精益生产课程大纲天精选版
精益生产培训课纲
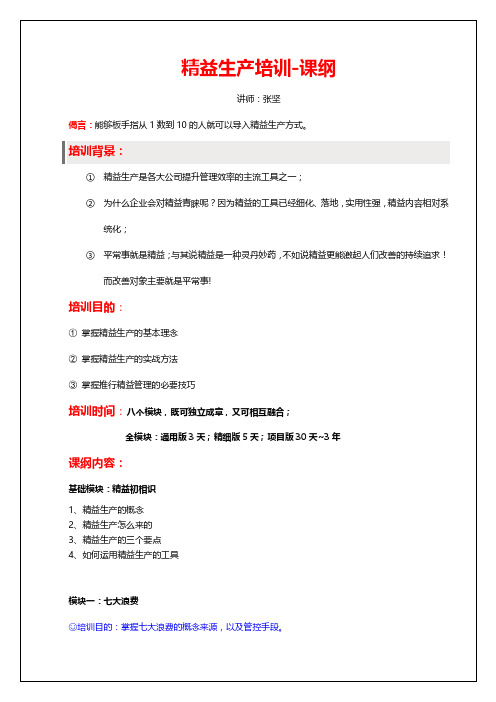
1、什么是七大浪费◆概念与价值2、七大浪费的详细阐述◆七大浪费:运输、库存、动作、等待、过度加工、过度生产、不良浪费◆七大浪费的管控手段3、关于七大浪费的视频与案例解析4、七大浪费的现场观察表5、如何“七大浪费”来管控生产练习:企业浪费初步梳理内容精彩度:★★★★☆模块二:5S管理☺培训目的:掌握5S管理的内涵,能推动企业5S的彻底贯彻。
1、什么是5S管理2、5S管理的实战内涵3、5S是如何消除浪费的4、可视化管理的基本技巧5、5S推行:从三个一定到八大接口6、管理者如何更好推进5S工作培训手法:视频、案例、图片、故事、练习内容精彩度:★★★★★模块三:标准作业☺培训目的:掌握以作业指导书为核心的作业标准化技巧。
1、作业标准化的价值2、作业指导书的主要内容及三原则3、制作作业指导书的八个步骤4、如何提升作业标准化水准练习:制作一张作业指导书内容精彩度:★★★★★模块四:TPMTPM是Total Preventive Maintainance缩写,即全员预防性维护。
TPM以5S管理为基础,聚焦于设备的维护。
☺培训目的:掌握推动TPM的基本技能。
1、什么是TPMTPM的价值2、TPM的主要支柱3、推行自主维护的七个步骤4、TPM的案例解析练习:TPM的改善书内容精彩度:★★★★☆模块五:问题解决☺培训目的:掌握问题解决的八个步骤及两个工具。
1、PDCA:问题改善的八个步骤2、问题解决的两个工具◆鱼骨图运用技巧◆五个为什么技巧3、9个五个为什么案例解析4、探讨:如何提升员工发现问题与解决问题的能力练习:鱼骨图与五个为什么的演练内容精彩度:★★★★★模块六:防呆法运用防呆法也叫愚巧法、防错法,日语罗马拼音为Poka-yoke,Poka指人为错误,Yoke是防止错误的意思。
☺培训目的:掌握防呆法的十大原理及运用。
1、防呆法的目的2、防呆法十大原理及案例解析3、工作中的防呆法案例运用4、推行防呆法的步骤5、探讨:身边有什么防呆法的例子?练习:某特定情境下,如何运用防呆手法?内容精彩度:★★★★★模块七:价值流分析价值流图是全局性及全流程的分析工具,通过绘制价值流图,发现存在的浪费及不平衡,从而缩短整个生产周期。
精益生产课程大纲

掌握工厂成本管理实战技巧,为您的企业找到降低生产成本的可行方案。
有效地降低生产成本、提高产品质量;
培训对象
厂长、生产部经理、车间主任,生产主管、质量主管、生产现场一线主管等相关人员
课程大纲
一、精益生产方式
1、精益生产方式简介
2、精益生产方式产生的背景
1、物料管理概述
2、物料的分类
3、物料管理的范围
4、物料管理的5R原则
5、物料管理执行流程
6、欠料对计划与交期的影响,解决对策
7、物料计划管理流程七步骤
分析:采购物料跟催系统分析
讨论:物料源头控制分析表
案例:仓库提前7天实物备料滚动排查
案例:车间提前3天实物领料滚动排查表
七、现场质量控制与改善
1、质量预防成本
(6)进度跟催箱
(7)目视管理看板
(8)推移图
5、生产异常管理
6、紧急订单处理的12种方法
7、少量多样化及其解决的六项措施
8、产销失调及其解决的六项措施
9、生产进度落后及其解决七项措施
10、跨部门生产进度控制七步骤
案例:某企业周异常工时统计表
案例:生产异常改善案例分析
案例:主生产计划员的中午两小时
六、物料计划统筹与物料进度控制
1、成本VS浪费
2、生产现场浪费之源
◆消除浪费的四步骤
◆了解七类浪费
1)纠正错误的浪费
2)过量生产的浪费
3.)物料搬运的浪费
4)动作的浪费
5)等待的浪费
6)库存的浪费
7)过量加工的浪费
讨论:现场浪费的具体现象分析
四、精益柔性计划与产能负荷分析
LCIA课程大纲(1天)

精益生产—LCIA(低成本自动化)课程大纲(6H)培训意义、目标或收益:通过培训,促使相关改善人员掌握低成本自动化的概念、原理及设计理念,学会运用相关的工具进行工厂低成本自动化设计,从而全面管控策划显性、隐形成本控制,保证和提高企业整体经营水平,降本增效,实现利润倍增。
第一章中国制造业现状1、现代制造业面临的困境2、工厂自动化实现的六大步骤第二章低成本自动化概述3、低成本自动化背景、定义4、低成本自动化实施六大条件5、低成本自动化的特点和优势6、低成本自动化的用途7、低成本自动化投资回报第三章低成本自动化设计原则1、低成本自动化设计六大原则2、动作优化3、人机分离4、防错防呆5、异常管理第四章低成本自动化应用1、组装作业简便自动化(12个应用场景)2、机加工简便自动化(12个应用场景)3、搬运简便化(12个应用场景)4、低成本自动化其他术语第五章案例讨论1、某工厂精益产线设计2、公司现场设计自动化●讲师简介:吕宁工业工程教练、精益导师上海跨境电商特约讲师苏州智汇联盟改善专家工业工程背景,专注于工业工程领域及精益生产项目推动。
精通IE,TOC,精益生产等先进的生产模式与管理理论,拥有丰富的工业工程改善及精益项目实施经验,成功推行精益体系。
拥有10多年精益生产项目推行与顾问经验,擅长运用“精益化+自动化+信息化”的落地咨询模式为企业降低成本,提高效率,尤其工艺的自动化改造。
曾任跨国公司500强企业精益运营负责人,全面负责精益生产项目推动、仓库效率提升、物流精益优化。
曾跟随日籍顾问、台湾籍顾问系统学习TPS,拥有丰富扎实的咨询顾问经验。
擅长课程:精益管理系列 IE工业工程实战训练IE改善七大手法生产计划与物料控制TOC项目管理班组长管理技能提升咨询擅长:标准工时体系建立、生产效率提升、生产计划与物流控制、运营体系降本增效、交期周期缩短、信息化自动化导入。
授课风格:丰富的咨询经验和专业的培训技巧,通过生动易懂的故事方式,去拓展学员的思维模式,揭示当下存在的问题及风险;通过案例分析,个人演练小面积讨论等方式进行引导互动,提高学员智慧输出效率,达到解决问题效果;教授的工具和方法奉行简单、实用、有效,并具有可实时性和可操作性。
《精益生产》教学大纲
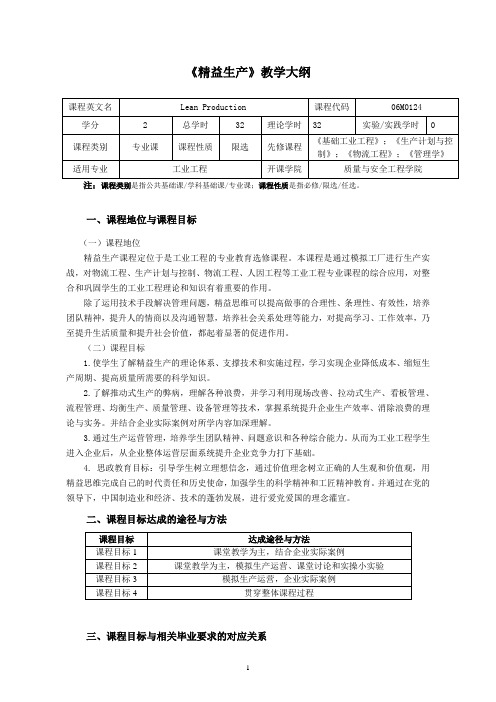
《精益生产》教学大纲注:课程类别是指公共基础课/学科基础课/专业课;课程性质是指必修/限选/任选。
一、课程地位与课程目标(一)课程地位精益生产课程定位于是工业工程的专业教育选修课程。
本课程是通过模拟工厂进行生产实战,对物流工程、生产计划与控制、物流工程、人因工程等工业工程专业课程的综合应用,对整合和巩固学生的工业工程理论和知识有着重要的作用。
除了运用技术手段解决管理问题,精益思维可以提高做事的合理性、条理性、有效性,培养团队精神,提升人的情商以及沟通智慧,培养社会关系处理等能力,对提高学习、工作效率,乃至提升生活质量和提升社会价值,都起着显著的促进作用。
(二)课程目标1.使学生了解精益生产的理论体系、支撑技术和实施过程,学习实现企业降低成本、缩短生产周期、提高质量所需要的科学知识。
2.了解推动式生产的弊病,理解各种浪费,并学习利用现场改善、拉动式生产、看板管理、流程管理、均衡生产、质量管理、设备管理等技术,掌握系统提升企业生产效率、消除浪费的理论与实务。
并结合企业实际案例对所学内容加深理解。
3.通过生产运营管理,培养学生团队精神、问题意识和各种综合能力。
从而为工业工程学生进入企业后,从企业整体运营层面系统提升企业竞争力打下基础。
4.思政教育目标:引导学生树立理想信念,通过价值理念树立正确的人生观和价值观,用精益思维完成自己的时代责任和历史使命,加强学生的科学精神和工匠精神教育。
并通过在党的领导下,中国制造业和经济、技术的蓬勃发展,进行爱党爱国的理念灌宣。
二、课程目标达成的途径与方法三、课程目标与相关毕业要求的对应关系1四、课程主要内容与基本要求第1章概论1.1 精益生产形成1.2 精益生产理念1.3 精益生产体系1.4 背景资料与案例介绍第2章推动式生产2.1 生产方式2.2批量生产方式与MRP2.3 推动式生产演示实验2.4 八大浪费与形成机理第3章精益原则与拉动式生产3.1 精益原则3.2 拉动式生产3.3 拉动式生产演示、实操及讨论3.4 拉动式生产的规则及前提条件第4章价值流图4.1 价值流图概述4.2价值流现状图4.3 价值流未来图4.4 案例介绍4.5 价值流图演练第5章纸飞机生产运营模拟5.1 推动式生产模拟5.2 现场观察与浪费识别5.3 生产改善方案设计及研讨5.4 拉动式生产模拟5.5 生产模拟总结第6章精益布局与精益物流与LCIA6.1 精益布局6.2 精益物流6.3 低成本自动化LCIA第7章均衡化生产与快速换模7.1 均衡化生产概念7.2 总量均衡27.3 品种均衡7.4 快速换模第8章现场管理/TPM/OEE/自働化8.1 现场管理与5S8.2 TMP8.3 OEE8.4 自働化与防错第9章精益生产与智能制造9.1 智能制造与自动化9.2 精益生产在智能制造中的作用五、课程学时安排六、实践环节及基本要求无七、考核方式及成绩评定3八、推荐教材与主要参考书推荐教材:《精益生产》刘叔华,机械工业出版社,2009主要参考书:(美)杰弗瑞·莱克,《丰田模式(实践手册篇):实施丰田4P的实践指南》,机械工业出版社,2012(美)杰弗瑞·莱克,《丰田模式:精益制造的14项管理原则》,机械工业出版社,20114。
精益生产管理工具应用课程大纲
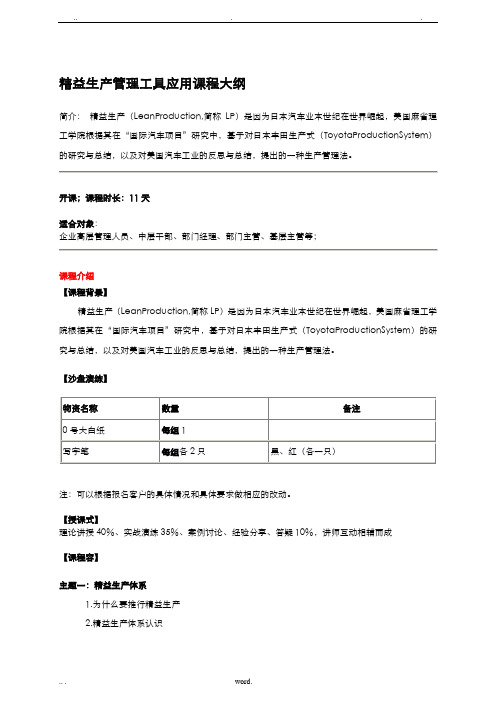
精益生产管理工具应用课程大纲简介:精益生产(LeanProduction,简称LP)是因为日本汽车业本世纪在世界崛起,美国麻省理工学院根据其在“国际汽车项目”研究中,基于对日本丰田生产式(ToyotaProductionSystem)的研究与总结,以及对美国汽车工业的反思与总结,提出的一种生产管理法。
开课;课程时长:11天适合对象:企业高层管理人员、中层干部、部门经理、部门主管、基层主管等;课程介绍【课程背景】精益生产(LeanProduction,简称LP)是因为日本汽车业本世纪在世界崛起,美国麻省理工学院根据其在“国际汽车项目”研究中,基于对日本丰田生产式(ToyotaProductionSystem)的研究与总结,以及对美国汽车工业的反思与总结,提出的一种生产管理法。
【沙盘演练】注:可以根据报名客户的具体情况和具体要求做相应的改动。
【授课式】理论讲授40%、实战演练35%、案例讨论、经验分享、答疑10%,讲师互动相辅而成【课程容】主题一:精益生产体系1.为什么要推行精益生产2.精益生产体系认识3.中国企业实施精益生产的障碍主题二:精益生产工具之一:5S管理1.现代企业5S推行误区2.现代5S活动推行步骤3.现代5S活动的开展实战指导4.实例分享:5S推行图片展示主题三:精益生产工具之二:现场定置管理1.建立地址系统定置管理3要素与定置状态2.现代定置实施原则3.定置画线秘笈4.三要点和三定认识5.定置容的几项原则主题四:精益生产工具之三:问题分析5Y法应用1.认识信息和原因2.找问题根源3.实例分享:杰佛逊纪念大厦的墙面保护计划4.5y分析演练--为活塞动作迟缓5.其他常用找问题与系统解决的法了解主题五:精益生产工具之四:精益设备的TPM活动1.如计划和实施TPM工作2.自主保全TPM与零故障3.实例分享:照片欣赏4.精益设备的选择主题六:精益生产工具之五:PDCA管理循环与ECRS法1.PDCA管理循环了解与应用2.ECRS法了解与应用主题七:精益生产工具之六:流程式布局1.U型生产线与单件流2.流线化生产的设计原则、要点3.柔性单元生产的实施4.实例分享:VCD欣赏5.单件及小批量物流6.实现一笔画生产7.案例讲解:某大型工厂装配线主题八:精益生产工具之七:作业标准化1.标准化作业正确认识2.区分标准化和非标准化作业3.实例分享:VCD欣赏4.案例:数据收集5.生产节拍、作业顺序、标准在制品运用6.标准化作业实施法主题九:精益生产工具之八:多能工与多工序操作1.员工多技能2.OPL教育3.实施一人多机4.实例分享:VCD欣赏5.如实现多工序操作6.动作经济原则主题十:精益生产工具之九:精益质量安定管理1.零缺陷2.品质安定与零不良原则3.品质中的“六个三”4.客户导向的品质目标管理5.全员质量意识再造与控制6.六西格玛的认识主题十一:精益生产工具之十:可视化管理1.可视化管理12中法的应用2看板在不同企业现场中的应用主题十二:精益生产工具之十一:快速换模1.快速切换的法和原则2.快速切换的改善着眼点及思路3.快速切换的实施法则4.SMED的实施技巧主题十三:精益生产工具之十二:平稳化生产1.平稳化生产计划制定2.生产计划安排原则3.生产进度随时掌控4.平稳化生产的技巧主题十四:精益生产工具之十三:自动化(jidoka)生产1.实现jidoka的三个手段2.jidoka的有效工具制度3.快速处理问题系统主题十五:精益生产工具之十四:防错、防误、防呆1.防错、防误、防呆认识2.改善的原则主题十六:精益生产工具之十五:工序平衡1.查找和分析生产瓶颈2.生产的均衡化3.建立并应用生产工序标准化系统4.生产的同期化5.准时化生产过程的一个流6.实例分享:VCD欣赏主题十七:精益生产工具之十六:价值流图分析1.价值流图分析认识2.如推行价值流图主题十八:精益生产实施的步骤1.点-线-面-链推进式2.追求变革全员参与3.激励渐进自动自发主题十九:课程回顾【鹏老师简介】讲师资历◇ 市生产师资团队成员◇ 中国制造型企业成本研究中心主任◇ 日本TPM项目株式会社研究院院长◇ 市中小型企业发展研究会副主任◇ 中国企业专题项目辅导研究所发起人◇ 清华、北大、交大、华科等大学特聘讲师实践/学术背景理光(日资)工业发展有限公司理光系制造部、改善推进部部长及TPM技术总监中国有色金属工业第六冶金建设公司工程师、厂长市福禧达实业有限公司总经理万基药业有限公司生产运营总监、精益生产咨询项目总监工程学院工程管理硕士,日本Japanese Graduate School博士。
精益生产课程教学大纲

《精益生产》课程教学大纲课程代码:010342002课程英文名称:Lean Production课程总学时:24 讲课:24 实验:0 上机:0适用专业:工业工程专业大纲编写(修订)时间:2017.7一、大纲使用说明(一)课程的地位及教学目标精益生产是工业工程专业开设的一门专业课,是当前工业界最佳的一种生产组织体系和方式。
本课程的教学目的是使学生掌握精益生产的基本分析理论和方法,并能灵活运用于实际生产管理系统,培养学生精益生产的理论水准和从事精益生产管理基本能力。
(二)知识、能力及技能方面的基本要求通过本门课程的学习,学生应了解精益生产的基本概念、基本理论和方法,掌握准时化生产、看板管理、均衡化生产、连续流生产、TPM、价值流图等基本方法,熟悉各种具体管理方法在生产管理系统中的应用方法。
培养学生正确分析、改进企业生产管理系统中实际问题的能力。
(三)实施说明1.精益生产是21世纪制造业的先进生产方式,内容广泛。
教学过程中可采用采用启发式的教学方式,教师讲解与学生自学结合、课堂教学与案例分析结合等的多种教学方方法,适当组织学生到大型企业参观,进行现场教学以扩大学生的知识面。
2. 教学手段采用多媒体与板书结合的形式,突出重点,在有限学时条件下使学生掌握精益生产的核心理论和方法,力求学生在分析问题和解决问题的能力上有一定的提高。
3. 执行本大纲过程中,随着学科的发展、实际情况和教学的需要,可以适当调整。
(四)对先修课的要求基础工业工程,生产计划与控制(五)对习题课、实践环节的要求根据章节内容,可以安排适量作业,多进行案例分析与讨论。
(六)课程考核方式1.考核方式:考查2.考核目标:考查学生对精益生产核心方法的掌握以及综合运用的能力。
3.成绩构成:通过案例分析、课后作业、论文等考查方式检验学生对知识的理解运用情况,总成绩综合考虑大作业或论文,课堂发言、出勤及作业情况。
平时成绩占40%,期末成绩占60%。
(七)参考书目《精益生产》,刘树华,鲁建厦,王家尧著.机械工业出版社,2010.1《精益生产实务》,乔毅.机械工业出版社,2016.7《精益生产》,吴迪,清华大学出版社,2016.6二、中文摘要精益生产是工业工程专业的一门专业课程。
精益生产及精益工具大纲(分享)

分享【培训大纲】精益生产第一单元精益生产基础篇企业自评表●企业的运营目的与获得利润的两手法:①降低成本②提高生产效率●精益生产起源①丰田生产方式起源②精益生产系统起源③丰田生产方式与精益生产系统●精益思想①成本每降低10%,等于经营规模扩大一倍②成本可以无限下降(改善无止境)③成本取决于制造的方法④工人动作到处都存在浪费现象●丰田生产方式的特征——消除浪费①工厂中的七大浪费制造过剩的浪费等待的浪费搬运的浪费加工的浪费库存的浪费动作的浪费生产不良品的浪费②浪费的源头制造过剩的浪费人员过多的浪费●精益生产方式两大支柱——自働化和准时化①自働化②准时化③丰田屋案例研究模拟游戏1:推动-流动-拉动(观察小结)第二单元精益生产工具篇●工具一:5S——现场改善基础①5S真经③工作场地有序安排(录像)●工具二:目视化管理(Visual Management)①周期性信息展示②3M的实时监控③基于“三现主义”的异常管理④目视化管理(录像)●工具三:问题解决①5Why③快速响应异常管理六要素●工具四:全员生产维护(TPM)①TPM的概念和目的②五大对策和八大策略③自主维护保养的七个层次④TPM实施的十大步骤●工具五:标准化作业①准作业条件②标准作业三要素(TT, WS,SWIP)●工具六:现场改善-Kaizen①改善步骤②改善ECRS手法③改善突破法—现场改善的利器(录像)●工具七:防错(Pokayoke)①追求零缺陷②品质三不政策③自働化三原则●工具八:看板(Kanban)①看板的种类与工作原理②看板的实施前提③看板六原则●工具九:快速换模(SMED原理)①明确划分内外部因素②将内部因素转化成外部因素③理顺留下的内部因素④理顺所有外部因素⑤使用工件更换器(快速夹紧装置或完全去除夹紧装置)⑥进行平行作业⑦去除调整/校准过程●工具十:价值流图析(Value Stream Mapping)①确定产品系列②现状图绘制③未来状态图绘制④计划与实施案例研究模拟游戏2:推动-流动-拉动(观察小结)第三单元精益生产总结篇●精益改善失败原因●精益改善-终身之旅①精益改善路线图②精益改善的顺序③精益改善的合理化建议④精益改善实施绩效指标⑤精益企业4项基本标准⑥精益企业5项基本特征案例研究模拟游戏3:推动-流动-拉动(观察小结)精益工具一:5S-工作场地有序安排第一部分5S基础篇一、现场5S改善科学推行二、现场管理与市场意识三、5S推行关系与成效四、5S活动原则与误区五、生产经理心智修炼六、建立最优素质模型七、专业能力与管理提升八、5S管理技巧分享第二部分5S推进篇一、整理推进快刀斩乱麻二、倡导提领法则三、整理不良的对策与分析四、整顿的推进重点五、目视化定置管理六、动作经济原则七、彻底杜绝污染源八、点检与点检通道优化九、清洁的最有效推进十、制度与标准化模型建立十一、修养的推进重点十二、标杆推进十三、团队作战十四、责任重于泰山十五、常见不安全现状与行为分析第三部分5S方法篇一、现场可视化管理要点二、3级标准管理方法三、可视化的合理分类四、颜色管理与视觉原理五、企业文化与基础设施六、看板管理三大要素七、识别管理大全八、识别与形迹管理第四部分5S督导篇一、建立5S推行组织二、拟定推进方针和目标三、拟定计划和实施方法四、5S推行过程五、样板区的选择与总结推广六、5S绩效考核七、确定评比方法八、5S纠正与预防第五部分持续改进篇一、5S推进中易存在问题二、问题意识与五现手法三、PDCA与SDCA递进四、改善与创新五、日常管理与改善六、激发创新思维七、标准化八、防错法九、提案改善活动第六部分5S延伸篇一、5S与制造业精益生产LP模式二、5S与设备维护管理TPM的推行三、办公室5S四、文件5S五、会议5S六、5S问与答精益工具二:目视化管理第一部分目视化管理1.什么是目视控制2.目视化管理的定义和作用3.目视化Vs. 目视化管理4.案例:目视化管理第二部分目视化管理的实施步骤5.练习活动:目视化管理第三部分目视化管理的应用精益工具三:问题解决一、如何看待问题二、什么是问题?三、问题的类别四、如何发现问题5why分析方法五、问题解决的步骤PDCA循环六、快速响应异常管理六要素精益工具四:全员生产维护第一模块、TPM基础篇1. TPM的起源和定义2. TPM的历史沿革3. TPM在设备维护体制中的定位①TPM现场设备管理自主维修②全系统生产维修体制4. TPM的3个“全”①总体全效率(盈利能力)②设备一生的全维护系统③全员参与5. 人员在TPM中所要起的作用①使零停机成为现实②消除浪费源③提高操作技能,增加机器的性能6. TPM的5大支柱①最高设备综合效率②全系统预防维修③所有部门全体参加④从领导到每个员工⑤小组活动动机管理7. 开展TPM的意义第二模块、TPM准备篇1. TPM的目标2. 如何识别生产设备性能①跟踪七种设备浪费的方法②综合设备效率计算(OEE)③设备使用率④人工效率计算⑤合格品率计算⑥企业中的21种损失(LOSS)3. 课堂练习第三模块、TPM震撼新解篇1 1. 新一代TPM 给企业带来变革的启示①淡化分工,专业覆盖,工作边界模糊化②从岗位分工报酬制走向能力报酬制③企业凝聚力和企业文化作用巨大④充分发挥教育培训功能,建设学习型和教育型组织⑤新团队精神的发挥2. TPM 定义新解①全面效益管理②全面生产管理③全面完美生产④全面生产维护与管理3. TPM 五大支柱新解①综合效益最大化②寿命周期损失最小化③横向全员:所有部门参与④纵向全员:从上至下投入⑤小组活动:TPM的基础和细胞4. TPM和TQM,JIT,ISO的关系TQM:设备是质量的保障JIT:零库存要全员控制TPM:设备保障体系ISO:需要深入细化的执行5. 安全与全员生产维护6. 换型改善流程步骤①区分外部和内部换型②内部换型外部化③缩短内部换型时间④改善外部换型,缩短总时间⑤改善后)内部、外部换型作业标准化,确保在规制时间内完成内部换型7. 五个基本的改善领域①通过消除六大浪费来提高设备效率(团队完成)②建立维护小团队(遵循七步法)③质量保证④维护部门制定维护计划⑤通过教育训练提高技能水平8. 五大对策①维护良好规范的基本条件②遵循适用的操作程序③复原坏旧设备④明确和改进设计问题⑤提高操作和维护技能第四模块、TPM实施篇1. TPM推进的三阶段①准备发动阶段——创造适宜的环境,概念开发,人员培训,全面发动②落实推进阶段——制订目标,建立组织,制订计划,难题解决,创造榜样③评价改进阶段——制定标准,检查评估,找出不足,改进提高。
精益生产课程教学大纲

《精益生产》课程教学大纲课程代码:010342002课程英文名称:Lean Production课程总学时:24 讲课:24 实验:0 上机:0适用专业:工业工程专业大纲编写(修订)时间:2017.7一、大纲使用说明(一)课程的地位及教学目标精益生产是工业工程专业开设的一门专业课,是当前工业界最佳的一种生产组织体系和方式。
本课程的教学目的是使学生掌握精益生产的基本分析理论和方法,并能灵活运用于实际生产管理系统,培养学生精益生产的理论水准和从事精益生产管理基本能力。
(二)知识、能力及技能方面的基本要求通过本门课程的学习,学生应了解精益生产的基本概念、基本理论和方法,掌握准时化生产、看板管理、均衡化生产、连续流生产、TPM、价值流图等基本方法,熟悉各种具体管理方法在生产管理系统中的应用方法。
培养学生正确分析、改进企业生产管理系统中实际问题的能力。
(三)实施说明1.精益生产是21世纪制造业的先进生产方式,内容广泛。
教学过程中可采用采用启发式的教学方式,教师讲解与学生自学结合、课堂教学与案例分析结合等的多种教学方方法,适当组织学生到大型企业参观,进行现场教学以扩大学生的知识面。
2. 教学手段采用多媒体与板书结合的形式,突出重点,在有限学时条件下使学生掌握精益生产的核心理论和方法,力求学生在分析问题和解决问题的能力上有一定的提高。
3. 执行本大纲过程中,随着学科的发展、实际情况和教学的需要,可以适当调整。
(四)对先修课的要求基础工业工程,生产计划与控制(五)对习题课、实践环节的要求根据章节内容,可以安排适量作业,多进行案例分析与讨论。
(六)课程考核方式1.考核方式:考查2.考核目标:考查学生对精益生产核心方法的掌握以及综合运用的能力。
3.成绩构成:通过案例分析、课后作业、论文等考查方式检验学生对知识的理解运用情况,总成绩综合考虑大作业或论文,课堂发言、出勤及作业情况。
平时成绩占40%,期末成绩占60%。
(七)参考书目《精益生产》,刘树华,鲁建厦,王家尧著.机械工业出版社,2010.1《精益生产实务》,乔毅.机械工业出版社,2016.7《精益生产》,吴迪,清华大学出版社,2016.6二、中文摘要精益生产是工业工程专业的一门专业课程。
- 1、下载文档前请自行甄别文档内容的完整性,平台不提供额外的编辑、内容补充、找答案等附加服务。
- 2、"仅部分预览"的文档,不可在线预览部分如存在完整性等问题,可反馈申请退款(可完整预览的文档不适用该条件!)。
- 3、如文档侵犯您的权益,请联系客服反馈,我们会尽快为您处理(人工客服工作时间:9:00-18:30)。
精益生产课程大纲天 Document serial number【KKGB-LBS98YT-BS8CB-BSUT-BST108】
精益生产培训
课程大纲(2天、12H)
课程目的:
通过培训,本课程在系统地介绍精益生产的理念、方法和工具的同时,重点引入了一个系统的全景式的沙盘演练,把抽象的精益生产理念和方法以实战的方式模拟出来,包括节拍生产(TaktTime)、单件流(Onepieceflow)、拉动式生产(Pullproduction)、七大浪费(7wastes)等,让参与者在参与中综合应用和深刻体会精益生产的理念、方法和工具,并通过持续改善清晰的体现精益生产变革带来的巨大效益。
同时,针对企业在实施精益生产的流程和关键要素,本课程也提供了一些有效的指引,最后,本课程还为您分享大量的精益生产推进活动和改善案例,帮助您找到一些适合本企业的变革和推行方法,促使相关改善人员掌握精益生产的概念、原理及理念,学会运用相关的工具进行工厂改善,从而全面管控成本,保证和提高企业整体经营水平,降本增效,实现利润倍增。
课程收益:
通过本课程的学习,不仅能让您系统地、深刻地理解和体会精益的理念、方法和工具,还能助您找到适合的精益的导入和推行的实践经验及有效方法。
如果您是企业的经营者和管理者,将为您呈现构建企业核心竞争力途径;
如果您是精益倡导者和推行者,将为您系统介绍推行精益生产的思路与阶梯;
如果您是精益的实施人和参与人,将为您提供组织精益改善的流程和方法;
如果您在推行过程中碰到困难和疑惑,将与您分享精益推行过程中克服障碍和阻力的经验和心得;
或许您觉得缺乏推行精益改善的技术和工具,将为您展示精益生产最有效的工具和方法;
第一章精益生产概论
1,现代企业经营基本理念
2,精益生产总体介绍与基本逻辑关系(精益起源,精益与IE的关系)
3,精益生产的五大原则(价值,价值流,流动,拉动,持续改善)
4,价值的概念及工作时间分析(通过饼图来展示有价值的工作时间)
5,七大浪费定义及适用条件(七大浪费的逻辑关系及案例展示)
6,七大浪费意识与因果关系
7,精益思想十二模式与深度认知(精益与正常公司的试点不同)
8,精益管理体系系统认知(精益到底是什么)
9,
10,
11,讨论:人为什么会拒绝改变(视频+案例分析)
第二章精益生产工具运用及案例分析
1,通过VSM价值流程图进行重大改善(某医疗企业案例分析)
2,精益布局与单元化生产(某医疗企业布局优化)
3,人机联合作业分析(某机加工企业案例分析)
4,标准作业的目的与意义(标准工时+动作分析)
5,现场5S与目视化管理(五百强企业案例展示)
6,品质管理三不原则及系统解决方案(某企业交期不稳定案例分析)
7,防呆十大原则及解决案例分析(案例展示)
8,快速换模及案例分析(某机加工企业案例展示与视频分享)
9,工序平衡分析与案例分析(某家电企业案例分析)
10,讨论:公司目前适用哪几个工具?(针对公司存在的问题进行现场指导)第三章持续改善
1,改善与革新的差别(意识上认知)
2,何谓改善工作小组与其目的
3,改善工作小组的架构(某企业组织架构分享)
4,改善工作组的形成流程
5,改善工作组的参与提案(某企业成功案例分享)
6,改善工作参与PDCA
7,建立以标准工时为基准的数据改善体系(数据化,信息化)
第四章课后讨论
针对某位学员提出的问题,进行系统性的研讨与总结讲师简介:
吕宁
工业工程教练、精益导师
管理公司高级顾问
苏州智汇联盟改善专家
AQA特约讲师
工业工程专业本科,专注于工业工程领域及精益生产项目推动。
精通IE,精益生产等先进的生产模式与管理理论,拥有丰富的工业工程改善及精益项目实施经验,成功推行精益体系。
拥有10多年精益生产项目推行与顾问经验,擅长运用“精益化+自动化+信息化”的落地咨询模式为企业降低成本,提高效率,尤其工艺的自动化改造。
曾任跨国公司500强企业精益运营负责人,全面负责精益生产项目推动、仓库效率提升、物流精益优化。
曾跟随日籍顾问、台湾籍顾问系统学习TPS,拥有丰富扎实的咨询顾问经验。
擅长课程:
精益管理系列 IE工业工程实战训练
IE改善七大手法生产计划与物料控制
TOC项目管理 VSM实战技术
咨询擅长:
标准工时体系建立、生产效率提升、生产计划与物流控制、
运营体系降本增效、交期周期缩短、信息化自动化导入。
授课风格:
丰富的咨询经验和专业的培训技巧,通过生动易懂的故事方式,去拓展学员的思维模式,揭示当下存在的问题及风险;
通过案例分析,个人演练小面积讨论等方式进行引导互动,提高学员智慧输出效率,达到解决问题效果;
教授的工具和方法奉行简单、实用、有效,并具有可实时性和可操作性。
讲课培训客户:
中华华能电力、中植新能源集团、成都一汽客车、烟台舒驰客车、振华机械江阴公司、振华机械南通公司、徕木电子、苏州方位包装、正源集团、友容自动化、广尔纳科技、爱迪士净化设备、赫励机械设备、文光集团、国芯科技、思凯路服饰、上海众力汽车零部件、胜利精密、富翔塑胶、贤坤物流、零点精密机械、同力塑胶、乐得鑫
精密、务实五金、菩提树五金、诚立无尘布、博飞光学、中创铝业、利奇、黑森林、
浙江舒友医疗器械、上海衡元、上海速益、苏州蔓莎、苏州云白环境、上海富新压
铸、苏州讯卓包装、汉得利电子股份有限公司、常州协鑫光伏科技、常州数控技术、
黑牡丹纺织、江苏雷利电机、常州华威电子、常柴股份、新誉轨道交通、新誉集团、
常州东风农机集团、常州灵特尔轻便展示系统、新阳科技集团、南京LG集团、苏州
维嘉电子、村上精密制版,苏州黑猫集团,其他客户不一一展现
节省50%仓库空间
库存从300万降低到170万
建立标杆5S车间
装配车间生产效率提升57.6%
建立标杆5S车间
冲压车间生产周期缩短48.3%
建立标准工时
生产效率提升最低27%,最高64%
2个月生产效率平均提升30%
改变工艺并导入新技术与自动化设备效率提升
100%
生产效率提升30%
生产周期缩短40%。