加氢裂化分馏系统操作法
加氢裂化操作规程
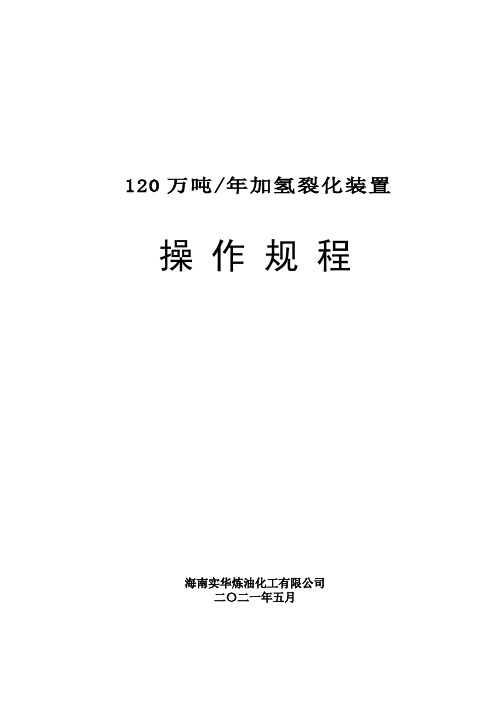
混合比例,m%
20.12
36.1
43.78
100.0
密度(20℃),g/cm3
0.863
0.893
0.911
0.896
硫含量,m%
1.21
氮含量,ppm
800
残炭,w%
-
-
倾点,℃
-
-
馏程℃
D-1160
D-1160
D-1160
D-1160
1%
254.92
330
195
192
5%
280.90
364
分馏部分:将反应部分来的生成油分馏为气体、液化石油气、轻石脑油、重石脑油、柴油及尾油(未转化油)等产品。由脱硫化氢塔、产品分馏塔、柴油汽提塔、石脑油分馏塔、吸收脱吸塔和石脑油稳定塔等组成。
3、装置技术特点
本装置采用双剂串联尾油全循环的加氢裂化工艺。反应部分采用国内成熟的炉前混氢方案;分馏部分采用脱硫化氢塔+常压塔出柴油方案,采用分馏进料加热炉;吸收稳定部分采用重石脑油作吸收剂的方案;循环氢脱硫部分采用MDEA作脱硫剂的方案;催化剂的硫化采用干法硫化;催化剂的钝化采用低氮油注氨的钝化方案;催化剂再生采用器外再生方案。
初期产品主要性质
项目,℃
<65
65~165
165~260
165~380
260~380
>380
密度(20℃),g/cm3
0.6547
0.7409
0.7810
0.8085
0.8298
0.8374
馏程,℃
IBP/10%
26/29
69/85
166/189
175/205
264/280
加氢裂化工艺
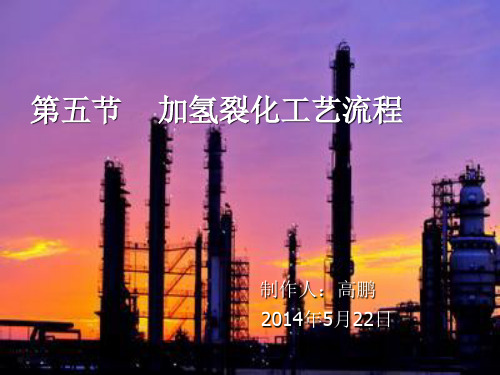
一段串联加氢裂化工艺流程示意图
循环氢 R-1 加热炉 R-2 急冷氢 循环氢压缩机 循环氢
www
பைடு நூலகம்
高 分
加热炉
www
循环氢 新鲜进料 补充氢 新氢增压机 洗涤水
w
w
酸性水
去气体装置
低分 去分馏系统 来自蒸馏塔底的循环油
一段串联加氢裂化工艺的特点:
精制段催化剂应具有较高的加氢活性(尤其是HDN 活性);裂化段催化剂应具有耐 H2S 和 NH3 的能 力;
二个或第二组反应器,这是两段过程的重要特征。
它适合处理高硫、高氮减压蜡油,催化裂化
循环油,焦化蜡油等
两段加氢裂化的工艺流程图
汽提塔的作用:脱去NH3和H2S以及残留在油中的气体。
两段法加氢裂化的特点
气体产率低,干气少,目的产品收率高,液体 总收率高;
产品质量好,特别是产品中芳香烃含量非常低; 氢耗较低;
产品质量好,生产灵活性大,运转周期长;
与一段法加氢裂化相比,其原料油适应性较强,
反应温度相对较低;
与两段法加氢裂化相比,其投资和能耗相对较低。
(二)两段法加氢裂化
在两段加氢裂化的工艺流程中设置两个反应器,
但在单个或一组反应器之间,反应产物要经过气
-液分离或者分馏装置将气体及轻质产品进行分
离,重质的反应产物和未转化反应产物再进入第
反应器,原料油的加氢精制和加氢裂化在同一个反应器内
进行,所用催化剂为无定形硅铝催化剂,它具有加氢性能 较强,裂化性能较弱以及一定抗氮能力的特点。该工艺最 适合于最大量生产中间馏分油。
单段加氢裂化可用三种方案操作:尾油一次通过、尾油部分
加氢裂化工艺流程介绍
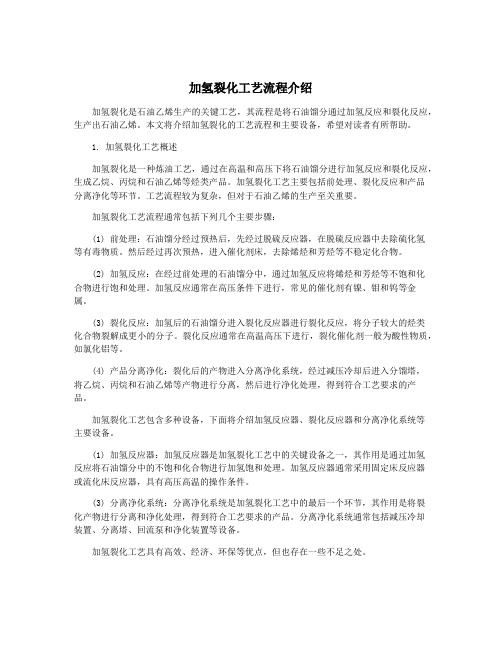
加氢裂化工艺流程介绍加氢裂化是石油乙烯生产的关键工艺,其流程是将石油馏分通过加氢反应和裂化反应,生产出石油乙烯。
本文将介绍加氢裂化的工艺流程和主要设备,希望对读者有所帮助。
1. 加氢裂化工艺概述加氢裂化是一种炼油工艺,通过在高温和高压下将石油馏分进行加氢反应和裂化反应,生成乙烷、丙烷和石油乙烯等烃类产品。
加氢裂化工艺主要包括前处理、裂化反应和产品分离净化等环节。
工艺流程较为复杂,但对于石油乙烯的生产至关重要。
加氢裂化工艺流程通常包括下列几个主要步骤:(1) 前处理:石油馏分经过预热后,先经过脱硫反应器,在脱硫反应器中去除硫化氢等有毒物质。
然后经过再次预热,进入催化剂床,去除烯烃和芳烃等不稳定化合物。
(2) 加氢反应:在经过前处理的石油馏分中,通过加氢反应将烯烃和芳烃等不饱和化合物进行饱和处理。
加氢反应通常在高压条件下进行,常见的催化剂有镍、钼和钨等金属。
(3) 裂化反应:加氢后的石油馏分进入裂化反应器进行裂化反应,将分子较大的烃类化合物裂解成更小的分子。
裂化反应通常在高温高压下进行,裂化催化剂一般为酸性物质,如氯化铝等。
(4) 产品分离净化:裂化后的产物进入分离净化系统,经过减压冷却后进入分馏塔,将乙烷、丙烷和石油乙烯等产物进行分离,然后进行净化处理,得到符合工艺要求的产品。
加氢裂化工艺包含多种设备,下面将介绍加氢反应器、裂化反应器和分离净化系统等主要设备。
(1) 加氢反应器:加氢反应器是加氢裂化工艺中的关键设备之一,其作用是通过加氢反应将石油馏分中的不饱和化合物进行加氢饱和处理。
加氢反应器通常采用固定床反应器或流化床反应器,具有高压高温的操作条件。
(3) 分离净化系统:分离净化系统是加氢裂化工艺中的最后一个环节,其作用是将裂化产物进行分离和净化处理,得到符合工艺要求的产品。
分离净化系统通常包括减压冷却装置、分离塔、回流泵和净化装置等设备。
加氢裂化工艺具有高效、经济、环保等优点,但也存在一些不足之处。
加氢裂化工艺流程介绍
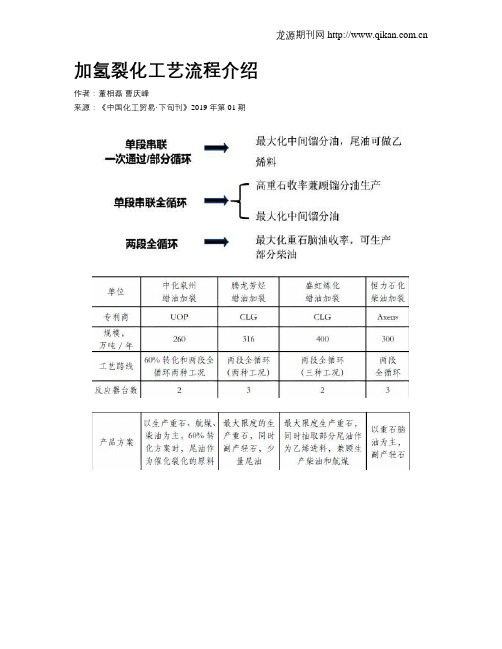
加氢裂化工艺流程介绍作者:董相磊曹庆峰来源:《中国化工贸易·下旬刊》2019年第01期摘要:本文介绍了高重石收率,既能走重整-PX路线,又能兼顾抽取尾油,走乙烯路线的两段全循环加氢裂化工艺流程。
关键词:加氢裂化;工艺流程;两段全循环1 加氢裂化的技术特点加氢裂化是重质馏分油深度加工的重要工艺之一,是炼厂生产轻质清洁油品的必选工艺,是燃料型炼厂向炼化一体化炼厂过渡的必选技术,是唯一能在重油轻质化的同时,生产低硫、低芳烃的清洁燃料和下游化工装置原料的工艺,它可以直接加工含硫的VGO,甚至是可以加工部分脱沥青油。
加氢裂化采取循环操作时,可以最大量生产高芳潜含量的优质重整原料,比直馏石脑油的芳潜含量高20%~30%,两段法加氢裂化工艺高附加值的重石收率可以达到70%,是大型炼厂最重要、最可靠、最灵活和最有效的加工手段之一。
2 加氢裂化工艺流程分类加氢裂化分为单段法工艺和两段法工艺,其它流程都是在这两种流程基础上演化而来的。
其中单段法工艺又分为单段串联一次通过、部分循环和全循环,两段法流程又分为两段全循环和两段部分循环。
2.1 单段串联工艺流程单段法加氢裂化从进料到反应产物导出,采用单个或一组反应器直接完成,即使使用两个及以上的反应器组,反应器之间也不存在反应物流的气-液分离过程,原料油经加氢精制后直接进入加氢裂化反应器(加氢裂化床层)。
单段法加氢裂化的特点:①精制段(精制反应器)催化剂具有较高的加氢活性(尤其是HDN活性);②裂化段催化剂具有耐H2S和NH3的能力;③一段反应物流直接进入二段反应器,不必将H2S和NH3分离;④体积空速较低、反应温度较高,原料油的氮含量不宜过高;⑤投资和能耗相对较低;⑥受催化剂性能的制约,中间馏分油的收率一般只能达到65%~75%左右,而且初末期目的产品的选择性变化较大。
单段串联加氢裂化流程简图如下:2.2 两段法工艺流程两段法加氢裂化采用两个反应器,原料油首先在一段反应器进行加氢精制(HDS、HDN、HDO、烯烃饱和和HAD并伴有部分转化)后,进入高压分离器进行气/液分离,高分分离出的富氢气体经脱硫后进入循环氢压缩机,高分分离出的液相进入分馏塔,切割成石脑油、航煤、柴油等产品,塔底未转化油进入二段反应器继续进行裂化反应。
加氢裂化工艺流程

加氢裂化工艺流程1. 简介加氢裂化是一种常用的炼油工艺,用于将重质石油馏分转化为高辛烷值的汽油。
该工艺通过在高温和高压下将长链烃分子分解为较短链的烃类,同时加入氢气来抑制烃类的进一步裂解和脱氢反应。
加氢裂化工艺流程包括预热、加氢裂化反应、分离和再生等步骤。
2. 步骤和流程2.1 预热首先,原料石油馏分经过预热过程,将其加热到适宜的温度。
预热有助于提高反应速率和转化率,并减少催化剂的热损失。
预热的温度和时间根据具体的石油馏分和工艺条件来确定。
2.2 加氢裂化反应预热后的石油馏分进入加氢裂化反应器,与催化剂和氢气一起进行反应。
催化剂通常采用铝硅比较高的沸石催化剂,具有较好的活性和选择性。
反应器内的温度和压力控制在适宜的范围内,以提高反应速率和转化率。
在加氢裂化反应中,长链烃分子发生裂解和氢化反应,生成较短链的烃类和饱和烃。
裂解产物中的短链烃类主要是高辛烷值的汽油组分,而饱和烃主要是石蜡。
2.3 分离反应器出口的混合物进入分离器,通过分馏和其他分离操作将产物分离。
分离过程主要包括汽油、石蜡、烯烃和气相的分离。
其中,石蜡可以作为工业原料或进一步加工成蜡烛、润滑油等产品。
2.4 再生经过分离的催化剂进入再生器,通过加热和氢气的作用将吸附在催化剂上的碳杂质和焦炭燃烧掉,再生催化剂的活性。
再生后的催化剂回流到加氢裂化反应器中,继续参与反应。
3. 工艺优化和改进为了提高加氢裂化工艺的效果和经济性,可以采取以下措施进行优化和改进:3.1 催化剂的选择和改进选择具有较高活性和选择性的催化剂,通过改变催化剂的物理和化学性质来提高其性能。
例如,改变催化剂的孔径大小、比表面积和酸性等,可以调节反应的速率和产物分布。
3.2 反应条件的优化通过调整反应器的温度、压力和氢气的用量等参数,优化反应条件,提高反应速率和转化率。
同时,可以采用多级反应器和换热器等装置,提高能量利用率和催化剂的利用率。
3.3 废气处理加氢裂化过程中产生的废气中含有大量的硫化物、氮化物和有机物等污染物,需要进行适当的处理。
加氢裂化工艺流程
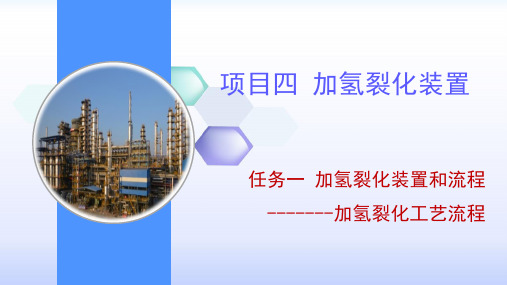
8.1.2金融投资理财国内外业务状况
1.美国理财业务的状况
美国理财业务经历了初创期、扩张期、成熟稳定期三个阶段。最早提供该服 务的是20世纪30年代的保险营销人员。由于1929年的经济危机,他们为了更好地 开展业务,对客户进行了一些简单的个人生活规划和综合资产运用策略,成为今 天个人理财规划师的前身。二战后,经济的复苏和社会财富的日益积累使美国个 人理财业务进入了扩张时期。从业人员不断增加,但由于缺乏相关的专业职业认 证,导致市场上鱼龙混杂,行业混乱。随着CFP(CertifiedFinancialPlanner) 制度逐步的建立,市场混乱问题才得以解决,得以规范化、专业化发展理财业务,
日本的证券市场已经相当成熟,东京股市已经成为日本经济的晴雨表,同时 在一定程度上也反映了亚洲经济发展的状况,已经成为继纽约和伦敦证券交易所 之后最为广大投资者所关注的证券交易所之一。日本的贷款也渗透到了每个人的 日常生活中,最主要的个人贷款就是住房贷款及消费贷款。
近几年,日本的理财业务发展极快。FP(FinancialPlanning)这个概念迅 速普及,即财务管理。它的发展背景主要有三个因素:金融资产增加;金融自由 化的发展;老龄化的高速发展。日本进入90年代以后,经济增长缓慢,政府又采 用低利率政策,在这种情况下,对FP的需求日益增加,各种专业理财咨询机构也 迅速地发展,如其国内的FP协会等。
3.国内理财业务状况
国内金融业的理财业务发展较晚,直到20世纪90年代中期,各金融机构才 开始重视这一业务。20世纪90年代末期,由于中国经济持续20年的高速增长, 公众的收入普遍增加,个人金融资产日益膨胀,人们开始关注自己资产的安全 性、收益性和流动性,因而有了较强烈的理财需求。
同时,中国加入了WTO,国外金融机构正在逐渐进入中国市场,其所经营 的包括理财的各种业务对国内金融机构造成极大冲击。另一方面,国内银行传 统零售业务的利润水平在逐渐下降,盈利能力受到了严峻的挑战。外资银行利 用其丰富的零售经验和混业优势,以优质客户为目标和国内金融机构展开激烈 竞争。
加氢裂化工艺流程概述
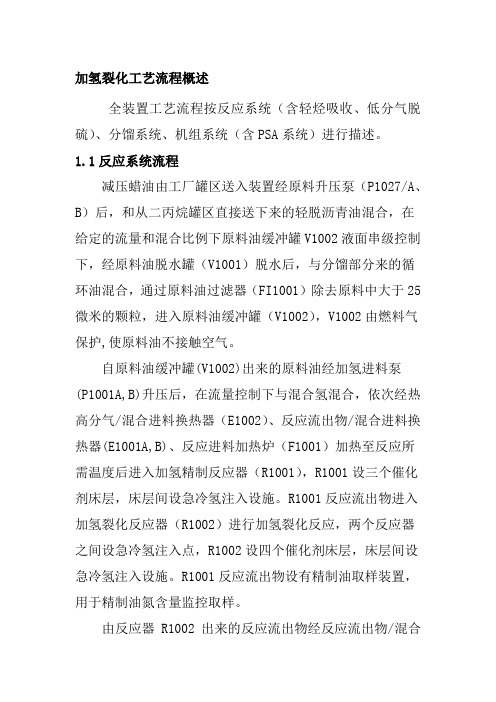
加氢裂化工艺流程概述全装置工艺流程按反应系统(含轻烃吸收、低分气脱硫)、分馏系统、机组系统(含PSA系统)进行描述。
1.1反应系统流程减压蜡油由工厂罐区送入装置经原料升压泵(P1027/A、B)后,和从二丙烷罐区直接送下来的轻脱沥青油混合,在给定的流量和混合比例下原料油缓冲罐V1002液面串级控制下,经原料油脱水罐(V1001)脱水后,与分馏部分来的循环油混合,通过原料油过滤器(FI1001)除去原料中大于25微米的颗粒,进入原料油缓冲罐(V1002),V1002由燃料气保护,使原料油不接触空气。
自原料油缓冲罐(V1002)出来的原料油经加氢进料泵(P1001A,B)升压后,在流量控制下与混合氢混合,依次经热高分气/混合进料换热器(E1002)、反应流出物/混合进料换热器(E1001A,B)、反应进料加热炉(F1001)加热至反应所需温度后进入加氢精制反应器(R1001),R1001设三个催化剂床层,床层间设急冷氢注入设施。
R1001反应流出物进入加氢裂化反应器(R1002)进行加氢裂化反应,两个反应器之间设急冷氢注入点,R1002设四个催化剂床层,床层间设急冷氢注入设施。
R1001反应流出物设有精制油取样装置,用于精制油氮含量监控取样。
由反应器R1002出来的反应流出物经反应流出物/混合进料换热器(E1001)的管程,与混合原料油换热,以尽量回收热量。
在原料油一侧设有调节换热器管程出口温度的旁路控制,紧急情况下可快速的降低反应器的入口温度。
换热后反应流出物温度降至250℃,进入热高压分离器(V1003)。
热高分气体经热高分气/混合进料换热器(E1002)换热后,再经热高分气空冷器(A1001)冷至49℃进入冷高压分离器(V1004)。
为了防止热高分气在冷却过程中析出铵盐堵塞管路和设备,通过注水泵(P1002A,B)将脱盐水注入A1001上游管线,也可根据生产情况,在热高分顶和热低分气冷却器(E1003)前进行间歇注水。
加氢裂化说明书
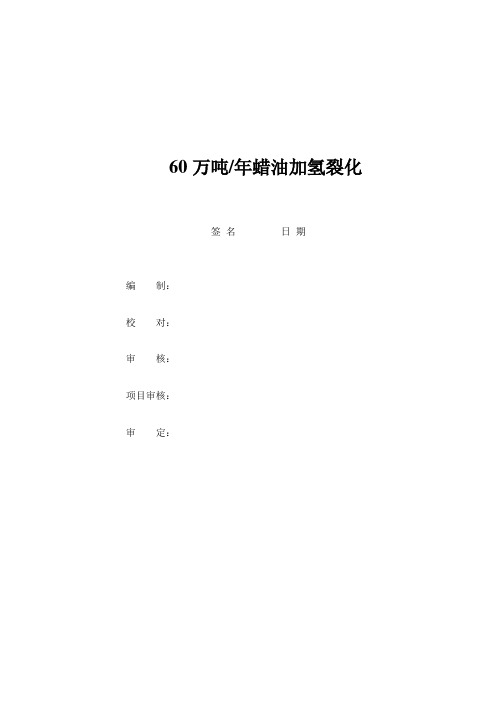
60万吨/年蜡油加氢裂化签名日期编制:校对:审核:项目审核:审定:目录1. 概述 (3)2.工艺设计技术方案 (4)3.原料、产品、催化剂和化学药剂 (5)4.物料平衡 (13)5.工艺流程简述 (15)6.主要设备选型 (20)7.消耗指标及能效 (29)8.生产控制分析 (34)9.装置定员 (37)10.环境保护 (38)11.职业安全卫生 (40)12.对外协作关系 (47)13.设计执行的主要标准目录 (49)1. 概述本项目工程内容包括厂区内新建50万吨/年润滑油基础油改质装置界区内所有工程。
1.1装置概况本装置是河北鑫海化工集团有限公司50万吨/年润滑油基础油改质装置,本装置以直馏蜡油和焦化蜡油为原料生产石脑油、柴油和尾油。
以直馏蜡油和焦化蜡油为原料生产石脑油、柴油和尾油。
装置设计兼顾全循环和一次通过两种操作方案。
1.1.1 装置规模方案一:50万吨/年,部分循环(按5%尾油);方案二:一次通过60万吨/年;操作弹性:60%~110%。
1.1.2 年开工时数本装置年开工时数为8000小时。
1.2 装置组成加氢裂化装置由反应部分(包括压缩机)、分馏部分、吸收稳定部分及公用工程部分构成。
2. 工艺设计技术方案2.1工艺技术方案采用一段串联全循环流程,兼顾一次通过生产乙烯料流程。
反应部分采用热分流程,炉前混氢工艺,设置双反应器,尾油循环至精制反应器入口。
分馏部分采用了“脱丁烷塔+分馏塔”方案,同时设置了轻烃回收设施。
这些工艺技术的优点是对原料油的适应性较强,具有较高的生产灵活性,其主产品煤油、柴油、石脑油以及尾油的产率均可进行较大幅度的调整。
该设计充分考虑了生产的灵活性,在流程设置上不仅考虑了全循环及一次通过两种工况下操作的可能性,而且进一步优化产品分馏系统的设计,提高反应产物中高价值组分的回收速率,清晰分割产品,增加经济效益。
2.2工艺技术特点(一)反应部分流程特点1)为获得低固体含量的进料,防止因系统压强过大而造成的非正常停工,原料油在进装置前应滤去直径大于50μm的颗粒。
- 1、下载文档前请自行甄别文档内容的完整性,平台不提供额外的编辑、内容补充、找答案等附加服务。
- 2、"仅部分预览"的文档,不可在线预览部分如存在完整性等问题,可反馈申请退款(可完整预览的文档不适用该条件!)。
- 3、如文档侵犯您的权益,请联系客服反馈,我们会尽快为您处理(人工客服工作时间:9:00-18:30)。
加氢裂化分馏系统操作法1.1岗位任务和职责1.1.1岗位任务1.1.1.1以加氢裂化反应生成油为原料,按工艺操作标准及工艺卡片的要求,操作加热炉、分馏塔等主要设备;采用分馏、汽提等分离方法,生产出合格的液态烃、轻重石脑油、航煤、柴油、乙烯料、轻中重润滑油组分等产品。
1.1.2岗位职责1.1.2.1严格按工艺卡片、平稳率指标及车间规定控制操作,保持各塔液位、压力、温度、流量平稳,平为其他岗位平稳操作创造条件。
1.1.2.2根据反应系统操作参数的变化,正确分析操作,及时调整,保证各产品质量合格。
1.1.2.3按工艺操作规程要求,加强对加热炉的维护和管理,对异常情况做出准确判断与处理。
1.1.2.4对本系统的所有设备、机泵及仪表设备进行定期巡检及不定期检查,有异常情况及时汇报班长并做相应的处理措施,做好操作记录。
1.1.2.5遇到异常情况岗位应冷静分析,准确判断,采取一切有效的方法恢复平稳操作;对报警与连锁动作做出快速判断,紧急情况下,有权实施分馏岗位紧急联锁。
1.2操作因素分析分馏系统的目的是生产符合质量标准的各类产品,并为反应系统提供符合要求的性质相对稳定的循环油。
保持分馏系统的物科平衡及热量平衡,是分馏系统的设计思想和依据,是分馏操作必须遵循的原则。
我装置分馏系统包括:脱丁烷塔(重沸炉)、脱乙烷塔、常压塔(常压进料炉)、减压塔(常压进料炉),操作遵循蒸馏原理。
1.2.1操作因素分析1.2.1.1脱丁烷塔(T1001)a.压力压力是产品的定性值,它决定油品的沸点,在相同温度相同组成下,决定油品的气化率。
塔顶压力是靠控制塔顶分液罐的压力来实现塔的压力对整个分馏塔组分的沸点有直接影响,随着塔压升高,产品的沸点也会升高,以致给组分的分离带来更大的困难。
正常的塔压不宜改变,塔操作的稳定由温度调节控制。
正常压力控制在1.55MPa。
b.温度:脱丁烷塔两路进料:从冷低分经E1015加热后约168℃进22层;从热低分底约250℃进28层。
保持进料流量温度及出料流量和温度的稳定是塔操作的关键①.脱丁烷塔进料温度:脱丁烷塔进料温度是对全塔热量的一个补充,应合理利用进料带进热量,降低重沸炉负荷。
但如果温度太高。
进料中的气相量过大,精馏段对组分分离效果变差,造成塔顶携带重组分,塔的效率降低。
进料温度应和重沸炉负荷统筹考虑。
②.重沸炉出口温度:重沸炉出口温度同重沸炉塔底液体循环量一样,提供了一个输入系统热量的指示,是一个需要控制温度。
设计炉出口温度325℃。
当输入系统的热量或分离程度不足时,应提大循环量或适当升高重沸炉出口温度。
如果温度升高到极限(炉出口温度最高不得超过370℃),油循环量应逐渐增大,保持脱丁烷塔在设计温度以内。
③.塔顶温度:主要予示了塔顶产品中重关键组份的含量的。
如果温度太高,表明塔顶重组分增加,应加大塔顶回流量或降低塔底温度,控制塔顶温度在指标范围内。
因此,为了减少塔顶组分中C5 含量,减少液体产品浪费,在脱丁烷塔操作中,塔顶、塔底温度的控制是应当注意的。
④.塔顶空气冷却器出口流体温度:塔顶空气冷却器出口流体温度,表示出空冷器和后冷器之间的热平衡,其空冷设计温度50℃⑤.回流温度:回流温度(指脱丁烷塔顶回流罐内)的温度对脱丁烷塔回流和进料均有影响,其设计温度为40℃。
为保证稳定操作,必须避免温度超高。
⑥.塔底温度:脱丁烷塔底液体温度是它的泡点温度,表示塔底液体中,轻质关键组分的浓度。
如果温度太高,必须加大回流量或降低塔顶液体产品的排出量,或调整重沸炉负荷。
塔底温度约为274℃c.进料量进料量增大或降低,必须按比例增大或降低回流量和重沸炉循环量,监视脱丁烷塔各点的温度和压力,以维持塔顶和塔底产物的质量稳定。
正常操作的重沸炉大概循环率可由下列数确定:重沸炉循环率(要求的)=进料(正常的)进料(要求的))重沸炉循环率(正常的 d.排出量塔底产品排出量的控制对产品的切割点有直接的影响。
要仔细调节塔底产品的排出量以使塔底液体产物中的轻组分含量合乎要求。
从而保证回流罐排气减至最少,以保证常压塔生产规定的轻石脑油,其它工艺参数如回流量和温度在排出量发生变化时均需要调节。
e.回流量回流量对产品的质量和收率有很大影响。
当回流比增大时,塔顶产品与塔底产物之间将得到精确的分离。
如果回流量和塔顶产品排出量增大,塔盘负荷也会增大。
因此,要注意总液体量的增大(回流量和产品的流量总和)以防止意外事故(如液冷)。
当进料中的液化气和轻馏份相对降低时,需要使用较高的回流比。
但回流比对塔的进料应相对地恒定。
1.2.1.2脱乙烷塔(T1002):如果T1001顶分析液化气质量合格,可以不启用该塔,液化气直接由T1001顶回流罐出装置。
装置设计有甩T1002流程。
a.压力脱乙烷塔设计操作压力3.05MPa (表),在此压力下要充分保证C2、C3的液化和分离,尽可能减少塔顶对C3的携带,回收液化气组分。
b.温度①.脱乙烷塔中有三个温度显示和一个主要温度控制器。
下列温度显示以脱丁烷塔部分同样的原理起作用。
TI-1226设在脱乙烷塔顶挥发线上(操作期间应在55℃范围内),依据此温度,对回流量进行调整。
TI-1223设于塔顶冷却器后抽出线上(操作期间必须低于40℃),将受循环水压力和水温的限制,如果冷后温度高,将造成塔压升高,同时对轻烃吸收塔的负荷造成影响。
TI-1221设于脱乙烷塔塔底液体流出线上(操作期间应在110℃左右),此温度是全塔操作负荷调整的关键,依据液化气分析,控制液化气中C2的含量,相应提降重沸器负荷,达到控制产品质量合格的目的。
②.装在第一层填料底部上的TIC-1228控制着进入重沸器的航煤流量,以维持输入系统的足够热量,塔底温度的实现,是通过TIC-1228的变化来实现的,当在塔底液化气产品中含有较轻的组分时,TIC—1228的给定值要相应的提高,以除去较轻组分。
在这种情况下,塔负荷增大。
该温度设计为112℃③.重沸器工作原理我装置使用的是循环式热虹吸式重沸器,具体讲是由于介质加热汽化,使得上升管内汽液混合物的相对密度明显低于入口管内液体的相对密度,由此重沸器的入方和出方产生静差压,塔底的液体不断被虹吸进入重沸器,加热后汽化后的气液混合物自动地返回塔内,实现不断循环。
重沸器的操作要注意防止塔底带水、热流进入重沸器过快,造成汽化率过高、塔底液面空。
c.进料量与回流量当脱乙烷塔进料量变化时,要手动调节冷凝冷却器和塔底冷却器的冷却水量,保持塔顶回流罐不超过5O℃的设计温度。
1.2.1.3常压塔(T-1003)a.压力塔的压力(包括汽提塔)是通过回流罐V-1009上的PIC-1306A、B 来控制。
PIC-1306B给定值相对要低一些大约0.10MPa,PIC-1306A给定值相对要高一些为0.13MPa,使常压塔顶压力波动在一定小的范围内,即控制平稳,又降低瓦斯浪费,常压塔顶瓦斯由于量少,当压力超高时,可向火炬排放。
b.温度T003共有顶温、进料温度、侧线抽出温度、中段回流温度等可用于调整的温度。
①.塔顶温度调节器TIC-1321设在塔顶挥发线上,通过反复调节轻石脑油回流量来控制塔顶温度。
塔顶温度决定轻石脑油干点,该温度在70一80℃的范围内。
如要提高轻石脑油切割点,就要增大TIC-1321的给定值。
②.进料温度指示着带入塔内热量的大小和油品的气化率,进料温度温度一般不作为调节手段,其温度由常压炉出口而定。
③.侧线抽出温度高,产品组分重,干点高,反之亦然,正常情况下靠抽出量调节,抽出量大,温度升高,随着进料性质和产品方案的不同而变化。
④.中段回流温度用装在返塔线上的温度调节器TIC1505通过调节蒸发器E1203正线和副线流量的调节阀来控制温度。
中段回流温度的高低影响塔内热平衡,温度高,返塔后的换热塔盘数少,取热少,塔盘温度上升,塔上部热量增大,顶温和侧线抽出温度都要上升,影响产品的分离效果。
正常操作中该温度不应有大的波动,取热量靠中段回流量来调节。
c.进料量进料来自脱丁烷塔,其流量由脱丁烷塔底液位控制。
通过控制阀来降低进料压力使之部分汽化。
d.侧线抽出量侧线抽出量改变时,塔的内回流改变,抽出量增大,内回流降低,汽相负荷相对增大,使塔下部温度升高,操作上为了保证顶部产品和侧线产品的质量,就需要增大顶回流量和中段回流量。
侧线抽出量的大小是由进料量和转化率决定的,同时也受生产方案的制约。
e.中段回流量中段回流量的控制是靠装在返塔线上的流量控制器来调节的,循环量的大小要根据塔内过剩的热量来决定,当顶取热过大时,侧线抽出温度高,顶温降低困难时,都要用增大中段回流的方法来调节,以降低塔顶负荷f.汽提蒸汽量汽提蒸汽包括塔底和各侧线汽提蒸汽,其作用都是将油品中较轻的组分分离出来以提高收率和保证产品质量,一般其大小为进料量的3~5%1.2.1.4减压塔(T1007)a.压力减压塔是在负压条件下操作的。
塔顶挥发线上装有二台抽空器,通过抽空器在塔顶形成负压。
如果操作负荷太小,可以停一台抽空器。
负压操作降低了油品的沸点,使油品在较低的温度下汽化,这样可以避免设备处于高温和防止油品过度裂解。
设计压力应为-0.095MPab.温度温度控制与常压塔类似。
c.进料量及排出量这些参数与常压部分同样的方式起作用。
d.回流量减压塔“侧线回流系统”,其性质与常压塔顶回流系统是一样的。
1.2.2操作调节1.2.2.1温度。