连续冲压模具设计流程
冲压模具设计全套步骤和流程

冲压模具设计全套步骤和流程1.零件设计:根据产品的功能要求和外观要求,进行零件的设计。
确定零件的几何形状、尺寸和所需的表面质量等。
2.材料选择:根据零件的要求和产品的使用环境,选择合适的材料。
考虑材料的强度、塑性和可加工性等因素。
3.模具结构设计:根据零件的几何形状和加工要求,设计模具的结构。
包括模具的底座、上模、下模、模具导向装置、顶针等部分。
4.模具零件设计:根据模具结构设计的要求,对模具的各个零部件进行设计。
包括模具的滑块、顶出装置、顶出销等。
5.模具总成设计:将各个模具零件组装成一个整体。
进行模具总成的设计,确定各个模具零件的安装位置、尺寸等。
6.模具加工工艺设计:根据模具结构和零件的加工要求,设计模具的加工工艺。
包括模具的加工工艺路线、加工顺序、机床设备等。
7.模具调试和试产:根据模具的设计和加工工艺,进行模具的组装和调试。
包括模具的调试、调整、测试以及初次试产。
根据试产结果,对模具进行优化和改进。
8.模具使用和维护:对模具进行使用和维护。
包括模具的防护、清洁、润滑和定期维护等。
9.模具性能评价:对模具进行性能评价。
包括模具的使用寿命、生产效率、加工精度等方面的评价。
10.模具改进和更新:根据使用中的问题和需求,对模具进行改进和更新。
包括模具的结构改进、材料选择和加工工艺的优化等。
以上是冲压模具设计的全套步骤和流程。
在进行设计的过程中,需要考虑零件的功能要求、材料的选择、模具的结构设计、加工工艺的确定等因素。
通过设计和优化,能够获得满足产品要求的冲压模具,提高生产效率和产品质量。
冲压模具设计流程

冲压模具设计流程1.产品分析和要求确认:首先需要对待冲压产品进行全面分析,包括产品的形状、材料、尺寸和工艺要求等。
同时与客户确认产品设计要求和特殊要求,以便在设计过程中有针对性地处理和解决问题。
2.毛坯设计和计算:在确认产品的形状和尺寸之后,需要设计模具的毛坯,在图纸上绘制出冷却模和顶杆模的轮廓。
对模具的毛坯材料及尺寸进行计算,确保在制作模具时有足够的材料和加工余量。
3.毛坯加工:根据毛坯的设计和计算结果,进行模具的毛坯制作。
这包括焊接加工、机械加工、热处理等过程,确保模具的材质和强度满足要求。
4.模具结构设计:根据产品的特点和要求,设计模具的结构,并进行相关计算和分析。
模具结构设计包括顶杆、导向柱、滑块等部件的大小、形状和材料选择。
5.零件设计和加工:模具的主要部件包括上模、下模和顶模。
根据模具结构设计的结果,设计和绘制相关模具零件的详细图纸。
然后进行零件的加工,包括铣削、切割、打孔、线切割等。
6.模具装配和调试:根据模具零件的加工完成情况,进行模具的装配。
在装配过程中需要保证模具的精度、配合度和可靠性。
装配完成后,进行模具的调试和试模,评估模具的功能和使用性能。
7.模具维护:在模具的使用过程中,需要进行定期的维护和保养。
这包括模具表面的清洁、润滑剂的加注、模具零件的更换等。
维护模具可以延长模具的使用寿命,保证模具的加工质量和精度。
8.问题分析和改进:在模具实际使用过程中,可能会出现一些问题或者需要改进的地方。
需要对问题进行分析,找出根本原因,并提出相应的改进措施。
这有助于提高模具的使用效率和加工质量。
总结起来,冲压模具设计流程包括产品分析、毛坯设计和计算、毛坯加工、模具结构设计、零件设计和加工、模具装配和调试、模具维护以及问题分析和改进等步骤。
不同的产品和要求可能会有些差异,但基本的流程是相似的。
通过合理的设计和精确的加工,可以保证冲压模具的质量和性能,提高生产效率和产品质量。
冲压模具流程
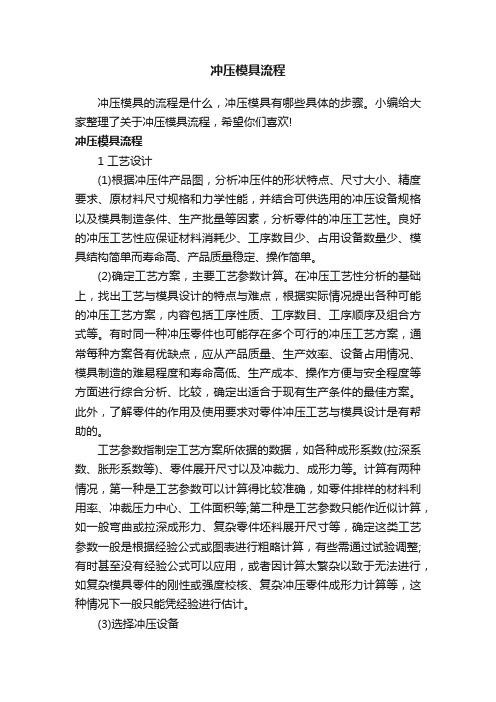
冲压模具流程冲压模具的流程是什么,冲压模具有哪些具体的步骤。
小编给大家整理了关于冲压模具流程,希望你们喜欢!冲压模具流程1 工艺设计(1)根据冲压件产品图,分析冲压件的形状特点、尺寸大小、精度要求、原材料尺寸规格和力学性能,并结合可供选用的冲压设备规格以及模具制造条件、生产批量等因素,分析零件的冲压工艺性。
良好的冲压工艺性应保证材料消耗少、工序数目少、占用设备数量少、模具结构简单而寿命高、产品质量稳定、操作简单。
(2)确定工艺方案,主要工艺参数计算。
在冲压工艺性分析的基础上,找出工艺与模具设计的特点与难点,根据实际情况提出各种可能的冲压工艺方案,内容包括工序性质、工序数目、工序顺序及组合方式等。
有时同一种冲压零件也可能存在多个可行的冲压工艺方案,通常每种方案各有优缺点,应从产品质量、生产效率、设备占用情况、模具制造的难易程度和寿命高低、生产成本、操作方便与安全程度等方面进行综合分析、比较,确定出适合于现有生产条件的最佳方案。
此外,了解零件的作用及使用要求对零件冲压工艺与模具设计是有帮助的。
工艺参数指制定工艺方案所依据的数据,如各种成形系数(拉深系数、胀形系数等)、零件展开尺寸以及冲裁力、成形力等。
计算有两种情况,第一种是工艺参数可以计算得比较准确,如零件排样的材料利用率、冲裁压力中心、工件面积等;第二种是工艺参数只能作近似计算,如一般弯曲或拉深成形力、复杂零件坯料展开尺寸等,确定这类工艺参数一般是根据经验公式或图表进行粗略计算,有些需通过试验调整;有时甚至没有经验公式可以应用,或者因计算太繁杂以致于无法进行,如复杂模具零件的刚性或强度校核、复杂冲压零件成形力计算等,这种情况下一般只能凭经验进行估计。
(3)选择冲压设备根据要完成的冲压工序性质和各种冲压设备的力能特点,考虑冲压加工所需的变形力、变形功及模具闭合高度和轮廓尺寸的大小等主要因素,结合工厂现有设备情况来合理选定设备类型和吨位。
常用冲压设备有曲柄压力机、液压机等,其中曲柄压力机应用最广。
冲压模具设计

冲压模具设计一、冲压模具设计的步骤1.确定需求:首先要明确冲压件的形状、尺寸和质量要求,以及加工工艺的要求,包括材料选材、工艺流程等。
2.分析冲压过程:了解冲压过程中的受力情况,确定冲压件的受力情况,考虑冲压件的结构和形状。
分析完成后,可以确定模具的结构和工作原理。
3.制定设计方案:设计方案是根据需求和分析决策,形成的模具设计的主要思路,包括模具的结构形式、材料选材、零件加工工艺等。
4.细化设计:在设计方案的基础上,进一步细化设计,包括每个零件的尺寸、形状和工艺要求,确保每个零件都符合设计要求。
5.制作样品:制作模具样品,进行试验和调试,验证设计方案的可行性,确定调整和改进方案。
6.定稿设计:根据试验结果,对设计方案进行调整和优化,形成最终的设计方案。
二、冲压模具设计的关键要点1.良好的受力结构:冲压模具在工作过程中要经受巨大的冲击力和挤压力,因此必须具备良好的受力结构,包括合理的分布受力、合理的受力传递和合理的受力集中。
2.优秀的耐磨材料:冲压模具的工作环境往往十分恶劣,耐磨材料可以大大延长模具的使用寿命,提高生产效率。
3.精密的加工工艺:冲压模具的加工精度直接影响到冲压件的质量,因此必须采用精密的加工工艺,确保模具的精密度和可靠性。
4.优化的结构设计:冲压模具的结构设计要尽可能简单,降低成本,提高生产效率。
同时也要考虑模具的易维护性,方便维修和更换零件。
5.可靠的试验与调试:为了保证冲压模具的质量和可靠性,必须进行全面的试验和调试,包括模具的运行测试、冲压件的检测评价等。
三、结语冲压模具设计是一个复杂而细致的工程,需要综合运用材料学、结构设计、机械加工、模具试验等多方面的知识。
只有具备扎实的理论基础和丰富的实践经验,才能设计出高质量的冲压模具。
希望以上内容对冲压模具设计有所帮助,能够指导相关行业的人士更好地进行冲压模具设计工作。
冲压模具设计是一个复杂的过程,需要设计人员深入且全面地了解冲压工艺、材料特性、机械结构、模具加工工艺等多方面知识,并且需要经验丰富的工程师进行设计。
冲压模具设计流程

冲压模具设计流程冲压模具设计是制造金属零件的常用工艺之一,它通过对金属材料进行连续冲击和变形,将原材料转变为所需形状的零件。
冲压模具设计的流程包括以下几个步骤。
第一步,确定产品需求。
在冲压模具设计的初期,需要明确产品的材料、尺寸、形状等需求。
这一步通常由产品设计师完成,并与冲压模具设计师进行沟通,确保设计方向一致。
第二步,分析产品特点。
冲压模具设计师需要仔细分析产品的特点,包括壁厚、曲线等,以确定冲压工艺和模具设计方案。
根据产品特点,冲压模具设计师可以选择合适的冲击力和变形方式。
第三步,制定产品工艺。
冲压模具设计师需要制定详细的产品工艺流程,包括冲孔、低速冲击、弯曲等。
同时,需要考虑产品数量,确定合适的冲压模具设计方案,以提高生产效率和产品质量。
第四步,构思模具结构。
在确定产品工艺流程后,冲压模具设计师开始构思模具结构。
首先,需要确定零件分割方式,将整个产品分割为几个零部件。
然后,设计模具结构,包括上下模、剪切边、凸包等。
第五步,绘制模具图纸。
在构思模具结构后,冲压模具设计师开始绘制模具的详细图纸。
图纸包括正视图、俯视图、侧视图等,以及各个零部件的放样图、工艺图等。
这些图纸是模具加工和制造的依据。
第六步,选择材料和制造方式。
根据模具的要求和图纸,冲压模具设计师需要选择合适的材料和制造方式。
常用的模具材料包括工具钢、硬质合金等,制造方式包括数控加工、数控铣削等。
第七步,模具试产和调试。
一旦模具制造完成,就可以进行模具试产和调试。
试产时,需要进行模具的安装、调整和操作。
通过试产和调试,可以检查模具是否满足产品要求,是否存在问题,并进行改进。
第八步,模具验收和优化。
最后,需要对模具进行验收和优化。
验收包括外观检查、尺寸检查等。
如果模具存在问题,需要及时进行调整和优化,以确保模具能够正常使用。
冲压模具设计流程是一个复杂的过程,需要冲压模具设计师具备丰富的经验和技能。
通过以上几个步骤的综合应用,可以设计出高效、精确的冲压模具,提高生产效率和产品质量。
冲压工艺及模具设计

冲压工艺及模具设计冲压工艺及模具设计是现代工业制造中常用的一种技术,它通过将金属板材或者其他形状的金属件置于模具中,然后通过冲压机的动作使得金属材料发生塑性变形以得到所需的形状和尺寸。
冲压工艺及模具设计是一门综合性强的工艺技术,以下将介绍其包括冲压工艺流程、模具设计原则、模具结构设计、模具构件选用等相关内容。
一、冲压工艺流程冲压工艺分为单道冲压和多道冲压两种。
单道冲压是指在一个冲压过程中完成产品的全体造型,多道冲压是指通过多次冲压工艺来完成产品的全体造型。
下面将以多道冲压为例介绍冲压工艺流程。
1.材料准备:选择合适的板材材料,进行剪切、铺料等准备工作。
2.模具设计:根据产品的形状和尺寸要求,设计合适的冲压模具。
3.上料:将材料板厚按照模具规格要求剪切成对应尺寸,然后放置在模具上。
4.开模:通过冲压机的动作,使得模具上的凸模与凹模对压,使材料发生塑性变形。
5.去杂及模具保养:在冲压过程中会产生一些杂质,需要及时清理,并对模具进行保养和维护。
二、模具设计原则模具设计是冲压工艺的核心环节,它直接影响着产品的质量和成本。
在进行模具设计时,需要遵循以下原则:1.合理性原则:模具结构要合理,能够满足产品的形状和尺寸要求,并且易于加工和调整。
2.稳定性原则:模具要具有足够的刚性和稳定性,能够承受冲压机的冲击力和振动。
3.高效原则:模具设计要考虑工作效率,设计出能够实现快速冲压的模具结构。
4.经济原则:模具的设计和制造成本要较低,以降低产品的制造成本。
三、模具结构设计模具的结构设计是模具设计的重要环节,它包括模具的整体结构、分段结构、导向结构等。
下面将介绍常用的模具结构设计方法:1.整体结构设计:将模具设计为一个整体结构,具有较好的刚性和稳定性。
2.分段结构设计:根据产品的形状和尺寸要求,将模具分为多个部分,通过连接件进行连接。
3.导向结构设计:模具需要具有良好的导向性,避免材料在冲压过程中发生歪斜和偏移。
4.其他辅助结构设计:模具还需要考虑各种辅助结构,如剪断边缘结构、定位结构、脱模结构等。
冲压模具开发流程

冲压模具开发流程1.产品需求分析和设计:首先,对于需要冲压的零部件,需要进行需求分析并确定产品的设计要求。
根据产品的形状、尺寸以及数量要求,制定相应的设计方案。
2.模具设计:根据产品设计方案,进行模具的设计。
包括三维模型设计、结构设计、模具零部件设计等。
模具的设计要满足产品要求,并且考虑到材料的选择、加工工艺等因素。
3.模具制造:在完成模具设计后,需要进行模具的制造。
包括模具标准件的采购、非标准件的加工以及模具的组装等。
制造过程中需要进行严格的质量控制和检测,以确保模具的质量。
4.模具调试:在模具制造完成后,需要进行模具的调试。
包括模具零部件的配合检查、模具操作的检验、以及产品的抽样试模等。
通过调试,可以确保模具的正常运行,并达到产品设计要求。
5.试产和修正:在模具调试过程中,进行初步的试产。
通过试产可以发现模具存在的问题,并进行修正。
包括模具结构的改进、零部件的更换等。
通过多次试产和修正,最终达到满足产品质量要求的模具。
6.批量生产:在完成模具的调试和修正后,进行批量生产。
根据客户的需求,进行大批量的产品生产。
生产过程中需要进行质量控制和检测,以确保产品的质量稳定。
7.模具维护和改进:在模具的使用过程中,需要进行定期的维护和保养。
包括模具的清洁、零部件的更换等。
同时,根据客户反馈和产品要求的变化,进行模具的改进和升级。
总结起来,冲压模具开发流程包括产品需求分析和设计、模具设计、模具制造、模具调试、试产和修正、批量生产以及模具维护和改进等环节。
在每个环节中,需要进行严格的质量控制和检测,以确保模具和产品的质量。
冲压模具开发流程的顺利进行,能够为企业提供优质的零部件,提高生产效率和产品质量。
冲压模具结构连续模步骤(设计标准)
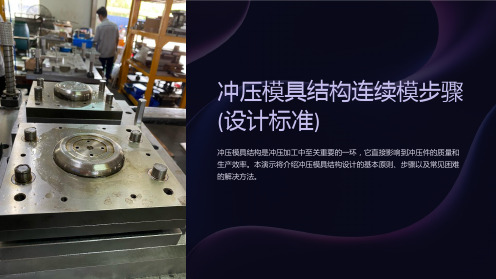
设计方案
2
的形状、材料和工艺要求。
根据需求,制定合适的模具结构设
计方案,并进行初步绘制。
3
详细设计
对模具进行详细设计,包括具体的
制造与组装
4
尺寸、部件,并进行组装和调试。
冲压模具结构设计的常见困难及解决 方法
复杂冲压件的结构 设计
对于复杂形状的冲压件, 需要深入分析,采用合 适的结构设计和加工工 艺。
高精度冲压设备
采用高精度的冲压设备,可 以提高冲压件的加工精度和 表面质量。
冲压模具结构设计的案例研究
案例1 案例2 案例3
汽车冲压件模具设计 电子产品外壳模具设计 家电冲压件模具设计
通过优化模具结构和工艺, 提高冲压零件的质量和效 率,降低成本。
采用连续模设计和模拟仿 真技术,提高电子产品外 壳的精度和一致性。
冲压模具结构设计的基本原则
• 合理布局:模具结构布局要科学合理、紧凑高效,便于加工和组装。 • 合理配合:各零部件之间的配合要合理,确保模具的稳定性和准确性。 • 合理分力:合理设计模具子零件的定位、卡紧以及支撑结构,使得在冲压过程中能承受合
理的力和压力。
冲压模具结构设计的步骤
1
需求分析
通过了解客户的需求,分析冲压件
通过优化模具结构和制造 工艺,提高家电冲压件的 生产效率和可靠性。
结论和总结
冲压模具结构设计是冲压加工中的关键环节,合理的模具结构设计可以提高冲压件的质量和生产 效率。随着技术的不断发展,冲压模具结构设计的前沿技术将不断涌现,为冲压加工带来更多的 可能性。
冲压模具结构连续模步骤 (设计标准)
冲压模具结构是冲压加工中至关重要的一环,它直接影响到冲压件的质量和 生产效率。本演示将介绍冲压模具结构设计的基本原则、步骤以及常见困难 的解决方法。
- 1、下载文档前请自行甄别文档内容的完整性,平台不提供额外的编辑、内容补充、找答案等附加服务。
- 2、"仅部分预览"的文档,不可在线预览部分如存在完整性等问题,可反馈申请退款(可完整预览的文档不适用该条件!)。
- 3、如文档侵犯您的权益,请联系客服反馈,我们会尽快为您处理(人工客服工作时间:9:00-18:30)。
Page:11
3.連續沖壓加工的料條佈置技術(3)
3-2彎曲加工的料條佈置技術: (A)彎曲加工法檢討 (B)向上彎曲與向下彎曲加工的差異 (C)向上彎曲加工的對策 (D)彎曲加工的製品取出 (E)彎曲加工與送料高度
沖壓模具研討會
Confidential
Page:12
4.連續沖壓模具設計的基本技術(1)
斷面慣矩
沖頭直段部長度 圓形時 加工孔徑
無脫料板-1,有脫料板-2
(C)沖頭的固定方式: 沖切力 (1)直柄形狀 (2)帶肩形狀 不宜在同一模具,混用多種不同的固定方式
彈性係數
被加工材抗拉強度
Confidential
Page:15
4.連續沖壓模具設計的基本技術(3)
4-3母模構造與形狀設計: (A)母模依功能分三部份(1)肩部 (2)滑動部 (3)調整部 (B)母模模塊的保持方式: (1)整體型 (2)鑲入型 (solid type) (insert type)
Confidential
Page:17
4.連續沖壓模具設計的基本技術(4)
(4)F型精密模座(四柱型-four post type) -單工程模及連續沖模均有使用,主要用於精密沖模, 其精度最高.
沖壓模具研討會
(B)導柱固定於模座的方式: (1)壓入式 (2)以壓入凸緣固定 (3)以螺絲固定--模板孔徑約為導柱直徑(D)-(0.003-0.005mm) (C)導套固定於模座的方式: (1)壓入固定式(2)以樹脂固定(gap=1.5-2.0mm,孔面要粗糙) (3)以止封劑固定(gap=0.01-0.03mm)(4)以凸緣固定 (5)以螺絲固定
Confidential
Page:3
1.連續沖模的製作製程(2)
沖壓模具研討會
(4)切刃形狀的設計-切刃的形狀應儘可能簡單化,應避免引起跳屑 的形狀,形狀銜接處應減少,考慮沖頭強度. (5)料條的佈置-沖導引孔的下一工程應設計導引銷(pilot), 考慮沖屑浮上及料條變形決定沖切形狀的順序, 重要的部份至少應在相鄰的工站加工, 料條容易發生變形的工站應設失誤檢出. (6)模具組立圖-必需標示模具高度,閉模高度及送料高度, 下死點與上模的位置關係要明確, 各元件的固定方式要朝易維護的原則考慮.
Confidential
Page:2
1.連續沖模的製作製程(1)
Plan(計劃) Do(實施) Check(確認) Action(處置) (1)概念設計(2)模具設計 (1)部品準備(2)模具組立 合模試模 修模調整
沖壓模具研討會
1-1沖切型連續沖模設計流程: (1)製品圖面檢討-製品的要求是否合理,製品的毛頭及沖切面要求, 無指定R角的決定,被加工材的壓延方向的影響, 外觀品質的要求,沖切加工的限制. (2)圖面資料的重組-依製品的尺寸公差決定加工目標值, 考慮製品的精度的重要決定料條的連接方式, 考慮製品及廢料的收取及處理決定其沖切形狀. (3)胚料形狀佈列-依連結部的寬度大小決定料寬及Pitch, 決定胚料形狀的佈置以達到較高的材料利用率, 注意沖切加工時,料條連結部的變形現象.
Confidential
Page:13
4.連續沖壓模具設計的基本技術(2)
4-2沖頭設計與固定方式: (A)沖頭依功能分三部份 (1)切刃部 (2)中間部 (3)柄部
安裝部(柄部)
沖壓模具研討會
中間部
切刃部
Confidential
Page:14
4.連續沖壓模具設計的基本技術(2)
沖壓模具研討會
(B)沖頭設計的原則: (1)刃部斷面形狀較小時,應設計成階梯形沖頭. (2)決定沖頭切刃部的長度-一般為斷面大小的十倍. (3)計算沖頭的座屈強度-歐拉公式.
沖壓模具研討會
4-1料條佈列設計的基本: (A)工程設計的基本形式 (1)下料法(blanking) (2)外切法(outer cutting) (3)外切下料法 (B)連續沖切加工注意事項 (1)沖孔(內形)加工 (2)下料(外形)加工 (C)料條佈置的設計原則-毛頭方向,沖切製品的平坦度, 沖切面的限制,複雜形狀的加工分割, 繫帶的設計,導引銷的設計, 沖切形狀與跳屑對策,材料的壓延方向, 彎曲成形加工與回彈行為的對策, 是否需作遇折線的加工, 彎曲與沖切順序檢討.
Confidential
Page:5
2.沖壓模具的工程規劃(1)
沖壓模具研討會
(1)配合製品的形狀及精度要求選擇適正的沖壓加工法. (2)規劃加工工程的順序. (3)沖壓加工製程條件及模具強度或剛性的檢討. (4)製品取出及廢料排除的對策檢討. (5)模具調整性及維護保養便利性的檢討. (6)考慮模具設計變更及工程追加的可能性. 2-1沖切加工的工程規劃: (1)多孔同時加工精度較高,如模具強度不足則應將工程分開. (2)沖切加工的優先順序.
Confidential
Page:4
1.連續沖模的製作製程(3)
沖壓模具研討會
1-2含彎曲工程型連續沖模設計流程: (1)製品圖面檢討-配合精度要求,有先彎曲再沖孔的需求嗎? 彎曲部形狀改善的檢討. (2)彎曲加工法的檢討-考慮採取上彎或下彎,決定料條的浮昇量, 考慮彎曲的回彈量,檢討其防止或解決對策. (3)圖面資料的重組-注意料條連結部與彎曲加工的關係(變形現象) (4)胚料尺寸的展開-胚料尺寸的展開(計算公式或經驗值) (5)胚料形狀佈列-注意沖壓加工時,料條連接部不可有變形的現象. (6)切刃形狀的設計 (7)料條的佈置 (8)模具組立圖-彎曲部的逃角設計,必需考慮送料過程的安定性.
沖壓模具研討會
(3)窩座型 (socket type)
(4)軛型 (yoke type)
(C)分割鑲件的基本原則及注意事項 (1)分割模塊的外形採圓形及方形等單純形狀為宜. (2)分割輪廓形狀儘可能以直角分割. (3)分割模塊應注易加工的難度,各分割塊應能確實固定於模板內.
Confidential
Page:16
(1)B型模座(後方型-back post type) -用於單工程模及小型沖模,作業方便,精度及剛性較差. (2)C型模座(中央型-center post type) -用於單工程模及小型沖模,作業方向受限制. (3)D型模座(對角型-diagonal post type) -單工程模及連續沖模均有使用,長度不宜超過300mm, 否則精度會受影響.
沖壓模具研討會
(C)中央繫帶法
(D)兩側繫帶橋帶供用法
Confidential
Page:10
3.連續沖壓加工的料條佈置技術(2)
3-1沖切加工的料條佈置技術: (A)連續沖切加工的變化 (B)外切加工的切刃形狀設計 (C)外切加工的銜接設計及對策 (D)沖切形狀佈置之沖屑對策
沖壓模具研討會
Confidential
ConfidBiblioteka ntialPage:72.沖壓模具的工程規劃(2)
2-2彎曲加工的工程規劃: (1)破斷面是彎曲部外側時,易發生彎曲破裂. (2)厚板彎曲時B/t<1,易發生彎曲破裂. (3)應考慮模具的強度及剛性決定彎曲的加工順序. (4)依下述判定基準 (a)彎曲加工的容易性 (b)彎曲與沖切加工的關係 (c )模具的逃角部形狀 (d)加工後製品容易取出, 決定製品向上或向下彎曲. (5)維持彎曲部的安定設計.
Confidential
Page:22
TEST
1.試說明含彎曲工程型連續沖模設計流程?(40%)
沖壓模具研討會
2.沖切加工的分類可分為那幾種.(30%)
3.模座依導柱的配置形式及位置可區分為那四種?(30%)
Confidential
Page:23
Confidential
Page:6
2.沖壓模具的工程規劃(1)
沖壓模具研討會
(3)細長槽孔與凸部的形狀及尺寸加工限制(0.8t<W<2t及L<5W).
工程規劃
(4)銳角突起部的先端R值必需大於0.25t. (5)細孔加工沖頭要有導引以增強其剛性. (6)料條開始位置不宜跨在沖切部上,沖切形狀不宜太單純,防跳屑.
精密 一般
Confidential
Page:19
4.連續沖壓模具設計的基本技術(5)
(2)導引銷的先端直線部建議為0.3t<X<1.2t
沖壓模具研討會
被加工材板厚
Confidential
Page:20
4.連續沖壓模具設計的基本技術(6)
沖壓模具研討會
4-6模板設計與螺絲定位銷的配置: (A)決定模板寬度及長度的因素: (1)模板寬度-被加工材料的寬度和鎖緊螺絲,彈簧等 安裝所需的空間. (2)模板長度-由料條的佈列長度決定. (B)螺絲定位銷的配置原則: (1)平衡的考量-採取直線式配置設計, 螺絲採等間隔設計(約50mm-100mm) (2)尺寸及數目-定位銷(Dowel pin)的直徑(約8mm)應大於螺絲, 定位銷至少2支以上,螺絲4支以上,並應作防呆. (3)其它原則-模具尺寸大時,模板中央加螺絲,防模板翹曲. 依裝卸性及加工性考量螺絲鎖緊方向(向上或向下). 定位銷不可靠近導柱導套附近.
沖壓模具研討會
連續沖壓模具設計流程
Department: NWInG CCD Stamping
Confidential
Page:1
Table of Contents
沖壓模具研討會
1.連續沖模的製作製程 1-1沖切型連續沖模設計流程 1-2含彎曲工程型連續沖模設計流程 2.沖壓模具的工程規劃 3.連續沖壓加工的料條佈置技術 4.連續沖壓模具設計的基本技術 4-1料條佈列設計 4-2沖頭設計 4-3母模設計 4-4導料裝置設計 4-5模座及導柱的選用 4-6螺絲及定位銷的配置 4-7脫料板的設計
4.連續沖壓模具設計的基本技術(4)