石油化工企业火灾爆炸事故原因分析
石油石化行业安全事故案例分析

投运第 6 套脱水脱烃装置。上午 10∶50 分左右, 该装置的系统压力( 介质为氮 气 ) 为 0.18 兆 帕 , 值 班 人 员 按 投 运 方 案 开始进气建压, 并用肥皂水对各密封 点 进 行 检 漏 , 11: 30 分 , 低 温 分 离 器 升 压 至 6.24 兆 帕 , 打 开 第 6 套 装 置 干 气 外 输 阀 , 此 时 J- T 阀 前 端 压 力 9.4 兆 帕 , 低 温 分 离 器 压 力 为 6.2 兆 帕 , 系 统 压 力 正 常 。12: 42 分 , 停 运 第 4 套 脱 水 脱烃装置, 第 6 套脱水脱烃装置低温 分 离 器 温 度 逐 渐 降 至 - 21℃( 低 温 分 离 器 设 计 最 低 工 作 温 度 为 - 41℃) , 13: 00 再次对各密封点进行肥皂水检漏, 没 有 发 现 漏 点 , 装 置 运 行 正 常 。15: 10 分 左右, 处理厂中心控制室值班人员听 到强烈的爆炸声, 随后看到装置区第 6 套装置附近的火光, 操作主岗立即启 动全厂紧急停车程序, 实施火灾爆炸 应急预案。正在生产的 4 口气井全部 自动关井, 切断进站气源。同时, 立即 启动消防喷淋系统, 对凝析油储罐进 行喷淋降温。由于自动控制电缆在爆 炸时严重损坏, 出站外输切断阀已不 能实现自动关断, 当时出站外输切断 阀处于着火的下风口, 抢险人员曾几 次试图靠近出站外输切断阀实行手动 关闭, 但终因火势太大, 热辐射温度过 高, 人员无法靠近。只能开车至输气干 线 1 号 阀 室 ( 距 该 处 理 厂 大 约 14 公 里 左 右 ) 进 行 人 工 切 断 输 气 干 线 气 源 , 16 时左右关闭了输气干线 1 号阀室切断 阀 , 16: 30 分 左 右 装 置 区 火 势 逐 步 减 弱 , 17 时 左 右 抢 险 人 员 身 穿 防 火 服 进 入出站外输切断阀处手动关断切断 阀, 并打开现场的消防干粉罐, 对管廊 架上着火的导热油管线等着火处进行 扑 救 , 17: 50 分 左 右 装 置 区 火 焰 完 全 被 扑灭。
化工火灾事故发生原因

化工火灾事故发生原因一、化工火灾的常见原因1. 人为操作失误化工火灾往往与人为操作失误密切相关。
在化工生产过程中,操作人员可能因疏忽大意、粗心马虎等原因,导致火灾的发生。
比如,在使用电焊、切割等高温作业时没有采取必要的安全措施,导致火灾的发生;未按规定操作,引发了事故等。
2. 设备故障化工生产过程中,设备故障可能是引发火灾的主要原因之一。
化工生产设备往往需要承受高温、高压等极端条件,一旦设备出现故障,可能引发火灾。
设备故障的原因可能是设备老化、维护不当、设计缺陷、材料缺陷等。
3. 火灾隐患在化工厂、仓库等场所,存在各种各样的火灾隐患。
比如:电气设备老化、线路短路;易燃易爆物品存放不当、操作不当等;安全设施不完善、未经定期检查等。
这些火灾隐患如果得不到及时排除,很容易引发火灾事故。
4. 自然灾害自然灾害也是导致化工火灾的原因之一。
比如:雷击引发火灾、地震引发设备故障、暴雨引发地质灾害等。
这些自然灾害在化工生产中可能造成严重后果。
5. 其他原因除了上述常见原因外,化工火灾还可能由其他原因引发,比如:恶意纵火、安全管理不当等。
二、化工火灾的预防措施1.加强安全教育培训为了预防化工火灾的发生,必须加强对操作人员的安全教育培训。
在化工生产过程中,操作人员应该具有一定的安全意识,清楚掌握化工生产操作规程,严格按照操作规程进行操作。
同时,还应不断加强安全知识培训,提高操作人员的安全意识。
2.加强设备检修维护为了减少设备故障引发火灾的可能性,必须加强对设备的检修维护工作。
确保设备具有良好的运行状态,避免因设备故障引发火灾事故。
定期对设备进行检查、维护,及时更换老化、磨损的设备部件。
3. 消防设施齐全化工厂、仓库等场所应该配备完备的消防设施,包括灭火器、消防水源、消防报警器等。
并且,定期对消防设施进行维护保养、演练等,确保在火灾发生时能够及时有效地进行灭火救援。
4. 加强安全管理在化工生产过程中,安全管理工作是至关重要的。
典型油库火灾事故案例分析
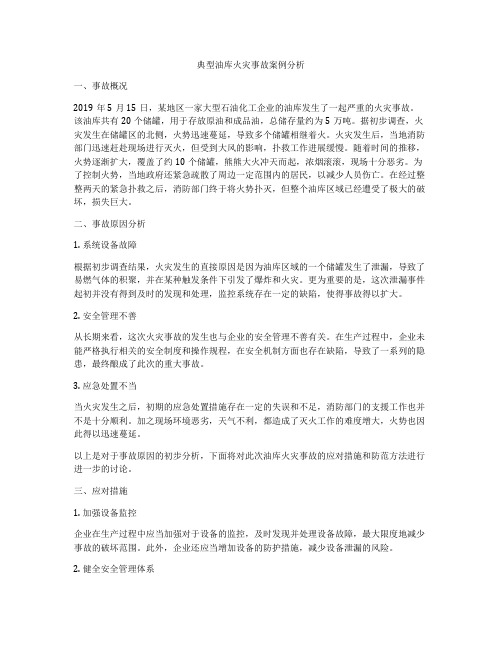
典型油库火灾事故案例分析一、事故概况2019年5月15日,某地区一家大型石油化工企业的油库发生了一起严重的火灾事故。
该油库共有20个储罐,用于存放原油和成品油,总储存量约为5万吨。
据初步调查,火灾发生在储罐区的北侧,火势迅速蔓延,导致多个储罐相继着火。
火灾发生后,当地消防部门迅速赶赴现场进行灭火,但受到大风的影响,扑救工作进展缓慢。
随着时间的推移,火势逐渐扩大,覆盖了约10个储罐,熊熊大火冲天而起,浓烟滚滚,现场十分恶劣。
为了控制火势,当地政府还紧急疏散了周边一定范围内的居民,以减少人员伤亡。
在经过整整两天的紧急扑救之后,消防部门终于将火势扑灭,但整个油库区域已经遭受了极大的破坏,损失巨大。
二、事故原因分析1. 系统设备故障根据初步调查结果,火灾发生的直接原因是因为油库区域的一个储罐发生了泄漏,导致了易燃气体的积聚,并在某种触发条件下引发了爆炸和火灾。
更为重要的是,这次泄漏事件起初并没有得到及时的发现和处理,监控系统存在一定的缺陷,使得事故得以扩大。
2. 安全管理不善从长期来看,这次火灾事故的发生也与企业的安全管理不善有关。
在生产过程中,企业未能严格执行相关的安全制度和操作规程,在安全机制方面也存在缺陷,导致了一系列的隐患,最终酿成了此次的重大事故。
3. 应急处置不当当火灾发生之后,初期的应急处置措施存在一定的失误和不足,消防部门的支援工作也并不是十分顺利。
加之现场环境恶劣,天气不利,都造成了灭火工作的难度增大,火势也因此得以迅速蔓延。
以上是对于事故原因的初步分析,下面将对此次油库火灾事故的应对措施和防范方法进行进一步的讨论。
三、应对措施1. 加强设备监控企业在生产过程中应当加强对于设备的监控,及时发现并处理设备故障,最大限度地减少事故的破坏范围。
此外,企业还应当增加设备的防护措施,减少设备泄漏的风险。
2. 健全安全管理体系企业应当建立健全的安全管理体系,严格执行相关的操作规程和安全制度,定期组织安全演练和培训,提高员工对于安全操作的重视和意识,最终降低事故的发生概率,并及时采取应对措施。
化工厂常见火灾原因
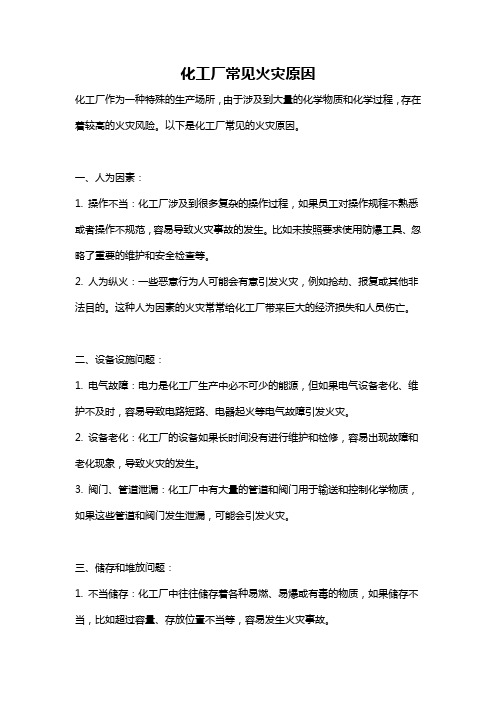
化工厂常见火灾原因化工厂作为一种特殊的生产场所,由于涉及到大量的化学物质和化学过程,存在着较高的火灾风险。
以下是化工厂常见的火灾原因。
一、人为因素:1. 操作不当:化工厂涉及到很多复杂的操作过程,如果员工对操作规程不熟悉或者操作不规范,容易导致火灾事故的发生。
比如未按照要求使用防爆工具、忽略了重要的维护和安全检查等。
2. 人为纵火:一些恶意行为人可能会有意引发火灾,例如抢劫、报复或其他非法目的。
这种人为因素的火灾常常给化工厂带来巨大的经济损失和人员伤亡。
二、设备设施问题:1. 电气故障:电力是化工厂生产中必不可少的能源,但如果电气设备老化、维护不及时,容易导致电路短路、电器起火等电气故障引发火灾。
2. 设备老化:化工厂的设备如果长时间没有进行维护和检修,容易出现故障和老化现象,导致火灾的发生。
3. 阀门、管道泄漏:化工厂中有大量的管道和阀门用于输送和控制化学物质,如果这些管道和阀门发生泄漏,可能会引发火灾。
三、储存和堆放问题:1. 不当储存:化工厂中往往储存着各种易燃、易爆或有毒的物质,如果储存不当,比如超过容量、存放位置不当等,容易发生火灾事故。
2. 反应堆积:化工厂中的反应堆中常常有一些残余的化学反应物,如果这些物质积聚过多,极易发生自燃或爆炸。
四、自然因素:1. 静电火花:在化工厂操作过程中,蓄积的静电有可能在一些特定环境中引起火花放电,从而引发火灾。
2. 闪电击中:化工厂通常存在很高的建筑物、管道和设备,容易成为闪电击中的目标,一旦发生闪电击中,可能会引发火灾。
五、其他因素:1. 化学反应:化工厂通常会涉及到大量的化学反应,某些化学反应是放出大量热能的,一旦反应失控,可能导致火灾。
2. 检修操作不当:在化工厂的检修过程中,如果操作不当,比如火焰使用不当、使用明火等,容易引发火灾事故。
化工厂火灾事故的发生往往给生产企业和周边环境带来巨大的损失,因此,化工厂应该高度重视火灾防控工作,加强设备设施的维护保养,加强员工的火灾防控培训,做好防火措施,确保生产过程的安全和环境的保护。
石化行业事故案例分析
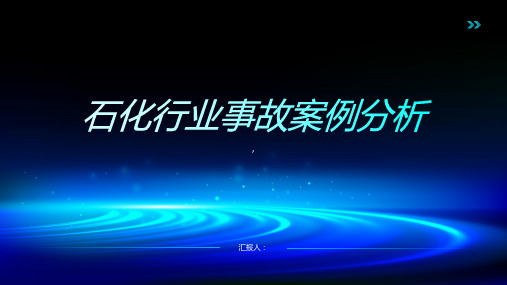
及时发现和修复设 备故障,避免事故 发生。
建立设备维护和检 修制度,确保设备 得到及时保养。
加强设备操作人员 的培训,提高其操 作技能和安全意识 。
定期开展安全培训,确保员工掌握安全知识和操作规程 建立奖惩机制,激励员工自觉遵守安全规定 开展应急演练,提高员工应对突发事故的能力 建立安全文化,营造人人关心安全的氛围
自然灾害:如地震、洪水等自然灾 害,可能导致石化企业设施损坏或 生产中断。
添加标题
添加标题
添加标题
添加标题
操作失误:员工在操作过程中违反 操作规程或操作不当,导致事故发 生。
恐怖袭击:恐怖组织可能对石化企 业进行袭击,导致人员伤亡和财产 损失。
定期对设备进行检 查和维护,确保设 备处于良好状态。
,
汇报人:
01
02
03
04
05
06
事故定义:指在生产、 工作过程中发生的意外 事件,可能导致人员伤 亡或财产损失
事故分类:按发生原因 分为机械、电气、化学、 辐射等类型;按伤亡程 度分为轻伤、重伤、死 亡等类型
设备故障:由于设备老化、维护不当等原因导致设备故障,引发事故。 操作失误:员工在操作过程中违反操作规程或疏忽大意,造成事故。 安全管理不到位:企业安全管理制度不健全、执行不严格,导致事故发生。 自然灾害:地震、洪水等自然灾害也可能导致石化企业发生事故。
制定针对不同事故的应急预案,明 确应急流程和责任人
建立快速响应机制,确保事故发生 后能够迅速启动应急预案
添加标题
添加标题
添加标题
添加标题
定期进行演练和培训,提高员工应 对事故的能力和意识
加强与政府、社区和企业的沟通与 协作,共同应对事故
制定完善的安全管理制度和操作规 程
典型事故二十一:中石油兰州石化“1.7”罐区爆炸事故

典型事故二十一:中石油兰州石化“1.7”罐区爆炸事故一、事故调查分析(一)事故概要1、事故简介2010年1月7日17时24分,兰州石化公司316#罐区发生火灾、爆炸事故,事故共造成6人死亡、1人重伤、5人轻伤,未造成次生事故和环境污染。
2、事故原因(1)直接原因设备缺陷。
由于316#罐区R202球罐出料管弯头母材焊缝热影响区存在组织缺陷,致使该弯头局部脆性开裂,导致碳四物料大量泄漏,泄漏汽化后的碳四物料蔓延至罐区东北侧丙烯腈装置焚烧炉,遇焚烧炉明火引燃爆炸。
(2)间接原因①特种设备安全监督管理不到位Ⅰ、未按规程规定对事故管线进行定期检验没有按照国家质监总局2003年6月试行的《在用工业管道定期检验规程》规定,对在用工业管道进行全面定期检验,致使R202球罐出料管线母材存在的组织缺陷未被发现和整改。
Ⅱ、未按规定落实事故管线更换计划2007年3月,经检验发现R203、R206、R207球罐底部进出物料管线腐蚀严重、壁厚减薄,定为4级,企业下达了R201、R202、R203、R204球罐底部进出物料管线更换计划。
实际仅更换了R201球罐底部进出物料管线,R202、R203、R204球罐底部进出物料管线一直未更换。
②设备管理人员没有认真履行设备管理职责设备管理部门和有关管理人员,没有按照规定要求对碳四车间R202等球罐进出物料管线进行全面检测检验,在R202球罐管线更换计划下达后,又没有履行监督落实职责,致使事故隐患长期存在并最终导致事故发生。
③安全应急处置设施不完善316#罐区自1986年建成投运以来,未按照《石油化工企业设计防火规范》(GB50160-2008)规定,对储罐进出物料管道设置自动联锁切断装置,致使事故状态下无法紧急切断泄漏源,导致泄漏扩大并引发事故。
(二)基本情况1、兰州石化公司基本情况兰州石化公司拥有原油加工能力1050万吨/年、乙烯生产能力70万吨/年、化肥生产能力52万吨/年、合成树脂生产能力124.5万吨/年、合成橡胶生产能力17.5万吨/年、炼油催化裂化剂生产能力5万吨/年。
石油化工火灾、爆炸事故案例分析
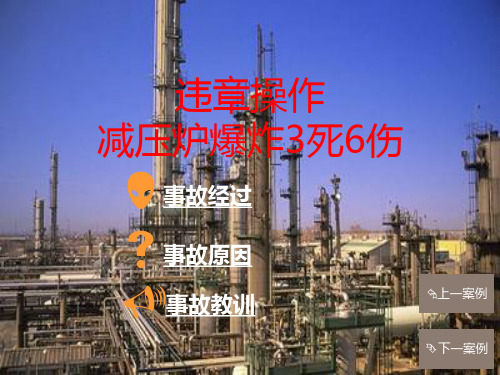
(其中1人经抢救无效,于10月26日
死亡),轻伤5人。直接经济损失3.5 万元,间接经济损失7万元。
可燃气体积聚 明火引起爆炸 ——事故经过
10月8日13时30分,按计划检修后的催化装置投料开车。 15时,前部操作基本正常,但因解析塔底再沸器泄漏,稳 定系统迟迟不能正常,不合格汽油开始出装置,送汽油罐 区214号储罐(该罐是容积为2000m3的钢制内浮顶罐)。 15时30分许,催化车间稳定岗位负责人为了降低稳定塔 304的液面,将塔内油品同时送往214号储罐,因稳定系统 的热源没有建立起来,汽油携带轻组分进入罐区。
油气线侧法兰口处出现青烟,接着爆燃起火。检修人员在躲闪时,
2人从6m高的平台上坠落,1人死亡,1人腰部受伤,其余5人被火 燎伤。
催化两器检修 引起爆炸伤人 ——事故原因
⑴此次停工仅检查两器,对分馏塔稳定系统不进行 动火检修,在翻盲-201前按操作规程对分馏塔 只进行了粗吹扫,残存的可燃气体进入大油气 线。 ⑵在翻盲-201过程中,由于2个螺栓卸不下来,被 迫用钢锯锯断螺栓,大大延长了装盲板的时间, 空气进入油气线内时间过长,大油气线内结焦 多,造成自然闪爆。
2. 应加强对设备的维修管理,定期对止逆阀进行检 查和维护,确保其灵敏好用。 3. 对设计上没有安装安全阀的低压脱氧水罐,应采 取有效的补救防护措施。
加热炉点火 发生闪爆 1人死亡 事故经过 事故原因 事故教训
下一案例
加热炉点火 发生闪爆 1人死亡 ——事故经过
2003年9约11日,乌鲁木齐石化分公司化肥厂二合成车间合成
含油污水溢出地面 浸泡高温管线着火 ——事故经过
化工厂火灾事故案例及分析总结
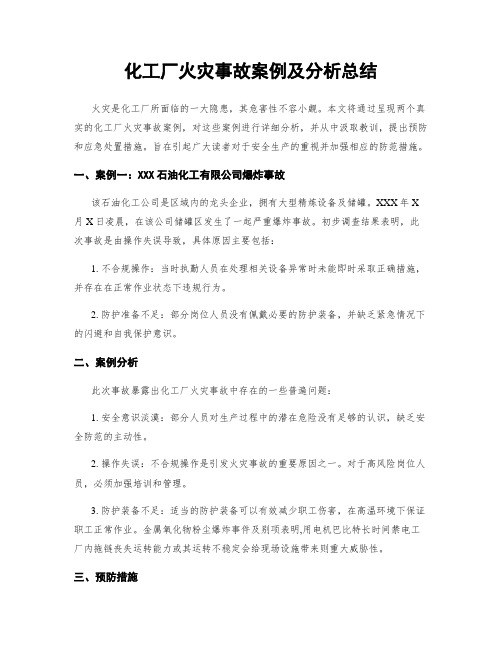
化工厂火灾事故案例及分析总结火灾是化工厂所面临的一大隐患,其危害性不容小觑。
本文将通过呈现两个真实的化工厂火灾事故案例,对这些案例进行详细分析,并从中汲取教训,提出预防和应急处置措施。
旨在引起广大读者对于安全生产的重视并加强相应的防范措施。
一、案例一:XXX石油化工有限公司爆炸事故该石油化工公司是区域内的龙头企业,拥有大型精炼设备及储罐。
XXX年X 月X日凌晨,在该公司储罐区发生了一起严重爆炸事故。
初步调查结果表明,此次事故是由操作失误导致,具体原因主要包括:1. 不合规操作:当时执勤人员在处理相关设备异常时未能即时采取正确措施,并存在在正常作业状态下违规行为。
2. 防护准备不足:部分岗位人员没有佩戴必要的防护装备,并缺乏紧急情况下的闪避和自我保护意识。
二、案例分析此次事故暴露出化工厂火灾事故中存在的一些普遍问题:1. 安全意识淡漠:部分人员对生产过程中的潜在危险没有足够的认识,缺乏安全防范的主动性。
2. 操作失误:不合规操作是引发火灾事故的重要原因之一。
对于高风险岗位人员,必须加强培训和管理。
3. 防护装备不足:适当的防护装备可以有效减少职工伤害,在高温环境下保证职工正常作业。
金属氧化物粉尘爆炸事件及别项表明,用电机巴比特长时间禁电工厂内拖链丧失运转能力或其运转不稳定会给现场设施带来则重大威胁性。
三、预防措施通过上述案例的分析,提出以下预防措施以确保化工厂火灾事故得到有效预防:1. 安全培训与技能考核:对所有从业人员进行系统且定期的安全培训,并建立相应的技能考核制度,保证人员具备必要的安全技能。
2. 制定操作规范:明确各类设备的操作规程和标准,严格执行,禁止任何不合规或擅自更改操作步骤。
3. 责任分工与制度落实:明确岗位责任与义务,在每个岗位上配备专职负责人,并建立相应的考核评价机制。
4. 增强防护意识:加强员工对火灾风险的认知,定期组织相关演练活动,并普及逃生和自救知识。
5. 配备合适的防护装备:确保所有员工都配备适当的个人防护装备,在作业过程中正确佩戴和使用。