PFMEA 汽车大灯配光镜注塑过程失效模式
轿车大灯配光镜注塑PFMEA

潜在的失效模式及后果分析(过程 FMEA)FMEA编号:项目名称:大灯配光镜过程责任部门:生产部编制人:FMEA日期(编制):2001.4.20车型年/车辆类型:轿车关键日期:2001.5FMEA日期(修订):2013.6.10页码:第页共页FMEA编号:项目名称:大灯配光镜过程责任部门:生产部编制人:FMEA日期(编制):2001.4.20车型年/车辆类型:轿车关键日期:2001.5FMEA日期(修订):2013.6.10页码: 第 页 共 页(S)潜在的失效模式及后果分析(过程 FMEA)银光丝(PZZ001)外观缺陷导致报废51.注塑速度过快;2.热流道、螺杆温度过高;3.模温过高;4.螺杆、针阀逃料41.按照注塑工艺文件对生产工艺进行点检;2.定期保养清理热流道针阀;3.定期对机床螺杆进行保养; 1.按照质量管理点对产品全数检查2.班组长每班定时巡检480无垃圾/颗粒(PZZ002)外观缺陷导致报废41.模具分型面较脏;2.车间清洁度不佳;3.静电风机未开;4.机械手夹具太脏4 1.定期保养模具;2.车间增加湿度;3.静电风机点检;4.定期更换夹具夹片;1.按照质量管理点对产品全数检查2.班组长每班定时巡检696无成形不足(PZZ003)外观及功能缺陷导致报废51.模温、热流道温度未达到生产要求;2.注塑量不足;3.螺杆内有混有空气31.模具生产前预热;2.按照注塑工艺文件对生产工艺进行点检;3.充分清洗螺杆;4.定期保养模温机,更换老化水道 1.按照质量管理点对产品全数检查2.班组长每班定时巡检690无气斑(PZZ004)外观缺陷导致报废51.注塑速度过快;2.热流道温度过低;3.模具排气不良5按照注塑工艺文件对生产工艺进行点检;1.按照质量管理点对产品全数检查2.班组长每班定时巡检41001.模具分型面开排气槽;2.启用压缩注塑功能53460丝流(PZZ005)外观缺陷导致报废41.模具镜面划伤;2.开机前未对模具镜面抛光5 1.首件确认;2.按照注塑开机标准作业书进行开机;3.定期对模具进行保养1.按照质量管理点对产品全数检查2.班组长每班定时巡检480无1-d-2注塑。
汽车大灯配光镜注塑过程PFMEA范例

FMEA编号:项目名称:大灯过程责任编制人:FMEA日期(编车型年/车辆类型:关键日FMEA日期(修页码:核心小开机潜在的失效模式及后果分析(过程FMEA)垃圾/颗粒(PZK002)外观缺陷导致报废41.模具分型面较脏;2.车间清洁度不佳51.定期保养模具;2.车间增加湿度首件点检5100按照注塑开机标准作业书进行开机43448成形不足(PZK003)外观及功能缺陷导致报废51.模温、热流道温度未达到生产要求;2.注塑量不足;3.螺杆内有混有空气41.模具生产前预热;2.按照注塑工艺文件对生产工艺进行点检;3.充分清洗螺杆首件点检360按照注塑开机标准作业书进行开机53345银光丝(PZZ001)外观缺陷导致报废51.注塑速度过快;2.热流道、螺杆温度过高;3.模温过高;4.螺杆、针阀逃料41.按照注塑工艺文件对生产工艺进行点检;2.定期保养清理热流道针阀;3.定期对机床螺杆进行保养;1.按照质量管理点对产品全数检查2.班组长每班定时巡检480无垃圾/颗粒(PZZ002)外观缺陷导致报废41.模具分型面较脏;2.车间清洁度不佳;3.静电风机未开;4.机械手夹具太脏41.定期保养模具;2.车间增加湿度;3.静电风机点检;4.定期更换夹具夹片;1.按照质量管理点对产品全数检查2.班组长每班定时巡检696无成形不足(PZZ003)外观及功能缺陷导致报废51.模温、热流道温度未达到生产要求;2.注塑量不足;3.螺杆内有混有空气31.模具生产前预热;2.按照注塑工艺文件对生产工艺进行点检;3.充分清洗螺杆;4.定期保养模温机,更换老化水道1.按照质量管理点对产品全数检查2.班组长每班定时巡检690无气斑(PZZ004)外观缺陷导致报废51.注塑速度过快;2.热流道温度过低;3.模具排气不良5按照注塑工艺文件对生产工艺进行点检;1.按照质量管理点对产品全数检查2.班组长每班定时巡检41001.模具分型面开排气槽; 2.启用压缩注塑功能534601-d-1开机1-d-2注塑设备故障设备导致产品无法生产51.螺杆加热系统损坏;2.安全保护装置失灵;3.锁模装置损坏;4.人为误操作损坏设备31.按照注塑开机标准作业书进行开机;2.定期对设备维护每天对设备进行设备点检230无1-d-3剪浇口破坏产品有效面外观,浇口修剪不平整外观缺陷造成报废4 1.操作人员手套不洁净;2.操作人员动作不规范;3.工具不良41.定期更换手套及操作工具;2.按照作业指导书进行操作;3.员工培训 1.按照质量管理点对产品全数检查2.班组长每班定时巡检464无污染产品表面外观缺陷造成报废3 1.操作人员手套不洁净;2.料车较脏21.定期更换手套;2.按照标准清洁料车班组长每班定时巡检424无产品有效面碰伤外观缺陷造成报废3 1.操作人员动作不规范;2.产品摆放不合理2 1.按照作业指导书进行操作;2.按照存放工艺卡放置产品;3.员工培训班组长每班定时巡检424无1e移至车间物流产品损坏导致产品报废4物流人员拉取过多2严禁超过最大拉取数量物流人员平稳拖运648无1f堆场存储表面尘点较多和产品混放导致产品报废,造成产品错装21.堆场混乱;2.堆场标识不清;3.堆场环境较差3对堆场进行目视化管理;增加清洁次数物流人员按标识拉取产品636无1g移至装配车间产品散落导致产品报废4物流人员拉取过多2严禁超过最大拉取数量物流人员平稳拖运648无标记处数标记日期1-d-4取放产品更改文件号签字日期处数更改文件号签字。
注塑件过程失效模式及后果分析表模板(PFMEA)

6
包装破损
零件污染,客户投 诉
5
产品碰伤砸伤 客户投诉
6
装箱时确认不足 货物堆积过高
搬运不规范
2
无
3
试验后制定合理堆 积标准
2
无
100目测 100目测 100目测
5 60 5 75 4 48
标签贴错 发错货,客户投诉 5
标签与实物未核对 2
无
100目测
4 40
产品数量不正确
客户投诉
6
80-出货检验
关键尺寸超差
第 1 页,共 2 页
注塑件过程失效模式及后果分析表模板(PFMEA)
零件号
设计责任部门
FMEA 编号
零件名称
关键日期
编制人
车型/年份
系统/子系统/部件
编制日期
核心小组
序号
过程
潜在的失效模式
严 潜在的失效后果 重
度
级 别
潜在的失效原因/机理
频 度 数
现行预防性设计控 制
现行探测性设计控 制
探 测 度
5 60 5 75
建议措施
责任人和目标 完成日期
无
采取的措施
严频探 R 重度测 P 度数度 N
无
无
无
无
不同产品分区放置, 并做好标识
6
2 5 60
无
对纸箱进行固定 6 2 5 60
无
无
无
无
无
不同产品分区放置, 并做好标识
6
2 5 60
无
对纸箱进行固定 6 2 5 60
无
40-原材料烘料
烘料时间不对 烘料温度不对
表面料花 色差
PFMEA失效模式分析案例

PFMEA失效模式分析案例标题:PFMEA失效模式分析案例研究PFMEA(Process Flure Modes and Effects Analysis)是一种用于识别、评估和防止潜在生产过程中可能出现的失效模式的工具。
本文将通过一个具体的案例来展示PFMEA的应用。
假设我们正在生产一款高端智能手机。
在生产过程中,我们发现产品的屏幕质量不稳定,经常出现亮点、坏点和其它显示问题。
为了解决这个问题,我们决定采用PFMEA进行失效模式分析。
首先,我们成立了一个由生产、质量、工程和技术人员组成的团队,对生产过程进行详细的分析。
我们发现,问题主要出现在液晶屏的贴合过程中,而这个过程又涉及到多个子过程,如屏幕切割、屏幕清洗、光学贴合等。
接下来,我们对每个子过程进行详细的失效模式分析。
我们发现,屏幕切割过程中可能会由于切割刀的磨损导致屏幕出现坏点;屏幕清洗过程中可能会由于清洗液的污染导致亮点;光学贴合过程中可能会由于压力不均导致坏点。
针对这些潜在的失效模式,我们提出了相应的风险评估和预防措施。
例如,对于屏幕切割过程中的切割刀磨损,我们可以采用更耐磨的切割刀,并定期进行检查和更换;对于屏幕清洗过程中的清洗液污染,我们可以定期更换清洗液,并定期检查清洗液的浓度;对于光学贴合过程中的压力不均,我们可以采用更先进的贴合设备,并定期进行维护和校准。
通过这些措施的实施,我们可以大大降低智能手机屏幕出现质量问题的风险。
我们还可以对生产过程中的其他潜在失效模式进行分析和预防,从而全面提升产品的质量和生产效率。
总结,PFMEA是一种有效的质量工具,可以帮助我们识别和预防生产过程中的潜在失效模式。
通过案例分析,我们可以看到,PFMEA不仅可以解决具体的问题,还可以帮助我们发现并解决更深层次的问题,从而实现持续改进和提升。
过程失效模式及后果分析(PFMEA)中英文

Process FMEA 过程FMEA
an analytical tool used by a process design team to identify potential product failures caused by failure of the manufacturing and assembly process to meet requirements, and identify corrective actions to be taken 是过程设计小组采用的一种分析方法,用于 识别由于制造或装配过程的失效而导致的潜 在产品失效模式,并确定所应采取的纠正措 施。
班组长) Industrial, mfg. And tool engineering,工业工程,工艺及
工装设计 quality,质量管理 materials engineering,材料工程 Service personnel,机修 Supplier of product and machinery,零件和设备供应商 Representatives from the next process, 后续工序代表
The leader should be the processresponsible engineer 小组组长应是过程设计责任工程师
2021/5/26
Cross-Functional Team 跨部门小组
5-9 people from,5-9人,由从事如下工作的人员组成
Design,设计 Assembly,装配 manufacturing (operators, supervisors),制造 (操作工,
2021/5/26
何谓PFMEA 何时作PFMEA 何人作PFMEA
PFMEA灯饰范本
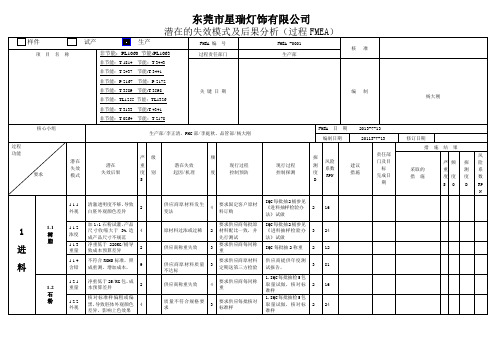
潜在的失效模式及后果分析(过程 FMEA)
样件
项 目 名 称
试产
√ 生产
非节能:PL1060 节能:PL1063
非节能:T-1814 节能:T-3443 非节能:T-2437 节能:T-3441 非节能:P-2167 节能:P-2172
FMEA 编
号
FMEA -0001 生产部
1.2.3 结 构 力 1.3.1 重量 1.3.2 拉力 1.4.1 重量 1.4.2 使 用 配比 1.5.1 颜色 1.5.2 重量
加 1:1 树脂试灌, 按产 品重量标准高度包装 试摔,胚体破碎, 低于 25KG/桶,成本预 算差异 脱模少于 300 次, 影响 模具使用次数及成本 预算 大桶低于 20KG/桶;小 罐低于 1KG/桶,造成 成本预算差异 最慢超过 30 分钟的反 应时间, 影响生产进度 颜色差异, 影响调油配 比 低于 4KG/加仑,成本 预算差异
漏电标注不符合 漏 电 UL 标注,有可能 (耐压) 导致人生安全
1.13.1 外观不 良
9
▲
3
1. 按 检 验 规 范 要 求抽检产品
5
135
1.对 所 有 产 品 100%打高 压测试
9 3
2
54
客人轻微抱怨
5
供应商检验不到 位
3
IQC 按检验规范要 求抽检产品 1.量 产 前 先 提 供 样品送第三方测 试, 2.IQC 按检验规范 要求抽检产品 IQC 按检验规范要 求抽检产品
2
30
抗压标准不及标准样, 4 潮湿,客户抱怨
3
3
36
1.12.1 安规标 识
不符合 UL 安规标 准,导致产品不 能出货 不合 UL 标准,导 致与客户要求不 符
冲压件FMEA 过程失效模式及后果分析

5 90
案●标准化运输 ●运输前进行确
流程
认,定期审核
5
90
●隔开包装
●零件固定包 装,防止零件 晃动 ●封闭车厢运 输●增加缓冲材 料
●运输模拟 ●运输模拟
●运输模拟 ●运输模拟
5 70
5 70
5 70 5 70
(编制)
果 RPN
●错检
●零件储存量
不足;影响产
品交付
6
●零件不良
●影响产品的 5
装配、焊接
机
●电极头氧化膜附着,电 流密度降低
3
机 ●电极头未对正
3
机 ●电极头端面直径超差
3
机 ●电极头端面不平
3
机 ●焊接分流
3
料 ●零件焊接面贴合不良
3
料 ●零件表面有油污,杂质 3
机
●焊接参数设置过低(焊 接电流,焊接时间和焊接
5
60
●调整前工序 ●班前零件检查 模具型腔
5
60
●焊接调试, ●使用电流计和 标准化参数 压力计定期检测
5
60
●零件表面除 ●班前零件检查 油
5
60
●标准化电极 ●班前电极检查 头管理规范
5
60
●标准化电极 ●班前电极检查 头管理规范
5
60
●作业人员培 ●定期检查 训
5 60
●按规定频次 ●班前焊接强度 打磨电极 检查
机
3
●叉车工违章操作,产品掉
人落
3
●包装器具破裂,零件放置
环 不稳定,掉落
3
●标识不明确
法
2
●放置区域不正确
法
2
●未按要求发料
过程潜在失效模式及后果分析程序(含表格)

文件制修订记录1.0目的:做好产前预防性工作,在设计与制造确定之前先探讨,并经由分析其中可能发生的错误、失效模式及失效模式对整体产品品质的影响,藉以早期找出失效原因与防止可预期性的错误发生,提高产品可靠度。
2.0范围:对公司生产汽车行业产品、军工类产品和客户有特殊要求的产品,以及超过了正常生产制作能力的产品。
3.0参考文件:3.1《文件控制程序》3.2《记录控制程序》3.3《纠正预防措施控制程序》4.0定义:4.1过程失效模式及后果分析(PFMEA:英文全称:Potential Failure Mode and Effects Analysis):由负责制造的工程师/工程师组为确保尽最大可能考虑并记录潜在失效模式和相关的原因/机理而使用的分析技术。
4.2控制计划(CP: 英文全称:Control Plan):是对用于控制生产零件和过程体系的文字描述。
由组织编写,陈述该产品重要特性和工程要求。
每个零件必须有一份控制计划,但是,在许多情况下可以对同一过程生产的一些零件应用“系列”控制计划。
在生产零件提交前要求客户认可控制计划。
4.3特殊产品的特性:特殊产品的特性(如关键、主要、重要、重点)是这样一种产品特性;对此合理地预测的变差,会明显影响产品安全性或政府标准或法规的一致性,或者会显著影响客户对产品的满意。
4.4特殊过程的特性:特殊过程的特性(如关键、主要、重要、重点)是这样一种过程特性;在制造和装配过程中,应保证特殊产品特性的变差保持在其目标值之内。
4.5 FMEA/CP多功能小组:由工艺工程师、工序主管、体系工程师、物理室主管、客服经理组成。
5.0职责权限:5.1体系部的职责:5.1.1负责参与FMEA、CP和WI一致性的评审。
负责FMEA正式版本的受控发行;5.2各部门:5.2.1 工艺部的职责:5.2.1.1负责作业指引和临时指引的编写修订;5.2.1.2 主导CP FMEA SPC的编写、修订控制和更新;5.2.1.3 负责修订文件或新岗位文件的培训和考核;5.2.1.4 依据顾客要求完成中英文版指引、控制计划、过程潜在失效模式及后果分析的编写、QC工程图等指导性文件的升级订本申请受控发行;5.2.2生产部的职责:5.2.2.1各个工序负责按照PFMEA的参数要求进行生产;5.2.2.2负责文件发行前的审核操作参数和保养频率的确认;5.2.2.3生产部各工序负责按照品质部的检验规范进行过程产品的自主检查和按照首板标准生产;5.2.2.4负责本生产部、生产工序的现用文件和资料使用及管理;5.2.3 FMEA/CP多功能小组的职责:每次FMEA/CP的更新前,由FMEA/CP多功能小组进行评审,从内部的需求,外部的需求,流程提醒的注意点等出发进行多方评审,保证FMEA、CP、工作指示一致性6.0程序:6.1工艺部针对新产品、新材料、新技术的要求,组织生产、工程、品质人员对本公司各生产工序在生产制造过程中存在的潜在失效模式及后果进行综合分析,并进行PFMEA活动。
- 1、下载文档前请自行甄别文档内容的完整性,平台不提供额外的编辑、内容补充、找答案等附加服务。
- 2、"仅部分预览"的文档,不可在线预览部分如存在完整性等问题,可反馈申请退款(可完整预览的文档不适用该条件!)。
- 3、如文档侵犯您的权益,请联系客服反馈,我们会尽快为您处理(人工客服工作时间:9:00-18:30)。
潜在的失效模式及后果分析
(过程 FMEA)
FMEA编号:
项目名称:大灯配光镜过程责任部门:生产部编制人:
FMEA日期(编制):
车型年/车辆类型:关键日期:FMEA日期(修订):
页码:第页共页
潜在的失效模式及后果分析
(过程 FMEA)
FMEA编号:
项目名称:大灯配光镜过程责任部门:生产部编制人:
FMEA日期(编制):
车型年/车辆类型:关键日期:FMEA日期(修订):
页码:第页共页
(过程 FMEA)
FMEA编号:
项目名称:大灯配光镜过程责任部门:生产部编制人:
FMEA日期(编制):
车型年/车辆类型:关键日期:FMEA日期(修订):
页码:第页共页
(过程 FMEA)
FMEA编号:
项目名称:大灯配光镜过程责任部门:生产部编制人:
FMEA日期(编制):
车型年/车辆类型:关键日期:FMEA日期(修订):
页码:第页共页
潜在的失效模式及后果分析
(过程 FMEA)
FMEA编号:
项目名称:大灯配光镜过程责任部门:生产部编制人:
FMEA日期(编制):
车型年/车辆类型:关键日期:FMEA日期(修订):
页码:第页共页
潜在的失效模式及后果分析
(过程 FMEA)
FMEA编号:
项目名称:大灯配光镜过程责任部门:生产部编制人:
FMEA日期(编制):
车型年/车辆类型:关键日期:FMEA日期(修订):
页码:第页共页。