Abaqus 焊缝模拟分析实例
ABAQUS焊接领域解决方案

Q焊接领域解决方案ABAQUS1国内外焊接变形预测方法固有应变焊接预测法23基于热弹塑性理论的焊接预测法Ab4Abaqus针对焊接行业的解决方案自始至终安心托付1国内外焊接变形预测方法固有应变焊接预测法23基于热弹塑性理论的焊接预测法Ab4Abaqus针对焊接行业的解决方案自始至终安心托付焊接变形预测的重要性焊接是船舶制造最主要的加工手段,焊接水平的高低在很大程度上决定了船体的质量和生产效率,而焊接变形又是焊接过程中最中最难控制的一环。
焊接变形的影响:焊接结构形状变异,尺寸精度下降;承载能力降低;船体在工作载荷作用下引起的附加弯矩和应力集中作用下导致结果失效;船舶结构疲劳降低。
船舶结构疲劳降低因此,对焊接变形的预测及控制已成为船舶生产中迫切需要解决的重要课题。
自始至终安心托付国内外焊接变形的预测方法1.经验(试验)法经验(实验)法是通过试验建立经验公式和数据曲线,用经验公式和数据曲线来估计焊缝的收缩量和角变形量和数据曲线来估计焊缝的收缩量和角变形量。
局限性:z一定条件下的试验或生产实际中得到的,一般被限制在特定的变形模式上变形模式上;z实验受到时间和成本的限制。
真实结构的复杂焊接变形是由多个基本变形组合而成的。
每个基本变形不可能通过有限的实验结果来区分。
自始至终安心托付22.解析法解析法(弹性理论方法)是基于经典弹性理论,忽略热弹塑性的方法。
局限性:由于该方法是建立在平截面假定和其它一些假定的基础上局限性:由于该方法是建立在平截面假定和其它些假定的基础上的,故只能适用于一些焊接是通过熔化金属进行连接的工艺过程。
自始至终安心托付3.数值模拟法焊接数值模拟法又叫焊接计算机仿真,实际上就是热传导有限元解析法和非线性有限元应力解析的组合,已成为线性问题及塑性破坏等非线性问题解析非线性有限元应力解析的组合已成为线性问题及塑性破坏等非线性问题解析不可或缺的手段。
焊接数值模拟是以试验为基础,采用一组控制方程来描述一个焊接过程或个焊接过程的某方面,采用分析或数值方法求解以获得该过程的定量认识。
基于ABAQUS的U型焊缝焊接过程模拟和应力分析
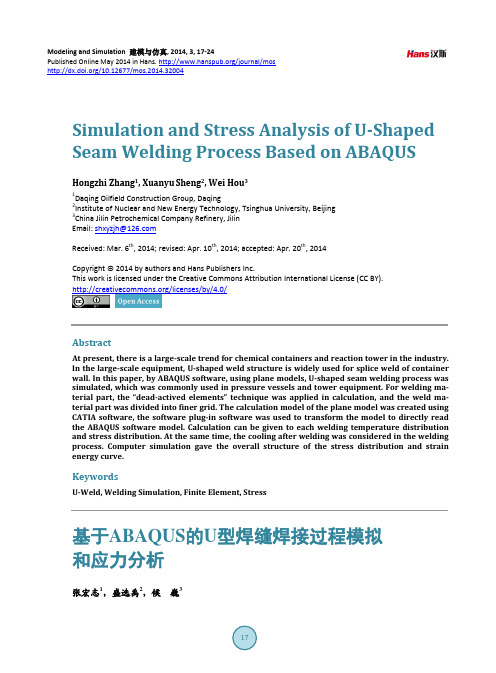
Modeling and Simulation 建模与仿真, 2014, 3, 17-24Published Online May 2014 in Hans. /journal/mos/10.12677/mos.2014.32004Simulation and Stress Analysis of U-Shaped Seam Welding Process Based on ABAQUSHongzhi Zhang1, Xuanyu Sheng2, Wei Hou31Daqing Oilfield Construction Group, Daqing2Institute of Nuclear and New Energy Technology, Tsinghua University, Beijing3China Jilin Petrochemical Company Refinery, JilinEmail: shxyzjh@Received: Mar. 6th, 2014; revised: Apr. 10th, 2014; accepted: Apr. 20th, 2014Copyright © 2014 by authors and Hans Publishers Inc.This work is licensed under the Creative Commons Attribution International License (CC BY)./licenses/by/4.0/AbstractAt present, there is a large-scale trend for chemical containers and reaction tower in the industry.In the large-scale equipment, U-shaped weld structure is widely used for splice weld of container wall. In this paper, by ABAQUS software, using plane models, U-shaped seam welding process was simulated, which was commonly used in pressure vessels and tower equipment. For welding ma-terial part, the “dead-actived elements” technique was applied in calculation, and the weld ma-terial part was divided into finer grid. The calculation model of the plane model was created using CATIA software, the software plug-in software was used to transform the model to directly read the ABAQUS software model. Calculation can be given to each welding temperature distribution and stress distribution. At the same time, the cooling after welding was considered in the welding process. Computer simulation gave the overall structure of the stress distribution and strain energy curve.KeywordsU-Weld, Welding Simulation, Finite Element, Stress基于ABAQUS的U型焊缝焊接过程模拟和应力分析张宏志1,盛选禹2,候巍31大庆油田建设集团,大庆市2清华大学核能与新能源技术研究院,北京市3中国吉林石化分公司炼油厂,吉林市Email: shxyzjh@收稿日期:2014年3月6日;修回日期:2014年4月10日;录用日期:2014年4月20日摘要目前,在工业界,化工容器、反应塔等有大型化的趋势。
Abaqus焊接模拟的例子
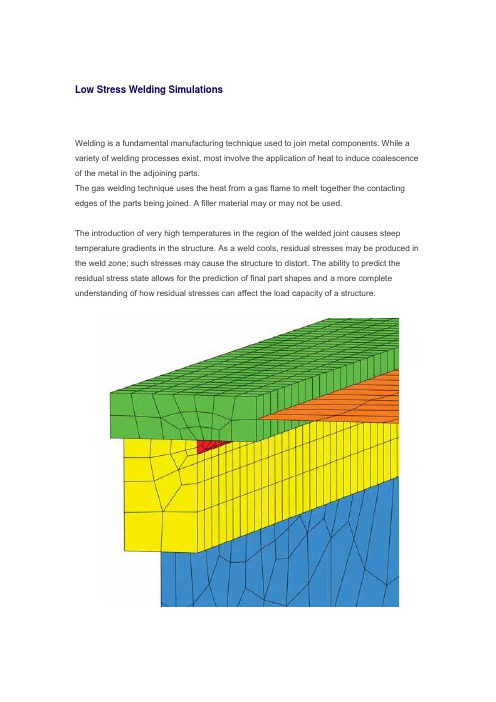
Low Stress Welding SimulationsWelding is a fundamental manufacturing technique used to join metal components. While a variety of welding processes exist, most involve the application of heat to induce coalescence of the metal in the adjoining parts.The gas welding technique uses the heat from a gas flame to melt together the contacting edges of the parts being joined. A filler material may or may not be used.The introduction of very high temperatures in the region of the welded joint causes steep temperature gradients in the structure. As a weld cools, residual stresses may be produced in the weld zone; such stresses may cause the structure to distort. The ability to predict the residual stress state allows for the prediction of final part shapes and a more complete understanding of how residual stresses can affect the load capacity of a structure.The finite element models described in this article represent structural beams. These structures are formed by welding plate sections together rather tha n producing the section directly in a mill. The cross-sectional size of these components can make direct manufacture impractical.The techniques discussed here are based on a generic model but are transferable to a range of applications.Finite Element Analysis ApproachThe simulation uses a sequentially coupled approach in which a thermal analysis is followed by a stress analysis. The temperature results from the thermal analysis are read into the stress analysis as loading to calculate the thermal stress effects. The thermal analysis makes use of ABAQUS user subroutines DFLUX, GAPCON, and FILM. The objective of the simulation is to predict post-weld deformation and residual stress distribution.Figure 1: Mesh of the structure being welded.The model is constructed using solid and shell elements. A solid representation is used in the weld area to ensure more accurate capture of the high solution gradients. Regions outside the weld zone, where thermal gradients are not as severe, are modeled with shell elements toreduce the overall model size. The transition between the shell and solid regions is achieved using tied contact for the thermal analysis and shell-to-solid coupling for the stress analysis. The mesh is shown in Figure 1 (left). The weld bead is shown in red.Thermal Analysis ProcedureThe thermal analysis is performed to calculate the heat transfer resulting from the thermal load of the moving torch. Three user subroutines are activated for the thermal analysis:DFLUX: Used to define the welding torch heat input as a concentrated flux. The heat source travels along the weld line to simulate the torch movement.GAPCON: Used to activate the conduction of heat between the deposited weld material and the parent materials once the torch has passed a given location.FILM: Similar to GAPCON in functionality, but used to activate film coefficients to simulate convective ambient cooling once the torch passes a given location.The simulation is run as a fully transient heat transfer analysis.Structural Analysis ProcedureThe structural analysis uses the thermal analysis (temperature) results as the loading. The objective of the structural analysis is to determine the stresses and strains induced in the weld region during the cooling transient. Boundary conditions are applied to restrain the system against rigid body motion.Figure 2: Nodal temperatures in a typical region of the weld as the torch traverses the weldline.Results and ConclusionTypical thermal results are shown in Figure 2 (left), which displays a contour of nodal temperature as the torch travels along the weld line.The weld is initialized at 1800° C, but no heat is allowed to transfer from the weld until the torch passes. As the torch passes a given point on the weld line, the flux input is initiated, resulting in a localized increase in temperature to more than 2000° C.Figure 3: Transient temperature profile at three points in the torch path.In addition, as the torch passes the same weld line point, conductive and convective heat transfer is activated, causing a rapid drop in temperature as thermal energy is transferred to the surrounding structure and environment.Figure 3 (right) shows the 35 s transient temperature profile at three points close to the start of the torch path. The peak temperature is reached when the torch is activated. A sharp temperature drop is observed after the torch passes.Figure 4: Von Mises stress in the weld region at t=35 s.The stress response of the structure is driven by the high thermal gradients. Figure 4 (left) and Figure 5 (below), respectively, show plots of the von Mises stress and the effective plastic strain approximately 35 s into the process.Figure 5: Effective plastic strain in the weld region at t=35 s.In conclusion, ABAQUS/Standard provides a set of general, flexible modeling tools that allow for the prediction of residual stresses and final shapes in welded components.。
abaqus多道焊子程序解释
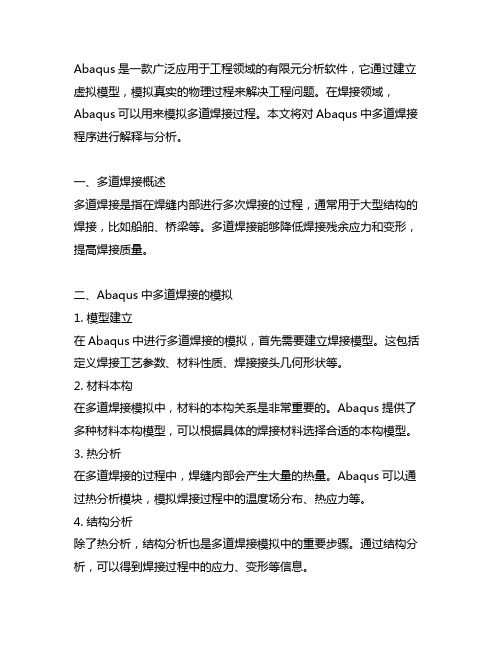
Abaqus是一款广泛应用于工程领域的有限元分析软件,它通过建立虚拟模型,模拟真实的物理过程来解决工程问题。
在焊接领域,Abaqus可以用来模拟多道焊接过程。
本文将对Abaqus中多道焊接程序进行解释与分析。
一、多道焊接概述多道焊接是指在焊缝内部进行多次焊接的过程,通常用于大型结构的焊接,比如船舶、桥梁等。
多道焊接能够降低焊接残余应力和变形,提高焊接质量。
二、Abaqus中多道焊接的模拟1. 模型建立在Abaqus中进行多道焊接的模拟,首先需要建立焊接模型。
这包括定义焊接工艺参数、材料性质、焊接接头几何形状等。
2. 材料本构在多道焊接模拟中,材料的本构关系是非常重要的。
Abaqus提供了多种材料本构模型,可以根据具体的焊接材料选择合适的本构模型。
3. 热分析在多道焊接的过程中,焊缝内部会产生大量的热量。
Abaqus可以通过热分析模块,模拟焊接过程中的温度场分布、热应力等。
4. 结构分析除了热分析,结构分析也是多道焊接模拟中的重要步骤。
通过结构分析,可以得到焊接过程中的应力、变形等信息。
三、多道焊接模拟的应用1. 优化焊接工艺通过Abaqus的多道焊接模拟,可以对焊接工艺进行优化。
比如确定合适的焊接顺序、焊接参数,以达到最佳的焊接质量。
2. 预测残余应力和变形多道焊接模拟可以预测焊接过程中产生的残余应力和变形,帮助工程师更好地设计焊接结构,减少后期修复工作。
3. 焊缝设计通过Abaqus的多道焊接模拟,可以对焊缝进行优化设计,提高焊接连接的强度和稳定性。
四、多道焊接模拟的局限性尽管Abaqus可以进行多道焊接模拟,但也存在一些局限性。
比如对于大型结构、复杂工艺的模拟需要计算资源较大,同时需要对模型的建立和参数选择有一定的专业知识。
总结起来,Abaqus多道焊接程序可以帮助工程师模拟多道焊接过程,优化焊接工艺,预测残余应力和变形,提高焊接结构的质量和可靠性。
然而,工程师在使用Abaqus进行多道焊接模拟时需要注意模型的建立和参数选择,以及计算资源的消耗。
Abaqus分析操作实例
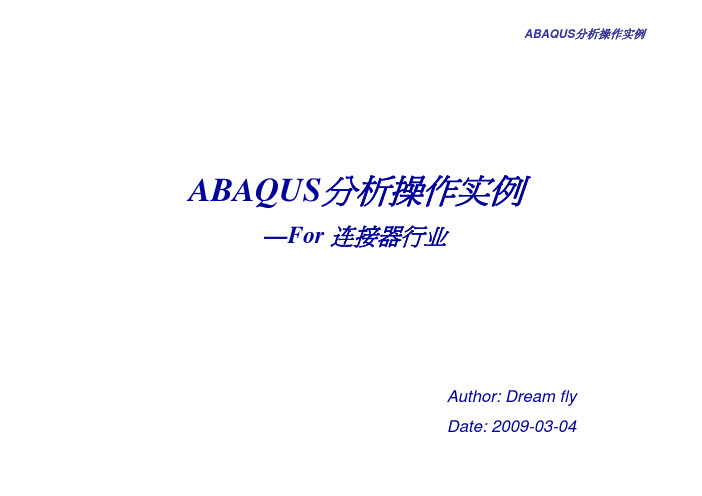
ABAQUS分析操作实例ABAQUS分析操作实例—For连接器行业Author:Dream flyDate: 2009-03-04操作流程介绍ABAQUS分析操作实例1.创建部件z ABAQUS CAD功能有限,对于复杂的几何模型一般都由其它CAD软件创建。
1.1 导入端子模型z在主菜单选择FileÆImportÆPart,在弹出的对话框中选择模型保存路径和格式类型。
部件导入对话框导入的端子模型1.2 创建解析刚性面z创建一解析刚性面以便对端子施加位移约束。
z在Module列表中选择Part模块,点击左侧工具区中的(Create Part),弹出Create Part 对话框,Type选择analytical rigid,把界面尺寸适当减小,点击Continue。
z在绘图环境中绘制一直线( ) ,然后点击三次中键确认,输入拉伸深度为1,完成解析刚性面创建。
z在主菜单选择ToolsÆReference point,创建一参考点来约束刚性面。
ABAQUS分析操作实例2.1 创建材料z 在Module 列表中选择Property 模块,点击左侧工具区中的(Create Material),弹出Edit Material 对话框,输入材料名称:C5210R-SH ,点击Mechanical ÆElasticity ÆElastic ,在数据表中设置材料Young’s Modulus 为110000,Poisson’s Ratio 为0.3,然后点击Mechanical ÆPlasticity ÆPlastic 输入两组材料塑性数据(710,0),(764,0.18),点击OK 。
2.1 创建截面属性z 点击左侧工具区中的(Create Section),点击Continue ,在弹出的Edit Section 对话框中,保持默认参数不变,点击OK 。
ABAQUS-Weld(双枪焊接建模流程)
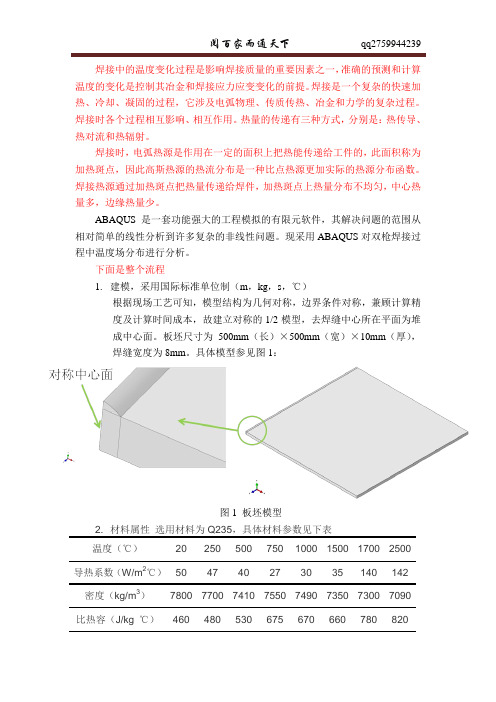
焊接中的温度变化过程是影响焊接质量的重要因素之一,准确的预测和计算温度的变化是控制其冶金和焊接应力应变变化的前提。
焊接是一个复杂的快速加热、冷却、凝固的过程,它涉及电弧物理、传质传热、冶金和力学的复杂过程。
焊接时各个过程相互影响、相互作用。
热量的传递有三种方式,分别是:热传导、热对流和热辐射。
焊接时,电弧热源是作用在一定的面积上把热能传递给工件的,此面积称为加热斑点,因此高斯热源的热流分布是一种比点热源更加实际的热源分布函数。
焊接热源通过加热斑点把热量传递给焊件,加热斑点上热量分布不均匀,中心热量多,边缘热量少。
ABAQUS 是一套功能强大的工程模拟的有限元软件,其解决问题的范围从相对简单的线性分析到许多复杂的非线性问题。
现采用ABAQUS对双枪焊接过程中温度场分布进行分析。
下面是整个流程1.建模,采用国际标准单位制(m,kg,s,℃)根据现场工艺可知,模型结构为几何对称,边界条件对称,兼顾计算精度及计算时间成本,故建立对称的1/2模型,去焊缝中心所在平面为堆成中心面。
板坯尺寸为500mm(长)×500mm(宽)×10mm(厚),焊缝宽度为8mm。
具体模型参见图1:图1 板坯模型2. 材料属性选用材料为Q235,具体材料参数见下表温度(℃)20 250 500 750 1000 1500 1700 2500导热系数(W/m2℃)50 47 40 27 30 35 140 142 密度(kg/m3)7800 7700 7410 7550 7490 7350 7300 7090比热容(J/kg ℃)460 480 530 675 670 660 780 820具体参数设置如图2所示。
图2 参数设置界面3. 装配,将板坯进行定位,为边界条件施加提供装配模型,对称面为YZ平面,焊道与Z轴平行,焊点沿Z轴移动,如图3所示。
图3 板坯组装图4.分析步设定,本为主要分析双枪焊接过程中,温度场变化情况,故选择分析类型为Heat transfer,根据实际工艺,选择Transient类型,分析步总时间根据现场工艺确定。
abaqus 实例
焊接ABAQUS建模实例一、网格的建立或导入在定义材料属性时,往往要根据单元的集合来定义,这些集合首先需要在part中定义。
当采用hypermesh来划分网格时,在hypermesh中定义的SET只存在于assembly中,而在part中没有,因此需要重新在part中定义这些集合,通常情况下可以通过修改inp文件来实现,具体操作步骤如下:1.导入hypermesh所生成的inp文件,具体操作为:File——import——models,出现Import models 对话框,File filter选择*.inp,然后选择所要导入的inp文件。
2. 建立新的job,重新生成inp文件,具体操作如下:在analysis模型树中,右击job——create,输入新的job名称,例如weld,点击continue,然后点击ok。
单击模型树job前的+,会出现刚才生成的weld,右键job,选择write input,就会在文件夹中生成新的inp文件。
3. 选用记事本或者写字板打开刚才生成的weld.inp文件,选择你需定义的材料单元集合,将它们复制到*end part之前,并删除后面的instance=part-1-1,保存。
4.重新用abaqus打开刚才修改后的inp文件,就可以进行后续的建模和分析了。
二、材料的定义材料的定义分为两个过程,首先定义材料性能参数,然后将这些材料性能参数赋予给具体的单元。
1.材料参数的定义。
右击material——create,出现edit material对话框,输入材料的名称,例如weld、base 、haz。
焊接过程需要定义的材料参数主要有density、elastic、plastic、expansion、conductivity、specific heat 、latent heat。
下面以elasticity为例作一个简单的介绍,单击对话框的mechanical——elasticity——elastic,会出现如下的对话框如果材料性能是温度的函数,把use temperature-dependent data 前的框选上。
应用ABAQUS模拟激光焊接温度场
(
!
)
变化, 材料温度相关的比热容与导热系数如表 " 所示, 表中 & 为温度; - 为比热容。 $ 为导热系数; ! 材质密度为 QR++P; 5 D , 熔点为 "*T!U , 熔化潜热 为 ,R"*++O 5 P;, 激光热源的功率为 ,PM, 光斑直径为 +< !DD, 热源移动速度为 ,+DD 5 F, 初始温度为 ,+U 。 在焊接中, 一般近似认为激光束是基模高斯光束, 功率 光斑半径为 2 的基模高斯光束, 其功率密度分布 为 1, [ S] ,1 可表示为 : ’, + ., # # # ( " ’, .) ) (!) , -./ ( , 2, !2 室温时多数金属对 "+< S #D 波长的 =V, 激光的反射率 都超过 T+W , 但是当焊接正常进行, 形成的小孔稳定 [ Q] 存在时, 对光速的吸收率都急剧增加 。在此考虑到 激光传输过程的损耗等取稳定时的吸收率为激光功率 的 +< QH 倍。 对于激光束的移动, 如图 ! 所示。假设 0 1 + 时刻 # #
[ *] 度& ( 坐标 ’ 为热源移动方向) 的理论计算式为 :
!, , (") ) + * * *, $ 为板的厚度; 0+ 为第二类零阶修正贝塞尔函 式中, 数; 传热系数 , 1 , ( "2 3 "4 ) 5 -#$; - 为材料比热容; #为 密度; " 为激光功率密度; " 2 为对流换热系数; " 4 为辐 射换热系数; * 为总换热系数;*+ 为热流 ! 为热导率; 集中程度系数; &+ 为初始时刻的温度。使用上式, 代入 材料特征参数, 就可以计算出准稳态激光焊的温度场分 布。代入相应的参数, 用 6$78$% 计算出的理论平板 焊接的温度场分布见图 ,。 & ( &+ ) " -./ ( ( ! ) ’ # , *+ ) 0+ % $, !!
abaqus在焊接工艺仿真中的应用
Abaqus在焊接工艺仿真中的应用1. 简介焊接工艺是制造业中常见且重要的工艺之一,其仿真技术的发展对于提高焊接工艺的质量和效率具有重要意义。
而Abaqus作为一款广泛应用于工程领域的仿真软件,其在焊接工艺仿真中的应用也备受关注。
本文将从深度和广度两个方面展开,探讨Abaqus在焊接工艺仿真中的应用以及对焊接工艺的优化与改进。
2. Abaqus在焊接工艺仿真中的基本原理Abaqus作为有限元分析软件,其在焊接工艺仿真中的应用主要依靠其强大的非线性有限元分析能力。
通过建立焊接工艺的三维模型,包括焊接材料的性质、热源激励和工艺参数等,Abaqus可以对焊接过程中的温度场、应力场、变形等进行精确的仿真计算。
这种基于实际物理过程的仿真分析,可以帮助工程师深入理解焊接工艺中的复杂物理现象,为优化焊接工艺提供重要参考。
3. 深度探讨Abaqus在焊接工艺仿真中的应用在焊接工艺仿真中,Abaqus可以有效地模拟焊接过程中的热传导、相变、材料塑性变形等复杂物理现象。
通过对焊接接头和母材的热影响区、残余应力、变形等进行仿真分析,可以预测焊接工艺中可能出现的缺陷,如裂纹、变形过大等,从而指导工程师采取相应的措施进行改进。
基于Abaqus的仿真结果,还可以进行后续的焊接残余寿命评估、断裂韧性分析等工作,为焊接工艺的质量控制和安全评估提供支持。
4. 广度探讨Abaqus在焊接工艺仿真中的应用除了对焊接过程本身的仿真分析,Abaqus在焊接工艺中还可以应用于焊接接头的结构强度和疲劳寿命的评估。
通过建立焊接接头的有限元模型,结合载荷作用下的应力分析和损伤累积分析,可以预测焊接接头的疲劳寿命,为设计提供重要参考。
Abaqus还可以进行多工步的焊接工艺仿真,包括预热、多道次焊接等复杂工艺的仿真分析,为工程师提供全面的工艺优化方案。
5. 个人观点和理解在我看来,Abaqus在焊接工艺仿真中的应用极大地丰富了焊接工艺优化与改进的手段。
Abaqus软件掌握大部件焊接仿真的解决思路
Abaqus软件掌握大部件焊接仿真的解决思路一、导读伴随着现代工业发展速度的不断加快,人们对工业产品需求增加,同时对其轻量化程度的要求也越来越高。
铝合金具有高的比强度、良好的机械性能以及耐腐蚀性等优点,已被广泛应用于许多焊接结构产品中,成为了现代工业用量最大和用途最广的轻量化金属材料,广泛应用在军工武器、汽车、轨道车辆、航空航天、机械制造、电工和船舶等领域在地铁车辆中,已大量采用铝合金车体。
常用的焊接方式为MIG 自动焊接。
焊接过程中加热和冷却过程的梯度温度场会导致焊后残余应力和焊接变形的产生。
焊接残余应力和焊接变形会降低产品尺寸精度和稳定性,严重影响轨道交通制造中焊接结构的制造和使用性能。
究其原因,在于当前的焊接应用中还存在很多落后的工艺方式,如何将现代的焊接数值仿真技术应用于传统的焊接工艺,利用先进的计算机数值模拟技术改造传统的焊接工艺,对加速我国焊接信息化与工业化的融合有着非常重要的意义。
焊接数值模拟技术的发展是随着焊接实践经验的积累,有限元数值模拟技术,计算机技术等的发展而逐步开始的。
焊接工艺的仿真,主要是针对焊接温度场,残余应力,变形等方面改善焊接部件的制造质量,提高产品服役性能,优化焊接顺序等工艺过程。
本文利用大型商用有限元分析软件ABAQUS对某地铁车辆侧墙总成焊接进行仿真。
研究在焊接过程中侧墙的变形情况,并测试在施加不同反变形的工况下侧墙焊后整体的平面度。
最后将仿真结果与实件焊接进行对比验证,为现场焊接工艺的指定提供理论指导。
二、地铁侧墙总成焊接现象描述某地铁项目中车体侧墙大部件采用搅拌摩擦焊墙板单元,该单元在焊接完成后与侧墙边梁经过MIG自动焊焊接而成,要求MIG自动焊后整体平面度1.5mm/m,结构示意图如下:图1 焊接区域图(1-边梁 2-墙板单元)图2 焊接示意图焊接时,先焊接第一道焊缝,将边梁正面和侧墙正面紧压在工装上,主要焊接参数为I=210,U=19.7,v=40cm/min。
- 1、下载文档前请自行甄别文档内容的完整性,平台不提供额外的编辑、内容补充、找答案等附加服务。
- 2、"仅部分预览"的文档,不可在线预览部分如存在完整性等问题,可反馈申请退款(可完整预览的文档不适用该条件!)。
- 3、如文档侵犯您的权益,请联系客服反馈,我们会尽快为您处理(人工客服工作时间:9:00-18:30)。
BOOKMARKS
SEARCH
3-Dimensional Repair Weld Simulations – Bead on Plate Comparisons
Dr CD Elcoate1, PJ Bouchard2, and Dr MC Smith2
1) Frazer-Nash Consultancy Limited, 1 Trinity Street, College Green, Bristol, BS1 5TE, UK. 2) British Energy Generation Limited, Barnett Way, Barnwood, Gloucester, GL4 3RS, UK. Full 3-dimensional simulation of multi-pass repair welds is now feasible and practical given the development of improved analysis tools (i.e. ABAQUS) and significantly greater computer power. A single weld bead of limited length, deposited on a flat plate, introduces a strongly varying 3dimensional residual stress field that has similar characteristics to a typical repair weld. This simple welded component is therefore a good vehicle to demonstrate new methods and validate thermal and mechanical predictions. This paper presents a series of results that simulate the deposition of a single weld bead on a flat plate. The work exploits newly developed features within ABAQUS (i.e. plastic strain annealing) which have been demonstrated to be robust and efficient and readily extendible to larger and more complex models. Good comparisons are achieved between simultaneous bead laying and moving heat source approaches whilst it is also noted that the simultaneous bead laying methods offer significant modelling advantages in terms of model creation and execution time.
2003 ABAQUS Users’ Conference
1
HOME
BOOKMARKS
SEARCH
(introduced in ABAQUS 6.2, (2001)) and the use of alternative elements types. The work is presented in more detail, includher block-dumped heat source models, in Elcoate (2003).
2. Welded plate test specimens
In support of this study, and other ENPOWER investigations, two test specimens have been prepared. Both of the specimens are similar in specification and the main features of one of the specimens (specimen 1) are provided in this section. Figure 1 is a diagrammatic picture and photograph of specimen 1 with the key dimensions. A piece of AISI Type 316L austenitic stainless steel plate, 180mm x 300mm x 17mm, was supplied by Mitsui Babcock for the validation studies. The as-received material test certificate composition (Heat 55841) was: C=0.02; Mn=1.404; P=0.027; S=0.0011; Si=0.582; Ni=11.11; Cr=17.834; Mo=2.06; N=0.0132 (% weight). A test specimen, 120mm x 180mm, was machined from the 17mm thick plate, and datum edges marked. Both the test specimen and the remaining plate were then solution heat treated in a vacuum furnace for 1 hour at 1050oC and slowly cooled, to eliminate fabrication residual stresses. The absence of residual stress in the test plate was confirmed by X-ray diffraction measurements. A single manual metal arc weld bead, with a low heat input procedure, was deposited along the centre-line of the plate by Mitsui Babcock, as shown in Figure 1. A Babcock type S-316, 2.4mm diameter electrode (approx. 19Cr12Ni21/2Mo, classification BS2926 19.12.3.L BR) was used. The following welding conditions were measured: current = 85A, closed circuit voltage = 25.4V, deposition time = 19.4s, bead length = 60mm, giving an average electrical heat input for this weld of 0.7kJ/mm. The increase in weight of the plate was measured to be 5.5g. After welding, a mould of the weld bead shape was made using a dental impression compound. The average width of the bead at the plate interface was about 7mm, and the bead height approximately 1.8mm.
a
b
Figure 1. Schematic diagram (a) and photograph (b) of the bead on plate specimen
2
2003 ABAQUS Users’ Conference
HOME
BOOKMARKS
SEARCH
3. Bead on plate finite element model
An ABAQUS, (2001) 3-dimensional model was constructed based on the measured dimensions of the welded test specimen 1. The model developed for the moving heat source analysis was a half model assuming that the geometry is symmetrical about the weld centreline (that is ignoring the small offset actually observed in the experimental weld). For the purposes of the block-dumped analysis advantage of the additional symmetry plane was exercised by reducing the half model to a quarter. The half model contains 5655 quadratic elements, within which 595 elements represent the bead. The bead geometry is an idealisation consistent with the measured width (7mm), length (60mm) and volume of weld deposit (mass = 5.5g). However, the top of the idealised bead is flatter than the observed profile (Figure 2) and the detailed profiles at the start and stop ends (Figure 3) are ignored. The physical geometry of the actual bead is such that the start end is rounded, while the stop end is flattened. The start and stop ends of the bead were idealised using a uniform cross-section along the entire length.