西安交大结构优化设计实验报告
结构优化设计大作业(北航)

《结构优化设计》大作业报告实验名称: 拓扑优化计算与分析1、引言大型的复杂结构诸如飞机、汽车中的复杂部件及桥梁等大型工程的设计问题,依靠传统的经验和模拟实验的优化设计方法已难以胜任,拓扑优化方法成为解决该问题的关键手段。
近年来拓扑优化的研究的热点集中在其工程应用上,如: 用拓扑优化方法进行微型柔性机构的设计,车门设计,飞机加强框设计,机翼前缘肋设计,卫星结构设计等。
在其具体的操作实现上有两种方法,一是采用计算机语言编程计算,该方法的优点是能最大限度的控制优化过程,改善优化过程中出现的诸如棋盘格现象等数值不稳定现象,得到较理想的优化结果,其缺点是计算规模过于庞大,计算效率太低;二是借助于商用有限元软件平台。
本文基于matlab软件编程研究了不同边界条件平面薄板结构的在各种受力情况下拓扑优化,给出了几种典型结构的算例,并探讨了在实际优化中优化效果随各参数的变化,有助于初学者初涉拓扑优化的读者对拓扑优化有个基础的认识。
2、拓扑优化研究现状结构拓扑优化是近20年来从结构优化研究中派生出来的新分支,它在计算结构力学中已经被认为是最富挑战性的一类研究工作。
目前有关结构拓扑优化的工程应用研究还很不成熟,在国外处在发展的初期,尤其在国内尚属于起步阶段。
1904 年Michell在桁架理论中首次提出了拓扑优化的概念。
自1964 年Dorn等人提出基结构法,将数值方法引入拓扑优化领域,拓扑优化研究开始活跃。
20 世纪80 年代初,程耿东和N. Olhoff在弹性板的最优厚度分布研究中首次将最优拓扑问题转化为尺寸优化问题,他们开创性的工作引起了众多学者的研究兴趣。
1988年Bendsoe和Kikuchi发表的基于均匀化理论的结构拓扑优化设计,开创了连续体结构拓扑优化设计研究的新局面。
1993年Xie.Y.M和Steven.G.P提出了渐进结构优化法。
1999年Bendsoe和Sigmund证实了变密度法物理意义的存在性。
西安交大本科生科研课题

基于神经网络的新能源光伏发电功率预测方法
刘俊
电气学院
周迪
分数阶复杂动态网络的同步控制与电路实现
司刚全
电气学院
邱凯翔
二维码身份证的设计和校验
杨旭
电气学院
江崇熙
基于多目标的分时多模式智能电梯模拟
司刚全
电气学院
江申
工厂管控一体化系统
胡飞虎
电气学院
黎亦凡
学生体育锻炼记录系统
丁文
电气学院
刘军宇
电气设备外绝缘放电紫外图像的分析及处理
田雅芬
基于热电制冷原理的便携式冷热双用箱
鱼剑琳
能动学院
连康
弹簧低温性能试验冷包初步设计
吴伟烽
能动学院
贺振武
金属材料干摩擦阻尼特性实验研究
张荻
能动学院
孙伟强
基于PLC的3G远程辐射监测系统方案设计与实施
胡华四
能动学院
黄琰
关于包装材料对陶瓷制品保护效果的研究
刘睫
能动学院
薛佩曈
流向微槽减阻的实验和数值研究
王晶
电信学院
傅思丹
量子成像与超材料的前沿探究
徐卓
电信学院
郑亚男
基于IPMAP的图形化数据质量管理设计系统
韩博
电信学院
彭勇
基于云的移动存储设备防丢失应用
张爱民
电信学院
吴治诚
基于物联网的环境智能系统
桂小林
电信学院
何超
基于移动智能终端的个人自我管理系统
乔亚男
电信学院
崔轶群
基于激光传感器的智能车系统设计
刘小勇
巫英伟
能动学院
史宝春
太阳能热发电蓄热系统的设计及蓄热材料的适应性选择
结构优化论证报告
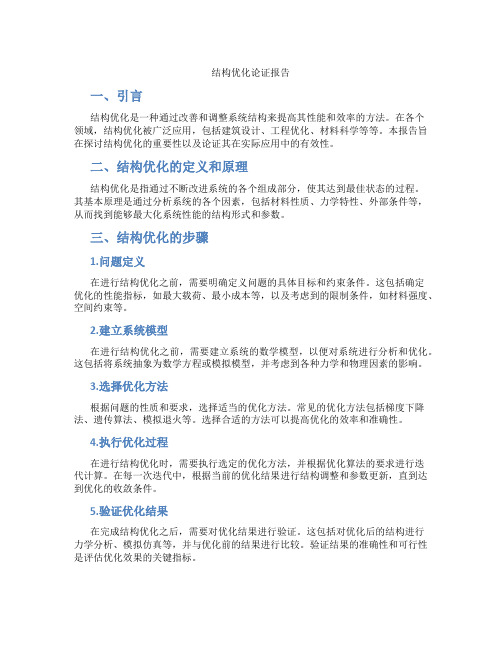
结构优化论证报告一、引言结构优化是一种通过改善和调整系统结构来提高其性能和效率的方法。
在各个领域,结构优化被广泛应用,包括建筑设计、工程优化、材料科学等等。
本报告旨在探讨结构优化的重要性以及论证其在实际应用中的有效性。
二、结构优化的定义和原理结构优化是指通过不断改进系统的各个组成部分,使其达到最佳状态的过程。
其基本原理是通过分析系统的各个因素,包括材料性质、力学特性、外部条件等,从而找到能够最大化系统性能的结构形式和参数。
三、结构优化的步骤1.问题定义在进行结构优化之前,需要明确定义问题的具体目标和约束条件。
这包括确定优化的性能指标,如最大载荷、最小成本等,以及考虑到的限制条件,如材料强度、空间约束等。
2.建立系统模型在进行结构优化之前,需要建立系统的数学模型,以便对系统进行分析和优化。
这包括将系统抽象为数学方程或模拟模型,并考虑到各种力学和物理因素的影响。
3.选择优化方法根据问题的性质和要求,选择适当的优化方法。
常见的优化方法包括梯度下降法、遗传算法、模拟退火等。
选择合适的方法可以提高优化的效率和准确性。
4.执行优化过程在进行结构优化时,需要执行选定的优化方法,并根据优化算法的要求进行迭代计算。
在每一次迭代中,根据当前的优化结果进行结构调整和参数更新,直到达到优化的收敛条件。
5.验证优化结果在完成结构优化之后,需要对优化结果进行验证。
这包括对优化后的结构进行力学分析、模拟仿真等,并与优化前的结果进行比较。
验证结果的准确性和可行性是评估优化效果的关键指标。
四、结构优化的应用案例1.建筑设计在建筑设计中,结构优化可以用于改善建筑物的强度和稳定性。
通过优化建筑结构和材料的选择,可以提高建筑物的抗震性能、降低成本,并实现更灵活的设计。
2.工程优化在工程领域,结构优化可以用于优化工程结构的形状和尺寸,以提高其承载能力和稳定性。
例如,在桥梁设计中,通过结构优化可以减少材料的使用量、提高桥梁的刚度和强度。
3.材料科学在材料科学中,结构优化可以用于改善材料的力学性能和物理特性。
优化设计实验报告

优化设计实验报告优化设计实验报告引言在当今科技高速发展的时代,优化设计成为了一项重要的研究领域。
通过优化设计,可以提高产品的性能和质量,降低生产成本,提高效率,满足不断增长的市场需求。
本实验报告旨在介绍优化设计的基本概念和方法,并通过一个具体案例来展示其在实际工程中的应用。
一、优化设计的基本概念优化设计是指通过系统地改进和调整设计参数,以达到最佳的设计目标的过程。
它是一种综合性的工程方法,涉及到多个学科领域,如数学、工程学、经济学等。
优化设计的基本概念包括目标函数、设计变量、约束条件等。
目标函数是指在优化设计中需要优化的设计指标,如最小化成本、最大化效率等。
设计变量是指可以调整的设计参数,如尺寸、材料、工艺等。
约束条件是指在设计过程中需要满足的限制条件,如材料强度、工艺要求等。
通过合理地选择目标函数、设计变量和约束条件,可以实现优化设计的目标。
二、优化设计的方法优化设计的方法有很多种,常见的有数学优化方法、试验设计方法和仿真优化方法等。
数学优化方法是利用数学模型和计算机算法来寻找最优解的方法,如线性规划、非线性规划等。
试验设计方法是通过设计一系列实验来寻找最优解的方法,如响应面法、Taguchi方法等。
仿真优化方法是通过建立数值模型,并通过计算机仿真来进行优化设计的方法,如有限元分析、计算流体力学等。
三、实际案例:汽车车身结构优化设计以汽车车身结构优化设计为例,介绍优化设计在实际工程中的应用。
汽车车身结构的优化设计旨在提高车身的刚度和强度,减少车身的重量和空气阻力,以提高汽车的性能和燃油经济性。
在汽车车身结构优化设计中,目标函数可以设定为最小化车身重量,设计变量可以包括材料的选择、截面的尺寸等,约束条件可以包括材料的强度、刚度要求等。
通过数学优化方法,可以建立数学模型,利用计算机算法来搜索最优解。
通过试验设计方法,可以设计一系列试验,通过响应面法来寻找最优解。
通过仿真优化方法,可以建立数值模型,通过有限元分析来进行优化设计。
优化实验设计实验报告

优化实验设计实验报告优化实验设计实验报告在科学研究中,实验设计是非常重要的一环。
一个合理的实验设计可以确保实验结果的准确性和可靠性,并且可以减少实验过程中的误差。
本文将讨论如何优化实验设计,以便获得更好的实验结果。
一、确定实验目标和假设在进行实验设计之前,我们首先需要明确实验的目标和假设。
实验目标应该明确而具体,假设应该有明确的预测。
这样可以帮助我们在实验设计中更好地选择变量和控制条件。
二、选择适当的实验方法在实验设计中,我们需要选择适当的实验方法。
不同的实验方法适用于不同的实验目的。
例如,如果我们想研究两个变量之间的关系,可以选择相关性实验设计;如果我们想比较不同处理组的效果,可以选择对比实验设计。
选择适当的实验方法可以提高实验的可靠性和有效性。
三、合理选择实验样本在实验设计中,样本的选择非常重要。
样本应该具有代表性,能够反映整个群体的特征。
同时,样本的大小也需要合理确定。
如果样本过小,可能无法得到可靠的统计结果;如果样本过大,可能会浪费资源。
因此,我们需要根据实验目的和预期效果来确定合适的样本大小。
四、控制实验条件在实验设计中,控制实验条件是非常重要的。
我们需要尽量控制其他可能影响实验结果的因素,以减少误差的干扰。
例如,我们可以使用随机分组的方法来消除处理组之间的差异;我们可以使用盲法来消除实验者主观因素的影响。
通过控制实验条件,可以提高实验结果的准确性和可靠性。
五、合理选择实验变量在实验设计中,选择合适的实验变量也是非常重要的。
实验变量应该具有一定的独立性,能够反映实验目标和假设。
同时,我们需要考虑实验变量的操作性和可测性。
如果实验变量过于复杂或难以操作,可能会影响实验的可行性和有效性。
因此,我们需要在实验设计中合理选择实验变量。
六、数据分析和结果解释在实验设计中,数据分析和结果解释是非常重要的。
我们需要使用适当的统计方法对实验数据进行分析,以得出可靠的结论。
同时,我们需要解释实验结果,并与实验目标和假设进行比较。
优化实验设计实验报告
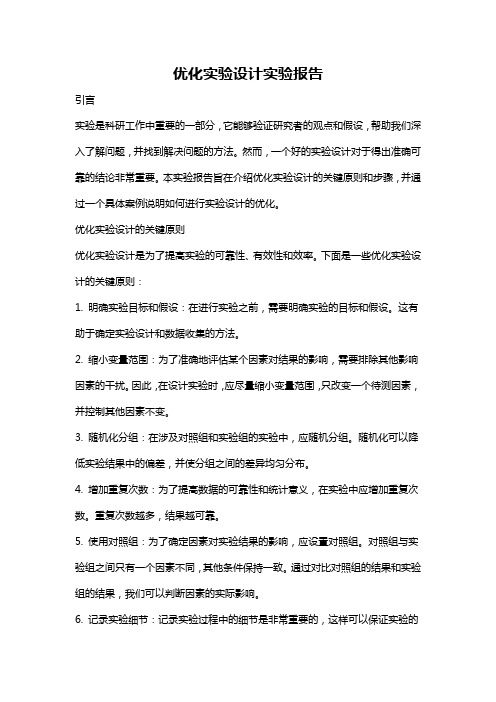
优化实验设计实验报告引言实验是科研工作中重要的一部分,它能够验证研究者的观点和假设,帮助我们深入了解问题,并找到解决问题的方法。
然而,一个好的实验设计对于得出准确可靠的结论非常重要。
本实验报告旨在介绍优化实验设计的关键原则和步骤,并通过一个具体案例说明如何进行实验设计的优化。
优化实验设计的关键原则优化实验设计是为了提高实验的可靠性、有效性和效率。
下面是一些优化实验设计的关键原则:1. 明确实验目标和假设:在进行实验之前,需要明确实验的目标和假设。
这有助于确定实验设计和数据收集的方法。
2. 缩小变量范围:为了准确地评估某个因素对结果的影响,需要排除其他影响因素的干扰。
因此,在设计实验时,应尽量缩小变量范围,只改变一个待测因素,并控制其他因素不变。
3. 随机化分组:在涉及对照组和实验组的实验中,应随机分组。
随机化可以降低实验结果中的偏差,并使分组之间的差异均匀分布。
4. 增加重复次数:为了提高数据的可靠性和统计意义,在实验中应增加重复次数。
重复次数越多,结果越可靠。
5. 使用对照组:为了确定因素对实验结果的影响,应设置对照组。
对照组与实验组之间只有一个因素不同,其他条件保持一致。
通过对比对照组的结果和实验组的结果,我们可以判断因素的实际影响。
6. 记录实验细节:记录实验过程中的细节是非常重要的,这样可以保证实验的可重复性,并有助于后续的数据分析和结论推导。
优化实验设计的步骤下面,我们将以一个实际案例为例,介绍优化实验设计的步骤。
案例背景假设我们要研究不同种类肥料对小麦生长的影响,现在有四种不同的肥料(A、B、C、D),我们想知道使用哪一种肥料可以获得最好的效果。
步骤一:明确实验目标和假设实验的目标是找到最佳肥料对小麦生长的影响。
在这个案例中,假设我们的研究假设是“不同种类肥料对小麦生长有差异”。
步骤二:设计实验组和对照组根据我们的假设,我们需要设计实验组和对照组。
在这个案例中,我们将使用四个实验组分别使用A、B、C、D 四种肥料,同时设置一个对照组不使用肥料。
机构优化设计综合实验报告 摆动导杆机构
机构优化设计综合实验报告摆动导杆机构一、实验目的1. 掌握机构优化设计流程及方法。
2. 熟悉MATLAB/Simulink等工具的简单使用。
3. 熟悉自动化设计软件ADAMS的使用方法。
4. 熟悉建模、仿真、分析和优化机构的基本思路和操作方法。
二、实验内容1. 摆动导杆机构的静态分析。
2. 建立摆动导杆机构的动力学模型。
3. 利用ADAMS进行动力学仿真。
4. 对机构进行优化设计,得到最优参数。
三、实验步骤1. 绘制摆动导杆机构的CAD图。
2. 利用SolidWorks进行三维建模。
3. 利用MATLAB编写静态分析程序,计算机构受力情况。
4. 建立机构的动力学模型,并将其导入ADAMS中。
5. 进行动力学仿真,得到机构运动情况。
6. 对机构进行优化设计,对比不同参数下的机构运动性能。
7. 分析优化结果及改进方向。
四、实验原理摆动导杆机构是一种广泛应用于工业和机械设计领域的机构。
该机构由固定主架、摆杆、导杆和从动架等组成,可以将旋转运动转化为直线运动。
同时,该机构结构简单、工作可靠、制造成本低、使用寿命长,因此得到广泛应用。
在进行机构优化设计前,需要对机构进行静态分析。
通过计算机程序模拟机构在不同外载荷作用下的受力情况,可以得到机构的力学特性,为优化设计提供数据支持。
在建立机构的动力学模型时,需考虑机构的受力情况、牵引质量以及摩擦等因素。
将机构的动力学模型导入ADAMS中,进行动力学仿真,可以得到机构的运动情况。
同时,可利用ADAMS进行优化设计,通过对比不同参数下的机构运动性能,得出最优解。
五、实验结果及分析经过静态分析程序计算,可以得到机构在不同外载荷下的受力情况。
例如,在机构受到10N的外载荷时,导杆处受到的最大压力为300N,摆杆的最大弯曲角度为5度。
这些数据可以为优化设计提供数据支持。
在进行动力学仿真时,可得到机构在不同的牵引质量下的运动情况。
例如,在牵引质量为100G的情况下,机构的运动速度最大,机构的平均运动速度为0.5m/s。
计算机系统结构实验报告 西安交通大学
《计算机系统结构课内实验》实验报告班级:计算机15班姓名:高君宇学号:2110505112日期:2014.5.7动态分支预测实验一、实验目的及要求1. 了解掌握动态分支与推断执行技术对流水线性能的改进效果2. 了解动态分支预测的基本技术;3. 了解推断执行的基本过程;4. 比较各种分支预测技术的性能。
二、实验环境Linux、SimpleScalar Tool Set、SPEC 测试程序三、实验内容利用SimpleScalar仿真器中的分支预测仿真程序sim-pred运行所提供的三个benchmark程序,分别采用五种不同的分支预测方法,即bimod方式,two-level adaptive方式,always taken方式,always not taken方式,comb方式,并对前两种分别使用下表中两种参数配置;分析仿真器输出的关于分支预测的统计参数集,填写表格,并对各仿真器的能力给出相应说明。
命令格式为: ./sim-bpred {-option} executable_benchmark –argument 对于三种动态方法,分别说明如下:bimod是最普通的,即采用一个2bit宽的分支方向预测表,按分支地址查找,2bit分支预测器的判断和更新与课本上的一致。
这种方式只有一个参数,就是分支预测表的长度。
2-level要复杂一些,它采用两级表格式,第一级是分支历史表,存放各组分支历史寄存器的值,第二级是全局/局部分支模式表,(全局或局部应是由表长相对于分支历史寄存器的长决定),它存放各分支历史模式的2bit预测器。
在判断时用当前分支指令对应的历史寄存器值去索引二级表得到相应预测器值。
更新时,把当前分支的方向左移入历史寄存器,并对使用过的2bit预测器作更新。
它有四个参数,前三个是一级表长度,二级表长度,历史寄存器宽度,最后一个是异或标志。
如果为1,则将历史寄存器的值与当前分支指令地址异或,用其结果再去索引二级模式表。
结构优化设计大作业(北航)
《结构优化设计》大作业报告实验名称: 拓扑优化计算与分析1、引言大型的复杂结构诸如飞机、汽车中的复杂部件及桥梁等大型工程的设计问题,依靠传统的经验和模拟实验的优化设计方法已难以胜任,拓扑优化方法成为解决该问题的关键手段。
近年来拓扑优化的研究的热点集中在其工程应用上,如: 用拓扑优化方法进行微型柔性机构的设计,车门设计,飞机加强框设计,机翼前缘肋设计,卫星结构设计等。
在其具体的操作实现上有两种方法,一是采用计算机语言编程计算,该方法的优点是能最大限度的控制优化过程,改善优化过程中出现的诸如棋盘格现象等数值不稳定现象,得到较理想的优化结果,其缺点是计算规模过于庞大,计算效率太低;二是借助于商用有限元软件平台。
本文基于matlab 软件编程研究了不同边界条件平面薄板结构的在各种受力情况下拓扑优化,给出了几种典型结构的算例,并探讨了在实际优化中优化效果随各参数的变化,有助于初学者初涉拓扑优化的读者对拓扑优化有个基础的认识。
2、拓扑优化研究现状结构拓扑优化是近20年来从结构优化研究中派生出来的新分支,它在计算结构力学中已经被认为是最富挑战性的一类研究工作。
目前有关结构拓扑优化的工程应用研究还很不成熟,在国外处在发展的初期,尤其在国内尚属于起步阶段。
1904 年Michell在桁架理论中首次提出了拓扑优化的概念。
自1964 年Dorn等人提出基结构法,将数值方法引入拓扑优化领域,拓扑优化研究开始活跃。
20 世纪80 年代初,程耿东和N. Olhoff在弹性板的最优厚度分布研究中首次将最优拓扑问题转化为尺寸优化问题,他们开创性的工作引起了众多学者的研究兴趣。
1988年Bendsoe和Kikuchi发表的基于均匀化理论的结构拓扑优化设计,开创了连续体结构拓扑优化设计研究的新局面。
1993年Xie.Y.M和Steven.G.P 提出了渐进结构优化法。
1999年Bendsoe和Sigmund证实了变密度法物理意义的存在性。
结构设计优化及体会总结
结构设计优化及体会总结结构设计是指利用工程原理和方法,通过对建筑物或其他工程的组成部分进行合理布置和连接,达到满足使用功能和保证安全性的目的。
结构设计优化就是对原有的结构设计进行改进和提升,使其更加符合实际需求、节约材料、提高安全性和经济性等方面的要求。
在进行结构设计优化的过程中,首先需要明确项目的功能要求和技术指标,了解使用条件、荷载情况和周围环境因素等。
然后通过对结构系统、构件属性、构造方式、连接形式等方面的优化,实现对原有结构设计的改进。
在结构系统的优化中,可以通过选择不同的结构体系,如框架结构、桁架结构、壳体结构等,来满足不同项目的要求。
同时,还可以根据结构的形象要求、力学性能要求和施工方便性要求等因素,进行结构系统的调整和优化。
在构件属性的优化中,可以利用不同材料和不同截面形式来满足结构的功能要求。
比如,在抗震设计优化中,可以通过使用高强度钢筋和混凝土预应力技术,提高结构的抗震性能;在跨度较大的横梁设计中,可以采用预应力混凝土构件来减小自重和增加刚度。
在构造方式的优化中,可以考虑采用预制技术、模数化技术等,将构件的制作和安装过程进行优化,减少现场施工时间和使用材料的浪费。
在连接形式的优化中,可以选择合适的连接方式,如焊接、螺栓连接等,来使结构的受力传递更加均匀和可靠。
结构设计优化的过程中,需要综合考虑经济性、安全性、可行性等多个方面的因素。
在经济性方面,需要对设计进行评估和比较,选择最佳方案;在安全性方面,需要进行结构的抗震、抗风、抗震动、抗火等方面的分析和检验;在可行性方面,需要考虑施工备料的可行性、施工过程的可操作性等。
在进行结构设计优化的实践中,我深刻认识到结构设计的重要性和复杂性。
优化设计并不是简单的调整和修改,而是需要综合考虑多个因素,进行合理的权衡和取舍。
在结构设计优化的过程中,更需要注重团队合作和交流。
因为涉及到多个专业领域的知识和技术,需要与结构、施工、材料等相关专业的人员进行密切的合作和沟通,才能在设计过程中充分发挥各自的优势,实现优化效果。
- 1、下载文档前请自行甄别文档内容的完整性,平台不提供额外的编辑、内容补充、找答案等附加服务。
- 2、"仅部分预览"的文档,不可在线预览部分如存在完整性等问题,可反馈申请退款(可完整预览的文档不适用该条件!)。
- 3、如文档侵犯您的权益,请联系客服反馈,我们会尽快为您处理(人工客服工作时间:9:00-18:30)。
结构优化设计实验报告1.实验背景结构优化能在保证安全使用的前提下保证工程结构减重,提高工程的经济效益,这也是课程练习的有效补充。
2.实验课题问题1:考察最速下降法、拟牛顿法(DFP,BFGS)、单纯形法的性能,使用matlab中的fminunc 和fminsearch 函数。
●目标函数1: 目标函数,多元二次函数其中,,,,初值运行结果:最小值迭代次数最速下降法-1.864 0.455 -0.046 5.750 20牛顿DFP法-1.864 0.455 -0.046 5.750 9牛顿BFGS法-1.864 0.455 -0.046 5.750 7单纯性法-2.010 0.503 0.003 5.750 57●目标函数2运行结果:最小值迭代次数2 最速下降法-3.596 -3.800 1.4011.3牛顿DFP法-0.329 -0.380 1.869 0.446 7牛顿BFGS法-0.329 -0.380 1.869 0.446 7单纯性法-55.85 -137.8 218.2 0 43结果分析:从上述结果可以看出牛顿法具有较好的稳定性,最速下降法和单纯形法在求解超越函数时稳定性不佳,最速下降法迭代次数最少,单纯形法迭代次数最多。
问题2:使用matlab中的linprog和quadprog函数验证作业的正确性。
用单纯形法求解线性规划问题的最优解●目标函数16,运行结果:单纯形法的解析解用两相法求解线性规划问题的最优解●目标函数2,运行结果:单纯形法的解析解求解二次规划问题的最优解●目标函数2,,运行结果:问题3:用Matlab命令函数fmincon求解非线性约束规划问题●目标函数1运行结果:迭代次数:8●目标函数2运行结果:迭代次数:16问题4:用Matlab命令函数fmincon求解人字形钢管架优化问题。
已知:2F = 600kN,2B = 6 m,T=5 mm,钢管材料E = 210 GPa,密度=,许用应力[ ]=160MPa,根据工艺要求2m ≤ h≤6m ,20mm ≤ D≤300mm 。
求h , D 使总重量W为最小。
求目标函数1运行结果:迭代次数:8问题5:修改满应力程序opt4_1.m和齿形法程序opt4_2.m,自行设计一个超静定桁架结构,并对其进行优化。
要求:(1)设计变量数目不小于2;(2)给出应力的解析表达式;(3)建立以重量最小为目标函数、应力为约束的优化模型。
分别用满应立法和齿轮法求解图2超静定结构,已知材料完全相同,,σ,=σ,1500=,2000满应力法和齿轮法运行结果:附录目标函数1的代码:●function f=objfun1_2(x)●f=exp(5*(x(1))+5*(x(2)))*(3*(x(1))^2+4*(x(2))^2+3*(x(3))^2+...● 4*x(1)*x(2)+2*x(2)*x(3)+5);●●x0=[-1 1 2];●options1=optimset('HessUpdate','bfgs','LineSearchType','quadcubic');●[x,fval,exitflag,output]=fminunc('objfun1_1',x0 ,options1)●●options2=optimset('HessUpdate','dfp','LineSearchType','quadcubic');●[x,fval,exitflag,output]=fminunc('objfun1_1', x0,options2)●●options3=optimset('HessUpdate','steepdesc');●[x,fval,exitflag,output]=fminunc('objfun1_1', x0,options3)●●[x,fval,exitflag,output]=fminsearch('objfun1_1', x0)目标函数2的代码●function f=objfun1_2(x)●f=exp(5*(x(1))+5*(x(2)))*(3*(x(1))^2+4*(x(2))^2+3*(x(3))^2+...● 4*x(1)*x(2)+2*x(2)*x(3)+5);●●x0=[1 1 2];●options3=optimset('HessUpdate','steepdesc');●[x,fval,exitflag,output]=fminunc('objfun1_2', x0,options3)●●options2=optimset('HessUpdate','dfp','LineSearchType','quadcubic');●[x,fval,exitflag,output]=fminunc('objfun1_2', x0,options2)●●options1=optimset('HessUpdate','bfgs','LineSearchType','quadcubic');●[x,fval,exitflag,output]=fminunc('objfun1_2',x0 ,options1)●[x,fval,exitflag,output]=fminsearch('objfun1_2', x0)问题2目标函数1的代码●x0=[0 0]';● c=[-2 -6]';● A=[-1 1; 2 1];● b=[1 2]';● lb=[0 0]';● options = optimset('LargeScale', 'off', 'Simplex', 'on')● [x,fval,exitflag,output] =linprog(c,A,b,[],[],lb ,[],x0,options)目标函数2的代码●x0=[0 0]';●c=[3 4]';●A=[-5 -4; 3 5;5 4];●b=[-100 150 200]';●lb=[0 0]';●options = optimset('LargeScale', 'off', 'Simplex', 'on')●[x,fval,exitflag,output] =linprog(c,A,b,[],[],lb ,[],x0,options)目标函数3的代码●H=[6 2; 2 2];●c= [-30;-14];●A=[1 1;2 -1; 0 1];●b=[3; 4; 2];●lb=[0; 0];●%有效集法(active-set)●[x,fval,exitflag,output ,lambda] =quadprog (H,c,A,b,[],[],lb)●问题3目标函数1●●function opt3_1●x0=[-1 1]●options=optimset('LargeScale', 'off');●[x,fval,exitflag,output]=fmincon('objfun3_1',x0,[],[],[],[],[],[],'confun3_1',options)●%目标函数●function f=objfun3_1(x)●f=(x(1))^4+(x(2))^4-14*(x(1))^2-38*(x(2))^2-24*x(1)+120*x(2);●%约束函数●function [c,ceq]=confun3_1(x)●%非线性不等式约束函数●c=[ x(1)^2+x(2)^2-18 ; x(1)-x(2)-5 ];●%非线性等式约束函数●ceq=[];目标函数2●function opt3_2●clc●x0=[1 1 1 1 1 1 1];●lb=[0;0;0;0;0;0;0];●options=optimset('LargeScale', 'off');●[x,fval,exitflag,output]=fmincon('objfun3_2',x0,[],[],[],[],lb,[],'confun3_2',options)●%目标函数●function f=objfun3_2(x)●e=2.7183;●f=-5*x(1)-5*x(2)-4*x(3)-6*x(4)-x(1)*x(3)-5*x(5)/(1+x(5))-8*x(6)/(1+x(6))...● -10*(1-2*e^(-x(7)))+2*e^(-x(7));●%约束函数●function [c,ceq]=confun3_2(x)●%非线性不等式约束函数●c=[ x(1)+x(2)+x(3)+x(4)-5 ;●x(1)+x(2)+x(3)+x(4)+x(5)+x(6)+x(7)-10;● x(1)+x(3)+x(5)+(5)^2-(x(7))^2-5];●非线性等式约束函数●ceq=[2*x(4)+x(5)+0.8*x(6)+x(7)-5;(x(2))^2+(x(3))^2+(x(5))^2+(x(6))^2-5];问题4●function opt4_1●clc●x0=[4 0.2];●lb=[2;0.02];●ub=[6;0.3];●options=optimset('LargeScale', 'off');●[x,fval,exitflag,output]=fmincon('objfun4_1',x0,[],[],[],[],lb,ub,'confun4_1',options)●●%目标函数●function f=objfun4_1(x)●f=245*x(2)*sqrt(9+(x(1))^2);●●%约束函数●function [c,ceq]=confun4_1(x)●%非线性不等式约束●c=[300*sqrt(9+(x(1))^2)/(15.71*x(1)*x(2))-160;● 300*sqrt(9+(x(1))^2)/(15.71*x(1)*x(2))-...● (259077.12*((x(2))^2+0.000025))/(9+(x(1))^2)];●%线性等式约束●ceq=[];问题5●function [sr]=stressratio(x,pb)●% 三杆超静定问题——应力计算●% 计算应力比●switch pb●case 1●% 两个工况● stress=[3000/x(1);● 3000/x(3);●2000*sqrt(2)*x(1)*x(3)/(x(1)*((x(1)*x(2)+x(2)*x(3)+sqrt(2)*x(3)*x(1))));●2000*(x(1)+x(3))/(sqrt(2)*(x(1)*x(3)+x(2)*x(3)+x(1)*x(2)));●2000*sqrt(2)*x(1)*x(3)/(x(3)*((x(1)*x(2)+x(2)*x(3)+sqrt(2)*x(3)*x(1))));]● astress=[ 2000;1500;2000;2000;2000];● sr=stress./astress;●End●function [w]=weight(x)●%目标函数●w=10*(sqrt(2)*x(1)+x(2)+sqrt(2)*x(3));●function [ksi]=getksi(sr,pb)●% 三杆超静定问题●%计算迭代算子●switch pb●case 1●% 两个工况● ksi=[max([sr(1) sr(3)]);sr(4);max([sr(2) sr(5)])];●end●function opt4_1●% 满应力法●clc●beta=1.0;●x0=[1.0;1.0;1.0];●miter=300;●pb=1●iter=0●while iter<miter● [sr]=stressratio(x0,pb)● [ksi]=getksi(sr,pb)● w=weight(x0)● x1=x0.*ksi.^beta● xn=norm(x1-x0);●if iter>1 & xn<1.0e-5●break;●end● x0=x1;● iter=iter+1●end●sr=stressratio(x1,pb);●%齿轮形法●function opt4_2●clc●beta=1.0; %松弛因子●alpha=0.8; %满应力步长因子●x0=[1.0;1.0;1.0]; %初值●w0=1.0e10;●miter=100; %对大迭代次数●pb=1 %问题1●iter=0●while iter<miter● [sr]=stressratio(x0,pb)● [ksi]=getksi(sr,pb)● eta=max(ksi)●%射步法● x0=x0*eta;● sr=sr/eta;● [ksi1]=getksi(sr,pb)● w=weight(x0)● wtol=abs(w-w0);●if iter>1 & (w>w0 | wtol<=1.0e-5)●break;●end●%忙应力步● x1=alpha*x0.*ksi1.^beta+(1.0-alpha)*x0● x0=x1;● w0=w;● iter=iter+1●end●sr=stressratio(x1,pb);11。