FMEA讲义-日版
FMEA工程应用培训讲义

FMEA工程应用培训讲义FMEA (Failure Mode and Effects Analysis)是一种常用的风险管理工具,广泛应用于工程设计和制造过程中,旨在提前识别和消除潜在的故障和缺陷。
FMEA可以帮助工程师在设计和制造过程中确定风险,并制定相应的措施来降低潜在故障和缺陷的发生概率。
一、FMEA的基本原理1.1 FMEA的概念FMEA是一种通过系统化的方法,对产品、设计或工作过程中的潜在故障模式进行分析和评估的方法。
通过找出故障模式的潜在原因和效应,可以采取相应的预防措施来减少故障的发生。
1.2 FMEA的目的FMEA的主要目的是通过提前识别和消除潜在的故障和缺陷,提高产品和流程的可靠性和质量。
它能够帮助工程师在设计和制造的过程中识别可能导致产品故障的因素,并制定相应的改进措施。
二、FMEA的应用步骤2.1 选择要分析的过程或产品首先确定要进行FMEA分析的具体产品或过程。
这可以是一个正在开发的新产品,也可以是一个现有产品的改进过程。
2.2 组织FMEA团队确定一个专门的团队来进行FMEA分析。
该团队应由各个领域的专家组成,包括设计工程师、制造工程师和质量控制专家。
2.3 确定潜在故障模式分析可能导致产品故障的各个环节,包括设计、制造、运输、安装和使用过程。
对每个环节,确定可能发生的故障模式。
2.4 评估故障模式的严重性对每个故障模式,评估其可能对产品或过程的影响程度,包括安全性、可靠性和成本等方面。
2.5 确定故障模式的原因对每个故障模式,找出可能导致其发生的潜在原因。
这些原因可以是设计缺陷、制造误差、操作错误等。
2.6 评估故障模式的概率对每个故障模式,评估其发生的概率。
这可以通过历史数据、专家访谈等方式进行评估。
2.7 评估故障模式的可探测性对每个故障模式,评估其是否可以通过检测手段及时发现。
如果不能及时发现,应考虑改进措施。
2.8 制定改进措施根据故障模式的严重性、原因、概率和可探测性,制定相应的改进措施。
FMEA讲义
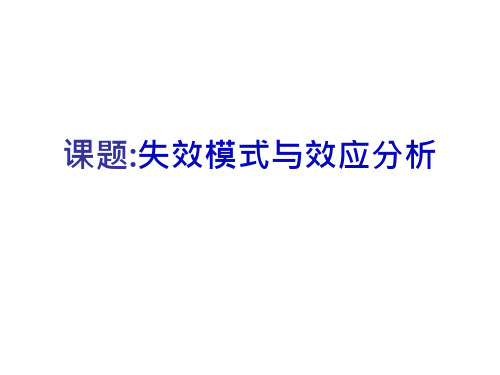
一.FMEA过程顺序
系统有那功能,特征,需要条件? 会有哪些错误?
频次
发生错误会有多惨?
那些错误是什么造成的?
严重度
发生之频率? 有哪些预防和检测? 检测方法能多好程度?
我们能做什么? -设计变更 -过程变更 -特殊控制 -改变标准程序或指南
难检度
一.风险优先数RPN
风险优先数(Risk Priority Number,RPN)
作为建立测试标准,质量管理程序(QCP),制程检验,标准操作 程序(SOP)及标准检验程序(SIP)等检验测试与管制规范的参 考。 7)可作为维护作业规划,维护保养手册编订以及备份料筹备等作 业的输入数据,也可据此制订避免导致失效的操作条件。
一.FMEA的功用
阶段
1.设计时间
2.开发阶段
功用
1.发掘所有可能的失效模式 2.依固有的技术进行设计变更 3.必要之处采用可靠性高的零组件
非常高 车辆/项目无法操作,丧失原来功能
等级 10
一.FMEA的目的
1)辅助设计与制造人员深入探讨产品各层级可能发生的失效模式, 发掘设计或制程上的弱点并改进或防范。
2)发掘可靠度关键件,列入作为设计验证及可靠度管制的重点。 3)研订失效准则,协助失效分析及改正作业,并可作为可靠度分
析的参考数据。 4)提供安全设计及可靠度评估的数据。 5)作为各研发阶段设计审查的输入数据。 6)设计初期即考虑制造组装的需求,并提供健全的失效信息基础,
一. 示例(4/5)
因素 温度太高 热电控制不当 应收帐款编号错误 打字错误 表面污染 高吊车使用时造成的 扔下电话 客户服务人数不足 釉层太薄 溶剂含量太高
一. 示例(5/5)
因素 脱胶 上胶不均匀且份量不足 鞋面破损 材质质量不良 鞋底断裂 鞋底材料配方不当 鞋面污点 模子与手套不洁所造成的 容易滑倒 鞋底材质不良,且设计不当
FMEA培训课件
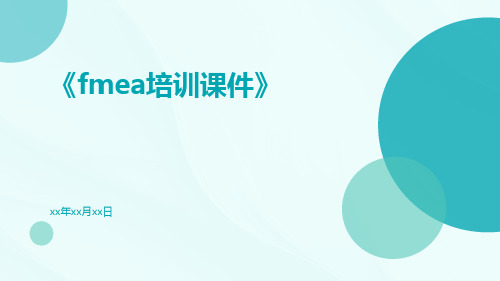
xx年xx月xx日
目录
• FMEA基础 • FMEA实施步骤 • FMEA关键工具和概念 • FMEA应用案例分析 • FMEA实践建议
01
FMEA基础
FMEA定义与目的
故障模式与影响分析(FMEA)是一种预防性的质量工具,用 于在产品设计阶段识别并优先处理潜在的故障模式。
分析故障原因
针对潜在故障,分析其可能的 原因,以便确定改进方向。
确定优先级
根据故障的严重程度、发生频率 和可检测性,确定改进优先级。
制定改进措施
根据确定的优先级,制定相应的改 进措施,并进行实施。
03
FMEA关键工具和概念
FMEA关键工具
FMEA图表
包括故障模式与影响分析( FMEA)表和故障模式、影响与 严重度分析(FMECA)表,用
故障原因
指导致故障模式出现的原因,可以 是设计、材料、工艺等方面的因素 。
风险优先级
指故障模式的优先级,根据故障影 响的大小和故障模式的概率来计算 。
04
FMEA应用案例分析
汽车制造领域FMEA应用案例
汽车制造领域FMEA应用范围
01
主要应用于汽车及其零部件制造过程中,识别、评估和消除潜
在的质量风险,提高产品质量和可靠性。
收集故障数据、分析故障模式、评估故障影响、确定故障优先级、制
定控制措施、实施控制措施并验证效果。
05
FMEA实践建议
如何提高FMEA实施效果Βιβλιοθήκη 明确FMEA的目的和范 围
明确FMEA的目的、分析范围和预期结果, 确保团队成员充分理解。
完善数据收集和分析
收集足够的数据,包括历史故障信息、潜在 的故障模式、影响等,并运用FMEA工具进 行深入分析。
FMEA培训教材(共30张)

7、确定當前的工序控制方法并評估其檢測失效的可能性,附表1、4。
8、确定 RPN 值并根据 RPN 值采取相應的改善措施,附表1。
第16页,共30页。
附表1:在附表 1 中包含以下 6 個方面的內容,因附表 1 容量
太大,另存在 Excel 中
第9页,共30页。
5、FMEA 的應用范圍(2)-品質改善程序
DFMEA
改善行動
消除變异
合并
惡性
良性
研究變异 的性質
PFMEA
控制(kòngzhì)方案
投入
工序
出貨
產品
改善系統
尋找預期 的變异
研究變异 的原因
第10页,共30页。
否
是否變 异?
是
研究 / 測量
与控制界限
進行比較
6、PFMEA 的程序步驟(2)
2、确定所要分析的失效模式 (potential failure mode), 附表1。
3、分析失效模式對客戶的所造成的影響 (potential failure effect), 附表1。
4、評估影響的嚴重程度 (severity), 附表1、2。 5、分析失效的可能原因 (failure cause),人、机、料、法、環等原
繪出流程(liúchéng)圖
确定各個工序的功能
确定失效模式
標識其效應
標識其原因
標識當前控制
方法
估計嚴重性 估計發生概率
估計測試性
RPN =O x S x D
是
RPN= 風險指數
制作 Pareto
圖
選擇失效模式
FMEA讲义
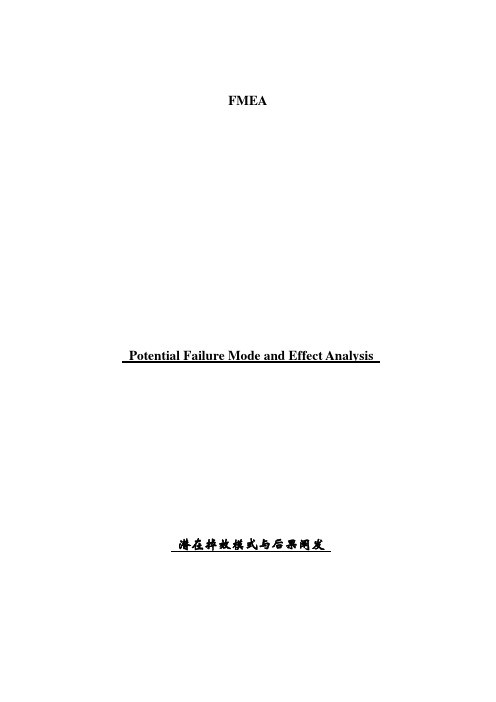
·有助于对设计要求和设计方案进行客不雅评价;
·有助于对制造和装配要求的最初设计;
·提高在设计/开发过程中考虑潜在掉效模式及其对系统和车辆运行影响的可能性;
·为全面、有效的设计试验和开发工程的筹划提供更多的信息;
·按照潜在掉效模式对“顾客〞的影响,对其进行排序列表,进而成立一套改良设计和开发试验的优先控制系统;
典型的掉效后果可能是但不限于:噪声、工作不正常、不良外不雅、不不变、
运行中断、粗拙、不起作用、异味、工作减弱等。
12)严重度(S)
严重度是潜在掉效模式发生时对下序零件、子系统、系统或顾客影响后果
严重程度(列于前一栏中)的评价指标。严重度仅适用于后果。要减少掉效的严重
度级别数值,只能通过点窜设计来实现,严重度的评估分为1到10级。
每一个在设计FMEA中有如上标识的工程应在过程FMEA中有特殊的过程控制。
14)潜在掉效的起因/机理
所谓潜在掉效起因是指一个设计薄弱局部的迹象,其作用成果就是掉效模式。在尽可能广的范围内,列出每个掉效模式的所有可以想到的掉效起因和/或机理。应尽可能简明扼要、完整地将起因/机理列出来,使得对相应的起因能采纳适当的纠正办法。
·为保举和跟踪降低风险的办法提供一个公开的讨论形式;
·为将来阐发研究现场情况、评价设计的更改及开发更先进的设计提供参考。
顾客的定义
设计FMEA中“顾客〞的定义,不仅仅是指“最终使用者〞,还包罗负责车型更高一级装配过程设计的工程师/小组,以及在出产过程中负责制造和售后效劳的工程师。
FMEA的全面实施要求对所有新的部件、更改的部件以及应用或环境有变化的沿用零件进行设计FMEA。FMEA始于负责设计工作的工程师,但对有专有权的设计来说,可能始于其供方。
FMEA讲义运用
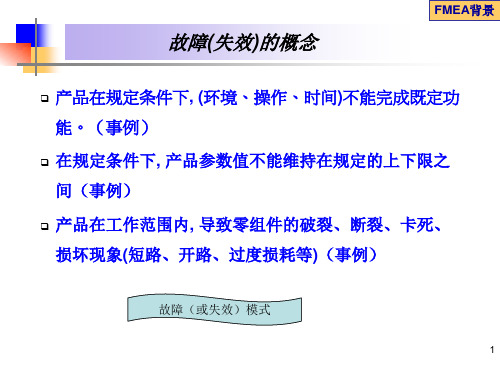
故障模式分析
3
FMEA背景
何谓 FMEA (Failure Mode & Effects Analysis)
以系统(产品)以及工序、设备等的构成要素为对象. 利用所谓的“故障模式(Failure Mode)”思考方式. 事先排除可能出现的问题. 通过故障的原因和影响说明问题的重要性. 连接设计(工艺)的手法.
•对现有设计或过程的修改;修改可能产生的相互影响
•将现有设计或过程用于新的环境、场所或应 用;新环境或场所对现有设计或过程的影响
18
FMEA的种类
基本知识
系统FMEA
设计FMEA
过程FMEA
对象 目的
实施阶段
产品(系统)
产品(零配件等)
确保系统设计的完整性 确保设计的完整性.
评估
找出产品的故障形态及其对
功能丧失,整机故障现 象
产品性能
停止;异常输出;无动作 变形;龟列;磨损;短路等
产品不良;后期工程 尺寸不良;破损等
共同点
•用表格整理 •相对评价发生频度,影响度,检知度等并找出主要故障(不良)模式 •筹划各种故障(不良)模式的对策.
19
系统、设计、过程FMEA之间的关系
系统FMEA
故障模式 问题
50年代:格鲁曼公司开发了FMEA,用于飞机发动机故障防范; 70年代:海军制定了FMEA标准, 1976年,美国国防部采纳了FMEA标准; 80年代:汽车工业和微电子工业应用FMEA 90年代:ISO9000推荐采用FMEA; 1994,FMEA成为QS-9000认证要求。21世纪:??????????? 军工产业,宇宙开发领域 可靠性、安全性评价工具
FMEA授课讲义(ppt 74页)

控制计划/过程流程结合图例
建议的产品质量计划顺序
过程流程清单 (包括所有的过程)
APQP程序 将启动这个过程
DFMEA
过程流程/ 控制计划 (所有的“”主要“过程)
过程流程清单 转化为
过程控制计划
PFMEA (所有的“”主要“过程) 利用RPN值来评定特性
prepared by kingie, Not copy without permission.
过程 FMEA在过程开发中运用太迟或没有改进产品/
过程循环发展 在产品寿命期内FMEA没有被重新评定和更新,
没有像动态工具一样被加工 FMEA被认为太复杂或花费太多的时间
prepared by kingie, Not copy without permission.
统或系统时,工程师/小组的设计思想 在最大范围內保证已充份的考虑到并指明潜在失
效模式及与其相关的后果起因/机理 在任何设计过程中正常经历的思维过程是一致的
,并使之规范化
prepared by kingie, Not copy without permission.
工具
目标:最大化的
工作站
全过程质量、
生产线 操作者培训
过程
可靠性、成本 和可维护性
测量 prepared by kingie, Not copy without
permission.
FMEAs的关联
失效模式
后果
原因
SFMEA
问题的分支
问题
问题产生的原因
DFMEA 问题产生的原因来自 准确的后果定义 设计失效模式产
期加工过程的描述 过程流程图
描述材料的整个加工流程,包括任何的返 工和修理操作
FMEA培训讲义1课件

FMEA培训讲义1
4
分类
• 由于产品故障可能与设计、制造过程、使用、承包商/ 供应商以及服务有关,因此FMEA又细分为:
• DFMEA:设计(Design)FMEA • PFMEA:过程(Process)FMEA • EFMEA:设备(Equipment)FMEA • SFMEA:体系(System)FMEA
糟糕
?
会是什么问题? -无功能 -部分功能/功能 过强/功能降级 -功能间歇 -非预期功能
起因是 什么?
发生的频 率如何?
能做些什么? -设计更改 -过程更改 -特殊控制 -标准、程序或 指南的更改
怎样能得到 预防和探测? 该方法在
探测时 有多好?
FMEA培训讲义1
12
失效模式分析—排列图
• 排列图 用從高到低的順序排列成矩形,表示各原因出現頻率高
FMEA培训讲义1
11
图1. FMEA过程顺序
系统
潜在
项目
失效
过程
模式
功能 要求
潜在 失效 后果
严 级 潜在 频 现行控制 探
重 别 失效 度
测
度
起因/ O 预 探 度
S
机理
防测D
R 建议 责任及
P 措施 目标完
N
成日期
措施结果
采取 的措 施
S O D RP N
功能、特 性或要求 是什么?
有多
后果是 什么?
低的一种图表。其原理是80%的問題仅來源於20%的主 要原因。 注意要点 • §明确問題和現象; • §寻找不良的情況統計資料; • §頻率計算和累計; • §对頻率从高到低的順序排列;
潜在失效模式及后果分析