d395橡胶压缩永久变形特性的试验方法
d395橡胶压缩永久变形特性试验方法
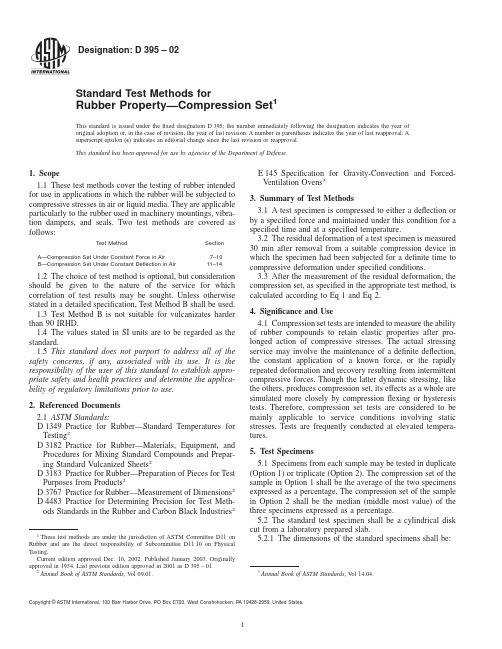
Designation:D395–02Standard Test Methods forRubber Property—Compression Set1This standard is issued under thefixed designation D395;the number immediately following the designation indicates the year of original adoption or,in the case of revision,the year of last revision.A number in parentheses indicates the year of last reapproval.A superscript epsilon(e)indicates an editorial change since the last revision or reapproval.This standard has been approved for use by agencies of the Department of Defense.1.Scope1.1These test methods cover the testing of rubber intended for use in applications in which the rubber will be subjected to compressive stresses in air or liquid media.They are applicable particularly to the rubber used in machinery mountings,vibra-tion dampers,and seals.Two test methods are covered as follows:Test Method Section A—Compression Set Under Constant Force in Air7–10B—Compression Set Under Constant Deflection in Air11–14 1.2The choice of test method is optional,but consideration should be given to the nature of the service for which correlation of test results may be sought.Unless otherwise stated in a detailed specification,Test Method B shall be used.1.3Test Method B is not suitable for vulcanizates harder than90IRHD.1.4The values stated in SI units are to be regarded as the standard.1.5This standard does not purport to address all of the safety concerns,if any,associated with its use.It is the responsibility of the user of this standard to establish appro-priate safety and health practices and determine the applica-bility of regulatory limitations prior to use.2.Referenced Documents2.1ASTM Standards:D1349Practice for Rubber—Standard Temperatures for Testing2D3182Practice for Rubber—Materials,Equipment,and Procedures for Mixing Standard Compounds and Prepar-ing Standard Vulcanized Sheets2D3183Practice for Rubber—Preparation of Pieces for Test Purposes from Products2D3767Practice for Rubber—Measurement of Dimensions2 D4483Practice for Determining Precision for Test Meth-ods Standards in the Rubber and Carbon Black Industries2E145Specification for Gravity-Convection and Forced-Ventilation Ovens33.Summary of Test Methods3.1A test specimen is compressed to either a deflection or by a specified force and maintained under this condition for a specified time and at a specified temperature.3.2The residual deformation of a test specimen is measured 30min after removal from a suitable compression device in which the specimen had been subjected for a definite time to compressive deformation under specified conditions.3.3After the measurement of the residual deformation,the compression set,as specified in the appropriate test method,is calculated according to Eq1and Eq2.4.Significance and Use4.1Compression set tests are intended to measure the ability of rubber compounds to retain elastic properties after pro-longed action of compressive stresses.The actual stressing service may involve the maintenance of a definite deflection, the constant application of a known force,or the rapidly repeated deformation and recovery resulting from intermittent compressive forces.Though the latter dynamic stressing,like the others,produces compression set,its effects as a whole are simulated more closely by compressionflexing or hysteresis tests.Therefore,compression set tests are considered to be mainly applicable to service conditions involving static stresses.Tests are frequently conducted at elevated tempera-tures.5.Test Specimens5.1Specimens from each sample may be tested in duplicate (Option1)or triplicate(Option2).The compression set of the sample in Option1shall be the average of the two specimens expressed as a percentage.The compression set of the sample in Option2shall be the median(middle most value)of the three specimens expressed as a percentage.5.2The standard test specimen shall be a cylindrical disk cut from a laboratory prepared slab.5.2.1The dimensions of the standard specimens shall be:1These test methods are under the jurisdiction of ASTM Committee D11onRubber and are the direct responsibility of Subcommittee D11.10on PhysicalTesting.Current edition approved Dec.10,2002.Published January2003.Originallyapproved st previous edition approved in2001as D395–01.2Annual Book of ASTM Standards,V ol09.01.3Annual Book of ASTM Standards,V ol14.04.1Copyright©ASTM International,100Barr Harbor Drive,PO Box C700,West Conshohocken,PA19428-2959,United States.Type1A2BThickness,mm(in.)12.560.5(0.4960.02)6.060.2 (0.2460.01)Diameter,mm(in.)29.060.5(1.1460.02)13.060.2 (0.5160.01)A Type1specimen is used in Test Methods A and B.B Type2specimen is used in Test Method B.5.2.2When cutting the standard specimen,the circular die having the required inside dimensions specified in5.2.1shall be rotated in a drill press or similar device and lubricated by means of a soap solution.A minimum distance of13mm(0.51 in.)shall be maintained between the cutting edge of the die and the edge of the slab.The cutting pressure shall be as light as possible to minimize cupping of the cut edges.The dies shall be maintained carefully so that the cutting edges are sharp and free of nicks.5.3An optional method of preparing the standard specimen may be the direct molding of a circular disk having the dimensions required for the test method used and specified in 5.2.1.N OTE1—It should be recognized that an equal time and temperature,if used for both the slab and molded specimen,will not produce an equivalent state of cure in the two types of specimen.A higher degree of cure will be obtained in the molded specimen.Adjustments,preferably in the time of cure,must be taken into consideration if comparisons between the specimens prepared by different methods are to be considered valid. N OTE2—It is suggested,for the purpose of uniformity and closer tolerances in the molded specimen,that the dimensions of the mold be specified and shrinkage compensated for therein.A two-plate mold with a cavity13.060.1mm(0.51060.004in.)in thickness and29.2060.05 mm(1.14860.002in.)in diameter,with overflow grooves,will provide Type1specimens for Test Method A and Test Method B.A similar mold but having a cavity of6.360.3mm(0.2560.012in.)in thickness and 13.260.1mm(0.5260.004in.)in diameter will provide Type2 specimens for Test Method B.5.4When the standard test specimen is to be replaced by a specimen taken from a vulcanized rubber part of greater thickness than the one indicated in5.2.1,the sample thickness shall be reducedfirst by cutting transversely with a sharp knife and then followed by buffing to the required thickness in accordance with Practice D3183.5.5An alternative method of preparing specimens is by plying up cylindrical disks cut from a standard sheet prepared in accordance with Practice D3182using the specimen sizes specified in5.2.1and cutting as described in5.2.2,or where a drill press is not available cutting the specimens with a single stroke from a cutting die.5.5.1The disks shall be plied,without cementing,to the thickness required.Such plies shall be smooth,flat,of uniform thickness,and shall not exceed seven in number for Type1 specimens and four in number for Type2specimens.5.5.2Care shall be taken during handling and placing of the plied test specimen in the testfixture by keeping the circular faces parallel and at right angles to the axis of the cylinder.5.5.3The results obtained on plied specimens may be different from those obtained using solid specimens and the results may be variable,particularly if air is trapped between disks.5.5.4The results obtained on the specimens prepared by one of the methods may be compared only to those prepared by the same method.5.6For routine or product specification testing,it is some-times more convenient to prepare specimens of a different size or shape,or both.When such specimens are used,the results should be compared only with those obtained from specimens of similar size and shape and not with those obtained with standard specimen.For such cases,the product specification should define the specimen as to the size and shape.If suitable specimens cannot be prepared from the product,the test method and allowable limits must be agreed upon between the producer and the purchaser.6.Conditioning6.1Store all vulcanized test specimens or product samples to be tested at least24h but not more than60days.When the date of vulcanization is not known,make tests within60days after delivery by the producer of the article represented by the specimen.6.2Allow buffed specimens to rest at least30min before specimens are cut for testing.6.3Condition all specimens before testing for a minimum of 3h at2362°C(73.463.6°F).Specimens whose compression set properties are affected by atmospheric moisture shall be conditioned for a minimum of24h in an atmosphere controlled to5065%relative humidity.7.Precision and Bias47.1These precision statements have been prepared in ac-cordance with Practice D4483.Please refer to Practice D4483 for terminology and other testing and statistical concepts.7.2Prepared test specimens of two rubbers for Test MethodsA andB were supplied tofive laboratories.These were tested in duplicate each day on two separate testing days.A test result, therefore,is the average of two test specimens,for both Test Methods A and B.7.3One laboratory did not run the Test Method A testing; therefore,the precision for Test Method A is derived from four laboratories.7.4The Type1precision results are given in Table1and Table2.4Supporting data are available from ASTM Headquarters.Request RR: D11–1138.TABLE1Type1Precision Results,%Compression Set—TestMethod AMaterialMeanLevelWithin Laboratory A Between Laboratory AS r r(r)S R R(R)1 1.73(%)0.0500.1428.20.1900.5431.1 226.10.898 2.549.7 2.37 6.7125.7A Sr=within laboratory standard deviation.r=repeatability(in measurement units).(r)=repeatability(in percent).S R=between laboratory standard deviation. R=reproducibility(in measurement units). (R)=reproducibility(in percent).7.5Bias—In test method statistical terminology,bias is the difference between an average test value and the reference or true test property value.Reference values do not exist for these test methods since the value or level of the test property is exclusively defined by the test method.Bias,therefore,cannot be determined.TEST METHOD A—COMPRESSION SET UNDERCONSTANT FORCE IN AIR8.Apparatus8.1Dial Micrometer—A dial micrometer,for measuring specimen thickness,in accordance with Practice3767,Method A1.8.2Compression Device,consisting of a force application spring and two parallel compression plates assembled bymeans of a frame or threaded bolt in such a manner that the device shall be portable and self-contained after the force has been applied and that the parallelism of the plates shall be maintained.The force may be applied in accordance with either 8.2.1or8.2.2.8.2.1Calibrated Spring Force Application—The required force shall be applied by a screw mechanism for compressing a calibrated spring the proper amount.The spring shall be of properly heat-treated spring steel with ends ground and per-pendicular to the longitudinal axis of the spring.A suitable compression device is shown in Fig. 1.The spring shall conform to the following requirements:8.2.1.1The spring shall be calibrated at room temperature 2365°C(73.469°F)by applying successive increments of force not exceeding250N(50lbf)and measuring the corresponding deflection to the nearest0.2mm(0.01in.).The curve obtained by plotting the forces against the corresponding deflections shall have a slope of7063.5kN/m(400620 lbf/in.)at1.8kN(400lbf).The slope is obtained by dividing the two forces above and below1.8kN by the difference between the corresponding deflections.8.2.1.2The original dimensions of the spring shall not change due to fatigue by more than0.3mm(0.01in.)after it has been mounted in the compression device,compressed under a force of1.8kN(400lbf),and heated in the oven for one week at70°C62°C(15863.6°F).In ordinary use,a weekly check of the dimensions shall show no greater change than this over a period of1year.8.2.1.3The minimum force required to close the spring (solid)shall be2.4kN(530lbf).8.2.2External Force Application—The required force shall be applied to the compression plates and spring by external means after the test specimen is mounted in the apparatus. Either a calibrated compression machine or known masses may be used for force application.Provision shall be made by the use of bolts and nuts or other devices to prevent the specimen and spring from losing their initial deflections when the external force is removed.The spring shall have essentially the same characteristics as described in8.2.1,but calibration is not required.A suitable compression device is shown in Fig.2.8.3Plates—The plates between which the test specimen is compressed shall be made of steel of sufficient thickness to withstand the compressive stresses without bending.8.3.1The surfaces against which the specimen is held shall have a chromium platedfinish and shall be cleaned thoroughly and wiped dry before each test.8.3.2The steel surfaces contacting the rubber specimens shall be ground to a maximum roughness of250µm(10µin.) and then chromium plated and polished.8.3.3The chromium plating and subsequent polishing shall not affect thefinalfinish beyond the tolerance stated in8.3.2.8.4Oven,conforming to the specification for a Type IIB laboratory oven given in Specification E145.8.4.1Type IIB ovens specified in Test Method E145are satisfactory for use through70°C.For higher Temperatures Type II A ovens are necessary.8.4.2The interior size shall be as follows or of an equivalent volume:TABLE2Type1Precision Results,%Compression Set—TestMethod BMaterial MeanLevelWithin Laboratory A Between Laboratory AS r r(r)S R R(R)113.7(%)0.591 1.6712.2 1.54 4.3631.8 252.80.567 1.60 3.0 5.9216.831.7 A Sr=within laboratory standard deviation.r=repeatability(in measurement units).(r)=repeatability(in percent).S R=between laboratory standard deviation.R=reproducibility(in measurement units).(R)=reproducibility(in percent).Interior size of air oven:min.300bt300mm by300mm(12by12by12in.)max.900by900by1200mm(36by36by48in.) 8.4.3Provision shall be made for placing test specimens in the oven without touching each other or the sides of the aging chamber.8.4.4The heating medium for the aging chamber shall be air circulated within it at atmospheric pressure.8.4.5The source of heat is optional but shall be located in the air supply outside of the aging chamber.8.4.6A suitable temperature measurement device located in the upper central portion of the chamber near the test speci-mens shall be provided to record the actual aging temperature.8.4.7Automatic temperature control by means of thermo-static regulation shall be used.8.4.8The following special precautions shall be taken in order that accurate,uniform heating is obtained in all parts of the aging chamber.8.4.8.1The heated air shall be thoroughly circulated in the oven by means of mechanical agitation.When a motor driven fan is used,the air must not come in contact with the fan motor brush discharge because of danger of ozone formation.8.4.8.2Baffles shall be used as required to prevent local overheating and dead spots.8.4.8.3The thermostatic control device shall be so located as to give accurate temperature control of the heating medium. The preferred location is adjacent to the temperature measuring device listed in section8.4.6.8.4.8.4An actual check shall be made by means of maxi-mum reading thermometers placed in various parts of the oven to verify the uniformity of the heating.9.Procedure9.1Original Thickness Measurement—Measure the original thickness of the specimen to the nearest0.02mm(0.001in.). Place the specimen on the anvil of the dial micrometer so that the presser foot will indicate the thickness at the central portion of the top and bottom faces.9.2Application of Compressive Force—Assemble the specimens in the compression device,using extreme care to place them exactly in the center between the plates to avoid tilting.If the calibrated spring device(see Fig.1)is used,apply the compressive force by tightening the screw until the deflection as read from the scale is equivalent to that shown on the calibration curve for the spring corresponding to a force of 1.8kN(400lbf).With the external loading device(see Fig.2), apply this force to the assembly in the compression machine or by adding required masses,but in the latter case,take care to add the mass gradually without shock.Tighten the nuts and bolts just sufficiently to hold the initial deflections of the specimen and spring.It is imperative that no additional force be applied in tightening the bolts.9.3Test Time and Test Temperature—Choose a suitable temperature and time for the compression set,depending upon the conditions of the expected service.In comparative tests,use identical temperature and heating periods.It is suggested that the test temperature be chosen from those listed in Practice D1349.Suggested test periods are22h and70h.The specimen shall be at room temperature when inserted in the compression device.Place the assembled compression device in the oven within2h after completion of the assembly and allow it to remain there for the required test period in dry air at the test temperature selected.At the end of the test period,take the device from the oven and remove the specimens immedi-ately and allow it to cool.9.4Cooling Period—While cooling,allow the specimens to rest on a poor thermally conducting surface,such as wood,for 30min before making the measurement of thefinal thickness. Conduct the cooling period at a standard laboratory tempera-ture of2362°C(73.463.6°F).Specimens whose compres-sion set property is affected by atmospheric moisture shall be cooled in an atmosphere controlled to5065%relative humidity.9.5Final Thickness Measurement—After the rest period, measure thefinal thickness at the center of the specimen in accordance with9.1.10.Calculation10.1Calculate the compression set as a percentage of the original thickness as follows:C A5@~t o2t i!/t o#3100(1) where:C A=Compression set(Test Method A)as a percentage ofthe original thickness,t o=original thickness(see9.1),andt i=final thickness (see 9.5).11.Report11.1Report the following information:11.1.1Original dimensions of the test specimen,including the original thickness,t o ,11.1.2Actual compressive force on the specimen as deter-mined from the calibration curve of the spring and spring deflection reading (see 8.2.1)or as applied by an external force (see 8.2.2),11.1.3Thickness of the test specimen 30min after removal from the clamp,t i ,11.1.4Type of test specimen used,together with the time and temperature of test,11.1.5Compression set,expressed as a percentage of the original thickness,11.1.6Test method used (Test Method A),and 11.1.7Number of specimens tested.TEST METHOD B—COMPRESSION SET UNDERCONSTANT DEFLECTION IN AIR 12.Apparatus12.1Dial Micrometer —A dial micrometer,for measuring the specimen thickness,in accordance with Practice D 3767,Method A 1.N OTE 3—For vulcanizates having a hardness below 35IRHD,the force on the presser foot should be reduced to 0.260.05N (0.0460.01lbf).12.2Spacer Bars ,to maintain the constant deflection re-quired under Test Method B.12.2.1Spacer bars for Type 1samples shall have a thickness of 9.560.02mm (0.37560.001in.).12.2.2Spacer bars for Type 2samples shall have a thickness of 4.5060.01mm (0.177060.0005in.).12.3Compression Device ,consisting of two or more flat steel plates between the parallel faces of which the specimens may be compressed as shown in Fig.3.Steel spacers for the required percentage of compression given in 13.2shall be placed on each side of the rubber specimens to control their thickness while compressed.12.4Oven ,see 8.4.12.5Plates —The plates between which the test specimen is compressed shall be made of steel of sufficient thickness to withstand the compressive stresses without bending.12.5.1The surfaces against which the specimen is held shall have a chromium-plated finish and shall be cleaned thoroughly and wiped dry before each test.12.5.2The steel surfaces contacting the rubber specimens shall be ground to a maximum roughness of 250µm (10µin.)and then chromium plated and polished.12.5.3The chromium plating and subsequent polishing shall not affect the final finish beyond the tolerance stated in 12.5.2.13.Procedure13.1Original Thickness Measurement —Measure the origi-nal thickness of the specimen to the nearest 0.02mm (0.001in.).Place the specimen on the anvil of the dial micrometer so that the presser foot will indicate the thickness at the central portion of the top and bottom faces.13.2Application of Compressive Force —Place the test specimen between the plates of the compression device with the spacers on each side,allowing sufficient clearance for the bulging of the rubber when compressed (see Fig.3).Where a lubricant is applied,it shall consist of a thin coating of a lubricant having substantially no action on the rubber.For most purposes,a silicon or fluorosilicon fluid is suitable.Tighten the bolts so that the plates are drawn together uniformly until they are in contact with the spacers.The amount of compression employed shall be approximately 25%.A suitable mechanical or hydraulic device may be used to facilitate assembling and disassembling the test fixture.13.3Test Time and Temperature —Choose a suitable tem-perature and time for the compression set,depending upon the conditions of the expected service.In comparative tests,use identical temperature and test periods.It is suggested that the test temperature be chosen from those listed in Practice D 1349.Suggested test periods are 22h and 70h.The test specimen shall be at room temperature when inserted in the compression device.Place the assembled compression device in the oven within 2h after completion of the assembly and allow it to remain there for the required test period in dry air at the test temperature selected.At the end of the test period,take the device from the oven and remove the test specimen immediately and allow them to cool.13.4Cooling Period —While cooling,allow the test speci-men to rest on a poor thermally conducting surface,such as wood,for 30min before making the measurement of the final thickness.Maintain the conditions during the cooling period in accordance with 9.4.13.5Final Thickness Measurement —After the rest period,measure the final thickness at the center of the test specimen in accordance with 13.1.14.Calculation14.1Calculate the compression set expressed as a percent-age of the original deflection as follows:C B 5@~t o 2t i !/~t o 2t n !#3100(2)where:C B =compression set (Test Method B)expressed aspercentage of the original deflection,t 0=original thickness of specimen (13.1),t i =final thickness of specimen (13.5),and t n =thickness of the spacer bar used.N OTE 4—Lubrication of the operating surfaces of thecompressionFIG.3Device for Compression Set Test Under ConstantDeflection,Test MethodBdevice is optional while giving more reproducible results;lubrication may somewhat alter the compression set values.15.Report15.1Report the following information:15.1.1Original dimensions of the test specimen including the original thickness,t o,15.1.2Percentage compression of the specimen actually employed,15.1.3Thickness of the test specimen30min after removal from the clamp,t i,15.1.4Type of test specimen used,together with the time and temperature of test,15.1.5Whether or not the surfaces of the compression device are lubricated.If they are,what type lubrication was used,15.1.6Compression set,expressed as a percentage of the original deflection,15.1.7Test method used(Test Method B),and15.1.8Number of specimens tested.16.Keywords16.1compression set;compression set under constant de-flection;compression set under constant force;deflection; deformation;elastic property;hysteresis;recoveryASTM International takes no position respecting the validity of any patent rights asserted in connection with any item mentioned in this ers of this standard are expressly advised that determination of the validity of any such patent rights,and the risk of infringement of such rights,are entirely their own responsibility.This standard is subject to revision at any time by the responsible technical committee and must be reviewed everyfive years and if not revised,either reapproved or withdrawn.Your comments are invited either for revision of this standard or for additional standards and should be addressed to ASTM International Headquarters.Your comments will receive careful consideration at a meeting of the responsible technical committee,which you may attend.If you feel that your comments have not received a fair hearing you should make your views known to the ASTM Committee on Standards,at the address shown below.This standard is copyrighted by ASTM International,100Barr Harbor Drive,PO Box C700,West Conshohocken,PA19428-2959, United States.Individual reprints(single or multiple copies)of this standard may be obtained by contacting ASTM at the above address or at610-832-9585(phone),610-832-9555(fax),or service@(e-mail);or through the ASTM website().。
压缩永久变形中文版

编号:D 395-03橡胶性能的标准试验方法----------压缩永久变形1此项标准在固定编号B 117下发布,紧随编号的数字表示标准采纳的年度,如果是修正,数字表示最后一次修正的年度。
在括号内的数字表示最后一次重申批准的年度。
上标 表示自最后一次修正或重申批准以来的编辑改动。
此项标准已被批准供美国国防部下属机构使用。
1范围1.1本测试方法测试应用中会在气体或液体媒介中承受压力的橡胶。
本测试方法特别适用于在机械固定器件,1.2测试方法可以选择,但是应考虑用于与测试结果关联的实际情况下使用的橡胶的性质。
除非在具体的规范中有其他规定,应使用测试方法B。
1.3测试方法B不适用于硬度大于90IRHD的硫化橡胶。
1.4以国际单位(SI)为单位的数值应被认为是标准。
在括号内的数值起参照作用。
1.5此项标准不包括与其应用有关的所有的安全隐患。
此项标准的使用者有责任在使用前建立合适的安全健康规范以及决定法规限制是否适用2 参考文件2.1 ASTM标准2:D1349 橡胶规范---测试的标准温度D 3182D 3183D 3767D 4483E 145---------------------------------------1此测试方法属于ASTM D 11橡胶委员会的工作范围,是其下属D11.10物理测试子委员会的直接责任。
目前的版本在2008.3.1批准,2008.07出版。
原始的版本在1934年批准。
上一个版本在2003年批准,编号为D395-03.2如需参照ASTM 标准,访问ASTM网站,. 如需要《ASTM标准年鉴》的内容信息,浏览ASTM网站的标准索引页。
3 测试方法概要3.1 用挠力或规定的力压缩试样,并在规定的温度下保持规定的时间。
3.2 在试样在合适的装置内,在规定的条件下经过特定时间的压缩变形后,取出试样,等待30分钟,测量试样的残留变形。
3.3 在测量残留变形后,根据Eq1和Eq2计算压缩永久变形。
压缩永久变形测试标准

压缩永久变形测试标准
压缩永久变形测试标准是指在材料的使用过程中,经受压缩后能够保持永久变
形的能力。
对于不同类型的材料,其压缩永久变形测试标准也有所不同。
本文将介绍压缩永久变形测试的一般标准和常见测试方法。
首先,压缩永久变形测试的一般标准包括测试条件、测试方法、测试设备和测
试步骤等内容。
在进行压缩永久变形测试时,首先需要确定测试条件,包括温度、湿度、压力等因素。
其次是选择合适的测试方法,常见的测试方法包括静态压缩测试和动态压缩测试。
在进行测试时,需要使用合适的测试设备,如万能材料试验机、压缩试验机等。
最后是测试步骤,包括样品制备、测试前处理、测试过程记录等。
其次,静态压缩测试是常见的压缩永久变形测试方法之一。
在进行静态压缩测
试时,需要将样品放置在测试设备上,施加一定的压力并保持一定的时间,然后观察样品的变形情况。
通过静态压缩测试可以得到材料在一定压力下的永久变形情况,为材料的设计和选用提供重要参考。
另外,动态压缩测试是另一种常见的压缩永久变形测试方法。
与静态压缩测试
不同的是,动态压缩测试是在不同频率下施加压力,观察材料的动态变形情况。
通过动态压缩测试可以得到材料在动态载荷下的永久变形情况,为材料的疲劳寿命和可靠性评定提供重要依据。
综上所述,压缩永久变形测试标准是材料测试中的重要内容之一,对于材料的
设计和选用具有重要意义。
通过对压缩永久变形测试的标准和方法的了解,可以更好地评定材料的性能和可靠性,为工程实践提供科学依据。
希望本文的介绍能够对压缩永久变形测试标准有所帮助,谢谢阅读!。
ASTM D395-2003压缩永久变形中文版

编号:D 395-03橡胶性能的标准试验方法----------压缩永久变形1此项标准在固定编号B 117下发布,紧随编号的数字表示标准采纳的年度,如果是修正,数字表示最后一次修正的年度。
在括号内的数字表示最后一次重申批准的年度。
上标 表示自最后一次修正或重申批准以来的编辑改动。
此项标准已被批准供美国国防部下属机构使用。
1范围1.1本测试方法测试应用中会在气体或液体媒介中承受压力的橡胶。
本测试方法特别适用于在机械固定器件,减震器,封条中使用的橡胶。
本测试方法包含以下两种方法:1.2测试方法可以选择,但是应考虑用于与测试结果关联的实际情况下使用的橡胶的性质。
除非在具体的规范中有其他规定,应使用测试方法B。
1.3测试方法B不适用于硬度大于90IRHD的硫化橡胶。
1.4以国际单位(SI)为单位的数值应被认为是标准。
在括号内的数值起参照作用。
1.5此项标准不包括与其应用有关的所有的安全隐患。
此项标准的使用者有责任在使用前建立合适的安全健康规范以及决定法规限制是否适用2 参考文件2.1 ASTM标准2:D1349 橡胶规范---测试的标准温度D 3182 混合标准化合物及制备标准硫化橡胶薄片用橡胶材料、设备及工序的标准实施规程D 3183 橡胶实施规范---从橡胶制品中制备试验目的用试片D 3767 橡胶的标准规程----尺寸测量D 4483 评定橡胶和炭黑制造工业试验方法标准的精度的实施规程E 145 重力对流式和强制通风式烘炉的规范---------------------------------------1此测试方法属于ASTM D 11橡胶委员会的工作范围,是其下属D11.10物理测试子委员会的直接责任。
目前的版本在2008.3.1批准,2008.07出版。
原始的版本在1934年批准。
上一个版本在2003年批准,编号为D395-03.2如需参照ASTM 标准,访问ASTM网站,或联系ASTM客户服务****************. 如需要《ASTM标准年鉴》的内容信息,浏览ASTM网站的标准索引页。
硅胶压缩永久变形测试标准SOP

硅胶压缩永久变形测试标准SOP在硅胶压缩永久变形率测定方面,经常采用的标准试验方法主要有4种:国际标准ISO 815-1:2008、美国材料与试验协会标准ASTM D395-03、日本工业标准JIS K6262:2013以及中国国家标准GB/T 77591996(1)ISO 815-120080(常温或高温条件下,硫化硅胶或热塑性硅胶压缩永久变形测定):ISO 815于1972年由国际化标准组织制定(ISO 815:19722),于1991年进行了修订,将ISO 815:1972规定的室温和高温下,压缩永久变形试验与ISO 1653:1975规定的低温下压缩永久变形试验进行统一合并,把压缩永久变形试验,从低温到高温归纳成一个标准ISO 815:进行了再次修订,此次修订将常温和高温条件下压缩永久变形与低温条件下压缩永久变形再次分开,形成了2个标准,即ISO 815-1和ISO815-2(2)ASTM D395-03(硅胶性能的标准试验方法一压缩永久变形):ASTM D395标准制定于1998年,分别于2001年、2002年和2003年进行了修订,现行有效版本为ASTM D395-03.ASTM D395-03规定了A和B共2种试验方法,方法A为空气中恒定压力条件下的压缩永久变形率测定方法,方法B为空气中恒定压缩比条件下压缩永久变形率测定方法",鉴于国内很少选用A方法,所以本文的内容仅涉及方法(3)JIS K6262:2013(硫化硅胶、热塑性硅胶常温、高温和低温下压缩永久变形测定):JS K6262源于JIS K6301(硫化硅胶物理性能试验方法,包括拉伸性能、硬度、撕裂性能和压缩永久变形率等共18种性能测试方法)0,日本工业标准调查会于1993年将JIS K6301中压缩永久变形测试方法独立出来,并等效采用了ISO 815:1972,同时,添加了拉伸永久变形测定的内容(等效采用ISO 2285:1988)形成了JIS K62621993。
橡胶和热塑性弹性体压缩永久变形阐述和解决方案
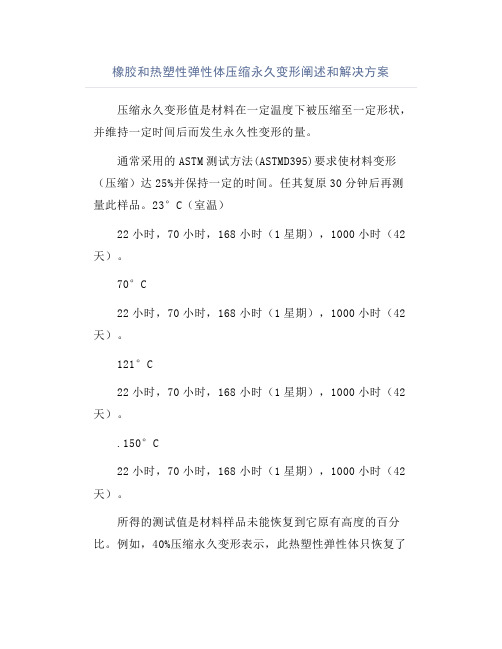
橡胶和热塑性弹性体压缩永久变形阐述和解决方案压缩永久变形值是材料在一定温度下被压缩至一定形状,并维持一定时间后而发生永久性变形的量。
通常采用的ASTM测试方法(ASTMD395)要求使材料变形(压缩)达25%并保持一定的时间。
任其复原30分钟后再测量此样品。
23°C(室温)22小时,70小时,168小时(1星期),1000小时(42天)。
70°C22小时,70小时,168小时(1星期),1000小时(42天)。
121°C22小时,70小时,168小时(1星期),1000小时(42天)。
.150°C22小时,70小时,168小时(1星期),1000小时(42天)。
所得的测试值是材料样品未能恢复到它原有高度的百分比。
例如,40%压缩永久变形表示,此热塑性弹性体只恢复了被压缩厚度的60%。
100%压缩永久变形则表示此热塑性弹性体无丝毫恢复,也就是说,它保持了被压缩的状态。
往往压缩永久变形易与蠕变相混淆。
然而,压缩永久变形是在某一恒定的应变条件下所发生变形的量,而蠕变则是在某一恒定应力条件下所发生变形的量。
变形是橡胶制品的重要性能指标之一。
硫化橡胶压缩永久变形的大小,涉及到硫化橡胶的弹性与恢复。
有些人往往简单地认为橡胶的弹性好,其恢复就快,永久变形就小。
这种理解是不够的,弹性与恢复是相互关联的两种性质。
但有时候,橡胶的本质没有发生根本的变化,永久变形的大小主要是受橡胶恢复能力的变化所支配。
影响恢复能力的因素有分子之问的作用力(粘性)、网络结构的变化或破坏、分子问的位移等。
当橡胶的变形是由于分子链的伸张引起的,它的恢复(或永久变形的大小)主要由橡胶的弹性所决定:如果橡胶的变形还伴有网络的破坏和分子链的相对流动,这部分可以说是不可恢复的,它是与弹性无关的。
所以,凡是影响橡胶弹性与恢复的因素,都是影响硫化橡胶压缩永久变形的因素。
有几个概念,如弹性、打击弹性(回弹性)、弹性与模量、压缩永久变形、扯断永久变形等,它们之间的关系,不易表述清楚,现将个人的理解提出与大家讨论。
ASTM_D395_2003压缩永久变形中文版

编号:D 395-03橡胶性能的标准试验方法----------压缩永久变形1此项标准在固定编号B 117下发布,紧随编号的数字表示标准采纳的年度,如果是修正,数字表示最后一次修正的年度。
在括号的数字表示最后一次重申批准的年度。
上标 表示自最后一次修正或重申批准以来的编辑改动。
此项标准已被批准供美国国防部下属机构使用。
1围1.1本测试方法测试应用中会在气体或液体媒介中承受压力的橡胶。
本测试方法特别适用于在机械固定器件,减震器,封条中使用的橡胶。
本测试方法包含以下两种方法:1.2测试方法可以选择,但是应考虑用于与测试结果关联的实际情况下使用的橡胶的性质。
除非在具体的规中有其他规定,应使用测试方法B。
1.3测试方法B不适用于硬度大于90IRHD的硫化橡胶。
1.4以国际单位(SI)为单位的数值应被认为是标准。
在括号的数值起参照作用。
1.5此项标准不包括与其应用有关的所有的安全隐患。
此项标准的使用者有责任在使用前建立合适的安全健康规以及决定法规限制是否适用2 参考文件2.1 ASTM标准2:D1349 橡胶规---测试的标准温度D 3182 混合标准化合物及制备标准硫化橡胶薄片用橡胶材料、设备及工序的标准实施规程D 3183 橡胶实施规---从橡胶制品中制备试验目的用试片D 3767 橡胶的标准规程----尺寸测量D 4483 评定橡胶和炭黑制造工业试验方法标准的精度的实施规程E 145 重力对流式和强制通风式烘炉的规---------------------------------------1此测试方法属于ASTM D 11橡胶委员会的工作围,是其下属D11.10物理测试子委员会的直接责任。
目前的版本在2008.3.1批准,2008.07出版。
原始的版本在1934年批准。
上一个版本在2003年批准,编号为D395-03.2如需参照ASTM 标准,访问,或联系ASTM客户服务. 如需要《ASTM标准年鉴》的容信息,浏览ASTM的标准索引页。
【免费下载】ASTM D395 压缩永久变形中文版

7.5 偏差---在测试方法统计术语里。
偏差是指测试平均值与参考或实际性能值的差异。
因为所测性能的值完全由此测试方法定义,所以不存在参考值。
应此,偏差不能被测定。
测试方法A---------空气中恒定力下的压力永久变形8 装置8.1 千分测试盘-------根据规范D3767,方法A1的用于测量试样厚度的千分测试盘8.2 压力装置由施力弹簧,两个平行的压力片组成。
压力装置由框架或螺纹螺栓固定。
压力装置的装配方法应使其可移动,并在施力后能够保持压力片的平行。
施加的力应符合8.2.1或8.2.2的规定。
8.2已校施力弹簧------应使用螺丝钉装置向已校弹簧施力。
弹簧应由经合适热处理的弹簧钢制成,弹簧应磨平,磨平面与弹簧长轴垂直。
图1 是一个合适的压力装置。
弹簧应符合以下要求:8.2.1.1 弹簧应在室温23 ±5℃(73.4±9℉)下校正。
连续施以递增的力[递增幅度不超过250N(50lbf)],测量相应的变形长度,取精度为0.2mm(0.01in.)。
在1.8kN(400lbf)的力下,力与变形距离的曲线的斜率应为70±3.5kN/m(400±20lbf/in.) 斜率用相应的变形长度除以1.8kN上下的两个力获得。
8.2.1.2 在弹簧被装入压力装置,在1.8kN(400lbf)的力下被压缩,在温度为70±2℃(158±3.6℉)的热空气炉中加热一周后,由于疲劳造成弹簧原始尺寸的变化不应超过3mm(0.01in.)。
在常规的使用中,在一年的时长内,每周对尺寸的检查得出的尺寸变化不应超过上述值。
8.2.1.3 压紧弹簧(压至各线圈接触)所需的最小力应为2.4kN(530lbf).图1 压力永久变形测试方法A使用的带有已校弹簧压力装置8.2.2 外部力的施加------在试样装入装置后,应向压力片和弹簧施加必要的外部力。
可以使用已校的压力器械或已知重量的重物。
- 1、下载文档前请自行甄别文档内容的完整性,平台不提供额外的编辑、内容补充、找答案等附加服务。
- 2、"仅部分预览"的文档,不可在线预览部分如存在完整性等问题,可反馈申请退款(可完整预览的文档不适用该条件!)。
- 3、如文档侵犯您的权益,请联系客服反馈,我们会尽快为您处理(人工客服工作时间:9:00-18:30)。
Designation:D395–02Standard Test Methods forRubber Property—Compression Set1This standard is issued under thefixed designation D395;the number immediately following the designation indicates the year of original adoption or,in the case of revision,the year of last revision.A number in parentheses indicates the year of last reapproval.A superscript epsilon(e)indicates an editorial change since the last revision or reapproval.This standard has been approved for use by agencies of the Department of Defense.1.Scope1.1These test methods cover the testing of rubber intended for use in applications in which the rubber will be subjected to compressive stresses in air or liquid media.They are applicable particularly to the rubber used in machinery mountings,vibra-tion dampers,and seals.Two test methods are covered as follows:Test Method Section A—Compression Set Under Constant Force in Air7–10B—Compression Set Under Constant Deflection in Air11–14 1.2The choice of test method is optional,but consideration should be given to the nature of the service for which correlation of test results may be sought.Unless otherwise stated in a detailed specification,Test Method B shall be used.1.3Test Method B is not suitable for vulcanizates harder than90IRHD.1.4The values stated in SI units are to be regarded as the standard.1.5This standard does not purport to address all of the safety concerns,if any,associated with its use.It is the responsibility of the user of this standard to establish appro-priate safety and health practices and determine the applica-bility of regulatory limitations prior to use.2.Referenced Documents2.1ASTM Standards:D1349Practice for Rubber—Standard Temperatures for Testing2D3182Practice for Rubber—Materials,Equipment,and Procedures for Mixing Standard Compounds and Prepar-ing Standard Vulcanized Sheets2D3183Practice for Rubber—Preparation of Pieces for Test Purposes from Products2D3767Practice for Rubber—Measurement of Dimensions2 D4483Practice for Determining Precision for Test Meth-ods Standards in the Rubber and Carbon Black Industries2E145Specification for Gravity-Convection and Forced-Ventilation Ovens33.Summary of Test Methods3.1A test specimen is compressed to either a deflection or by a specified force and maintained under this condition for a specified time and at a specified temperature.3.2The residual deformation of a test specimen is measured 30min after removal from a suitable compression device in which the specimen had been subjected for a definite time to compressive deformation under specified conditions.3.3After the measurement of the residual deformation,the compression set,as specified in the appropriate test method,is calculated according to Eq1and Eq2.4.Significance and Use4.1Compression set tests are intended to measure the ability of rubber compounds to retain elastic properties after pro-longed action of compressive stresses.The actual stressing service may involve the maintenance of a definite deflection, the constant application of a known force,or the rapidly repeated deformation and recovery resulting from intermittent compressive forces.Though the latter dynamic stressing,like the others,produces compression set,its effects as a whole are simulated more closely by compressionflexing or hysteresis tests.Therefore,compression set tests are considered to be mainly applicable to service conditions involving static stresses.Tests are frequently conducted at elevated tempera-tures.5.Test Specimens5.1Specimens from each sample may be tested in duplicate (Option1)or triplicate(Option2).The compression set of the sample in Option1shall be the average of the two specimens expressed as a percentage.The compression set of the sample in Option2shall be the median(middle most value)of the three specimens expressed as a percentage.5.2The standard test specimen shall be a cylindrical disk cut from a laboratory prepared slab.5.2.1The dimensions of the standard specimens shall be:1These test methods are under the jurisdiction of ASTM Committee D11onRubber and are the direct responsibility of Subcommittee D11.10on PhysicalTesting.Current edition approved Dec.10,2002.Published January2003.Originallyapproved st previous edition approved in2001as D395–01.2Annual Book of ASTM Standards,V ol09.01.3Annual Book of ASTM Standards,V ol14.04.1Copyright©ASTM International,100Barr Harbor Drive,PO Box C700,West Conshohocken,PA19428-2959,United States.Type1A2BThickness,mm(in.)12.560.5(0.4960.02)6.060.2 (0.2460.01)Diameter,mm(in.)29.060.5(1.1460.02)13.060.2 (0.5160.01)A Type1specimen is used in Test Methods A and B.B Type2specimen is used in Test Method B.5.2.2When cutting the standard specimen,the circular die having the required inside dimensions specified in5.2.1shall be rotated in a drill press or similar device and lubricated by means of a soap solution.A minimum distance of13mm(0.51 in.)shall be maintained between the cutting edge of the die and the edge of the slab.The cutting pressure shall be as light as possible to minimize cupping of the cut edges.The dies shall be maintained carefully so that the cutting edges are sharp and free of nicks.5.3An optional method of preparing the standard specimen may be the direct molding of a circular disk having the dimensions required for the test method used and specified in 5.2.1.N OTE1—It should be recognized that an equal time and temperature,if used for both the slab and molded specimen,will not produce an equivalent state of cure in the two types of specimen.A higher degree of cure will be obtained in the molded specimen.Adjustments,preferably in the time of cure,must be taken into consideration if comparisons between the specimens prepared by different methods are to be considered valid. N OTE2—It is suggested,for the purpose of uniformity and closer tolerances in the molded specimen,that the dimensions of the mold be specified and shrinkage compensated for therein.A two-plate mold with a cavity13.060.1mm(0.51060.004in.)in thickness and29.2060.05 mm(1.14860.002in.)in diameter,with overflow grooves,will provide Type1specimens for Test Method A and Test Method B.A similar mold but having a cavity of6.360.3mm(0.2560.012in.)in thickness and 13.260.1mm(0.5260.004in.)in diameter will provide Type2 specimens for Test Method B.5.4When the standard test specimen is to be replaced by a specimen taken from a vulcanized rubber part of greater thickness than the one indicated in5.2.1,the sample thickness shall be reducedfirst by cutting transversely with a sharp knife and then followed by buffing to the required thickness in accordance with Practice D3183.5.5An alternative method of preparing specimens is by plying up cylindrical disks cut from a standard sheet prepared in accordance with Practice D3182using the specimen sizes specified in5.2.1and cutting as described in5.2.2,or where a drill press is not available cutting the specimens with a single stroke from a cutting die.5.5.1The disks shall be plied,without cementing,to the thickness required.Such plies shall be smooth,flat,of uniform thickness,and shall not exceed seven in number for Type1 specimens and four in number for Type2specimens.5.5.2Care shall be taken during handling and placing of the plied test specimen in the testfixture by keeping the circular faces parallel and at right angles to the axis of the cylinder.5.5.3The results obtained on plied specimens may be different from those obtained using solid specimens and the results may be variable,particularly if air is trapped between disks.5.5.4The results obtained on the specimens prepared by one of the methods may be compared only to those prepared by the same method.5.6For routine or product specification testing,it is some-times more convenient to prepare specimens of a different size or shape,or both.When such specimens are used,the results should be compared only with those obtained from specimens of similar size and shape and not with those obtained with standard specimen.For such cases,the product specification should define the specimen as to the size and shape.If suitable specimens cannot be prepared from the product,the test method and allowable limits must be agreed upon between the producer and the purchaser.6.Conditioning6.1Store all vulcanized test specimens or product samples to be tested at least24h but not more than60days.When the date of vulcanization is not known,make tests within60days after delivery by the producer of the article represented by the specimen.6.2Allow buffed specimens to rest at least30min before specimens are cut for testing.6.3Condition all specimens before testing for a minimum of 3h at2362°C(73.463.6°F).Specimens whose compression set properties are affected by atmospheric moisture shall be conditioned for a minimum of24h in an atmosphere controlled to5065%relative humidity.7.Precision and Bias47.1These precision statements have been prepared in ac-cordance with Practice D4483.Please refer to Practice D4483 for terminology and other testing and statistical concepts.7.2Prepared test specimens of two rubbers for Test MethodsA andB were supplied tofive laboratories.These were tested in duplicate each day on two separate testing days.A test result, therefore,is the average of two test specimens,for both Test Methods A and B.7.3One laboratory did not run the Test Method A testing; therefore,the precision for Test Method A is derived from four laboratories.7.4The Type1precision results are given in Table1and Table2.4Supporting data are available from ASTM Headquarters.Request RR: D11–1138.TABLE1Type1Precision Results,%Compression Set—TestMethod AMaterialMeanLevelWithin Laboratory A Between Laboratory AS r r(r)S R R(R)1 1.73(%)0.0500.1428.20.1900.5431.1 226.10.898 2.549.7 2.37 6.7125.7A Sr=within laboratory standard deviation.r=repeatability(in measurement units).(r)=repeatability(in percent).S R=between laboratory standard deviation. R=reproducibility(in measurement units). (R)=reproducibility(in percent).7.5Bias—In test method statistical terminology,bias is the difference between an average test value and the reference or true test property value.Reference values do not exist for these test methods since the value or level of the test property is exclusively defined by the test method.Bias,therefore,cannot be determined.TEST METHOD A—COMPRESSION SET UNDERCONSTANT FORCE IN AIR8.Apparatus8.1Dial Micrometer—A dial micrometer,for measuring specimen thickness,in accordance with Practice3767,Method A1.8.2Compression Device,consisting of a force application spring and two parallel compression plates assembled bymeans of a frame or threaded bolt in such a manner that the device shall be portable and self-contained after the force has been applied and that the parallelism of the plates shall be maintained.The force may be applied in accordance with either 8.2.1or8.2.2.8.2.1Calibrated Spring Force Application—The required force shall be applied by a screw mechanism for compressing a calibrated spring the proper amount.The spring shall be of properly heat-treated spring steel with ends ground and per-pendicular to the longitudinal axis of the spring.A suitable compression device is shown in Fig. 1.The spring shall conform to the following requirements:8.2.1.1The spring shall be calibrated at room temperature 2365°C(73.469°F)by applying successive increments of force not exceeding250N(50lbf)and measuring the corresponding deflection to the nearest0.2mm(0.01in.).The curve obtained by plotting the forces against the corresponding deflections shall have a slope of7063.5kN/m(400620 lbf/in.)at1.8kN(400lbf).The slope is obtained by dividing the two forces above and below1.8kN by the difference between the corresponding deflections.8.2.1.2The original dimensions of the spring shall not change due to fatigue by more than0.3mm(0.01in.)after it has been mounted in the compression device,compressed under a force of1.8kN(400lbf),and heated in the oven for one week at70°C62°C(15863.6°F).In ordinary use,a weekly check of the dimensions shall show no greater change than this over a period of1year.8.2.1.3The minimum force required to close the spring (solid)shall be2.4kN(530lbf).8.2.2External Force Application—The required force shall be applied to the compression plates and spring by external means after the test specimen is mounted in the apparatus. Either a calibrated compression machine or known masses may be used for force application.Provision shall be made by the use of bolts and nuts or other devices to prevent the specimen and spring from losing their initial deflections when the external force is removed.The spring shall have essentially the same characteristics as described in8.2.1,but calibration is not required.A suitable compression device is shown in Fig.2.8.3Plates—The plates between which the test specimen is compressed shall be made of steel of sufficient thickness to withstand the compressive stresses without bending.8.3.1The surfaces against which the specimen is held shall have a chromium platedfinish and shall be cleaned thoroughly and wiped dry before each test.8.3.2The steel surfaces contacting the rubber specimens shall be ground to a maximum roughness of250µm(10µin.) and then chromium plated and polished.8.3.3The chromium plating and subsequent polishing shall not affect thefinalfinish beyond the tolerance stated in8.3.2.8.4Oven,conforming to the specification for a Type IIB laboratory oven given in Specification E145.8.4.1Type IIB ovens specified in Test Method E145are satisfactory for use through70°C.For higher Temperatures Type II A ovens are necessary.8.4.2The interior size shall be as follows or of an equivalent volume:TABLE2Type1Precision Results,%Compression Set—TestMethod BMaterial MeanLevelWithin Laboratory A Between Laboratory AS r r(r)S R R(R)113.7(%)0.591 1.6712.2 1.54 4.3631.8 252.80.567 1.60 3.0 5.9216.831.7 A Sr=within laboratory standard deviation.r=repeatability(in measurement units).(r)=repeatability(in percent).S R=between laboratory standard deviation.R=reproducibility(in measurement units).(R)=reproducibility(in percent).Interior size of air oven:min.300bt300mm by300mm(12by12by12in.)max.900by900by1200mm(36by36by48in.) 8.4.3Provision shall be made for placing test specimens in the oven without touching each other or the sides of the aging chamber.8.4.4The heating medium for the aging chamber shall be air circulated within it at atmospheric pressure.8.4.5The source of heat is optional but shall be located in the air supply outside of the aging chamber.8.4.6A suitable temperature measurement device located in the upper central portion of the chamber near the test speci-mens shall be provided to record the actual aging temperature.8.4.7Automatic temperature control by means of thermo-static regulation shall be used.8.4.8The following special precautions shall be taken in order that accurate,uniform heating is obtained in all parts of the aging chamber.8.4.8.1The heated air shall be thoroughly circulated in the oven by means of mechanical agitation.When a motor driven fan is used,the air must not come in contact with the fan motor brush discharge because of danger of ozone formation.8.4.8.2Baffles shall be used as required to prevent local overheating and dead spots.8.4.8.3The thermostatic control device shall be so located as to give accurate temperature control of the heating medium. The preferred location is adjacent to the temperature measuring device listed in section8.4.6.8.4.8.4An actual check shall be made by means of maxi-mum reading thermometers placed in various parts of the oven to verify the uniformity of the heating.9.Procedure9.1Original Thickness Measurement—Measure the original thickness of the specimen to the nearest0.02mm(0.001in.). Place the specimen on the anvil of the dial micrometer so that the presser foot will indicate the thickness at the central portion of the top and bottom faces.9.2Application of Compressive Force—Assemble the specimens in the compression device,using extreme care to place them exactly in the center between the plates to avoid tilting.If the calibrated spring device(see Fig.1)is used,apply the compressive force by tightening the screw until the deflection as read from the scale is equivalent to that shown on the calibration curve for the spring corresponding to a force of 1.8kN(400lbf).With the external loading device(see Fig.2), apply this force to the assembly in the compression machine or by adding required masses,but in the latter case,take care to add the mass gradually without shock.Tighten the nuts and bolts just sufficiently to hold the initial deflections of the specimen and spring.It is imperative that no additional force be applied in tightening the bolts.9.3Test Time and Test Temperature—Choose a suitable temperature and time for the compression set,depending upon the conditions of the expected service.In comparative tests,use identical temperature and heating periods.It is suggested that the test temperature be chosen from those listed in Practice D1349.Suggested test periods are22h and70h.The specimen shall be at room temperature when inserted in the compression device.Place the assembled compression device in the oven within2h after completion of the assembly and allow it to remain there for the required test period in dry air at the test temperature selected.At the end of the test period,take the device from the oven and remove the specimens immedi-ately and allow it to cool.9.4Cooling Period—While cooling,allow the specimens to rest on a poor thermally conducting surface,such as wood,for 30min before making the measurement of thefinal thickness. Conduct the cooling period at a standard laboratory tempera-ture of2362°C(73.463.6°F).Specimens whose compres-sion set property is affected by atmospheric moisture shall be cooled in an atmosphere controlled to5065%relative humidity.9.5Final Thickness Measurement—After the rest period, measure thefinal thickness at the center of the specimen in accordance with9.1.10.Calculation10.1Calculate the compression set as a percentage of the original thickness as follows:C A5@~t o2t i!/t o#3100(1) where:C A=Compression set(Test Method A)as a percentage ofthe original thickness,t o=original thickness(see9.1),andt i=final thickness (see 9.5).11.Report11.1Report the following information:11.1.1Original dimensions of the test specimen,including the original thickness,t o ,11.1.2Actual compressive force on the specimen as deter-mined from the calibration curve of the spring and spring deflection reading (see 8.2.1)or as applied by an external force (see 8.2.2),11.1.3Thickness of the test specimen 30min after removal from the clamp,t i ,11.1.4Type of test specimen used,together with the time and temperature of test,11.1.5Compression set,expressed as a percentage of the original thickness,11.1.6Test method used (Test Method A),and 11.1.7Number of specimens tested.TEST METHOD B—COMPRESSION SET UNDERCONSTANT DEFLECTION IN AIR 12.Apparatus12.1Dial Micrometer —A dial micrometer,for measuring the specimen thickness,in accordance with Practice D 3767,Method A 1.N OTE 3—For vulcanizates having a hardness below 35IRHD,the force on the presser foot should be reduced to 0.260.05N (0.0460.01lbf).12.2Spacer Bars ,to maintain the constant deflection re-quired under Test Method B.12.2.1Spacer bars for Type 1samples shall have a thickness of 9.560.02mm (0.37560.001in.).12.2.2Spacer bars for Type 2samples shall have a thickness of 4.5060.01mm (0.177060.0005in.).12.3Compression Device ,consisting of two or more flat steel plates between the parallel faces of which the specimens may be compressed as shown in Fig.3.Steel spacers for the required percentage of compression given in 13.2shall be placed on each side of the rubber specimens to control their thickness while compressed.12.4Oven ,see 8.4.12.5Plates —The plates between which the test specimen is compressed shall be made of steel of sufficient thickness to withstand the compressive stresses without bending.12.5.1The surfaces against which the specimen is held shall have a chromium-plated finish and shall be cleaned thoroughly and wiped dry before each test.12.5.2The steel surfaces contacting the rubber specimens shall be ground to a maximum roughness of 250µm (10µin.)and then chromium plated and polished.12.5.3The chromium plating and subsequent polishing shall not affect the final finish beyond the tolerance stated in 12.5.2.13.Procedure13.1Original Thickness Measurement —Measure the origi-nal thickness of the specimen to the nearest 0.02mm (0.001in.).Place the specimen on the anvil of the dial micrometer so that the presser foot will indicate the thickness at the central portion of the top and bottom faces.13.2Application of Compressive Force —Place the test specimen between the plates of the compression device with the spacers on each side,allowing sufficient clearance for the bulging of the rubber when compressed (see Fig.3).Where a lubricant is applied,it shall consist of a thin coating of a lubricant having substantially no action on the rubber.For most purposes,a silicon or fluorosilicon fluid is suitable.Tighten the bolts so that the plates are drawn together uniformly until they are in contact with the spacers.The amount of compression employed shall be approximately 25%.A suitable mechanical or hydraulic device may be used to facilitate assembling and disassembling the test fixture.13.3Test Time and Temperature —Choose a suitable tem-perature and time for the compression set,depending upon the conditions of the expected service.In comparative tests,use identical temperature and test periods.It is suggested that the test temperature be chosen from those listed in Practice D 1349.Suggested test periods are 22h and 70h.The test specimen shall be at room temperature when inserted in the compression device.Place the assembled compression device in the oven within 2h after completion of the assembly and allow it to remain there for the required test period in dry air at the test temperature selected.At the end of the test period,take the device from the oven and remove the test specimen immediately and allow them to cool.13.4Cooling Period —While cooling,allow the test speci-men to rest on a poor thermally conducting surface,such as wood,for 30min before making the measurement of the final thickness.Maintain the conditions during the cooling period in accordance with 9.4.13.5Final Thickness Measurement —After the rest period,measure the final thickness at the center of the test specimen in accordance with 13.1.14.Calculation14.1Calculate the compression set expressed as a percent-age of the original deflection as follows:C B 5@~t o 2t i !/~t o 2t n !#3100(2)where:C B =compression set (Test Method B)expressed aspercentage of the original deflection,t 0=original thickness of specimen (13.1),t i =final thickness of specimen (13.5),and t n =thickness of the spacer bar used.N OTE 4—Lubrication of the operating surfaces of thecompressionFIG.3Device for Compression Set Test Under ConstantDeflection,Test MethodBdevice is optional while giving more reproducible results;lubrication may somewhat alter the compression set values.15.Report15.1Report the following information:15.1.1Original dimensions of the test specimen including the original thickness,t o,15.1.2Percentage compression of the specimen actually employed,15.1.3Thickness of the test specimen30min after removal from the clamp,t i,15.1.4Type of test specimen used,together with the time and temperature of test,15.1.5Whether or not the surfaces of the compression device are lubricated.If they are,what type lubrication was used,15.1.6Compression set,expressed as a percentage of the original deflection,15.1.7Test method used(Test Method B),and15.1.8Number of specimens tested.16.Keywords16.1compression set;compression set under constant de-flection;compression set under constant force;deflection; deformation;elastic property;hysteresis;recoveryASTM International takes no position respecting the validity of any patent rights asserted in connection with any item mentioned in this ers of this standard are expressly advised that determination of the validity of any such patent rights,and the risk of infringement of such rights,are entirely their own responsibility.This standard is subject to revision at any time by the responsible technical committee and must be reviewed everyfive years and if not revised,either reapproved or withdrawn.Your comments are invited either for revision of this standard or for additional standards and should be addressed to ASTM International Headquarters.Your comments will receive careful consideration at a meeting of the responsible technical committee,which you may attend.If you feel that your comments have not received a fair hearing you should make your views known to the ASTM Committee on Standards,at the address shown below.This standard is copyrighted by ASTM International,100Barr Harbor Drive,PO Box C700,West Conshohocken,PA19428-2959, United States.Individual reprints(single or multiple copies)of this standard may be obtained by contacting ASTM at the above address or at610-832-9585(phone),610-832-9555(fax),or service@(e-mail);or through the ASTM website().。