电风扇常见故障维修
电风扇不转原因及维修方法
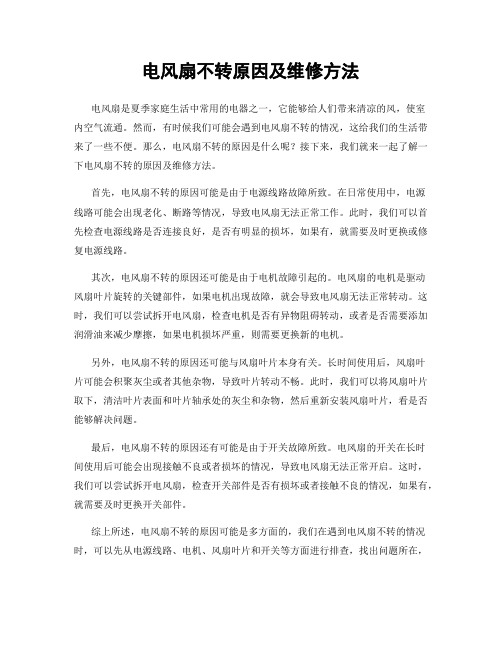
电风扇不转原因及维修方法电风扇是夏季家庭生活中常用的电器之一,它能够给人们带来清凉的风,使室内空气流通。
然而,有时候我们可能会遇到电风扇不转的情况,这给我们的生活带来了一些不便。
那么,电风扇不转的原因是什么呢?接下来,我们就来一起了解一下电风扇不转的原因及维修方法。
首先,电风扇不转的原因可能是由于电源线路故障所致。
在日常使用中,电源线路可能会出现老化、断路等情况,导致电风扇无法正常工作。
此时,我们可以首先检查电源线路是否连接良好,是否有明显的损坏,如果有,就需要及时更换或修复电源线路。
其次,电风扇不转的原因还可能是由于电机故障引起的。
电风扇的电机是驱动风扇叶片旋转的关键部件,如果电机出现故障,就会导致电风扇无法正常转动。
这时,我们可以尝试拆开电风扇,检查电机是否有异物阻碍转动,或者是否需要添加润滑油来减少摩擦,如果电机损坏严重,则需要更换新的电机。
另外,电风扇不转的原因还可能与风扇叶片本身有关。
长时间使用后,风扇叶片可能会积聚灰尘或者其他杂物,导致叶片转动不畅。
此时,我们可以将风扇叶片取下,清洁叶片表面和叶片轴承处的灰尘和杂物,然后重新安装风扇叶片,看是否能够解决问题。
最后,电风扇不转的原因还有可能是由于开关故障所致。
电风扇的开关在长时间使用后可能会出现接触不良或者损坏的情况,导致电风扇无法正常开启。
这时,我们可以尝试拆开电风扇,检查开关部件是否有损坏或者接触不良的情况,如果有,就需要及时更换开关部件。
综上所述,电风扇不转的原因可能是多方面的,我们在遇到电风扇不转的情况时,可以先从电源线路、电机、风扇叶片和开关等方面进行排查,找出问题所在,然后采取相应的维修方法来解决。
希望以上内容能够帮助大家更好地应对电风扇不转的问题,让我们的生活更加便利舒适。
电风扇常见故障维修

电风扇常见故障维修电风扇常见故障维修随着天气的逐步炎热,使用电风扇日益频繁,电风扇的故障在所难免,为了使您对电风扇有所了解,进而尝试着自己维修电风扇。
下面,将我维修电风扇的一点做法写出来,供有兴趣的朋友参考。
一、电风扇电机不转的维修从维修的实践中得知,如果电风扇电机启动电容两端有 1.3KΩ电阻值,就可快速判定电风扇电机是好的。
反之,则可断定电机损坏。
电机不转的原因,主要有:绕组断路,缺油抱轴,电容异常等。
从对电风扇的维修实践来看,后两种故障居多。
对于不转的电风扇,我的维修步骤是:测插头、转电机、量电容、再处理第一步,测量电风扇运行和调速绕组。
先把电风扇定时器旋转一下,当听到有嗒嗒声时,说明定时器是正常的。
(定时器触点损坏或积碳除外)。
如果没有嗒嗒声,说明定时器损坏。
如果定时器正常,把万用表调到R×100Ω档,用一手持两只万用表笔,夹住电风扇电源插头,(电源插头内部或电源线内断的情况极少)一手分别按动电风扇档位开关,测量电风扇电机的运行和调速绕组电阻值。
大多数电风扇的正常电阻值在600—1000Ω之间。
且快、中、慢每档电阻值相差100Ω左右。
如果电阻值相符,说明电风扇运行调速绕组基本正常。
但是,不能说电风扇电机就是好的。
因为,电机还有启动绕组,以及绕组存在局部短路的可能。
如果无电阻值,一,可能是电机绕组烧毁断路。
二,对串有热熔断器的电机,可能是热熔断器开路,还应拆开电机看一看,如果只是开路,短接热熔断器即可恢复正常,三,档位开关全部损坏,但可能性不大。
第二步,检查是否抱轴:拆开电风扇护罩,用手旋动电机轴,如果转不动,说明电机抱轴严重。
拆开电机,先清除前后轴套和电机轴上的油污、锈迹,然后在前后轴套的油毡上加足缝纫机油,大部分电风扇都能排除故障。
拆电机时,只要卸掉电机的四颗固定螺丝以及妨碍拆卸的摇头拉杆螺丝后,就可轻轻地拉开电机外壳。
动作一定要轻,防止拉坏电机绕组漆包线。
特别是鸿运扇电机,转子大多数只能从后边拉出,如果硬从前面拉出,就有可能造成电机报废。
电风扇的常见故障及维修方法

电风扇的常见故障及维修方法
随着夏季来临,电风扇成为人们生活中必不可少的电器之一。
然而,由于长期使用或其他原因,电风扇也会出现各种故障。
下面,我们就来了解一下电风扇常见的故障及维修方法。
一、电风扇不转
如果电风扇无法转动,首先要检查电源是否连接正常。
如果电源连接正常,那么就可能是电机出现了故障。
此时需要拆开电风扇外壳,检查电机的运转情况。
如果电机转动不灵活,需要清洗电机轴承或更换电机。
二、电风扇噪音过大
如果电风扇工作时噪音过大,可能是由于风扇叶片或电机轴承磨损或松动所致。
此时需要清洗或更换叶片或轴承,以减少噪音。
三、电风扇风力不足
如果电风扇工作时风力不足,可能是由于风扇叶片或机壳内积灰所致。
此时需要拆开电风扇外壳,清洗叶片和机壳内部,以提高电风扇的风力。
四、电风扇无法正常调速
如果电风扇无法调速,可能是由于调速器出现故障。
此时需要检查调速器的运转情况,如果调速器出现故障,需要更换调速器。
以上是电风扇常见的故障及维修方法。
需要注意的是,在维修电风扇时,一定要先断开电源,以免发生电击事故。
如果以上方法无法解决问题,建议寻求专业的维修帮助。
如何修复电风扇风力弱的故障
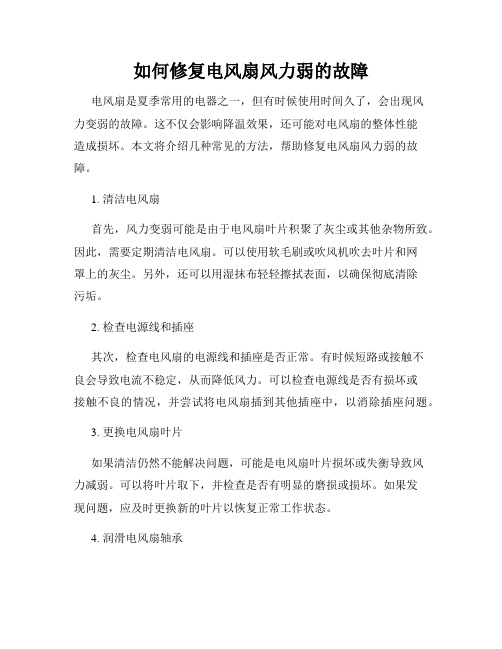
如何修复电风扇风力弱的故障电风扇是夏季常用的电器之一,但有时候使用时间久了,会出现风力变弱的故障。
这不仅会影响降温效果,还可能对电风扇的整体性能造成损坏。
本文将介绍几种常见的方法,帮助修复电风扇风力弱的故障。
1. 清洁电风扇首先,风力变弱可能是由于电风扇叶片积聚了灰尘或其他杂物所致。
因此,需要定期清洁电风扇。
可以使用软毛刷或吹风机吹去叶片和网罩上的灰尘。
另外,还可以用湿抹布轻轻擦拭表面,以确保彻底清除污垢。
2. 检查电源线和插座其次,检查电风扇的电源线和插座是否正常。
有时候短路或接触不良会导致电流不稳定,从而降低风力。
可以检查电源线是否有损坏或接触不良的情况,并尝试将电风扇插到其他插座中,以消除插座问题。
3. 更换电风扇叶片如果清洁仍然不能解决问题,可能是电风扇叶片损坏或失衡导致风力减弱。
可以将叶片取下,并检查是否有明显的磨损或损坏。
如果发现问题,应及时更换新的叶片以恢复正常工作状态。
4. 润滑电风扇轴承如果以上方法都没有解决问题,可能是电风扇的轴承发生了摩擦,导致风力减弱。
可以使用润滑油,滴一两滴在轴承处进行润滑。
但要注意选择合适的润滑油,避免过多使用,以免影响电风扇的正常运转。
5. 调整电风扇转速最后,某些电风扇具有多档风速,可能是由于误操作导致电风扇风力减弱。
在这种情况下,需要调整电风扇的转速。
可以根据电风扇的说明书或操作说明,找到相应的按键或旋钮进行调节。
总结对于电风扇风力弱的故障,我们可以通过清洁电风扇、检查电源线和插座、更换叶片、润滑轴承以及调整转速等方法进行修复。
这些方法都比较简单,但需要细心和耐心来完成。
如果问题依然存在,建议请专业人士进行维修或更换电风扇。
希望以上方法对修复电风扇风力弱的故障有所帮助!请确保在进行任何维修或清洁操作之前,先将电风扇断开电源,以确保安全。
电风扇不转的维修方法

电风扇不转的维修方法风扇使用中出现损坏或者故障是正常的,在它的风叶转不动的时候,我们应该怎么去修理,下面介绍几种方法。
1、很多时候引起风扇风叶不转的原因,都是保养较差的问题。
如果关闭电源后用手拨动风叶转动僵硬,则应该用一些润滑油滴入转轴,让它能被润滑,才不会影响动机拖动风叶。
2、针对磨损导致的风叶不转动,最简单的还是更换零件,特别是轴套,如果磨损后容易烧掉的。
3、如果电容容量变小引起风扇不转,可以拆下电容,换一个同型号的新的电容,建议选择比原来的电容大20%的,会有更好的转动效果。
4、转轴轴向间隙太大的问题,可以选择拆卸电机后调整垫片。
不过记得在把电机安装回去的时候,要注意转子必须和轴承同心,润滑用螺丝对角慢慢的扭紧,最后用木把敲一下转轴,确保它同心。
拆电机是很容易的,但是装回去比较困难,千万别随随便便,否则很容易把风扇修坏。
如果拆下电机时发现轴瓦磨损严重的话,应该换一个新的零件。
5、如果是因为电气故障,可以检查接线的各条线路,有时是电线损坏等,可以就问题修理。
普遍来说,电风扇不转多是电机引起,虽然风扇小小的,但是也不容忽视。
我们在使用电风扇时,要多注意保养,防止老化过快,也就不会出现风叶不转的问题了。
当我们经过检修后,会发现风扇转动的比之前还要好的。
电风扇的选购技巧看随机文件每台电风扇的随机文件包括使用说明书、产品合格证、电气线路图和装箱单,购买时要按照装箱单清查、核对零部件的数量和质量。
看网罩和扇叶是否有明显变形在装配好的电风扇网罩上,用一支笔指向一个扇叶最高点,缓缓移动扇叶,其他几个扇叶相对应点与笔尖之距离应十分相近,再转动扇叶,注意观察转动是否轻快灵活,并且可以在任一位置停下。
看控制机构是否灵活控制机构包括调速开关、定时旋钮、摇头开关、照明灯开关等,这些控制机构应该操作灵活、接触可靠。
对调速挡,不允许有两挡同时接通或一挡按不下去的现象。
按下停止键,各速度挡键应正常复位。
看活动部分性能电风扇扇头俯、仰各角度运转灵活,锁紧牢靠,调整到最大俯角或摇头到最终位置,网罩均不得与风扇支柱相碰。
电风扇常见故障检修

电风扇常见故障检修电风扇电机有单相交流电容运转式、单相交流罩极式、交直流串激整流式等类型,最普及常用的则是单相交流电容式电风扇,其电机的主绕组与启动绕组并联运行,电容器串接于启动绕组中形成相移获得旋转磁场而启动运转。
交流电容式电风扇结构主要由微型单相电动机、摇摆机械传动机构、调速器、定时器等几部分组合而成。
使用中最常见的故障一般有,电扇不启动、启动缓慢、低速挡不能启动、调速失灵、运行无力、摇摆头转动不灵活、电扇外壳麻电等一些故障问题。
一、常见故障分析1.不启动。
若转轴无阻卡,通常为保险丝烧断、电源电路断线、调速开关触点接触不良、电容器与绕组间脱焊及电容器损坏等故障最为常见。
2.电扇不转,有嗡嗡响声。
此类故障一般为电机转轴被卡死、电容器不良或启动绕组间断路、启动断路、短路等。
其中转子与轴套之间因缺少润滑油被卡死较常见,可拆下端盖抽出转子,擦磨净铁锈污物后滴些机油,使之灵活无卡堵即可。
如果启动绕组短路、局部烧损毁,只有更换电机或重绕电机各绕组。
3.电扇运行无力,旋转速度很慢。
这常见是串接在启动绕组中的电容器不良或容量不足不能起到移相作用。
可用放电火花判断,或用万用表电阻挡测量。
但测量时,应先放电后焊去连线,然后正负电笔交替互换测量,观测电容器充放电情况来判断。
4.电扇扇叶转动时晃动或前后窜动。
扇叶运行抖晃是由于扇叶变形或扇叶中心固定轴产生松动所造成。
对于叶片变形,造成动平恒失调很难自行校正,通常只有更换扇叶。
对于扇叶轴松动可将中心轴套的固定螺钉或铆钉重新拧紧或铆紧。
对于前后窜动,可能为扇叶中心轴与电机轴间松动,可将固定螺丝重新紧固即可。
还有是转子与前后轴套的间隙距离过大,可拆下前后机壳,在转了的前后轴端处分别垫入垫圈使之既无轴向窜动,又无卡阻为宜。
5.电扇摇头时产生时摇时停现象。
摇头故障大多在电机主轴与摇头联动机构处,常见一是由于转子蜗杆与斜齿轮间的润滑黄油干涸,造成相互间的硬摩擦,或因此造成斜齿轮损坏,检修时应补充加入润滑黄油或更换已磨损的斜齿轮。
电风扇不转的维修方法
电风扇不转的维修方法
如果电风扇不转,有几种可能的故障原因和解决方法:
1. 电源问题:首先确保电源插座正常工作,并检查电源线是否正常连接。
如果电源线损坏或松动,可以更换或重新连接。
2. 风扇开关问题:检查风扇的开关是否损坏或卡住。
如果开关损坏,可以更换新的开关。
如果开关卡住,可以尝试清洁和润滑开关。
3. 风扇电机问题:如果以上两点都正常,那么可能是风扇的电机损坏或堵塞。
可以尝试将风扇底座拆开,清理电机周围的灰尘和杂物。
如果电机损坏,可能需要更换电机。
4. 电风扇转动困难:电风扇的转动受到灰尘、油污等因素的影响,可以拆卸电风扇的保护网和叶片,清洁并润滑转轴部分。
如果以上方法都无法解决问题,建议联系专业的维修人员进行更进一步的检查和维修。
风扇不转了,是哪里出问题了
风扇不转了,是哪里出问题了
电风扇不会转了共有四大原因:一是积尘太多,二是控制回路故障,三是电机启动电容故障,四是电机绕组故障。
1、积尘太多
当电风扇积有太多的灰尘时,比如风扇轴卷入头发等杂物,轴承严重缺油等,电风扇的正常转动就会受到影响,严重的情况下,可能就不转了。
检修方法:拆开电风扇,取出电机,将电机端盖打开,轻轻抽出转子,有前后两个轴承,往轴承中滴入几滴润滑就可以了。
2、控制回路故障
当电风扇的控制回路有故障时,电风扇也会出现不转的现象。
检修方法:断电,用万用表通断档或电阻测量风扇的控制回路,重点排查下电路中的插头、调速开关等元器件,针对风扇调速开关、保护电阻、插头等配件,检查出问题的,更换下新的配件即可。
3、电机启动电容故障
当电风扇的启动电容出现故障时,电机不能正常启动,电风扇自然就不能转动了。
检修方法:用万用表电容档测量风扇电容,将电
容的实际测量值与电容额定值对比,判断出启动电容的好坏。
或用万用表的电阻档,也可以判断出电容好坏。
注意事项:在用电容档测量电容时,测量前先短接电容正负端进行充分放电,然后再测量。
4、电机绕组故障
当风扇的电机绕组有故障时,电机无法正常启动,电风扇就会出现不转的现象。
检修方法:更换同型号电机或对电机重新绕组。
电风扇故障及其解决办法(超实用)
电风扇故障及其解决办法(超实用)电风扇不转 1.转子轴不同心 1)轴与轴瓦之间间隙过大,这主要是由于扇叶受碰撞、挤压,动平衡被破坏,引起抖动,经长期磨损造成的。
2)风扇保养差,长期在无润滑中运转。
3)端盖变形或压力片松动。
排除方法:如图1所示,打开后端盖,取出转子。
检查瓦与轴之间的间隙,间隙过大不能使用。
如果轴瓦损坏严重,转子轴磨损,应更换新件。
2.电气故障的检查 1)先检查接线点各部位线为什么风扇会有很大的噪音?原因分析:1.风扇叶片变形或其电机故障;2.转盘电机故障或滚道上有杂物;3.变压器/磁控管固定不良;4.变压器/磁控管本身不合格。
解决方法:查看各可能原因造成点。
为何风扇会出现不能通电的现象?原因分析:1.电源不通;2.烧保险;3.温控开关坏;4.变压器/高压二极管/时间功率分配器/磁控管等接线松脱或毁坏;5.电压低于187伏,无法启动。
解决办法:查看电源、保险管及各主回路元器件和接线。
功率低的原因是什么?原因分析:1.电压低;2.磁控管不合格;3.时间功率分配器不良。
解决方法:查看电压或更换磁控管、分配器。
周期性停机是怎么一回事?原因分析:1.电机坏或转速低于800L/min;2.温控器失灵。
解决方法:更换温控器或风扇电机。
为什么通电后无微波功率输出?原因分析:1.时间功率分配器坏(触点没接触);2.联锁开关坏(微动开关);3.磁控管坏。
解决方法:查看或更换各元器件。
如何修理电风扇的摇头失灵故障?原因分析:电扇的摇摆机构的动力来自电动机转轴后端的蜗杆,经两级变速,驱使四连杆系统作往复摆动。
摇头失灵主要分不摇头和摇头不止两种情况。
解决方法:1.不摇头其原因一是摇头受阻,是由于连杆变形弯曲造成的,这时会有“的的”的响声,可将变形的连杆拆下,整形后即可排除;二是传动失灵,使动力得不到传递,可检查牙杆、摆头盘、齿箱、离合器等,凡发现有脱落、有异物卡死,以及因严重磨损后不能啮合等现象,应排除或更换损失的零件。
电风扇维修方法
电风扇维修方法风扇使用中出现损坏或者故障是正常的,在它的风叶转不动的时候,我们应该怎么去修理,下面介绍几种方法。
1、很多时候引起风扇风叶不转的原因,都是保养较差的问题。
如果关闭电源后用手拨动风叶转动僵硬,则应该用一些润滑油滴入转轴,让它能被润滑,才不会影响动机拖动风叶。
2、针对磨损引致的风叶不旋转,最简单的还是更改零件,特别就是轴套,如果磨损后难付之一炬的。
3、如果电容容量变小引起风扇不转,可以拆下电容,换一个同型号的新的电容,建议选择比原来的电容大20%的,会有更好的转动效果。
4、转轴轴向间隙太小的问题,可以挑选拆除电机后调整垫片。
不过回忆起在把电机加装回来的时候,必须特别注意转子必须和轴承同心,杀菌用螺丝对角慢慢的普增,最后用木把敲打一下转轴,保证它同心。
拆毁电机就是很难的,但是上装回来比较困难,千万别随随便便,否则很难把风扇TNUMBERSFX。
如果拆下来电机时辨认出轴瓦磨损轻微的话,必须换一个代莱零件。
5、如果是因为电气故障,可以检查接线的各条线路,有时是电线损坏等,可以就问题修理。
广泛来说,电风扇九洲电气多就是电机引发,虽然风扇小小的,但是也不容忽视。
我们在采用电风扇时,必须多特别注意维修保养,避免老化过慢,也就不能发生风叶九洲电气的问题了。
当我们经过检修后,可以辨认出风扇旋转的比之前还要不好的。
电风扇的选购技巧看看随机文件每台电风扇的随机文件包含采用说明书、产品合格证、电气线路图和装箱单,出售时必须按照装箱单清查、录入零部件的数量和质量。
看网罩和扇叶是否有明显变形在装配好的电风扇网罩上,用一支笔指向一个扇叶最高点,缓缓移动扇叶,其他几个扇叶相对应点与笔尖之距离应十分相近,再转动扇叶,注意观察转动是否轻快灵活,并且可以在任一位置停下。
看看掌控机构与否有效率掌控机构包含变频控制器、定时旋钮、摇摇头控制器、照明灯控制器等,这些掌控机构必须操作方式有效率、碰触可信。
对变频挡,不容许存有两压同时拨打或一压按不能下去的现象。
- 1、下载文档前请自行甄别文档内容的完整性,平台不提供额外的编辑、内容补充、找答案等附加服务。
- 2、"仅部分预览"的文档,不可在线预览部分如存在完整性等问题,可反馈申请退款(可完整预览的文档不适用该条件!)。
- 3、如文档侵犯您的权益,请联系客服反馈,我们会尽快为您处理(人工客服工作时间:9:00-18:30)。
电风扇常见故障维修集团企业公司编码:(LL3698-KKI1269-TM2483-LUI12689-ITT289-电风扇常见故障维修?随着天气的逐步炎热,使用电风扇日益频繁,电风扇的故障在所难免,为了使您对电风扇有所了解,进而尝试着自己维修电风扇。
下面,将我维修电风扇的一点做法写出来,供有兴趣的朋友参考。
?一、电风扇电机不转的维修?从维修的实践中得知,如果电风扇电机启动电容两端有1.3KΩ电阻值,就可快速判定电风扇电机是好的。
反之,则可断定电机损坏。
?电机不转的原因,主要有:绕组断路,缺油抱轴,电容异常等。
从对电风扇的维修实践来看,后两种故障居多。
对于不转的电风扇,我的维修步骤是:测插头、转电机、量电容、再处理第一步,测量电风扇运行和调速绕组。
先把电风扇定时器旋转一下,当听到有嗒嗒声时,说明定时器是正常的。
(定时器触点损坏或积碳除外)。
如果没有嗒嗒声,说明定时器损坏。
如果定时器正常,把万用表调到R×100Ω档,用一手持两只万用表笔,夹住电风扇电源插头,(电源插头内部或电源线内断的情况极少)一手分别按动电风扇档位开关,测量电风扇电机的运行和调速绕组电阻值。
大多数电风扇的正常电阻值在600—1000Ω之间。
且快、中、慢每档电阻值相差100Ω左右。
如果电阻值相符,说明电风扇运行调速绕组基本正常。
但是,不能说电风扇电机就是好的。
因为,电机还有启动绕组,以及绕组存在局部短路的可能。
如果无电阻值,一,可能是电机绕组烧毁断路。
二,对串有热熔断器的电机,可能是热熔断器开路,还应拆开电机看一看,如果只是开路,短接热熔断器即可恢复正常,三,档位开关全部损坏,但可能性不大。
第二步,检查是否抱轴:拆开电风扇护罩,用手旋动电机轴,如果转不动,说明电机抱轴严重。
拆开电机,先清除前后轴套和电机轴上的油污、锈迹,然后在前后轴套的油毡上加足缝纫机油,大部分电风扇都能排除故障。
拆电机时,只要卸掉电机的四颗固定螺丝以及妨碍拆卸的摇头拉杆螺丝后,就可轻轻地拉开电机外壳。
动作一定要轻,防止拉坏电机绕组漆包线。
特别是鸿运扇电机,转子大多数只能从后边拉出,如果硬从前面拉出,就有可能造成电机报废。
?第三步,测量启动电容:如果电机轴旋转灵活,就要测量电风扇电机的启动电容。
首先,用万用表R×100Ω档,测量电机启动电容两端(整个电风扇电机运行、启动和调速绕组的电阻值),即黑色和黄色引线的电阻值。
如果电阻值在1.3KΩ左右,说明电机启动、运行和调速绕组正常。
如果电阻值为无穷大,可以判定电风扇电机启动绕组断路损坏。
如果用户不想更换电机,维修到此结束。
如果要继续维修,在现在电风扇成品电机价格,比重绕、下线、清漆、烘干修复电机来的快和便宜情况下,一般不费时费力修复电机其次,电风扇旋转速度下降或根本不转。
也可能是启动电容不正常造成的。
在各绕组电阻值正常的情况下,应进一步测量启动电容容量。
通过测量,根据实际情况,进行处理。
(如果没有电容表,也可用同型号的电容直接代换试之),。
?如果,一切都正常,通电,电机应旋转。
用手指捏不住电机轴,说明电风扇电机正常。
反之,电机旋转无力,用手指可以捏住,并且可以用手轻易改变电机的旋转方向,一般是电机局部绕组短路,只有更换电机了。
通过上述检查步骤,基本可以搞清电风扇电机的故障所在,对症排除,修好电风扇。
?现在各种电风扇的电机电阻值基本上差不多,现附上YSZ-300mm鸿运扇电机和YSY-12400mm台式电风扇电机接线图和各线之间电阻值,可供参考?.png?现实中,很多人喜欢用加、并电容的方法,来增大电风扇启动电容的容量,使电风扇旋转快一点。
殊不知,这会增大本来就捉襟见肘电机参数富余量的负荷,极容易烧毁电机,得不偿失。
二、能动电风扇的维修?对电机能动的电风扇,我是根据实际情况,一步到位。
而不是象上述那样,按部就班地进行维修。
如果用户说,电风扇先慢慢转,然后渐渐变快。
根据经验,一般是电机轻微抱轴。
原因是电风扇润滑油初期缺失。
直接拆开电风扇电机,在前后轴套的油毡上加足缝纫机油,一般即可修复。
如果用户说:电风扇早先能慢慢转,一段时间后渐渐变快,现在只能微微转动了。
说明电风扇电机干涸的润滑油残渣,滞涩、阻碍着电机的转动,形成了严重抱轴。
也可直接拆开电机,先清除前后轴套和电机轴上的油污和锈迹,然后在前后轴套的油毡上加足缝纫机油,大部分电风扇都能恢复正常。
?如果用户说:电风扇快档象慢档,只能能慢慢地转,则有可能是电扇的启动电容容量变小,直接代换电容试一试。
往往即可手到病除三、遥控电扇,上电就转故障的排除?现在的遥控电扇,控制执行元件基本上都是可控硅。
从原理可知,可控硅实质等同于开关,可控硅击穿等同于开关接通。
接通电源,电风扇当然就转啦了。
?如一台莱格落地遥控电风扇,使用时,遥控各功能基本正常,但是,电风扇关闭后(不是拔掉电源),手摸电风扇,有明显的震动感,并且电风扇发出嗡嗡声,夜晚尤为明显,细看电风扇扇叶,也在缓慢地转动。
因为各项控制功能基本正常,说明MCU正常,从上述原理可知,可控硅有故障。
拆开电风扇。
测量各可控硅,阻值正常。
由于只是缓慢地转动,估计低速档可控硅有故障。
焊开低速档连线,嗡嗡声消失,更换可控硅,故障排除。
另有一台永生牌遥控壁挂式电风扇,用户说:除非拔掉电源,一插上电源,电风扇就转,关不掉。
拆机测量可控硅,高速档的可控硅击穿短路,更换后,故障排除。
?遥控电风扇的可控硅损坏,可以用97A6、ZD607、?BT131等互换四、遥控电扇电源故障的排除?遥控电扇降压电容容易损坏,如果降压电容不正常,单片机正常工作所需的首要条件:工作电流和电压就无从保障。
必然导致遥控电扇不能正常工作。
根据电容容量的不同,会形成多种故障。
在遥控电扇的维修中,降压电容不正常,占有一定比例,一般更换电容后,故障就会排除。
电风扇降压电容一般为1-1.5uf。
如没有CBB22/630V电容更换,可以用电风扇常用电容CBB61/450V直接代换。
只不过体积大一点,并不影响使用。
?如一台美的FS40-6CR400mm遥控落地扇,插电有“嘀”的提示音,按“开/关”键,电扇转,一松手,电扇就停转,按着“开/关”键不松手,电扇转,但指示灯闪烁,“嘀嘀”声不断。
根据维修经验,判断为电源故障。
拆开电风扇,直接测量降压电容,标注1UF 的电容,实际只有0.1uf,不正常。
更换降压电容后,故障排除。
五、用台式风扇电机代换壁扇电机?对于壁扇电机损坏的,早期我都是购买同型号的电机进行更换。
在买不到同型号的情况下,用台式风扇电机,去掉的调速器,锯掉电机尾轴进行改造代换。
在多次的代换中,我发现市场售卖的壁扇电机质量较差,没有台式电机质量好,而价格却一样。
我便购买台式电机,去掉调速器,直接代换。
(不用锯断电机尾轴),从维修的角度来看,花一样的价钱,购买质量更好的电机,而且还可以多得到一个电扇调速器,不用锯掉尾轴,省时省力。
对用户对自己都有好处,何乐而不为呢??六、用电扇电容调速在维修电风扇中,时常遇到电风扇低速损坏缺失,用户要求修复低速档时,我采用从高速档接电容的办法,进而解决高低档的改造。
电容的大小可通过实验确定。
不用换电机,方便快捷,效果也不错。
为方便家里老人和儿童夏日夜晚的安全用电扇,对于即使电风扇开在最小档也觉得风太大的用户,希望把电风扇速度降下来,慢一些的用户,我们可以在电风扇的外壳里面,把电源进线未接电容的一根,从中间剪断,串接一个2uf左右的电扇电容,再在串接电容的两头,各引出一根电线,接入一个开关,固定在电扇的适当位置,就可以把原先三档的电风扇,变成六档电风扇。
接通后加开关,电风扇恢复原样,我叫它快三档;断开开关,就变成了慢三档电风扇是夏日常用的消暑电器,几乎家家都有,因而,天一热,电风扇的维修量就会增大。
在维修中,经常听到用户抱怨:过去买的电风扇。
用了多少多少年,不管怎么用都不坏。
现在买的电风扇,用不了几个月,就不转了。
从大家的议论中,不难看出,生产电风扇的技术和工艺都是成熟的。
而现在的电风扇易坏的主要原因,是生产厂家为了追求利益的最大化,降低成本,在生产电风扇的过程中,所用材料能省就省的原因造成的。
在市场经济的今天,对生产厂家来说,也无可厚非。
但对整个社会来说,却是资源的浪费,不符合国家倡导的节能环保政策。
国家应从宏观上,制度上,用标准,来鼓励、控制、约束生产企业节能环保,尽快使用新技术新材料,对产品的关键易损部件使用好材料。
从维修的实践看:大多数电风扇故障,都是因电风扇电机轴套部分发热严重,引起润滑油的干涸、滞涩,形成抱轴故障而损坏。
如果,电风扇的轴套,使用传热快的铜质材料,而不使用现在都用的铁质材料,将会大大提高电风扇的使用寿命。
怎么用数字万用表测量风扇电机的好坏断电一表笔接红线:对黑约为490欧对黄约为730欧黑。
黄=490+730=1220欧。
一表笔接白;对红约95欧对蓝约95欧红,蓝=95+95=190欧。
数据与线的材质和电机功率有关。
与你的电机不尽一至。
但它的阻值规律不变。
追问:按你的方法测得数据为:一表笔接红线对黑940,红对黄无数据,黑对黄无数。
一表笔接白线对红145,白对蓝142,红对蓝288,从这些数据怎么看出电机的好坏?追答:黄线接启动运行电容。
为副绕组一端引出线。
阻值无穷大。
说明该绕组己断。
可判电机坏了。
能找到断点重新接上可修复。
(断点在黄蓝之间)不然则只有更换电机了。
将档位放在Ω档2kΩ档,风扇电机是单相交流220v的,用启动电容启动,电机有两个绕组,一个是启动绕组,一个是运行绕组;启动绕组电阻大些,运行绕组电阻小些。
实际电机出线有3根,用万用表分别测3根线间的直流电阻,最大值为启动绕组+运行绕组的阻值,其次为启动绕组的阻值,再次为运行绕组的阻值。
在将万用表档位放在20MΩ档,测量绕组(用电机三根线中任意一根)与电机定子铁芯间的,阻值应该在2MΩ以上,即可判定电机唯有问题。
追问:是变速器上的“红、白、蓝”三根线吗?是插上220V的电源测还是不插电测追答:测电阻是不能带电测量的万能表具体使用方法?一、观察和了解万用表的结构。
万用表种类很多,外形各异,但基本结构和使用方法是相同的。
常用万用表的结构和外形见彩页附图。
万用表面板上王要有表头和选择开关。
还有欧姆档调零旋钮和表笔插孔。
下面介绍各部分的作用:?(一)表头万用表的表头是灵敏电流计。
表头上的表盘印有多种符号,刻度线和数值(如图3-4(B))。
符号A一V一Ω表示这只电表是可以测量电流、电压和电阻的多用表。
表盘上印有多条刻度线,其中右端标有“Ω”的是电阻刻度线,其右端为零,左端为∞,刻度值分布是不均匀的。
符号“-”或“DC”表示直流,“~”或“AC”表示交流,“~”表示交流和直流共用的刻度线。
刻度线下的几行数字是与选择开关的不同档位相对应的刻度值。