNANANANANANANANANANANAPNAPNAPNAPNAPNAPNAPNAPNAPNAPQuality ControlReceipt of raw material Production Quality Control Disapproved product segregation Calibration of measuring instruments Specific test benchAdditional TestsProduct traceabilityObservations AAAAAAAAPAPAPAPAPAPAPNANANANANANANANAPNAPNAPNAPNAPNAPNAPChek List for Suppliers and Materials Qualification (Q-LV-QUAL)Additional RecordsSuperintendence of Procurement and Strategic Contracts - CSDepartment of Material Inspection and Qualification - CSQ Identification of the form quality:Chek List for Suppliers and Materials Qualification (Q-LV-QUAL)EvaluationFormula Calculation ResultR = Nº A + (Nº AP) / 2 x 100Nº AplicáveisNormative Tests of the Product – NTP Observations:R=MeetR ≥ 70 = MeetR < 70 = Don’t MeetDon’t meet ConclusionR ≥ 70 e ENP meetR ≥ 70 e ENP don’t meet R < 70 e ENP meetR < 70 e ENP don’t meetQualifiedUnqualifiedUnqualifiedUnqualified Validity Qualification3 Months Responsible SABESP:6 Months12 MonthsPlace and Date:18 Months。
POSITIVE MATERIAL QUALITY PROCEDURE材料质量鉴定质量程序

QUALITY PROCEDURE POSITIVE MATERIAL IDENTIFICATIONCONTENTS1.0 SCOPE2.0 PURPOSE3.0 DEFINITION4.0 RESPONSIBILITIES5.0 REFERENCES6.0 QUALITY PROCEDURE7.0 ATTACHMENT1. SCOPEThis procedure is applicable for quantitative analysis of composition of Cr、Ni、Mo、Ti、V 、Mn、Nb、Cu、W、Fe in every kinds of alloy material, pressure-containing components in shop and field fabricated equipment and piping (both base metal and welds), detect and replace incorrect materials,2. PURPOSEPrevent equipment /system failures due to installation of incorrect materials.Construction and fabrication quality control is vital and PMI is a very important part of total quality control.3. DEFINITIONPMI Positive Material IdentificationMRR Material Receiving ReportsMMIR Manufacturer Material Identification Reports4. Responsibilities and qualification of testing personnelQuality engineer is responsible for the supervision of overall NDT operations, coordination and contact with TR and relevant.NDE Project Manager is responsible for commanding construction, coordinating all works related with this project, monitoring and checking works of every departments of this project and assigning and coordinating the resources in this project, such as personnel, equipments, material, etc.participate working meeting organized by owner, supervisor.NDE HSE Manager is responsible for assuring that every testing being carried out safely, reposefully and normally.NDE quality Controlling Manager is responsible for compiling and revising and approving every technical document related to this project, organizing to supervise, check, and instruct, the final assessing of testing results and organizing to settling and submitting project-finishing documents.Testing personnel is responsible for carrying out testing works according to the requirements of standards, regulations, and operation instructions, carefully filling in records, feeding-back quality information in time and keeping the cleaning of facility environment, maintaining equipments and testing apparatus and assuring its normal running.Prior to commencing PMI testing, instrument operators shall be qualified to operate approved equipment on a representative sample of the alloy materials with 100% correct assessment as the performance criteria. The instrument operator shall work to a written procedure and shall have been trained to use the instrument in accordance with that procedure. Training shall be documented.The person(s) performing the PMI testing shall calibrate and/or verify the test equipment performance as specified by the equipment manufacturer.5. REFERENCESSAES-A-206Positive Material IdentificationASME B31.3Chemical Plant and Petroleum Refinery PipingASME B31.4 Pipeline Transportation Systems for Liquid Hydrocarbonsand Other LiquidASME B31.8 Gas Transmission and Distribution Piping SystemsASTM A193 Standard Specification for Alloy-Steel and Stainless SteelBolting Materials for High-Temperature Service ASTM A751 Standard Methods Practices and Terminology for ChemicalAnalysis of Steel Products6. QUALITY PROCEDURE6.1 Extent of VerificationA. The PMI program covers alloy material, pressure-containingcomponents in shop and field fabricated equipment and piping (bothbase metal and welds) and materials used for repair or replacementof pressure containing components.B. One hundred percent PMI testing (each component and weld istested) shall be performed on all pressure components and welds ofalloy materials.C. PMI testing of weld material shall be performed in the same manneras for the adjacent base metal.D. Welding consumables (welding rod or welding wire) shall also beperformed.6.2 The elements of the basic alloy materials to be verified shall be inaccordance with following as:A. For Carbon-Molybdenum, Manganese-Molybdenum, andChromium-Molybdenum steels, the Elements of Chromium andMolybdenum shall be verified.B. For Nickel steels, the Elements of Nickel shall be verified.C. For Regular carbon grade stainless steels, the Elements ofChromium, Nickel, and Molybdenum shall be verified.D. For Low-carbon stainless steels, the Elements of Chromium, Nickel,Molybdenum, and Carbon shall be verified.E. For Stabilized stainless steels, the Elements of Chromium, Nickel,Molybdenum, Titanium and Niobium shall be verified.F. For Nickel-based alloys steels, the Elements of Nickel, Iron, Copper,Chromium, and Molybdenum shall be verified.G. For Copper-based alloys steels, the Elements of Copper, Zinc, andother elements shall be verified.6.3 Testing RequirementsA. The subcontractor shall ensure that the required PMI program hasbeen carried out at any off site fabrication facilities where applicable.Items requiring PMI that have not been tested prior to shipment andreceipt on-site, shall be tested at site.B. Prior to performing any PMI inspection on bulk or lose materialreceived at site, the subcontractor shall be traceable to the MMIR,MRR, and determine what percentage of the material requires PMIverification based on the project specification.C. Prior to performing any PMI inspection at the warehouse or stockyard, the subc ontractor’s PMI inspector shall perform a visualinspection of the material for defects, proper material,manufacturer’s markings, heat number verification and codeidentification markings.D. If no MMIR were shipped with the alloy welding filler metal, each lotof that alloy filler metal shall be tested. As a minimum one samplefrom each Lot shall be measured in the chemical mode forcompliance, and recorded on a PMI report log.E. The subcontractor shall maintain dissimilar alloy material isolation inaccordance with the material management procedure.F. The quality inspector shall consign the NDT personnel for doingPMI testing of alloy materials according to required percent andelement.G. When analysing welds (butt, or groove), the subc ontractor’s PMIinspector shall do a three point check using the ID mode as aminimum, which includes the base metal, heat effect zone andwelding seam .If the base metal has already been identified fromthe warehouse and documented as such, a two point check may beperformed on the weld and remaining base metal. The results shallbe documented for the two points and a comment added for thepreviously inspected fitting on the PMI report form.H. Both inside and outside weld surfaces shall be tested whereaccessible. PMI testing of welds shall be done after removal of slagand oxide from the weld surface.I. The surface to be analyzed shall be clean bare metal, free ofgrease or oil, with a surface finish as specified by the instrumentmanufacturer.6.4 Inspect equipment and/or instrumentA. A portable optical emission spectrograph may be used to check forall the required elements, including carbon, Chromium,Molybdenum, Nickel, Titanium, Iron, Copper etc.B. The PMI inspection equipment and instrument shall be calibrated,reconditioned and leak tested for continuous effectiveness of theinstrument’s radiation shielding by the manufacturer.C. As with all electrical instruments, care should be taken in handlinganalyzers. Avoid dropping or striking the instrument on hardsurfaces at all costs, unless the safety of the operator is at risk.6.5 Methods of TestingA. The instruments and methods used shall be suitable for identifyingthe material by quantitative measurement of the major alloyingelements required in the applicable material specification or weldingprocedure specification.B. Check the battery capability, insure instrument is on normal status.C. Clean the surface of material.D. Test with certified standard steel sample, confirm whether theanalysing process is normal and analysing date is correct.E. Select different radiating time, and not less than 15 secondsaccording to the range of element compositions.F. According to testing piece material and jobsite conditions, selectmost optimum analysing condition, such as operating mode,programme, analysing time and analysing times.G. Analyse and record the results according to the requirements ininstrument instruction.6.6 Criteria of AcceptanceA. For acceptance, it must be demonstrated that materials contain theamounts of alloying elements shown in the material specification.Alloys shall be acceptable if the alloying elements are each withinthe stated tolerance range for the instrument but in no case lessthan 10% of the minimum specified value or greater than 10% ofmaximum specified value in the material specification.B. For deposited weld metal between similar base materials usingmatching consumables, the recorded concentration shall be withinthe stated tolerance range for the instrument but in no case lessthan 12.5% of the minimum specified value or greater than 12.5%of maximum specified value in the material specification.C. Acceptance criteria for dissimilar metal alloy welds and weldoverlays shall be in accordance with the welding consumablespecified in the approved welding procedure. The effects of dilutionbetween the different base metals and the filler metal shall be takeninto account for determining the nominal as-deposited weld metalcomposition.D. If any component, basic material or weld is found unacceptable, itshall be replaced and the replacement shall be alloy verified inaccordance with correlative standard.E. All rejected alloy material, component or weld shall be replaced and100% of the replacement alloy material, component or weld shall besubjected to PMI testing in accordance with correlative standard. 6.7 Testing InspectionThe responsible Inspector shall ensure and verify that alloy materials have been verified by PMI testing as required and the element of the alloy steel shall be within the stated tolerance range.6.8 Verification MarkingA. After the testing, the tester should mark with water-insolublematerial that contains no substances that harmfully affect the metalat ambient or elevated temperatures, In particular, the markingmaterial shall be free of lead, sulfur, zinc, cadmium, mercury,chlorine, or other halogens.B. All verified materials with an acceptable analysis shall be markedwith the letters "PMI" using a certified low-stress stamp. Themarking shall be placed as follows:A. For pipe, one mark, 75 mm from one end on the outer surface ofthe pipe.B. For welds, adjacent to the welder's mark on the weld.C. For fittings and valves, adjacent to the manufacturer's markings.D. For valves, Adjacent to the valve manufacturer's markings onbodies and other pressure parts.E. For steel plates, 75 mm from one edge, adjacent to manufacturer'smarkings.C. PMI markings shall be transferred when a plate or pipe is cut.D. All components, and welds unaccepted shall be marked red “×”.6.9 Colour codeEach component shall be coded and painted characters indicating the specification number of the material if it is not permanently marked or tagged according to the applicable material specification, as following:A. For piping and fitting, each length of pipe and fitting shall have a 5mm or larger stripe running full length (lengthways). One inch andsmaller may have a 3 mm stripe running full length (lengthways).B. For valves, when required, stripe across the body from flange toflange or end to end.C. For flanges, when required, stripe across edge up to hub.D. For spiral-wound gaskets, shall be colour coded in accordance withASME B16.20.E. For bolts, stripe around the midpoint of each bolt or stud.6.10 Record and ReportA. When operators finish the PMI testing, they shall keep the all recordof PMI testing and submit the report to TR’s quality control team.B. The following should be included in reports:Weld, base material, or area examinedFiller metal designation or part identificationEquipment piece or tag numberExamination procedure (standard), identification, and revisionnumberDate of examinationPMI Inspectors or operator nameExamination resultsThe type of testing performed and the type and model of analyzerusedThird party PMI Agency name and authentication result7. ATTACHMENT。
产品材料的可靠性鉴定之管制程序 -中英文对照
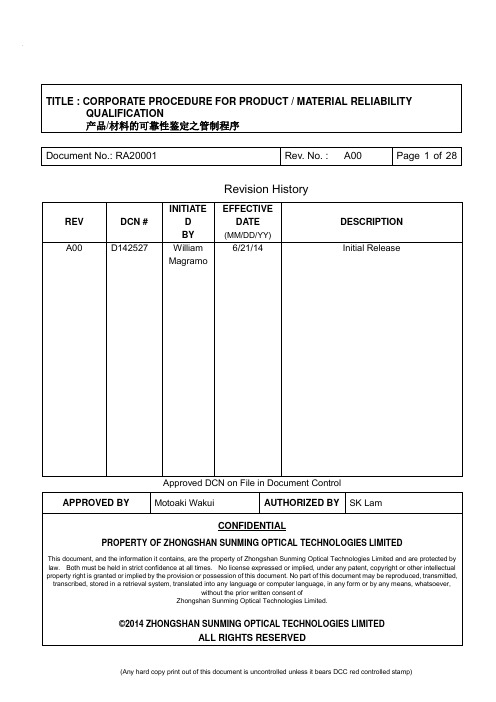
TITLE : CORPORATE PROCEDURE FOR PRODUCT / MATERIAL RELIABILITY QUALIFICATION产品/材料的可靠性鉴定之管制程序Document No.: RA20001 Rev. No. : A00 Page 1 of 28Revision HistoryREV DCN # INITIATEDBYEFFECTIVEDATE(MM/DD/YY)DESCRIPTIONA00 D142527 WilliamMagramo6/21/14 Initial ReleaseApproved DCN on File in Document ControlAPPROVED BY Motoaki Wakui AUTHORIZED BY SK LamCONFIDENTIALPROPERTY OF ZHONGSHAN SUNMING OPTICAL TECHNOLOGIES LIMITEDThis document, and the information it contains, are the property of Zhongshan Sunming Optical Technologies Limited and are protected by law. Both must be held in strict confidence at all times. No license expressed or implied, under any patent, copyright or other intellectual property right is granted or implied by the provision or possession of this document. No part of this document may be reproduced, transmitted, transcribed, stored in a retrieval system, translated into any language or computer language, in any form or by any means, whatsoever,without the prior written consent ofZhongshan Sunming Optical Technologies Limited.©2014 ZHONGSHAN SUNMING OPTICAL TECHNOLOGIES LIMITED1.0 PURPOSE 目的1.1 This procedure describes the 此程序描述了:1.1.1 Recommended practices for the qualification of new products, processes,materials and facilities.新产品,制程,材料及设施鉴定的建议措施。
materials and qualification procedures for ships

Materials and Qualification Procedures for ShipsBook BProcedure 1-1Periodic Inspection of Approved WorksRevision 1, December 2013Lloyd’s Register Group Limited, its subsidiaries and affiliates and their respective officers, employees or agents are, individually and collectively, referred to in this clause as ‘Lloyd’s Register’. Lloyd’s Register assumes no responsibility and shall not be liable to any person for any loss, damage or expense caused by reliance on the information or advice in this document or howsoever provided, unless that person has signed a contract with the relevant Lloyd’s Register entity for the provision of this information or advice and in that case any responsibility or liability is exclusively on the terms and conditions set out in that contract.© Lloyd's Register Group Limited 2013. All rights reserved.Except as permitted under current legislation no part of this work may be photocopied, stored in a retrieval system, published, performed in public, adapted, broadcast, transmitted, recorded or reproduced in any form or by any means, without the prior permission of the copyright owner. Enquiries should be addressed to Lloyd's Register Group Limited, 71 Fenchurch Street, London, EC3M 4BS.Periodic Inspection of Approved Works1 Introduction1.1 General1.1.1 In order that consideration may be given to the continued inclusion of a companyon the LR List of Approved Manufacturers of Materials and Recognized ProvingEstablishments, LR Surveyors are to carry out a periodic inspection to determinethat the works still satisfies the criteria established during the initial approval. Areport is to be submitted by the Surveyor to the Materials and NDE Department. 1.2 Scope1.2.1 This document provides general guidelines for the procedures to be followed inorder that a satisfactory periodic inspection of a LR approved manufacturer may be carried out.1.2.2 The lists referred to in this procedure are as follows:List 1 A pproved Manufacturers of Steel Plates, Strip, Section and Bars.List 2 Approved Manufacturers of Steel Castings.List 3 Approved Manufacturers of Steel Forgings.List 4 Approved Manufacturers of Steel Pipes and Tubes.List 5 Approved Manufactures of Iron Castings.List 6(a) Approved Manufacturers of Aluminium Alloy Plates, Sections,Bars and Castings.List 6(b) Approved Manufacturers of Aluminium/Steel TransitionJoints.List 7(a) Approved Manufacturers of Copper Alloy Castings for Propellers.List 7(b) Approved Manufacturers of Copper Alloy Castings for Valves,Liners and Bushes.List 7(c) A pproved Manufacturers of Copper and Copper Alloy TubesList 8 Recognized Proving Establishments for Anchoring and MooringEquipment.List 9(a) Approved Manufacturers of Chain Cable.List 9(b) Approved Manufacturers of Fittings for Chain Cable.List 10 Approved Manufacturers of Short Link Chain Cable.List 11 Approved Manufacturers of Steel Wire Rope.List 12(a) Approved Manufacturers of Fusion Welded Pressure Vessels,Class 1.List 12(b) Approved Manufacturers of Fusion Welded Pressure Vessels,Class 2.1List 12(c) Approved Manufacturers of Fusion Welded Pressure Vessels,Class 2.2.1.2.3 The period between inspections of works should not exceed three years.1.2.4 Any deviation from the recommended frequency is first to be agreed with Materialsand NDE Department. Failure to carry out an inspection prior to the expiry date ofthe existing approval may lead to deletion from the approved list. Once deleted, re-approval will require full procedure tests to be carried out.1.3Related Rules1.3.1LR's Rules and Regulations for the Classification of Ships (hereinafter referred to asthe Rules for Ships).1.3.2 LR's Rules for the Manufacture, Testing and Certification of Materials (hereinafterreferred to as the Rules for Materials).2.0Inspection procedure2.1 Preparation for the inspection visit2.1.1Materials and NDE Department will advise the local Surveyors in advance that theperiodic inspection is due and will detail the current record of:Firm's name and address.The extent of the approval.Approved testing machines.2.1.2The Surveyor is to liaise with the firm to establish a mutually acceptable time forthe inspection visit with an appropriate representative (e.g. Works Manager,Quality Manager). For the visit to be successful the Surveyor must check beaccorded access to all relevant parts of the works at all times. The arrangementswith the Surveyor are to include checking all relevant production processesincluding subcontracted processes.2.1.3The Surveyor is to ensure that the firm's representative is aware of:The extent of the approval.The firm's entries in the latest edition of the Approved List.2.1.4 The Surveyor and firm's representative are to agree the accuracy of the informationpresented prior to the inspection of the works taking place.2.1.5When the scope of approval requires to be extended (e.g. new grade, increaseddimensions), then the programme of appropriate procedure tests is to be agreed.2.2 The inspection visit2.2.1The appropriate sections of the check list in Form 2035 (available in LRForms2) willbe utilised. This checklist is issued as a guide only and is not to be considered ascomprehensive or to restrict the scope of survey.2.2.2Due attention is to be given to confirming that the plant and testing equipmentcontinue to be suitably maintained and calibrated. In particular, the method andfrequency of calibration of thermocouples, recorders, testing machines andanalytical equipment are to be noted.2.2.3 Where appropriate, NDE and weld procedures and operator qualifications are to beexamined to ensure that these remain valid2.2.4 As a check on the manufacturer's system, one product/order, chosen at random, isto be traced through to completion in accordance with the ordering specification.Records reviewed include, where appropriate:Purchase orders.Copies of relevant standards/specifications.Melting and casting records.Manufacturing procedures.Forming records.Heat treatment records.Inspection records, including NDE and any dimensional checks.Mill certificates.The above records are to be reviewed for compliance with the manufacturing plan or in-house quality control procedures.2.3 Reporting and approval2.3.1Consideration for continued inclusion in the approved list will be given to a firmwhere Surveyors are in regular attendance. In this instance the firm is to submit adeclaration endorsed by the Surveyor confirming that:(a) No changes have occurred to plant or procedures since the last periodicinspection visit, or(b) Listing the changes to the plant and procedures.2.3.2Form 2035 is to be completed and, together with any other related information,forwarded to Materials and NDE Department for review. The form is available inLRForms2.2.3.3Any non-compliance requiring remedial action and all outstanding comments areto be dealt with before an extension is given.2.3.4 A satisfactory inspection will be indicated to the firm by the local office on theadvice from Materials and NDE Department and a prestige certificate will be issued.The certificate will show a validity date on or before which a subsequent periodicinspection is to be carried out. The firm will be retained on the approved list untilthat date provided that they comply with the Rules for Materials.。
材料工程要求

Anti-corrosion, aging, interior air quality: 3 samples/ item
5)禁限用物质:根据检测需求,但至少1件;
Restricted/prohibited substance: dependent on test requirements but at least 1 sample
材料工程要求
Material Engineering Requirements
1.前期策划Preliminary planning
序号No.
职责描述Reasonability Description
主导方led by
1
制定整车/零部件的防腐、老化、车内环境、回收、禁限用物质要求
Formulate requirements on anti-corrosion, aging, interior environment, recycling, restricted/prohibited substance for parts and complete vehicle
2.材料工艺控制Materialprocess control
序号
No.
职责描述
Reasonability Description
主导方led by
1
材料工艺定义:零部件的材料工艺包括金属件的热处理工艺(如回火、淬火、渗碳、渗氮等)、零件成型工艺(如冲压、铸造、锻造、热成型等)、表面处理工艺(如电泳、喷塑、镀锌、锌铝涂覆等)等,非金属件的注塑、吹塑等。
供应商Supplier
4
建立满足要求的材料工艺供应商清单,支持供应商选用
Establish supplier list ofmaterialprocess that satisfies requirement for supplier selection
一次性使用工艺组件-ASMEBPE-2023新增内容解读

一次性使用工艺组件|ASMEBPE—2023新增内容解读加添了一次性使用部件和组件的要求,分为三个章节,分别是第七章一次性使用设计、第八章一次性使用工艺组件和第九章一次性使用的制造、组装和安装。
本文连续介绍第八章一次性使用工艺组件。
一次性使用工艺组件1.蒸汽直通和蒸汽直通连接器2.无菌连接器2.1制造商责任制造商应:(a)进行微生物侵入试验,以确认连接后无菌液路不会受到损害(b)定义连接器是干连接器还是湿连接器(1)干燥意味着液体不能进入连接器。
使用前,必需使用夹钳或其他合适的技术将液体与连接器隔离。
(2)湿意味着连接器中可以有液体进行连接。
(c)供给产品规格,包括但不限于以下内容:(1)温度额定值(2)压力额定值(3)灭菌方法的兼容性(例如,伽马灭菌,高压灭菌)(4)产品流路清洁度(微粒、内毒素、生物负载)(5)流速(d)定义连接器两半部分的性别(1)独。
特的阳半部分和阴半部分(2)没有性别,每一半都是一样的(e)定义连接是设计用于一次性连接还是多个连接(1)设计用于一次性连接的连接器应具有不可逆的锁定机制,除非其专门设计用于无菌断开。
(2)设计用于多重连接和断开的连接器应具有规定的最大连接数。
(f)供给装配说明,以确保正确连接2.2 全部者/用户责任全部者/用户应(a)依据全部适用过程和灭菌条件的服务要求,审查制造商的质量标准(b)确保由经过适当培训的操作员依照合格程序进行连接,以保持系统完整性3.柔性生物工艺容器(袋)3.1材料多层膜通常用于制造一次性袋。
制造商应确定袋的全部薄膜和连接层的构造材料。
对于预期用于过程接触的袋,制造商应识别全部材料(例如,重要材料、粘结层和添加剂),这些材料可能会掺杂袋内产品。
3.2确认制造商应供给一次性袋的工作温度和压力限值。
制造商应规定适当的灭菌方法,包括暴露范围、灭菌后有效期和其他限制。
制造商应供给处理和安全使用程序,包括悬挂限制、填充限制和二次密封建议。
挪威船级社
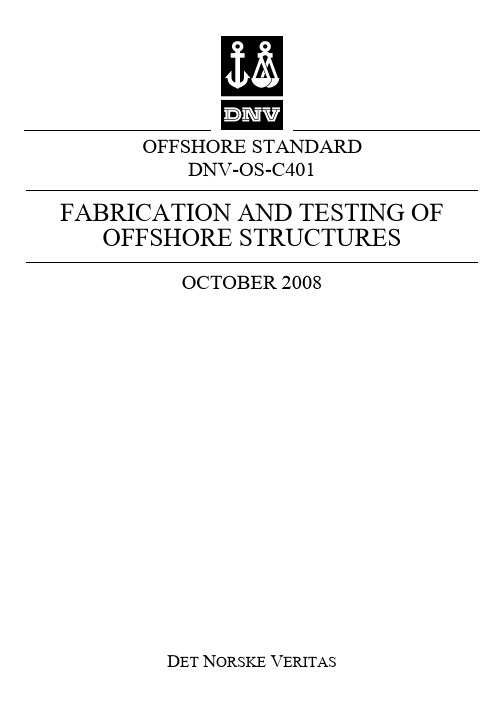
For an overview of all types of DNV offshore documents and their update status, see the “Amendments and Corrections” document located at: /global/, under category “Offshore Codes”.
Sec. 1 Introduction........................................................... 9
A. General.................................................................................... 9 A 100 Introduction....................................................................... 9 A 200 Objective........................................................................... 9 A 300 Organisation of contents ................................................... 9
Offshore Service Specifications and Offshore Standards. DNV Offshore Codes are offered within the following areas: A) Qualification, Quality and Safety Methodology B) Materials Technology C) Structures D) Systems E) Special Facilities F) Pipelines and Risers G) Asset Operation H) Marine Operations J) Wind Turbines O) Subsea Systems
Material and Qualification Procedures for Ships

Material and Qualification Procedures for ShipsIntroductionThis document contains the links to procedures to be followed when applying for approval /recognition against Lloyd's Register's Rules for the Manufacture, Testing and Certification of Materials(hereinafter referred to as the Rules for Materials) which forms part of Lloyd's Register's Rules andRegulations for the Classification of Ships (hereinafter referred to as the Rules for Ships) and othermarine related Regulations and Requirements.Related procedures are grouped together into Books A to P.The procedures are intended to be available to LR Surveyors and manufacturers, fabricators, testingestablishments seeking approval.Upon completion of the specified inspection and/or testing programme required by these procedures,a report is submitted to the Global Technology Centre - Materials and NDE. If considered to besatisfactory a certificate will be issued and the approved manufacturer / product / procedure will beentered in the relevant Lloyd’s Register approved / recognized / accepted list.ContentsBook A Guidelines for Qualification of Welding Procedures, Welders and WeldabilityBook B Procedure for Periodic Inspection of Approved WorksBook C Procedures for Approval of a Works for Steelmaking and Rolled Steel ProductsBook D Procedures for Approval of a Works for the Manufacture of Steel CastingsBook E Procedures for Approval of a Works for the Manufacture of Steel ForgingsBook F Procedures for Approval of a Works for the Manufacture of Iron CastingsBook G Procedures for Approval of a Works for the Manufacture of Non-FerrousAlloy ProductsBook H Procedures for Approval of a Works or Proving Establishment for Chain Cableor Wire RopeBook J Procedures for Approval of Welding Consumables and Manufacture ofFabricated Steel SectionsBook K Procedures for Approval of Plastic MaterialsBook L Procedures for Approval of Repair ProceduresBook M Procedures for the Approval in accordance with the Materials Quality Scheme (MQS)Book N Procedures for Approval of NDE Firms & Service SuppliersBook P Procedures for Approval of Paints and CoatingsProcedure 3-6Approval of a Works for the Manufacture of Clad Steel Plate for Tank ProductionProcedure 3-7 Approval of a Steelworks for the Manufacture of Bar Material forChain CableBook AGuidelines for Qualification of Welding Procedures, Welders and WeldabilityProcedure 0-3Guidelines for Weldability Tests for Normal and High Strength SteelProcedure 0-4Approval of Works for the Manufacture of Fusion Welded Pressure VesselsBook BProcedure for Periodic Inspection of Approved WorksProcedure 1-1Periodic Inspection of Approved WorksBook CProcedures for Approval of a Works for the Manufacture of SteelProcedure 3-0Approval of a Steelworks for the Manufacture of Steel and Semi- finished ProductsProcedure 3-1Approval of a Steelworks for the Manufacture of Ship Steels and Boiler and Pressure Vessel Steels with the option of Specified Through-Thickness PropertiesProcedure 3-2Approval of a Steelworks for the Manufacture of Ferritic Steels and Nickel Steels for Low Temperature ApplicationsProcedure 3-3Approval of a Steelworks for the Manufacture of Corrosion Resistant Steel for Cargo Oil Tanks of Crude Oil Carrier in compliance with IMO Resolution MSC289(87)Procedure 3-4Approval of a Steelworks for the Manufacture of High Strength Quench and Tempered SteelsProcedure 3-5Approval of a Steelworks for the Manufacture of Stainless SteelsProcedure 6-1Approval of a Works for the Manufacture of Steel Pipes and TubesProcedure 6-2Approval of a Works for the Manufacture of Non-Heat Treated ERWSteel Pipes.Procedure 6-3Approval of a Works for the Manufacture of Ferritic Steel and NickelSteel Pipes for Low Temperature ServiceBook D Procedures for Approval of a Works for the Manufactureof Steel CastingsProcedure 4-1Approval of a Works for the Manufacture of Steel CastingsProcedure 4-2Approval of a Works for the Manufacture of Steel Castings forCrankshaftsProcedure 4-3Approval of a Works for the Manufacture of Stainless Steel Castingsincluding PropellersProcedure 4-4Approval of a Works for the Manufacture of Steel Castings forContainer Corner FittingsProcedure 4-5Approval of a Works for the Manufacture of Ferritic Steel Castings forLow Temperature ServiceBook E Procedures for Approval of a Works for the Manufactureof Steel ForgingsProcedure 5-1Approval of a Works for the Manufacture of Steel ForgingsProcedure 5-2Approval of a Works for the Manufacture of Steel Forgings for Semi-Built and Continuous Grain Flow CrankshaftsApproval of a Works for the Manufacture of Chain Cable for ships Procedure 10-2 Approval of a Works for the Manufacture of Offshore Mooring Chain CableBook FProcedures for Approval of a Works for the Manufacture of Iron CastingsProcedure 7-1Approval of a Foundry for the Manufacture of Iron CastingsProcedure 7-2Approval of a Foundry for the Manufacture of Iron Castings for CrankshaftsBook GProcedures for Approval of a Works for the Manufacture of Non-Ferrous AlloysProcedure 8-1Approval of a Works for the Manufacture of Plates, Sections and Bars in Aluminium AlloysProcedure 8-2Approval of a Works for the Manufacture of Aluminium CastingsProcedure 8-3Approval of a Works for the Manufacture of Explosion Bonded Transition JointsProcedure 8-4Approval of a Works for the Manufacture of Aluminium ForgingsProcedure 9-1Approval of a Works for the Manufacture of Copper Alloy Castings for PropellersProcedure 9-2Approval of a Works for the Manufacture of Copper Alloy Castings for Valves, Liners and BushesProcedure 9-3Approval of a Works for the Manufacture of Copper and Copper Alloy TubesBook HProcedures for Approval of a Works or Proving Establishmentsfor Chain Cable and Wire RopeProcedure 10-1Procedure 10-3Approval of a Works for the Manufacture of Fittings for Ship Chain CableProcedure 10-4Approval of a Works for the Manufacture of Fittings for Mooring Chain CableProcedure 10-5Approval of a Works for the Manufacture of Steel Wire RopeProcedure 10-6Recognition of a proving EstablishmentProcedure 10-7Approval of Short Link Chain CableBook J Procedures for Approval of Welding Consumables andManufacture of Fabricated Steel SectionsProcedure 11-1Approval of welding ConsumablesProcedure 11-2Annual Re-approval of Welding ConsumablesProcedure 11-3Acceptance of a QA System for Maintenance of Approval of WeldingConsumablesProcedure 11-4Approval of Welding Consumables Manufactured Under Guarantee(MUG)Procedure 11-5Approval of Welding Consumables for Companies Marketing aManufacturer’s Approved ProductProcedure 11-6Deleted – now shown in the List of Approved Welding ConsumablesProcedure 11-7Determination of Hydrogen in Weld Metal using a Glycerine MethodProcedure 11-8Determination of Hydrogen in Weld Metal: Adaptation of ISO 3690for Other Welding ProcessesProcedure 11-9Low Hydrogen Approval of Temporary Backing Material for One-sideWeldingProcedure 12-1Approval of a Works for the Manufacture of Fabricated Steel SectionsProcedure 19-3 Approval procedure for water ballast tank coating systems inaccordance with IMO MSC.215(82) and IACS UI SC223 (PSPC-WBT)Book K Procedures for Approval of Plastic MaterialsProcedure 14-1Approval of Gel Coat and Laminating ResinsProcedure 14-2Approval of Fibre ReinforcementsBook LProcedures for Approval of Repair ProceduresProcedure 15-1Approval Scheme for Firms undertaking Thermal Spraying ProcessesProcedure 15-2Approval Scheme for Firms undertaking Electrolytic Plating ProcessesBook MProcedures for the Approval in accordance with the Materials Quality Scheme (MQS)Procedure 1-2Approval of a Manufacturer according to the Materials Quality SchemeBook NProcedures for Approval of NDE Firms & Service Suppliers Procedure 17-1Approval for Thickness Measurement of Hull StructureProcedure 17-2Recognition of NDE CompaniesBook PProcedures for Approval of Paints and CoatingsProcedure 19-1Approval procedure for Laboratories engaged in testing of coating systems in accordance with IACS Z17 and IMO MSC. 215(82) and/or MSC.288(87).Procedure 19-2Approval procedure for Laboratories engaged in testing of corrosion resistant steels in accordance with IMO MSC.289(87)Procedure 19-4Approval procedure for cargo oil tank coating systems in accordancewith IMO MSC.288(87) and IACS UI SC259 (PSPC-COT)Procedure 19-5Approval procedure for pre-fabrication primersProcedure 19-6Procedure for recognition of TBT-free anti-fouling coatings inaccordance with IMO AFS ConventionProcedure 19-7Procedure for recognition of corrosion control coatingsProcedure 19-8Procedure for recognition of abrasion resistant ice coatingsProcedure 19-9Procedure for recognition of maintenance coatingsLloyd’s Register Group Limited, its subsidiaries and affiliates and their respective officers, employees or agents are, individually and collectively, referred to in this clause as ‘Lloyd’s Register’. Lloyd’s Register assumes noresponsibility and shall not be liable to any person for any loss, damage or expense caused by reliance on the information or advice in this document or howsoever provided, unless that person has signed a contract with the relevant Lloyd’s Register entity for the provision of this information or advice and in that case anyresponsibility or liability is exclusively on the terms and conditions set out in that contract.© Lloyd's Register Group Limited 2015. All rights reserved.Except as permitted under current legislation no part of this work may be photocopied, stored in a retrievalsystem, published, performed in public, adapted, broadcast, transmitted, recorded or reproduced in any form or by any means, without the prior permission of the copyright owner. Enquiries should be addressed toLloyd's Register Global Technology Centre, Southampton Boldrewood Innovation Campus, Burgess Road,Southampton, SO16 7QF.。
- 1、下载文档前请自行甄别文档内容的完整性,平台不提供额外的编辑、内容补充、找答案等附加服务。
- 2、"仅部分预览"的文档,不可在线预览部分如存在完整性等问题,可反馈申请退款(可完整预览的文档不适用该条件!)。
- 3、如文档侵犯您的权益,请联系客服反馈,我们会尽快为您处理(人工客服工作时间:9:00-18:30)。
Materials and Qualification Procedures for ShipsBook GProcedure 9-1Approval of a Works for the Manufacture of Copper Alloy Castings for PropellersRevision 1, Sept 2013Lloyd’s Register Group Limited, its subsidiaries and affiliates and their respective officers, employees or agents are, individually and collectively, referred to in this clause as ‘Lloyd’s Register’. Lloyd’s Register assumes no responsibility and shall not be liable to any person for any loss, damage or expense caused by reliance on the information or advice in this document or howsoever provided, unless that person has signed a contract with the relevant Lloyd’s Register entity for the provision of this information or advice and in that case any responsibility or liability is exclusively on the terms and conditions set out in that contract.© Lloyd's Register Group Limited 2014. All rights reserved.Except as permitted under current legislation no part of this work may be photocopied, stored in a retrieval system, published, performed in public, adapted, broadcast, transmitted, recorded or reproduced in any form or by any means, without the prior permission of the copyright owner. Enquiries should be addressed to Lloyd's Register Group Limited, 71 Fenchurch Street, London, EC3M 4BS.Approval of a Works for the Manufacture of Copper Alloy Castings for Propellers1 General Requirements1.1 The Approval Process1.1.1 The approval scheme is intended to verify the manufacturer’s capability toprovide satisfactory products under effective process, production andinspection controls in accordance with the Rules for the Manufacture, Testing & Certification of Materials Chapter 1.1.1.2 In order that consideration may be given to approval of a foundry for themanufacture of copper alloy castings for propellers, the process given inSection 2 is to be followed.1.1.3 Works are to communicate to Surveyors the information which will result inthe following reports, each of which is to be submitted to the Materials andNDE Department (MNDE) by the surveyor:•An initial report giving the information listed in Sections 3 and 4, together with a proposed test programme in accordance with section5.• A final report containing the results of approval tests carried out under Sections 5 and 6.1.1.4 The name of the approved works will appear in Lloyd’s Register’s List ofApproved Manufacturers of Copper Alloy Castings which is published onLloyd’s Register’s Class Direct website ().1.2 Scope1.2.1 The procedure applies to foundries manufacturing propeller and propellerblade castings in copper base alloys. (as included in Chapter 9, Section 1 of LR Rules for Materials)Rules1.3 Related1.3.1 Lloyd’s Register’s Rules and Regulations for the Classification of Ships(hereinafter referred to as the Rules for Ships).1.3.2 Lloyd’s Register’s Rules for the Manufacture, Testing and Certification ofMaterials (hereinafter referred to as the Rules for Materials).2 Application for Approvalapproval2.1 Stagesof2.1.1 This section sets out the five stages involved in the granting of Lloyd’s Registerapproval as follows.(a) Preliminary Review [Stage 1]The purpose of the preliminary review is to confirm the general capabilities of the works and identify any major non-compliance which will need to be addressed prior to further consideration of the approval process. This review may involve a preliminary assessment visit to the works.During the course of the review the works shall also demonstrate to the satisfaction of the surveyor that they operate a robust Health & Safety Management System.Based upon the findings of the preliminary review, the surveyor will issue areport to the company :•Giving a recommendation that the works approval process proceeds to the next stage (see the Flow Chart below) or•Giving the reasons why the works is not considered suitable for LR approval at this time.(b) Submission of Works Approval Information [Stage 2]Following the surveyor’s recommendation to progress with the approval process, the manufacturer will be invited to compile and submit the detailed information requested in Sections 3 and 4 to the local Lloyd’s Register office.The report shall be formatted to follow the sections and sub-sections of this procedure and shall preferably be submitted in electronic format. The report and all supporting documents should be presented in English or annotated in English in an appropriate manner.Additionally, the manufacturer must submit a proposed test programme in accordance with Section 5.The local surveyor will review the submitted information from the works and shall conduct an on-site survey during which the contents of the submitted information are verified and any technical or procedural issues related to the approval are resolved.On satisfactory review of these documents, the surveyor will submit thefollowing to the Materials & NDE Department:• A short visit report•The information submitted by the works in accordance with Sections 3 & 4• A proposed test programme in accordance with Section 5(c) Review of Submission by Materials & NDE Department [Stage 3]Lloyd’s Register Materials & NDE Department will review the submitted information before any manufacture and testing commences.Where necessary, clarification will be sought regarding major issues that are discovered during this stage of review of the submitted information.The outcome of the review will be conveyed to the surveyor and the Materials & NDE Department will confirm the approval test programme and any otheractions they require the surveyor to carry out during the surveyor’sattendance at the manufacturer whilst witnessing approval manufacture andtesting.The surveyor will communicate this information to the manufacturer.(d) Approval Tests & Survey [Stage 4]Following Materials & NDE Department agreement to the test plan, the Works will manufacture the approval test castings. The Lloyd’s Register surveyor will arrange to attend the works to survey the manufacture and witness the testing of the approval test products.In addition, during attendance, the surveyor will follow up on actions requested by the Materials & NDE Department.The surveyor will appropriately appraise and endorse all test reports which are required by this procedure.The surveyor will review a manufacturer’s report which collates all requiredinformation in a clear and concise manner. The format of the report mustfollow the sections and sub-sections of this procedure and it shouldpreferentially be in electronic form. If the report is found to be satisfactory by the surveyor, it will be endorsed by the manufacturer and verified andstamped by the LR surveyor. It will then be forwarded to the Materials & NDE Department for final review and approval.(e) Review of Results [Stage 5]The surveyor’s report and endorsed test results will be reviewed by Lloyd’sRegister Materials & NDE Department. During this process, points ofclarification may be required to be followed up with the surveyor incooperation with the manufacturer. On satisfactory review the works will beadded to Lloyd’s Register’s list of approved manufacturers and a Certificate of Approval will be issued.3 Written information required for the manufacturing capability review3.1 Product specific information3.1.1 The manufacturer is to provide the following product related details in writing tothe local surveyor:(a) Types of castings and alloy grades in general production.(b) The finished weight as dressed (ie after removal of all runners and feeders) of thelargest casting which can be manufactured for each generic copper grade.(c) Largest casting in terms of finished weight after removal of all runners andfeeders (as dressed condition) required for approval.(d) Estimated total annual production of finished castings in each generic coppergrade(e) Types of castings and alloy grades for which approval is required.(f) Contact details that the manufacturer would like on the published approved listincluding sales telephone number, fax number, email address and website.(g) The year of issue of the copy of the Rules for Materials which are held by theWorks and the means whereby possible Rule changes are incorporated intocompany procedures.(h) Details of the inspection and quality control systems established in the works,including details of the personnel involved(i) Third party certification held (eg ISO 9001, ISO 14001 and/or ISO 18001, etc), asapplicable.(j) A flow diagram showing all stages of production, testing and inspection points. (k) An organogram showing the organisational structure shall be submitted.3.2 Process specific information3.2.1 The manufacturer is to provide the following process related details in writing tothe local surveyor:(a) Melting facilities; details of the number of individual melting units and for eachunit; type and individual single melt capacity.(b) Details of the origin and storage of raw materials.(c) Details of melting and refining practices.(d) Production of moulds and cores; details are required of; the different types ofsand systems used; types of moulding and core making systems used; routinedaily, weekly, monthly tests carried out on mixed sand and the raw materials for mould and core production; method and frequency of sand mixer calibrations;methods used to determine that moulds and cores are sufficiently cured forcasting; application methods and materials used for mould and core coating,including quality control checks.(e) Melting and charge composition control; details are required of the typicalmaterials used for charge make, and method of calculating / controllingcomposition; charging practice and control including typical melt out; holdingand superheat temperatures.(f) Casting and pouring practices and controls; details of the types and range of sizesof pouring ladles; method of pouring (manual / automatic); typical castingtemperatures used for different casting weights and/or configurations.(g) Facilities and practices for mechanical testing; details should include the normalpractices for manufacture and preparation of mechanical test specimens and the name of the manufacturer, model number or description, manufacturers unique serial number, maximum test capacity and calibration status for each item ofmechanical test equipment.(h) Heat treatment facilities and control; details should include; the number offurnaces used including dimensions, type of fuel used and facilities fortemperature measurement and control including positions of thermocouples;details of the methods, frequency, and acceptance parameters of checks carriedout to assess the temperature distribution of each furnace; details of how eachfurnace is loaded including restrictions of volume, mass, number of items, etc;details of the loading temperatures, heating rates, holding times (including how these have been determined) and cooling rates used.(i) Welding procedures for each type and grade of copper casting material for whichapproval is required. Each welding procedure submitted for review is to include, as a minimum, the following information:i) Welding equipment.ii) Welding process.iii) Parent metal.iv) Welding consumables.v) Type of joint and preparation of the edges to be welded as well as backings.vi) Thickness of the parent metal.vii) Welding position.viii) Welding sequence (number and order of metal depositions).ix) Welding parameters: amperage and voltage, welding speed.x) Pre-heating and post weld heat treatment.xi) Heat input and interpass temperature(j) Details of any subcontracted activities and particulars relating to the related requirements of the appropriate sections above (eg Section (h) applies tosubcontracted heat treatment)4 Survey of the manufacturing, testing and inspection capabilities4.1 The local surveyor will carry out a survey of the works and subcontractor asapplicable, which will include the manufacturing, inspection and testing processes and procedures. As a minimum, the following manufacturing areas are to beincluded in the survey, with a view towards verification of the informationcontained in the manufacturer’s written report (see Section 3 above). Ifpermitted, photographs might be used to support appropriate information.(a) Raw materials used and their procurement and storage(b) Manufacture and control of patterns and core boxes(c) Production of moulds and cores(d) Methoding practicesfacilities(e) Melting(f) Melting and charge composition and control, including de-oxidation practices.(g) Chemical analysis equipment and practice(h) Casting and pouring practices and control(i) Equipment and procedures for fettling/dressing of castings(j) Product and test material Identification and control(k) Heat treatment facilities and controls(l) Facilities and practices for mechanical testing(m) Facilities and control procedures for metallographic testing and microstructure control(n) Facilities and practices for routine castings inspection, including NDE(o) Manufacture, test or inspection activities or services which are sub-contracted and the controls in place4.2 Where responses to any questions raised by the survey are not forthcoming fromthe manufacturer, the reasons for omission must be clearly stated in writing.4.3 Following review of submitted documentation and its verification through thesite survey, the surveyor will issue a report of their findings together with aproposed scope of approval testing based upon the guidance given in Section 5and Section 6. The surveyor will issue a final recommendation stating theiropinion as to whether the works should be considered for the next stage ofapproval. If the surveyor decides that approval application would not beappropriate at this time, this will be communicated to the works together withthe reasons why this decision was made and suggestions as to actions which could be undertaken to improve the application.If the surveyor deems the approval application to be suitable for progression, the documents listed in 3.1.2 and the proposed test programme will be sent to theMaterials & NDE Department for specialist review before testing commences.5 Approval test programme 5.1Selection of material5.1.1 Approval tests are to be carried out on at least three castings taken from currentproduction. Where possible, one of the castings selected for this purpose is to be a propeller with a diameter approaching the maximum which can bemanufactured. Approval will be limited to the grades of alloy of the castings submitted.5.1.2 Approval is based on the dressed weight of castings (after removal of runningand feeding systems) and a minimum of one casting shall be at the maximum weight for which approval is required. If the maximum weight is less than 50 tonnes, a justification could be submitted for increasing the maximum weight of approval to a figure of 1.33x the weight of the largest sample casting. This request would be subject to review by the Materials and NDE Dept. 5.1.3 Testing shall be carried out according to Chapter 2 and Chapter 9 of LR Rules forMaterials or to an agreed National Standard or proprietary specification. Details of the applicable testing standards shall be submitted. 5.1.4 For each of the proposed test castings, the following shall be providedi) A sketch showing method of casting with details of the gating and feeding systems, this should clearly show the positions and sizes of pouring basins, down-sprues, runner bars, in-gates, and feeders. Types of feeders used should be detailed, as well as any other aids used in the methoding such as chills or filters. Where computer simulations have been used to assess the methoding used, the results should be submitted together with the name of the software used.ii) The aim chemical analysis to which the casting is to be made (including tolerances).iii) Applicable specification. Copies of specifications should be submitted where these are not National/International standards. English copies are preferred although documents annotated in English will be acceptable.iv) The NDE procedures to be used (as approved by Level III NDE specialist) and proposed test locations for each test casting are to be submitted.(v) The full details of the proposed heat treatments (full thermal cycle) which is applied to each test casting.5.1.5 Testing is required to include weld repair procedures for each type and grade ofcopper casting material for which approval is being sought.All repairs made to copper castings during manufacture are to be in accordancewith the requirements of Ch 9 of the Rules for Materials.All welders and welding procedures and qualifications in accordance with arecognized National or International Standard. As an alternative to this, a welder may be approved on the basis of past experience provided that qualification tests acceptable to the Surveyor are undertaken satisfactorily for each type and gradeof material.Material to used in qualification tests is to be of a cast and of a size suitable toensure a reasonable heat distribution and suitable equivalence to practical useWeld consumables are to be approved typesAll tests and examinations are made after any heat treatment has been carriedout. For copper alloy castings the weld test sample is to be subjected to a stressrelief heat treatment prior to testing.5.2 Tests, test samples and specimens5.2.1 The dimensions of separately cast test samples, dimensions of test specimens andmechanical testing procedures are to be in accordance with Ch 2 and Ch 9 of theRules for Materials or an agreed specification. The test samples are to be taken at the end of the pouring of the castings.5.2.2 The following tests and examinations are to be carried out, as a minimum, oneach casting submitted for approval tests:(a) Visual examination before and after final machining.(b) Dye penetrant testing of all surfaces after final machining.(c) Ultrasonic or radiographic examination, where appropriate, particularly in way ofthe blade roots.(d) Mechanical tests in accordance with the requirements of the applicablespecification.(e) Chemical analysis of the propeller including, for the manganese bronze alloys, thevalue for the calculated zinc equivalent.(h) Representative photomicrographs of the test material at x100 magnification. Thisis to be issued in the form of a report giving which gives details of the etchantsused and a description of the microstructure shown.(i) For manganese bronze alloys determination of the proportion of alpha phasepresent in the structure(j) Where castings are made to National, International, or proprietary specifications the results of any additional tests and inspections required by these must besubmitted.5.2.3 For approval of the weld repair process, tests and examinations on the weldedassembly are to include the following:(a) Two cross-weld tensile tests. The minimum tensile strengths are to be: Grades Cu1 and Cu2 375 N/mm2 Grade Cu3 500 N/mm2 Grade Cu4 550 N/mm2(b) Two root bend and two face bend tests. The tests are to be made over a mandrelwith a diameter six times the thickness of the test specimen. Thebend angles at which cracking commences are to be recorded for information.Photographs of the specimens after test are to be included in the report. (.(c) Where the Rules require the cast material to be impact tested, then impact testsshould be taken from the weld centreline and heat affected zone and exhibitproperties equivalent to that specified for the cast material.(d) Two macrographs showing the weld, heat affected zone and parent metal andphotomicrographs at x100magnification showing the microstructures of thesethree regions6Specific approval test results6.1 General6.1.1 Following Materials & NDE Department agreement to the test plan, the Workswill manufacture approval test castings and stages of manufacture and all approval testing, including weld procedure testing, is to be witnessed by the Lloyd’s Register surveyor.All test results will be endorsed by the surveyor.All details listed in Section 6.2 together with the test results will be submitted tothe Materials & NDE Department for review.6.2 Approval test submission6.2.1 For each casting selected for approval tests, the foundry is to provide thefollowing information:(a) Information required as indicated in Section 5.1.4.(b) Results of tests undertaken in accordance with 5.2.2 and 5.2.36.2.2 In addition to selecting and witnessing the above tests, surveyors will carry out acareful visual examination of other products in general production and report on the general quality and surface condition.6.2.3 The surveyor will submit the information requested in Section 6.1-6.2 to Materials& NDE Department together with any additional survey reports that were requested by Materials & NDE Department specialists.Photographs may be used to support the submitted information.7Validity of approval certificateapproval7.1 Initial7.1.1 On satisfactory review of the submitted approval test report Materials & NDEDepartment will enter the manufacturer onto the List of ApprovedManufacturers and an initial approval certificate will be issued.7.1.2 The approval will state the approved copper alloy grades and the maximumweight.7.1.3 The initial approval certificate will have a validity of three years.7.2 Extension of the scope of approval7.2.1 Manufacturers who intend to extend their scope of approval will be required torepeat the approval process in Section 2 and the scope of information to besubmitted and test program is to be agreed with Materials & NDE Department.7.3 Re-approval of works7.3.1 For the validity to be renewed for a further three years the Surveyors shouldundertake a periodic inspection in accordance with Procedure 1-1. To ensurecontinuity, this should be carried out within six months of the approval expirydate.7.3.2 It is a Rule requirement that during material surveys the works will be subject toregular visits to confirm continued compliance with the original approval. Thefrequency of visits will depend on the frequency of material surveys. Records of these visits will be kept by the surveyors.7.3.3 Manufacturers that have not produced products under Lloyd’s Register surveyduring the approval period must either conduct new approval tests (according to Sections 5 and 6) or contact Lloyd’s Register to agree on any additionalrequirements to continue approval.7.3.4 Where a manufacturer physically moves the location of an approved works fromthe approved location to a new site, the manufacturer will be required to follow the initial approval process in full unless they can present a satisfactory case tothe MNDE Dept that this would not be necessary.。