常见的退火问题及解决技巧
退火过程中易出现的问题

退火过程中易出现的问题
退火过程是一种常用的热处理方法,用于改善材料的力学性能和微观结构。
然而,在退火过程中,可能会遇到以下几个常见问题:
1. 晶粒长大不均匀:退火过程中,晶粒会发生再结晶和长大的过程,但有时晶
粒的长大不均匀,导致材料性能的不稳定性。
这可能是由于材料中的应力不均匀或退火温度过高造成的。
为解决这个问题,可以采取减小应力差异或降低退火温度的措施。
2. 结构过度软化:退火过程中,材料的晶格结构会发生调整,从而使其变得更
加柔软。
然而,如果退火时间过长或退火温度过高,结构可能会过度软化,导致材料强度过低。
要避免这种问题,可以通过控制退火时间和温度来调整结构软化的程度。
3. 晶界腐蚀:退火过程中,晶界区域是材料中最容易受到腐蚀和氧化的部分。
晶界腐蚀会导致晶界区域的性能下降,影响材料的整体性能。
为防止晶界腐蚀,可以采取气氛调节、封闭式退火或在退火过程中添加抗氧化剂等方法。
4. 尺寸变化:退火过程中,材料的尺寸可能会发生变化,尤其是在高温条件下。
这可能会导致工件尺寸不符合要求,给生产造成困扰。
为避免尺寸变化问题,可以在设计工艺时预留适当的收缩量,或在退火过程中采取适当的渐变冷却方法。
退火过程是一项复杂的工艺,需要考虑到多个因素的影响。
通过合理的操作和
控制,可以解决退火过程中出现的问题,确保材料获得良好的力学性能和结构特征。
退火处理_精品文档
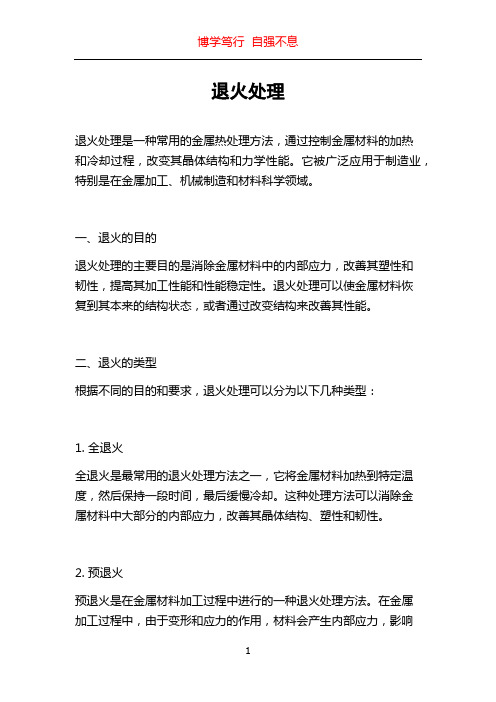
退火处理退火处理是一种常用的金属热处理方法,通过控制金属材料的加热和冷却过程,改变其晶体结构和力学性能。
它被广泛应用于制造业,特别是在金属加工、机械制造和材料科学领域。
一、退火的目的退火处理的主要目的是消除金属材料中的内部应力,改善其塑性和韧性,提高其加工性能和性能稳定性。
退火处理可以使金属材料恢复到其本来的结构状态,或者通过改变结构来改善其性能。
二、退火的类型根据不同的目的和要求,退火处理可以分为以下几种类型:1. 全退火全退火是最常用的退火处理方法之一,它将金属材料加热到特定温度,然后保持一段时间,最后缓慢冷却。
这种处理方法可以消除金属材料中大部分的内部应力,改善其晶体结构、塑性和韧性。
2. 预退火预退火是在金属材料加工过程中进行的一种退火处理方法。
在金属加工过程中,由于变形和应力的作用,材料会产生内部应力,影响其性能和稳定性。
预退火可以在加工前或加工过程中,通过加热和冷却来消除这些应力,提高加工性能和稳定性。
3. 理化退火理化退火是一种结合热处理和化学处理的退火方法。
它将金属材料加热到特定温度,然后在某种气氛或液体中进行一定的化学处理,最后进行冷却。
这种处理方法可以改善金属材料的表面性能,并增加其抗腐蚀性和耐磨性。
4. 高温退火高温退火是一种在高温下进行的退火方法,通常用于改善金属材料的晶体结构和强度。
高温退火可以使金属材料的晶粒生长,提高其晶体结构的稳定性和塑性,同时改善其抗变形和抗断裂性能。
三、退火的过程退火处理通常包括以下几个过程:1. 加热加热是退火处理的第一步,它将金属材料加热到特定温度,以改变其晶体结构和力学性能。
不同的金属材料有不同的加热温度要求,通常根据金属的熔点、晶体结构和性能要求来确定加热温度。
2. 保温保温是将金属材料在加热到目标温度后保持一定时间,使其晶体结构达到稳定状态的过程。
保温时间的长短取决于金属材料的类型和厚度,通常需要根据实际情况进行调整。
3. 冷却冷却是将金属材料从加热温度迅速冷却到室温的过程。
齿轮退火及正火常见缺陷及其对策

齿轮退火及正火常见缺陷及其对策齿轮的热处理分为预备热处理和最终热处理。
预备热处理的目的是消除和改善前工序引起的缺陷,为后续工序做好组织和性能准备。
而最终热处理的目的是使齿轮达到设计和使用的性能要求。
由铸造和锻造或轧制所产生的物件一般称为毛胚或钢材。
铸造时因铸件各部位自高温冷却时的冷却速度和凝固速度不同,或锻造轧制时因其各部分的壁厚和热加工终了温度不同。
常常会出现过热、粗大、不均匀晶粒等组织缺陷。
通过正火或退火改善以上组织缺陷:细化晶粒与组织,并消除残余应力,有利于切削加工,减小淬火变形以及提高力学性能等。
本文主要介绍预备齿轮热处理的退火和正火过程中常见的缺陷,产生的原因以及应对的策略退火常见缺陷及其对策退火:指将工件加热到适当的稳温度定,保持一定的时间,然后缓慢冷却的热处理工艺。
缓冷是指炉冷或坑冷。
即在炉中冷却到500度以下,再在空气中冷却到室温,或随炉冷却到室温。
一、硬度过高产生原因:1、中碳钢退火时加热温度过高,冷却速度太快,等温温度过低所致。
2、高速合金钢等温退火时,等温时间不足,随后冷至室温的速度过快,产生部分贝氏体和马氏体转变。
对策:严格执行退火工艺规范,控制冷却速度。
补救措施:重新退火。
二、粗大魏氏组织形成原因:加热温度过高和冷却速度较快时,在退火组织中容易产生。
对策:严格控制加热温度和冷却速度。
补救措施:通过完全退火或重新加热正火。
将针状组织完全溶解于奥氏体中,再进行正确的冷却,使晶粒细化,加以消除。
三、残留应力大产生原因:出炉温度偏高对策:随炉冷至350度以下出炉空冷补救措施:重新退火正火常见缺陷及其对策正火指加热到一定的温度,保温一定的时间后进行空冷风冷或喷雾冷却,以得到片状珠光体(或索氏体),获得较高的硬度和强度等的工艺方法。
一、表面严重脱碳产生原因:在氧化性气氛中长时间加热或重复加热。
对策:1、采用保护气氛或涂覆防氧化涂料2、适当增加工件的加工余量补救措施:无加工余量的齿轮进行复碳处理,对有加工余量的则采用机械加工去除脱碳层。
退火炉常见故障问题分析
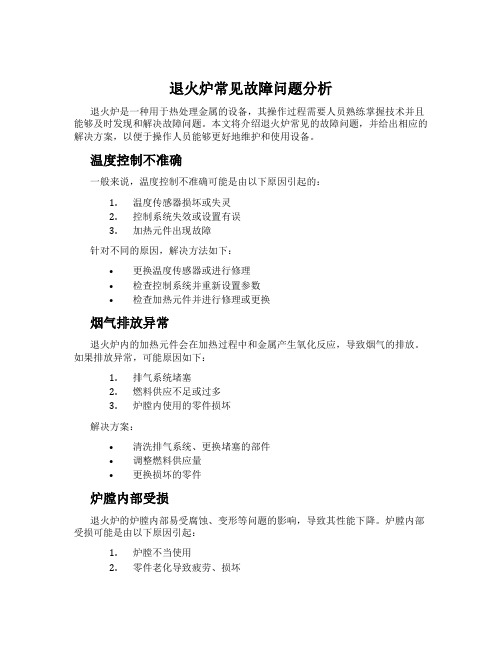
退火炉常见故障问题分析退火炉是一种用于热处理金属的设备,其操作过程需要人员熟练掌握技术并且能够及时发现和解决故障问题。
本文将介绍退火炉常见的故障问题,并给出相应的解决方案,以便于操作人员能够更好地维护和使用设备。
温度控制不准确一般来说,温度控制不准确可能是由以下原因引起的:1.温度传感器损坏或失灵2.控制系统失效或设置有误3.加热元件出现故障针对不同的原因,解决方法如下:•更换温度传感器或进行修理•检查控制系统并重新设置参数•检查加热元件并进行修理或更换烟气排放异常退火炉内的加热元件会在加热过程中和金属产生氧化反应,导致烟气的排放。
如果排放异常,可能原因如下:1.排气系统堵塞2.燃料供应不足或过多3.炉膛内使用的零件损坏解决方案:•清洗排气系统、更换堵塞的部件•调整燃料供应量•更换损坏的零件炉膛内部受损退火炉的炉膛内部易受腐蚀、变形等问题的影响,导致其性能下降。
炉膛内部受损可能是由以下原因引起:1.炉膛不当使用2.零件老化导致疲劳、损坏解决方案:•合理使用,保证操作规范,避免与金属接触时产生腐蚀、变形等情况•定期检查和更换老化太旧的零件,减少疲劳、损坏等不良影响其他故障问题除上述故障之外,退火炉还可能出现其他问题,如:1.电气设备故障2.液压油温过高或过低3.加热速度过慢针对不同的问题,解决方式如下:•修复电气故障•调整液压油温度设定值,检查油路是否通畅,更换损坏零件等•调整加热速度或更换损坏元件结论退火炉是一种重要的金属热处理设备,其稳定可靠的使用对于提高产品质量、增加生产效率具有重要作用。
不同的故障需要针对性的解决方案,操作人员应当在日常使用中,熟悉设备运行方式,避免或者及时解决出现的故障问题。
退火问题

提问:dennyktm退火后少子寿命会提高,是不是只是在一定的退火温度与退火时间内?另外如果硅块表面退火后表面形成氧化层,少子寿命也应该提高?最近一个单晶硅块头部、尾部退火后平均的少子寿命都比退火前各自的少子寿命低,与此同时少子寿命的宽度【min-max】较退火前也变窄了。
这是什么原因造成的呢?网友解答:jinmu205退火的范围很广,它至少包括退火温度、高温保持时间、降温速率以及您的工艺环境等。
就你所描述的,我认为:您的退火温度至少在950度以上,且降温过快。
可能是减少了氧的影响,因为氧会产生虚假寿命。
降温过快,使体杂质扩散开来,降底了体寿命。
解释仅供参考。
dennyktm我们退火温度是850度+6H,发现少子寿命降低后,尝试进行600度+1H,少子寿命依然在降低。
都是全程通少量氩气减少氧化、随炉冷却,没有采取快速冷却的工艺。
Ps:1、氧一般产生的是虚假的电阻率,对少子寿命应该是提高作用。
2、该温度下对其他体杂质的影响具体是什么呢?是金属杂质还是氧碳呢?jinmu205你做的是单晶样片吗?我也做过类似的实验,结果和你的差的多,寿命也降低了。
1、如果是单晶头部样片,应该出现氧施主,中心电阻率升高甚至转型。
退火后,这部分电阻率应该降低了吧?氧的存在,主要是多出的电子对对少子的捕获和施放,产生虚假高寿命。
经过高温纯化后,这部份就消除了。
2、退火不能改变氧、碳、金属等杂质的含量,但能改变其存在方式。
你高温6小时,冷却时加大氩气流量,使其快降温试试。
快冷能避免金属杂质的成核沉淀,能提高寿命。
个人见解。
dennyktm您退火完少子寿命也降低了?能说下退火的工艺吗?也是对开方完的单晶硅块退火吗?后来做出少子寿命升高的情况了吗?现在主要就是做少子寿命方面。
850度退火而且还是较长的时间,应该会有部分新施主形成,这个应该也会加剧少子寿命降低的幅度,但其本质原因是什么呢?我们做出的少子寿命分布图明显看出头部中心处少子寿命最低,而且衰减的最严重,反而边缘处少子寿命还会有所增加。
退火的三种主要方法

退火的三种主要方法
常用的退火方法有三种:
1、不完全退火
不完全退火是将铁碳合金加热到Ac1-Ac3之间温度,达到不完全奥氏体化,随之缓慢冷却的退火工艺。
不完全退火主要适用于中、高碳钢和低合金钢锻轧件等,其目的是细化组织和降低硬度,加热温度为Ac1+(40-60)℃,保温后缓慢冷却。
2、球化退火
只应用于钢的一种退火方法。
将钢加热到稍低于或稍高于Ac1的温度或者使温度在A1上下周期变化,然后缓冷下来。
目的在于使珠光体内的片状渗碳体以及先共析渗碳体都变为球粒状,均匀分布于铁素体基体中(这种组织称为球化珠光体)。
具有这种组织的中碳钢和高碳钢硬度低、被切削性好、冷形变能力大。
对工具钢来说,这种组织是淬火前最好的原始组织。
3、去应力式退火
去应力退火是将工件加热到Ac1以下的适当温度(非合金钢在
500-600℃),保温后随炉冷却的热处理工艺称为去应力退火。
去应力加热温度低,在退火过程中无组织转变,主要适用于毛坯件及经过切削加工的零件,目的是为了消除毛坯和零件中的残余应力,稳定工件尺寸及形状,减少零件在切削加工和使用过程中的形变和裂纹倾向。
厚玻璃退火常见问题的解决方法
厚玻璃退火常见问题的解决方法赵建军(秦皇岛耀华国投浮法玻璃有限责任公司,秦皇岛066000)摘 要: 浮法玻璃的退火常见问题主要是厚玻璃的切割难、边部炸裂,通过分析产生的原因,提出合理控制玻璃退火温度制度和边部温度;同时,采用烧边火等方法改善玻璃边部应力、减少裂边,提高切裁率。
关键词: 浮法玻璃; 退火温度; 应力; 烧边火Solution to FAQ(Frequently Asked Q uestions)of ThickG lass AnnealingZHA O Jian2j un(Qinhuangdao Y aohua Guotou Float G lass Co.,Ltd,Qinhuangdao066000,China)Abstract: FAQ(frequently asked questions)of float glass annealing are cutting difficulty and edge bursting of thick glass.This paper analyzes the reasons and puts forward reasonable control of glass annealing temperature schedule&edge temperature,and suggests the way of side firing which may be adopted to improve glass edge stress,reduce edge crack and increase cutting rate.K ey w ords: float glass; annealing temperature; stress; side firing 随着市场对平板玻璃原片不断增长的需求,浮法线的数量成倍增加,我国浮法玻璃的产能已位居世界第1位,同时建筑用的10mm以上厚度的需求量也在不断上升,我们注意到厚玻璃生产时成品率偏低,其中厚玻璃在退火过程中易发生裂边和切割困难,成为影响成品率的主要因素之一。
玻璃退火问题与切割
玻璃退火问题与切割一、厚玻璃退火问题的解决(1)生碴(糖状物)产生生碴的根本原因在于表层应力曲线不合理、板芯温度高、残余的板芯张应力过大,玻璃板在横掰时经常在断面上出现白色的生碴。
在退火曲线上表现为降温速度过快,调节的方法为降低锡槽出口温度,使A区入口温度保持在575〜580℃左右,提高B1区温度10℃左右、B2区15〜20℃左右、C1区20〜25℃左右、C2区出口15℃左右,上述数值是与5mm玻璃退火温度相比的。
(2)裂口玻璃板在横掰处,在刀口断面上有小的裂纹延伸到板里约1〜10mm左右。
这种玻璃在冷端斜坡输送辊上稍微受力就会自动炸开,有的在装箱后运输中炸裂。
这种情况出现的原因,一种是因为横掰辊子抬得过高引起,这可以通过调节辊子高度解决;另一种是因为退火造成的,又可分为两种情况:①裂口处在退火区温度相对较高,退火后区裂口处温度偏低,使此部位张应力太大。
可通过降低退火区裂口对应部位玻璃温度或升高退火后区裂口对应部位玻璃温度解决。
②板上下温差过大,有的C区板下温度比板上要高60〜70℃,而F区离横切较近,F区风管由于板下比板上堵塞严重,这就造成板下比板上风量小,这些因素使端面上部受张应力过大,强行掰断就易产生裂口。
调解上可以将C区板上温度适当上调。
有时裂口与生碴同时出现,调解上可先按处理生碴的方法调解,这时裂口有时会同时消失,若消失不了再按处理裂口方法调解。
(3)中分表现为中分不走刀口,出现多角或少角。
某厂曾对12mm玻璃进行过大片离线应力检测,应力曲线如图5-H(a)所示。
图$-11宜力曲线冷风工艺的应力曲线应为图5-n(b)所示。
(注:应力单位为度,1度=3.27m口光程差)由此可以看出,板中与两肋受永久压应力,造成中分不走刀口。
这种情况一般可通过提高B区中部温度或降低C区中部温度,增大横向温差,从而增大中间的张应力加以解决。
(4)掰边表现为掰边时出现多角或少角,掰不完整。
这种情况主要由自由边薄、散热快、温度低及退火窑边部密封不好使边部压应力过大引起的。
铝合金电缆退火炉常见问题及处理
铝合金电缆退火炉常见问题及处理铝合金电缆在制造过程中,通常需要进行退火处理以增加其强度和延展性。
铝合金电缆退火炉是用于对铝合金电缆进行退火处理的设备,但在使用过程中可能会出现一些常见问题。
下面将介绍几个常见问题及相应的处理方法。
问题1:温度控制不准确温度控制不准确是铝合金电缆退火炉常见的问题之一。
这可能是由于炉子的温度控制系统出现故障或者使用不当造成的。
处理方法:1.检查温度控制仪表和控制系统,确保仪表和传感器的准确性和正常工作。
2.检查温度控制系统的设定值和实际温度的差异,如果有差异,可以进行校正或调整。
3.如果是人为操作不当导致温度控制不准确,需要对操作人员进行培训和指导,确保正确操作。
问题2:加热时间过长或过短加热时间过长或过短可能会导致铝合金电缆的质量问题,如硬度不均匀或变形。
处理方法:1.检查加热控制系统,确保加热时间的设定值和实际加热时间的一致性。
2.如果加热时间过长,可以适当调低加热功率或增加传热介质的流速。
3.如果加热时间过短,可以适当增加加热功率或减小传热介质的流速。
4.对操作人员进行培训,确保加热时间的准确控制。
问题3:退火效果不理想退火效果不理想可能是由于退火炉的设计不合理、设备老化或退火工艺参数设置不正确所导致的。
处理方法:1.检查退火炉的设计,确保炉膛结构和退火工艺参数的设置符合退火要求。
2.定期对退火炉的设备进行维护和保养,如清洗加热元件、更换老化部件等。
3.重新评估退火工艺参数,根据实际情况进行调整和优化。
问题4:能源消耗高退火炉的能源消耗过高会增加生产成本,并对环境造成负面影响。
处理方法:1.对退火炉进行能源消耗的评估和分析,找出能源消耗高的原因。
2.升级退火炉的加热系统,采用更加节能高效的加热方式,如电磁加热或气体加热等。
3.加强维护和保养,确保设备的正常运行和高效利用。
问题5:安全隐患退火炉使用过程中,可能存在一些安全隐患,如温度过高导致炉体变形或热辐射引起人身伤害。
冷轧薄板退火工序中存在的三大问题冷轧薄板退火工序中存在的三大问题
冷轧薄板退火工序中存在的三大问题冷轧薄板退火工序中存在的三大问题冷轧薄板退火工序中存在的三大问题冷轧薄板退火工序中存在的三大问题粘结、氧化色和性能不合格是冷轧薄板退火工序中存在的三大问题,尤其是粘结与氧化色这两种缺陷较为突出。
一、粘结1、缺陷特征:退火钢卷层间互相粘在一起称粘结,粘结的形式有点状、线状和大块面粘合,粘结较严重时,手摸有突起感觉,多分布于带钢的边部或中间;严重的面粘结,开卷时被撕裂或出现孔洞,甚至无法开卷,成为“死卷”。
2、产生原因:(1)张力过大,张力是引起钢卷粘结的主要原因之一。
张力包括轧机的轧制张力和卷取张力。
张力过大时,会使保护气体的气流循环不好而产生热阻滞,使钢板发生粘结。
(2)板形不良,板形不好会使带钢在纵向上出现两边厚,中间薄或两边薄,中间厚或边浪、中间浪、多条浪及周边性的局部浪形等,经高温退火后,都能产生粘结。
(3)卷取时出现参差不齐的溢出边,带钢卷取不齐,特别是较薄的的板子,容易产生粘结。
(4)乳化液不纯,乳化液中有杂物,经退火蒸发后残留于钢板与钢板之间,如吹除不净,也会产生粘结。
(5)超温,不管是什么原因引起的,如果炉内出现严重超温时,也必然要引起粘结。
(6)气体循环不良,由于装炉堆垛不符合要求,致使保护气体在炉内循环不好,使炉温不均匀,个别部位形成热阻滞严重,温差大而产生粘结。
(7)带钢表面粗糙度太小。
(8)钢质太软,钢中碳、硅含量少,粘结倾向高。
(9) 冷却速度太快。
3、预防及消除方法:(1)正确选择卷曲张力。
(2)控制工作辊粗糙度。
(3)控制好板形和卷形。
(4)按堆垛原则堆垛,将塔形卷,溢出边卷放置钢垛上部。
(5)遵守操作规程,控制退火温度和时间。
(6)保证退火设备的完整性,检测仪表准确,热电偶插放到位等。
4、检测判断:(1)用肉眼检查。
(2)普通冷轧板及钢带允许有局部的粘结痕迹,标准中有明确规定的不允许存在。
(3)严重的粘结判废。
二、氧化色(氧化边)1、缺陷特征:钢板及钢带表面被氧化,其颜色由边部的深蓝色逐步过渡到浅蓝色、淡黄色,统称氧化色。
- 1、下载文档前请自行甄别文档内容的完整性,平台不提供额外的编辑、内容补充、找答案等附加服务。
- 2、"仅部分预览"的文档,不可在线预览部分如存在完整性等问题,可反馈申请退款(可完整预览的文档不适用该条件!)。
- 3、如文档侵犯您的权益,请联系客服反馈,我们会尽快为您处理(人工客服工作时间:9:00-18:30)。
应力消除退火则是在变态点以下450~650℃加热一段时间后徐徐冷却至室温,可消除钢材内部在切削、冲压、铸造、熔接过程所產生的残留应力。对碳钢而言,参考的加热温度為625±25℃;对合金钢而言,参考的加热温度為700±25℃。持温时间亦会有所差异,对碳钢而言,保持时间為每25mm厚度持温1小时;对合金钢而言,保持时间為每25mm厚度持温2小时,冷却速率為每后25mm以275℃/小时以下的冷却速率冷却之。
常体结构?
退火处理会使钢材变软,淬火处理会使钢材变硬,相比较之下,如施以『正常化』处理,则可获得层状波来铁组织,可有效改善钢材的切削性及耐磨性,同时又兼具不会產生裂痕、变形量少与操作方便等优点。然而正常化处理是比较难的一种热处理技术,因為它採用空冷的方式冷却,会受到许多因素而影响空冷效果,例如夏天和冬天之冷却效果不同、工件大小对空冷速率有别、甚至风吹也会影响冷却速率。因此正常化处理要使用各种方法来维持均一性,可利用遮阳、围幕、坑洞、风扇等。
完全退火处理主要目的是要软化钢材、改善钢材之切削性,其热处理程序為加热至A3点以上20~30℃(亚共析钢)或A1点以上30~50℃持温一段时间,使形成完全沃斯田体组织后(或沃斯田体加雪明碳体组织),在A1点下方50℃使充分发生波来体变态,获至软化的钢材。另外应力消除退火则是在变态点以下450~650℃加热一段时间后徐徐冷却至室温,可消除钢材内部在切削、冲压、铸造、熔接过程所產生的残留应力。
如何预防加热变形?
预防加热变形的发生,最好是缓慢加热,并实施预热处理。一般钢材在选择预热温度时,可依下列準则来选定预热温度:(1)以变态点以下作為预热温度,例如普通钢约在650~700℃,高速钢则在800~850℃左右。(2)以500℃左右作為预热温度。(3)二段式预热,先在500℃左右作第一段预热,保持一段时间充分预热后,在将预热温度调高至A1变态点以下。(4)三段式预热,针对含有高含量合金之大型钢材,例如高速钢,有时需要在1000~1050℃作第三段预热。
正常化处理与退火处理之差异
正常化处理维加热至A3点或Acm点以上40~60℃保持一段时间,使钢材组织变成均匀的沃斯田体结构后,在静止的空气中冷却至室温的热处理程序。对亚共析钢而言,可获得晶粒细化的目的而拥有好的强度与韧性;对过共析钢而言,则可防止雪明碳铁在沃斯田铁晶粒边界上形成网状析出,以降低材料的韧性。