环己酮工艺规程
环己酮工艺流程

环己酮工艺流程
《环己酮工艺流程》
环己酮是一种重要的有机化合物,广泛应用于工业生产、医药制造、化工领域等。
环己酮的生产工艺流程是一个复杂的过程,需要经过多道工序才能得到高纯度的环己酮产品。
首先,环己酮的生产工艺通常是从环己烷开始。
通过氧化反应,将环己烷氧化为环己醇。
接下来,环己醇会经过脱氢反应,生成环己酮。
这一步骤通常需要利用金属催化剂进行催化反应,以提高反应速率和收率。
随后,得到的环己酮会经过精馏、结晶等物理方法进行分离和提纯。
在这一过程中,需要考虑产品的纯度、收率、设备投资、能耗以及工艺技术水平等因素。
在工艺流程中,通常会配合使用各种先进的分离技术和设备,以提高环己酮的生产效率和质量。
在整个工艺流程中,需要控制反应温度、压力、催化剂用量、溶剂用量等参数,以确保反应的高效进行。
同时,还需要考虑工艺的安全性和环保性,避免废水、废气的排放对环境造成污染和危害。
总的来说,环己酮的生产工艺流程是一个综合性的过程,需要综合考虑反应工程学、分离工程学、机械工程技术、自动化技术等多个方面的知识和技术。
只有在这些方面都达到一定的水
平,才能够将环己酮生产工艺流程进行优化,提高产品质量,降低成本,提高生产效率。
环己酮的制备
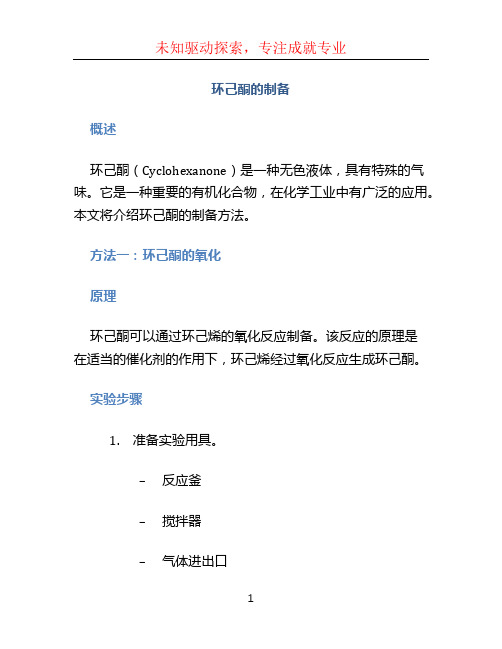
环己酮的制备概述环己酮(Cyclohexanone)是一种无色液体,具有特殊的气味。
它是一种重要的有机化合物,在化学工业中有广泛的应用。
本文将介绍环己酮的制备方法。
方法一:环己酮的氧化原理环己酮可以通过环己烯的氧化反应制备。
该反应的原理是在适当的催化剂的作用下,环己烯经过氧化反应生成环己酮。
实验步骤1.准备实验用具。
–反应釜–搅拌器–气体进出口–温度控制装置2.平衡反应温度和氧气供应。
–将反应釜加热至适宜的温度,保持温度稳定。
–向反应釜中通入氧气,保持适当的氧气供应量。
3.加入催化剂。
–在适量溶剂中溶解催化剂。
–将溶解好的催化剂缓慢加入反应釜中。
4.加入环己烯。
–将环己烯缓慢添加到反应釜中。
–这一步要控制加入速度,避免产生副反应。
5.反应结束。
–观察反应的进程,直到反应结束。
–可通过监测温度的变化和检测反应溶液中环己烯和环己酮浓度的变化来判断反应是否结束。
6.分离环己酮。
–将反应溶液进行蒸馏,将环己酮分离出来。
方法二:环己酮的还原原理环己酮可以通过环己酮的还原反应制备。
该反应的原理是在适当的催化剂的作用下,环己酮经过还原反应生成环己烯。
实验步骤1.准备实验用具。
–反应釜–搅拌器–温度控制装置2.加入催化剂。
–在适量溶剂中溶解催化剂。
–将溶解好的催化剂缓慢加入反应釜中。
3.加入环己酮。
–将环己酮缓慢添加到反应釜中。
–这一步要控制加入速度,避免产生副反应。
4.反应进行。
–观察反应的进行情况,控制反应温度和时间。
–可通过监测温度的变化和检测反应溶液中环己酮和环己烯浓度的变化来判断反应的进行情况。
5.分离环己烯。
–将反应溶液进行蒸馏,将环己烯分离出来。
6.清除催化剂。
–对反应釜进行清洗,将催化剂残留清除。
方法三:环己酮的酰胺加成反应原理环己酮可以通过酰胺加成反应制备。
该反应的原理是环己酮和酰胺在催化剂的作用下发生加成反应生成相应的酰胺产物。
实验步骤1.准备实验用具。
–反应釜–搅拌器–温度控制装置2.加入催化剂。
环己酮的制备
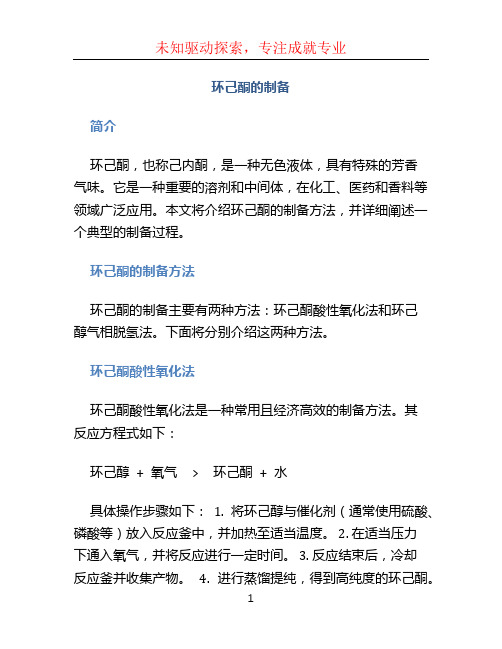
环己酮的制备简介环己酮,也称己内酮,是一种无色液体,具有特殊的芳香气味。
它是一种重要的溶剂和中间体,在化工、医药和香料等领域广泛应用。
本文将介绍环己酮的制备方法,并详细阐述一个典型的制备过程。
环己酮的制备方法环己酮的制备主要有两种方法:环己酮酸性氧化法和环己醇气相脱氢法。
下面将分别介绍这两种方法。
环己酮酸性氧化法环己酮酸性氧化法是一种常用且经济高效的制备方法。
其反应方程式如下:环己醇 + 氧气 > 环己酮 + 水具体操作步骤如下:1. 将环己醇与催化剂(通常使用硫酸、磷酸等)放入反应釜中,并加热至适当温度。
2. 在适当压力下通入氧气,并将反应进行一定时间。
3. 反应结束后,冷却反应釜并收集产物。
4. 进行蒸馏提纯,得到高纯度的环己酮。
1环己醇气相脱氢法环己醇气相脱氢法是另一种制备环己酮的方法。
其反应方程式如下:环己醇 > 环己酮 + 氢气具体操作步骤如下: 1. 将环己醇与催化剂(通常使用碱性金属盐如钾盐或钠盐)与适量的溶剂放入反应釜中。
2. 在适当的温度和压力下进行脱氢反应。
3. 反应结束后,冷却反应釜并通过冷凝器收集环己酮。
典型制备过程下面将详细介绍环己酮的制备典型过程,采用环己酮酸性氧化法。
实验材料•环己醇•硫酸•氧气•反应釜2•冷凝器•蒸馏设备实验步骤1.将100 ml 环己醇倒入反应釜中,并加入10 ml 硫酸作为催化剂。
2.加热反应釜至100150°C,确保硫酸完全溶解在环己醇中。
3.在适当压力下通入氧气,并继续加热反应釜,控制反应时间为23小时。
4.反应结束后,停止加热并冷却反应釜至室温。
将反应产物通过冷凝器收集,并进行进一步蒸馏提纯。
环己酮是一种重要的溶剂和中间体,广泛应用于化工、医药和香料等领域。
本文介绍了环己酮的制备方法,并通过具体的典型制备过程加以说明。
环己酮的制备过程可以选择环己酮酸性氧化法或环己醇气相脱氢法,具体选择取决于实际需求和制备条件。
环己酮装置工艺流程资料

三、工艺流程明
1)苯的原处理及进料 界区外送入的苯进入苯进料预热器,加热到 60℃后进入苯 干燥塔,使苯中所含水份以苯、水共沸物的形式从塔顶蒸出, 经苯干燥塔顶冷凝器冷凝,在苯水分离器中进行苯水分离, 苯溢流回干燥塔,含微量苯的污水排往污水处理站。
脱除水分的苯从苯干燥塔底出来与进料苯在苯进料预热器 中换热,再经出料冷却器用循环水冷却至常温流入苯储槽备 用。加氢催化剂从运输槽车中卸入催化剂贮罐,贮罐用氮气 封闭。开车时,通过开车用催化剂泵把催化剂注入主反应器 底部出料管。当催化剂活性逐渐降低后,通过催化剂泵适时 补加催化剂,以维持反应活性。
6)热回收
循环冷环己烷由冷烷泵从环己烷回流罐抽出,泵出口分 成两股,第一股通过冷却洗涤塔冷却器冷却到 40℃送入冷却 洗涤塔的顶部,用来控制冷却洗涤塔顶的温度,第二股直接 送入冷却洗涤塔上部一、二段填料之间,冷却来自热交换塔 的气相环己烷,冷却洗涤塔塔釜料经洗涤塔釜泵抽出,送入 烷水分离器,顶部气相烷进入热交换塔,底部水和有机液排 往废水汽提塔。循环热环己烷由热烷泵从烷二塔冷凝槽抽出, 送入热交换塔顶部,用于冷却从塔下部进入来自氧化反应的 高温气相环己烷,冷凝的环己烷从塔底流出,经反应系统加 料泵加压,再与反应器进料加热器提升温度后送入氧化反应 器继续循环反应。
分解系统压力 烷一塔系统压力
轻塔操作压力 酮塔操作压力 醇塔操作压力 酮塔顶含酮量 醇脱氢反应温度
单位 ℃
MPa(G) MPa(G) MPa(G) MPa(G) MPa(绝) MPa(绝) MPa(绝) %(wt)
℃
控制参数 160~165
1.2 1.1~1.15
0.4 0.5 真空 真空 真空 >99.8 265
5)氧化
环己烷经反应系统加料泵从热交换塔底抽出,送入进料加 热器,环己烷被壳程蒸汽加热到 159℃,进入串联的六个氧 化反应器中,与加入的空气进行氧化反应,生成环己基过氧 化氢氧化液。从第六氧化反应器流出的氧化液经第一氧化液 换热器、第二氧化液换热器换热冷却到 70℃后送分解工序。
环己酮生产工艺
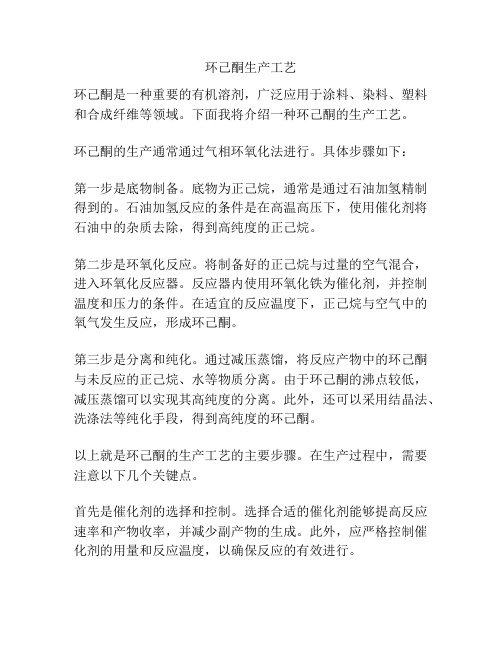
环己酮生产工艺环己酮是一种重要的有机溶剂,广泛应用于涂料、染料、塑料和合成纤维等领域。
下面我将介绍一种环己酮的生产工艺。
环己酮的生产通常通过气相环氧化法进行。
具体步骤如下:第一步是底物制备。
底物为正己烷,通常是通过石油加氢精制得到的。
石油加氢反应的条件是在高温高压下,使用催化剂将石油中的杂质去除,得到高纯度的正己烷。
第二步是环氧化反应。
将制备好的正己烷与过量的空气混合,进入环氧化反应器。
反应器内使用环氧化铁为催化剂,并控制温度和压力的条件。
在适宜的反应温度下,正己烷与空气中的氧气发生反应,形成环己酮。
第三步是分离和纯化。
通过减压蒸馏,将反应产物中的环己酮与未反应的正己烷、水等物质分离。
由于环己酮的沸点较低,减压蒸馏可以实现其高纯度的分离。
此外,还可以采用结晶法、洗涤法等纯化手段,得到高纯度的环己酮。
以上就是环己酮的生产工艺的主要步骤。
在生产过程中,需要注意以下几个关键点。
首先是催化剂的选择和控制。
选择合适的催化剂能够提高反应速率和产物收率,并减少副产物的生成。
此外,应严格控制催化剂的用量和反应温度,以确保反应的有效进行。
其次是反应条件的控制。
环氧化反应是一个放热反应,温度过高会导致副反应的发生,而温度过低则会影响反应速率。
因此,在反应过程中需要精确控制反应温度,确保反应的高效进行。
最后是底物和产物的纯度控制。
正己烷作为底物要保证高纯度,以减少副反应的发生。
而环己酮的纯度可通过适当的分离和纯化工艺来提高,以满足不同领域的需求。
总之,环己酮的生产工艺涉及到底物制备、环氧化反应、分离和纯化等步骤,并需要合理选择催化剂和控制反应条件,以提高产物的纯度和收率。
通过科学的工艺控制,可以实现环己酮的高效生产,满足不同领域的需求。
环己酮生产技术

环己酮生产技术(总8页)--本页仅作为文档封面,使用时请直接删除即可----内页可以根据需求调整合适字体及大小--环己酮装置生产技术二〇一一年一月苯加氢技术1 综述以纯苯和氢氮气为原料,在填充有镍催化剂的反应器中进行加氢反应,生成环己烷,供氧化工序作为原料使用。
2 反应原理主反应C6H6+3H2 C6H12+mol(温度162—173℃附有Ni-AL2O3)副反应①当反应温度高于200℃时,会生成甲基环戊烷:C6H6+3H2 - CH3C6H6+9H2 6CH4↑③温度过高(>600℃)且氢气分压较低时,甲烷进一步深度裂解生成碳:CH4 C+2H2↑④生成的碳与原料气中的氧结合,生成一氧化碳和二氧化:2C+O2 2COC+O2 CO2氧化技术1 综述以环已烷与空气为原料,通过环已烷液相空气氧化,以获得以环已基过氧化氢为主的氧化液,再经水溶性钴盐的定向催化分解作用,将过氧化物分解以获得环已酮、环已醇混合物。
2 反应原理环已烷氧化是一个极为复杂的烃类氧化反应过程。
一般认为其属于链锁反应中的退化支链反应,其反应过程通常可简单表述如下:氧化与分解过程1液态不已烷与空气中的氧在165℃、 (G)和无催化剂条件下反应,生成环已基过氧化氢:环已基过氧化氢(简称:过氧化物)催化分解生成环已酮和环已醇:过氧化物在酸性,碱性或较高温度等条件下,分解速度加快;在钴盐催化剂存在下,不但使分解反应速度加快,还朝着生成环已酮与环已醇的方向进行,从而可提高分解的收率.环已烷也可直接氧化生成环已醇和环已酮环已酮可通过环已醇进一步氧化生成,其过程复杂,且生成量较少,其反应历程可简化写作:环已酮与环已醇比环已烷更容易氧化,在氧化过程中发生一系列副反应,生成以已二酸为代表的各种羧酸:生成的羧酸与环已醇反应,可生成各种羧酸环已醇酯:皂化过程在分解器中,羧酸与氢氧化钠发生中和反应,生成羧酸钠盐和水:酯发生水解,生成羧酸盐和环已醇:在氧化与分解过程中不可避免地还要生成一些其他酸、酯、杂酮、醛类等杂质,这些杂质在二次皂化过期作废程中,在都转化为高分子的偏聚物等,为有利于在粗馏工序中将基加以分离,从而提高产品环已酮的质量,而采用二次皂化。
环己酮的制备
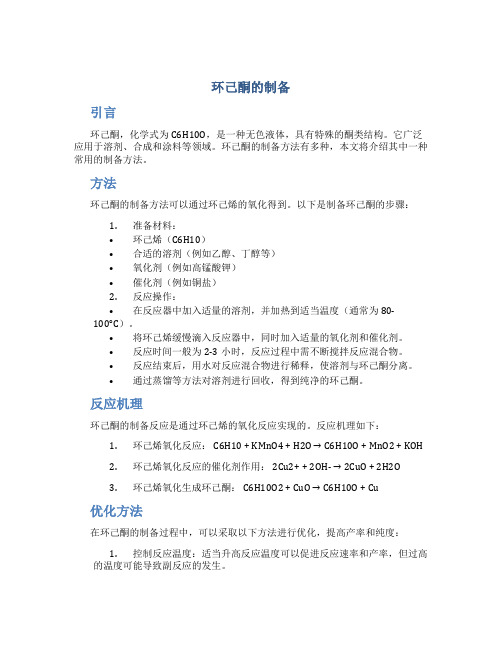
环己酮的制备引言环己酮,化学式为C6H10O,是一种无色液体,具有特殊的酮类结构。
它广泛应用于溶剂、合成和涂料等领域。
环己酮的制备方法有多种,本文将介绍其中一种常用的制备方法。
方法环己酮的制备方法可以通过环己烯的氧化得到。
以下是制备环己酮的步骤:1.准备材料:•环己烯(C6H10)•合适的溶剂(例如乙醇、丁醇等)•氧化剂(例如高锰酸钾)•催化剂(例如铜盐)2.反应操作:•在反应器中加入适量的溶剂,并加热到适当温度(通常为80-100°C)。
•将环己烯缓慢滴入反应器中,同时加入适量的氧化剂和催化剂。
•反应时间一般为2-3小时,反应过程中需不断搅拌反应混合物。
•反应结束后,用水对反应混合物进行稀释,使溶剂与环己酮分离。
•通过蒸馏等方法对溶剂进行回收,得到纯净的环己酮。
反应机理环己酮的制备反应是通过环己烯的氧化反应实现的。
反应机理如下:1.环己烯氧化反应:C6H10 + KMnO4 + H2O → C6H10O + MnO2 + KOH2.环己烯氧化反应的催化剂作用: 2Cu2+ + 2OH- → 2CuO + 2H2O3.环己烯氧化生成环己酮:C6H10O2 + CuO → C6H10O + Cu优化方法在环己酮的制备过程中,可以采取以下方法进行优化,提高产率和纯度:1.控制反应温度:适当升高反应温度可以促进反应速率和产率,但过高的温度可能导致副反应的发生。
2.优化催化剂用量:合适的催化剂用量可以加速反应速率,但过多的催化剂可能降低纯度。
3.改善溶剂选择:选择适合的溶剂可以提高产率和纯度,减少副反应的发生。
4.优化反应时间:适当控制反应时间,避免过长造成产率下降。
5.对产物进行后处理:通过蒸馏等方法对产物进行提纯,提高产物的纯度。
结论通过环己烯的氧化反应,可以制备得到环己酮。
在实际操作过程中,可以通过控制反应条件和优化操作方法来提高产率和纯度。
环己酮作为一种重要的化学品,在溶剂、合成和涂料等领域有广泛的应用前景。
环己酮工艺技术
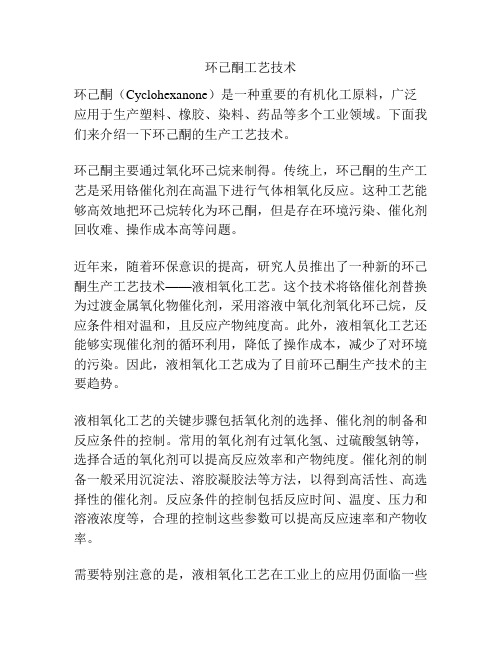
环己酮工艺技术环己酮(Cyclohexanone)是一种重要的有机化工原料,广泛应用于生产塑料、橡胶、染料、药品等多个工业领域。
下面我们来介绍一下环己酮的生产工艺技术。
环己酮主要通过氧化环己烷来制得。
传统上,环己酮的生产工艺是采用铬催化剂在高温下进行气体相氧化反应。
这种工艺能够高效地把环己烷转化为环己酮,但是存在环境污染、催化剂回收难、操作成本高等问题。
近年来,随着环保意识的提高,研究人员推出了一种新的环己酮生产工艺技术——液相氧化工艺。
这个技术将铬催化剂替换为过渡金属氧化物催化剂,采用溶液中氧化剂氧化环己烷,反应条件相对温和,且反应产物纯度高。
此外,液相氧化工艺还能够实现催化剂的循环利用,降低了操作成本,减少了对环境的污染。
因此,液相氧化工艺成为了目前环己酮生产技术的主要趋势。
液相氧化工艺的关键步骤包括氧化剂的选择、催化剂的制备和反应条件的控制。
常用的氧化剂有过氧化氢、过硫酸氢钠等,选择合适的氧化剂可以提高反应效率和产物纯度。
催化剂的制备一般采用沉淀法、溶胶凝胶法等方法,以得到高活性、高选择性的催化剂。
反应条件的控制包括反应时间、温度、压力和溶液浓度等,合理的控制这些参数可以提高反应速率和产物收率。
需要特别注意的是,液相氧化工艺在工业上的应用仍面临一些挑战。
首先,液相氧化反应需要较高的选择性,以防止副反应产生,保证产物的纯度。
其次,在催化剂循环利用过程中,需要对催化剂进行再生和处理,以减少资源浪费和环境污染。
第三,液相氧化工艺的工艺优化和生产规模化仍需进一步研究。
总体来说,环己酮的生产工艺技术正朝着更加环保、高效的方向发展。
液相氧化工艺作为一种新的技术,相比传统的气相氧化工艺具有很多优势,但仍需进一步研究和改进。
相信随着工艺技术的不断突破和创新,环己酮的生产将更加高效、环保,为各个工业领域的发展提供更好的支持。
- 1、下载文档前请自行甄别文档内容的完整性,平台不提供额外的编辑、内容补充、找答案等附加服务。
- 2、"仅部分预览"的文档,不可在线预览部分如存在完整性等问题,可反馈申请退款(可完整预览的文档不适用该条件!)。
- 3、如文档侵犯您的权益,请联系客服反馈,我们会尽快为您处理(人工客服工作时间:9:00-18:30)。
3.1 苯 项目
名称 比重 色度(Pt—Co) 凝固点
指标 石油纯苯 0.882~0.886
≤20 ≥5.4℃
4
总硫 1~96%馏程(包括 80.1℃) H2S 试验 溴指标 酸洗色度 甲苯+甲基环己烷 正庚烷
≤1mg/kg ≤1℃ 阴性 ≤10 ≤1#
≤300mg/kg ≤50mg/kg
3.2 氢气
环己酮生产工艺规程
1. 范围 本标准规定了产品概述、生产原理、物料衡算、产品所需的原料、中间产品、
工艺过程、岗位安全操作法、安全技术、三废处理、以及产品的包装和运输的特殊 要求等内容。
本标准适用于环己酮生产工艺过程。 2. 产品概述 2.1 产品名称:环己酮 2.1.1 化学分子式:C6H10O 2.1.2 分子量:98.15 2.2 产品规格 2.2.1 物理性质
μ s/Cm
max
H2 CL2 H2S CO CO2 温度 压力
项目
指标 ≥99.5% ≤0.1mg/Nm3 ≤0.1mg/Nm3 ≤10mg/Nm3 ≤10mg/Nm3 ≤40℃ ≥78KPa
3.3 液碱 NaOH NaCl
Fe(以 Fe2O3 计)
30%wt~32% 最大 400mg/kg NaOH, 平均 200mg/kg NaOH
≤50mg/kg NaOH
5
3.4 中间产品环己烷
环己烷作为中间产品,产品质量按企业内部质量标准控制。
序号
项目
指标
1
凝固点(℃)≥
6.0
2
馏程(℃)
80.0~81.0
3
芳烃含量(%)≤
0.1
4
非挥发物(g/kg)≤
10
5
密度(kg/m320℃)
778
6
总硫量(mg/kg)≤
2
3.5 公用工程规格 3.5.1 蒸汽
—
—
2.2.4.2 设计产品规格 环己酮≥99.95%,水份 0.013%,轻组份 0.0196%,环己醇 0.013%。
2.2.4.3 用于供己内酰胺生产,质量良好的环己酮至少应具有以下特征: ——丁醇+戊醇+环戊醇,小于 300ppm;(此数据受轻塔操作情况影响) ——环己醇:100 至 200ppm 之间;(此数据受酮塔操作情况影响) ——丁醇+戊醇十环戊醇+环己醇之和应小于 500ppm; ——庚酮:小于 50ppm; ——醛(己醛,庚醛):小于 50ppm;
3
2.2 回收碱(Na2CO3) 2.2.1 碱灰:固体状态
纯度:≥85%(正常生产时>92%) 用途:玻璃等行业 年产量:5387 吨(每天约 17.95 吨) 2.2.2 熔融碱,块状固体(由熔融 Na2CO3 冷却形成) 纯度:≥95% 用途:玻璃等行业 年产量:7230 吨(每天 24.1 吨) 2.3 饱和蒸汽(废碱回收副产) 压力:1.27Mpa 温度:194℃ 年产量:10.8 万吨(每天 360 吨) \\ 3. 产品所需的原料
外观:无色透明油状液体,有丙酮气味。 相对密度:d400.9644;d4150.951;d4200.9478;d4250.9421。与空气比较的 相对密度蒸汽:3.4。 沸点:155.65±0.5℃。 熔点:—26℃。 折光率:nD201.4507 粘度:n152.45×10-3pa.s, n301.803×10-3pa.s,n65.91.01×10-3pa.s 比热:液体(15~18℃)1.803J/g℃ 蒸发潜热:4.18×(114-0.141t)KJ/kg 闪点:43℃ 自燃点:430℃
0.946~0.947 0.944~0.948 0.944~0.948
在 0℃,101.3Kpa 下馏程范
153~157
153~157
152~157
围℃,馏出 95ml 时的间隔温
1.5
3.0
5.0
度℃≤
水份%≤
0.10
0.15
0.30
酸度%(以乙酸计)≤
0.01
0.01
—
折光率
n 20 0
1.499~1.451
2p 轨道和碳的 sp2 杂化轨道重叠形成一个 σ 键,两原子的 2p 轨道侧面又重叠形成
一个 π 键,一起组成双键。C=O 键能为 176—179 千卡/摩,比两个 C—O 键的键能
(2×86 千卡/摩)还大,而酮分子的羰基由于氧原子的电负性比碳原子大,故其有
相当大的极性,对酮的某些化学性质起决定性作用,其易与氢、氢氰酸,亚硫酸氢
蒸汽名称 低压蒸汽(界区内减压) 低压蒸汽(界区内减压) 低压蒸汽(界区内副产减压) 低压蒸汽(装置内副产)
压力 MPa 2.1 1.1 0.5 0.2
温度℃ 216 187 151 120
3.5.2 氮气
纯度 氧
N2≥99.5% ≤100mg/Nm3
6
CO2 C0mg/Nm3 ≤0.02mg/Nm3
温度℃
77.5
90.4
110.3
132.5
155.6
压力 pa 7.998×103 1.333×104 2.666×104 5.332×104 1.013×105
2.2.2 化学性质
分子式 C6H10O
结构式
=O
分子量:98.15
化学特性:环己酮的结构式中,具有羰基(>C=O),羰基中的碳氧双键由氧的
钠,格氏试剂,羟胺,苯胺等物质起加成反应,也能够自身发生羟醛缩合反应。
2.2.3 用途
环己酮主要用于生产己内酰胺,也用于制造防老剂,树脂,溶剂,医药等。
2.2.4 质量标准
2
2.2.4.1 中华人民共和国标准(GB10669-89)
项目名称
优等品
指
标
一等品
合格品
色度(Hazen)≤
15
—
—
密度ρ 20g/cm3
1
爆炸极限:1.1~9.4%(体积)
溶解度:
水在酮中:(wt)10℃ 5.6%;20℃ 5.7%;50℃ 6.5%
酮在水中:(wt)10℃ 10.5%;20℃ 9.0%;50℃ 6.15%
蒸汽压
温度℃
14
26.4
38.7
52.5
67.8
压力 pa 1.333×102 6.665×102 1.333×103 2.666×103 5.332×103
≤2mg/Nm3 -20℃
3.5.3 仪表空气、工厂空气
仪表空气
露点
―40℃
油含量
≤8ppm(wt)
含尘粒径不应大于 3um,含尘量<1mg/m3
压力
0.7Mpa
温度
常温
工厂空气
水含量
饱和(―40℃时)
油含量
无
供应压力
0.7Mpa
供应温度
常温
3.5.4 冷凝回水
压力
MPa(abs)
温度
℃
max
电导率