冲压工艺与模具设计复习知识点
冲压工艺与模具设计复习总结

冲压工艺与模具设计复习总结引言冲压工艺与模具设计是现代制造业中非常重要的一环。
冲压工艺是指通过冲击或压力使板材产生塑性变形,进而得到所需模板形状的一种制造工艺。
而模具设计那么是为了实现冲压工艺需要制造的模具。
本文将从冲压工艺和模具设计两个方面进行复习总结。
冲压工艺复习总结冲压工艺流程冲压工艺的根本流程一般包括:设计图纸准备、材料选择、模具设计和加工、冲压工艺参数确定、冲压件成型、检验和修正。
冲压工艺参数冲压工艺参数是指在冲压过程中控制冲压件形状和尺寸、外表质量以及冲压件的损伤情况的各种参数。
常见的冲压工艺参数包括:冲头和模具间隙、冲头速度、冲头形状、冲头下摆量、引导装置和托板设计等。
冲压损伤冲压过程中,由于材料的塑性变形和外力的作用,冲压件可能会出现各种损伤,如裂纹、皱纹、拉伸变形等。
为了减少冲压损伤,需要合理选择冲压工艺参数,并进行模拟和优化。
冲压材料常见的冲压材料主要包括金属板材和塑料板材。
金属板材常用的有冷轧钢板、热轧钢板、不锈钢板等,而塑料板材那么包括ABS板、聚酰亚胺板等。
不同的冲压材料在冲压工艺和模具设计上具有不同的要求。
冲压工艺的开展趋势随着制造业的开展和技术的进步,冲压工艺也在不断开展。
目前,冲压工艺的开展趋势主要包括:自动化和智能化、快速成型与精密成型、模拟与优化计算等。
模具设计复习总结模具根本要素模具设计中的根本要素包括:模具结构、模具材料、模具加工工艺、模具使用性能等。
其中,模具结构是模具设计中最重要的要素之一,主要包括模具底板、模仁、顶针、导柱等。
模具设计流程模具设计的根本流程包括:产品资料分析、模具三维设计、模具零件设计、模具总装设计、模具加工工艺、模具试制和调试、模具使用与维护等。
模具材料选择模具材料的选择应综合考虑材料的强度、韧性、耐磨性、热稳定性以及切削加工性能等因素。
常用的模具材料有工具钢、合金钢、硬质合金等。
模具设计的关键技术模具设计中的关键技术包括:模具结构设计、模具零件设计、模具安装设计、模具导向设计、模具冷却设计等。
冲压工艺与模具设计复习题(DOC)

第一章概述一、填空、解释、选择类型题:1冷冲压工艺方法大致分为分离工序、成型工序2、分离工序分落料,冲孔和切割等。
成型工序分弯曲、拉深、翻边、翻孔、胀形等。
3冷冲压生产过程的主要特征是依靠冲模和冲压设备完成。
便于实现自动化,效率高。
第二章冷冲压变形基础1•影响金属塑性和变形抗力的因素1,金属组织2•变形温度3.变形速度4•尺寸因素2•塑性条件决定受力物体内质点由弹性状态向塑性状态过度的条件3•加工硬化随变形程度增加,所有强度指标均增加,硬度也增加,同时塑性指标下降的现象4•冲压件的质量指标主要是尺寸精度,厚度变化,表面质量及成形后的物理力学性能。
5•影响工件表面质量的主要因素是原材料的表面状态,晶粒大小,冲压时材料占模2的情况以及对工件的表面擦伤6•反载软化现象是反向加载时材料的屈服应力效拉伸时的屈服应力有所降低,出现所谓反载软化现象7•冷冲压常用材料有:黑色金属,有色金属,非金属材料8板料力学性能与冲压成形性能效为重要的有那几项?p21第三章冲裁一、填空、解释、选择类型题1、冲裁是利用模具使板料产生分离的工序。
从板料沿封闭曲线相互分离,封闭曲线以内的部分作为冲裁件时,称落料,封闭曲线以外的部分作为冲裁件时,称冲孔。
2、冲裁变形过程三个阶段是从弹、塑性变形开始的,以断裂告终。
3、冲裁变形过程使工件断面明显地分成四个特征区:塌角,光面,毛面,和毛刺。
4、影响冲裁件质量的诸多因素中,间隙是主要的因素。
5•分析冲裁件的工艺,主要从冲裁件的结构工艺性,冲裁件的精度和断面粗糙度三方面进行分析6、、凸、凹模刃口的制造公差要按工件的尺寸要求来决定7、冲裁凸、凹模的常以磨钝、与崩刃的形式失效。
8、排样三种方法有废料排样、少废料排样、无废料排样。
9・凸、凹模刃口分开加工法为了保证间隙值应满足的条件| 3制| S d| < Z rn aXmin 10・搭边的作用是补偿定位误差和剪板误差,还可以使条料有一定的刚度,便于送进11・降低冲裁力的方法有材料加热冲裁、阶梯凸模、斜刃冲裁12・冲裁时所产生的总压力包括冲裁力,卸料力,顶件或推件力13・冲模加工方法不同,刃口尺寸的计算方法基本分为两类1凸,凹模分别加工法2凸,凹模配作法14・模具压力中心应该通过压力机滑块的中心线。
冲压与模具设计知识点
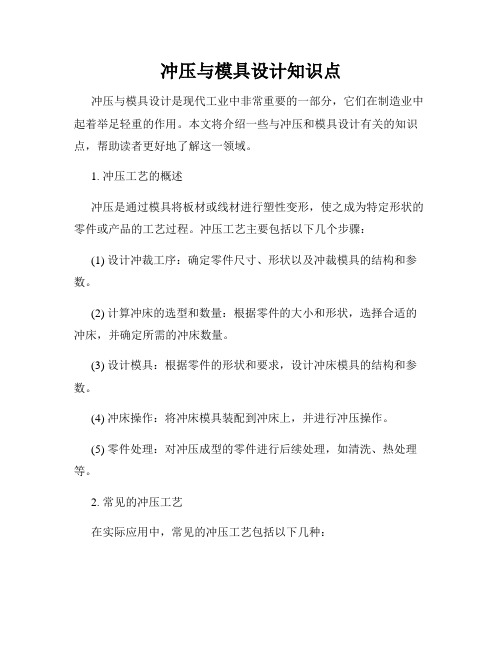
冲压与模具设计知识点冲压与模具设计是现代工业中非常重要的一部分,它们在制造业中起着举足轻重的作用。
本文将介绍一些与冲压和模具设计有关的知识点,帮助读者更好地了解这一领域。
1. 冲压工艺的概述冲压是通过模具将板材或线材进行塑性变形,使之成为特定形状的零件或产品的工艺过程。
冲压工艺主要包括以下几个步骤:(1) 设计冲裁工序:确定零件尺寸、形状以及冲裁模具的结构和参数。
(2) 计算冲床的选型和数量:根据零件的大小和形状,选择合适的冲床,并确定所需的冲床数量。
(3) 设计模具:根据零件的形状和要求,设计冲床模具的结构和参数。
(4) 冲床操作:将冲床模具装配到冲床上,并进行冲压操作。
(5) 零件处理:对冲压成型的零件进行后续处理,如清洗、热处理等。
2. 常见的冲压工艺在实际应用中,常见的冲压工艺包括以下几种:(1) 单冲工艺:利用单个冲头进行冲床操作,适用于简单的零件成型。
(2) 连续冲工艺:通过一次连续的冲压过程,在一张板材上同时冲制多个零件。
(3) 多工位冲工艺:利用多个工作位进行连续冲压,每个工作位上完成一个或多个冲裁工序。
(4) 拉伸冲工艺:将板材拉伸至所需形状,使得材料在冲压过程中得到加工硬化,从而提高强度和韧性。
3. 模具设计的基本原则模具设计是冲压工艺中至关重要的一环,良好的模具设计能够提高生产效率和质量。
以下是一些模具设计的基本原则:(1) 充分考虑冲压力和模具应力:模具设计时要考虑到冲压力的大小和方向,并合理安排模具的结构,以保证模具能够承受冲压力。
(2) 合理选择材料:模具应选择具有足够强度和韧性的材料,以延长模具的使用寿命。
(3) 确定模具结构:根据零件的形状和要求,确定合适的模具结构,包括凸模、凹模、导向装置、顶针等。
(4) 考虑材料利用率:模具设计中要尽量减小废料的产生,提高材料利用率。
4. 模具设计的常见问题与解决方法在模具设计过程中,可能会遇到一些常见的问题,下面是一些常见问题与相应的解决方法:(1) 模具寿命太短:可以选择更耐磨损的材料制作模具或者加入表面处理,如表面硬化、涂层等。
《冲压工艺与模具设计》知识点——精华版
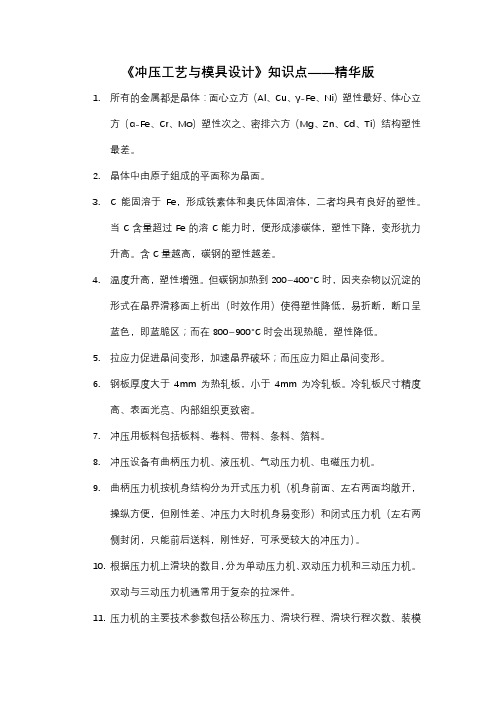
《冲压工艺与模具设计》知识点——精华版1.所有的金属都是晶体:面心立方(Al、Cu、γ-Fe、Ni)塑性最好、体心立方(α-Fe、Cr、Mo)塑性次之、密排六方(Mg、Zn、Cd、Ti)结构塑性最差。
2.晶体中由原子组成的平面称为晶面。
3.C能固溶于Fe,形成铁素体和奥氏体固溶体,二者均具有良好的塑性。
当C含量超过Fe的溶C能力时,便形成渗碳体,塑性下降,变形抗力升高。
含C量越高,碳钢的塑性越差。
4.温度升高,塑性增强。
但碳钢加热到200~400°C时,因夹杂物以沉淀的形式在晶界滑移面上析出(时效作用)使得塑性降低,易折断,断口呈蓝色,即蓝脆区;而在800~900°C时会出现热脆,塑性降低。
5.拉应力促进晶间变形,加速晶界破坏;而压应力阻止晶间变形。
6.钢板厚度大于4mm为热轧板,小于4mm为冷轧板。
冷轧板尺寸精度高、表面光亮、内部组织更致密。
7.冲压用板料包括板料、卷料、带料、条料、箔料。
8.冲压设备有曲柄压力机、液压机、气动压力机、电磁压力机。
9.曲柄压力机按机身结构分为开式压力机(机身前面、左右两面均敞开,操纵方便,但刚性差、冲压力大时机身易变形)和闭式压力机(左右两侧封闭,只能前后送料,刚性好,可承受较大的冲压力)。
10.根据压力机上滑块的数目,分为单动压力机、双动压力机和三动压力机。
双动与三动压力机通常用于复杂的拉深件。
11.压力机的主要技术参数包括公称压力、滑块行程、滑块行程次数、装模高度、工作台面及滑块底面尺寸、漏料孔尺寸、模柄孔尺寸、电动机功率。
12.总冲压力等于冲裁力、卸料力、推件力和顶件力之和。
13.落料尺寸等于凹模尺寸,冲孔尺寸等于凸模尺寸。
14.冲孔件设置压料板、落料件设置顶件器,以减少弯拱回弹、提高冲裁件精度。
15.冲裁间隙决定断面质量,根据理论计算法、查表法、经验记忆法确定冲裁间隙。
16.根据冲裁件受剪切周长(mm)、厚度(mm)、剪切强度(MPa)计算冲裁力。
冲压工艺与模具设计总复习

第一部分概论复习题一、填空题1.冲裁模的工作零件主要有凸模、凹模、凸凹模。
2.按照模具完成的冲压工序内容分,冲压模具可分为单工序模、复合模和级进模。
3.冲压模具的模架基本零件包括了上下模座、导柱、导套。
4.冲压加工的基本工序可分为分离和成型两类。
5.导柱和导套在和模座的装配中,应采用的配合关系是过盈配合 .6.冷冲压工艺在常温下,在压力机上,利用模具对材料施加压力,使其产生分离或塑性变形从而获得所需零件的一种压力加工方法。
7.要使冷冲压模具正常而平稳地工作,必须要求模具压力中心和模柄的轴心线要求重合(或偏移不大)。
8.普通曲柄压力机的闭合度是指滑快在下止点位置时,滑快底面到工作台上平面之间的距离。
模具的闭合高度是指冲模处于闭合状态时,模具上模座上平面至下模座下平面之间的距离。
9.选择压力机时,必须使模具的闭合高度介于压力机的最大闭合高度和最小闭合高度之间。
10.具有过载保护功能的压力机是摩檫压力机。
行程可调的冲床是偏心冲床。
二.选择题1.在设计冲压模的模柄时,模柄的直径和冲床滑块上的模柄孔径相比,只能是 C 。
A 大于B 小于 C等于 D都可以2.在复合模的一次行程动作中,可以完成的冲压工序数是 C 。
A 一次B 只有两次C 两次或两次以上 D三次或三次以上3.下面零件中,属于冲压模成型零件的是 A 。
A 凸模B导套 C 导柱D压边圈4.在单工序冲裁模的一次行程动作中,可以完成的冲压工序数是 A 。
A 一次B 只有两次C 两次或两次以上 D三次或三次以上5.冲压工艺适用于多种金属材料,下面材料中,不适用于冲压工艺的是 C 。
A 铜B钢 C 铸铁D铝6.模柄的作用是将模具的某一部分固定在冲床的滑块上,这部分是 C 。
A 凸模B 凹模C 上模座 D下模座7.下面各种零件中,属于卸料零件的是 C\D 。
A. 凸模B. 导料板C. 压边圈D. 弹簧8.在冲压模中,若采用滑动导柱和导套,则导柱和导套之间采用的配合类型是 A 。
河北工程大学冲压工艺与模具设计考试重点

一、填空题1、冲压是指在常温下安装在(压力机)上的(模具)对材料施加外力,使之(产生塑性变形或分离),从而获得所需形状和尺寸的工件的一种加工方法。
2、冲压加工三要素是指(设备(压力机))、(模具)和(原材料)3、对于伸长类变形,变长区最大的主应力为(拉)应力,其破坏形式为(拉裂),特征是变形区材料厚度(减薄),如胀形。
4、对于压缩类变形,变形区最大的主应力为(压)应力,其破坏形式为(起皱),特征是变形区材料厚度(增厚),如拉深。
5、用间接试验方法得到的板料冲压性能指标有(总伸长率、均匀伸长率、屈强比、弹性模量、硬化指数、塑性应变比r和塑性应变比各向异性系数△r)。
6、在筒形件拉深中如果材料的塑性应变比各向异性系数△r越大,则凸耳的高度(越大)。
7、硬化指数n值越大,硬化效应就越大,这对于(伸长类)变形来说就是有利的。
8、材料对各种冲压加工方法的适应能力称为材料的(冲压成形性能),主要体现为(抗破裂性)、(贴模性)和(定形性)三方面。
9、(σs/σb)的比值称为屈强比。
屈强比(小),对所有的冲压成型工艺都有利10、对冲压材料的基本要求是满足(使用性能的要求),满足(冲压工艺的要求)。
11、曲柄压力机型号JB23-63中,J的意义是:(机械压力机),63的意义是:(630kN)。
12、一般来说,冲裁工艺主要是指(冲孔)和(落料)工序。
13、冲裁变形过程大致可分为(弹性变形)、(塑性变形)、(断裂分离)三个阶段。
14、冲裁件的切断面由(圆角带)、(光亮带)、(剪裂带)、(毛刺)四个阶段。
15、影响冲裁件件尺寸精度的因素有两大方面,一是(冲模本身的制造偏差),二是冲裁结束后冲裁件相对于(凸模或凹模)尺寸的偏差。
16、当间隙较小时,冲裁后材料的弹性恢复使落料件的尺寸(大于)凹模尺寸,冲孔件的尺寸(小于)凸模尺寸。
17、当间隙较大时,冲裁后材料的弹性恢复使落料件的尺寸(小于)凹模尺寸,冲孔件的尺寸(大于)凸模尺寸。
冲压工艺及模具设计知识点
冲压工艺及模具设计知识点冲压工艺及模具设计是在制造业中广泛应用的一项技术。
冲压工艺主要是通过冲压设备对金属板材进行加工,将其压制成所需形状,广泛应用于汽车、家电、电子产品等行业。
而冲压工艺的实施离不开模具设计,合理的模具设计能够提高冲压工艺的效率与质量。
一、冲压工艺知识点1. 材料选择:在冲压工艺中,常用的材料有钢板、不锈钢板、铝板等。
根据实际应用需求,选择合适的材料可以确保产品的性能与可靠性。
2. 冲压工艺流程:冲压工艺一般包括开料、冲孔、剪裁、弯曲、整形等步骤。
不同产品的冲压流程可能有所不同,但整个过程需要严格把控,以确保产品的精度和一致性。
3. 润滑与冷却:在冲压过程中,适当的润滑与冷却是非常重要的。
润滑能够减少模具与材料之间的摩擦,冷却则可以避免材料过热导致变形或破损。
4. 冲压设备与工艺参数:冲压工艺中的设备选择和工艺参数设置直接关系到产品的加工效果。
对于不同的冲压需求,需要选择适合的设备和合理的工艺参数。
5. 质量控制与检测:冲压工艺中的质量控制与检测是确保产品性能可靠性的关键。
通过合理的质量控制措施和严格的检测标准,能够有效提高产品的质量。
二、模具设计知识点1. 模具材料选择:模具的材料一般选择硬度高、耐磨性好的工具钢。
根据冲压工艺的要求和模具的使用寿命,选择合适的材料可以延长模具的使用寿命。
2. 模具结构设计:模具的结构设计对冲压工艺具有重要影响。
合理的模具结构能够提高冲压效率、减少材料浪费,并且方便维修与更换。
3. 模具加工工艺:模具加工工艺包括数控加工、电火花加工等。
不同零部件的加工工艺选择需要考虑加工难度、效率和加工精度等因素。
4. 模具装配与调试:在模具制造完成后,需要进行模具的装配与调试。
合理的装配与调试过程能够确保模具的精度和性能达到要求。
5. 模具维护与管理:模具的维护与管理是保证模具使用寿命的关键。
定期的润滑、清洁和维修工作可以延长模具的寿命,减少生产中的故障和停机时间。
冲压工艺与模具设计复习要点总结
一填空题1.冷冲压的优点有:生产率高、操作简便,尺寸稳定、互换性好,材料利用率高。
2.冷冲压是利用安装在压力机上的模具对材料施加压力,使其产生、分离或塑性变形,从而获得所需零件的一种加工方法。
3.一般的金属材料在冷塑变形时会引起材料性能的变化。
随着变形程度的增加,所有的强度、硬度都提高,同时塑性指标降低,这种现象称为冷作硬化。
4.拉深时变形程度以拉深系数m 表示,其值越小,变形程度越大5.材料的屈强比—小______ ,均匀延伸率大_有利于成形极限的提高。
6. 冲裁件的断面分为 __________________ 圆角,—光面,一毛面,—毛刺四个区域。
7.翻孔件的变形程度用翻孔系数K 表示,变形程度最大时,口部可能出现开裂8.缩孔变形区的应力性质为双向压缩应力,其可能产生的质量问题是失稳起皱9.精冲时冲裁变形区的材料处于三向压应力,并且由于采用了极小的间隙,冲裁件尺寸精度可达IT8-IT6级。
10.冷冲压模具是实现冷冲压工艺的一种工艺装备__一11.落料和冲孔属于分离工序,拉深和弯曲属于成形工序12.变形温度对金属塑性的影响很大,一般来说,随着变形温度的升高,塑性提高变形抗力降低14.材料在塑性变形中,变形前的体积等于变形后的体积,用公式来表示即:£1+£2+£3=0—。
15.冲裁的变形过程分为弹性变形,塑性变形,断裂分离三个阶段。
16.冲裁模工作零件刃口尺寸计算时,落料以凹模为基准,冲孔以凸模为基准,凸模和凹模的制造精度比工件高2-3级_____________17.冲裁件之间及冲裁件与条料侧边之间留下的余料称作_搭边_______ 。
它能补偿条料送进时的定位误差和下料误差,确保冲出合格的制件。
18.弯曲零件的尺寸与模具工作零件尺寸不一致是由于弯曲回弹而引起的_________校正弯曲比自由弯曲时零件的尺寸精度」高—19.拉深时可能产生的质量问题是起皱和开裂__________21用于实现冷冲压工艺的一种工艺装备称为冲压模具22冲压工艺分为两大类、一类叫分离工序,一类是变形工序23物体在外力作用下会产生变形,若外力去除以后,物体并不能完全恢复自己的原有形状和尺寸,称为塑性变形。
冲压工艺与模具设计知识点
冲压工艺与模具设计知识点冲压工艺简介冲压是一种常见的金属成型工艺,通常用于生产大批量金属零部件。
它通过将金属板材置于模具中,然后使用冲压机械对金属进行压制、拉伸、剪切等操作,使得金属板材转化为所需形状的零部件。
冲压工艺具有生产效率高、成本低、精度高等优点,因此广泛应用于汽车制造、家电制造等行业。
冲压工艺流程冲压工艺通常包括以下几个主要步骤:1.材料准备:根据需要的零部件形状和尺寸,选择合适的金属板材进行切割和修整。
2.模具设计:根据零部件的形状和尺寸,设计适用的冲压模具,包括下模和上模。
3.模具加工制造:根据模具设计图纸,进行下模和上模的加工和制造。
4.冲压操作:将金属板材放置于冲压机械中,根据冲压工艺要求,进行压制、拉伸、剪切等操作。
5.零部件处理:对冲压成型的零部件进行去毛刺、抛光等处理,以提高表面质量。
6.检验和品质控制:对冲压零部件进行尺寸、外观等检验,确保产品质量符合要求。
7.包装和发货:将合格的冲压零部件进行包装,并按需求进行发货。
模具设计知识点模具设计是冲压工艺的关键环节,直接影响冲压零部件的质量和生产效率。
以下是一些模具设计的重要知识点:1. 模具结构良好的模具结构能够提高冲压零部件的质量和生产效率。
常见的模具结构包括单向模、复式模和多工位模。
在设计模具结构时,需要考虑零部件形状、尺寸、生产数量等因素,选择合适的结构形式。
2. 模具材料模具材料的选择对模具的寿命和生产成本有重要影响。
常见的模具材料包括合金工具钢、硬质合金等。
在选择材料时,需要考虑模具使用环境、零部件材料等因素,以确保模具具有足够的硬度和耐磨性。
3. 模具零件设计模具零件设计包括模具底板、模具芯、导向柱、导向套等零部件的设计。
在设计模具零部件时,需要考虑强度要求、零部件加工难度、装配精度等因素,以提高模具的使用寿命和生产效率。
4. 模具表面处理模具表面处理能够提高冲压零部件表面质量和模具使用寿命。
常见的表面处理方法包括电镀、喷涂等。
冷冲压工艺与模具设计复习题库
第一章概述1.1 基本概念1.1.1 冷冲压概念1.加压将金属或非金属板料分离、成形或接合而得到制件的工艺装备称为(C)。
A.压铸模B.压缩模C.冲模D.金属模2. 下列不属于冲压加工三要素的是(D)。
A.冲压工艺与模具B.冲压设备C.冲压材料D.冲压件3.加压将金属或非金属板料分离,成形或接合而得到制件的工艺装备称为冲模。
(×)4.冲压是对板料施加压力,使之产生变形或分离,从而获得零件或毛坯的加工方法。
(√)5.冲压加工是一种金属塑性加工工艺,有时又叫做冷冲压或板料冲压。
(√)6.冲模是将材料(金属或非金属)批量加工成所需冲件的专用工具。
(√)7.冲压加工的三要素是冲压成型与模具、冲压设备以及冲压材料。
(×)8.冲压是利用安装在冲压设备(主要是压力机)上的模具对材料施加压力,使其产生分离或9.塑性变形,从而获得所需零件的一种压力加工方法。
(√)1.1.2 冷冲压加工的特点1. 下列说法中,(D)不是冲压生产的特点。
A.生产效率高B.产品互换性好C.材料利用率高D.高温下生产2.冲压加工材料利用率高,可做到少废料或无废料。
(√)3.冲压加工和其他加工方法相比,无论在技术上或是经济效果上,都有很多优点。
(√)4.冲压的制造一般是单件小批量,所以冲压件也是小批量生产。
(×)5.冲压件尺寸精度,主要靠模具确保。
(√)6.冲压加工仅能加工形状简单的零件。
(×)7.冲模的高精度特点是由冲压件的高精度决定的。
(×)8.有同学说,模具的技术含量高,附加值大,凑点钱,多造些模具到市场上销售,定能挣大钱。
(×)1.1.3 冷冲压加工及模具在现代制造业中的地位1.1.4 冷冲压技术及模具的发展趋势1.1.5 课程特点与学习方法1.2 冷冲压基本工序及模具1.冷冲压工序可分成(A)。
A.分离工序和成形工序B.冲孔工序和弯曲工序C.冲裁工序和拉深工序D.成形工序和冲裁工序2.利用冲模使板料相互分离的冲压工序称为(D)。
- 1、下载文档前请自行甄别文档内容的完整性,平台不提供额外的编辑、内容补充、找答案等附加服务。
- 2、"仅部分预览"的文档,不可在线预览部分如存在完整性等问题,可反馈申请退款(可完整预览的文档不适用该条件!)。
- 3、如文档侵犯您的权益,请联系客服反馈,我们会尽快为您处理(人工客服工作时间:9:00-18:30)。
一、板料成形(冲压、冷冲)就是利用安装在压力机上的模具,对板料施加变形力,使板料在模具里产生变形,从而获得一定形状、尺寸与性能的产品零件的一种压力加工方法二、分离工序:指冲压过程中使冲压件与板料沿一定的轮廓相互分离的工序。
基本工序:冲孔、落料、切断、切口、切边、剖切、整修等。
三、冲孔:用冲孔模沿封闭轮廓冲裁工件或毛坯,冲下部分为废料。
四、落料:用落料模沿封闭轮廓冲裁板料或条料,冲下部分为制件。
五、切断:用剪刃或模具切断板料或条料的部分周边,并使其分离。
六、切口:用切口模将部分材料切开,但并不使它完全分离,切开部分材料发生弯曲。
七、塑性成形工序:指材料在不破裂的条件下产生塑性变形,从而获得一定形状、尺寸与精度要求的零件。
基本工序:弯曲、拉深、成形等。
八、弯曲:把平面毛坯料制成具有一定角度与尺寸要求的一种塑性成形工艺。
九、冲压模具的基本结构组成:按模具零件的功能可分为工艺零件与结构零件两部分。
工艺零件:工作零件:凸模、凹模、凸凹模: 结构零件:导向零件:导柱、导套、导板十、冲压模具按工序组合可分为单工序模、级进模、复合模。
十一、冲裁就是利用模具使板料沿一定的轮廓形状分离的一种冲压工序。
主要指落料、冲孔十二、冲裁变形过程:弹性变形阶段、塑性变形阶段、断裂分离阶段、十三、断面特征: 圆角带、光亮带、断裂带十四、冲裁件断面质量影响因素:1)材料的性能对断面质量的影响2)模具刃口状态对断面质量的影响3)模具冲裁间隙大小对断面质量的影响十五、冲裁间隙的概念:指冲裁模的凸模与凹模刃口之间的间隙,也就就是凸、凹模刃口间缝隙的距离。
十六、冲裁间隙对冲裁件质量的影响:冲裁件的质量主要就是指断面质量、尺寸精度与形状误差十七、1、尺寸精度:指冲裁件的实际尺寸与基本尺寸的差值,差值越小则精度越高。
冲裁间隙对冲裁件尺寸精度的影响:当模具制造精度确定后:间隙较大时,拉伸作用增大,落料件尺寸小于凹模尺寸,冲孔孔径大于凸模直径;间隙较小时,挤压力大,落料件尺寸增大冲孔孔径变小。
2 冲裁间隙对冲裁工艺力的影响:间隙小,材料所受压应力增大,拉应力减小,材料不易撕裂,冲裁力增大;间隙增大,材料所受拉应力增大,材料易产生裂纹,冲裁力减小。
3 间隙对模具寿命的影响:间隙小,冲裁力增大,接触压力增大,摩擦力增大,模具发生磨损,模具寿命降低;间隙过大时,板料的弯曲拉伸相应增加,使模具刃口端面上的增压力增大,容易产生崩刃或产生塑性变形使磨损加剧,降低模具寿命。
为提高模具寿命,一般需要采用较大间隙。
十八、凸、凹模刃口尺寸计算的依据与原则:1、先确定基准件(落料:以凹模为基准,间隙取在凸模上;冲孔反之) 2、考虑冲模的磨损规律(落料模: 凹模基本尺寸应取工件尺寸公差范围内的较小尺寸;冲孔模反之) 3、冲裁间隙采用最小合理间隙值(Cmin 单边) 4、凸、凹模刃口制造公差应合理5、尺寸偏差应按“入体”原则标注( 落料件上偏差为零,下偏差为负;冲孔件上偏差为正,下偏差为零)十九、凸、凹模刃口尺寸的计算方法二十、降低冲裁力的措施:阶梯凸模冲裁、斜刃口冲裁、加热红冲二十一、排样:指冲裁件在板料或条料上的布置方式。
目的: 提高材料的利用率冲裁排样的方式:1)有废料排样2)少废料排样3)无废料排样二十二、搭边:指冲裁时制件与制件之间、制件与条料边缘之间的余料。
搭边的作用: 1)能够补偿定位误差,保证冲出合格的制件;2)能保持条料具有一定的刚性,便于送料;3)能起到保护模具的作用。
二十三、影响搭边值大小的因素:1、材料的力学性能2、材料的厚度3、工件的形状与尺寸4、排样的形式5、送料及挡料方式二十四、冲裁材料:1、金属材料(钢、铝、各种贵重金属及各种合金) 2、非金属材料(纸板、塑料板、胶合板等) 3、复合材料(涂层板、复合板等)二十五、对冲裁材料机械性能的要求:1、有一定强度与韧性,避免过硬、过软、过脆。
2、电工硅钢,材料较硬较脆; 3、低碳钢,具有较好的冲裁性能二十六、冲裁件的工序性质就是指冲裁件加工成形所需的工序种类如冲孔、切废料、冲缺、冲槽、落料、切断、切口等;二十七、复合冲裁模:压力机的一次工作行程,在模具的同一工位同时完成数道冲压工序。
级进冲裁模: 级进模就是指压力机在一次行程中一次在模具几个不同的位置上同时完成多道冲压工序的冲模二十八、常见的凹模结构形式有整体式凹模与组合式凹模两种形式。
整体式凹模只适用于冲制中、小型工件;组合式凹模适用于冲大、中型工件上的孔。
二十九、定位零件的作用:(1)定距:在送料方向上控制送料的进距;(2)导向:保证板料沿送料方向正确送进。
三十、定位零件的结构形式:(1)定位板与定位销(2)挡料销(3)导正销(导头) (4)导料销(5)导料板(导尺) (6)侧刃三十一、定位方式分类:(1)以导料销、挡料销组合定位(2)以始用挡料销、挡料销与导料板组合定位(3)以始用挡料销、挡料销、导正销与导料板组合定位(4)以侧刃与导料板组合定位(5)以侧刃、导正销与导料板组合定位三十二、卸料板:指将包在凸模上的制件或废料从凸模上刮下来的零件。
形式:刚性卸料板与弹性卸料板。
刚性卸料板分为封闭式、悬臂式、钩形三十三、出件装置:指将在凹模中的制件或废料从凹模口推或顶出的装置。
1)刚性推件装置2)弹性推件装置3)弹性顶件装置三十四、模架:由上下模座与导向零件组成,它就是整副模具的骨架,就是安装模具其它零件的基础零件。
分类:后侧导柱模架、对角导柱模架、中间导柱模架、四导柱模架等。
三十五、模具压力中心:指模具冲压力合力的作用点。
要求:冲压时,其压力中心应与压力机滑块中心相重合。
作用:(1)以避免模具在工作中产生偏弯矩而发生歪斜,加速模具导向机构的不均匀;(2)保证凸凹模间隙的一致,从而保证制件质量与延长模具寿命。
三十六、弯曲就是将板料、棒料、管料或型材等弯成一定曲率或角度,并得到一定形状零件的冲压工序弯曲材料:板料、棒料、型材、管材弯曲方法:压弯、折弯、拉弯、辊弯三十七、弯曲变形特点:1、变形区主要发生在弯曲件的圆角部分,直线部分没有变形只就是刚性移动。
2、变形区内,纵向金属纤维长度发生变化,内层纵向纤维受压缩短,外层纵向纤维受拉变长。
由于材料的连续性,因而在内层与外层中间存在一个既不伸长也不缩短的中间层,称为应变中性层。
3、弯曲变形区材料变薄变形程度愈大,变薄现象愈严重4、板材弯曲时,分:窄板(b / t <3 )与宽板(b / t >3 )两种情况,窄板横断面形状为外窄内宽的扇形,宽板基本保持为矩形。
5、弯曲变形程度可以用相对弯曲半径r/t来表示三十八、弯曲变形区的应力应变状态:板料在塑性弯曲时,变形区内的应力应变状态取决于弯曲毛坯的相对宽度b/t以及弯曲变形程度r/t、1、窄板弯曲的应变状态就是立体的,应力状态就是平面的2、宽板弯曲的应变状态就是平面的,应力状态就是立体的。
三十九、弯曲时的主要质量问题:拉裂、截面畸变、翘曲及回弹四十、回弹:弯曲卸载后,塑性变形保留,弹性变形消失,弯曲角形状与尺寸都发生与加载时变形方向相反的变化,这种现象称为回弹。
四十一、影响回弹的因素:1)材料的机械性能2)相对弯曲半径3)弯曲角4)弯曲方式与模具结构5)摩擦6)弯曲件形状、模具间隙:形状越复杂,回弹越小四十二、减少回弹的措施:1、材料选择(尽可能选用弹性模量大的,屈服极限小,机械性比较稳定的材料、) 2、改进弯曲件的结构设计3、从工艺上采取措施: 1)采用热处理工艺2)增加校正工序3)采用拉弯工艺4、从模具结构采取措施1)补偿法2)校正法3)纵向加压法4)采用聚氨酯弯曲模四十三、影响最小弯曲半径的因素:1)材料的力学性能2)弯曲角3)板料的冲裁断面质量与表面质量4)板料的宽度与厚度5)板料的纤维方向四十四、弯曲工序安排原则:(1):对多角弯曲件,因变形会影响弯曲件的形状精度,故一般应先弯外角,后弯内角。
前次弯曲要给后次弯曲留出可靠的定位,并保证后次弯曲不破坏前次已弯曲的形状。
(2):结构不对称弯曲件,弯曲时毛坯容易发生偏移,应尽可能采用成对弯曲后,再切开的工艺方法。
(3):批量大、尺寸小的弯曲件,应采用级进模弯曲成形工艺以提高生产率。
(4):如果弯曲件上孔的位置受弯曲过程影响而且精度要求较高,则应在弯曲后再冲孔,否则孔的位置精度无法保证。
四十五、填空1、弯曲变形程度用相对弯曲半径(r / t )表示。
2、最小相对弯曲半径r min/ t表示材料的弯曲变形极限。
判断1、在其它条件相同的情况下,弯曲线垂直于钢板轧制方向允许的弯曲半径较小。
(√)2、材料的机械性能对弯曲件影响较大,其中材料的塑性越差,其允许的最小相对弯曲半径越小。
(×)3、相对弯曲半径(r / t)就是表示零件结构工艺性好坏的指标之一。
(√)四十六、弯曲件展开长度的计算依据就是弯曲前后应变中性层长度不变。
四十七、拉深的基本概念: 拉深-也称拉延,就是利用模具使平板毛坯成为开口空心零件或将已制成的开口空心件加工成其它形状与尺寸空心件的冲压加工方法。
四十八、拉深变形过程:1 、平面凸缘区—主要变形区 2 、凸缘圆角部分—过渡区3 、筒壁部分—传力区 4 、底部圆角部分—过渡区 5 、圆筒底部分—小变形区四十九、拉深成形过程中出现的问题及防止措施1 、起皱主要就是由于凸缘处的切向压应力超过了板料的临界压应力所引起的1)起皱的影响: 起皱不利于拉深变形: a、由于起皱,毛坯不能被拉过凸凹模间隙面而拉断b、轻微起皱的毛坯即使拉过凸凹模间隙,也会在筒壁上留下起皱痕迹而影响质量。
起皱的影响因素: a:凸缘部分材料的相对厚度b:切向压应力的大小c:材料的力学性能防皱措施:主要采用压边圈防皱2 、拉裂原因:1)由于法兰起皱,坯料不能通过凸凹模间隙,使筒壁拉应力增大2)压边力过大,使径向拉应力增大3)变形程度太大防止拉裂的措施:1)采用适当的拉深比与压边力2)增加凸模的表面粗糙度,改善凸缘部分变形材料的润滑条件3)合理设计模具工作部分的形状4)选用拉深性能好的材料、五十、拉深毛坯尺寸计算的原则:a、形状相似原则b、面积相等原则c、在计算毛坯尺寸时,必须计入修边余量δ五十一、拉深系数就是指拉深后圆筒形件的直径与拉深前毛坯(或半成品)的直径之比在保证侧壁不破坏的情况下所能得到的最小拉深系数称为极限拉深系数拉深变形程度用拉深系数m 表示。
拉深系数越小,说明拉深变形程度越大矩形件拉深时,直边部分变形程度相对较小,圆角部分的变形程度相对较大。
拉深加工时,润滑剂涂在与凹模接触的毛坯表面上。
拉深过程中的辅助工序有中间退火、润滑、酸洗等。
五十二、影响极限拉深系数的因素:1)材料的内部组织与力学性能:2)毛坯相对厚度t/D: 3)拉深模具4)拉深条件五十三、有凸缘筒形件的拉深特点:⑴宽凸缘变形程度不能单纯用拉深系数来衡量;⑵首次拉深系数比圆筒件要小; ⑶首次拉深极限变形程度与dt/d 有关。