环己酮生产技术及其工艺路线分析
环己烷氧化制备环己酮
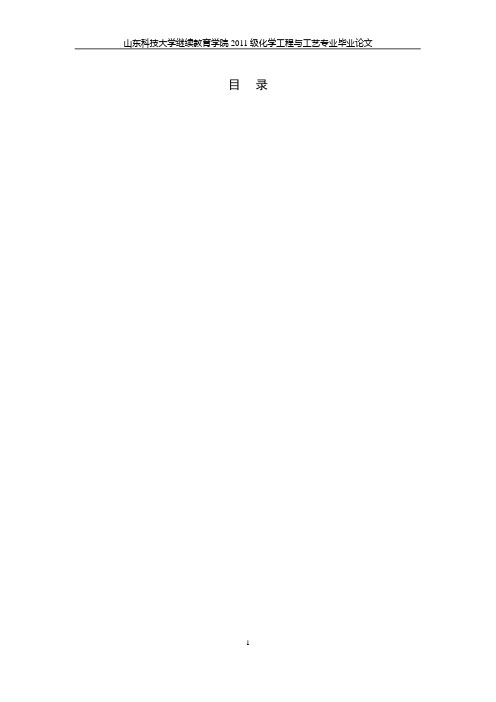
目录环己烷的氧化制环己酮工艺技术作者:指导教师:摘要:环己酮是制备己内酰胺、己二酸的主要中间体,也是制备各种乙烯树脂漆的主要原料,并且被广泛用作许多高分子聚合物的溶剂,因此,环己酮在有机化工、涂料工业等方面都有着极其重要的作用。
目前世界上环己酮生产工艺路线按原料分主要有3种:环己烷液相氧化法、苯酚加氢法和水合法。
山东方明化工有限公司是由环己烷氧化制环己酮,该工序下同时还生成一些其他物质,如环己醇、X油、轻质油等。
合成和制备环己酮的方法较多,工业化生产方法主要有苯酚加氢法;苯部分加氢法;环己烷氧化法。
其中环己烷氧化法的应用最为普遍,本文对以苯为起始原料的合成环己烷然后氧化成环己酮,对公司生产环己酮的过程及原理做了详细叙述,对于生产中出现的异常现象做出合理的解释,也给出其处理方法。
本论文重点介绍了环己烷氧化制备环己酮工艺技术。
关键词:环己烷;环己酮;氧化;进展引言环己酮是一种重要的有机化工产品,是制造尼龙、己内酰胺和己二酸的主要中间体,具有高溶解性和低挥发性,可以作为特种溶剂,对聚合物如硝化棉及纤维素等是一种理想的溶剂;也是重要的有机化工原料,是制备己内酰胺和己二酸的主要中间体。
1893年A. Bayer采用庚二酸和石灰(庚二酸钙)干馏首先合成了环己酮。
1943年德国I.G.Farben公司建成了苯酚加氢法合成环己酮生产装置。
1960年德国BASF公司采用环己烷氧化法建成大型环己酮生产装置,使环己烷氧化技术得以迅速发展,并导致聚酰胺纤维的大规模发展。
本论文突出详述了环己烷氧化制环己酮生产过程。
项目概述公司概况山东方明化工股份有限公司拥有的8万吨/年环己酮装置是目前国内单套最大的环己酮生产装置,采用先进的工艺,各种消耗特别是苯耗、碱耗是国内乃至世界最低的,具有较强的市场竞争力。
公司隶属山东洪业集团,公司董事长余庆明先生是全国五一劳动奖章获得者、并先后荣获全国优秀企业家、山东省劳动模范等荣誉称号,现为山东省人大代表。
环己酮的制备
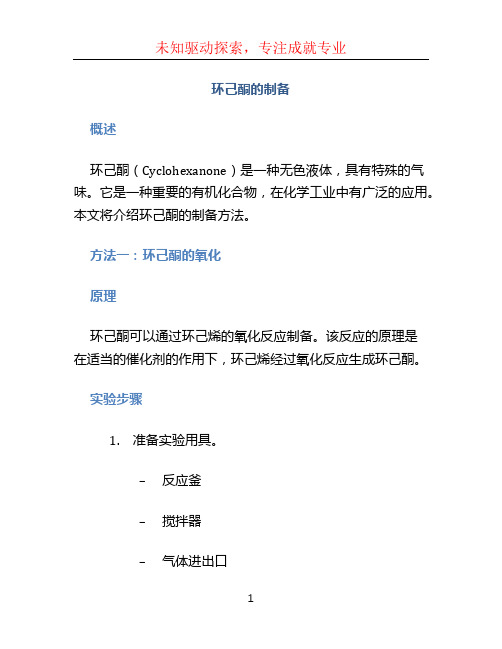
环己酮的制备概述环己酮(Cyclohexanone)是一种无色液体,具有特殊的气味。
它是一种重要的有机化合物,在化学工业中有广泛的应用。
本文将介绍环己酮的制备方法。
方法一:环己酮的氧化原理环己酮可以通过环己烯的氧化反应制备。
该反应的原理是在适当的催化剂的作用下,环己烯经过氧化反应生成环己酮。
实验步骤1.准备实验用具。
–反应釜–搅拌器–气体进出口–温度控制装置2.平衡反应温度和氧气供应。
–将反应釜加热至适宜的温度,保持温度稳定。
–向反应釜中通入氧气,保持适当的氧气供应量。
3.加入催化剂。
–在适量溶剂中溶解催化剂。
–将溶解好的催化剂缓慢加入反应釜中。
4.加入环己烯。
–将环己烯缓慢添加到反应釜中。
–这一步要控制加入速度,避免产生副反应。
5.反应结束。
–观察反应的进程,直到反应结束。
–可通过监测温度的变化和检测反应溶液中环己烯和环己酮浓度的变化来判断反应是否结束。
6.分离环己酮。
–将反应溶液进行蒸馏,将环己酮分离出来。
方法二:环己酮的还原原理环己酮可以通过环己酮的还原反应制备。
该反应的原理是在适当的催化剂的作用下,环己酮经过还原反应生成环己烯。
实验步骤1.准备实验用具。
–反应釜–搅拌器–温度控制装置2.加入催化剂。
–在适量溶剂中溶解催化剂。
–将溶解好的催化剂缓慢加入反应釜中。
3.加入环己酮。
–将环己酮缓慢添加到反应釜中。
–这一步要控制加入速度,避免产生副反应。
4.反应进行。
–观察反应的进行情况,控制反应温度和时间。
–可通过监测温度的变化和检测反应溶液中环己酮和环己烯浓度的变化来判断反应的进行情况。
5.分离环己烯。
–将反应溶液进行蒸馏,将环己烯分离出来。
6.清除催化剂。
–对反应釜进行清洗,将催化剂残留清除。
方法三:环己酮的酰胺加成反应原理环己酮可以通过酰胺加成反应制备。
该反应的原理是环己酮和酰胺在催化剂的作用下发生加成反应生成相应的酰胺产物。
实验步骤1.准备实验用具。
–反应釜–搅拌器–温度控制装置2.加入催化剂。
环己酮生产技术

环己酮装置生产技术二〇一一年一月苯加氢技术1 综述以纯苯和氢氮气为原料,在填充有镍催化剂的反应器中进行加氢反应,生成环己烷,供氧化工序作为原料使用。
2 反应原理主反应C6H6+3H2 C6H12+mol(温度162—173℃附有Ni-AL2O3)副反应①当反应温度高于200℃时,会生成甲基环戊烷:C6H6+3H2 - CH3C6H6+9H2 6CH4↑③温度过高(>600℃)且氢气分压较低时,甲烷进一步深度裂解生成碳:CH4 C+2H2↑④生成的碳与原料气中的氧结合,生成一氧化碳和二氧化:2C+O2 2COC+O2 CO2氧化技术1 综述以环已烷与空气为原料,通过环已烷液相空气氧化,以获得以环已基过氧化氢为主的氧化液,再经水溶性钴盐的定向催化分解作用,将过氧化物分解以获得环已酮、环已醇混合物。
2 反应原理环已烷氧化是一个极为复杂的烃类氧化反应过程。
一般认为其属于链锁反应中的退化支链反应,其反应过程通常可简单表述如下:氧化与分解过程1液态不已烷与空气中的氧在165℃、(G)和无催化剂条件下反应,生成环已基过氧化氢:2.1.2环已基过氧化氢(简称:过氧化物)催化分解生成环已酮和环已醇:过氧化物在酸性,碱性或较高温度等条件下,分解速度加快;在钴盐催化剂存在下,不但使分解反应速度加快,还朝着生成环已酮与环已醇的方向进行,从而可提高分解的收率.环已烷也可直接氧化生成环已醇和环已酮2.1.4环已酮可通过环已醇进一步氧化生成,其过程复杂,且生成量较少,其反应历程可简化写作:2.1.5环已酮与环已醇比环已烷更容易氧化,在氧化过程中发生一系列副反应,生成以已二酸为代表的各种羧酸:2.1.6生成的羧酸与环已醇反应,可生成各种羧酸环已醇酯:皂化过程2.2.1在分解器中,羧酸与氢氧化钠发生中和反应,生成羧酸钠盐和水:2.2.2酯发生水解,生成羧酸盐和环已醇:2.2.3在氧化与分解过程中不可避免地还要生成一些其他酸、酯、杂酮、醛类等杂质,这些杂质在二次皂化过期作废程中,在都转化为高分子的偏聚物等,为有利于在粗馏工序中将基加以分离,从而提高产品环已酮的质量,而采用二次皂化。
环己酮的制备方法
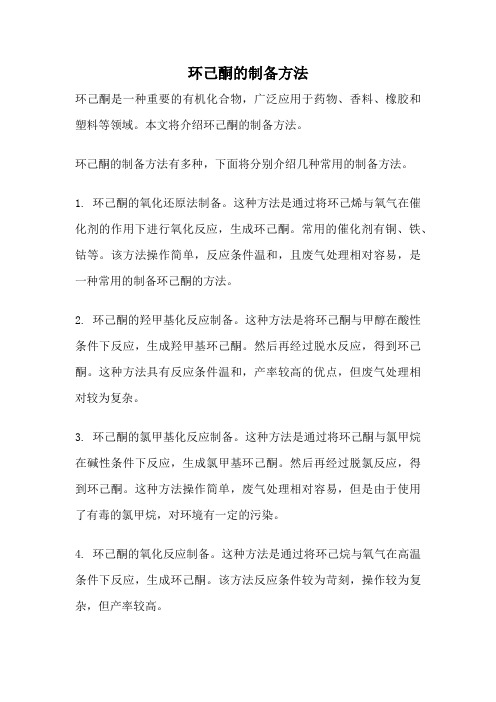
环己酮的制备方法环己酮是一种重要的有机化合物,广泛应用于药物、香料、橡胶和塑料等领域。
本文将介绍环己酮的制备方法。
环己酮的制备方法有多种,下面将分别介绍几种常用的制备方法。
1. 环己酮的氧化还原法制备。
这种方法是通过将环己烯与氧气在催化剂的作用下进行氧化反应,生成环己酮。
常用的催化剂有铜、铁、钴等。
该方法操作简单,反应条件温和,且废气处理相对容易,是一种常用的制备环己酮的方法。
2. 环己酮的羟甲基化反应制备。
这种方法是将环己酮与甲醇在酸性条件下反应,生成羟甲基环己酮。
然后再经过脱水反应,得到环己酮。
这种方法具有反应条件温和,产率较高的优点,但废气处理相对较为复杂。
3. 环己酮的氯甲基化反应制备。
这种方法是通过将环己酮与氯甲烷在碱性条件下反应,生成氯甲基环己酮。
然后再经过脱氯反应,得到环己酮。
这种方法操作简单,废气处理相对容易,但是由于使用了有毒的氯甲烷,对环境有一定的污染。
4. 环己酮的氧化反应制备。
这种方法是通过将环己烷与氧气在高温条件下反应,生成环己酮。
该方法反应条件较为苛刻,操作较为复杂,但产率较高。
5. 环己酮的酮化反应制备。
这种方法是通过将环己醇与氧气在催化剂的作用下进行氧化反应,生成环己酮。
该方法反应条件较为温和,但催化剂的选择和废气处理都需要考虑。
总结起来,环己酮的制备方法有氧化还原法、羟甲基化反应、氯甲基化反应、氧化反应和酮化反应等多种。
不同的方法适用于不同的应用场景,制备过程中需要考虑反应条件、产率和废气处理等因素。
在实际生产中,应根据具体需求选择合适的制备方法。
环己酮装置工艺流程资料

三、工艺流程明
1)苯的原处理及进料 界区外送入的苯进入苯进料预热器,加热到 60℃后进入苯 干燥塔,使苯中所含水份以苯、水共沸物的形式从塔顶蒸出, 经苯干燥塔顶冷凝器冷凝,在苯水分离器中进行苯水分离, 苯溢流回干燥塔,含微量苯的污水排往污水处理站。
脱除水分的苯从苯干燥塔底出来与进料苯在苯进料预热器 中换热,再经出料冷却器用循环水冷却至常温流入苯储槽备 用。加氢催化剂从运输槽车中卸入催化剂贮罐,贮罐用氮气 封闭。开车时,通过开车用催化剂泵把催化剂注入主反应器 底部出料管。当催化剂活性逐渐降低后,通过催化剂泵适时 补加催化剂,以维持反应活性。
6)热回收
循环冷环己烷由冷烷泵从环己烷回流罐抽出,泵出口分 成两股,第一股通过冷却洗涤塔冷却器冷却到 40℃送入冷却 洗涤塔的顶部,用来控制冷却洗涤塔顶的温度,第二股直接 送入冷却洗涤塔上部一、二段填料之间,冷却来自热交换塔 的气相环己烷,冷却洗涤塔塔釜料经洗涤塔釜泵抽出,送入 烷水分离器,顶部气相烷进入热交换塔,底部水和有机液排 往废水汽提塔。循环热环己烷由热烷泵从烷二塔冷凝槽抽出, 送入热交换塔顶部,用于冷却从塔下部进入来自氧化反应的 高温气相环己烷,冷凝的环己烷从塔底流出,经反应系统加 料泵加压,再与反应器进料加热器提升温度后送入氧化反应 器继续循环反应。
分解系统压力 烷一塔系统压力
轻塔操作压力 酮塔操作压力 醇塔操作压力 酮塔顶含酮量 醇脱氢反应温度
单位 ℃
MPa(G) MPa(G) MPa(G) MPa(G) MPa(绝) MPa(绝) MPa(绝) %(wt)
℃
控制参数 160~165
1.2 1.1~1.15
0.4 0.5 真空 真空 真空 >99.8 265
5)氧化
环己烷经反应系统加料泵从热交换塔底抽出,送入进料加 热器,环己烷被壳程蒸汽加热到 159℃,进入串联的六个氧 化反应器中,与加入的空气进行氧化反应,生成环己基过氧 化氢氧化液。从第六氧化反应器流出的氧化液经第一氧化液 换热器、第二氧化液换热器换热冷却到 70℃后送分解工序。
环己酮工艺规程
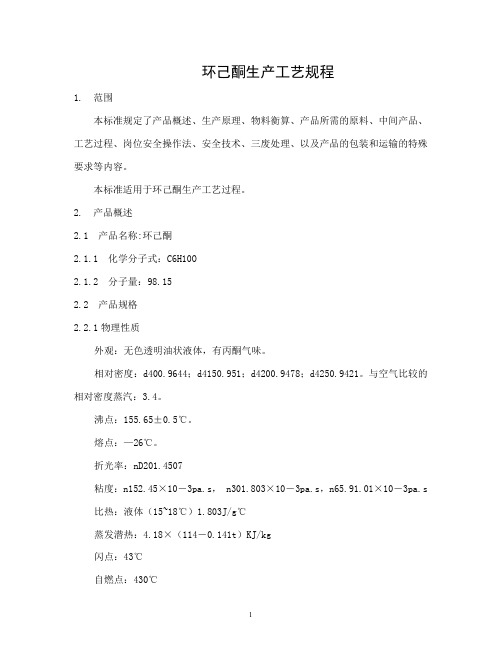
3.1 苯 项目
名称 比重 色度(Pt—Co) 凝固点
指标 石油纯苯 0.882~0.886
≤20 ≥5.4℃
4
总硫 1~96%馏程(包括 80.1℃) H2S 试验 溴指标 酸洗色度 甲苯+甲基环己烷 正庚烷
≤1mg/kg ≤1℃ 阴性 ≤10 ≤1#
≤300mg/kg ≤50mg/kg
3.2 氢气
环己酮生产工艺规程
1. 范围 本标准规定了产品概述、生产原理、物料衡算、产品所需的原料、中间产品、
工艺过程、岗位安全操作法、安全技术、三废处理、以及产品的包装和运输的特殊 要求等内容。
本标准适用于环己酮生产工艺过程。 2. 产品概述 2.1 产品名称:环己酮 2.1.1 化学分子式:C6H10O 2.1.2 分子量:98.15 2.2 产品规格 2.2.1 物理性质
μ s/Cm
max
H2 CL2 H2S CO CO2 温度 压力
项目
指标 ≥99.5% ≤0.1mg/Nm3 ≤0.1mg/Nm3 ≤10mg/Nm3 ≤10mg/Nm3 ≤40℃ ≥78KPa
3.3 液碱 NaOH NaCl
Fe(以 Fe2O3 计)
30%wt~32% 最大 400mg/kg NaOH, 平均 200mg/kg NaOH
≤50mg/kg NaOH
5
3.4 中间产品环己烷
环己烷作为中间产品,产品质量按企业内部质量标准控制。
序号
项目
指标
1
凝固点(℃)≥
6.0
2
馏程(℃)
80.0~81.0
3
芳烃含量(%)≤
0.1
4
非挥发物(g/kg)≤
10
5
环己酮生产工艺
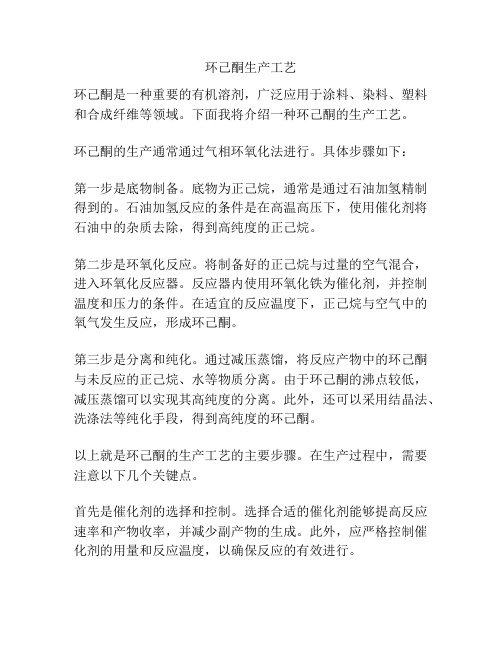
环己酮生产工艺环己酮是一种重要的有机溶剂,广泛应用于涂料、染料、塑料和合成纤维等领域。
下面我将介绍一种环己酮的生产工艺。
环己酮的生产通常通过气相环氧化法进行。
具体步骤如下:第一步是底物制备。
底物为正己烷,通常是通过石油加氢精制得到的。
石油加氢反应的条件是在高温高压下,使用催化剂将石油中的杂质去除,得到高纯度的正己烷。
第二步是环氧化反应。
将制备好的正己烷与过量的空气混合,进入环氧化反应器。
反应器内使用环氧化铁为催化剂,并控制温度和压力的条件。
在适宜的反应温度下,正己烷与空气中的氧气发生反应,形成环己酮。
第三步是分离和纯化。
通过减压蒸馏,将反应产物中的环己酮与未反应的正己烷、水等物质分离。
由于环己酮的沸点较低,减压蒸馏可以实现其高纯度的分离。
此外,还可以采用结晶法、洗涤法等纯化手段,得到高纯度的环己酮。
以上就是环己酮的生产工艺的主要步骤。
在生产过程中,需要注意以下几个关键点。
首先是催化剂的选择和控制。
选择合适的催化剂能够提高反应速率和产物收率,并减少副产物的生成。
此外,应严格控制催化剂的用量和反应温度,以确保反应的有效进行。
其次是反应条件的控制。
环氧化反应是一个放热反应,温度过高会导致副反应的发生,而温度过低则会影响反应速率。
因此,在反应过程中需要精确控制反应温度,确保反应的高效进行。
最后是底物和产物的纯度控制。
正己烷作为底物要保证高纯度,以减少副反应的发生。
而环己酮的纯度可通过适当的分离和纯化工艺来提高,以满足不同领域的需求。
总之,环己酮的生产工艺涉及到底物制备、环氧化反应、分离和纯化等步骤,并需要合理选择催化剂和控制反应条件,以提高产物的纯度和收率。
通过科学的工艺控制,可以实现环己酮的高效生产,满足不同领域的需求。
环己酮生产技术及其工艺路线分析

工 业 中已 内酰胺 的产 量逐 年在 增加 ,同时 对环 己酮 的需 求 量也 越来 越
大 ,因此 ,它具 有广 阔的开发 利用 前景 。
一
源较 低 ,并 且 除却消 耗较 高 的蒸 汽之 外 ,新 鲜水 、电 、天然 气耗 量均
比环 己烷法要 少 。 3 . 环 己烷 法和环 己烯法制 备环 己酮过程 中废物 排放 量的对 比 在 采用 环 己烷 法制 备 环 己酮时 ,由于 只有 7 5 %一 8 0 %的原 料苯 转
。
关 键 词 :环 己 酮
生产 技 术
工 艺路 线
环 己酮作 为一种 重要 的化工 原料和化 工溶 剂 ,既是 制造 己 内酰 胺 、
己二酸 和尼龙 的重要 中间体 ,也可 以用来作 为 甲基 丙烯 酸 、硝化 纤 维 、 氯 乙 烯 聚合 物及 其 共 聚物 的 油漆 等 。伴 随 我 国化 纤工 业 的迅 猛发 展 ,
氧化 生成 环 己酮 的工艺 目前 在国 内外的应 用最 为广 泛。 3 . 环 已烯法 生产环 己酮
三 、有 效提高 环 己酮 生产效 率的合理建 议
首先 ,为 适应 近年 来我 国 己 内酰胺产 量 的增长 速度 ,要在 新建 的
环 己酮装置 中采 取环 己烯 法生产 工艺 路线 。 其 次 ,逐 渐用 先进 的部 分加 氢制 环 己烯 以及水 合制 环 己醇 的环 己 烯法 工艺技 术 ,将 传统 的环 已烷 氧化工 艺取代 。
利 用的 副产 品 ,因而会 带来很 大 的环 保压 力 。而环 己烯 法却 将 9 9 . 5 %
采用 苯酚 法生产 环 己酮 是工业化 生 产最早 用来 制备 环 己酮的方 法 ,
- 1、下载文档前请自行甄别文档内容的完整性,平台不提供额外的编辑、内容补充、找答案等附加服务。
- 2、"仅部分预览"的文档,不可在线预览部分如存在完整性等问题,可反馈申请退款(可完整预览的文档不适用该条件!)。
- 3、如文档侵犯您的权益,请联系客服反馈,我们会尽快为您处理(人工客服工作时间:9:00-18:30)。
环己酮生产技术及其工艺路线分析
摘要:作为一种重要的有机化工原料,环己酮它在工业上主要用来作为有机合成的溶剂及原料,在我国有65%以上的环己酮被当做生产己内酰胺的原料。
本文从环己酮的性质、用途及生产技术着手,对现有的环己酮工艺路线加以对比和分析,提出了一些能够有效提高环己酮生产率的合理建议。
关键词:环己酮生产技术工艺路线
环己酮作为一种重要的化工原料和化工溶剂,既是制造己内酰胺、己二酸和尼龙的重要中间体,也可以用来作为甲基丙烯酸、硝化纤维、氯乙烯聚合物及其共聚物的油漆等。
伴随我国化纤工业的迅猛发展,工业中已内酰胺的产量逐年在增加,同时对环己酮的需求量也越来越大,因此,它具有广阔的开发利用前景。
一、环己酮的生产技术
从起始原料上分,现代工业生产环己酮的主要方法有苯酚法和苯法,后者在工艺上又被氛围环己烯法和环己烷法。
1.苯酚法生产环己酮
采用苯酚法生产环己酮是工业化生产最早用来制备环己酮的方法,其具体过程是,首先在苯酚中添加镍作为催化剂,并通过加氢作用生成环己醇,然后在锌的催化作用下将环己醇脱氢,最后生成环己酮。
这种生产方法工艺路线流程简单,且制得的环己酮产品质量与纯度均很高。
只是苯酚的价格昂贵且材料短缺,因而目前只有少数的几家美国公司利用该工艺技术进行制备环己酮和己内酰胺
的生产[1]。
2.环己烷法生产环己酮
目前有液相加氢和气相加氢两种苯加氢的方法。
后者在工业上的应用比较广泛。
气相加氢法是指将镍或铂作为催化剂放置在固定床中,将一定压力下气相的苯和氢气通过镍铂催化剂床层,使之发生加氢反应,而生成环己烷产物。
然后在空气或贫氧的环境下,令环己烷发生氧化反应,从而得到环己酮及环己醇。
由该方法制得环己酮的过程中,当对环己烷进行氧化反应时还会产生一定数量的副产物,需要加以焚烧处理。
最后,将环己酮和环己醇加以分离,得到纯净的环己酮;并在锌钙等催化作用下对环己醇脱氢,使之转化成环己酮。
采用环己烷氧化生成环己酮的工艺目前在国内外的应用最为广泛。
3.环己烯法生产环己酮
环己烯法生产环己酮是最近新开发出来的一种首先利用苯在钌系作为催化剂的作用下加氢生成环己烯及少量环己烷;再将两者加以分离之后,在硅系作为催化剂的作用下对环己烯(至于环己烷则能被当成副产品进行销售)进行水合反应,形成环己醇;最后利用铜硅作为催化剂,对环己醇进行脱氢反应,从而生成氢气和环己酮
[2]。
二、对环己酮生产技术工艺路线进行对比分析
目前,国内外广泛以石油苯作为原材料来生产环己酮,这种采取苯法生产环己酮工艺中所包括的环己烷法和环己烯法两种工艺,前
者是比较传统的工艺,后者是新近开发的工艺。
现以10万t级规模的石油苯原材,来对两种工艺的原料消耗、能耗以及废弃物排放等加以对比分析。
1.环己烷法和环己烯法制备环己酮过程中消耗主要原料的对比。
这两种工艺技术制备环己酮均以苯和氢气作为主要原料。
其中环己烷法中只有75%-80%的原料苯转化成环己酮,剩余的苯则在环己烷氧化过程中生成一定数量的副产物,这些副产物难以回收,最后被用碱加以中和后再进行焚烧处理。
其中燃气年耗量1600万m3,年耗碱量为1.5万t。
而环己烯法可以将99.5%转化为环己酮和环己烷,其中环己酮的量可达到80%以上,并且消耗的氢和碱均比环己烷法少了很多[3]。
2.环己烷法和环己烯法制备环己酮过程中能源动力消耗的对比由于环己烷法采用的是气相加氢,因而能耗量比较大,并且其氧化过程产生的大量不可回收的副产物在焚烧处理中,还会耗掉一定量的天燃气。
而环己烯法是在液相中进行加氢及水合反应,因而消耗能源较低,并且除却消耗较高的蒸汽之外,新鲜水、电、天然气耗量均比环己烷法要少。
3.环己烷法和环己烯法制备环己酮过程中废物排放量的对比
在采用环己烷法制备环己酮时,由于只有75%-80%的原料苯转化为环己酮产品,而有20%的原料苯则转化成废气、废液等难以回收利用的副产品,因而会带来很大的环保压力。
而环己烯法却将99.5%的苯转化为环己酮及环己烷等产品,其中产生的废气及废液比之环
己烷法减少量达90%以上,并且其产生的废弃物还有部分可以用作清洁燃料,因而很大程度上降低了处理废弃物的消费。
由环己烷法和环己烯法两种工艺方法生产环己酮的原料消耗、能源动力消耗及废弃物排放量对比可知,采用环己烯法能够有效地降低原料及能源的消耗,并且生产的环己酮产品质量良好,同时还产生较少的废弃物排放量,因而大量节省了项目的投资,是一种环境友好型、经济节约型的良好生产工艺路线[4]。
三、有效提高环己酮生产效率的合理建议
首先,为适应近年来我国己内酰胺产量的增长速度,要在新建的环己酮装置中采取环己烯法生产工艺路线。
其次,逐渐用先进的部分加氢制环己烯以及水合制环己醇的环己烯法工艺技术,将传统的环己烷氧化工艺取代。
此外,为了有效提高环己酮的生产效率,还要加强对水合专用催化剂及加氢专用催化剂的深入研究,从而进一步加快国产化的工业步伐[5]。
四、结束语
目前,国内外制备环己酮的方法主要是苯酚法、环己烷法和环己烯法,鉴于苯酚法的材料稀缺和价格昂贵不谈,本文通过对环己烷法和环己烯法所消耗的原料、能源及排放量加以对比,从而得出环己烯法是一种具有循环利用原料、无污染并大量节省资源的优良工艺,因而值得目前我国制备已内酰胺的化工企业大量地推广应用。
参考文献
[1] 任培兵,任雁,张妍等.环己酮生产技术分析[j].化学工业,2010,28(1):120-121.
[2] 陶沙.环己酮生产中皂化废碱液的资源化利用及处理[j].化学工业与工程技术,2010,31(5):158-160.
[3] 谭钦文,尹光志,李斗等.环己酮生产废水处理工程技术改造[j].水处理技术,2008,34(6):182-183.
[4] 周维友,胡炳成,赵乐荣等.hplc-ms/ms联用技术定性定量分析环己酮生产过程中的副产物[j].质谱学报,2009,30(1):131-135.
[5] 刘洪武,金士威,周小文等.环己酮生产过程中苯对环己烷氧化反应的影响[j].武汉工程大学学报,2009,31(3):116-122.。