Higgs-Mediated Electric Dipole Moments in the MSSM An Application to Baryogenesis and Higgs
AGA 9 - 多路超声流量计测量技术(第2版)说明书
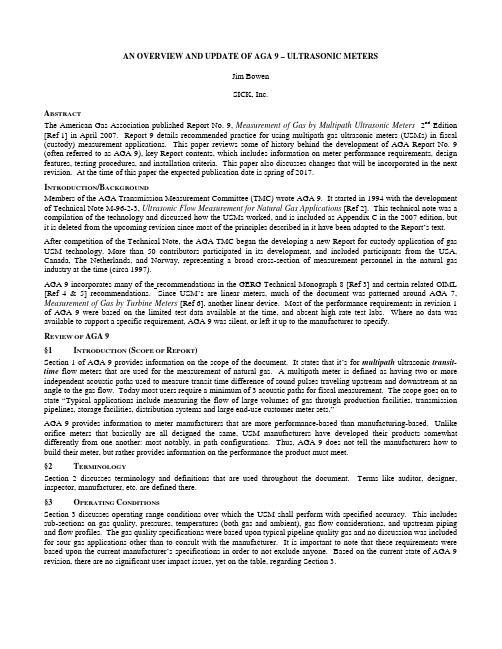
AN OVERVIEW AND UPDATE OF AGA 9 – ULTRASONIC METERSJim BowenSICK, Inc.A BSTRACTThe American Gas Association published Report No. 9, Measurement of Gas by Multipath Ultrasonic Meters 2nd Edition [Ref 1] in April 2007. Report 9 details recommended practice for using multipath gas ultrasonic meters (USMs) in fiscal (custody) measurement applications. This paper reviews some of history behind the development of AGA Report No. 9 (often referred to as AGA 9), key Report contents, which includes information on meter performance requirements, design features, testing procedures, and installation criteria. This paper also discusses changes that will be incorporated in the next revision. At the time of this paper the expected publication date is spring of 2017.I NTRODUCTION/B ACKGROUNDMembers of the AGA Transmission Measurement Committee (TMC) wrote AGA 9. It started in 1994 with the development of Technical Note M-96-2-3, Ultrasonic Flow Measurement for Natural Gas Applications [Ref 2]. This technical note was a compilation of the technology and discussed how the USMs worked, and is included as Appendix C in the 2007 edition, but it is deleted from the upcoming revision since most of the principles described in it have been adapted to the Report’s text. After competition of the Technical Note, the AGA TMC began the developing a new Report for custody application of gas USM technology. More than 50 contributors participated in its development, and included participants from the USA, Canada, The Netherlands, and Norway, representing a broad cross-section of measurement personnel in the natural gas industry at the time (circa 1997).AGA 9 incorporates many of the recommendations in the GERG Technical Monograph 8 [Ref 3] and certain related OIML [Ref 4 & 5] recommendations. Since USM’s are linear meters, much of the document was patterned around AGA 7, Measurement of Gas by Turbine Meters [Ref 6], another linear device. Most of the performance requirements in revision 1 of AGA 9 were based on the limited test data available at the time, and absent high rate test labs. Where no data was available to support a specific requirement, AGA 9 was silent, or left it up to the manufacturer to specify.R EVIEW OF AGA9§1 I NTRODUCTION (S COPE OF R EPORT)Section 1 of AGA 9 provides information on the scope of the document. It states that it’s for multipath ultrasonic transit-time flow meters that are used for the measurement of natural gas. A multipath meter is defined as having two or more independent acoustic paths used to measure transit time difference of sound pulses traveling upstream and downstream at an angle to the gas flow. Today most users require a minimum of 3 acoustic paths for fiscal measurement. The scope goes on to state “Typical applications include measuring the flow of large volumes of gas through production facilities, transmission pipelines, storage facilities, distribution systems and large end-use customer meter sets.”AGA 9 provides information to meter manufacturers that are more performance-based than manufacturing-based. Unlike orifice meters that basically are all designed the same, USM manufacturers have developed their products somewhat differently from one another: most notably, in path configurations. Thus, AGA 9 does not tell the manufacturers how to build their meter, but rather provides information on the performance the product must meet.§2 T ERMINOLOGYSection 2 discusses terminology and definitions that are used throughout the document. Terms like auditor, designer, inspector, manufacturer, etc. are defined there.§3 O PERATING C ONDITIONSSection 3 discusses operating range conditions over which the USM shall perform with specified accuracy. This includes sub-sections on gas quality, pressures, temperatures (both gas and ambient), gas flow considerations, and upstream piping and flow profiles. The gas quality specifications were based upon typical pipeline quality gas and no discussion was included for sour gas applications other than to consult with the manufacturer. It is important to note that these requirements were based upon the current manufacturer’s specifications in order to not exclude anyone. Based on the current state of AGA 9 revision, there are no significant user impact issues, yet on the table, regarding Section 3.§4 M ETER R EQUIREMENTSSection 4, titled “Meter Requirements”, addresses specific mechanical and electrical reuqirments manufacturers need meet to operate the devices in a hazardous environment. Sub-sections on codes and regulations, meter body markings, ultrasonic transducers, electronics, computer programs, and supporting documentation are included.§4.3 Meter BodyThe section on meter body discusses items such as operating pressure, corrosion resistance, mechanical issues relative to the meter body, and markings. Here is says manufacturers should publish the overall lengths of their ultrasonic meter bodies for the different ANSI flange ratings.External and Internal Corrosion resistance and compatibility with gas mixtures commonly found in today’s pipeline is stipulated.The inside diameter of the ultrasonic meter shall have the same inside diameter as the upstream tube’s diameter and must be within 1%. The value of 1% was based mainly on early European studies and also work performed at the Southwest Research Institute’s MRF (Metering Research Facility) in San Antonio, Texas.AGA 9 discusses the ability to remove transducers under pressure. Experience shows that transducers are rarely extracted under pressure, since many meter stations employ multiple runs, making short term outages possible. This allows de-pressurization and transducer removal after blow-down. Additionally, once the meter run is de-pressurized, the internal condition of the meter and associated piping can be inspected if boroscope and inspection ports are available.Proposed Changes:•Reference to use of extraction tools is eliminated.§4.4 TransducersThe section on transducers discusses a variety of issues including specifications, rate of pressure change, and transducer tests. The intent was to insure the manufacturer provided sufficient information to the end user in order to insure reliable and accurate operation in the field, and also to insure accurate operation should one or more pairs need replacement in the field. Subsections include basic specifications, rate of pressure change, exchange and transducer tests.Proposed Changes:•Hydrostatic test of meter bodies shall not be done with transducers installed if test pressure is above ANSI rating.For higher pressures, transducers need be removed.•§4.4.3, “Exchange”, in reference to transducers, is deleted and replaced with existing §4.4.4, “Transducer Tests” , which itself remains unchanged.§4.5 ElectronicsThe electronics section includes two suggested types of flow output communicated to flow computers: serial and frequency. Serial communication (digital using either RS-232 or RS-485) is suggested because the ultrasonic meter is clearly a very “smart” instrument and much of its usefulness relies on the internal information contained in the meter. The frequency output is a not required but standard on all USM, and is needed in applications where flow computers and Remote Terminal Units (RTUs) do not have the necessary software application to poll the USM using the serial port.A majority of users apply the frequency output as input to flow computers. Most USM manufacturers employ standard Modbus collection of measurement information via a serial link or Ethernet adapter. Additional serial or Ethernet ports are used for local interrogation using the manufacturer’s software.AGA 9 requires the manufacturer to also provide digital outputs (DOs) for flow direction and data valid. A digital out is used for monitoring by the flow computer to determine direction of flow (when a single frequency is used for both forward and reverse flow). Data valid is an indicator that the meter has an alarm condition that may impact its accuracy.AGA 9 requires the meter be electrically rated for a hazardous environment as defined by the National Electrical Code [Ref 12]. The minimum rating for a USM is for Class 1, Division 2, Group D environments. Some users specify a rating of Division 1, and, for the most part, all manufacturers design for the more stringent Division 1 requirement.Proposed Changes:•Elimination of the requirement for a scaled 4-20 ma output, now making it an option.•Added statement that a scaled 4-20 ma output is not to be used for custody measurement.•Delete of the paragraph specifying “significant change” as +/- 0.2% shift in the meter’s output, and new stipulation that Manufacturer’s replacement of cables, electronics, transducers, etc won’t shift meter output more that Manufacturer stated repeatability (0.2%).§4.6 Computer Programs Meter Firmware and SoftwareUSMs typically do not provide a local display or keyboard for communicating with the meter as is traditional with some flow computers. USM Manufacturers provide their meter specific software for meter configuration and diagnostic interrogation. There are few specific diagnostic data requirement in manufacturer’s to have similar looking and functioning software, but Report 9 does cite some in §4.6.4, “Meter Diagnostics”.The velocity data is used to indicate flow profile irregularities and to calculate volume rate from average velocity. The flow rate is determined from by multiplying velocity times the meter’s cross-sectional area of the meter. The speed-of-sound data is used as a diagnostic tool to check for erroneous transit time measurement errors. Other information is required to judge the quality of the data such as percent of accepted ultrasonic pulses, signal to noise ratio and transducer gains. A discussion on these is documented in several papers [Ref 13 & 14].Other meter requirements in this section include anti-roll devices (feet), pressure tap design and location on the meter, and standard meter markings. Many of these requirements are based on field experience and the lessons learned from other metering technologies.§4.7 §6 Individual Meter Testing Requirements Moved to “dimensional measurements” et alSection’s 4.7 discusses how the manufacturer will perform tests on the USM prior to shipment. Many also call this testing dry calibration. In reality dry calibration is simply an assembly process to help verify proper meter operation prior being installed in the field. Since there were no calibration facilities in North America until the late 1990’s, it was felt that if a manufacturer could precisely control the assembly process, flow calibration would not be required. Hence the term dry calibration has often been used to describe this section.AGA 9 requires the manufacturer to document the internal diameter of the meter to the nearest 0.0001 inches. This is to be determined from 12 separate inside diameter measurements. This dimension is to be adjusted back to 68 °F and reported on the documents. Measurements should be traceable to a national standard such as NIST, the National Institute for Standards and Technology.Individual meters are to be tested to strict tolerances for leaks and imperfections. AGA 9 also specifies a Zero-Flow Verification Test and a Flow-Calibration Test procedure (although a flow-calibration is not required).No significant changes have been proposed to §4.7 at this time.§4.8 DocumentationSection 4.7 of Report 9’s 2nd edition discusses the manufacturing and certification documents required to be delivered by USM builders. The section has been significantly reworked to add description of required dimensional measurements, leakage tests, etc.§5.0 Performance Requirements Installation (was §7 in second edition of Report 9)Many of the variables the designer should take into consideration when using USMs are addressed, such as operating conditions, use of flow conditioners and meter tube configurations etc.§5.2 Piping Configuration Metering Package Design CriteriaReport 9’s 1st Edition was developed with only limited empirical data. The 2nd Edition, published in 2007 was not much of an improvement. For instance, Section 5.2 of AGA 9 discusses upstream piping issues. The intent here is to provide the designer with some basic designs that will provide accurate measurement. It states “Recommend upstream and downstream piping configuration in minimum length — one without a flow conditioner and one with a flow conditioner — that will not create an additional flow-rate measurement error of more than +0.3% due to the installation configuration. This error limit should apply for any gas flow rate between q min and q max. The recommendation should be supported by test data.” In other words, the manufacturer is required to let the designer know what type of piping is permitted upstream so that the impact on accuracy will not be greater than 0.3%.In reality this is difficult given the variety of upstream pipe configurations operators use, so the so-called end-treatments (or entrance/exit piping) are often included in the calibration of the “metering package”.Much data has been taken and published since 1998, and, as a consequence of this data, and the desire to provide the highest level of accuracy, most users have elected to use a high-performance flow conditioner with their USM. Testing has shown that the use of a 19-tube bundle, typical with turbine and orifice metering, will not improve the USM performance, and inmost cases actually will degrade accuracy [Ref 7]. However, high performance flow conditioners, usually specified in meter package design, help to obtain a uniform and repeatable flow profile.Proposed Changes:•Process section added to indicate guidance for operating conditions such as pulsating flow and a more detailed discussion of potential noise impacts on USM operation.•Recommended Default Meter Run Configurations (§5.2.3) are modified to eliminate the optional entrance to the meter run through either a tee or elbow, leaving users to their design preference so long a meter performance meets §6 requirements.Corrected flow rate output requires USM metering packages include temperature measurement on the outlet leg of the meter run. AGA 9 recommends the thermowell be installed between 2D and 5D downstream of the USM on a uni-directional installation. It states the thermowell should be at least 3D from the meter on a bi-directional installation. This was based on research done at SwRI sponsored by GRI in the 1990’s. These studies found measurable influence onset at 2D downstream of USMs during and the committee settled on 3D as a reasonable distance.§6.0 Performance RequirementsSince Report 9 is a performance based document, “Performance Requirements” are core to its scope, and it addresses minimum performance requirements the USM’s must meet. It requires flow calibration for fiscal use.AGA 9’s second edition (2007) separates ultrasonic meters into two categories; smaller than 12” and meters that are 12” and larger. This division was created to allow relaxed accuracy requirements for smaller meters where tolerances are more difficult to maintain. All other requirements, including repeatability, resolution, velocity sampling interval, peak-to-peak error and zero-flow readings are the same, regardless of meter size.The edition preparing for release in 2017 will have 3 size ranges and new accuracy limits:•>10” Max Error: +/-0.7% q t≤q i≤q max; +/-1.4% for q min≤q i≤q t with linearity of+/-0.2% for q t≤q i≤q max•3”-8”: Max Error: +/-1.0% q t≤q i≤q max; +/-1.4% for q min≤q i≤q t with linearity of+/-0.2% for q t≤q i≤q max•<3”: Max Error: +/-2.0% q t≤q i≤q max; +/-3.0% for q min≤q i≤q t with linearity of+/-0.2% for q t≤q i≤q maxPer the second edition, the maximum error allowable for a 12-inch and larger ultrasonic flow meter is ±0.7%, and ±1.0% for small meters. This error expands to ±1.4% below Q t, the transition flowrate. Within the error bands, the error peak-to-peak error (also thought of as linearity) must be less than 0.7%. The repeatability of the meters must be with ±0.2% for the higher velocity range, and is permitted to be ±0.4 below Q t. Figure 1 is a graphical representation of these performance requirements as shown in AGA 9.Figure 1 – Performance Specification Summary, 2nd EditionSection 5 also discusses the potential effects of pressure, temperature and gas composition on the USM. Here is states “The UM shall meet the above flow-measurement accuracy requirements over the full operating pressure, temperature and gas composition ranges without the need for manual adjustment, unless otherwise stated by the manufacturer.” There has been some concern about calibrating a USM at one pressure and then operating at a different pressure. Although there are a variety of opinions on this, most believe the meter’s accuracy is not significantly impacted by pressure [Ref 13] since there has not been correlation with significant per pat Speed of Sound measurements (one would expect if the meter were changing dimensions due to pressure change that a path length change would result and turn up in a path SoS deviation).§7 C OMMISSIONING &F IELD V ERIFICATIONSection 7 briefly discusses field verification requirements. Since each USM provides somewhat different software to interface with the meter, AGA 9 was not too specific about how to verify field performance. Rather they left it up to the manufacturer to provide a written field verification procedure that the operator could follow. The 2nd edition made limited progress on Field Verification, but it is intended the 3rd edition will be much more expansive regarding Field Verification practice. Much debate is occurring on these topics now to insure recommended practice matches Operator requirements, current Field practice and Manufacturer capability, and since this discussion is on-going, it is difficult to state proposed changes due to their number and variety.Typically today the operator would check the basic diagnostic features including velocity profile, speed-of-sound by path, transducer performance, signal to noise ratios and gain. One additional test is to compare the meter’s reported SOS with that computed by a program based upon AGA 8 [Ref 12].At the time of the first release there was no universally excepted document that discussed how to compute SOS. However, in 2003 AGA published AGA Report No. 10, Speed of Sound in Natural Gas and Other Related Hydrocarbon Gases [Ref 13]. This document, based upon AGA 8, provides the foundation for computing SOS that most software uses today, and is incorporated by reference into the 2nd Edition. It will pass that AGA 10 collapses into AGA 8 and that the SoS calculation will be harmonized, to some extent with SGERG, the European consortium’s method to calculate SoS in hydrocarbon mixtures. This effort is nearly complete now and will result in an AGA 8 Equation of State document that includes AGA 10 Detailed and SGERG.R EFERENCES1.AGA Report No. 9, Measurement of Gas by Multipath Ultrasonic Meters, 2nd Edition, April 2007, American GasAssociation, 1515 Wilson Boulevard, Arlington, VA 222092.AGA Engineering Technical Note M-96-2-3, Ultrasonic Flow Measurement for Natural Gas Applications,AmericanGas Association, 1515 Wilson Boulevard, Arlington, VA 222093.GERG Technical Monograph 8 (1995), Present Status and Future Research on Multi-path Ultrasonic Gas Flow Meters,Christian Michelsen Research AS, the GERG Project Group and Programme Committee No. 2 - Transmission and Storage, Groupe Européen De Recherches Gazières4.OIML R 6General provisions for gas volume meters,1989 (E), International Recommendation, OrganizationInternationale de Métrologie Légale, Bureau International de Métrologie Légale, 11, rue Turgot - 75009 Paris - France 5.OIML D 11General requirements for electronic measuring instruments,1994 (E), International Document,Organization Internationale de Métrologie Légale, Bureau International de Métrologie Légale, 11, rue Turgot - 75009 Paris - France6.AGA Transmission Measurement Committee Report No. 7, Measurement of Gas by Turbine Meters, American GasAssociation, 1515 Wilson Boulevard, Arlington, VA 222097.T. A. Grimley, Ultrasonic Meter Installation Configuration Testing, AGA Operations Conference, 2000, Denver, CO8.John Stuart, Rick Wilsack, Re-Calibration of a 3-Year Old, Dirty, Ultrasonic Meter, AGA Operations Conference, 2001,Dallas, TX9.Code of Federal Regulations, Title 49 —Transportation, Part 192, (49 CFR 192), Transportation of Natural Gas andOther Gas by Pipeline: Minimum Federal Safety Standards, U.S. Government Printing Office, Washington, DC 20402 10.NFPA 70, National Electrical Code,1996 Edition, National Fire Protection Association, Batterymarch Park, Quincy,MA 0226911.Umesh Karnik & John Geerlings, Effect of Steps and Roughness on Multi-Path Ultrasonic Meters, ISFFM 2002,Washington, DC12.AGA Transmission Measurement Committee Report No. 8, Compressibility Factors of Natural Gas and Other RelatedHydrocarbon Gases, American Gas Association, 1515 Wilson Boulevard, Arlington, VA 2220913.AGA Report No 10, Speed of Sound in Natural Gas and Other Related Hydrocarbon Gases, July 2002, American GasAssociation, 1515 Wilson Boulevard, Arlington, VA 22209。
Quantum Mechanics
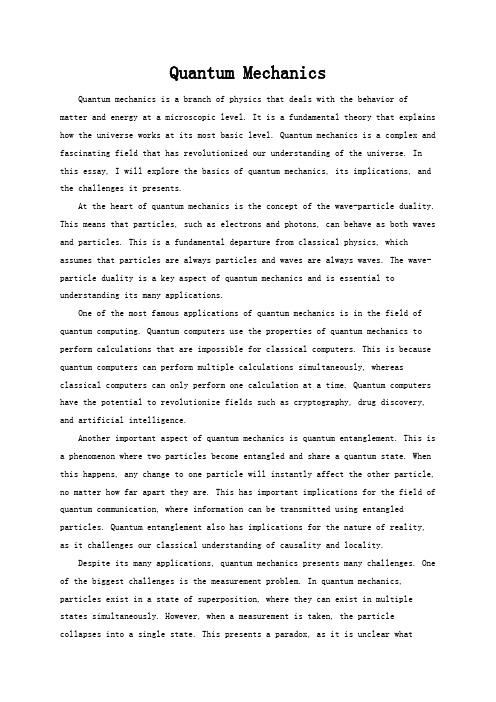
Quantum MechanicsQuantum mechanics is a branch of physics that deals with the behavior of matter and energy at a microscopic level. It is a fundamental theory that explains how the universe works at its most basic level. Quantum mechanics is a complex and fascinating field that has revolutionized our understanding of the universe. In this essay, I will explore the basics of quantum mechanics, its implications, and the challenges it presents.At the heart of quantum mechanics is the concept of the wave-particle duality. This means that particles, such as electrons and photons, can behave as both waves and particles. This is a fundamental departure from classical physics, which assumes that particles are always particles and waves are always waves. The wave-particle duality is a key aspect of quantum mechanics and is essential to understanding its many applications.One of the most famous applications of quantum mechanics is in the field of quantum computing. Quantum computers use the properties of quantum mechanics to perform calculations that are impossible for classical computers. This is because quantum computers can perform multiple calculations simultaneously, whereas classical computers can only perform one calculation at a time. Quantum computers have the potential to revolutionize fields such as cryptography, drug discovery, and artificial intelligence.Another important aspect of quantum mechanics is quantum entanglement. This is a phenomenon where two particles become entangled and share a quantum state. When this happens, any change to one particle will instantly affect the other particle, no matter how far apart they are. This has important implications for the field of quantum communication, where information can be transmitted using entangled particles. Quantum entanglement also has implications for the nature of reality, as it challenges our classical understanding of causality and locality.Despite its many applications, quantum mechanics presents many challenges. One of the biggest challenges is the measurement problem. In quantum mechanics, particles exist in a state of superposition, where they can exist in multiple states simultaneously. However, when a measurement is taken, the particle collapses into a single state. This presents a paradox, as it is unclear whatcauses the collapse of the wave function. This has led to many interpretations of quantum mechanics, such as the Copenhagen interpretation, the many-worlds interpretation, and the pilot wave theory.Another challenge presented by quantum mechanics is the problem of decoherence. Decoherence is the process by which a quantum system interacts with its environment, causing it to lose its quantum properties. This makes it difficult to maintain a quantum state for any length of time, which is a major obstacle for the development of practical quantum technologies.In conclusion, quantum mechanics is a fascinating and complex field that has revolutionized our understanding of the universe. It is a fundamental theory that has many applications, from quantum computing to quantum communication. However,it also presents many challenges, such as the measurement problem and the problem of decoherence. Despite these challenges, quantum mechanics is a field that is constantly evolving, and it will continue to shape our understanding of the universe for many years to come.。
外文翻译

High-Energy Pulse-Switching Characteristics of ThyristorsAbstractExperiments were conducted to study the high energy, high dildt pulse-switching characteristics of SCR's with and without the amplifying gate. High dildt. high-energy single- shotexperiments were first done. Devices without the amplifying gate performed much better than thedevices with the amplifying gate. A physical model is presented to describe the role of the amplifying gate in the turn-on process, thereby explaining the differences in the switching characteristics. The turn-on area for the failure of the devices was theoretically estimated and correlated with observations. This allowed calculation of the current density required for failure. Since the failure of these devices under high dildt conditions was thermal in nature, a simulation using a finite-element method was performed to estimate the temperature rise in the devices. The results from this simulation showed that the temperature rise was significantly higher in the devices with the amplifying gate than in the devices without the amplifying gate. From these results, the safe operating frequencies for all the devices under high dildt conditions was estimated. These estimates were confirmed by experimentally stressing the devices under high di/dt repetitive operation.1 INTRODUCTIONRecent innovations in semiconductor device designs and advances in manufacturing technologies have helped evolve high-power thyristors. These devices are designed to operate in a continuous mode for applications such as ac- to-dc power conversion and motor drives. Until recently, their application to high-power pulse switching was mostly unknown. One of the main reasons that has discouraged the use of thyristors for high-speed, high-energy switching is their low dildt rating. The limiting value of the dildt before damage occurs is related to the size of the initial turn-on area and the spreading velocity [I]. Recent experimental results presented in [2]-[4] show that with increased gate device, SCR's and GTO's having highlyinterdigitated gate-cathode structures can reliably operate under high dildt conditions on a single-shot basis. Previously, SCR's have also been used for repetitive switching of 1 kA, 10 ps wide pulses having a dildt of about 10 000 Alps, at 500 and 800 Hz for a 10 h period [SI. It is reported in [6] that GTO modules (five devices in series) can block 11.5 kV and switch 4.5 kA pulses having a dildt of 2500 A/ks at frequencies of 100 Hz.Asymmetric devices, such as the ASCR's in a stack assisted by saturable inductors, have shown the potential to repetitively switch high-current pulses with di/dt of about 2000 Alps, on the order of kilohertz [7].Under high dildt conditions the junction temperatures can vary rapidly in high-power devices (~106C/s) [8]. The failure of these devices under these conditions is normally thermal in nature. It has been reported [9],that the temperature of destruction due to a tum-on dildt failure is in the range of1100~1300C, below the melting point of silicon (1415°C). The rise in average temperature is therefore completely inade- quate as a measure of device applicability for pulse-switching applications. Since a simple experimental technique is not available to measure the instantaneous temperature rise, the spatio-temporal distribution of temperatures in the devices has to be estimated using computer-aided techniques.In this paper, the high dildt single-shot experimental re- sults are given in brief. A qualitative physical model is then proposed to explain the experimental results, which are presented in detail elsewhere [3]. Next, the results from the thermal analysis using FEM, given in detail in [lo], are briefly presented. The particulars of the experimental arrangement for the repetitive testing of the devices, results from these experi- ments, and their correlation with the numerical predictions are given in the discussion.2 SINGLE-SHOTEXPERIMENTSInverter-grade SCR's with the amplifying gate (unshorted device) and without the amplifying gate (shorted device) were used for experimental studies to determine the role of the amplifying gate during the turn-on processes of the device. The SCR's used for the tests were symmetric with involute gate-cathode structures. They wererated for a forward and reverse blocking voltage of 2.4 kV (at 25°C) and 2.2. kV (at 125°C). The experimental details and results are fully presented elsewhere [3]. The experimental arrangement and the results are given in brief below.The devices were electrically characterized initially and recharacterized after testing in a type E pulse-formingnetwork (PFN) that has a total impedance of 0.1 0. This network delivers a 15 kA, 10 ps wide pulse when charged to a voltage of 2.5 kV. The di/dt of this 15-kA pulse is 125000 A/?s. The gate trigger used for switching the SCR's was a 100 A, 500 ns trapezoidal current pulse.The di/dt of the gate pulse was 980 A/s.The unshorted devices failed while switching a peak anode current of 10.5 kA at a dildt of about 26000 A/?s in a PFN charged to 1.7 kV. Under the same trigger conditions, the shorted devices successfully switched 13 kA at a dildt of 100000 A/s, in a PFN charged to 2 kV.A comparison of the performance of the two types of devices is presented in Table I. The ampliyfing gate seems to inhibit the tum-onspeed of the device. In the unshorted devices,which failed catastrophically, the region of failure around the amplifying gate can be seen as a hot spot. All these results point to the fact that the conduction area near the amplifying gate region in the unshorted device is very small. This leads to an increase in current density in the device and, therefore, the instantaneous rise in temperature exceeds the threshold value for failure: about 1100°C [9].TABLE1SINGLE-SHOT EXPERIMENTAL RESUILSTSFig. 1. Typical IA(CH1) andV AK (CH2) switching waveforms of theunshorted device, CH1-1931 A/div, CH2-500 V/div, Time base-100ns/div.3 ROLEOF THE AMPLIFYINGGATEThe results presented in the previous section show that the devices without the amplifying gate (shorted devices) better than the devices with the amplifying gate (unshorted devices). The typical switching waveforms of the unshorted and theshorted devices are shown in Figs. 1 and 2, respectively. In the case of the unshorted device, the anode current rises to a certain value and remains at that value for about ns before rising further its peak value (when the resistance of the device reduces as a result of more turned-on area). This behavior is not seen when the shorted device is used for switching. The anode current switched by the shorted devices has a smooth rising edge. The dynamic resistance of the two devices (computed from the V,Kand IAH.waveforms) .TypicalIA(CH1) and V AK(CH2)and power loss(MULL) of the shorted device . CH1-3190 A/div, CH2-500 V/div, MULL-8.2MW/ div.Time baser-100ns/div.Dynamic resistance of the device versus time is shown in Fig. 3. From this plot it can be seen that the shorted device has a lower dynamicresistance compared to the unshorted device at every instant of time during the rise- time phase of the tum-on process. The results presented so far indicate that more device area is tumed on in the shorted device as compared to that in the unshorted device. It can be concluded that the amplifying gate is inhibiting the tum-on process under high di/dt switching conditions and is therefore to the performance Of the device. This be understood by 'Onsidering the tum-on sequences in the two types Of devices with the proposed given For this the cross-sectional views of the unshorted device and that Of the shorted device are shown in Figs. 4and 5,respectively.When the gate current (1) is injected into the p-base through the pilot gate contact (Fig. 4), electrons are injected intothe p-base by the n emitter with a certain emitter injection efficiency. These electrons traverse through the p-base (time taken for this process is called the transit time) and accumulate near the depletion region. This negative charge accumulation leads to injection of holes from the anode. At this time the device turns on after a certain delay, dictated by the P-base transit time [ll], and the pilot anode current (2) begins to flow through a small region near the pilot gate contact as shown in Fig. 4. This flow of pilot anode current corresponds to the initial sharp rise in the anode current waveform (phase I) shown in Fig. 1. The device then goes into phase 11, during which the anode current remains fairly constant, suggesting that the resistance of the region has reached its lower limit. This is becausethe pilot anode current (2) takes a finite time to traverse through the p-base laterally and become the gate current for the main cathode area. As a result, the n emitters start to inject electrons, which traverse the p-base vertically and after a certain finite time (transit time of the p-base) reach the region. The time taken by the above said processes is the reason for observing this characteristic phase The width Of the phase'I is to the switching delay, suggesting that the p-base transit time is responsible. Once the main cathode region tums on, the resistance of the device decreases and the anode current begins to rise again (transition from phase I1 to phase 111). From here on the plasma-spreading velocity will dictate the rate at which the conduction area will increase. The dip in the Fig. 6. Typical IC (CHI), (CH2) and power loss (MULT) of theunshorted device. C H I 4 0 A/div, CH2-20 V/div, MULT4096 W/div.Time base-100 ns/div.gate current (IG)and the increase in the gate-cathode voltage (VGK),shown in Fig. 6,corresponds in time, to the pilot anode current flow. This supports the above suggestion that the anode current is initially forced to flow through a small area (high resistance) near the pilot-gate contact. Therefore the current density during phase I and phase I1 is very high and leads toa considerable increase in the local temperature. It was reported earlier in [9] that failure temperature of the device is about 1200°C. Based on this the conduction area and the current density for the failure of the device can be estimated as follows. fie adiabatic heat energy of dissipation in a volume can be mathematically related to the temperature rise in the volume as given below.where E is the energy dissipated in the volume, M is the mass of the volume, C is the heat capacity (specific heat at constant pressure) of the material, and AT is the temperature rise in the volume.Equation (1) can be modified as:where? is the mass density of the material and V is the volume of the material = area A thickness h. Therefore, the conduction area for failure can be estimated as Specific heat is a function of temperature, but Saturates at about 140°C. Since the failure temperature is 1000°C, the value of specific heat used for the calculation is its saturated value. The values for the properties of silicon used in the calculations are given below.The thickness of the device is approximately 500?m. Using these values the computed area is 3.5 mm2.A photograph of the damaged unshorted device is shown in Fig. 7. The burnt spot is visible near the pilot-gate contact, and the width of the burnt spot is about 2 mm. Assuming the current was flowing in an annular region with this width, the area of current conduction was calculated to be 3.8mm2.This agrees with the value computed in terms of thenergy from (3). The current density in the device during phase I1 is then 1.86?109A/m2. This agrees with the value given in [ 121 for the failure of the device. Turn-on Process in the Shorted DeviceThe cross-sectional view of the shorted device (in which the ampliyfing gate was bypassed) is shown in Fig. S. When the gate current is injected, it flows laterally (l), and directly tums on part of the main cathode area, and the anode current (2) starts to flow. The current rise is therefore smooth (Fig. 2) and the phase II interval observed in the switching waveforms of the unshorted device is not seen here. The resistance of the device is continually decreasing as controlled by the plasma- spreading velocity. The dynamic resistance of the shorted device is lower compared to that of the unshorted device. The fact that phase II interval is not present in the switching waveforms of the shorted device causes less power loss in the device. This is further supported by the gate waveforms shown in Fig. 8, which are not distorted when the anode current begins to flow. Therefore the shorted devices are able to switch higher currents at very high di/dt values as compared to the unshorted devices. Finally, it can be concluded that the amplifying gate structure is detrimental to the device's performance if the rise time of the anode current is comparable to the p-base transit time.4 TRANSIENTTHERMALANALYSISThe di/dt failure is caused by the instantaneous rise in temperature in the small conduction area obtained immediately after tum-on. Transient thermal analysis was performed inFig. 8. Typical IC (CHI), L.i.1~ (CH2) and power loss (MULT) for theshorted device. C H 1 4 0 A/div, CH2--10 V/div, MULT-2048 W/div. Timebase-I00 ns/div.order to estimate the temperature rise in the shorted and unshorted devices. A general-purpose FEM program called FIDAP' was employed for this analysis. The modeling pro- cedure and all the results are presented in detail in [lo]. A brief summary of this analysis is given below.The device and the mounting structure taking the symme- tries into account were modeled as the heat flow domain. This domain was represented by specifying the actual coordinates of the various regions in the domain. Depending on the temperature gradients expected in the various regions, the number of grids required for the analysis in order to obtain accurate results was decided. The properties of the various materials, namely, thermal conductivity, specific heat, andmass density, were specified. The initial conditions were specified to be 27°C for the entire domain. The symmetry boundaries were treated as insulating boundaries and were modeled by specifying the heat flux outflow to be zero. The other boundaries were maintained at 27°C. Since the experimental tests were on a single-shot basis, the nature of the problem had to be classified as transient. The current flow paths were different in the shorted and the unshorted devices, so different domains were used for each type. Also, the peak power loss and the total energy loss during switching were higher in the unshorted device compared to that in the shorted device. Therefore, the heat source models for both cases were different. The conduction areas in the devices were estimated and the heat generation terms (i.e., instantaneous power loss/unit volume) were calculated and incorporated in the analysis. The procedure just outlined is discussed in more detail in [ 101. The results of this thermal analysis are briefly summarized below.From the analysis, it was seen that the temperature rise in the shorted device is about 350°C per pulse. This is much lower compared to the numerically computed temperature rise of about 1100°C per pulse in the unshorted device. These results explain the failure of the unshorted deivces under high di/dt conditions and the superior performance of the shorted devices. These results, the qualitative model and the discussion given earlier to explain the role of the ampliyfing gate during Fig. 9. Simulated cooling cycle of the unshorted device.Fig. 10. Simulated cooling cycle of the shorted devicethe turn-on process, add credibility to the conclusion that the amplifying gate structure is detrimental to the performance of the device under high dildt conditions. A large transient thermal analysis time window was used to obtain the time taken for the device and its mounting structure to cool back to room temperature. The cooling cycles for the unshorted and shorted devices are shown in'Figs. 9 and 10, respectively. Using this cooling cycle, the safe operating frequencies of the shorted devices were estimated to be in the 1-2 kHz range under these high dildt conditions.Result from the single-shot experiments and the transmit thermal analysis suggest that the device without the amplifying gate ,under high gate-drive conditions,are capable of operating reliably under high di/dt repetitive conditions.5 REPETITIVEEXPERIMENTSTest Device DetailsTwo devices were used for the experimental studies. One of the devices was an involute-structure, inverter-grade SCR, rated for a forward and reverse blocking voltage of 2.4 kV (at 25?). This device is 33 mm in diameter with about 252 mm of gate-cathode (G-K) periphery. The other device is a symmetric, anchor-structure GTO, rated for a forward and reverse blocking voltage of 2.6 kV. This device is 51 mm in diameter with a G-K periphery of about 600 mm. From the single-shot experimental and numerical results it was seen that the devices without the amplifying gate have a better potential to operate at higher frequencies compared to the devices with the amplifying gate. Hence, for the repetitive experimental tests, both the SCR and the GTO were tested with the pilot-gate shorted to the amplifying gate.Characterization for DegradationThe devices were electrically characterized initially and recharacterized after the switching tests in the pulse-forming network (PFN), in order to evaluate the damage to the devices from the stress in the PFN. The following parameters were used as indicators.The most important parameters for damage evaluation were the forward andreverse leakage currents; it was to be used as a parameter to evaluate the condition of the three junctions in the device. The leakage currents were measured at 25 and 125°C. Low current forward and reverse V-I characteristics of the G-K junction, with the anode open circuited, were obtained using a curve tracer. These curves were used to determine any degradation that might have occurred in the G-K region.Experimental ArrangementThe experimental arrangement was designed to test devices in a burst mode at a repetition rate of 400 Hz. The experimental arrangement is shown in Fig. 11. The four different sections are: i) the dc power supply and the command resonant charging circuit, ii) the pulse forming network, iii) the gate drive circuit for the DUT, and iv) the timing and control circuit. Details of these circuits are given in the following subsections.Resonant Charging Circuit The resonant charging circuit consists of a dc power supply, a capacitor .bank, a charging inductor, and the command switch.The capacitor bank is first charged to a desired voltage. Then the command switch is closed, and the resonant action begins. The PFN will continue to charge until the point when the charging current starts to swing negative. At this time the voltage across the PFN would be approximately twice the Power Supply and Resonant Circuit bank voltage.The capacitor bank has a total capacitance of I mF, and its own dump resistor and a dump switch. This capacitor bank can resonantly charge the PFN five times with a voltage droop of 25%. The charging inductor has a value of 10 mH, but has a slight nonlinear characteristic. A 1.2 kV SCR was used as the command switch with an appropriate snubber circuit.晶闸管的高能脉冲式开关特性摘要通过实验对有和没有放大门的可控硅的高能、高di/dt的脉冲式开关特性进行了研究。
aurora流式 激发方式
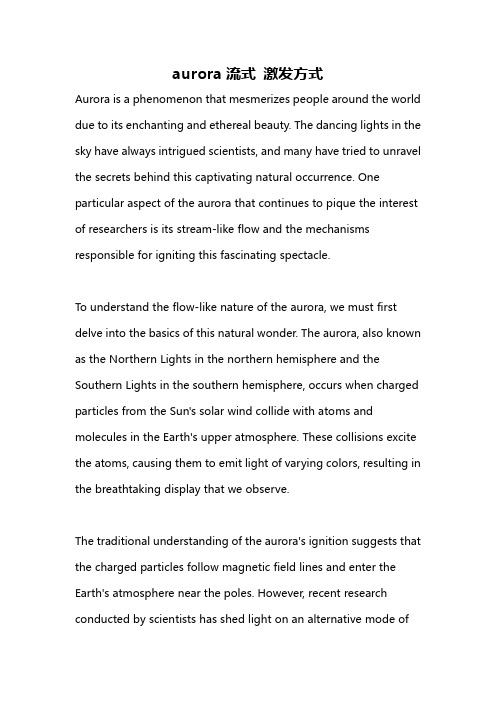
aurora流式激发方式Aurora is a phenomenon that mesmerizes people around the world due to its enchanting and ethereal beauty. The dancing lights in the sky have always intrigued scientists, and many have tried to unravel the secrets behind this captivating natural occurrence. One particular aspect of the aurora that continues to pique the interest of researchers is its stream-like flow and the mechanisms responsible for igniting this fascinating spectacle.To understand the flow-like nature of the aurora, we must first delve into the basics of this natural wonder. The aurora, also known as the Northern Lights in the northern hemisphere and the Southern Lights in the southern hemisphere, occurs when charged particles from the Sun's solar wind collide with atoms and molecules in the Earth's upper atmosphere. These collisions excite the atoms, causing them to emit light of varying colors, resulting in the breathtaking display that we observe.The traditional understanding of the aurora's ignition suggests that the charged particles follow magnetic field lines and enter the Earth's atmosphere near the poles. However, recent research conducted by scientists has shed light on an alternative mode ofactivation known as the auroral streamer or aurora streamer.Auroral streamers are narrow bands of glowing lights that appear perpendicular to the magnetic field lines in the upper atmosphere. They resemble rays or curtains of light stretching across the sky. These streamers are believed to be triggered when the magnetic field lines disturb and stretch the plasma in the magnetosphere, creating a localized region of enhanced electric field. This enhanced electric field accelerates the charged particles along the magnetic field lines towards the Earth's atmosphere, ultimately causing the stream-like flow we observe during auroral displays.The process of triggering the streamers begins with solar eruptions, such as coronal mass ejections or solar flares, which release massive amounts of charged particles into the solar wind. As these particles travel towards Earth, they carry a magnetic field that interacts with our planet's magnetic field. When the magnetic field lines of the charged particles connect with those of the Earth, it creates a magnetic reconnection.During this reconnection event, the magnetic field lines break and reconnect, releasing a tremendous amount of energy. This energyaccelerates the charged particles and sends them shooting towards the Earth along the newly formed magnetic field lines. It is this accelerated flow of charged particles that creates the localized region of enhanced electric field, which ignites the streamers in the upper atmosphere.The phenomenon of auroral streamers becomes more pronounced during high solar activity. As the frequency and intensity of solar eruptions increase, a greater number of charged particles are propelled towards Earth. This, in turn, leads to a larger number of magnetic reconnection events and subsequently enhances the formation of streamers.Studying the aurora's flow-like streamers is crucial for several reasons. Firstly, understanding the mechanisms behind their activation can aid in predicting and forecasting auroral displays, allowing enthusiasts and researchers alike to maximize their chances of witnessing this natural phenomenon. Secondly, unraveling the intricacies of the streamers can provide insight into the overall dynamics and behavior of Earth's magnetosphere and further our understanding of space weather.In conclusion, the stream-like flow of the aurora is ignited through a unique process called auroral streamer activation. This mechanism involves magnetic reconnection events, which accelerate the charged particles and create enhanced electric fields that trigger the formation of the streamers. As scientists continue to delve deeper into this captivating natural occurrence, we inch closer to unraveling the mysteries of the aurora and gaining a deeper appreciation for the wonders of our universe.。
磁致伸缩超声换能器阻抗匹配网络的设计
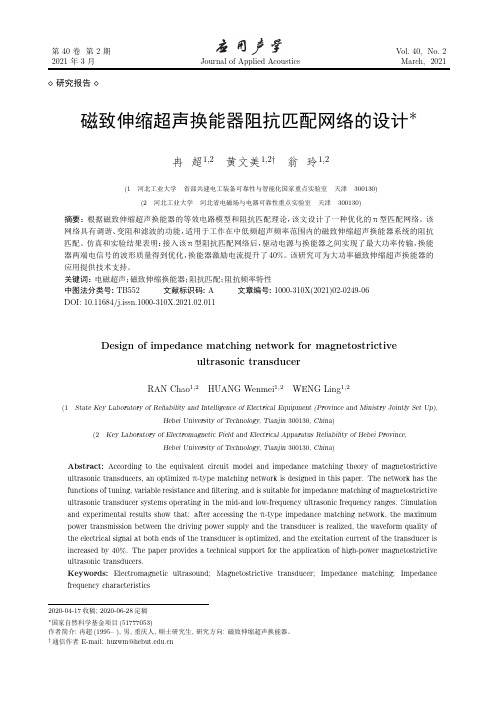
第40卷第2期Vol.40,No.2 2021年3月Journal of Applied Acoustics March,2021⋄研究报告⋄磁致伸缩超声换能器阻抗匹配网络的设计∗冉超1,2黄文美1,2†翁玲1,2(1河北工业大学省部共建电工装备可靠性与智能化国家重点实验室天津300130)(2河北工业大学河北省电磁场与电器可靠性重点实验室天津300130)摘要:根据磁致伸缩超声换能器的等效电路模型和阻抗匹配理论,该文设计了一种优化的π型匹配网络。
该网络具有调谐、变阻和滤波的功能,适用于工作在中低频超声频率范围内的磁致伸缩超声换能器系统的阻抗匹配。
仿真和实验结果表明:接入该π型阻抗匹配网络后,驱动电源与换能器之间实现了最大功率传输,换能器两端电信号的波形质量得到优化,换能器激励电流提升了40%。
该研究可为大功率磁致伸缩超声换能器的应用提供技术支持。
关键词:电磁超声;磁致伸缩换能器;阻抗匹配;阻抗频率特性中图法分类号:TB552文献标识码:A文章编号:1000-310X(2021)02-0249-06DOI:10.11684/j.issn.1000-310X.2021.02.011Design of impedance matching network for magnetostrictiveultrasonic transducerRAN Chao1,2HUANG Wenmei1,2WENG Ling1,2(1State Key Laboratory of Reliability and Intelligence of Electrical Equipment(Province and Ministry Jointly Set Up),Hebei University of Technology,Tianjin300130,China)(2Key Laboratory of Electromagnetic Field and Electrical Apparatus Reliability of Hebei Province,Hebei University of Technology,Tianjin300130,China)Abstract:According to the equivalent circuit model and impedance matching theory of magnetostrictive ultrasonic transducers,an optimizedπ-type matching network is designed in this paper.The network has the functions of tuning,variable resistance andfiltering,and is suitable for impedance matching of magnetostrictive ultrasonic transducer systems operating in the mid-and low-frequency ultrasonic frequency ranges.Simulation and experimental results show that:after accessing theπ-type impedance matching network,the maximum power transmission between the driving power supply and the transducer is realized,the waveform quality of the electrical signal at both ends of the transducer is optimized,and the excitation current of the transducer is increased by40%.The paper provides a technical support for the application of high-power magnetostrictive ultrasonic transducers.Keywords:Electromagnetic ultrasound;Magnetostrictive transducer;Impedance matching;Impedance frequency characteristics2020-04-17收稿;2020-06-28定稿∗国家自然科学基金项目(51777053)作者简介:冉超(1995–),男,重庆人,硕士研究生,研究方向:磁致伸缩超声换能器。
关于惠更斯原理的英文作文

关于惠更斯原理的英文作文The Huygens Principle is a fundamental concept in the field of wave theory, illustrating how each point on a wavefront can be considered as a source of secondary spherical wavelets.This principle, proposed by the Dutch scientist Christiaan Huygens in the 17th century, revolutionized our understanding of wave propagation. It posits that the wavefront at any given moment can be seen as the envelope of these secondary wavelets.In the context of light waves, the Huygens Principle helps explain phenomena such as reflection and refraction. When light encounters a boundary between two media, the principle suggests that each point on the wavefront generates new wavelets that interfere with each other, resulting in the observed bending of light.Moreover, the principle is instrumental in understanding diffraction, the bending of waves around obstacles and the spreading of waves through openings. It elegantly demonstrates how the wavefront continues to advance even when obstructed, a behavior crucial for technologies like optical fibers and diffractive lenses.Despite its simplicity, the Huygens Principle is not without its limitations. It does not account for the waveamplitude, which is essential for explaining the intensity of light. However, when combined with Fermat's Principle of Least Time, it provides a comprehensive framework for analyzing wave behavior.In essence, the Huygens Principle is a powerful tool in the study of wave phenomena, offering a visual and intuitive approach to understanding how waves interact with their environment and propagate through space. It remains a cornerstone of modern physics, with applications in various scientific and engineering disciplines.。
里德堡原子微波电场测量

doi:10.11823/j.issn.1674-5795.2021.01.01里德堡原子微波电场测量白金海,胡栋,贡昊,王宇(航空工业北京长城计量测试技术研究所,北京100095)摘要:里德堡原子是处于高激发态的原子,其主量子数大、寿命高,具有极化率高、电偶极矩大等特点,对外电场十分敏感。
基于热蒸气室中里德堡原子的量子干涉原理(电磁感应透明和Autler-Towns分裂效应)的微波电场精密测量不仅具有远高于传统偶极天线的灵敏度,且具有自校准、对外电场干扰少、测量频率范围大等优点,是下一代电场测量标准。
本文综述了里德堡原子的微波电场测量研究,详细介绍了其基本原理和当前研究进展,并讨论了未来发展方向。
关键词:量子精密测量;里德堡原子;微波电场;电磁感应透明中图分类号:TB97文献标识码:A文章编号:1674-5795(2021)01-0001-09Rydberg Atoms Based Microwave Electric Field SensingBAIJinhai,HU Dong,GONG Hao$WANG Yu(Changcheng Institute of Metrology&Measurement,Beijing100095,China)Abstract:Rydberg atoms are the atoms in highly excited states with lar-e principaO quantum numbers n,and long lifetimes.The lar-e Ryd-ber-atom polarizabilitu and strong dipole transitions between enereetically nearby states are highly sensitive to electris fielOs.The new developed scheme for microwave electric field precision measurement is based on quantum interference effects(electromaaneticclly induced transparency and Autler-Townes splitting)in Rydbere atoms contained in a dielectric vapoe cell.The mininium measured strengths of microwave electric fieies of the new scheme are far below the standard values obtained by traditional antenna methods.And it has several advantages,such as self-calibration,non-perturbation to the measured field,a broadband measurement frequency range,etc,is the next-generation electric field standard.In this review,we describe work on the new method for measuring microwave electric field based on Rydberg atoms.We introducc the basic theory and experimental techniques of the new method,and discuss the future development direction.Key words:quantum precision measurement;Rydberg atoms;microwave electric fielO;electromagnetically induced transparency0引言原子是一种典型的量子体系,具有可复现、性能稳定、能级精确等优点。
潮汐锁定的原理 英文
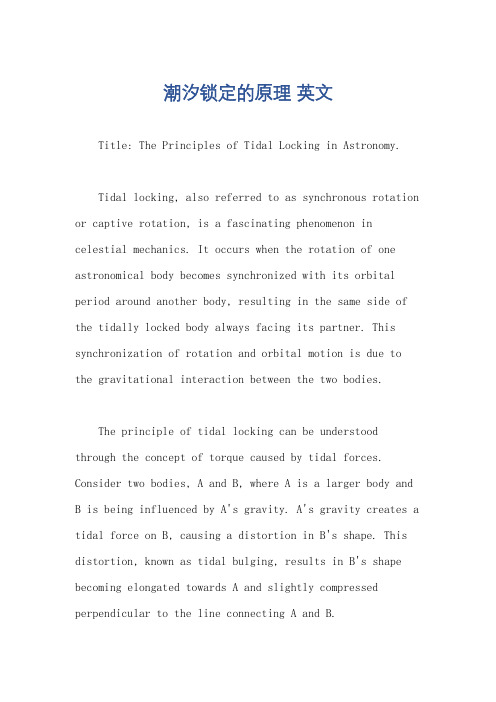
潮汐锁定的原理英文Title: The Principles of Tidal Locking in Astronomy.Tidal locking, also referred to as synchronous rotation or captive rotation, is a fascinating phenomenon in celestial mechanics. It occurs when the rotation of one astronomical body becomes synchronized with its orbital period around another body, resulting in the same side of the tidally locked body always facing its partner. This synchronization of rotation and orbital motion is due to the gravitational interaction between the two bodies.The principle of tidal locking can be understood through the concept of torque caused by tidal forces. Consider two bodies, A and B, where A is a larger body and B is being influenced by A's gravity. A's gravity creates a tidal force on B, causing a distortion in B's shape. This distortion, known as tidal bulging, results in B's shape becoming elongated towards A and slightly compressed perpendicular to the line connecting A and B.As B rotates, this tidal bulging travels over its surface. However, due to the gravitational influence of A, the bulging is not free to move anywhere on B's surface. Instead, it is forced to lag behind B's rotation, creating a torque that acts to slow down B's rotation. Over time, this torque causes B's rotation to slow down until it matches its orbital period around A. At this point, B becomes tidally locked to A, with the same side of B always facing A.The process of tidal locking can be further understood through the concept of "tidal friction." As B's rotation slows down and approaches synchronization with its orbit, the tidal bulging on B's surface starts to lag behind the rotation even more. This lagging creates a friction-like effect between B's rotation and the tidal forces exerted by A, gradually draining B's rotational energy. Eventually, this process leads to a stable configuration where B's rotation is synchronized with its orbit around A.Tidal locking is a common phenomenon in the solarsystem and beyond. For example, the moon is tidally locked to the Earth, which is why we always see the same side of the moon. Similarly, Mercury is tidally locked to the Sun, and Pluto is tidally locked to its moon Charon. In fact, tidal locking is so common in the solar system that it has been proposed as a possible explanation for the lack of habitable planets around certain stars.The mechanism of tidal locking also plays a role in the evolution of planetary systems. For example, in a system of multiple planets orbiting a star, tidal interactions between the planets can lead to their rotations becoming synchronized with their orbital periods. This synchronization can have profound effects on the climates and geologies of these planets.In conclusion, tidal locking is a fascinating phenomenon that occurs when the rotation of one astronomical body becomes synchronized with its orbital period around another body due to gravitational interactions. It is a common occurrence in the solar system and beyond, affecting the dynamics and evolution ofplanetary systems. Understanding the principles of tidal locking is crucial for comprehending the diverse array of celestial bodies and their interactions in our universe.。
- 1、下载文档前请自行甄别文档内容的完整性,平台不提供额外的编辑、内容补充、找答案等附加服务。
- 2、"仅部分预览"的文档,不可在线预览部分如存在完整性等问题,可反馈申请退款(可完整预览的文档不适用该条件!)。
- 3、如文档侵犯您的权益,请联系客服反馈,我们会尽快为您处理(人工客服工作时间:9:00-18:30)。
and neutron electric
dipole moments below their present experimental limits. Based on this observation, we discuss the constraints that the non-observation of electric dipole moments imposes on the radiativelygenerated CP-violating Higgs sector and on the mechanism of electroweak baryogenesis in the MSSM. We improve previously suggested benchmark scenarios of maximal CP violation for analyzing direct searches of CP-violating MSSM Higgs bosons at high-energy colliders, and stress the important complementary rˆ ole that a possible high-sensitivity measurement of the muon electric dipole moment to the level of 10−24 e cm can play in such analyses.
arXiv:hep-ph/0207277v4 2 Oct 2002
Apostolos Pilaftsis a,b
b
Theory Division, CERN, CH-1211 Geneva 23, Switzerland Department of Physics and Astronomy, University of Manchester, Manchester M13 9PL, United Kingdom
a
ABSTRACT
We perform a comprehensive study of the dominant two- and higher-loop contributions to the
205 Tl,
neutron and muon electric dipole moments induced by Higgs bosons, third-
(1.3)
In (1.3), the dots denote CP-odd operators of dimension 7 and higher. In our analysis, we will assume that like CT , the CP-odd operators of dimension 7 and higher give rise generically to negligible effects on the 205 Tl EDM. Moreover, although the contributions of the neglected CP-odd operators to other heavy atoms may be comparable to that of de , the experimental upper limits are still much weaker than dTl , by at least one order of magnitude. Consequently, we will only analyze predictions for the thallium EDM dTl and consider only two operators: the electron EDM de and the CP-odd electron–nucleon operator CS . From (1.1) and (1.3), it is then not difficult to deduce the following 2σ upper limits on these two CP-odd operators: |de |
PACS numbers: 11.30.Er, 14.80.Er
1
1
Introduction
The non-observation of electric dipole moments (EDMs) of the thallium atom and neutron, as well as the absence of large flavour-changing neutral-current (FCNC) decays put severe constraints on the parameters of a theory. Especially, these constraints become even more severe for supersymmetric theories, such as the MSSM, in which too large FCNC and CPviolating effects are generically predicted at the one-loop level, resulting in gross violations with experimental data. A possible resolution of such FCNC and CP crises, often considered in the literature [1], makes use of the decoupling properties of the heavy squarks and sleptons of the first two generations, whose masses should be larger than ∼ 10 TeV. Thus, for sufficiently heavy squarks and sleptons, the one-loop predictions for FCNC and EDM observables can be suppressed up to levels compatible with experiment. Also, such a solution poses no serious problem to the gauge hierarchy, as long as the first two generations of squarks and sleptons are not much heavier than 10 TeV. In this case, because of their suppressed Yukawa couplings, the radiative effect of the first two generations of sfermions on the Higgs-boson mass spectrum is still negligible, with respect to that of TeV scalar top and bottom quarks.1 Recently, it has been shown [2, 3] that even third-generation squarks may lead by themselves to observable effects on the electron and neutron EDMs through Higgs-bosonmediated two-loop graphs of the Barr–Zee type [4]. This observation offers new possibilities to probe the CP-violating soft-supersymmetry-breaking parameters related to the thirdgeneration squarks. Most interestingly, the same CP-violating parameters may induce radiatively a CP-noninvariant Higgs-sector [5, 6, 7, 8], leading to novel signatures at highenergy colliders [8, 9, 10, 11]. It is then obvious that EDM constraints do have important implications for the phenomenological predictions within the above framework of the MSSM with explicit CP violation. Moreover, employing upper limits on EDMs, one is, in principle, able to derive constraints on the phase of the SU(2)L gaugino mass, mW , which plays a central rˆ ole in electroweak baryogenesis [12] in the MSSM [13, 14]. On the experimental side, the current upper limit on the electron EDM de , as derived from the absence of a permanent atomic EDM for 205 Tl, has improved by a factor of almost 2 over the last few years [15, 16]. Specifically, the reported 2σ upper limit on a thallium EDM is [16] < 1.3 × 10−24 e cm . |dTl | ∼ (1.1)