与挤出吹塑成型相比,注射吹塑成型的优点有哪些
塑料模具设计教程009:挤出吹塑成型和注射吹塑成型的区别是什么?

塑料模具设计教程009:挤出吹塑成型和注射吹塑成型的区别是什么?视频主要介绍注射成型、挤出成型及吹塑成型的原理、生产过程,讲得比较透彻且通俗易懂,推荐大家都看一下!挤出吹塑成型挤出吹塑成型是成型中空塑件的主要方法,其成型工艺过程如图2-7所示。
成型时,先由挤出机挤出管状型坯,如图2-7a所示;然后截取一段管坯趁热将其放入模具中,在闭合模具的同时夹紧型坯上下两端,如图2-7b所示;再用吹管通入压缩空气,使型坯吹胀并贴于型腔表壁成型,如图2-7c所示;最后经保压和冷却定型,便可排除压缩空气并开模取出塑件,如图2-7d所示。
挤出吹塑成型的模具结构简单,投资少,操作容易,适合多种塑料的中空吹塑成形。
缺点是成型塑件的壁厚不均匀,塑件需要后加工以去除飞边和余料。
图2-7 挤出吹塑成型1—挤出机头;2—吹塑模;3—型坯;4—压缩空气吹管;5—塑件二注射吹塑成型注射吹塑成型是先用注射机将塑料在注射模中注射成型坯,然后将热的塑料型坯移入中空吹塑模具中进行中空吹塑成型,其工艺过程如图2-8所示。
成型时,首先用注射机将熔融塑料注入注射模中制成型坯,型坯成型在周壁带有微孔的空心凸模上,如图2-8a所示;接着趁热将空心凸模与型坯一起移入吹塑模内,如图2-8b所示;然后合模并从空心凸模的管道内通入压缩空气,使型坯吹胀并贴于吹塑模的型壁上,如图2-8c所示;最后经保压、冷却定型后放出压缩空气并开模取出塑件,如图2-8d所示。
注射吹塑成型的优点是塑件壁厚均匀,无飞边,不需后加工。
由于注射的型坯有底面,因此中空塑件的底部没有拼合缝,不仅外观美、强度高,而且生产效率高。
但是注射吹塑成型所用的设备与模具的投资较大,因而多用于小型中空塑件的大批量生产。
图2-8 注射吹塑成型1—注塑机喷嘴;2—注塑型坯;3—空心凸模;4—加热器;5—吹塑模;6—塑件。
塑料成型必看题库知识点三
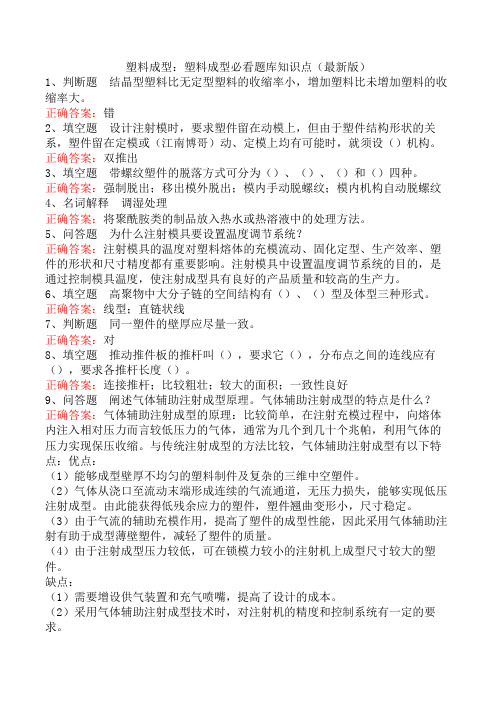
塑料成型:塑料成型必看题库知识点(最新版)1、判断题结晶型塑料比无定型塑料的收缩率小,增加塑料比未增加塑料的收缩率大。
正确答案:错2、填空题设计注射模时,要求塑件留在动模上,但由于塑件结构形状的关系,塑件留在定模或(江南博哥)动、定模上均有可能时,就须设()机构。
正确答案:双推出3、填空题带螺纹塑件的脱落方式可分为()、()、()和()四种。
正确答案:强制脱出;移出模外脱出;模内手动脱螺纹;模内机构自动脱螺纹4、名词解释调湿处理正确答案:将聚酰胺类的制品放入热水或热溶液中的处理方法。
5、问答题为什么注射模具要设置温度调节系统?正确答案:注射模具的温度对塑料熔体的充模流动、固化定型、生产效率、塑件的形状和尺寸精度都有重要影响。
注射模具中设置温度调节系统的目的,是通过控制模具温度,使注射成型具有良好的产品质量和较高的生产力。
6、填空题高聚物中大分子链的空间结构有()、()型及体型三种形式。
正确答案:线型;直链状线7、判断题同一塑件的壁厚应尽量一致。
正确答案:对8、填空题推动推件板的推杆叫(),要求它(),分布点之间的连线应有(),要求各推杆长度()。
正确答案:连接推杆;比较粗壮;较大的面积;一致性良好9、问答题阐述气体辅助注射成型原理。
气体辅助注射成型的特点是什么?正确答案:气体辅助注射成型的原理:比较简单,在注射充模过程中,向熔体内注入相对压力而言较低压力的气体,通常为几个到几十个兆帕,利用气体的压力实现保压收缩。
与传统注射成型的方法比较,气体辅助注射成型有以下特点:优点:(1)能够成型壁厚不均匀的塑料制件及复杂的三维中空塑件。
(2)气体从浇口至流动末端形成连续的气流通道,无压力损失,能够实现低压注射成型。
由此能获得低残余应力的塑件,塑件翘曲变形小,尺寸稳定。
(3)由于气流的辅助充模作用,提高了塑件的成型性能,因此采用气体辅助注射有助于成型薄壁塑件,减轻了塑件的质量。
(4)由于注射成型压力较低,可在锁模力较小的注射机上成型尺寸较大的塑件。
挤出成型和注塑成型的异同点

挤出成型和注塑成型的异同点挤出成型和注塑成型是两种常见的塑料加工工艺,它们在塑料制品生产中起着重要作用。
虽然它们都属于塑料成型工艺,但在操作原理、应用范围等方面存在一些明显的异同点。
相同点首先,挤出成型和注塑成型都是将塑料原料在一定温度下加工成所需形状的工艺过程。
它们都需要先将塑料颗粒加热熔化,然后通过成型模具得到成品。
在生产效率方面,两者也都能实现批量生产,适用于大规模生产。
其次,挤出成型和注塑成型都能生产多种形状和尺寸的塑料制品,如管材、板材、型材等。
无论是挤出成型还是注塑成型,都可以根据客户需求设计相应的模具,生产出符合要求的塑料制品。
异点1.操作原理不同挤出成型是通过挤压融化的塑料料料挤出成型,其操作原理是利用螺杆在加热的缸体中将熔融的塑料挤出成型。
而注塑成型是将熔化的塑料通过喷嘴注入模具腔内,通过高压使塑料充实模具腔形成成品。
2.适用范围不同挤出成型适用于生产连续性较强的产品,如各种塑料管材、型材等。
注塑成型则更适合生产成型精度要求高、产品结构复杂的塑料制品,如塑料零件、外壳等。
3.生产周期不同一般情况下,注塑成型的生产周期相对较短,适合快速交付需求较紧的订单。
而挤出成型的生产周期较长,主要由于挤出成型需要连续挤压和冷却时间。
4.设备结构不同挤出成型设备主要由挤出机、模具、冷却系统等组成,而注塑成型设备包含注射机、模具、冷却系统等部件。
挤出机专门用于挤出工艺,而注射机则是专门为注塑工艺设计。
总的来说,挤出成型和注塑成型各有其适用的场合和优势,根据具体产品要求和生产需求选择合适的工艺是至关重要的。
通过充分了解挤出成型和注塑成型的异同点,可以更好地进行生产计划和工艺优化,提高生产效率和产品质量。
注射拉伸吹塑成型工艺
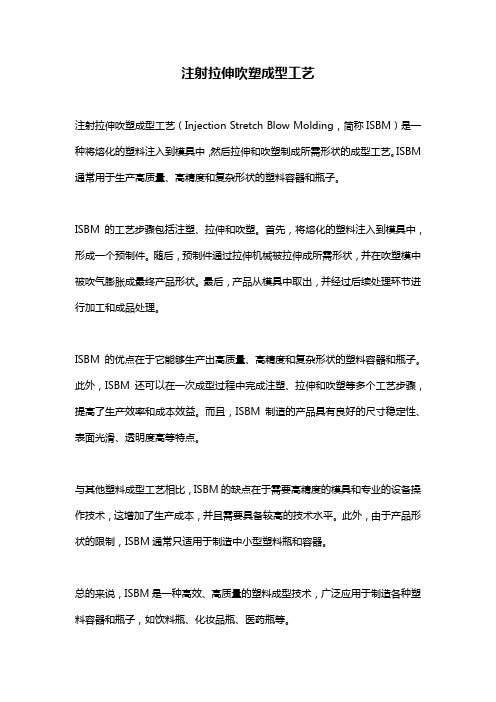
注射拉伸吹塑成型工艺
注射拉伸吹塑成型工艺(Injection Stretch Blow Molding,简称ISBM)是一种将熔化的塑料注入到模具中,然后拉伸和吹塑制成所需形状的成型工艺。
ISBM 通常用于生产高质量、高精度和复杂形状的塑料容器和瓶子。
ISBM的工艺步骤包括注塑、拉伸和吹塑。
首先,将熔化的塑料注入到模具中,形成一个预制件。
随后,预制件通过拉伸机械被拉伸成所需形状,并在吹塑模中被吹气膨胀成最终产品形状。
最后,产品从模具中取出,并经过后续处理环节进行加工和成品处理。
ISBM的优点在于它能够生产出高质量、高精度和复杂形状的塑料容器和瓶子。
此外,ISBM还可以在一次成型过程中完成注塑、拉伸和吹塑等多个工艺步骤,提高了生产效率和成本效益。
而且,ISBM制造的产品具有良好的尺寸稳定性、表面光滑、透明度高等特点。
与其他塑料成型工艺相比,ISBM的缺点在于需要高精度的模具和专业的设备操作技术,这增加了生产成本,并且需要具备较高的技术水平。
此外,由于产品形状的限制,ISBM通常只适用于制造中小型塑料瓶和容器。
总的来说,ISBM是一种高效、高质量的塑料成型技术,广泛应用于制造各种塑料容器和瓶子,如饮料瓶、化妆品瓶、医药瓶等。
挤出成型和注塑成型的区别和联系
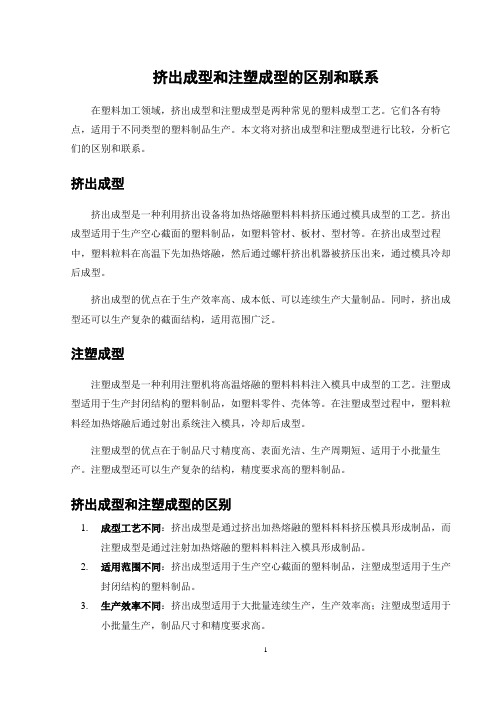
挤出成型和注塑成型的区别和联系在塑料加工领域,挤出成型和注塑成型是两种常见的塑料成型工艺。
它们各有特点,适用于不同类型的塑料制品生产。
本文将对挤出成型和注塑成型进行比较,分析它们的区别和联系。
挤出成型挤出成型是一种利用挤出设备将加热熔融塑料料料挤压通过模具成型的工艺。
挤出成型适用于生产空心截面的塑料制品,如塑料管材、板材、型材等。
在挤出成型过程中,塑料粒料在高温下先加热熔融,然后通过螺杆挤出机器被挤压出来,通过模具冷却后成型。
挤出成型的优点在于生产效率高、成本低、可以连续生产大量制品。
同时,挤出成型还可以生产复杂的截面结构,适用范围广泛。
注塑成型注塑成型是一种利用注塑机将高温熔融的塑料料料注入模具中成型的工艺。
注塑成型适用于生产封闭结构的塑料制品,如塑料零件、壳体等。
在注塑成型过程中,塑料粒料经加热熔融后通过射出系统注入模具,冷却后成型。
注塑成型的优点在于制品尺寸精度高、表面光洁、生产周期短、适用于小批量生产。
注塑成型还可以生产复杂的结构,精度要求高的塑料制品。
挤出成型和注塑成型的区别1.成型工艺不同:挤出成型是通过挤出加热熔融的塑料料料挤压模具形成制品,而注塑成型是通过注射加热熔融的塑料料料注入模具形成制品。
2.适用范围不同:挤出成型适用于生产空心截面的塑料制品,注塑成型适用于生产封闭结构的塑料制品。
3.生产效率不同:挤出成型适用于大批量连续生产,生产效率高;注塑成型适用于小批量生产,制品尺寸和精度要求高。
4.产品特点不同:挤出成型制品常为长条状或截面类,注塑成型制品常为封闭塑件或精密器件。
挤出成型和注塑成型的联系尽管挤出成型和注塑成型有着明显的区别,但它们也有一些联系点:1.塑料材料相同:挤出成型和注塑成型都是利用熔融后的塑料原料进行成型,所使用的塑料材料可能是相同的。
2.后处理工艺相似:挤出成型和注塑成型在成型后都需要进行一定的后处理工艺,如切割、去毛刺、打磨等,以满足制品的质量要求。
3.在某些制品上可互相替代:在一些特定情况下,挤出成型和注塑成型也可以相互替代,根据制品的形状、尺寸和数量来选择合适的生产工艺。
塑料加工技术

塑料加工技术一、引言随着塑料的广泛应用,塑料加工技术越来越重要。
塑料加工技术是指将塑料原料进行加工和改性处理,以得到满足不同需求的塑料制品的一系列工艺。
本文将介绍几种常见的塑料加工技术。
二、注塑成型技术注塑成型技术是利用塑料原料通过一定加热和加压的方式,使其成为液态或半固态状态,然后通过模具的开合和腔板之间的空隙将塑料进入模具腔内,在一定的温度、时间和压力下冷却固化成型的一种技术。
注塑成型技术可以生产出各种复杂形状的塑料制品,如盘子、碗、塑料外壳等,其优点是制品尺寸精度高、生产效率高、产品质量稳定。
三、挤出成型技术挤出成型技术是通过将塑料原料加热到熔融状态后,通过挤出机将熔化的塑料通过挤出口挤出模具,经过冷却后形成所需要的塑料制品的一种技术。
这种技术通常用于生产管道、线管、薄膜等。
挤出成型技术的优点是生产速度快、制品尺寸精度高、产品表面平整度高。
四、吹塑成型技术吹塑成型技术是将熔融的塑料原料通过挤出机拉出一条塑料管,再通过吹塑机将塑料管吹膨胀成型的一种技术。
这种技术通常用于生产塑料瓶、塑料盆等制品。
吹塑成型技术的优点是制品外观美观、生产效率高、生产成本低。
五、压延成型技术压延成型技术是将塑料原料加热到熔融状态后,通过压延机将其压延成薄膜或片状,然后通过冷却装置冷却并定型的一种技术。
这种技术通常用于生产薄膜、塑料泡沫板等制品。
压延成型技术的优点是生产成本低、生产效率高、制品厚度均匀。
六、回顾和总结塑料加工技术是指将塑料原料进行加工和改性处理,以得到满足不同需求的塑料制品的一系列工艺。
本文介绍了注塑成型技术、挤出成型技术、吹塑成型技术和压延成型技术四种常见的塑料加工技术。
每种技术都有其独特的工艺和优点,可以根据不同需求进行选择。
对于塑料生产厂家和消费者来说,选择合适的塑料加工技术很重要,可以确保制品的质量和性能。
注拉吹成型工艺

注拉吹成型工艺
注拉吹成型(Blow Molding)是一种常用的塑料制造工艺,用于制造中空容器或零件,如瓶子、桶、容器等。
该工艺结合了注塑成型和吹塑成型的特点,可以生产出具有复杂形状和中空结构的塑料制品。
注拉吹成型的基本步骤如下:
注塑(Injection Molding):在注拉吹成型机上,将熔化的塑料通过螺杆注射进注射腔体中。
注塑腔体通常具有与最终产品相似的外形,但内部为空心。
拉伸吹塑(Stretch Blow Molding):在注塑后,注射腔体会移动到吹塑腔体中。
在吹塑腔体中,通过先对塑料进行拉伸,然后再用气压吹塑,使塑料与腔体壁紧密贴合,形成中空的产品形状。
冷却与固化:在吹塑完成后,用冷却系统迅速冷却塑料,使其固化。
取出产品:一旦塑料完全固化,打开模具,取出成品。
注拉吹成型工艺具有以下优点:
高效生产:相对于传统的吹塑成型工艺,注拉吹成型速度更快,生产效率更高。
灵活性:可以制造出多种形状和尺寸的中空产品,适用于不同的应用领域。
产品质量:注拉吹成型制造的产品具有较好的密封性和均匀的壁厚,表面光滑,质量稳定。
成本效益:注拉吹成型相对于其他成型工艺来说,模具制造成本较低,适用于大规模生产。
注拉吹成型广泛应用于食品和饮料包装、化妆品容器、医疗器械、汽车零件等领域。
注吹成型工艺的优势及技术特点
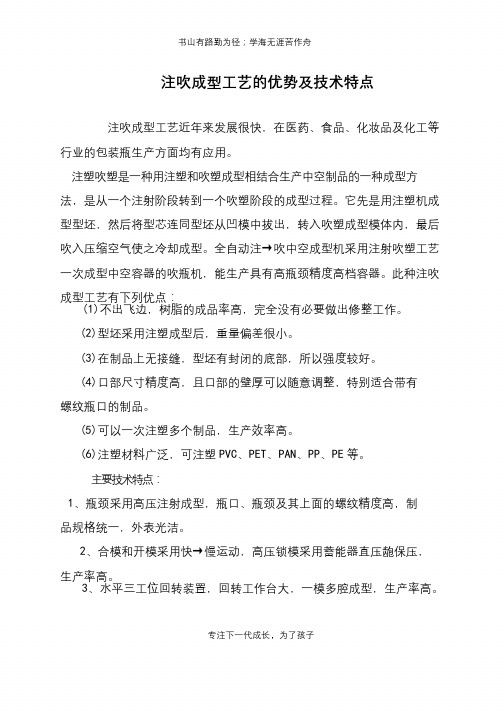
书山有路勤为径;学海无涯苦作舟
注吹成型工艺的优势及技术特点
注吹成型工艺近年来发展很快,在医药、食品、化妆品及化工等行业的包装瓶生产方面均有应用。
注塑吹塑是一种用注塑和吹塑成型相结合生产中空制品的一种成型方
法,是从一个注射阶段转到一个吹塑阶段的成型过程。
它先是用注塑机成型型坯,然后将型芯连同型坯从凹模中拔出,转入吹塑成型模体内,最后吹入压缩空气使之冷却成型。
全自动注→吹中空成型机采用注射吹塑工艺一次成型中空容器的吹瓶机,能生产具有高瓶颈精度高档容器。
此种注吹成型工艺有下列优点:
(1)不出飞边,树脂的成品率高,完全没有必要做出修整工作。
(2)型坯采用注塑成型后,重量偏差很小。
(3)在制品上无接缝,型坯有封闭的底部,所以强度较好。
(4)口部尺寸精度高,且口部的壁厚可以随意调整,特别适合带有
螺纹瓶口的制品。
(5)可以一次注塑多个制品,生产效率高。
(6)注塑材料广泛,可注塑PVC、PET、PAN、PP、PE等。
主要技术特点:
1、瓶颈采用高压注射成型,瓶口、瓶颈及其上面的螺纹精度高,制
品规格统一,外表光洁。
2、合模和开模采用快→慢运动,高压锁模采用蓄能器直压龅保压,
生产率高。
3、水平三工位回转装置,回转工作台大,一模多腔成型,生产率高。
专注下一代成长,为了孩子。
- 1、下载文档前请自行甄别文档内容的完整性,平台不提供额外的编辑、内容补充、找答案等附加服务。
- 2、"仅部分预览"的文档,不可在线预览部分如存在完整性等问题,可反馈申请退款(可完整预览的文档不适用该条件!)。
- 3、如文档侵犯您的权益,请联系客服反馈,我们会尽快为您处理(人工客服工作时间:9:00-18:30)。
与挤出吹塑相比,注射吹塑有下述优点。
(1)熔体被注入型坯模具型腔内时在周向受到一定的取向效应。
此外,型坯吹胀时的温度比挤出吹塑的低些,吹胀产生的取向效应能较多地保留下来,这些有助于提高容器的强度等性能。
(2)容器尺寸(尤其是颈部螺纹尺寸)精度高:较易于按要求保证容器壁厚的均匀性,容器规格均一。
(3)容器上不形成接合缝,不需修整,一般不产生边角料(挤出吹塑产生的边角料通常为5%~30%)。
(4)容器光泽度较高,采用透明聚合物成型的容器总是透明的。
(5)吹塑模具上可设置滑动式底模块,故容器底部形状的设计灵活性较大。
(6)更适于成型硬质朔料容器与广口容器。