疲劳强度设计原则
动载焊接结构设计Ⅲ(疲劳强度寿命计算)
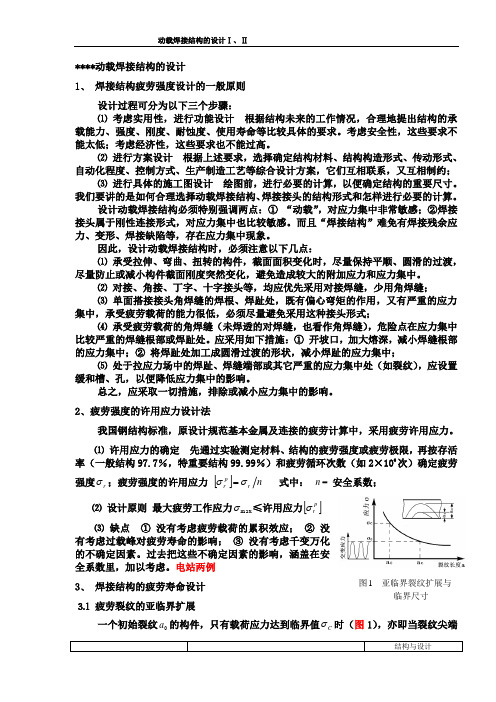
****动载焊接结构的设计1、 焊接结构疲劳强度设计的一般原则设计过程可分为以下三个步骤:⑴ 考虑实用性,进行功能设计 根据结构未来的工作情况,合理地提出结构的承载能力、强度、刚度、耐蚀度、使用寿命等比较具体的要求。
考虑安全性,这些要求不能太低;考虑经济性,这些要求也不能过高。
⑵ 进行方案设计 根据上述要求,选择确定结构材料、结构构造形式、传动形式、自动化程度、控制方式、生产制造工艺等综合设计方案,它们互相联系,又互相制约;⑶ 进行具体的施工图设计 绘图前,进行必要的计算,以便确定结构的重要尺寸。
我们要讲的是如何合理选择动载焊接结构、焊接接头的结构形式和怎样进行必要的计算。
设计动载焊接结构必须特别强调两点:① “动载”,对应力集中非常敏感;②焊接接头属于刚性连接形式,对应力集中也比较敏感。
而且“焊接结构”难免有焊接残余应力、变形、焊接缺陷等,存在应力集中现象。
因此,设计动载焊接结构时,必须注意以下几点:⑴ 承受拉伸、弯曲、扭转的构件,截面面积变化时,尽量保持平顺、圆滑的过渡,尽量防止或减小构件截面刚度突然变化,避免造成较大的附加应力和应力集中。
⑵ 对接、角接、丁字、十字接头等,均应优先采用对接焊缝,少用角焊缝; ⑶ 单面搭接接头角焊缝的焊根、焊趾处,既有偏心弯矩的作用,又有严重的应力集中,承受疲劳载荷的能力很低,必须尽量避免采用这种接头形式;⑷ 承受疲劳载荷的角焊缝(未焊透的对焊缝,也看作角焊缝),危险点在应力集中比较严重的焊缝根部或焊趾处。
应采用如下措施:① 开坡口,加大熔深,减小焊缝根部的应力集中;② 将焊趾处加工成圆滑过渡的形状,减小焊趾的应力集中;⑸ 处于拉应力场中的焊趾、焊缝端部或其它严重的应力集中处(如裂纹),应设置缓和槽、孔,以便降低应力集中的影响。
总之,应采取一切措施,排除或减小应力集中的影响。
2、疲劳强度的许用应力设计法我国钢结构标准,原设计规范基本金属及连接的疲劳计算中,采用疲劳许用应力。
注塑机筒疲劳强度计算的设计准则

2023年 第49卷·71·作者简介:袁卫明(1971-),男,本科,正高级工程师,副总工程师,现从事塑料注射成型机研发设计。
收稿日期:2023-07-200 引言注塑机机筒是注射机构中的重要零部件,在工作中其要承载注射高压的冲击,当前注塑机的注射压力已从传统的170 MPa 发展到270 MPa 以上。
面对机筒在高压和超高压中出现的失效现象,沿用传统的注塑机筒强度理论[1],不能圆满解释机筒失效的实际现象。
本文从厚壁圆筒的弹塑性力学理论[2]分析研究注塑机筒的工作特性,阐述以往用弹性力学角度分析研究机筒强度的局限性,提出了符合实际的注塑机筒疲劳强度的设计准则,并用实例加以论证。
1 厚壁圆筒1.1 厚壁圆筒的应力分析根据厚壁圆筒体[3]的应力变形特点,我们假设将厚壁圆筒看成是由许多个薄壁圆筒相互连在一起所组成,如图1所示,当厚壁圆筒内径承受内压力后,其组成的各层薄壁圆筒由里至外逐步受力,其变形受到里层薄壁圆筒的约束和受到外层薄壁圆筒的限制,因此各个单元薄壁圆筒体都会受到内外侧变形的约束和限制所引起的均布压力作用,从里往外各层薄壁圆筒体的变形被受到的约束和限制是不同的,环向应力沿壁厚方向分布是不均匀的,这是厚壁圆筒形变和应力的一个基本特点。
厚壁圆筒应力、应变的另一个特点是:由于厚壁圆筒是由多个薄壁圆筒组成,在多层材料变形的相互约束和限制下,沿径向方向产生了径向应力,沿壁厚方向径向应力分布是不均匀的。
厚壁圆筒和薄壁圆筒注塑机筒疲劳强度计算的设计准则袁卫明,成明祥(德清申达机器制造有限公司,浙江 湖州 313205)摘要:传统注塑机筒强度设计理论未能合理解释回答在实际中产生的一些失效现象问题,对比厚壁圆筒的力学分析,确认判断注塑机筒沿用以往的设计理论具有局限性和适用范围。
通过引用分析目前在厚壁圆筒中较常用的弹塑性强度理论设计观点,结合实例,提出了符合实际的注塑机筒强度理论的设计准则。
第6章结构件及连接的疲劳强度计算原理

148第6章 结构件及连接的疲劳强度随着社会生产力的发展,起重机械的应用越来越频繁,对起重机械的工作级别要求越来越高。
《起重机设计规范》GB/T 3811-2008规定,应计算构件及连接的抗疲劳强度。
对于结构疲劳强度计算,常采用应力比法和应力幅法,本章仅介绍起重机械常用的应力比法。
6.1 循环作用的载荷和应力起重机的作业是循环往复的,其钢结构或连接必然承受循环交变作用的载荷,在结构或连接中产生的应力是变幅循环应力,如图6-1所示。
起重机的一个工作循环中,结构或连接中某点的循环应力也是变幅循环应力。
起重机工作过程中每个工作循环中应力的变化都是随机的,难以用实验的方法确定其构件或连接的抗疲劳强度。
然而,其结构或连接在等应力比的变幅循环或等幅应力循环作用下的疲劳强度是可以用实验的方法确定的,对于起重机构件或连接的疲劳强度可以用循环记数法计算出整个循环应力中的各应力循环参数,将其转化为等应力比的变幅循环应力或转化为等平均应力的等幅循环应力。
最后,采用累积损伤理论来计算构件或连接的抗疲劳强度。
6.1.1 循环应力的特征参数 (1) 最大应力一个循环中峰值和谷值两极值应力中绝对值最大的应力,用max σ表示。
(2) 最小应力一个循环中峰值和谷值两极值应力中绝对值最小的应力,用min σ表示。
(3) 整个工作循环中最大应力值构件或连接整个工作循环中最大应力的数值,用max ˆσ表示。
(4) 应力循环特性值一个循环中最小应力与最大应力的比值,用minmaxr σσ=表示。
(5) 循环应力的应力幅一个循环中最大的应力与最小的应力的差的绝对值,用σ∆表示。
149,r i i N σ-曲线max min max (1)r σσσσ∆=-=-(6) 应力半幅一个循环中最大的应力与最小的应力的差的绝对值的一半,用a σ来表示。
max min /2a σσσ=-(7) 应力循环的平均值一个循环中最大的应力与最小的应力的和的平均值,用m σ表示。
疲劳强度设计

疲劳强度设计对承受循环应力的零件和构件,根据疲劳强度理论和疲劳试验数据,决定其合理的结构和尺寸的机械设计方法。
机械零件和构件对疲劳破坏的抗力,称为零件和构件的疲劳强度。
疲劳强度由零件的局部应力状态和该处的材料性能确定,所以疲劳强度设计是以零件最弱区为依据的。
通过改进零件的形状以降低峰值应力,或在最弱区的表面层采用强化工艺,就能显著地提高其疲劳强度。
在材料的疲劳现象未被认识之前,机械设计只考虑静强度,而不考虑应力变化对零件寿命的影响。
这样设计出来的机械产品经常在运行一段时期后,经过一定次数的应力变化循环而产生疲劳,致使突然发生脆性断裂,造成灾难性事故。
应用疲劳强度设计能保证机械在给定的寿命内安全运行。
疲劳强度设计方法有常规疲劳强度设计、损伤容限设计和疲劳强度可靠性设计。
简史19 世纪40 年代,随着铁路的发展,机车车轴的疲劳破坏成为非常严重的问题。
1867年,德国A.沃勒在巴黎博览会上展出了他用旋转弯曲试验获得车轴疲劳试验结果,把疲劳与应力联系起来,提出了疲劳极限的概念,为常规疲劳设计奠定了基础。
20 世纪40 年代以前的常规疲劳强度设计只考虑无限寿命设计。
第二次世界大战中及战后,通过对当时发生的许多疲劳破坏事故的调查分析,逐渐形成了现代的常规疲劳强度设计,它非但提高了无限寿命设计的计算精确度, 而且可以按给定的有限寿命来设计零件,有限寿命设计的理论基础是线性损伤积累理论。
早在1924年,德国A.帕姆格伦在估算滚动轴承寿命时,曾假定轴承材料受到的疲劳损伤的积累与轴承转动次数(等于载荷的循环次数)成线性关系,即两者之间的关系可以用一次方程式来表示。
1945 年,美国M.A. 迈因纳根据更多的资料和数据,明确提出了线性损伤积累理论,也称帕姆格伦-迈因纳定理。
随着断裂力学的发展,美国 A.K. 黑德于1953 年提出了疲劳裂纹扩展的理论。
1957年,美国P.C.帕里斯提出了疲劳裂纹扩展速率的半经验公式。
2疲劳强度及寿命可靠性估计原理
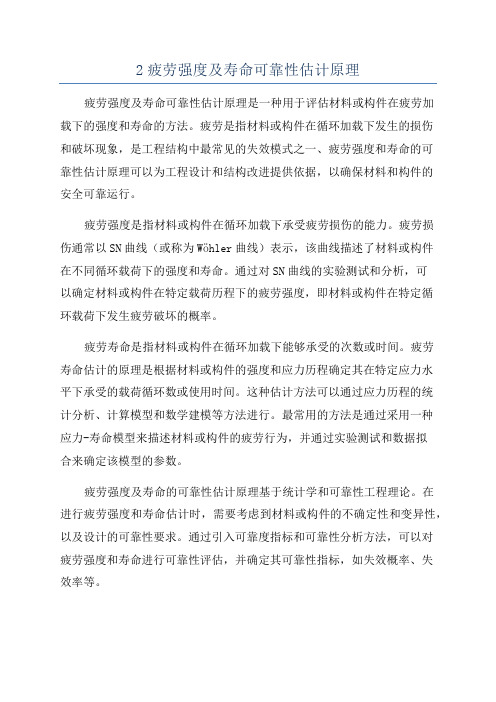
2疲劳强度及寿命可靠性估计原理疲劳强度及寿命可靠性估计原理是一种用于评估材料或构件在疲劳加载下的强度和寿命的方法。
疲劳是指材料或构件在循环加载下发生的损伤和破坏现象,是工程结构中最常见的失效模式之一、疲劳强度和寿命的可靠性估计原理可以为工程设计和结构改进提供依据,以确保材料和构件的安全可靠运行。
疲劳强度是指材料或构件在循环加载下承受疲劳损伤的能力。
疲劳损伤通常以SN曲线(或称为Wöhler曲线)表示,该曲线描述了材料或构件在不同循环载荷下的强度和寿命。
通过对SN曲线的实验测试和分析,可以确定材料或构件在特定载荷历程下的疲劳强度,即材料或构件在特定循环载荷下发生疲劳破坏的概率。
疲劳寿命是指材料或构件在循环加载下能够承受的次数或时间。
疲劳寿命估计的原理是根据材料或构件的强度和应力历程确定其在特定应力水平下承受的载荷循环数或使用时间。
这种估计方法可以通过应力历程的统计分析、计算模型和数学建模等方法进行。
最常用的方法是通过采用一种应力-寿命模型来描述材料或构件的疲劳行为,并通过实验测试和数据拟合来确定该模型的参数。
疲劳强度及寿命的可靠性估计原理基于统计学和可靠性工程理论。
在进行疲劳强度和寿命估计时,需要考虑到材料或构件的不确定性和变异性,以及设计的可靠性要求。
通过引入可靠度指标和可靠性分析方法,可以对疲劳强度和寿命进行可靠性评估,并确定其可靠性指标,如失效概率、失效率等。
在疲劳强度及寿命可靠性估计过程中,还需要考虑到材料和构件的预防措施和改进措施。
预防措施包括材料的优化设计、制备和处理,以提高材料的抗疲劳性能;改进措施包括结构的几何形状和尺寸优化、加载历程和工况的优化等,以减小结构的疲劳应力和增加结构的寿命。
总之,疲劳强度及寿命可靠性估计原理是一种综合应用力学、材料科学、统计学和可靠性工程理论的方法,通过实验测试、数据分析和数学建模等方式,对材料和构件在疲劳加载下的强度和寿命进行评估和预测。
这种估计方法可以为工程设计和结构改进提供依据,以确保材料和构件的安全可靠运行。
机械零件的疲劳强度.

M' ('me,'ae)
B’
E E’
/K
0/2K
45° O
135° S (s,0)
m
K N 1 1 a m (k ) D (k ) D
直线E’S方程:
2 1 0
0
' max
m s a
按静强度计算 当
10 3 (10 4 ) N N 0 ——高周循环疲劳
N
有限寿命区 无限寿命区
随循环次数↑疲劳极限↓
N
O
N
N0
N
2
N ——持久极限
对称循环:
无限寿命区 N N0
1 1
有限寿命区
脉动循环:
0 0
注意:有色金属和高强度合金钢无无限寿命区。
3、 无明显塑性变形的脆性突然断裂
4 、破坏时的应力(疲劳极限)远小于材料的屈服极限 三、疲劳破坏的机理:
损伤的累积 四、影响因素: 不仅与材料性能有关,变应力的循环特性,应力循环
次数,应力幅(应力集中、表面状态、零件尺寸)都
对疲劳极限有很大影响。
§ 3—2 材料的疲劳曲线和极限应力图
N ( N )——疲劳极限,循环变应力下应力循环N次后
第三章 机械零件的疲劳强度
疲劳强度计算方法: 1、安全——寿命设计 2、破损——安全设计
§ 3—1 疲劳断裂的特征
一、失效形式:疲劳断裂
二、疲劳破坏特征: 1、断裂过程:① 产生初始裂纹 (应力较大处) ② 裂纹尖端在切应力作用下,反复扩 展,直至产生疲劳裂纹。 2 、断裂面:① 光滑区(疲劳发展区) ② 粗糙区(脆性断裂区)
机械设计之机械零件的疲劳强度

注意点:
1) rN , rH 与 rN 相似
2) N 0 为循环基数,与材料有关
3) r不同,同一材料疲劳曲线不同
2. 无限寿命区 N N0
疲劳曲线为一水平线,疲劳极限不随N的增加而降低。
3.2.3 极限应力图 m a(表示材料在不同的循环特性
下不同的疲劳极限)
是根据光滑小试件的试验结果绘制的。试验是在不同循环特 性(r =-1~+1)和相同循环次数(等寿命)的条件下进行。通 常取N0为107或106。试验结果即为材料的疲劳极限
1. 循环特性等于常数 如:轴的弯曲应力
O
循环特性相同的变应力都在同一射线上
tg a 1 r const m 1 r
r=1 tg 0 00
r=0 tg 1 450 r=-1 tg 900
零件的工作应力C( m , a ), m + a = max ,C点距O愈远,
例:已知某机械零件的材料的屈服极限σs=600MPa, σ-1=300MPa,(kσ)D=1.5,m=9,ψσ=0.2,实际应力循环 为106,(取N0=107),当零件截面上的最大应力为 200MPa,最小应力为-40MPa,(1)画出零件的疲劳极 限应力图;(2)求该零件的安全系数(r=常数)
k
D
k
k
D
k
应力集中、尺寸和表面状态都只对 a有影响,而对 m影响不大
3.4 许用疲劳极限应力图
3.4.1 稳定变应力和非稳定变应力
稳定变应力, a 、 m周期不 随时间变化(单向,复合)
非稳定变应力, a 、 m周期随 时间变化 (周期性,随机性 )
3.4.2 许用疲劳极限应力图
3.4.3 工作应力增长规律
解:
钢结构设计中的疲劳强度考虑与分析
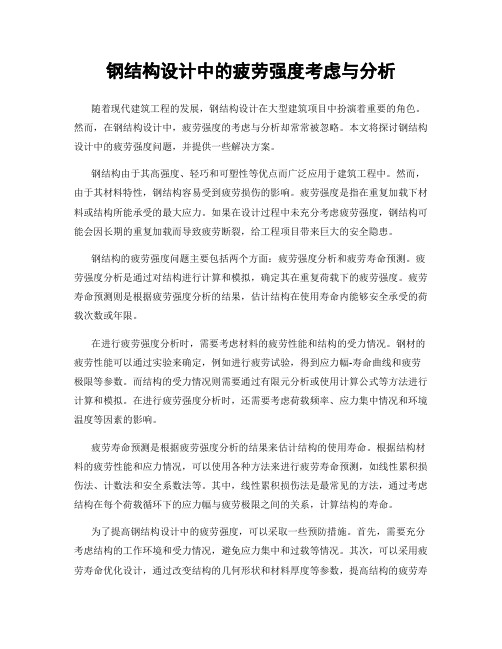
钢结构设计中的疲劳强度考虑与分析随着现代建筑工程的发展,钢结构设计在大型建筑项目中扮演着重要的角色。
然而,在钢结构设计中,疲劳强度的考虑与分析却常常被忽略。
本文将探讨钢结构设计中的疲劳强度问题,并提供一些解决方案。
钢结构由于其高强度、轻巧和可塑性等优点而广泛应用于建筑工程中。
然而,由于其材料特性,钢结构容易受到疲劳损伤的影响。
疲劳强度是指在重复加载下材料或结构所能承受的最大应力。
如果在设计过程中未充分考虑疲劳强度,钢结构可能会因长期的重复加载而导致疲劳断裂,给工程项目带来巨大的安全隐患。
钢结构的疲劳强度问题主要包括两个方面:疲劳强度分析和疲劳寿命预测。
疲劳强度分析是通过对结构进行计算和模拟,确定其在重复荷载下的疲劳强度。
疲劳寿命预测则是根据疲劳强度分析的结果,估计结构在使用寿命内能够安全承受的荷载次数或年限。
在进行疲劳强度分析时,需要考虑材料的疲劳性能和结构的受力情况。
钢材的疲劳性能可以通过实验来确定,例如进行疲劳试验,得到应力幅-寿命曲线和疲劳极限等参数。
而结构的受力情况则需要通过有限元分析或使用计算公式等方法进行计算和模拟。
在进行疲劳强度分析时,还需要考虑荷载频率、应力集中情况和环境温度等因素的影响。
疲劳寿命预测是根据疲劳强度分析的结果来估计结构的使用寿命。
根据结构材料的疲劳性能和应力情况,可以使用各种方法来进行疲劳寿命预测,如线性累积损伤法、计数法和安全系数法等。
其中,线性累积损伤法是最常见的方法,通过考虑结构在每个荷载循环下的应力幅与疲劳极限之间的关系,计算结构的寿命。
为了提高钢结构设计中的疲劳强度,可以采取一些预防措施。
首先,需要充分考虑结构的工作环境和受力情况,避免应力集中和过载等情况。
其次,可以采用疲劳寿命优化设计,通过改变结构的几何形状和材料厚度等参数,提高结构的疲劳寿命。
此外,还可以使用疲劳增强技术,如表面处理、焊接缺陷处理和应力容限设计等,提高结构的疲劳强度。
总之,钢结构设计中的疲劳强度考虑与分析是保证工程项目安全有效的重要一环。
- 1、下载文档前请自行甄别文档内容的完整性,平台不提供额外的编辑、内容补充、找答案等附加服务。
- 2、"仅部分预览"的文档,不可在线预览部分如存在完整性等问题,可反馈申请退款(可完整预览的文档不适用该条件!)。
- 3、如文档侵犯您的权益,请联系客服反馈,我们会尽快为您处理(人工客服工作时间:9:00-18:30)。
疲劳强度设计原则
1)承受拉伸、弯曲和扭转的构件应采用长而圆滑的过渡结构以减少刚度的突然变化。
2)优先选用对接焊缝、单边V形焊缝和K形焊缝,尽可能不用角焊缝。
3)采用角焊缝时最好用双面焊缝,避免使用单面焊缝。
4)采用带有搭接板(盖板)的搭接接头和弯搭接接头,尽可能不用偏心搭接。
5)使焊缝位于低应力区,使缺口效应分散而避免其叠加。
6)在焊趾缺口、焊缝根部缺口和焊缝端面缺口之前或之后设置一些缓冲缺口以消除或降低上述缺口部位的应力。
7)承受横向弯曲的构件应缩短支撑间距以减小弯矩。
8)横向力应作用于剪切中心之上以减小扭矩。
9)承受拉伸与弯曲的构件如需加强,则加强长度应小,以减小加强对于构件变形的约束。
10)承受扭转的构件,为避免横截面翘曲受阻可采用切除翼缘端部、翼缘端部斜接等形式以及采用横截面不产生翘曲的型材。
11)使焊缝能包围较大面积或局部增加构件壁厚以减轻外力作用于薄壁构件上时引起的局部弯曲。
12)在薄壁范围内合理布置焊缝以减轻弯曲变形。
13)避免能扰乱力流的开口,但与力流垂直的加劲肋板角部应切除。
14)在特别危险的部位以螺栓接头或铆接接头、锻造连接件或铸造连接件代替焊接接头。
15)消除能引起腐蚀的根部间隙。