受热面的腐蚀问题及对策
【知识点】锅炉高温腐蚀、高温氧化和低温腐蚀

【知识点】锅炉高温腐蚀、高温氧化和低温腐蚀一、锅炉的腐蚀。
1、锅炉受热面通常指接触火焰或者烟气一侧是金属表面积,另一侧是水或者导热油,用来进行热交换的金属表面。
包括过热器、再热器、省煤器、水冷壁、SCR、烟道冷凝器、空气预热器等。
2、锅炉受热面一般有两种腐蚀:高温腐蚀、高温氧化和低温腐蚀,主要介质为硫酸盐和硫化物的腐蚀。
二、高温腐蚀及其预防措施1、高温腐蚀:锅炉受热面管子,在高温情况下,烟气侧和蒸汽侧均有发生腐蚀的可能性。
烟气对管壁的高温腐蚀,主要是灰中的碱金属在高温下升华,与烟气中的SO3生成复合硫酸盐,在550—710℃范围内呈液态凝结在管壁上,破坏管壁表面的氧化膜,即发生高温腐蚀。
另外,灰中的钒在高温下升华,并生成V2O5,在550—660℃时凝结在管壁上起催化作用,使烟气中的SO2及O2生成Na2SO4及原子氧(O),对管壁也有强烈的腐蚀作用。
高温腐蚀是反复进行的,它将氧化膜破坏、生成、再破坏,管壁逐渐减薄,最后导致爆管。
燃烧区高温受热面容易产生高温腐蚀、结焦、结渣,2、一般的防护措施:运行中调整好燃烧,控制合理的过剩空气系数,防止一次风冲刷壁面,使未燃烬煤粉在结焦面上停留;合理配风,防止喷燃器附近壁面出现还原性气体。
提高金属的抗腐蚀能力。
降低燃料中的含硫量。
确定合适的煤粉细度。
提高金属的抗腐蚀能力,可以采用抗腐蚀更强的合金钢,或者喷涂抗高温防腐陶瓷涂料。
三、低温腐蚀及预防。
1、低温腐蚀:锅炉尾部受热面(省煤器、空气预热器)的硫酸腐蚀,因为尾部受热面区域的烟气和管壁温度较低。
燃料中的硫燃烧生成二氧化硫(S+O2→SO2),二氧化硫在催化剂的作用下进一步氧化生成三氧化硫(2SO2+O2→2SO3),SO3与烟气中的水蒸气生成硫酸蒸气。
硫酸蒸气的存在使烟气的露点显著升高。
由于空气预热器下部空气的温度较低,预热器下部的烟气温度不高,壁温常低于烟气露点。
硫酸蒸气会凝结在预热器受热面上,造成了硫酸腐蚀。
论锅炉受热面的高温腐蚀-精品文档

论锅炉受热面的高温腐蚀目前在高参数、大容量火电机组中,锅炉受热面的高温腐蚀问题已很普遍且迫切需要解决。
因发生高温腐蚀导致受热面管件损坏严重而被迫停机的事故屡见不鲜。
受热面的高温腐蚀已经成为燃煤锅炉机组安全稳定运行的一大隐患。
在锅炉的设计及运行调整中如稍有不慎则高温腐蚀便很容易发生,腐蚀使得受热面承压部件的管壁变薄,严重时会使受热面管子在短时间内爆管,导致锅炉漏泄而被迫停机或事故跳机。
可见其迫害程度非常之大,在运行中必须避免受热面的高温腐蚀。
1高温腐蚀的形成机理所谓高温腐蚀是指在煤粉锅炉高温火焰及高温烟气区,过热器和再热器管子及其悬挂件产生的外部腐蚀。
锅炉受热面的高温腐蚀是一个复杂的物理化学过程。
与其他有关煤的反应机理一样,由于煤自身的复杂性以及迄今对它的认识有限,这类机理都是粗糙的和带有推理性的,在结论的定量上也都具有相当宽的范围。
高温腐蚀多发生在燃烧器区域的水冷壁、高温过热器、高温再热器,亦即受热面管壁金属温度超越一定界限的部位。
从对高温腐蚀的现象及调查研究结果表明,这种腐蚀都是因壁面与积灰层间的一层液相物反应而产生的。
污染后的受热面会受到灰渣和烟气的复杂的化学反应。
高温过热器与高温再热器多布置于烟温高于700-800C的烟道内,管子的外表面积灰由内层、外层两部分组成,内层灰密实,与管子黏结牢固,不易清除;外层灰松散,容易清除。
低熔灰在炉膛内高温烟气区已成为气态,随着烟气流向烟道。
由于高温过热器及高温再热器区域的烟温较高,低熔灰若不接触温度较低的受热面则不会凝固,若接到温度较低的受热面就会凝固在受热面上,形成黏结灰层。
灰层形成后,表面温度随灰层厚度的增加而增加。
此后,一些中、高熔灰粒也被黏附在黏性灰层中。
这种积灰在高温烟气中的氧化硫气体的长期作用下,形成白色的硫酸盐密实灰层,这个过程称为烧结。
随着灰层厚度的增加,其外表面温度继续升高,低熔灰的黏结结束。
但是中熔灰和高熔灰在密实灰层表面还进行着动态沉积,形成松散而且多孔的外层灰。
燃气热水锅炉尾部受热面低温腐蚀问题及预防措施
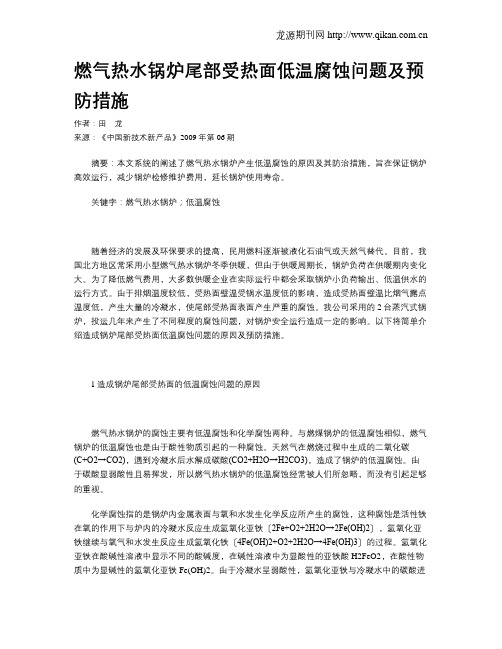
燃气热水锅炉尾部受热面低温腐蚀问题及预防措施作者:田龙来源:《中国新技术新产品》2009年第06期摘要:本文系统的阐述了燃气热水锅炉产生低温腐蚀的原因及其防治措施,旨在保证锅炉高效运行,减少锅炉检修维护费用,延长锅炉使用寿命。
关键字:燃气热水锅炉;低温腐蚀随着经济的发展及环保要求的提高,民用燃料逐渐被液化石油气或天然气替代。
目前,我国北方地区常采用小型燃气热水锅炉冬季供暖,但由于供暖周期长,锅炉负荷在供暖期内变化大。
为了降低燃气费用,大多数供暖企业在实际运行中都会采取锅炉小负荷输出、低温供水的运行方式。
由于排烟温度较低,受热面壁温受锅水温度低的影响,造成受热面壁温比烟气露点温度低,产生大量的冷凝水,使尾部受热面表面产生严重的腐蚀。
我公司采用的2台蒸汽式锅炉,投运几年来产生了不同程度的腐蚀问题,对锅炉安全运行造成一定的影响。
以下将简单介绍造成锅炉尾部受热面低温腐蚀问题的原因及预防措施。
1造成锅炉尾部受热面的低温腐蚀问题的原因燃气热水锅炉的腐蚀主要有低温腐蚀和化学腐蚀两种。
与燃煤锅炉的低温腐蚀相似,燃气锅炉的低温腐蚀也是由于酸性物质引起的一种腐蚀。
天然气在燃烧过程中生成的二氧化碳(C+O2→CO2),遇到冷凝水后水解成碳酸(CO2+H2O→H2CO3),造成了锅炉的低温腐蚀。
由于碳酸显弱酸性且易挥发,所以燃气热水锅炉的低温腐蚀经常被人们所忽略,而没有引起足够的重视。
化学腐蚀指的是锅炉内金属表面与氧和水发生化学反应所产生的腐蚀,这种腐蚀是活性铁在氧的作用下与炉内的冷凝水反应生成氢氧化亚铁〔2Fe+O2+2H2O→2Fe(OH)2〕,氢氧化亚铁继续与氧气和水发生反应生成氢氧化铁〔4Fe(OH)2+O2+2H2O→4Fe(OH)3〕的过程。
氢氧化亚铁在酸碱性溶液中显示不同的酸碱度,在碱性溶液中为显酸性的亚铁酸H2FeO2,在酸性物质中为显碱性的氢氧化亚铁Fe(OH)2。
由于冷凝水呈弱酸性,氢氧化亚铁与冷凝水中的碳酸进一步反应生成碳酸亚铁〔Fe(OH)2+H2CO3→FeCO3+2H2O〕;碳酸亚铁继续与碳酸发生中和反应生成重碳酸亚铁〔Fe(OH)2+H2CO3→Fe(HCO3)2〕;最终碳酸亚铁和重碳酸亚铁与冷凝水中的溶解氧发生氧化-还原反应生成氢氧化铁并释放出二氧化碳:4Fe(CO)3+O2+6H2O→4Fe(OH)3+4CO24Fe(HCO3)2+O2+2H2O→4Fe(OH)3+8CO2如上述铁的腐蚀过程中二氧化碳起了相当大的作用,当二氧化碳融于水变成碳酸后,碳酸经过加热变成蒸汽直接腐蚀金属的表面使锅炉产生低温腐蚀,主要发生在氢氧化亚铁对金属表面的钝化作用还没有形成以前。
锅炉受热面高温腐蚀的机理及防范措施

锅炉受热面高温腐蚀的机理及防范措施锅炉受热面高温腐蚀是指在高温工作条件下,锅炉受热面材料发生化学反应而引起的腐蚀现象。
锅炉受热面高温腐蚀一般分为氧化腐蚀、助燃剂腐蚀、灰腐蚀和酸性腐蚀等几种类型。
为了防止锅炉受热面高温腐蚀,需要采取一系列的防范措施。
首先,氧化腐蚀是指受热面材料与氧气在高温条件下发生反应产生氧化物的腐蚀现象。
为了防范氧化腐蚀,可以通过采用耐高温材料、控制燃烧过程中氧浓度和减少受热面的氧化物形成。
选用高温耐腐蚀材料,如耐热合金、耐火材料等,可以提高受热面材料的耐腐蚀性能。
同时,控制燃烧过程中的氧浓度,降低烟尘氧化反应的速率,可以减少腐蚀的发生。
此外,可以通过脱硫、除尘等措施,减少受热面材料上的氧化物形成,从而降低氧化腐蚀。
助燃剂腐蚀是指在高温条件下,受热面材料与助燃剂中的硫、氯等元素发生反应而引起的腐蚀现象。
为了防范助燃剂腐蚀,可以采用硫氧结合方法、合理控制燃烧过程中的氯量、选择耐蚀材料等措施。
硫氧结合方法是将硫氧结合物(如镁、钙、锶等)加入燃料或燃烧剂中,使之与燃烧过程中产生的SO2等硫化物反应,形成硫氧结合物沉降在受热面上,防止硫腐蚀的发生。
合理控制燃烧过程中的氯量,降低烟尘中氯化物的含量,可以减少助燃剂腐蚀的发生。
此外,选择耐蚀材料,如耐酸钢、耐磨钢等,可以提高受热面的抗腐蚀性能。
灰腐蚀是指在高温条件下,受热面材料与烟尘中的主要成分之一的碱金属发生反应而引起的腐蚀现象。
为了防范灰腐蚀,可以采用降低烟尘中碱金属含量、增加受热面温度和选择耐蚀材料等措施。
降低烟尘中碱金属含量可以通过煤炭处理、喷煤等方式实现。
增加受热面温度,可以使反应速率提高,减少灰腐蚀的发生。
选择耐蚀材料,如耐磨钢、耐酸钢等,可以提高受热面的抗腐蚀性能。
酸性腐蚀是指在高温条件下,受热面材料与燃料中的含硫物质发生反应而引起的腐蚀现象。
为了防范酸性腐蚀,可以采用脱硫、减少燃料中含硫物质、选择耐蚀材料等措施。
脱硫是指通过采用燃烧后脱硫和洗涤法脱硫等方式,降低燃料中硫含量,减少酸性腐蚀的发生。
生物质锅炉受热面高温腐蚀分析及预防

生物质锅炉受热面高温腐蚀分析及预防生物质锅炉受热面腐蚀造成承压部件泄漏是制约生物质机组安全稳定长周期运行的主要原因之一,从而直接影响了生物质发电企业的经济效益。
通过长期分析生物质锅炉运行情况,结合生物质入炉燃料品质不稳定,生物质锅炉燃烧不稳定的特点,除一般锅炉均有发生的汽、水、烟侧腐蚀外,发现造成生物质锅炉受热面腐蚀减薄的主要原因就是高温腐蚀。
所以,如何避免受热面壁温超限就是控制生物质锅炉受热面腐蚀减薄的主要方法。
0引言锅炉受热面腐蚀减薄损坏,一般会造成受热面爆管[1]。
故障一旦发生常导致锅炉故障停炉,涉及范围较大,检查、更换不到位则会重复泄漏停炉,而且检修工作量较大。
国内一些生物质锅炉曾因受热面腐蚀造成一年内停炉十几次,对设备安全运行、电厂经济效益造成巨大影响。
1生物质锅炉受热面腐蚀特点及分析生物质锅炉受热面腐蚀多为高温腐蚀[2]。
高温腐蚀的形成主要包括缺氧、高温、还原性气氛的形成,燃料的腐蚀性元素(氯、钾、硅、铁、铬和硫)含量高等因素,锅炉受热面长期在高温下运行,出现还原氧化交替剥离受热面管排壁面现象,导致管壁达到承压极限值发生爆管[3-4]。
生物质燃料的成分复杂,通过对燃料化验分析得出,燃料可燃成分中硫分较低,氯含量较高,还含有钾、氟等。
灰成分中钾、钠含量高,锰含量高,铝成分较低。
通过分析生物质燃料成分,试验及研究,目前公认的高温腐蚀主要分为气相、固相和液相3种形式。
气相腐蚀即氧化性气氛腐蚀、还原性气氛腐蚀、气态碱金属氯化物腐蚀,主要特点为由于生物质中氯元素的含量较高,气相中含有的氯气及含氯化物与受热面金属反应,加速金属合金的氧化所引起的腐蚀,如图1、2、3所示。
固相腐蚀即沉积物碱金属硫酸盐化腐蚀、沉积物中氯化物对金属表面的腐蚀、碱金属氯化物对金属碳化物的腐蚀,主要特点为烟气中的有害元素在受热面表面凝结、沉积,加速金属合金的氧化所引起的腐蚀,如图4、5、6所示。
液相腐蚀即液相氯化物的腐蚀、液相硫酸盐化腐蚀,主要特点为积灰中的有害元素在受热面表面形成局部液相,增加了受热面腐蚀速率,如图7、8所示。
燃油锅炉尾部受热面积灰腐蚀问题的分析及对策
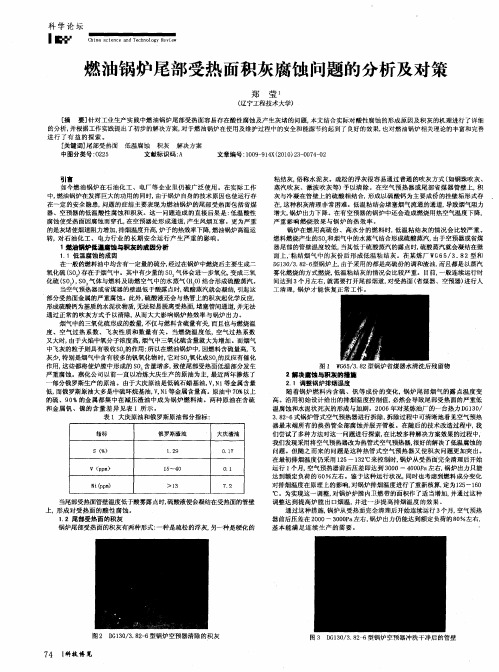
的是灰堵使烟 道阻 力增加, 排烟温度 升高, 炉子 的热 效率下 降, 燃油 锅炉 高温 运 转 , 石 油化 工 、 电力行 业 的 长期 安 全运 行 产 生严 重 的影 响 。 对 1燃 油锅炉 低沮 腐蚀 与 积灰的 戚 因分析 1 1低温腐 蚀 的成 因 . 在 一般的燃 料油中均 含有一定 量的硫分, 经过在锅炉 中燃烧后 主要 生成 二 氧化 硫 (O) 在于 烟气 中。其 中有少 量 的 s , s 。存 O 气体 会进 一步 氧化 , 成三 氧 变 化硫 (O)s s , O 气体 与燃料 及助 燃空 气 中的水 蒸气 (.) 合形 成硫酸 蒸汽 。 HO 结 当空气预 热器 或省煤器 的壁温 低 于酸露 点时, 硫酸蒸 汽就会 凝结, 引起 这 部分 受热 面金属 的严重 腐蚀 。此 外, 硫酸 液还会 与热 管上 的积灰 起化 学反应 , 形成硫 酸钙为基质 的水泥状 物质, 无法轻 易脱离 受热匾 堵塞 管间通道, 并无法 通过 正常 的 吹灰方 式予 以清除, 而大 大影 响锅 炉热 效 率 与锅炉 出力 。 从 烟气 中的三 氧化硫 形成 的数量, 不仅 与燃 料含硫 量有关, 而且 也与 燃烧温 度 、空 气过 热 系数 、 飞灰 性质 和 数量 有 关 。 当燃烧 温 度 低 , 空气 过 热 系数 又大 时, 由于火 焰中氧 分子浓 度高 , 气 中三氧 化硫含 量就 大为增 加 。而烟 气 烟 中飞 灰的粒 子则具 有吸 收s O的作用 : 以在燃 油锅 炉 中, 所 因燃 料 含硫量 高, 飞 灰少, 别是烟 气中含 有较 多的钒 氧化物 时, 特 它对 s 0氧化 成 s O的反 应有催 化 作用, 些都将 使炉膛 中 形成 的 s 这 O 含量 增 多, 致使 尾部受 热面低 温 部分发 生 严重腐 蚀 。燕化 公司 以前一 直 以冶炼 大庆 生产 的原 油为 主, 最近两 年 掺炼 了 部分俄 罗斯 生产 的原油 。 由于大庆 原油 是低硫 石蜡 基油 , , i 金属含 量 VN 等 低, 而俄 罗斯原 油大 多是 中硫 环烷 基油, , i VN 等金属 含量 高 。原油 中 7%以上 0 的硫 、9 %的金 属都 集 中在 减压 渣 油中 成 为锅 炉燃 料油 。两 种原 油 在含 硫 0 和 金 属 钒 、镍 的 含量 差 异 见表 1所 示 。 表 i大庆 原 油和俄 罗斯 原油部 分指 标
垃圾焚烧锅炉受热面高温腐蚀与对策研究

垃圾焚烧锅炉受热面高温腐蚀与对策研究摘要:在垃圾焚烧处理操作中,垃圾所含有大量的氯、硫等元素,在高温的作用下这些元素会形成酸性气体,之后与锅炉受热面上的金属反应,转变成金属氯化物、金属硫化物等腐蚀产物,最终造成锅炉受热面被腐蚀和损坏。
受热面高温腐蚀问题是影响锅炉安全稳定运行的关键因素,所以,垃圾焚烧厂必须明确影响受热面高温腐蚀的相关因素,提出有效的解决对策。
关键词:垃圾焚烧;锅炉;受热面;高温腐蚀;对策垃圾焚烧主要是借助于高温燃烧垃圾,将无机物质转变成废气、灰渣,将有机物质转变成水、二氧化碳,该处理方式具有减量化程度高、无公害、废弃物资源化利用等优点。
因此,当前我国各地纷纷建设垃圾焚烧厂,以进一步缓解垃圾围城的问题。
然而随着垃圾焚烧厂使用时间的增长,锅炉受热面往往会出现高温腐蚀甚至穿管等问题,这些问题会大大降低锅炉运行的安全性与稳定性。
基于此,垃圾焚烧厂必须积极探索可以有效解决锅炉受热面高温腐蚀问题的对策,从而保证自身运行的可靠性与运行效率,减少维护量。
一、垃圾焚烧锅炉受热面高温腐蚀的相关概述在垃圾焚烧处理过程,锅炉内会产生大量具有较强腐蚀性的复杂气体、氯化物与硫酸盐等,这些物质在高温的作用下会导致受热面被腐蚀。
垃圾焚烧锅炉受热面腐蚀大多发生在过热器、预热器、水冷壁等位置。
同时,垃圾组分具有不定性,垃圾焚烧时锅炉内的垃圾燃烧温度与工质参数往往会产生较大范围的波动,致使受热面金属更快疲劳,形成疲劳裂纹,加上外部腐蚀性气体侵蚀裂纹间隙,导致管壁腐蚀速度加快。
据国内外相关实验研究发现:在垃圾焚烧锅炉不同受热面区域(水冷壁、尾部烟道、省煤器、过热器等)的腐蚀情况的模拟分析中,锅炉受热面上的腐蚀与气、液、固多相耦合过程以及烟气中的硫化物、氯化物、碱金属化合物等存在非常密切的联系,且锅炉内气氛、重金属含量等均与腐蚀发生相关[1]。
垃圾焚烧所产生的烟气中含有的固态颗粒和频繁吹灰,也会导致受热面金属管壁腐蚀磨损。
受热面高温腐蚀的原因

受热面高温腐蚀的原因以受热面高温腐蚀的原因为标题,我们来探讨一下这个问题。
高温腐蚀是指材料在高温环境下与气体、液体或固体的化学反应,导致材料表面发生腐蚀破坏的现象。
受热面高温腐蚀是指在受热面上发生的高温腐蚀现象。
下面我们将通过分析,探讨受热面高温腐蚀的原因。
高温环境下的氧化腐蚀是导致受热面高温腐蚀的主要原因之一。
在高温空气中,材料表面的氧化层会与氧气发生化学反应,生成氧化物,从而导致材料表面的氧化腐蚀。
这种氧化腐蚀会破坏材料的表面结构,导致材料的性能下降。
高温环境下的熔融盐腐蚀也是造成受热面高温腐蚀的重要原因。
熔融盐的腐蚀性很强,可以溶解材料表面的氧化层,从而使材料暴露在更为恶劣的腐蚀环境中。
此外,熔融盐还可以与材料表面的金属发生化学反应,生成新的化合物,进一步加剧腐蚀的程度。
高温环境下的硫化物腐蚀也是导致受热面高温腐蚀的一个重要原因。
在含硫的燃料燃烧过程中,生成的硫化物会与金属表面发生反应,形成硫化物产物,从而导致受热面的腐蚀。
这种硫化物腐蚀特点是破坏性强、速度快,对材料的腐蚀作用很严重。
除了以上几种原因外,高温下的氢腐蚀也是导致受热面高温腐蚀的一个重要因素。
在高温下,氢会渗透到材料内部,与金属内部的晶粒界面发生反应,导致金属内部结构的破坏,从而引起受热面的腐蚀现象。
受热面高温腐蚀的原因还包括材料的化学成分、结构和制造工艺等因素。
不同的材料在高温下的耐腐蚀性能是不同的,一些材料具有良好的耐腐蚀性能,而另一些材料则容易受到高温腐蚀的影响。
此外,材料的结构也会影响受热面的腐蚀情况,例如晶界的存在会加剧腐蚀的程度。
制造工艺的不合理也会导致受热面高温腐蚀的发生,例如焊接过程中的气孔和缺陷会使受热面更容易受到腐蚀的侵蚀。
受热面高温腐蚀是在高温环境下材料与气体、液体或固体发生化学反应导致的现象。
高温腐蚀的原因包括氧化腐蚀、熔融盐腐蚀、硫化物腐蚀、氢腐蚀等。
此外,材料的化学成分、结构和制造工艺等因素也会影响受热面的高温腐蚀情况。
- 1、下载文档前请自行甄别文档内容的完整性,平台不提供额外的编辑、内容补充、找答案等附加服务。
- 2、"仅部分预览"的文档,不可在线预览部分如存在完整性等问题,可反馈申请退款(可完整预览的文档不适用该条件!)。
- 3、如文档侵犯您的权益,请联系客服反馈,我们会尽快为您处理(人工客服工作时间:9:00-18:30)。
受热面的腐蚀问题及对策高温腐蚀由于垃圾中水、灰含量较高, 特别是轻质灰和不易燃尽物质较多, 因此烟气中水分、飞灰含量高。
由于垃圾中含氯, 当塑料和盐类分解时,烟气中含一定量的HCl 气体, 其浓度约400~800 Lgö g。
垃圾焚烧炉多采用层燃方式, 易形成还原性气氛, 还原性气氛下, 能生成H2S高温腐蚀性气体。
另外, 烟气中还有N 2、CO 2、CO、SO 2、SO 3、NO x 等成分。
高温腐蚀过程通常过热器工作烟温较高, 管内工质为蒸汽, 换热性能较差, 它是最易发生高温腐蚀的部件。
由碳素钢或碳素合金钢制成的过热器管, 壁面上覆盖有飞灰选择性沉积附着层, 其层理为:金属基体+ 氧化层+ 浸润性附着内层+ 外附着层。
氧化层在投运前已形成, 积灰层在投运后形成并与氧化膜发生浸润性附着。
X 光衍射分析结果[ 4 ] 表明, 在腐蚀过程中, 氧化膜中FeO经中间物相——郁氏体(Fe3O 4在FeO 中的固溶体) 向尖晶磁性氧化铁(Fe3O 4) 转变, 而磁性氧化铁继而向赤色A- Fe3O 4的转变过程中, 还要经由中间物相C- Fe2O 3过渡。
氧化膜具有一定的抗腐蚀能力。
但当烟气中各腐蚀性成分源源不断地传递到管壁外表面, 并开始积聚时, 氧化膜将会破坏。
经过纯气体腐蚀、熔盐腐蚀、固相附着物参与的气体腐蚀、腐蚀气体参与的熔盐腐蚀等一系列复杂的、持续的腐蚀反应,Fe3O 4、Cr2O 3 保护膜都可能脱离金属表面。
因此, 尽管高温腐蚀存在气、液、固多项反应混合发展, 多孔介质中的传递、同相和异相间传递交替发生, 并受晶界过程、电化学过程、应力演变过程等多重因素的共同影响, 但腐蚀性物质向管壁传递是最根本的原因[ 3, 5 ]。
因此, 分析影响高温腐蚀的机理, 宜充分考虑各腐蚀性物质的作用。
防止高温腐蚀, 也宜优先考虑在进入过热器前吸收腐蚀性物质, 降低其浓度, 从而缓解高温条件下的腐蚀反应。
2 高温腐蚀的防护2.1 技术思路最易使人想到的方法是采用抗高温腐蚀的合金钢, 如碳钢, 最大工作温度为750 K, 12% Cr, 1%Mo 钢最大工作温度为855 K。
310号钢最大工作温度大于975 K[ 4 ]。
但提高钢材等级,将使设备造价大幅度增长。
对垃圾进行分选, 将含氯、硫高的物质分出, 不送入炉内焚烧, 但这不仅耗费大量人力工时, 且含氯、硫高的物质,如塑料等, 往往是热值较高的可燃物, 减少可燃物含量, 将影响燃烧稳定。
这种使投资和运行费用增加太多的方法在实际工程中不易推广。
正确的技术思路是, 在经济性和安全性均允许的前提下, 采用较简易的方法, 缓解高温腐蚀。
尽管它不能完全根除高温腐蚀, 但能将腐蚀速度降低到允许的限度, 从而延长设备寿命, 一般能保证一个大修期即可。
2.2 炉内加添加剂在煤粉炉中, 炉内喷钙的脱硫率不高, 约20%~ 40%。
这主要是因为煤粉炉中燃烧温度高, 煤粉停留时间短。
迅速生成的CaSO 3 易将CaO 微孔堵塞, 使尚未反应的CaO、SO 2或SO 3在炉内来不及反应。
在炉中喷石灰石CaCO 3,主要存在以下两个反应,锻烧反应: CaCO3→CaO + CO 2; (31)固硫反应: CaO + SO 2→CaSO 3。
(32)锻烧反应和固硫反应均宜在800~ 950 ℃温度下进行, 煤粉炉炉温一般在1 300 ℃以上,故脱硫率较低。
而垃圾中含水、灰较多, 热值较低, 理论燃烧温度也较低, 对表1中的垃圾进行热力计算, 其理论燃烧温度在980~ 1 435 ℃之间。
对焚烧垃圾锅炉测量炉温, 在750~ 1 000℃之间[ 3 ]。
这一炉温, 正适合于炉内脱硫。
脱硫剂以其脱硫效率而言, 以M g (OH ) 2、Ca (OH ) 2为优, 其次是M gO、CaO , 再次是白云石CaCO 3õM gCO 3, 最低是石灰石CaCO 3。
但其价格则相反, CaCO 3最为廉价, CaO 居中,M g (OH ) 2最昂贵。
2.3 渗铝钢管将母材(通常为普通碳钢管) 通过热浸渗铝(浸渍型或扩散型) , 使钢材表面形成3部分渗层结构, 如表2所示[ 4 ]。
渗铝钢具有复合材料性能,在一些场合能替代优质合金钢, 而造价比优质合金钢大幅度降低。
2.4 燃烧工况调整如式(1)~ (3)、(27)~ (30) , 还原性气氛下加重高温腐蚀, 故可通过如下途径, 避免还原性气氛形成。
2. 4. 1 分级配风如表1, 垃圾中水分多, 前期反应弱; 垃圾中灰分多, 后期反应也弱。
故在炉排前、后均送较少量的风, 而在反应较强烈的中期, 宜加大风量。
分级配风方式如图4所示2. 4. 2 二次风可燃基下, 垃圾中固定碳较少(Crgd= 20%~ 30% ) , 挥发分较多(V r= 70%~ 80% ) , 故以容积反应为主[ 8 ]。
因此, 焚烧垃圾锅炉多做成瘦高炉型, 保证足够的反应空间。
因此, 宜在垃圾层上部送入适量的二次风。
二次风不仅能补充足够的氧气, 而且能加强炉内扰动。
2. 4. 3 喷空气保护膜在腐蚀部位装散风管, 管上布置很多馈风小孔, 热风流过小孔布散在炉管和炉墙间隙中,仍维持一定静压, 可渗入炉衬, 防止腐蚀性介质靠近壁管, 并形成了氧化性气氛, 能抑制高温腐蚀。
3 结束语(1)由于垃圾中含有硫、氯, 而硫、氯及其化合物在一定条件下易对金属壁面产生高温腐蚀, 焚烧垃圾锅炉最易腐蚀的部件是过热器。
(2)影响高温腐蚀的主要因素有, 壁温、材质、腐蚀物含量、烟气中水分含量及炉内气氛等。
(3)防止高温腐蚀较为经济的方法有, 通过加添加剂, 部分吸收腐蚀性物质, 减少烟气中腐蚀性物质含量, 并形成高熔点灰, 减少积灰;采用比优质合金钢价低, 而具有抗高温腐蚀性能的渗铝钢管; 调整燃烧工况, 避免还原性气氛。
低温腐蚀一般来说,烟气中HCL、CL2、SOx对垃圾焚烧锅炉产生高温腐蚀事故频发率较高,往往引起足够的重视。
但低温腐蚀对锅炉受热面破坏作用,亦不应忽视。
某垃圾焚烧厂采用大气式热力除氧器,锅炉给水温度为104℃,布置在锅炉尾部烟道的省煤器仅运行二年就因低温腐蚀原因损坏。
深圳市政环卫综合厂投产之初,1、2号垃圾焚烧锅炉室外烟道采用波纹管式膨胀器,局部截面积较大且裸露在大气中,运行仅一年,就因局部低温而全部腐蚀。
垃圾锅炉产生低温腐蚀主要因素是燃烧烟气中SOx、HCL与H2O的存在,当烟温低于该种气体的饱和温度以下凝结,发生露点腐蚀。
一般HCL露点在27-60℃之间,SOx露点约在110-150℃之间。
通常这种露点腐蚀在酸性气体露点温度以下20-50℃最为严重。
因而,一般垃圾焚烧项目设计将排烟温度控制在露点以上30-50℃,使SOx、HCL与H2O保持在气相,避免在金属受热面表面凝结。
而将布置在垃圾焚烧锅炉尾部烟道的省煤器、空气预热器加热介质温度提高到露点以上,则是避免垃圾焚烧锅炉发生的低温腐蚀现象有郊途径。
在常规燃料锅炉中,SOx是金属受热面产生低温腐蚀的主要原因。
而生活垃圾中,废旧塑料、橡胶、漂白剂、含氯盐类占有一定比例且生活垃圾含水率一般在40-60%之间,因而垃圾焚烧烟气中HCL、SOx等酸性气体和H2O比例较高。
一般生活垃圾焚烧烟气中HCL浓度为200-800mg/Nm3;H2O为15-30%,远远高于常规单一燃料锅炉,是垃圾锅炉发生低温腐蚀的主要因素且越是发达地区垃圾中废旧橡塑与纸、布类成份越多,因而在项目设计中必须引起足够重视。
垃圾锅炉低温腐蚀主要发生在布置在锅炉尾部烟道的空气预热器、省煤器等表面式热交换加热介质入口端。
此外,当排烟温度过低时,锅炉的室外烟道;垃圾锅炉在启动、停炉时,炉温较低时段,锅炉本体金属受热面亦有可能发生低温腐蚀。
垃圾锅炉低温腐蚀防范措施:1.提高锅炉给水温度,热力系统采用压力式除氧器。
垃圾发电厂的除氧器除满足热力除氧外,还作为一级混合式热交换器,加热锅炉给水。
大多数垃圾焚烧发电厂采用压力式除氧器,保持省煤器给水入口端管壁温度始终高于烟气露点,从根本上解决了省煤器低温腐蚀问题。
深圳市政环卫综合处理厂除氧器参数为0.27Mpa(表压),锅炉给水温度为140℃,自1988年投产至今,日本进口的横置双锅筒式1、2号炉对流管段,国产单锅筒式3号炉布置在尾部烟道的省煤器并未发生低温腐蚀现象。
2.提高布置在尾部烟道空气预热器入口风温。
垃圾锅炉采用热风助燃,对提高入炉垃圾烘干速度,改善炉内燃烧工况,起着极其重要的作用。
当前,国内城市生活垃圾低位发热量大多在3350kj/kg-6280kj/kg之间,焚烧锅炉助燃空气温度多选择在250℃,一般设计为二级空气预热器。
第一级采用蒸汽式空气预热器,将助燃空气提高到150-160℃,使布置在尾部烟道的第二级烟气式空气预热器入口风温高过酸性气体露点,避免第二级空气预热器入口端出现低温腐蚀问题。
3.垃圾焚烧锅炉烟气中HCL含量远大于其它类型锅炉,因此应适度提高锅炉排烟温度。
室外烟道尤其需做好保温和防雨措施,避免因烟道局部位置暴露,在烟道内壁发生低温腐蚀。
深圳市政环卫综合厂垃圾锅炉的室外烟道,在发生腐蚀后采用自行设计套接型自由裕度膨胀节,重新制作保温和防护层,排烟温度控制在200℃,运行超过10年,未发生室外烟道低温腐蚀现象。
4.较大型垃圾焚烧锅炉为适应应力释放,启、停炉均有严格的工艺要求,要求按升温和停炉曲线操作。
MARTIN型垃圾焚烧锅炉启动时按50h℃/h升温,在300℃区段保温6h,之后炉膛开始投入垃圾并按100℃/h升至额定温度,停炉亦有相应操作要求。
在起、停炉时段按工艺要求需投人辅助燃油,避免垃圾燃烧烟气在低温时段对金属受热面产生低温腐蚀。
深圳市政环卫综合厂建厂初期曾对日本三菱公司进口的两台垃圾焚烧锅炉进行不投油停炉试验,事后检测两台炉上下锅筒间对流管束外壁结露,Ph值仅为1.5。
因此,垃圾焚烧锅炉启、停炉亦必须严格按工艺规程进行投用辅助燃油操作,避免在该时段发生低温腐蚀。