齿轮硬度要求
齿轮硬度要求

齿轮硬度要求 IMB standardization office【IMB 5AB- IMBK 08- IMB 2C】二、典型零部件选材及工艺分析金属材料、高分子材料、陶瓷材料及复合材料是目前的主要工程材料。
高分子材料的强度、刚度较低、易老化,一般不能用于制作承受载荷较大的机械零件。
但其减振性好,耐磨性较好,适于制作受力小、减振、耐磨、密封零件,如轻载齿轮、轮胎等。
陶瓷材料硬而脆,一般也不能用于制作重要的受力零部件。
但其具有高熔点、高硬度、耐蚀性好、红硬性高等特点,可用于制作高温下工作的零部件、耐磨耐蚀零部件及切削刀具等。
复合材料克服了高分子材料和陶瓷材料的不足,具有高比强度、高减振性、高抗疲劳能力、高耐磨性等优异性能,是一种很有发展前途的工程材料。
与以上三类工程材料相比,金属材料具有优良的使用性能和工艺性能,储藏量大,生产成本比较低、广泛用于制作各种重要的机械零件和工程构件,是机械工业中最主要、应用最广泛的一类工程结构材料。
下面介绍几种钢制零部件的选材及热处理工艺分析。
㈠齿轮类零件的选材齿轮是机械工业中应用广泛的重要零件之一,主要用于传递动力、调节速度或方向。
1、齿轮的工作条件、主要失效形式及对性能的要求。
⑴齿轮的工作条件:①啮合齿表面承受较大的既有滚动又有滑动的强烈磨擦和接触疲劳压应力。
②传递动力时,轮齿类似于悬臂梁,轮齿根部承受较大的弯曲疲劳应力。
③换挡、启动、制动或啮合不均匀时,承受冲击载荷。
⑵齿轮的主要失效形式:①断齿:除因过载(主要是冲击载荷过大)产生断齿外,大多数情况下的断齿,是由于传递动力时,在齿根部产生的弯曲疲劳应力造成的。
②齿面磨损:由于齿面接触区的磨擦,使齿厚变小、齿隙加大。
③接触疲劳;在交变接触应力作用下,齿面产生微裂纹,遂渐剥落,形成麻点。
⑶对齿轮材料的性能要求:①高的弯曲疲劳强度;②高的耐磨性和接触疲劳强度;③轮齿心部要有足够的强度和韧性。
2、典型齿轮的选材⑴机床齿轮机床齿轮的选材是依其工作条件(园周速度、载荷性质与大小、精度要求等)而定的。
球磨机小齿轮(含轴)技术要求03.21
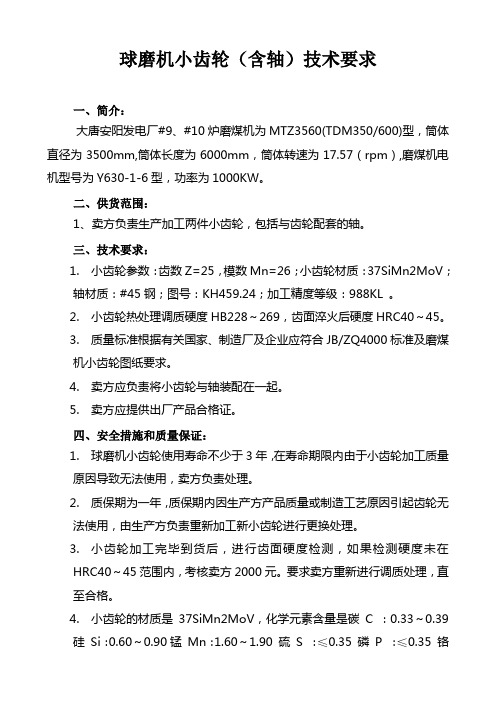
球磨机小齿轮(含轴)技术要求一、简介:大唐安阳发电厂#9、#10炉磨煤机为MTZ3560(TDM350/600)型,筒体直径为3500mm,筒体长度为6000mm,筒体转速为17.57(rpm),磨煤机电机型号为Y630-1-6型,功率为1000KW。
二、供货范围:1、卖方负责生产加工两件小齿轮,包括与齿轮配套的轴。
三、技术要求:1.小齿轮参数:齿数Z=25,模数Mn=26;小齿轮材质:37SiMn2MoV;轴材质:#45钢;图号:KH459.24;加工精度等级:988KL 。
2.小齿轮热处理调质硬度HB228~269,齿面淬火后硬度HRC40~45。
3.质量标准根据有关国家、制造厂及企业应符合JB/ZQ4000标准及磨煤机小齿轮图纸要求。
4.卖方应负责将小齿轮与轴装配在一起。
5.卖方应提供出厂产品合格证。
四、安全措施和质量保证:1.球磨机小齿轮使用寿命不少于3年,在寿命期限内由于小齿轮加工质量原因导致无法使用,卖方负责处理。
2.质保期为一年,质保期内因生产方产品质量或制造工艺原因引起齿轮无法使用,由生产方负责重新加工新小齿轮进行更换处理。
3.小齿轮加工完毕到货后,进行齿面硬度检测,如果检测硬度未在HRC40~45范围内,考核卖方2000元。
要求卖方重新进行调质处理,直至合格。
4.小齿轮的材质是37SiMn2MoV,化学元素含量是碳 C :0.33~0.39 硅Si:0.60~0.90锰 Mn:1.60~1.90 硫 S :≤0.35 磷 P :≤0.35 铬 Cr:≤0.30镍 Ni:≤0.30铜 Cu:≤0.30钒 V :0.60~0.90钼 Mo:0.60~1.50 加工好齿轮后到厂买方对小齿轮材质进行验收,验收不合格考核卖方3000元,并要求卖方重新加工制造。
五、供货周期:1、签订合同后,一个月内供货。
超出供货周期每推迟一天考核1000元。
常用的齿轮材料

一、常用的齿轮材料是钢、铸铁和非金属材料。
1、锻钢钢材的韧性好,耐冲击,还可以通过热处理或化学热处理改善其力学性能及提高齿面硬度,故最适应于用来制造齿轮。
除尺寸过大(da>400~600mm)或者是结构形状复杂只宜铸造者外,一般都用锻钢制造齿轮,常用的是含碳量在(0.15~0.6)%的碳钢或合金钢。
制造齿轮的锻钢可分为:软齿面(硬度≤350HBS):经热处理后切齿的齿轮所用的锻钢对于强度、速度及精度都要求不高的齿轮,应采用以便于切齿,并使刀具不致迅速磨损变钝。
因此,应将齿轮毛坯经过正火(正火)或调质处理后切齿。
切制后即为成品。
其精度一般为8级,精切时可达7级。
这类齿轮制造简便、经济、生产效率高。
硬齿面(硬度>350HBS):需进行精加工的齿轮所用的锻钢高速、重载及精密机器(如精密机床、航空发动机)所用的主要齿轮传动,除要求材料性能优良,轮齿具有高强度及齿面具有高硬度(如58~65HRC)外,还应进行磨齿等精加工。
需精加工的齿轮目前多是先切齿,再做表面硬化处理,最后进行精加工,精度可达5级或4级。
这类齿轮精度高,价格较贵,所以热处理方法有表面淬火、滲碳、氮化、软氮化及氰化等。
所以材料视具体要求及热处理方法而定。
合金钢根据所含金属的成分及性能,可分别使材料的韧性、耐冲击、耐磨及抗胶合的性能等获得提高,也可通过热处理或化学热处理改善材料的力学性能及提高齿面的硬度。
所以对于既是高速、重载又要求尺寸小、质量小的航空用齿轮,就都用性能优良的合金钢(如20CrMnTi,20Cr2Ni4A等)来制造。
2、铸钢铸钢的耐磨性及强度均较好,但应经退火及正火处理,必要时也可进行调质。
铸钢常用于尺寸较大的齿轮。
3.铸铁灰铸铁性质较脆,抗冲击及耐磨性都较差,但抗胶合及抗点蚀的能力较好。
灰铸铁齿轮常用于工作平稳、速度较低、功率不大的场合。
4.非金属材料对高速轻载及精度不高的齿轮传动,为了降低噪声,常用非金属材料(如夹布胶木、尼龙等)做小齿轮,大齿轮仍用钢或铸铁制造。
20crmnmo齿轮的工作条件

1. 概述20CrMnMo是一种常用的合金结构钢,具有较高的强度和硬度,广泛用于制造各种齿轮零件。
在实际工作中,齿轮通常处于高强度、高速度、高温度等苛刻的工作条件下。
了解20CrMnMo齿轮在不同工作条件下的性能表现对于提高齿轮的使用寿命具有重要意义。
2. 高强度要求在工程机械、汽车、航空航天等领域,20CrMnMo齿轮通常需要承受较高的载荷和冲击。
这就要求齿轮材料具有足够的强度和韧性,以保证齿轮在工作中不易发生断裂或变形。
20CrMnMo钢具有较高的强度,可以满足齿轮在高载荷和冲击下的使用要求。
3. 高速度要求在一些工业设备中,齿轮需要以较高的转速工作,这就对齿轮的耐磨性能提出了较高的要求。
20CrMnMo齿轮具有良好的耐磨性能,可以适应高速度工作条件下的需求。
4. 高温度要求在一些特殊环境中,齿轮可能需要在较高的温度下工作,例如高温熔炼设备、高温润滑环境等。
20CrMnMo合金结构钢具有较好的高温强度和热稳定性,能够适应高温工作条件下的使用需求。
5. 总结在工程实践中,20CrMnMo齿轮的工作条件通常是多种因素综合作用的结果,需要综合考虑其强度、硬度、韧性、耐磨性、高温性能等多方面因素。
在实际设计和使用过程中,应根据具体工作条件对齿轮材料和热处理工艺进行合理的选择和设计,以确保齿轮在各种工作条件下都能够正常运行并具有较长的使用寿命。
还需注意齿轮使用过程中的维护和保养工作,及时检查和更换磨损严重的齿轮零件,以确保齿轮系统的可靠性和安全性。
6. 热处理对20CrMnMo齿轮的影响20CrMnMo齿轮在使用前通常需要经过热处理工艺,以提高其强度、硬度和耐磨性。
热处理工艺对20CrMnMo齿轮的性能具有重要影响,一般包括热处理温度、冷却速度和时效处理等环节。
6.1 热处理温度对20CrMnMo齿轮进行热处理时,热处理温度的选择对最终的组织结构和性能具有较大影响。
通常情况下,热处理温度会根据钢的化学成分和工作要求进行合理选择。
齿轮材料的基本要求
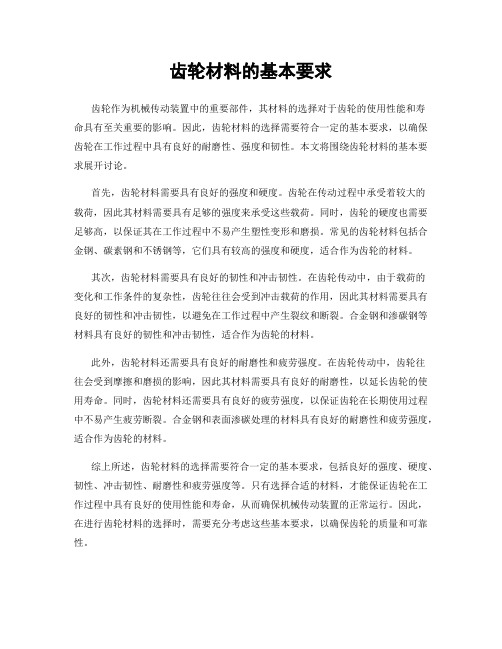
齿轮材料的基本要求齿轮作为机械传动装置中的重要部件,其材料的选择对于齿轮的使用性能和寿命具有至关重要的影响。
因此,齿轮材料的选择需要符合一定的基本要求,以确保齿轮在工作过程中具有良好的耐磨性、强度和韧性。
本文将围绕齿轮材料的基本要求展开讨论。
首先,齿轮材料需要具有良好的强度和硬度。
齿轮在传动过程中承受着较大的载荷,因此其材料需要具有足够的强度来承受这些载荷。
同时,齿轮的硬度也需要足够高,以保证其在工作过程中不易产生塑性变形和磨损。
常见的齿轮材料包括合金钢、碳素钢和不锈钢等,它们具有较高的强度和硬度,适合作为齿轮的材料。
其次,齿轮材料需要具有良好的韧性和冲击韧性。
在齿轮传动中,由于载荷的变化和工作条件的复杂性,齿轮往往会受到冲击载荷的作用,因此其材料需要具有良好的韧性和冲击韧性,以避免在工作过程中产生裂纹和断裂。
合金钢和渗碳钢等材料具有良好的韧性和冲击韧性,适合作为齿轮的材料。
此外,齿轮材料还需要具有良好的耐磨性和疲劳强度。
在齿轮传动中,齿轮往往会受到摩擦和磨损的影响,因此其材料需要具有良好的耐磨性,以延长齿轮的使用寿命。
同时,齿轮材料还需要具有良好的疲劳强度,以保证齿轮在长期使用过程中不易产生疲劳断裂。
合金钢和表面渗碳处理的材料具有良好的耐磨性和疲劳强度,适合作为齿轮的材料。
综上所述,齿轮材料的选择需要符合一定的基本要求,包括良好的强度、硬度、韧性、冲击韧性、耐磨性和疲劳强度等。
只有选择合适的材料,才能保证齿轮在工作过程中具有良好的使用性能和寿命,从而确保机械传动装置的正常运行。
因此,在进行齿轮材料的选择时,需要充分考虑这些基本要求,以确保齿轮的质量和可靠性。
减速机齿轮常用材料

一、锻钢钢的强度高,耐冲击,用热处理方法能显著改善机械性能,所有它是制造齿轮的主要材料。
由于锻造毛坯的纤维方向有利于提高轮齿的弯曲强度,所以大部分齿轮如采用锻造毛坯,只有受力小和不重要的齿轮才直接采用轧制钢材。
按照齿坯处理方法和切齿工艺,制造齿轮的钢材及热处理方法分为两大类:*类:齿面硬度HB≤350,用中碳钢45号钢、50号钢或中碳合金钢40Gr、40MnB、35SiMn等近行调质或正火处理,终切齿可在热处理后进行。
调质后,硬度不高(HB=220~250),材料的综合性能(机械强度和冲右韧性等)比较好,适用于低速、中速和中等平稳载荷下工作。
工控设备机械中的减速机齿轮多用此类。
45号钢价格低,供应充足,应用最普遍。
正火后,综合性能有所改善,但不如调质,多用于直径很大不便调质和不重要的齿轮。
选用第—类材料时,小齿轮硬度要比大齿轮硬度高出20~40HB,以使两个齿轮寿命接近相等。
第二类:齿面硬度HB≥350,用中碳钢和中碳合金钢进行表面淬火(齿面硬度HRG=50一55),或者用低碳钢和低碳合金钢进行表面掺碳淬火处理(齿面硬度HRG=58—63)。
处理后齿面硬度高;齿芯韧性好。
所以承载能力强,耐冲击,但加工困难,成本较高,减速机中应用较少。
二、铸钢当齿轮直径较大(D>400—600毫米)时,齿坯不易锻造,因而常采用铸钢齿坯并进行正火处理。
常用的牌号有ZG45及ZH50等。
三、铸铁铸铁价格低廉,能铸造出复杂的结构形状,但灰铸铁的抗弯强度及耐冲击能力较差,故只用于低速轻载的开式齿轮传动中,常用的牌号有HT15-33、HT20—40、HTr30—54等,球墨铸铁的机械性能比灰铸铁高,可部分代替碳素钢,常用的牌号有QT60-2等。
四、非金属材料高速轻载的齿轮传功,常用非金属齿轮与另一金属齿轮配合工作,以减少齿轮传动的噪音。
常用的非金属材料有酚醛层压板(夹布胶木)、尼龙等。
这种齿轮的承载能力低、寿命短,其许用载荷只有钢齿轮的25—30%。
齿轮锻钢件技术要求

齿轮锻钢件技术要求
齿轮锻钢件的技术要求包括以下几个方面:
1. 余量尺寸:齿轮锻件余量尺寸应符合国家标准。
2. 锻造比:齿轮锻件在锻造中要保证合适的锻造比,不得使用尺寸近似的圆钢锻打。
3. 材质:齿轮锻件的材质应与零件的材质一致,化学成分应符合国家标准,并出具材质单。
4. 温度:要保证正常的锻打温度,不能低温锻打或过烧。
5. 外形:锻件外形要整齐、均匀,不允许有叠皮、断裂等锻造缺陷。
6. 精度:齿轮的精度对齿轮传动性能和使用寿命有着重要影响。
根据齿轮使用场合的不同,需要选择不同精度等级的齿轮。
7. 齿面硬度:齿轮齿面硬度是根据工作载荷和转速等因素来确定的,不同硬度的齿轮适用于不同的工作条件。
8. 润滑油:齿轮传动需要润滑油,以减少齿面磨损和摩擦阻力,提高齿轮使用寿命。
9. 热处理:齿轮需要进行热处理,以改变其内部组织结构,提高其力学性能和耐久性。
10. 清洁度:齿轮应保持清洁,以防止杂质和污物对齿轮传动造成不良影响。
11. 防锈处理:齿轮应进行防锈处理,以防止其生锈和腐蚀。
以上是齿轮锻钢件的一些主要技术要求,这些要求需要根据具体的工作条件和使用要求来制定。
同时,还需要根据具体情况进行相应的实验和测试,以确保齿轮锻钢件的质量和可靠性。
齿 轮 热 处 理 技 术 要 求

齿轮热处理技术要求编制:校对:审核:批准:南京华实齿轮传动设备有限公司二零一三年十月1.齿轮件热处理技术要求1.1渗碳件热处理质量要求1.1.1 热处理1.1.1.1 预备热处理1.1.1.1.1 对于18Cr2NiWA、20Cr2Ni4A,采用正火+高温回火作为预备热处理。
1.1.1.1.2 预备热处理后,要求按照GB/T 231-2009 《金属布氏硬度试验》进行硬度检查,要求硬度170-210HBW。
热处理后硬度应均匀,单件硬度差值≤20HBW(三点),同批硬度差值≤30HBW,组织允许为均匀分布的珠光体+铁素体+粒状贝氏体。
1.1.1.2 渗碳准备1.1.1.2.1 热处理前要求:所有零件及吊装夹具在入炉前应彻底清洗、去油。
经清洗后的工件,表面不应有锈迹、油污、斑点等影响渗碳质量的表面缺陷。
1.1.1.2.2 工件清洗后应自然干燥或风干、烘干。
进入渗碳炉的工件应完全干燥。
1.1.1.2.3 防渗:应根据工件外形及机械加工要求对工件的非渗碳部位进行有效的防渗保护。
1.1.1.3 渗碳+淬火+低温回火+喷丸1.1.1.3.1 渗碳应采用可控气氛渗碳炉进行处理,能精确控制炉内气氛的碳势及各项工艺参数,确保渗碳质量的稳定性与一致性。
1.1.1.3.2 渗碳:应根据工件热处理要求,选择适当的强渗、扩散的碳势、保温时间、渗碳后处理方式(中冷、高回等)等工艺参数,以使工件达到相应的组织和性能。
1.1.1.3.3 淬火:根据工件所需的冷却特性选择合适的淬火介质及淬火温度,淬后清洗。
1.1.1.3.4 低温回火:工件必须在淬火出油后2小时之内回火,回火温度及时间、次数等视工件大小及有效硬化层深、金相组织而定。
1.1.1.3.5 喷抛丸:经热处理完毕的齿轮,应进行抛丸处理,喷丸表面覆盖率≥200%,喷丸强度≥0.35A,喷丸后要求齿根部为残余压应力。
抛丸后,所有表面不允许存在裂纹。
1.1.2 热处理质量检验1.1.2.1 标准试样1.1.2.1.1 试样要求:材料从锻件本体切取、同预备热处理制作。