SMT防错料PFMEA
SMT如何防止错料

填寫收料單与進料檢驗報 告并通知W/H
線外 發料
物料員按發料單与料站表核 對SMT料(須有進料合格 標簽) 上的料號備料,物料員 貼上標有料站的色點
Y
FQA核對料號/品名/色 點料站號是否OK 是否与料站表一致 (每一卷)
Y
在包裝LABEL上蓋合格章
Hale Waihona Puke N退回W/H重新備料 并發出制程异常通知單
物料員按發料單領料并核對數 量/料號/有無色點FQA合格章;
正常生產
PROD上料者負責讀料站 表上料站/料號,另一人 讀FEEDER上 物料的料號/机器的料站
N
將錯料換下并發出 制程异常通知單
N
FQA一人負責讀料站 表上料站/料號,另一人 讀物料的料號/机器的料站
PROD
SMT 上 料
備料,按料站表核對物料 上料號相應類型FEEDER 后置于備料架
上料時按料站表核對机 器上料站位及物料上料 號并填寫記錄
換料記錄表
班別: 日期:
項 換料 次 時間 1 2 3 4 5 6 7 8 9 10 11 12 13 14 15 16 17
產品名稱: 線 別:
料號
品名
換料者 簽名
机台:
确認者 簽名
備注
The end! Thanks!
IQC 檢 驗
按收料單与進料檢驗報告 核對外箱及REEL LABEL 上的料號/品名;
1.IQC量測REEL零件電性,依 一盤check 至少1 pcs,其他項 目依AQL
品名/料號是
Y
否有誤
N
外觀/尺寸/電性測試 N
是否OK
Y
貼上當月合格標簽
將不良材料貼上 紅色標簽并置于 退貨區
什么是PFMEA
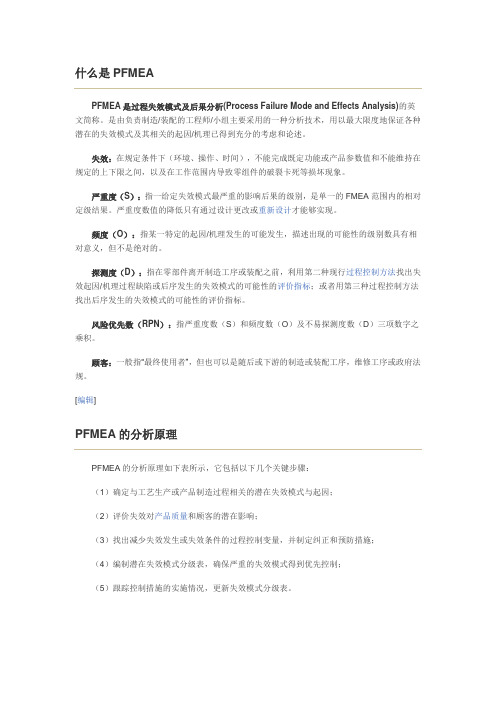
什么是PFMEAPFMEA是过程失效模式及后果分析(Process Failure Mode and Effects Analysis)的英文简称。
是由负责制造/装配的工程师/小组主要采用的一种分析技术,用以最大限度地保证各种潜在的失效模式及其相关的起因/机理已得到充分的考虑和论述。
失效:在规定条件下(环境、操作、时间),不能完成既定功能或产品参数值和不能维持在规定的上下限之间,以及在工作范围内导致零组件的破裂卡死等损坏现象。
严重度(S):指一给定失效模式最严重的影响后果的级别,是单一的FMEA范围内的相对定级结果。
严重度数值的降低只有通过设计更改或重新设计才能够实现。
频度(O):指某一特定的起因/机理发生的可能发生,描述出现的可能性的级别数具有相对意义,但不是绝对的。
探测度(D):指在零部件离开制造工序或装配之前,利用第二种现行过程控制方法找出失效起因/机理过程缺陷或后序发生的失效模式的可能性的评价指标;或者用第三种过程控制方法找出后序发生的失效模式的可能性的评价指标。
风险优先数(RPN):指严重度数(S)和频度数(O)及不易探测度数(D)三项数字之乘积。
顾客:一般指“最终使用者”,但也可以是随后或下游的制造或装配工序,维修工序或政府法规。
[编辑]PFMEA的分析原理PFMEA的分析原理如下表所示,它包括以下几个关键步骤:(1)确定与工艺生产或产品制造过程相关的潜在失效模式与起因;(2)评价失效对产品质量和顾客的潜在影响;(3)找出减少失效发生或失效条件的过程控制变量,并制定纠正和预防措施;(4)编制潜在失效模式分级表,确保严重的失效模式得到优先控制;(5)跟踪控制措施的实施情况,更新失效模式分级表。
(1)“过程功能/要求”:是指被分析的过程或工艺。
该过程或工艺可以是技术过程,如焊接、产品设计、软件代码编写等,也可以是管理过程,如计划编制、设计评审等。
尽可能简单地说明该工艺过程或工序的目的,如果工艺过程包括许多具有不同失效模式的工序,那么可以把这些工序或要求作为独立过程列出;(2)“潜在的失效模式”:是指过程可能发生的不满足过程要求或设计意图的形式或问题点,是对某具体工序不符合要求的描述。
PFMECA

PFMEAPFMEA的分析原理PFMEA是过程失效模式及后果分析(Process Failure Mode and Effects Analysis)的英文简称,是由负责制造/装配的工程师/小组主要采用的一种分析技术,用以最大限度地保证各种潜在的失效模式及其相关的起因/机理已得到充分的考虑和论述。
基本简介PFMEA[1]失效:在规定条件下(环境、操作、时间),不能完成既定功能或产品参数值和不能维[2]持在规定的上下限之间,以及在工作范围内导致零组件的破裂卡死等损坏现象。
严重度(S):指一给定失效模式最严重的影响后果的级别,是单一的FMEA范围内的相对定级结果。
严重度数值的降低只有通过设计更改或重新设计才能够实现。
频度(O):指某一特定的起因/机理发生的可能发生,描述出现的可能性的级别数具有相对意义,但不是绝对的。
探测度(D):指在零部件离开制造工序或装配之前,利用第二种现行过程控制方法找出失效起因/机理过程缺陷或后序发生的失效模式的可能性的评价指标;或者用第三种过程控制方法找出后序发生的失效模式的可能性的评价指标。
风险优先数(RPN):指严重度数(S)和频度数(O)及不易探测度数(D)三项数字之乘积。
顾客:一般指“最终使用者”,但也可以是随后或下游的制造或装配工序,维修工序或政府法规。
适用范围新件模具设计阶段。
新件试模、试做阶段。
新件进入量产前阶段。
新件客户抱怨阶段。
原理分析PFMEA的分析原理PFMEA的分析原理如下表所示,它包括以下几个关键步骤:PFMEA(1)确定与工艺生产或产品制造过程相关的潜在失效模式与起因;(2)评价失效对产品质量和顾客的潜在影响;(3)找出减少失效发生或失效条件的过程控制变量,并制定纠正和预防措施;(4)编制潜在失效模式分级表,确保严重的失效模式得到优先控制;(5)跟踪控制措施的实施情况,更新失效模式分级表。
模式分析“过程功能/要求”是指被分析的过程或工艺。
该过程或工艺可以是技术过程,如焊接、产品设计、软件代码编写等,也可以是PFMEA管理过程,如计划编制、设计评审等。
SMT 通用PFMEA
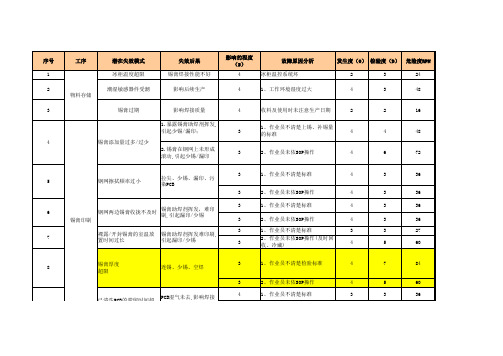
2
2
16
1.暴露锡膏助焊剂挥发, 引起少锡/漏印;
3
1、作业员不清楚上锡、补锡量 的标准
4
锡膏添加量过多/过少
2.锡膏在钢网上未形成 滚动,引起少锡/漏印
3
2、作业员未依SOP操作
4
4
48
6
72
钢网擦拭频率过小
拉尖、少锡、漏印、污 染PCB
3
1、作业员不清楚标准
4
3
2、作业员未依SOP操作
4
钢网两边锡膏收拢不及时
2
5
1、未作首件检查
4
5
2、首检人员疏忽
3
5
1、作业员对标准不熟悉
4
5
2、作业员未按SOP标准检验
4
5
1、制作部门出错
2
5
2、作业员工作疏忽取错文件
2
5
作业员不清楚客户记号内容
5
5
作业员未执行检验标准,无防 呆措施,
4
5
1、作业员不清楚标识标准
3
4
60
3
36
3
36
6
72
2
24
3
30
3
60
2
30
2
30
在作业指导书内规定过炉方式
对作业员培训作业指导书
当线技术员/管理员纠正 制作测温板时须5点以上,测出炉 温的各曲线之间相差≤5℃
改大体积的焊接工艺为手工焊接
更换马达
更换发热丝 重新安装控制软件
每周点检、确保其差异≤1mm
技术员检查并及时修复 技术员检查并及时修复 每周点检、确保其正常排风 对炉膛清洁:一次/每周 ≥1/4(油瓶容量) 有跳动时,在线工程师及时改善
SMT质量零缺陷控制计划PFMEA
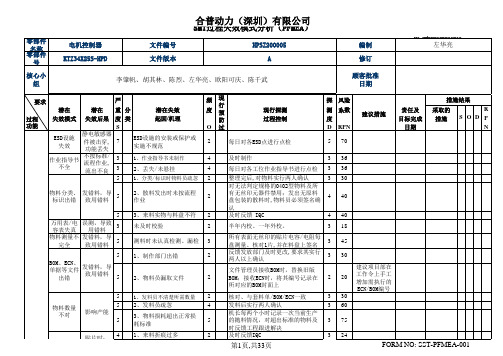
4
每日对各ESD点进行点检
5 70
及时制作
3 36
每日对各工位作业指导书进行点检 3 36
对作业员培训各类机器、Feeder类
型的识别方法
3 18
对作业员培训各Feeder类型与物料 类型匹配的方法
3
18
上料/换料后,对所上Feeder与物料 的匹配情况进行两人核对、确认
3
27
1、站位表制作后,实行两人确认
N
作业指导书 不按标准/ 3
不全
流程作业, 流出不良 3
5
1、作业指导书未制作
4
2、丢失/未悬挂
4
1、分类/标识时物料员疏忽 2
及时制作
3 36
每日对各工位作业指导书进行点检 3 36
整理完后,对物料实行两人确认
3 30
物料分类、 发错料,导 标识出错 致用错料 5
2、散料发出时未按流程 作业
2
对无法判定规格的0402型物料及所
度预 防
O过
现行探测 过程控制
3
执行“先出先消耗”原则
探 风险 测 系数 度 D RPN
2 18
该区环境湿 度过大
PCB、IC等 返潮,影响
焊接品质
4 4
1、空调性能下降
5
2、空调性能下降,该区管 理员未及时点检
5
及时反馈空调维修员
将裸露MSD置于恒温恒湿的干燥箱 内;对环境温湿度定期点检/监控
4 80 2 40
有无丝印元器件禁用;发出无原料 盘包装的散料时,物料员必须签名确
4
40
认
5 3、来料实物与料盘不符 2
及时反馈 IQC
4 40
万用表/电 容表失真
SMT上料防错解决方案

在SMT行业,贴片设备是连续高速运行的,如果在机种切换时不能有效的防止用错料或用错FEEDER,将造成批量的返工或报废从而给企业带来巨大损失。
要避免这种情况的发生,最好的办法就是在机种切换时、续料时、换料时、ECN变更时,能便捷有效地将待上料的机台、料站、料枪、通道以及料盘的对应关系与标准料站表进行比较,由系统自动根据校验规则进行校验,从而起到智能防错的效果。
简单的讲,上料防错就是由系统完成用户上料过程中扫描的物料标签、Feeder标签、站位标签与料站表资料的一致性校验,用自动化的系统校验取代出错率高的人工目检,从而简化人员作业、保障作业质量、提高生产效率。
那么要满足上述目标,首要的就必须对物料、料枪、料站甚至机台、料站表进行前期的统一编码管理,尤其是物料的内部编码。
在有些企业可能存在自主产品和OEM产品的生产,也就会有自购料和客供料的存在,不同供应商的物料编码、标签各自的规则都是不一样的,甚至有些国内的物料都没有条码,这就增加了物料编码的难度。
一般来讲上了ERP系统的企业,物料内部编码体系是比较健全的,但是也较少形成内部统一打印物料编码标签的规范。
所以在导入上料防错系统前,我们会协助企业进行编码及标签打印的规范化。
另外,上料防错系统也支持针对不同类型的物料的编码规则进行仿真,对已经有了物料编码标签的物料就可以进行识别。
图1:上料防错原理示意图我们的SMT上料防错系统需要提供下面几项功能:其一,提供上料、换料/续料、退料、QC抽检比对四种业务类型的上料扫描作业,并且特别考虑到用户的作业习惯,采用掌上作业终端和无线扫描枪+数据采集终端(DCT)等多种作业方式,最大程度上降低用户操作的繁杂度;其二,大部分SMT企业生产的电子产品涉及到单面板、双面板或者阴阳板,我们的上料防错系统支持各种复杂的产品结构,并最大程度上保持与客户的业务习惯相协调;其三,上料防错系统需要在收集了作业人员扫描的各种标签信息后才可以比对料站表资料,系统从扫描的便捷性、系统的易用性、作业结果及时反馈性、良好的错误预警提示等多个方面来防止作业人员的漏失,让系统真正发挥了作用,同时也减少一线人员对系统的抵触情绪。
PFMEA
3
不规范
3
作业员写错物料编码或位号
3
○ 1、维修员申请物料出错
3
2、维修员换错
5
1、作业员不清楚标识标准
5
2、作业员未按标准摆放
5
作业者不注意
5
全能工上物料时将物料上错
3
物料摆放不规范
第2页,共8页
频
度
现行预防
过程控制
现行探测 过程控制
O
2
每次生产时使用测温板测 试模拟锡膏供应商提供标 准制作温度曲线
每次生产前IPQC检查温度曲线是否符合标 准
6
根据IPC-A-610E三级标准 及客户的标准检查;
AOI
每天测试静电环,按防静
3
电要求操作,定期检测静 测试记录,IPQC巡检
电皮
培训员工的检查标准,无
3
法确认的需QE联系客户确 AOI
认
4
在SOP要求单项不良超2个 需要改善
AOI
4
按照《PCBA防护规范》作 业
静电敏感材料流入静电
元件早期失效
焊点虚焊、连焊
后续工序补焊 工序增多
焊接预热温度过高或过低
DIP焊接
根据PCBA产品工艺 要求
由于热冲击使 元件受损
PCB变形
锡炉速度快、慢
确认功能
符合参数指标
静电敏感材料流入静电
ESD设施 失效
首件(检查)出错
目视检查焊点达到
外观检查
焊接标准,不多件少 件,无损伤
BOM、ECN、丝印图出错
3
没按要求作业
3
1、作业员疏忽
3
1、书
3
2、作业员一时疏忽
SMT过程失效模式分析范例(PFMEA)
严频探潜在潜在重分潜在失效度现行探测测R 失效模式失效后果度类起因/机理过程控制度PSO DN冰柜温度过高锡膏焊接性能不好4冰柜温控系统坏2对冰箱温度进行每日点检324冰柜温度过低锡膏焊接性能不好4冰柜温控系统坏2对冰箱温度进行每日点检324真空封装机气压过高影响封装效果4气压过高2每日对真空封装机进行点检/空压机日常点检216真空封装机温度过高包装破损4设置不当3每日对真空封装机进行点检336真空封装机温度过低封装不严4设置不当3每日对真空封装机进行点检336真空封装机时间过长包装破损4设置不当3每日对真空封装机进行点检336真空封装机时间过短封装不严4设置不当3每日对真空封装机进行点检336ESD 装置/设备失效元器件静电击穿7ESD 设施安装保护实施不规范2每日对各ESD点进行点检570潮湿敏感器件受潮影响后续生产41、工作环境湿度过大4将MSD置于恒温恒湿的干燥箱内;对环境温湿度定期点检/监控34851、由于核对送货单时未核对出3收料员在接收原材料时,核对送货单与外箱标识、实物的物料编码、及采购订单确认一致后方可收料23052、由于外箱标识与送货单一致,但内装实物与单据不一致2对原包装最小包装5%的比例进行抽检55031、原包装本身就少料。
4对原包装最小包装5%的比例进行抽检560责任及目标完成日期建议措施措施结果DS O 现行预防过程控制无法使用影响生产送货单数量与实物不符物料购买/暂存送货单物料编码与实物不符文件版本A修订SMT过程失效模式分析(PFMEA)零部件名称电机控制器文件编号编制RPN 采取的措施核心小组顾客批准日期零部件号过程功能要求第1页,共36页FORM NO: SST-PFMEA-001等文件出错用错料第3页,共36页FORM NO: SST-PFMEA-00131、烘烤人员不清楚温度标准4培训《MSD管制办法》33632、MSD的标识不清晰2将《SMT MSD干燥记录表》记录清楚21233、未生产而长时间放置3长时间放置的MSD实行真空包装21831、烘烤人员不清楚厚度/间距标准4培训《PCB、IC烘烤作业指导书》33632、烘烤人员因“烤箱空间”不够而随意加厚、加密4严格执行《PCB、IC烘烤作业指导书》33631、烘烤人员不清楚裸露时间标准4培训《PCB、IC烘烤作业指导书》33632、烘烤人员未执行“先出先消耗”的原则3执行“先出先消耗”原则21841、空调性能下降5及时反馈空调维修员48042、空调性能下降,该区管理员未及时点检5将裸露MSD置于恒温恒湿的干燥箱内;对环境温湿度定期点检/监控24041、冰箱冷藏性能下降3及时反馈冰箱维修员33642、锡膏管理员不清楚标准3培训标准:锡膏存储温度在0~10℃22443、锡膏管理员未及时监控4点检(1次/2小时)控制在0~10℃23241、锡膏管理员不清楚标准3培训标准:锡膏存储温度在0~10℃22442、锡膏管理员未及时监控4点检(1次/2小时)控制在0~10℃23241、锡膏进料后的有效期短4检验出厂的瓶身标签:有效期≥6月34842、未执行“先进先出”3标识清晰,执行“先进先出”,严格控制锡膏存储期在6个月内22441、锡膏管理员不清楚标准4培训标准:室温下锡膏回温时间≥4H 23242、管理员控制的起止回温时间不清晰4利用《锡膏使用标识卡》严格记录/管控34843、因"急"而超前使用4“急”则须提前解冻34841、锡膏管理员不清楚标准4培训标准:室温下锡膏回温时间≥4H 23242、回温的起止时间标识不清楚4利用《锡膏使用标识卡》严格记录/管控34843、停产时,未将已解冻品及时回冻4《锡膏使用标识卡》标识清晰,工作环境中未开封放置不能超过24小时232烧录器电压不稳定程序拷贝时出错,影响功能5220V输入电压不稳定2每日对其进行点检44051、硬件、软件运行有误2每日对其画面显示状况进行确认33052、作业员违规操作3按照“PI-150”作业,禁止多余操作345拷贝电脑运行不正常程序拷贝时出错,影响功能锡膏活性下降,导致印刷性能下降锡膏回温解冻时间过长锡膏存储期限过长PCB、IC等返潮,影响焊接品质开封/烘烤后裸露时间过长PCB、IC等返潮,影响焊接品质该区环境湿度过大锡膏活性下降锡膏存储温度过低PCB、IC等湿度仍过大,影响焊接品质锡膏存储温度过高缩短锡膏存储周期,影响焊接品质摆放厚度过厚、间距过小PCB、IC等反潮,影响焊接品质MSD于干燥箱内的时间过长备/领出锡膏变质,影响焊接品质锡膏吸水引起锡珠\气泡\炸锡锡膏回温解冻时间过短第5页,共36页FORM NO: SST-PFMEA-00131、拷贝槽的拷贝脚弹性不够3每日对拷贝脚的完好性进行点检32732、IC的放置不到位3保证作业员将IC脚充分接触到拷贝槽的底部32733、IC脚氧化2发现时,及时反馈IQC63651、软件确认书或效验和或备录忘或ECN/BOM等文件出3对每个工单的首次软件拷贝的IC要求物料房拉长进行首件确认46052、用错软件5对每个工单的首次软件拷贝的IC要求物料房拉长进行首件确认37553、用错IC5对每个工单的首次软件拷贝的IC要求物料房拉长进行首件确认,并使用BOM/ECN核对所拷贝IC实物的正确性37551、作业员不能识别辅料型号/用途3对作业员培训《辅料型号、使用对照表》34552、作业员疏忽3领辅料时,实行两人确认345ESD设施失效静电敏感器件被击穿,功能丢失7ESD设施的安装或保护或实施不规范2每日对各ESD点进行点检57031、作业指导书未制作4及时制作33632、丢失/未悬挂4每日对各工位作业指导书进行点检33631、作业员不能识别Feeder类型2对作业员培训各类机器、Feeder类型的识别方法31832、作业员未掌握物料类型与Feeder类型的匹配方法2对作业员培训各Feeder类型与物料类型匹配的方法31833、作业员疏忽3上料/换料后,对所上Feeder与物料的匹配情况进行两人核对、确认32751、站位表的制作出错31、站位表制作后,实行两人确认2、站位表在上线使用之前,技术员必须用BOM核对站位表是否正确,交助工签名后方可使用34552、拿错站位表4拉长依据客户、机型、程序名领取站位表,与技术员实行两人确认36051、站位表出错3拉长依据客户、机型、程序名领取站位表,与技术员实行两人确认345拷贝槽与IC 的接触不良作业指导书不全不按标准/流程作业,流出不良程序不能拷入,影响功能生产辅料发错用错辅料拷错程序,影响功能/换错物料软件确认书,效验和,备录忘ECN,BOM未核对物料上线物料抛损、影响贴片质量Feeder(类型)使用出错错料站 位 表出错第6页,共36页FORM NO: SST-PFMEA-001清晰第8页,共36页FORM NO: SST-PFMEA-001出。
smt防错料方案
1. 引言在表面贴装技术(Surface Mount Technology,SMT)过程中,材料的选择和使用是至关重要的。
选择错误的材料可能导致焊接不良、元器件失效以及其他质量问题。
为了保证SMT过程的质量和可靠性,我们需要采取一系列的防错措施来确保选用正确的材料。
本文将介绍一些常用的SMT防错料方案,包括材料选择的考虑因素、过程控制的注意事项以及常见材料错误选用的解决方法。
2. 材料选择考虑因素在选择SMT材料时,需要考虑以下因素:2.1 元器件要求不同的元器件有不同的要求。
例如,某些元器件可能需要特殊的焊接温度曲线,而某些元器件可能对环境条件更为敏感。
因此,我们需要根据元器件的要求选择合适的材料。
2.2 焊接工艺要求不同的焊接工艺需要使用不同的材料。
例如,对于传统的波峰焊接工艺,我们需要选择具有良好耐热性和耐化学腐蚀性的材料;而对于无铅焊接工艺,我们需要选择符合RoHS要求的无铅材料。
2.3 成本考虑材料的成本也是一个重要的考虑因素。
我们需要在保证质量的前提下,选择性价比最优的材料。
3. 过程控制的注意事项在SMT过程中,除了材料选择外,我们还需要注意一些过程控制方面的问题。
3.1 温度控制温度是影响焊接质量的重要因素之一。
我们需要控制好焊接过程中的温度,确保温度不会过高或过低。
过高的温度可能导致元器件损坏,而过低的温度可能导致焊接不完全。
3.2 粘度控制在SMT过程中,我们通常使用胶水或焊膏来粘贴元器件。
粘度的控制非常重要,过高或过低的粘度都会影响焊接质量。
我们需要根据具体工艺要求,选择合适的粘度。
3.3 设备维护SMT设备的维护对于保证焊接质量也非常重要。
我们需要定期检查和保养设备,确保设备的正常运行。
同时,对于一些易损件,如喷嘴、胶管等,需要及时更换。
4. 常见材料错误选用的解决方法在SMT过程中,常见的材料错误选用问题包括焊膏和胶水的不匹配,无铅焊料的选择错误等。
以下是一些常见的解决方法:4.1 焊膏和胶水不匹配如果焊膏和胶水不匹配,在焊接过程中可能出现焊点开裂、焊接剥离等问题。
SMT贴片工程FMEA
每一失效模式的全部失效原因
O
1.客户/供方发料包装错误; 2.客户/供方发料时未确认数量;
4
Prevention 预防行动
CURRENT CONTROLS
Detection 侦测行动
Current controls to prevent failures occurring or detection of failure including Detectability ranking estimate
1.未开检查台灯;2.检查台灯损坏不亮;3.未配置 检查外观光源要求;
1.无外观缺陷检验标准;2.检查人员能力不足
1.上岗前未进行培训及考核;2.未对岗位员工能力 认定;
1.车间温湿度未监控;2.员工未使用防静电措施
2 1.按作业指导书进行生产前准备执行; 2 1.按作业指导书进行生产前准备执行; 3 1.按作业指导书执行; 3 1.按作业指导书执行; 2 1.按作业指导书执行; 3 1.培训及考核,并作成上岗技能矩阵图; 3 1.按作业指导书执行;
1.无外观缺陷检验标准;2.检查人员能力不足
2 1.按作业指导书执行; 3 1.培训及考核,并作成上岗技能矩阵图; 3 1.按作业指导书执行; 3 1.培训及考核,并作成上岗技能矩阵图; 3 1.按作业指导书执行; 2 1.按作业指导书执行;
1.吸头保养计划及记录 1.首件检查表 1.环境检查确认,每天/3次记录温湿度 1.首件检查表 1.检查前确认光源 1.主管确认检查人检查方式及要求
1.主管确认检查人检查方式及要求
3 1.培训及考核,并作成上岗技能矩阵图;
1.首件检查表
1.车间温湿度未监控;2.员工未使用防静电措施
3 1.按作业指导书执行;
- 1、下载文档前请自行甄别文档内容的完整性,平台不提供额外的编辑、内容补充、找答案等附加服务。
- 2、"仅部分预览"的文档,不可在线预览部分如存在完整性等问题,可反馈申请退款(可完整预览的文档不适用该条件!)。
- 3、如文档侵犯您的权益,请联系客服反馈,我们会尽快为您处理(人工客服工作时间:9:00-18:30)。
2
上料
上料放错站位
10
1、用错Feederlist; 2、Feederlist出错; 3、操作员放错站位
3
7
210
3
散料回补 散料回补放错料 feeder
6
散料回补时未确认极性、阻容 感数值及本体丝印
4
7
168
4
传输程序
程序版本错误
7
1、程序误操作 2、程序传输版本错
2
9
126
5
生产中物 Feeder取下重回 料报警 机器时放错站位
9
作业员混淆站位,未经确认即 开线
2
7
126
6
手摆件至 PCB
手摆件错料
6
1、炉前手摆件错料 2、取料维修时料取错
3
7
126
7
来料
来料错料
8
1、库房发错料 2、供应商直到物料搞混
1
5
40
8
BOM发放
BOM版本搞混
8
1、生产时未得到最新BOM 2、已有BOM发放搞混2232序号
工序
潜在失效模式
影响的程度 (S) 10
故障原因分析
发生度 检验度(D) (O) 4 7
危险度RPN
现行方案
需求方案
1
更换物料
换料时拿错料
作业员疏忽,核对不仔细
280
更换物料时,作业员相互确认,线长确认后方可继续 增加QA确认,QA人员 生产; 已到岗。 1、Feederlist由工程师专职管理签字,填写 Feederlist发放,回收记录,生产线禁止现生产产品 之外的list在线; 开线查料由操作员、 2、Feederlist发放前由工程师与程序核对,签字记 线长、QA三方核对无 录; 误后方可开线 3、开线查料时由操作员、线长、SMT工程师三人核对 无误后方可开线。 1、chip元件的电阻、电容、电感不得回补feeder; 2、 散料回补时必须在还有余料时回补,必须核对极 性及丝印,由线长或工程师确认,填写散料回补记录 单; 3、有散料回补后第一块PCB生产通知炉前检验,认真 检验极性。 1、程序电脑密码锁定,仅工程师、技术员授权操 作; 2、修改程序,填写程序修改记录;传输程序前核对 BOM,并填写程序传输记录; 1、同时间只允许一把Feeder离开机台,严禁多把 Feeder同时离开机台操作; 2、Feeder离开返回机台,需填写物料更滑记录; 1、炉前手摆件,需作业员以丝印图相互确认,线长 确认后方可过炉,填写手摆件记录单。 2、取料时以手摆件为参考,填写手摆件记录单,物 料标记清晰后粘贴在所需维修PCBA上; 1、所有电阻、电容、电感来料,LCR检测阻容感值; 2、芯片类与BOM和Sourcing部门核对本体丝印; 3、若料带中间有拼接,则所有拼接段都做阻容值测 量; 1、每次生产前工艺工程师与客户、与物控部门双向 确认BOM版本; 2、所有生产线使用BOM由工程师签字、记录、发放, 产品完成后收回,保证产线无当天生产之外BOM在 线; 3、生产车间禁止任何形式的BOM打印。