精益生产8大工具培训
精益生产八大浪费培训心得

精益生产八大浪费培训心得
精益生产八大浪费的培训让我深刻认识到了生产过程中的种种浪费现象,以及如何通过消除这些浪费来提高生产效率和质量。
下面是我的培训心得:首先,培训中提到的八大浪费包括:不良品、过度加工、多余搬运、等待、库存、运输、多余动作和制造过多。
这些浪费不仅会降低生产效率,还会增加成本,甚至影响产品质量。
通过培训,我了解到消除这些浪费的方法。
例如,对于不良品,可以通过提高质量控制和加强员工技能培训来减少;对于过度加工,可以通过优化工艺流程和合理安排生产计划来避免;对于多余搬运,可以通过合理布局生产和储存区域以及优化物流来减少;对于等待,可以通过实施精益生产中的“拉动”原则和实施紧急补货来消除;对于库存,可以通过实施“单件流”和“准时制”等精益原则来降低;对于运输,可以通过优化运输方式和提高生产计划的准确性来减少;对于多余动作,可以通过优化工作流程和实施“5S”管理来消除;对于制造过多,可以通过实施“计划受控”和“按需生产”等原则来避免。
在培训中,我们还学习了如何实施精益生产的各种工具和方法,如价值流分析、流程图、鱼骨图、5Why分析法等。
这些工具可以帮助我们更好地识别和消除浪费,提高生产效率和质量。
总之,精益生产八大浪费的培训让我深刻认识到了生产过程中消除浪费的重要性,以及如何通过实施精益原则和工具来提高生产效率和质量。
我相信这些知识和经验将对我未来的工作和生活产生积极的影响。
精益生产的十大工具

精益生产的十大工具精益生产的十大工具是精益生产方法中使用的工具和技术,旨在帮助企业提高生产效率、降低成本、提高质量。
精益生产是一套关于如何优化生产流程的方法论,其核心理念是通过消除浪费,实现更高效、更灵活的生产。
第一个工具是价值流图。
价值流图是将产品的生产流程可视化的工具,它可以帮助企业了解产品从原材料到最终交付的整个流程,从而找出生产中的浪费和瓶颈,并进行优化。
第二个工具是流程平衡。
流程平衡是通过平衡工作站之间的工作量,达到生产过程中的最佳效益。
通过优化工作站之间的工作分配,可以有效地降低等待时间,提高整体生产效率。
第三个工具是一体化生产系统。
一体化生产系统是通过整合产线上的各个工作站,实现生产过程的无缝衔接。
通过一体化生产系统,企业可以实现生产过程的整合和优化,提高生产效率。
第四个工具是短交付时间。
短交付时间是指将产品从订单到交付的时间尽量缩短。
通过缩短交付时间,可以提高客户满意度,同时也可以减少库存和浪费。
第五个工具是标准化工作。
标准化工作是指制定明确的工作标准和操作规范,确保每一项工作都能按照规定的要求进行。
通过标准化工作,可以提高产品质量和生产效率。
第六个工具是柔性生产。
柔性生产是指企业具备快速调整生产线的能力,以适应市场需求的变化。
通过柔性生产,企业可以更加灵活地应对市场变化,降低库存和生产成本。
第七个工具是持续改进。
持续改进是指企业不断地寻找改进的机会,并采取行动来实现持续的改变。
通过持续改进,企业可以不断提高生产效率和产品质量,保持竞争优势。
第八个工具是团队合作。
团队合作是指利用团队的力量,共同解决问题和实现目标。
通过团队合作,可以激发员工的创造力和合作精神,提高生产效率。
第九个工具是视觉管理。
视觉管理是指通过可视化的手段来传达信息和管理生产过程。
通过视觉管理,可以提高沟通效率,减少错误和浪费。
第十个工具是员工培训。
员工培训是指提供必要的培训和教育,使员工能够更好地理解和应用精益生产的方法。
精益生产管理的十大工具

精益生产管理的十大工具精益生产管理是一种通过优化生产过程,减少浪费和提高效率的方法。
在精益生产管理中,有许多工具和技术可用于帮助企业实现这些目标。
以下是精益生产管理的十大工具。
1. 价值流图:价值流图是一种可视化工具,用于展示产品或服务在整个价值流中的流动,包括所有的价值和非价值活动。
通过使用价值流图,企业可以识别出浪费和瓶颈,并制定改进计划。
2. 5S:5S是一个用于组织和维护工作场所的系统。
它包括整理、整顿、清扫、标准化和维持的步骤。
通过实施5S,企业可以改善工作环境,减少浪费和提高工作效率。
3. 高效供应链管理:高效供应链管理是通过优化供应链中的物流和信息流来降低成本和提高响应速度。
它包括减少库存、改善交付时间和优化供应链合作伙伴关系等方面。
4. 物料需求计划:物料需求计划是一种用于确定需要多少原材料和零部件的工具。
通过正确计划物料需求,企业可以避免库存积压和缺货的问题。
5. 单点作业:单点作业是一种通过减少从一台机器到另一台机器的传送时间来减少生产周期的方法。
这可以通过重新布局设备、改进工艺流程和优化工作站来实现。
6. 柔性生产:柔性生产是一种能够快速适应市场需求和变化的生产方式。
它包括灵活的工作组织、多功能的设备和高度培训的员工。
7. 持续改进:持续改进是一种通过不断寻找和消除浪费、改进工艺和提高质量来提升生产效率的方法。
它可以通过实施PDCA循环(计划、执行、检查、行动)和员工参与来实现。
8. 产能平衡:产能平衡是一种通过平衡生产线上的工作负荷来避免瓶颈和过度生产的方法。
这可以通过调整生产节奏、提高设备利用率和优化工艺来实现。
9. 供应商合作:供应商合作是一种与供应商建立长期合作关系,并与其共同努力改进质量、交付和成本的方法。
这可以通过共享信息、共同制定目标和进行持续改进活动来实现。
10. 质量管理工具:质量管理工具是一系列用于识别和解决质量问题的方法和技术。
其中包括流程图、因果图、直方图、散点图等。
精益生产培训之十大工具
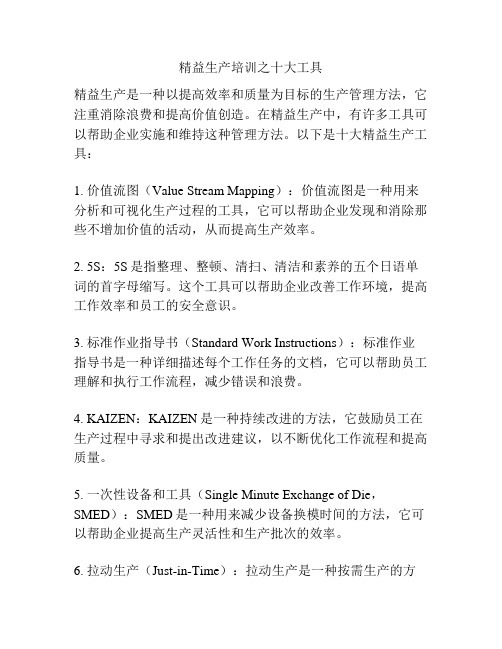
精益生产培训之十大工具精益生产是一种以提高效率和质量为目标的生产管理方法,它注重消除浪费和提高价值创造。
在精益生产中,有许多工具可以帮助企业实施和维持这种管理方法。
以下是十大精益生产工具:1. 价值流图(Value Stream Mapping):价值流图是一种用来分析和可视化生产过程的工具,它可以帮助企业发现和消除那些不增加价值的活动,从而提高生产效率。
2. 5S:5S是指整理、整顿、清扫、清洁和素养的五个日语单词的首字母缩写。
这个工具可以帮助企业改善工作环境,提高工作效率和员工的安全意识。
3. 标准作业指导书(Standard Work Instructions):标准作业指导书是一种详细描述每个工作任务的文档,它可以帮助员工理解和执行工作流程,减少错误和浪费。
4. KAIZEN:KAIZEN是一种持续改进的方法,它鼓励员工在生产过程中寻求和提出改进建议,以不断优化工作流程和提高质量。
5. 一次性设备和工具(Single Minute Exchange of Die,SMED):SMED是一种用来减少设备换模时间的方法,它可以帮助企业提高生产灵活性和生产批次的效率。
6. 拉动生产(Just-in-Time):拉动生产是一种按需生产的方法,它可以帮助企业减少库存和生产浪费,并且能够更好地满足顾客需求。
7. 故障模式与影响分析(Failure Mode and Effects Analysis,FMEA):FMEA是一种用来分析和评估潜在故障模式和其影响的方法,它可以帮助企业识别潜在风险,并采取措施进行预防和改进。
8. 委托管理(Gemba Walk):委托管理是一种通过实地走访生产现场来了解问题和挑战的方法,它可以帮助管理层与现场员工保持沟通,并及时解决问题。
9. PDCA循环:PDCA循环是指计划、实施、检查和行动的四个步骤,它是一种持续改进的管理方法,可以帮助企业不断优化工作流程和提高绩效。
精益生产培训中这些工具的作用

精益生产培训工具有哪些?精益生产培训工具如下:1.价值流分析(VSM)精益生产始终围绕着价值这个核心,关于价值有两个层面:①客户需要支付的价值; ②客户愿意多付的价值(增值)。
精益生产的价值更趋向于第②个层面。
价值流分析就是通过价值的2个层面对产品生产流程中的要素进行界定,首先去除浪费(客户不支付的),进而缩减客户不愿意多付的要素,从而实现设备和员工有效时间的最大化和价值最大化。
2.标准化作业(SOP)所谓作业标准化,就是对在作业系统调查分析的基础上,将现行作业方法的每一操作程序和每一动作进行分解,以科学技术、规章制度和实践经验为依据,以安全、质量效益为目标,对作业过程进行改善,从而形成一种优化作业程序,逐步达到安全、准确、高效、省力的作业效果。
生产流程经过价值流分析后,根据科学的工艺流程和操作程序形成文本化标准,标准不仅是产品质量判定的依据,也是培养员工规范操作的依据。
3.6S与目视化管理6S是现场目视化管理的有效工具,同时也是员工素养提升的有效工具。
目视化管理可以使标准可视化,问题点显露(异常早期发现,早期对策);可以使管理效率化,节省沟通的时间和异常反馈的时间;可以使浪费、不稳定暴露化,与理想、标准状态对比。
目视化管理的内容,一是规章制度与工作标准公开化,二是生产任务和完成情况图表化。
4.全员设备保全(TPM)TPM以设备全生命周期为对象,最大限度的发挥设备性能,追求生产系统效率化的极限,以零故障、零缺陷、零事故、(生产)零损失为总目标。
TPM以6s(整理、整顿、清扫、清洁、素养、安全)为基础,开展自主维护活动。
TPM以降低六大损失(设备故障、安装调整、空转短暂停机、速度降低、加工废品、初期未达产)来提高设备综合效率。
5.精益质量管理(LQM)精益质量管理是对作业系统质量、效率、成本综合改善的方法,是在精益生产与六西格玛关于作业系统相关理论方法基础上,吸收其他关于作业系统综合改善的相关理论和方法形成的管理模式。
精益生产知识培训(ppt
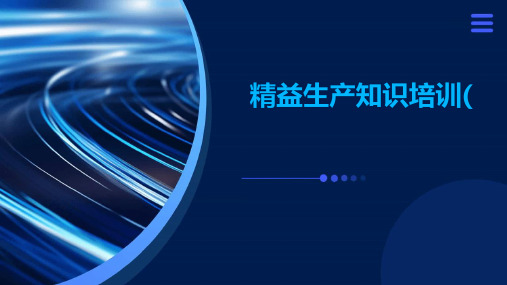
积极引入新技术、新工艺和新设备,提高生产效率和产品质量。
鼓励员工创新
鼓励员工提出改进意见和建议,激发员工的创新精神,促进企业持 续发展。
04
CATALOGUE
精益生产在服务业中的应用
服务流程优化
识别并消除浪费
01
通过对服务流程的全面分析,找出并消除浪费的时间、人力和
资源,提高服务效率。
客户需求导向
精益生产以客户需求为导向,注重满足客户需求和提高客 户满意度,通过快速响应市场需求和灵活调整生产计划, 实现个性化、定制化的生产。
02
CATALOGUE
精益生产的主要工具
5S管理
01
02
03
04
05
整理(Seiri)
整顿(Seiton) 清扫(Seiso)
清洁(Seiketsu 素养(Shitsuke
精益生产的核心思想
消除浪费
精益生产强调消除生产过程中的浪费,包括时间、人力、 物力等方面的浪费,以提高生产效率和降低成本。
持续改进
精益生产强调持续改进和优化生产过程,通过不断改进生 产方法、引入新技术、提高员工技能等方式,不断提高生 产效率和产品质量。
提高效率
精益生产注重提高生产效率,通过优化生产流程、提高设 备利用率、减少停机时间等方式,实现高效、低成本的生 产。
客户反馈机制
建立有效的客户反馈机制,及时了解客户的需求和意见,不断改 进服务,提高客户忠诚度。
持续改进与创新
持续改进
不断寻求改进的机会,通过持续改进提高服务质量和效率。
创新思维
鼓励员工提出创新性的想法和建议,以适应不断变化的市场需求和 客户需求。
跨部门合作
促进不同部门之间的合作,共同寻找改进和创新的机会,推动公司持 续发展。
精益生产培训(精选)
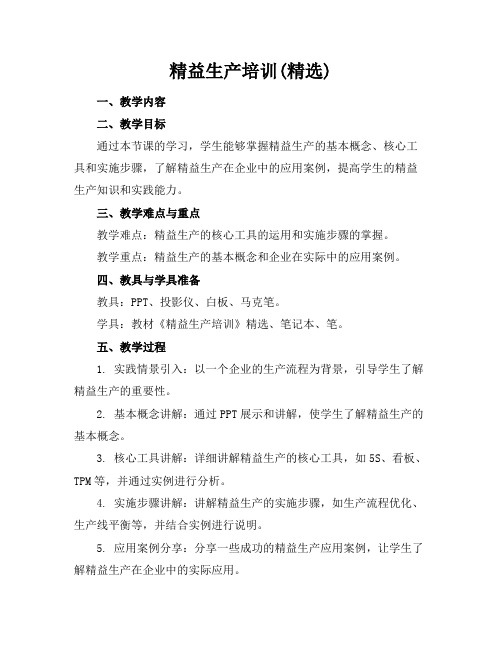
精益生产培训(精选)一、教学内容二、教学目标通过本节课的学习,学生能够掌握精益生产的基本概念、核心工具和实施步骤,了解精益生产在企业中的应用案例,提高学生的精益生产知识和实践能力。
三、教学难点与重点教学难点:精益生产的核心工具的运用和实施步骤的掌握。
教学重点:精益生产的基本概念和企业在实际中的应用案例。
四、教具与学具准备教具:PPT、投影仪、白板、马克笔。
学具:教材《精益生产培训》精选、笔记本、笔。
五、教学过程1. 实践情景引入:以一个企业的生产流程为背景,引导学生了解精益生产的重要性。
2. 基本概念讲解:通过PPT展示和讲解,使学生了解精益生产的基本概念。
3. 核心工具讲解:详细讲解精益生产的核心工具,如5S、看板、TPM等,并通过实例进行分析。
4. 实施步骤讲解:讲解精益生产的实施步骤,如生产流程优化、生产线平衡等,并结合实例进行说明。
5. 应用案例分享:分享一些成功的精益生产应用案例,让学生了解精益生产在企业中的实际应用。
6. 随堂练习:布置一些与精益生产相关的练习题,让学生进行思考和巩固。
7. 作业布置:布置一些有关精益生产的作业,让学生在课后进行深入学习和思考。
六、板书设计板书设计主要包括精益生产的基本概念、核心工具、实施步骤和应用案例等内容,用简洁明了的语言和图示展示给学生。
七、作业设计作业题目:1. 请简述精益生产的基本概念。
2. 请列举出精益生产的核心工具。
3. 请解释一下精益生产的实施步骤。
4. 请分享一个你了解的精益生产在企业中的应用案例。
答案:1. 精益生产是一种以消除浪费为核心的生产方式,旨在提高生产效率和质量,降低成本。
2. 精益生产的核心工具包括5S、看板、TPM、SMED等。
3. 精益生产的实施步骤包括生产流程优化、生产线平衡、标准化作业等。
4. 精益生产在企业中的应用案例可以是某汽车制造公司通过实施精益生产,提高了生产效率和质量,降低了成本。
八、课后反思及拓展延伸课后反思:本节课通过实践情景引入、基本概念讲解、核心工具讲解、实施步骤讲解、应用案例分享等环节,使学生了解了精益生产的基本概念、核心工具和实施步骤,并通过随堂练习和作业布置,让学生巩固所学知识。
精益生产的十大工具
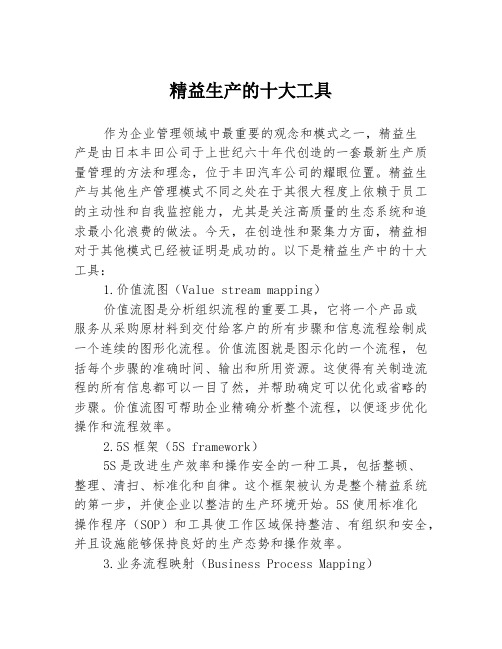
精益生产的十大工具作为企业管理领域中最重要的观念和模式之一,精益生产是由日本丰田公司于上世纪六十年代创造的一套最新生产质量管理的方法和理念,位于丰田汽车公司的耀眼位置。
精益生产与其他生产管理模式不同之处在于其很大程度上依赖于员工的主动性和自我监控能力,尤其是关注高质量的生态系统和追求最小化浪费的做法。
今天,在创造性和聚集力方面,精益相对于其他模式已经被证明是成功的。
以下是精益生产中的十大工具:1.价值流图(Value stream mapping)价值流图是分析组织流程的重要工具,它将一个产品或服务从采购原材料到交付给客户的所有步骤和信息流程绘制成一个连续的图形化流程。
价值流图就是图示化的一个流程,包括每个步骤的准确时间、输出和所用资源。
这使得有关制造流程的所有信息都可以一目了然,并帮助确定可以优化或省略的步骤。
价值流图可帮助企业精确分析整个流程,以便逐步优化操作和流程效率。
2.5S框架(5S framework)5S是改进生产效率和操作安全的一种工具,包括整顿、整理、清扫、标准化和自律。
这个框架被认为是整个精益系统的第一步,并使企业以整洁的生产环境开始。
5S使用标准化操作程序(SOP)和工具使工作区域保持整洁、有组织和安全,并且设施能够保持良好的生产态势和操作效率。
3.业务流程映射(Business Process Mapping)业务流程映射也被称为过程绘图,是企业中获得一些方案和改善的关键步骤。
此工具小组可以使用符号和图形描述企业中任何类型的业务流程和相关信息。
这可以揭示在过程中发生的问题、浪费、冗余和延迟,因此有助于消除不必要的步骤、改善流程的质量和效率。
4.一次流程变更(Single Piece Flow)这是一种最小化生产时间的原则,可以通过同一物品的生产技术一步步生产出多个物品。
使用一次流程变更工具,可以有效地降低制造成本,并使产品变得更加高效和可追溯,提高产品的核心竞争力。
5.生产平衡(Production Levelling)生产平衡是实现精益生产中的关键工具,可以帮助企业产生一个稳定的、平均的生产率水平。
- 1、下载文档前请自行甄别文档内容的完整性,平台不提供额外的编辑、内容补充、找答案等附加服务。
- 2、"仅部分预览"的文档,不可在线预览部分如存在完整性等问题,可反馈申请退款(可完整预览的文档不适用该条件!)。
- 3、如文档侵犯您的权益,请联系客服反馈,我们会尽快为您处理(人工客服工作时间:9:00-18:30)。
1913 1930
福特创造 了世界上 第一条流 水线
1950
1984
1997
ELSS
1975
丰田生产 系统(TPS) 概念提出 -丰田英二
1991
丰田与通 用汽车在 美国建立 合资工厂 (NUMMI) 精益研究 所在美国 成立,精益 概念提出
2001
精益的含义
精益是一种运营哲学,它的目标是不断缩短从定单接受到货物发运的时 间.它致力于削减这一过程中各环节的成本和耗用时间
Cycle Time = Process cycle time / (no of machines* no of pcs/cycle) Adjusted cycle time = cycle time / OEE (Uptime) WIP WIP Assy & Ship Grind Lead Time = Process cycle time HeatProcess Treat 5,600 1,200 单循环时间=过程循环时间/(设备数*生产件数/循环) Pieces Pieces 调整后的单循环时间 =单循环时间/OEE(正常运行时间) 过程生产周期=过程循环时间
Shifts/day
7.75 days CT ACT PLT = 60 = 66.7 = 120
4.0 days CT ACT PLT = 72 = 80 = 36000
5.6 days CT ACT PLT = 73.3 = 77.2 = 220
1.2 days CT ACT PLT = 60 = 60 = 60
Maintenance Issues 维护保养问题
Processes Not Capable过程能力 不足
Reducing inventory levels uncovers problems and forces their resolution.降低存货水平以揭露问题,最终迫使其 解决。
精益的演变及含义
7.75 days CT ACT PLT = 60 = 66.7 = 120
4.0 days CT ACT PLT = 72 = 80 = 36000
5.6 days CT ACT PLT = 3 = 77.2 = 220
1.2 days CT ACT PLT = 60 = 60 = 60
Suppliers’ Issues供应商 问题 Long Setups设 置时间长 Machine Downtime设备 宕机时间
Quality Productivity Problems质量 Problems生产率问 问题 题
Imbalanced Lines不平衡的 线路
Lack of Teamwork 缺乏合作
TLT = 19 days TPLT = 36,400 VAR = 2.36%
Lead Time & Cycle Times生产周期和单循环时间
Value Stream Map Minimum Requirements价值流图的最小要求
Production Control
Steel Suppliers
Value Stream Mapping (VSM)价值流图
5S Standardized Work标准化工作
Continuous Flow Manufacturing (CFM)连续流生产 Set up Reduction降低设置时间
Error Proofing防错 Total Productive Maintenance (TPM)全员生产性维护 Pull System (Kanban)拉动系统(看板)
七大浪费
精益8大工具
精益(工具)模型
点及连续 流改善
连续化作 业 减少换模 时间
系统化改 善
拉动系统 (看板,水平 化生产,‖邮 递员”供料 系统)
产品 族确认
价值流 程当前 图 5S 标准化 作业
价值流 程将来 图
防错 全面设备 维护 六个西格 玛工具
过程循环
捕捉最大的改善机会
Eaton Lean System Tools (ELS - 8) 伊顿精益生产系统工具
SS>>>Six Sigma, 六个西格玛
ELSS代表伊顿精益西格玛系统
精益的演变及含义
七大浪费
精益8大工具
七大浪费(Waste)
等待
运输
废/次品 残次品
过度生产
程序/流程
多余动作
库存
库存掩盖问题
Inventory Hides Problems存货隐含问题
Inventory Level 存货水平
绘制一幅地图去到达那里(执行计划)
绘制价值流图
观察并绘制从原材料到成品的物流及信息流的一种方法。这种方法可通过当前 状态价值流图帮助我们识别浪费、瓶颈和延误,并激励组织去开发一个未来的 精益状态景象。
Value Stream Mapping绘制价值流图
具体步骤是什么?
1 0.9
2 0.9
2 60
1 1.2
5 40.3
1
Total = 57 天 Total = 1 小时. 44.9 分.
为什么要先做价值流图?
如果你已知道要去何处,那速度才是最重 要的
– Joel Barker
Value Stream Mapping helps: 价值流图帮助
清楚我们所处的位置(当前状态价值流图) 我们要去何处(未来状态价值流图)
WIP
Heat Treat
WIP
Assy & Ship
4,000
Pieces
5,600
Pieces
1,200
Pieces
7,750
Pieces
# of Machines Pieces/Cycle Cycle Time 2 1 120
# of Machines Pieces/Cycle Cycle Time Setup Time OEE Shifts/day Men/shift
ELSS八个工具- 1 价值链流程图 (Value Stream Mapping)
采购定单
供应商
交货期15天
MRP
客户定单 单件节拍时间
客户
Takt Time = 440 min/44 = 10 min/unit
Bi-Monthly
45 天
工序 1
1天
工序 2 S/U = 0.08 hr CT = 0.9 min
市场开发 产品开发 供应商开发 开票及收款
制造 “墙到墙”
OEM 产品
设计 配置
物料计划及采购
客户询价,合同 谈判
客户定单输 入
定制 标准产品
生产计划
产品开发 及交付系统
元器件制造
组装及测试
包装及发运
业务规划
财务规划
其他
人力资源规 划
ELSS
E>>>Eaton, 伊顿公司 L>>>Lean, 精益
Daily Ship Orders Daily Priorities Daily Priorities
Delivery & Ship Schedules交付及发运计划
Forge
WIP WIP
Daily Demand 20 X Month and Takt Time =time/demand日需求
Grind
1 1
Process
Inventory Setup Time 3600 OEE 90% Information 存货信息
Shifts/day Men/shift 3 1
60 Flows 过程流程 0 100% 3 2
Process 95% 3 Information 过程信息 Men/shift 3
Supermarket 超级市场
Withdrawal 运回(需求)
Production Kanban 生产看板
Kanban arriving in Batches 一批看板到达
FIFO
Withdrawal Kanban 需求看板 Signal Kanban 信号看板 Kanban Post 看板架 First In First Out Lane 先进先出线路 Operator 操作工
1 500 36000 0 90% 3 1
# of Machines Pieces/Cycle Cycle Time Setup Time OEE
3 1 220 1800
# of Machines Pieces/Cycle Cycle Time Setup Time OEE Shifts/day Men/shift
# of Machines Pieces/Cycle Cycle Time Setup Time OEE Shifts/day Men/shift 1 500 36000 0 90% 3 1 # of Machines Pieces/Cycle Cycle Time Setup Time OEE Shifts/day Men/shift 3 1 220 1800 95% 3 3 # of Machines Pieces/Cycle Cycle Time Setup Time OEE Shifts/day Men/shift 1 1 60 0 100% 3 2
开发一个功能小组 根据价值流图标用铅笔进行绘制,以便于修改 从右上角的顾客开始绘制 计算需求节拍时间 信息收集后绘制顾客环、供应商环、过程环及信息 环 计算生产周期、增值时间及增值率 设定衡量标准及标杆 开发未来状态价值流图并不断重复此过程