换热器技术要求汇总
板式换热器国家标准
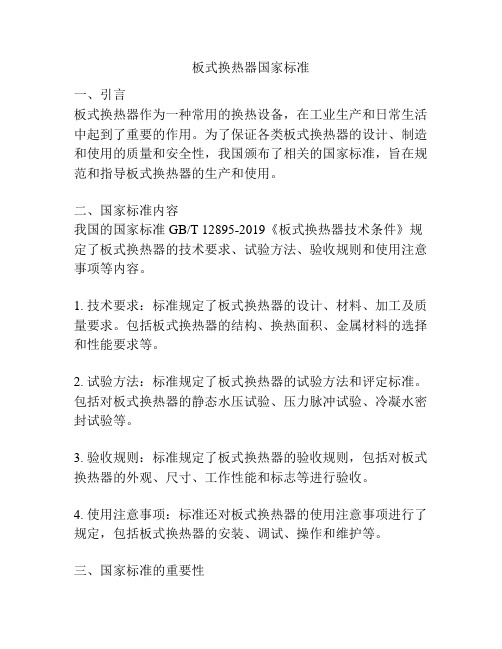
板式换热器国家标准一、引言板式换热器作为一种常用的换热设备,在工业生产和日常生活中起到了重要的作用。
为了保证各类板式换热器的设计、制造和使用的质量和安全性,我国颁布了相关的国家标准,旨在规范和指导板式换热器的生产和使用。
二、国家标准内容我国的国家标准GB/T 12895-2019《板式换热器技术条件》规定了板式换热器的技术要求、试验方法、验收规则和使用注意事项等内容。
1. 技术要求:标准规定了板式换热器的设计、材料、加工及质量要求。
包括板式换热器的结构、换热面积、金属材料的选择和性能要求等。
2. 试验方法:标准规定了板式换热器的试验方法和评定标准。
包括对板式换热器的静态水压试验、压力脉冲试验、冷凝水密封试验等。
3. 验收规则:标准规定了板式换热器的验收规则,包括对板式换热器的外观、尺寸、工作性能和标志等进行验收。
4. 使用注意事项:标准还对板式换热器的使用注意事项进行了规定,包括板式换热器的安装、调试、操作和维护等。
三、国家标准的重要性国家标准对于确保板式换热器的质量和安全性起到了重要的作用。
1. 规范了行业生产:国家标准规定了板式换热器的设计和制造要求,能够规范行业生产水平,提高板式换热器的质量。
2. 保障了使用安全:国家标准对板式换热器的使用进行了规定,能够提供操作人员的安全保障,降低事故风险。
3. 方便了市场交流:有了国家标准作为依据,生产企业和用户之间的交流更加方便,能够提高板式换热器的通用性和互换性。
四、结论国家标准对于板式换热器的设计、制造和使用具有重要的指导意义。
通过严格遵守国家标准,能够提高板式换热器的质量和安全性,促进行业的协调发展。
同时,国家标准的制定也需要与时俱进,及时更新和完善,以适应新技术、新材料和新工艺的发展。
五、国家标准的主要内容解析1. 技术要求:国家标准GB/T 12895-2019《板式换热器技术条件》明确了板式换热器的技术要求。
其中包括了换热器的尺寸、材料、传热系数等方面的要求。
换热器技术要求

4.2.2容积式换热器一、设备供货范围和施工范围说明设备名称单位数量导流型容积式换热器(供spa,职淋)(机房内) RV-04-10.0(0.4/1.0)B台 2 V=10.0M3 管程压力Ps=0.4mpa 壳体压力Ps=1.0mpa (壳体316L不锈钢)配备温度计,压力表,安全阀等导流型容积式换热器(供大堂,厨房)(机房内) RV-04-7.0(0.4/1.0)BV=7.0M3台 2管程压力Ps=0.4mpa 壳体压力Ps=1.0mpa (壳体316L不锈钢)配备温度计,压力表,安全阀等导流型容积式换热器(供客房A翼低区)(机房内)RV-04-2.5(0.4/1.0)B V=2.5M3台 2管程压力Ps=0.4mpa 壳体压力Ps=1.0mpa (壳体316L不锈钢)配备温度计,压力表,安全阀等导流型容积式换热器(供客房A翼高区)(机房内)RV-04-4.0(0.4/1.0)B V=4.0M3台 2管程压力Ps=0.4mpa 壳体压力Ps=1.0mpa (壳体316L不锈钢)配备温度计,压力表,安全阀等导流型容积式换热器(供客房B翼低区)(机房内)RV-04-2.0(0.4/1.0)B V=2.0M3台 2管程压力Ps=0.4mpa 壳体压力Ps=1.0mpa (壳体316L不锈钢)配备温度计,压力表,安全阀等导流型容积式换热器(供客房B翼高区)(机房内)RV-04-2.5(0.4/1.0)B V=2.5M3台 2管程压力Ps=0.4mpa 壳体压力Ps=1.0mpa (壳体316L不锈钢)配备温度计,压力表,安全阀等容积式换热器(供洗衣机房)(机房内) RV-04-3.5 (1.0/1.0) V=3.5M3台 2管程压力Ps=1.0MPa 壳体压力Ps=1.0MPa (壳体不锈钢)配备温度计,压力表,安全阀等每一台换热器应由同一厂家整体装配生产,其中包括贮水容器、热交换组件、内循环水系统、温度控制及压力表、安全阀、保温、外壳、控制设备等。
管壳换热器要求

管壳换热器是一种常见的换热设备,它由一对平行管子和壳体组成,管子内部流过流体,壳体外部流过冷却剂或加热剂。
这种设备在化工、石油、制药、能源、食品等行业中的应用十分广泛。
要求管壳换热器的制造过程需要严格遵循一定的规范和标准,以确保设备的稳定性和可靠性。
具体来说,要求如下:1. 材质要求:管壳换热器通常采用碳钢、不锈钢、钛合金、铝合金等材料制成。
在制造过程中,必须确保所选材料符合相关标准,并经过严格的质量控制,确保材料的质量稳定可靠。
2. 加工精度要求:管壳换热器的加工精度要求较高,包括管子与壳体的平行度、垂直度、同心度等。
这些精度要求直接影响设备的性能和使用寿命,因此必须严格控制加工过程中的误差,确保设备的精度符合规范要求。
3. 焊接要求:管壳换热器通常采用焊接工艺进行连接,因此焊接质量对设备的质量和可靠性至关重要。
在制造过程中,必须采用合格的焊接材料和工艺,并进行严格的焊接质量检查,确保焊接质量符合规范要求。
4. 防腐要求:管壳换热器通常处于腐蚀性介质的包围中,因此防腐性能是设备的重要指标之一。
在制造过程中,必须采取有效的防腐措施,如表面处理、涂层等,以延长设备的使用寿命。
5. 清洗和干燥要求:在制造完成后,必须对设备进行彻底的清洗和干燥,以确保设备内部无杂质和水分,避免影响设备的性能和使用寿命。
6. 标识和记录要求:在制造过程中,必须对每个部件进行标识和记录,以确保设备的可追溯性和质量稳定性。
同时,必须建立完善的档案管理制度,保存相关记录和文件,以便日后检查和维修。
综上所述,管壳换热器的制造过程需要严格遵循上述要求,以确保设备的稳定性和可靠性。
同时,在使用过程中,也需要定期检查和维护设备,及时发现和处理潜在的问题,以确保设备的正常运行和使用寿命。
总之,管壳换热器作为一种常见的换热设备,在化工、石油、制药、能源、食品等行业中的应用十分广泛。
为了保证设备的稳定性和可靠性,我们需要严格遵守上述要求进行制造和维护,从而保证设备的安全和高效运行。
换热器操作工序及要求

换热器操作工序及要求为保证产品质量,明确责任和责任范围。
责任和利益挂钩,引入监督制约机制,保证每道工序不出现瑕疵,下道应用工序是上道的检验员,未达到质量要求的,下道工序应完善对上道工序的利益扣减,补偿给下道工序人员。
本办法是单位根据实际情况制定的暂行办法,不作为对外的技术标准。
一、割板1、必须符合尺寸要求,基本尺寸+1mm,合格率98%。
2、对角线长度差≤2㎜,合格率98%。
3、切割面应光滑,与大面保持垂直,应无波纹。
4、注意割嘴工作状态,割嘴带病工作不应超过一个固定板长板面长度。
5、切割面出现锯齿、槽沟、长棱必须进行处理,使之能够进入下道工序。
下道工序无法直接使用的,应进行打腻子处理。
6、切割面出现长沟的,打磨板后打腻子处理。
7、问题切割面不处理,按拆算工时扣款;超过五对扣当月奖金。
二、摞板1、要保证两块板对齐时,焊点一对。
2、注意大板面质量,切面应尽量朝看面。
有凹坑面朝里面。
从工艺上保证紧固板。
三、钻板3、定位孔必须规定使用钻头,孔径超过钻头直径应小于1㎜.4、定位孔中心距比波纹板定位孔中心距 +1.00/+0.50,当1.5≤2mm为次品,每付板扣1元。
5、换热器接口通上边缘不能凸出周边平面。
凸出时应打磨平整。
通口内侧边缘突出周边平面不能超过1mm,超出时应及时进行清理。
不清理,按每个孔径扣0.1元。
一付板口个不清理,该板不计工作任务数。
6、紧固板板面的铁屑应清理干净。
钻孔后残片不应留在板面上,留一块扣0.1元。
接口周围不应有铁屑存在。
不清理每口扣0.1元。
连续四块或连续10个孔不清理,扣当日工资。
四、铣床7、应保持加工尺寸和加工面垂直。
8、加工后的紧固板铁屑应进行清理干净。
五、焊接9、法兰焊接①按相应长度尺寸焊接。
注意内在质量和外观质量,按对应要求焊接厚度,打磨光滑平整。
②碳钢法兰及接管除密封线及焊接用的一段管外,内外应均涂漆,或批焊接内涂率100%,不得低于98%,低于扣0.1元。
10、成品板焊接①法兰管焊接要保证一定厚度和外观质量。
换热器标准

YB/T 4053-1991 高效喷流换热器技术条件(中文)YS/T 288-1994 空调机换热器铜管(中文)CJ/T 3047-1995 半即热式换热器(中文)HG/T 2376-1992 搪玻璃套筒式换热器(中文)HG/T 3187-1980 矩型块孔式石墨换热器(中文)JB/T 8701-1998 制冷用板式换热器(中文)JB/T 4715-1992 固定管板式换热器型式与基本参数(中文)JB/T 4717-1992 U型管式换热器型式与基本参数(中文)JB/T 4718-1992 管壳式换热器用金属包垫片(中文)JB/T 4719-1992 管壳式换热器用缠绕垫片(中文)JB/T 4720-1992 管壳式换热器用非金属垫片(中文)JB/T 4722-1992 管壳式换热器用螺纹换热管基本参数和技术条件(中文)JB/T 4723-1992 不可拆式螺旋板换热器型式与基本参数(中文)JB/T 4740-1997 空冷式换热器型式与基本参数及编制说明(中文)JB/T 6631-1993 机械密封系统用螺旋管式换热器(中文)JB/T 6919-1993 螺旋板式换热器性能实验方法(中文)JB/T 7262-1994 铝制板翅式换热器型号编制方法(中文)JB/T 7659.5-1995 氟利昂制冷装置用翅片式换热器(中文)QB/T 19-1990 食品工业用板式换热器(中文)制糖机械压力容器通用零部件换热器用奥氏体不锈钢焊接钢QB/T 2072.3-1994管(中文)SHS 019-1992 管壳式换热器维护检修规程(试行)中文)SHS 03010-1992 超高压套管换热器维护检修规程(中文)SHS 03051-1992 高压套管换热器维护检修规程(中文)SHS 03052-1992 石墨换热器维护检修规程(中文)SHS 108-1992 切换板翅换热器维护检修规程(试行)中文)GB/T 14845-1993 板式换热器用钛板(中文)GB/T 15386-1994 空冷式换热器(中文)GB 16409-1996 板式换热器(中文)HG 20537.2-1992 管壳式换热器用奥氏体不锈钢焊接钢管技术规定(中文)JB/T 10379-2023 换热器热工性能和流体阻力特性通用测定方法(中文)JB/T 4751-2023螺旋板式换热器(中文)HG/T 3112-1998 浮头列管式石墨换热器()HG/T 3113-1998 YKA型圆块孔式石墨换热器()JB/T 4714-1992 浮头式换热器和冷凝器型式与基本参数中文)YB 4103-2023 换热器用焊接钢管(中文)HG/T 2650-1995 钢制管式换热器(中文)GB 151-1999 钢制管壳式换热器(中文)SH/T 3119-2023 石油化工钢制套管换热器设计规范(中文)HG/T 20701-2023 容器换热器专业工程设计管理规定(中文)HG/T 20701-2023 容器换热器专业工程设计管理规定(中文)热互换器.区域供暖用水换热器.拟定性能数据的实验程BS EN 1148-1999序(英文)ANSI/ASME PTC 30-1991 空气冷却换热器(英文)ANSI/API 660-2023 一般炼油设备用管壳式换热器(英文)锅炉,过热器和换热器用无缝铁素体和奥氏体合金钢管规范ANSI/ASTM A 213/A 213M-2023(英文)锅炉、过热器和换热器用无缝铁素体和奥氏体合金钢管的标ASTM A 213/A 213Ma-2023准规范(英文)焊接奥氏体钢制锅炉、过热器、换热器和冷凝管的标准规范ASTM A 249/A 249M-2023(英文)JIS A 47-1995 风扇式对流换热器(日文)CB/T 1036-1997 船用板式热互换器(中文)CB/T 3685-1995 船用热互换器修理技术规定(中文)CB/T 3690-1995 船用热互换器通用技术条件(中文)CB/T 3820-1998 船用翅片管热互换器(中文)QB/T 2098-1995 房间空气调节器用热互换器(中文)GB/T 2531-1981 热互换器固定板用黄铜板(中文)GB 8890-1988 热互换器用铜合金管(中文)GB 12262-1990 人工心肺机热互换器(中文)GB 13296-1991 锅炉、热互换器用不锈钢无缝钢管(中文)GB/T 3625-1995 热互换器及冷凝器用钛及钛合金管(中文)船舶技术.技术文献图形符号.第5部分:蒸气发生器、热互换器、容器德文) 管束式热互换器;带法兰浮头档数2内管25正交分度32内管数及装置排列操作杆和滑轨德文) 壳管束式热互换器;带焊接浮头档数2内管25正交分度32;内管数及装置把手及滑轨德文)GB/T 19447-2023 热互换器用铜及铜合金无缝翅片管(中文) CB/T 3961-2023 船用热互换器设计计算方法(中文) GB/T 18816-2023 船用热互换器通用技术条件(中文) YS/T 446-2023钎焊式热互换器用铝合金复合箔(中文) DIN 28192-1994 管式热互换器用弹性垫圈德文) DIN 30697-3-1990 燃烧液化气带热互换器的移动式热风机.安全枝术规定.检查. 标记德文) DIN 32727-1981 热互换器的流动量安全装置安全技术规定和检查.德文) DIN 32728-1981 装料控制器装有有机液体的热互换器用液位控制器. 安全技术规定和检查.德文) DIN 45635-14-1980机器噪声测量。
换热器设备规范标准最新
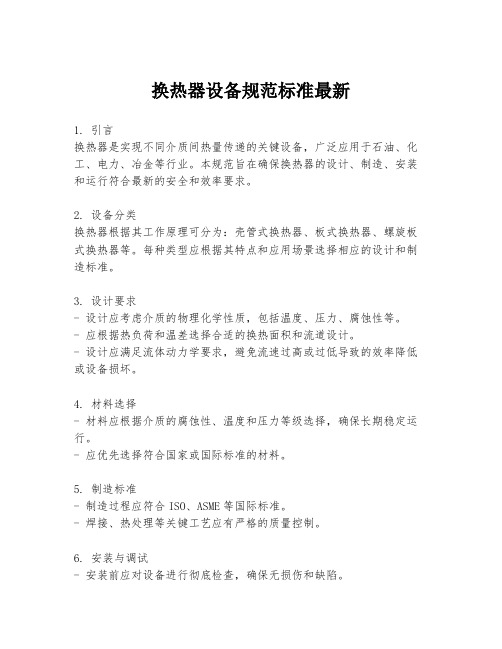
换热器设备规范标准最新1. 引言换热器是实现不同介质间热量传递的关键设备,广泛应用于石油、化工、电力、冶金等行业。
本规范旨在确保换热器的设计、制造、安装和运行符合最新的安全和效率要求。
2. 设备分类换热器根据其工作原理可分为:壳管式换热器、板式换热器、螺旋板式换热器等。
每种类型应根据其特点和应用场景选择相应的设计和制造标准。
3. 设计要求- 设计应考虑介质的物理化学性质,包括温度、压力、腐蚀性等。
- 应根据热负荷和温差选择合适的换热面积和流道设计。
- 设计应满足流体动力学要求,避免流速过高或过低导致的效率降低或设备损坏。
4. 材料选择- 材料应根据介质的腐蚀性、温度和压力等级选择,确保长期稳定运行。
- 应优先选择符合国家或国际标准的材料。
5. 制造标准- 制造过程应符合ISO、ASME等国际标准。
- 焊接、热处理等关键工艺应有严格的质量控制。
6. 安装与调试- 安装前应对设备进行彻底检查,确保无损伤和缺陷。
- 安装应严格按照设计图纸和制造商指导进行。
- 调试过程中应监测设备运行参数,确保达到设计要求。
7. 安全与环保- 设备应配备必要的安全装置,如压力释放阀、温度监控器等。
- 应采取措施减少噪音和振动,符合环保要求。
8. 运行与维护- 制定详细的操作规程,确保操作人员正确使用设备。
- 定期对设备进行检查和维护,及时发现并解决问题。
9. 质量保证- 制造商应提供完整的质量保证体系,包括材料证明、工艺流程记录、出厂检验报告等。
10. 附录- 附录包括换热器的典型设计参数、计算方法、故障排除指南等。
11. 结语本规范标准旨在指导换热器的设计、制造、安装和运行,以确保设备的安全、可靠和高效。
建议用户根据具体应用场景和最新技术发展,对本规范进行适当调整和更新。
请注意,上述内容为示例文本,实际的换热器设备规范标准应根据具体的行业标准和法规进行制定。
板式换热器技术要求

(二)板式换热器3设计与运行条件3.1板式换热器型式板式换热器采用等截面可拆卸板式换热器(水-水),换热面材质材质为GB316不锈钢。
3.2板式换热器的配置本次招标共需配备2台可拆卸板式换热器(水-水),单台功率22.5MW,单台换热面积950 m2,换热器接管管径按设计所提管径配置,换热器按本技术规范书所提面积订货。
3.3板式换热器设计参数下表为单台22.5兆瓦板式换热器的参数下表为15兆瓦单台板式换热器的参数3.4热网循环水水质板式换热器工作介质为热网循环水,水质为软化水,具体水质如下:3.5运行方式板式换热器并联运行。
板式换热器换热量的控制通过控制一次侧(高温介质)流量和控制二次侧(低温介质)流量来实现。
3.6设备的安装地点及标高板式换热器安装在换热站0米层。
4技术要求投标方提供的板式换热器设计、制造、检验与验收应满足国家相关规范中的相关规定,同时应满足本技术规范书中技术要求,如有矛盾时按较高要求执行。
4.1板式换热器性能要求4.1.1投标方所提供的板式换热器是可拆卸板式换热器(水-水),其技术先进、经济合理,成熟可靠的产品,具有较高的运行灵活性。
4.1.2板式换热器能在最大工况点长期连续运行,能满足板式换热器不同运行工况的需要,并且预留能增加10%换热能力板片的安装空间和技术条件。
4.1.3板式换热器不宜选择单板面积太小的板片,避免板片数量过多,要求单板面积大于等于2.5 m2。
4.1.4板式换热器采用板型应使换热器内流体充分湍动,防止板片表面结垢。
4.1.5板式换热器应选用阻力小的板型,保证一次侧(高温介质)压降不大于0.03MPa,二次侧(低温介质)压降不大于0.03MPa。
4.1.6板式换热器板片厚度应不小于0.7mm。
4.1.7板式换热器额定工况运行时,二次侧(低温介质)出口温度偏差不应出现负偏差。
4.1.8板片波纹形式应采用技术成熟、有成功使用业绩的波纹形式。
4.1.9板式换热器外部、内部保证不泄漏,一、二次水禁止混流。
换热站设备技术要求

换热站设备技术要求换热设备:1.热交换器应选用高效、可靠的换热设备,具备高换热效率和低压降的特点,并具备良好的防腐蚀性能和可靠的密封设计。
2.热交换器的设计应符合流体力学和换热原理,通过合理的管道布局和流体分布设计,最大程度地提高换热效率。
3.热交换器的材质应符合工作介质的特性和使用环境的要求,能够承受高温、高压和腐蚀等不利条件。
水泵:1.水泵的选型应符合系统的流量、压力和工作条件需求,具备稳定的性能曲线、高效的水力性能和可靠的操作性能。
2.水泵的材质应符合介质的特性和使用环境的要求,能够承受高温、高压和腐蚀等不利条件。
3.水泵的工作噪音应控制在合理范围内,不得超过国家规定的噪声限值。
阀门:1.阀门的选型应符合系统的流量、压力和工作条件需求,具备良好的控制性能和可靠的密封性能。
2.阀门的材质应符合介质的特性和使用环境的要求,能够承受高温、高压和腐蚀等不利条件。
3.阀门的操作方式应方便、灵活,能够实现对流体的精确控制,并具备防冻和自动排空功能。
仪表:1.仪表的选型应符合系统的测量要求,能够准确测量流量、温度、压力等关键参数,并具备稳定的性能和可靠的操作性能。
2.仪表的测量范围、精确度和可靠性应符合系统设计和运行的要求。
3.仪表的材质应符合介质的特性和使用环境的要求,能够承受高温、高压和腐蚀等不利条件。
自动控制系统:1.自动控制系统应能够实现对换热站的自动化控制和监测,能够根据需要调节和控制换热设备、水泵和阀门等关键设备的运行状态。
2.自动控制系统应具备可靠性高、响应速度快、操作方便的特点,能够自动启停和调节设备的运行,提高能源利用效率和运行安全性。
3.自动控制系统应具备数据采集和远程监控功能,能够实时监测和分析换热站的运行状态,并能够预测和提前处理故障和异常情况。
综上所述,换热站设备的技术要求主要包括高效、可靠的换热设备、稳定、高效的水泵、精确、可靠的阀门和仪表、以及可靠、高效的自动控制系统等方面。
- 1、下载文档前请自行甄别文档内容的完整性,平台不提供额外的编辑、内容补充、找答案等附加服务。
- 2、"仅部分预览"的文档,不可在线预览部分如存在完整性等问题,可反馈申请退款(可完整预览的文档不适用该条件!)。
- 3、如文档侵犯您的权益,请联系客服反馈,我们会尽快为您处理(人工客服工作时间:9:00-18:30)。
一.总图技术要求:
1、设备法兰和管板采用16Mn锻件,应符合NB/T 47008-2010《承压设备用碳素钢和合金钢锻件》标准,合格级别见图样规定;接管使用20无缝钢管,应符合GB 9948-2013《石油裂化用无缝钢管》的规定,供货状态为正火。
2、设备按照NB/T 47015-2011《压力容器焊接规程》焊接,焊接工艺评定根据NB/T 47014-2011《承压设备焊接工艺评定》进行,焊接接头除图中注明外,其余均为连续焊接接头,角焊接接头的焊角尺寸为施焊件中较薄件的厚度,法兰按相应的标准焊接。
3、管板密封面与壳体轴线垂直,垂直度公差为1mm。
4、换热器制造完毕后应彻底除锈,涂漆前钢材表面应达到GB/T8923.1-2011中规定的Sa2.5级的要求。
壳体底层用环氧云铁防锈漆涂装3道,每道干膜厚度不得小于40μm,涂层总厚度不得小于120μm。
5、本设备管束需要做内防腐,管束内表面涂"SHY99"防腐涂料,防腐涂层干膜总厚度不得低于120μm。
管束的涂料防腐应符合SH/T3540-2007<<钢制换热设备管束复合涂层施工及验收规范>>的规定,且防腐处理应由有成熟经验的专业防腐处理厂进行施工。
6、滑动鞍座采用双螺母固定,地脚螺栓上的第一个螺母拧紧后倒退一圈,然后用第二个螺母锁紧。
7、产品和注册铭牌座安装在壳程壳体(左侧)中间部位,材质与壳体一致,并保证高出保温层50mm以上。
注:1.在设计寿命期内,压力容器使用单位,应根据装置的操作状态或TSG R7001-2004"压力容器定期检验规则"的要求,对该设备进行定期检验,并确认实际寿命和设计寿命的符合性,设计寿命不包括管束。
二.前端管箱技术要求:
1.管箱组焊完毕后,应进行消除应力热处理,然后法兰和隔板密封面应一起进行精加工。
2.法兰密封面及表面不得有裂纹及其它降低法兰强度或连接可靠的缺陷。
3.其它要求见装配图。
4.此吊耳仅用于前端管箱的吊装。
三、后端管箱技术要求:
1.法兰密封面及表面不得有裂纹及其它降低法兰强度或连接可靠的缺陷。
2.其它要求见装配图。
3.此吊耳仅用于前端管箱的吊装。
四.滑道技术要求:
1.滑道必须平直,不得翘曲。
2.周边去毛刺,棱角倒钝。
五.垫片的技术要求:
1.波齿复合垫应参照GB/T 19066.3-2008《柔性石墨金属波齿形复合垫片技术条件》的要求进行制造、检验和验收。
2.金属骨架应采用整张钢板制作,不允许拼接。
3.本波齿复合垫片应进行压缩、回弹及密封性能试验,其压缩率应≥25%。
六.钩圈的技术要去:
1.锻件应符合NB/T47008-2010《承压设备用碳素钢和合金钢锻件》中规定的Ⅲ级锻件的要求。
2.制作后切为两半.
3.钩圈密封面及表面不得有裂纹及其它降低钩圈强度或连接可靠的缺陷.
4.相邻两螺栓孔弦长公差±0.6mm.
5.任意两螺栓孔弦长公差±1.5mm.
注:棱边倒钝。
七.固定管板
1.锻件应符合NB/T 47008-2010《承压设备用碳素钢和合金钢锻件》规定Ⅲ级的要求。
2.管板钻孔后,≥96%的孔桥宽度不得小于5.83mm,最小孔桥宽度不得小于4.05mm,但不超过4%。
3.管孔应严格垂直于管板密封面,垂直公差为0.08mm,孔表面不允许有贯通的纵向条痕。
4.管板密封面应与设备轴线垂直,垂直度公差为0.30mm。
八.管束的技术要求:
1.换热管与管板的连接采用强度焊加贴胀.
2.所有定距管长度偏差均为.
3.换热管需逐根进行水压试验,试验压力为20MPa,以30秒无泄漏为合格.
4.换热管内壁做防腐处理,防腐技术要求见总图.
九.折流版的技术要求:
1.折流板应平整,其平面度公差为3mm.
2.相邻两孔中心距离极限偏差为±0.3mm,允许有4%相邻两孔中心距,极限偏差为±0.5mm, 任意两管孔中心距极限偏差为±1mm.
3.钻孔后应除去管孔周边的毛刺.。