CS 301 Fall 2002Assembly Instructions
Festo产品说明书
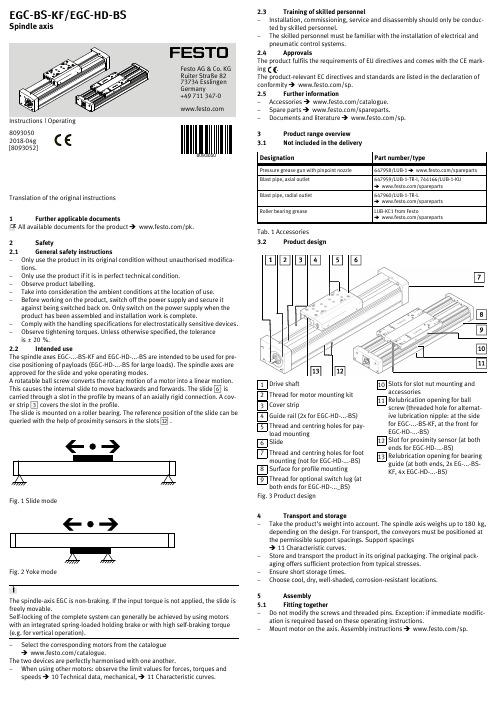
Translation of the original instructionsFurther applicable documentsè /pk.2Safety2.1General safety instructions–Only use the product in its original condition without unauthorised modifications.–Only use the product if it is in perfect technical condition.–Observe product labelling.–Take into consideration the ambient conditions at the location of use.–Before working on the product, switch off the power supply and secure itagainst being switched back on. Only switch on the power supply when theproduct has been assembled and installation work is complete.–Comply with the handling specifications for electrostatically sensitive devices.–Observe tightening torques. Unless otherwise specified, the toleranceis ± 20 %.2.2Intended useThe spindle axes EGC...BSKF and EGCHD...BS are intended to be used for precise positioning of payloads (EGCHD...BS for large loads). The spindle axes areapproved for the slide and yoke operating modes.A rotatable ball screw converts the rotary motion of a motor into a linear motion.This causes the internal slide to move backwards and forwards. The slide 6 iscarried through a slot in the profile by means of an axially rigid connection. A cover strip 3 covers the slot in the profile.The slide is mounted on a roller bearing. The reference position of the slide can bequeried with the help of proximity sensors in the slots aB.Fig. 1 Slide modeFig. 2 Yoke modeThe spindleaxis EGC is nonbraking. If the input torque is not applied, the slide isfreely movable.Selflocking of the complete system can generally be achieved by using motorswith an integrated springloaded holding brake or with high selfbraking torque(e.g. for vertical operation).–Select the corresponding motors from the catalogueè /catalogue.The two devices are perfectly harmonised with one another.–When using other motors: observe the limit values for forces, torques andspeeds è 10 Technical data, mechanical, è 11 Characteristic curves.2.3Training of skilled personnel–Installation, commissioning, service and disassembly should only be conducted by skilled personnel.–The skilled personnel must be familiar with the installation of electrical andpneumatic control systems.2.4ApprovalsThe product fulfils the requirements of EU directives and comes with the CE marking .The productrelevant EC directives and standards are listed in the declaration ofconformity è /sp.2.5Further information–Accessories è /catalogue.–Spare parts è /spareparts.–Documents and literature è /sp.3Product range overview3.1Not included in the deliveryDesignationPart number/typePressure grease gun with pinpoint nozzle647958/LUB1 è /sparepartsBlast pipe, axial outlet647959/LUB1TRI, 744166/LUB1KUè /sparepartsBlast pipe, radial outlet647960/LUB1TRLè /sparepartsRoller bearing grease LUBKC1 from Festoè /sparepartsTab. 1 Accessories3.2Product design1Drive shaft2Thread for motor mounting kit3Cover strip4Guide rail (2x for EGCHD...BS)5Thread and centring holes for payload mounting6Slide7Thread and centring holes for footmounting (not for EGCHD...BS)8Surface for profile mounting9Thread for optional switch lug (atboth ends for EGCHD..._BS)10Slots for slot nut mounting andaccessories11Relubrication opening for ballscrew (threaded hole for alternative lubrication nipple: at the sidefor EGC...BSKF, at the front forEGCHD...BS)12Slot for proximity sensor (at bothends for EGCHD...BS)13Relubrication opening for bearingguide (at both ends, 2x EG...BSKF, 4x EGCHD...BS)Fig. 3 Product design4Transport and storage–Take the product’s weight into account. The spindle axis weighs up to 180 kg,depending on the design. For transport, the conveyors must be positioned atthe permissible support spacings. Support spacingsè 11 Characteristic curves.–Store and transport the product in its original packaging. The original packaging offers sufficient protection from typical stresses.–Ensure short storage times.–Choose cool, dry, wellshaded, corrosionresistant locations.5Assembly5.1Fitting together–Do not modify the screws and threaded pins. Exception: if immediate modification is required based on these operating instructions.–Mount motor on the axis. Assembly instructions è /sp.8093050EGC-BS-KF/EGC-HD-BSSpindle axis8093050201804g[8093052]Festo AG & Co. KGRuiter Straße 8273734 EsslingenGermany+49 711 34705.2InstallationMounting the axisPrerequisites:1.Position the spindle axis in such a way that its operating elements are accessible (e.g. relubrication openings).2.The mounting components must be outside the travel range of the slide.3.Install spindle axis without tension or distortion.Fig. 54.Mount spindle axis on a mounting surface with flatness of 0.05% of the strokelength, but max. 0.5mm. For gantry applications, attention must also be paid to parallel alignment or product height when aligning the axes.5.Take the required support spacings into consideration .6.Mount the spindle axis è Tab. 2 Interfaces for mounting components. Interfaces for mounting componentsTab. 2 Interfaces for mounting componentsDanger of screws being pulled out if the spindle axis is only mounted to the covers and the torque load around the longitudinal axis is too great.•If there is high loading, mount the spindle axis on the profile with additional mounting components.•Tighten the retaining screws to the following tightening torques:Size7080120185Screw (cover)M5M5M8M10 Tightening torque[Nm] 5.9 5.92447Tab. 3 Tightening torques of the retaining screwsFor installation in a vertical or sloping position:Risk of injury due to falling working loads.In a power failure or if the spindle nut breaks, the working load may fall.•Only use motors with integrated springloaded holding brakes.•Implement external safety precautions to prevent the spindle nut from breaking (e.g. tooth clinking, moveable bolts or emergency buffers).Fig. 6 Working loadMounting the payload1.Position the payload in such a way that the breakdown torque resulting fromthe force F (parallel to the axis of motion) and the lever arm a remains low. 2.Mount the payload on the slide with the screws and centring sleeves.Fig. 8 Maximum screwin depth3.The maximum screwin depth D must not be exceeded.Size7080120125160185220 Screw (side/top)M5M5/M6M5M6M6/M8M6 Max. screwin depth D[mm]8.49.5108.49.51510Centring hole (H7)[mm]Æ5Æ7/Æ9Æ5/Æ9Æ9Æ9Æ9Tightening torque[mm] 5.9 5.9/9.9 5.99.99.9/249.9Tab. 4 Mounting the payloadFor payload with own guide:•Adjust the guides of the payload and spindle axis so that they are exactly parallel. This will avoid overloading the guide and increased wear.For hard and stiff payloads (e.g. made from steel):If the aluminium slide is bent against a curved payload, the service life of the guide will be reduced.•The mounting surface of the payload must have a flatness of t = 0.01 mm.When using additional slides, any differences in height must be compensated.Fig. 9 Flatness of the payloadFor payloads with projection in the longitudinal direction of the slide:•The payload must not knock against the motor.Mounting accessoriesTo protect the end positions against uncontrolled overtravel:•Check whether proximity sensors are necessary (hardware limit switches). If proximity sensors are used as limit switches:•Preferably use proximity sensors with normallyclosed function. These will protect a spindle axis against overtravel of the end position in case of a broken proximity sensor cable.If proximity sensors are used as reference switches:•Use proximity sensors that correspond to the input of the controller being used.•Use inductive proximity sensors with switch lug. Assembly instructions è /sp.•Avoid external influence caused by magnetic or ferritic parts in the vicinity of the proximity sensors (spacing min. 10 mm from slot nuts).To protect the end positions:•Use emergency buffer. Assembly instructions è /sp.To avoid contamination:•Use slot covers in all unused slots.6CommissioningDanger of crushing as a result of moving loads•Do not reach into the path of the moving components.•Install the corresponding protective devices (e.g. protective grille).Incorrect specification values for the braking ramp in STOP statuses (e.g. EMERGENCY OFF, Quick Stop) result in an overloading of the spindle axis and can destroy it or drastically reduce service life.•Check the settings for all braking ramps in the controller or the higherorder controller (deceleration values and jerk).•Taking the travel speed, moving load and mounting position into account, set the deceleration values (brake deceleration and deceleration times) in such a way that the maximum drive torque or feed force of the spindle axis used is not exceeded.•When designing the spindle axis, use the Festo engineering software PositioningDrives è .Blockshaped acceleration profiles (without jerk limitation) cause high peaks in the drive force that can lead to an overloading of the drive. Due to overshooting effects, positions outside of the permissible range may also occur. A jerklimited acceleration specification reduces vibrations in the entire system and has a positive effect on stress in the mechanical system.•Check adjustments to controller settings (e.g. jerk limitation, smoothing of the acceleration profile).Control travel Homing Test runDetermining the approach direction of the motorComparison of real situation tothe image in the controllerChecking the overall behaviourTab. 61.Start control travel with low dynamic response.Even with identical control, motors of the same design turn in opposite directions due to different wiring. The spindle of the EGC turns in a clockwise direction. When the drive trunnion is turned clockwise, the slide moves in the direction of the motor.2.Start homing in accordance with the operating instructions for your motordrive system with low dynamic response to the reference switch.–The homing run may only be performed towards the reference switch.3.Start a test run with low dynamic response4.Check whether the spindle axis fulfils the following requirements:–The slide can move through the complete intended positioning cycle.–The slide stops as soon as it reaches a limit switch.7OperationMovement of componentsRisk of injury caused by rotating components.•Protective devices must be in place before commissioning the drive.•Do not reach into the swivel angle of the drive.For installation in a vertical or sloping position:The reference position is lost when the motor is dismounted (e.g. when turning the motor around).•Start homing in order to determine the reference position once more è 6 Commissioning.8ServicePerform the following actions during each service:•Check the reversing backlash of the slide for wear to the spindle nut. The wear on the ball screw will lead to increased noise in the long term and thus cause the ball screw to block or the spindle nut to break.Size7080120125160185220Max. permissible reversingbacklash[mm]0.10.10.20.10.10.20.2 Tab. 7 Max. permissible reversing backlashThe lubrication interval S int is dependent on the load acting on the product.Cut the lubrication interval S intè Fig.11 by half if any of the following situations apply:•Dusty and dirty environment•Nominal strokes > 2000 mm•Speeds > 2 m/s•Travel profile Z triangular operation (frequent acceleration and braking)•Ambient temperatures > 40°C•Service age of product > 3 yearsWe recommend lubricating the ball screw and the bearing guide at the same time. The shorter lubrication interval should be used here. If several of these factors apply at the same time, the lubrication interval should be quartered.Lubrication Ball screw Bearing guide Cover strip Guide railLubricating point Relubricationopening (lubrication nipple)Relubricationopening (lubrication hole)InterfaceLubrication intervalè Fig.11If required1)Grease2)Roller bearing grease1) or if the component no longer has a layer of grease2) Pressure grease gun, Blast pipes and greaseTab. 8 LubricationGrease the ball screw:1.Calculate the load comparison factor f v with the help of the formula for combined loads (è 10 Technical data, mechanical).Fig. 11 Lubrication interval2.Determine the lubrication interval S int from èFig.11.Fig. 12 Relubrication opening in spindle axis3.Grease the spindle axis at the relubrication opening (lubrication nipple)è Fig.12.4.Move the slide the complete travel distance during greasing in order to distribute the grease evenly inside.Grease the bearing guide (not possible for EGC...GP/GQ):1.Calculate the load comparison factor f v with the help of the formula for combined loads è 10 Technical data, mechanical.2.Determine the lubrication interval S int from èFig.11.Fig. 13 Greasing the bearing guide3.Grease the bearing guide on both sides at all relubrication openings (lubrication holes) è Fig.13.4.Move the slide the complete travel distance during greasing in order to distribute the grease evenly inside.8.1Cleaning and maintenance•Clean the guide rail with a soft cloth as required. Cleaning agents include allnonabrasive media.9Malfunctions 9.1Fault clearanceMalfunctionPossible causeRemedyCoupling mounted too closeObserve the permissible coupling spacingsè /sp.Install spindle axis without tension è 5.1 Fitting together.Align the spindle axis so that it is exactly parallel to the second axis.Grease the spindle axis è 8 Service.TensionsAlter the travel speed.Squeaking noises, vibrations,axis not running smoothly.Incorrect controller settings Change controller parameters.MalfunctionPossible causeRemedySqueaking noises, vibrations,axis not running smoothly.Bearing guide is faulty.Return spindle axis to Festo for repair.Coupling hub spins freely.Check mounting of the motor mounting kitè /sp.Loads too high.Reduce payload/travel speed.Slide does not move.Retaining screws for the payload are too long.Observe the maximum screwin depth è 5.2 Installation.The reversing backlash is too large è 8 Service.WearReturn spindle axis to Festo for repair è 9.2 Repair.Slide travels beyond end position.Proximity sensors do not switch.Check proximity sensor, connections and controller.The idling torque increases.WearReturn spindle axis to Festo for repair è 9.2 Repair.Tab. 9 Fault clearance 9.2Repair–Send the spindle axis to the Festo repair service.–Information about spare parts and accessoriesè /spareparts.10Technical data, mechanicalSize 1)7080120125Spindle pitch101020102510Design Electromechanical linear axis with ball screw GuideRecirculating ball bearing guide Mounting position Any Max. feed force Fx[N]4006501500400Max. noload driving torque 2)[Nm]0.450.752.250.45Max. rotational speed [rpm]300036003000Max. speed [m/s]0.510.61.50.5Max. acceleration [m/s 2]15Repetition accuracy [mm]± 0.02Reversing backlash (new)[mm]< 0.01Reversing backlash (faulty)è 8 ServiceFeed constant [mm/rev]101020102510Ambient temperature [°C]–10 … +60Degree of protectionIP401) The PositioningDrives engineering software is available for sizing tasks.2) measured at max. speed.Tab. 10 Technical data, mechanical, size 70...125Size 1)160185220Spindle pitch1020401025Design Electromechanical linear axis with ball screw GuideRecirculating ball bearing guide Mounting position Any Max. feed force Fx[N]65030001500Max. noload driving torque 2)[Nm]0.75 6.52.25Max. rotational speed [rpm]30003600Max. speed[m/s]0.5120.6 1.5Max. acceleration [m/s 2]15Repetition accuracy [mm]± 0.02Reversing backlash (new)[mm]< 0.01Reversing backlash (faulty)è 8 ServiceFeed constant [mm/rev]1020401025Ambient temperature [°C]–10 … +60Degree of protectionIP401) The following tool is available for sizing tasks: PositioningDrives engineering software.2) measured at max. speed.Tab. 11 Technical data, mechanical, size 160 (220)Tab. 12 Technical data, mechanical, EGC...BSKFCondition for combined loads:Tab. 13 Technical data, mechanical, EGCHD...BS11Characteristic curvesMax. permissible support spacing L as a function of the force F for EGC...BSKF: Fig. 14 Support spacing EGC-...-BS-KF600100014001800220026003000340024681012141618202224Fig. 16EGC-...-BS-KF600100014001800220026003000340024681012141618202224Fig. 17Fig. 18Fig. 19 Force distributionY-Richtung EGC-HD-...-BS10001500200025003000012345678910111213EGCHD160Fig. 20Z-Richtung EGC-HD-...-BS50010001500200025003000012345678910111213EGCHD160Fig. 21Speed v as a function of working stroke l:EGC-70-BS-KF50010001500200000.20.40.60.81Fig. 22EGC-80-BS-KF50010001500200000.20.40.60.81Fig. 23EGC-...-BS-KF5001000150020002500300000.40.81.21.62Fig. 24EGC-185-BS-KF5001000150020002500300000.40.81.21.62Fig. 25•Graphs of maximum feed force (N) for all sizes è /catalogue。
DC-20 GHZ MMIC SPDT 反射开关数据手册说明书

ELECTRICAL SPECIFICATIONS (based on on-wafer measurements):
PARAMETER
CONDITIONS
MIN
Insertion Loss
(DC-10) GHz, Small Signal
Insertion Loss
(10-15) GHz, Small Signal
-5V control
Note: TAMBIENT = 25°C, Vctrl = 0V/-5V, ZIN = ZOUT = 50Ω
TYP
1.2 1.35 1.55 48 42 37 15 10 26
MAX
UNITS
dB dB
dB dB dB dB dB ns dBm
Tel: +44 (0) 1325 301111
The back of the die is metallised and the recommended mounting method is by the use of solder or conductive epoxy. If epoxy is selected then it should be applied to the attachment surface uniformly and sparingly to avoid encroachment of epoxy on to the top face of the die and ideally should not exceed half the chip height. For automated dispense Ablestick LMISR4 is recommended and for manual dispense Ablestick 84-1 LMI or 84-1 LMIT are recommended. These should be cured at a temperature of 150°C for 1 hour in an oven especially set aside for epoxy curing only. If possible the curing oven should be flushed with dry nitrogen.
CS作弊参数

CS作弊参数CSO—NST程序很复杂,无限子弹我也不会,但我会改后备弹药打开文件nst_wpn.ini路径X:\CSO-NST1009 BY CSO单机版\cstrike\addons\amxmodx\configs\nst_wpn.ini查找你要修改的武器名字查找“破碎炙炎”能找到这么一段[type]5[name]破碎炙炎[model]dbarrel[wpn_change]21[damage]3.5[speed]1.0[zoom]0[c lip]2[ammo]32[recoil]0.7[gravity]240[knockback]20[cost]2500[so und]1[team]0[buy]1[s_timereload]1.7子弹数就改[clip]2 ,例如我要改成能装10发子弹就改成[clip]10后备弹药就改[ammo]32 ,想改多少就改多少后坐力就改[recoil]0.7 ,改成0就没后坐力了击退就改[knockback]20 ,改大了僵尸到处乱飞购买金钱就改[cost]2500 ,改成0就免费送了====================================== ========================================= ==================机甲风暴最佳答案路径X:\CSO-NST1011\cstrike\addons\amxmodx\configs找到nst_human_scenario.ini 这个文件打开HUMAN_HEALTH = 100 生命HUMAN_ARMOR = 100 护甲MONEY_START = 32000 开始金钱MONEY_MAX = 64000 金钱上限====================================== ========================================= ==================最佳答案这需要修改参数。
c++编译器错误代码大全

C/C++编译器错误代码大全-编译器错误C2001 错误消息常数中有换行符字符串常数不能继续到第二行,除非进行下列操作:•用反斜杠结束第一行。
•用一个双引号结束第一行上的字符串,并在下一行用另一个双引号开始该字符串。
用\n 结束第一行是不够的。
编译器错误C2002 错误消息无效的宽字符常数多字节字符常数是非法的。
通过检查下面的可能原因进行修复1.宽字符常数包含的字节比需要的多。
2.未包括标准头文件STDDEF.h。
3.宽字符不能与一般字符串连接。
4.宽字符常数之前必须是字符“L”:编译器错误C2003 错误消息应输入“defined id”标识符必须跟在预处理器关键字之后。
编译器错误C2004 错误消息应为“defined(id)”标识符必须出现在预处理器关键字之后的括号中。
也可能由于为V isual Studio .NET 2003 进行的编译器一致性工作生成此错误:在预处理器指令中缺少括号。
如果预处理器指令缺少右括号,则编译器将生成一个错误。
编译器错误C2005 错误消息#line 应跟一个行号,却找到“token”#line 指令后面必须跟行号。
编译器错误C2006 错误消息“directive”应输入文件名,却找到“token”诸如#include 或#import 等指令需要文件名。
若要解决该错误,请确保token 是一个有效文件名。
并且将该文件名放在双引号或尖括号中。
编译器错误C2007 错误消息#define 语法#define 后未出现标识符。
若要解决该错误,请使用标识符。
编译器错误C2008 错误消息“character”: 宏定义中的意外该字符紧跟在宏名之后。
若要解决该错误,宏名之后必须有一个空格。
编译器错误C2009 错误消息宏形式“identifier”重复使用宏定义的形参表多次使用该标识符。
宏的参数列表中的标识符必须是唯一的。
编译器错误C2010 错误消息“character”: 宏形参表中的意外该字符在宏定义的形参表中使用不正确。
CS_Command_命令

+forward 客户端 玩家 前进
+jump 客户端 玩家 跳跃
+klook 客户端 玩家 用键盘看
+left 客户端 玩家 向左转
+lookdown 客户端 玩家 向下看
+lookup 客户端 玩家 向上看
+mlook 客户端 鼠标 用鼠标看
users 列出线上使用者名称及Userid(Server产生)及Uniqueid(WON server产生)
changelevel 地图名 立刻换地图,所有玩家不会离开游戏
map 地图名 立刻换地图,但所有玩家会离开游戏
mp_maxrounds X X→几回合之后换地图
mp_winlimit X 任一队胜X场便换图,例5战3胜制,X=3
cl_gaitestimatio 1 是否衔接人物两个动作
gl_picmip 0 渲染质量,越大的数字图象质量越低速度越快
r_drawviewmodel 1 是否显示武器
fastsprites 0 烟雾特效,0最好,3最差
录像(DEMO)相关指令
说明:要使用本类的指令要在启动CS的快捷方式中加入-condebug,注意:参数和参数之间要有空格
net_graphwidth 192 设定显示工具的大小(设定范围不详)
disconnect 离开游戏,保持在CS console状态
exit 离开游戏退回到桌面
quit 同上
reconnect 不离线重新连接服务器
retry 离线并重新连接服务器
connect 服务器地址 连接到指定的Server
CCS3.3编译中常见错误解决(有备无患)

CCS3.3中常见问题解决(待续)(2013-05-22 18:05:59)转载▼问题1:用CCS3.3编译时出现“entry point other than _c_int00 specified”的错误的问题解决出现的错误如下:[Linking...] \"D:\\CCStudio_v3.1\\C2000\\cgtools\\bin\\cl2000\" -@\"Debug.lkf\">> warning: entry point other than _c_int00 specifiedBuild Complete,0 Errors, 1 Warnings, 0 Remarks.此错误在Autoinit Model:Project>Build Options…>Linker>Basic选择Run-Time Autoinitialization不变,只需把Code Entry Point:项的code_start 改为:c_int0问题2:用CCS3.3编译时出现“last line of file ends without a newline”的错误的问题解决出现的错误如下:"expFile.c", line 7: warning: last line of file ends without a newline[Linking...] "C:\CCStudio_v3.3\C2000\cgtools\bin\cl2000" -@"Debug.lkf"Build Complete,0 Errors, 1 Warnings, 0 Remarks.此错误在程序.C代码的最后一行打几个回车问题3:用CCS3.3编译时出现“linking files with incompatible memory models (*\\rts2800.lib', member'args_main.obj')”的错误的问题解决出现的错误如下:>> error: linking files with incompatible memory models (library 'C:\\CCStudio_v3.3\\C2000\\cgtools\\lib\\rts2800.lib', member 'args_main.obj')>> Compilation failureBuild Complete,n Errors, 0 Warnings, 0 Remarks.此错误将库文件rts2800.lib移除(右击rts2800.lib>Remove from projet),然后添加rts2800_ml.lib库(右击Libraries>Add Files to project...>CCstdio_v3.3\C2000\cgtools\librts2800_ml.lib)。
BOB Travel Bag Assembly Instructions说明书

Congratulations on your purchase of the BOB ® Travel Bag. It is designed to contain and protect your single seat BOB Sport Utility, Revolution ® or Stroller Strides ® stroller duringtransport. The Travel Bag may be rolled and guided by the end handle or carried via shoulder strap and/or side handle. The Travel Bag will need to be assembled prior to use.Before attempting to assemble or use your new Travel Bag, read and understand these instructions to ensure proper assembly and operation. If you are unclear on any point,contact your dealer or BOB before use.. This product is designed exclusively for use with BOB single Sport Utility, Revolution or Stroller Strides ® strollers. It is not intended for use with any other strollers, accessories or products.. When not in use, keep out of reach of children.. Maximum Weight Capacity 30lb (13.6Kg) Do not overload.. Never leave child unattended.. The Travel Bag is designed to reduce the possibility of damage to your stroller during transportation but does not eliminate it completely.. We recommend inspecting your stroller and Travel Bag before and after each transport journey to ensure functionality and safety.ASSEMBLY INSTRUCTIONS1. Remove bag from packaging. Place bag fl at on ground or table with wheels down. Open Travel Bag top cover zipper and locate components. Fig. A identifi es the anatomy and components of the Travel Bag.2. Unfasten the Velcro of the fi ve fabric fl aps along inboard sides of travel bag. Temporarily place top of each over side and out of the way as shown in Fig. A.3. Locate wall support panel, (black plastic sheet) unroll and note orientation of notch at each end.4. Orient wall support panel with notches toward top cover (up) and feed each end into each respective pocket along inside corners of Travel Bag as shown in Fig B. Push ends of wall support panel fully into each pocket until notch is aligned with pocket seam.5. Align and fasten Velcro of fabric fl aps straight and secure around wall support panel. You may fi nd it helpful to bend the support panel top edge slightly inboard while the Velcro of each fabric fl ap is secured.6. Locate fork dropout protector andconfi rm it is attached securely to endof small red webbing as shown in Fig. C. The fork dropout protector can be replaced easily if lost or damaged with most other common fork dropout protector(s) used on strollers and bicycles for shipping, available through your bicycle or stroller e Instructions:7. Prepare Travel Bag: Zip Travel Bag zipper completely open and fold top cover over, exposing pockets for Front Wheel and front wheel quick release (QR). Locate center strap and unfasten side release buckle. Place center strap ends outboard of Travel Bag as shown in Fig. 1.8. Prepare stroller to place in Travel Bag. Remove contents from stroller (occupant and all contents of Low Boy cargo basket). Remove stroller rear wheels. Close rear wheel QR’s. (See rear wheel section of your stroller’s owner’s manual).NOTE: Remove Snack Tray or Infant Car Seat Adapter and Infant Car Seat from strollers featuring the Accessory Adapter. (See strollers owners manuals to verify if stroller has accessory adapter).9. Remove front wheel from stroller (See front wheel section of your stroller’s owner’s manual).TRAVEL BAG INSTRUCTIONSFig. B: Panel ends into corner pocket (right side shown).Pocket SeamNotchInside Notch fully up toSeamENGLISHFig. C: Fork dropout protector shown properly attached.Red - Fork Protector & StrapFig. 1: Travel Bag fully assembled and prepared for stroller.Center Strap open with ends outboardTop Cover OpenFig. 2: Front QR anatomy shown properly assembled.Cam HousingRodConical SpringsAdjusting NutFig. A: Anatomy of the BOB Travel BagZippered Top Cover Wall Support Panel (rolled up)Center Strap & Buckle Fork Protector & StrapFront QR Pocket Fabric Flaps (open)Shoulder Strap Handles Front WheelPocketQR LeverRemove front QR from front wheel. Reassemble front QR components in proper orientation as shown in Fig. 2, and place inside the gray pocket located inside top cover of Travel Bag. Locate black plastic axle protectors at ends of red straps inside large front wheel pocket. Push hollow end of each plastic axle protector fully over each end of front wheel axle as shown in Fig. 3. Place front wheel into pocket inside top cover and fasten Velcro closures.10. Place rear wheels inside Travel Bag with stub axles facing up. Position stroller wheels along center line as far back towards base of bag as possible, leaving extra space for fork protector, as shown in Fig. 4.NOTE: For single Sport Utility Strollers featuring the accessory adapter, remove front fender. (See stroller owners manuals for front fender instructions/removal).11. For Sport Utility Stroller (fi xed wheel) models, close caliper brake quick release lever after removing wheel, as stroller will fold more completely. (See hand brake section of your stroller’s owner’s manual). For Revolution and Stroller Strides (swivel wheel) models, unlock swivel lockout knob and rotate the fork rearwards in order to minimize overall length as shown in Fig. 5A. (See Swivel Lockout section of your stroller’s owner’s manual).12. Fold stroller completely and secure with wrist strap. (See folding section of your stroller’s owner’s manual). Make sure Low Boy fabric is not pinched between stroller components. 13. Place stroller in Travel Bag such that the handlebar is on top and the stroller fork is near the fork protector at end of small red strap.NOTE: Push seat back down toward stroller.14. Rock stroller side to side and gently push down to allow wheels to shift onto space located between outer frame components. Metal shock brackets of stroller should contact hard plastic bottom of Travel Bag.15. Push black plastic fork protector on to fork dropouts as shown respectively by model in Fig. 5A.16. Route red center strap over top of stroller and fasten buckle. Pull end of strap to tighten and secure stroller. Fig. 6A.17. Fold Travel Bag top cover into position and zip closed. Now it is ready to travel.Note: When checking on to transportation services, we recommend you remove the shoulder strap and place it inside Travel Bag to reduce the possibility of damage or loss.CARE INSTRUCTIONSClean the fabric of Travel Bag by hand with clean damp cloth or sponge and air-dry fl at. Do not dry clean, iron, or place in dryer.LIMITED WARRANTYBOB Trailers Inc. takes pride in its workmanship and strives to manufacture the best products possible. Therefore, we warranty the Travel Bag against defects in material and workmanship subject to the conditions listed below. Since no product is indestructible, it does not cover defects attributable to or resulting from normal wear, abuse or alteration.The Travel Bag is warranted for one year from the date of original purchase.• Warranty is only valid for the original purchaser.• Proof of purchase is required to exercise this warranty.• Labor and freight charges are not included.• Normal wear, neglect, abuse, accidents, improper use are not covered by this warranty.• Damage incurred during travel is not covered by this warranty.• Warranty claims must be made through an authorized dealer.• This warranty is limited to the repair or replacement of the defective part. BOB shall in no event be responsible for consequential or special damages.• This limited warranty is the only express or implied warranty applicable to BOB. Any implied warranties, including warranties of merchantability and fitness shall be limited in scope and duration in accordance with this limited warranty.Copyright © 2011 BOB Trailers, Inc.BOB TRAILERS, Inc.(800) 893-2447 Fig. 3: Plastic Axle Protectors properly installed on front wheel.Axle ProtectorsFig. 4: Wheels and front QR placement (alloy wheels shown).Fig. 5A: Fork protector placement onRevolution model stroller.Fig. 6A: Fixed wheel model shown properly placed into Travel Bag.。
CS2000系统说明书【模板】

CS2000系统说明书目录第一章硬件系统 (3)1.1 系统主要特点 (4)1.2 实验对象组成结构 (4)1.3 控制台组成结构 (7)1.4 RS-485接口转换器与通讯电缆 (11)第二章MCGS组态系统 (13)2.1主控窗口 (13)2.2 设备窗口 (13)2.3 用户窗口 (14)2.4 实时数据库 (14)2.5 运行策略 (14)第一章硬件系统生产与生活的自动化是人类长久以来所梦寐以求的目标,在18世纪自动控制系统在蒸汽机运行中得到成功的应用以后,自动化技术时代开始了。
随着工业技术的更新,特别是半导体技术、微电子技术、计算机技术和网络技术的发展,自动化仪表已经进入了计算机控制装置时代。
在石油、化工、制药、热工、材料和轻工等行业领域中,以温度、流量、物位、压力和成分为主要被控变量的控制系统都称为“过程控制”系统。
过程控制不仅在传统工业改造中,起到了提高质量,节约原材料和能源,减少环境污染等十分重要的作用,而且已成为新建的规模大、结构复杂的工业生产过程中不可缺少的组成部分。
随着计算机控制装置在控制仪表基础上的发展,自动化控制手段也越来越丰富。
其中有在工业领域有着广泛应用的智能数字仪表控制系统、智能仪表加计算机组态软件控制系统、计算机DDC控制系统、PLC控制系统、DCS分布式集散控制系统、FCS现场总线控制系统等。
在现代化工业生产中,过程控制技术正为实现各种最优的技术经济指标、提高经济效益和劳动生产效率、改善劳动条件、保护生态环境等起到越来越大的作用。
CS2000型过程控制实验装置是根据我国工业自动化及相关专业教学特点,吸取了国外同类实验装置的特点和长处,并与目前大型工业装置的自动化现场紧密联系,采用了工业上广泛使用并处于领先的AI智能仪表加组态软件控制系统、DCS(分布式集散控制系统),经过精心设计、多次实验和反复论证后,推出的一套基于本科生、研究生教学和学科基地建设的实验设备。
- 1、下载文档前请自行甄别文档内容的完整性,平台不提供额外的编辑、内容补充、找答案等附加服务。
- 2、"仅部分预览"的文档,不可在线预览部分如存在完整性等问题,可反馈申请退款(可完整预览的文档不适用该条件!)。
- 3、如文档侵犯您的权益,请联系客服反馈,我们会尽快为您处理(人工客服工作时间:9:00-18:30)。
AX/operand (DX:AX)/operand
(EDX:EAX)/operand EAX
IMUL – Multiply Signed Integers
Flags: Affects CF and OF. (AF,PF,SF, and ZF are undefined)
Format dest source1 IMUL IMUL IMUL IMUL reg IMUL reg
3/28/2012 15
Symbolic Instructions 15 Transfer (Unconditional)
CALL: Call a Procedure INT: Interrupt IRET: Interrupt Return JMP: Jump RET: Return RETN/RETF: Return Near/Far
3/28/2012 13
Symbolic Instructions 13 Transfer (Conditional) 2
JLE: Jump if Less/Equal JNA: Jump if Not Above JNAE: Jump if Not Above/Equal JNB: Jump if Not Below JNBE: Jump if Not Below/Equal JNC: Jump if No Carry JNE: Jump if Not Equal JNG: Jump if Not Greater JNGE: Jump if Not Greater/Equal JNL: Jump if Not Less
3/28/2012 4
Symbolic Instructions 4 Comparison
BSF/BSR: Bit Scan BT/BTC/BTR/BTS: Bit Test CMP: Compare CMPSn: Compare String CMPXCHG: Compare and Exchange CMPXCHG8B: Compare and Exchange TEST: Test bits
3/28/2012 7
Symbolic Instructions 7 Input/Output
IN: Input Byte or Word OUT: Output Byte or Word INSn: Input String OUTSn: Output String
3/28/2012
8
Symbolic Instructions 8 Logical Operations
3/28/2012
Effect AX = AL * 8-bit operand DX:AX = AX * 16-bit operand EDX:EAX = EAX * 32-bit operand
20
DIV - Divide Unsigned Integers IDIV – Divide Signed Integers
3/28/2012 11
Symbolic Instructions 11 String Operators
CMPS: Compare String LODS: Load String MOVS: Move String REP: Repeat String REPE: Repeat While Equal REPZ: Repeat While Zero REPNE: Repeat While Not Equal REPNZ: Repeat While Not Zero SCAS: Scan String STOS: Store String
3/28/2012 19
MUL - Multiply Unsigned Integers
Flags: Affects CF and OF. (AF,PF,SF, and ZF are undefined) MUL reg/mem
Size of operand 8-bit 16-bit 32-bit
CS 301 Fall 2002 Assembly Instructions
Slide Set 4
3/28/2012
1
Symbolic Instructions 1 Arithmetic
ADD: Add ADC: Add with carry SUB: Subtract SBB: Subtract with borrow NEG: Negate XADD: Exchange and add INC: Increment by 1 DEC: Decrement by 1 MUL: Unsigned multiply DIV: Unsigned divide IMUL: Signed multiply IDIV: Signed divide
3/28/2012
10
Symbolic Instructions 10 Stack Operations
ENTER: Make Stack Frame LEAVE: Terminate Stack Frame POP: Pop Word Off Stack PUSH: Push Word On Stack POPF: Pop Flags Off Stack PUSHF: Push Flags On Stack POPA: Pop All General Registers PUSHA: Push All General Registers
3/28/2012 5
Symbolic Instructions 5 Data Transfer
LDS: Load DS register LEA: Load Effective Address LnS: Load nS register LODS: Load String MOV: Move Data MOVSn: Move String MOVSX: Move with Sign-Extend MOVZX: Move with Zero-Extend STOS: Store String XCHG: Exchange XLAT: Translate
3/28/2012 12
Symbolic Instructions 12 Transfer (Conditional) 1
INTO: Interrupt On Overflow JA: Jump if Above JAE: Jump if Above/Equal JB: Jump if Below JBE: Jump if Below/Equal JC: Jump if Carry JCXZ: Jump if CX is Zero JE: Jump if Equal JG: Jump if Greater JGE: Jump if Greater/Equal JL: Jump if Less
3/28/2012 14
Symbolic Instructions 14 Transfer (Conditional) 3
JNLE: Jump if Not Less/Equal JNO: Jump if No Overflow JNP: Jump if No Parity JNS: Jump if No Sign JNZ: Jump if Not Zero JO: Jump if Overflow JP: Jump if Parity JPE: Jump if Parity Is Even JPO: Jump if Parity Is Odd JS: Jump if Sign JZ: Jump if Zero
3/28/2012
17
MOV – Move Data
Flags: Affects no flags MOV reg/mem,reg/mem/imm
3/28/2012
18
ADD (and ADC/SUB/SBB)
Add, Add with Carry, Subtract, Subtract with borrow. Flags: All affect AF,CF,OF,PF,SF, and ZF ADD reg/mem, reg/mem/imm ADC reg/mem, reg/mem/imm SBB reg/mem, reg/mem/imm SUB reg/mem, reg/mem/imm
3/28/2012 2
Symbolic Instructions 2 ASCII-BCD conversion
AAA: ASCII Adjust After Addition AAS: ASCII Adjust After Subtraction AAM: ASCII Adjust After Multiplication AAD: ASCII Adjust Before Division DAA: Decimal Adjust After Addition DAS: Adjust After Subtraction
Flags: Affect AF,CF,OF,PF,SF, and ZF (all undefined) DIV reg/mem IDIV reg/mem
Size of operand Operation 8-bit 16-bit 32-bit
3/28/2012
Quotient Remainder AL AX AH DX EDX
3/28/2012 16
Symbolic Instructions 16 Type Conversion
CBW: Convert Byte To Word CDQ: Convert Doubleword to Quadword CWD: Convert Word to DoubleWord CWDE: Convert Word to Extended DoubleWord
3/28/2012
Effect source2 AX = AL * source1 DX:AX = AX * source1 EDX:EAX = EAX * source1 dest *= source1 imm dest = source1 * source2