A Modified Model, Simulation, and Tests of a Full-Scale Sailing Yacht
System Modeling and Simulation

System Modeling and SimulationSystem modeling and simulation is a critical process that helps organizations to design, develop, and test complex systems before they are implemented. It involves creating a virtual model of the system and simulating its behavior under different conditions to identify potential issues and optimize its performance. The use of system modeling and simulation has become increasingly important in various industries, including aerospace, automotive, defense, healthcare, and manufacturing. In this response, I will discuss the importance of system modeling and simulation, its benefits, challenges, and future trends.First and foremost, system modeling and simulation help organizations to reduce the risk of failure and save costs. By creating a virtual model of the system, engineers can identify potential issues and optimize its performance before it is implemented. This helps to reduce the risk of failure and minimize the cost of rework. For example, in the aerospace industry, system modeling and simulation are used to test the performance of aircraft before they are built. This helps to identify potential issues and optimize the design, which can save millions of dollars in development costs.Secondly, system modeling and simulation help organizations to improve their decision-making process. By simulating the behavior of the system under different conditions, engineers can evaluate the impact of different design choices and make informed decisions. This helps to reduce the risk of making costly mistakes and ensures that the system meets the requirements of the stakeholders. For example, in the healthcare industry, system modeling and simulation are used to evaluate the impact of different treatment options on patients. This helps doctors to make informed decisions and provide the best possible care to their patients.Thirdly, system modeling and simulation help organizations to improve their productivity and efficiency. By simulating the behavior of the system, engineers can identify potential bottlenecks and optimize the system's performance. This helps to improve productivity and reduce the time and cost of production. For example, in the manufacturing industry, system modeling and simulation are used to optimize the production process and reduce the time and cost of production.However, there are also challenges associated with system modeling and simulation. One of the biggest challenges is the complexity of the systems being modeled. As systems become more complex, it becomes increasingly difficult to create an accurate model and simulate its behavior. This can lead to inaccurate results and increase the risk of failure. Another challenge is the availability of data. In order to create an accurate model, engineers need access to a large amount of data. However, in some cases, data may not be availableor may be difficult to obtain.Looking into the future, there are several trends that are likely to shape the future of system modeling and simulation. One of the trends is the use of artificial intelligence (AI) and machine learning (ML) to improve the accuracy of models. AI and ML can help to identify patterns in data and create more accurate models. Another trend is the use of cloud computing to improve the scalability and accessibility of system modeling and simulation. Cloud computing allows engineers to access powerful computing resources and collaborate with others in real-time.In conclusion, system modeling and simulation are critical processes that help organizations to design, develop, and test complex systems before they are implemented. They help to reduce the risk of failure, improve decision-making, and improve productivity and efficiency. However, there are also challenges associated with system modeling and simulation, such as the complexity of the systems being modeled and the availability of data. Looking into the future, there are several trends that are likely to shape the future of system modeling and simulation, including the use of AI and ML and cloud computing.。
实测数据与理论模型驱动的Adams-EDEM_耦合仿真挖掘阻力研究
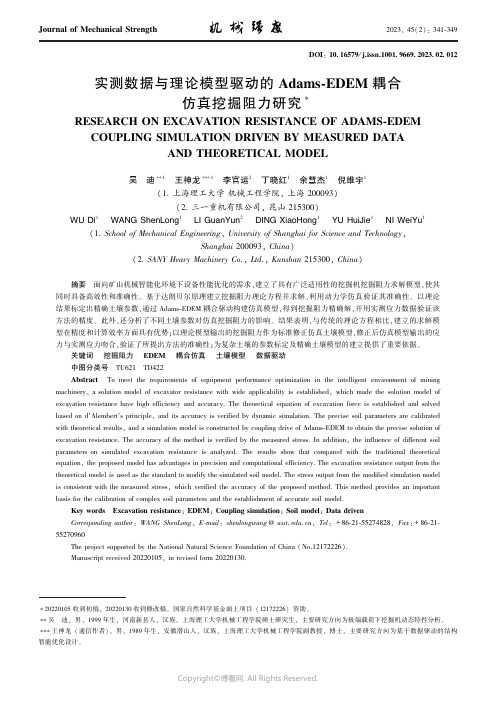
Journal of Mechanical Strength2023,45(2):341-349DOI :10.16579/j.issn.1001.9669.2023.02.012∗20220105收到初稿,20220130收到修改稿㊂国家自然科学基金面上项目(12172226)资助㊂∗∗吴㊀迪,男,1999年生,河南新县人,汉族,上海理工大学机械工程学院硕士研究生,主要研究方向为极端载荷下挖掘机动态特性分析㊂∗∗∗王神龙(通信作者),男,1989年生,安徽潜山人,汉族,上海理工大学机械工程学院副教授,博士,主要研究方向为基于数据驱动的结构智能优化设计㊂实测数据与理论模型驱动的Adams-EDEM 耦合仿真挖掘阻力研究∗RESEARCH ON EXCAVATION RESISTANCE OF ADAMS-EDEM COUPLING SIMULATION DRIVEN BY MEASURED DATAAND THEORETICAL MODEL吴㊀迪∗∗1㊀王神龙∗∗∗1㊀李官运2㊀丁晓红1㊀余慧杰1㊀倪维宇1(1.上海理工大学机械工程学院,上海200093)(2.三一重机有限公司,昆山215300)WU Di 1㊀WANG ShenLong 1㊀LI GuanYun 2㊀DING XiaoHong 1㊀YU HuiJie 1㊀NI WeiYu 1(1.School of Mechanical Engineering ,University of Shanghai for Science and Technology ,Shanghai 200093,China )(2.SANY Heavy Machinery Co.,Ltd.,Kunshan 215300,China )摘要㊀面向矿山机械智能化环境下设备性能优化的需求,建立了具有广泛适用性的挖掘机挖掘阻力求解模型,使其同时具备高效性和准确性㊂基于达朗贝尔原理建立挖掘阻力理论方程并求解,利用动力学仿真验证其准确性㊂以理论结果标定出精确土壤参数,通过Adams-EDEM 耦合驱动构建仿真模型,得到挖掘阻力精确解,并用实测应力数据验证该方法的精度㊂此外,还分析了不同土壤参数对仿真挖掘阻力的影响㊂结果表明,与传统的理论方程相比,建立的求解模型在精度和计算效率方面具有优势;以理论模型输出的挖掘阻力作为标准修正仿真土壤模型,修正后仿真模型输出的应力与实测应力吻合,验证了所提出方法的准确性;为复杂土壤的参数标定及精确土壤模型的建立提供了重要依据㊂关键词㊀挖掘阻力㊀EDEM㊀耦合仿真㊀土壤模型㊀数据驱动中图分类号㊀TU621㊀TD422Abstract ㊀To meet the requirements of equipment performance optimization in the intelligent environment of miningmachinery,a solution model of excavator resistance with wide applicability is established,which made the solution model of excavation resistance have high efficiency and accuracy.The theoretical equation of excavation force is established and solved based on dᶄAlembertᶄs principle,and its accuracy is verified by dynamic simulation.The precise soil parameters are calibratedwith theoretical results,and a simulation model is constructed by coupling drive of Adams-EDEM to obtain the precise solution of excavation resistance.The accuracy of the method is verified by the measured stress.In addition,the influence of different soil parameters on simulated excavation resistance is analyzed.The results show that compared with the traditional theoretical equation,the proposed model has advantages in precision and computational efficiency.The excavation resistance output from thetheoretical model is used as the standard to modify the simulated soil model.The stress output from the modified simulation model is consistent with the measured stress,which verified the accuracy of the proposed method.This method provides an important basis for the calibration of complex soil parameters and the establishment of accurate soil model.Key words㊀Excavation resistance ;EDEM ;Coupling simulation ;Soil model ;Data drivenCorresponding author :WANG ShenLong ,E-mail :shenlongwang @ ,Tel :+86-21-55274828,Fax :+86-21-55270960The project supported by the National Natural Science Foundation of China (No.12172226).Manuscript received 20220105,in revised form 20220130.㊀342㊀机㊀㊀械㊀㊀强㊀㊀度2023年㊀0㊀引言㊀㊀挖掘机作为基建中最主要的工程机械之一,其工作性能一直受到广泛关注㊂挖掘阻力计算是挖掘机结构设计与性能优化的基础,因此,建立具有广泛适用性的挖掘阻力求解模型具有重要的理论与实践意义㊂在实际工况中,挖掘阻力随时间变化存在随机性,难以直接测量[1]㊂目前挖掘阻力的获取方法主要分为三类:经验公式法㊁理论计算法和仿真分析法㊂经验公式法会抑制挖掘阻力的峰值,在复合挖掘工况中抑制效果尤为明显[2-4]㊂理论计算法的主要技术路线是对挖掘机铲斗㊁斗杆及整机列刚体平衡方程[5]㊂CHEN J等[6-7]将作用在铲斗上的挖掘阻力简化为斗齿尖端的切向力和法向力,推导出平衡方程并在一个周期内进行求解㊂REN Z G等[8]通过测量运动参数和缸压强度间接计算了正常状态下的挖掘阻力,推导了不完全挖掘阻力的测算方法㊂GODWIN R J等[9]推导出预测作用于齿上力的土壤力学方程,通过挖掘深度㊁土壤物理特性等参数计算出挖掘工具的垂向力㊂理论方法有实测数据支撑,计算简便,但其将动力学问题简化为静力学处理,会产生误差且无法反映极端工况,同时具有计算效率低下㊁普适性不强等缺点㊂随着计算机与仿真软件的快速发展,学者们试图用数字仿真的方法求解挖掘阻力㊂邱清盈等[10]建立了挖掘机铲斗挖掘土壤过程的有限元仿真模型,在LS-DYNA中通过数值模拟计算,求得整个挖掘过程的阻力载荷谱㊂毕秋实等[11]提出了基于离散元-多体动力学联合仿真的挖掘阻力数值模拟方法,使用挖掘阻力测试系统试验测量了同等挖掘条件下的阻力值㊂然而,由于仿真系统的多样性和仿真模型的不确定性[12],仿真方法得到的挖掘阻力结果差异性较大㊂为解决此问题,一些学者将理论与仿真的方法相互结合㊂例如,刘文国等[13]基于Adams动力学仿真对工作装置挖掘力进行了仿真测试,并与经验公式得到的结果对比验证;彭丽娜等[14]运用矢量力学方法,推导在任意姿态下的最大理论挖掘阻力计算公式,并借助Adams动力学仿真软件对动臂辅助液压缸长度取不同值进行仿真㊂理论与动力学仿真相结合的方法发展迅速,但由于实况中土壤系统复杂且模型参数难以测量,基于挖掘机-土壤模型的离散元仿真还少有能和理论方法紧密结合的㊂综上所述,本文针对现有问题,将挖掘机-土壤离散元模型㊁Adams动力学模型㊁理论挖掘阻力求解模型有机结合,提出一种多模型融合的挖掘阻力求解方法,弥补了理论方法普适性不足以及仿真中土壤建模不准㊀㊀确的缺陷㊂此外,以Adams-EDEM耦合方式驱动仿真模型,解决了仿真方法普遍存在的挖掘阻力计算低效的问题㊂最后,分析了土壤相关参数对挖掘阻力的影响,根据理论与仿真模型输出的挖掘阻力调整土壤参数,建立精确的土壤模型,用实测应力数据验证精确的土壤模型的准确性,为难以测量的土壤参数标定奠定了基础㊂1㊀挖掘阻力理论模型1.1㊀理论模型求解㊀㊀挖掘机整机模型由基座㊁动臂㊁斗杆㊁铲斗㊁油缸㊁连杆以及四杆机构组成㊂某25.5t型挖掘机几何模型如图1所示,该型号挖掘机最大挖掘阻力为175kN㊂所有实测数据采集装置如图2所示,其中油缸位移通过位移传感器获取,液压缸压力利用压力传感器采集,工作装置上各部位应力通过贴应变片及应变花的形式采集㊂选取连续作业中一个工作循环进行分析,挖掘循环时间历程曲线如图3所示,具体分为4个阶段: 0~3s为准备阶段,调整挖掘姿态到挖掘初始位置; 3~7s为挖掘阶段,动臂油缸不参与挖掘,主要由铲斗油缸挖掘;7~10s为提升阶段,动臂油缸收缩,其余油缸不动;10~14s为卸料阶段,动臂油缸保持不变,由斗杆及铲斗油缸完成卸料㊂选取油缸推力作为理论模型的输入,其计算式为F c=2(S c1P c1-S c2P c2)F d=(S d1P d1-S d2P d2)F e=(S e1P e1-S e2P e2)ìîíïïïï(1)式中,S c1㊁S c2㊁S d1㊁S d2㊁S e1和S e2分别为动臂㊁斗杆㊁铲斗油缸的大腔面积和小腔面积;P c1㊁P c2㊁P d1㊁P d2㊁P e1和P e2分别为动臂㊁斗杆㊁铲斗油缸的大腔压强和小腔压强㊂求解得油缸推力如图4所示㊂图1㊀挖掘机整机模型Fig.1㊀Model of excavator图4中动臂油缸推力为左㊁右两动臂油缸推力之和,最大油缸推力为600kN㊂理想状态下连接油缸两端的铰点受力等值反向,各部分受力情况如图5所示㊂利用达朗贝尔原理列平衡方程,主矢在水平方向投影为0,即㊀第45卷第2期吴㊀迪等:实测数据与理论模型驱动的Adams-EDEM 耦合仿真挖掘阻力研究343㊀㊀图2㊀数据采集装置Fig.2㊀Equipment of dataacquisition图3㊀油缸位移时间历程曲线Fig.3㊀Time history curves of cylinderdisplacement图4㊀动臂㊁斗杆及铲斗油缸推力Fig.4㊀Cylinder thrust of the boom,dipper andbucket图5㊀挖掘机动臂㊁斗杆和铲斗受力分析Fig.5㊀Force analysis of excavator boom,dipper and bucketF A x +F B x +F C x +F D x +F G2x=0-F B x -F D x +F L x +F Q x +F G3x =0-F Q x -F L x +F J x +F G4x=0ìîíïïïï(2)㊀㊀主矢在竖直方向投影为0,即F A y +F B y +F C y +F D y +F G2y=0-F B y -F D y +F L y +F Q y +F G3y =0-F Q y -F L y +F J y +F G4y=0ìîíïïïï(3)㊀㊀动臂㊁斗杆和铲斗力系分别简化到其质心G 2㊁G 3㊁G 4处,主矩为0,即F A x (Y G2-Y A )+F B x (Y G2-Y B )+F C x (Y G2-Y C )+㊀F D x (Y G2-Y D )-F A y (X G2-X A )-F B y (X G2-X B )-㊀F C y (X G2-X C )-F D y (X G2-X D )+M G2=0-F B x (Y G3-Y B )-F D x (Y G3-Y D )+F L x (Y G3-Y L )+㊀F Q x (Y G3-Y Q )+F B y (X G3-X B )+F D y (X G3-X D )-㊀F L y (X G3-X L )-F Q y (X G3-X Q )+M G3=0-F Q x (Y G4-Y Q )-F L x (Y G4-Y L )+F J x (Y G4-Y J )+㊀F Q y (X G4-X Q )+F L y (X G4-X L )-F J y (X G4-X J )+㊀M G4+M J =0(4)ìîíïïïïïïïïïïï式中,F G2㊁F G3㊁F G4㊁M G2㊁M G3㊁M G4分别为动臂㊁斗杆和铲斗的惯性力及惯性力矩;X k 和Y k 分别为在全局坐标系下,K 点的X 方向坐标和Y 方向坐标㊂设铲斗满载时土壤重量为m soil ,动臂㊁斗杆和铲斗的质量为m i ,绝对线性加速度为a i ,绝对角加速度为αi ,重力加速度为g ,转动惯量为J i ,则水平方向惯性力为F G i =-m i a i (5)㊀㊀竖直方向惯性力为F G i =-(m i +m soil )(a i +g )(6)㊀㊀惯性力矩为M G i =-J i αi(7)㊀㊀连杆和铲斗油缸成钝角时,连杆力为F L =F 油缸cos α-sin αtan θ(8)㊀㊀连杆和铲斗油缸成锐角时,连杆力为F L =F 油缸cos α+sin αtan θ(9)㊀㊀四杆机构的力为F N =F L cos θ(10)式中,α为四杆机构和铲斗油缸的锐夹角;θ为连杆与铲斗油缸垂线的锐夹角㊂联立式(1)~式(7),可得理论模型输出的挖掘阻力,如图6所示㊂图6表明,挖掘阶段主要受力在水平方向,当铲斗逐渐下挖并达到最大挖掘深度时,挖掘阻力达到最大值,且最大挖掘阻力不超过175kN㊂当铲斗离开土壤,挖掘阻力平缓下降㊂提升阶段主要受土壤重力的影响,此阶段挖掘阻力保持稳定直至开始卸料㊂此外,㊀344㊀机㊀㊀械㊀㊀强㊀㊀度2023年㊀图6㊀挖掘阻力理论计算结果Fig.6㊀Theoretical results of excavation resistance由于理论值通过油缸压力计算得出,且存在整机自重,因此油缸压力始终不为零,导致在未与土壤接触时仍存在挖掘阻力㊂图6中,铲斗卸料(12s)后挖掘阻力值仍不为零㊂1.2㊀理论模型验证㊀㊀本节通过动力学仿真对上述理论模型进行验证㊂对挖掘机模型添加约束㊁驱动㊁载荷以建立样机模型㊂其中约束为铰点转动及活塞移动;驱动为真实油缸位移编写的Spline函数;以经验公式得到的挖掘阻力切向㊁法向分力及土壤重力作为载荷输入㊂选取理论模型的输入力和输出力作为验证对象,输入力为油缸推力和连杆力,输出力为动臂与基座铰接处铰点力㊁斗杆与动臂铰接处铰点力,对比结果如图7所示㊂由图7可知,理论方法得到的铰点力与动力学仿真模型输出的铰点力趋势吻合度较高㊂然而,由于动力学仿真中的输入为经验公式所得的挖掘阻力,输出的铰点力明显低于实际值㊂图7c~图7e表明,整个工作周期中,四杆机构所受载荷远大于连杆所受载荷,因而该机构通常更有可能成为危险部位,与工程经验相符㊂此外,由于理论计算中所用数据的采集误差及动力学仿真中的模型不确定性,理论与仿真的部分铰点力存在偏差㊂2㊀Adams-EDEM耦合仿真㊀㊀基于上述理论结果,标定土壤参数以建立精确的土壤模型,分析土壤参数对仿真挖掘阻力的影响㊂本图7㊀理论与仿真铰点力对比Fig.7㊀Comparison of theoretical and simulation values of hinge forces㊀第45卷第2期吴㊀迪等:实测数据与理论模型驱动的Adams-EDEM 耦合仿真挖掘阻力研究345㊀㊀节采用离散元软件EDEM 进行仿真挖掘阻力求解,其基本思想是针对颗粒单元进行研究[15-16]㊂给定颗粒尺寸及物理性质,通过接触力模型求解接触力及力矩,依据动量定理及动量矩定理建立动力学方程,运用中心差分法求解,反复迭代即可得到整个系统的实时运动特征㊂本文所用接触力模型为Hertz-Mindlin 无滑动接触模型,具有高效的计算性能[17]㊂依据刚体动力学普遍定理,建立颗粒i 的运动方程m i u ㊆i=ðF I i θ㊆i=ðM{(11)式中,μ㊆和θ㊆i 分别为颗粒i 的加速度和角加速度;m i 和I i 分别为颗粒i 的质量和转动惯量;ðF 和ðM 分别为颗粒在质心处受到的合外力和合外力矩㊂对式(11)用中心差分法进行数值求解,选取两次迭代时间步长的中间点,得到新的迭代速度为u .i ()N +12=u .i ()N -12+ðF m i éëêêùûúúN Δt θ.i ()N +12=θ.i ()N -12+ðM I i éëêêùûúúN Δt ìîíïïïïïï(12)式中,Δt 是时间步长;N 对应时间t ㊂对式(12)进行积分,可得到关于位移的表达式为(u i )N +1=(u i )N +u i .()N +12Δt (θi )N +1=(θi )N +θi .()N +12Δt ìîíïïïï(13)㊀㊀由式(13)得出颗粒单元的新位移值,将其重新代入到式(11)计算出新的作用力,反复迭代即可求得每个颗粒在任意时刻的运动,从而实时分析系统的运动特征㊂2.1㊀初始土壤建模㊀㊀由于建立精确的土壤模型需要数据庞大的离散单元及难以测量的土壤参数(土壤密度ρ㊁剪切模量G ㊁颗粒之间的恢复系数e ㊁滚动摩擦因数C R ㊁静摩擦因数C S 等),建模困难,且仿真效率低下㊂因此,以40ʎ堆积角作为粗糙土壤模型建模的标准㊂堆积角与颗粒流动性相关,颗粒流动性越好,堆积角越小㊂颗粒的内摩擦力㊁黏聚力㊁堆积密度等均影响流动性㊂本节在土壤建模中采用的参数如表1所示,其中恢复系数㊁静摩擦因数和滚动摩擦因数是通过设定堆积角为40ʎ,用参数标定的方法得出㊂表1中,滚动摩擦因数主要用于补偿颗粒形状设置不准确造成的影响,其对物料的性能影响很小㊂静摩擦因数是主要的耗能机制之一,但对物料刚度的影响较小[18]㊂按照试验场地的土壤形状,以不同数量的球形单元最大限度还原土壤模型的形状,同时在保证精度的基础上增大单个颗粒模型的半径㊂颗粒模型如图8所示,图8a ~图8d 单个颗粒的半径分别为13.5mm㊁18mm㊁17mm 和10mm,其中小于10mm 的土壤颗粒均使用10mm 的单球模型㊂表1㊀EDEM 仿真中参数的设定Tab.1㊀Parameter setting in EDEM simulation 参数Parameter 符号Symbol取值Value 来源Origin 土壤密度Soil density /(kg /m 3)ρ3100标定Calibration 剪切模量Shear modulus /Pa G 1ˑ107文献[19]Ref.[19]颗-颗恢复系数Intergranular recoverycoefficient e 10.55标定Calibration 颗-颗静摩擦因数Intergranular static friction coefficient C S10.56标定Calibration 颗-颗滚动摩擦因数Intergranular rolling friction coefficient C R10.2标定Calibration 颗-斗恢复系数Recovery coefficient between particles and bucket e 20.5标定Calibration颗-斗静摩擦因数Static friction coefficient between particles and bucket C S20.7标定Calibration颗-斗滚动摩擦因数Rolling friction coefficientbetween particles and bucketC R20.15标定Calibration图8㊀颗粒单元建模Fig.8㊀Particle unit modeling2.2㊀仿真设置㊀㊀仿真设置分为三部分:离散单元仿真设置㊁动力学㊀346㊀机㊀㊀械㊀㊀强㊀㊀度2023年㊀仿真设置和耦合仿真设置,具体流程如图9所示㊂挖掘机模型材料按规定选取Q345,参数如表2所示㊂在离散元仿真设置中,选取时间步为20%,较大的时间步会导致颗粒相互渗透,土壤模型失稳㊂动力学仿真设置需在挖掘机样机模型中添加广义内力(GForce 函数)以控制外部耦合㊂图9㊀Adams-EDEM 耦合仿真流程图Fig.9㊀Flow chart of the Adams-EDEM coupling simulation表2㊀EDEM 仿真中挖掘机材料参数Tab.2㊀Material parameters of excavator in EDEM simulation 泊松比Poisson s ratio μ密度Density ρfe /(kg /m 3)弹性模量Elasticity modulus G fe /Pa 0.2978012.07ˑ1011耦合仿真的设置主要为对部分程序的修改,通过修改包含模型信息的模型语言Adm 文件和仿真控制语言ACF 文件,达到配合外部程序耦合求解的效果㊂耦合后的模型在离散元中求解,可得土壤和设备间力的关系,耦合仿真模型如图10所示㊂图10㊀Adams-EDEM 耦合仿真模型Fig.10㊀Model of Adams-EDEM coupling simulation2.3㊀土壤模型参数对挖掘阻力的影响特性分析㊀㊀针对上述土壤建模的难点,进行不同剪切模量㊁土壤密度㊁恢复系数及摩擦因数对仿真挖掘阻力的影响效应分析,如图11所示㊂其中,所选择的每组参数均可生成堆积角为40ʎ的土壤模型㊂图11a 表明,挖掘阶段,挖掘阻力随剪切模量的增加而增大;提升阶段,随剪切模量的增大而减小,且过大的剪切模量会导致仿真时颗粒互相渗透,引发模型失效;由图11b 和图11c 可知,挖掘阻力随土壤密度和颗粒间恢复系数的增加而增大,但土壤密度在整个阶段对挖掘阻力均有较大影响,恢复系数仅在挖掘阶段有影响,且影响较小;图11d 和图11e 表明,挖掘阻力与静摩擦因数成正比,与动摩擦因数成反比,但总体上摩擦因数对挖掘阻力影响较小㊂3㊀精确土壤模型㊀㊀分析土壤参数对仿真挖掘阻力的影响特性可知,离散元仿真挖掘阻力只能得到近似趋势㊂为得到与实际更贴近的结果,需基于上述分析结果对土壤参数做修正,建立精确的土壤模型㊂选择理论模型输出的挖掘阻力作为基准,修正土壤模型参数:G =4ˑ107Pa,ρ=4000kg /m 3,颗粒间恢复系数㊁静摩擦因数㊁滚动摩擦因数分别为0.55㊁0.56和0.2㊂3.1㊀理论与仿真挖掘阻力对比㊀㊀将精确的土壤参数代入仿真模型中,重新计算挖掘阻力,可得到与理论模型较为一致的结果,如图12所示㊂基于理论计算结果,仿真模型的土壤剪切模量不宜取大值㊂此外,在挖掘阶段铲斗主要受与土壤的摩擦力及破坏颗粒的剪切力,但由于EDEM 仿真是基㊀第45卷第2期吴㊀迪等:实测数据与理论模型驱动的Adams-EDEM 耦合仿真挖掘阻力研究347㊀㊀㊀㊀图11㊀不同参数对挖掘阻力的影响Fig.11㊀Influence of parameters on excavationresistance图12㊀理论与仿真挖掘阻力对比Fig.12㊀Comparison of theoretical and simulationexcavation resistance于球单元建模,土壤模型流动性强,导致理论与仿真挖掘阻力存在偏差㊂图12显示,理论与仿真结果趋势基本一致,可通过调整土壤模型密度或修改离散元接触力模型进一步精确结果㊂此外,基于理论与仿真挖掘阻力对比的土壤模型参数获取方法,可辅助标定出实际中难以得到的土壤参数㊂3.2㊀仿真与实测应力对比㊀㊀用精确土壤模型输出的仿真挖掘阻力替换由经验公式所得到的载荷,对比仿真应力和实测应力,其中,实测应力选取部位均为故障点或焊缝附近,如图13所示㊂通过应变花采集数据,除2号部位应变花在回转过程中失效,其余实测应力均属合理数据,应力对比结果如图14所示㊂图13㊀实测应力部位示意图Fig.13㊀Schematic diagram of measured stress positions实际挖掘中,8~10s 属于回转提升阶段,但挖掘阻力的仿真模型仅在二维平面内求解,并未涉及到回转运动,因此该阶段仿真与实测应力值存在误差㊂此外,仿真模型输出的挖掘阻力经过小波分解处理,将得到的趋势项编写成step 函数,一定程度上抑制了仿真应力的波动,同时也产生了误差㊂由图14可知,1号㊁2号和5号部位的最大应力值约为60MPa,此时仿真和实测应力的趋势一致性较高;3号和6号部位实测应力在20MPa 左右,略小于理想状态下的仿真应力㊂㊀348㊀机㊀㊀械㊀㊀强㊀㊀度2023年㊀图14㊀动力学仿真与实测应力对比Fig.14㊀Comparison between dynamic simulation and measured stresses 4㊀结论㊀㊀本文针对建立具有广泛适用性的挖掘阻力模型难题,基于实测数据与理论模型驱动的Adams-EDEM耦合仿真,提出了一种高效㊁准确的挖掘阻力计算方法㊂对挖掘机的静态特征和动力学特征进行分析,结合土壤特性及离散元模型,研究了不同土壤参数对挖掘阻力的影响效应,并依据挖掘阻力理论模型及实测应力建立精确的土壤模型,得出主要结论如下:1)挖掘阻力理论模型可反应挖掘机铲斗阻力的变化趋势,但无法得到系统参数对结果的影响㊂由于挖掘阻力不具备严格意义上的周期特性,因此要得到多周期的挖掘阻力,仅依靠理论模型的计算效率低下㊂2)基于离散元的挖掘阻力仿真研究要求具备精确的土壤模型㊂根据理论与仿真模型挖掘阻力的一致性调整土壤参数以建立精确的土壤模型,以实测应力数据作为标准验证,可得到更精确的结果,同时可广泛适用于多种复杂的工况㊂此外,这也为土壤模型参数标定奠定基础㊂3)将理论模型与基于Adams-EDEM耦合仿真的离散元法相结合,求解得到的挖掘阻力可直观反应多工况下挖掘阻力特性,在未来挖掘阻力研究中,该方法具有更高效㊁直观且准确的优势㊂本文主要以干燥土方和常规挖掘工况为研究对象,对复杂土壤环境和极端工况下的挖掘阻力研究尚未涉及,这将会是后续工作的重点㊂参考文献(References)[1]㊀陈㊀进,李维波,张石强,等.大型矿用正铲液压挖掘机挖掘阻力试验研究[J].中国机械工程,2008(5):518-521.CHEN Jin,LI WeiBo,ZHANG ShiQiang,et al.Experimentalresearch on digging resistance for large hydraulic face-shovel[J].China Mechanical Engineering,2008(5):518-521(In Chinese).[2]㊀穆晓鹏,权㊀龙,程㊀珩,等.矿用电铲整机运行特性联合仿真研究[J].机械设计与制造,2021(5):8-13.MU XiaoPeng,QUAN Long,CHENG Heng,et al.Co-simulationresearch on operation characteristics of mining electric shovel[J].Machinery Design&Manufacture,2021(5):8-13(In Chinese).[3]㊀郎冲冲,徐路路,潘吴建,等.三七种苗仿生挖掘铲设计与有限元分析[J].中国农机化学报,2020(9):82-88.LANG ChongChong,XU LuLu,PAN WuJian,et al.Design andfinite element analysis of panax notoginseng seedlings bionic diggingshovel[J].Journal of Chinese Agricultural Mechanization,2020(9):82-88(In Chinese).[4]㊀任志贵,孙浩然,王军利,等.基于不同工作载荷的铲斗结构特性分析[J].机电工程,2020,37(3):247-252.REN ZhiGui,SUN HaoRan,WANG JunLi,et al.Analysis of bucketstructure characteristics based on different working loads[J].Journalof Mechanical&Electrical Engineering,2020,37(3):247-252(InChinese).㊀第45卷第2期吴㊀迪等:实测数据与理论模型驱动的Adams-EDEM耦合仿真挖掘阻力研究349㊀㊀[5]㊀刘广军,刘可臻,孙㊀波,等.基于刚-柔耦合的反铲液压挖掘机工作装置多体动力学分析与仿真[J].同济大学学报(自然科学版),2021,49(7):1053-1060.LIU GuangJun,LIU KeZhen,SUN Bo,et al.Multi-body dynamicanalysis and simulation of backhoe hydraulic excavator workingdevice based on rigid-flexible coupling[J].Journal of TongjiUniversity(Natural Science),2021,49(7):1053-1060(InChinese).[6]㊀CHEN J,ZOU Z H,PANG X P.S digging performancecharacterization for hydraulic excavator considering uncertaintyduring digging operation[J].Proceedings of the Institution ofMechanical Engineers,Part C:Journal of Mechanical EngineeringScience,2018,232(5):857-871.[7]㊀陈㊀进,任志贵,庞晓平,等.液压挖掘机挖掘力计算新方法[J].同济大学学报(自然科学版),2014,42(4):596-603.CHEN Jin,REN ZhiGui,PANG XiaoPing,et al.Novel diggingforce calculation method for hydraulic excavator[J].Journal ofTongji University(Natural Science),2014,42(4):596-603(InChinese).[8]㊀REN Z G,WANG J L,CHEN J.Active-side calculation method fora backhoe hydraulic excavator with incomplete digging resistance in anormal state[J].Mathematical Problems in Engineering,2019:1-13.[9]㊀GODWIN R J,OᶄDOGHERTY M J.Integrated soil tillage forceprediction models[J].Journal of Terramechanics,2007,44(1):3-14.[10]㊀邱清盈,魏振凯,高㊀宇,等.挖掘机工作装置疲劳分析方法[J].吉林大学学报(工学版),2016,46(1):159-165.QIU QingYing,WEI ZhenKai,GAO Yu,et al.Fatigue analysismethod of working devices of hydraulic excavator[J].Journal of JilinUniversity(Engineering and Technology Edition),2016,46(1):159-165(In Chinese).[11]㊀毕秋实,王国强,陈立军,等.基于离散元-多体动力学联合仿真的机械式挖掘机挖掘阻力仿真与试验[J].吉林大学学报(工学版),2019,49(1):106-116.BI QiuShi,WANG GuoQiang,CHEN LiJun,et al.Numericalsimulation and experiment on excavation resistance of mechanicalexcavator based on DEM-MBD co-simulation[J].Journal of JilinUniversity(Engineering and Technology Edition),2019,49(1):106-116(In Chinese).[12]㊀刘㊀征,陈谊超,丁华锋.一种新型矿用正铲液压挖掘机的运动学分析[J].机械工程学报,2014,50(15):28-33.LIU Zheng,CHEN YiChao,DING HuaFeng.Kinematics analysis ofa new hydraulic face-shovel excavator in mining[J].Journal ofMechanical Engineering,2014,50(15):28-33(In Chinese).[13]㊀刘文国,周宏兵,吴伟胜,等.挖掘机工作装置挖掘力及铰点受力仿真分析[J].机械科学与技术,2015(10):1482-1487.LIU WenGuo,ZHOU HongBing,WU WeiSheng,et al.Simulationanalysis of digging force and force acted on hinged joints of workingdevice for excavator[J].Mechanical Science and Technology forAerospace Engineering,2015(10):1482-1487(In Chinese). [14]㊀彭丽娜,史青录,贾旭峰,等.三节臂轮式液压挖掘机整机理论挖掘力分析[J].矿山机械,2021,49(3):13-18.PENG LiNa,SHI QingLu,JIA XuFeng,et al.Analysis ontheoretical excavation force of three-arm wheeled hydraulic excavator[J].Mining&Processing Equipment,2021,49(3):13-18(InChinese).[15]㊀胡国明.颗粒系统的离散元素法分析仿真[M].武汉:武汉理工大学出版社,2010:7-20.HU GuoMing.Analysis and simulation of particle system by discreteelement method[M].Wuhan:Wuhan University of TechnologyPress,2010:7-20(In Chinese).[16]㊀王国强.离散单元法及其在EDEM上的实践[M].西安:西北工业大学出版社,2010:14-33.WANG GuoQiang.Discrete element method and its practice inEDEM[M].Xiᶄan:Northwestern Polytechnical University Press,2010:14-33(In Chinese).[17]㊀FAVIER J.Industrial application of DEM:Opportunities andchallenges[R].Proceedings of Discrete Element Methods(DEM),UK,2007:7.[18]㊀AJMAL M,ROESSLER T,RICHTER C.Calibration of cohesiveDEM parameters under rapid flow conditions and low consolidationstresses[J].Power Technology,2020(374):22-32. [19]㊀张大鹏,雷勇军,段静波,等.土壤参数对返回舱着陆冲击特性的影响分析[J].振动与冲击,2014,33(7):120-125.ZHANG DaPeng,LEI YongJun,DUAN JingBo,et al.Impactanalysis of soil parameters on space capsuleᶄs impact characteristic[J].Journal of Vibration and Shock,2014,33(7):120-125(InChinese).。
Modelling, simulation and experimental investigation
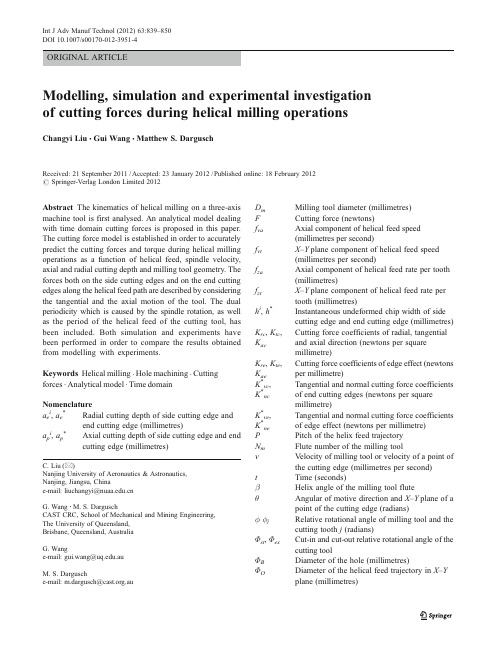
ORIGINAL ARTICLEModelling,simulation and experimental investigation of cutting forces during helical milling operationsChangyi Liu &Gui Wang &Matthew S.DarguschReceived:21September 2011/Accepted:23January 2012/Published online:18February 2012#Springer-Verlag London Limited 2012Abstract The kinematics of helical milling on a three-axis machine tool is first analysed.An analytical model dealing with time domain cutting forces is proposed in this paper.The cutting force model is established in order to accurately predict the cutting forces and torque during helical milling operations as a function of helical feed,spindle velocity,axial and radial cutting depth and milling tool geometry.The forces both on the side cutting edges and on the end cutting edges along the helical feed path are described by considering the tangential and the axial motion of the tool.The dual periodicity which is caused by the spindle rotation,as well as the period of the helical feed of the cutting tool,has been included.Both simulation and experiments have been performed in order to compare the results obtained from modelling with experiments.Keywords Helical milling .Hole machining .Cutting forces .Analytical model .Time domainNomenclature a e i ,a e *Radial cutting depth of side cutting edge andend cutting edge (millimetres)a p i ,a p *Axial cutting depth of side cutting edge and endcutting edge (millimetres)D m Milling tool diameter (millimetres)F Cutting force (newtons)f va Axial component of helical feed speed (millimetres per second)f vt X –Y plane component of helical feed speed (millimetres per second)f za Axial component of helical feed rate per tooth (millimetres)f zt X –Y plane component of helical feed rate per tooth (millimetres)h i ,h *Instantaneous undeformed chip width of side cutting edge and end cutting edge (millimetres)K rc ,K tc ,K ac Cutting force coefficients of radial,tangential and axial direction (newtons per square millimetre)K re ,K te ,K ae Cutting force coefficients of edge effect (newtons per millimetre)K *vc ,K *nc Tangential and normal cutting force coefficients of end cutting edges (newtons per square millimetre)K *ve ,K *ne Tangential and normal cutting force coefficients of edge effect (newtons per millimetre)P Pitch of the helix feed trajectory N m Flute number of the milling toolv Velocity of milling tool or velocity of a point of the cutting edge (millimetres per second)t Time (seconds)βHelix angle of the milling tool fluteθAngular of motive direction and X –Y plane of a point of the cutting edge (radians)ϕϕj Relative rotational angle of milling tool and the cutting tooth j (radians)Φst ,Φex Cut-in and cut-out relative rotational angle of the cutting toolΦB Diameter of the hole (millimetres)ΦODiameter of the helical feed trajectory in X –Y plane (millimetres)C.Liu (*)Nanjing University of Aeronautics &Astronautics,Nanjing,Jiangsu,Chinae-mail:liuchangyi@G.Wang :M.S.DarguschCAST CRC,School of Mechanical and Mining Engineering,The University of Queensland,Brisbane,Queensland,Australia G.Wange-mail:gui.wang@.au M.S.Dargusche-mail:m.dargusch@.auInt J Adv Manuf Technol (2012)63:839–850DOI 10.1007/s00170-012-3951-4ΩSpindle rotating angular velocity(radians per second)Ωh Helix feed rotating angular velocity(radians per second)1IntroductionHelical milling has been applied to generate boreholes by means of a milling tool to some difficult-to-cut materials. This innovative method was found to facilitate hole making in AISI D2tool steel in its hardened state,resulting in an enhancement in cutting tool life and the ability to machine H7quality holes with a surface finish of0.3μm Ra[1].The operation has also been applied to hole making in composite-metal compounds as a substitute for drilling operations.The impact of the axial and tangential feed per tooth on the process forces[2]has been investigated. Employing helical milling to aluminium with minimum quantity lubrication has shown an improvement in geometri-cal accuracy and a reduction in burr formation,lower cutting temperature and a smaller cutting force compared to drilling operations[3].The prediction of cutting force through modelling and simulation is an important research area in order to improve process ling is the most complex machining operation.Previously in the literature,machining mechanisms have been derived from a general model[4,5]and applied to the specific application,for example,five-axis milling, three-axis milling,peripheral milling,face milling and plunge milling.Modelling peripheral milling is a fundamental requirement in order to model more complex milling operations.A theoretical model based on the oblique cutting principle and cutting force coefficients has been developed in order to predict the cutting forces during peripheral milling[6–8].Considering the helical flute(or side cutting edge)of the milling cutters,an attempt to accurately simulate milling forces including the effects of engaged flute length and the number of engaged flutes caused by the radial and axial depths of cut has been previously presented[9].A common approach to facilitate the modelling of this complex situation including the milling tool geometry and the interaction with the workpiece involves analysing the cutting forces on axial discrete milling tools,then integrating these force elements.The intersection of the tool path swept envelope with the workpiece Z-buffer elements has been used to find the contact area between the cutter and the workpiece. An axial slice cutting tool discrete mechanistic model was used to estimate the cutting force vectors[10].Cutter entry and exit angles,along with the immersion angles,were used as boundary conditions in order to predict cutting forces when flank milling ruled surfaces with tapered,helical and ball end mills[11].The effect of lead and tilt angles between the cutter and the workpiece on the milling forces,tool deflections and form errors during multi-axis end milling have been analysed[12,13].During modelling of the cutting forces and system dynamics,one of the outstanding characteristics is that both side cutting edges and end cutting edges interact with the workpiece during helical milling processing.An accurate predictive model should describe and sum up the mechanics on both edges simultaneously.Ball end milling tools are most often used in three-axis or five-axis milling.Ball end milling tool processing models have been separated into ball end and cylindrical sections in order to obtain accurate prediction[10,14,15].A mechanistic force model describing the cutting force as a sum of the cutting and edge forces has been developed for a general end milling cutter(cylindrical,taper,ball,bull nose)with the specific cutting and edge force coefficients identified[16].As one type of three-axis milling operation,axial feed is a typical characteristic of helical milling operations. This operation uses a flat end mill not a ball end mill that is used in typical3-axis and5-axis milling situations.Axial feed using a flat end mill is also applied in plunge milling which is a two-axis operation.Considering rigid body motion of the cutter,the cutting force model and dynamics model for the plunge milling process in the time domain have been established[17,18].The cutting forces associated with plunge milling operations are predicted by considering the feed,radial engagement,tool geometry,spindle speed and the regenera-tion of the chip load due to vibrations[19].Considering the flexibility of the workpiece,tool setting errors and tool kine-matics and geometry,a horizontal approach was used to compute the chip area including the contribution of the main and side edge in the cutting zone[20].Drilling operations and boring operations typically involve axial feed.Both these operations are similar to helical milling and plunge milling operations but with different cutting tools.The drilling cutting forces and dynamics have been integrated into the model in order to obtain drilled hole profiles[21].A mechanistic model for predicting thrust force and torque during the drilling process using a drill tool with double-point angle edges [22].To predict temperatures and forces on both the drilling and ball end milling operations,the cutting edges of the twist drill lip and the ball end mill were divided into oblique cutting elements[23].A theoretical model to predict thrust and torque in high-speed drilling has been presented[24,25].The methodology for extracting cutting force coefficients for drilling operations has also been investigated[26].When modelling the drilling process, the axial feed effect was not considered explicitly because the lip of the twist drill has a taper angle(point angle),and the interaction between the lip and workpiece caused by spindle rotation could lead to a spontaneous axial force(thrust).In the literature,helical milling has been introduced as an enabling technology to substitute for drilling operations [1–3].In recent years,research on modelling the mechanics of the helical milling process has been published [27,28].Although both the side cutting edges and the end cutting edges have been considered to participate in the machining process,the detail interaction between the end cutting edges and workpiece still needs more elaborate investigation and description.Modelling,simulation and experimental investigation during cutting forces of the helical milling operation will be discussed in this paper including the influence of helical feed.This research aims to develop an analytical cutting force model in the time domain including both the axial cutting depth and the radial cutting depth associated with helical milling operations.The model considers the effects of both the tangential feed and axial feed,and the combination of both mechanics on the side cutting edges and the end cutting edges.2Kinematics of helical millingIn helical milling,the trajectory of a point on the milling toolcutting edge is the result of the spiral curve movement of the axis of the tool (reference frame)and the circular movement of the edge point relative to the axis (relative motion).Two sets of coordinates are defined to describe the motion of the cutter and the cutting force on the cutter;an X,Y ,Z global coordinate frame fixed to the workpiece and an x,y,z local coordinate frame fixed to the cutting tool with the origin at the centre of the end flat surface which defines the reference frame.A description of helical milling with tool feed using helical trajectory and the coordinate settings are depicted inFig.1.The feed motion of the tool is decomposed into two components,f va and f vt .f vt ¼ΦB ÀD m ðÞΩh 2¼N m Ωf zt2p mm =s ðÞð1Þf va ¼P Ωh 2p ¼N m Ωf za 2pmm =s ðÞð2ÞThe flat-end cylinder milling tools suitable for helical milling operations have two types of cutting edges:the side cutting edge (peripheral cutting edge)and the end cutting edge through the centre.The interaction characteristics of these two types with the workpiece are different.The side edges participate in the peripheral cutting component,while the end edges participate in the plunge cutting component.Therefore,these two movements will be initially analysed separately before being assembled or composed.The side edge cutting process is typical intermittent cutting.The undeformed chip geometry,width,depth,and thickness have been described in the literature [2].The side edge cutting process that is typical intermittent cutting is depicted in Fig.2(using superscript i ).The velocity composition of an arbitrary point on the side cutting edge is described in cross section perpendicular to the tool axis.The undeformed chip geometry can be described as a i e ¼D m ;hole generating ΦB ÀΦO2;hole enlarging&ð3Þa i p ðt Þ¼f va t ;t 2p =Ωh P ;t >2p =Ωh&ð4Þh i ¼f zt sin fð5ÞFig.1Kinematics of helical millingwhere ϕ¼2p ΩÆΩh ðÞt is the relative rotational angle of the cutter (+up milling,−down milling).The end edge cutting process,which is continuous cutting,is depicted in Fig.3(using superscript *).The velocity composition of an arbitrary point on the end cutting edge is described in the cross section perpendicular to the end cutting edge.The undeformed chip geometry,width and height can be described as:a Ãe ¼D m ;hole making ΦB ÀΦO 2;hole enlarging &ð6Þh üf za cos θð7Þ3Cutting force model for helical milling 3.1Cutter feed influence on the cutting forcesThe influence of cutter feed movement on the cutting forces during machining processing is almost always neglected.Similar to spindle rotation resulting in the relative movement between cutter and workpiece,cutter feed motion leads to relative movement also.This relative movement between the cutter and workpiece could influence the directionand magnitude of the cutting forces.The premise that the influence of the feed can be neglected is based on the assumption that the relative displacement and velocity from spindle rotation are much larger than the feed.Thus,in most situations,the influence of feed is insignificant and can be ignored.However,when modelling some specific machining operations including axial feed,such as drilling,plunge milling and helical milling,to ignore the feed motion is unreasonable.If the axial feed effect is not considered,the cutting force along the axial direction might not be expressed accurately.For this reason,analysis of the influence of axial feed on cutting forces when modelling helical milling operations is necessary.In this paper,the feed motion effect on cutting forces has been analysed completely.Firstly,the movement of an arbitrary point P at the side cutting edge could be decomposed to cylinder helical move-ment (reference movement)and circular movement perpen-dicular to the cutter axis,as depicted in Fig.1.The reference movement can be decomposed to horizontal tangential feed and perpendicular axial feed,shown in Fig.2.The horizon-tal velocity of point P is defined as v P 0v PO +v O ,where v O is identical to f vt .For Ω>>Ωh ,means |v PO |>>|v O |,and therefore,v P ≈v PO .The influence of horizontal tangential feed on the side edge cutting force can beignored.Fig.2Kinematics of the side cuttingedgeFig.3Kinemics of the end cutting edgeSecondly,axial feed f vz may result in a portion of the axial cutting force being on the side edge.For every axial feed,the cutting volume of the side edge is proportional to f za a e h i ,but the cutting volume of the end edge is proportional to f za a e p ΦB ÀD m ðÞ=sin θ.That means that the side edge undergoes intermittent cutting while the end edge undergoes continuous cutting.In the same time period,the cutting force derived from axial feed on the side edge is much smaller than that on the end side.So,the influence of axial feed on the side edge cutting force can also be ignored.Then,assuming the top points on an end cutting edge in a straight line,the radial distance of point P to the cutting axis is variable.The influence of the horizontal feed f vt is more outstanding when P is near to the axis.The horizontal movement of point P at the end edge can be decomposed into the relative tangential part v t and relative radial part v r ,as described in pared to drilling or plunge milling operations in which tangential cutting forces are vanished andtangential velocity of the z -axis is zero,tangential forces and axis tangential velocity of the helical milling are not zero,as depicted in Fig.4.For the aforementioned reason,the influence of horizontal tangential feed on end edge cutting forces can be ignored.The existence of the relative radial part v r of the end edge implies that the radial force also exists.If we consider the end cutting edge of the flat-end milling cutter as approximately a straight line,the cutting edge along the radial direction slides rather than shears.F r *should be the friction force that is smaller than the shear force.Therefore,the radial force onthe end edge can be neglected,or F Ãa ¼0.Finally,due to the axial feed associated with f va ,the dis-placement direction of the end edge is not horizontal but having an angle θrelative to f va and f vz .After calculating this angle,the actual direction of the machined surface,the variation of the rake angle and the clearance angle can be defined.The cutting force on the end edge derived from axial feed can be defined within the plane to which the machined surface belongs.3.2Side cutting edgeBased on the kinematics of the helical milling process,two new features that may influence the cutting force and dynamics of the helical milling process have been considered.One was the periodic force variation created by the circular or tangential feed of the tool,and the other is the additional force component generated by the axial feed of the tools.The axial feed force mostly occurs at the end cutting edge of the milling tools.The interaction conditions between the tool and the workpiece are the combination of side edge cutting forces and end edge cutting forces.F !¼F !i þF!Ãð8ÞWhere,F !i is the side cutting edge component and F !Ãis end cutting edge component.Considering a point P on the (jth)Fig.4Horizontal feed influence to forces on end cuttingedgesFig.5Cutting forces on the side cutting edgecutting tooth,shown in Fig.5,the integration cutting force F !i(defined in the local coordinate system)along the in-cut por-tion of the flute j is similar to that presented in the referenced literature [4].F i x ;jϕj ðz ÞÀÁ¼f zt 4k b ÀK tc cos2ϕj ðz ÞþK rc 2ϕj ðz ÞÀsin2ϕj ðz ÞÀÁÂÃþ1k b K te sin ϕj ðz ÞÀK re cos ϕj ðz ÞÂÃ&'ϕj ;z z j ;1ðÞϕj ;z z j ;1ðÞð9ÞF iy ;j ϕj ðz ÞÀÁ¼Àf zt 4k b K tc 2ϕj ðz ÞÀsin2ϕj ðz ÞÀÁþK rc cos2ϕj ðz ÞÂÃþ1k b K te cos ϕj ðz ÞþK re sin ϕj ðz ÞÂÃ&'ϕj ;z z j ;1ðÞϕj ;z z j ;1ðÞð10ÞF iz ;jϕj ðz ÞÀÁ¼1k bK ac f zt cos ϕj ðz ÞþK ae ϕj ðz ÞÂÃϕj ;z z j ;1ðÞϕj ;z zj ;1ðÞð11Þwhere k b ¼2tan b D m=The detail of the integration of these forces is complicated because the contours of the side edge of the generic milling cutter are helical circles.To get the details of the forces at an arbitrary time,the integration procedure at one period (e.g.from zero to 2π)of the forces on the discrete cutter has to beFig.6Different intervals of a cutting period.a a p >Φex ÀΦst ðÞ=k b ,b a p <Φex ÀΦst ðÞ=k bFig.7Cutting forces on theend cutting edgedivided into several time intervals,as shown in Fig.6.The oblique lines represent the unfolding of the milling tool flutes in a plane.If a p >Φex ÀΦst ðÞ=k b is as shown in Fig.6a ,axial cutting depth is large.Φst and Φex is the cut-in and cut-out relative rotational angle of the cutter,respectively.0.0050.010.0150.020.0250.030.035−1,500−7500750bTime (sec)F o r c e (N )0.0050.010.0150.020.0250.030.035−1,500−75007501500Time (sec)F o r c e (N )Cutting force of Side edge No. 20.0050.010.0150.020.0250.030.035−1,500−75007501,500Time (sec)F o r c e (N )Result Cutting force of Side edges−4000−2000020004000Time (sec)F o r c e (N )Cutting force of End edge No. 1−4000−2000020004000Time (sec)F o r c e (N )Cutting force of End edge No. 20.0050.010.0150.020.0250.030.035−20000200040006000Time (sec)F o r c e (N )Result Cutting force of End edgesFig.8Simulation of the cutting forces during helical milling (milling tool diameter D m 16mm,five flutes,cutting speed v c 100m/min,axial feed rate per tooth f za 0.2mm,tangential feed rate per tooth f zt 0.5mm,radial cutting depth a e 8mm,up milling)In intervals 1and 5,there are no interactions between the cutter and workpiece,and therefore,the cuttingforce 0 ϕj <Φst ;F !j ¼0;Φq ϕj <2p ;F !j ¼0During interval 2,the cutting tooth begins to cut into the workpiece,where Φst ϕj <Φex ;ϕj z 1ðÞ¼ϕj ;ϕj z 2ðÞ¼ΦstDuring interval 3,the cutting tooth is fully involved in cutting the workpiece until the maximum axial cutting depth a p ,where Φex ϕj <Φp ;ϕj z 1ðÞ¼Φex ;ϕj z 2ðÞ¼Φst is obtained.During interval 4,the cutting tooth completes the cutting and quits the interaction finally,where Φp ϕj <Φq ;ϕj z 1ðÞ¼Φex ;ϕj z 2ðÞ¼ϕj ÀΦp ÀΦst ðÞIf a p <Φex ÀΦst ðÞ=k b as shown in Fig.6b ,axial cutting depth is large.In interval 1and 5,there is no interaction between the cutter and workpiece,and therefore no cutting force.0 ϕj <Φst ;F !j ¼0;Φq ϕj <2p ;F !j ¼0During interval 2,the cutting tooth begins to cut into the workpiece and progress towards the maximum axial cutting depth a p ,where Φst ϕj <Φp ;ϕj z 1ðÞ¼ϕj ;ϕj z 2ðÞ¼ΦstDuring interval 3,the cutting tooth interacts with the workpiece with a p ,where Φp ϕj <Φex ;ϕj z 1ðÞ¼ϕj ;ϕj z 2ðÞ¼ϕj ÀΦp ÀΦst ðÞDuring interval 4,the cutting tooth completes the cutting operation and quits the interaction finally,where Φex ϕj <Φq ;ϕj z 1ðÞ¼Φex ;ϕj z 2ðÞ¼ϕj ÀΦp ÀΦst ðÞ3.3End cutting edgeSince both the tangential feed f vt and axial feed f va are present during helical milling,the end cutting edge force component and the edge of these teeth are assumed to be a straight line and coincide with the radial line during analysis.If the friction force is neglected along the endcutting edge,the radial force F Ãa ¼0.As shown in Fig.7,the end cutting edge force component can be represented asd F Ãv¼K Ãvc f za cos θd r þK Ãve d r ð12Þd F Ãn ¼K Ãnc f za cos θd r þK Ãne d rð13Þd F Ãt ¼d F Ãv cos θÀd F Ãn sin θð14Þd F Ãa¼d F Ãv sin θþd F Ãn cos θð15Þd T ür d F Ãt ð16Þ00.0050.010.0150.020.0250.030.035−5000Time (sec)F o r c e (N )00.0050.010.0150.020.0250.030.035−50005000Time (sec)F o r c e (N )Cutting force of cutting edge No. 20.0050.010.0150.020.0250.030.035−20000200040006000Time (sec)F o r c e (N )Result Cutting force of milling toolFig.8(continued)Denote A ¼N m f za 2p ,B ¼N m f zt cos ϕj 2p ,θ¼argtan v av t¼argtan A r þB ,Θ½ ¼R D m 2D m 2Àa eÃd r cos θÀsin θ0sin θcos θ0000r cos θÀr sin θ026643775;K ý ¼K Ãvc K Ãve K ÃncK Ãne K ÃrcK Ãre2435,therefore,F Ãt ;j F Ãa ;jF Ãr ;j T Ãj8>><>>:9>>=>>;¼Θ½ K ý f za 1&'ð17ÞTransform to the local coordinate,F Ãx ;j F Ãy ;j F Ãz ;j T Ãj 8>><>>:9>>=>>;¼ÀF Ãt ;j cos ϕj ðt ÞÀÁF Ãt ;j sin ϕj ðt ÞÀÁF Ãa ;j T Ãj8>><>>:9>>=>>;ð18ÞSum up side cutting edge forces and end cutting forces onthe j th tooth and convert to global coordinates.F x ;j F Y ;j F Z ;j T Z ;j 8>><>>:9>>=>>;¼cos Ωh t sin Ωh t00Àsin Ωh tcos Ωh t 0000100126643775F i x ;j þF Ãx ;j F i y ;j þF Ãy ;j F i z ;j þF Ãz ;j T Ãj8>><>>:9>>=>>;ð19ÞThen,sum up all the cutting forces on the cutting teeth toobtain the cutting force model.246810−400400Time (sec)F o r c e (N )Experimental Cutting Force of X directionab246810−400400Time (sec)F o r c e (N )Experimental Cutting Force of Y direction0200400Time (sec)F o r c e (N )Experimental Cutting Force of Z direction−4000400Time (sec)F o r c e (N )Simulate Cutting Force of X direction246810−4000400Time (sec)F o r c e (N )Simulate Cutting Force of Y direction0200400Time (sec)F o r c e (N )Simulate Cutting Force of Z directionFig.9Cutting force result from experiment and simulation during helical milling cutting (milling tool M.A.Ford 20-mm five-flute end mill 17878703A,cutting speed v c 100m/min,axial feed rate per toothf za 0.005mm,tangential feed rate per tooth f zt 0.1mm,radial cutting depth a e 1mm,down milling)12345678x 10−3−300−200−100100200300400Time (sec)F o r c e (N )Experimental cutting force of single tooth periodcd12345678x 10−3−300−200−100100200300400Time (sec)F o r c e (N )Simulation cutting force of single tooth periodFig.9(continued)F X F Y F Z T Z8>><>>:9>>=>>;¼X N m j ¼1F X ;j Ωt þj À1ðÞ2pN ÀÁF Y ;j Ωt þj À1ðÞ2p N ÀÁF Z ;j Ωt þj À1ðÞ2pN ÀÁT Z ;j Ωt þj À1ðÞ2p NÀÁ8>><>>:9>>=>>;ð20ÞThe cutting force model during helical milling operationsin the time domain has therefore been established analyti-cally.This model defines both the cutting force on the side cutting edge and on the end cutting edge,incorporating the interactions between the cutter and the workpiece on the effect of the spindle rotation and the helical feed.4Simulations and experimental resultsCutting forces during helical milling have been simulated on the MATLAB platform using the models presented previ-ously,and experiments have been performed to compare with the model predictions.The process parameters includ-ed the workpiece material,cutting conditions,tool material and geometry.The Ti6Al4V alloy was cast and then HIPed (hot isostatic pressing,HIP)at a pressure of 100–140MPa at 920°C for 2.5h;then,the casting was rough milled to the end geometry (160×160×20mm)with a hole in a diameter of 60mm in the centre of the plate as shown in Fig.1.There were two types of cutting tools,the M.A.Ford 20-mm five-flute carbide end mill (17878703A)and the M.A.Ford 16-mm five-flute carbide end mill (17862903A).Experiments were carried out on a five-axis high-speed Mikron UCP-710CNC machining centre.A three-axis piezo-electric Kistler 9265B type dynamometer was set up on the fixture with the workpiece.The accessory data ac-quisition system of the dynamometer consisted of a Kistler 5019A type multi-channel charge amplifier and signal pro-cessing software DynoWare.Before commencing the experiments,the dynamometer was calibrated using static loads.The simulated cutting forces in an entire milling tool revolution on the side edges,end edges and whole cutter during the typical cutting conditions are depicted in Fig.8.In this simulation,the up milling and large radial cutting depth are considered as the significant characteristics of the operation.Figure 8a shows the simulated cutting forces that acted on first side cutting edge,second side cutting edge and cutting forces that acted on the milling tool from both the five cutting edges,respectively.For the up milling condi-tion,the j th edge engages with the workpiece,and the (j -1)th edge engages following.The large radial cutting depth means that before the previous cutting edge has completed cutting,the next cutting edge has engaged the workpiece.Therefore,there is a period of time that forces overlap between the consecutive cutting edges.Figure 8b shows thesimulated cutting forces that acted on the end cutting edges.There are similar cutting forces superposing between consec-utive side cutting edges.However,the sum of the X ,Y direc-tion forces are nearly zero,that is one of the important features of helical milling and plunge milling operations.Figure 8c shows the cutting forces that acted on the milling tool.These results are the integration of the component forces from Fig.8a and b .The simulated and experimental cutting force results are compared in Fig.9.In this case,cutting tools travel along an entire helical curve and machine an entire helical milling period.The X ,Y ,Z coordinates are fixed to the workpiece,during the helical feed motion of the tool,the amplitude of F X and F Y change with time following a sine relationship.The amplitude of Fig.9a and b counter profile is the maximum result of F X and F Y .Figure 9c and d shows the experimental and simulated cutting forces in detail in a single tooth period.The comparison result from experiment and simulation are shown in Table 1.This figure depicts the simulation results to an accuracy of about 10%in these selected indicators.The maximum value of F X ,F Y and F Z indicates for a single tooth period for both simulation and experimental results shown.The maximum of ffiffiffiffiffiffiffiffiffiffiffiffiffiffiffiffiffiF 2X þF 2Yp indicates the amplitude of force of F X and F Y during helical milling.The errors probably result from cutting tool deflection and cutting tool wear.5ConclusionIn this paper,cutting forces during helical milling operations have been modelled in the time domain.The cutting forces both on the side cutting edges and on the end cutting edges along the helical feed path have been modelled by considering the tangential and the axial motion of the tool.The cutting force model can be used to predict cutting forces both on the side cutting edges and the end cutting edges.The model can also predict forces on the whole helix milling tool considering the process parameters and tool geometry.The experimental results show that for the given helix milling operation param-eters,the result of simulation predicts the cutting forces effec-tively and accurately.Table 1Comparison of experiment and simulation resultsExperiment (average)SimulationErrorHelical feed period (s)9.509.4750.263%Maximum of F X (N)371.1341.2−8.06%Maximum of F Y (N)253.2283.211.8%Maximum of F Z (N)287.7269.4−6.36%Maximum of ffiffiffiffiffiffiffiffiffiffiffiffiffiffiffiffiffiF 2X þF 2Yp (N)365.3397.68.84%。
adams问题补充(Adamsquestionsadded)
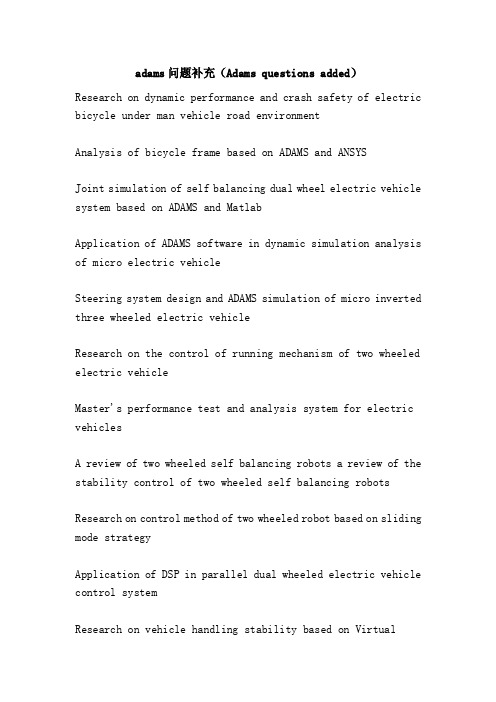
adams问题补充(Adams questions added)Research on dynamic performance and crash safety of electric bicycle under man vehicle road environmentAnalysis of bicycle frame based on ADAMS and ANSYSJoint simulation of self balancing dual wheel electric vehicle system based on ADAMS and MatlabApplication of ADAMS software in dynamic simulation analysis of micro electric vehicleSteering system design and ADAMS simulation of micro inverted three wheeled electric vehicleResearch on the control of running mechanism of two wheeled electric vehicleMaster's performance test and analysis system for electric vehiclesA review of two wheeled self balancing robots a review of the stability control of two wheeled self balancing robotsResearch on control method of two wheeled robot based on sliding mode strategyApplication of DSP in parallel dual wheeled electric vehicle control systemResearch on vehicle handling stability based on VirtualPrototyping TechnologyMajor: Vehicle EngineeringKeywords: virtual prototype, vehicle multi-body system dynamics, handling stability, electric power steering, PID controlClassification number: U469.4Research on vehicle handling stability based on Virtual Prototyping TechnologyResearch on joint simulation of EPS based on ADAMS and MATLABReduction Ratio is rack translation 1mm, steering wheel turn angle (in radians)So the Reduction Ratio unit should be rad/mm, not 1The rack ratio is used in vehicle simulation to define the variable (displacement, force, etc.) input of the steering column to control.Reduction ratio for steering input.For rack and pinion steering, it seems that the curve and the power curve of the template in the share can not be used to achieve the steering back and steering handiness. I see an article written before a steering column and a steering column with a three force, and I don't know how to write it... I don'tknow if you feel the same wayLeft_tire_forces inside the lateral, you can see the lateral force of the tireCornering force refers to the steering resistance of the tire, not the lateral forceAt the static load setup interface, the cornering force (steering force at the tire ground) includes the static friction torque,Blue for no power, red for power, you can observe, without power when the steering wheel required to enter a greater torque, this is clearly established.At the same time, some problems are found in the middle of the simulation results. For example, the input torque of the steering wheel is observed, and the maximum is 300N-mm, 0,3N-m,It's obviously small. Another angel=0 degrees, that is, the steering wheel in the middle, the steering wheel input torque is 0, in other words, with only a little force, steering wheelIt starts to rotate. This ignores the existence of static friction resistance between the tire and the road. Only when the input torque is greater than a certain value will the steering wheel startTurn.Analysis reason:Adams is actually a parameterized model, and the accuracy of the simulation results is related to the parameters that are filled. The mechanical parameters are better, fill in the wheelbase, load,The key is that the tire parameters on the static load settings interface are not filled. The tires are important components of the car, and its structural parameters andMechanical characteristics determine the main driving performance of a car.So the problem that needs to be solved now is..,How do you determine the correct tyre parameters on the static load settings interface, including back torque, steering force?,Brake force, traction force, vertical input, vertical input, overturning torque, rolling resistance, lateral force, and lateral force acting on the radius of the carcass.Since my simulation condition is a local steering on the plane, the speed is 0, so the braking force and traction force can not be filled. Due to the study of steering performance, rather thanRide comfort, so vertical input selection and vertical input can not be filled. Since the model is on the plane, there is no roll, so the overturning moment can not be filled.As the speed is 0, the wheel does not roll, so the rolling resistance and lateral force can not be filled. Therefore, the key is to measure the positive torque and steering force.As for the 2 parameters, I have considered them in 2 directions. One is to calculate the theoretical values from the point of view of the kinetic model and the existing parameter values. The other one isThe simulation results are obtained from the tool Tire Testrig, which comes with Adams, but the results are not satisfactory, and some even fail to be theoreticalCv_ is the prefix of the communicator variableSelect Pick Feature custom.-After studying for a few days, Adams people are talking about the simulation of vehicle dynamics. There is one of the most basic problems. Do you know what is the use of modeling?Very simple, right? My model is more accurate so that the leader will believe it! That makes sense! Blunder! What are you going to study based on the model? What are some of the useful information about the project, if you can not recognize this level, your behavior is not a rigorous engineering behavior, don't say the government always engage in performance face job, think of yourself first, you such a person as a civil servantis the same, if you really want to do for Chinese to improve your own heart to self cultivation. (it does not contradict or oppose or criticize some incorrect behavior.)If your vehicle model test has nothing else to do except that you do it, can you understand the design elements of no ground for blame, suspension K&C characteristics, understand what is anti brake nod, driving anti squat, understand why only the pitch center above the wheel center, drive shaft have good anti squat you, you may even even pitch center do not know, the more important the related concepts of the roll center and clear? It's not clear. It doesn't matter. You need to have a mind to think about, not something that has nothing to do with technology. It takes up most of your day. If you don't have a think of the heart, you want to rely on professors and experts will be taught, it is not the right attitude, the ultimate point is like a proud man took the money and said, you give me, I will look at the results, but the chassis performance design process in this field, the result is. For a vehicle, especially the reverse models, at the design stage, the most important is to understand the suspension parameters (size and stiffness) influence on the performance of suspension systems, such processes in the adjustment, how to adjust the You'll see. The value of whole vehicle simulation in modern chassis engineering (two years' new car cycle) lies in the contrast of different design schemes, which makes you find the problem,Verify the solution is correct, such as a car that the vertical stiffness is very large, uncomfortable, a look at the results through the analysis of the original design of the vertical bushing has a greater coupling to movement and lateral movement,so I this bush outwards from the axis of down about which direction to the right? Analysis - Design - vehicle simulation verification - adjustment, closed loop, problem solving.For the most simple example, you have seen the lotus, Porsche give you do not die simulation research. They can't check it, you can experience, we can also check, but one is limited to engineering practice is not necessary, on the other hand is in the world, a vehicle system research, now mainly used forin-depth study on the impact on the dynamics of the automobile chassis design, research of high speed characteristics, model testing needs have a certain basis, for example, to understand the tire model, such as the lateral stiffness in several large stiffness units, vehicle steering characteristics there will be some changes, because the test can not be absolutely accurate, so to be integrated according to the experience in the test data, the load status of the bushing test results, tire test results, comprehensive find a correction value. So, what do you think you need if you do that? How long will it take? So, go steady, one of the simplest, perhaps the most convincing reference, you see how the lotus do.Different plants have different cooperation in mind, we did find a group of like-minded partners, these people are friends as well as students or teachers, make people feel that the car China hope, mainly that the spirit of hard work. If you don't have the spirit to do this, we advise you to think more, the leaders of the country to call everyone should hold together, no matter from life or work on all should think how to benefit the development of things, learn about Scientific Outlook on Development!1., I built the vehicle model, after repeated debugging, and finally add tires and road to add success, but in the process of simulation, the following error occurred:ERROR:, The, simulation, stopped, at, time = 3.38783E-04. ADAMS, cannot, solveThe equations of motion.The, greatest, error, in, an, equation, is, 16.131, in, theEquation, for, GFORCE, JEEP.WHEEL4.forceThe, greatest, change, in, a, variable, is, 1.97857E-16, the, inVariable, for, PART, JEEP.Right_KnuckleTry, the, following, in, this, order:1., Use, the, MAXIT, argument, on, the, EQUILIBRIUM, IC, KINEMATICS,Or, INTEGRATOR, command, to, increase, the, maximum, number, ofIterations.The "Temporarily change the value of the PATTERN argument on the"EQUILIBRIUM, IC, KINEMATICS, or, INTEGRATOR, command, toPATTERN = T.The "Temporarily increase the value of the ERROR argument on the"EQUILIBRIUM, IC,运动学,或积分命令。
机械专业外文翻译-挖掘机的机械学和液压学
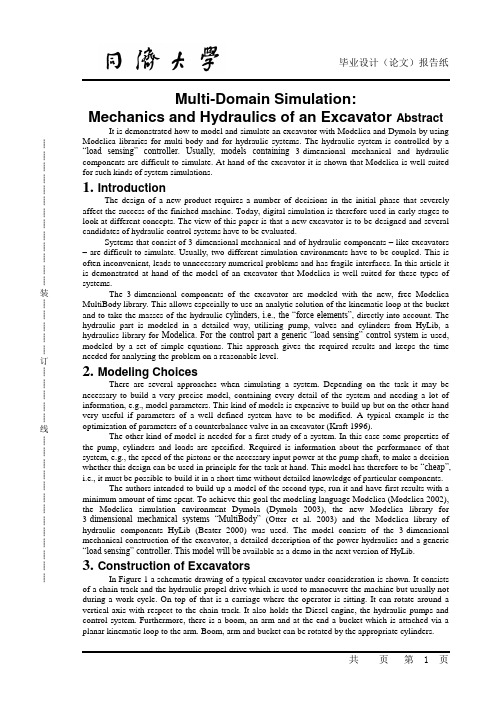
┊┊┊┊┊┊┊┊┊┊┊┊┊装┊┊┊┊┊订┊┊┊┊┊线┊┊┊┊┊┊┊┊┊┊┊┊┊Multi-Domain Simulation:Mechanics and Hydraulics of an Excavator Abstract It is demonstrated how to model and simulate an excavator with Modelica and Dymola by using Modelica libraries for multi-body and for hydraulic systems. The hydraulic system is controlled by a “load sensing” controller. Usually, models containing3-dimensional mechanical and hydraulic components are difficult to simulate. At hand of the excavator it is shown that Modelica is well suited for such kinds of system simulations.1. IntroductionThe design of a new product requires a number of decisions in the initial phase that severely affect the success of the finished machine. Today, digital simulation is therefore used in early stages to look at different concepts. The view of this paper is that a new excavator is to be designed and several candidates of hydraulic control systems have to be evaluated.Systems that consist of 3-dimensional mechanical and of hydraulic components – like excavators – are difficult to simulate. Usually, two different simulation environments have to be coupled. This is often inconvenient, leads to unnecessary numerical problems and has fragile interfaces. In this article it is demonstrated at hand of the model of an excavator that Modelica is well suited for these types of systems.The 3-dimensional components of the excavator are modeled with the new, free Modelica MultiBody library. This allows especially to use an analytic solution of the kinematic loop at the bucket and to take the masses of the hydraulic cylinders, i.e., the “force elements”, directly into account. The hydraulic part is modeled in a detailed way, utilizing pump, valves and cylinders from HyLib, a hydraulics library for Modelica. For the control part a generic “load sensing” control system is used, modeled by a set of simple equations. This approach gives the required results and keeps the time needed for analyzing the problem on a reasonable level.2. Modeling ChoicesThere are several approaches when simulating a system. Depending on the task it may be necessary to build a very precise model, containing every detail of the system and needing a lot of information, e.g., model parameters. This kind of models is expensive to build up but on the other hand very useful if parameters of a well defined system have to be modified. A typical example is the optimization of parameters of a counterbalance valve in an excavator (Kraft 1996).The other kind of model is needed for a first study of a system. In this case some properties of the pump, cylinders and loads are specified. Required is information about the performance of that system, e.g., the speed of the pistons or the necessary input power at the pump shaft, to make a decision whether this design can be used in principle for the task at hand. This model has therefore to be “cheap”, i.e., it must be possible to build it in a short time without detailed knowledge of particular components.The authors intended to build up a model of the second type, run it and have first results with a minimum amount of time spent. To achieve this goal the modeling language Modelica (Modelica 2002), the Modelica simulation environment Dymola (Dymola 2003), the new Modelica library for 3-dimensional mechanical systems “MultiBody”(Otter et al. 2003) and the Modelica library of hydraulic components HyLib (Beater 2000) was used. The model consists of the 3-dimensional mechanical construction of the excavator, a detailed description of the power hydraulics and a generic “load sensing” controller. This model will be available as a demo in the next version of HyLib.3. Construction of ExcavatorsIn Figure 1 a schematic drawing of a typical excavator under consideration is shown. It consists of a chain track and the hydraulic propel drive which is used to manoeuvre the machine but usually not during a work cycle. On top of that is a carriage where the operator is sitting. It can rotate around a vertical axis with respect to the chain track. It also holds the Diesel engine, the hydraulic pumps and control system. Furthermore, there is a boom, an arm and at the end a bucket which is attached via a planar kinematic loop to the arm. Boom, arm and bucket can be rotated by the appropriate cylinders.┊┊┊┊┊┊┊┊┊┊┊┊┊装┊┊┊┊┊订┊┊┊┊┊线┊┊┊┊┊┊┊┊┊┊┊┊┊Figure 2 shows that the required pressures in the cylinders depend on the position. For the “stretched” situation the pressure in the boom cylinder is 60 % higher than in the retracted position. Not only the position but also the movements have to be taken into account. Figure 3 shows a situation where the arm hangs down. If the carriage does not rotate there is a pulling force required in the cylinder. When rotating –excavators can typically rotate with up to 12 revolutions per minute –the force in the arm cylinder changes its sign and now a pushing force is needed. This change is very significant because now the “active” chamber of the cylinder switches and that must be taken into account by the control system. Both figures demonstrate that a simulation model must take into account the couplings between the four degrees of freedom this excavator has. A simpler model that uses a constant load for each cylinder and the swivel drive leads to erroneous results4. Load Sensing SystemExcavators have typically one Diesel engine, two hydraulic motors and three cylinders. There exist different hydraulic circuits to provide the consumers with the required hydraulic energy. A typical design is a Load Sensing circuit that is energy efficient and user friendly. The idea is to have a flow rate control system for the pump such that it delivers exactly the needed flow rate. As a sensor the pressure drop across an orifice is used. The reference value is the resistance of the orifice. A schematic drawing is shown in figure 4, a good introduction to that topic is given in (anon. 1992).The pump control valve maintains a pressure at the pump port that is typically 15 bar higher than the pressure in the LS line (= Load Sensing line). If the directional valve is closed the pump has therefore a stand-by pressure of 15 bar. If it is open the pump delivers a flow rate that leads to a pressure drop of 15 bar across that directional valve. Note: The directional valve is not used to throttle the pump flow but as a flow meter (pressure drop that is fed back) and as a reference (resistance). The circuit is energy efficient because the pump delivers only the needed flow rate, the throttling losses are small compared to other circuits.If more than one cylinder is used the circuit becomes more complicated, see figure 5. E.g. if the boom requires a pressure of 100 bar and the bucket a pressure of 300 bar the pump pressure must be above 300 bar which would cause an unwanted movement of the boom cylinder. Therefore compensators are used that throttle the oil flow and thus achieve a pressure drop of 15 bar across the particular directional valve. These compensators can be installed upstream or downstream of the directional valves. An additional valve reduces the nominal pressure differential if the maximum pump flow rate or the maximum pressure is reached (see e.g. Nikolaus 1994).5. Model of Mechanical PartIn Figure 6, a Modelica schematic of the mechanical part is shown. The chain track is not modeled, i.e., it is assumed that the chain track does not move. Components “rev1”, ..., “rev4” are the 4 revolute joints to move the parts relative to each other. The icons with the long black line are “virtual”rods that are used to mark specific points on a part, especially the mounting points of the hydraulic cylinders. The light blue spheres (b2, b3, b4, b5) are bodies that have mass and an inertia tensor and are used to model the corresponding properties of the excavator parts.The three components “cyl1f”, “cyl2f”,and “cyl3f” are line force components that describe a force interaction along a line between two attachment points. The small green squares at these components represent 1-dimensional translational connectors from theModelica.Mechanics. Translational library. They are used to define the 1- dimensional force law acting between the two attachment points. Here, the hydraulic cylinders described in the next section are directly attached. The small two spheres in the icons of the “cyl1f,cyl2f, cyl3f” components indicate that optionally two point masses are taken into account that are attached at defined distances from the attachment points along the connecting line. This allows to easily model the essential mass properties (mass and center of mass) of the hydraulic cylinders with only a very small computational overhead.The jointRRR component (see right part of Figure 6) is an assembly element consisting of 3 revolute joints that form together a planar loop when connected to the arm. A picture of this part of an excavator, a zoom in the corresponding Modelica schematic and the animation view is shown in Figure 7. When moving revolute joint “rev4” (= the large red cylinder in the lower part of Figure 7; the small┊┊┊┊┊┊┊┊┊┊┊┊┊装┊┊┊┊┊订┊┊┊┊┊线┊┊┊┊┊┊┊┊┊┊┊┊┊red cylinders characterize the 3 revolute joints of the jointRRR assembly component) the position and orientation of the attachment points of the “left”and “right” revolute joints of the jointRRR component are known. There is a non-linear algebraic loop in the jointRRR component to compute the angles of its three revolute joints given the movement of these attachment points. This non-linear system of equations is solved analytically in the jointRRR object, i.e., in a robust and efficient way. For details see In a first step, the mechanical part of the excavator is simulated without the hydraulic system to test this part separatly. This is performed by attaching translational springs with appropriate spring constants instead of the hydraulic cylinders. After the animation looks fine and the forces and torques in the joints have the expected size, the springs are replaced by the hydraulic system described in the next sections.All components of the new MultiBody library have “built-in” animation definitions, i.e., animation properties are mostly deduced by default from the given definition of the multi-body system. For example, a rod connecting two revolute joints is by default visualized as cylinder where the diameter d is a fraction of the cylinder length L (d = L/40) which is in turn given by the distance of the two revolute joints. A revolute joint is by default visualized by a red cylinder directed along the axis of rotation of the joint. The default animation (with only a few minor adaptations) of the excavator is shown if Figure 8. The light blue spheres characterize the center of mass of bodies. The line force elements that visualize the hydraulic cylinders are defined by two cylinders (yellow and grey color) that are moving in each other. As can be seen, the default animation is useful to get, without extra work from the user side, a rough picture of the model that allows to check the most important properties visually, e.g., whether the center of masses or attachment points are at the expected places.For every component the default animation can be switched off via a Boolean flag. Removing appropriate default animations, such as the “centerof- mass s pheres”, and adding some components that have pure visual information (all visXXX components in the schematic of Figure 6) gives quickly a nicer animation, as is demonstrated in Figure 9. Also CAD data could be utilized for the animation, but this was not available for the examination of this excavator.6. The Hydraulics Library HyLibThe (commercial) Modelica library HyLib (Beater 2000, HyLib 2003) is used to model the pump, metering orifice, load compensator and cylinder of the hydraulic circuit. All these components are standard components for hydraulic circuits and can be obtained from many manufacturers. Models of all of them are contained in HyLib. These mathematical models include both standard textbook models (e. g. Dransfield 1981, Merrit 1967, Viersma 1980) and the most advanced published models that take the behavior of real components into account (Schulz 1979, Will 1968). An example is the general pump model where the output flow is reduced if pressure at the inlet port falls below atmospheric pressure. Numerical properties were also considered when selecting a model (Beater 1999). One point worth mentioning is the fact that all models can be viewed at source code level and are documented by approx. 100 references from easily available literature.After opening the library, the main window is displayed (Figure 10). A double click on the “pumps” icon opens the selection for all components that are needed to originate or end an oil flow (Figure 11). For the problem at hand, a hydraulic flow source with internal leakage and externally commanded flow rate is used. Similarly the needed models for the valves, cylinders and other components are chosen.All components are modeled hierarchically. Starting with a definition of a connector –a port were the oil enters or leaves the component – a template for components with two ports is written. This can be inherited for ideal models, e.g., a laminar resistance or a pressure relief valve. While it usually makes sense to use textual input for these basic models most of the main library models were programmed graphically, i.e., composed from basic library models using the graphical user interface. Figure12 gives an example of graphical programming. All mentioned components were chosen from the library and then graphically connected.7. Library Components in Hydraulics CircuitThe composition diagram in Figure 12 shows the graphically composed hydraulics part of the excavator model. The sub models are chosen from the appropriate libraries, connected and the┊┊┊┊┊┊┊┊┊┊┊┊┊装┊┊┊┊┊订┊┊┊┊┊线┊┊┊┊┊┊┊┊┊┊┊┊┊parameters input. Note that the cylinders and the motor from HyLib can be simply connected to the also shown components of the MultiBody library. The input signals, i.e., the reference signals of the driver of the excavator, are given by tables, specifying the diameter of the metering orifice, i.e. the reference value for the flow rate. From the mechanical part of the excavator only the components are shown in Figure 12 that are directly coupled with hydraulic elements, such as line force elements to which the hydraulic cylinders are attached.8. Model of LS ControlFor this study the following approach is chosen: Model the mechanics of the excavator, the cylinders and to a certain extent the pump and metering valves in detail because only the parameters of the components will be changed, the general structure is fixed. This means that the diameter of the bucket cylinder may be changed but there will be exactly one cylinder working as shown in Figure 1. That is different for the rest of the hydraulic system. In this paper a Load Sensing system, or LS system for short, using one pump is shown but there are other concepts that have to be evaluated during an initial design phase. For instance the use of two pumps, or a separate pump for the swing.The hydraulic control system can be set up using meshed control loops. As there is (almost) no way to implement phase shifting behavior in purely hydraulic control systems the following generic LS system uses only proportional controllers.A detailed model based on actual components would be much bigger and is usually not available at the begin of an initial design phase. It could be built with the components from the hydraulics library but would require a considerable amount of time that is usually not available at the beginning of a project.In Tables 1 and 2, the implementation of the LS control in form of equations is shown. Usually, it is recommended for Modelica models to either use graphical model decomposition or to define the model by equations, but not to mix both descrip- tion forms on the same model level.For the LS system this is different because it has 17 input signals and 5 output signals. One might built one block with 17 inputs and 5 outputs and connect them to the hydraulic circuit. However, in this case it seems more understandable to provide the equations directly on the same level as the hydraulic circuit above and access the input and output signals directly. For example, ”metOri1.port_A.p” used in table 2 is the measured pressure at port_A of the metering orifice metOri1. The calculated values of the LS controller, e.g., the pump flow rate “pump.inPort.signal[1] = ...” is the signal at the filled blue rectangle of the “pump” component, see Figure 12).The strong point of Modelica is that a seamless integration of the 3-dimensional mechanical library, the hydraulics library and the non standard, and therefore in no library available, model of the control system is easily done. The library components can be graphically connected in the object diagram and the text based model can access all needed variables.9. Some Simulation ResultsThe complete model was built using the Modelica modeling and simulation environment Dymola (Dymola 2003), translated, compiled and simulated for 5 s. The simulation time was 17 s using the DASSL integrator with a relative tolerance of 10-6 on a 1.8 GHz notebook, i.e., about 3.4 times slower as real-time. The animation feature in Dymola makes it possible to view the movements in an almost realistic way which helps to explain the results also to non-experts, see Figure 9.Figure 13 gives the reference signals for the three cylinders and the swing, the pump flow rate and pressure. From t = 1.1 s until 1.7 s and from t = 3.6 s until 4.0 s the pump delivers the maximum flow rate. From t = 3.1 s until 3.6 s the maximum allowed pressure is reached. Figure 14 gives the position of the boom and the bucket cylinders and the swing angle. It can be seen that there is no significant change in the piston movement if another movement starts or ends. The control system reduces the couplings between the consumers which are very severe for simple throttling control.Figure 15 shows the operation of the bucket cylinder. The top figure shows the reference trajectory, i. e. the opening of the directional valve. The middle figure shows the conductance of the compensators. With the exception of two spikes it is open from t = 0 s until t = 1 s. This means that in┊┊┊┊┊┊┊┊┊┊┊┊┊装┊┊┊┊┊订┊┊┊┊┊线┊┊┊┊┊┊┊┊┊┊┊┊┊that interval the pump pressure is commanded by that bucket cylinder. After t = 1 s the boom cylinder requires a considerably higher pressure and the bucket compensator therefore increases the resistance (smaller conductance). The bottom figure shows that the flow rate control works fine. Even though there is a severe disturbance (high pump pressure after t = 1 s due to the boom) the commanded flow rate is fed with a small error to the bucket cylinder.10. ConclusionFor the evaluation of different hydraulic circuits a dynamic model of an excavator was built. It consists of a detailed model of the 3 dimensional mechanics of the carriage, including boom, arm and bucket and the standard hydraulic components like pump or cylinder. The control system was not modeled on a component basis but the system was described by a set of nonlinear equations.The system was modeled using the Modelica MultiBody library, the hydraulics library Hylib and a set of application specific equations. With the tool Dymola the system could be build and tested in a short time and it was possible to calculate the required trajectories for evaluation of the control system.The animation feature in Dymola makes it possible to view the movements in an almost realistic way which helps to explain the results also to多畴模拟:挖掘机的机械学和液压学概要:通过使用用于多体和液压系统的Modelica程序库,示范通过Modelica和Dymola如何模拟和仿真挖掘机。
基于MATLAB/Simulink的汽车平顺性的仿真模型(可编辑)
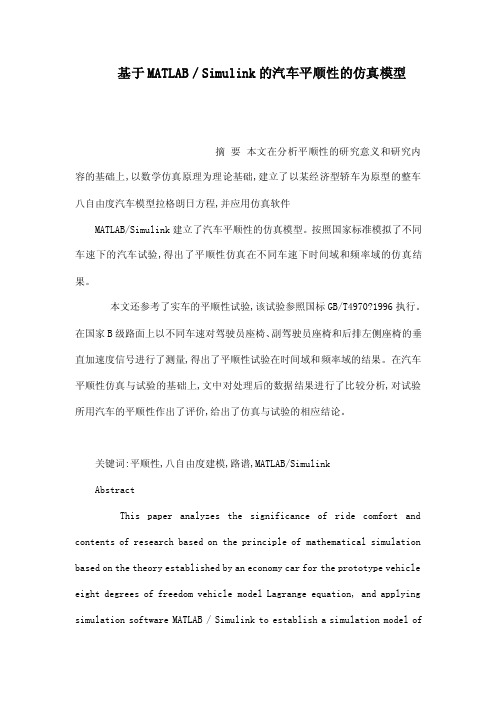
基于MATLAB/Simulink的汽车平顺性的仿真模型摘要本文在分析平顺性的研究意义和研究内容的基础上,以数学仿真原理为理论基础,建立了以某经济型轿车为原型的整车八自由度汽车模型拉格朗日方程,并应用仿真软件MATLAB/Simulink建立了汽车平顺性的仿真模型。
按照国家标准模拟了不同车速下的汽车试验,得出了平顺性仿真在不同车速下时间域和频率域的仿真结果。
本文还参考了实车的平顺性试验,该试验参照国标GB/T4970?1996执行。
在国家B级路面上以不同车速对驾驶员座椅、副驾驶员座椅和后排左侧座椅的垂直加速度信号进行了测量,得出了平顺性试验在时间域和频率域的结果。
在汽车平顺性仿真与试验的基础上,文中对处理后的数据结果进行了比较分析,对试验所用汽车的平顺性作出了评价,给出了仿真与试验的相应结论。
关键词:平顺性,八自由度建模,路谱,MATLAB/SimulinkAbstractThis paper analyzes the significance of ride comfort and contents of research based on the principle of mathematical simulation based on the theory established by an economy car for the prototype vehicle eight degrees of freedom vehicle model Lagrange equation, and applying simulation software MATLAB / Simulink to establish a simulation model ofvehicle ride comfort. Simulated in accordance with national standards of vehicles under different speed test results, the simulation ride at different speeds time domain and frequency domain simulation results This article also during the actual car test ride, test the light of the implementation of national standard GB/T4970-1996. B-class roads in the country at different speeds on the driver's seat, co-pilot seat and left rear seat of the vertical acceleration signal was measured, obtained test ride in the time domain and frequency domain results. In the car ride simulation and experiment based on the text of the processed data results were compared, the test used in ride comfort has been evaluated, the simulation and testing the corresponding conclusionsKey words: Comfort,Eight degrees of freedom model, Road spectrum, MATLAB/Simulink 目录前言 11绪论 21.1汽车平顺性研究的意义21.2汽车平顺性研究的主要内容 21.3汽车行驶平顺性研究发展概况 42汽车行驶平顺性的评价 62.1行驶平顺性评价的研究62.2人体对振动的反应 62.3平顺性指标评价方法72.3.1ISO 2631标准评价法72.3.2吸收功率法112.4平顺性评价流程113随机路面模型的研究 133.1随机路面模型133.1.1路面不平度的概述133.1.2路面不平度的表达133.1.3时域模型143.1.4时域响应153.2建立随机路面模型 153.2.1汽车前轮所受路面随机激励153.2.2前后轮滞后输入的处理164汽车平顺性模型的建立及仿真184.1建模基本原理与要求184.1.1建模基本要求184.1.2建模基本原理194.2 汽车平顺性建模194.2.1 八自由度整车力学模型的建立204.2.2 数学模型的建立214.2.3 汽车座椅的布置254.2.4 汽车八自由度Simulink仿真模型的建立26 4.3整车平顺性仿真284.3.1仿真参数的选取 284.3.2 50km/h车速下汽车平顺性仿真结果304.3.3 60km/h车速下汽车平顺性仿真结果314.3.4 70km/h车速下汽车平顺性仿真结果325整车平顺性试验与结果分析335.1 平顺性试验原理及试验过程335.2 仿真与试验结果的数据处理345.3 仿真与试验结果的时域分析365.4 仿真与试验结果的频域分析37结论38致谢39参考文献40前言汽车平顺性主要是指保持汽车在行驶过程中产生的振动和冲击环境对乘员舒适性的影响在一定界限之内,对载货汽车还包括保持货物完好的性能,它是现代高速汽车的主要性能之一。
计量经济学(英文版)
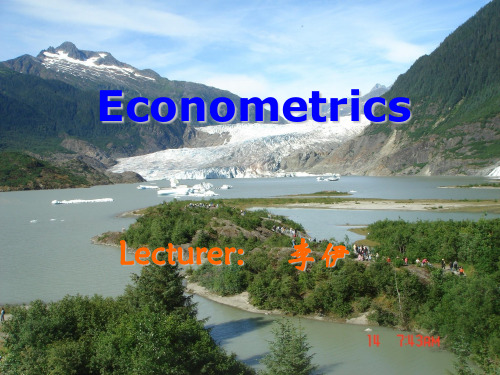
(Measure GDP, Growth velocity, Fluctuation)
●Analysis the factors that impact GDP?
(Investment, Consumption, Exportation…..)
9
Contact Information
PPT download:
Public Email: econometrics_ly@ Password: fall2011
Contact Me: Email: liy@ Office:通博楼B208 Office hour:TW 1-3 pm
design the policy?
13
Case3:Share price analysis of Chinese Stocks
●How does share price change ?
( Measure by stock index)
●What is the main effect factors
Course Arrangement and Requirement
Term mission (30 %):
10 terms are grouped by yourselves. Each term is responsible for one chapter (assign randomly).
VII. Autocorrelation (3)
5
Course Contents
VIII. IX. X. XI. Model Specification and Diagnostic testing (3) Autoregressive and distributed lag models (6) Simultaneous Equation Models (6) Time Series Econometrics (6)
智轨电车多编组铰接动力学建模仿真与验证

收稿日期:2020-06-14作者简介:黄瑞鹏(1991—),男,工程师,研究方向为车辆动力学控制、自动驾驶运动规划与控制。
基金项目:国家重点研发计划(2018YFB1201600)智轨电车多编组铰接动力学建模仿真与验证黄瑞鹏,袁希文,胡云卿,张新锐,张 沙,李晓光(中车株洲电力机车研究所有限公司,湖南 株洲 412001)摘 要:智轨电车取消了传统的钢轮钢轨,利用机器视觉并采用胎地耦合跟踪中央虚拟轨迹线的方式对整车运动实现控制。
为了迭代优化,降低中央轨迹线跟随控制系统的横向偏差,文章搭建了符合智轨电车胎地耦合及多编组柔性铰接结构特点的35 m 列车动力学模型,并通过Matlab / Simulink 动力学模型仿真测试验证了该动力学模型能实现智轨电车在老城区的狭窄限界中的快速类轨道行驶和站台小间隙(偏差控制在8~12 cm )的精准进站停车。
关键词:动力学建模;智轨电车;模型预测控制;路径跟踪;循迹控制系统;机器视觉中图分类号 :U461.6 文献标识码 :A 文章编号 :2096-5427(2020)06-0019-05doi:10.13889/j.issn.2096-5427.2020.06.004Dynamic Modeling of Multi-category Jointing for the Autonomous-railRapid Tram and Real Vehicle ValidationHUANG Ruipeng, YUAN Xiwen, HU Yunqing, ZHANG Xinrui, ZHANG Sha, LI Xiaoguang( CRRC Zhuzhou Institute Co., Ltd., Zhuzhou, Hunan 412001, China )Abstract: Autonomous-rail rapid tram replaces traditional steel wheels with rubber tires, and uses machine vision to track the central virtual track line to control vehicle motion. In order to iteratively optimize and reduce the lateral deviation of the precision lane keeping control system, a 35 m train dynamic model was built in this paper to meet the characteristics of autonomous-rail rapid tram such as tire-ground coupling and multi-group flexible articulating. Through the Matlab / Simulink dynamic model simulation test, it is verified that the dynamic model can show fast track driving of an autonomous-rail rapid tram in a narrow gauge of an old city and precise docking of a small platform gap (the deviation is controlled at 8~12 cm).Keywords: dynamic model simulation; autonomous-rail rapid tram; model predictive control; path tracking; lane keeping control system; machine vision0 引言智轨电车是中车株洲电力机车研究所有限公司(简称“中车株洲所”)2017年率先发布的一款新制式轨道交通车辆。
- 1、下载文档前请自行甄别文档内容的完整性,平台不提供额外的编辑、内容补充、找答案等附加服务。
- 2、"仅部分预览"的文档,不可在线预览部分如存在完整性等问题,可反馈申请退款(可完整预览的文档不适用该条件!)。
- 3、如文档侵犯您的权益,请联系客服反馈,我们会尽快为您处理(人工客服工作时间:9:00-18:30)。
The goal of control is to define the simplest model that effectively captures the vehicle dynamics, and neither of the above models relate the sail coefficients to a single, simple control. The most straightforward way to depower a sail plan is to let the main sail out (decrease its deflection angle, δb) to decrease heeling force. When this is insufficient, the entire sail area should be reduced (reefing). For control applications, it is the effect of the whole sail plan that is important, meaning the combined effect of the main sail and jib, genoa, or spinnaker. The model explored in this work is inspired by those used in aerospace control applications where total airplane aerodynamic coefficients are modified by linear curves. For example, the typical breakdown for the total lift coefficient of an aircraft is[11]:
βeff = tan−1 ( tan βA cosφ )
(1)
Veff = Байду номын сангаасA 1− sin2 βA sin2 φ
(2)
The drawback of current aerodynamic models for sailing yachts is the assumption that sails are in optimal trim when reporting coefficients. Different methods of describing the trim of the sails away from the fully powered up state that put the sails in optimal trim for the conditions investigated have been used. The most common is the early solution that modifies the coefficients using the parameters of reef and flat[10] to represent decreases from the optimal sail coefficients that occur when sailing in real-life conditions. An alternate depowering model[7] uses a single parameter, power, which is based on the ratio between the real heeling moment coefficient and the optimum, to modify aerodynamic coefficients. Both of these models aim to capture the effect of utilizing the many secondary controls available on a sailing yacht such as reefing points, outhauls, boom vangs, etc that are used to depower and trim the sails.
I. INTRODUCTION
VPP’s and race simulations represent most of the research into modeling the dynamics of a sailing yacht and have been highly motivated by competitive racing teams[1-6]. Aerodynamic data for these models is reported using the ‘optimum’ sail angle which produces the best “velocity made good” for the sailing yacht for either an apparent or true wind angle[7-9]. The goal of an autonomous sailing yacht will likely be very different than that of a racing boat, tenths of a knot gains in speed will not be as important as maintaining a constant course, safety, and minimizing wear on the yacht itself. It would be extremely useful for an autonomous control system for a sailing yacht to exploit the sails as real control inputs to the dynamic system. At the simplest level, that means including sail deflections in the physics based dynamic model of sailing yachts, something non-existent in current models.
An accepted solution to the dependence of aerodynamic coefficients on heel is to use effective angle theory[7, 10] to define an effective wind angle, βeff, and velocity, Veff, in the heeled plane, and use those variables rather than βA and VA, to define forces and corresponding coefficients. For our application of 4 DOF excluding heave and pitch, the βeff and Veff are defined as follows[7]:
combination of the boat velocity, VB, and the true wind velocity, VT, as shown in Fig. 1. Also defined in this figure are the mainsail angle, δb, and leeway angle, γ.
Abstract— Sailing yachts have great potential to act as future long-term oceanic observing platforms, yet to date there have not been complete autonomous sailing systems robust enough to handle long term operation in the harsh and continually changing ocean environment. The basis of control system design is a mathematical model capable of describing and capturing the physics based dynamics of the sailboat. The mathematical model represents the system to be controlled, however, a sailing yacht is a very difficult system to model from a controls perspective because of its heavy reliance on the uncontrolled spatial and temporal distribution of the wind. Presented in this paper is a modified aerodynamic force model which includes the sail angle as a control input to the sailing yacht system. The new model has been incorporated into a 4 degree of freedom (DOF) rigid body dynamic yacht model, and implemented in MATLAB/Simulink. The simulations shows model exhibits similar behavior to that observed in full scale sailing yacht sea trial data. Data taken aboard a Precision 23 day-sailer is analyzed, and it is found that the model is a likely candidate for including sail input to a physics based dynamic model for identification and control system design.