磷化影响因素
磷化质量影响因素及其提高途径

磷化质量影响因素及其提高途径引言磷化是一种化学与电化学反应形成磷酸盐化学转化膜的过程。
早在1869年W. A. Ross 就申请了磷化专利技术 [ 2 ] ,随着科技的不断进步,金属磷化处理作为传统的表面处理技术在金属防护、减磨耐磨及涂层打底等方面得到广泛的发展和应用。
磷化处理有多种分类方法:按成膜体系可分为锌系、锌锰系、锰系、铁系、锌钙系及非晶相铁系等六大类;按磷化处理温度可分为常温(不加温)、低温(30~45℃)、中温(60~70℃)、高温(大于80℃)四类;按材质可分为钢铁件、铝件、锌件以及混合件磷化;其它的还有按磷化膜厚度或促进剂类型等分类。
用于防锈磷化的主要有铁系磷化、锌系磷化、锰系磷化三种;用于耐磨减磨磷化的种类有锌系磷化和锰系磷化;而锌锰系和锌钙系主要用于漆前磷化。
一磷化基本原理磷化成膜是一个化学动态平衡,目前,大多数学者认同的磷化原理由以下四个步骤组成:首先是金属的溶解过程。
当金属浸入磷化液中时,先与磷化液中的磷酸作用,生成一代磷酸铁,并有大量的氢气析出。
其化学反应为;Fe –2e→Fe2+2H+ + 2e→H2上式表明,磷化开始时,仅有金属的溶解,而无膜生成。
第二是促进剂加速形成磷化膜。
其化学反应式为:[O]+[H] → [R]+H2OFe2++[O] → Fe3++[R]式中[O]为促进剂(氧化剂),[R]为还原产物,由于促进剂氧化掉第一步反应所产生的氢原子,加快了反应(1)的速度,进一步导致金属表面H+浓度急剧下降。
同时也将溶液中的Fe2+氧化成为Fe3+。
第三是磷酸根的多级离解。
H3PO4→H2PO4-+H+→HPO42-+2H+→PO43-+3H+由于金属表面的H+浓度急剧下降,导致磷酸根各级离解平衡向右移动,最终离解为PO43-。
最后磷酸盐沉淀结晶成为磷化膜当金属表面离解出的PO43-与溶液中(金属界面)的金属离子(如Zn2+、Mn2+、Ca2+、Fe2+)达到溶度积常数Ksp时,就会形成磷酸盐沉淀Zn2++ Fe2++ PO43-+H2O→Zn2Fe(PO4)2·4H2O↓ (4)3Zn2++2PO43-+4H2O=Zn3(PO4)2·4H2O↓ (5)磷酸盐沉淀与水分子一起形成磷化晶核,晶核继续长大成为磷化晶粒,无数个晶粒紧密堆集形而上学成磷化膜。
火山岩型磷化作用机理与成岩环境分析
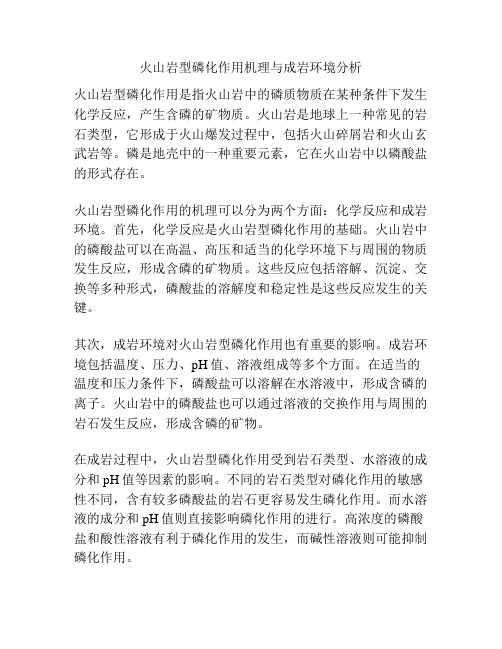
火山岩型磷化作用机理与成岩环境分析火山岩型磷化作用是指火山岩中的磷质物质在某种条件下发生化学反应,产生含磷的矿物质。
火山岩是地球上一种常见的岩石类型,它形成于火山爆发过程中,包括火山碎屑岩和火山玄武岩等。
磷是地壳中的一种重要元素,它在火山岩中以磷酸盐的形式存在。
火山岩型磷化作用的机理可以分为两个方面:化学反应和成岩环境。
首先,化学反应是火山岩型磷化作用的基础。
火山岩中的磷酸盐可以在高温、高压和适当的化学环境下与周围的物质发生反应,形成含磷的矿物质。
这些反应包括溶解、沉淀、交换等多种形式,磷酸盐的溶解度和稳定性是这些反应发生的关键。
其次,成岩环境对火山岩型磷化作用也有重要的影响。
成岩环境包括温度、压力、pH值、溶液组成等多个方面。
在适当的温度和压力条件下,磷酸盐可以溶解在水溶液中,形成含磷的离子。
火山岩中的磷酸盐也可以通过溶液的交换作用与周围的岩石发生反应,形成含磷的矿物。
在成岩过程中,火山岩型磷化作用受到岩石类型、水溶液的成分和pH值等因素的影响。
不同的岩石类型对磷化作用的敏感性不同,含有较多磷酸盐的岩石更容易发生磷化作用。
而水溶液的成分和pH值则直接影响磷化作用的进行。
高浓度的磷酸盐和酸性溶液有利于磷化作用的发生,而碱性溶液则可能抑制磷化作用。
火山岩型磷化作用在地质历史中具有重要的意义。
它是磷矿床形成的主要途径之一,也是磷肥资源的重要来源。
在岩石圈的构造作用下,磷酸盐通过地下水和热液等途径进入火山岩中,形成含磷的矿物质。
随着地壳的抬升和侵蚀,这些含磷的矿物质被暴露在地表,形成磷矿床。
由于磷是植物生长的必需元素,磷矿床是磷肥资源的重要来源。
火山岩型磷化作用的认识对于磷资源的勘探和利用具有重要的指导意义。
总之,火山岩型磷化作用是火山岩中的磷酸盐在特定的化学环境下发生反应,形成含磷的矿物质的过程。
化学反应和成岩环境是火山岩型磷化作用的机理,岩石类型、水溶液的成分和pH值等因素对其影响很大。
火山岩型磷化作用在地质历史中起着重要的作用,是磷矿床形成和磷肥资源开发的重要途径。
黑色磷化的影响因素与工艺改进
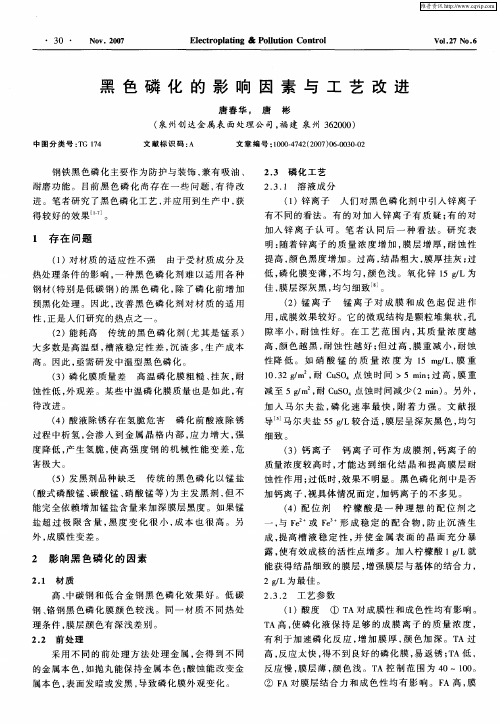
维普资讯
・
3 ・ 0
No . 0 7 v 20
Elc r p a i g & P lu o e to l tn o l t n Con r l i to
采 用 不 同的前 处 理 方法 处 理金 属 , 得 到不 同 会 的金 属本 色 , 如抛 丸能保 持金 属本 色 ; 酸蚀 能改 变金 属本 色 , 面发暗 或发黑 , 表 导致磷 化 膜外观 变化 。
2 3 2 工 艺参 数 .. ( )酸度 1 ① T A对成膜性 和成色性 均有影 响 。 T A高 , 使磷 化 液 保持 足 够 的 成膜 离 子 的质 量浓 度 , 有利 于加 速磷 化 反 应 , 加 膜厚 , 色加 深 。T 增 颜 A过 高, 反应 太快 , 得不 到 良好 的磷 化膜 , 易返 锈 ; A低 , T 反 应慢 , 膜层 薄 , 色浅 。T 颜 A控 制 范 围 为 4 0~10 0。
l 存 在 问题
( ) 材 质 的 适 应 性 不 强 由 于 受 材 质 成 分 及 1 对
提高 , 色黑度增 加 。过高 , 晶粗 大 , 颜 结 膜厚 挂灰 ; 过 低 , 化膜 变薄 , 均 匀 , 色 浅 。氧 化锌 1 L为 磷 不 颜 5
佳 , 层 深 灰 黑 , 匀 细 致 。 膜 均
能 获得结 晶细 致 的膜 层 , 强膜 层 与基体 的结合 力 , 增
2g L为 最 佳 。 /
高、 中碳 钢和 低 合 金钢 黑 色 磷化 效 果 好 。低 碳
钢 、 钢黑 色磷化 膜 颜 色 较浅 。同一 材 质 不 同热 处 铬 理条件 , 膜层 颜色有 深浅 差别 。
磷化影响因素

磷化处理温度温度愈高,磷化层愈厚,结晶愈粗大。
温度愈低,磷化层愈薄,结晶愈细。
但温度不宜过高,否则Fe2+ 易被氧化成Fe3+,加大沉淀物量,溶液不稳定。
游离酸度游离酸度指游离的磷酸。
其作用是促使铁的溶解,已形成较多的晶核,使膜结晶致密。
游离酸度过高,则与铁作用加快,会大量析出氢,令界面层磷酸盐不易饱和,导致晶核形成困难,膜层结构疏松,多孔,耐蚀性下降,令磷化时间延长。
游离酸度过低,磷化膜变薄,甚至无膜。
总酸度总酸度指磷酸盐、硝酸盐和酸的总和。
总酸度一般以控制在规定范围上限为好,有利于加速磷化反应,使膜层晶粒细,磷化过程中,总酸度不断下降,反映缓慢。
总酸度过高,膜层变薄,可加水稀释。
总酸度过低,膜层疏松粗糙。
PH值锰系磷化液一般控制在2-3之间,当PH﹥3时,共件表面易生成粉末。
当PH‹1.5时难以成膜。
铁系一般控制在3-5.5之间。
溶液中离子浓度①溶液中Fe2+极易氧化成Fe3+,导致不易成膜。
但溶液中Fe2+浓度不能过高,否则,形成的膜晶粒粗大,膜表面有白色浮灰,耐蚀性及耐热性下降。
②Zn2+的影响,当Zn2+浓度过高,磷化膜晶粒粗大,脆性增大,表面呈白色浮灰;当Zn2+浓度过低,膜层疏松变暗。
工件表面状态金属工件表面状态对磷化质量影响较大,即使是同一磷化工艺,同一磷化制剂,同一工件的不同部位的磷化膜质量也可能相差较大,这就是因为工件表面状态差异所致。
一般来说,高、中碳钢和低合金钢容易磷化,磷化膜黑而厚,但磷化膜结晶有变粗的倾向,低碳钢磷化膜结晶致密,颜色较浅,若磷化前进行适当的酸洗,可有助于提高磷化膜质量,冷轧板因其表面有硬化层,磷化前最好进行适当的酸洗或表调,否则膜不均匀,膜薄,耐蚀性低。
水质磷化后用水冲洗磷化膜的作用是去除吸附在膜表面的可溶性物质等,以防止涂抹在湿热条件下起泡,脱落,提高涂膜附着力,耐腐蚀性,通过对一同磷化膜分别采用去离子水,下水道水,车间排放水冲洗实验得知其耐蚀性、柔韧性逐个降低。
磷化处理影响因素及常见问题审批稿

磷化处理影响因素及常见问题YKK standardization office【 YKK5AB- YKK08- YKK2C- YKK18】一、磷化工艺参数的影响1、总酸度————总酸度过低、磷化必受影响,因为总酸度是反映磷化液浓度的一项指标。
控制总酸度的意义在于使磷化液中成膜离子浓度保持在必要的范围内。
2、游离酸度————游离酸度过高、过低均会产生不良影响。
过高不能成膜,易出现黄锈;过低磷化液的稳定性受威胁,生成额外的残渣。
游离酸度反映磷化液中游离H+的含量。
控制游离酸度的意义在于控制磷化液中磷酸二氢盐的离解度,把成膜离子浓度控制在一个必须的范围。
磷化液在使用过程中,游离酸度会有缓慢的升高,这时要用碱来中和调整,注意缓慢加入,充分搅拌,否则碱液局部过浓会产生不必要的残渣,出现越加碱,游离酸度越高的现象。
单看游离酸度和总酸度是没有实际意义的,必须一起考虑。
3、酸比————酸比即指总酸度与游离酸度的比值。
一般的说酸比都在5~30的范围内。
酸比较小的配方,游离酸度高,成膜速度慢,磷化时间长,所需温度高。
酸比较大的配方,成膜速度快,磷化时间短,所需温度低。
因此必须控制好酸比。
4、温度————磷化处理温度与酸比一样,也是成膜的关键因素。
不同的配方都有不同的温度范围,实际上,他在控制着磷化液中的成膜离子的浓度。
温度高,磷酸二氢盐的离解度大,成膜离子浓度相应高些,因此可以利用此种关系在降低温度的同时提高酸比,同样可达到成膜,其关系如下:70℃ 60℃ 50℃ 40℃ 30℃ 20℃1/5 1/7 1/10 1/15 1/20 1/25生产单位确定了某一配方后,就应该严格控制好温度,温度过高要产生大量沉渣,磷化液失去原有平衡。
温度过低,成膜离子浓度总达不到浓度积,不能生成完整磷化膜。
温度过高,磷化液中可溶性磷酸盐的离解度加大,成膜离子浓度大幅度提高,产生不必要的沉渣,白白浪费了磷化液中的有效成分,原有的平衡被迫坏,形成一个新的温度下的平衡,如,低温磷化液在温度失控而升高时,H2PO4→H++PO43- 的离解反应向右进行,从而使磷酸根浓度升高,产生磷酸锌沉淀,使磷化液的酸比自动升高。
影响磷化的工艺因素
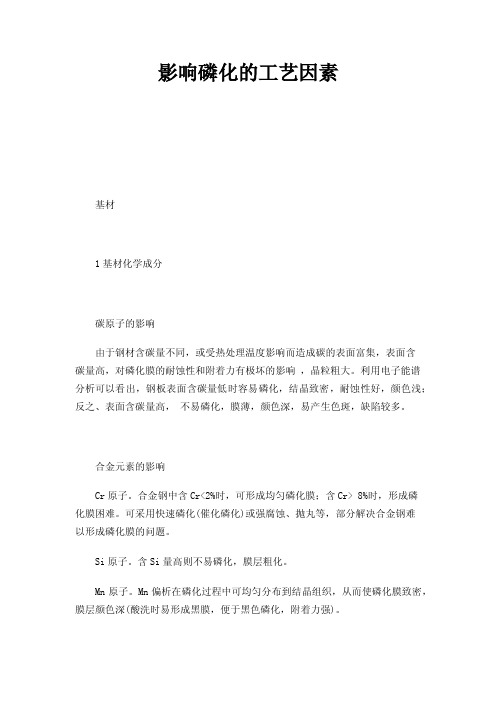
影响磷化的工艺因素基材1基材化学成分碳原子的影响由于钢材含碳量不同,或受热处理温度影响而造成碳的表面富集,表面含碳量高,对磷化膜的耐蚀性和附着力有极坏的影响,晶粒粗大。
利用电子能谱分析可以看出,钢板表面含碳量低时容易磷化,结晶致密,耐蚀性好,颜色浅;反之、表面含碳量高,不易磷化,膜薄,颜色深,易产生色斑,缺陷较多。
合金元素的影响Cr原子。
合金钢中含Cr<2%时,可形成均匀磷化膜;含Cr> 8%时,形成磷化膜困难。
可采用快速磷化(催化磷化)或强腐蚀、抛丸等,部分解决合金钢难以形成磷化膜的问题。
Si原子。
含Si量高则不易磷化,膜层粗化。
Mn原子。
Mn偏析在磷化过程中可均匀分布到结晶组织,从而使磷化膜致密,膜层颜色深(酸洗时易形成黑膜,便于黑色磷化,附着力强)。
Ni原子。
含Ni材质经热处理后,合金组织发生变化,磷化困难,且易出现缺陷。
活性冷轧钢板的活性大小对磷化效果产生不同的影响。
即活性小的冷轧钢板磷化效果好;而活性大的磷化效果差。
生产表明,几种冷轧钢板的活性大小顺序:宝钢板2030>日本板>宝钢1550。
需要钢板生产厂家,降低钢板活性。
表面状态粗糙度在相同磷化条件下,磷化工件表面光洁度越高,磷化过程进行越缓慢,获得的膜层薄而致密,且颜色浅。
反之,表面粗糙,磷化反应快,膜层厚而疏松,均匀性差,颜色深。
可以解释为:光洁度高的表面比粗糙的表面电位正,基体表面在磷化液中不易被酸蚀所致。
所以,光洁度高的工件,磷化前必须进行充分预处理(抛丸或酸蚀)。
锈蚀度。
锈蚀钢板会影响磷化质量(无论采用何种涂锈方法,其磷化膜耐蚀性差)。
况且由于酸洗造成工件表面黑白不均匀,同样影响磷化效果(白色部位较难磷化)。
因此,尽量不要选用锈蚀的钢板加工工件。
特别要防止采用不同厂家、不同批次的钢板来加工同一工件(如汽车车身等)。
否则。
因钢板的差异而造成磷化质量不一样。
同时要注意加工过程中尽量不要破坏钢板防锈膜和加工后长时间存放(采取防锈措施)。
磷化处理影响因素及常见问题

磷化处理影响因素及常见问题一、磷化工艺参数的影响1、总酸度————总酸度过低、磷化必受影响,因为总酸度是反映磷化液浓度的一项指标。
控制总酸度的意义在于使磷化液中成膜离子浓度保持在必要的范围内。
2、游离酸度————游离酸度过高、过低均会产生不良影响。
过高不能成膜,易出现黄锈;过低磷化液的稳定性受威胁,生成额外的残渣。
游离酸度反映磷化液中游离H+的含量。
控制游离酸度的意义在于控制磷化液中磷酸二氢盐的离解度,把成膜离子浓度控制在一个必须的范围。
磷化液在使用过程中,游离酸度会有缓慢的升高,这时要用碱来中和调整,注意缓慢加入,充分搅拌,否则碱液局部过浓会产生不必要的残渣,出现越加碱,游离酸度越高的现象。
单看游离酸度和总酸度是没有实际意义的,必须一起考虑。
3、酸比————酸比即指总酸度与游离酸度的比值。
一般的说酸比都在5~30的范围内。
酸比较小的配方,游离酸度高,成膜速度慢,磷化时间长,所需温度高。
酸比较大的配方,成膜速度快,磷化时间短,所需温度低。
因此必须控制好酸比。
4、温度————磷化处理温度与酸比一样,也是成膜的关键因素。
不同的配方都有不同的温度范围,实际上,他在控制着磷化液中的成膜离子的浓度。
温度高,磷酸二氢盐的离解度大,成膜离子浓度相应高些,因此可以利用此种关系在降低温度的同时提高酸比,同样可达到成膜,其关系如下:70℃ 60℃ 50℃ 40℃ 30℃ 20℃Fe+2H+→Fe2++H2↑这个反应能够消耗大量的氢离子,促使固液界面的PH上升,进而促使磷化液中的磷酸二氢盐的三级离解平衡右移,以致使锌离子浓度和磷酸根浓度在界面处达到溶度积而成膜。
如果不添加一些有效物质,阴极析出的氢气的滞留会造成阴极极化,使反应不能继续进行,因而磷酸盐膜的沉积也不能连续下去。
因此凡能加速这个反应的物质,必能加速磷化。
氧化剂正是起着阴极去极化的作用而加速反应。
常用的氧化剂有硝酸盐、亚硝酸盐、双氧水、溴酸盐、碘酸盐、钼酸盐、有机硝基化合物、有机过氧化物等。
磷化处理影响因素及常见问题
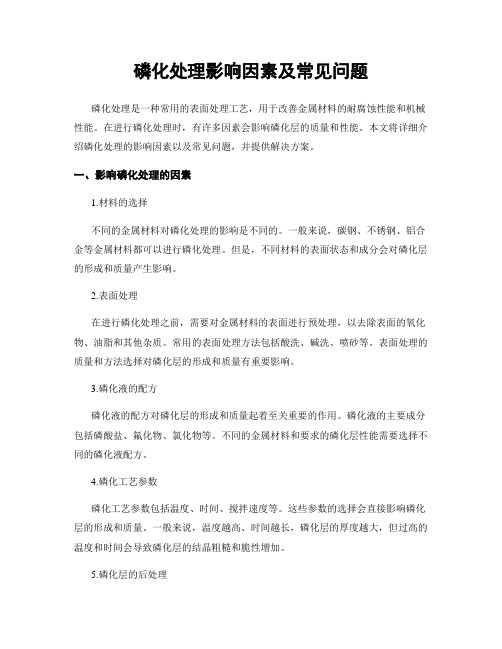
磷化处理影响因素及常见问题磷化处理是一种常用的表面处理工艺,用于改善金属材料的耐腐蚀性能和机械性能。
在进行磷化处理时,有许多因素会影响磷化层的质量和性能。
本文将详细介绍磷化处理的影响因素以及常见问题,并提供解决方案。
一、影响磷化处理的因素1.材料的选择不同的金属材料对磷化处理的影响是不同的。
一般来说,碳钢、不锈钢、铝合金等金属材料都可以进行磷化处理。
但是,不同材料的表面状态和成分会对磷化层的形成和质量产生影响。
2.表面处理在进行磷化处理之前,需要对金属材料的表面进行预处理,以去除表面的氧化物、油脂和其他杂质。
常用的表面处理方法包括酸洗、碱洗、喷砂等。
表面处理的质量和方法选择对磷化层的形成和质量有重要影响。
3.磷化液的配方磷化液的配方对磷化层的形成和质量起着至关重要的作用。
磷化液的主要成分包括磷酸盐、氟化物、氯化物等。
不同的金属材料和要求的磷化层性能需要选择不同的磷化液配方。
4.磷化工艺参数磷化工艺参数包括温度、时间、搅拌速度等。
这些参数的选择会直接影响磷化层的形成和质量。
一般来说,温度越高、时间越长,磷化层的厚度越大,但过高的温度和时间会导致磷化层的结晶粗糙和脆性增加。
5.磷化层的后处理磷化层形成后,需要进行后处理,以提高磷化层的耐腐蚀性能和机械性能。
常用的后处理方法包括中和、封闭、涂覆等。
后处理的质量和方法选择对磷化层的性能有重要影响。
二、常见问题及解决方案1.磷化层不均匀磷化层不均匀可能是由于磷化液的搅拌不均匀、材料表面存在油脂或氧化物等杂质、磷化液配方不合理等原因造成的。
解决方法包括加强搅拌、提高表面处理质量、优化磷化液配方等。
2.磷化层结晶粗糙磷化层结晶粗糙可能是由于磷化液温度过高、时间过长、磷化液配方不合理等原因造成的。
解决方法包括控制磷化液的温度和时间、优化磷化液配方等。
3.磷化层附着力差磷化层附着力差可能是由于材料表面存在油脂、氧化物等杂质、磷化液配方不合理等原因造成的。
解决方法包括提高表面处理质量、优化磷化液配方等。
- 1、下载文档前请自行甄别文档内容的完整性,平台不提供额外的编辑、内容补充、找答案等附加服务。
- 2、"仅部分预览"的文档,不可在线预览部分如存在完整性等问题,可反馈申请退款(可完整预览的文档不适用该条件!)。
- 3、如文档侵犯您的权益,请联系客服反馈,我们会尽快为您处理(人工客服工作时间:9:00-18:30)。
游离酸度和总酸度的影响
(一)游离酸度
所谓游离酸度是指磷化液中游离态氢离子的浓度,它主要由磷酸和其它酸电离产生。
随着反应的进行,氢离子浓度逐渐降低,PH值上升。
当磷化液中的游离酸度过高时,钢铁件表面腐蚀反应过快,反应产生的气泡过多,阻碍磷化膜的形成,使磷化膜结晶粗大、疏松、易泛黄、抗腐蚀能力差。
溶液中酸度过低时,腐蚀反应进行缓慢,磷化膜难以形成,溶液中沉淀物多,膜呈浮粉状,产生挂灰。
(二)总酸度
总酸度也称为全酸度,是指磷化液中化合酸(H2PO4-)和游离酸浓度的总和。
化合酸起着离解出游离态的H+维持溶液中的酸比,保持溶液酸度平衡的作用。
同时化合酸的酸根又是参与成膜的主要成分。
提高总酸度可以增加磷化膜的生成速度,而且成膜细致、均匀。
增加总酸度还可适当降低磷化液的温度。
但总酸度过高,游离酸度太低,也会降低腐蚀速度,成膜也易产生浮粉物;总酸度过低、则反应速度缓慢,磷化膜生成困难。
(三)酸比
酸比是保证处理液相对平衡的一个数值,酸比的计算方法为:
溶液的酸比=游离酸度/总酸度
不同品种磷化液的酸比比值不同。
一般,酸比比值越高,磷化膜越细、越薄,但酸比过高时,不易成膜,皮膜易产生腐蚀现象,磷化液中沉淀多;酸比比值过低时,皮膜结晶粗大、疏松。
七、温度的影响
磷化处理随着温度的升高,其反应加快。
磷化液配制后,溶液中的酸比随温度的变化而变化,温度升高,酸比升高,如果再降低温度时,酸比并不随之降低,这个反应是不可逆的。
这是因为磷化液中的主要成分磷酸二氢锌在温度升高时分解产生H+,增加了游离酸浓度,并产生磷酸锌沉淀的缘故。
3Zn(H2PO4)2→ Zn3(PO4)↓+4H3PO4
在游离酸度增加的同时,磷化锌的大量沉淀使磷化液损失很大,因此,在实际操作过程中,一定要根据工艺规定的温度进行磷化处理。
否则,会大量浪费原材料,破坏液体的内部平衡。
对于同一配方的磷化液,温度越高,磷化膜形成越快,磷化膜加厚,防腐蚀性能提高;但温度过高时,工件表面磷化膜质量降低并易附着灰尘和微粒,影响工件涂装后涂膜的附着力。
温度过低时,反应速度减慢,磷化膜成膜不充分,结晶颗粒大,防蚀性能低。
影响因素
1、温度
温度愈高,磷化层愈厚,结晶愈粗大。
温度愈低,磷化层愈薄,结晶愈细。
但温度不宜过高,否则Fe2+ 易被氧化成Fe3+,加大沉淀物量,溶液不稳定。
2、游离酸度
游离酸度指游离的磷酸。
其作用是促使铁的溶解,已形成较多的晶核,使膜结晶致密。
游离酸度过高,则与铁作用加快,会大量析出氢,令界面层磷酸盐不易饱和,导致晶核形成困难,膜层结构疏松,多孔,耐蚀性下降,令磷化时间延长。
游离酸度过低,磷化膜变薄,甚至无膜。
3、总酸度
总酸度指磷酸盐、硝酸盐和酸的总和。
总酸度一般以控制在规定范围上限为好,有利于加速磷化反应,使膜层晶粒细,磷化过程中,总酸度不断下降,反映缓慢。
总酸度过高,膜层变薄,可加水稀释。
总酸度过低,膜层疏松粗糙。
4、PH值
锰系磷化液一般控制在2-3之间,当PH﹥3时,共件表面易生成粉末。
当PH‹1.5时难以成膜。
铁系一般控制在3-5.5之间。
5、溶液中离子浓度
①溶液中Fe2+极易氧化成Fe3+,导致不易成膜。
但溶液中Fe2+浓度不能过高,否则,形成的膜晶粒粗大,膜表面有白色浮灰,耐蚀性及耐热性下降。
②Zn2+的影响,当Zn2+浓度过高,磷化膜晶粒粗大,脆性增大,表面呈白色浮灰;当Zn2+浓度过低,膜层疏松变暗。
磷化渣
1、磷化渣的影响
①磷化中生成的磷化渣,既浪费药品又加大清渣工作量,处理不好还影响磷化质量,视为不利。
②磷化中在生成磷化渣的同时还会挥发出磷酸,有助于维持磷化液的游离酸度,保持磷化液的平衡,视为有利。
2、磷化渣生成的控制
①降低磷化温度。
②降低磷化液的游离酸度。
③提高磷化速度,缩短磷化时间。
④提高NO-3 与PO3-4的比值。
常见故障
产生的主要原因
解决方法
工件表面均匀泛黄,但均匀疏松的磷化膜
1.总酸度低、酸比低
2.促进剂浓度低
3.磷化温度低、时间短
1.补加磷化液和碱
2.补加促进剂
3.提高温度
4.延长时间
磷化成膜速度慢,但延长磷化时间仍可形成均匀完整膜
1.表面调整能力不强
2.促进剂浓度不够
3.酸比低
4.磷化温度低
1.改进表调或换槽
2.补加促进剂
3.补加碱
4.提高温度
磷化膜局部块状条状挂灰,挂灰处磷化膜不均匀,有时彩色膜1.工件在进入磷化槽前已经形成二次黄绿锈
2.表面调整能力差
3.磷化液中杂质多
1.加快工序间周转或实施水膜保护
2.改进表调
3.更换槽液
磷化膜均匀出现彩色膜或均匀挂白
1.促进剂含量过高
2.表调失去作用或是表调后水洗过度
3.磷化液杂质过多、老化
1.让促进剂自然降低
2.加强表调
3.换槽
工件表面覆盖一层结晶体
1.游离酸度过低
2.温度过高
1.加一些磷酸
2.降低温度
槽液沉渣过多
1.促进剂浓度过高
2.游离酸度过高
3.工件磷化时间过长
4.中和过度形成结晶沉淀
1.让其自然降低
2.补加碱
3.缩短时间
4.补加磷酸
缺陷及防止方法
1、磷化膜结晶粗糙多孔产生原因:磷化槽液中游离酸度过高,磷化液中氧化剂量不足,槽液中亚铁离子含量过高,零件表面有残酸,发生过腐蚀。
防止方法:降低槽液中游离酸的含量,增加氧化剂比例,加双氧水进行调整,加强中和及水洗,控制酸洗浓度和时间。
2、表面粘附白色粉状沉淀产生原因:槽液中游离酸度低,游离磷酸量少,含铁离子少,零件表面氧化物未除净,溶液中氧化剂过量,总酸度过高,槽内沉淀物过多。
防止方法:补充磷酸二氢锌,在特殊情况下可加磷酸调整游离酸度,磷化溶液中应留一定量的沉淀物,使新配槽液与老槽液混合使用;加强酸洗,充分进行水洗;停加氧化剂,调整酸的比值;清除过多的沉淀物。
3、磷化膜不均匀、发花或有斑点产生原因:除油不干净,槽液温度过低,表面钝化,游离酸度和总酸度的比例失调。
卖仪器网防止方法:加强除油清洗,适当提高槽液温度,加强酸洗,将酸比调整到工艺规定范围。
4、磷化膜的耐腐蚀性差和生锈产生原因:磷化膜晶粒过粗或过细,游离酸含量过高,表面过腐蚀,溶液中磷酸盐含量不足,表面有残酸。
防止方法:调整游离酸度与总酸度的比例;降低游离酸含量,可加氧化锌或氢氧化锌;控制酸洗过程;补充磷酸二氢盐;加强中和与水洗过程。
磷化的时间主要根据产品配方的要求
在额定工艺温度下:
磷化时间过长,磷化液腐蚀磷化膜,造成不必要的消耗,且磷化膜粗糙、沉渣过多
磷化时间过短,磷化反应未完成,磷化膜层生长不完全、露底
时间的判断可根据反应状况来决定,线材进入磷化槽初期,反应剧烈,一般情况下5~7分钟时,反应速度趋于平缓,待无明显气泡浮出即可判断为磷化进程结束。