塑胶成型常见不良与改善方法
塑胶成型不良分析
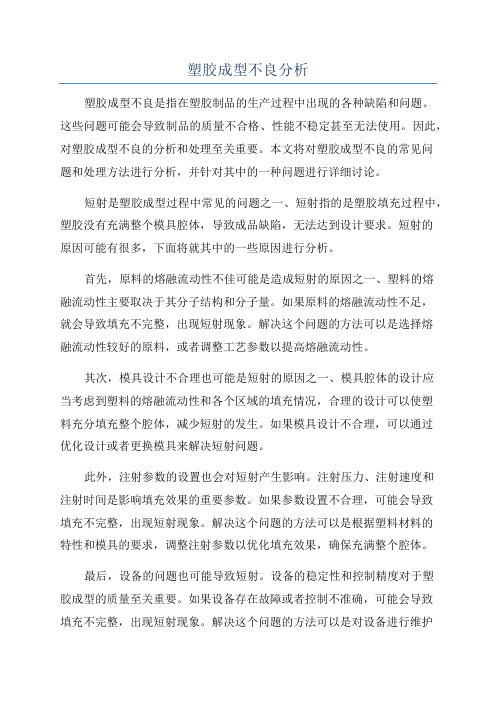
塑胶成型不良分析塑胶成型不良是指在塑胶制品的生产过程中出现的各种缺陷和问题。
这些问题可能会导致制品的质量不合格、性能不稳定甚至无法使用。
因此,对塑胶成型不良的分析和处理至关重要。
本文将对塑胶成型不良的常见问题和处理方法进行分析,并针对其中的一种问题进行详细讨论。
短射是塑胶成型过程中常见的问题之一、短射指的是塑胶填充过程中,塑胶没有充满整个模具腔体,导致成品缺陷,无法达到设计要求。
短射的原因可能有很多,下面将就其中的一些原因进行分析。
首先,原料的熔融流动性不佳可能是造成短射的原因之一、塑料的熔融流动性主要取决于其分子结构和分子量。
如果原料的熔融流动性不足,就会导致填充不完整,出现短射现象。
解决这个问题的方法可以是选择熔融流动性较好的原料,或者调整工艺参数以提高熔融流动性。
其次,模具设计不合理也可能是短射的原因之一、模具腔体的设计应当考虑到塑料的熔融流动性和各个区域的填充情况,合理的设计可以使塑料充分填充整个腔体,减少短射的发生。
如果模具设计不合理,可以通过优化设计或者更换模具来解决短射问题。
此外,注射参数的设置也会对短射产生影响。
注射压力、注射速度和注射时间是影响填充效果的重要参数。
如果参数设置不合理,可能会导致填充不完整,出现短射现象。
解决这个问题的方法可以是根据塑料材料的特性和模具的要求,调整注射参数以优化填充效果,确保充满整个腔体。
最后,设备的问题也可能导致短射。
设备的稳定性和控制精度对于塑胶成型的质量至关重要。
如果设备存在故障或者控制不准确,可能会导致填充不完整,出现短射现象。
解决这个问题的方法可以是对设备进行维护和保养,确保设备正常运行。
此外,定期检查和校准设备的控制系统,确保精度和稳定性。
综上所述,塑胶成型不良是塑胶制品生产过程中常见的问题。
对于短射这一问题,其原因可能包括原料、模具设计、注射参数和设备等方面。
为了解决短射问题,可以选择合适的原料,优化模具设计,调整注射参数以及维护设备等措施。
塑胶成形不良现象

塑胶加工成形不良现象与不良对策方法 1.披风不良现象∶模具的分模线、分模面或模具边角之处多胶或有毛刺等。
原因∶塑胶温度过高,射出压力过大,合模压力不足。
对策∶(1)锁模压力增大。
(2)注塑压力减低。
(3)射胶行程减低。
(4)注射速度减低。
(5)模板温度减低。
(6)背压降低。
(7)射胶筒温度降低。
(8)检查模具。
2.结合线不良现象∶胶件之表面有明显的夹线纹。
原因∶两股以上分流射入模腔,细线冷却而生成汇合细纹。
对策∶(1)射胶筒温度提高。
(2)模板温度提高。
(3)射嘴温度提高。
(4)注射压力加大。
(5)注射速度加大。
(6)疏气线加多。
(7)加大入水口。
3.缩水不良现象∶胶件之表面有明显的凹入现象。
t=T/2 以下原因∶肉厚较厚,如右所示∶对策∶(1)射胶行程加大。
(2)螺杆向前时间延长。
(3)保压加大。
(4)注射压力加大。
(5)模板温度降低。
(6)射胶筒温度降低。
(7)注射温度加大。
4.拖花(拖模)不良现象1∶胶件之表面有拖伤条痕。
原因∶金型有伤痕,打光不良,金型有倒扣等现象。
对策∶检查模具是否有伤痕,模具要充分打光,金型倒扣位省平,打光。
不良现象2∶シボ(蝕紋)の場合(表面有拖伤条痕)。
原因∶シボ目大(粗),抜勾配(斜度)小。
(噴沙)对策∶シボ目小(細)に変更,勾配(斜度)大に変更,ビーズ加工5.走水不齐(充填不足)不良现象∶胶件中有部分骨位或较薄部分之胶位有不满胶现象。
原因∶胶件中肉厚太薄,排气不良,浇口截面太小。
对策∶(1)增加料管供料。
(2)增加射出速度。
(3)加大射出行程。
(4)注射压力加大。
(5)保压加大。
(6)射胶筒温度加高。
(7)背压加大。
(8)射嘴温度提高(9)模板温度提高。
(10)入水口加大。
(11)加大浇道截面。
6.流痕不良现象∶浇口或其他窄段成形品表面生成年轮状细条纹。
原因∶溶状聚合物推动固化聚合物前移时,生成细条纹。
对策∶(1)射胶筒温度提高。
(2)射嘴温度提高。
(3)提高模温。
塑胶成型常见不良原因分析及对策
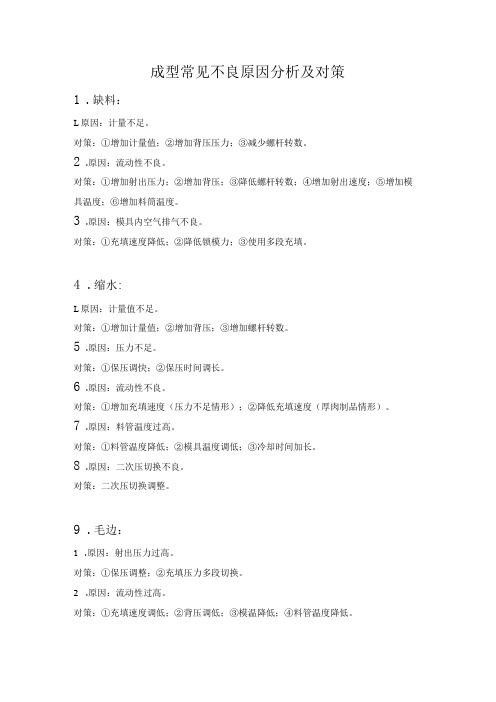
成型常见不良原因分析及对策1.缺料:L原因:计量不足。
对策:①增加计量值;②增加背压压力;③减少螺杆转数。
2.原因:流动性不良。
对策:①增加射出压力;②增加背压;③降低螺杆转数;④增加射出速度;⑤增加模具温度;⑥增加料筒温度。
3.原因:模具内空气排气不良。
对策:①充填速度降低;②降低锁模力;③使用多段充填。
4.缩水:L原因:计量值不足。
对策:①增加计量值;②增加背压;③增加螺杆转数。
5.原因:压力不足。
对策:①保压调快;②保压时间调长。
6.原因:流动性不良。
对策:①增加充填速度(压力不足情形);②降低充填速度(厚肉制品情形)。
7.原因:料管温度过高。
对策:①料管温度降低;②模具温度调低;③冷却时间加长。
8.原因:二次压切换不良。
对策:二次压切换调整。
9.毛边:1.原因:射出压力过高。
对策:①保压调整;②充填压力多段切换。
2.原因:流动性过高。
对策:①充填速度调低;②背压调低;③模温降低;④料管温度降低。
3.原因:二次压切换不良。
对策:①提前切换二次压;②减少计量值。
4.原因:模内空气排出不良。
对策:①充填速度降低;②多段射出;③型缔力调低。
5.原因:锁模力不足,模具密合不够。
对策:锁模力增大。
4.气泡:1.原因:计量时空气进入。
对策:①背压调高;②螺杆转数调低;③进料段温度降低;④降低加热筒后段温度。
2.原因:加热筒内部异常发热。
对策:①增加背压;②减少螺杆转数。
3.原因:松退量过多。
对策:①松退量减少;②松退速度减小。
4.原因:体积收缩。
对策:①增加背压;②延长保压时间;③增高模具温度;④降低料管温度;⑤降低充填速度(厚肉制品情形);⑥增加充填速度(压力不足情形)。
5.原因:模具内空气排出不良。
对策:①降低充填速度;②多段射出;③降低锁模力。
6.气纹:1.原因:速度过快或压力过大。
对策:降压或减速。
2.原因:料温过低。
对策:提高前段温度。
对策:提升模具温度。
4.原因:浇口或太小或太大。
对策:模具改善。
塑胶常见不良及解决方法

塑胶常见不良及解决方法塑胶是一种常见的材料,广泛应用于各种行业和领域。
然而,由于塑胶的特性以及制造过程中的一些问题,常常会出现一些不良现象。
本文将重点介绍一些常见的塑胶不良及其解决方法。
1.氣泡:塑膠制品中常見的一種不良現象是氣泡,這會在成品表面或内部形成小气囊。
气泡的形成是由于塑胶熔融时含有的空气或挥发物没有充分释放出来。
解决方法包括降低加工温度、增加熔体压力、增加注射速度和使用抗气泡添加剂等。
2.热胀冷缩:塑胶制品在温度变化下会发生热胀冷缩,导致尺寸变化。
这可能会导致配件无法正常连接或安装。
为了解决这个问题,可以采用材料改性或加工工艺改进,如增加冷却时间、降低注射温度等。
3.白化:白化是指塑胶制品表面或内部出现白色斑点或条纹。
这种现象通常是由于塑胶在注射过程中发生气泡聚集或制品未达到均匀熔融所致。
解决方法包括优化注射工艺、增加熔体压力、使用抗白化添加剂等。
4.热裂纹:热裂纹是指在塑胶产品成型过程中出现的裂纹现象。
这通常是由于塑胶在成型过程中存在过大的应力集中,导致塑胶产生裂纹。
解决方法包括改变模具设计、增加冷却时间、预混塑胶料等。
5.变色:变色是指塑胶制品在使用或储存过程中出现颜色变化。
这可能是由于塑胶材料受到光、热、氧化等外界因素的影响所致。
解决方法包括选择适当的防褪色添加剂、合理储存塑胶制品等。
6.毛刺:毛刺是指塑胶制品表面出现不平整、刺状的小颗粒。
这通常是由于模具表面不平整或注射工艺不当所导致的。
解决方法包括优化模具设计、控制注射压力、调整注射速度等。
7.缩水:缩水是指塑胶制品在冷却过程中发生体积收缩。
这可能导致尺寸偏离设计要求。
解决方法包括优化塑胶成型工艺、增加冷却时间和选择合适的材料等。
8.潜伏期延长:有些塑胶在使用一段时间后会发生不良现象,如变形、断裂等。
这可能是由于塑胶受到环境因素、应力或热老化的影响导致的。
解决方法包括选择合适的材料、控制加工温度、降低应力等。
总结起来,塑胶制品的不良现象可能是由于材料、工艺或环境等多种因素造成的。
塑胶产品外观不良改善管控方案

塑胶产品外观不良改善管控方案一、塑胶产品外观不良的原因1. 原材料问题:塑胶产品的外观质量与原材料的质量密切相关。
如果原材料的质量不稳定或掺杂了杂质,就会导致产品表面出现气泡、色差、瑕疵等问题。
2. 生产工艺问题:塑胶产品的生产过程中,如果温度、压力、注塑速度等工艺参数控制不当,就会导致产品外观不良。
比如温度过高会导致熔融塑料流动性增加,容易产生短射、缩短等问题。
3. 模具问题:模具的质量和设计也会对产品外观产生影响。
如果模具的表面粗糙度不达标或者设计不合理,就容易导致产品表面出现模纹、毛刺等问题。
二、改善管控方案的制定1. 优化原材料选用:选择质量稳定的原材料供应商,并与供应商建立长期稳定的合作关系。
同时,建立原材料质量检验标准,对原材料进行全面检测,确保其符合要求。
2. 优化生产工艺:制定严格的生产工艺流程,并进行员工培训,提高员工的操作技能。
同时,建立完善的生产工艺控制系统,定期对关键工艺参数进行监控和调整,确保产品质量稳定。
3. 优化模具设计和制造:与专业的模具设计师合作,进行模具的设计和制造。
确保模具的表面粗糙度达到要求,并且模具结构合理,以提高产品的外观质量。
三、改善管控方案的实施1. 建立质量管理体系:制定塑胶产品质量管理手册,明确各个环节的责任和要求。
同时,建立全面的质量管理体系,包括原材料进货检验、生产过程控制、产品出货检验等。
2. 定期进行质量检查:制定检查计划,定期对产品进行抽样检验,包括外观质量、尺寸偏差等方面。
对不合格产品进行分类处理,并分析原因,及时采取纠正措施。
3. 进行质量培训:对质量管理人员和生产操作人员进行培训,提高其质量意识和操作技能。
培训内容包括质量控制知识、工艺参数调整方法等。
4. 建立反馈机制:建立客户投诉反馈机制,及时处理客户反馈的问题,并进行分析和改进。
同时,建立内部质量反馈机制,对内部质量问题进行跟踪和整改。
总结:通过对塑胶产品外观不良的原因进行分析,并制定和实施改善管控方案,可以有效提高塑胶产品的外观质量。
注塑成型常见不良现象及处理措施

注塑成型常见不良现象及处理措施注塑成型常见的不良现象有以下几种:
1. 短射:指注塑料进模型中未充满模腔,导致产品缺陷。
处理措施:增加注射
压力、延长注射时间、增加料缸温度、增加模具温度、增加模具出料口直径等。
2. 气泡:指产品表面或内部出现气泡,影响产品质量。
处理措施:增加注射压力、延长注射时间、增加模具温度、增加料缸温度、增加模具出料口直径、增加模具排气孔等。
3. 热熔线:指产品表面出现细小的线状缺陷,通常是由于注射速度过快导致的。
处理措施:减小注射速度、增加模具温度、增加模具出料口直径等。
4. 毛刺:指产品表面出现细小的凸起,通常是由于模具设计不合理或模具磨损
导致的。
处理措施:修复模具、修改模具设计、增加模具温度、增加模具出料口直径等。
5. 缩水:指产品尺寸缩小,通常是由于注射压力不足或冷却时间不足导致的。
处理措施:增加注射压力、延长冷却时间、增加模具温度等。
6. 毛洞:指产品表面或内部出现凹陷,通常是由于注射速度过快或模具设计不
合理导致的。
处理措施:减小注射速度、修改模具设计、增加模具温度等。
处理不良现象的关键是找到问题的根源,然后针对性地采取相应的处理措施。
同时,注塑成型过程中的参数控制和模具维护也是关键的因素,需要进行定期检查和调整。
塑胶件常见缺陷产生的原因及解决方法

塑胶件常见缺陷产生的原因及解决方法一、材料问题1.材料选择不当:选择不适合的塑胶材料或材料质量不达标,容易导致塑胶件的缺陷。
解决方法是根据具体要求选择合适的塑胶材料,并进行必要的材料测试和质量控制。
2.材料批次差异:不同批次的塑胶材料可能存在差异,如流动性、收缩率等,导致成型件的缺陷。
解决方法是进行材料测试和合理的材料配方设计,确保不同批次的材料性能稳定一致。
二、工艺问题1.注塑工艺参数不合理:注塑工艺参数(如注射速度、保压时间等)不合理会导致成型件的缺陷,如短流、气泡等。
解决方法是通过优化注塑工艺参数,使之更加合理和稳定。
2.注塑模具设计和制造问题:模具结构不合理、尺寸精度不达标等问题会导致成型件的缺陷,如模具表面瑕疵、尺寸偏差等。
解决方法是进行合理的模具设计和制造,并进行必要的模具修整和维护。
3.注塑材料温度控制不当:材料温度过高或过低都会导致成型件的缺陷,如熔接线、气泡等。
解决方法是通过调整料筒温度、模具温度等进行合理的温度控制。
4.模具开合不良:模具开合不良或夹模力不足会导致成型件的缺陷,如模具压痕、塌陷等。
解决方法是保持模具开合顺畅,并确保夹模力适当。
三、设计问题1.设计尺寸不合理:设计尺寸过大或过小、壁厚不均匀等问题会导致成型件的缺陷,如尺寸偏差、变形等。
解决方法是根据塑胶件的使用要求和成型工艺特点进行合理的尺寸设计,并进行必要的尺寸优化。
2.设计结构不合理:设计结构复杂、壁薄部位过多等问题容易导致成型件的缺陷,如留痕、焊痕等。
解决方法是简化设计结构、增加加强筋等措施,提高塑胶件的强度和表面质量。
3.装配接口设计不当:塑胶件的装配接口设计不当会导致装配困难、配套件脱落等问题,影响整体使用效果。
解决方法是合理设计装配接口,确保装配紧固可靠。
以上是塑胶件常见缺陷产生的原因及解决方法的概述。
在实际生产中,还需要根据具体情况进行详细分析和解决。
为了确保塑胶件的质量,需要在材料选择、工艺控制和设计优化等方面进行全面的控制和改进。
塑胶常见不良解决方法
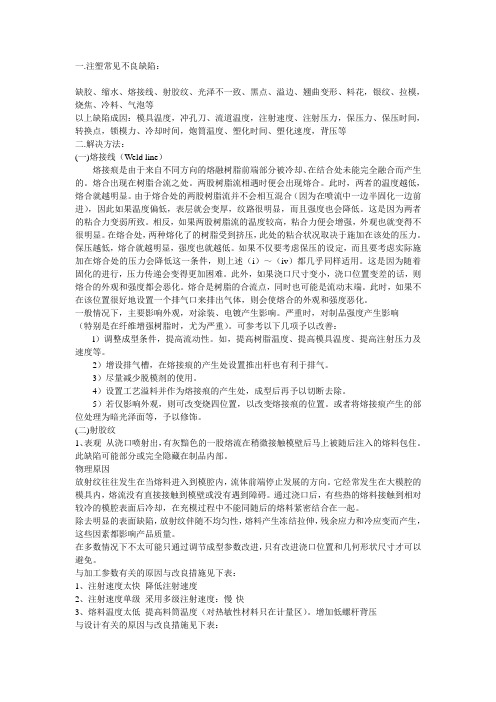
一.注塑常见不良缺陷:缺胶、缩水、熔接线、射胶纹、光泽不一致、黑点、溢边、翘曲变形、料花,银纹、拉模,烧焦、冷料、气泡等以上缺陷成因:模具温度,冲孔刀、流道温度,注射速度、注射压力,保压力、保压时间,转换点,锁模力、冷却时间,炮筒温度、塑化时间、塑化速度,背压等二.解决方法:(一)熔接线(Weld line)熔接痕是由于来自不同方向的熔融树脂前端部分被冷却、在结合处未能完全融合而产生的。
熔合出现在树脂合流之处。
两股树脂流相遇时便会出现熔合。
此时,两者的温度越低,熔合就越明显。
由于熔合处的两股树脂流并不会相互混合(因为在喷流中一边半固化一边前进),因此如果温度偏低,表层就会变厚,纹路很明显,而且强度也会降低。
这是因为两者的粘合力变弱所致。
相反,如果两股树脂流的温度较高,粘合力便会增强,外观也就变得不很明显。
在熔合处,两种熔化了的树脂受到挤压,此处的粘合状况取决于施加在该处的压力。
保压越低,熔合就越明显,强度也就越低。
如果不仅要考虑保压的设定,而且要考虑实际施加在熔合处的压力会降低这一条件,则上述(i)~(iv)都几乎同样适用。
这是因为随着固化的进行,压力传递会变得更加困难。
此外,如果浇口尺寸变小,浇口位置变差的话,则熔合的外观和强度都会恶化。
熔合是树脂的合流点,同时也可能是流动末端。
此时,如果不在该位置很好地设置一个排气口来排出气体,则会使熔合的外观和强度恶化。
一般情况下,主要影响外观,对涂装、电镀产生影响。
严重时,对制品强度产生影响(特别是在纤维增强树脂时,尤为严重)。
可参考以下几项予以改善:l)调整成型条件,提高流动性。
如,提高树脂温度、提高模具温度、提高注射压力及速度等。
2)增设排气槽,在熔接痕的产生处设置推出杆也有利于排气。
3)尽量减少脱模剂的使用。
4)设置工艺溢料并作为熔接痕的产生处,成型后再予以切断去除。
5)若仅影响外观,则可改变烧四位置,以改变熔接痕的位置。
或者将熔接痕产生的部位处理为暗光泽面等,予以修饰。
- 1、下载文档前请自行甄别文档内容的完整性,平台不提供额外的编辑、内容补充、找答案等附加服务。
- 2、"仅部分预览"的文档,不可在线预览部分如存在完整性等问题,可反馈申请退款(可完整预览的文档不适用该条件!)。
- 3、如文档侵犯您的权益,请联系客服反馈,我们会尽快为您处理(人工客服工作时间:9:00-18:30)。
5:缩水或走胶不齐--其充填不足的主要 原因有以下几个方面 : a. 因機械注塑及塑化性能不足。 b. 型腔内加压不足(注塑壓力及速度不夠或模 具溫度.溶料溫度及噴嘴溫度太低) 。 c. 树脂流动性不足。 d. 排气效果不好 e.澆口及流道截面太細。 f.結構設計不合理,產品厚度與長度不成比例。 (一般塑膠件厚度在1--6MM,超過8MM或少 於0.5MM均不易成型)。
14:溶接線:成形材料合流時在成品表面形成的 紋痕。其部位強度較其他部位要弱(易斷裂)。
五:针对以上不良狀況,主要改善方法如下:
1:烧焦:可以用降低炮筒温度和烘料温度,以及增 加模具排氣和加大澆口来解决。
2:異物:首先要保證成型機及材料放置區域的清潔, 特別是原料要清潔干淨;及成型機不得過熱,不能使材料 滯留。
3:混色(色差):检查原料是否为全原料,其主要 是由于长期生产未对炮筒及螺杆进行清洗,残留在螺杆 上多余的原料经高温长期烘烤导致原料变质射出后而形 成。可用PP料对炮筒及螺杆进行清洗。
4:入水纹.夹水纹.气纹或光澤不足:可以降低料筒 温度;消除存料现象;降低注塑速度;加大浇口或流道尺寸; 按规定条件进行预干燥;降低注塑压力;加大模具排气及模 具本身的研磨程度等方面改善(模具原則上要達到鏡 面)。
240-260
230-290 280-330
40-80 85-120 30-80 30-80 30-50
30-80
500以上 800以 上
180-210 220-280 180-240
60-80 40-80 30-80
240-300
85-120
200-230
40-80
四, 射出成型時常见外观不良情形:
1.023 180-210 190-220 60-80 600以上
1.005 180-240 190-260 30-80 400以上
AS PC NYLON+20%GF NYLON+40%GF PP+20%GF
PBT
P.O.M GF AS GF PS GF
PC GF
ABS GF NYLON6 TPE-50A
1:烧焦:由热引起的材料分解,看起来象烧焦 痕迹。在清晰材料表面形成的朦胧点或区域
2:異物:在材料内部或表面的黑色可见杂质,或 烧焦的塑胶碎片形成的黑点或有色块状。
3:混色(色差):偏离原色或颜色不一致及不 均。主要由于材料(色粉)有问题或某些啤作参数 (如温度、速度)不当引起的胶件颜色与标准色板 不同。
二:注塑成型的五大要素简介:
1:温度。2:时间。3:压力。4:位置。5:速度 一:温度:包括烘料温度, 模具温度,炮热筒料 温
二:时间:包括冷却时间,射出时间,保壓时间。
三:压力:包括锁模压力,射出压力,保壓压力。
四:速度:包括锁模速度,射出速度,保壓速度。
五:位置:包括锁模位置,射出位置,顶出位置
AS树脂 聚碳酸酯树脂
尼龙+玻纤 尼龙+玻纤 PP+玻纤 聚丁烯苯 二甲酸脂 玻纤补强P.O.M .005 1.005 1.005 1.001 1.004
1.007
1.005 1.005 1.005
1.001
1.001 1.016 1.006
220-280 260-310 260-300 260-300 260-300
塑胶成型常见不良及解决方法
一,注塑成型的基本原理 二,注塑成型的五大要素简介 三,常见塑胶材料之射出成形条件 四,射出時常见外观不良原因及情形 五,針對成型時常见外观不良的主要
改善對策及方法
一,注塑成型的基本过程:
首先,让我们简单地了解一下注塑成型的基 本原理: (溶化 流动 固化)
颗粒状的高分子材料(塑胶原料),經過注塑机 螺杆的挤压和加热,成为熔融状态的可以流动的熔 体,在螺杆的推动下,塑料熔体通过注塑机喷嘴.模 具的主流道.分流道和浇口进入模具型腔,成型出具 有一定形状和尺寸制品的过程。注塑的结果是生 产出用户要求的塑料制品。(成型过程的一个完整 循环操作包括合模.填充.保压.冷却.开模.顶出等阶 段) 。
6:粘模:由于開模時圓柱位.卡勾位或檔牆開模時
粘前模,而啤出零件缺柱、缺肉或變形现象。
7:断针:由于模具上頂针或鑲件断掉,而使啤出
胶件无孔或多胶的现象。
8:披锋:通常是在分模面.排氣槽.頂針位或鑲件位
處,由于合模力不够,注射压力太大或模具合模面 贴合不好,形成的塑胶飞边料。
9:变形:胶件由于啤作太快或未包装或长时 间受压,制品收缩不均或内应力太大而导致 扭曲或弯曲之现象。
三,常见塑胶材料之射出成形条件
成形条件
材料名称 ABS
NYLON+43%GF PP PE PVC
ACRYLIC NYLON610 NYLON66 DURACON(P.O.
M) PS
名称
ABS树脂 尼龙+玻纤
聚丙烯 聚乙烯 氯化乙烯树脂 压克力(PMMA) 尼龙 尼龙 赛钢 聚苯乙烯
收缩 率
1.005 1.006 1.016 1.006 1.020 1.005 1.016 1.016
4:入水纹:夹水纹:气纹: 它會從澆口處以扇 形方式向外輻射發展,塑胶流动形成的象干涸河道 一样的条纹表面。由塑胶表面熔接在一起时形成的 可见线或可见痕。
5:缩水或走胶不齐:也叫欠注或缺料,一般發
生在制品壁厚較薄的地方,或流動路徑末端區域。 表面收缩或陷痕。由于温度太低,压力不足或射胶 时间太短等原因而使胶件缺料。
射出温 度 (℃)
200-300
200-260 200-260 180-200 240-280 230-290 240-280
树脂温 度 (℃)
200-240
模温 (℃)
40-80
射出压力 (Kg/cm2)
800以 上
210-280 30-50 400以上 210-290 30-50 500以上 180-200 260-280 40-80 6 0 0 以 上 240-300 30-60 600以上 250-310 60-80 600以上
10:烘痕(料花):因排气时气体被压缩,使 胶件局部表面温度较高造成光泽与别处不同。
11:拉伤、顶白:由于胶件成型后脱模不顺, 致使胶件开模时拉伤, 或顶针顶出胶件时压力 太大而在胶件上顶出的白痕。
12:强度差:由于原材料或其它啤作因素引起的胶 件易断或易裂现象。
13:油渍:指影响外观的顶针位或鑲件位及其它地 方之油污。