锂离子动力电池组冷却方案优化策略
电动汽车动力电池冷却系统的设计与优化
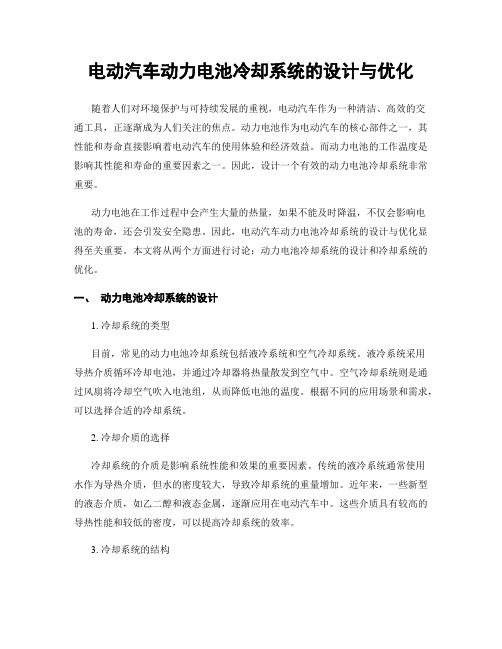
电动汽车动力电池冷却系统的设计与优化随着人们对环境保护与可持续发展的重视,电动汽车作为一种清洁、高效的交通工具,正逐渐成为人们关注的焦点。
动力电池作为电动汽车的核心部件之一,其性能和寿命直接影响着电动汽车的使用体验和经济效益。
而动力电池的工作温度是影响其性能和寿命的重要因素之一。
因此,设计一个有效的动力电池冷却系统非常重要。
动力电池在工作过程中会产生大量的热量,如果不能及时降温,不仅会影响电池的寿命,还会引发安全隐患。
因此,电动汽车动力电池冷却系统的设计与优化显得至关重要。
本文将从两个方面进行讨论:动力电池冷却系统的设计和冷却系统的优化。
一、动力电池冷却系统的设计1. 冷却系统的类型目前,常见的动力电池冷却系统包括液冷系统和空气冷却系统。
液冷系统采用导热介质循环冷却电池,并通过冷却器将热量散发到空气中。
空气冷却系统则是通过风扇将冷却空气吹入电池组,从而降低电池的温度。
根据不同的应用场景和需求,可以选择合适的冷却系统。
2. 冷却介质的选择冷却系统的介质是影响系统性能和效果的重要因素。
传统的液冷系统通常使用水作为导热介质,但水的密度较大,导致冷却系统的重量增加。
近年来,一些新型的液态介质,如乙二醇和液态金属,逐渐应用在电动汽车中。
这些介质具有较高的导热性能和较低的密度,可以提高冷却系统的效率。
3. 冷却系统的结构冷却系统的结构设计需要兼顾热量传递效果和系统的安全性。
一种常见的设计是将电池组分成若干小单元,每个单元配备一个独立的冷却模块。
这样可以提高散热效率,同时在某个单元发生故障时不会对整个电池组造成影响。
此外,还可以在冷却系统中加入温度传感器和控制装置,实现智能化的温度控制。
二、冷却系统的优化1. 优化冷却介质的流动路径冷却介质的流动路径对冷却效果有很大的影响。
通常情况下,冷却介质应该能够充分覆盖电池的所有部分,特别是热点区域。
通过合理设计冷却流道和散热片,可以增加冷却介质与电池之间的接触面积,最大限度地提高热量传递效果。
某车用锂离子动力电池组冷却系统仿真及优化

某车用锂离子动力电池组冷却系统仿真及优化徐志龙;朱晓琼;田玉冬;吴旭陵;余万【摘要】本文研究了纯电动汽车在90 km/h匀速行驶条件下锂离子电池组的温度分布,以及基于实验结果的冷却系统的实验温度分布和优化.首先,利用能量守恒定律和傅立叶导热定律,建立了电池组传热过程的简化数学模型,并利用FLUENT将其转化为有限元模型;其次,建立边界条件和负载条件,求解有限元模型,预测温度分布;再次,在电池模组水平进行热管理台架试验,得到真实的温度分布数据,与仿真结果具有较高的一致性,并根据试验数据对仿真模型进行了进一步标定,提高了有限元模型的精度;最后,经过仿真,对冷却系统进行了优化设计,以达到设计目标.【期刊名称】《三峡大学学报(自然科学版)》【年(卷),期】2018(040)006【总页数】5页(P79-83)【关键词】热管理实验;冷却系统;锂离子电池组【作者】徐志龙;朱晓琼;田玉冬;吴旭陵;余万【作者单位】上海理工大学机械工程学院,上海 200093;上海汽车集团股份有限公司商用车技术中心,上海200940;上海理工大学机械工程学院,上海 200093;上海汽车集团股份有限公司商用车技术中心,上海200940;三峡大学机械与动力学院,湖北宜昌 443002【正文语种】中文【中图分类】TM911;U463动力电池是电动汽车的心脏,是电动汽车的动力之源[1-2].随着国家相关政策对电动汽车续航里程、安全性能和电池能量密度要求的提升,对电动汽车的热管理技术提出了越来越严峻的挑战[3-4].常用的动力电池散热方式有空气冷却,液体冷却,制冷剂直接冷却以及相变材料冷却等.空气冷却结构简单,成本低,但散热性能较差;液体冷却技术成熟,冷却效果较好,目前应用广泛;直接冷却效果较好,但制冷剂分配较难,目前应用较少;相变材料冷却成本较高,目前应用尚不普及[5-8].本文采用液体冷却方式.以某电芯厂生产的动力电池模组为研究对象,通过仿真分析了水平路面90 km/h 匀速工况下电池的发热量以及温度场的分布,并结合试验研究了电池测试过程中的温感布置方式和实测电芯温度,并基于实验结果,对电池冷却系统进行了优化,改善了散热效果,加快了此种型号电池箱市场化的进程.1 电池箱结构及其模型建立1.1 电池箱体结构研究对象为某公司生产的三元锂离子电池,电池箱体为L型,下箱体内采用集成式液冷板,其上安装4个模组,如图1所示.电池成组相关参数见表1.图1 锂离子电池箱结构示意图表1 某车用锂离子电池箱技术参数模组数量电芯数量单电芯电压/V成组方式额定电压/V额定电量/Ah箱体材质4个96个3.72P96S35526铸铝每个模组都由多层材料组成,依次为导热硅胶垫、电芯、框架泡棉、电芯、导热硅胶垫、铝制导热片.其中框架泡棉主要起固定和缓冲作用,铝导热片主要用于增强模组的纵向导热能力,导热硅胶垫用于使电芯和铝导热片紧密接触.1.2 电池组的能量平衡由傅里叶定律和能量守恒,可得出电池的三维非稳态导热微分方程为[9]:(1)式中,ρ为密度,τ为时间,c为比热容,Φ为内热源强度,x、y、z分别为x、y、z三个方向的热导率.对于动力电池而言,其内热源的生成热的大小是求解温度场分布的关键.锂离子电池的最佳工作温度为20~45℃,电池内部的产热量主要包括:焦耳热Qj、极化热Qp、反应热Qr和副反应热Qs[10],即Q=Qj+Qp+Qr+Qs (2)由于锂离子电池只有在过充或过放的情况下才会发生副反应,在实际工作过程中会避免此种现象的发生,因此Qs可以忽略不计[11].电池内部的焦耳热是电池产热的主要来源,由焦耳定律可得:Qj=I2Re (3)式中,I为充放电过程中的电流大小(A);Re为电池的内阻(Ω).锂离子电池在反应过程中会伴随着锂离子的移动,在此过程中会产生(放电)或吸收(充电)大量的热量,Qr可以通过式(4)计算:(4)式中,N表示电池数量;I为当前工况下的电流(A);m为电极质量(g);M为摩尔质量(g/mol);q表示电化学反应(J);F为法拉第常数,96 484.5 C/mol.锂离子电池在一定倍率充放电的过程中会产生极化内阻,当电流通过时会产生极化热,其计算公式为:Qp=I2Rp=I2(RΩ+Rn+Rd) (5)式中,Rp为极化内阻阻值,RΩ为欧姆极化内阻,Rn为浓差极化造成的内阻,Rd为电化学极化内阻,单位均为Ω.1.3 电池组的有限元模型为缩短计算时间、保证网格质量,在不影响计算精度的前提下,在网格划分前对电池模组进行适当的简化处理,模组仅保留电芯、导热垫和导热翅片,采用Hypermesh将模组划分为六面体网格,网格数量为608万个.电池箱中各材料属性见表2.表2 电池箱材料属性材料材质密度/(kg·m-3)比热容/(J·(kg·K)-1)导热率/(W·(m·K)-1)动力粘度/(N·s·m-2)冷却液乙二醇水溶液(质量分数50%)1071.133000.3840.00339导热硅胶垫硅胶120013002电芯-140014001/32.5/32.5导热铝板AL60612700896167导热铜板铜8900397396端板AL60612700896167绝缘板ABS110014000.25导热胶水有机硅150014001为简化计算过程,假定电池箱中每块方型电芯的工作性能一致,不考虑电池组因受热而导致的变形,且流体为不可压缩物质.利用FLUENT软件进行仿真分析,冷却液的流动类型选择标准k-ε湍流模型,将流体和固体相接触的界面设置为耦合传热边界.设定电动汽车以90 km/h的速度在水平道路上匀速行驶,环境温度30℃,冷却液入口温度12℃,流量12 L/min.单电芯经实验测得发热量为10.5 W,xx、yy、zz 3个方向的导热系数分别为1 W/(m·K),32.5 W/(m·K)和32.5 W/(m·K).1.4 实验方案实验的电池箱共包含4个电池模组,每个模组包含24块电芯,电芯按照图2所示箭头方向进行编号.模组1、2从左至右电芯编号为从1~24;模组3、4从上到下电芯编号为1~24.每块模组选择其中3块电芯检测温度,每个电芯上布置6个监测点,监测点位置分布如图3所示.图2 电芯编号示意图图3 电芯监测点位置分布图温感布点共102个,分为电芯级、模组级、水冷板和pack级,具体温感分布数量及布点电芯编号见表3.表3 温感分布数量类别区域测点数量温感编号备注电芯模组118T1~T18电芯8、13、24模组218T19~T36电芯1、12、20模组318T37~T54电芯3、8、19模组418T55~T72电芯2、11、21模组模组表面和侧面8T73~T80每个模组2个,位于模组上表面及侧面BUSBAR12T81~T92每个模组各3个水冷板水冷板5T93~T97Pack级上箱体和电池包内空气温度3T98~T100上箱体2个测点水温进出口冷却液温度2T101~T102总计102为验证数学模型和仿真结果的准确性,在3种工况下进行了实验验证.实验中车速为90 km/h,冷却液入口温度为12℃.实验1中环境温度为20℃,水泵流量为12 L/min,此时压缩机不工作,冷却液在冷却系统中自循环,也即冷却液吸收电池产生的热量,在水冷板中未与制冷剂换热,冷却液未被冷却.实验2、3中环境温度为30℃,压缩机转速为1 500 r/min,水泵流量分别为6.7 L/min和12L/min.2 结果与分析2.1 电池组温度场仿真结果仿真计算时在每个模组上分别设置1个监测点,共4个,用以监测电芯的温度变化,电池各模组温度温升曲线如图4所示.图4 电池组各模组温升曲线由仿真结果可得,电池组的最高温度为49.2℃,最低温度为34.8℃,最大温差为14.4℃,4个监测点的温度分别为:38.6℃、44.9℃、43.7℃、49.2℃,电池组温度均匀性较差.电池组1与2的温度场分布基本相同,电池组3与4的温度场分布基本相同.2.2 电池组温升的实验结果图5给出了在不同实验工况下的电芯监测点的温升曲线.从图5可以发现,在不同的实验工况下,电芯的温升有较大的分别.在3种实验条件下,电芯的最高温度分别为48.6℃、47.6℃和47.2℃,最低温度分别为36.8℃、36.5℃和36.0℃.对比实验1、3可发现当液冷系统冷却液工作但压缩机侧不工作时电芯温升范围较大为18~29.8℃,压缩机侧工作时电芯温升较小为7.7~18.8℃,可见液冷系统及制冷剂侧工作状态对整个电池系统散热效果较明显;对比实验1、3可发现,虽然水冷系统能降低电池的整体温升,但是对于降低电芯间的温差效果不明显;对比实验2、3可发现,冷却液流量变动对电池散热系统影响不明显.图5 试验温升记录曲线2.3 电池组温升的实验结果与仿真结果的对比表4给出了电池组的最高温度、最低温度、4个监测点的温度的实验值和仿真值.通过仿真与实验对比可得,仿真温度与试验温度存在一定程度的误差,但是温升趋势基本吻合,试验与仿真之间产生的误差是由于在仿真时将单体电池视为均匀的生热源,没有考虑到放电时单体电池内各部位由于随着荷电状态的变化其化学反应产生的热量也不同,即单体电池在一定程度上具有温度不均匀性,因此势必会产生一定的误差.但总体而言,采用本文的仿真计算方法所得的结果基本符合实际情况.表4 仿真与实验结果对比表 (单位:℃)对比参数最高温度最低温度监测点1温度监测点2温度监测点3温度监测点4温度仿真49.234.838.644.943.749.2实验50.337.1394442.950.3误差-1.1-2.3-0.40.90.8-1.1误差百分比/%-2.19-6.20-1.032.051.86-2.193 电池箱体结构优化为获得更好的散热效果,本文对电池箱体进行了优化,给出了3种方案.3.1 水冷板流道优化由以上仿真和实验结果可得,采用液冷效果较为明显,在90 km/h匀速工况下电芯温度均能维持在50℃以内,但是电芯之间的温差较大.电池箱体采用L型结构,冷却流道内部及流向如图6(a)所示.目前所采用的流道结构无法使冷却液流过全部区域,经过对仿真和试验数据的分析,这些区域温差较大.为提高电芯与电芯之间以及为模组间的温度一致性,将对液冷板的流道进行结构优化.考虑到电池箱体轻量化的要求,暂不能对电池箱体进行过大更改,优化将在现有箱体结构的基础上进行,将最下方的主流道分解成3个小流道,使冷却液能够逐个流过整个箱体,如图6(b)所示.图6 水冷板流道示意图3.2 导热材料的优化由前所述,电池组中每两块电芯放置一块0.5 mm的铝导热片和一块0.3 mm的硅胶垫,用于将电芯热量更快地传至液冷板,简称优化方案1.仿真和试验结果表明电芯上下温差较大,热量从电芯上部传至液冷板的环节热阻较大.为了减小电芯上下温差,本文拟通过减小该环节热阻来进一步优化传热路径.模组其他结构不变,采用导热系数比铝大的相同厚度铜导热垫片,优化结构简称优化方案2,将方案1和方案2耦合后的结构简称优化方案3.3.3 优化结果分析表5给出了优化后的电池组的温升情况.表5 优化方案与原始方案对比表对比参数最高温度最低温度最大温差监测点1温度监测点2温度监测点3温度监测点4温度压降/kPa原始方案49.234.814.438.644.943.749.253.6优化方案144.435.19.338.544.438.644.448.8优化方案243.230.712.531.037.237.243.153.6优化方案339.331.08.331.538.632.039.348.8从表5可以发现:优化方案1的最大温差为9.3℃,较原始方案下降了5.1℃,说明此优化方案提高了电池间的温度均匀性;优化方案1最高温度较原始方案下降了4.8℃,最低温度上升了0.3℃,说明方案1的流道结构较原始方案带走了更多的热量,在控制电池组温升上效果比原始方案显著;优化后的流道采用多通道,并且在流道拐角处的直角改变成圆弧形,降低了沿程阻力,减少了能量消耗;由于优化后的流道流经全部模组区域,所以监测点3、4的温度显著下降,提高了模组间的温度均匀性.优化方案2最大温差为12.5℃,与原始方案相比整体温差下降不太明显;同时各个电芯竖直方向上的温差较原始方案大大降低,这是因为导热系数更高的铜导热片降低了竖直方向上热阻的原因.3.4 优化后水冷板和铜导热片的耦合优化方案1降低了模组的整体温差,但对改善电池单元竖直方向上温度均匀性效果不明显,优化方案2降低了竖直方向上的热阻,从而提高了该方向上的温度均匀性.本节考虑将方案1和方案2进行耦合.耦合后的结构简称优化方案3.优化模型后的仿真分析时的环境温度、初始边界条件与优化前的仿真参数完全一致.结果表明采用方案3后,电池组的最高温度和最低温度分别为39.3℃、31℃,最大温差为8.3℃.较方案1、2冷却效果以及电池单元间的温度均匀性有了较大提高,冷却系统压降也有所降低,该系统已满足电动汽车电池对温度的要求.4 结论1)本文通过实验得到了电动汽车在90 km/h匀速行驶工况下不同环境温度下的温升曲线;研究发现未进行散热系统优化的电池箱温升较大,电芯之间温度均匀性较差.2)通过对实验3工况下的仿真对比,验证了实验的准确性以及仿真的精度.3)通过对增加分支流道、更换铜导热垫片优化,以及两者耦合的优化方案的仿真,分析了不同方案的优化效果,为工程优化提供了参考方向.参考文献:【相关文献】[1] Zhou Xuesong. The Current Research on Electric Vehicle[M]. Chinese Control & Decision Conference, 2016:5190-5194.[2] 程启明,吴凯,王鹤霖,等.电动汽车技术发展研究[J].电机与控制应用,2013,40(6):1-6.[3] 梁波,欧阳陈志,刘燕平,等.往复流散热方式的锂离子电池热管理[J].汽车工程,2014,36(12):1449-1454.[4] 李哲,韩雪冰,卢兰光.动力型磷酸铁锂电池的温度特性[J].机械工程学报,2011,47(18):115-120.[5] Rao Zhonghao, Wang Shuangfeng. A Review of Power Battery Thermal Energy Management [J]. Renewable and Sustainable Energy Reviews,2011,15(9):4554-4571.[6] Taheri P, Mansouri A,Schweitzer B.Electrical Constriction Resistance in Current Collectors Of Large-Scale Lithium-Ion Batteries[J]. Journal of The Electrochemical Society,2013,160(10):1731-1740.[7] Kamyar Makinejad,Raghavendra Arunachala,Sabine Arnold, Hassen Ennifar, A Lumped Electro-Thermal Model for Li-Ion Cells in Electric Vehicle Application[J]. World Electric Vehicle Journal, 2015 , 7 (1):1-13.[8] 朱晖,张逸成.电动汽车电池组热管理系统的研究[J].实验室研究与探索,2011,30(6):8-14.[9] 杨世铭,陶文铨.传热学[M].北京:高等教育出版社,2006.[10] Song H S, Jeong J B, et al. Experimental Study on the Effects of Pre-heating a Batteryin a Low-temperature Environment[C]. Vehicle Power and PropulsionConference (VPPC), IEEE, 2012:1198-1201.[11] 李仲兴,李颖,等.纯电动汽车不同行驶工况下电池组的温升研究[J].机械工程学报,2014,50(8):180-185.。
车用锂离子电池冷却方案优化设计
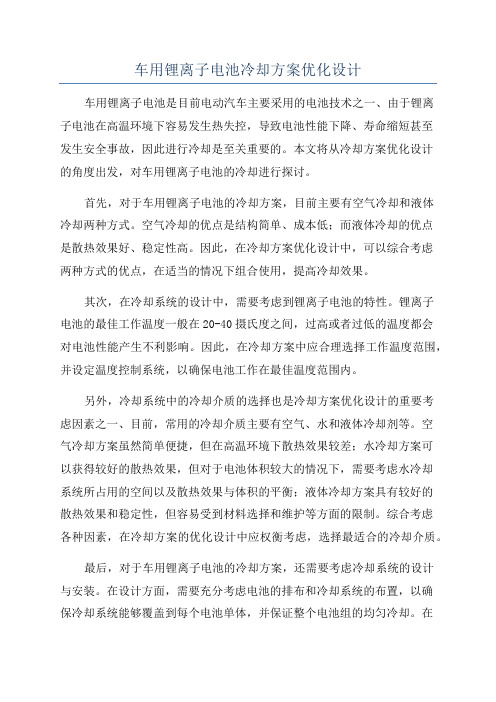
车用锂离子电池冷却方案优化设计车用锂离子电池是目前电动汽车主要采用的电池技术之一、由于锂离子电池在高温环境下容易发生热失控,导致电池性能下降、寿命缩短甚至发生安全事故,因此进行冷却是至关重要的。
本文将从冷却方案优化设计的角度出发,对车用锂离子电池的冷却进行探讨。
首先,对于车用锂离子电池的冷却方案,目前主要有空气冷却和液体冷却两种方式。
空气冷却的优点是结构简单、成本低;而液体冷却的优点是散热效果好、稳定性高。
因此,在冷却方案优化设计中,可以综合考虑两种方式的优点,在适当的情况下组合使用,提高冷却效果。
其次,在冷却系统的设计中,需要考虑到锂离子电池的特性。
锂离子电池的最佳工作温度一般在20-40摄氏度之间,过高或者过低的温度都会对电池性能产生不利影响。
因此,在冷却方案中应合理选择工作温度范围,并设定温度控制系统,以确保电池工作在最佳温度范围内。
另外,冷却系统中的冷却介质的选择也是冷却方案优化设计的重要考虑因素之一、目前,常用的冷却介质主要有空气、水和液体冷却剂等。
空气冷却方案虽然简单便捷,但在高温环境下散热效果较差;水冷却方案可以获得较好的散热效果,但对于电池体积较大的情况下,需要考虑水冷却系统所占用的空间以及散热效果与体积的平衡;液体冷却方案具有较好的散热效果和稳定性,但容易受到材料选择和维护等方面的限制。
综合考虑各种因素,在冷却方案的优化设计中应权衡考虑,选择最适合的冷却介质。
最后,对于车用锂离子电池的冷却方案,还需要考虑冷却系统的设计与安装。
在设计方面,需要充分考虑电池的排布和冷却系统的布置,以确保冷却系统能够覆盖到每个电池单体,并保证整个电池组的均匀冷却。
在安装方面,需要注意冷却系统与其他部件的连接和密封,以保证冷却介质能够流通,并防止渗漏。
综上所述,车用锂离子电池冷却方案优化设计是一个综合考虑多方面因素的问题,需要合理选择冷却方式、工作温度范围、冷却介质和冷却系统的设计与安装等。
通过优化设计,可以提高电池的散热效果,延长电池的使用寿命,确保电池组的安全性能,最终提升电动汽车的整体性能和用户的使用体验。
锂电池冷却系统的优化设计与性能研究

锂电池冷却系统的优化设计与性能研究随着电动汽车的普及和可再生能源的逐渐替代传统能源,锂电池作为一种高能量密度,低自放电和环保的电池技术,得到了广泛应用。
然而,锂电池在运行过程中会产生大量的热量,超过一定温度会降低电池的寿命甚至引发安全事故。
因此,优化设计锂电池冷却系统并研究其性能,对于电池性能的提升和安全保障至关重要。
一、锂电池冷却系统的原理和分类锂电池的冷却系统主要通过热传导、热对流和热辐射等方式,将电池产生的热量散发到周围环境中。
根据冷却介质的不同,可以将锂电池冷却系统分为气冷式、液冷式和复合式三类。
气冷式锂电池冷却系统主要利用自然对流或强制对流的方式,通过风扇或其他外部设备将空气引入电池组内部,实现热量的散发和降温。
这种方式简单、成本低廉,但对于大功率和长时间高能耗运行的锂电池,其散热效果相对较差。
液冷式锂电池冷却系统通过将导热液体(如水、乙二醇等)循环注入电池组内部,吸收热量后再通过散热装置将热量散发到环境中。
液冷系统具有散热效果好、温度均匀、适应性强等优点,但液冷系统的设计和维护成本相对较高。
复合式锂电池冷却系统结合了气冷式和液冷式的优点,采用液冷系统作为主要散热手段,辅以气冷系统进行局部散热。
这种方式既可以满足锂电池在高温条件下的快速散热需求,又能降低整体的成本。
二、锂电池冷却系统的优化设计1. 优化散热结构针对不同的锂电池类型和功率需求,设计合理的散热结构是优化锂电池冷却系统的关键。
例如,对于高功率密度的锂电池,可以采用多层散热结构来提高散热效率。
同时,可以在散热结构的设计中考虑流体力学原理,使冷却介质在流过电池表面时能够更好地吸收热量。
2. 优化冷却介质的选择液体冷却介质在优化设计中起到了至关重要的作用。
传统的水冷系统由于密度大、比热容小,导致散热效率不高。
因此,一些研究者提出了改进的液体冷却介质,如乙二醇等。
这些液体具有较高的比热容和较低的密度,能够提高散热效率,降低温度。
3. 优化冷却系统的控制策略冷却系统的控制策略也对系统的性能起到了重要的影响。
锂离子动力电池冷却技术分析与启示
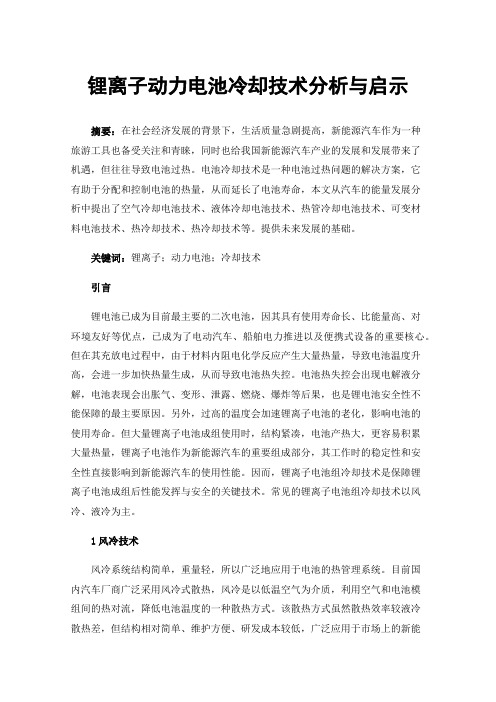
锂离子动力电池冷却技术分析与启示摘要:在社会经济发展的背景下,生活质量急剧提高,新能源汽车作为一种旅游工具也备受关注和青睐,同时也给我国新能源汽车产业的发展和发展带来了机遇,但往往导致电池过热。
电池冷却技术是一种电池过热问题的解决方案,它有助于分配和控制电池的热量,从而延长了电池寿命,本文从汽车的能量发展分析中提出了空气冷却电池技术、液体冷却电池技术、热管冷却电池技术、可变材料电池技术、热冷却技术、热冷却技术等。
提供未来发展的基础。
关键词:锂离子;动力电池;冷却技术引言锂电池已成为目前最主要的二次电池,因其具有使用寿命长、比能量高、对环境友好等优点,已成为了电动汽车、船舶电力推进以及便携式设备的重要核心。
但在其充放电过程中,由于材料内阻电化学反应产生大量热量,导致电池温度升高,会进一步加快热量生成,从而导致电池热失控。
电池热失控会出现电解液分解,电池表现会出胀气、变形、泄露、燃烧、爆炸等后果,也是锂电池安全性不能保障的最主要原因。
另外,过高的温度会加速锂离子电池的老化,影响电池的使用寿命。
但大量锂离子电池成组使用时,结构紧凑,电池产热大,更容易积累大量热量,锂离子电池作为新能源汽车的重要组成部分,其工作时的稳定性和安全性直接影响到新能源汽车的使用性能。
因而,锂离子电池组冷却技术是保障锂离子电池成组后性能发挥与安全的关键技术。
常见的锂离子电池组冷却技术以风冷、液冷为主。
1风冷技术风冷系统结构简单,重量轻,所以广泛地应用于电池的热管理系统。
目前国内汽车厂商广泛采用风冷式散热,风冷是以低温空气为介质,利用空气和电池模组间的热对流,降低电池温度的一种散热方式。
该散热方式虽然散热效率较液冷散热差,但结构相对简单、维护方便、研发成本较低,广泛应用于市场上的新能源车型。
风冷按照通风方式可分为串行式风冷散热和并行式风冷散热。
大部分电动车厂家电池组风冷方案均采用并行冷却方案。
但由于气固对流换热系数低,风冷技术冷却效率难以大幅提高,受制约较严重。
液冷锂电池组温度优化方案

液冷锂电池组温度优化方案液冷锂电池组温度优化方案步骤一:了解液冷锂电池组的工作原理和温度影响因素在制定液冷锂电池组温度优化方案之前,首先需要了解液冷锂电池组的工作原理以及温度对其性能的影响因素。
液冷锂电池组由多个电池单体组成,每个单体的温度会直接影响整个电池组的性能和寿命。
过高的温度会导致电池组容量下降、内阻增加、循环寿命缩短等问题,而过低的温度则会使电池组的放电能力下降。
因此,控制液冷锂电池组的温度是至关重要的。
步骤二:确定液冷锂电池组的温度目标范围根据液冷锂电池组的工作原理和性能要求,确定一个合适的温度目标范围是必要的。
一般来说,液冷锂电池组的温度应该控制在20°C-30°C之间,以确保电池组的性能和寿命达到最佳状态。
同时,需要考虑到电池组在不同环境条件下的工作温度,如高温环境和低温环境。
步骤三:优化液冷系统的设计为了实现液冷锂电池组的温度优化,需要优化液冷系统的设计。
首先,确保液冷系统的散热能力能够满足电池组的散热需求。
可以采用散热片、风扇或冷凝器等散热设备来提高热量的散发效率。
其次,需要设计合理的冷却循环,以保证液冷系统能够及时将热量带走。
可以考虑采用流体泵、冷凝器以及管道等设备来实现循环冷却。
步骤四:控制电池组的工作温度为了控制液冷锂电池组的工作温度,可以采取以下措施。
首先,安装温度传感器,实时监测电池组的温度变化。
可以通过数据采集系统将温度数据传输到控制系统中进行处理。
其次,根据温度传感器的数据,调节液冷系统的工作状态。
当温度过高时,增加散热设备的工作频率或增大冷却循环的流速,以降低电池组的温度。
当温度过低时,可以采取加热措施,如加热器或加热传感器。
通过控制系统的反馈机制,实现对电池组温度的精确控制。
步骤五:进行实验验证和优化为了验证和优化液冷锂电池组温度优化方案的有效性,需要进行实验验证。
在实验过程中,可以通过改变散热设备的参数、冷却循环的速度以及加热措施的强度等方式,评估不同方案对电池组温度的影响。
车用锂离子电池冷却方案优化设计
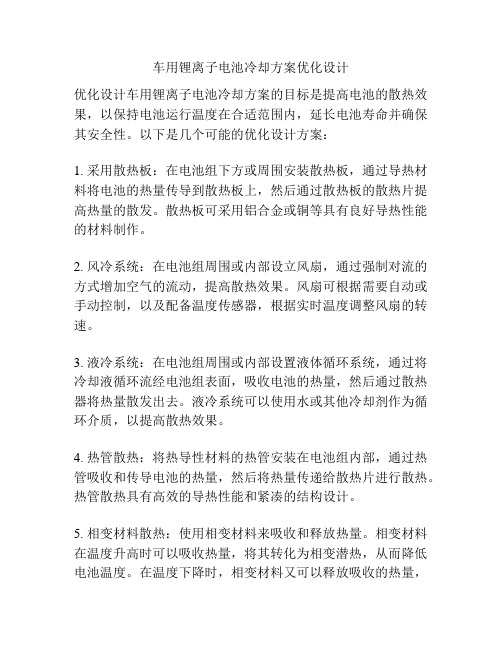
车用锂离子电池冷却方案优化设计
优化设计车用锂离子电池冷却方案的目标是提高电池的散热效果,以保持电池运行温度在合适范围内,延长电池寿命并确保其安全性。
以下是几个可能的优化设计方案:
1. 采用散热板:在电池组下方或周围安装散热板,通过导热材料将电池的热量传导到散热板上,然后通过散热板的散热片提高热量的散发。
散热板可采用铝合金或铜等具有良好导热性能的材料制作。
2. 风冷系统:在电池组周围或内部设立风扇,通过强制对流的方式增加空气的流动,提高散热效果。
风扇可根据需要自动或手动控制,以及配备温度传感器,根据实时温度调整风扇的转速。
3. 液冷系统:在电池组周围或内部设置液体循环系统,通过将冷却液循环流经电池组表面,吸收电池的热量,然后通过散热器将热量散发出去。
液冷系统可以使用水或其他冷却剂作为循环介质,以提高散热效果。
4. 热管散热:将热导性材料的热管安装在电池组内部,通过热管吸收和传导电池的热量,然后将热量传递给散热片进行散热。
热管散热具有高效的导热性能和紧凑的结构设计。
5. 相变材料散热:使用相变材料来吸收和释放热量。
相变材料在温度升高时可以吸收热量,将其转化为相变潜热,从而降低电池温度。
在温度下降时,相变材料又可以释放吸收的热量,
保持电池的稳定温度。
优化设计车用锂离子电池冷却方案需要综合考虑安全性、散热效果、成本和维护等因素,根据具体的应用场景和需求进行选择和调整。
基于不同工况温升规律分析的锂电池组散热方案优化

基于不同工况温升规律分析的锂电池组散热方案优化孙蕾;林歆悠【摘要】为了确保电动汽车行驶过程中锂离子电池组保持良好的工作性能,基于FLUENT软件对锂电池组在恒流放电下进行了温度场仿真,为了考察电池组不同工况的温升程度,分别建立了不同的整车行驶车速、坡度与电池组温升的关系,为开展电池组热管理提供参考依据,提出了基于温升变化规律的强制风冷电池组散热优化方案,同时通过对电池组不同工作条件下的仿真结果的比较,结果表明优化方案能实现电池组良好的散热,最高温度都控制在最佳工作温度范围内.%For ensuring lithium-ion battery pack good performance while electric vehicle driving , battery pack temperature field was simulated with FLUENT software under constant-current discharge. In order to investigate the battery temperature increasing level, the relationship between different vehicle speed、slope and battery temperature increasing was set up respectively. For providing reference to battery thermal management, the optimization scheme of battery forced air cooling based on temperature rising change law was proposed. The simulation results of batteries of different working conditions was compared at the same time, the results show that optimization scheme can realize good heat dissipation of the battery pack and highest temperature was controlled in the optimal operating temperature range.【期刊名称】《机械设计与制造》【年(卷),期】2017(000)010【总页数】5页(P55-59)【关键词】电动汽车;锂电池组;FLUENT;恒流放电;散热优化;行驶工况【作者】孙蕾;林歆悠【作者单位】华侨大学机电与自动化学院,福建厦门 361021;福州大学机械工程及自动化学院,福建福州 350002【正文语种】中文【中图分类】TH16锂离子动力电池由于自身高电压、高比功率、高比能量等优点[1],能显著减轻整车质量,大大提高电动汽车的最高车速、加速性能、续驶里程。