生产过程中的危险因素分析
生产现场危险点分析及预控措施

生产现场危险点分析及预控措施在生产现场,存在着各种各样的危险因素,这些危险因素可能对工作人员的健康和安全带来严重的威胁。
为了确保生产现场的安全和工人的健康,必须进行危险点分析,并采取相应的预控措施。
下面将对生产现场常见的危险因素进行分析,并提出相应的预控措施。
1.高处作业的危险高处作业是生产现场常见的作业,但也是最危险的作业之一、工人可能面临失足坠落、物体掉落以及梯子折断等危险。
为了预防这些危险,应采取以下措施:a.为高处作业区域配备安全护栏和防护网,确保工人不会失足坠落。
b.对高处作业区域进行定期检查和维护,确保脚手架、梯子等设备的可靠性。
c.对高处作业人员进行安全培训,包括正确使用安全带和熟悉高处作业相关规定。
2.机械设备的危险在生产现场中,机械设备的使用可能会造成严重的伤害和事故。
为了减少机械设备的危险性,应采取以下预控措施:a.确保机械设备的正常运转和维护,包括定期检查和润滑。
b.为机械设备周围设置安全护栏,确保工人不会意外接触到运动部件。
c.增加安全开关和紧急停止按钮,方便工人在发生紧急情况时立即停止机械设备的运转。
d.对机械设备操作人员进行专业培训,确保他们能正确操作和维护机械设备。
3.危险化学品的危险许多生产过程中都会使用危险化学品,这些化学品可能对工人的健康和环境造成严重的危害。
为了减少危险化学品的危险性,应采取以下预控措施:a.对危险化学品进行分类和标识,以便工人能够识别危险性和采取相应的防护措施。
b.存储危险化学品时,应使用专门的储存柜,并确保柜门关闭和密封。
c.使用危险化学品时,工人应佩戴适当的防护装备,如防护眼镜、手套和防护服等。
d.进行危险化学品的处理和清洁时,应遵循相关的操作规程和安全程序。
4.电气设备的危险电气设备是生产现场常见的设备,但不正确的使用和维护可能会引发火灾和触电等事故。
为了预防电气设备的危险,应采取以下预控措施:a.确保电气设备的安装和维护符合相关的安全标准和规定。
生产可能接触的危险因素

生产可能接触的危险因素
在生产过程中,可能会接触到各种危险因素。
以下是一些常见的危险因素:
1. 物理危险:例如机械设备、移动部件、高温表面、尖锐工具等可能导致创伤或损伤的物理因素。
2. 化学危险:生产过程中可能涉及到化学物质,例如有毒气体、腐蚀性物质、易燃物质等,这些物质可能对人体健康造成损害。
3. 生物危险:在某些生产环境中,可能会接触到病原体、细菌、真菌等微生物,这些生物可能引发疾病或感染。
4. 电气危险:与电力设备和电气线路的接触可能导致电击、电火灾等危险。
5. 高噪声:某些生产环境中可能存在噪音污染,长期暴露于高噪音环境可能会对听力和健康产生负面影响。
6. 辐射:在某些生产过程中,可能会产生电离辐射或非电离辐射,例如X射线、紫外线等,这些辐射可能对人体组织和器官造成损害。
7. 人机因素:不当的工作姿势、重复性工作、缺乏适当的培训和安全意识等人机因素可能导致事故和伤害。
为了减少这些危险因素的风险,生产环境中通常需要采取安全措施,包括提供个人防护装备、培训员工有关安全操作的方法、定期维护和检查设备等。
此外,定期进行安全审查和风险评估也是必要的。
危险因素分析及预防控制措施

危险因素分析及预防控制措施危险因素分析及预防控制措施危险因素分析和预防控制措施是企业和个人在日常生产和生活中应该非常了解和熟悉的知识,这样才能避免出现一些风险和危险,防止损失的发生。
一、危险因素分析1.人为因素:人为因素往往是导致事故发生的主要因素之一,例如员工操作不规范、疏忽大意、缺乏安全意识等。
2.设备因素:设备的维护和保养工作是重要的,设备不良或者维护不当都会导致需要维修或更换,不及时更换会有严重的后果。
3.环境因素:环境因素是指周围的环境对员工的身体和心理都有影响,例如高温、低温、噪音、尘土等,如果不正视这些因素将会大大影响员工的工作效率和健康状况。
4.物料因素:物料因素是指在生产过程中使用的物质影响员工的身体健康,例如在危险化学品、有害气体等方面。
5.管理因素:管理中出现的问题通常是管理不善导致的,例如生产计划不合理、人员安排不当以及产生的缺陷制品没有及时处理等。
二、预防控制措施1.人为因素需要加强培训和意识提醒,通过加强员工安全意识来避免出现危险情况。
2.设备因素需要加强设备的检验和维护,定期做好设备的维修和保养工作。
3.环境因素需要根据环境特点加以防范,例如在高温环境下保持员工水分供应、在噪音较大环境下为员工配备防噪耳罩等。
4.物料因素需要建立安全保障措施,例如制定使用安全规程、保证物料质量等。
5.管理因素需要建立更完善的制度和规章制度,加强对员工的管理和监督,落实生产计划,及时处理产生的缺陷制品等。
三、总结在实际工作中,危险因素分析和预防控制措施是非常重要的,这样才能不断提高工作效率和员工的生产健康。
企业应该根据自身特点制定相应的措施,不断完善自身的管理制度,以应对预防和应对突发事件的需求。
公司生产主要危险因素及防范措施

公司生产主要危险因素及防范措施引言工作场所安全事故不可避免,公司生产中也存在各种危险因素,因此预防和减少安全事故的发生是非常必要的。
本文将详细介绍公司生产中的主要危险因素及防范措施。
危险因素机器设备1.机器不良维护:机器如果长时间不进行维护就可能造成故障,甚至事故。
2.电锯、钻床等机器:这些机器操作不慎或操作不当就可能危及生命。
化学品1.溶剂、油漆等:这些物品容易燃烧和爆炸,在使用过程中也可能造成中毒。
2.有毒、有害的工艺辅助剂:在接触时会伤害眼睛和皮肤,可能会引起中毒。
物料堆积1.物料积压堆放:物料堆积过高过满或者不稳定,可能会引起意外事故。
2.堆放不正确的危险品:这些危险品要求特别的存放方法和存放环境,否则可能会发生爆炸、着火等事故。
防范措施•设立规章制度:公司生产必须要有相应的规章制度,员工必须遵守制度,以免出现不必要的意外事故。
•做好安全防护工作:对于可能引起安全事故的区域、设备等应该进行安全防护,如安装警示线、锁扣、警告标志等,员工可以根据这些防护措施来提高安全意识。
•培训养成安全意识:组织员工进行安全培训和考核,养成做好鉴定风险、危险因素、预防方法的工作习惯。
•污染防治措施:对于可能产生化学污染的化学品,必须要进行停用或采取相应的污染治理措施,比如收集和处理有害物质。
•人员管理策略:安全工作的有效性是靠全员参与保证的。
加强人员管理,鼓励员工提高安全意识,发现并及时纠正不良操作行为,及时进行安全教育,是预防危险事故最有效的方法。
总结以上是公司生产中的主要危险因素及防范措施,防范措施的理念是在实践中不断完善和提高的,期望各位读者能通过本文对公司生产中的安全防范有一个圆满的认识。
同时,建议公司生产中定期加强安全培训,针对危险因素采取多种方式进行防范和减少事故的发生。
3.生产过程中危险、有害因素分析

生产过程中危险、有害因素分析生产过程中潜在的危险、有害因素有:机械伤害、触电、火灾、压力容器爆炸、物体打击、粉尘、噪声等。
1、机械伤害机械伤害为车间生产线中的最主要危险因素。
该项目机械设备比较多,在生产线的各个部位都存在着发生机械伤害事故的危险性,如果机械设备安全防护设施不全或损坏、安全生产管理措施跟不上,会发生机械伤害事故,造成人员伤亡或财产损失。
造成机械伤害事故,主要是由于设备制造质量不符合设计要求或设计上本身就存在缺陷、设备的安全防护装置没有或损坏、违章指挥、违章操作及对机械设备的故障不及时维修、设备在非正常状态下工作等造成的。
常见的有:(1)机械设备制造质量不合格或设计上本身就存在缺陷。
(2)设备控制系统失灵,造成设备误动作,导致事故发生。
(3)电源开关布局不合理,一种是有了紧急情况不便立即停车台机械设备开关设在一起,极易造成误开机引发事故。
(4)机械设备安全防护装置缺乏或损坏,或在运输、安装过程中被拆除等。
(5)机械设备有故障不及时排除,设备带有故障运行。
(6)在机械运转中从事清理卡料、修理等工作。
(7)在检修时,机械装置突然被人随意启动;不具备操作机械素质的人员上岗或其他人乱动机械设备。
(8)在与机械相关联的不安全场所停留、休息;任意进入机械运行危险区域。
(9)皮带运转过程中清理物料,处理故障,发生皮带卷人伤害:人接触传动部位(加油、清理、处理故障等),皮带突然启动伤人。
(10)违章操作,穿戴不符合安全规定的服装进行操作。
2、触电在生产过程中,电力设备较多,操作中稍有不慎就可能导致触电事故的发生。
因此,触电事故也是生产线生产过程中主要的危险因素。
对于触电事故的防范决不可掉以轻心。
触电危险的分布极广,凡是用到电气设备的和有电气线路通过的场所触电事故可能发生的场所。
引起触电事故的主要原因,除了没备缺陷、设计不周等技术因素外,大部分是由于违章指挥、违章操作引起的,常见的有:(1)电线、电气设施的绝缘或外壳损坏、设备漏电,一些设备由于绝缘老化、接地失灵、线头裸露等原因。
公司生产中主要危险因素及防范措施:机械伤害、高处坠落、电击、火灾、爆炸及中毒
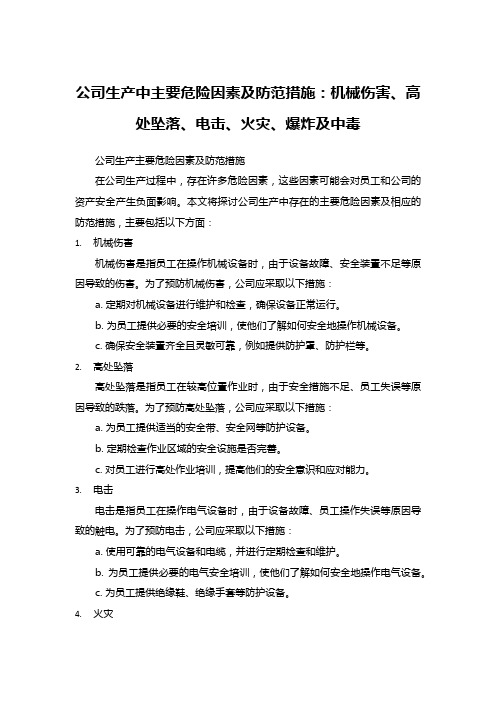
公司生产中主要危险因素及防范措施:机械伤害、高处坠落、电击、火灾、爆炸及中毒公司生产主要危险因素及防范措施在公司生产过程中,存在许多危险因素,这些因素可能会对员工和公司的资产安全产生负面影响。
本文将探讨公司生产中存在的主要危险因素及相应的防范措施,主要包括以下方面:1.机械伤害机械伤害是指员工在操作机械设备时,由于设备故障、安全装置不足等原因导致的伤害。
为了预防机械伤害,公司应采取以下措施:a. 定期对机械设备进行维护和检查,确保设备正常运行。
b. 为员工提供必要的安全培训,使他们了解如何安全地操作机械设备。
c. 确保安全装置齐全且灵敏可靠,例如提供防护罩、防护栏等。
2.高处坠落高处坠落是指员工在较高位置作业时,由于安全措施不足、员工失误等原因导致的跌落。
为了预防高处坠落,公司应采取以下措施:a. 为员工提供适当的安全带、安全网等防护设备。
b. 定期检查作业区域的安全设施是否完善。
c. 对员工进行高处作业培训,提高他们的安全意识和应对能力。
3.电击电击是指员工在操作电气设备时,由于设备故障、员工操作失误等原因导致的触电。
为了预防电击,公司应采取以下措施:a. 使用可靠的电气设备和电缆,并进行定期检查和维护。
b. 为员工提供必要的电气安全培训,使他们了解如何安全地操作电气设备。
c. 为员工提供绝缘鞋、绝缘手套等防护设备。
4.火灾火灾是指生产过程中由于设备故障、员工操作失误等原因导致的火灾事故。
为了预防火灾,公司应采取以下措施:a. 对易燃易爆物品进行严格管理和控制,避免其泄漏或接触火源。
b. 对电气设备进行防火措施,如使用防火电缆、定期检查电缆绝缘等。
c. 为员工提供必要的消防安全培训,使他们了解如何正确使用灭火器材和逃生方法。
5.爆炸爆炸是指生产过程中由于设备故障、员工操作失误等原因导致的瞬间产生高压和高温的现象。
为了预防爆炸,公司应采取以下措施:5.爆炸:爆炸是指生产过程中由于设备故障、员工操作失误等原因导致的瞬间产生高压和高温的现象。
药厂生产过程中的危险有害因素分析及安全对策
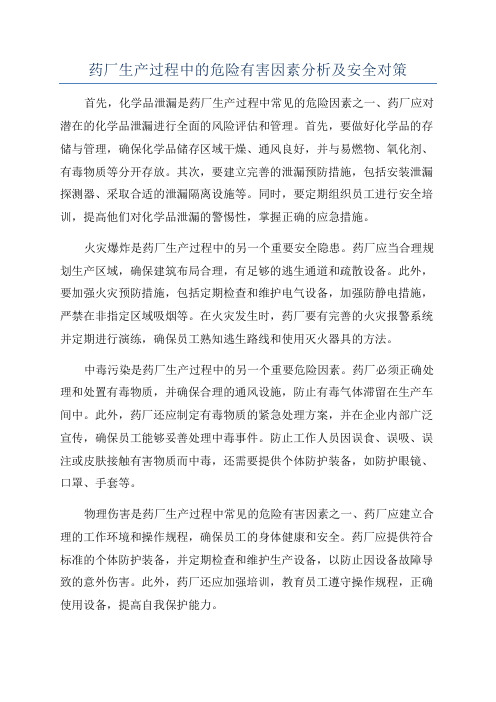
药厂生产过程中的危险有害因素分析及安全对策首先,化学品泄漏是药厂生产过程中常见的危险因素之一、药厂应对潜在的化学品泄漏进行全面的风险评估和管理。
首先,要做好化学品的存储与管理,确保化学品储存区域干燥、通风良好,并与易燃物、氧化剂、有毒物质等分开存放。
其次,要建立完善的泄漏预防措施,包括安装泄漏探测器、采取合适的泄漏隔离设施等。
同时,要定期组织员工进行安全培训,提高他们对化学品泄漏的警惕性,掌握正确的应急措施。
火灾爆炸是药厂生产过程中的另一个重要安全隐患。
药厂应当合理规划生产区域,确保建筑布局合理,有足够的逃生通道和疏散设备。
此外,要加强火灾预防措施,包括定期检查和维护电气设备,加强防静电措施,严禁在非指定区域吸烟等。
在火灾发生时,药厂要有完善的火灾报警系统并定期进行演练,确保员工熟知逃生路线和使用灭火器具的方法。
中毒污染是药厂生产过程中的另一个重要危险因素。
药厂必须正确处理和处置有毒物质,并确保合理的通风设施,防止有毒气体滞留在生产车间中。
此外,药厂还应制定有毒物质的紧急处理方案,并在企业内部广泛宣传,确保员工能够妥善处理中毒事件。
防止工作人员因误食、误吸、误注或皮肤接触有害物质而中毒,还需要提供个体防护装备,如防护眼镜、口罩、手套等。
物理伤害是药厂生产过程中常见的危险有害因素之一、药厂应建立合理的工作环境和操作规程,确保员工的身体健康和安全。
药厂应提供符合标准的个体防护装备,并定期检查和维护生产设备,以防止因设备故障导致的意外伤害。
此外,药厂还应加强培训,教育员工遵守操作规程,正确使用设备,提高自我保护能力。
在总结中,药厂生产过程中的危险有害因素分析涉及化学品泄漏、火灾爆炸、中毒污染、物理伤害等。
为了确保生产过程的安全,药厂需要制定合理的管理措施,包括化学品存储与管理、防火安全、中毒处理和个体防护等方面,并加强员工培训,提高他们对危险因素的认识和应对能力。
只有全面进行危险有害因素分析,并采取相应的安全对策,药厂才能确保生产过程的安全性和稳定性。
生产过程中主要危险因素

生产过程中主要危险因素
生产过程中的主要危险因素包括:
1. 机械危险:由于使用机械设备、工具和设施,可能存在飞溅物、旋转部件、可移动部件或运输工具的碰撞等伤害风险。
2. 化学危险:在某些制造过程中,可能使用或产生具有毒性、腐蚀性、易燃性、爆炸性或致窒息性的化学物质。
3. 电气危险:可能存在电击、触电、火灾或电器设备损坏等电气风险。
4. 动力危险:涉及到使用高压气体、锅炉、蒸汽、压缩空气、气体瓶等设备和系统,可能引发爆炸、火灾、物质泄漏或机械故障等风险。
5. 高温危险:涉及到高温或长时间暴露在高温环境下的制造过程,可能导致烫伤、中暑或火灾等风险。
6. 人为因素:包括疲劳、不当操作、违规操作、缺乏培训、缺乏个人保护装备、压力和应激等导致的人为错误和疏忽。
7. 噪声和振动:某些制造过程可能产生高强度的噪音和振动,长期暴露可能导致听力损伤或其他身体损伤。
8. 健康危害:某些制造过程可能产生有害气体、粉尘、蒸气、毒物或其他有害物质,长期暴露可能导致职业病或健康问题。
9. 物料堆积和储存:不正确的物料堆积和储存可能导致坍塌、滑倒、物理伤害或化学反应等危险。
10. 火灾危险:由于使用易燃材料、高温设备或火焰操作,可能发生火灾或爆炸。
11. 紧急情况:包括火灾、泄漏、故障等突发事件,可能导致人员伤亡、财产损失或环境污染。
- 1、下载文档前请自行甄别文档内容的完整性,平台不提供额外的编辑、内容补充、找答案等附加服务。
- 2、"仅部分预览"的文档,不可在线预览部分如存在完整性等问题,可反馈申请退款(可完整预览的文档不适用该条件!)。
- 3、如文档侵犯您的权益,请联系客服反馈,我们会尽快为您处理(人工客服工作时间:9:00-18:30)。
生产过程中的危险因素分析在《企业职工伤亡事故分类》GB6441中,将生产过程中的危险因素分为以下20类:物体打击、车辆伤害、机械伤害、起重伤害、触电、淹溺、灼烫、火灾、高处坠落、坍塌、冒顶片帮、透水、放炮、火药爆炸、瓦斯爆炸、锅炉爆炸、容器爆炸、其他爆炸、中毒和窒息、其他伤害等。
参考以上分类标准,对甲基纤维素醚生产装置的危险因素进行分析,在生产过程中存在下面几种危险因素:1)火灾、爆炸危险火灾是可燃物质燃烧失去控制而造成的事故,爆炸是物质发生变化的速度不断急剧增大,并在极短的时间内释放出大量能量的现象,火灾和爆炸事故都能造成较大的人员伤亡和财产损失的后果。
a.化学性火灾、爆炸分析生产中使用的原料性质,精棉虽不属于危险化学品,但极易发生燃烧引起火灾事故,加工精棉时散发的棉纤维还能形成爆炸性的粉尘,还存在发生爆炸的危险。
环氧丙烷、异丙醇、甲苯、氯甲烷属于易燃物质,遇到火源会发生燃烧,形成的爆炸性气体遇到火源会发生爆炸事故。
因此生产过程中存在危险物料发生火灾、爆炸的危险性。
危险物质的泄漏主要发生在加料、反应过程中,如果设备、输料管、阀门、法兰等处密封不严,容易造成物料泄漏,遇到火源就会发生燃烧,易燃物料泄漏后挥发的蒸汽还会形成爆炸性气氛,遇到火源会发生爆炸,因此存在火灾爆炸的危险。
易燃物料的高位槽液位计损坏不能正常指示,打料时容易发生跑料现象,遇到明火、火花等有发生火灾、爆炸的危险。
操作失误或自控系统失灵,造成反应超温超压发生沸料、喷料现象,可能造成大量易燃物质泄漏,或形成爆炸性蒸汽,容易发生火灾、爆炸。
设备框架、基础不牢固发生坍塌现象,罐、釜中的易燃物料发生外泄,容易发生火灾、爆炸事故。
爆炸区域内电气设施不防爆或防爆级别达不到要求,运行过程中易产生电火花,容易引燃引爆系统内的可燃物料而发生火灾、爆炸事故。
设备、管线的防静电装置不合格,在易燃物料输送、搅拌时会产生静电并集聚,达到一定程度会产生静电火花,构成引火源。
检修时未进行置换或置换不彻底,容器、管线内存在易燃易爆物料,动火作业时容易发生爆炸事故。
外来火源引发易燃物质发生的火灾、爆炸,如人员吸烟、铁器撞击产生火花、电气火花、雷击火花、车辆排气管火花等b.电气火灾变压器中的绝缘油若遇到高温易挥发,同空气混合能形成爆炸性混合物,一旦变压器内部发生过载或短路,内部的可燃材料和油就会因高温或电火花、电弧在作用而分解、膨胀以致汽化,使变压器内部压力剧增,引起变压器外壳爆炸,绝缘油喷出燃烧,造成火灾事故。
生产系统中使用大量的电气设施,当电气设施、线路发生短路、过载、接触不良等情况时,会发热、产生火花,从而引起电气火灾。
电缆的外皮、填充物和覆盖层具有可燃性,遇到高温或火源会燃烧,电缆一旦着火会很快蔓延,引发火灾。
电缆敷设不规范,交叉过多,电缆接头接触不良,容易在运行过程中发热,引起电气火灾。
电缆选型不当,长期处于超负荷运行状态,电缆容易发热、老化引起绝缘降低,可能发生击穿短路起火。
在管道施工中,任意挖掘、砸砍,造成使用中的电缆受到损坏,可能发生短路起火现象。
电缆沟内积水,容易造成电缆老化发热,发生电气火灾。
c.建筑物及其它类火灾如在建筑设计或施工时,建筑材料达不到耐火等级,或用可燃材料做建筑材料,有可能在使用过程中引发建筑火灾。
生产车间、仓库内包装材料使用可燃物质,生产设备润滑用的润滑油也属可燃物质,其他如检修时使用的油类、棉纱等可燃物,若管理不当,有可能引起此类物质的燃烧而引发火灾事故。
d.容器爆炸生产装置中氯甲烷罐、液氮罐、氯化氢钢瓶、氯甲烷计量罐、醚化釜、醚化冷凝器等设备属于压力容器,氯甲烷管道属于压力管道。
压力容器、管道使用时间过长,发生腐蚀损坏、脆性破坏等造成耐压性不足,未及时进行维护更换,带病运行存在爆炸的危险。
操作失误造成系统设备、管线内压力升高,超过设备、管线的承压能力会造成管线、设备爆炸事故。
压力容器安全附件不全,缺少安全阀、压力表,或安全附件不合格,在超压情况下不能及时卸压,会发生超压爆炸事故。
未经过检测合格的压力容器,带病运行,容易发生超压爆炸事故。
氯化氢钢瓶在储存、运输、使用过程中使用不当,受日光曝晒、明火、热辐射或强烈碰撞等作用,致使瓶温过高,瓶内温度升高会显著地提高瓶内压力,容易发生容器爆炸事故。
2)中毒和窒息生产中使用的危险化学品都有一定的毒性,对人体有毒害性作用,尤其是氯甲烷、环氧丙烷,对人体的毒害作用很大,其他物料对人体有刺激性、麻醉性伤害。
有毒物质主要通过皮肤、吸入、食入侵害人体,如果在防护不当的情况下接触高浓度蒸汽会发生急性中毒,出现头晕、恶心、呕吐、腹泻、昏迷甚至死亡。
有毒物质扩散在车间环境中,能对人员造成慢性毒害影响。
生产设备、设施、管道中有毒物料发生跑、冒、滴、漏,人员接触引起中毒。
泄漏的物料处理不及时,或处理时人员防护不当,吸入散发的蒸汽会发生中毒。
设备检修时,若没有将设备、管道中残存的易燃、易爆、有毒性、腐蚀性的物料进行彻底的置换、清洗,人员进入设备内作业会发生中毒事故。
发生火灾、爆炸事故情况下,飘散的有毒物质、有毒烟气,会造成接触人员中毒。
在生产系统中多处使用氮气,储罐用氮气进行密封,在设备检修时可能进行氮气吹扫,因此在设备中可能残留氮气,氮气具有窒息性,人员进入氮气含量较高的容器内会发生窒息伤害,进入容器作业时如果氧气含量过低,也会造成人员窒息。
防护用品配备不足或者不合格,处理紧急情况时会发生中毒事故。
3)灼烫灼烫分化学灼伤和高温烫伤两种情况。
氢氧化钠属于碱性腐蚀品,片碱、液碱具有腐蚀性,醋酸属于酸性腐蚀品,是造成化学灼伤的物质,人体直接接触会造成组织灼伤,吸入蒸汽会灼伤呼吸器官。
氯化氢气体泄漏后吸收空气中的水分形成酸性腐蚀品,也会对设备造成腐蚀破坏,对人员造成刺激性伤害。
在醚化、脱溶工序中,反应温度较高,物料、设备的温度在80℃以上,保温不好会造成触及人员烫伤。
其他如汽包、蒸汽管等设备设施,如果保温层损坏或包裹不全,外壁裸露,人员误触会造成烫伤。
设备、管道损坏可造成高温物料泄漏,管道外保温损坏,人员接触到高温物料及高温设备表面可造成烫伤。
4)触电触电伤害表现为多种形式。
电流通过人体内部器官,会破坏人的心脏、肺部、神经系统等,使人出现痉挛、呼吸窒息、心室纤维性颤动、心跳骤停甚至死亡。
发生触电事故的因素很多,主要有以下几种:电气线路、设备安装有缺陷,使设备或线路存在漏电、过热、短路、断线、绝缘不良等隐患,易造成触电。
外部环境中的不良因素,如腐蚀、高温、日晒、雨淋等,造成电气设备、线路老化损坏,导致出现漏电,人员接触造成触电伤害。
未设置必要的防触电措施(如保护接零、漏电保护、安全电压、等电位联结等)。
现场管理不当,安全管理制度不健全,电气检修时未严格执行规程,如悬挂“禁止启动”牌、执行监护人制度等,易发生人员触电事故。
违章作业造成的触电,未取得电工操作证人员从事电工作业。
雷雨天气在高处作业,会发生雷击触电事故。
5)高处坠落凡在离基准面2m以上(含2m)有可能坠落的高处进行作业,称高处作业,高处作业时发生坠落事故叫高处坠落。
生产现场有高度超过2m的贮罐和工作梯等工作场所,在工作平台损坏、围栏高度、强度不够、没有防滑措施、没有踢脚板等情况下都有高处坠落的危险。
在高处检修作业时,员工没有正确佩戴安全防护用具(如安全带等),没有采取必要的防护措施或防护措施不到位等,有可能发生高处坠落事故。
6)物体打击物体打击是指物体在重力或其他外力的作用下产生运动,打击人体造成人身伤亡事故。
在高处不稳定的物体,如高处作业(高处设备安装、更换阀门、维修电气仪表等)时使用的工器具、零配件等,尤其是较大较重的物体,会因人的失误行为落下,有造成低处人员受到物体打击伤害的危险。
车间操作平台上和仓库中若未按规定取放物品或物品固定不牢,操作平台无挡板或挡板缺失导致工具物品坠落,高处作业过程中的工具、材料上下投掷和放置、传递不当等情况,极易发生物体打击伤害。
建筑物、框架、设施等在外力或重力作用下,超过自身支撑能力发生坍塌,掉落的设备、设施对人员造成打击伤害。
7)机械伤害机械伤害是指高速运转设备或部件对人体造成的伤害,机泵在高速运转时连接轴可能对人体造成机械伤害,如果缺乏防护罩,人员不慎接触就会发生机械伤害事故。
另外,在检查、维修设备时,若操作不当麻痹大意,会发生刮、碰、割、切等机械伤害。
8)起重伤害在生产装置中安装电动葫芦,用于检修时提升固体物料、设备、工具等,在提升过程中存在起重伤害,主要有以下几种:捆绑不牢固,会发生吊物坠落砸、压伤;质量不合格,发生吊钩、钢丝绳断裂,吊物脱落伤人事故;吊物、吊具夹伤人员;9)车辆伤害车辆伤害主要发生在罐区、仓库内进行装卸车时,司机精力不集中,车辆失控容易伤人,进厂车辆不按规定路线行驶、速度过快、盲目驾驶液会造成车辆伤害事故。
10)冻伤使用的冷冻盐水设备、管路温度较低,保温措施不当会造成人员冻伤,液氮气化设备表面、液氮管路表面温度较低,也存在冻伤的危险。
11)淹溺循环水池、消防水池未设栏杆、盖板,人员在边缘不慎跌入池中,存在淹溺的危险。
职业危害因素分析生产中存在的职业危害有以下几种:1)粉尘精制棉粉碎时会产生棉尘,产品干燥、粉碎、包装过程中会产生纤维素粉尘,其粉尘极易随呼入的气流进入员工支气管,并阻留在支气管肺泡上,可引起肺组织纤维化、硬化,严重的会失去呼吸功能。
长时间大量吸入粉尘,可导致尘肺病的发生。
2)噪音噪音危害主要是粉碎机组、冷冻机组、真空泵产生的,噪声会引起听觉功能敏感度下降,甚至造成耳聋,或引起神经衰弱、心血管和消化系统疾病;噪声同时干扰和影响信息的交流,使工作人员听不清谈话或发出的语音信号,导致操作失误率上升,因此高噪音场所应采取消音、吸音处理和采用独立的隔音房。
3)振动机械设备在运行过程中会产生振动,振动危害有全身振动和局部振动,可导致接触人员中枢神经、植物神经功能紊乱等伤害。