A 3D discrete FEM iterative algorithm for solving the water pipe cooling problems of massive
a转换成膜a算法
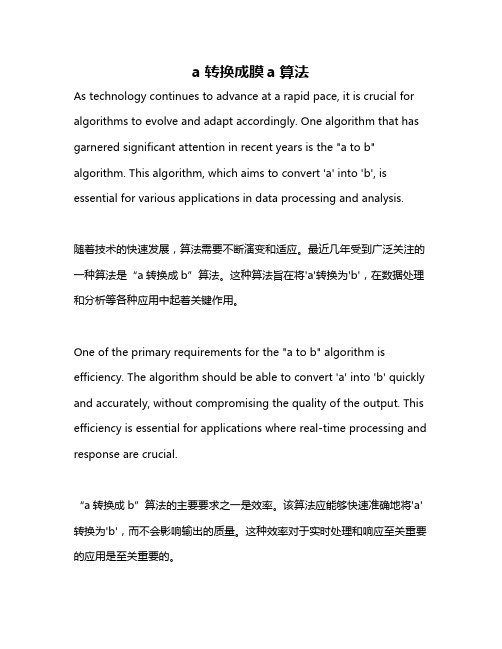
a转换成膜a算法As technology continues to advance at a rapid pace, it is crucial for algorithms to evolve and adapt accordingly. One algorithm that has garnered significant attention in recent years is the "a to b" algorithm. This algorithm, which aims to convert 'a' into 'b', is essential for various applications in data processing and analysis.随着技术的快速发展,算法需要不断演变和适应。
最近几年受到广泛关注的一种算法是“a转换成b”算法。
这种算法旨在将'a'转换为'b',在数据处理和分析等各种应用中起着关键作用。
One of the primary requirements for the "a to b" algorithm is efficiency. The algorithm should be able to convert 'a' into 'b' quickly and accurately, without compromising the quality of the output. This efficiency is essential for applications where real-time processing and response are crucial.“a转换成b”算法的主要要求之一是效率。
尺度不变特征变换算法

尺度不变特征变换算法一、前言尺度不变特征变换算法(Scale-Invariant Feature Transform,SIFT)是一种用于图像处理和计算机视觉的算法,由David Lowe于1999年提出。
SIFT算法可以在不同尺度和旋转下找到图像中的关键点,并提取出这些关键点的局部特征描述符,从而实现对图像的匹配、识别等任务。
二、SIFT算法原理1. 尺度空间构建SIFT算法首先通过高斯滤波器构建尺度空间,以便在不同尺度下检测图像中的关键点。
高斯滤波器可以模拟人眼对图像的模糊效果,使得在不同尺度下能够检测到具有相似形状但大小不同的物体。
2. 关键点检测在构建好尺度空间后,SIFT算法通过DoG(差分高斯)金字塔来寻找关键点。
DoG金字塔是由相邻两层高斯金字塔之差得到的,它可以有效地检测出具有不同尺度和方向的局部极值点。
3. 方向分配为了使得特征描述子具有旋转不变性,在确定关键点位置后,SIFT算法还需要计算每个关键点的主方向。
它通过计算关键点周围像素的梯度方向直方图来确定主方向,从而使得特征描述子能够在不同角度下进行匹配。
4. 特征描述在确定了关键点位置和主方向之后,SIFT算法通过计算关键点周围像素的梯度幅值和方向来生成特征描述子。
这个过程中,SIFT算法使用了一个16×16的窗口,并将其分成4×4个小窗口,在每个小窗口中计算8个梯度方向的直方图,最终生成一个128维的特征向量。
5. 特征匹配在提取出两幅图像中所有关键点的特征描述子后,SIFT算法采用欧氏距离来计算两个特征向量之间的相似度,并使用比率测试来判断是否为匹配点。
如果两个特征向量之间的距离小于一定阈值,并且与次近邻之间距离比例大于一定比例,则认为是匹配点。
三、SIFT算法优缺点1. 优点:(1)尺度不变性:SIFT算法可以在不同尺度下检测到具有相似形状但大小不同的物体;(2)旋转不变性:SIFT算法可以计算每个关键点的主方向,从而使得特征描述子能够在不同角度下进行匹配;(3)鲁棒性:SIFT算法对于光照、视角、噪声等因素有较好的鲁棒性。
3D脑肿瘤分割的Dice损失函数的优化
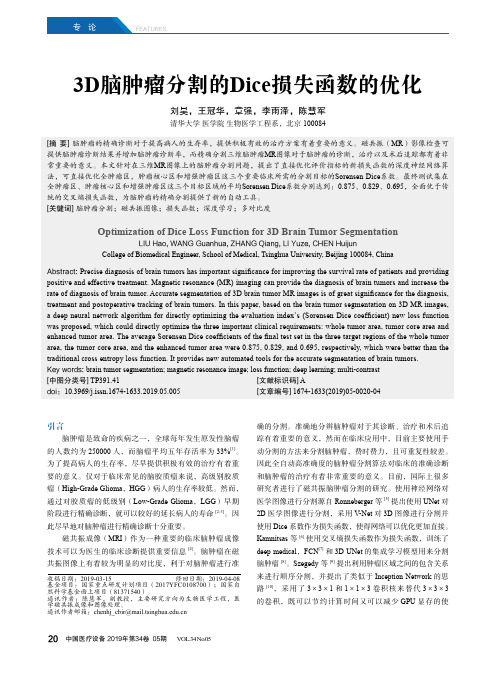
专 论FEATURES3D脑肿瘤分割的Dice损失函数的优化刘昊,王冠华,章强,李雨泽,陈慧军清华大学医学院生物医学工程系,北京 100084[摘 要] 脑肿瘤的精确诊断对于提高病人的生存率,提供积极有效的治疗方案有着重要的意义。
磁共振(MR)影像检查可提供脑肿瘤诊断结果并增加脑肿瘤诊断率,而精确分割三维脑肿瘤MR图像对于脑肿瘤的诊断,治疗以及术后追踪都有着非常重要的意义。
本文针对在三维MR图像上的脑肿瘤分割问题,提出了直接优化评价指标的新损失函数的深度神经网络算法,可直接优化全肿瘤区,肿瘤核心区和增强肿瘤区这三个重要临床所需的分割目标的Sorensen Dice系数。
最终测试集在全肿瘤区、肿瘤核心区和增强肿瘤区这三个目标区域的平均Sorensen Dice系数分别达到:0.875、0.829、0.695,全面优于传统的交叉熵损失函数,为脑肿瘤的精确分割提供了新的自动工具。
[关键词] 脑肿瘤分割;磁共振图像;损失函数;深度学习;多对比度Optimization of Dice Loss Function for 3D Brain Tumor SegmentationLIU Hao, WANG Guanhua, ZHANG Qiang, LI Yuze, CHEN HuijunCollege of Biomedical Engineer, School of Medical, Tsinghua University, Beijing 100084, ChinaAbstract: Precise diagnosis of brain tumors has important significance for improving the survival rate of patients and providing positive and effective treatment. Magnetic resonance (MR) imaging can provide the diagnosis of brain tumors and increase the rate of diagnosis of brain tumor. Accurate segmentation of 3D brain tumor MR images is of great significance for the diagnosis, treatment and postoperative tracking of brain tumors. In this paper, based on the brain tumor segmentation on 3D MR images, a deep neural network algorithm for directly optimizing the evaluation index’s (Sorensen Dice coefficient) new loss function was proposed, which could directly optimize the three important clinical requirements: whole tumor area, tumor core area and enhanced tumor area. The average Sorensen Dice coefficients of the final test set in the three target regions of the whole tumor area, the tumor core area, and the enhanced tumor area were 0.875, 0.829, and 0.695, respectively, which were better than the traditional cross entropy loss function. It provides new automated tools for the accurate segmentation of brain tumors.Key words: brain tumor segmentation; magnetic resonance image; loss function; deep learning; multi-contrast[中图分类号]TP391.41 [文献标识码] Adoi:10.3969/j.issn.1674-1633.2019.05.005 [文章编号] 1674-1633(2019)05-0020-04引言脑肿瘤是致命的疾病之一,全球每年发生原发性脑瘤的人数约为250000人,而脑瘤平均五年存活率为33%[1]。
一种用于三维重建的彩色Sift准稠密匹配算法

Q ai e s t igb sdo oo i l rh fr eo s u t n u s— nema hn ae nc l Sf a oi m D rc nt ci d c r t g t o3 r o
Z HAO L —u ,GEN G o h a ul G u — u ,Z HOU Mi g q a n —u n ' ,W AN Xi of n G a — g e
第2 9卷 第 9期
2 in Re e r h o mp t  ̄ p l t s a c fCo u e c o
Vo . 9 No 9 12 . S p. 01 e 2 2
一
种 用 于 三 维 重 建 的 彩 色 Sf准 稠 密 匹 配 算 法 水 i t
B ln om lU i rt, ei 0 85,C ia e gN r a nv sy B in 10 7 i t e i jg hn )
A b t a t Th spa rp o os d aqu s— ns thig a g rt ba e n t e Kub l a M u k t e r o nc lb ae ma e , sr c : i pe r p e a ide e mac n lo hm s d o h i e k — n h o yf ru a ir td i g s i o rbu e o mo e a c ae 3 r c nsr t n. c us i lo i tc nti t d t r c ur t D e o tuci Be a e S f ag rt o t hm s ls a bl fma c n rc l ri g s u de wa e s c pa e o thig f o o ma e n r o
集成梯度特征归属方法-概述说明以及解释
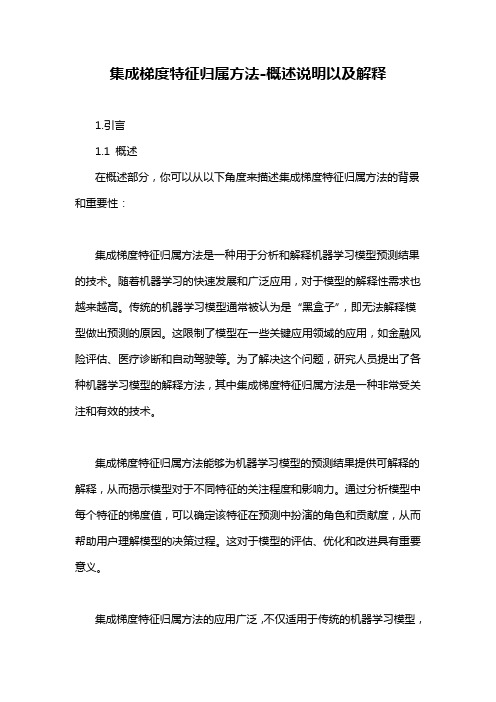
集成梯度特征归属方法-概述说明以及解释1.引言1.1 概述在概述部分,你可以从以下角度来描述集成梯度特征归属方法的背景和重要性:集成梯度特征归属方法是一种用于分析和解释机器学习模型预测结果的技术。
随着机器学习的快速发展和广泛应用,对于模型的解释性需求也越来越高。
传统的机器学习模型通常被认为是“黑盒子”,即无法解释模型做出预测的原因。
这限制了模型在一些关键应用领域的应用,如金融风险评估、医疗诊断和自动驾驶等。
为了解决这个问题,研究人员提出了各种机器学习模型的解释方法,其中集成梯度特征归属方法是一种非常受关注和有效的技术。
集成梯度特征归属方法能够为机器学习模型的预测结果提供可解释的解释,从而揭示模型对于不同特征的关注程度和影响力。
通过分析模型中每个特征的梯度值,可以确定该特征在预测中扮演的角色和贡献度,从而帮助用户理解模型的决策过程。
这对于模型的评估、优化和改进具有重要意义。
集成梯度特征归属方法的应用广泛,不仅适用于传统的机器学习模型,如决策树、支持向量机和逻辑回归等,也可以应用于深度学习模型,如神经网络和卷积神经网络等。
它能够为各种类型的特征,包括数值型特征和类别型特征,提供有益的信息和解释。
本文将对集成梯度特征归属方法的原理、应用优势和未来发展进行详细阐述,旨在为读者提供全面的了解和使用指南。
在接下来的章节中,我们将首先介绍集成梯度特征归属方法的基本原理和算法,然后探讨应用该方法的优势和实际应用场景。
最后,我们将总结该方法的重要性,并展望未来该方法的发展前景。
1.2文章结构文章结构内容应包括以下内容:文章的结构部分主要是对整篇文章的框架进行概述,指导读者在阅读过程中能够清晰地了解文章的组织结构和内容安排。
第一部分是引言,介绍了整篇文章的背景和意义。
其中,1.1小节概述文章所要讨论的主题,简要介绍了集成梯度特征归属方法的基本概念和应用领域。
1.2小节重点在于介绍文章的结构,将列出本文各个部分的标题和内容概要,方便读者快速了解文章的大致内容。
纹理物体缺陷的视觉检测算法研究--优秀毕业论文
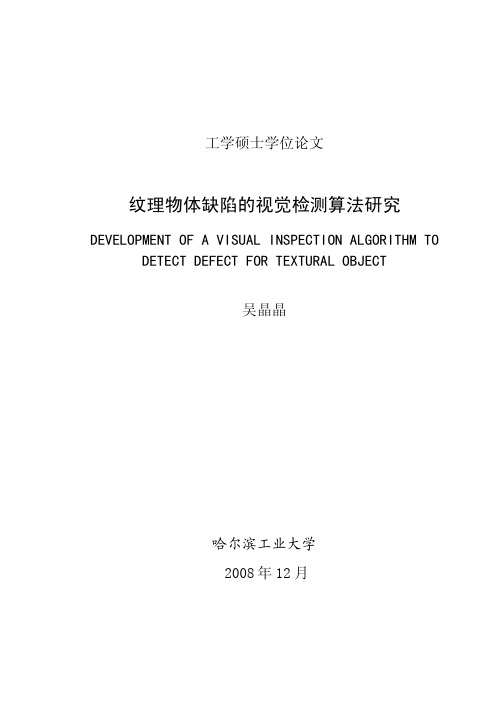
摘 要
在竞争激烈的工业自动化生产过程中,机器视觉对产品质量的把关起着举足 轻重的作用,机器视觉在缺陷检测技术方面的应用也逐渐普遍起来。与常规的检 测技术相比,自动化的视觉检测系统更加经济、快捷、高效与 安全。纹理物体在 工业生产中广泛存在,像用于半导体装配和封装底板和发光二极管,现代 化电子 系统中的印制电路板,以及纺织行业中的布匹和织物等都可认为是含有纹理特征 的物体。本论文主要致力于纹理物体的缺陷检测技术研究,为纹理物体的自动化 检测提供高效而可靠的检测算法。 纹理是描述图像内容的重要特征,纹理分析也已经被成功的应用与纹理分割 和纹理分类当中。本研究提出了一种基于纹理分析技术和参考比较方式的缺陷检 测算法。这种算法能容忍物体变形引起的图像配准误差,对纹理的影响也具有鲁 棒性。本算法旨在为检测出的缺陷区域提供丰富而重要的物理意义,如缺陷区域 的大小、形状、亮度对比度及空间分布等。同时,在参考图像可行的情况下,本 算法可用于同质纹理物体和非同质纹理物体的检测,对非纹理物体 的检测也可取 得不错的效果。 在整个检测过程中,我们采用了可调控金字塔的纹理分析和重构技术。与传 统的小波纹理分析技术不同,我们在小波域中加入处理物体变形和纹理影响的容 忍度控制算法,来实现容忍物体变形和对纹理影响鲁棒的目的。最后可调控金字 塔的重构保证了缺陷区域物理意义恢复的准确性。实验阶段,我们检测了一系列 具有实际应用价值的图像。实验结果表明 本文提出的纹理物体缺陷检测算法具有 高效性和易于实现性。 关键字: 缺陷检测;纹理;物体变形;可调控金字塔;重构
Keywords: defect detection, texture, object distortion, steerable pyramid, reconstruction
II
mfista算法
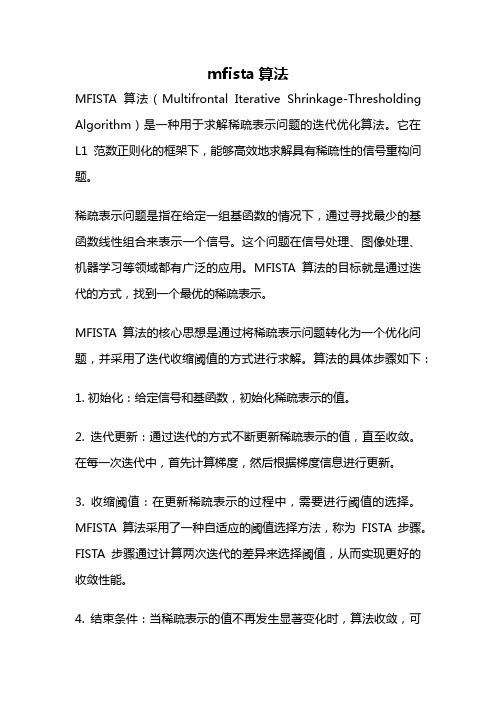
mfista算法MFISTA算法(Multifrontal Iterative Shrinkage-Thresholding Algorithm)是一种用于求解稀疏表示问题的迭代优化算法。
它在L1范数正则化的框架下,能够高效地求解具有稀疏性的信号重构问题。
稀疏表示问题是指在给定一组基函数的情况下,通过寻找最少的基函数线性组合来表示一个信号。
这个问题在信号处理、图像处理、机器学习等领域都有广泛的应用。
MFISTA算法的目标就是通过迭代的方式,找到一个最优的稀疏表示。
MFISTA算法的核心思想是通过将稀疏表示问题转化为一个优化问题,并采用了迭代收缩阈值的方式进行求解。
算法的具体步骤如下:1. 初始化:给定信号和基函数,初始化稀疏表示的值。
2. 迭代更新:通过迭代的方式不断更新稀疏表示的值,直至收敛。
在每一次迭代中,首先计算梯度,然后根据梯度信息进行更新。
3. 收缩阈值:在更新稀疏表示的过程中,需要进行阈值的选择。
MFISTA算法采用了一种自适应的阈值选择方法,称为FISTA步骤。
FISTA步骤通过计算两次迭代的差异来选择阈值,从而实现更好的收敛性能。
4. 结束条件:当稀疏表示的值不再发生显著变化时,算法收敛,可以得到最终的稀疏表示结果。
MFISTA算法相比于其他稀疏表示算法具有以下优点:1. 收敛速度快:MFISTA算法通过引入FISTA步骤,能够更快地收敛,提高算法的运行效率。
2. 稀疏性更好:MFISTA算法能够得到更加稀疏的稀疏表示结果,即使用更少的基函数来表示信号。
3. 适用性广:MFISTA算法在不同领域的稀疏表示问题中都有较好的应用效果,包括图像处理、压缩感知、信号恢复等。
4. 鲁棒性强:MFISTA算法对噪声和数据不完整性具有较好的鲁棒性,能够处理一些复杂的实际问题。
尽管MFISTA算法在稀疏表示问题中取得了较好的效果,但仍然存在一些局限性。
首先,算法的收敛性与初始化值有关,不同的初始化值可能导致不同的收敛结果。
颠覆传统建模!3D阿尔茨海默病体外模型诞生了!可巧妙模拟人脑,为痴呆治疗带来重大进步
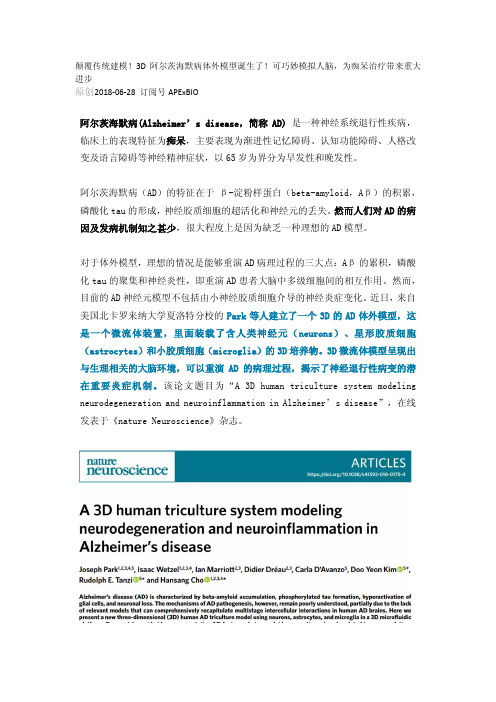
颠覆传统建模!3D阿尔茨海默病体外模型诞生了!可巧妙模拟人脑,为痴呆治疗带来重大进步原创2018-06-28 订阅号APExBIO阿尔茨海默病(Alzheimer’s disease,简称AD) 是一种神经系统退行性疾病,临床上的表现特征为痴呆,主要表现为渐进性记忆障碍、认知功能障碍、人格改变及语言障碍等神经精神症状,以65岁为界分为早发性和晚发性。
阿尔茨海默病(AD)的特征在于β-淀粉样蛋白(beta-amyloid,Aβ)的积累,磷酸化tau的形成,神经胶质细胞的超活化和神经元的丢失。
然而人们对AD的病因及发病机制知之甚少,很大程度上是因为缺乏一种理想的AD模型。
对于体外模型,理想的情况是能够重演AD病理过程的三大点:Aβ的累积,磷酸化tau的聚集和神经炎性,即重演AD患者大脑中多级细胞间的相互作用。
然而,目前的AD神经元模型不包括由小神经胶质细胞介导的神经炎症变化。
近日,来自美国北卡罗来纳大学夏洛特分校的Park等人建立了一个3D的AD体外模型,这是一个微流体装置,里面装载了含人类神经元(neurons)、星形胶质细胞(astrocytes)和小胶质细胞(microglia)的3D培养物。
3D微流体模型呈现出与生理相关的大脑环境,可以重演AD的病理过程,揭示了神经退行性病变的潜在重要炎症机制。
该论文题目为“A 3D human triculture system modeling neurodegeneration and neu roinflammation in Alzheimer’s disease”,在线发表于《nature Neuroscience》杂志。
这个三重培养装置看起来像一个“圆盆”(见下图),神经元和星形胶质细胞在3D凝胶状培养物中生长,来模拟一个“微型大脑”。
淀粉样前体蛋白(amyloid precursor protein, APP)的突变会导致AD。
在这里,瑞典突变(K670/M671L)和伦敦突变(V717I)APP通过慢病毒感染在神经元和星形胶质细胞中表达,导致β-淀粉样蛋白(Aβ)的累积和tau的磷酸化——这是AD的两个病理标志。
- 1、下载文档前请自行甄别文档内容的完整性,平台不提供额外的编辑、内容补充、找答案等附加服务。
- 2、"仅部分预览"的文档,不可在线预览部分如存在完整性等问题,可反馈申请退款(可完整预览的文档不适用该条件!)。
- 3、如文档侵犯您的权益,请联系客服反馈,我们会尽快为您处理(人工客服工作时间:9:00-18:30)。
See discussions, stats, and author profiles for this publication at: /publication/280874377 A 3D discrete FEM iterative algorithm for solving the water pipe cooling problems of massive concrete structuresARTICLE in INTERNATIONAL JOURNAL FOR NUMERICAL AND ANALYTICAL METHODS IN GEOMECHANICS · JULY 2015Impact Factor: 1.38 · DOI: 10.1002/nag.2409READS84 AUTHORS, INCLUDING:Zhao LanhaoHohai University32 PUBLICATIONS 15 CITATIONSSEE PROFILEA 3D discrete FEM iterative algorithm for solving the water pipe cooling problems of massive concrete structuresJing Cheng*,†,T.C.Li,Xiaoqing Liu and L.H.Zhao1College of Water Conservancy and Hydropower Engineering,Hohai University,Nanjing,210098,ChinaSUMMARYWater pipe cooling has been widely used for the temperature control and crack prevention of massive con-crete structures such as high dams.Because both under-cooling and over-cooling may reduce the ef ficiency of crack prevention,or even lead to great harm to structures,we need an accurate and robust numerical tool for the prediction of cooling effect.Here,a 3D discrete FEM Iterative Algorithm is introduced,which can simulate the concrete temperature gradient near the pipes,as well as the water temperature rising along the pipes.On the basis of the heat balance between water and concrete,the whole temperature field of the problem can be computed exactly within a few iteration steps.Providing the pipe meshing tool for building the FE model,this algorithm can take account of the water pipe distribution,the variation of water flow,water temperature,and other factors,while the traditional equivalent algorithm based on semi-theoretical solutions can only solve problems with constant water flow and water temperature.The validation and convergence are proved by comparing the simulated results and analytical solutions of two standard second-stage cooling problems.Then,a practical concrete block with different cooling schemes is analyzed and the in fluences of cooling factors are investigated.In the end,detailed guidance for pipe system optimization is provided.Copyright ©2015John Wiley &Sons,Ltd.Received 16May 2014;Revised 15February 2015;Accepted 5June 2015KEY WORDS:numerical methods;iterative algorithm;water pipe cooling;transient heat transfer;thermal stress1.INTRODUCTIONMassive concrete structures such as hydraulic dams,sluices,pumping stations,and nuclear plant foundation always suffer crack problems.Research on crack formation and relevant prevention measures remains an important topic for civil engineers.Despite the fact that dry shrinkage,poor material quality,and many other factors may contribute to the cracking,thermal stress is considered as the toughest to treat with for massive concrete structures.Normally,the cement hydration lasts several days for common concrete or weeks for RCC,during which the core temperature will rise signi ficantly without controlling measures [1,2].However,because of the inherent poor heat conductivity of concrete,it may take several years for core temperature to fall down to steady or quasi-steady state in accordance with natural conditions.During the early age after construction,the core temperature is much higher than the surface temperature,and the inner expansion will cause surface cracks.After years of heat emission,the core temperature drops signi ficantly,and then,the inner shrinkage crack may occur under the constraints of surrounding parts.Apparently,to prevent these two major kinds of thermal cracks,the key issue is to control the temperature rising and the inner-surface temperature difference.Many measures have been taken such as cement reduction,aggregate pre-cooling,placing *Correspondence to:J.Cheng,College of Water Conservancy and Hydropower Engineering,Hohai University,Nanjing,210098,China.†E-mail:mscj042@INTERNATIONAL JOURNAL FOR NUMERICAL AND ANALYTICAL METHODS IN GEOMECHANICS Int.J.Numer.Anal.Meth.Geomech.(2015)Published online in Wiley Online Library ().DOI:10.1002/nag.2409J.CHENG ET AL.temperature controlling,and block surface protection[3].Among them,the water pipe cooling proves to be the most efficient and economic.Dating from the1930s,the water pipe cooling technique wasfirst used by the Bureau of Reclamation in Hoover Dam,of which the thin-walled metal pipes were embedded in the concrete block during construction period[1].Since then,it spread over the world from common concrete to roller-compacted concrete(RCC), and from dams to sluices and other structures[4–6].In the1970s,a high-density polyethylene(HDPE)pipe with high thermal conductivity arose and soon took over metal pipe in hydraulic projects,such as Sayano–Shushenskaya Dam and Ertan Dam,because of its greatflexibility for shaping[6].Figure1(a)shows the configuration of Jinping-I Arch Dam with26sections divided by temporary transverse joints.Each dam section was placed layer by layer at a vertical interval of3m.The cooling pipes were usually embedded in horizontal section planes like an S curve shown in Figure1(b),with both vertical and horizontal pipe spacing of about1.2–3.0m.To keep the effectiveness,the pipe length should better not exceed250m. For those huge concrete structures like arch dams,which arefirst built by several parts and then joined together to meet their uneven deformations,the cooling process generally includes two stages.Thefirst-stage cooling begins several hours after the concrete placement,aiming to suppress the maximum concrete temperature rising.Before the joint grouting between neighboring parts,a second-stage cooling is carried out to make the inner temperature decrease till it gets near its static state.There are three essential categories of computation methods for pipe cooling problems:the analytical methods,the equivalentfinite element method(FEM),and the discrete FEM.In1949,the US Bureau of Reclamation obtained thefirst analytical solution in series for second-stage cooling problems via the method of separation of variables,with the following assumptions:(1)both the temperature andflow of cooling water were constant;(2)pipes were equally spaced;and(3)exothermal heating was complete and the concrete temperature was evenly distributed at the start of pipe cooling[7].Another solution in series was given out by Zhu in1956using the Laplace transform method,with amuchFEM ITERATIVE ALGORITHM FOR WATER PIPE COOLING PROBLEMS OF CONCRETEhigher convergence rate.After that,Zhu proposed analytical solutions forfirst-stage cooling problems with metal pipes in1957[8]and non-metal pipes in1999[9].Analytical solutions provide quantitative insight into the cooling effect,but it lacks practical utilization.With these analytical solutions,an equivalent FEM was developed for cooling problems,of which the cooling effect was considered as a negative heat source in an average meaning[10,11].This brought great convenience for the application of FEM.Though without obtaining the real temperature gradient and stress near the pipes,the equivalent algorithm remains to be the most widely used method in engineering practice.The discrete FEM directly simulates the pipes with elements;thus,the inner heat sources and surface convection along interior pipe wall could be considered simultaneously.By the early1990s, three methods were used for the computation of water temperature along the pipes,the simple method,the iteration method,and the prediction method[10].However,requirements for small element size near pipes and consequent large element number made it difficult for practical use.In recent years,great progress has been achieved in the controlling of pipe cooling on account of the informationization of construction and the digitalization of dam data.For this new pipe cooling system often denoted as‘intelligent water-pipe cooling’,the real-time information of concrete temperature, water temperature,waterflow,and other indexes are collected automatically,and the cooling process can be adjusted freely[12].Accordingly,the executive cooling criteria extends from a single maximum allowable temperature to a temperature history curve based on material properties and structure features,and the optimization of cooling scheme can bring benefit in millions of dollars for high dams. With the faintness of traditional semi-theoretical FEM for these innovations,many efforts have been made to provide much more accurate and robust numerical tools for the prediction of cooling effect. Xie et ed a3Dfinite element relocating mesh method to simulate the temperature distribution for different pipe cooling schemes of RCC arch dams during construction and operation period[5]. Kim et al.developed a line element to model the pipe,and the internalflow theory was adopted for calculating the temperature variation of pipe water[13].Yazdi et al.developed a temperature simulation model usingfinite volume method[14].On the basis of the heat balance between concrete and cooling water,Liu proposed a direct algorithm for metal pipe cooling problems,of which the fully coupled finite element equations were established with both the piped water temperature and the concrete temperature as unknown.Thus,the water temperature can be solved directly without iteration[15].In2003,Zhu et al.proposed an FEM that uses the discretefinite element to model the pipes,and the water temperature can be calculated by iterations[16].To distinguish this method from other approaches based on FEM,we call it a‘discrete FEM iteration algorithm’.Without any assumptions,almost all factors can be simulated easily,including pipe cooling parameters,concrete material parameters,and complex boundary conditions.However,this method did not attract much attention until recently when the great progress was achieved in the digitalization of dam data and high performance computing.In this paper,the kernel idea of the3D discrete FEM iterative algorithm for pipe cooling problems of massive concrete is presented.The key items,including the discretization of matrix equation,the calculation of water temperature along the pipe,the iterative algorithm for temperaturefield simulation,and the incremental method for thermal stress calculation,are described,respectively.For those practical problems with complex embedded pipes,a very useful and novel pipe meshing tool is developed on the basis of coarse mesh and pipe distribution information.Then,the two standard second-stage pipe cooling problems are simulated for the verification of the algorithm and its convergence evaluation.Finally,a practical application is provided as an instruction for the proposed method and for the practical design of pipe cooling system.2.THEORY AND METHODOLOGY2.1.Discretized matrix equation of heat conductionTo solve the pipe cooling problems of massive concrete structures above,the3D transient heat conduction governing equation is involved.In the given domainΩincluding the structure and its basement within a certain range,it can be expressed as[17,18]∂∂xλx∂T∂xþ∂∂yλy∂T∂yþ∂∂zλz∂T∂zþQÀc cρ∂T∂t¼0(1)where T=T(x,y,z,t)denotes the temperaturefield at time t;λx,λyλz denote the thermal conductivity in the x,y,and z directions,and for homogenous material,λx=λy=λz=λ;The heat source term Q here has the following form for newly placed concrete:Q¼c cρ∂θ∂t(2)whereθ=θ(t)denotes the adiabatic temperature rise of concrete due to hydration heat;This partial differential equation can be solved with the following initial and boundary conditions, which is known or specified:T¼T0x;y;zðÞ;when t¼t0initial condition(3)T¼T b x;y;z;tðÞonΓT;essential boundary(4)Àλ∂T∂n¼βTÀT aðÞonΓq;convection boundary(5)where T b(x,y,z,t)is the known boundary temperature function or specified function,∂T/∂n is the temperature gradient along the n direction,and for3D problems,it can be expressed as follows:∂T ∂n ¼∂T∂x n xþ∂T∂y n yþ∂T∂z n z(6)and n x,n y,and n z are the direction cosines of the external normal to the boundary.Generally,ΓT includes the bottom of rock-base model where the temperature is specified according to geological information,whileΓq includes the surface in contact with water or air.The above problem can be discretized into elements and solved in the following matrix form using standard FEMs[17]:C_dþKd¼P(7)where C and K are the global specific heat matrix and heat conductivity matrix,P is the load vector, and d and_d are the node temperature vector and its time derivative,respectively.C¼∫Ωc cρN T N dΩ(8)K¼∫Ωλ∂N∂xT∂N∂xþ∂N∂yT∂N∂yþ"∂N∂zT∂N∂z#dΩþ∫Γ3βN T N dΓ(9) P¼∫Ωc cρ∂θ∂t NT dΩþ∫Γ2N T q dΓþ∫Γ3N TβT a dΓ(10)d¼T1T2…T nf g T n is the total node number(11) N is the shape function described in the FEM method.J.CHENG ET AL.Using the weighted residual approximation for temperature field within the time interval Δt =t n+1Àt n ,Eq.7can be written asC =Δt þK ϕðÞd n þ1þÀC =Δt þK 1ÀϕðÞ½ d n ¼P (12)This is the well-known θalgorithm or θmethod for solving the first-order equations.To avoid confusion with the previous mentioned heat generation,here,the weighting parameter ϕis used instead.Different values of φlead to various time difference approximations:(1)ϕ=0,forward-difference approximation (or Euler difference approximation);(2)ϕ=1/2,central-difference approximation (Crank –Nicholson difference approximation);(3)ϕ=2/3,Galerkin difference approximation;;and (4)ϕ=1,backward-difference approximation.Then,the solution of Eq.12yields the following:C =Δt þK ϕðÞd n þ1¼P ÀÀC =Δt þK 1ÀϕðÞ½ d n ¼P þC =Δt þK ϕÀ1ðÞ½ d n(13)It can be written as follows:K C 1d n þ1¼P þK C 2d n(14)where K C1and K C2are working matrices:K C 1¼C =Δt þK ϕ;K C 2¼C =Δt þK ϕÀ1ðÞ(15)The load vector can be calculated as follows:P ¼P n 1ÀϕðÞþP n þ1ϕ(16)Here,ϕ=1is retained in the simulation of this paper.2.2.Calculation of water temperature along the pipe`On the early stage of arti ficial pipe cooling,the temperature difference between concrete and water is comparatively large,which leads to the signi ficant rising of water temperature along the pipes.The water temperature in the inlet of the pipe is preset from refrigeration plant or just from the river because of its source;thus,for solving the pipe cooling problems de fined by Eq.1under conditions Eqs.3–5,the only left to be calculated is the water temperature increase along the pipe.For a typical vertical section of the concrete block in Figure 2(a),the pipes are distributed at a spacing of S H ×S V ,and each pipe only effects a certain part approximating to a column or prism in Figure 2(b,c).As a type of convection boundary de fined in Eq.5,the heat transferfrom Figure 2.Physical model for concrete block embedded with cooling pipe.FEM ITERATIVE ALGORITHM FOR WATER PIPE COOLING PROBLEMS OF CONCRETEconcrete to water can be denoted as follows:q¼Àλ∂T∂n(17)The water temperature increase between two neighboring sections S1and S2of the column is denoted asΔT S.During a very small time interval d t,1.The heat transferred from concrete to water through the inner surfaceΓp of the pipe betweenSection S1and S2can be expressed as follows:d Q p¼∬Γp q i d s d t¼Àλ∬Γp∂Td s d t(18)2.The heat energy of the waterflowing through the inlet section S1isd Q S1¼c wρw q w T S1d t(19)3.The heat energy of the waterflowing through the outlet section S2isd Q S2¼c wρw q w T S2d t(20)In Eqs.19and20,T S1and T S2are the water temperatures in Sections S1and S2.4.The change of the heat energy of the water between S1and S2is as follows:d Q w¼∫S2S1c wρw∂T S∂t d tA p d l(21)where A p is the area of the pipe section,T s denotes the water temperature in any section S,and d l is the distance between S1and S2.According to the heat equilibrium,we haved Q S2¼d Q S1þd Q PÀd Q w(22)Substituting Eqs.18–21into Eq.22,the water temperature increase between S1and S2can be expressed as follows:ΔT S¼T S2ÀT S1¼Àλc wρw q w∬Γp∂T∂n d s d tÀA pq w∫S2S1∂T S∂t d td l(23)Considering that both the volume and temperature increase of water are very small within d l, d Q w is a higher order trace relative to d Q p and can be omitted;thus,Eq.23can be written as follows:ΔT S¼Àλc wρw q w∬Γp∂T∂n d s d t(24)Providing the concrete temperaturefield is known,the above integral can be executed easily on Γp.Because the inlet water temperature T w0is known,we can calculate the water temperature inJ.CHENG ET AL.any section S i by dividing the pipe into m sections and accumulating the temperature increase along the pipe as follows:T S i ¼T w0þ∑i j ¼1ΔT S j ;i ¼1;2;3;…;m (25)2.3.Iterative algorithm for temperature fieldFrom Eq.24,it can be seen that the increase of water temperature along the pipe is in fluenced by the axial temperature gradient of the concrete.Note that the water temperature and the structural concrete temperature interact with each other;we adopt the following iterative algorithm to solve this nonlinear boundary problem.1.At the first step,the water temperature along the pipe at time t =t i is assumed to be constant as equal to the inlet water temperature T w0;then,a temporary transient temperature field T 0(x ,y ,z ,t i )can be calculated.2.On the basis of the computed results T 0,the radial concrete temperature gradient along the pipe (∂T /∂n)0is obtained,as well as the water temperature along the pipe T S 0using Eqs.24and 25.3.With the updated water temperature T S 0,the transient temperature T 1(x ,y ,z ,t i )can be calculated,which is much more close to the real temperature than T (x ,y ,z ,t i ).4.By repeating steps (2)and (3),we can obtain a series of (T S k ,T k (x ,y ,z ,t i ),k =0,1,2,…).When two neighboring series are close enough to ful fill the following condition,stop the iteration,max T k þ1Si ÀT k SiÀÁ<ε;i ¼1;2;3;…;m ;ε>0(26)where k is the iteration times and εis the speci fied tolerance,which can be set as 0.01°C.Normally,2–3iterations will be enough.2.4.Pipe meshing toolThe meshing for discrete FEM algorithm is very time consuming.Here,an effective meshing tool PipeMeshF is developed to create the pipe-embedded mesh model on the basis of a coarse FEM model and the pipe distribution information including inlet elements,corner elements,and outlet paring a coarse model and its associated pipe-embedded model in Figure 3,we can observe the following:1.With the PipeMeshF tool,only those elements that pipes go through are remeshed;thus,the total element number is not enlarged somuch.Figure 3.Finite element meshing for pipe-embedded model using PipeMeshF .FEM ITERATIVE ALGORITHM FOR WATER PIPE COOLING PROBLEMS OF CONCRETE2.Thefine mesh model with embedded pipes can be easily created from a coarse model by any pop-ularfinite element meshing packages,provided that those elements pipes go through are hexahe-dron elements.3.Because most parts of the two models keep the same,the results from discrete algorithm withpipe embedded model and equivalent algorithm with coarse model can be compared conveniently.4.The element density around the pipes can be easily changed,depending on the accuracyrequirement.2.5.Thermal stress calculation for massive concreteBecause thefinal purpose of cooling is to control the stress of massive concrete,here,we briefly introduce the theory used for thermal stress calculation.On the basis of the common FEM approach for mechanical problems,the main idea of time-dependent thermal stress calculation is executed by introducing the following relationship between stress and temperature strain:Δσf g¼DΔεÀΔεTf g(27) where{Δσ}is the stress increment,{Δε}the total strain increment,{ΔεT}the total strain increment, and D the elasticity matrix.Concrete creep and time-dependent elastic modulus are the two fundamental features to distinguish thermal stress of concrete structures from that of others.The modulus of elasticity can be expressed by one of the following two equations:EτðÞ¼E01ÀeÀAτBEτðÞ¼E0τHþτ(28)and the unit creep(creep produced under the action of unit stress)Cr(t,τ)is expressed asCr t;τðÞ¼∑n ci¼1ψi1ÀeÀr i tÀτðÞh i(29)ψi¼f iþg iτÀp i(30) where E0,A,B,H,f i,g i,p i,r i,and n c in Eqs.28–30are material constants.With these two factors considered,we call the thermal stress as elasto-creeping or viscoelastic.To reduce the large memory requirement for recording the stress history in the process of creep strain computation,B.F.Zhu proposed an implicit incremental method with unequal time intervals as shown in Figure 4.For this method,the relation between stress increment vector andstrainFigure4.Incremental method for stress calculation.J.CHENG ET AL.increment vector for complex stress state is derived:Δσn f g ¼D n ÂÃΔεn f g Àηn f g ÀΔεT nÈÉÀÁ(31)where D n ÂüE n Q ½ À1;E n ¼E τn ðÞ1þE τn ðÞC t n ;;τn ðÞ;τn ¼τn À1þτn ðÞ=2(32)and ηn is an intermediate variable for calculation the creep strain:ηn ¼∑n c i 1Àe Àr i Δτn ÀÁωi ;n ÈÉωi ;n Èɼωi ;n À1ÈÉe Àr i Δτn À1þQ ½ Δσn À1f g ψi τn À1ðÞe À0:5r i Δτn À1ωi ;1ÈɼQ ½ Δσ0f g ψi τ0ðÞ(33)Here,only the main formulas are collected to save space;more detail about matrix [D],[Q],[Q]À1and the deduction of the implicit method can be found in Reference [6].3.METHOD VERIFICATION AND DISCUSSIONAs indicated in Section 2.2,the concrete region controlled by each pipe can be approximated to a column or prism.Here,a second-stage arti ficial cooling problem for a single concrete column is analyzed by the proposed method to investigate its performance.The problem ful fills the three assumptions mentioned in the third paragraph of introduction,and the column section is shown in Figure 5(a).With an isolated external boundary and without heat source,it possesses analytical solutions for both conditions of metal pipes and HDPE pipes.The initial temperature difference between the concrete and cooling water is de fined as T 0.Other parameters are taken as c =0.016and b /c =100.For the numerical implementation based on the proposed method,four schemes (named as M1T1,M1T2,M2T1,and M2T2,respectively)with different mesh models (named as Mesh1and Mesh2)and time marching schemes (named as TList1and TList2)are computed and compared.Both mesh models are created in a way that the element size d increases along the axis with a constant ratio.As shown in Figure 5(b,c),N Div means the division number of the radius,d max the maximum element size along the axis,and d min the maximum element size along the axis.Two time marching schemes are set asfollows:Figure 5.A single concrete column embedded with cooling pipe.(a)Schematic of section plane;(b)Mesh1,N Div =20,d max /d min =10,d min =0.0198m;(c)Mesh2,N Div =40,d max /d min =20,d min =0.00614m.FEM ITERATIVE ALGORITHM FOR WATER PIPE COOLING PROBLEMS OF CONCRETETList1:0.05,0.15,0.25,0.5,1,1.5,2,2.5,3,4,5,6,8,10,12,14,17,20,25,30,35,40,50,60,70,80,90,100;(unit:day)TList2:0.01,0.02,0.03,0.04,0.05,0.075,0.1,0.125,0.15,0.175,0.2,0.225,0.25,0.3,0.35,0.4,0.45,0.5,0.75,1,1.25,1.5,1.75,2,2.25,2.5,2.75,3,3.5,4,4.5,5,5.5,6,7,8,9,10,11,12,13,14,16,18,20,24,28,32,36,40,45,50,55,60,65,70,75,80,85,90,95,100;(unit:day)Thus,M1T1means the combined scheme with Mesh1and TList1,and similarly M1T2with Mesh1and TList2.The numerical solutions are compared and analyzed for metal pipes and HDPE pipes,respectively.3.1.Second-stage arti ficial cooling with metal pipesWhen the pipe in Figure 5(a)is made of metal,the internal boundary for the concrete column is almost equal to the water temperature because of the high conductivity coef ficient of metal.Analytical solution of temperature field is given by [6]via the Laplace transform method:T r ;τðÞ¼T 0∑∞n ¼12e Àα2n b 2a τ=b 2αn b ÁJ 1αn b ðÞY 0αn r ðÞÀY 1αn b ðÞJ 0αn r ðÞR αn b ðÞ(34)Figure 7.Analytical temperature solution along the radius at different times (N order =5,e T r =2.64e À2).Figure 6.Analytical temperature solution along the radius at different times (N order =3;e T r =3.91e À2).R αn b ðÞ¼c =b ðÞJ 1αn b ðÞY 1αn c ðÞÀJ 1αn c ðÞY 1αn b ðÞ½þJ 0αn c ðÞY 0αn b ðÞÀJ 0αn b ðÞY 0αn c ðÞ½ (35)where both the temperature field T (r ,τ)at t =τand initial temperature T 0at t =0are de fined on a relative temperature coordinate with water temperature as the origin;J 0and J 1are the first and second orders of the Bessel function of the first kind;Y 0and Y 1are the first and second orders of the Bessel function of the second kind;and αn b is the root of the following characteristic equation:J 1αn b ðÞY 0αn c ðÞÀJ 0αn c ðÞY 1αn b ðÞ¼0(36)Note that the analytical solutions in Eq.34are given in series and that the different numbers of order N order we retain may greatly in fluence their accuracy.The solutions with N order =3,5,and 10for this problem are shown in Figures 6–9where a normalized temperature T /T 0,distance r x /b and time a τ/D 2are used for ing the following relative error notation,e Tr ¼T =T 0ðÞmax À1(37)we obtain the relative error of analytical solutions with N order =1,2,3,4,5,10,and 20as e Tr =5.51e À2,4.19e À2,3.91e À2,3.29e À2,2.64e À2,1.66e À3,and 9.3e À7.It can be seen that N order has great effecton Figure 9.Analytical temperature history for different points along the radius.(N order =10).Figure 8.Analytical temperature solution along the radius at different times (N order =10;e T r =1.66e À3).the accuracy of the temperature especially when the time a τ/D 2is small.Because N order >10,the relative error e Tr is less than 0.167%,which can be enough for engineering purposes.Here analytical solutions with N order =20are taken for comparison with the numerical results in Sections3.1and 3.2.The temperature results at three time points for different computation schemes are compared in Figures 10–12,as well as the relative error,which is de fined as follows:e T ¼T =T 0ðÞsim ÀT =T 0ðÞana (38)where the subscript ‘sim ’means simulation results and ‘ana ’means analytical solutions with N order =20.We can conclude the following:(1)simulated results for all schemes are close to analytical solutions,which proves the ef ficiency of the proposed algorithm;(2)for a certain time step list,when the mesh is re fined,the results become much more accurate and closer to the analytical solutions;and (3)for a certain mesh model,when the time step is decreased,the results become much farther from the analytical solutions.This phenomenon of convergence seems strange but can be clari fied well as follows.Remark 1Errors of numerical methods generally include two parts:one due to mesh model and the other from time marching schemes.Here,for the second-stage cooling problem and for the backward-difference approximation (ϕ=1),Eq.12can be deduced asFigure 10.Temperature along the radius and its relative error.(a τ/D 2=0.0781).Figure 11.Temperature along the radius and its relative error (a τ/D 2=0.3906).。