热轧带钢厚度精度控制技术的优化
热轧带钢短行程控制策略优化
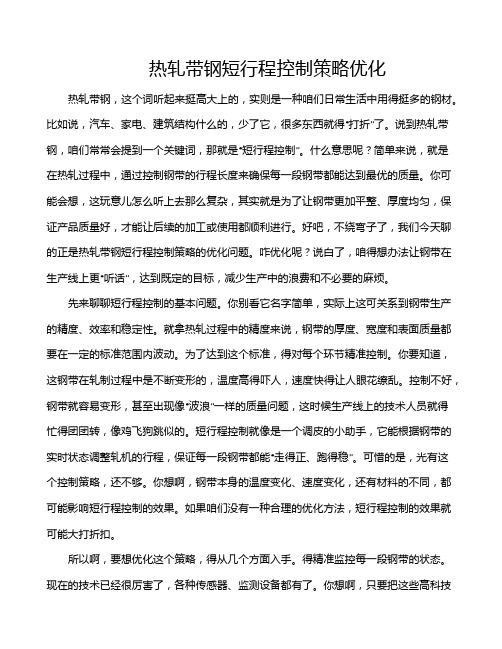
热轧带钢短行程控制策略优化热轧带钢,这个词听起来挺高大上的,实则是一种咱们日常生活中用得挺多的钢材。
比如说,汽车、家电、建筑结构什么的,少了它,很多东西就得“打折”了。
说到热轧带钢,咱们常常会提到一个关键词,那就是“短行程控制”。
什么意思呢?简单来说,就是在热轧过程中,通过控制钢带的行程长度来确保每一段钢带都能达到最优的质量。
你可能会想,这玩意儿怎么听上去那么复杂,其实就是为了让钢带更加平整、厚度均匀,保证产品质量好,才能让后续的加工或使用都顺利进行。
好吧,不绕弯子了,我们今天聊的正是热轧带钢短行程控制策略的优化问题。
咋优化呢?说白了,咱得想办法让钢带在生产线上更“听话”,达到既定的目标,减少生产中的浪费和不必要的麻烦。
先来聊聊短行程控制的基本问题。
你别看它名字简单,实际上这可关系到钢带生产的精度、效率和稳定性。
就拿热轧过程中的精度来说,钢带的厚度、宽度和表面质量都要在一定的标准范围内波动。
为了达到这个标准,得对每个环节精准控制。
你要知道,这钢带在轧制过程中是不断变形的,温度高得吓人,速度快得让人眼花缭乱。
控制不好,钢带就容易变形,甚至出现像“波浪”一样的质量问题,这时候生产线上的技术人员就得忙得团团转,像鸡飞狗跳似的。
短行程控制就像是一个调皮的小助手,它能根据钢带的实时状态调整轧机的行程,保证每一段钢带都能“走得正、跑得稳”。
可惜的是,光有这个控制策略,还不够。
你想啊,钢带本身的温度变化、速度变化,还有材料的不同,都可能影响短行程控制的效果。
如果咱们没有一种合理的优化方法,短行程控制的效果就可能大打折扣。
所以啊,要想优化这个策略,得从几个方面入手。
得精准监控每一段钢带的状态。
现在的技术已经很厉害了,各种传感器、监测设备都有了。
你想啊,只要把这些高科技玩意儿好好利用,实时反馈钢带的温度、厚度、速度等数据,系统就能自动做出调整。
这就像你在开车时,汽车的仪表盘会实时显示油量、车速、发动机温度等信息,方便你掌握车况。
热轧板带厚度控制

板带厚度控制一、概述热轧带钢厚度精度一直是提高产品质量的主要目标,随着市场对板带钢厚度精度要求的提高,板带的厚度控制变得越来越重要。
二、影响板带厚度的因素热带厚度精度可分为:一批同规格带钢的厚度异板差和每一条带钢的厚度的同板差。
为此可将厚度精度分解为带钢头部厚差和带钢全长厚度偏差。
影响头部厚差的因素:1、设定模型精度不高(主要是温降模型和轧制加模型的精度)2、带坯在厚度方向上存在温度差,所测表面温度与带坯实际平均温度有差异。
3、带坯头部低温段过长。
影响带钢全长厚度偏差的因素可分为两类:1、由带钢本身工艺参数波动造成,这包括来料头尾温度不均,来料厚度不幸免以及化学成份偏析等。
2、由轧机参数变动造成,这包括支撑辊偏心,轧辊热膨胀,轧辊磨损以及油膜轴承、油膜厚度变化等。
从厚差分布特征来看,产生厚差的原因有以下几种:1、头尾温差。
2、钢坯表面的低温段。
3、活套起套过猛,对带钢产生冲击,使颈部厚度变薄。
4、咬钢时由于速度设定不协调加上初态速降造成钢套过大,起套并投入高度控制后,由于纠偏过快造成带钢拉钢,这一松一紧使厚度减速薄,宽度拉窄。
5、温度随机波动造成轧制力以及厚度波动。
6、现代带钢热连轧机都采用低速咬钢,等带钢进入郑取机后再同步加速至高度的办法进行轧制。
在轧辊转速变动较大时,将使油膜轴承厚度发生变化而使实际辊缝变小,影响轧件厚度。
7、轧辊偏心(椭圆度)将直接使实际辊缝产生高频周期变化。
三、自动厚度控制(AGC)P-H图是分析自动厚度控制系统的一个有效工具,通过该图可以分析轧制过程中造成厚差的各种原因,说明轧制过程中的调整原则。
如图1所示,说明了来料原差影响及AGC控制,图2说明了来料硬度变动(变形搞力变动)的影响及AGC控制。
为了消除此厚差,可采用各种不同的厚度控制方案:1、移动压下。
如图所示,如原来轧制力为P,轧制厚度为R,当入口厚度或硬度(虚线)时,轧制力变为P`轧出厚度变为h`,为消去δh,需移动压下δs。
热轧带钢生产中的板形控制

热轧带钢生产中的板形控制是指通过有效的生产工艺和控制措施,使得热轧带钢的板形达到设计要求,保证其质量和使用性能。
板形是指热轧带钢在轧制过程中产生的纵横向偏差,包括厚度不均匀、横向偏斜、波浪形状等。
合理的板形控制不仅能提高产品的表面质量、平坦度和尺寸精度,还能减少废品率和提高生产效率。
本文将从板形控制的重要性、主要影响因素和改善措施等方面进行分析和探讨。
一、板形控制的重要性热轧带钢的板形控制对产品质量和性能至关重要,具有以下重要性:1. 保证产品的平整度和尺寸精度。
合理的板形控制可以减少热轧带钢在轧制过程中产生的纵横向偏差,从而提高产品的平整度和尺寸精度,确保产品符合设计要求。
2. 改善产品的表面质量。
板形不均匀会导致带钢表面产生波浪、皱纹等缺陷,降低产品的表面质量。
通过有效的板形控制,可以减少这些缺陷的发生,提高产品的表面光洁度和平坦度。
3. 减少废品率和提高生产效率。
不合格的板形会导致产品剪切不良、卷取不良等问题,增加废品率。
通过优化板形控制,可以减少废品率,提高产品的一次成型合格率,提高生产效率。
二、主要影响因素热轧带钢的板形受到多个因素的影响,主要包括以下几个方面:1. 轧制工艺参数。
轧制工艺参数对板形的影响是最直接和关键的。
包括轧制温度、轧制速度、带材的展宽比、轧辊的形状等。
合理的调整和控制这些参数,可以有效地改善板形。
2. 带钢的翘曲性能。
带钢的翘曲性能取决于材料的力学性能和内应力状态。
当带钢的翘曲性能较差时,易出现板形不佳的现象。
3. 轧机设备的状态。
轧机设备的磨损程度、轧辊的偏差和挠度等都会对板形产生影响。
定期检查和维护轧机设备,保持其正常状态,对于控制板形至关重要。
4. 轧机辊系布置。
轧机辊系布置的合理性会对板形产生直接影响。
轧机辊系的过柱、过程和反曲等布置方式,可以通过对带材的实际形变过程进行控制,达到改善板形的效果。
三、改善措施为了控制热轧带钢的板形,可以采取以下措施:1. 合理调整和控制轧制工艺参数。
提高热轧带钢厚度精度研究

带 钢头部 的厚 度和 温度 。精 轧设 定计算 主要 是根
据 带钢成 品 的 目标 厚 度 和来 料 带 钢厚 度 , 压 下 用
厚度 控 制 ) 入 方 式 对 带 钢 头 部 厚 度 的补 偿 作 投
用 , 用绝 对 随 A C和监 控 A C相 结合 的投 入 采 G G
分 配模 型确定 各机 架 的 出 口板 厚 ; 层别 文 件 中 用 的数据决 定末 架 的穿 带 速 度 ; 以精 轧 末架 作为 其 基 准机架 , 用秒 流 量 相 等原 理 和 前滑 模型 求 出 各 机 架 的穿 带 速 度。根 据 粗 轧机 出 口实测 温 度 , 用 温 度模型 求 出精 轧机 人 口温度 及带钢在 各机架 的 出 口温 度 ; 用轧 制力 模型 汁算 各机 架 的轧制力 ; 用
Ab t a t Ac o d n o t ik e s f cu t n a e d n d e o t p s e n 1 8 o ol g sr c c r i g t hc n s u t ai tla i g e g fsr t li 7 0 h tr l n l o i e i
弹 跳模型计 算 各机 架 的弹 跳量 ; 辊 缝模 型求 出 用 各 机架 的辊缝 没定值 。
方式 , 实现 了提高 带 钢 头部 厚 度精 度 和 全 长厚 度
精度 的 目的。
李 文 斌 , 程 师 ,02年 毕业 于 西 安 建 筑 科 技 大 学 金 属 压 力 工 20 加 工 专 业 , : 作 于鞍 钢 股 份 有 限公 司技 术 中心 钢 铁 产 品研 究 所 现 f ‘
p o ucin ln n Ang nga o r d t i e i o a nd c mbi n t h sc ie n c nr li hikn s c u a y o ti nig wih t eba i d a o o tolngt c e sa c r c fsrp
热轧带钢厚度精度的提升及控制技术优化

热轧带钢厚度精度的提升及控制技术优化上海梅山钢铁股份有限公司,江苏南京 210039)摘要:为提升厚度精度控制,产线通过对影响厚度精度的异常波动进行分析,然后融入分段控制理念,将带钢全长厚度通过AGC自动调整,实现了降低不同区域厚度波动幅度的目标,通过不断的优化调整,厚度标准差控制能力得到不断提升。
关键词:厚度; AGC;厚度波动Improvement of Thickness Accuracy of Hot Rolled Strip andoptimization of control technologyWANG Ming-xin LI Mei-hua(Hot rolling plant of Meishan IRON&STEEL CO.,Nanjing 210039)Abstract: To improve the thickness accuracy control, theproduction line analyzes the abnormal fluctuations that affect the thickness accuracy, then the concept of subsection control is integrated, the full length thickness of strip steel is automatically adjusted by AGC, the target of reducing thickness fluctuationamplitude in different regions is realized,. Through continuous optimization and adjustment, the control ability of thickness standard deviation has been improved continuously.Key words: Thickness; AGC; Thickness fluctuation1 前言随着现场设备及控制系统的升级,目前绝大部分热轧带钢的厚度尺寸超差问题已经得到解决,而随着下游用户质量意识的不断提升及产能过剩的客观条件,用户对厚度精度要求也越来越苛刻,通常的问题主要有两个方面:带钢长度方向上的厚度一致性和局部厚度波动大,这两个问题对用户的焊接工艺、成材率及生产效率等方面影响较大,并且规格越薄要求越严格。
热轧薄规格带钢精轧穿带稳定性的改善

区域治理前沿理论与策略九十年代初期,热轧工艺得以在国内迅速发展,该工艺具备耗能低,便于加工,生产效率高等特点。
热轧原理具体是在钢材退火温度足够高时进行轧制,经过这足够长的时间,在材料中产生无应变能力的新晶粒,新晶粒开始产生的温度就是再结晶温度的初始温度,新晶粒占据全部材料的时的温度为再结晶温度的终了温度,再结晶温度取初始温度与终了温度的平均值,一般情况下此温度主要受到材料成分与环境温度这两个因素的影响。
这便是关于热轧的简单原理,其实在我们的实际加工薄规格产品中主要的轧制方式而言,主要分为单坯轧制、半无头轧制以及全无头轧制三种方式,以下通过简单介绍这三种方式,进一步了解如何改善相关工艺的稳定性。
一、热轧薄规格产品的轧制方式、原理以及技术特点1.单块板坯轧制技术,其原理是将钢材的首尾安置在没有张力情况下,即非稳定轧制状态下进行生产的,这样轧制的钢材精度很难控制,比较容易造成钢材之间相互重叠。
当钢材的尾部离开精轧机时容易弯曲,制造的产品公差基数大,相对应的尺寸精度与性能达不到合格标准。
因此对于规格要求较薄的热轧板采用此技术生产时难度较大,且产品达不到所要求的性能指标。
2.半无头轧制技术,该技术原理是利用薄板坯连铸连轧生产线中长于普通板坯四到六倍的板坯,来保证带钢不间断进行轧制,再由相关的机器平均裁制成相等质量的钢材。
跟上述介绍的单块板坯轧制技术不同的是,此技术虽然对相关的生产设备以及技术提出了更高的要求,但是大幅度地提高了产品的生产效率,进而增强了产品的性能指标。
3.全无头轧制技术,具体原理是通过板坯对粗轧机与精轧机之间进行连接,并且在此过程中需要进行板坯加热以及协调两台加工设备之间的工作频率,才可最终实现无头轧制。
上述可见对技术要求相当高,尤其是粗轧机与精轧机的连接技术,直至上世纪九十年代末期,在日本的川崎钢厂此项技术才得以实现。
在我国粗轧机与精轧机之间的连接方式主要分为两种,即变形链接与感应加热链接,用以保障当板坯在进入精轧机后正常的运行。
热轧带钢尺寸精度的提升

总第302期2021年第2期HEBEI METALLURGYTotal No. 302 2021 , Number 2广.• ^t^•• ^t^•• ^t^•• ^t^•• ^t^•• ^t^••、|生产实践|乂"—|—••—|—••—|—••—|—••—|—••—|—•••*^热轧带钢尺寸精度的提升马啸晨,翟进坡,梁鹏,冯润壮(唐山市德龙钢铁有限公司,河北唐山063600)摘要:热乳带钢同条尺寸差及横截面三点差是反映带钢尺寸精度的两项重要指标。
本文综合分析了热乳带钢生产过程中影响尺寸精度的关键因素,通过优化加热温度、降低中间坯厚度、优化立辊孔型、降低乳辊热膨胀、更改除尘方式、优化生产计划编排等措施,带钢生产过程稳定,尺寸精度得到显著提高,横截断面厚度差$0.02 m m,同条厚度差$0.05 m m。
关键词:热乳带钢;尺寸精度;同条差;三点差;加热温度;孔型;除尘方式中图分类号:TG335.5 文献标识码:B 文章编号:1006 - 5008 (2021) 02 -0042-06d o i:10. 13630/j. cnki. 13 -1172.2021.0209IMPROVEMENT OF DIMENSIONALACCURACY OF HOT ROLLED STRIP STEELMa Xiaochen,Zhai Jinpo,Liang Peng,Feng Runzhuang(Tangshan Delong Iron and Steel C o.,L t d.,Tangshan,H e b e i,063600)A bstract:The dimension difference and cross section three - point difference o f the same strip are two im portant indexes to reflect the dim ensional accuracy o f hot rolled strip. This paper comprehensively analyzes thekey factors that affect the dim ensional accuracy in the production process o f hot rolled strip. B y optim izingthe heating temperature , reducing intermediate b ille t thickness , optim izing the vertical ro ll pass , reducing thethermal expansion o f the r o ll,changing the dust rem oval m ethod,optim izing the production plan arrangementand other measures,the strip production process is stable,the dimensional accuracy is significantly imp roved,the thickness difference o f the cross section is ^0.02m m,and the thickness difference o f the samestrip is 彡0. 5 mm.Key W o rd s:hot rolled s trip;dimensional accuracy; same strip difference;three -point differ temperature ;pass ;dust rem oval method0 引言近年来,随着我国经济发展和城市化进程的加 快,产业结构逐步升级,高附加值的深加工冷轧板带 产品需求量显著增加,并将长期保持一个增长的态 势。
提高热轧带钢精轧厚度控制精度实践

提高热轧带钢精轧厚度控制精度实践发布时间:2022-06-28T02:28:44.542Z 来源:《科学与技术》2022年5期作者:张辉,宋光磊,王仕雷,谢新刚,侯立国[导读] 分析制约热轧精轧带钢厚度控制的原因,重点针对模型控制、轧辊磨损量、张辉,宋光磊,王仕雷,谢新刚,侯立国山东泰山钢铁集团有限公司,山东济南,271100摘要:分析制约热轧精轧带钢厚度控制的原因,重点针对模型控制、轧辊磨损量、精轧开轧温度三项主要因素,采取模型功能升级、磨辊量调节、温度控制等有效措施,实现精轧厚度精度控制在±0.05mm以内,有效提升带钢厚度控制。
关键词:模型控制;磨损量;温度;厚度1 前言为顺应企业产品质量新要求,全体热轧职工凝聚力量,在提升产品质量上下功夫。
提高带钢厚度控制精度,是提升产品质量主要方向之一。
终轧厚度控制精度直接关系着钢带的产品成品质量,精轧对厚度控制起着决定性作用,而精轧模型对终轧厚度的控制精度超出了规定的±0.1mm,存在质量隐患。
精轧厚度控制精度关系到带钢实物质量的持续改进,满足客户已知的、潜在的要求,质量问题的避免,经济的不必要损失。
因此,完善精轧模型对厚度精度的优化,来提高产品质量,使质量趋于精品化,设定目标实现精轧厚度精度控制在±0.05mm以内。
2 影响精轧厚度控制的原因分析离线模型的数据,是在开始轧制前给定一个参考值,后续靠人工经验值进行修定。
在对历史数据统计发现设定辊缝一开始计算的值是多少,到轧完同规格带钢,辊缝值基本还是最初的设定值。
随着轧辊的偏心运转、轧辊的磨损、轧辊轴承油膜厚度、热膨胀等因素,导致辊缝误差[1] ,辊缝的变化是引起厚度偏差大的主要原因。
2.1离线模型没有自动设定功能因为轧制节奏快,离线模型没有自动设定功能,人工干预缓慢,辊缝误差不能及时修正,是引起厚度偏差大的主要原因。
2.2轧辊磨损量的调整轧辊磨损主要是轧件与轧辊的相对滑动磨损、轧制力腐蚀磨损、温度应力磨损、冷却氧化铁皮剥落磨损及正常的氧化磨损[2]。
- 1、下载文档前请自行甄别文档内容的完整性,平台不提供额外的编辑、内容补充、找答案等附加服务。
- 2、"仅部分预览"的文档,不可在线预览部分如存在完整性等问题,可反馈申请退款(可完整预览的文档不适用该条件!)。
- 3、如文档侵犯您的权益,请联系客服反馈,我们会尽快为您处理(人工客服工作时间:9:00-18:30)。
热轧带钢厚度精度控制技术的优化郭勇,刘小军,何斌(新疆八一钢铁股份有限公司)摘要:分析了八钢1750热轧机组生产高精度厚度要求的带钢存在的问题及影响厚度精度的原因,通过对设 定模型,以及厚度自动控制(A G C)程序的完善和优化,提升了产品的厚度精度,满足了市场需求。
关键词:模型;AGC;自学习;尾部补偿中图分类号:TG335.i l文献标识码:B文章编号:1672—4224(2016)04—0029—03Improve the Control Technology of Thickness Accuracyof Hot Rolled StripGUO Yong,LIU Xiao-jun,HE Bin(Xinjiang Bayi Iron&Steel Co.,Ltd)Abstract:This paper briefly describes existing problems during high-precision thickness strip steel production,and analyzes the reasons of affecting the thickness accuracy.Through optimization of setting model and the automatic gauge control(AGC)program,and to improve the thickness precision,and to meet the market demand.Key words:model;AGC;self-learning;tail compensation1前言随着钢铁市场的不断发展,用户对钢铁产品质量的要求也在不断提升。
例如提供给用户的热轧带钢产品,厚度有时会出现“合标不合用”的现象,即满足国家标准,但不能满足用户使用要求。
国标只是一个基准,适应客户需求是企业生存的根本。
为此八钢热轧通过优化控制技术改进生产工艺,提升了 产品厚度精度。
2产品实例分析以八钢热轧产线生产厚度4.57mm的酸洗板为 例,国家标准为± 〇.15mm即为较高标准的要求,同时对带钢头尾15m可放宽要求。
但用户在实际使用 过程中,要求通板尺寸保证在± 〇.l〇mm以内。
在实 际生产过程中,生产出的带钢厚度情况如图1所示。
通过图1的图形可以看出,带钢头尾均有一定 程度的超厚现象,无法完全满足用户的要求。
图1带钢厚度控制实绩图3热轧带钢厚度控制的关键点关于热轧带钢厚度控制的理论和方法有很多,归结起来其实就是两个关键点:一是模型设定精度,即厚度模型能够准确的计算出相应的轧制力和辊 缝;二是AGC控制精度,即受热轧中间坯来料厚度 波动、中间坯纵向温差等轧制过程中各种扰动因素 的影响,成品带钢厚度的纵向厚度亦将随之波动。
自动厚度控制系统(AGC)的目的是通过调节精轧机各 机架棍缝来消除各种扰动影响,以达到精轧末机架 出口目标厚度并维持出口厚度恒定。
联系人:郭勇,男,44岁,硕士研究生,自动化高级工程师,乌鲁木齐(830022)新疆八一钢铁股份有限公司轧钢厂热轧分厂E-m ail : guoyong@29通过对八钢热轧带钢厚度曲线、轧制力曲线、AGC辊缝补偿曲线等相关性分析,认为带钢头部厚 度偏差主要是L2设定不准确,造成了轧制力偏差 较大,以及AGC参数设定不合理AGC厚度补偿不 及时等原因。
尾部是由于活套失张,造成尾部偏厚。
4提高热轧带钢厚度精度的控制措施4.1提高模型设定精度4.1.1提高温度计算精度模型能否计算准确,温度的准确与否至关重要。
温度的数据来源于中间坯温度,再加上时间计算得 来。
中间述测温计安装在粗轧机出口,带钢表面经过 除鳞,表面没有氧化铁的影响,但是表面覆盖的水汽 会影响到检测结果。
同时因北方冬季气温偏低,水雾 较大也会对检测结果造成较大影响。
针对此问题,采 用线性回归与二次项回归来计算头部温度;采用温 度反馈调整加速度来保障终轧温度;同时通过热卷 箱模式和直通模式加以分离来提高温度计算精度。
4丄2自学习优化首先,对U的程序进行优化,原来其厚度自学 习及轧制力自学习均采用通长自学习的方法,即将 带钢通条所有满足要求的段数据均用于自学习,这 样的好处是可以将更稳定的值用于模型学习,但是 由于其本体及尾部均已进行了 AGC控制,这样不利 于头部设定的准确性。
将自学习程序进行优化,可进 行头部自学习选择,当选中头部自学习时,仅对带钢 前七个有效段进行学习,并且在模型中设定可对每 段的比重进行设定,技术人员可以根据现场实际来 设定每段的学习比重,经现场实践发现前七段比率 依次为15%、30%、20%、15%、10%,而10%最为合理有效。
4.2 AG C控制优化4.2.1头部响应控制参数优化对轧制力AGC的延迟时间进行了调整,主要针 对薄规格带钢,将F,~F6的GM-AGC延迟时间由 500m s改为200ms;将F,~F6的前馈AGC控制延迟 时间由1.5s改为500ms;同时将前馈AGC控制死区 取消。
这样可使得其更快进行响应,减少头部厚度偏 差的长度。
4.2.2增加尾部补偿对于尾部超厚的问题,主要考虑增加尾部补偿 功能。
在带钢热连轧的过程中,当带钢尾部每离开一 个机架时,由于后张力的消失,必然导致尾部增厚。
为了防止尾部增厚的产生,在带钢尾部离开第i- 1架时,应增大对第i机架的压下量,这种方法称为带 钢尾部补偿。
所谓的压尾部是在带钢的尾部多压一些,为了 达到此目的,采用将现有的厚度偏差控制信号厶A 适当放大,这种放大的厚度偏差信号就是压尾的补 偿值厶知。
A h^G j^-A h(1)式中:压尾补偿量;gt-调节增益;厶V现有的厚度偏差;-第i-1机架带钢尾部厚度;t-带钢尾部由第i-1机架向第i机架的移送时间。
当带钢尾部离开第i- 1架之后,对应于第i机 架的压下行程A S t*:ASr=J^AhT (2)对轧制力AGC的尾部锁定功能进行优化,在尾 部压尾与尾部锁定(避免尾部轧烂)之间做好平衡,最终确定2.3m m以上米用尾部压尾,2.3mm及以下 采用尾部锁定,不进行压尾,避免轧烂。
5 优化后的效果实施改进措施,带钢厚度控制实绩图见图2。
F M E K i t T h i c f c n e s s图2带钢厚度控制实绩图(优化后)控制系统优化后,抽取了一个月的生产数据进 行统计分析,统计了不同规格热轧带钢头尾及本体 的厚度精度,头尾精度为头部、尾部l〇m、本体(去头 尾10m)范围内的± 0.1mm精度。
表2数据为优化后 一个月内连续生产的6mm及以下带钢的厚度精度 数据。
表2 带钢头尾优化后生产实绩表(1732卷)厚度规格mm生产卷数头部精度,〇/。
本体精度,〇/。
尾部精度,〇/。
彡2. 534093. 1799.321002. 5〜4. 0113295.6999.8299.98>4. 026097.3699.72100从表2数据可以看出,通过优化,生产出的带钢30基本满足用户对高精度要求。
针对带钢头部精度的 提升上还需进一步研究优化。
6结束语通过对热轧带钢头尾厚度偏差的原因分析,认 为由于L2设定偏差大及AGC补偿不及时导致了头部厚度偏差大,从厚度自学习段、带钢温度计算、AGC控制参数等方面的优化解决了头部厚度精度 问题。
针对增加带钢尾部厚度补偿解决带钢尾部厚 度问题的措施实施后,厚度精度改善明显,产品质量 满足了生产用户的需求,用户反映良好。
•科普知识•钢材分类标号(二)5. 低合金高强度钢标号规则(1) 钢号的表示方法,基本上和合金结构钢相同。
(2) 对专业用低合金高强度钢,应在钢号后标明。
例如16M ii钢,用于桥梁的专用钢种为“16M nq”,汽车大梁的专用钢种为“16MnL”,压力容器的专用钢种为“16M n R”。
6. 易切削钢标号规则(1) 钢号冠以“Y”,以区别与优质碳素结构钢。
(2) 字母“Y”后的数字表示碳含量,以平均碳含量的万分之几表示,例如平均碳含量为0.3%的易切削钢,其钢号为“Y30”。
(3) 锰含量较高者,亦在钢号后标出“M ii”,例如“Y40M ii”。
7. 弹簧钢标号规则弹簧钢按化学成分可分为凝素弹簧钢和合金弹簧钢两类,其钢号表示方法,前者基本上与优质碳■素钢结构钢相同,后者基本上与合金结构钢相同。
8. 滚动轴承钢标号规则(1) 钢号冠以字母“G”,表示滚动轴承钢类。
(2) 高凝铬轴承钢钢号的凝含量不标出,铬含量以千分之几表示例如G C rl5。
參凝轴承钢的钢号表示方法,基本上和合金结构钢相同。
9. 合金工具钢和高速工具钢标号规则(1)合金工具钢钢号的平均碳含量彡1.0%时,不标出碳含量;当平均碳含量<1.0%时,以千分之几表示。
例如C rl2、CrW Mn、9SiCr、3Cr2W8V〇(2) 钢中合金元素含量的表示方法,基本上与合金结构钢相同。
但对铬含量较低的合金工具钢钢号,其铬含量以千分之几表示,并在表示含量的数字前加“0”,以便把它和一般元素含量按百分之几表示的方法区别开来。
例如Cr06。
(3)高速工具钢的钢号一般不标出凝含量,只标出各种合金元素平均含量的百分之几。
例如鹤系高速钢的钢号表示为“W18Cr4V”。
钢号冠以字母“C”者,表示其碳含量高于未冠“C”的通用钢号。
10. 不锈钢和耐热钢标号规则(1) 钢号中碳含量以千分之几表示。
例如“2C rl3”钢的平均碳含量为0.2%;若钢中含碳量矣0.03%或矣0.08%者,钢号前分别冠以“00”及“0”表示之。
例如 00C rl7N il4M o2、0C r l8 N19 等。
(2) 对钢中主要合金元素以百分之几表示,而钬、视、锆、氮...等则按上述合金结构对微合金元素的表示方法标出。
11. 焊条钢标号规则钢号前冠以字母“H”,以区别于其他钢类。
例如不锈钢焊丝“H2C rl3”,可以区别于不锈钢“2C rl3”。
12. 电工用硅钢标号规则(1) 钢号由字母和数字组成。
钢号头部字母D R表示电工用热轧硅钢,D W表示电工用冷轧无取向硅钢,D Q表示电工用冷轧取向用钢。
(2) 字母之后的数字表示铁损值(W/kg)的100倍。
(3) 钢号尾部加字母“G”者,表示在高频率下检验的;未加“G”者,表示在频率为50周波下检验的。
例如钢号DW470表示 电工用冷轧无取向硅钢产品在50赫频率时的最大单位重量铁损值为4.7W/kg。
13. 电工用纯铁钢标号规则(1) 它的牌号由字母“D T”和数字组成,“D T”表示电工用纯铁,数字表示不同牌号的顺序号,例如D T3。
(2) 在数字后面所加的字母表示电磁性能:A-高级、E-特级、C-超级,例如D TSA。