冶炼烟气余热回收—余热发电技术
国内烟气余热利用技术的新进展

国内烟气余热利用技术的新进展国内烟气余热利用技术的新进展是当前能源领域的一个研究热点,也是节能减排的重要技术之一,已得到了广泛的应用,相关的尖端技术在不断发展。
烟气余热利用技术指的是从烟气中捕获余热,将余热转化为可利用的能源。
首先,国内烟气余热利用技术主要有三大技术方案:一是余热回收技术,即将烟气余热吸收到烟道内部的余热回收装置,通过烟气保温隔热系统,将烟气余热转化为温度更高的热水或蒸汽供企业使用;二是余热利用技术,即将烟气余热通过热交换器热力机等设备转化为可利用的能源,如电能、水冷却能源等;三是余热回收利用技术,即将烟气余热收集到烟道内部,然后由烟道内部的热交换器转化为可利用的能源。
其次,此外,还有一些新技术可以实现烟气余热的精细利用,如烟气热泵技术。
烟气热泵技术是利用烟气的温度差,将低温的烟气加热到较高的温度,再用来加热需要的热水或蒸汽,从而节约能源。
烟气热泵技术的优点在于它能够有效地利用烟气的余热,大大提高烟气余热的利用率,并且具有运行成本低、节能效果明显等优点。
此外,关于烟气余热利用技术,还有一些新的进展,如烟气余热回收利用技术,烟气余热回收利用技术是利用烟道内部的热交换器,将烟气余热转化为可利用的能源,如电能、水冷却能源等,从而节约能源。
再者,烟气余热利用技术还有一些新的发展,如余热发电技术。
余热发电技术是利用烟气余热,将其转化为电能,从而实现节能减排。
余热发电技术的优点在于可以有效地利用烟气余热,大大提高烟气余热的利用率,并且具有运行成本低、节能效果明显等优点。
最后,烟气余热利用技术还有一些新的发展,如余热蒸汽技术。
余热蒸汽技术是利用烟气余热,将其转化为可利用的蒸汽,从而实现节能减排。
余热蒸汽技术的优点在于可以有效地利用烟气余热,大大提高烟气余热的利用率,并且具有运行成本低、节能效果明显等优点。
总之,国内烟气余热利用技术已经取得了很大的进展,其中包括余热回收、余热利用、烟气热泵、余热发电、余热蒸汽等技术,它们可以有效利用烟气余热,从而节约能源,减少污染,为节能减排作出贡献。
转炉烟气余热回收流程

转炉烟气余热回收流程转炉是一种用于冶炼钢铁的设备,在生产过程中会产生大量的烟气。
这些烟气中含有大量的热能,如果不能有效地回收利用,不仅会造成能源的浪费,还会对环境造成污染。
因此,利用转炉烟气余热回收技术,将其中的热能回收利用,不仅可以降低能源消耗,还可以减少环境污染。
转炉烟气余热回收流程主要包括烟气净化、余热回收和余热利用三个步骤。
第一步,烟气净化。
转炉烟气中含有大量的粉尘、二氧化硫、氮氧化物等有害物质,需要进行净化处理。
烟气净化的方式主要包括干法和湿法两种方式。
干法烟气净化主要是利用静电除尘器、布袋除尘器等设备将烟气中的粉尘和微小颗粒物过滤掉。
湿法烟气净化则是将烟气通过喷淋等方式与水接触,使烟气中的有害气体转化为水溶液,进而进行分离和回收。
第二步,余热回收。
在烟气净化后,烟气中的热能仍然很高,需要通过余热回收设备进行回收利用。
常用的余热回收设备包括烟气余热锅炉、烟气换热器等。
烟气余热锅炉是利用烟气中剩余的热量产生蒸汽或热水的设备。
烟气换热器则是利用烟气与其他介质接触,将烟气中的热能传递给其他介质,进而产生蒸汽或热水。
这些蒸汽或热水可以用于工业生产或供热等领域。
第三步,余热利用。
回收到的余热可以直接供应给工业生产中的热源,也可以通过热电联产等方式将其转化为电能供应给电网。
热电联产技术是利用余热锅炉产生的高温高压蒸汽驱动汽轮机发电,并将过程中产生的低温余热通过换热器回收利用,从而实现能量的高效利用。
转炉烟气余热回收技术不仅可以降低能源消耗,还可以减少环境污染。
目前,该技术已经在钢铁、化工、建材等领域得到广泛应用,为企业节能减排、提高经济效益做出了贡献。
有色冶金烟气余热回收利用

艺周期性变化 , 这些烟气的特点都在很大程度上 影响着对有色冶金炉窑烟气余热的回收利用。 12 回收现 状 . 目前较为普遍的对有色炉窑的烟气余热进行 回收利用的方法有: ( )在 烟道安装余热锅炉 1 生产蒸汽 ;( )利用余热发电 ; ( )利用烟气 2 3
V0. O N 2 J3 D . Ma . 01 r2 1
冶
金
能
源
5 9
E ER OR ME A J U I AL I N GY F T l RG C NDU RY L S
有色 冶 金 烟气 余 热 回收利 用
张健敏 于 海
(. 1 洛阳栾川钼业集团冶炼有限责任公司, . 2 东北大学材料与冶金学院)
Z a gJa mi Yu Ha h n in n i
( . hn oyd n m S e igC . Ld 2 otes r nvr t) 1C i M l e u m ln o , t., .N r at U i sy a b t h e n ei
A s at T esu tno w s et f o eru e l e d syadt rbe s f t r・ bt c h i ao f at ha n r sm tl M i ut n epolm s e r t i e o nf o a ̄ n r h o i
温度在 6O一10 ℃之 间 的 中温烟气 余热 和温度 0 00
收稿 1期 : 1 0—1 3 2 0—1 0 1
的热效率也越低。因而尽可能最大限度地 回收烟 气余热是提高炉窑热效率的必要措施 。 另外 , 由于大多数有色金属冶炼所用 的原材 料都是硫化矿 , 炉窑产生的烟气 中含 S O 等腐蚀 性气体较多 , 并且大部分的烟气温度很高 因此烟 气容易对换热设备造成高温或低温腐蚀。同时 ,
冶炼烟气余热回收利用的技术研究

张 晓
( 昆明冶金研究院
云南昆明
6 5 0 0 3 1 )
广 / /
摘
节约材料 、 降低 成本方面具有独到的特点。 要: 近年来, 我 国的钢铁 工业飞速 的发展 , 钢铁产 \ 、 在热量 的刚收 、 现在进 行的烟气回收利用的形式大体上分为 三种 : 一种 是炯
L 、 \
关键词: 冶炼; 烟气余热; 余热回收; 节能
至 储水 箱 , 与 系 统互 补 后 送 至 热 用 户 。 2 . 2烟 气 余 热 回 收 利用 的解 决 方 法
随着工业的发展 , 能源 } 肖 耗量不 断地 增加 , 空气污染 日渐严
热 管式 换 热器 不仅 可 以降低 能 源 的消耗 还 能 降低排 炯 温
提高热能 的利用效 率 , 减少高 温炯气造成锅 炉壁的损坏 。使 重, 所 以当下减少能源 的消耗 , 合理利用 现有 能源 的二次 回收利 度 , 用热管式 的换热器 热阻极小 , 热 密度高 , 可 以克服 常规换热 器的 用是研究 的重要课题。烟气余热是二次能源 , 煤炭 、 石 油等不 可冉
烟气余 热虽然 热量很 高 , 得 到利 用 , 降低 了能 源的消耗 , 提高 了整体
另一方 面该 烟气余 热 回收装置能够把排 娴温度降低至 值, 但是烟气余 热回收利用的难度很高。因为若排烟温度低 , 锅炉 的经济性 , 6 0度 以下 , 有效地减少 了热污染 , 降低经济成本 。 尾部 受热面的烟气 和工 质的换热 温差 就会 减少 , 导致传热面积 的
耗 能 和 热 量 ,虽 然 在 节 能 方 面 我 国 也 在 努 力 并 且 取 得 了 一 些 效 下面设置落灰 斗, 这是 为了防止换热器工作时烟气 流速 下降时烟
烟气余热回收技术方案

烟气余热回收技术方案1. 背景介绍烟气是许多工业生产过程中产生的一种重要废气。
燃烧产生的烟气中含有大量的热量,如果不进行有效的回收利用,将会造成能源的浪费和环境的污染。
因此,烟气余热回收技术成为了重要的研究方向之一。
本文将介绍一种烟气余热回收技术方案,以实现高效能源利用和环境保护。
2. 技术原理该烟气余热回收技术方案基于换热原理,通过烟气与工艺流体之间的热量交换,实现热能回收。
具体的技术原理如下:1.烟气预处理:在烟气进入烟道前,对其进行预处理,去除大颗粒的烟尘和其他污染物,以确保烟气的净化程度和换热器的正常运行。
2.烟气与工艺流体换热:将烟气通过烟道引导至烟气换热器中,与工艺流体进行热量交换。
工艺流体可以是水、油等,在换热器内与烟气进行流体间的热交换,使烟气中的热量传递给工艺流体,从而实现热能的回收利用。
3.对工艺流体进行冷却:烟气中的热能传递给工艺流体后,工艺流体温度升高。
为了保证回收后的热能能够有效利用,需要对工艺流体进行冷却。
这可以通过使用冷却器或进行进一步的热量转移实现。
4.回收后的热能利用:冷却后的工艺流体可以用于供热、供暖或其他工业生产过程中的热能需求,从而实现能源的高效利用。
3. 技术优势该烟气余热回收技术方案具有以下优势:•高效能源利用:通过回收烟气中的热能,将原本浪费的能源转化为可用的能源,提高能源利用率。
•环境保护:减少煤、油等能源的消耗,降低二氧化碳等温室气体的排放,对环境具有积极的影响。
•经济效益:通过烟气余热的回收利用,降低了企业的能源消耗成本,提高了企业的经济效益。
•可持续发展:烟气余热回收技术是一种可持续发展的技术,有助于提高能源的可再生利用率,减少对自然资源的依赖。
4. 技术应用烟气余热回收技术可以应用于各个领域,包括但不限于以下几个方面:•工业生产:适用于钢铁、化工、电力等工业生产过程中产生的烟气,将烟气中的余热转化为工艺流体的热能需求,减少能源浪费。
•建筑供热:可将烟气余热应用于建筑供热系统中,为建筑提供温暖的供暖水源,减少传统能源的消耗。
重有色冶金炉窑余热回收利用技术规范
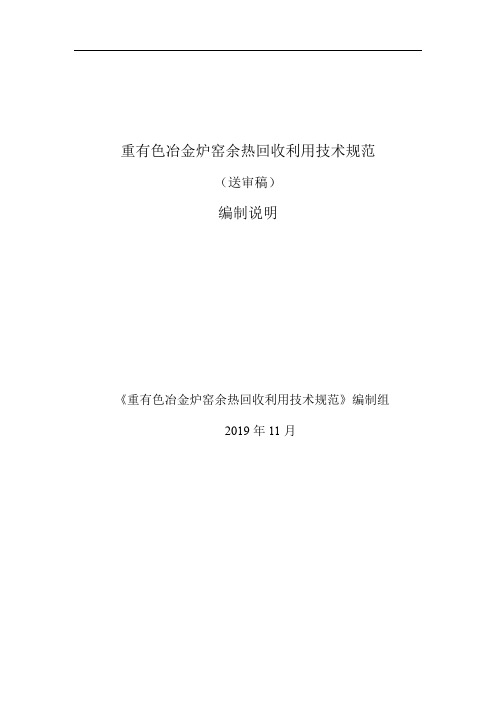
重有色冶金炉窑余热回收利用技术规范(送审稿)编制说明《重有色冶金炉窑余热回收利用技术规范》编制组2019年11月《重有色冶金炉窑余热回收利用技术规范》编制说明1.工作简况1.1重有色冶金可持续发展的需要随着社会的不断进步以及经济的快速发展,人们对有色金属的冶炼也提出了越来越高的要求。
其中,能源消耗大和环境保护要求高是有色冶炼行业中面临的主要问题。
为满足各项环保指标要求和降低能源消耗成本,开发针对有色金属冶炼系统中主要能耗设备冶金炉窑的预热回收技术至关重要。
当前,冶金炉窑的余热回收目前在国内外已有多种成熟的技术,各类技术不尽相同,缺少对该技术的技术性指导文件。
因此,通过制定《重有色冶金炉窑余热回收利用技术规范》来对冶金炉窑的余热回收规范化管理,有利于技术的标准化和规范化,同时将为贯彻执行相关法律法规及产业政策起到纽带作用。
我国有色金属工业单位产品能耗(标煤)约为 4.76t,约占全国能源消费量的3.5%以上。
其中铜、铝、铅、锌冶炼能耗占有色金属工业总能耗90%以上。
余热利用率低是造成能耗高的重要原因之一。
从另一角度看,我国工业余热资源丰富,广泛存在于工业各行业生产过程中,余热资源约占其燃料消耗总量的17%~67%,其中可回收率达60%,余热利用率提升空间大,节能潜力巨大。
工业余热回收利用被认为是一种“新能源”,近年来成为推进我国节能减排工作的重要内容。
有色金属工业作为高能耗行业,生产集中度小,但能耗高。
随着当今社会经济水平的不断提高以及现代工业的快速发展,有色金属的冶炼作为工业生产过程中的重要环节,其能源消耗情况以及资源回收利用水平不仅会对企业自身效益产生极其重要的直接影响,还会对社会经济、节能环保等方面产生间接影响。
伴随工业产业的不断发展以及能源消耗总量的不断增加,资源短缺也成为了未来一个时期人类发展所面对的一项重要问题,而烟气余热的回收和利用正是应对该问题的一个有效解决方案。
未来,余热回收在节能工作中仍占有极为重要的地位。
钢铁冶金行业余热发电技术
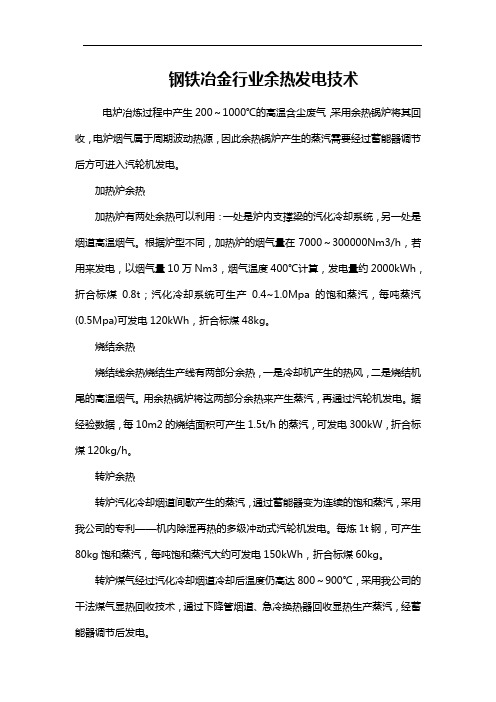
钢铁冶金行业余热发电技术电炉冶炼过程中产生200~1000℃的高温含尘废气,采用余热锅炉将其回收,电炉烟气属于周期波动热源,因此余热锅炉产生的蒸汽需要经过蓄能器调节后方可进入汽轮机发电。
加热炉余热加热炉有两处余热可以利用:一处是炉内支撑梁的汽化冷却系统,另一处是烟道高温烟气。
根据炉型不同,加热炉的烟气量在7000~300000Nm3/h,若用来发电,以烟气量10万Nm3,烟气温度400℃计算,发电量约2000kWh,折合标煤0.8t;汽化冷却系统可生产0.4~1.0Mpa的饱和蒸汽,每吨蒸汽(0.5Mpa)可发电120kWh,折合标煤48kg。
烧结余热烧结线余热烧结生产线有两部分余热,一是冷却机产生的热风,二是烧结机尾的高温烟气。
用余热锅炉将这两部分余热来产生蒸汽,再通过汽轮机发电。
据经验数据,每10m2的烧结面积可产生1.5t/h的蒸汽,可发电300kW,折合标煤120kg/h。
转炉余热转炉汽化冷却烟道间歇产生的蒸汽,通过蓄能器变为连续的饱和蒸汽,采用我公司的专利——机内除湿再热的多级冲动式汽轮机发电。
每炼1t钢,可产生80kg饱和蒸汽,每吨饱和蒸汽大约可发电150kWh,折合标煤60kg。
转炉煤气经过汽化冷却烟道冷却后温度仍高达800~900℃,采用我公司的干法煤气显热回收技术,通过下降管烟道、急冷换热器回收显热生产蒸汽,经蓄能器调节后发电。
电炉余热冲渣热水。
每吨铁排出约0.3t渣,每吨渣可产生80~95℃,5~10t的冲渣水,将这部分热水减压产生低压蒸汽,再进入饱和蒸汽凝汽式汽轮机发电。
每吨90℃热水可发电1.5kWh,折标煤0.6kg,80℃热水可发电1kWh,折标煤0.4kg。
干法熄焦采用惰性气体来冷却红焦,加热后的气体在余热锅炉中产生蒸汽,蒸汽可发电或并入蒸汽管网。
吨焦可生产3.9Mpa、300℃的蒸汽0.45t~0.6t,可发电85~115kWh,折合标煤35~46kg。
高炉煤气余压利用高炉炉顶煤气的压力能和热能,通过透平膨胀机做功发电,但不影响煤气后续利用。
烟气余热回收技术方案

烟气余热回收技术方案一、引言工业生产过程中产生的烟气中含有大量的余热能量,如果能够将这部分余热回收并有效利用,不仅可以提高能源利用率,减少能源消耗,还可以减少对环境的污染。
因此,烟气余热回收技术的开发和应用对于企业的可持续发展具有重要意义。
二、烟气余热回收技术的原理烟气余热回收技术主要包括两个方面的内容:烟气的热量回收和余热的利用。
烟气的热量回收主要是通过烟气净化设备对烟气中的热量进行回收,常见的技术有烟气换热器、烟气脱硫设备等。
余热的利用则需要通过适当的设备将余热转化为可用能源,常见的方式有蒸汽循环、制冷循环等。
三、烟气换热器的设计和应用烟气换热器是烟气余热回收的核心设备,其主要功能是通过换热器将烟气中的热量传递给工艺流体,从而实现能量的转化。
烟气换热器的设计应考虑以下几个因素:1.换热器的材料选择:应根据烟气中存在的腐蚀物质和工艺流体的特性选择合适的材料,常见的材料有不锈钢、碳钢等。
2.换热器的热交换效率:应通过优化换热器的结构和流体的流动方式,提高热交换效率。
可以采用流体的迂回流动、增加流体的速度等方式提高换热效率。
3.换热器的清洁方式:由于烟气中含有灰尘和颗粒物等杂质,容易在换热器的表面形成污垢,影响换热效果。
因此,应考虑对换热器进行清洗和维护。
四、余热利用技术方案1.蒸汽循环技术:将回收的余热用于蒸汽发生器中,产生蒸汽用于工艺或供暖等用途。
蒸汽循环技术的优点是热效率高,适用于大量余热的回收利用。
2.制冷循环技术:将回收的余热用于制冷设备中,通过制冷设备产生低温热能,可用于制冷或其他低温工艺需求。
制冷循环技术的优点是适用于低温余热的回收利用。
3.热泵技术:热泵是一种将低温热能转化为高温热能的装置,通过热泵技术可以将回收的低温余热升温并利用于工艺流程。
热泵技术的优点是能够实现高效率的能量转化,适用于低温余热的回收利用。
五、烟气余热回收技术应用案例1.钢铁行业:钢铁生产中烟气中含有大量高温余热,可以通过烟气换热器将余热回收并用于烧结热风炉、蒸汽发生器等设备,提高能源利用率。
- 1、下载文档前请自行甄别文档内容的完整性,平台不提供额外的编辑、内容补充、找答案等附加服务。
- 2、"仅部分预览"的文档,不可在线预览部分如存在完整性等问题,可反馈申请退款(可完整预览的文档不适用该条件!)。
- 3、如文档侵犯您的权益,请联系客服反馈,我们会尽快为您处理(人工客服工作时间:9:00-18:30)。
冶炼烟气余热回收—余热发电技术
一、所属行业:有色金属行业
二、技术名称:冶炼烟气余热回收—余热发电技术
三、适用范围:有色金属、钢铁、水泥等行业
四、技术内容:
1.技术原理
利用强制循环余热锅炉回收冶炼烟气余热,生产中压饱和蒸汽,配套饱和蒸汽汽轮机组,发电机组抽汽供热,实现供热、电联产,最大限度提高余热蒸汽利用效率。
2.关键技术
国内自行设计制造的耐高温腐蚀性、粘结性冶炼烟气余热锅炉。
工艺流程
原水→脱盐→除氧→余热锅炉→汽轮发电机组→凝结水→余热锅炉。
五、技术指标:
1.节能技术相关生产环节的能耗现状:
有色行业冶炼高温烟气余热损耗占较大比率,有色系统余热锅炉应用率不高,而配套余热发电站的企业更少,余热利用水平较低。
2.技术指标:
余热锅炉蒸汽量5-100t/h,工作压力3.0-5.0MPa,蒸汽温度一般为饱和温度(236-265℃)。
汽轮发电机入口压力3.0-5.0MPa,抽汽压力0.5-1.0MPa,排气压力
0.008-0.03 MPa,电站容量0.5-15MW。
六、技术鉴定及应用情况:
本技术已在云南铜业股份有限公司等多家企业投入商业运行,尚没有进行过技术鉴定。
在云南铜业股份有限公司、云南冶金集团驰宏锌锗股份公司、云南锡业股份有限公司、白银有色金属公司等多家企业投入运行,取得良好经济效益。
七、典型用户及投资效益:
应用典型案例一:云南铜业股份有限公司
余热电站规模9470kW,汽轮发电机组1台,另配套ISA炉余热锅炉1台,转炉余热锅炉2台、阳极炉余热锅炉2台。
总蒸汽量55-85t/h,蒸汽压力4.2MPa,蒸汽温度253℃。
建设期为1年,节能技改投资额为6232万元(不包括余热锅炉系统投资)。
年发电量达到68752MWh,年供热量573772GJ。
年创产值约为2539万元,新增利润总额1531万元,投资回收期4.8年。
应用典型案例二:云南锡业股份有限公司
国产汽轮发电机组1台,功率6000kW,电压6kV,进汽压力2.5MPa,蒸汽量30t/h;余热锅炉3台。
建设期为1年,余热发电站投资为2456万元(不包括余热锅炉系统投资)。
年发电量达到39600MWh,年创产值约为1660万元,新增利润总额880万元。
投资回收期3年。
八、推广前景和节能潜力:
本技术可用于有色行业的各个大、中型冶炼厂,其余热锅炉蒸汽量大于5t/h,压力大于1.0MPa。
也可用于钢铁、水泥等相关行业。
“十一五”期间,该技术在大、中型企业推广率可达85%以上,需要总投入约为2-3亿元,可取得总节能量444100吨标煤/年(按中等容量估算)。
九、推广措施及建议:
1.在项目立项和实施过程中,将冶炼烟气余热回收-余热发电同步立项,同步实施余热利用也应热电联产,提高余热利用效率。
2.政府部门给予优惠贷款、提高上网电价。
3.鼓励企业发展余热电站,取消某些地方存在的限制上网的规定。