客车底盘总装焊装生产工艺流程
1全承载底盘骨架焊装工艺流程
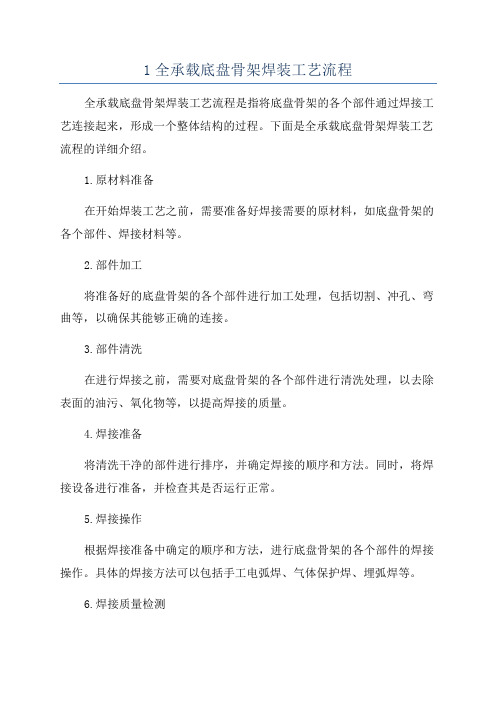
1全承载底盘骨架焊装工艺流程全承载底盘骨架焊装工艺流程是指将底盘骨架的各个部件通过焊接工艺连接起来,形成一个整体结构的过程。
下面是全承载底盘骨架焊装工艺流程的详细介绍。
1.原材料准备在开始焊装工艺之前,需要准备好焊接需要的原材料,如底盘骨架的各个部件、焊接材料等。
2.部件加工将准备好的底盘骨架的各个部件进行加工处理,包括切割、冲孔、弯曲等,以确保其能够正确的连接。
3.部件清洗在进行焊接之前,需要对底盘骨架的各个部件进行清洗处理,以去除表面的油污、氧化物等,以提高焊接的质量。
4.焊接准备将清洗干净的部件进行排序,并确定焊接的顺序和方法。
同时,将焊接设备进行准备,并检查其是否运行正常。
5.焊接操作根据焊接准备中确定的顺序和方法,进行底盘骨架的各个部件的焊接操作。
具体的焊接方法可以包括手工电弧焊、气体保护焊、埋弧焊等。
6.焊接质量检测在焊接完成后,对焊接接头进行质量检测。
可以使用目测、渗透检测、超声波检测等方法,以确保焊接接头的质量达到要求。
7.后处理对焊接完成的底盘骨架进行后处理,包括除渣、抛光、打磨等,以提高其外观质量和加工精度。
8.部件组装将焊接好的底盘骨架的各个部件进行组装,包括螺栓连接、焊接等方式,以形成一个稳固的整体结构。
9.表面处理对底盘骨架进行表面处理,包括喷漆、镀锌等,以提高其抗腐蚀性和美观度。
10.最终检测对整体焊装完成的底盘骨架进行最终的质量检测,包括外观检测、尺寸检测、功能检测等,以确保其质量达到要求。
以上就是全承载底盘骨架焊装工艺流程的详细介绍。
通过以上步骤的实施,能够保证底盘骨架的焊接质量和整体结构的稳固性,从而提高整车的质量和安全性能。
25型客车车底架组焊工艺过程
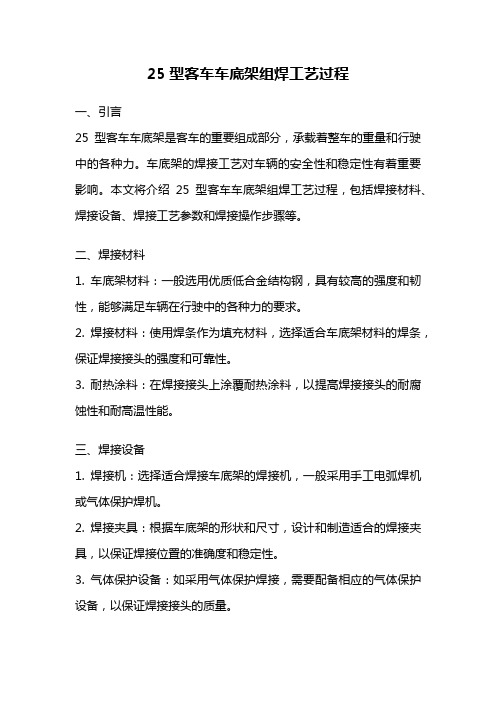
25型客车车底架组焊工艺过程一、引言25型客车车底架是客车的重要组成部分,承载着整车的重量和行驶中的各种力。
车底架的焊接工艺对车辆的安全性和稳定性有着重要影响。
本文将介绍25型客车车底架组焊工艺过程,包括焊接材料、焊接设备、焊接工艺参数和焊接操作步骤等。
二、焊接材料1. 车底架材料:一般选用优质低合金结构钢,具有较高的强度和韧性,能够满足车辆在行驶中的各种力的要求。
2. 焊接材料:使用焊条作为填充材料,选择适合车底架材料的焊条,保证焊接接头的强度和可靠性。
3. 耐热涂料:在焊接接头上涂覆耐热涂料,以提高焊接接头的耐腐蚀性和耐高温性能。
三、焊接设备1. 焊接机:选择适合焊接车底架的焊接机,一般采用手工电弧焊机或气体保护焊机。
2. 焊接夹具:根据车底架的形状和尺寸,设计和制造适合的焊接夹具,以保证焊接位置的准确度和稳定性。
3. 气体保护设备:如采用气体保护焊接,需要配备相应的气体保护设备,以保证焊接接头的质量。
四、焊接工艺参数1. 电流和电压:根据焊接材料和焊接接头的要求,选择适当的电流和电压,以保证焊接接头的强度和质量。
2. 焊接速度:控制焊接速度,使得焊条和工件的熔化和凝固时间适合,以获得良好的焊接效果。
3. 焊接温度:根据焊接材料的熔点和热变形性能,控制焊接温度,以避免焊接接头的变形和裂纹。
五、焊接操作步骤1. 检查车底架:对车底架进行检查,确保没有明显的缺陷和损伤,以保证焊接接头的质量。
2. 清洁工件表面:使用砂轮或刷子清洁焊接接头的表面,除去氧化物和污垢,以提高焊接接头的质量。
3. 定位和固定:将车底架放置在焊接夹具上,根据焊接接头的位置和要求进行定位和固定,以确保焊接位置的准确度和稳定性。
4. 焊接接头:根据焊接工艺参数,使用焊接机进行焊接,保持稳定的焊接速度和适当的焊接温度,完成焊接接头的焊接。
5. 检查和修复:对焊接接头进行检查,发现焊接缺陷或不合格的接头,及时进行修复或重新焊接,以保证焊接接头的质量和可靠性。
全承载客车底架焊接工艺工装的设计
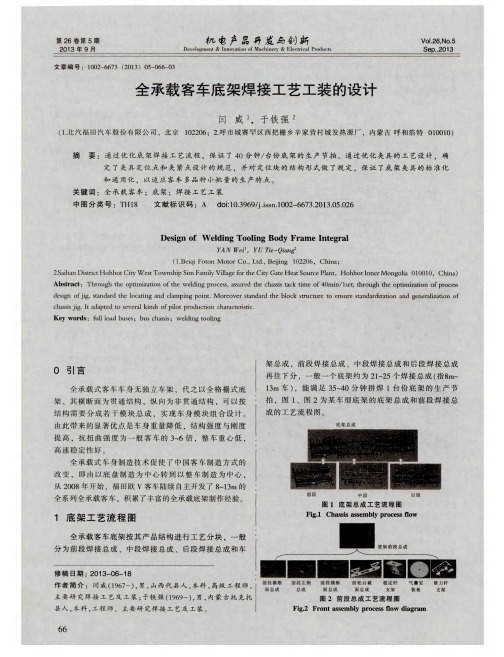
表 4计 算 结 果 与试 验 结 果 对 比 ( 单位 : H z )
T a b . 4 C omp a r i s o n b e t we e n c a l c u l a t e d r e s u l t s a n d
e x p e r i me n t a l r e s u l t s
装 工位 完成 的 ,严 重影 响此工 位 的生产 节拍 。
④ 异 型管 棱边 的扭 曲每 2 m 不 大于 l m m,如超 差应 增 加
法 ,采取 化 整为零 ,从 系 统到 部件 的策 略 ,逐个 验证 建
立 全 局 模 型 ,可 以较 低 的 成 本 获 取 较 好 的 效 果 。 参 考文献 :
[ 1 ] 张令弥. 直 升 机 全 机 振 动 分 析 与控 制 [ J 1 . 南 京航空航天 大学学报,
1 9 7 9, 3 .
( 上接第 6 7页)
尺寸精度检查 :①下料长度误差控
架 夹具 的通 用 性差 。只适 应单 一 车型 ,造 成投 入和 维护
制在 O  ̄ l m m;②下料的角度误差 2 。 以内;③ 弧杆件 成
形 与 理论 曲线 不贴 合小 于 l m m,扭 曲误差 在 l mm 以内 ;
成 本较 高 ;③ 底架 总成焊 接后 的两 端修 正 是在 六面体 合
增 加 试 验 及 建 模 成 本 的 情况 下 。获 得 了前 8阶全 局 固 有频 率最大误差不超 过 5 %的 高 精 度 计 算 模 型 ,完 全 能满 足 工 程 实 际 需 要 。
[ 6 ] 杜 永 峰, 魏仲彬. 施工过 程中隔震层钢筋砼 梁变形初步 分析l J ] . 地
震工 程 学 报 , 2 0 1 3 。 1 .
底盘车间装配工艺流程图

2
3
4
5
6
7
8
9
10
发 动 机 与 变 速 箱 分 装
散 热 器 分 装
制 动 系 统 各 阀 类
装 装 配 配 前 后 桥 桥 板 板 簧 簧
装 配 前 后 桥
吊 装 车 架 上 线
装 配 备 胎 升 降 器
装 配 限 位 块
装 配 稳 定 杆 上 支 架
装 配 传 动 轴 保 护 支 架
装 配 减 振 器 上 支 架
装 配 分 动 箱 高 低 速 机 构
铺 装 水 暖 管 路
油 管 接 头 连 接
11
12
加 注 冷 却 液
加 注 油 脂
加 注 汽 车 燃 油
打印 底盘 VIN 码
加 注 汽 车 燃 油
发 动 机 启 动
底 盘 启 明 星 试 验
底 盘 终 检
底 盘 下 线
标 记
处 数
通知单号
签字
日期
编制 校对 审核 批准 日期
装 配 储 气 筒
装 配 空 气 干 燥 剂
制 动 系 统 各 类 阀 装 配 额
车 架 翻 转
装 配 车 轮
装 配 消 声 器
装 配 制 动 管
装 配 燃 油 供 给 系 统
分 装
装 配 发 动 机 及 变 速 箱 总 成
装 配 冷 却 包
装 配 散 热 器 上 下 水 管
装 配 中 冷 器 进 出 气 管
底盘装配工 艺流程图
共 数 量
页 比 例
第
页
东风特汽(十堰) 客车有限公司
装 配 分 动 箱
装 配 传 动 轴
装 配 减 振 器
客车焊接工艺
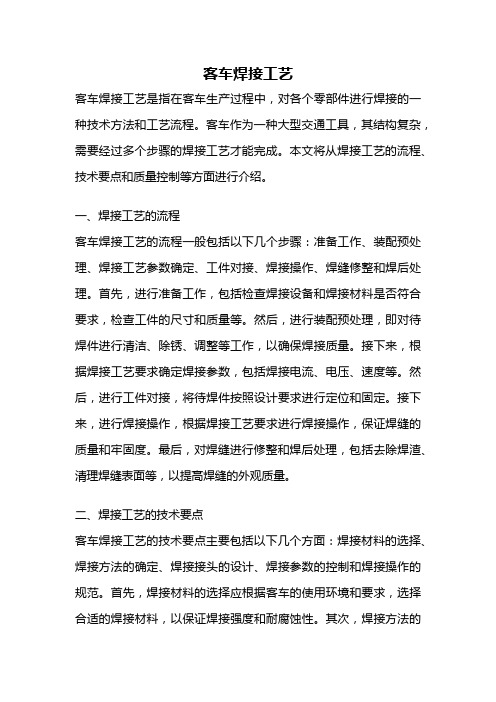
客车焊接工艺客车焊接工艺是指在客车生产过程中,对各个零部件进行焊接的一种技术方法和工艺流程。
客车作为一种大型交通工具,其结构复杂,需要经过多个步骤的焊接工艺才能完成。
本文将从焊接工艺的流程、技术要点和质量控制等方面进行介绍。
一、焊接工艺的流程客车焊接工艺的流程一般包括以下几个步骤:准备工作、装配预处理、焊接工艺参数确定、工件对接、焊接操作、焊缝修整和焊后处理。
首先,进行准备工作,包括检查焊接设备和焊接材料是否符合要求,检查工件的尺寸和质量等。
然后,进行装配预处理,即对待焊件进行清洁、除锈、调整等工作,以确保焊接质量。
接下来,根据焊接工艺要求确定焊接参数,包括焊接电流、电压、速度等。
然后,进行工件对接,将待焊件按照设计要求进行定位和固定。
接下来,进行焊接操作,根据焊接工艺要求进行焊接操作,保证焊缝的质量和牢固度。
最后,对焊缝进行修整和焊后处理,包括去除焊渣、清理焊缝表面等,以提高焊缝的外观质量。
二、焊接工艺的技术要点客车焊接工艺的技术要点主要包括以下几个方面:焊接材料的选择、焊接方法的确定、焊接接头的设计、焊接参数的控制和焊接操作的规范。
首先,焊接材料的选择应根据客车的使用环境和要求,选择合适的焊接材料,以保证焊接强度和耐腐蚀性。
其次,焊接方法的确定应根据焊接材料和工件的特点,选择合适的焊接方法,如手工电弧焊、气体保护焊等。
再次,焊接接头的设计应考虑到工件的受力情况和使用要求,选择合适的接头形式和尺寸。
然后,焊接参数的控制是保证焊接质量的关键,应根据焊接材料和工件的要求,控制好焊接电流、焊接速度等参数。
最后,焊接操作的规范是保证焊接质量的基础,焊工应按照操作规程进行焊接,保证焊缝的牢固度和质量。
三、焊接工艺的质量控制客车焊接工艺的质量控制主要包括焊接质量的检测和焊接过程的监控。
焊接质量的检测应包括焊缝的外观质量、尺寸偏差、焊缝的强度和密封性等方面。
其中,焊缝的外观质量应符合设计要求,焊缝的尺寸偏差应在允许范围内,焊缝的强度和密封性应满足使用要求。
1 全承载底盘骨架焊装工艺流程
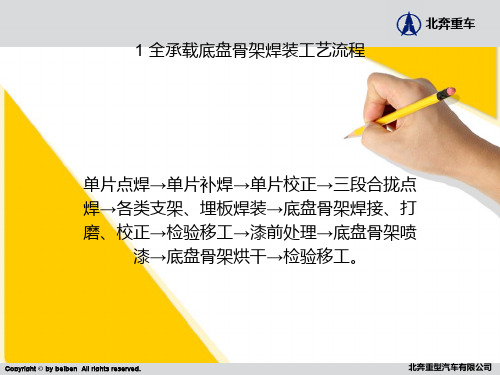
1 全承载底盘骨架焊装工艺流程
单片点焊→单片补焊→单片校正→三段合拢点 焊→各类支架、埋板焊装→底盘骨架焊接、打 磨、校正→检验移工→漆前处理→底盘骨架喷 漆→底盘骨架烘干→检验移工。
Copyright © by beiben All rights reserved.
北奔重型汽车有限公司
2 全承载车身焊装工艺流程
Copyright © by beiben All rights reserved.
北奔重型汽车有限公司
北奔客车公司工作汇报
北奔客车
89
玻璃安装举升平台
安装前后风挡玻 璃
1 总装:137万
6
6
询价(郑州多元)
90
底盘焊装 工具、检具、 样板 车身焊装胎 工具、检 具、样板 底盘、车身 工艺小车
工字钢、槽钢、 矩形管、角钢 工字钢、槽钢、 矩形管、角钢 槽钢、轴承、钢 轮
北奔重型汽车有限公司
北奔客车公司工作汇报
北奔客车
4 工艺 4.1底盘骨架焊装工艺 4.1.1主要工艺特点 底盘骨架焊装及涂装由东向西布置一条主生产线,生产线设8个工位, 1-6工位为全承载客车底盘骨架焊装,7-8工位为底盘骨架涂装。生产形式 为间歇式流水作业,生产节拍2H∕辆。 4.1.2主要工艺流程 单片点焊→单片补焊→单片校正→三段合拢点焊→各类支架、埋板焊
询价 (市场价)
询价(市场价) 询价 (市场价) 询价 (市场价)
工装、工具:83万 投资概算总计:1618万 说明:1.投资概算不包括原总装厂房内设备设施的拆除、土建改造、厂房工作区部分增加母线、电缆、配电柜的费用; 2.不包括新增12条地沟(长×宽×高:1200×920×1500)的费用; 北奔重型汽车有限公司 Copyright © by beiben All rights reserved.
浅析BFC6120L1D6客车底盘悬架结构及安装工艺流程
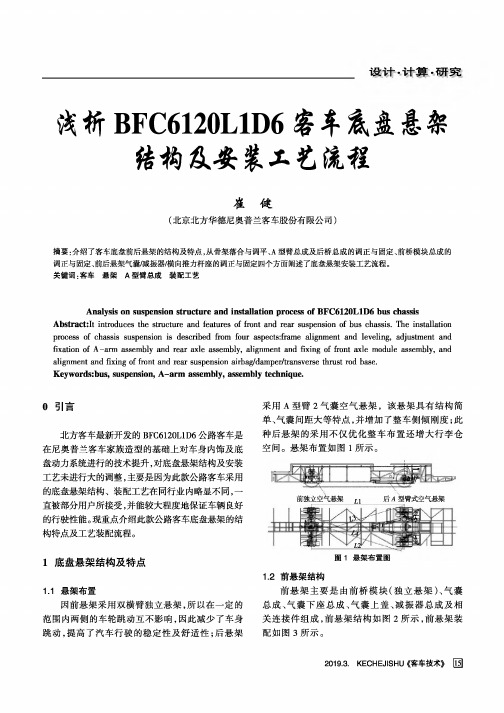
设计.计算.研究炭析BFC6120L1D6窗车爲盘壽栾箱构处妥装工艺诡翟崔健(北京北方华德尼奥普兰客车股份有限公司)摘要:介绍了客车底盘前后悬架的结构及特点,从骨架落合与调平、A型臂总成及后桥总成的调正与固定、前桥模块总成的调正与固定、前后悬架气囊/减振器/横向推力杆座的调正与固定四个方面阐述了底盘悬架安装工艺流程。
关键词:客车悬架A型臂总成装配工艺Analysis on suspension structure and installation process of BFC6120L1D6bus chassis Abstract:It introduces the structure and features of front and rear suspension of bus chassis.The installation process of chassis suspension is described from four aspects:frame alignment and leveling,adjustment and fixation of A-arm assembly and rear axle assembly,alignment and fixing of front axle module assembly,and alignment and fixing of front and rear suspension airbag/damper/transverse thrust rod base.Keywords:bus,suspension,A-arm assembly,assembly technique.0引言北方客车最新开发的BFC6120L1D6公路客车是在尼奥普兰客车家族造型的基础上对车身内饰及底盘动力系统进行的技术提升,对底盘悬架结构及安装工艺未进行大的调整,主要是因为此款公路客车采用的底盘悬架结构、装配工艺在同行业内略显不同,一直被部分用户所接受,并能较大程度地保证车辆良好的行驶性能。
客车底盘总装焊装生产工艺流程

客车生产工艺流程简介一、客车制造工艺概述客车制造工艺特点客车制造的主要工艺技术二、客车制造工艺流程常见工艺流程简介我公司主要生产线、工艺流程及其概况客车制造工艺概述客车制造从原材料和外购件的投入至整车装配检测完毕,其过程经过多条生产线,采用多级综合工艺,生产方式是流水线生产和批量生产混在一起,而主要生产线的生产方式为流水线生产方式,生产形态是连续性生产客车制造工艺的特点➢客车的特点:多品种、小批量、大尺寸、装配工作量大。
➢我公司客车产品覆盖从6米到13米,目前在用约1700多个车型代码➢小型客车工艺形式及方法:车身壳体主要由车身覆盖件和构件等冲压件构成,其制造工艺与乘用车相近。
➢中型、大型客车工艺形式及方法:车身有车身骨架,且车身尺寸大、品种多、生产纲领小,其制造工艺与乘用车有着明显的不同,多采用典型的混合流水线生产方式。
为了与此生产方式相适应,从工艺布置、工位设置、作业安排到设备选型、生产管理等,形成了客车制造的工艺特点。
➢工艺路线布置特点:1.由客车主要生产线构成的工艺路线多采用回转式布置,其主要特点是工艺路线便捷,工艺传递方便,主要生产线之间产品流动通畅,有利于生产进度控制和现场管理。
在主要生产线衔接处设置缓冲工位,以控制生产节拍。
设置后备工位,对于有特殊要求、作业量较大的产品,移到后备工位进行制作,保证生产线平稳运行。
工位布置特点:客车生产线的工位面积大、工位数少、工位作业量大、作业内容繁杂、作业时间不均衡。
所以对作业量大的瓶颈工位设置了必要的辅助工位,并通过设置辅助生产线,适当分组装配,减少生产线上的总装配量,提高生产线对多品种混合生产的适应性,以稳定流水线生产。
2.一些生产规模较大的客车企业为了提高生产能力,适应客车品种多、批量小的生产特点,多采用设置两条并行的车身焊装线和两条并行的车身装配线与一条车身涂装线相衔接的方式,焊装线、装配线的工位采用串联式布置,整体浸渍磷化和浸漆、电泳底漆生产线工位采用串联式布置;涂装线其他工位采用并列式布置。
- 1、下载文档前请自行甄别文档内容的完整性,平台不提供额外的编辑、内容补充、找答案等附加服务。
- 2、"仅部分预览"的文档,不可在线预览部分如存在完整性等问题,可反馈申请退款(可完整预览的文档不适用该条件!)。
- 3、如文档侵犯您的权益,请联系客服反馈,我们会尽快为您处理(人工客服工作时间:9:00-18:30)。
客车生产工艺流程简介一、客车制造工艺概述客车制造工艺特点客车制造的主要工艺技术二、客车制造工艺流程常见工艺流程简介我公司主要生产线、工艺流程及其概况客车制造工艺概述客车制造从原材料和外购件的投入至整车装配检测完毕,其过程经过多条生产线,采用多级综合工艺,生产方式是流水线生产和批量生产混在一起,而主要生产线的生产方式为流水线生产方式,生产形态是连续性生产客车制造工艺的特点➢客车的特点:多品种、小批量、大尺寸、装配工作量大。
➢我公司客车产品覆盖从6米到13米,目前在用约1700多个车型代码➢小型客车工艺形式及方法:车身壳体主要由车身覆盖件和构件等冲压件构成,其制造工艺与乘用车相近。
➢中型、大型客车工艺形式及方法:车身有车身骨架,且车身尺寸大、品种多、生产纲领小,其制造工艺与乘用车有着明显的不同,多采用典型的混合流水线生产方式。
为了与此生产方式相适应,从工艺布置、工位设置、作业安排到设备选型、生产管理等,形成了客车制造的工艺特点。
➢工艺路线布置特点:1.由客车主要生产线构成的工艺路线多采用回转式布置,其主要特点是工艺路线便捷,工艺传递方便,主要生产线之间产品流动通畅,有利于生产进度控制和现场管理。
在主要生产线衔接处设置缓冲工位,以控制生产节拍。
设置后备工位,对于有特殊要求、作业量较大的产品,移到后备工位进行制作,保证生产线平稳运行。
工位布置特点:客车生产线的工位面积大、工位数少、工位作业量大、作业内容繁杂、作业时间不均衡。
所以对作业量大的瓶颈工位设置了必要的辅助工位,并通过设置辅助生产线,适当分组装配,减少生产线上的总装配量,提高生产线对多品种混合生产的适应性,以稳定流水线生产。
2.一些生产规模较大的客车企业为了提高生产能力,适应客车品种多、批量小的生产特点,多采用设置两条并行的车身焊装线和两条并行的车身装配线与一条车身涂装线相衔接的方式,焊装线、装配线的工位采用串联式布置,整体浸渍磷化和浸漆、电泳底漆生产线工位采用串联式布置;涂装线其他工位采用并列式布置。
由于主要生产线位于不同的厂房内,能更好地满足环境保护和安全性要求。
3.一些生产规模较大的客车企业为了提高生产能力,适应客车品种多、批量小的生产特点,多采用设置两条并行的车身焊装线和两条并行的车身装配线与一条车身涂装线相衔接的方式,焊装线、装配线的工位采用串联式布置,整体浸渍磷化和浸漆、电泳底漆生产线工位采用串联式布置;涂装线其他工位采用并列式布置。
由于主要生产线位于不同的厂房内,能更好地满足环境保护和安全性要求。
客车制造工艺的特点➢客车工装、设备特点:针对客车的生产特点,所采用的工装设备一般具有一定的通用性,以降低生产成本,缩短生产车型变化时生产线调整时间。
如焊接设备采用半自动CO2气体保护焊、适应几种车型生产的车身骨架组焊胎具、通用的气动和电动装配工具等。
客车因其车身尺寸大,形成了如侧围蒙皮张拉工艺、顶盖两侧蒙皮辊压成型工艺、车身骨架联装组焊等特点显著的工艺形式。
➢客车制造工艺水平相关因素:与客车结构、生产规模、生产条件等因素密切相关。
由于客车结构的不同和工厂生产规模的差异,造成所选择的工艺方法和工装设备呈现多样性。
客车制造主要工艺技术基本工艺:冲压、焊接、喷涂和装配工艺是客车制造的四种基本工艺。
这四种基本工艺在客车车身制造中的具体应用,形成了车身骨架制造、车身蒙皮制造、车身构件冲压成型、车身焊装、金属构件磷化和车身喷涂、底盘和车身装配,以及整车性能调试检测等客车制造工艺。
主要设备:在客车车身生产中所使用的主要设备有下料设备、冲压设备、焊接设备、磷化设备、喷涂设备以及转运设备等;主要工艺装备:工艺装备主要有冲压模具、骨架焊装胎具、前后风窗框组焊胎具、各种工作台以及检验样板等。
冲压:小型客车车身的构件、覆盖件等零部件大部分是冲压件,大客车车身的板弯件、部分车身外蒙皮、司机门门体、乘客门门体、保险杠等零部件也是冲压件。
因此冲压工艺是车身零部件的主要生产工艺。
车身冲压零件的尺寸精度和表面质量是保证车身质量的基础,只有稳定的冲压件质量才能保证生产出合格的车身总成。
板材、模具和冲压设备是冲压生产的三大要素。
焊装:客车车身骨架采用CO2气体保护焊,在焊接胎具上组焊而成。
其制造过程包括矩形管下料、矩形管弯曲成型、车身骨架五大片(前围、后围、左侧围、右侧围和顶盖骨架)的组焊和车身骨架联装组焊等。
骨架构件在五大片焊接胎具上定位、夹紧并组焊,形成五大片车身骨架。
五大片焊接胎具一般由底架、胎具本体和定位夹紧装置等部件组成,可以保证骨架组焊精度要求。
车身骨架的五大片与车身底架或车架在骨架联装组焊胎具上完成整车车身骨架的组焊。
利用组装胎组焊整车车身骨架,组焊精底高,质量好。
因此骨架联装组焊胎具是车身骨架制造工艺中的关键设备。
车身焊装工艺:是在车身焊装线上进行的多种作业方法的总称。
对于小型车车身,冲压成型的构件和覆盖件通过焊装而形成车身总成(又称之白皮车身),焊装是车身成型的关键。
车身焊装工艺将车身零部件焊装为合件,再将若干合件和零部件焊装为分总成,最后将分总成、合件、零件装焊成白车身。
在车身焊装过程中,通常使用专用的装焊胎具将其零件进行定位、夹紧,装焊胎具和焊接设备是焊装的主要工装设备。
对于大型客车,在车身焊装线上的各工位依次完成车身骨架联装组焊、侧围蒙皮张拉、前后围蒙皮组焊、各种门体以及前后保险杠的安装等作业。
车身焊装质量不但影响车的外观质量,也影响车身装配件的装配质量。
磷化处理工艺:能有效提高车身金属构件的耐腐蚀能力和车身的使用寿命,金属表面的磷化处理方法一般采用喷射法和浸渍法。
喷射法是指磷化液借助喷嘴以一定的压力喷向构件表面来实现磷化处理的方法,适用于大型的连续生产的构件。
对于复杂的金属构件,采用浸渍法更好,其生成的磷化膜致密平滑。
客车车身采用的磷化处理方法有金属构件的浸渍法磷化、车身总成(白皮车身)整体浸渍法和车身总成喷射法磷化三种。
磷化处理工艺包括金属表面在涂装前的除油、除锈和磷化处理,也称为涂装前金属表面处理。
金属表面磷化处理后应立即涂装防锈底漆。
涂装工艺:是对客车零、部件和车身表面处理的工艺。
客车对装饰性、耐候性、耐腐蚀性要求很高,车身涂层具有保护功能和装饰功能。
装配工艺:就是把零部件按照整车工艺流程的需要进行装配,是保证整车品质的最终关口。
总装配工艺(包括整车的检测调试)是客车生产中的最后一道工序,汽车检测线是企业对出厂客车的装配质量、技术性能和安全性能进行检测的质量保证措施和主要手段。
客车制造工艺流程客车制造的主要生产线采用流水线作业方式。
各客车制造厂因其生产规模、生产条件和生产车型的不同,所采取的工艺流程亦有所不同,常见的工艺流程可归纳为三类。
1、脱壳式2、扣合式我公司生产线、工艺流程概况一、部件准备车间,主要完成车身及底盘零部件自制件的加工。
按工作内容主要可分为:剪折工位、钳工工位、焊接工位、等离子工位、备料工位、浸漆工位。
矩形管下料,重点控制的是下料尺寸、角度。
其下料的准确程度关系到小总成乃至车身总成的尺寸准确程度。
下料设备一般采用带式锯床、盘式锯床、弓式锯床、冲床等。
零部件公司:自制车架,后期计划。
二、底盘装配车间,主要工作是将各个零部件进行组装,最终装配成能够独立行走的三类底盘,目前单班产约10台客车底盘,共分13个装配工位,底盘装配通过地板链进行输送。
1、翻转工位:拥有底盘翻转设备,可以实现底盘的翻转。
2、支架工位:主要装配转向系统及打车辆的唯一身份识别号码——VIN码。
3、吊装工位:主要工作内容是将分装好的发动机带变速箱总成通过行车吊装到车架上。
4、底盘调试:底盘调试即对下线的底盘的各个系统进行调整,加油,加防冻液,启动发动机。
最终要求是底盘能达到独立行走状态。
三、焊装车间主要工作内容是进行车身骨架、封板的焊装以及车身与底盘的扣合,目前单班最高产能为73台(18+18+20+15+2)。
共分大巴、公交、中巴、三条焊装线,每条生产线18个装配工位。
以及大型车事业部和豪华车事业部。
1、顶盖低位作业工位:中顶蒙皮、侧顶蒙皮采用低位作业的方法,不仅降低了员工劳动强度,大大提高了操作的安全性,而且也便于控制顶蒙皮的焊接、制作质量,缩短了顶蒙皮焊接、空调进/回风口以及天窗口的制作工时。
2、总拼工位:采用我司独立研发的总拼工装,通过限位块的快速翻转能实现多种大巴、中巴车型的车身总拼工作,满足了柔性化生产的需要。
每台车身的总拼,都严格按工艺要求操作,对于车身的关键尺寸,除了工装上加以保证外,现场员工每台车都要进行测量、记录,保证车身的总体尺寸在可控的范围内。
3、侧蒙皮安装工位:采用液压拉伸机张拉蒙皮。
与传统的手工张拉机相比,不仅省时、省力,而且也解决了手工张拉在拉紧蒙皮的同时极易造成骨架变形的问题,蒙皮张拉后的平整度有了较大提高。
另外,液压拉伸机还能根据车型的不同,自动调整夹具的高度、长度、宽度方向的位置,满足了多品种、柔性化生产的要求。
4、车身扣合工位:严格控制车身相对底盘的位置,进行多点、多维度的测量并记录,保证车身与底盘的相对位置偏差控制在5mm范围内。
非电泳工艺流程:1顶盖低位作业— 2总拼工位— 3校正工位—4二层骨架工位—5侧蒙皮工位— 6顶盖补焊工位—7乘客区封板工位—8驾驶区封板工位—9侧仓门安装工位—10车身扣合— 11仓骨架—12仓封板— 13底盘件安装—14乘客门、保险杠工位— 15打磨— 16修整— 17交检电泳后工艺流程:1顶盖低位作业—2总拼工位—3校正工位—4二层骨架工位—5侧蒙皮工位—6顶盖补焊工位—7乘客区封板工位—8驾驶区封板工位—9行李仓骨架、踏步骨架工位—10行李仓封板、踏步封板工位—11侧仓门安装工位、乘客门、保险杠工位—12打磨、修整—车身电泳(后台阶隔音棉、仓门气弹簧、打胶<后台阶、发泡挡板、轮罩>、工艺撑杆拆除)—13扣车身、底盘防护工位—14行李仓骨架补焊工位—15仓封板补焊工位—16底盘件、前后保— 17下线修整—18交检手工前处理 喷涂底漆 底漆烘干 发阻尼胶 刮涂腻子、大顶打胶腻子自干喷中涂漆(底部喷黑漆) 腻子打磨 中涂打磨 中涂烘干 图案制喷彩条漆 喷涂面漆 面漆烘干 下线修整 彩条漆烘干 底盘漆 总装 油漆修整 特殊防腐整车电泳 焊装扣合 发泡 阻尼胶 车身表面清洁、焊点处理 腻子自干喷中涂漆(底部黑漆取消) 腻子打磨 中涂打磨 中涂烘干 图案制作 喷彩条漆 喷涂面漆 面漆烘下线修整 彩条漆烘干 底盘漆总装 油漆修整特殊防腐刮涂腻子、大顶打胶仓门打胶非电泳结构涂装工艺流程电泳结构涂装工艺流程:黄色表示电泳后制作顺序或工作内容发生变化的工位。
电泳车间简介电泳生产线占地面积10000多平方米,生产节拍7~8分钟,年产达25000台车身和车架。