钻孔工艺精度标准
公制、英制、美制、各种螺纹钻孔标准

公 制 细螺纹
规格 M1.0x0.2 M1.1x0.2 M1.2x0.2 M1.4x0.2 M1.6x0.2 M1.7x0.2 M1.8x0.2 M2.0x0.25 M2.2x0.25 M2.3x0.25 M2.5x0.35 M2.6x0.35 M3.0x0.35 M3.5x0.35 M4.0x0.5 M4.5x0.5 M5.0x0.5 M5.5x0.5 M6.0x0.75 M6.0x0.5 M7.0x0.75 M7.0x0.5 M8.0x1.0 M8.0x0.75 M8.0x0.5 M9.0x1.0 M9.0x0.75 M10x1.25 M10x1.0 M10x0.75 M10x0.5 M11x1.0 M11x0.75 M12x1.5 M12x1.25 M12x1.0 M12x0.5 M14x1.5 M14x1.0 M15x1.5 M15x1.0 M16x1.5 标准径 0.80 0.90 1.00 1.20 1.40 1.45 1.60 1.75 1.95 2.05 2.20 2.20 2.70 3.20 3.50 4.00 4.50 5.00 5.30 5.50 6.30 6.50 7.00 7.30 7.50 8.00 8.30 8.80 9.00 9.30 9.50 10.00 10.30 10.50 10.80 11.00 11.50 12.50 13.00 13.50 14.00 14.50 2级牙钻孔径 最大 0.821 0.921 1.021 1.221 1.421 1.500 1.621 1.785 1.985 2.061 2.221 2.246 2.721 3.221 3.599 4.099 4.599 5.099 5.378 5.550 6.378 6.550 7.153 7.378 7.520 8.153 8.378 8.912 9.153 9.378 9.520 10.153 10.378 10.676 10.912 11.153 11.520 12.676 13.153 13.676 14.153 14.676 最小 0.783 0.883 0.983 1.183 1.383 1.460 1.583 1.729 1.929 2.001 2.121 2.186 2.621 3.121 3.459 3.959 4.459 4.959 5.188 5.400 6.188 6.400 6.917 7.188 7.400 7.917 8.188 8.647 8.917 9.188 9.400 9.917 10.188 10.376 10.647 10.917 11.400 12.376 12.917 13.376 13.917 14.376 规格
孔加工技术

攻螺纹和套螺纹
用丝锥来加工内螺纹的操作称为攻螺纹。用板牙加工外螺纹 的方法称为套扣。攻螺纹和套螺纹可以在钻床上也可以在车床上 进行。但单件小批生产主要用手工操作。
在工件上加工一个直径为ф20H9 的圆孔,要求孔的 加工质量达到 IT7 、表面粗糙度 Ra0.8 。试将加工工艺列 于下表。 加工顺序及方法
在钻床上,钻削的主运动是刀具的旋转运动,进给运 动是刀具的轴向进给。
除钻孔外,钻床还可用于扩孔、铰孔、孔口加工和螺纹加工等。
钻
床
常用的钻床有台式钻床、立式钻床和摇臂钻床。它们 的共同特点是:工件固定在工作台上,刀具安装在主轴 上,刀具一边旋转一边做轴向移动。
进给手柄 皮带塔轮
一、台式钻床 台式钻床是一种 安装在台桌上使用 的小型钻床,一般 用于加工小型零件 上直径不超过12mm 的小孔
二、立式钻床
立式钻床的规格 用最大钻孔直径 来表示, 常用的有25mm、35mm、40mm、 50mm等。 特点 刚性好、功率大,可以采用较 大的 切削用量,可以自动走刀,生产 率较高, 加工精度也较高。 由于工作台尺寸不大并且不能在水 平面内移动,必要时只能手工移动工 件,因此立式钻床仅用于加工中小型 工件上的孔。
2、麻花钻Drilling operation and twist drill
2、麻花钻 twist drill :直柄麻花钻(φ0.5~φ20)、 锥柄麻花钻(φ8~φ80) 麻花钻的几何角度主要有螺旋角、顶角、前角、后角和横 刃斜角。 : 前角γ0为正交平面内前刀面与基面的夹角,由于钻头的 前刀面为螺旋面,故越靠近中心,前角越小,横刃为负前 角。 侧后角α为轴向圆柱剖面内后刀面与切削平面的夹角 。 故越靠近中心,后角越大。 顶角2φ两主切削刃在中心截面上投影的夹角。标准钻头 顶角为118°。 横刃斜角Ψ 主切削刃与横刃在钻头端面上投影的夹角。 螺旋角β 最外缘螺旋线切线与轴线的夹角
5.2 孔的常规加工方法
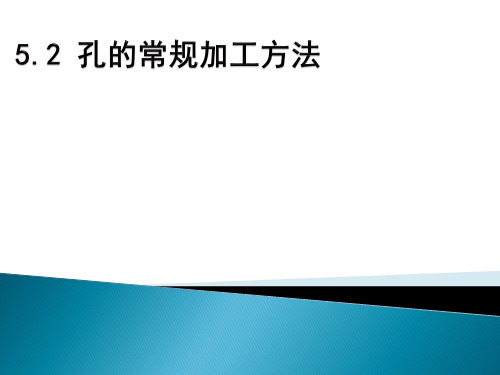
手用铰刀
可调节手用铰刀
手用1:50 锥度铰刀
铰刀的类型
1) 铰削余量
粗铰余量为0.10mm~0.35 mm; 精铰余量为0.04mm~0.06mm。
2) 切削速度和进给量
铰削速度为 1.5m/min ~ 5m/min; 铰削钢件时,进给量为 0.3mm/r ~ 2mm/r; 铰削铸铁件时,进给量为 0.5mm/r ~ 3mm/r。
圆柱形沉头孔 锥形沉头孔 凸台端面
锪孔
hD
rn=0.008-0.018mm
hD
hD=0.01-0.03mm
铰削过程不完全是 一个切削过程,而是包 括切削、刮削、挤压、 熨平和摩擦等效应的一 个综合作用过程。
手铰刀结构
直柄机用铰刀 锥柄机用铰刀 硬质合金锥柄机用铰刀 直柄莫氏圆锥铰刀 套式机用铰刀
1) 铰刀分为三个精度等级,分别用于铰削H7、H8、H9 精度的孔。
2) 铰刀大都留有研磨余量,待用户用铸铁套筒或铜套 筒自行研磨。 3) 对于高精度孔,在精铰前应经过扩孔、粗铰、粗拉 或粗镗等工序。 4) 铰削时最好是工件旋转,铰刀只作进给运动;铰刀 最好采用浮动装夹。
5) 切削液在铰削时起着十分重要的作用。
珩磨头结构
珩磨原理与珩磨头的结构 1-引导杆 2-接头 3、8-锥体 4、6-平板条5-弹簧 7-油石9-支架10-珩头 体11-固定螺杆
(1)珩磨尺寸精度可达IT6; (2)圆度、圆柱度可达0.003 mm~0.005 mm; (3)表面粗糙度的值一般为Ra 0.63μm~Ra 0.04μm, 有时甚至可达到Ra0.02μm~Ra0.01μm的镜面; (4)不能用珩磨加工来纠正孔的位置误差 ; (5)珩磨时因磨头往复速度较高,参加切削的磨粒多 ,故生产率较高; (6)珩磨可加工铸铁、淬硬或不淬硬钢件。
浅谈保证钻孔位置精度的几点要求
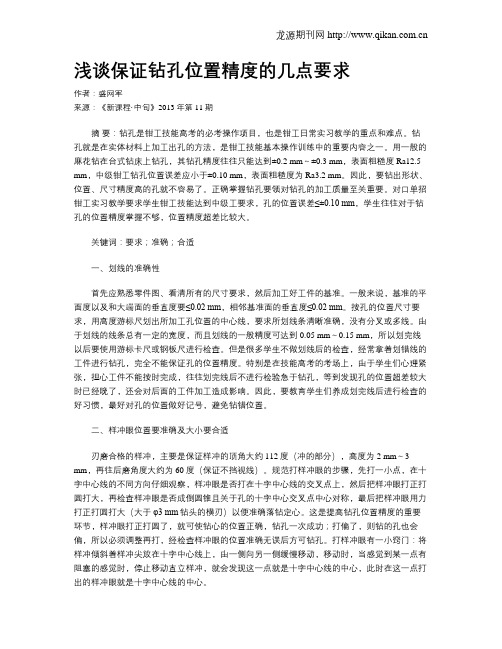
浅谈保证钻孔位置精度的几点要求作者:盛网军来源:《新课程·中旬》2013年第11期摘要:钻孔是钳工技能高考的必考操作项目,也是钳工日常实习教学的重点和难点。
钻孔就是在实体材料上加工出孔的方法,是钳工技能基本操作训练中的重要内容之一。
用一般的麻花钻在台式钻床上钻孔,其钻孔精度往往只能达到±0.2 mm~±0.3 mm,表面粗糙度Ra12.5 mm,中级钳工钻孔位置误差应小于±0.10 mm,表面粗糙度为Ra3.2 mm。
因此,要钻出形状、位置、尺寸精度高的孔就不容易了。
正确掌握钻孔要领对钻孔的加工质量至关重要。
对口单招钳工实习教学要求学生钳工技能达到中级工要求,孔的位置误差≤±0.10 mm,学生往往对于钻孔的位置精度掌握不够,位置精度超差比较大。
关键词:要求;准确;合适一、划线的准确性首先应熟悉零件图、看清所有的尺寸要求,然后加工好工件的基准。
一般来说,基准的平面度以及和大端面的垂直度要≤0.02 mm,相邻基准面的垂直度≤0.02 mm。
按孔的位置尺寸要求,用高度游标尺划出所加工孔位置的中心线,要求所划线条清晰准确,没有分叉或多线。
由于划线的线条总有一定的宽度,而且划线的一般精度可达到0.05 mm~0.15 mm,所以划完线以后要使用游标卡尺或钢板尺进行检查。
但是很多学生不做划线后的检查,经常拿着划错线的工件进行钻孔,完全不能保证孔的位置精度。
特别是在技能高考的考场上,由于学生们心理紧张,担心工件不能按时完成,往往划完线后不进行检验急于钻孔,等到发现孔的位置超差较大时已经晚了,还会对后面的工件加工造成影响。
因此,要教育学生们养成划完线后进行检查的好习惯,最好对孔的位置做好记号,避免钻错位置。
二、样冲眼位置要准确及大小要合适刃磨合格的样冲,主要是保证样冲的顶角大约112度(冲的部分),高度为2 mm~3 mm,再往后磨角度大约为60度(保证不挡视线)。
浅谈保证钻孔位置精度的几点要求

2013-11百花园地法”的方法,以确保培养出真才实学的师范生。
3.落实就业指导工作根据学生自身的学习情况,让大学生明确自己适合从事什么样的职业,同时也让他们了解各种职业之间的差别及社会需求。
学校在搞好实习工作的同时,要千方百计搜集各种就业信息并及时进行公布,让大学生在最短的时间内了解职位的需求状况;同时利用各种资源,举办有针对性的招聘会,这就能够给大学生就业提供良好的平台。
总之,我们应该理性地面对师范生就业难现象。
一般来说,由于大学教育能够有效地增强大学生人力资本和社会适应能力,毕业后的学生经过一定时期的职业搜寻,成功就业的概率还是比较高的。
所以,即使一个学生毕业失业,也是暂时现象,我们不必过于担心。
(作者单位通化师范学院分院)•编辑徐婷一、划线的准确性首先应熟悉零件图、看清所有的尺寸要求,然后加工好工件的基准。
一般来说,基准的平面度以及和大端面的垂直度要≤0.02mm,相邻基准面的垂直度≤0.02mm。
按孔的位置尺寸要求,用高度游标尺划出所加工孔位置的中心线,要求所划线条清晰准确,没有分叉或多线。
由于划线的线条总有一定的宽度,而且划线的一般精度可达到0.05mm~0.15mm,所以划完线以后要使用游标卡尺或钢板尺进行检查。
但是很多学生不做划线后的检查,经常拿着划错线的工件进行钻孔,完全不能保证孔的位置精度。
特别是在技能高考的考场上,由于学生们心理紧张,担心工件不能按时完成,往往划完线后不进行检验急于钻孔,等到发现孔的位置超差较大时已经晚了,还会对后面的工件加工造成影响。
因此,要教育学生们养成划完线后进行检查的好习惯,最好对孔的位置做好记号,避免钻错位置。
二、样冲眼位置要准确及大小要合适刃磨合格的样冲,主要是保证样冲的顶角大约112度(冲的部分),高度为2mm~3mm,再往后磨角度大约为60度(保证不挡视线)。
规范打样冲眼的步骤,先打一小点,在十字中心线的不同方向仔细观察,样冲眼是否打在十字中心线的交叉点上,然后把样冲眼打正打圆打大,再检查样冲眼是否成倒圆锥且关于孔的十字中心交叉点中心对称,最后把样冲眼用力打正打圆打大(大于φ3mm 钻头的横刃)以便准确落钻定心。
钻孔时的切削用量
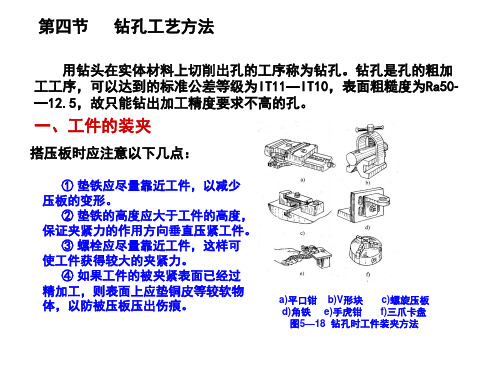
钻孔工艺方法
用钻头在实体材料上切削出孔的工序称为钻孔。钻孔是孔的粗加 工工序,可以达到的标准公差等级为IT11—IT10,表面粗糙度为 Ra50—12.5,故只能钻出加工精度要求不高的孔。
一、工件的装夹
搭压板时应注意以下几点:
① 垫铁应尽量靠近工件,以减少 压板的变形。 ② 垫铁的高度应大于工件的高度, 保证夹紧力的作用方向垂直压紧工件。 ③ 螺栓应尽量靠近工件,这样可 使工件获得较大的夹紧力。 ④ 如果工件的被夹紧表面已经过 精加工,则表面上应垫铜皮等较软物 体,以防被压板压出伤痕。
a)平口钳 b)V形块 c)螺旋压板 d)角铁 e)手虎钳 f)三爪卡盘 图5—18 钻孔时工件装夹方法
第四节
钻孔工艺方法
二、一般工件的钻孔方法
钻孔开始,先调整钻头和工件的位置,使钻尖 对准钻孔中心,然后试钻一浅坑。
通孔在将要钻穿时,必须减小进给量,如果 采用自动进给,要改换成手动进给。 钻不通孔时,可按钻孔深度调整挡块, 并通过测量实际尺寸来控制钻孔深度。 钻深孔时,一般钻进深度达到钻头直径 的3倍时,要退出钻头排屑,以后每钻进一定深度, 提起钻头排屑一次,以免切屑阻塞而扭断钻头。 钻直径较大的孔(一般直径大于 30mm),可分两次钻削,先选用0.5—0.7倍的钻 头直径钻底孔,然后再用所需直径钻头扩孔。
三、钻孔时切削液的使用
表5-9 钻孔时使用的切削液
工件材料 切削液(体积分数)
各类结构钢
不锈钢,耐热钢 纯铜、黄铜、青铜 铸铁 铝及铝合金 有机玻璃
3—5%乳化液,7%硫化乳化液
3%肥皂加2%亚麻油水溶液,硫化切削油 不用,5%—8%乳化液 不用,5%—8%乳化液,煤油 不用,5%—8%乳化液,煤油,煤油与菜油的混合油 5%—8%乳化液,煤油
钻孔施工技术要求
一、地质,钻探工程质量要求钻孔施工过程中,工程质量严格按颁发的《煤炭地质勘察钻孔质量标准》执行。
1、钻孔定测:按设计钻孔位置采用手持GPS测量进行实地定位,由于实际情况需要移动孔位,必须经招标人批准后方可做适当移动。
钻孔结束后使GPS正式准确定测。
2、钻具丈量:钻孔钻进中,每百米进行一次丈量。
孔深误差井深500m以内不大于0.25m,500m以上不大于0.05%,终孔后进行钻具丈量,各次丈量要进行合理平差。
3、终孔直径:钻孔直径半径深度:第四系(5.00m),但必须进入中等风化基岩1.00m。
直径φ426mm,钻孔终孔直径不得小于195mm,终孔深度要求:钻进寒武系上统150m,,满足水文孔要求。
4、钻进方法:回转钻进5、循环液:下入套管进入奥灰层段后必须清水钻进。
6、岩芯采取率:岩芯采取率不小于75%。
7、孔斜:钻进过程中每50m进行一次测斜、纠偏,钻进中要求靶域控制,钻孔开孔至终孔,孔斜水平投影偏斜值在半径20m的靶域内,钻井质量要求达到《煤炭地质勘查钻孔质量标准》甲级孔要求。
8、简易水文观测:施工钻孔全部要求进行简易水文观测,在提钻后下钻前观测水位一次,钻进过程中每小时观测冲洗液消耗量一次,遇涌(漏)水位层,详细记录其深度。
要仔细观测奥灰水的漏水情况及导水高度。
9、地质编录:全孔进行地质编录,钻孔地质编录应按ZD/T0078-93《固体矿产勘查原始地质编录》执行,包括岩芯采取率、观测RQD值、裂隙频率(条数/米)随深度的直方图。
10、岩芯编号装箱:岩芯要认真编号,并按顺序装箱。
岩芯箱统一按下列规定依次编号:顺序号+回次号。
岩芯长大于5cm者都要按回次顺序进行编号(编号一律用红油漆)。
二、水文地质工作要求1、止水:对非抽(注)水层段要进行严格止水,避免不同含水层之间发生水力。
考虑到奥灰顶面起伏不平,故下套管需进入奥灰不小于2m(具体深度要求根据实际情况确定),水泥止水段必须全封闭。
扫空后,在套管内注满清水,连续观测4小时,要求水柱每小时降低不超过20mm,否则重新止水。
加工中心钻头钻孔参数【免费下载】
以下为加工中心钻头钻孔参数,一起来了解一下吧。
扩展资料:加工中心高效钻孔:相对于数控加工中心的表面加工,孔加工要复杂的多,加工孔也要比加工内外表面更为困难。
虽然如此,钻孔加工依然是数控加工中心最为常用的加工方式之一。
采购加工中心作为加工设备的话,孔加工的方法技巧一定要烂熟于心。
数控加工中心常见的孔加工方式主要有:钻孔、绞孔、镗孔、拉孔等,其中钻孔和铰孔最为常用,这两种工艺几乎每个制造车间,生产厂家都可以应用到。
以小型高精的vmc650加工中心为例,钻孔、铰孔的工艺技巧需要重点掌握。
钻孔:钻孔之所以最为常用,那是因为这是在实心材料上加工孔的第一道工序。
钻孔加工有两种方式:一种是钻头旋转;另一种是工件旋转。
钻孔直径一般小于80mm,精度和准确度要求较高。
而两种钻孔方式产生的误差是不相同的。
在钻头旋转的钻孔方式中,由于切削刃不对称和钻头刚性不足而使钻头引偏时,被加工孔的中心线会发生偏斜或不直,但孔径基本不变;而在工件旋转的钻孔方式中则相反,钻头引偏会引起孔径变化,而孔中心线仍然是直的。
常用钻孔刀具有:麻花钻、中心钻、深孔钻等,VMC850加工中心最配备的是麻花钻。
铰孔:铰孔是孔的精加工方法之一,在生产中应用很广。
铰孔余量对铰孔质量的影响很大,余量太大,铰刀的负荷大,切削刃很快被磨钝,不易获得光洁的加工表面,尺寸公差也不易保证;余量太小,不能去掉上工序留下的刀痕,自然也就没有改善孔加工质量的作用。
一般粗铰余量取为0.35~0.15mm,精铰取为01.5~0.05mm。
铰孔时必须用适当的切削液进行冷却、润滑和清洗,以防止产生积屑瘤并及时清除切屑。
与磨孔和镗孔相比,铰孔生产率高,容易保证孔的精度;但铰孔不能校正孔轴线的位置误差,孔的位置精度应由前工序保证。
VMC850加工中心具有完备的切削冷却系统可以完美解决铰孔工艺,但是铰孔不宜加工阶梯孔和盲孔。
钻孔工艺精度标准
不同精度及不同毛坯的圆柱孔加工例:孔Φ25(0,+0.033),孔公差H8,麻花钻至孔Φ24.8,铰孔至Φ25(0,+0.033)孔Φ35(0,+0.062),孔公差H7,麻花钻Φ34.8,铰孔至Φ35(0,+0.062)Φ8(0,+0.018),孔公差约H7-H8,中心钻定位,麻花钻至Φ6,粗镗至Φ7.5,精镗至Φ8(0,+0.018)1、钻削直径较大的孔(大于30mm)时,不宜用大钻头一次钻出,最好分多次钻削,即先用直径较小的钻头钻孔,再用较大直径钻头扩到所要求的尺寸。
基孔制选作基准的孔称为基准孔,基准孔代号H(下偏差值0,上偏差值正值)基轴制选作基准的轴称为基准轴,基准轴代号h(上偏差值0,下偏差值负数)外圆面加工1.粗车:主要作为外圆的预加工,除淬硬钢以外,各种零件的加工都适用。
当零件的外圆要求精度低、表面粗糙度较大时,只粗车即可。
2.粗车-半精车:用于各类零件上不重要的表面或非配合表面。
3.粗车-半精车-精车:精度更高4.粗车-半精车-磨削:用于加工精度稍高、粗糙度值较小、且淬硬的钢件外圆面,也可广泛地用于加工未淬硬的钢件或铸铁件。
平面加工方法未注公差等级GB/T1804-2000公差等级约IT10-IT14之间下面是赠送的励志的100句经典话,需要的朋友可以学习下,不需要的朋友可以下载后编辑删除!!谢谢!!【励志的话】平凡却无私的人啊千万不要抱怨命运的不公。
也许,命运只是用另一种方式偏爱着你那是因为善良的她想让你尽快长大感知人间悲喜,聆听世间哀乐。
虽然有时跌倒,有时失败但请记住跌倒不是失败,失败不是否定。
平凡却无私的人啊千万不要抱怨命运的不公也许,命运只是用透明的方式倾向与你那是因为,慈爱的她想让你尽早成熟看尽人间繁华,尝便世间甘苦。
虽然有时哭泣,有时逃避但请记住哭泣不是永久逃避不是永恒平凡却无私的人啊千万不要抱怨命运的不公也许,命运只是施舍于被它偏爱的人那是因为严厉的她不想让你溺爱长大,感受人们欢呼,享受世界鼓舞虽然有时悲愤,有时无助。
浅述钻孔精度“六关”提高法
C OCCUPATION2012 0894案例ASES浅述钻孔精度“六关”提高法文/阮强志所谓钻孔就是在实体材料上加工出孔的方法。
操作起来并不是很复杂,但要保证孔的形状精度、位置精度和尺寸精度并没那么容易。
一般来说,用普通的麻花钻在普通钻床上钻孔,其钻孔精度只能达到IT10~IT11,表面粗糙度为Ra 50~12.5μm。
按照钳工实习教学大纲的要求,中级钳工钻孔位置误差应小于±0.10mm,表面粗糙度为Ra 3.2μm;高级钳工的钻孔位置误差应小于±0.05mm,表面粗糙度为Ra 1.6μm。
因此,将普通手工钻孔的位置精度提高到小于±0.05mm、表面粗糙度为Ra 1.6μm,或者要钻出形状精度高,位置、尺寸精度高的孔不是件容易的事。
一、准确把握好“划线关”划线正确与否,是钻孔对错的关键。
因此,钻孔前,首先应熟悉图样要求。
加工好工件的基准;一般基准的平面度≤0.04mm,相邻基准的垂直度≤0.04mm。
按钻孔的位置尺寸要求,使用高度尺划出孔位置的十字中心线,要求线条清晰准确。
线条越细,精度越高。
由于划线的线条总有一定的宽度,而且划线的一般精度可达到0.25~0.5mm,所以划完线以后要使用游标卡尺进行检验。
如若学生对于划线后检验做得不够,拿着划错线的工件进行钻孔,则根本无法保证孔的位置精度。
因此,要教育学生养成划完线后进行检验的好习惯。
二、熟练掌握好钻头“刃磨关”钻头是钻孔好坏、精度高低的根本保证,选择钻头直径要合理,熟悉钻头的几何尺寸、熟练掌握钻头的手工刃磨方法是学生钻孔技能的基础。
1.标准麻花钻刃磨对于标准麻花钻要磨出一支理想的钻头,就要正确理解和判断钻头上的各种几何参数,如顶角、横刃斜角、前角、后角等。
刃磨的操作要领很多,教师辅导刃磨时要反复讲解并操作示范,在学生具有感性认识和理性认识的基础上,进行主切削刃刃磨练习,反复训练目测判断120°、60°、10~14°、55°等特定角度。
- 1、下载文档前请自行甄别文档内容的完整性,平台不提供额外的编辑、内容补充、找答案等附加服务。
- 2、"仅部分预览"的文档,不可在线预览部分如存在完整性等问题,可反馈申请退款(可完整预览的文档不适用该条件!)。
- 3、如文档侵犯您的权益,请联系客服反馈,我们会尽快为您处理(人工客服工作时间:9:00-18:30)。
不同精度及不同毛坯的圆柱孔加工
孔Φ35(0,+0.062),孔公差H7,麻花钻Φ34.8,铰孔至Φ35(0,+0.0
62)
Φ8(0,+0.018),孔公差约H7-H8,中心钻定位,麻花钻至Φ6,粗镗至Φ7.5,
精镗至Φ8(0,+0.018)
1、钻削直径较大的孔(大于30mm )时,不宜用大钻头一次钻出,最好分多次钻
削,即先用直径较小的钻头钻孔,再用较大直径钻头扩到所要求的尺寸。
基孔制选作基准的孔称为基准孔,基准孔代号H (下偏差值0,上偏差值正值) 基轴制选作基准的轴称为基准轴,基准轴代号h (上偏差值0,下偏差值负数)
1. 粗车:主要作为外圆的预加工,除淬硬钢以外,各种零件的加工都适用。
当
零件的外圆要求精度低、表面粗糙度较大时,只粗车即可。
2. 粗车-半精车:用于各类零件上不重要的表面或非配合表面。
3. 粗车-半精车
-精车:精度更高
4. 粗车-半精车-磨削:用于加工精度稍高、粗糙度值较小、且淬硬的钢件外圆
面,也可广泛地用于加工未淬硬的钢件或铸铁件。
未注公差等级GB/T1804-2000公差等级约IT10-IT14之间
(注:文档可能无法思考全面,请浏览后下载,供参考。
可复制、编制,期待你的好评与关注)。