工业类汉译英论文翻译和过滤产品研究中英对照样稿
工业产品设计外文翻译参考文献

工业产品设计外文翻译参考文献工业产品设计外文翻译参考文献(文档含中英文对照即英文原文和中文翻译)Design Without DesignersI will always remember my first introduction to the power of good product design.I was newly arrived at Apple, still learning the ways of business, when I was visited by a member of Apple's Industrial Design team. He showed me a foam mockup of a proposed product. "Wow," I said, "I want one! What is it?"That experience brought home the power of design: I was excited and enthusiastic even before I knew what it was. This type of visceral "wow" response requires creative designers. It is subjective, personal. Uh oh, this is not what engineers like to hear. If you can't put a number to it, it's not important. As a result, there is a trend to eliminate designers. Who needs them when we can simply test our way to success? The excitement of powerful, captivating design is defined as irrelevant. Worse, the nature of design is in danger.Don't believe me? Consider Google. In a well-publicized move, a senior designer at Google recently quit, stating that Google had no interest in or understanding of design. Google, it seems, relies primarily upon test results, not human skill or judgment. Want to know whether a design is effective? Try it out. Google can quickly submit samples to millions of people in well-controlled trials, pitting one design against another, selecting the winner based upon number of clicks, or sales, or whatever objective measure they wish. Which color of blue is best? Test. Item placement? T est. Web page layout? Test.This procedure is hardly unique to Google. /doc/f51636438.html, has long followed this practice. Years ago I was proudly informed that they no longer have debates about which design is best: they simply test them and use the data to decide. And this, of course, is the approach used by the human-centered iterative design approach: prototype, test, revise.Is this the future of design? Certainly there are many who believe so. This is a hot topic on the talk and seminar circuit. After all, the proponents ask reasonably, who could object to making decisions based upon data?Two Types of Innovation: Incremental Improvements and New ConceptsIn design—and almost all innovation, for that matter—there are at least two distinct forms. One is incremental improvement. In the manufacturing of products, companies assume that unit costs will continually decrease through continual, incremental improvements. A steady chain of incremental innovation enhances operations, the sourcing of parts and supply-chain management. The product design is continually tinkered with, adjusting the interface, adding new features, changing small things here and there. New products are announced yearly that are simply small modifications to the existing platform by a different constellation of features. Sometimes features are removed to enable a new, low-cost line. Sometimes features are enhanced or added. In incremental improvement, the basic platform is unchanged. Incremental design and innovation is less glamorous than the development of new concepts and ideas, but it is both far more frequent and far more important. Most of these innovations are small, but most are quite successful. This iswhat companies call "their cash cow": a product line that requires very little new development cost while being profitable year after year.The second form of design is what is generally taught in design, engineering and MBA courses on "breakthrough product innovation." Here is where new concepts get invented, new products defined, and new businesses formed. This is the fun part of innovation. As a result, it is the arena that most designers and inventors wish to inhabit. But the risks are great: most new innovations fail. Successful innovations can take decades to become accepted. As a result, the people who create the innovation are not necessarily the people who profit from it.In my Apple example, the designers were devising a new conception. In the case of Google and Amazon, the companies are practicing incremental enhancement. They are two different activities. Note that the Apple product, like most new innovations, failed. Why? I return to this example later.Both forms of innovation are necessary. The fight over data-driven design is misleading in that it uses the power of one method to deny the importance of the second. Data-driven design through testing is indeed effective at improving existing products. But where did the idea for the product come from in the first place? From someone's creative mind. Testing is effective at enhancing an idea, but creative designers and inventors are required to come up with the idea.Why Testing Is Both Essential and IncompleteData-driven design is "hill-climbing," a well-known algorithm for optimization. Imagine standing in the dark in an unknown, hilly terrain. How do you get to the top of the hill when you can't see? Test the immediate surroundings to determine whichdirection goes up the most steeply and take a step that way. Repeat until every direction leads to a lower level.But what if the terrain has many hills? How would you know whether you are on the highest? Answer: you can't know. This is called the "local maximum" problem: you can't tell if you are on highest hill (a global maximum) or just at the top of a small one.When a computer does hill climbing on a mathematical space, it tries to avoid the problem of local maxima by initiating climbs from numerous, different parts of the space being explored, selecting the highest of the separate attempts. This doesn't guarantee the very highest peak, but it can avoid being stuck on a low-ranking one. This strategy is seldom available to a designer: it is difficult enough to come up with a single starting point, let alone multiple, different ones. So, refinement through testing in the world of design is usually only capable of reaching the local maximum. Is there a far better solution (that is, is there a different hill which yields far superior results)? Testing will never tell us.Here is where creative people come in. Breakthroughs occur when a person restructures the problem, thereby recognizing that one is exploring the wrong space. This is the creative side of design and invention. Incremental enhancements will not get us there.Barriers to Great InnovationDramatic new innovation has some fundamental characteristics that make it inappropriate for judgment through testing. People resist novelty. Behavior tends to be conservative. New technologies and new methods of doing things usually take decades to be accepted - sometimes multiple decades. But the testing methods allassume that one can make a change, try it out, and immediately determine if it is better than what is currently available.There is no known way to tell if a radical new idea will eventually be successful. Here is where great leadership and courage is required. History tells us of many people who persevered for long periods in the face of repeated rejection before their idea was accepted, often to the point that after success, people could not imagine how they got along without it before. History also tells us of many people who persevered yet never were able to succeed. It is proper to be skeptical of radical new ideas.In the early years of an idea, it might not be accepted because the technology isn't ready, or because there is a lot more optimization still to be done, or because the audience isn't ready. Or because it is a bad idea. It is difficult to determine which of those reasons dominates. The task only becomes easy in hindsight, long after it becomes established.These long periods between formation and initial implementation of a novel idea and its eventual determination of success or failure in the marketplace is what defeats those who wish to use evidence as a decision criterion for following a new direction. Even if a superior way of doing something has been found, the automated test process will probably reject it, not because the idea is inferior, but because it cannot wait decades for the answer. Those who look only at test results will miss the large payoff.Of course there are sound business reasons why ignoring potentially superior approaches might be a wise decision. After all, if the audience is not ready for the new approach, it wouldinitially fail in the marketplace. That is true, in the short run. But to prosper in the future, the best approach would be to develop and commercialize the new idea to get marketplace experience, to begin the optimization process, and to develop the customer base. At the same time one is preparing the company for the day when the method takes off. Sure, keep doing the old, but get ready for the new. If the company fails to recognize the newly emerging method, its competitors will take over. Quite often these competitors will be a startup that existing companies ignored because what they were doing was not well accepted, and in any event did not appear to challenge the existing business: see "The innovator's dilemma."Gestural, multi-touch interfaces for screen-driven devices and computer games are good examples. Are these a brilliant new innovation? Brilliant? Yes. New? Absolutely not. Multi-touch devices were in research labs for almost three decades before the first successful mass-produced products. I saw gestures demonstrated over two decades ago. New ideas take considerable time to reach success in the marketplace. If an idea is commercialized too soon, the result is usually failure (and a large loss of money).This is precisely what the Apple designer of my opening paragraph had done. What I was shown was a portable computer designed for schoolchildren with a form factor unlike anything I had ever seen before. It was wonderful, and even to my normally critical eye, it looked like a perfect fit for the purpose and audience. Alas, the product got caught in a political fight between warring Apple divisions. Although it was eventually released into the marketplace, the fight crippled its integrity and it was badly executed, badly supported, and badly marketed.The resistance of a company to new innovations is well founded. It is expensive to develop a new product line with unknown profitability. Moreover, existing product divisions will be concerned that the new product will disrupt existing sales (this is called "cannibalization"). These fears are often correct. This is a classic case of what is good for the company being bad for an existing division, which means bad for the promotion and reward opportunities for the existing division. Is it a wonder companies resist? The data clearly show that although a few new innovations are dramatically successful, most fail, often at great expense. It is no wonder that companies are hesitant - resistant - to innovation no matter what their press releases and annual reports claim. To be conservative is to be sensible.The FutureAutomated data-driven processes will slowly make more and more inroads into the space now occupied by human designers. New approaches to computer-generated creativity such as genetic algorithms, knowledge-intensive systems, and others will start taking over the creative aspect of design. This is happening in many other fields, whether it be medical diagnosis or engineering design.We will get more design without designers, but primarily of the enhancement, refinement, and optimization of existing concepts. Even where new creative artificial systems are developed, whether by neural networks, genetic algorithms, or some yet undiscovered method, any new concept will still face the hurdle of overcoming the slow adoption rate of people and of overcoming the complex psychological, social, and political needs of people. T o do this, we need creative designers, creative business people, and risk takers willing to push the boundaries.New ideas will be resisted. Great innovations will come at the cost of multiple great failures.Design without designers? Those who dislike the ambiguity and uncertainty of human judgments, with its uncertain track record and contradictory statements will try to abolish the human element in favor of the certainty that numbers and data appear to offer. But those who want the big gains that creative judgment can produce will follow their own judgment. The first case will bring about the small, continual improvements that have contributed greatly to the increased productivity and lowering of costs of our technologies. The second case will be rewarded with greatfailures and occasional great success. But those great successes will transform the world.不需要设计师的设计唐·诺曼我永远也不会忘记我第一次向人们介绍优秀产品设计的魅力的经历,那时候我刚刚到苹果公司,还在逐渐的学习工作上的事务。
污水处理工业废水回用中英文对照外文翻译文献

污水处理工业废水回用中英文对照外文翻译文献XXX and resource recovery in us industries。
and they are of significant XXX-catalysis has been well established for water recovery and reuse。
chemo-catalysis is only starting to make an XXX-catalytic processes for water reuse。
XXX。
XXX.2.Chemo-XXX reuseChemo-XXX。
including XXX。
One of the most promising ns of chemo-XXX。
XXX。
This process has been shown to be effective in removing COD (chemical oxygen demand) XXX.3.XXX COD removalXXX treatment。
The process involves the use of a XXX can be a metal oxide or a metal complex。
and the oxidizing agent can be hydrogen peroxide。
ozone。
or XXX mild ns。
and the process is XXX.4.XXXXXX (AOPs) such as XXX。
photo-Fenton n。
and electro-XXX include the use of anic frameworks (MOFs) XXX.5.nIn n。
chemo-catalytic processes。
XXX。
XXX。
such as AOPs。
MOFs。
and nanomaterials。
机械类文章翻译案例 中英对照

妙文翻译公司翻译样稿One concept – the whole system for all functions一个概念–具有所有功能的整体系统Power units动力单元The power unit is the heart of the turbine, supplying the power necessary to operate pitch, yaw and braking systems and providing backup in case of power failure, ensuring a safe stop with no risk of damage.Our hydraulic power units are designed with reliabilty, ease of maintenance and a wide operating temperature range in mind.动力单元是风轮机的心脏,为浆距、偏航和制动系统的运行提供必要的电力,并在断电时提供备用措施,保证安全停止,无损坏危险。
我们的液压动力单元在设计时充分考虑了可靠性、维护方便性及宽温度范围。
Added life寿命增加Parker filtration technology extends the life and increases the reliability of wind turbines by using environmental solutions.In addition to a wide range of hydraulic filters, lube filters and reservoir accessories, Parker offers you the global leader in fluid condition monitoring with the Laser CM portable particle counter.A comprehensive range of quality products to cover all your needs!通过应用环境条件解决方案,Parker过滤技术延长了风轮机的寿命并提高了可靠性。
中英文文献以及翻译(化工类)

Foreign material:Chemical Industry1.Origins of the Chemical IndustryAlthough the use of chemicals dates back to the ancient civilizations, the evolution of what we know as the modern chemical industry started much more recently. It may be considered to have begun during the Industrial Revolution, about 1800, and developed to provide chemicals roe use by other industries. Examples are alkali for soapmaking, bleaching powder for cotton, and silica and sodium carbonate for glassmaking. It will be noted that these are all inorganic chemicals. The organic chemicals industry started in the 1860s with the exploitation of William Henry Perkin’s discovery if the first synthetic dyestuff—mauve. At the start of the twentieth century the emphasis on research on the applied aspects of chemistry in Germany had paid off handsomely, and by 1914 had resulted in the German chemical industry having 75% of the world market in chemicals. This was based on the discovery of new dyestuffs plus the development of both the contact process for sulphuric acid and the Haber process for ammonia. The later required a major technological breakthrough that of being able to carry out chemical reactions under conditions of very high pressure for the first time. The experience gained with this was to stand Germany in good stead, particularly with the rapidly increased demand for nitrogen-based compounds (ammonium salts for fertilizers and nitric acid for explosives manufacture) with the outbreak of world warⅠin 1914. This initiated profound changes which continued during the inter-war years (1918-1939).Since 1940 the chemical industry has grown at a remarkable rate, although this has slowed significantly in recent years. The lion’s share of this growth has been in the organic chemicals sector due to the development and growth of the petrochemicals area since 1950s. The explosives growth in petrochemicals in the 1960s and 1970s was largely due to the enormous increase in demand for synthetic polymers such as polyethylene, polypropylene, nylon, polyesters and epoxy resins.The chemical industry today is a very diverse sector of manufacturing industry, within which it plays a central role. It makes thousands of different chemicals whichthe general public only usually encounter as end or consumer products. These products are purchased because they have the required properties which make them suitable for some particular application, e.g. a non-stick coating for pans or a weedkiller. Thus chemicals are ultimately sold for the effects that they produce.2. Definition of the Chemical IndustryAt the turn of the century there would have been little difficulty in defining what constituted the chemical industry since only a very limited range of products was manufactured and these were clearly chemicals, e.g., alkali, sulphuric acid. At present, however, many intermediates to products produced, from raw materials like crude oil through (in some cases) many intermediates to products which may be used directly as consumer goods, or readily converted into them. The difficulty cones in deciding at which point in this sequence the particular operation ceases to be part of the chemical industry’s sphere of activities. To consider a specific example to illustrate this dilemma, emulsion paints may contain poly (vinyl chloride) / poly (vinyl acetate). Clearly, synthesis of vinyl chloride (or acetate) and its polymerization are chemical activities. However, if formulation and mixing of the paint, including the polymer, is carried out by a branch of the multinational chemical company which manufactured the ingredients, is this still part of the chemical industry of does it mow belong in the decorating industry?It is therefore apparent that, because of its diversity of operations and close links in many areas with other industries, there is no simple definition of the chemical industry. Instead each official body which collects and publishes statistics on manufacturing industry will have its definition as to which operations are classified as the chemical industry. It is important to bear this in mind when comparing statistical information which is derived from several sources.3. The Need for Chemical IndustryThe chemical industry is concerned with converting raw materials, such as crude oil, firstly into chemical intermediates and then into a tremendous variety of other chemicals. These are then used to produce consumer products, which make our livesmore comfortable or, in some cases such as pharmaceutical produces, help to maintain our well-being or even life itself. At each stage of these operations value is added to the produce and provided this added exceeds the raw material plus processing costs then a profit will be made on the operation. It is the aim of chemical industry to achieve this.It may seem strange in textbook this one to pose the question “do we need a chemical industry?” However trying to answer this question will provide(ⅰ) an indication of the range of the chemical industry’s activities, (ⅱ) its influence on our lives in everyday terms, and (ⅲ) how great is society’s need for a chemical industry. Our approach in answering the question will be to consider the industry’s co ntribution to meeting and satisfying our major needs. What are these? Clearly food (and drink) and health are paramount. Other which we shall consider in their turn are clothing and (briefly) shelter, leisure and transport.(1)Food. The chemical industry makes a major contribution to food production in at least three ways. Firstly, by making available large quantities of artificial fertilizers which are used to replace the elements (mainly nitrogen, phosphorus and potassium) which are removed as nutrients by the growing crops during modern intensive farming. Secondly, by manufacturing crop protection chemicals, i.e., pesticides, which markedly reduce the proportion of the crops consumed by pests. Thirdly, by producing veterinary products which protect livestock from disease or cure their infections.(2)Health. We are all aware of the major contribution which the pharmaceutical sector of the industry has made to help keep us all healthy, e.g. by curing bacterial infections with antibiotics, and even extending life itself, e.g. ß–blockers to lower blood pressure.(3)Clothing. The improvement in properties of modern synthetic fibers over the traditional clothing materials (e.g. cotton and wool) has been quite remarkable. Thus shirts, dresses and suits made from polyesters like Terylene and polyamides like Nylon are crease-resistant, machine-washable, and drip-dry or non-iron. They are also cheaper than natural materials.Parallel developments in the discovery of modern synthetic dyes and the technology to “bond” th em to the fiber has resulted in a tremendous increase in the variety of colors available to the fashion designer. Indeed they now span almost every color and hue of the visible spectrum. Indeed if a suitable shade is not available, structural modification of an existing dye to achieve this canreadily be carried out, provided there is a satisfactory market for the product.Other major advances in this sphere have been in color-fastness, i.e., resistance to the dye being washed out when the garment is cleaned.(4)Shelter, leisure and transport. In terms of shelter the contribution of modern synthetic polymers has been substantial. Plastics are tending to replace traditional building materials like wood because they are lighter, maintenance-free (i.e. they are resistant to weathering and do not need painting). Other polymers, e.g. urea-formaldehyde and polyurethanes, are important insulating materials f or reducing heat losses and hence reducing energy usage.Plastics and polymers have made a considerable impact on leisure activities with applications ranging from all-weather artificial surfaces for athletic tracks, football pitches and tennis courts to nylon strings for racquets and items like golf balls and footballs made entirely from synthetic materials.Like wise the chemical industry’s contribution to transport over the years has led to major improvements. Thus development of improved additives like anti-oxidants and viscosity index improves for engine oil has enabled routine servicing intervals to increase from 3000 to 6000 to 12000 miles. Research and development work has also resulted in improved lubricating oils and greases, and better brake fluids. Yet again the contribution of polymers and plastics has been very striking with the proportion of the total automobile derived from these materials—dashboard, steering wheel, seat padding and covering etc.—now exceeding 40%.So it is quite apparent even from a brief look at the chemical industry’s contribution to meeting our major needs that life in the world would be very different without the products of the industry. Indeed the level of a country’s development may be judged by the production level and sophistication of its chemical industry4. Research and Development (R&D) in Chemical IndustriesOne of the main reasons for the rapid growth of the chemical industry in the developed world has been its great commitment to, and investment in research and development (R&D). A typical figure is 5% of sales income, with this figure being almost doubled for the most research intensive sector, pharmaceuticals. It is important to emphasize that we are quoting percentages here not of profits but of sales income, i.e. the total money received, which has to pay for raw materials, overheads, staff salaries, etc. as well. In the past this tremendous investment has paid off well, leading to many useful and valuable products being introduced to the market. Examplesinclude synthetic polymers like nylons and polyesters, and drugs and pesticides. Although the number of new products introduced to the market has declined significantly in recent years, and in times of recession the research department is usually one of the first to suffer cutbacks, the commitment to R&D remains at a very high level.The chemical industry is a very high technology industry which takes full advantage of the latest advances in electronics and engineering. Computers are very widely used for all sorts of applications, from automatic control of chemical plants, to molecular modeling of structures of new compounds, to the control of analytical instruments in the laboratory.Individual manufacturing plants have capacities ranging from just a few tones per year in the fine chemicals area to the real giants in the fertilizer and petrochemical sectors which range up to 500,000 tonnes. The latter requires enormous capital investment, since a single plant of this size can now cost $520 million! This, coupled with the widespread use of automatic control equipment, helps to explain why the chemical industry is capital-rather than labor-intensive.The major chemical companies are truly multinational and operate their sales and marketing activities in most of the countries of the world, and they also have manufacturing units in a number of countries. This international outlook for operations, or globalization, is a growing trend within the chemical industry, with companies expanding their activities either by erecting manufacturing units in other countries or by taking over companies which are already operating there.化学工业1.化学工业的起源尽管化学品的使用可以追溯到古代文明时代,我们所谓的现代化学工业的发展却是非常近代(才开始的)。
机械加工毕业论文中英文资料外文翻译文献
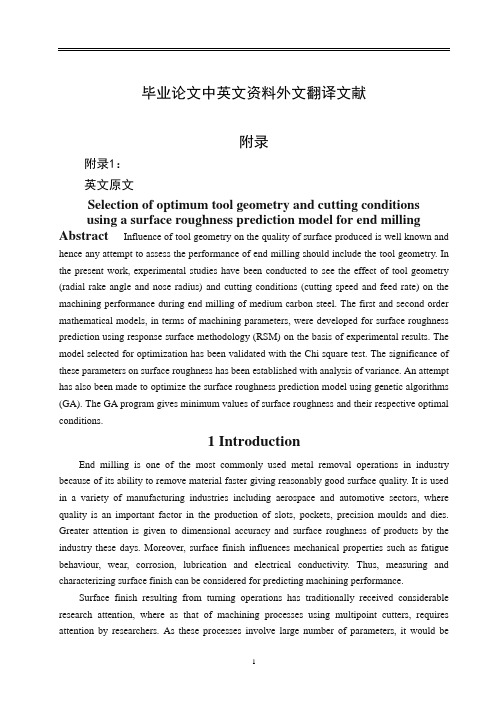
毕业论文中英文资料外文翻译文献附录附录1:英文原文Selection of optimum tool geometry and cutting conditionsusing a surface roughness prediction model for end milling Abstract Influence of tool geometry on the quality of surface produced is well known and hence any attempt to assess the performance of end milling should include the tool geometry. In the present work, experimental studies have been conducted to see the effect of tool geometry (radial rake angle and nose radius) and cutting conditions (cutting speed and feed rate) on the machining performance during end milling of medium carbon steel. The first and second order mathematical models, in terms of machining parameters, were developed for surface roughness prediction using response surface methodology (RSM) on the basis of experimental results. The model selected for optimization has been validated with the Chi square test. The significance of these parameters on surface roughness has been established with analysis of variance. An attempt has also been made to optimize the surface roughness prediction model using genetic algorithms (GA). The GA program gives minimum values of surface roughness and their respective optimal conditions.1 IntroductionEnd milling is one of the most commonly used metal removal operations in industry because of its ability to remove material faster giving reasonably good surface quality. It is used in a variety of manufacturing industries including aerospace and automotive sectors, where quality is an important factor in the production of slots, pockets, precision moulds and dies. Greater attention is given to dimensional accuracy and surface roughness of products by the industry these days. Moreover, surface finish influences mechanical properties such as fatigue behaviour, wear, corrosion, lubrication and electrical conductivity. Thus, measuring and characterizing surface finish can be considered for predicting machining performance.Surface finish resulting from turning operations has traditionally received considerable research attention, where as that of machining processes using multipoint cutters, requires attention by researchers. As these processes involve large number of parameters, it would bedifficult to correlate surface finish with other parameters just by conducting experiments. Modelling helps to understand this kind of process better. Though some amount of work has been carried out to develop surface finish prediction models in the past, the effect of tool geometry has received little attention. However, the radial rake angle has a major affect on the power consumption apart from tangential and radial forces. It also influences chip curling and modifies chip flow direction. In addition to this, researchers [1] have also observed that the nose radius plays a significant role in affecting the surface finish. Therefore the development of a good model should involve the radial rake angle and nose radius along with other relevant factors.Establishment of efficient machining parameters has been a problem that has confronted manufacturing industries for nearly a century, and is still the subject of many studies. Obtaining optimum machining parameters is of great concern in manufacturing industries, where the economy of machining operation plays a key role in the competitive market. In material removal processes, an improper selection of cutting conditions cause surfaces with high roughness and dimensional errors, and it is even possible that dynamic phenomena due to auto excited vibrations may set in [2]. In view of the significant role that the milling operation plays in today’s manufacturing world, there is a need to optimize the machining parameters for this operation. So, an effort has been made in this paper to see the influence of tool geometry(radial rake angle and nose radius) and cutting conditions(cutting speed and feed rate) on the surface finish produced during end milling of medium carbon steel. The experimental results of this work will be used to relate cutting speed, feed rate, radial rake angle and nose radius with the machining response i.e. surface roughness by modelling. The mathematical models thus developed are further utilized to find the optimum process parameters using genetic algorithms.2 ReviewProcess modelling and optimization are two important issues in manufacturing. The manufacturing processes are characterized by a multiplicity of dynamically interacting process variables. Surface finish has been an important factor of machining in predicting performance of any machining operation. In order to develop and optimize a surface roughness model, it is essential to understand the current status of work in this area.Davis et al. [3] have investigated the cutting performance of five end mills having various helix angles. Cutting tests were performed on aluminium alloy L 65 for three milling processes (face, slot and side), in which cutting force, surface roughness and concavity of a machined plane surface were measured. The central composite design was used to decide on the number of experiments to be conducted. The cutting performance of the end mills was assessed usingvariance analysis. The affects of spindle speed, depth of cut and feed rate on the cutting force and surface roughness were studied. The investigation showed that end mills with left hand helix angles are generally less cost effective than those with right hand helix angles. There is no significant difference between up milling and down milling with regard tothe cutting force, although the difference between them regarding the surface roughness was large. Bayoumi et al.[4] have studied the affect of the tool rotation angle, feed rate and cutting speed on the mechanistic process parameters (pressure, friction parameter) for end milling operation with three commercially available workpiece materials, 11 L 17 free machining steel, 62- 35-3 free machining brass and 2024 aluminium using a single fluted HSS milling cutter. It has been found that pressure and friction act on the chip – tool interface decrease with the increase of feed rate and with the decrease of the flow angle, while the cutting speed has a negligible effect on some of the material dependent parameters. Process parameters are summarized into empirical equations as functions of feed rate and tool rotation angle for each work material. However, researchers have not taken into account the effects of cutting conditions and tool geometry simultaneously; besides these studies have not considered the optimization of the cutting process.As end milling is a process which involves a large number f parameters, combined influence of the significant parameters an only be obtained by modelling. Mansour and Abdallaet al. [5] have developed a surface roughness model for the end milling of EN32M (a semi-free cutting carbon case hardening steel with improved merchantability). The mathematical model has been developed in terms of cutting speed, feed rate and axial depth of cut. The affect of these parameters on the surface roughness has been carried out using response surface methodology (RSM). A first order equation covering the speed range of 30–35 m/min and a second order equation covering the speed range of 24–38 m/min were developed under dry machining conditions. Alauddin et al. [6] developed a surface roughness model using RSM for the end milling of 190 BHN steel. First and second order models were constructed along with contour graphs for the selection of the proper combination of cutting speed and feed to increase the metal removal rate without sacrificing surface quality. Hasmi et al. [7] also used the RSM model for assessing the influence of the workpiece material on the surface roughness of the machined surfaces. The model was developed for milling operation by conducting experiments on steel specimens. The expression shows, the relationship between the surface roughness and the various parameters; namely, the cutting speed, feed and depth of cut. The above models have not considered the affect of tool geometry on surface roughness.Since the turn of the century quite a large number of attempts have been made to find optimum values of machining parameters. Uses of many methods have been reported in the literature to solve optimization problems for machining parameters. Jain and Jain [8] have usedneural networks for modeling and optimizing the machining conditions. The results have been validated by comparing the optimized machining conditions obtained using genetic algorithms. Suresh et al. [9] have developed a surface roughness prediction model for turning mild steel using a response surface methodology to produce the factor affects of the individual process parameters. They have also optimized the turning process using the surface roughness prediction model as the objective function. Considering the above, an attempt has been made in this work to develop a surface roughness model with tool geometry and cutting conditions on the basis of experimental results and then optimize it for the selection of these parameters within the given constraints in the end milling operation.3 MethodologyIn this work, mathematical models have been developed using experimental results with the help of response surface methodolog y. The purpose of developing mathematical models relating the machining responses and their factors is to facilitate the optimization of the machining process. This mathematical model has been used as an objective function and the optimization was carried out with the help of genetic algorithms.3.1 Mathematical formulationResponse surface methodology(RSM) is a combination of mathematical and statistical techniques useful for modelling and analyzing the problems in which several independent variables influence a dependent variable or response. The mathematical models commonly used are represented by:where Y is the machining response, ϕ is the response function and S, f , α, r are milling variables and ∈is the error which is normally distributed about the observed response Y with zero mean.The relationship between surface roughness and other independent variables can be represented as follows,where C is a constant and a, b, c and d are exponents.To facilitate the determination of constants and exponents, this mathematical model will have to be linearized by performing a logarithmic transformation as follows:The constants and exponents C, a, b, c and d can be determined by the method of least squares. The first order linear model, developed from the above functional relationship using least squares method, can be represented as follows:where Y1 is the estimated response based on the first-order equation, Y is the measured surface roughness on a logarithmic scale, x0 = 1 (dummy variable), x1, x2, x3 and x4 are logarithmic transformations of cutting speed, feed rate, radial rake angle and nose radiusrespectively, ∈is the experimental error and b values are the estimates of corresponding parameters.The general second order polynomial response is as given below:where Y2 is the estimated response based on the second order equation. The parameters, i.e. b0, b1, b2, b3, b4, b12, b23, b14, etc. are to be estimated by the method of least squares. Validity of the selected model used for optimizing the process parameters has been tested with the help of statistical tests, such as F-test, chi square test, etc. [10].3.2 Optimization using genetic algorithmsMost of the researchers have used traditional optimization techniques for solving machining problems. The traditional methods of optimization and search do not fare well over a broad spectrum of problem domains. Traditional techniques are not efficient when the practical search space is too large. These algorithms are not robust. They are inclined to obtain a local optimal solution. Numerous constraints and number of passes make the machining optimization problem more complicated. So, it was decided to employ genetic algorithms as an optimization technique. GA come under the class of non-traditional search and optimization techniques. GA are different from traditional optimization techniques in the following ways:1.GA work with a coding of the parameter set, not the parameter themselves.2.GA search from a population of points and not a single point.3.GA use information of fitness function, not derivatives or other auxiliary knowledge.4.GA use probabilistic transition rules not deterministic rules.5.It is very likely that the expected GA solution will be the global solution.Genetic algorithms (GA) form a class of adaptive heuristics based on principles derived from the dynamics of natural population genetics. The searching process simulates the natural evaluation of biological creatures and turns out to be an intelligent exploitation of a random search. The mechanics of a GA is simple, involving copying of binary strings. Simplicity of operation and computational efficiency are the two main attractions of the genetic algorithmic approach. The computations are carried out in three stages to get a result in one generation or iteration. The three stages are reproduction, crossover and mutation.In order to use GA to solve any problem, the variable is typically encoded into a string (binary coding) or chromosome structure which represents a possible solution to the given problem. GA begin with a population of strings (individuals) created at random. The fitness of each individual string is evaluated with respect to the given objective function. Then this initial population is operated on by three main operators – reproduction cross over and mutation– to create, hopefully, a better population. Highly fit individuals or solutions are given theopportunity to reproduce by exchanging pieces of their genetic information, in the crossover procedure, with other highly fit individuals. This produces new “offspring” solutions, which share some characteristics taken from both the parents. Mutation is often applied after crossover by altering some genes (i.e. bits) in the offspring. The offspring can either replace the whole population (generational approach) or replace less fit individuals (steady state approach). This new population is further evaluated and tested for some termination criteria. The reproduction-cross over mutation- evaluation cycle is repeated until the termination criteria are met.4 Experimental detailsFor developing models on the basis of experimental data, careful planning of experimentation is essential. The factors considered for experimentation and analysis were cutting speed, feed rate, radial rake angle and nose radius.4.1 Experimental designThe design of experimentation has a major affect on the number of experiments needed. Therefore it is essential to have a well designed set of experiments. The range of values of each factor was set at three different levels, namely low, medium and high as shown in Table 1. Based on this, a total number of 81 experiments (full factorial design), each having a combination of different levels of factors, as shown in Table 2, were carried out.The variables were coded by taking into account the capacity and limiting cutting conditions of the milling machine. The coded values of variables, to be used in Eqs. 3 and 4, were obtained from the following transforming equations:where x1 is the coded value of cutting speed (S), x2 is the coded value of the feed rate ( f ), x3 is the coded value of radial rake angle(α) and x4 is the coded value of nose radius (r).4.2 ExperimentationA high precision ‘Rambaudi Rammatic 500’ CNC milling machine, with a vertical milling head, was used for experimentation. The control system is a CNC FIDIA-12 compact. The cutting tools, used for the experimentation, were solid coated carbide end mill cutters of different radial rake angles and nose radii (WIDIA: DIA20 X FL38 X OAL 102 MM). The tools are coated with TiAlN coating. The hardness, density and transverse rupture strength are 1570 HV 30, 14.5 gm/cm3 and 3800 N/mm2 respectively.AISI 1045 steel specimens of 100×75 mm and 20 mm thickness were used in the present study. All the specimens were annealed, by holding them at 850 ◦C for one hour and then cooling them in a furnace. The chemical analysis of specimens is presented in Table 3. Thehardness of the workpiece material is 170 BHN. All the experiments were carried out at a constant axial depth of cut of 20 mm and a radial depth of cut of 1 mm. The surface roughness (response) was measured with Talysurf-6 at a 0.8 mm cut-off value. An average of four measurements was used as a response value.5 Results and discussionThe influences of cutting speed, feed rate, radial rake angle and nose radius have been assessed by conducting experiments. The variation of machining response with respect to the variables was shown graphically in Fig. 1. It is seen from these figures that of the four dependent parameters, radial rake angle has definite influence on the roughness of the surface machined using an end mill cutter. It is felt that the prominent influence of radial rake angle on the surface generation could be due to the fact that any change in the radial rake angle changes the sharpness of the cutting edge on the periphery, i.e changes the contact length between the chip and workpiece surface. Also it is evident from the plots that as the radial rake angle changes from 4◦to 16◦, the surface roughness decreases and then increases. Therefore, it may be concluded here that the radial rake angle in the range of 4◦to 10◦would give a better surface finish. Figure 1 also shows that the surface roughness decreases first and then increases with the increase in the nose radius. This shows that there is a scope for finding the optimum value of the radial rake angle and nose radius for obtaining the best possible quality of the surface. It was also found that the surface roughness decreases with an increase in cutting speed and increases as feed rate increases. It could also be observed that the surface roughness was a minimum at the 250 m/min speed, 200 mm/min feed rate, 10◦radial rake angle and 0.8 mm nose radius. In order to understand the process better, the experimental results can be used to develop mathematical models using RSM. In this work, a commercially available mathematical software package (MATLAB) was used for the computation of the regression of constants and exponents.5.1 The roughness modelUsing experimental results, empirical equations have been obtained to estimate surface roughness with the significant parameters considered for the experimentation i.e. cutting speed, feed rate, radial rake angle and nose radius. The first order model obtained from the above functional relationship using the RSM method is as follows:The transformed equation of surface roughness prediction is as follows:Equation 10 is derived from Eq. 9 by substituting the coded values of x1, x2, x3 and x4 in termsof ln s, ln f , lnαand ln r. The analysis of the variance (ANOV A) and the F-ratio test have been performed to justify the accuracy of the fit for the mathematical model. Since the calculated values of the F-ratio are less than the standard values of the F-ratio for surface roughness as shown in Table 4, the model is adequate at 99% confidence level to represent the relationship between the machining response and the considered machining parameters of the end milling process.The multiple regression coefficient of the first order model was found to be 0.5839. This shows that the first order model can explain the variation in surface roughness to the extent of 58.39%. As the first order model has low predictability, the second order model has been developed to see whether it can represent better or not.The second order surface roughness model thus developed is as given below:where Y2 is the estimated response of the surface roughness on a logarithmic scale, x1, x2, x3 and x4 are the logarithmic transformation of speed, feed, radial rake angle and nose radius. The data of analysis of variance for the second order surface roughness model is shown in Table 5.Since F cal is greater than F0.01, there is a definite relationship between the response variable and independent variable at 99% confidence level. The multiple regression coefficient of the second order model was found to be 0.9596. On the basis of the multiple regression coefficient (R2), it can be concluded that the second order model was adequate to represent this process. Hence the second order model was considered as an objective function for optimization using genetic algorithms. This second order model was also validated using the chi square test. The calculated chi square value of the model was 0.1493 and them tabulated value at χ2 0.005 is 52.34, as shown in Table 6, which indicates that 99.5% of the variability in surface roughness was explained by this model.Using the second order model, the surface roughness of the components produced by end milling can be estimated with reasonable accuracy. This model would be optimized using genetic algorithms (GA).5.2 The optimization of end millingOptimization of machining parameters not only increases the utility for machining economics, but also the product quality toa great extent. In this context an effort has been made to estimate the optimum tool geometry and machining conditions to produce the best possible surface quality within the constraints.The constrained optimization problem is stated as follows: Minimize Ra using the model given here:where xil and xiu are the upper and lower bounds of process variables xi and x1, x2, x3, x4 are logarithmic transformation of cutting speed, feed, radial rake angle and nose radius.The GA code was developed using MATLAB. This approach makes a binary coding system to represent the variables cutting speed (S), feed rate ( f ), radial rake angle (α) and nose radius (r), i.e. each of these variables is represented by a ten bit binary equivalent, limiting the total string length to 40. It is known as a chromosome. The variables are represented as genes (substrings) in the chromosome. The randomly generated 20 such chromosomes (population size is 20), fulfilling the constraints on the variables, are taken in each generation. The first generation is called the initial population. Once the coding of the variables has been done, then the actual decoded values for the variables are estimated using the following formula: where xi is the actual decoded value of the cutting speed, feed rate, radial rake angle and nose radius, x(L) i is the lower limit and x(U) i is the upper limit and li is the substring length, which is equal to ten in this case.Using the present generation of 20 chromosomes, fitness values are calculated by the following transformation:where f(x) is the fitness function and Ra is the objective function.Out of these 20 fitness values, four are chosen using the roulette-wheel selection scheme. The chromosomes corresponding to these four fitness values are taken as parents. Then the crossover and mutation reproduction methods are applied to generate 20 new chromosomes for the next generation. This processof generating the new population from the old population is called one generation. Many such generations are run till the maximum number of generations is met or the average of four selected fitness values in each generation becomes steady. This ensures that the optimization of all the variables (cutting speed, feed rate, radial rake angle and nose radius) is carried out simultaneously. The final statistics are displayed at the end of all iterations. In order to optimize the present problem using GA, the following parameters have been selected to obtain the best possible solution with the least computational effort: Table 7 shows some of the minimum values of the surface roughness predicted by the GA program with respect to input machining ranges, and Table 8 shows the optimum machining conditions for the corresponding minimum values of the surface roughness shown in Table 7. The MRR given in Table 8 was calculated bywhere f is the table feed (mm/min), aa is the axial depth of cut (20 mm) and ar is the radial depth of cut (1 mm).It can be concluded from the optimization results of the GA program that it is possible toselect a combination of cutting speed, feed rate, radial rake angle and nose radius for achieving the best possible surface finish giving a reasonably good material removal rate. This GA program provides optimum machining conditions for the corresponding given minimum values of the surface roughness. The application of the genetic algorithmic approach to obtain optimal machining conditions will be quite useful at the computer aided process planning (CAPP) stage in the production of high quality goods with tight tolerances by a variety of machining operations, and in the adaptive control of automated machine tools. With the known boundaries of surface roughness and machining conditions, machining could be performed with a relatively high rate of success with the selected machining conditions.6 ConclusionsThe investigations of this study indicate that the parameters cutting speed, feed, radial rake angle and nose radius are the primary actors influencing the surface roughness of medium carbon steel uring end milling. The approach presented in this paper provides n impetus to develop analytical models, based on experimental results for obtaining a surface roughness model using the response surface methodology. By incorporating the cutter geometry in the model, the validity of the model has been enhanced. The optimization of this model using genetic algorithms has resulted in a fairly useful method of obtaining machining parameters in order to obtain the best possible surface quality.中文翻译选择最佳工具,几何形状和切削条件利用表面粗糙度预测模型端铣摘要:刀具几何形状对工件表面质量产生的影响是人所共知的,因此,任何成型面端铣设计应包括刀具的几何形状。
高速切削加工中英文对照外文翻译文献

中英文对照外文翻译文献(文档含英文原文和中文翻译)英文:High-speed millingHigh-speed machining is an advanced manufacturing technology, different from the traditional processing methods. The spindle speed, cutting feed rate, cutting a small amount of units within the time of removal of material has increased three to six times. With high efficiency, high precision and high quality surface as the basic characteristics of the automobile industry, aerospace, mold manufacturing and instrumentation industry, such as access to a wide range of applications, has made significant economic benefits, is the contemporary importance of advanced manufacturing technology. For a long time, people die on the processing has been using a grinding or milling EDM (EDM) processing, grinding, polishing methods. Although the high hardness of the EDM machine parts, but the lower the productivity of its application is limited. With the development of high-speed processing technology, used to replace high-speed cutting, grinding and polishing process to die processing has become possible. To shorten the processing cycle, processing and reliable quality assurance, lower processing costs.1 One of the advantages of high-speed machiningHigh-speed machining as a die-efficient manufacturing, high-quality, low power consumption in an advanced manufacturing technology. In conventional machining in a series of problems has plagued by high-speed machining of the application have been resolved.1.1 Increase productivityHigh-speed cutting of the spindle speed, feed rate compared withtraditional machining, in the nature of the leap, the metal removal rate increased 30 percent to 40 percent, cutting force reducedby 30 percent, the cutting tool life increased by 70% . Hardened parts can be processed, a fixture in many parts to be completed rough, semi-finishing and fine, and all other processes, the complex can reach parts of the surface quality requirements, thus increasing the processing productivity and competitiveness of products in the market.1.2 Improve processing accuracy and surface qualityHigh-speed machines generally have high rigidity and precision, and other characteristics, processing, cutting the depth of small, fast and feed, cutting force low, the workpiece to reduce heat distortion, and high precision machining, surface roughness small. Milling will be no high-speed processing and milling marks the surface so that the parts greatly enhance the quality of the surface. Processing Aluminum when up Ra0.40.6um, pieces of steel processing at up to Ra0.2 ~ 0.4um.1.3 Cutting reduce the heatBecause the main axis milling machine high-speed rotation, cutting a shallow cutting, and feed very quickly, and the blade length of the workpiece contacts and contact time is very short, a decrease of blades and parts of the heat conduction. High-speed cutting by dry milling or oil cooked up absolute (mist) lubrication system, to avoid the traditional processing tool in contact with the workpiece and a lot of shortcomings to ensure that the tool is not high temperature under the conditions of work, extended tool life.1.4 This is conducive to processing thin-walled partsHigh-speed cutting of small cutting force, a higher degree of stability, Machinable with high-quality employees compared to the company may be very good, but other than the company's employees may Suanbu Le outstanding work performance. For our China practice, we use the models to determine the method of staff training needs are simple and effective. This study models can be an external object, it can also be a combination of internal and external. We must first clear strategy for the development of enterprises. Through the internal and external business environment and organizational resources, such as analysis, the future development of a clear business goals and operational priorities. According to the business development strategy can be compared to find the business models, through a comparative analysis of the finalization of business models. In determining business models, a, is the understanding of its development strategy, or its market share and market growth rate, or the staff of the situation, and so on, according to the companies to determine the actual situation. As enterprises in different period of development, its focus is different, which means that enterprises need to invest the manpower and financial resources the focus is different. So in a certain period of time, enterprises should accurately selected their business models compared with the departments and posts, so more practical significance, because the business models are not always good, but to compare some aspects did not have much practical significance, Furthermore This can more fully concentrate onthe business use of limited resources. Identify business models, and then take the enterprise of the corresponding departments and staff with the business models for comparison, the two can be found in the performance gap, a comparative analysis to find reasons, in accordance with this business reality, the final identification of training needs. The cost of training is needed, if not through an effective way to determine whether companies need to train and the training of the way, but blind to training, such training is difficult to achieve the desired results. A comparison only difference between this model is simple and practical training.1.5 Can be part of some alternative technology, such as EDM, grinding high intensity and high hardness processingHigh-speed cutting a major feature of high-speed cutting machine has the hardness of HRC60 parts. With the use of coated carbide cutter mold processing, directly to the installation of a hardened tool steel processing forming, effectively avoid the installation of several parts of the fixture error and improve the parts of the geometric location accuracy. In the mold of traditional processing, heat treatment hardening of the workpiece required EDM, high-speed machining replace the traditional method of cutting the processing, manufacturing process possible to omit die in EDM, simplifying the processing technology and investment costs .High-speed milling in the precincts of CNC machine tools, or for processing centre, also in the installation of high-speed spindle on the general machine tools. The latter not only has the processing capacity of general machine tools, but also for high-speed milling, a decrease of investment in equipment, machine tools increased flexibility. Cutting high-speed processing can improve the efficiency, quality improvement, streamline processes, investment and machine tool investment and maintenance costs rise, but comprehensive, can significantly increase economic efficiency.2 High-speed millingHigh-speed milling the main technical high-speed cutting technology is cutting the development direction of one of it with CNC technology, microelectronic technology, new materials and new technology, such as technology development to a higher level. High-speed machine tools and high-speed tool to achieve high-speed cutting is the prerequisite and basic conditions, in high-speed machining in the performance of high-speed machine tool material of choice and there are strict requirements.2.1 High-speed milling machine in order to achieve high-speed machiningGeneral use of highly flexible high-speed CNC machine tools, machining centers, and some use a dedicated high-speed milling, drilling. At the same time a high-speed machine tool spindle system and high-speed feeding system, high stiffness of the main characteristics of high-precision targeting and high-precision interpolation functions, especially high-precision arc interpolation function. High-speed machining systems of the machine a higher demand, mainly in the followingareas:General use of highly flexible high-speed CNC machine tools, machining centers, and some use a dedicated high-speed milling, drilling. At the same time a high-speed machine tool spindle system and high-speed feeding system, high stiffness of the main characteristics of high-precision targeting and high-precision interpolation functions, especially high-precision arc interpolation function. High-speed machining systems of the machine a higher demand, mainly in the following areas:High-speed milling machine must have a high-speed spindle, the spindle speed is generally 10000 ~ 100000 m / min, power greater than 15 kW. But also with rapid speed or in designated spots fast-stopping performance. The main axial space not more than 0 .0 0 0 2 m m. Often using high-speed spindle-hydrostatic bearings, air pressure-bearing, mixed ceramic bearings, magnetic bearing structure of the form. Spindle cooling general use within the water or air cooled.High-speed processing machine-driven system should be able to provide 40 ~ 60 m / min of the feed rate, with good acceleration characteristics, can provide 0.4 m/s2 to 10 m/s2 acceleration and deceleration. In order to obtain good processing quality, high-speed cutting machines must have a high enough stiffness. Machine bed material used gray iron, can also add a high-damping base of concrete, to prevent cutting tool chatter affect the quality of processing. A high-speed data transfer rate, can automatically increase slowdown. Processing technology to improve the processing and cutting tool life. At present high-speed machine tool manufacturers, usually in the general machine tools on low speed, the feed of the rough and then proceed to heat treatment, the last in the high-speed machine on the half-finished and finished, in improving the accuracy and efficiency at the same time, as far as possible to reduce processing Cost.2.2 High-speed machining toolHigh-speed machining tool is the most active one of the important factors, it has a direct impact on the efficiency of processing, manufacturing costs and product processing and accuracy. Tool in high-speed processing to bear high temperature, high pressure, friction, shock and vibration, such as loading, its hardness and wear-resistance, strength and toughness, heat resistance, technology and economic performance of the basic high-speed processing performance is the key One of the factors. High-speed cutting tool technology development speed, the more applications such as diamond (PCD), cubic boron nitride (CBN), ceramic knives, carbide coating, (C) titanium nitride Carbide TIC (N) And so on. CBN has high hardness, abrasion resistance and the extremely good thermal conductivity, and iron group elements between the great inertia, in 1300 ℃ would not have happened significant role in the chemical, also has a good stability. The experiments show that with CBN cutting toolHRC35 ~ 67 hardness of hardened steel can achieve very high speed. Ceramics have good wear resistance and thermal chemical stability, its hardness, toughness below the CBN, can be used for processing hardness of HRC <5 0 parts. Carbide Tool good wear resistance, but thehardness than the low-CBN and ceramics. Coating technology used knives, cutting tools can improve hardness and cutting the rate, for cutting HRC40 ~ 50 in hardness between the workpiece. Can be used to heat-resistant alloys, titanium alloys, hightemperature alloy, cast iron, Chungang, aluminum and composite materials of high-speed cutting Cut, the most widely used. Precision machining non-ferrous metals or non-metallic materials, or the choice of polycrystalline diamond Gang-coated tool.2.3 High-speed processing technologyHigh-speed cutting technology for high-speed machining is the key. Cutting Methods misconduct, will increase wear tool to less than high-speed processing purposes. Only high-speed machine tool and not a good guide technology, high-speed machining equipment can not fully play its role. In high-speed machining, should be chosen with milling, when the milling cutter involvement with the workpiece chip thickness as the greatest, and then gradually decreased. High-speed machining suitable for shallow depth of cut, cutting depth of not more than 0.2 mm, to avoid the location of deviation tool to ensure that the geometric precision machining parts. Ensure that the workpiece on the cutting constant load, to get good processing quality. Cutting a single high-speed milling path-cutting mode, try not to interrupt the process and cutting tool path, reducing the involvement tool to cut the number to be relatively stable cutting process. Tool to reduce the rapid change to, in other words when the NC machine tools must cease immediately, or Jiangsu, and then implement the next step. As the machine tool acceleration restrictions, easy to cause a waste of time, and exigency stop or radical move would damage the surface accuracy. In the mold of high-speed finishing, in each Cut, cut to the workpiece, the feed should try to change the direction of a curve or arc adapter, avoid a straight line adapter to maintain the smooth process of cutting.3 Die in high-speed milling processing ofMilling as a highly efficient high-speed cutting of the new method,inMould Manufacturing has been widely used. Forging links in the regular production model, with EDM cavity to be 12 ~ 15 h, electrodes produced 2 h. Milling after the switch to high-speed, high-speed milling cutter on the hardness of HRC 6 0 hardened tool steel processing. The forging die processing only 3 h20min, improve work efficiency four to five times the processing surface roughness of Ra0.5 ~ 0.6m, fully in line with quality requirements.High-speed cutting technology is cutting technology one of the major developments, mainly used in automobile industry and die industry, particularly in the processing complex surface, the workpiece itself or knives rigid requirements of the higher processing areas, is a range of advanced processing technology The integration, high efficiency and high quality for the people respected. It not only involves high-speed processing technology, but also including high-speed processing machine tools, numerical control system, high-speed cutting tools and CAD / CAMtechnology. Die-processing technology has been developed in the mold of the manufacturing sector in general, and in my application and the application of the standards have yet to be improved, because of its traditional processing with unparalleled advantages, the future will continue to be an inevitable development of processing technology Direction.4 Numerical control technology and equipping development trend and countermeasureEquip the engineering level, level of determining the whole national economy of the modernized degree and modernized degree of industry, numerical control technology is it develop new developing new high-tech industry and most advanced industry to equip (such as information technology and his industry, biotechnology and his industry, aviation, spaceflight, etc. national defense industry) last technology and getting more basic most equipment. Marx has ever said "the differences of different economic times, do not lie in what is produced, and lie in how to produce, produce with some means of labor ". Manufacturing technology and equipping the most basic means of production that are that the mankind produced the activity, and numerical control technology is nowadays advanced manufacturing technology and equips the most central technology. Nowadays the manufacturing industry all around the world adopts numerical control technology extensively, in order to improve manufacturing capacity and level, improve the adaptive capacity and competitive power to the changeable market of the trends. In addition every industrially developed country in the world also classifies the technology and numerical control equipment of numerical control as the strategic materials of the country, not merely take the great measure to develop one's own numerical control technology and industry, and implement blockading and restrictive policy to our country in view of " high-grade, precision and advanced key technology of numerical control " and equipping. In a word, develop the advanced manufacturing technology taking numerical control technology as the core and already become every world developed country and accelerate economic development in a more cost-effective manner, important way to improve the overall national strength and national position. Numerical control technology is the technology controlled to mechanical movement and working course with digital information, integrated products of electromechanics that the numerical control equipment is the new technology represented by numerical control technology forms to the manufacture industry of the tradition and infiltration of the new developing manufacturing industry, namely the so-called digitization is equipped, its technological range covers a lot of fields: (1)Mechanical manufacturing technology; (2)Information processing, processing, transmission technology; (3)Automatic control technology; (4)Servo drive technology;(5)Technology of the sensor; (6)Software engineering ,etc..Development trend of a numerical control technologyThe application of numerical control technology has not only brought the revolutionary change to manufacturing industry of the tradition, make the manufacturing industry become the industrialized symbol , and with the constant development of numerical control technology andenlargement of the application, the development of some important trades (IT , automobile , light industry , medical treatment ,etc. ) to the national economy and the people's livelihood of his plays a more and more important role, because the digitization that these trades needed to equip has already been the main trend of modern development. Numerical control technology in the world at present and equipping the development trend to see, there is the following several respect [1- ] in its main research focus.5 A high-speed, high finish machining technology and new trend equippedThe efficiency, quality are subjavanufacturing technology. High-speed, high finish machining technology can raise the efficiency greatly , improve the quality and grade of the products, shorten production cycle and improve the market competitive power. Japan carries the technological research association first to classify it as one of the 5 great modern manufacturing technologies for this, learn (CIRP) to confirm it as the centre in the 21st century and study one of the directions in international production engineering.In the field of car industry, produce one second when beat such as production of 300,000 / vehicle per year, and many variety process it is car that equip key problem that must be solved one of; In the fields of aviation and aerospace industry, spare parts of its processing are mostly the thin wall and thin muscle, rigidity is very bad, the material is aluminium or aluminium alloy, only in a situation that cut the speed and cut strength very small high, could process these muscles, walls. Adopt large-scale whole aluminium alloy method that blank " pay empty " make the wing recently, such large-scale parts as the fuselage ,etc. come to substitute a lot of parts to assemble through numerous rivet , screw and other connection way, make the intensity , rigidity and dependability of the component improved. All these, to processing and equipping the demand which has proposed high-speed, high precise and high flexibility.According to EMO2001 exhibition situation, high-speed machining center is it give speed can reach 80m/min is even high , air transport competent speed can up to 100m/min to be about to enter. A lot of automobile factories in the world at present, including Shanghai General Motors Corporation of our country, have already adopted and substituted and made the lathe up with the production line part that the high-speed machining center makes up. HyperMach lathe of U.S.A. CINCINNATI Company enters to nearly biggest 60m/min of speed, it is 100m/min to be fast, the acceleration reaches 2g, the rotational speed of the main shaft has already reached 60 000r/min. Processing a thin wall of plane parts, spend 30min only, and same part general at a high speed milling machine process and take 3h, the ordinary milling machine is being processed to need 8h; The speed and acceleration of main shaft of dual main shaft lathes of Germany DMG Company are up to 120000r/mm and 1g.In machining accuracy, the past 10 years, ordinary progression accuse of machining accuracy of lathe bring 5μm up to from 10μm already, accurate grades of machining center from 3~5μm, rise to 1~1.5μm, and ultrap recision machining accuracy is it enter nanometer grade to begin already(0.01μm).In dependability, MTBF value of the foreign numerical control device has already reached above 6 000h, MTBF value of the servo system reaches above 30000h, demonstrate very high dependability .In order to realize high-speed, high finish machining, if the part of function related to it is electric main shaft, straight line electrical machinery get fast development, the application is expanded further .5.2 Link and process and compound to process the fast development of the lathe in 5 axesAdopt 5 axles to link the processing of the three-dimensional curved surface part, can cut with the best geometry form of the cutter , not only highly polished, but also efficiency improves by a large margin . It is generally acknowledged, the efficiency of an 5 axle gear beds can equal 2 3 axle gear beds, is it wait for to use the cubic nitrogen boron the milling cutter of ultra hard material is milled and pared at a high speed while quenching the hard steel part, 5 axles link and process 3 constant axles to link and process and give play to higher benefit. Because such reasons as complicated that 5 axles link the numerical control system , host computer structure that but go over, it is several times higher that its price links the numerical control lathe than 3 axles , in addition the technological degree of difficulty of programming is relatively great, have restricted the development of 5 axle gear beds.At present because of electric appearance of main shaft, is it realize 5 axle complex main shaft hair structure processed to link greatly simplify to make, it makes degree of difficulty and reducing by a large margin of the cost, the price disparity of the numerical control system shrinks. So promoted 5 axle gear beds of head of complex main shaft and compound to process the development of the lathe (process the lathe including 5).At EMO2001 exhibition, new Japanese 5 of worker machine process lathe adopt complex main shaft hair, can realize the processing of 4 vertical planes and processing of the wanton angle, make 5 times process and 5 axles are processed and can be realized on the same lathe, can also realize the inclined plane and pour the processing of the hole of awls. Germany DMG Company exhibits the DMUVoution series machining center, but put and insert and put processing and 5 axles 5 times to link and process in once, can be controlled by CNC system or CAD/CAM is controlled directly or indirectly.5.3 Become the main trend of systematic development of contemporary numerical control intelligently, openly, networkedly.The numerical control equipment in the 21st century will be sure the intelligent system, the intelligent content includes all respects in the numerical control system: It is intelligent in order to pursue the efficiency of processing and process quality, control such as the self-adaptation of the processing course, the craft parameter is produced automatically; Join the convenient one in order to improve the performance of urging and use intelligently, if feedforward control , adaptiveoperation , electrical machinery of parameter , discern load select models , since exactly makes etc. automatically; The ones that simplified programming , simplified operating aspect are intelligent, for instance intelligent automatic programming , intelligent man-machine interface ,etc.; There are content of intelligence diagnose , intelligent monitoring , diagnosis convenient to be systematic and maintaining ,etc..Produce the existing problem for the industrialization of solving the traditional numerical control system sealing and numerical control application software. A lot of countries carry on research to the open numerical control system at present, such as NGC of U.S.A. (The Next Generation Work-Station/Machine Control), OSACA of European Community (Open System Architecture for Control within Automation Systems), OSEC (Open System Environment for Controller) of Japan, ONC (Open Numerical Control System) of China, etc.. The numerical control system melts to become the future way of the numerical control system open. The so-called open numerical control system is the development of the numerical control system can be on unified operation platform, face the lathe producer and end user, through changing, increasing or cutting out the structure target(numerical control function), form the serration, and can use users specially conveniently and the technical know-how is integrated in the control system, realize the open numerical control system of different variety , different grade fast, form leading brand products with distinct distinction. System structure norm of the open numerical control system at present, communication norm , disposing norm , operation platform , numerical control systematic function storehouse and numerical control systematic function software development ,etc. are the core of present research.The networked numerical control equipment is a new light spot of the fair of the internationally famous lathe in the past two years. Meeting production line , manufacture system , demand for the information integration of manufacturing company networkedly greatly of numerical control equipment, realize new manufacture mode such as quick make , fictitious enterprise , basic Entrance that the whole world make too. Some domestic and international famous numerical control lathes and systematic manufacturing companies of numerical control have all introduced relevant new concepts and protons of a machine in the past two years, if in EMO2001 exhibition, " Cyber Production Center " that the company exhibits of mountain rugged campstool gram in Japan (Mazak) (intellectual central production control unit, abbreviated as CPC); The lathe company of Japanese big Wei (Okuma ) exhibits " IT plaza " (the information technology square , is abbreviated as IT square ); Open Manufacturing Environment that the company exhibits of German Siemens (Siemens ) (open the manufacturing environment, abbreviated as OME),etc., have reflected numerical control machine tooling to the development trend of networked direction.5.4 Pay attention to the new technical standard, normal setting-up5.4.1 Design the norm of developing about the numerical control systemAs noted previously, there are better common ability, flexibility, adaptability, expanding in theopen numerical control system, such countries as U.S.A. ,European Community and Japan ,etc. implement the strategic development plan one after another , carry on the research and formulation of the systematic norm (OMAC , OSACA , OSEC ) of numerical control of the open system structure, 3 biggest economies in the world have carried on the formulation that nearly the same science planned and standardized in a short time, have indicated a new arrival of period of change of numerical control technology. Our country started the research and formulation of standardizing the frame of ONC numerical control system of China too in 2000.5.4.2 About the numerical control standardThe numerical control standard is a kind of trend of information-based development of manufacturing industry. Information exchange among 50 years after numerical control technology was born was all because of ISO6983 standard, namely adopt G, M code describes how processes, its essential characteristic faces the processing course, obviously, he can't meet high-speed development of modern numerical control technology's needs more and more already. For this reason, studying and making a kind of new CNC system standard ISO14649 (STEP-NC) in the world, its purpose is to offer a kind of neutral mechanism not depending on the concrete system, can describe the unified data model in cycle of whole life of the products, thus realize the whole manufacture process, standardization of and even each industrial field product information.The appearance of STEP-NC may be a revolution of the technological field of the numerical control, on the development and even the whole manufacturing industry of numerical control technology, will exert a far-reaching influence. First of all, STEP-NC puts forward a kind of brand-new manufacture idea, in the traditional manufacture idea, NC processes the procedures to all concentrate on individual computer. Under the new standard, NC procedure can be dispersed on Internet, this is exactly a direction of open , networked development of numerical control technology. Secondly, STEP-NC numerical control system can also reduce and process the drawing (about 75%), process the procedure to work out the time (about 35%) and process the time (about 50%) greatly.At present, American-European countries pay much attention to the research of STEP-NC, Europe initiates IMS plan (1999.1.1-2001.12.3) of STEP-NC. 20 CAD/CAM/CAPP/CNC users, manufacturers and academic organizations from Europe and Japan participated in this plan. STEP Tools Company of U.S.A. is a developer of the data interchange software of manufacturing industry in the global range, he has already developed the super model (Super Model ) which accuses of information exchange of machine tooling by counting, its goal is to describe all processing courses with the unified norm. Such new data interchange form has already been verified in allocating the SIEMENS, FIDIA and European OSACA-NC numerical control at present.6 pairs of basic estimations of technology and industry development of numerical control of our country。
化工 外文翻译模板

毕业设计(论文)外文资料翻译学院:机械工程学院专业班级:机械设计制造及其自动化 G机械132 学生姓名:孙铷学号: 2013150075指导教师:訾克明(副教授) 外文出处:Biotechnology Reports 3(2014)99-107附件:1.外文资料翻译译文; 2.外文原文在双螺杆挤出机中酶法水解预处理后的玉米穗轴蒸汽爆炸残留物Jun Zhenga ,Kim Chooa,b ,Chris Bradtc ,Rick Lehouxc ,Lars Rehmanna, *A 化学工程与生物工程系,西安大略大学,里士满1151街,伦敦,在N6A 3K7。
B 加拿大莱姆顿学院,1457街,伦敦路,在N7S 6K4。
摘要将结合有过滤装置的改进的双螺杆挤出机用作液体/固体分离器,用于从蒸汽爆炸玉米芯中除去木糖。
面心为中心的复合设计用于研究各种酶水解过程变量(酶负载,表面活性剂添加和水解时间)与两种不同挤出的玉米芯(7%木糖去除,80%木糖去除)对葡萄糖转化的组合效应。
结果表明,挤出过程导致纤维素结晶度的增加,而结构变化也可以通过SEM观察到。
开发了用于预测葡萄糖转化的二次多项式模型,并且拟合的模型提供了通过方差分析(ANOVA)验证的真实响应的充分近似。
简介木质纤维素生物质向乙醇的生物转化被认为是石油基液体燃料的最重要的替代品之一[14-15,17,29,35]。
木质纤维素生物质是高度丰富的,具有高能量潜力并且是用于乙醇生产的低成本材料。
典型来源是林产品,农业残余物,城市固体废物和专用能源作物[18,31]。
玉米芯,玉米籽粒生产的副产品,在欧洲的一些地区曾经用于动物饲料和肥料,用于农业生产,而在美国,玉米芯目前被用作纤维素乙醇生产的潜在原料,由于其低木质素和高碳水化合物含量。
此外,玉米芯具有产生约8000Btu / lb的高热值(HHV)。
平均玉米棒产量为谷粒产量的约14%,占玉米秸秆总产量的约16%[4,22,32]。
机械类英语论文与翻译翻译

High-speed millingHigh-speed machining is an advanced manufacturing technology, different from the traditional processing methods. The spindle speed, cutting feed rate, cutting a small amount of units within the time of removal of material has increased three to six times. With high efficiency, high precision and high quality surface as the basic characteristics of the automobile industry, aerospace, mold manufacturing and instrumentation industry, such as access to a wide range of applications, has made significant economic benefits, is the contemporary importance of advanced manufacturing technology. For a long time, people die on the processing has been using a grinding or milling EDM (EDM) processing, grinding, polishing methods. Although the high hardness of the EDM machine parts, but the lower the productivity of its application is limited. With the development of high-speed processing technology, used to replace high-speed cutting, grinding and polishing process to die processing has become possible. To shorten the processing cycle, processing and reliable quality assurance, lower processing costs.1 One of the advantages of high-speed machiningHigh-speed machining as a die-efficient manufacturing, high-quality, low power consumption in an advanced manufacturing technology. In conventional machining in a series of problems has plagued by high-speed machining of the application have been resolved.1.1 Increase productivityHigh-speed cutting of the spindle speed, feed rate compared withtraditional machining, in the nature of the leap, the metal removal rate increased 30 percent to 40 percent, cutting force reduced by 30 percent, the cutting tool life increased by 70% . Hardened parts can be processed, a fixture in many parts to be completed rough, semi-finishing and fine, and all other processes, the complex can reach parts of the surface quality requirements, thus increasing the processing productivity and competitiveness of products in the market.1.2 Improve processing accuracy and surface qualityHigh-speed machines generally have high rigidity and precision, and other characteristics, processing, cutting the depth of small, fast and feed, cutting force low, the workpiece to reduce heat distortion, and high precision machining,surface roughness small. Milling will be no high-speed processing and milling marks the surface so that the parts greatly enhance the quality of the surface. Processing Aluminum when up Ra0.40.6um, pieces of steel processing at up to Ra0.2 ~ 0.4um.1.3 Cutting reduce the heatBecause the main axis milling machine high-speed rotation, cutting a shallow cutting, and feed very quickly, and the blade length of the workpiece contacts and contact time is very short, a decrease of blades and parts of the heat conduction. High-speed cutting by dry milling or oil cooked up absolute (mist) lubrication system, to avoid the traditional processing tool in contact with the workpiece and a lot of shortcomings to ensure that the tool is not high temperature under the conditions of work, extended tool life.1.4 This is conducive to processing thin-walled partsHigh-speed cutting of small cutting force, a higher degree of stability, Machinable with high-quality employees compared to the company may be very good, but other than the company's employees may Suanbu Le outstanding work performance. For our China practice, we use the models to determine the method of staff training needs are simple and effective. This study models can be an external object, it can also be a combination of internal and external. We must first clear strategy for the development of enterprises. Through the internal and external business environment and organizational resources, such as analysis, the future development of a clear business goals and operational priorities. According to the business development strategy can be compared to find the business models, through a comparative analysis of the finalization of business models. In determining business models, a, is the understanding of its development strategy, or its market share and market growth rate, or the staff of the situation, and so on, according to the companies to determine the actual situation. As enterprises in different period of development, its focus is different, which means that enterprises need to invest the manpower and financial resources the focus is different. So in a certain period of time, enterprises should accurately selected their business models compared with the departments and posts, so more practical significance, because the business models are not always good, but to compare some aspects did not have much practical significance, Furthermore This can more fully concentrate on the business use of limited resources. Identify business models, and then take the enterprise of the corresponding departments and staff with the business models for comparison, the two can be found in the performance gap, a comparative analysis to find reasons, in accordance with this business reality, the final identification of training needs.The cost of training is needed, if not through an effective way to determine whether companies need to train and the training of the way, but blind to training, such training is difficult to achieve the desired results. A comparison only difference between this model is simple and practical training.1.5 Can be part of some alternative technology, such as EDM, grinding high intensity and high hardness processingHigh-speed cutting a major feature of high-speed cutting machine has the hardness of HRC60 parts. With the use of coated carbide cutter mold processing, directly to the installation of a hardened tool steel processing forming, effectively avoid the installation of several parts of the fixture error and improve the parts of the geometric location accuracy. In the mold of traditional processing, heat treatment hardening of the workpiece required EDM, high-speed machining replace the traditional method of cutting the processing, manufacturing process possible to omit die in EDM, simplifying the processing technology and investment costs . High-speed milling in the precincts of CNC machine tools, or for processing centre, also in the installation of high-speed spindle on the general machine tools. The latter not only has the processing capacity of general machine tools, but also for high-speed milling, a decrease of investment in equipment, machine tools increased flexibility. Cutting high-speed processing can improve the efficiency, quality improvement, streamline processes, investment and machine tool investment and maintenance costs rise, but comprehensive, can significantly increase economic efficiency.2 High-speed millingHigh-speed milling the main technical high-speed cutting technology is cutting the development direction of one of it with CNC technology, microelectronic technology, new materials and new technology, such as technology development to a higher level. High-speed machine tools and high-speed tool to achieve high-speed cutting is the prerequisite and basic conditions, in high-speed machining in the performance of high-speed machine tool material of choice and there are strict requirements.2.1 High-speed milling machine in order to achieve high-speed machiningGeneral use of highly flexible high-speed CNC machine tools, machining centers, and some use a dedicated high-speed milling, drilling. At the same time a high-speed machine tool spindle system and high-speed feeding system, high stiffness of the main characteristics of high-precision targeting and high-precision interpolation functions, especially high-precision arc interpolation function. High-speedmachining systems of the machine a higher demand, mainly in the following areas: General use of highly flexible high-speed CNC machine tools, machining centers, and some use a dedicated high-speed milling, drilling. At the same time a high-speed machine tool spindle system and high-speed feeding system, high stiffness of the main characteristics of high-precision targeting and high-precision interpolation functions, especially high-precision arc interpolation function. High-speed machining systems of the machine a higher demand, mainly in the following areas: High-speed milling machine must have a high-speed spindle, the spindle speed is generally 10000 ~ 100000 m / min, power greater than 15 kW. But also with rapid speed or in designated spots fast-stopping performance. The main axial space not more than 0 .0 0 0 2 m m. Often using high-speed spindle-hydrostatic bearings, air pressure-bearing, mixed ceramic bearings, magnetic bearing structure of the form. Spindle cooling general use within the water or air cooled.High-speed processing machine-driven system should be able to provide 40 ~ 60 m / min of the feed rate, with good acceleration characteristics, can provide 0.4 m/s2 to 10 m/s2 acceleration and deceleration. In order to obtain good processing quality, high-speed cutting machines must have a high enough stiffness. Machine bed material used gray iron, can also add a high-damping base of concrete, to prevent cutting tool chatter affect the quality of processing. A high-speed data transfer rate, can automatically increase slowdown. Processing technology to improve the processing and cutting tool life. At present high-speed machine tool manufacturers, usually in the general machine tools on low speed, the feed of the rough and then proceed to heat treatment, the last in the high-speed machine on the half-finished and finished, in improving the accuracy and efficiency at the same time, as far as possible to reduce processing Cost.2.2 High-speed machining toolHigh-speed machining tool is the most active one of the important factors, it has a direct impact on the efficiency of processing, manufacturing costs and product processing and accuracy. Tool in high-speed processing to bear high temperature, high pressure, friction, shock and vibration, such as loading, its hardness and wear-resistance, strength and toughness, heat resistance, technology and economic performance of the basic high-speed processing performance is the key One of the factors. High-speed cutting tool technology development speed, the more applications such as diamond (PCD), cubic boron nitride (CBN), ceramic knives, carbide coating, (C) titanium nitride Carbide TIC (N) And so on. CBN has high hardness, abrasion resistance and the extremely good thermal conductivity, and iron group elements between the great inertia, in 1300 ℃ would not have happened significantrole in the chemical, also has a good stability. The experiments show that with CBN cutting toolHRC35 ~ 67 hardness of hardened steel can achieve very high speed. Ceramics have good wear resistance and thermal chemical stability, its hardness, toughness below the CBN, can be used for processing hardness of HRC <5 0 parts. Carbide Tool good wear resistance, but the hardness than the low-CBN and ceramics. Coating technology used knives, cutting tools can improve hardness and cutting the rate, for cutting HRC40 ~ 50 in hardness between the workpiece. Can be used to heat-resistant alloys, titanium alloys, hightemperature alloy, cast iron, Chungang, aluminum and composite materials of high-speed cutting Cut, the most widely used. Precision machining non-ferrous metals or non-metallic materials, or the choice of polycrystalline diamond Gang-coated tool.2.3 High-speed processing technologyHigh-speed cutting technology for high-speed machining is the key. Cutting Methods misconduct, will increase wear tool to less than high-speed processing purposes. Only high-speed machine tool and not a good guide technology, high-speed machining equipment can not fully play its role. In high-speed machining, should be chosen with milling, when the milling cutter involvement with the workpiece chip thickness as the greatest, and then gradually decreased. High-speed machining suitable for shallow depth of cut, cutting depth of not more than 0.2 mm, to avoid the location of deviation tool to ensure that the geometric precision machining parts. Ensure that the workpiece on the cutting constant load, to get good processing quality. Cutting a single high-speed milling path-cutting mode, try not to interrupt the process and cutting tool path, reducing the involvement tool to cut the number to be relatively stable cutting process. Tool to reduce the rapid change to, in other words when the NC machine tools must cease immediately, or Jiangsu, and then implement the next step. As the machine tool acceleration restrictions, easy to cause a waste of time, and exigency stop or radical move would damage the surface accuracy. In the mold of high-speed finishing, in each Cut, cut to the workpiece, the feed should try to change the direction of a curve or arc adapter, avoid a straight line adapter to maintain the smooth process of cutting.3 Die in high-speed milling processing ofMilling as a highly efficient high-speed cutting of the new method,in Mould Manufacturing has been widely used. Forging links in the regular production model, with EDM cavity to be 12 ~ 15 h, electrodes produced 2 h. Milling after the switch to high-speed, high-speed milling cutter on the hardness of HRC 6 0 hardenedtool steel processing. The forging die processing only 3 h20min, improve work efficiency four to five times the processing surface roughness of Ra0.5 ~ 0.6m, fully in line with quality requirements.High-speed cutting technology is cutting technology one of the major developments, mainly used in automobile industry and die industry, particularly in the processing complex surface, the workpiece itself or knives rigid requirements of the higher processing areas, is a range of advanced processing technology The integration, high efficiency and high quality for the people respected. It not only involves high-speed processing technology, but also including high-speed processing machine tools, numerical control system, high-speed cutting tools and CAD / CAM technology. Die-processing technology has been developed in the mold of the manufacturing sector in general, and in my application and the application of the standards have yet to be improved, because of its traditional processing with unparalleled advantages, the future will continue to be an inevitable development of processing technology Direction.4 Numerical control technology and equipping development trend and countermeasure Equip the engineering level, level of determining the whole national economy of the modernized degree and modernized degree of industry, numerical control technology is it develop new developing new high-tech industry and most advanced industry to equip (such as information technology and his industry, biotechnology and his industry, aviation, spaceflight, etc. national defense industry) last technology and getting more basic most equipment. Marx has ever said "the differences of different economic times, do not lie in what is produced, and lie in how to produce, produce with some means of labor ". Manufacturing technology and equipping the most basic means of production that are that the mankind produced the activity, and numerical control technology is nowadays advanced manufacturing technology and equips the most central technology. Nowadays the manufacturing industry all around the world adopts numerical control technology extensively, in order to improve manufacturing capacity and level, improve the adaptive capacity and competitive power to the changeable market of the trends. In addition every industrially developed country in the world also classifies the technology and numerical control equipment of numerical control as the strategic materials of the country, not merely take the great measure to develop one's own numerical control technology and industry, and implement blockading and restrictive policy to our country in view of " high-grade, precision and advanced key technology of numerical control " and equipping. In a word, develop the advanced manufacturing technology taking numerical control technology as the core and already become every world developed country and accelerate economic development in a more cost-effective manner, important way to improve the overall national strength and national position.Numerical control technology is the technology controlled to mechanical movement and working course with digital information, integrated products ofelectromechanics that the numerical control equipment is the new technology represented by numerical control technology forms to the manufacture industry of the tradition and infiltration of the new developing manufacturing industry, namely the so-called digitization is equipped, its technological range covers a lot of fields: (1)Mechanical manufacturing technology; (2)Information processing, processing, transmission technology; (3)Automatic control technology; (4)Servo drive technology; (5)Technology of the sensor; (6)Software engineering ,etc.. Development trend of a numerical control technologyThe application of numerical control technology has not only brought the revolutionary change to manufacturing industry of the tradition, make the manufacturing industry become the industrialized symbol , and with the constant development of numerical control technology and enlargement of the application, the development of some important trades (IT , automobile , light industry , medical treatment ,etc. ) to the national economy and the people's livelihood of his plays a more and more important role, because the digitization that these trades needed to equip has already been the main trend of modern development. Numerical control technology in the world at present and equipping the development trend to see, there is the following several respect [1- ] in its main research focus.5 A high-speed, high finish machining technology and new trend equippedThe efficiency, quality are subjavanufacturing technology. High-speed, high finish machining technology can raise the efficiency greatly , improve the quality and grade of the products, shorten production cycle and improve the market competitive power. Japan carries the technological research association first to classify it as one of the 5 great modern manufacturing technologies for this, learn (CIRP) to confirm it as the centre in the 21st century and study one of the directions in international production engineering.In the field of car industry, produce one second when beat such as production of 300,000 / vehicle per year, and many variety process it is car that equip key problem that must be solved one of; In the fields of aviation and aerospace industry, spare parts of its processing are mostly the thin wall and thin muscle, rigidity is very bad, the material is aluminium or aluminium alloy, only in a situation that cut the speed and cut strength very small high, could process these muscles, walls. Adopt large-scale whole aluminium alloy method that blank " pay empty " make the wing recently, such large-scale parts as the fuselage ,etc. come to substitute a lot of parts to assemble through numerous rivet , screw and other connection way, make the intensity , rigidity and dependability of the component improved. All these, to processing and equipping the demand which has proposed high-speed, high precise and high flexibility.According to EMO2001 exhibition situation, high-speed machining center is it give speed can reach 80m/min is even high , air transport competent speed can up to 100m/min to be about to enter. A lot of automobile factories in the world at present, including Shanghai General Motors Corporation of our country, have already adopted and substituted and made the lathe up with the production line part that the high-speed machining center makes up. HyperMach lathe of U.S.A. CINCINNATI Companyenters to nearly biggest 60m/min of speed, it is 100m/min to be fast, the acceleration reaches 2g, the rotational speed of the main shaft has already reached 60 000r/min. Processing a thin wall of plane parts, spend 30min only, and same part general at a high speed milling machine process and take 3h, the ordinary milling machine is being processed to need 8h; The speed and acceleration of main shaft of dual main shaft lathes of Germany DMG Company are up to 120000r/mm and 1g.In machining accuracy, the past 10 years, ordinary progression accuse of machining accuracy of lathe bring 5μm up to from 10μm already, accurate grades of machining center from 3~5μm, rise to 1~1.5μm, and ultraprecision machining accuracy is it e nter nanometer grade to begin already (0.01μm).In dependability, MTBF value of the foreign numerical control device has already reached above 6 000h, MTBF value of the servo system reaches above 30000h, demonstrate very high dependability .In order to realize high-speed, high finish machining, if the part of function related to it is electric main shaft, straight line electrical machinery get fast development, the application is expanded further .5.2 Link and process and compound to process the fast development of the lathe in 5 axesAdopt 5 axles to link the processing of the three-dimensional curved surface part, can cut with the best geometry form of the cutter , not only highly polished, but also efficiency improves by a large margin . It is generally acknowledged, the efficiency of an 5 axle gear beds can equal 2 3 axle gear beds, is it wait for to use the cubic nitrogen boron the milling cutter of ultra hard material is milled and pared at a high speed while quenching the hard steel part, 5 axles link and process 3 constant axles to link and process and give play to higher benefit. Because such reasons as complicated that 5 axles link the numerical control system , host computer structure that but go over, it is several times higher that its price links the numerical control lathe than 3 axles , in addition the technological degree of difficulty of programming is relatively great, have restricted the development of 5 axle gear beds.At present because of electric appearance of main shaft, is it realize 5 axle complex main shaft hair structure processed to link greatly simplify to make, it makes degree of difficulty and reducing by a large margin of the cost, the price disparity of the numerical control system shrinks. So promoted 5 axle gear beds of head of complex main shaft and compound to process the development of the lathe (process the lathe including 5).At EMO2001 exhibition, new Japanese 5 of worker machine process lathe adopt complex main shaft hair, can realize the processing of 4 vertical planes and processing of the wanton angle, make 5 times process and 5 axles are processed and can be realized on the same lathe, can also realize the inclined plane and pour the processing of the hole of awls. Germany DMG Company exhibits the DMUVoution series machining center, but put and insert and put processing and 5 axles 5 times to link and process in once, can be controlled by CNC system or CAD/CAM is controlled directly or indirectly.。
- 1、下载文档前请自行甄别文档内容的完整性,平台不提供额外的编辑、内容补充、找答案等附加服务。
- 2、"仅部分预览"的文档,不可在线预览部分如存在完整性等问题,可反馈申请退款(可完整预览的文档不适用该条件!)。
- 3、如文档侵犯您的权益,请联系客服反馈,我们会尽快为您处理(人工客服工作时间:9:00-18:30)。
工业类汉译英论文翻译网站样稿——华译网翻译公司提供中英文翻译版本请注意:对应英文版请见本文件后半部分。
本论文英文译文是年前翻译的,目前我们公司增加了外籍校对环节,而且译者资历要求也提高了,所以目前的翻译水平要远高于这个水平。
发布的文件仅作为语料素材供参考,不能作为英文译文模板等使用。
华译网翻译公司提供专业学术资料、法律资料、商务资料和技术资料翻译服务,本文件我们为某工业公司翻译的净化设备和薄膜液体过滤器文件摘录内容,供参考,欢迎惠顾。
详细价格和译者资质以及论文翻译控制流程请登陆其官方网站/。
中文原文广告语:创新引领发展、品质缔造未来、满意成就市场我们的公司上海市AAAA有限公司是致力于多种形式工业用过滤产品研究、开发、制造和服务的专业公司,是“中国环保产业百强企业”和“上海市高新技术企业”。
公司位于上海市XXXX,占地5万㎡,现有员工280人,年销售额达1亿多元。
公司有高度主动协调的管理团队和完善的生产体系,严格遵照ISO9000的规定运行。
我们坚持不断的技术创新,并建有自己的技术中心,拥有“膨体聚四氟乙烯薄膜”、“回转切换定位喷吹清灰装置”等多项专有和专利技术,生产袋式除尘器、滤筒式除尘器/过滤段、薄膜液体过滤器及PTFE产品系列,已广泛应用于冶金、水泥、机械、化工、电力、垃圾焚烧、烟草、制药等众多行业。
我们有25年的专业经验,在国内处于领先地位。
我们的产品》》》》》工业除尘与净化设备及配件系列1.袋式除尘器2.覆膜滤袋3.滤筒式除尘器/过滤段4.覆膜滤筒》》》》》膨体聚四氟乙烯(ePTFE)微孔膜系列1.工业过滤用覆膜滤料2.卫生医疗用过滤材料另:覆膜滤料(示意)、覆膜滤料(成品)》》》》》100%聚四氟乙烯(PTFE)纤维系列》》》》》薄膜液体过滤器及配件系列1.薄膜液体过滤器2.液体过滤袋、滤芯3.挠性夹管阀另:液体过滤器(外观)、液体过滤器(花板)滤袋、滤芯组合件详见产品资料》》》》》应用行业冶金水泥机械化工电力垃圾焚烧烟草制药等》》》》》应用领域工业除尘、净化和过滤特种面料(消防服、登山服)电池隔膜卫生医疗过滤液体密封等》》》》》应用领域工业除尘、净化和过滤压缩包装物建筑织物工业用缝纫线医疗用牙线等》》》》》应用行业钢铁能源化工电力医药电子等我们的优势》》》》》“领”先技术我们拥有“膨体聚四氟乙烯薄膜”、“回转切换定位喷吹清灰装置”等多项专有和专利技术,拥有多个“国内首创、国际先进”的产品,并在政府专项基金的资助下,继续加快新技术、新产品的开发和推广。
》》》》》“巧”思设计我们不是简单的选型,而是针对客户的具体要求和应用条件提供量体裁衣式的解决方案及全方位的技术服务,包括产品本身及其应用方面的咨询。
》》》》》“环”绕市场贴近客户、满足客户是我们所有工作的基础,每一张订单从开始到完成,客户始终是整个过程的焦点,高度的灵活性和诚信使我们与客户建立起长久的彼此信赖的合作伙伴关系。
》》》》》“保”持品牌我们拥有专业的经验,提供高品质的产品和服务,并充分体现在我们的业绩和信誉中,保证我们在行业中的优势地位。
不管是过去、现在、还是未来,我们都加倍努力,非常严肃地维护公司的声誉,持续不断地发展和完善。
英文译文Slogan:Leading Development through Innovation, Forging Future with Quality,Establishing Market with SatisfactionOur companyShanghai XXXX Environmental Protection Equipment Works Co,. Ltd, is a professional company devoted to research, R&D, manufacturing and service of various industrial filtration products, and is one of the “100 Best Enterprises in Chinese Environmental Protection Industry” and “and is a “Shanghai High-Tech Enterprise”. Located in XXXXi, the company covers a land area of 50,000 square meters and boasts 280 employees at present with an annual sales volume of over RMB 0.1 billion yuan. The company has established a highly initiative and well-coordinated management team and a prefect production system, which is operating in strict conformity with the regulations of ISO9000.We stick to constant technical innovations and has set up a technical center of our own. Moreover, we boast many exclusive and patented techniques, and we produce bag filters, pleated element filter/filtration section, membrane filter and PTFE product series, which have been widely applied in many industries such as metallurgy, cement, machinery, chemical industry, electric power, garbage incineration, tobacco and pharmacy, etc. With 25 years’ professional experience, we have won a leading position nationwide.Our products✧Series industrial dedusting and purification equipment and fittings1. Bag filter2. filter bags laminated with ePTFE membrane3. Pleated element filter4. Pleated Elements✧Series ePTFE microporous membrane1. filter medium laminated with ePTFE membrane in industrial filtration2.filtration material for medical and sanitary uses.In Addition l: filter medium laminated with ePTFE membrane (sketch), filter medium laminated with ePTFE membrane (finished product)✧Series 100% PTFE fiber✧Series membrane liquid filter and fittings1. membrane liquid filter2. Filter bag/cartridge3. Automatic Pinch ValvesIn addition: liquid filter(appearance), liquid filter(tube plate)bag filter and filter assemblySee product materials for details✧Applied Industry :Metallurgical IndustryCement IndustryMechanical IndustryChemical IndustryPower IndustryGarbage IncinerationTobacco IndustryPharmacy✧Applied Area:Industry Dedusting, Purification and FiltrationSpecial Cloth (Fireman Cloth, Mountaineering Suit) Battery Membrane BarrierMedical and Sanitary FiltrationLiquid Sealing and etc.✧Applied Area:Industry Dedusting, Purification and FiltrationCompressed PackingsBuilding FabricSewing Thread for Industry ApplicationDental Floss for Medical Treatment and etc.✧Applied Industy:Iron and Steel IndustryEnergy IndustryChemical IndustryPower IndustryMedicalElectronics and etc.Our Advantages✧Advanced TechnologyWe hold many exclusive and patented techniques, such as ePTFE membrane and, rotary-switching dust remover with the function of locating blowing, and have developed several products which are totally new in domestic and have met international advanced standard. With the support of government’s special research funds, we continue to develop and generalize our new technologies and products in the world.✧Perfect DesignWe do not merely help our clients to select products, but provide customized solution and all-round technical service to them to meet their specific needs and working conditions, including consultation on the products and their application.✧Market OrientedTo know our clients and to satisfy them are the objectives of all our work. And the clients always lie at the focus throughout the whole process of transacting each order. And we have established long-term partnership in which we and our clients trust each other due to high flexibility in business and good faith.✧Build Our BrandWe possess professional experiences and are able to provide high-quality products and service, which have been fully reflected by our outstanding performance and good reputation, and therefore we have got an dominant status in the industry successfully. Regardless of the past, today or the future, we will work harder in future to maintain thecompany’s reputation seriously and devote us to the development of the company with no hesitation.文献来源:华译网翻译公司官方网站/。