磷化膜——材料表面与界面
磷化膜组成及性质

磷化膜组成及性质磷化膜组成及性质分类磷化液主要成份膜组成膜外观单位面积膜重/ g/m2锌系 Zn(H2PO4)2 磷酸锌和磷酸锌铁浅灰→深灰 1-60锌钙系Zn(H2PO4)2和Ca (H2PO4)2 磷酸锌钙和磷酸锌铁浅灰→深灰 1-15锰系 Mn(H2PO4)2 和Fe(H2PO4)2 磷酸锰铁灰→深灰 1-60锰锌系Mn(H2PO4)2 和Zn(H2PO4)2 磷酸锌、磷酸锰、磷酸铁混合物灰→深灰 1-60铁系 Fe(H2PO4)2 磷酸铁深灰色 5-102.磷化膜组成磷化膜为闪烁有光,均匀细致,灰色多孔且附着力强的结晶,结晶大部分为磷酸锌,小部分为磷酸氢铁。
锌铁比例取决于溶液成分、磷化时间和温度。
3、性质(1)耐蚀性在大气、矿物油、植物油、苯、甲苯中均有很好的耐蚀性,但在碱、酸、水蒸气中耐蚀性较差。
在200-300℃时仍具有一定的耐蚀性,当温度达到450℃时膜层的耐蚀性显著下降。
(2)特殊性质如增加附着力,润滑性,减摩耐磨作用。
磷化工艺流程预脱脂→脱脂→除锈→水洗→(表调)→磷化→水洗→磷化后处理(如电泳或粉末涂装)影响因素1、温度温度愈高,磷化层愈厚,结晶愈粗大。
温度愈低,磷化层愈薄,结晶愈细。
但温度不宜过高,否则Fe2+ 易被氧化成Fe3+,加大沉淀物量,溶液不稳定。
2、游离酸度游离酸度指游离的磷酸。
其作用是促使铁的溶解,已形成较多的晶核,使膜结晶致密。
游离酸度过高,则与铁作用加快,会大量析出氢,令界面层磷酸盐不易饱和,导致晶核形成困难,膜层结构疏松,多孔,耐蚀性下降,令磷化时间延长。
游离酸度过低,磷化膜变薄,甚至无膜。
3、总酸度总酸度指磷酸盐、硝酸盐和酸的总和。
总酸度一般以控制在规定范围上限为好,有利于加速磷化反应,使膜层晶粒细,磷化过程中,总酸度不断下降,反映缓慢。
总酸度过高,膜层变薄,可加水稀释。
总酸度过低,膜层疏松粗糙。
4、PH值锰系磷化液一般控制在2-3之间,当PH﹥3时,共件表面易生成粉末。
磷化钝化膜形成原理
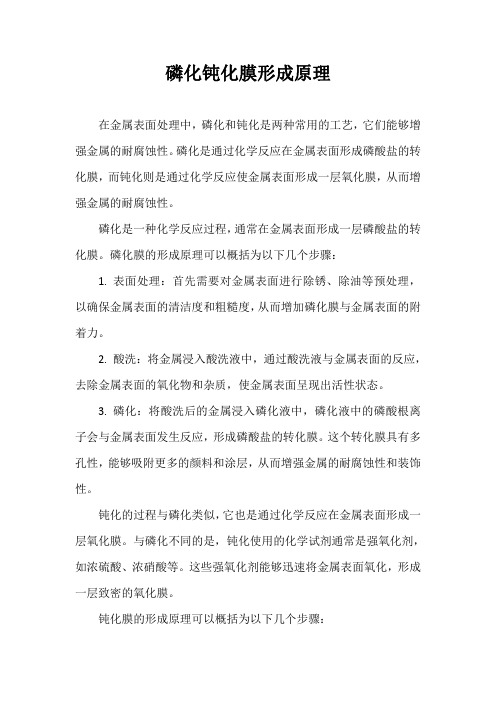
磷化钝化膜形成原理在金属表面处理中,磷化和钝化是两种常用的工艺,它们能够增强金属的耐腐蚀性。
磷化是通过化学反应在金属表面形成磷酸盐的转化膜,而钝化则是通过化学反应使金属表面形成一层氧化膜,从而增强金属的耐腐蚀性。
磷化是一种化学反应过程,通常在金属表面形成一层磷酸盐的转化膜。
磷化膜的形成原理可以概括为以下几个步骤:1.表面处理:首先需要对金属表面进行除锈、除油等预处理,以确保金属表面的清洁度和粗糙度,从而增加磷化膜与金属表面的附着力。
2.酸洗:将金属浸入酸洗液中,通过酸洗液与金属表面的反应,去除金属表面的氧化物和杂质,使金属表面呈现出活性状态。
3.磷化:将酸洗后的金属浸入磷化液中,磷化液中的磷酸根离子会与金属表面发生反应,形成磷酸盐的转化膜。
这个转化膜具有多孔性,能够吸附更多的颜料和涂层,从而增强金属的耐腐蚀性和装饰性。
钝化的过程与磷化类似,它也是通过化学反应在金属表面形成一层氧化膜。
与磷化不同的是,钝化使用的化学试剂通常是强氧化剂,如浓硫酸、浓硝酸等。
这些强氧化剂能够迅速将金属表面氧化,形成一层致密的氧化膜。
钝化膜的形成原理可以概括为以下几个步骤:1.表面处理:同样需要对金属表面进行除锈、除油等预处理,以提高钝化膜与金属表面的附着力。
2.酸洗:将金属浸入酸洗液中,去除金属表面的氧化物和杂质,使金属表面呈现出活性状态。
3.钝化:将酸洗后的金属浸入钝化液中,钝化液中的强氧化剂会迅速将金属表面氧化,形成一层致密的氧化膜。
这个氧化膜能够阻挡腐蚀介质对金属的侵蚀,从而提高金属的耐腐蚀性。
通过磷化和钝化处理,金属表面的耐腐蚀性能得到了显著提高。
同时,这两种处理方法还可以增强金属的装饰性能,使其具有更美观的外观。
在实际应用中,应根据不同的需求选择合适的处理方法。
总的来说,磷化、钝化都是通过化学反应在金属表面形成一层保护膜,从而提高金属的耐腐蚀性。
虽然它们的化学反应机理和所用试剂有所不同,但它们的表面处理和反应过程是相似的。
磷化培训资料讲解

金属基体的腐蚀
▪ 酸的浸蚀使基体金属表面H+浓度降低 : ▪ Fe – 2e→ Fe2+
2H++2e→2[H]
▪ Fe+2H+→Fe2++H2 (1)
氧化去氢
▪ 第一步产生的氢原子吸附在金属基体会对磷化反应
造成不良影响,因此需要氧化去除。
磷化培训资料
诚星化工技术部编制 2009年10月
磷化的定义
▪ 什么是磷化
磷化是指将金属工件(如钢铁、锌、铝)浸入 (或喷淋或涂刷)含有磷酸、磷酸盐和其 他化学物质的微酸性溶液中,发生化学反 应而在金属工件表面生成一层主要为不溶 或难溶的磷酸盐膜层的一种化学处理方法, 该磷酸盐膜称为磷化膜。
磷化的作用
总酸度
▪ 总酸度过高,磷化膜结晶粗糙,表面易产生浮
粉,磷化沉渣增加,可加水调整。
▪ 总酸度过低,磷化速度缓慢,磷化膜生成困难,
磷化膜结晶粗糙疏松,磷化膜变薄,耐蚀性也 差,可加磷化剂调整 。
酸比
▪ 酸比越高,磷化膜越细、越薄,过高不易成
膜、渣多。
▪ 酸比过小,磷化膜结晶粗大,疏松。 ▪ 常温磷化的酸比一般在20-30左右。
磷化的分类
▪ 按磷化膜种类分:锌系、铁系、锌钙系、锌锰系、锰系、非
晶相铁系六大类
▪ 按磷化方式分:浸渍磷化、喷淋磷化、刷涂磷化 ▪ 按磷化温度高低分 :高温磷化、中温磷化、 常温磷化 ▪ 按磷化膜单位面积膜层质量分(附用途):
A、次轻量级 膜重0.2-1.0g/㎡( 用作耐蚀性要求较低的涂装
底层)
磷化的成膜机理
▪ 磷化工作液的主要组成为酸式磷酸盐,在
磷化处理工艺流程,表面处理黑色磷化工艺
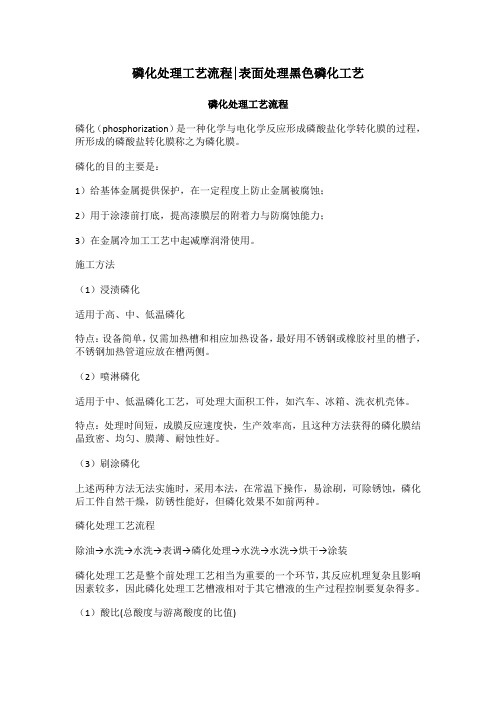
磷化处理工艺流程|表面处理黑色磷化工艺磷化处理工艺流程磷化(phosphorization)是一种化学与电化学反应形成磷酸盐化学转化膜的过程,所形成的磷酸盐转化膜称之为磷化膜。
磷化的目的主要是:1)给基体金属提供保护,在一定程度上防止金属被腐蚀;2)用于涂漆前打底,提高漆膜层的附着力与防腐蚀能力;3)在金属冷加工工艺中起减摩润滑使用。
施工方法(1)浸渍磷化适用于高、中、低温磷化特点:设备简单,仅需加热槽和相应加热设备,最好用不锈钢或橡胶衬里的槽子,不锈钢加热管道应放在槽两侧。
(2)喷淋磷化适用于中、低温磷化工艺,可处理大面积工件,如汽车、冰箱、洗衣机壳体。
特点:处理时间短,成膜反应速度快,生产效率高,且这种方法获得的磷化膜结晶致密、均匀、膜薄、耐蚀性好。
(3)刷涂磷化上述两种方法无法实施时,采用本法,在常温下操作,易涂刷,可除锈蚀,磷化后工件自然干燥,防锈性能好,但磷化效果不如前两种。
磷化处理工艺流程除油→水洗→水洗→表调→磷化处理→水洗→水洗→烘干→涂装磷化处理工艺是整个前处理工艺相当为重要的一个环节,其反应机理复杂且影响因素较多,因此磷化处理工艺槽液相对于其它槽液的生产过程控制要复杂得多。
(1)酸比(总酸度与游离酸度的比值)提高酸比可加快磷化处理工艺反应速度,使磷化处理工艺膜薄而细致,但酸比过高会使膜层过薄,易引起磷化处理工艺工件挂灰;酸比过低,磷化处理工艺反应速度缓慢,磷化处理工艺晶体粗大多孔,耐蚀性低,磷化处理工艺工件易生黄锈。
一般来说磷化处理工艺yao液体系或配方不同其酸比大小要求也不同。
(2)温度槽液温度适当提高,成膜速度加快,但温度过高,会影响酸比的变化,进而影响槽液的稳定性,同时膜层晶核粗大,槽液出渣量增大。
(3)沉渣量随着磷化处理工艺反应的不断进行,槽液内的沉渣量会逐渐增多,过量的沉渣会影响工件表面的界面反应,导致磷化处理工艺膜发花、挂灰严重,甚至不成膜,因此槽液必须根据处理的工件量和使用时间适时进行倒槽,进行清渣除淤。
磷化膜的作用
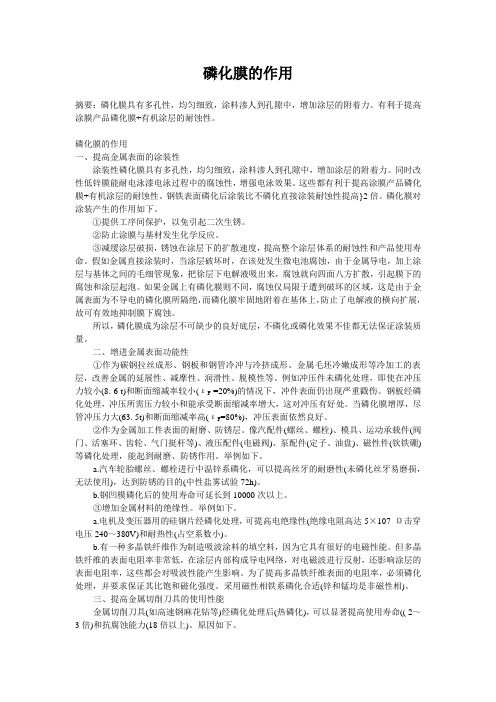
磷化膜的作用摘要:磷化膜具有多孔性,均匀细致,涂料渗人到孔隙中,增加涂层的附着力。
有利于提高涂膜产品磷化膜+有机涂层的耐蚀性。
磷化膜的作用一、提高金属表面的涂装性涂装性磷化膜具有多孔性,均匀细致,涂料渗人到孔隙中,增加涂层的附着力。
同时改性低锌膜能耐电泳漆电泳过程中的腐蚀性,增强电泳效果。
这些都有利于提高涂膜产品磷化膜+有机涂层的耐蚀性。
钢铁表面磷化后涂装比不磷化直接涂装耐蚀性提高}2倍。
磷化膜对涂装产生的作用如下。
①提供工序间保护,以免引起二次生锈。
②防止涂膜与基材发生化学反应。
③减缓涂层破损,锈蚀在涂层下的扩散速度,提高整个涂层体系的耐蚀性和产品使用寿命。
假如金属直接涂装时,当涂层破坏时,在该处发生微电池腐蚀,由于金属导电,加上涂层与基体之间的毛细管现象,把徐层下电解液吸出来,腐蚀就向四面八方扩散,引起膜下的腐蚀和涂层起泡。
如果金属上有磷化膜则不同,腐蚀仅局限于遭到破坏的区域,这是由于金属表面为不导电的磷化膜所隔绝,而磷化膜牢固地附着在基体上,防止了电解液的横向扩展,故可有效地抑制膜下腐蚀。
所以,磷化膜成为涂层不可缺少的良好底层,不磷化或磷化效果不佳都无法保证涂装质量。
二、增进金属表面功能性①作为碳钢拉丝成形、钢板和钢管冷冲与冷挤成形、金属毛坯冷嫩成形等冷加工的表层,改善金属的延展性、减摩性、润滑性、脱模性等。
例如冲压件未磷化处理,即使在冲压力较小(8. 6 t)和断面缩减率较小(εF =20%)的情况下,冲件表面仍出现严重戳伤。
钢板经磷化处理,冲压所需压力较小和能承受断面缩减率增大,这对冲压有好处。
当磷化膜增厚,尽管冲压力大(63. 5t)和断面缩减率高(εF=80%),冲压表面依然良好。
②作为金属加工件表面的耐磨、防锈层。
像汽配件(螺丝、螺栓)、模具、运动承载件(阀门、活塞环、齿轮、气门挺杆等)、液压配件(电磁阀)、泵配件(定子、油盘)、磁性件(钦铁硼)等磷化处理,能起到耐磨、防锈作用。
磷化膜质量评定项目与方法
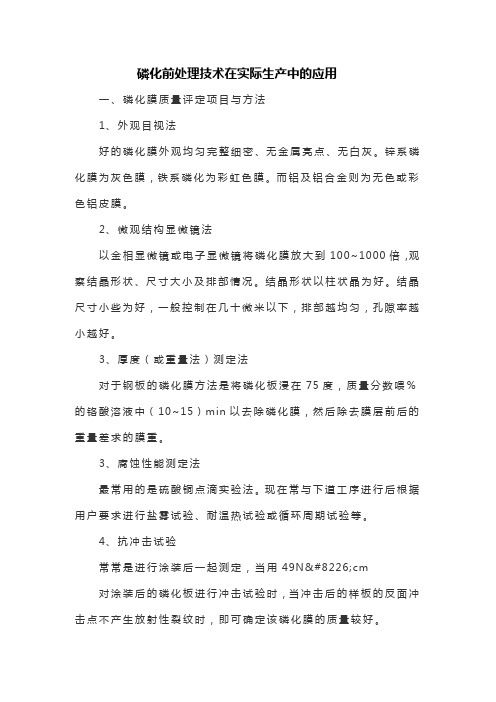
磷化前处理技术在实际生产中的应用一、磷化膜质量评定项目与方法1、外观目视法好的磷化膜外观均匀完整细密、无金属亮点、无白灰。
锌系磷化膜为灰色膜,铁系磷化为彩虹色膜。
而铝及铝合金则为无色或彩色铝皮膜。
2、微观结构显微镜法以金相显微镜或电子显微镜将磷化膜放大到100~1000倍,观察结晶形状、尺寸大小及排部情况。
结晶形状以柱状晶为好。
结晶尺寸小些为好,一般控制在几十微米以下,排部越均匀,孔隙率越小越好。
3、厚度(或重量法)测定法对于钢板的磷化膜方法是将磷化板浸在75度,质量分数喂%的铬酸溶液中(10~15)min以去除磷化膜,然后除去膜层前后的重量差求的膜重。
3、腐蚀性能测定法最常用的是硫酸铜点滴实验法。
现在常与下道工序进行后根据用户要求进行盐雾试验、耐温热试验或循环周期试验等。
4、抗冲击试验常常是进行涂装后一起测定,当用49N•cm对涂装后的磷化板进行冲击试验时,当冲击后的样板的反面冲击点不产生放射性裂纹时,即可确定该磷化膜的质量较好。
5、二次附着力测定磷化膜涂装后测定的附着力为一次附着力。
在一定条件下进行耐温水实验后测定的附着力称为二次附着力。
一般是在耐水试验后的样板上用划格法作附着力的测定,以胶带剥离后观察涂膜脱落等级,一般均为平行比较实验。
6、磷化膜孔隙率的测定取14%的NaCL和3%的铁氰化钾溶液,表面活性剂的质量分数为0.1%的蒸馏水溶液,保存在褐色瓶中24小时,用滤纸过滤。
使用时将滤纸切成长、宽均为 2.5厘米的纸片,用塑料镊子将纸片浸入上述溶液中,提出滴净多余试液,将他覆盖在戴测的磷化膜表面,经过一段时间(1分钟)后将试纸拿掉,观察膜层表面,有兰色斑点处表示有孔隙部分。
6、磷化膜的耐碱性比较磷化膜在浸碱液0.1mol/L的氢氧化钠,25度,5分钟前后的质量差,可以得到磷化膜在碱液中的溶解量。
7、磷化膜的耐酸性比较磷化膜在PH值位为2的酸液中的溶解量来评价磷化膜的耐酸性。
磷化-基本原理及分类
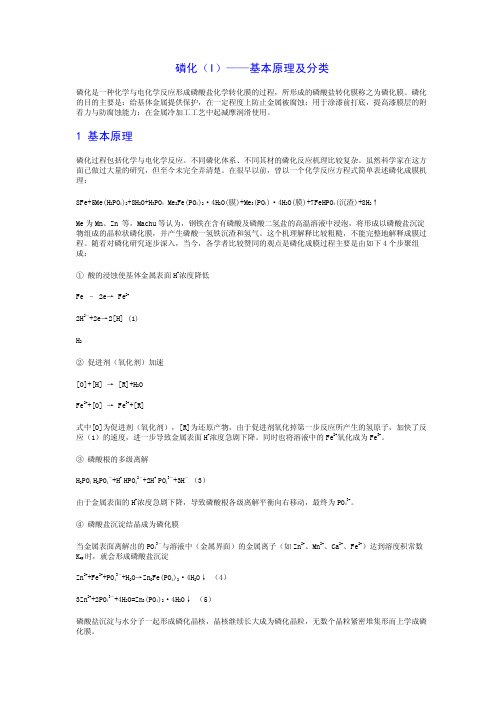
磷化(I)——基本原理及分类磷化是一种化学与电化学反应形成磷酸盐化学转化膜的过程,所形成的磷酸盐转化膜称之为磷化膜。
磷化的目的主要是:给基体金属提供保护,在一定程度上防止金属被腐蚀;用于涂漆前打底,提高漆膜层的附着力与防腐蚀能力;在金属冷加工工艺中起减摩润滑使用。
1 基本原理磷化过程包括化学与电化学反应。
不同磷化体系、不同其材的磷化反应机理比较复杂。
虽然科学家在这方面已做过大量的研究,但至今未完全弄清楚。
在很早以前,曾以一个化学反应方程式简单表述磷化成膜机理:8Fe+5Me(H2PO4)2+8H2O+H3PO4 Me2Fe(PO4)2·4H2O(膜)+Me3(PO4)·4H2O(膜)+7FeHPO4(沉渣)+8H2↑Me为Mn、Zn 等,Machu等认为,钢铁在含有磷酸及磷酸二氢盐的高温溶液中浸泡,将形成以磷酸盐沉淀物组成的晶粒状磷化膜,并产生磷酸一氢铁沉渣和氢气。
这个机理解释比较粗糙,不能完整地解释成膜过程。
随着对磷化研究逐步深入,当今,各学者比较赞同的观点是磷化成膜过程主要是由如下4个步聚组成:①酸的浸蚀使基体金属表面H+浓度降低Fe – 2e→ Fe2+2H2-+2e→2[H] (1)H2②促进剂(氧化剂)加速[O]+[H] → [R]+H2OFe2++[O] → Fe3++[R]式中[O]为促进剂(氧化剂),[R]为还原产物,由于促进剂氧化掉第一步反应所产生的氢原子,加快了反应(1)的速度,进一步导致金属表面H+浓度急剧下降。
同时也将溶液中的Fe2+氧化成为Fe3+。
③磷酸根的多级离解H3PO4 H2PO4-+H+ HPO42-+2H+ PO43-+3H-(3)由于金属表面的H+浓度急剧下降,导致磷酸根各级离解平衡向右移动,最终为PO43-。
④磷酸盐沉淀结晶成为磷化膜当金属表面离解出的PO43-与溶液中(金属界面)的金属离子(如Zn2+、Mn2+、Ca2+、Fe2+)达到溶度积常数K sp时,就会形成磷酸盐沉淀Zn2++Fe2++PO43-+H2O→Zn2Fe(PO4)2·4H2O↓(4)3Zn2++2PO43-+4H2O=Zn3(PO4)2·4H2O↓(5)磷酸盐沉淀与水分子一起形成磷化晶核,晶核继续长大成为磷化晶粒,无数个晶粒紧密堆集形而上学成磷化膜。
磷化膜主要成分

磷化膜主要成分
磷化膜是一种常见的防腐涂层,主要成分是磷化物。
磷化物是由磷和金属元素组成的化合物,可以在金属表面形成一层致密的磷化膜,起到防腐、耐磨、导电等作用。
磷化膜的形成是通过磷化反应实现的。
磷化反应是将金属表面暴露在含磷化合物的气氛中,使磷元素与金属表面发生反应,生成磷化物。
磷化反应可以通过多种方法实现,如热浸磷化、气相磷化、电化学磷化等。
磷化膜的主要成分是磷化物,但其它元素的存在也会对磷化膜的性能产生影响。
例如,镁、锌等元素可以促进磷化反应的进行,提高磷化膜的质量和厚度;铜、银等元素可以提高磷化膜的导电性能;而铁、铬等元素则会降低磷化膜的质量和耐腐蚀性能。
磷化膜的性能与其成分和结构密切相关。
一般来说,磷化膜的成分越纯,结构越致密,其防腐、耐磨、导电等性能就越好。
此外,磷化膜的厚度也是影响其性能的重要因素。
磷化膜的厚度越大,其防腐、耐磨性能就越好,但过厚的磷化膜也会影响金属件的尺寸精度和表面质量。
总之,磷化膜的主要成分是磷化物,但其它元素的存在也会对其性能产生影响。
磷化膜的性能与其成分、结构和厚度密切相关,因此在实际应用中需要根据具体要求选择合适的磷化方法和工艺参数,以获得最佳的防腐、耐磨、导电等性能。
- 1、下载文档前请自行甄别文档内容的完整性,平台不提供额外的编辑、内容补充、找答案等附加服务。
- 2、"仅部分预览"的文档,不可在线预览部分如存在完整性等问题,可反馈申请退款(可完整预览的文档不适用该条件!)。
- 3、如文档侵犯您的权益,请联系客服反馈,我们会尽快为您处理(人工客服工作时间:9:00-18:30)。
磷化膜汽车的喷涂工艺或者喷漆工艺,集中体现了材料的表面与界面的知识,而磷化膜就是其中一个对喷漆工艺有很大影响的部分。
磷化(Phosphorization)是一种化学与电化学反应形成磷酸盐化学转化膜的过程,所形成的磷酸盐转化膜称之为磷化膜。
1、磷化过程的反应机理磷化过程的反应机理相对比较复杂,目前尚无统一的完整的理论。
磷化过程可归纳为化学反应和电化学反应,不同的磷化体系,不同的基材,磷化反应机理不尽相同,但大都包括以下几个步骤:(1)基体金属溶解:当工件浸入磷化液时,磷化液中游离的磷酸把工件表面的铁溶解并放出氢气,降低了磷化界面的酸度,这是磷化反应的起点,可净化金属表面,破坏磷化槽液中的水解平衡,使水解反应向生磷化膜方向进行,界面处浓度降低。
Me-2e→Me2+2H++ 2e→2 [H]→H2↑(2)促进剂加速:铁溶解过程释放出的氢气吸附在工件表面上,阻止了磷化膜的形成,为加速反应,常加入氧化型促进剂,去除氢气,界面处H+浓度可进一步降低。
[o]+[H]→[R]+H20(3)磷酸根的多级离解:磷化液的基本成分是一种或多种重金属的酸式磷酸盐,其分子式一般用Me(H2P04)2, Me通常指锌、铁、锰等金属离子。
这些酸式th溶于水,在一定条件发生水解反应,产生游离磷酸。
由于界面处H+浓度急剧下降,导致磷酸根离子各级离解平衡向右移动,最终离解出PO43-。
Me(H2PO4)2→MeHPO4+H3PO43 MeHPO4→Me3(PO4)2+ H3PO4H3PO4→H2PO4-+H+→HP042-+2H+→PO43-(4)磷酸盐沉淀结晶成膜当溶液中离解出的PO43-与界面处的金属离子达到溶度积常数Ksp时,就会形成磷酸沉淀结晶成膜。
3Zn2++2 PO43- +4H20→Zn3 (PO4)2·4H202Zn2++Me2++2 P043- +4H20→Zn2Me (P04)2·4H20 例如上述磷酸锌生成的Zn3(PO4)2·4H20和Zn2Fe(PO4)2·4H20的结晶体,其中Me2+代表的是其他金属离子。
由于金属表面氧化过程的产生,从而破坏了磷化液的电离与水解平衡,随着磷化的不断进行,游离H3PO4的不断消耗,促进了原电离反应和水解反应的进行,Me2+、H2PO4-及PO43-浓度不断增大,当磷化反应进行到MeHPO4, FeHPO4、及Me3(PO4)2等物质浓度分别达到其各自的溶度积时,这些难溶的磷酸盐便在被处理金属表面活性点上形成晶核,并以晶核为中心不断向表面延伸增长而形成晶体;晶体不断经过结晶一溶解一再结晶的过程,直至在被处理表面形成连续均匀的磷化膜。
磷酸盐与水分子一起形成磷化晶核,晶核继续长大成为磷化晶粒,无数晶粒紧密堆积形成磷化膜。
磷化膜分为假转化膜和转化膜两种,假转化膜靠磷化液本身所含的阳离子来成膜,膜是结晶型的,转化膜靠铁基体腐蚀产生的铁离子成膜,加入的碱金属离子不参与成膜,膜属无定型的。
初生的Fe-Zn混合磷酸盐,由于铁参与成膜反应,故与基体金属的结合力非常好。
磷酸盐膜中一般总有含铁层的存在,但膜层中含铁量增高,膜层的耐蚀性将下降。
磷酸盐膜的孔隙率一般为0. 5-1. 5%,属晶体结构,主要由重金属的二代和三代磷酸盐的晶体构成,不同的磷化液得到的膜层组成不同。
锌系磷化膜主要由斜方晶体Zn3(PO4)2·4H20(H相)和单斜晶体Zn2Fe(PO4)2·4H20(p相)组成。
Zn3(PO4)2·4H20结晶是斜方晶系结构(a=1.0629nm, b=1.8339nm, c=0.504nm),其骨架为[ZnO4]或[P04]的四面体和[Zn02(H2O)1]的七面体;Zn2Fe(PO4)2·4H20结晶是单斜晶系结构(a=1. 03nm, b=0. 508nm, c=1. 055nm, β=121. 140),骨架为[Zn2P2O7]四面体和[Fe (H20) 4]的八面体。
2、影响磷化质量的因素分析(1)游离酸度的影响。
游离酸反映磷化液中游离酸的量,游离酸度过高,磷化速度慢,膜层不连续,结晶粗大,疏松、易泛黄;过低磷化槽液不稳定,沉渣量大,磷化膜成膜困难,表面易产生浮粉。
随着游离酸度的增加,基体的腐蚀也随之增加,降低游离酸浓度可减少基体腐蚀量。
酸比(总酸度与游离酸度的比值)提高可加快反应速度,使磷化膜薄而致密,但酸比过高会使膜层过薄,易引起工件挂灰;酸比过低,磷化反应速度缓慢,磷化晶体粗大多孔,耐蚀性低,磷化工件易生黄锈。
(2)温度的影响。
磷化处理温度是成膜的关键因素,温度升高,成膜速度加快,磷化反应可在较短的时间内完成。
按温度分类磷化一般分为三种类型:高温磷化(800C以上)、中温磷化(45-700C)和常温磷化(250C以下)。
前者耐蚀性好、磷化速度快,但也存在能耗高、结晶粗大、槽液沉渣多、稳定性差等缺点,难以满足口益发展的金属加工业的要求。
为了解决中高温磷化所存在的问题,节约能源,提高工作效率,降低生产成本。
目前国内外磷化工艺正朝着常温低渣快速方向发展。
但在常温磷化中,由于温度的降低不利于磷化反应的进行,因此常温磷化成膜较为缓慢,磷化膜质量难以得到保证。
温度过低,成膜离子浓度总达不到浓度积,不能生成完整磷化膜。
磷化温度升高能够提高磷化液中反应活化分子的百分含量以及反应分子的热运动,从而大大提高磷化速度。
温度升高还加快了氢气析出的速度,使锌表面pH迅速升高,加速了膜层的形成速度;另外,由于不溶性四水磷酸锌的溶解度随温度的升高而降低,因此升高温度就等于加快磷酸盐的沉淀速度。
磷化的主要反应为:2H++ 2e→2 [H]→H2↑3Zn2++2 PO43- +4H20→Zn3 (PO4)2·4H20上述反应的平衡常数为:K= [H2P04- ]2/ [Zn3(P04)2·4H20]3平衡常数K是温度的函数:logK= - △H/(2.303RT) +CK随温度的变化而变化。
水解反应是吸热过程,升高温度使K值增大,K值增大,促进了水解反应,有利于磷化膜晶体的形成。
同时水解反应的增强,增加了体系中H3PO4的浓度,从而促进了金属表面的阳极氧化反应,提高整个磷化速度。
同时,磷化温度的升高提高了磷化液中反应活化分子的百分含量以及反应分子的热运动,从而大大提高磷化速度。
温度升高有利于磷化反应的进行;但对不同的磷化体系,磷化温度应控制在一定的工艺范围内。
温度过高或过低都将影响磷化的进行。
温度过高则反应过快,磷化膜结晶粗大疏松。
(3)促进剂的影响。
如果在磷化液中加入有效的促进剂,则发生下列反应:Zn+[O]+2H3PO4→Zn3(P04)2·4H20+H20[o]表示促进剂,例如当促进剂的氧化能力较强时,此反应的标准焓△H1可达到-376.6 kJ/mol,反应3Zn2++2 PO43- +4H20→Zn3 (PO4)2·4H20的标准焓△H2约为221.8 kJ/mol,总的△H=△H1+ △H2= -151.8 kJ/mol <0。
此时无须从外部吸收热量,在常温下磷化反应也可顺利进行,因此实现常温磷化的关键在于是开发出高效促进剂。
因而促进剂可以对磷化产生很大的影响。
(4)其他。
其他如磷化膜的干燥程度、其他离子影响等等也会对磷化产生影响,但是比较复杂,不再赘述。
3、磷化的具体应用磷化能够给基体金属提供保护,在一定程度上防止金属被腐蚀,也能用于涂漆前打底,提高漆膜层的附着力与防腐蚀能力,而汽车的喷涂工艺中的磷化就是使用的磷化。
汽车的喷漆大致有以下几层:基层(合金材料)、底漆、腻子层(原子灰粉层)、中涂层、面漆层。
所以在汽车的喷漆工艺中涉及到的材料界面现象有:基层—底漆层、底漆层—腻子层、腻子层—中涂层、中涂层—面漆层,有些还要在面漆的基础上喷清漆(总体上来说也属于面漆),而且在喷漆的时候也不是一次性就喷好每一层,比如刮腻子(补原子灰)就需要几次,而面漆也是需要两次喷漆,所以总体上来说,这里涉及到的材料界面现象就很多了。
当然,喷漆完成后还有与空气接触的表面问题。
喷漆工艺中最重要的就是要使整个喷漆层牢牢地和车身结合在一起,而整个汽车车身一般说来都是合金材料。
在进行喷涂前,需要进行除油、除锈、清洗,生成磷化膜等步骤。
其中除油、除锈等工艺很好理解,这是为了提高车身与喷漆的粘合性能,而生成磷化膜一步非常重要。
金属表面在除油、除锈后,为了防止重新生锈,通常要进行化学处理,使金属表面生成一层保护膜,该膜通常只有几微米,主要起增强涂层和底材附着力的作用,较厚的膜层还能增强防锈性能。
而常用的、而且在汽车喷漆工艺中使用的便是磷化膜。
汽车车身材料(主要是合金材料)经含有锌(Zn)、锰(Mn)、铬(Cr)、铁(Fe)等磷酸盐的溶液处理后,在基底金属表面形成一种不溶性磷酸盐膜,此种过程称为磷化。
磷化使金属表面形成一层附着良好的保护膜,以在汽车喷漆工艺中一般使用的磷酸锌为例,在氧化剂的存在下,所生成的磷化膜为Zn3(PO4)2·4H20和Zn2Fe(PO4)2·4H20的结晶体,该磷化膜厚通常为0.1—50μm。
磷化膜虽然薄,但由于它是一层非金属的不导电隔离层,能使金属工件表面的优良导体转变为不良导体,抑制金属工件表面微电他的形成,进而有效阻止涂膜的腐蚀。
假如金属直接涂装时,当涂层破坏时,在该处发生微电池腐蚀,由于金属导电,加上涂层与基体之间的毛细管现象,把徐层下电解液吸出来,腐蚀就向四面八方扩散,引起膜下的腐蚀和涂层起泡。
如果金属上有磷化膜则不同,腐蚀仅局限于遭到破坏的区域,这是由于金属表面为不导电的磷化膜所隔绝,而磷化膜牢固地附着在基体上,防止了电解液的横向扩展,故可有效地抑制膜下腐蚀。
磷化膜与金属工件是一个结合紧密的整体结构。
其间没有明显界限。
磷化膜具有的多孔性,使封闭剂、涂料等可以渗透到这些孔隙之中,与磷化膜紧密结合,从而使附着力提高。
研究表明钢铁表面磷化后比不磷化涂装性能提高两倍以上。
而且不仅如此,磷化后磷化膜能够阻止金属层与涂装材料之间的反应。
所以说磷化是必不可少的一个工艺。
【参考文献】[1]牛丽媛.镁合金锌系复合磷化膜成膜机理、微观结构及性能的研究[D].吉林:吉林大学[2]李永霞.基于底漆的客车车身防腐性能研究[D].吉林:吉林大学[3]何健.铸铁中温磷化新技术研究[D].重庆:重庆大学[4]兰伟,何红林,张丁非等.镁合金磷化工艺及磷化膜性能的研究[J].材料保护,2006[5]苏晓贺.镁合金磷化工艺及耐蚀性研究[D].沈阳:沈阳工业大学。