永久阴极法铜电解生产工艺优化
浅析永久不锈钢电解和常规电解工艺

M etallurgical smelting冶金冶炼浅析永久不锈钢电解和常规电解工艺汪 涵摘要:本文对传统始极片电解和永久不锈钢电解工艺在生产中的各种要素进行了对比,对两种工艺的流程及主要生产环节的优缺点进行了全面的比较。
关键词:PC电解法;CT电解法;铜电解;铜冶炼;电解铜1 概述目前国内主要的铜电解精炼工艺可分为永久不锈钢阴极法和传统始极片大极板长周期常规电解法。
永久不锈钢阴极电解法简称PC电解(permanent cathode),是采用永久不锈钢阴极取代始极片的现代电解工艺。
传统常规电解法也称CT常规始极片(the conventional starting sheet process)电解,使用始极片(铜片)作为阴极的传统常规电解工艺。
PC电解技术与常规电解技术相比,具有工艺技术指标先进、产品质量高、劳动生产率高、生产成本低等优势,并在现代铜精炼工厂得到广泛应用。
在当前行业大力倡导绿色循环经济的发展模式下,PC电解技术不仅仅节约了生产成本,降低能耗,在技术上精益求精,也让企业获得了长足发展。
并且企业生产规模越大,在节水、节电以及减少二氧化碳排放的效应上就越明显。
金隆公司电解车间就是采用PC电解、常规电解两种工艺方法生产阴极铜,年产量共可达46万吨。
2 工艺流程PC电解系统的整个生产工艺基本实现机械自动化,阴极板是采用可循环使用的永久不锈钢板。
CT电解系统的生产工艺同样实现了高度的机械化,通过种板系统生产出电解所需的始极片(阴极板)。
两种电解方法的工艺流程如下。
2.1 常规电解工艺流程常规电解系统主要分为四部分,即始极片生产班组(种板生产班组)、机组加工班组、运转班组以及出铜班组。
首先是将合格的阳极板送至常规阳极整形加工机组,加工后的阳极按105mm极距排列,由电解专用吊车吊入种板电解槽。
同时种板生产班组将包边好的钛板按105mm极距排列,由电解专用吊车吊入种板电解槽。
先在阳极周期十八天,阴极周期一天。
永久不锈钢阴极铜电解槽系统的设计与实践

永久不锈钢阴极铜电解槽系统的设计与实践收稿⽇期:2011-06-30作者简介:代红坤(1969—),男,⾼级⼯程师,主要从事铜冶⾦⼯程设计研究、管理⼯作。
0前⾔为提⾼技术、装备⽔平,云铜引进了不锈钢阴极铜电解⽣产技术和极板、机组等设备建设新增电解产能项⽬。
该项⽬设计年产180kt ⾼纯阴极铜,已于2010年底投⼊试⽣产,系统运⾏正常,⽣产出了⾼品质的产品。
电解槽及其内、外部部件所构成的电解槽系统是电解⽣产中的关键部分,最终产品在其中产⽣,其设计的好坏对于产品质量、劳动强度、消耗等等都⾄关重要,本⽂重点介绍该系统的设计、施⼯和试⽣产⽅⾯的情况,对设计中存在的问题进⾏了分析。
1主要设计内容1.1主要设计参数云铜永久不锈钢阴极铜电解槽系统主要设计参数见表1。
1.2车间配置经计算,所需电解槽数为766个,考虑⼯艺配置和⽣产管理⽅便,取电解槽总数为784个,双跨配置,分24组,每跨12组,每跨有4组为每组32槽,8组为每组33槽,每组设⼀个⼤电流短路开关。
1.3电解槽电解槽为钢筋混凝⼟为槽体,内衬玻璃钢防腐层。
槽内尺⼨为:5750×1070×1250/1450mm 。
电解槽侧壁厚90mm ,端⾯及底⾯壁厚为150mm ,每两个电解槽之间的缝隙为30mm ,槽底单⾯纵向坡度4%,内衬玻璃钢防腐层厚度6mm (9层)。
1.4极板1.4.1阳极板结合云铜的现实情况,新的电解⼯场仍采⽤⼩永久不锈钢阴极铜电解槽系统的设计与实践代红坤(云南铜业股份有限公司,云南昆明650102)〔摘要〕介绍了云铜永久不锈钢阴极铜电解槽系统的设计主要内容及特点,对施⼯中出现的问题、试⽣产过程、取得效果进⾏了描述,对设计存在的问题进⾏了分析并提出了改进措施。
〔关键词〕永久不锈钢阴极;电解槽;极板;实践中图分类号:TF111.52⽂献标识码:B⽂章编号:1004-4345(2011)06-0029-04Design and Practice of Copper Electrolytic Tank System with Permanent Stainless Steel CathodesDAI Hong-kun(Yunnan Copper Co.,Ltd.,Kunming,Yunnan 650102,China)Abstract The paper introduces the design and design feature of copper electrolytic tank system with permanent stainless steel cathodes,describes the process of test run,problems in construction and the outcome obtained,analyzes the problems existing in design and puts forward some improvement measures.Keywords permanent stainless steel cathode;electrolytic tank;pole plate;practice表1主要设计参数项⽬参数项⽬参数电铜规模,kt/a 180阳极重量,kg 270年⼯作⽇,d 350阴极有效尺⼨,mm 908×900电解回收率,%99.6阳极周期,d 18电流密度,A/m 2280阴极周期,d 9残极率,%18每槽阳极数,⽚57同极距,mm 95每槽阴极数,⽚56电流效率,%96槽电压,V 0.35槽作业率,%96电解液循环速度,L/min ·槽30阳极有效尺⼨,mm 878×840有⾊冶⾦设计与研究第32卷2011年第6期12⽉图1电解车间配置极板,但与传统法所使⽤的⼤⼩⽿铜阳极板有明显的区别。
阴极铜生产工艺技术标准

阴极铜生产工艺技术标准引言阴极铜是一种重要的金属材料,在电子、通信、电力和建筑等领域有广泛的应用。
阴极铜的质量和性能直接影响到最终产品的质量。
因此,制定阴极铜生产工艺技术标准对于保证产品质量、提高生产效率具有重要意义。
本文档旨在提供阴极铜生产工艺技术标准的指导,包括原料准备、工艺流程、工艺参数等方面的要求。
1. 原料准备阴极铜生产过程中所使用的原料应符合以下要求:•铜源:使用高纯度电解铜作为铜源。
•补剂:根据工艺需要,选用适当补剂进行添加,如铁、镍、锡等。
2. 工艺流程阴极铜的生产工艺流程应包括以下几个主要步骤:2.1. 净化铜源使用电解铜作为主要原料时,应先进行铜源净化,以去除杂质和不纯物质。
具体净化步骤如下:1.采用酸洗方法,将铜源浸泡在稀盐酸中,去除铜表面的氧化皮和杂质。
2.用水冲洗铜源,去除酸洗残留物。
3.在碱性溶液中浸泡铜源,帮助去除冷冲孔和油脂等表面污染。
4.最后用纯水冲洗,确保铜源的纯净度。
2.2. 电解制备阴极铜电解制备阴极铜是主要的生产工艺步骤,具体流程如下:1.准备电解槽:选择合适的电解槽,并根据工艺要求调整槽液的组成和温度。
2.安装阳极和阴极:将净化后的铜源做为阴极,阳极使用铅。
3.填充电解槽:将电解槽填满电解液,液面应保持在适当位置。
4.启动电流:逐步增加电流强度,直到达到设定值。
5.电解反应:在设定电流和时间下,铜离子在电解中还原并沉积在阴极上,形成阴极铜。
6.分离阴极铜:根据生产需要,定期停止电解反应,将阴极铜从阴极上取下。
7.清洗和处理阴极铜:对取下的阴极铜进行清洗和处理,以去除表面污染,并得到纯净的阴极铜产品。
2.3. 后续处理根据生产需要,还可以对阴极铜进行进一步的处理,如除氧、除杂、静电除尘等,以提高产品质量。
3. 工艺参数要求阴极铜生产过程中的一些工艺参数需符合以下要求:1.电流密度:根据生产设备和工艺要求,设定适当的电流密度范围,以保证电解反应效果和阴极铜质量。
阴极铜的生产工艺流程
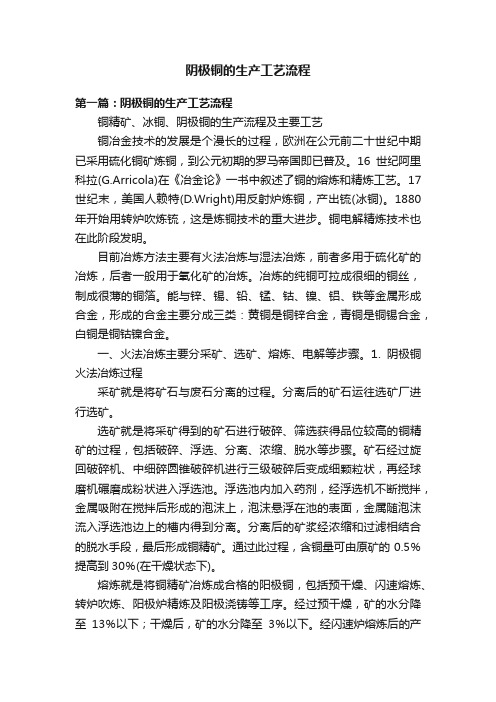
阴极铜的生产工艺流程第一篇:阴极铜的生产工艺流程铜精矿、冰铜、阴极铜的生产流程及主要工艺铜冶金技术的发展是个漫长的过程,欧洲在公元前二十世纪中期已采用硫化铜矿炼铜,到公元初期的罗马帝国即已普及。
16世纪阿里科拉(G.Arricola)在《冶金论》一书中叙述了铜的熔炼和精炼工艺。
17世纪末,美国人赖特(D.Wright)用反射炉炼铜,产出锍(冰铜)。
1880年开始用转炉吹炼锍,这是炼铜技术的重大进步。
铜电解精炼技术也在此阶段发明。
目前冶炼方法主要有火法冶炼与湿法冶炼,前者多用于硫化矿的冶炼,后者一般用于氧化矿的冶炼。
冶炼的纯铜可拉成很细的铜丝,制成很薄的铜箔。
能与锌、锡、铅、锰、钴、镍、铝、铁等金属形成合金,形成的合金主要分成三类:黄铜是铜锌合金,青铜是铜锡合金,白铜是铜钴镍合金。
一、火法冶炼主要分采矿、选矿、熔炼、电解等步骤。
⒈ 阴极铜火法冶炼过程采矿就是将矿石与废石分离的过程。
分离后的矿石运往选矿厂进行选矿。
选矿就是将采矿得到的矿石进行破碎、筛选获得品位较高的铜精矿的过程,包括破碎、浮选、分离、浓缩、脱水等步骤。
矿石经过旋回破碎机、中细碎圆锥破碎机进行三级破碎后变成细颗粒状,再经球磨机碾磨成粉状进入浮选池。
浮选池内加入药剂,经浮选机不断搅拌,金属吸附在搅拌后形成的泡沫上,泡沫悬浮在池的表面,金属随泡沫流入浮选池边上的槽内得到分离。
分离后的矿浆经浓缩和过滤相结合的脱水手段,最后形成铜精矿。
通过此过程,含铜量可由原矿的0.5%提高到30%(在干燥状态下)。
熔炼就是将铜精矿冶炼成合格的阳极铜,包括预干燥、闪速熔炼、转炉吹炼、阳极炉精炼及阳极浇铸等工序。
经过预干燥,矿的水分降至13%以下;干燥后,矿的水分降至3%以下。
经闪速炉熔炼后的产物称“冰铜”,液体状,铜含量50%--75%,与硫混合。
“冰铜”经转炉吹炼后的产物是“粗铜”,铜含量98.5%左右。
粗铜再经阳极炉精炼并经过圆盘浇铸机浇铸,即形成阳极铜。
铜电解不锈钢永久阴极的对比

铜电解不锈钢永久阴极的对比摘要本文介绍了目前各种不锈钢永久阴极的发展史、在国内铜行业的分布情况以及各种永久阴极的特点。
关键词铜电解不锈钢永久阴极导电棒一、概述铜电解精炼工艺1869年首次在工业上应用至今,就其基本原理而言,并没有重大变化。
而在围绕提高技术装备水平、扩大生产规模、提高阴极铜质量、降低能源和人工消耗等方面,则有了巨大的进步。
永久阴极铜电解,由于具有显著的优越性,从其问世伊始,就引起了铜冶金行业的巨大关注,并迅速在国外得以推广。
永久阴极工艺开发背景都是为了寻求平直的、垂直度好的阴极,从而消除因始极片弯曲不平给产品带来的影响。
目前世界上有六家阴极板生产厂家。
1、艾萨法永久阴极铜电解技术最早由澳大利亚Mount lsa公司的Townsville冶炼厂在1978年研制成功并投入生产,称为艾萨(ISA)电解法。
目前用ISA法生产的电解铜占全世界产量的1/3.我国最早引进该技术的是江铜贵溪冶炼厂。
2、Kidd法1986年加拿大鹰桥公司Kidd Creek冶炼厂也开发出了另一种不锈钢阴极生产工艺,成为Kidd法。
我国铜陵的金隆公司采用的就是此工艺。
3、EPCM法成立于1980年的EPCM公司制造不锈钢阴极已经20年了,它下属的则子公司Cobra是KIDD工艺的唯一制造商,由于鹰桥公司于2006年被XSTRATA收购,双方未能达成合作协议,于2007年终止合作。
于是开始自主开发了EPCM工艺,包括高性能阴极板(SP)和机器人剥片机组。
现在我国的山东阳谷祥光铜业公司后20万吨和中国瑞林设计院给紫金矿业设计的20万吨铜电解运用此工艺。
4、OT法OT法是芬兰奥托昆普公司近年来开发的另一种不锈钢阴极生产工艺,我国的山东阳谷祥光铜业公司前20万吨采用的就是此工艺。
5、博寿(Brochot)法BROCHOT公司创建于1825年,为重型物料搬运工业领域提供专用设备的制造。
BROCHOT公司在1987年成功进入中国市场,先后为20多家大型冶炼企业提供先进的设备及技术,现在已经确定在我国的天津建设一个不锈钢永久阴极的生产厂。
电解精炼工艺

本设计采用ISA法电解工艺。
图3-1 常规铜电解精炼工艺流程图
但是传统法的始极片制作工艺复杂,不仅需要独立的生产系统,而且制作过程中劳动强度过大。除此之外,这种工艺流程自身还存在两个难以克服的缺点:(l)电解精炼过程中存在“极限电流密度”,电解精炼时的实际电流密度必须低于极限电流密度,否则就会使阴极铜沉积表面粗糙,甚至形成“枝晶”,造成电解槽短路,使电解过程能耗大大增加,并且影响正常生产过程和产品质量。(2)容易形成“阳极钝化”,在正常电压下阳极不能溶解,必须提高电压使钝化膜在更高的电压下被破坏并溶解,不仅影响正常生产,还会造成电能浪费和阴极铜的化学成分不稳定,进而影响产品的质量和物理性能。
2、周期反向电流电解
周期性短时间改变直流电流方向的电解方法。电解阴极及阳极和常规电解相同,周期性短暂反向,是为了克服阳极钝化,电流密度达300~350A/m2。,可强化生产,节省投资,缩短电解铜在产周期。缺点是电流效率低,电耗高于常规电解。适于老厂扩大生产能力和电价低廉地区采有常规电解、周期反向电流电解和永久阴极电解三种方法可供选用。
1、常规电解
以纯铜始极片为阴极,电源为恒向直流电,电流密度为220~280A/m2。该法在世界各国均已有多年生产历史,工艺成熟可靠,电耗低。特别是采用了机械化、自动化水平高的阴阳极加工机组,并采用新技术适当提高了阴阳极板的垂直度以后,阴极铜产品质量得到显著的改善。常规电解精炼工艺流程见图3-1。
铜的电解精炼技术
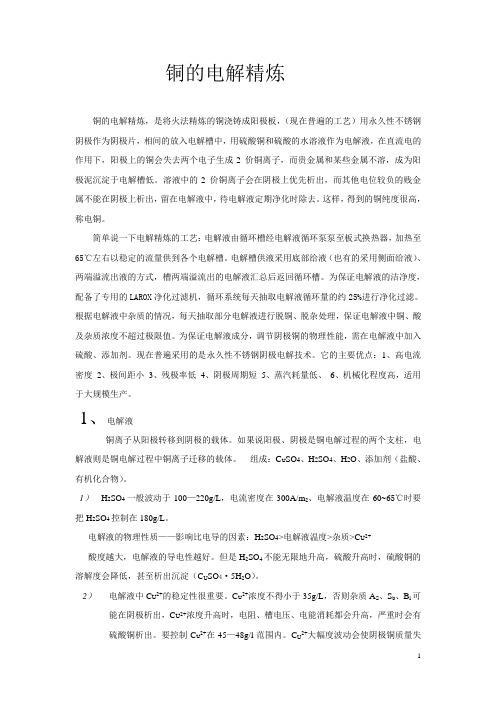
铜的电解精炼铜的电解精炼,是将火法精炼的铜浇铸成阳极板,(现在普遍的工艺)用永久性不锈钢阴极作为阴极片,相间的放入电解槽中,用硫酸铜和硫酸的水溶液作为电解液,在直流电的作用下,阳极上的铜会失去两个电子生成-2价铜离子,而贵金属和某些金属不溶,成为阳极泥沉淀于电解槽低。
溶液中的-2价铜离子会在阴极上优先析出,而其他电位较负的贱金属不能在阴极上析出,留在电解液中,待电解液定期净化时除去。
这样,得到的铜纯度很高,称电铜。
简单说一下电解精炼的工艺:电解液由循环槽经电解液循环泵泵至板式换热器,加热至65℃左右以稳定的流量供到各个电解槽。
电解槽供液采用底部给液(也有的采用侧面给液)、两端溢流出液的方式,槽两端溢流出的电解液汇总后返回循环槽。
为保证电解液的洁净度,配备了专用的LAROX净化过滤机,循环系统每天抽取电解液循环量的约25%进行净化过滤。
根据电解液中杂质的情况,每天抽取部分电解液进行脱铜、脱杂处理,保证电解液中铜、酸及杂质浓度不超过极限值。
为保证电解液成分,调节阴极铜的物理性能,需在电解液中加入硫酸、添加剂。
现在普遍采用的是永久性不锈钢阴极电解技术。
它的主要优点:1、高电流密度2、极间距小3、残极率低4、阴极周期短5、蒸汽耗量低、6、机械化程度高,适用于大规模生产。
1、电解液铜离子从阳极转移到阴极的载体。
如果说阳极、阴极是铜电解过程的两个支柱,电解液则是铜电解过程中铜离子迁移的载体。
组成:C U SO4、H2SO4、H2O、添加剂(盐酸、有机化合物)。
1)H2SO4一般波动于100—220g/L,电流密度在300A/m2、电解液温度在60~65℃时要把H2SO4控制在180g/L。
电解液的物理性质——影响比电导的因素:H2SO4>电解液温度>杂质>C U2+酸度越大,电解液的导电性越好。
但是H2SO4不能无限地升高,硫酸升高时,硫酸铜的溶解度会降低,甚至析出沉淀(C U SO4·5H2O)。
铜的电解精炼

铜的电解精炼铜的电解精炼,是将火法精炼的铜浇铸成阳极板,(现在普遍的工艺)用永久性不锈钢阴极作为阴极片,相间的放入电解槽中,用硫酸铜和硫酸的水溶液作为电解液,在直流电的作用下,阳极上的铜会失去两个电子生成-2价铜离子,而贵金属和某些金属不溶,成为阳极泥沉淀于电解槽低。
溶液中的-2价铜离子会在阴极上优先析出,而其他电位较负的贱金属不能在阴极上析出,留在电解液中,待电解液定期净化时除去。
这样,得到的铜纯度很高,称电铜。
简单说一下电解精炼的工艺:电解液由循环槽经电解液循环泵泵至板式换热器,加热至65℃左右以稳定的流量供到各个电解槽。
电解槽供液采用底部给液(也有的采用侧面给液)、两端溢流出液的方式,槽两端溢流出的电解液汇总后返回循环槽。
为保证电解液的洁净度,配备了专用的LAROX净化过滤机,循环系统每天抽取电解液循环量的约25%进行净化过滤。
根据电解液中杂质的情况,每天抽取部分电解液进行脱铜、脱杂处理,保证电解液中铜、酸及杂质浓度不超过极限值。
为保证电解液成分,调节阴极铜的物理性能,需在电解液中加入硫酸、添加剂。
现在普遍采用的是永久性不锈钢阴极电解技术。
它的主要优点:1、高电流密度2、极间距小3、残极率低4、阴极周期短5、蒸汽耗量低、6、机械化程度高,适用于大规模生产。
1、电解液铜离子从阳极转移到阴极的载体。
如果说阳极、阴极是铜电解过程的两个支柱,电解液则是铜电解过程中铜离子迁移的载体。
组成:C U SO4、H2SO4、H2O、添加剂(盐酸、有机化合物)。
1)H2SO4一般波动于100—220g/L,电流密度在300A/m2、电解液温度在60~65℃时要把H2SO4控制在180g/L。
电解液的物理性质——影响比电导的因素:H2SO4>电解液温度>杂质>C U2+酸度越大,电解液的导电性越好。
但是H2SO4不能无限地升高,硫酸升高时,硫酸铜的溶解度会降低,甚至析出沉淀(C U SO4·5H2O)。
- 1、下载文档前请自行甄别文档内容的完整性,平台不提供额外的编辑、内容补充、找答案等附加服务。
- 2、"仅部分预览"的文档,不可在线预览部分如存在完整性等问题,可反馈申请退款(可完整预览的文档不适用该条件!)。
- 3、如文档侵犯您的权益,请联系客服反馈,我们会尽快为您处理(人工客服工作时间:9:00-18:30)。
永久阴极法铜电解生产工艺优化
自1978年不锈钢阴极板应用于铜精炼,铜电解工业实现了跨越式发展。
永久阴极法采用了更平直的不锈钢阴极,经过几十年工艺不断的改进,其经济技术指标明显优于传统的始极片法电解,所以被大部分新建铜电解项目所采用。
在生产实践中各厂家均在持续优化铜精炼工艺,提升技术经济指标,降低生产成本。
1大冶有色30万t铜电解系统简介
大冶有色是国有控股的大型铜冶炼企业,于2012年10月竣工投产的30万t铜加工清洁生产示范项目,采用不锈钢永久阴极法电解。
电解系统2014年6月达产达标后,于2015年8月在英国金属交易所阴极铜注册成功。
电解分为东西区两个独立的系统,每个系统拥有电解槽512个,配置硫酸铜、电积和硫酸镍系统,电解流程图见图1。
火法系统浇铸的阳极板经阳极机组整形铣耳后,用专用行车装槽。
阴极到周期后,整槽起吊运至阴极剥片机组进行剥离作业,不锈钢阴极板返回电解槽,进人下一个周期。
剥离的阴极铜堆码打包,残极经过残极机组洗涤后返回火法系统。
换装作业人工用电解液冲洗电解槽底部阳极泥,用泥沙泵转人浓密机,再从底部输送到板框压滤机进行压滤,滤后液返回电解循环系统。
抽取四分之一的循环电解液进行精密
过滤。
每天外输一定体积的电解液通过硫酸铜、电积和硫酸镍系统进行净化。
电解系统工艺参数如表
2、生产中出现的主要问题
在电解过程中,阳极板中的脱模剂和石英砂沉人电解槽底部,然后被冲人地坑,因其比重较大,经常将地坑的搅拌桨淹没,影响正常生产,需要定期进行人工清坑作业。
为达到阳极泥含水要求,滤饼要经过大约一个半小时的吹风。
造成酸雾弥漫厂房,现场环境恶劣,经常发生阳极泥含水超标,2014年平均含水高达28. 5%。
当同区两组(32槽/组)同时洗槽作业,两台板框压缩机无法满足生产需求,现场无新设板框压滤机空间。
未及时更换破损的过滤布,会发生“跑黑”现象,
使阳极泥颗粒进人电解液的循环系统,影响的阴极铜质量。
电解项目自达产达标后,各项经济技术指标与同行业有一定的差距,其中A级铜产出率一般在99%,出现阴极铜质量波动。
电流效率在95%上下波动,直流电单耗在310 kW h/t.Cu左右。
3.1工艺优化
阳极泥压滤系统改造地坑新增流量为60m3/h,扬程52m,功率30kW,转速2950r/min的泥沙泵。
每次作业时,先进行搅拌,再启动泵。
每次作业完确保地坑无累积。
替换一台阳极泥板框为隔膜水压板框,其过滤面积为100 m2,高压鼓膜,自动液压压紧、保压、拉板卸料模式。
阳极泥先用隔膜水压板框进行第一次压滤,滤后液进人普通板框进行第二次过滤,滤后液进行精密过滤机过滤。
阳极泥泥浆经过了一次压滤、一次过滤和一次精密过滤后,电解液的纯净度明显提高。
改造后的阳极泥过滤流程如图2。
3.2电解液成分控制
一般认为高电流密度生产,需要提高Cu,浓度,确保阴极铜质量的稳定。
提高H2SO4的浓度,可以增加电解液的导电性,为降低电耗提供条件。
但Cu2+和H2SO4浓度的升高,增加电解液的比重,影响阳极泥的沉降。
在生产中有时电解液中Cu2+降到40g/L以下,依然能高产出高纯铜。
于是降低Cu2+浓度,在控制电解液比重前提下,适当提高H2SO4浓度,严格控制电解液其他杂质含量。
电解成分的控制主要是依靠增大开路的净化量。
电解液先经硫酸铜系统脱铜及其中的残胶,再经过一二段电积深度脱铜和脱杂,终液输送到硫酸镍系统脱镍。
3.3添加剂调整
铜电解的添加剂一般有明胶(骨胶)、硫脉和盐酸,少数厂家使用阿维酮等。
虽然铜电解使用添加剂已有百年的历史,但其机理目前还没有完全解释清楚。
添加剂的在线检测系统有人进行了研究,但一般还是凭经验调整加人量。
添加剂主要是控制阴极铜板面质量,过量是适量的好几倍。
添加剂有时效性,而其是否适量从阴极铜板面反应有延迟性,所以每个系统最佳的加入量非常难掌握。
在不影响阴极铜质量前提下,逐步降低其用量,达到最低值后,稳定加入量,最后明胶加入量稳定在43g/t,Cu、硫脲控制在70 g/t. Cu,2015年明胶单耗趋势如图3, 硫脲单耗趋势如图4。
在调整明胶和硫脉时,稳定盐酸加人量,按照180 mL/tCu的量加入。
新增阿维酮,按照9g/tCu的量加入。
3.4提高电解液温度
电解液的温度关系电解中离子扩散、离子活性和粘度等,即影响电解液导电性能和阳极泥的沉降等。
在高温下,漂浮阳极泥也会减少。
一般认为提高温度会增加添加剂消耗、提高溶解率、增加蒸发量和蒸
汽耗量等。
将电解温度由60-63℃控制提升到65-67℃。
4优化后效果
阳极泥过滤系统经过改造优化后,没有出现因板框压滤机正在压滤影响生产。
全年阳极泥含水量达到要求,平均22.6%,最低降到20%,详见图5。
压滤时间大幅缩短了,过滤饼一般10min就可以压干,卸完后马上进液,进行连续作业。
提升电解液温度,发现对加快添加剂的分解、阴极铜的溶解、电解液的蒸发量影响不是十分明显。
因为高电流密度生产,产生大量的焦耳热,并且电解
槽保温效果好,蒸汽耗量基本没有增加。
阳极泥过滤系统优化改造后,确保了电解液纯度,降低了添加剂用量和电解液粘度。
控制好电解液比重,有利于阳极泥的沉降。
增加净化开路量,减少系统残胶及杂质含量。
提高温度也会降低电解粘度,同时增加了离子的扩散和活性。
这些均有利于提升阴极铜质量,高纯铜产出率由2014年的平均99%提升至2015的99.5%,高纯铜产出率如图6。
当阴极铜质量稳定,工艺控制平稳,电流效率也稳定上升,2015年末升至98,详见图7。
电解液成分的合理控制,离子扩散的加快,致使槽压大幅下。