0245-001调质齿轮锻件技术条件
锻件通用技术要求

1 、锻件通用技术要求(JB/ZQ4000.7-86)2 、铸件通用技术要求(JB/ZQ4000.5-86)(铸件技术要求) :铸件尺寸公差要求CT3 、焊接件通用技术要求(JB/ZQ400.3-86)1. 焊接结构件的长度尺寸公差见1-245c 尺寸和形位公差数值.plb, 适用于焊接零件和焊接组件的长度尺寸. 焊接件的直线度. 平面度和平行度公差见1-245c 尺寸和形位公差数.plb, 焊接结构件的尺寸公差与形位公差等级选用见1-245b 尺寸和形位公差等级.plb2. 标注和未标注角度的偏差见1-246a 角度偏差.plb, 角度偏差的公称尺寸以短边为基准边, 其长度从图样标明的基准点算起.3. 喷丸处理的焊接件, 为了防止钢丸钻入焊缝, 必须焊接内焊缝, 并尽量避免内室和内腔. 如果结构上必须有内室和内腔,则必须进行酸洗, 以便达到表面除锈质量等级Be(见JB/ZQ4000.10-86 附录A). 对此图样需作标注.4. 由平炉钢制造的低碳钢结构件, 可在任何温度下进行焊接. 但为了避免焊接过程产生裂纹及脆性断裂, 厚度较大的焊接件, 焊削必须根据工艺要求,进行预热和缓冷. 板厚超过30mm的重要焊接结构,焊后应立即消除内应力, 消除内应力采用550- 600℃ 回火, 或200℃局部低温回火.5. 普通低合金结构钢制造的焊接件, 必须按照焊接零件的碳当量和合金元素含量、零件的厚度、钢结构件的用途和要求进行焊前预热和焊后处理, 见表 1 .4 、涂装通用技术条件(JB/ZQ4000.10-88)1. 涂装前对物体的表面要求应符合本标准的规定.2. 除锈后的金属表面与涂底漆的间隔时间不得大于6h, 酸洗处理表面与第一次涂底漆时间不少于48h, 但无论间隔时间多少, 涂漆前表面不得有锈蚀或污染.3. 铆接件相互接触的表面, 在联接前必须涂厚度30-40 μm防锈漆. 由于加工或焊接损坏的底漆,要重新涂装.4. 不封闭的箱形结构内表面, 在组焊前必须涂厚度60-80 μ m防锈漆, 封闭的箱体结构件内表面不涂漆.5. 溜槽、漏斗、裙板内表面、平衡的重箱内表面、安全罩内表面、封闭箱且在运输过程中是敞开的内表面等, 必须涂厚度60-80 μ m防锈漆.6. 涂层的检查项目及方法应符合本标准的规定.6 、装配通用技术条件(JB/ZQ4000.9-86)1. 外购材料与零部件应具有JB/ZQ4000.1-86< 产品检验通用技术要求>中规定的检验报告与合格证.2. 用于紧固机架, 机座和压力容器压紧法兰的紧固件,在紧固后, 螺钉或螺母的端面与被紧固零件间的倾斜不得大于1°.3. 螺栓与螺母拧紧后, 螺栓应露出螺母2-4 扣, 不许露出过长或过短.120 0.10 10C=Lα △t+0.15式中:C─ 轴承外座圈与端盖间的间隙,mm.L─ 两轴承中心距,mm.α─ 轴材料的线膨胀系数(取α=12×10^( -6)△t─ 轴工作时温度与环境温度之差,℃ . 0.15 ─ 轴膨胀后剩余的间隙,mm.15. 单列圆锥滚子轴承、向心推力球轴承、双向推力球轴承向游隙按(表1)调整. 双列和四列圆锥滚子轴承在装配时均应检查其轴向游隙,并应符合(表2)的要求.四列圆锥滚子轴承内径225-3150.30-0.40 0.70-0.80 315-560 0.40-0.50 0.90-1.00120-180 0.15-0.25 180-315 0.20-0.30 315-400 0.25-0.35 400-500 0.30-0.40 500-630 0.30-0.40 630-8000.35-0.45800-1000 0.35-0.4516. 滑动轴承上、 下轴瓦的接合面要接触良好 , 无螺钉把紧的轴瓦接合面 , 用 0.05mm 和塞尺从外侧 检查, 在各处的塞入深度 , 都不得大于接合面的 1/3.17. 上、下轴瓦装配后其外圆应与相关轴承孔良好接触 , 如果图样或相关设计文件对接触率未作具 体规定时 , 应按下表的规18. 轴瓦内孔刮研后 , 应与相关轴颈接触良好 , 如图样或相关设计文件未作具体规定时 , 则按下表 的规定执行 . 轴向游隙注: 受力较小的轴瓦、接触点可在25×25mm^2的面积上, 按表中数值降低 1 个接触点.19. 上、下轴瓦接触角α 以外的部分均需刮出油楔(如下表所示C1), 楔形从瓦口开始由最大逐步过渡到零, 楔形最大值按下表中规定. 上、下轴瓦经刮研达要求并组装后, 轴瓦内径与轴顶部处的间隙值 C 应达到图样配合公差的中间值或接近上限值.20. 轴瓦中装固定销用的通孔, 应在瓦口面与相关轴承孔的开合面保持平齐的情况下, 与其配钻铰. 固定销打入后, 应与销孔紧密配合, 不得有松动现象, 销子的端面应低于轴瓦内孔2-3mm.21. 过盈配合零件在装配前必须对配合部位进行复检, 并做好记录. 过盈量应符合图样或工艺文件的规定; 与轴肩相靠的相头轮或环的端面, 以及作为装配基准的轮缘端面, 与孔的垂直度偏差应在图样规定的范围内.22. 压装的轴和套允许在引入端制作导锥, 导锥的长度不准超过配合部位长度的15%,锥度各工厂自定.23. 采用压力机压装时,应做好压力变化的记录, 压力变化应当平稳,出现异常时就进行分析,不准有压坏零件配合表面的现象. 图样有最大压入力的要求时, 应达到规定数值,不准过大或过小.24. 压装完成后,在轴肩处必须靠紧, 间隙不得大于0.10mm.25. 热装薄环或轮缘时, 在端面处应设置可靠的定位基准.热装后轴与环或轮毂与轮缘之间的中心不准出现互相偏斜现象.26. 除铸铁轮毂与钢制轮缘在热装后可向轮毂内壁均匀浇冷水外, 其余热装零件均应自然冷却, 不准急冷.27. 零件热装时,必须靠紧轴肩或其它相关端面. 零件经过冷缩后, 零件与轴肩或其它相关端面的间隙在图样未做规定时, 不得大于配合长度尺寸的1/1000.28. 主动链轮和被动链轮齿的中心线应当重合. 其偏移误码差不得大于两链轮中心距2/1000.29. 链条非工作边的下垂度, 在图样没有具体规定时, 按两链轮中心距的1-4.5% 的规定.30. 相关的两个平面需要互研时, 只能在两个平面各自按平板或平尺刮研接近合格后,方准两件互研. 被刮研表面接触点在图样或相关设计文件无具体规定或以精磨代替刮研时, 应符合下表规定.31. 下列回转零件必须做静平衡试验1). 图样已给出不平衡力矩限值的零件2). 对于没有注明静平衡试验的回转零件, 当Q.nmax> 25时均需进行静平衡试验. 式中Q为回转零件的质量,t;nmax 为回转零件的最大转速,r/min. 当nmax≤20r/min 的以及锻造的全加工、全对称的回转零件不作静平衡试验.32. 对于需要作平衡试验,但未规定平衡精度时,按JB/ZZ4-86<< 刚体转动件的平衡>>规定的平衡精度G18执行.33. 所有铸造液压缸体等容器, 如试压工序是安排在粗加工后进行的, 而在精加工后表面又出现了气孔、裂纹、夹渣等缺陷时, 则必须重新进行试压.34. 所有钢板焊接的液压罐等容器,焊后应进行试压, 焊缝处经过切削加工时, 则要重新试压.35. 锻造或锻焊结构的液压缸等, 要采用外观、超声波探伤、液压试验等方法, 对承压的可靠性进行检验.36. 探伤表面粗糙度应达到Ra3.2 μm.37. 承压母体试压与装配后的密封试压, 如无特殊规定试验压力, 一般为工作压力的 1.5 倍.38. 零件母体承压可靠性的试压, 保压15min( 允许补压), 母体各部不准有渗漏现象.39. 装配件密封性试压, 保压2min, 不降压, 且各密封处不准有渗漏现象.。
各类齿轮热处理要求及材质要求

各类齿轮热处理要求及材质要求一、工作条件以及材料与热处理要求1.条件:低速、轻载又不受冲击要求:HT200HT250HT300去应力退火2.条件:低速(<1m/s)、轻载,如车床溜板齿轮等要求:45调质,HB200-2503.条件:低速、中载,如标准系列减速器齿轮要求:4540Cr40MnB(5042MnVB)调质,HB220-250Y4.条件:低速、重载、无冲击,如机床主轴箱齿轮要求:40Cr(42MnVB)淬火中温回火HRC40-455.条件:中速、中载,无猛烈冲击,如机床主轴箱齿轮要求:40Cr、40MnB、42MnVB调质或正火,感应加热表面淬火,低温回火,时效,HRC50-556.条件:中速、中载或低速、重载,如车床变速箱中的次要齿轮要求:45高频淬火,350-370℃回火,HRC40-45(无高频设备时,可采用快速加热齿面淬火)7.条件:中速、重载要求:40Cr、40MnB(40MnVB、42CrMo、40CrMnMo、40CrMnMoVBA)淬火,中温回火,HRC45-50.8.条件:高速、轻载或高速、中载,有冲击的小齿轮要求:15、20、20Cr、20MnVB渗碳,淬火,低温回火,HRC56-62.38CrAl38CrMoAl渗氮,渗氮深度0.5mm,HV9009.条件:高速、中载,无猛烈冲击,如机床主轴轮.要求:40Cr、40MnB、(40MnVB)高频淬火,HRC50-55.10.条件:高速、中载、有冲击、外形复杂和重要齿轮,如汽车变速箱齿轮(20CrMnTi淬透性较高,过热敏感性小,渗碳速度快,过渡层均匀,渗碳后直接淬火变形较小,正火后切削加工性良好,低温冲击韧性也较好)要求:20Cr、20Mn2B、20MnVB渗碳,淬火,低温回火或渗碳后高频淬火,HRC56-62.18CrMnTi、20CrMnTi(锻造→正火→加工齿轮→局部镀同→渗碳、预冷淬火、低温回火→磨齿→喷丸)渗碳层深度1.2-1.6mm,齿轮硬度HRC58-60,心部硬度HRC25-35.表面:回火马氏体+残余奥氏体+碳化物.中心:索氏体+细珠光体11.条件:高速、重载、有冲击、模数要求:20Cr、20Mn2B渗碳、淬火、低温回火,HRG56-62.12.条件:高速、重载、或中载、模数>6,要求高强度、高耐磨性,如立车重要螺旋锥齿轮要求:18CrMnTi、20SiMnVB渗碳、淬火、低温回火,HRC56-6213.条件:高速、重载、有冲击、外形复杂的重要齿轮,如高速柴油机、重型载重汽车,航空发动机等设备上的齿轮.要求:12Cr2Ni4A、20Cr2Ni4A、18Cr2Ni4WA、20CrMnMoVBA(锻造→退火→粗加工→去应力→半精加工→渗碳→退火软化→淬火→冷处理→低温回火→精磨)渗碳层深度1.2-1.5mm,HRC59-62.14.条件:载荷不高的大齿轮,如大型龙门刨齿轮要求:50Mn2、50、65Mn淬火,空冷,15.条件:低速、载荷不大,精密传动齿轮.要求:35CrMO淬火,低温回火,HRC45-5016.条件:精密传动、有一定耐磨性大齿轮.要求:35CrMo调质,HB255-302.17.条件:要求抗磨蚀性的计量泵齿轮.要求:9Cr16Mo3VRE沉淀硬化18.条件:要求高耐磨性的鼓风机齿轮.要求:45调质,尿素盐浴软氮化.19.条件:要求耐、保持间隙精度的25L油泵齿轮。
铸锻件调质工艺守则

铸锻件调质工艺守则1范围本标准规定了碳素钢及合金钢铸锻件调质处理的技术要求及操作规程。
本标准适用于材料为碳素钢、合金钢,截面小于800mm,硬度HB≤320的一般机器零件(如:轴、齿轮、圆盘等锻件及形状比较简单的铸件)的调质处理。
2规范性引用文件GB231-1984 金属布氏硬度试验方法GB/T699-1999 优质碳素结构钢GB/T3077-1999 合金结构钢GB/T6402-1991 钢锻件超声波检验方法GB7232-1999 金属热处理工艺术语GB7233-1987 铸钢件超声波探伤及质量评级GB8539-1987 齿轮材料及热处理检验的一般规定GB9452-1988 热处理炉有效加热区测定方法GB11352-1989 一般工程用铸造碳素钢件GB/T16923-1997 钢的正火与退火处理GB/T17394-1998 金属里氏硬度试验方法JB3877-1985 钢的淬火回火处理3名词术语3.1淬火将钢件加热到AC3或AC1点以上某一温度,保持一定时间,然后以适当速度冷却获得马氏体或贝氏体组织的热处理工艺。
3.2回火钢件淬硬后,再加热到AC1点以下某一温度,保温一定时间,然后冷却到室温的热处理工艺。
3.3调质钢件淬火后高温回火的复合热处理工艺。
3.4待调质件凡要求进行调质处理的钢材、零件坯料等统称待调质件。
3.5调质件经过调质处理的钢材或零件坯料。
4待调质件的有关规定4.1待调质件的钢种牌号适用于调质的部分钢种牌号列于表1。
表1钢组及标准号钢种牌号(1)结构钢大型碳素结构钢锻件普通含锰钢大型合金结构钢锻件35,45,55,60硅锰钢硅锰钼钒钢铬钢铬钼钢铬钼铝钢铬锰钼钢铬镍钢铬镍钼钢铬锰硅钢重型机械用弹簧钢轴承钢35SiMn,50SiMn37 SiMn2MoV40Cr, 50Cr35CrMo, 42CrMo,50 CrMo38CrMoAl40CrMnMo40CrNi, 45 CrNi34CrNiMo, 40CrNiMo30CrMnSi, 35 CrMnSi65Mn, 60Si2Mn, 50CrVAGCr15, GCr15SiMn(2) 工具钢大型锻件用碳素工具钢大型锻件用合金工具钢T7、T8、T10、T129CrSi,9Cr2,9 Cr2Mo,5 CrMnMo,5 CrNiMo,60 CrMnMo(3)特殊钢大型不锈、耐酸耐热钢锻件1 Cr13,2 Cr13,3 Cr13,4 Cr13,(4)铸钢一般工程用铸造碳钢件大型低合金钢铸件ZG270-500,ZG310-570,ZG340-640ZG40Mn2,ZG50Mn2,ZG35CrMnSi, ZG35SiMn, ZG34CrNiMo4.2 调质件的原始资料a、一般零件必须提供:钢号、预先热处理方法等。
锻件通用技术条件

锻件通用技术条件交通部上海港口机械制造厂企业标准锻件通用技术条件说明为了保证产品零部件质量,首先必须重视原材料和毛坯件质量。
原材料和毛坯件质量标准是基础标准。
在锻件方面,根据有关资料结合我厂实际制定了三种通用基础标准,即“JQ/GJ21—1—82锻件通用技术条件”“JQ/GJ21—2—82锻件毛坯质量分级标准”“JQ/GJ21—3—82锻件加工余量及尺寸公差”。
“锻件通用技术条件”是考核锻件全面质量的。
“锻件毛坯质量分级标准”主要是考核锻件外形毛坯质量。
本标准经船舶检验局上海办事处于1981年3月4日(81)沪船检字第94号文审查修正,作为起重运输机械锻造通用技术条件。
本标准适用于港口起重运输机械自由锻造,胎膜锻造的普通碳素钢,优质碳素钢和合金结构钢锻件。
对本标准中未规定的特殊要求应在其他专用技术条件中补充规定。
本标准中所以用的国标,部标或其他标准,均以最新标准为准。
一锻件试验分级1、根据设计要求,工作特性和用途,按进行的试验项目和试验数量,将锻件分为Ⅰ、Ⅱ、Ⅲ、Ⅳ、Ⅴ五级,见(表1)表1锻件试验等级硬度 HB 拉力冲击 b 实验项目试验数量典型零件σs或σαk 1Ⅰ无如标准件螺栓螺9母垫圈等。
Ⅱ√每批取5%,但不少于一般的销轴、操纵件 3杆件、高强度螺栓、传动轴等。
Ⅲ√热处理后每件试验硬减速箱传动轴、齿度轮、链轮、滚轮、联轴器零件等。
Ⅳ√√√(1)热处理后,每件变幅螺杆、轮条,做硬度试验 Q≦50T吊钩、吊(2)每批取2%做拉钩横梁螺帽、卷筒力冲击试验,但轴变幅、起升系统不少于2件Ⅴ√√√的铰轴。
(1)典型受力部件Q≧50T吊钩,横每件做实验梁,螺母大型旋转(2)非典型锻件但座圈,锻件等。
项目重量超过1000~1500Kg或长度为≧3M时都必须进行三种试验注:(1)各级锻件必须要符合“二技术要求”中各项规定(2)凡表1中未列出的机械零件,应视零件的具体作用及重要性,按“表1 所列类似性质的典型零件确定实验等级(3)表1中试验数量,均指同钢号、同一热处理的一批锻件,并允许一批锻件中包括根据各图号制造的外形尺寸近似的锻件。
锻件通用技术要求内容

其它尺寸的一般公差降一级选用, 如图样上标明一般公差为CT10 级的话,则壁厚公差选用CT11级.
5.特殊要求的公差, 应直接标注毛坯件基本尺寸的后面,如95±1.1. 特殊要求的公差可比一般公差
高或低.一般情况下不能低于1-176 小批单件毛坯尺寸公差.plb规定的公差等级围,当要求的
应力后再继续焊满坡口, 最后再做一次消除应力热处理.补焊大型或碳当量(碳当量的计算见本标
准附录A)超过0.4%的铸钢件的缺陷时, 在补焊后应立即入炉进行消除应力的热处理.
8.设计人员根据铸件的技术要求填写下表,并将此表贴在铸件图样的右上部.
(铸件技术要求) :
通用技术要求
JB/ZQ4000.5
铸件尺寸公差要求
CT
密封试验
是/否
耐压试验
是/否
注:表中空格中可补充其它技术要求.
3、焊接件通用技术要求(JB/ZQ400.3-86)
1.焊接结构件的长度尺寸公差见1-245c尺寸和形位公差数值.plb,适用于焊接零件和焊接组件的长度尺寸. 焊接件
的直线度.平面度和平行度公差见 1-245c尺寸和形位公差数.plb,焊接结构件的尺寸公差与形位公差等级选用见
二、锻件组别:Ⅱ
1.组别的基本标志
1)检验特性: 测定每批中锻件的硬度.
2)组成批的条件:
根据同一规进行热处理的同一钢号的锻件.
2.验收时的必要力学性能指标: HB
3.试验方法
1)力学性能: -
2)硬度: 每批中试验5%,但不少于5件.
三、锻件组别:Ⅲ
1.组别的基本标志
1)检验特性: 测定每一锻件的硬度.
常用齿轮钢材的调质热处理工艺
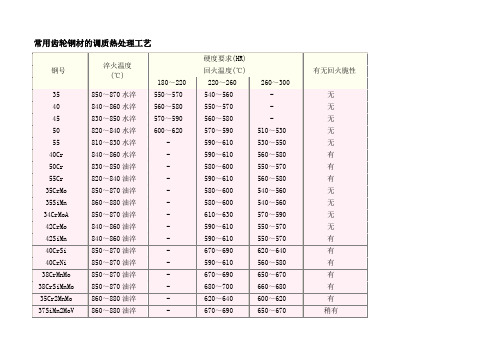
常用齿轮钢材的调质热处理工艺
常用大型锻件用钢的正火、高温回火温度3
热装炉过冷、正火、高温回火
工具钢锭制件锻后热处理
热装炉正火、高温回火(Ⅰ组钢过冷400~500℃,Ⅱ、Ⅲ组钢350~400℃)
曲轴感应加热淬火常见缺陷及防止方法
钢的退火工艺分类及应用
加热速度及保温时间
退火工件一般是随炉加热,加热速度不会太高。
为防止及热过程中开裂,高合金大件退火时,在700℃ 以下加热速度应为30~70℃/h ,温度超过750℃后增大为80~100℃/h 。
正或工件厂采用热炉装料,大型工件应注意控制装料时的炉温。
保温时间决定于钢的化学成分、炉温、装炉方式及装炉量,一般可按1.5~2.5min/mm(厚度或直径)估算。
钢件完全退火工艺规范
常用结构钢退火及正火工艺规范
常用工具钢退火及正火工艺规范
退火及正火缺陷
Fe-Fe3C合金相图Fe-Fe3C合金相图描述
Fe-Fe3C合金相图的特性点
Fe-Fe3C合金相图的特性线
铁碳合金常用临界温度代号。
齿轮锻钢件技术要求

齿轮锻钢件技术要求
齿轮锻钢件的技术要求包括以下几个方面:
1. 余量尺寸:齿轮锻件余量尺寸应符合国家标准。
2. 锻造比:齿轮锻件在锻造中要保证合适的锻造比,不得使用尺寸近似的圆钢锻打。
3. 材质:齿轮锻件的材质应与零件的材质一致,化学成分应符合国家标准,并出具材质单。
4. 温度:要保证正常的锻打温度,不能低温锻打或过烧。
5. 外形:锻件外形要整齐、均匀,不允许有叠皮、断裂等锻造缺陷。
6. 精度:齿轮的精度对齿轮传动性能和使用寿命有着重要影响。
根据齿轮使用场合的不同,需要选择不同精度等级的齿轮。
7. 齿面硬度:齿轮齿面硬度是根据工作载荷和转速等因素来确定的,不同硬度的齿轮适用于不同的工作条件。
8. 润滑油:齿轮传动需要润滑油,以减少齿面磨损和摩擦阻力,提高齿轮使用寿命。
9. 热处理:齿轮需要进行热处理,以改变其内部组织结构,提高其力学性能和耐久性。
10. 清洁度:齿轮应保持清洁,以防止杂质和污物对齿轮传动造成不良影响。
11. 防锈处理:齿轮应进行防锈处理,以防止其生锈和腐蚀。
以上是齿轮锻钢件的一些主要技术要求,这些要求需要根据具体的工作条件和使用要求来制定。
同时,还需要根据具体情况进行相应的实验和测试,以确保齿轮锻钢件的质量和可靠性。
锻件通用技术要求
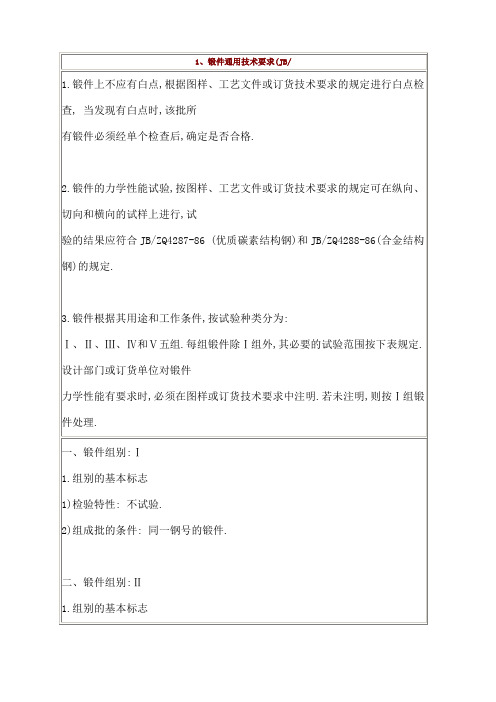
4、涂装通用技术条件(JB/
1.涂装前对物体的表面要求应符合本标准的规定.
2.除锈后的金属表面与涂底漆的间隔时间不得大于 6h,酸洗处理表面与第一次涂底漆时间不少
于 48h,但无论间隔时间多少,涂漆前表面不得有锈蚀或污染.
3.铆接件相互接触的表面, 在联接前必须涂厚度30-40μm防锈漆.由于加工或焊接损坏的底漆,
4.由平炉钢制造的低碳钢结构件, 可在任何温度下进行焊接.但为了避免焊接过程产生裂纹及脆性断裂, 厚度较大的焊
接件,焊削必须根据工艺要求,进行预热和缓冷. 板厚超过30mm的重要焊接结构,焊后应立即消除内应力,消除内应力
采用550-600℃回火,或200℃局部低温回火.
5.普通低合金结构钢制造的焊接件,必须按照焊接零件的碳当量和合金元素含量、零件的厚度、 钢结构件的用途和要求
2)组成批的条Leabharlann :?共同进行热处理的同一钢号的锻件.
2.验收时必要力学性能指标: HB
3.试验方法:
1)力学性能: -
2)硬度: 每一锻件均受试验.
四、锻件组别:Ⅳ
1.组别的基本标志
1)检验特性:?
测定每一锻件的硬度和每一批中的力学性能.
2)组成批的条件:
共同进行热处理的同一炉号的锻件.
2.验收时的必要力学性能指标:?
率在齿长和齿高方向上均不得低于50%,研合时可用0.05mm的塞尺检查齿侧隙,塞尺不得插入全齿长.
8.锥轴伸与轴孔配合表面接触应均匀, 着色研合检验时其接触率不得低于70%.
9.各类联轴器技术要求及轴向(△X)、径向(△Y)与角向(△α)的许用补偿量,应符合有关联轴器标准的规定.
10.轴承外圈与开式箱体或轴承座的各半圆孔间不准有"夹帮"现象,各半圆孔的"修帮"尺寸,不准超过下表规定的最大值.
- 1、下载文档前请自行甄别文档内容的完整性,平台不提供额外的编辑、内容补充、找答案等附加服务。
- 2、"仅部分预览"的文档,不可在线预览部分如存在完整性等问题,可反馈申请退款(可完整预览的文档不适用该条件!)。
- 3、如文档侵犯您的权益,请联系客服反馈,我们会尽快为您处理(人工客服工作时间:9:00-18:30)。
---------------------------------------------------------------最新资料推荐------------------------------------------------------ 0245-001调质齿轮锻件技术条件工工艺技术文件调质齿轮锻件技术条件0245-001 编制审核批准总工程师沈阳鼓风机(集团)公司沈阳透平机械股份有限公司二 O O 四年十一月调质齿轮锻件技术条件 1 适用范围本技术条件适用于经调质处理使用的合金结构钢锻件,这些锻件供制造离心鼓风机和离心压缩机变速机齿轮及齿轮联轴器内、外套之用。
本技术条件做为上述锻件的采购、验收、制造标准,当与产品设计图样和产品专用工艺文件有矛盾时,按产品设计图样和产品专用工艺文件的规定执行。
2 引用标准 GB3077 合金结构钢技术条件 GB222 钢的化学分析用试样取样法及成品化学成分允许偏差 GB/T22
3 钢铁及合金化学成分分析方法GB228 金属材料室温拉伸试验方法GB/T229 金属夏比缺口冲击试验方法 GB231 金属布氏硬度试验方法 JIS G0555 钢中夹杂物含量的显微镜试验方法 JIS G0551 钢中奥氏体结晶粒度的试验方法 ITN02151 锻件、冲压件及轧材超声波探伤方法 3 技术条件 3.1 齿轮锻件用钢的牌号及化学成分见表1。
3.2. 冶炼:
锻件用钢允许在酸性平炉或电炉中冶炼,也可以采用能保证本技
1 / 6
术要求的其它冶炼方法。
表 1 齿轮用钢的化学成分 3.3 锻造:
在锻压时应使零件整个截面得到充分的锻造,其总锻造比不应少于 3,牌号化学成分(%) C Mn Si Cr Mo V Ni S P 35CrMo 0.32-0.40 0.40-0.70 0.17-0.37 0.80-1.10 0.15-0.25 0.030 0.03535CrMoV 0.30-0.38 0.40-0.70 0.17-0.37 1.0-1. 3 0.20-0.30
0.1-0.2 0.03 0.03542CrNiMo6 0.38-0.45 0.40-0.70 0.15-0.35
1.4-1.7 0.15-0.25 1.4-1.7 0.03 0.035并注意保持锻件的中心线与钢锭的中心线重合。
3.4 热处理:
锻件在锻后应进行起伏冷却,并在粗加工后进行调质处理。
表 2 齿轮用钢的力学性能注:
轴类齿轮取纵向试样;套类齿轮取切向试样 3.5 机械加工:
锻件应根据合同规定按粗加工图样规定进行粗加工(合同规定毛坯交货的锻件除外),并加工好探伤面,以备超声波探伤检验,在调质处理后,应按粗加工图样规定切取试样,轴类齿轮取纵向试样,套类齿轮取切向试样。
调质处理后的力学性能应符合表 2 之规定。
4 材料的检验和验收标准 4.1 化学分析:
4.1.1 钢厂应按 GB222 钢的化学分析用试样取样法及成品化学成分允许偏差,GB/T223 钢铁及合金化学成分分析方法对每一炉次
---------------------------------------------------------------最新资料推荐------------------------------------------------------
钢水进行化学分析,以确保表 1 所列的化学成分要求。
在化学成分超出规定范围时,由双方协商研究决定。
4.1.2 锻件进厂后进行化学成分核查分析,一般同冶炼炉次抽检一件进行定量分析,其余采用定性分析,当发生疑问时可取双倍试样进行定量分析,化学成分分析结果应存挡备查。
4.2 力学性能试验:
4.2.1 锻件经调质处理后测定硬度,硬度之绝对值作为质量合格与否的依据,硬度合格后,按粗加工图样规定切取试样,每套力学性能试样包括一个拉伸试样和强度等级推荐用钢有效厚度(mm)力学性能(不低于)硬度 HB 备注 R P0。
2 MPa R m MPa A % Z % Aku2 J5 35CrMo 150 490 660 12 35 39 230260 5 35CrMo 151-300 490 660 12 35 31 230260 10 35CrMoV 150 735 845 12 35 39 269302 10 35CrMoV 151-300 735 845 12 35 31 269302 纵向 Aku2=39J10 42CrNiMo6 300 735 845 12 35 39 269302 两个冲击试样。
4.2.2 力学性能试验应按 GB228 规定进行。
用五倍的圆截面试样作拉伸试验,按GB/T229 规定用尺寸为101055mm,工作剖面为 810mm 之梅氏试样做冲击试验。
拉伸及冲击试验的结果应符合表 2 之规定。
4.2.3 力学性能试验如有一个试样不合格时,应取该试样相邻的两个试样重试,重试的结果数据全合格则视为合格。
3 / 6
若仍有不合格者,则视为不合格,对于不合格者必须经有关部门研究后,方可使用。
力学性能不合格的锻件,允许重新进行热处理。
重新热处理后的锻件,应按新的锻件取样试验。
4.3 无损检测 4.3.1 超声波探伤检验:
每一个齿轮锻件在粗加工后均应进行超声波探伤检验,轴类零件沿整个轴之径向进行,套类及盘类零件在端面进行,其检测结果必须符合下述规定:
4.3.1.1 当发现肯定有白点和裂纹则报废。
4.3.1.2 锻件允许缺陷按下述规定进行检验:
对低速大型齿环锻件,齿环外圆及内孔 200mm 宽度区域按 I 级评定,中间区域按 II 级评定。
其他齿轮锻件均按 I级评定。
4.3.1.3 当发现超过 4.3.1.2 项规定时,应由双方共同研究协商解决。
4.3.1.4 缺陷超标的锻件由总工程师批准,方可使用。
表 3 超声波探伤检验标准注:
A%:
当出现缺陷时,底波减少的百分比。
d%:
缺陷波高与无缺陷时底波高的百分比。
级别 I II A(%) 0 10 d(%) >10 510 <5 >20 1020 <10
---------------------------------------------------------------最新资料推荐------------------------------------------------------
F(mm) >4 24 1.5F<2 >5 45 2F<4N(个数) 0 4 10 0 4 10 D(mm) 100 80 80 80 N:
可接受的缺陷数 D:
缺陷之间的距离 F:
缺陷当量尺寸,F 值为换算值仅供参考。
4.3.2 磁粉探伤:
每一个齿轮锻件在精加工后均应进行磁粉探伤检验。
磁粉探伤采用交流连续法,电流 I=10D。
检查结果必须符合下述规定。
4.3.2.1 如发现肯定有白点和裂纹则报废。
4.3.2.2 允许的缺陷应符合表 4 规定的 II 级以内。
表 4.磁粉探伤的缺陷等级分类缺陷等级线状缺陷圆状缺陷允许缺陷个数* 2 发纹* 1 其它 I 无无<1 3 个以下/100mm100mm II <4mm 无 1-2 5 个以下/100mm100mm 注:
*1 这里指非金属夹杂物、气孔等经过锻轧而形成的线状缺陷。
*2 0.5mm 以下的磁痕不计入缺陷个数 4.3.2.3 如发现超过4.3.2.2 项规定时,应由有关技术部门研究后,由总工程师决定。
4.4 表面缺陷及尺寸:
锻件表面不允许有裂纹、伤疤等缺陷,局部缺陷允许铲除。
其深度必须满足本公司提供的粗加工图的要求。
5 / 6
5 交货状态、验收项目及书面文件 5.1 锻件交货状态由本公司与钢厂有关技术部门研究协商决定。
并签订相应的交货及验收技术条件。
5.2 锻件从冶炼到精加工磁粉探伤结束的整个制造过程,均应按本技术条件规定程序及标准进行检验,并提出书面文件,所提出的书面文件应包括表 5 规定的各项检验结果。
表 5 检验项目及结果一览表序号检查项目检验指标及结果 1 化学分析 2 力学性能检验 3 金相检验 4 超声波探伤检验 5 磁粉探伤检验 6 表面缺陷及尺寸。