Chapter 5 Inventory and supply chain
小保罗·R·墨菲《当代物流学》习题辅导
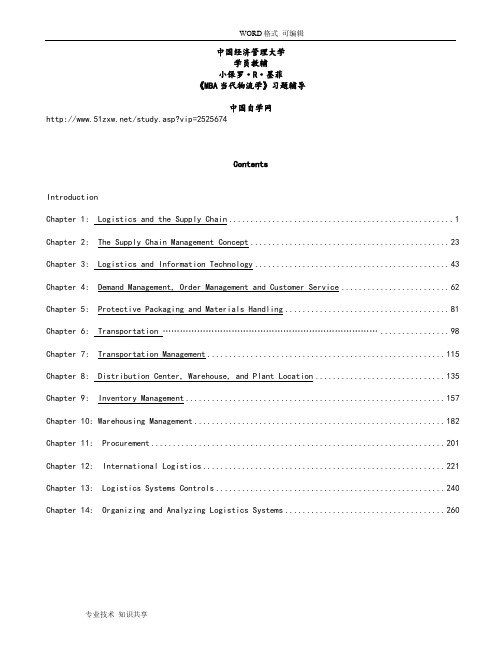
中国经济管理大学学员教辅小保罗·R·墨菲《MBA当代物流学》习题辅导中国自学网/study.asp?vip=2525674ContentsIntroductionChapter 1: Logistics and the Supply Chain (1)Chapter 2: The Supply Chain Management Concept (23)Chapter 3: Logistics and Information Technology (43)Chapter 4: Demand Management, Order Management and Customer Service (62)Chapter 5: Protective Packaging and Materials Handling (81)Chapter 6: Transportation (98)Chapter 7: Transportation Management (115)Chapter 8: Distribution Center, Warehouse, and Plant Location (135)Chapter 9: Inventory Management (157)Chapter 10: Warehousing Management (182)Chapter 11: Procurement (201)Chapter 12: International Logistics (221)Chapter 13: Logistics Systems Controls (240)Chapter 14: Organizing and Analyzing Logistics Systems (260)PART IIANSWERS TO END-OF-CHAPTER QUESTIONSCHAPTER 1: LOGISTICS AND THE SUPPLY CHAIN1. Did it surprise you that logistics can be such an important component in a country’s economic system? Why or why not?它构成了一个国家至少10%的GDP、对于经济增长有很重要的作用The answer to this question likely depends on a student’s prior exposure to logistics.A “typical” student in an undergraduate basic logistics course likely has had limitedexposure to and knowledge about logistics and thus would likely be unaware as tologistics’ impact on a country’s economic system. As such, she/he might be pl easantly surprised to learn that logistics often accounts for at least 10% of a country’s GDPand also is important for economic growth and development.2.Distinguish between possession, form, time, and place utility.Possession utility refers to the value or usefulness that comes from a customer beingable to take possession of a product and can be influenced by the relevant payment terms.Form utility refers to a product’s being in a form that (1) can be used by the customer and (2) is of value to the customer. Time utility refers to having products availablewhen they are needed by customers while place utility refers to having productsavailable where they are needed by customers.3.How does logistics contribute to time and place utility?时间效用:不同产品有不同的时间敏感度,香蕉和铅笔;地点效用:把产品从价至少的地方运到价值大的地方。
专业英语物流与供应链管理-5
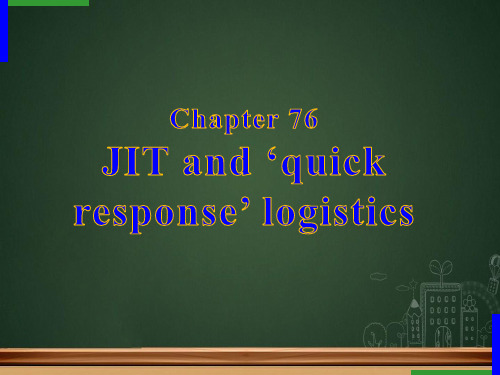
What’s reorder point (ROP)?
it’s a form of statistical inventory
balances the cost of holding inventory
against the costs of placing
replenishment orders.
指能平衡库存持有 成本和订购成本的
订购量。
Total cost
cost
Inventory 库存持有成本
carrying cost
This distinction is crucial because whilst independent demand may be forecast using traditional methods, dependent demand must be calculated, based on the demand at the next level in the logistics c二ha者i的n.区别很明显,因
How to determine a reorder point ?
a reorder point or reorder level is
predetermined based on the
expected length of the
replenishment lead time (see figure
•Essentially JIT is a ‘pull’ concept
where demand at the end of the
毕业论文物流英语作文模板
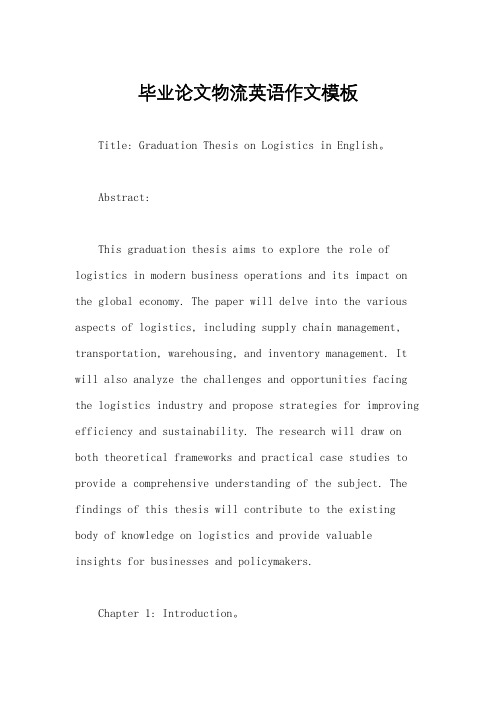
毕业论文物流英语作文模板Title: Graduation Thesis on Logistics in English。
Abstract:This graduation thesis aims to explore the role of logistics in modern business operations and its impact on the global economy. The paper will delve into the various aspects of logistics, including supply chain management, transportation, warehousing, and inventory management. It will also analyze the challenges and opportunities facing the logistics industry and propose strategies for improving efficiency and sustainability. The research will draw on both theoretical frameworks and practical case studies to provide a comprehensive understanding of the subject. The findings of this thesis will contribute to the existing body of knowledge on logistics and provide valuableinsights for businesses and policymakers.Chapter 1: Introduction。
供应链专业英语词汇总结

供应链专业英语词汇总结以下是一些供应链专业英语词汇的总结:1. 供应链管理 Supply Chain Management (SCM)2. 采购 Purchasing3. 供应商 Supplier4. 生产制造 Manufacturing5. 物流 Logistics6. 配送 Distribution7. 库存管理 Inventory Management (IM)8. 需求预测 Demand Forecasting9. 供应链协同 Supply Chain Collaboration (SCC)10. 供应商管理库存 Vendor Managed Inventory (VMI)11. 采购执行 Purchase Execution12. 物流执行 Logistics Execution13. 逆向物流 Reverse Logistics14. 准时制生产 Just-In-Time (JIT) Manufacturing15. 快速响应 Quick Response (QR)16. 有效客户响应 Efficient Consumer Response (ECR)17. 连续库存补充 Continuous Replenishment Program (CRP)18. 电子数据交换 Electronic Data Interchange (EDI)19. 全球定位系统 Global Positioning System (GPS)20. 射频识别技术 Radio Frequency Identification (RFID)21. 自动化仓库 Automated Warehouse22. 高级计划与排程 Advanced Planning and Scheduling (APS)23. 企业资源规划 Enterprise Resource Planning (ERP)24. 客户关系管理 Customer Relationship Management (CRM)25. 电子采购 e-Procurement26. 供应链风险管理 Supply Chain Risk Management (SCRM)27. 精益供应链管理 Lean Supply Chain Management (LSCM)28. 环境可持续供应链管理 Environmentally Sustainable Supply Chain Management (ESSCM)29. 社会可持续供应链管理 Socially Sustainable Supply Chain Management (SSSCM)30. 可持续供应链管理 Sustainable Supply Chain Management (SSCM)31. 供应商评价 Supplier Evaluation32. 采购谈判 Purchasing Negotiation33. 供应链绩效评估 Supply Chain Performance Evaluation (SCPE)34. 总成本分析 Total Cost Analysis (TCA)35. 总持有成本 Total Cost of Ownership (TCO)36. 经济订货量模型 Economic Order Quantity Model (EOQ)37. 安全库存 Safety Stock38. 采购周期 Purchasing Cycle39. 供应链网络 Supply Chain Network40. 多供应商 Multi-supplier41. 多配送中心 Multi-distribution Center42. 库存周转率 Inventory Turnover Rate43. 在途库存 In-transit Inventory44. 在途货物 In-transit Cargo45. 在途车辆 In-transit Vehicle46. 在途订单 In-transit Order47. 在途发票 In-transit Invoice。
供应链的名词解释
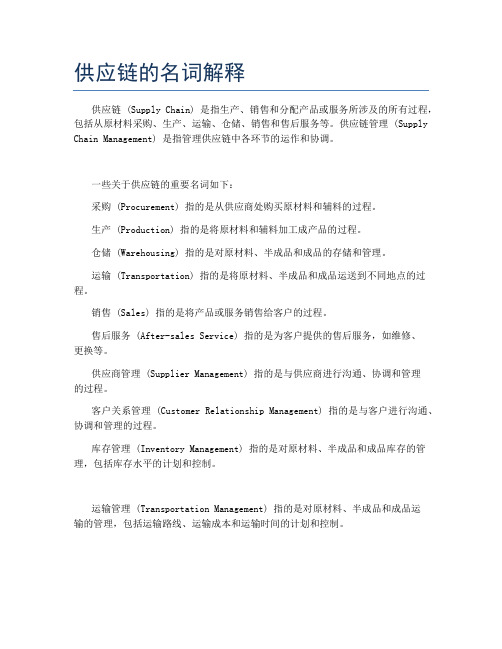
供应链的名词解释供应链 (Supply Chain) 是指生产、销售和分配产品或服务所涉及的所有过程,包括从原材料采购、生产、运输、仓储、销售和售后服务等。
供应链管理 (Supply Chain Management) 是指管理供应链中各环节的运作和协调。
一些关于供应链的重要名词如下:采购 (Procurement) 指的是从供应商处购买原材料和辅料的过程。
生产 (Production) 指的是将原材料和辅料加工成产品的过程。
仓储 (Warehousing) 指的是对原材料、半成品和成品的存储和管理。
运输 (Transportation) 指的是将原材料、半成品和成品运送到不同地点的过程。
销售 (Sales) 指的是将产品或服务销售给客户的过程。
售后服务 (After-sales Service) 指的是为客户提供的售后服务,如维修、更换等。
供应商管理 (Supplier Management) 指的是与供应商进行沟通、协调和管理的过程。
客户关系管理 (Customer Relationship Management) 指的是与客户进行沟通、协调和管理的过程。
库存管理 (Inventory Management) 指的是对原材料、半成品和成品库存的管理,包括库存水平的计划和控制。
运输管理 (Transportation Management) 指的是对原材料、半成品和成品运输的管理,包括运输路线、运输成本和运输时间的计划和控制。
供应链风险管理 (Supply Chain Risk Management) 指的是识别、评估和应对供应链中各环节的风险,以确保供应链的稳定和可靠性。
物流管理 (Logistics Management) 指的是对原材料、半成品和成品的运输、仓储和配送的管理。
生产计划与控制 (Production Planning and Control) 指的是对生产活动的计划和控制,包括生产进度计划,生产计划调整,生产线调度。
供应链开发流程 英语

供应链开发流程英语Supply Chain Development Process.The supply chain development process is a crucial aspect of any business operation, as it involves the orchestration of various activities across different organizations to ensure the efficient flow of goods and services from suppliers to customers. This process involves several stages, from initial planning and strategy development to implementation, monitoring, and continuous improvement.1. Strategy Development.The first step in the supply chain development process is strategy development. This involves identifying the objectives and goals of the supply chain, taking into account the overall business strategy and the specific needs of the organization. This stage also involves analyzing the current supply chain structure, identifyingany bottlenecks or inefficiencies, and devising strategies to address these issues.2. Supplier Selection and Management.Supplier selection and management is a crucial part of the supply chain development process. It involves evaluating potential suppliers based on various criteria such as quality, cost, delivery reliability, and service. Establishing long-term relationships with reliable suppliers is essential for ensuring the smooth operation of the supply chain.3. Logistics Planning.Logistics planning involves managing the movement of goods and materials from suppliers to manufacturing facilities and ultimately to customers. This stage involves planning and executing transportation, warehousing, and distribution activities to ensure timely delivery and cost-efficiency.4. Inventory Management.Inventory management is another critical aspect of the supply chain development process. It involves managing the stock of goods and materials to ensure availability when needed, while also minimizing inventory carrying costs. Effective inventory management requires accurate demand forecasting, inventory planning, and the use of advanced inventory control techniques.5. Customs and Compliance.When dealing with international suppliers or customers, customs and compliance become crucial considerations. This stage involves understanding and complying with allrelevant import and export regulations, tariffs, and quotas. Failure to comply with these regulations can result in delays, fines, and other costs that can significantlyimpact the efficiency of the supply chain.6. Risk Management.Risk management is a critical component of the supply chain development process. It involves identifyingpotential risks and vulnerabilities in the supply chain, assessing their impact, and devising strategies to mitigate these risks. This can include managing supplier risk, transportation risk, demand risk, and other types of risks that can disrupt the flow of goods and services.7. Technology Integration.In today's digital era, technology integration is essential for effective supply chain management. This involves the use of advanced technologies such as supply chain management software, analytics tools, and other digital solutions to improve visibility, efficiency, and collaboration across the supply chain. Technology integration can help organizations make better decisions, respond quickly to changes, and optimize their operations.8. Monitoring and Evaluation.Monitoring and evaluation are ongoing activities in thesupply chain development process. They involve tracking key performance indicators (KPIs) and metrics to assess the performance of the supply chain and identify any areas that need improvement. Regular monitoring and evaluation enable organizations to adapt to changes in the market, customer demand, and supplier performance, and make necessary adjustments to ensure the optimal operation of the supply chain.9. Continuous Improvement.The supply chain development process is an ongoing journey of continuous improvement. Organizations should strive to identify areas for improvement, implement changes, and measure the results to ensure that the supply chain remains competitive and efficient. This can involveadopting new technologies, implementing lean or agile methodologies, or developing stronger relationships with suppliers and customers.In conclusion, the supply chain development process isa complex and multifaceted task that requires a holisticapproach. It involves strategy development, supplier selection and management, logistics planning, inventory management, customs and compliance, risk management, technology integration, monitoring and evaluation, and continuous improvement. By following this process, organizations can ensure the efficient and effective operation of their supply chain, improve customer satisfaction, and drive competitive advantage.。
临床实验室管理英语翻译

临床实验室管理英语翻译Clinical Laboratory Management: English TranslationIntroductionClinical laboratory management plays a crucial role in ensuring the smooth functioning of healthcare facilities. Effective management practices in this field are essential for accurate diagnoses, patient care, and overall healthcare system efficiency. This article aims to provide an English translation of the key concepts and terminology related to clinical laboratory management.1. Quality Control and AssuranceThe management of a clinical laboratory revolves around maintaining high-quality standards. Quality control involves various processes and measures to ensure accurate and reliable test results. This includes regular calibration and maintenance of laboratory equipment, proper training of staff members, and adherence to established protocols and procedures.2. Accreditation and CertificationAccreditation and certification are vital aspects of clinical laboratory management. Accreditation refers to the recognition of a laboratory's competence to perform specific tests and procedures. Certification, on the other hand, validates the proficiency of laboratory professionals who execute these tests. Both accreditation and certification contribute to ensuring the reliability and credibility of laboratory results.3. Inventory and Supply Chain ManagementThe effective management of laboratory resources, including inventory and supply chain, is crucial for uninterrupted laboratory operations. Maintaining an accurate inventory record, tracking the usage of supplies, and ensuring timely procurement are key responsibilities of laboratory management. A well-managed supply chain ensures the availability of necessary reagents, consumables, and equipment, thereby preventing delays in test results.4. Staffing and TrainingClinical laboratory management involves overseeing the staffing and training processes. Hiring qualified laboratory personnel, assigning appropriate roles and responsibilities, and providing adequate training and continuing education are essential to ensure proficiency and competence among the laboratory staff. Regular performance evaluations and career development opportunities further contribute to staff motivation and retention.5. Laboratory Information Systems (LIS)The implementation and management of laboratory information systems are essential for efficient laboratory operations. These systems include electronic medical record integration, result reporting, billing, and data analysis functionalities. By utilizing LIS, laboratories can streamline their workflow, reduce human errors, enhance communication with healthcare providers, and improve overall laboratory efficiency.6. Safety and Biosecurity MeasuresClinical laboratory management places significant emphasis on safety and biosecurity measures. Compliance with safety protocols, including the appropriate handling, storage, and disposal of hazardous materials, is essential to safeguard laboratory personnel, patients, and the environment. Additionally, consistent adherence to biosecurity guidelines helps prevent the spread of infectious diseases within the laboratory setting.7. Continuous Quality ImprovementContinuous quality improvement is a fundamental principle in clinical laboratory management. Regular audits, performance assessments, and feedback mechanisms help identify areas for improvement. By analyzing these findings, laboratory management can implement necessary changes to enhance processes, reduce errors, and optimize overall laboratory performance.ConclusionIn conclusion, effective management of clinical laboratories is imperative for the delivery of accurate and timely diagnostic services. This article has provided an English translation of the key aspects of clinical laboratory management, including quality control, accreditation, inventory management, staffing, laboratory information systems, safety measures, and continuous quality improvement. By implementing these management practices, laboratories can ensure optimal patient care and contribute to the overall efficiency of healthcare systems.。
物流英语Chapter 5

1 Inventory Classifications
It’s important to know the key classifications of inventory because the classification influences the way that inventory is managed. While inventory generally exists to service demand, in some situations inventory is carried to stimulate demand, also know as psychic stock. This type of inventory is associated with retail stores, and the general idea is that customer purchases are stimulated by inventory that they can see.
Where R=Reorder point in units; D=Average daily demand in units;
- 1、下载文档前请自行甄别文档内容的完整性,平台不提供额外的编辑、内容补充、找答案等附加服务。
- 2、"仅部分预览"的文档,不可在线预览部分如存在完整性等问题,可反馈申请退款(可完整预览的文档不适用该条件!)。
- 3、如文档侵犯您的权益,请联系客服反馈,我们会尽快为您处理(人工客服工作时间:9:00-18:30)。
Dependent:
Demand for a particular product is directly related to another product. (e.g.: component parts) Demand often occurs in lumps Demand is managed based on plans (e.g.: MPS) MRP and MRP Ⅱ systems are used for these elements. 5
3
Types of Demand
Review: Types of Inventory
4
Types of Demand
Independent:
Demand for one particular product isn’t related to the demand for any other product. (e.g.: finished goods made-to-stock) Demand often occurs at constant rate Demand is managed based on forecasts EOQ approach is commonly used for products with independent demand.
① ② ③ ④ develop a much closer relationship with the retailer; giving a much better visibility of real demand; make the planning of production much easier; lead to signification reductions in inventory holding.
6
Types of Demand
The pull approach is a reactive one where the emphasis is on responding directly to actual customer demand, which pulls the required product through the system. The idea of a pull system is that it can react very quickly to sudden changes in demand. The pull system is most useful where there is independent demand and where there is uncertainty of demand requirements or of order cycle time.
7
Push and Pull System
推-拉 界限 推式系统 拉式系统 末端顾客
独立性需求 JIT
原材料
相关性需求 MRP
8
Approaches to Inventory Reduction
9
Approaches to Inventory Reduction
The aim of lead-time reduction is to reduce the amount of unnecessary time within the order-to delivery process and thus reduce the need to hold so much inventory as cover for this time delay. 提前期减少的目的是为了减少从订货到送 货过程中不必要的时间,由此减少持有太 多库存的必要,来掩盖时间的延迟。
11
12
Inventory Planning for Manufacturing
1 2 MRP JIT DRP
Time Compression
13
3 4
Inventory Planning for Manufacturing
Material requirement planning (MRP), which is a computerized system for forecasting materials requirements based on a company’s master production schedule and bill of material for each product.
Types of Demand
A push approach to inventory planning is usually based on a set plan that is predetermined according to creatures of inventory reordering. This approach is a proactive one in the sense that it is planned on the basis of estimated, or forecast demand for products from customers. The aim is to locate the demand and ensure that adequate stock is available in the right place at the right time. Typically, a push system is applicable for dependent demand and for cases where there are uncertainties in supply, source or production capacity limitations or the need to cater for seasonal demand.15Leabharlann ① ② ③ ④ ⑤ ⑥ ⑦
Social demand file
Suppliers’ resource file
DRP
Inventory File
Ordering planning
Delivery planning
16
Inventory Planning for Manufacturing
The concept of time compression is an important approach in the planning of manufacturing inventory requirements or perhaps it should be termed as the planned reduction in manufacturing and WIP inventory.
19
Inventory Planning for Retailing
The advantages of VMI For retailers:
① the reduction of operating costs; ② the delay in payment for the products.
For manufacturers:
③ Costs can be variable. Order costs relationships have changed with the introduction of automatic and EDI-related ordering procedures.
④ Production capacity can be at a premium; may not always be feasible to supply a given product as and when required. ⑤ Individual products are closely linked to others and need to be supplied with them, so that ‘complete order fulfillment’ is achieved.
Problems for example:
① Demand is not as predictable as it may once have been.
② Lead times are not constant. They can vary for the same product at different order times.
17
Inventory Planning for Retailing
1 2 VMI CRP QR
ECR
18
3 4
Inventory Planning for Retailing
Vendor Managed Inventory (VMI)
Inventory replenishment arrangement whereby the supplier either monitors the customer's inventory with own employees or receives stock information from the customer. The vendor then refills the stock automatically, without the customer initiating purchase orders. See also collaborative planning, forecasting, and replenishment (CPFR)协同规划、预测与补货
1
Problems with Traditional Inventory Planning
EOQ模型假设基础:
需求量为恒定、有循环性且已知 提前期为恒定且已知 不允许缺货 物料大量下单或制造,且整批入库 单位成本固定、无数量折扣、持有成本依 平均库存水平估算 物品为单一产品,与其他产品无相关性