曲轴的热处理工艺.
热处理淬火工艺规范

热处理车间淬火工艺规范一、调质1.1 调质定义为了达到产品的工艺硬度要求,得到回火索氏体,得到良好的强韧性,提高使用性能和寿命,因此曲轴和连杆产品需进行调质处理。
调质,即淬火加高温回火,以获得回火索氏体组织,主要用于中碳碳素结构钢或低合金结构钢以获得良好的综合机械性能。
1.1.1 淬火的定义淬火是将钢加热到临界温度Ac3 (亚共析钢)或Ac1 (过共析钢)以上温度,保温一段时间,使之全部或部分奥氏体化,然后以大于临界冷却速度的冷速快冷到Ms以下(或Ms附近等温)进行马氏体(或贝氏体)转变的热处理工艺。
通常也将铝合金、铜合金、钛合金、钢化玻璃等材料的固溶处理或带有快速冷却过程的热处理工艺也称为淬火。
1.1.2淬火的目的淬火的目的是使过冷奥氏体进行马氏体或贝氏体转变,得到马氏体或贝氏体组织,然后配合以不同温度的回火,以大幅提高钢的刚性、硬度、耐磨性、疲劳强度以及韧性等,从而满足各种机械零件和工具的不同使用要求。
也可以通过淬火满足某些特种钢材的铁磁性、耐蚀性等特殊的物理、化学性能。
1.1.3回火的定义回火是工件淬硬后加热到Ac1 (加热时珠光体向奥氏体转变的开始温度)以下的某一温度,保温一定时间,然后冷却到室温的热处理工艺。
按回火温度范围,回火可分为低温回火、中温回火和高温回火。
4.1.1低温回火:工件在150~250C进行的回火。
目的是保持淬火工件高的硬度和耐磨性,降低淬火残留应力和脆性,回火后得到回火马氏体,指淬火马氏体低温回火时得到的组织。
应用范围:主要应用于各类高碳钢的工具、刃具、量具、模具、滚动轴承、渗碳及表面淬火的零件等。
4.1.2中温回火:工件在350〜500 C之间进行的回火。
目的是得到较高的弹性和屈服点,适当的韧性。
回火后得到回火屈氏体,指马氏体回火时形成的铁素体基体内分布着极其细小球状碳化物(或渗碳体)的复相组织。
应用范围:主要用于弹簧、发条、锻模、冲击工具等。
4.1.3高温回火:工件在500~650C以上进行的回火。
曲轴加工工艺

曲轴加工工艺曲轴的加工工艺、设计步骤、流程引擎的主要旋转机件,装上连杆后,可承接连杆的上下(往复)运动变成循环(旋转)运动。
是发动机上的一个重要的机件,其材料是由碳素结构钢或球墨铸铁制成的,有两个重要部位:主轴颈,连杆颈,(还有其他)。
主轴颈被安装在缸体上,连杆颈与连杆大头孔连接,连杆小头孔与汽缸活塞连接,是一个典型的曲柄滑块机构。
曲轴的润滑主要是指与摇臂间轴瓦的润滑和两头固定点的润滑.这个一般都是压力润滑的,曲轴中间会有油道和各个轴瓦相通,发动机运转以后靠机油泵提供压力供油进行润滑、降温。
发动机工作过程就是,活塞经过混合压缩气的燃爆,推动活塞做直线运动,并通过连杆将力传给曲轴,由曲轴将直线运动转变为旋转运动。
曲轴的旋转是发动机的动力源。
也是整个船的源动力。
曲轴制造技术/工艺的进展1、球墨铸铁曲轴毛坯铸造技术(1)熔炼高温低硫纯净铁水的获得是生产高质量球墨铸铁的关键。
国内主要是以冲天炉为主的生产设备,铁水未进行预脱硫处理;其次是高纯生铁少、焦炭质量差。
目前已采用双联外加预脱硫的熔炼方法,采用冲天炉熔化铁水,经炉外脱硫,然后在感应电炉中升温并调整成分。
目前,在国内铁水成分的检测已普遍采用真空直读光谱仪来进行。
(2)造型气流冲击造型工艺明显优于粘土砂型工艺,可获得高精度的曲轴铸件,该工艺制作的砂型具有无反弹变形量等特点,这对于多拐曲轴尤为重要。
目前,国内已有一些曲轴生产厂家从德国、意大利、西班牙等国引进气流冲击造型工艺,不过,引进整条生产线的只有极少数厂家,如文登天润曲轴有限公司引进了德国KW铸造生产线。
2、钢曲轴毛坯的锻造技术近几年来,国内已引进了一批先进的锻造设备,但由于数量少,加之模具制造技术和其他一些设施跟不上,使一部分先进设备未发挥应有的作用。
从总体上来讲,需改造和更新的陈旧的普通锻造设备多,同时,落后的工艺和设备仍占据主导地位,先进技术有所应用但还不普遍。
3、机械加工技术目前国内曲轴生产线多数由普通机床和专用机床组成,生产效率和自动化程度相对较低。
机械加工常见热处理工艺

渗碳渗碳热处理渗碳:是对金属表面处理的一种,采用渗碳的多为低碳钢或低合金钢,具体方法是将工件置入具有活性渗碳介质中,加热到900--950摄氏度的单相奥氏体区,保温足够时间后,使渗碳介质中分解出的活性碳原子渗入钢件表层,从而获得表层高碳,心部仍保持原有成分。
相似的还有低温渗氮处理。
这是金属材料常见的一种热处理工艺,它可以使渗过碳的工件表面获得很高的硬度,提高其耐磨程度。
概述渗碳(carburizing/carburization)是指使碳原子渗入到钢表面层的过程。
也是使低碳钢的工件具有高碳钢的表面层,再经过淬火和低温回火,使工件的表面层具有高硬度和耐磨性,而工件的中心部分仍然保持着低碳钢的韧性和塑性。
渗碳工件的材料一般为低碳钢或低碳合金钢(含碳量小于0.25%)。
渗碳后﹐钢件表面的化学成分可接近高碳钢。
工件渗碳后还要经过淬火﹐以得到高的表面硬度﹑高的耐磨性和疲劳强度﹐并保持心部有低碳钢淬火后的强韧性﹐使工件能承受冲击载荷。
渗碳工艺广泛用于飞机﹑汽车和拖拉机等的机械零件﹐如齿轮﹑轴﹑凸轮轴等。
渗碳工艺在中国可以上溯到2000年以前。
最早是用固体渗碳介质渗碳。
液体和气体渗碳是在20世纪出现并得到广泛应用的。
美国在20年代开始采用转筒炉进行气体渗碳。
30年代﹐连续式气体渗碳炉开始在工业上应用。
60年代高温(960~1100℃)气体渗碳得到发展。
至70年代﹐出现了真空渗碳和离子渗碳。
分类按含碳介质的不同﹐渗碳可分为气体渗碳、固体渗碳﹑液体渗碳﹑和碳氮共渗(氰化)。
气体渗碳是将工件装入密闭的渗碳炉内,通入气体渗剂(甲烷、乙烷等)或液体渗剂(煤油或苯、酒精、丙酮等),在高温下分解出活性碳原子,渗入工件表面,以获得高碳表面层的一种渗碳操作工艺。
固体渗碳是将工件和固体渗碳剂(木炭加促进剂组成)一起装在密闭的渗碳箱中,将箱放入加热炉中加热到渗碳温度,并保温一定时间,使活性碳原子渗人工件表面的一种最早的渗碳方法。
液体渗碳是利用液体介质进行渗碳,常用的液体渗碳介质有:碳化硅,―603‖渗碳剂等。
汽车发动机曲轴的热处理与失效分析
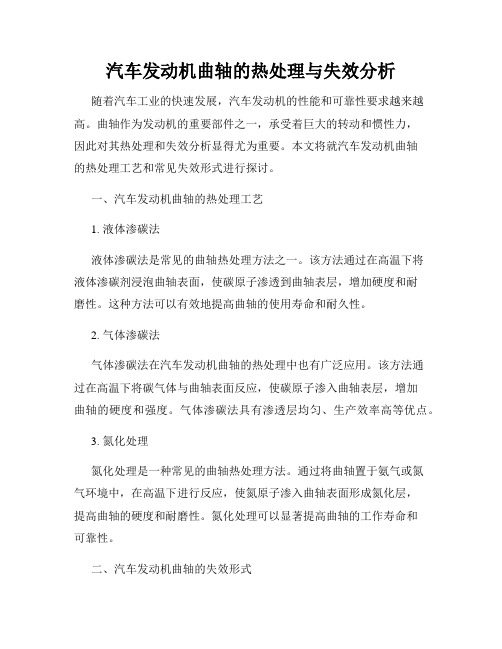
汽车发动机曲轴的热处理与失效分析随着汽车工业的快速发展,汽车发动机的性能和可靠性要求越来越高。
曲轴作为发动机的重要部件之一,承受着巨大的转动和惯性力,因此对其热处理和失效分析显得尤为重要。
本文将就汽车发动机曲轴的热处理工艺和常见失效形式进行探讨。
一、汽车发动机曲轴的热处理工艺1. 液体渗碳法液体渗碳法是常见的曲轴热处理方法之一。
该方法通过在高温下将液体渗碳剂浸泡曲轴表面,使碳原子渗透到曲轴表层,增加硬度和耐磨性。
这种方法可以有效地提高曲轴的使用寿命和耐久性。
2. 气体渗碳法气体渗碳法在汽车发动机曲轴的热处理中也有广泛应用。
该方法通过在高温下将碳气体与曲轴表面反应,使碳原子渗入曲轴表层,增加曲轴的硬度和强度。
气体渗碳法具有渗透层均匀、生产效率高等优点。
3. 氮化处理氮化处理是一种常见的曲轴热处理方法。
通过将曲轴置于氨气或氮气环境中,在高温下进行反应,使氮原子渗入曲轴表面形成氮化层,提高曲轴的硬度和耐磨性。
氮化处理可以显著提高曲轴的工作寿命和可靠性。
二、汽车发动机曲轴的失效形式1. 疲劳断裂汽车发动机曲轴承受着巨大的转动和振动力,长期工作下容易发生疲劳断裂。
曲轴的弯曲应力和旋转应力作用下,会产生应力集中现象,导致曲轴发生疲劳断裂。
疲劳断裂的发生会导致曲轴的完全失效,严重影响发动机的工作正常性。
2. 磨损曲轴在长时间工作中,会与连杆轴承、活塞等零部件产生摩擦,从而导致磨损。
磨损严重影响曲轴的精度和运转平稳性,进一步影响整个发动机的工作效率和寿命。
3. 腐蚀汽车发动机在工作中,由于油污和湿度等环境因素的影响,曲轴表面容易发生腐蚀。
腐蚀会导致曲轴表面的金属材料逐渐溶解,使曲轴的强度大幅下降,最终导致曲轴的失效。
三、失效分析与预防措施1. 失效分析在曲轴的热处理与失效分析中,需要通过工艺参数的分析和实验数据的对比,来确定曲轴热处理工艺的优化方案。
同时,可以通过金相显微镜等测试手段,对曲轴的金属组织进行分析,查找潜在的裂纹和磨损等问题。
曲轴的生产工艺
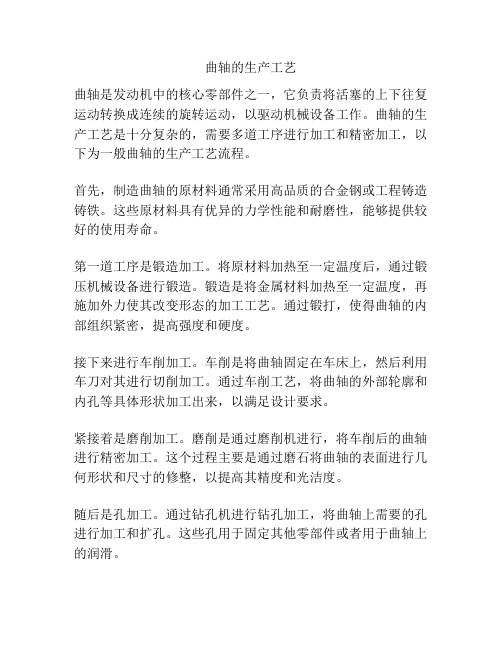
曲轴的生产工艺曲轴是发动机中的核心零部件之一,它负责将活塞的上下往复运动转换成连续的旋转运动,以驱动机械设备工作。
曲轴的生产工艺是十分复杂的,需要多道工序进行加工和精密加工,以下为一般曲轴的生产工艺流程。
首先,制造曲轴的原材料通常采用高品质的合金钢或工程铸造铸铁。
这些原材料具有优异的力学性能和耐磨性,能够提供较好的使用寿命。
第一道工序是锻造加工。
将原材料加热至一定温度后,通过锻压机械设备进行锻造。
锻造是将金属材料加热至一定温度,再施加外力使其改变形态的加工工艺。
通过锻打,使得曲轴的内部组织紧密,提高强度和硬度。
接下来进行车削加工。
车削是将曲轴固定在车床上,然后利用车刀对其进行切削加工。
通过车削工艺,将曲轴的外部轮廓和内孔等具体形状加工出来,以满足设计要求。
紧接着是磨削加工。
磨削是通过磨削机进行,将车削后的曲轴进行精密加工。
这个过程主要是通过磨石将曲轴的表面进行几何形状和尺寸的修整,以提高其精度和光洁度。
随后是孔加工。
通过钻孔机进行钻孔加工,将曲轴上需要的孔进行加工和扩孔。
这些孔用于固定其他零部件或者用于曲轴上的润滑。
最后是热处理。
利用热处理技术对曲轴进行加热,使其组织结构发生变化,提高其机械性能。
热处理可以增加曲轴的硬度和耐磨性,提高其使用寿命和稳定性。
整个生产工艺中还包括一些次要工序,如喷漆、平衡、清洗等。
喷漆是为了防止曲轴生锈,平衡是为了保证曲轴运转过程中的平衡性,清洗是为了去除加工中产生的铁屑和油渍。
综上所述,曲轴的生产工艺是一个复杂的过程,需要多道工序进行加工和精密加工。
每个工序都需要严格控制,确保曲轴的质量和使用寿命。
只有生产出合格的曲轴,才能够保证发动机的运行稳定性和可靠性。
发动机曲轴加工工艺及其夹具设计
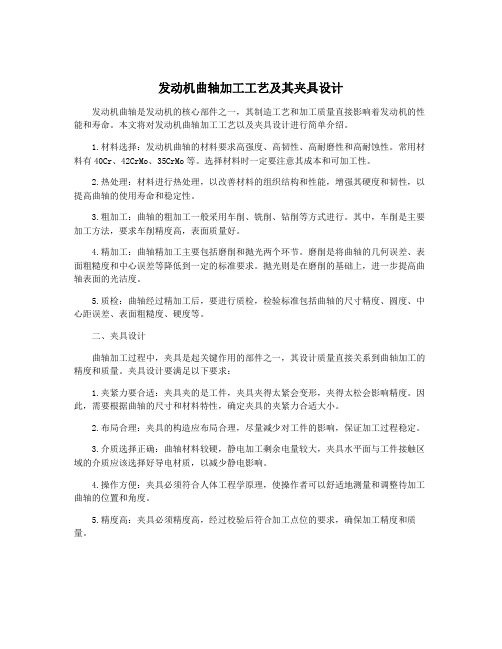
发动机曲轴加工工艺及其夹具设计发动机曲轴是发动机的核心部件之一,其制造工艺和加工质量直接影响着发动机的性能和寿命。
本文将对发动机曲轴加工工艺以及夹具设计进行简单介绍。
1.材料选择:发动机曲轴的材料要求高强度、高韧性、高耐磨性和高耐蚀性。
常用材料有40Cr、42CrMo、35CrMo等。
选择材料时一定要注意其成本和可加工性。
2.热处理:材料进行热处理,以改善材料的组织结构和性能,增强其硬度和韧性,以提高曲轴的使用寿命和稳定性。
3.粗加工:曲轴的粗加工一般采用车削、铣削、钻削等方式进行。
其中,车削是主要加工方法,要求车削精度高,表面质量好。
4.精加工:曲轴精加工主要包括磨削和抛光两个环节。
磨削是将曲轴的几何误差、表面粗糙度和中心误差等降低到一定的标准要求。
抛光则是在磨削的基础上,进一步提高曲轴表面的光洁度。
5.质检:曲轴经过精加工后,要进行质检,检验标准包括曲轴的尺寸精度、圆度、中心距误差、表面粗糙度、硬度等。
二、夹具设计曲轴加工过程中,夹具是起关键作用的部件之一,其设计质量直接关系到曲轴加工的精度和质量。
夹具设计要满足以下要求:1.夹紧力要合适:夹具夹的是工件,夹具夹得太紧会变形,夹得太松会影响精度。
因此,需要根据曲轴的尺寸和材料特性,确定夹具的夹紧力合适大小。
2.布局合理:夹具的构造应布局合理,尽量减少对工件的影响,保证加工过程稳定。
3.介质选择正确:曲轴材料较硬,静电加工剩余电量较大,夹具水平面与工件接触区域的介质应该选择好导电材质,以减少静电影响。
4.操作方便:夹具必须符合人体工程学原理,使操作者可以舒适地测量和调整待加工曲轴的位置和角度。
5.精度高:夹具必须精度高,经过校验后符合加工点位的要求,确保加工精度和质量。
汽车曲轴的软氮化技术
汽车曲轴的软氮化技术为提高曲轴的疲劳强度,许多曲轴生产厂采用了气体软氮化技术(气体软氮化是一种由液体软氮化发展起来的、化学热处理工艺,其实质是以渗氮为主的低温碳氮共渗。
它的特点是处理温度低、时间短,工件变形小,质量稳定,不受钢种限制,能显著提高零件的耐磨性、疲劳强度、抗咬合、抗擦伤等性能,同时还能解决液体软氮化中的毒性问题,避免了公害,因而劳动条件好。
此外,设备和操作都简单,容易推广。
其基本原理是气体软氮化的原理是在530°~580℃的气氛中产生2CO →[C]+CO_2(渗碳)及2NH3→2[N]+3H_2(氮化)反应,使钢铁表面形成氮化物或碳氮化物。
),其中采用这项技术以山东曲轴总厂、潍坊柴油机厂、重汽集团复强动力公司等为典型代表。
仅山东曲轴总厂,就拥有连续软氮化生产设备及5-2型气体软氮化设备近10多台。
而重汽集团复强动力公司设备能力达到技术国内最先进、功率最大、装炉量最多,同时比同行业设备更具有节能环保效应。
目前,国内生产曲轴所采用的典型材料为45钢和42CrMoTi。
曲轴气体软氮化与处理其他软氮化零件相类似,其氮化工艺过程一般要经过前清洗、升温、保温、冷却、后清洗等5个阶段,包括出装炉。
不同的厂家在气体软氮化工艺上略有不同。
1.前清洗工艺待处理零件装炉前应通过清洗使零件表面清洁无油,目前采用的主要清洗方法主要有下列方式:高温蒸汽加清洗剂洗涤然后加高温蒸汽漂洗涤、自动清洗机清洗、汽油擦洗。
清洗的好坏将直接影响曲轴的处理质量和延长处理周期。
如果曲轴表面脏,处理后的曲轴表面附着很多碳黑,既影响产品外观又影响产品质量。
经改进清洗工艺后,处理质量大大提高。
据实际经验来看,表面清洁易形成连续的厚度较为均匀的化合物层,反之则不易形成连续和厚度均匀的化合物层。
而在气体软氮化时化合物层对硬度、耐磨及抗疲劳性能有较大贡献。
本文的第三种方式是在生产条件不具备时的变通方法,仅适用于小规模清洗。
2.预氧化工艺为保证零件性能的综合要求,在气体软氮化之前一般还需要进行预先热处理,气体软氮化的预热温度一般取400~490℃,保温1h左右,去除工件表面油污、油脂,并在表面形成一层氧化物,使(合金)氮化物缓慢形成,使深层更加均匀。
金属工艺学(第五版上册)课后答案
1、说明σS 、σ0.2 、σb、σ-1 、δ%、αk、45-50HRC、300HBS的名称含义答案:见教材。
45-50HRC表示洛氏硬度为45-50;300HBS表示布氏硬度为300.2、解释应力与应变的概念答:应力:物体由于外因(受力、湿度变化等)而变形时,在物体内各部分之间产生相互作用的内力,以抵抗这种外因的作用,并力图使物体从变形后的位置回复到变形前的位置。
在所考察的截面某一点单位面积上的内力称为应力。
应变:物体受力产生变形时,体内各点处变形程度一般并不相同。
用以描述一点处变形的程度的力学量是该点的应变。
为此可在该点处到一单元体,比较变形前后单元体大小和形状的变化。
1、说明晶粒粗细对力学性能的影响。
一般情况下,晶粒越细小,金属材料的强度和硬度越高,塑性和韧性越好。
因为晶粒越小,晶界越多。
晶界处的晶体排列是非常不规则的,晶面犬牙交错,互相咬合,因而加强了金属间的结合力。
工业中常用细化晶粒的方法来提高金属材料的机械性能,称为细晶强化。
晶粒的大小与过冷度和变质处理密切相关:过冷度:过冷度越大,产生的晶核越多,导致晶粒越细小。
通常采用改变浇注温度和冷却条件的办法来细化晶粒。
变质处理:也叫孕育处理。
金属液中晶核多,则晶粒细小。
通常采用浇注前添加变质剂的办法来促进晶核产生,以拟制晶粒长大。
2、你如何理解相与组织,指出Fe -C状态图中的相与组织。
相与组织相是指材料中结构相同、化学成分及性能同一的组成部分,相与相之间有界面分开。
“相”是合金中具有同一原子聚集状态,既可能是一单相固溶体也可能是一化合物;组织一般系指用肉眼或在显微镜下所观察到的材料内部所具有的某种形态特征或形貌图像,实质上它是一种或多种相按一定方式相互结合所构成的整体的总称。
因此,相与组织的区别就是结构与组织的区别,结构描述的是原子尺度,而组织则指的是显微尺度。
合金的组织是由相组成的,可由单相固溶体或化合物组成,也可由一个固溶体和一个化合物或两个固溶体和两个化合物等组成。
曲轴的热处理
曲轴的热处理下载温馨提示:该文档是我店铺精心编制而成,希望大家下载以后,能够帮助大家解决实际的问题。
文档下载后可定制随意修改,请根据实际需要进行相应的调整和使用,谢谢!并且,本店铺为大家提供各种各样类型的实用资料,如教育随笔、日记赏析、句子摘抄、古诗大全、经典美文、话题作文、工作总结、词语解析、文案摘录、其他资料等等,如想了解不同资料格式和写法,敬请关注!Download tips: This document is carefully compiled by the editor. I hope that after you download them, they can help yousolve practical problems. The document can be customized and modified after downloading, please adjust and use it according to actual needs, thank you!In addition, our shop provides you with various types of practical materials, such as educational essays, diary appreciation, sentence excerpts, ancient poems, classic articles, topic composition, work summary, word parsing, copy excerpts,other materials and so on, want to know different data formats and writing methods, please pay attention!曲轴是内燃机的重要零部件之一,在发动机运转过程中起着转动连杆的作用。
发动机曲轴的加工工艺
济源职业技术学院毕业设计设计任务书设计题目:发动机曲轴的加工工艺设计要求:通过对曲轴的了解认识,在掌握曲轴的相关概念、性能的基础上,能够合理的制定一套加工曲轴的工艺过程。
其中包括它的毛坯及材料的选定等,确定其加工路线,并能对其特点进行合理的分析和阐述。
从而初步掌握发动机曲轴的加工工艺。
设计进度要求:第一周:简述曲轴的结构、性能及应用;第二周:确定曲轴的加工工艺过程;第三周:分析曲轴的加工工艺特点;第四周:确定曲轴的机械加工余量、工序尺寸及公差;第五周:根据要求绘制图纸及论文的撰写,打电子稿;第六周:经老师检查后修改毕业论文;第七周:打印论文,完成毕业设计;第八周:进行论文答辩指导老师(签名):摘要曲轴是车辆发动机的关键零件之一,其性能好坏直接影响到车辆发动机的质量和寿命.曲轴在发动机中承担最大负荷和全部功率,承受着强大的方向不断变化的弯矩及扭矩,同时经受着长时间高速运转的磨损,因此要求曲轴材质具有较高的刚性、疲劳强度和良好的耐磨性能。
发动机曲轴的作用是将活塞的往复直线运动通过连杆转化为旋转运动,从而实现发动机由化学能转变为机械能的输出。
本课题仅175Ⅱ型柴油机曲轴的加工工艺的分析与设计进行探讨。
工艺路线的拟定是工艺规程制订中的关键阶段,是工艺规程制订的总体设计。
所撰写的工艺路线合理与否,不但影响加工质量和生产率,而且影响到工人、设备、工艺装备及生产场地等的合理利用,从而影响生产成本。
所以,本次设计是在仔细分析曲轴零件加工技术要求及加工精度后,合理确定毛坯类型,经过查阅相关参考书、手册、图表、标准等技术资料,确定各工序的定位基准、机械加工余量、工序尺寸及公差,最终制定出曲轴零件的加工工序卡片。
关键词:发动机,曲轴,工艺分析,工艺设计目录摘要 (Ⅲ)1概述 (1)1.1 曲轴的类型结构和应用 (1)1.1.1 曲轴的类型 (1)1.1.2 曲轴的结构 (4)1.1.3 曲轴的应用 (6)2 确定曲轴的加工工艺过程 (7)2.1 曲轴的结构特点 (7)2.2 曲轴的主要技术要求分析 (7)2.3 曲轴的材料和毛坯的确定 (8)2.4 曲轴的机械加工工艺过程 (8)2.5 曲轴的机械加工工艺路线 (8)3 曲轴的机械加工工艺过程分析 (9)3.1 曲轴的机械加工工艺特点 (9)3.1.1 形状复杂 (10)3.1.2 刚性差 (10)3.1.3 技术要求高 (10)3.2 曲轴的机械加工工艺特点分析 (10)3.3 曲轴主要加工工序分析 (11)3.3.1 铣曲轴两端面及钻中心孔 (11)3.3.2 曲轴主轴颈的车削 (11)3.3.3 曲轴连杆轴颈的车削 (12)3.3.4 键槽加工 (12)3.3.5 轴颈的磨削 (12)4 机械加工余量工序尺寸及公差的确定 (13)4.1 曲轴主要加工表面的工序安排 (13)4.2 机械加工余量工序尺寸及公差的确定 (13)4.2.1 主轴颈工序尺寸及公差的确定 (13)4.2.2 连杆轴颈工序尺寸及公差的确定 (14)4.2.3 φ220-0.12 mm外圆工序尺寸及公差的确定 (14)4.2.4 φ200- 0.021 mm外圆工序尺寸及公差的确定 (14)4.3 确定工时定额 (14)4.4 连杆机械加工工艺过程卡的制定 (15)5结论 (15)致谢 (16)参考文献 (17)附录 (18)1 概述1.1 曲轴的类型结构及应用1.1.1 曲轴的类型曲轴有整体曲轴、组合曲轴和半组合曲轴三种结构形式,一般采用整体曲轴。
- 1、下载文档前请自行甄别文档内容的完整性,平台不提供额外的编辑、内容补充、找答案等附加服务。
- 2、"仅部分预览"的文档,不可在线预览部分如存在完整性等问题,可反馈申请退款(可完整预览的文档不适用该条件!)。
- 3、如文档侵犯您的权益,请联系客服反馈,我们会尽快为您处理(人工客服工作时间:9:00-18:30)。
曲轴的热处理工艺
曲轴是引擎的主要旋转机件,装上连杆后,可承接连杆的上下(往复运动变成循
环(旋转运动。
是发动机上的一个重要的机件,其材料是由碳素结构钢或球墨铸铁制成的。
曲轴的性能在很大程度上影响着汽车发动机的可靠性与寿命。
曲轴在发动机中承担着最大的负荷和全部的功率, 承担着强大的方向不断变化的弯矩和扭矩, 同时承受着长时间的高速运转的磨损, 圆角过渡处处于薄弱环节,主轴颈与圆角的过渡处更为严重。
因而,需要合适的热处理工艺,以保证其达到所要求的各项性能指标。
在曲轴工作的过程中,往复的惯性力和离心力使之承受很大的弯曲 ---扭转应力, 轴颈表面容易磨损, 且轴颈与曲臂的过渡圆角处最为薄弱。
除曲轴的材质, 加工因素外,曲轴的工作条件(温度、环境介质、负荷特性等都是影响曲轴服役的。
曲轴的主要失效形式有(1疲劳断裂:多数断裂时曲柄与轴颈的圆角处产生疲劳裂纹, 随后向曲柄深处发展, 造成曲柄的断裂, 其次是曲柄中部的油道内壁产生裂纹,发展为曲柄处的断裂。
(2轴颈表面的严重磨损。
因此, 曲轴的选材十分重要, 既需要满足曲轴的力学性能, 也需要考虑强度和耐磨性。
由于曲轴需要承受交变的弯曲 ---扭转载荷以及发动机的大的功率, 因此,要求其具有高的强度,良好的耐磨、耐疲劳性以及循环韧性等。
因而,根据曲轴材料的要求,各项技术要求,及材料的成分,机械性能,淬透性,同时需考虑成本的经济性,最终可以选择 40Cr 作为汽车发动机的材料。
所以曲轴的大致加工路线是, 锻造→正火→机械加工→去应力退火→调质处理→表面热处理 (高频淬火 +低温回火 , 其中预备热处理为正火, 然后可能有必要进行去应力退火,最终热处理为调质处理和表面热处理的高频淬火和低温回火。
40Cr 的显微组织不均匀,且晶粒粗大,需要进行预备热处理来细化晶粒和改善其内部组织。
翻阅书籍后我决定采用正火的方法来作为预备热处理。
正火温度为Ac3或 Acm 以上 40到 60℃,故取正火温度为 880℃,来改善晶粒大小,使晶粒细化,
可以获得更好的切削加工性能,并为后续热处理工艺打好基础。
正火后组织变成了片状 P 和片状渗碳体,此时的钢的切削性能较好,硬度较低, 便于切削加工。
在进行粗加工后组织内部可能会产生一些残余应力, 影响后续热处理工艺, 于是需要用去应力退火来消除组织应力。
一般去应力退火加热温度低于回火温度,故取 540℃,再保温 2小时,以防止产生新的残余应力。
完成上述工序后 40Cr 的性能任未满足曲轴的要求,需要进行更进一步的操作,即最终热处理,在这里选择的是调质处理以及表面高频淬火。
对于调质处理, 40Cr 是亚共析钢, 淬火温度为 Ac3+30到 50℃, 所以取淬火温度为 830℃,而 40Cr 淬透性较好,为了避免 40Cr 钢在淬火时出现淬裂现象, 因此选择淬火介质——油,保温 10分钟。
淬透之后采用高温回火,加热温度在 560℃左右,保温两个小时空冷。
实现淬火的必要条件是加热温度必须高于临界点温度以上, 以获得奥氏体组织, 其冷却速度必须大于临界冷却速度, 而淬火得到的组织是马氏体或下贝氏体。
对
40Cr 进行淬火前,其组织状态为珠光体,而淬火后组织为马氏体。
马氏体具有很高的硬度,但很脆,所以需要高温回火来提高韧性适当降低硬度。
回火后 40Cr 的组织为回火索氏体,保留了淬火效应,索氏体均匀细密,晶粒细小,具
有良好的硬度与韧性。
但是曲轴的表面要求有良好的耐磨性, 调质态的硬度远远不够, 因此需要进行表面热处理即高频淬火与低温回火来增加表面硬度及其耐磨性。
通过表面热处理可以再工件表面一定深度内获得马氏体组织, 而其心部仍保持着表面淬火前的组织状态,以获得表面层硬而耐磨,心部又有足够塑性、韧性的工件。
对于 40Cr 曲轴的表面热处理采用高频淬火+低温回火,利用高频淬火炉进行淬火,淬火温度在 860摄氏度(普通淬火温度+30~200℃ ,油冷。
高频淬火后, ,为了降低残余应力和钢的脆性,而又不至于降低硬度,因此需要进行低温回火。
回火温度取160℃,保温 1.5小时。
经过高频淬火以后, 表面得到的并不是所需要的针状马氏体, 而是粗大的组织。
其原因是高频淬火时加热时间太长而引起的。
这种粗大的组织硬度比细马氏体降低很多。
因此是不希望获得的组织, 在加热时一定要严格控制温加热温度范围和加热时间。
得到颗粒大小均匀, 综合性能良好的回火索氏体, 其表层为针状马氏体,而心部则保持了原始的组织与性能。
此时 40Cr 的材料性能已经基本符合制作曲轴的要求 . 可以投入生产中了。
这次曲轴的热处理设计通过选用 40Cr 钢,加上合适的热处理工艺,即正火→调质处理, 获得良好的综合机械性能, 可以很大限度的提高曲轴强度, 并且通过高频表面淬火工艺,可以很好的提高曲轴的表面硬度以及表面耐磨性。
在对 40Cr 钢进行热处理时由于淬透性比较好,很容易出现淬裂,所以对选择淬火介质是要选择冷速较慢的介质比如空冷、油冷等等。
加热保温时间应严格控制, 避免在调质回火时保温时间过短所引起的硬度过高, 同时避免保温时间过长引起晶粒粗大。