聚合反应器技术及应用
聚合反应工程

聚合反应工程的重要性
01
02
03
工业生产
聚合反应是工业生产中重 要的化学反应之一,广泛 应用于塑料、橡胶、纤维、 涂料等领域。
新材料开发
通过聚合反应工程可以开 发新型高分子材料,满足 各种特殊需求,如高性能、 低成本、环保等。
优化生产过程
聚合反应工程研究有助于 优化聚合反应过程,提高 生产效率和产品质量,降 低能耗和物耗。
备的长期稳定运行。
04
聚合反应工程应用
高分子材料合成
高分子材料合成
聚合反应工程在合成高分子材料方面 具有广泛应用,如合成塑料、合成橡 胶和合成纤维等。
合成橡胶
聚合反应工程在合成橡胶方面也发挥 了重要作用,如合成丁苯橡胶、合成 橡胶等,这些橡胶在汽车、航空航天 和建筑等领域有广泛应用。
塑料合成
通过聚合反应工程,可以合成各种类 型的塑料,如聚乙烯、聚丙烯、聚氯 乙烯等,这些塑料在日常生活中有着 广泛的应用。
案例分析
以涤纶合成为例,通过聚酯聚合反应,对苯 二甲酸和乙二醇在催化剂的作用下发生聚合, 最终形成高分子量的聚酯。该案例中,聚合 反应工程的关键在于反应速度的控制和聚酯 的分子量调节。
涂料与粘合剂应用案例
涂料与粘合剂应用
聚合反应工程合成的涂料和粘合剂具有良好的粘附性、耐久性和绝缘性,广泛应用于建 筑、电子、航空航天等领域。
橡胶的性能改进
通过聚合反应工程,可以改进橡胶的 性能,如提高橡胶的耐热性、耐油性 和耐老化性等。
合成纤维
纤维的合成
聚合反应工程在合成纤维方面具有重要作用,可以合成各种类型 的纤维,如涤纶、尼龙、腈纶等。
纤维的性能改进
通过聚合反应工程,可以改进纤维的性能,如提高纤维的强度、耐 磨性和抗皱性等。
尼龙聚合反应器

尼龙聚合反应器
尼龙(Nylon)聚合反应器是用于合成尼龙聚合物的反应设备。
尼龙是一类合成纤维和塑料的通用名称,它们属于聚酰胺类聚合物。
尼龙聚合通常包括以下主要步骤:
原料准备:
原料通常包括二元或多元胺(如己二胺)和二元或多元酸(如己二酸)。
这些原料在反应器中按照一定的比例准备。
酸胺反应:
首先进行酸胺反应,通过在反应器中加热和混合,使胺和酸发生缩合反应,生成酰胺链段。
缩聚反应:
在酸胺反应后,通过缩聚反应,将酰胺链段连接成大分子聚合物。
这一步骤通常需要一定的温度和压力。
聚合物化学处理:
完成缩聚反应后,进行聚合物的化学处理,例如中和、清洗等步骤,以确保产物的质量。
升温和固化:
最后,将聚合物升温至一定温度,使其进一步固化和定型。
这通常包括拉伸、定型等步骤,以得到所需的尼龙产品形态。
在尼龙聚合反应器中,控制温度、压力和反应物质的比例是关键的操作参数。
这些参数的调节可以影响尼龙聚合物的分子结构、物理性质和用途。
此外,现代尼龙聚合反应器通常配备先进的自动化控制系统,以确保生产的高效、稳定和可控。
PET聚合反应器建模及在聚合流程动态模拟中的应用
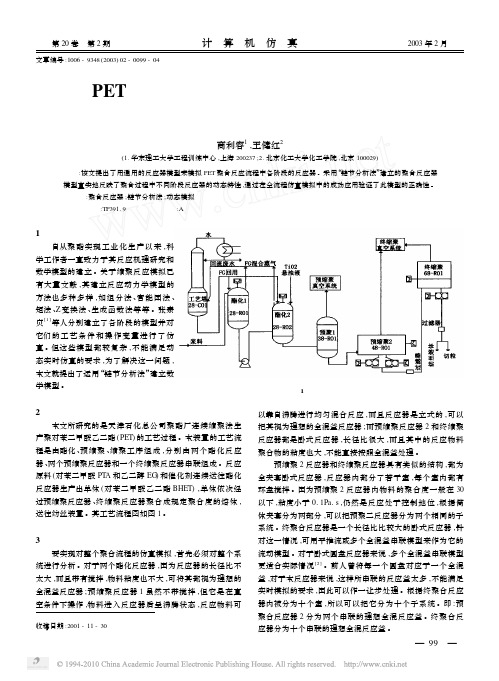
表 1 模型所用动力学参数表
酯化一 k1 酯化二 k2 缩聚反应 k3 生成 DEG的反应 k4 热降解 k7 热降解 k8
活化能 kcal/ mol
17. 6 17. 6 18. 5 29. 8 37. 8 29. 8
指前因子 平衡常数
L/ mol . min
4. 985 ×106 4. 985 ×106 3. 259 ×106 4. 16 ×107 5. 4 ×109 4. 16 ×107
第 20 卷 第 2 期 文章编号 :1006 - 9348 (2003) 02 - 0099 - 04
计 算 机 仿 真
2003 年 2 月
PET 聚合反应器建模及在聚合流程动态 模拟中的应用
商利容1 ,王健红2
(1. 华东理工大学工程训练中心 ,上海 200237 ;2. 北京化工大学化工学院 ,北京 100029)
(PTA) 的对称结构 ,根据前人的经验[3] : PTA 也可看成是小分 子的 PET ,因而仍可用“链节分析法”对其进行分析 。
体系内“活性链节”有两种 : 1) —Ф—COOCH2 CH2OH 2) —Ф—COOH 体系内“死链节”为 : —Ф—COOCH2 CH2OOC —Ф— 这样该体系就由端羧基 Ea ( —Ф—COOH) 、端羟基 Eg ( —Ф— COOCH2 CH2OH) 、死链节 Z ( —Ф—COOCH2 CH2OOC —Ф—) 、 游离 EG( HOCH2 CH2OH) 、游离水 W( H2O) 、乙醛 A (CH3CHO) 、 乙烯基 Ev ( —Ф—COOCH = CH2) 、二甘醇基 DEG(包括 DEG 链 节 在 聚 酯 内 部 的 —Ф—COOCH2 CH2OCH2CH2OOC —Ф—、 DEG链节在端部的 —Ф—COOCH2 CH2OCH2 CH2OH 和游离的 DEG ( HOCH2 CH2OCH2 CH2OH) ) 八种组分组成 。 412 建立链节反应动力学 运用“链节分析法”所确定的组分写出整个的反应网络
连续聚合反应器-概述说明以及解释

连续聚合反应器-概述说明以及解释1.引言1.1 概述连续聚合反应器是一种在化学工业和研究领域中广泛应用的反应器。
它具有连续、高效、可控的特点,被广泛用于聚合反应的过程中。
与传统的批量聚合反应器相比,连续聚合反应器具有许多优势。
在连续聚合反应器中,原料通过连续流动的方式输入,反应产物也通过连续的方式输出。
这种流动式的操作方式使得反应更加均匀,能够有效地控制反应的温度、压力和物料的混合程度。
此外,由于反应物料的连续供应,连续聚合反应器具有较高的反应速度和产能,能够满足大规模生产的需求。
连续聚合反应器在聚合反应过程中还具有很好的控制性能。
通过合理设计反应器的结构和控制参数,可以实现对反应速率和产物分布的精确控制。
同时,连续聚合反应器还能够方便地与其他单元操作进行集成,实现多步反应的一体化操作,进一步提高了反应的效率和产物质量。
由于连续聚合反应器具有以上种种优势,因此在聚合反应领域得到了广泛的应用。
例如,连续聚合反应器可以用于合成高分子材料,如聚合物和纳米材料,以满足各种领域的需求,如塑料制品、涂料、医用材料等。
此外,连续聚合反应器还可以应用于制备有机化合物和药物等领域,为实现高效、低成本的生产提供了新的思路和技术支持。
总之,连续聚合反应器是一种具有连续、高效、可控等优势的反应器。
它在化学工业和研究领域的应用前景广阔,并且具有很大的发展潜力。
随着科学技术的不断进步和人们对高效、环保工艺的需求不断增加,连续聚合反应器必将在未来发展中发挥更加重要的作用。
1.2 文章结构文章结构部分应该对整篇文章的结构和每个章节的内容进行简要介绍,方便读者了解文章的组织和主要论点。
具体如下所示:第2部分正文将主要介绍连续聚合反应器的定义、原理、优点和应用。
在2.1节中,将详细介绍连续聚合反应器的定义和原理,包括其基本概念、工作原理和特点。
2.2节将重点讨论连续聚合反应器的优点和应用领域。
通过分析其在化工生产、药物合成和材料制备等领域的具体应用案例,展示连续聚合反应器在提高反应效率、降低能耗和减少废物排放等方面的显著优势。
(优选)聚合反应器的分类介绍

3.卧式搅拌反应器 该型式可设置多个搅拌器,每个搅拌器之间
用隔板分开,使物料在反应器内流动状况类似 于多级串联搅拌反应器,从而减少设备台数, 降低安装高度。
同时由于聚合反应器内物料粘度高、易结垢,因而要求传热速率高、结构简 单、避免易挂料的粗糙面及导致结垢的死角并易于清洗。
聚合反应器常用的传热装置型式有夹套传热、釜内传热件及釜外传热等。
1.夹套 根据工艺要求,夹套内可通入传热介 质(水、水蒸气或热载体等)。
为了提高夹套的传热系数,可通过提 高夹套传热介质的流速来实现,为此, 常在夹套内安装导流挡板。
优点:当设备较大时,搅拌轴可做成短而
细,稳定性好,且可降低安装高度。同时由 于把笨重的传动装置安装在地面基础上,从 而改善了釜体上封头的受力状态,也便于维 护与检修。
缺点:轴密封较困难,而且搅拌器下部
至轴封处常有固体物料粘积,影响产品的质 量,检修时需将釜内物料全部排净。该型式 较常用于大型搅拌设备。
1.以液体粘度和反应釜体积为依 据选型
右图为在较合理搅拌功率消耗下, 物料粘度与反应体积的关系图。图 中表示各种叶轮适用范围。
2.以流动状态、搅拌目的为依据选型 下表就列出了根据流动状态和搅拌目 的来选择搅拌器。
三、传热装置
化学反应过程伴有放热或吸热,对聚合反应而言,往往要求严格控制反应温 度,使其恒定或按一定的温度曲线进行。
其他型式的搅拌反应器
1. 偏心式搅拌反应器 偏心式搅拌反应器是搅拌器中
心偏离容器中心。由于其搅拌轴偏 离容器的中心轴线,使流体在各点 所受的压力不同,因而液层间的相 对运动加强,增加液层的湍动,明 显提高搅拌效果。但容易引起振动, 故一般多用于较小型设备。
2.底部传动搅拌反应器
第八章 聚合过程及聚合反应器
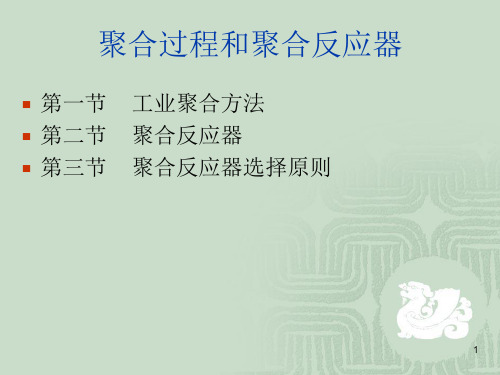
2.悬浮聚合
悬浮聚合产品的纯度高,工艺过程的简单程
度仅次于本体聚合。 主要缺点为: (1)不易实现连续化 主要原因是聚合物粒 子在一定的转化范围内是发粘的,易于粘在 反应器的壁面,通过搅拌可以防止或减轻粘 壁。 而在连续悬浮聚合时,釜与釜间输送物 料的管道由于没有搅拌,粒子很易粘于管壁, 最终堵塞管道,使操作无法进行。
11
3.乳液聚合
单体在水介质中,由乳化剂分散成乳液状态进行的
聚合,称为乳液聚合。 乳液聚合是在乳胶粒中进行反应,反应速率高,产 物聚合度高,乳液聚合也是用水作连续相,所以传 热问题也易于解决。但为了稳定乳液,必须在聚合 体系中加入多种配合剂,而又有些配合剂很难从产 物中去除,故乳液聚合的产品适用于制品纯度要求 不高的场合。 乳液聚合时,链自由基处于孤立隔离状态,长链自 由基很难彼此相遇,以致自由基寿命较长,终止速 率较小,因此聚合速率高,且可获得高的分子量。
17
1.釜式聚合反应器
釜式聚合反应器是一种形式多变的聚合装置,它广
泛应用于低粘度的悬浮聚合过程,乳液聚合过程。 也能用于高粘度的本体聚合和溶液聚合过程。从操 作方式看它能进行间歇、半连续、单釜和多釜连续 操作,以满足不同聚合过程的要求。为了保证釜中 物料的流动、混合与传热,液滴的分散或固体物料 的均匀悬浮,釜中设有搅拌装置。。 对低粘度系统主要使用平桨式、推进式、涡轮式、 三叶后掠式及布鲁马金式桨叶,当与各类挡板配合 使用时可获得所需的剪切与循环作用。对高粘度体 系主要使用锚式、螺带、带导流筒的螺杆桨叶以及 特殊型式的浆叶。
16
第二节 聚合反应器
在高分子合成工业中,根据聚合反应体系的
特征和对产品高质量的要求,可以采用多种 型式的聚合反应器。 聚合反应器按其型式可分为釜式、塔式、管 式和特殊型四种。在聚合物产生中约有70% 采用搅拌釜,这是应用最广泛的聚合反应器。 而塔式,特殊型聚合反应器则主要用于高粘 度聚合体系中。
各种反应器特点优缺点及应用
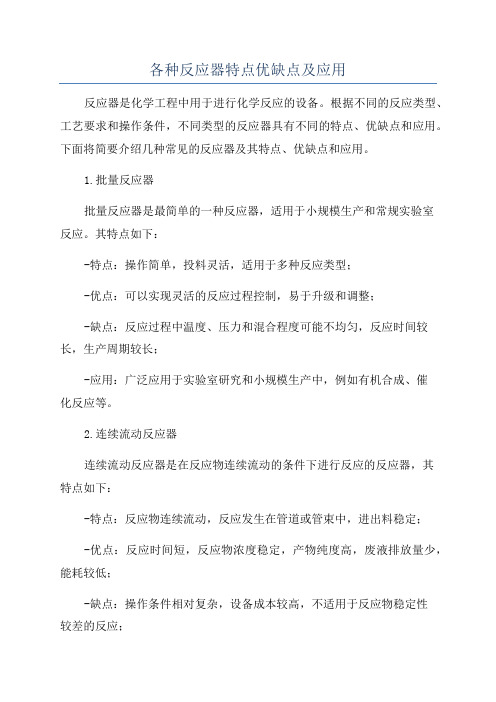
各种反应器特点优缺点及应用反应器是化学工程中用于进行化学反应的设备。
根据不同的反应类型、工艺要求和操作条件,不同类型的反应器具有不同的特点、优缺点和应用。
下面将简要介绍几种常见的反应器及其特点、优缺点和应用。
1.批量反应器批量反应器是最简单的一种反应器,适用于小规模生产和常规实验室反应。
其特点如下:-特点:操作简单,投料灵活,适用于多种反应类型;-优点:可以实现灵活的反应过程控制,易于升级和调整;-缺点:反应过程中温度、压力和混合程度可能不均匀,反应时间较长,生产周期较长;-应用:广泛应用于实验室研究和小规模生产中,例如有机合成、催化反应等。
2.连续流动反应器连续流动反应器是在反应物连续流动的条件下进行反应的反应器,其特点如下:-特点:反应物连续流动,反应发生在管道或管束中,进出料稳定;-优点:反应时间短,反应物浓度稳定,产物纯度高,废液排放量少,能耗较低;-缺点:操作条件相对复杂,设备成本较高,不适用于反应物稳定性较差的反应;-应用:广泛应用于底物稳定性较好的化学反应,如合成化学和催化反应等。
3.管式反应器管式反应器是一种连续流动反应器,具有管状结构,反应物在管内流动进行反应。
其特点如下:-特点:反应物在直管中流动,具有较大的接触面积和较高的传热效率;-优点:反应时间短,反应速度快,能够实现高温反应和高压反应;-缺点:管内积垢和堵塞的问题较突出,操作不够灵活,难以对反应过程进行调控;-应用:广泛应用于有机合成、聚合反应、氧化反应等。
4.搅拌式反应器搅拌式反应器是一种常见的批量反应器,其特点如下:-特点:反应物在搅拌器的作用下进行混合和反应;-优点:能够实现较好的混合程度,反应均匀,温度、压力和浓度控制相对容易;-缺点:能耗较高,产物分布不均匀,反应速率受到混合效果的影响;-应用:广泛应用于有机合成、聚合反应、酯化反应等。
5.固定床反应器固定床反应器是将催化剂固定在固体床上进行反应的反应器-特点:催化剂固定,反应物流经固体床进行反应;-优点:反应过程相对稳定,操作简单,可以持续生产较长时间;-缺点:反应物质传质受到限制,催化剂活性容易降低,床层温度不易均匀;-应用:广泛应用于催化反应,如重油加氢、氯化反应等。
聚合反应器介绍
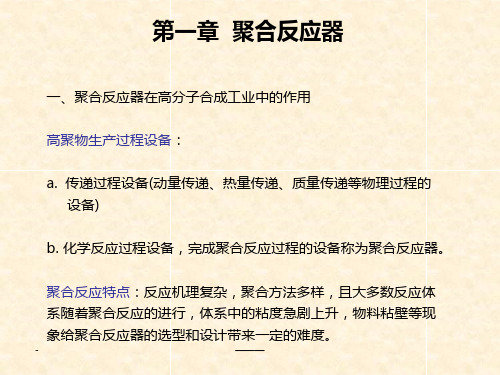
———
2.以流动状态、搅拌目的为依据选型 表1—I列出了根据流动状态和搅拌目的 来选择搅拌器。
———
(三)搅拌附件
为了消除釜内液体的打漩现象,可在 反应釜内设置挡板。挡板的作用是将 切向流动转变为轴向和径向流动,增 大被搅动液体的湍动程度,从而改善 搅拌效果。
此外在聚合物的生产过程中,除聚合反应器外,还有许多带 搅拌装置的容器(如原料配制槽、溶解槽、浆料配制槽、沉 析槽等)。
———
2.管式(塔式)反应器 管式(塔式)聚合反应器的构造比较简单, 这种反应器一般用于处理粘度较高的均相反应物料。它属于连续 流动反应器,原料从管的一端连续送入,在管内完成升温、反应 等,而产物和未反应的单体从另一端连续排出。
———
———
2.锚式(框式)搅拌器 对于粘度较大的液体搅拌,可把桨叶形状做成与反应釜底部的形状相似,
且桨叶与釜壁的隔隙小。 锚式搅拌器的转速比较低,故剪切作用较小,但搅动范围大,不易产生死
区。对高粘度流体的搅拌,可利用桨叶的刮扫作用来防止搅拌器与釜壁之间 产生滞流层,利于促进传热和去除釜壁沉积物。 当锚式搅拌器中间加设横梁或竖梁时,即称为框式搅拌器。
当搅拌浆料时,挡板与釜壁之间应留 1/6板宽的空隙,以防止固体物料的 沉积。如有必要,挡板也可做成空心 状,内部能通入传热介质,既可改善 搅拌效果,又增加传热面积。
———
2.导流筒 无论采用何种型式的搅拌器,釜内液体总是从各个方向流向搅拌器,所 以不同的液体行程长短不一.在需要控制回流的速度和方向以确定某一特定流型时, 可在反应器内设置导流筒。导流筒一般是一个圆筒,安装在搅拌器的外面或上方。
———
第二节 搅拌釜式反应器
- 1、下载文档前请自行甄别文档内容的完整性,平台不提供额外的编辑、内容补充、找答案等附加服务。
- 2、"仅部分预览"的文档,不可在线预览部分如存在完整性等问题,可反馈申请退款(可完整预览的文档不适用该条件!)。
- 3、如文档侵犯您的权益,请联系客服反馈,我们会尽快为您处理(人工客服工作时间:9:00-18:30)。
聚合反应器技术及应用31聚合反应工艺及设备分类;郝静祖;摘要:以聚乙烯为例简单介绍了聚合反应的工艺流程,;1、聚合反应工艺流程及主要控制回路简介;聚合反应机理复杂,是强放热反应,过程具有大滞后、;其一般流程图如下:;图1聚合反应流程图;系统主要由聚合反应器(C4001)、循环汽冷却器;以聚乙烯合成为例[1],聚合反应在硫化床反应器(;温度控制回路,主要依靠进入反应器入口的循环汽温度聚合反应工艺及设备分类郝静祖摘要:以聚乙烯为例简单介绍了聚合反应的工艺流程,及聚合反应器的一般分类关键词:聚合反应器聚合反应1、聚合反应工艺流程及主要控制回路简介聚合反应机理复杂,是强放热反应,过程具有大滞后、大惯性、非线性等特性。
温度、压力、浓度及催化剂的活性与牌号等都对化学平衡产生重要影响。
其中,反应器床层温度对产品的质量、产率影响最大。
其一般流程图如下:图1 聚合反应流程图系统主要由聚合反应器(C4001)、循环汽冷却器(E4002)和循环汽压缩机组成。
反应循环汽体在压缩机的作用下,连续经过被硫化的树脂反应床和冷却器,同时移走反应产生的热量。
冷却器是单程壳式换热器,汽体走管程,调温水走壳层。
以聚乙烯合成为例[1],聚合反应在硫化床反应器(C4001)中进行,反应压力为2.1MPa,反应温度88℃左右,具体数值视产品牌号而定。
反应用料乙烯、H2、T2、CH及其共聚单体等从反应器底部加入,一部分转化为聚乙烯,大部分单体和共聚单体从反应器顶部作为循环汽又返回到反应器。
循环汽冷却器(E4002)的调温水由水泵加入,从循环器冷却器出来的调温水带出大量的热量。
催化剂Cat 来自加料器STC4036。
反应器有两套出料循环系统,一路排出料粉进入出料缸C4101,另一路从塔顶排出,循环反应。
温度控制回路,主要依靠进入反应器入口的循环汽温度来调节,循环汽的温度由冷却水流量控制,而水流量的控制为分程控制。
控制系统结构为串级控制,主调节器4001T26,副调节器4001T46。
循环汽流量控制:反应器流量由4001FIC检测并发出调节信号给入口导向阀4003FV,通过调节入口导向阀的开度来控制循环汽流量。
反应器温度400126.PV在负荷平稳、催化剂加料均匀、活性好的情况下基本能维持稳定的正常88℃±1℃。
当工况负荷有变化,或其它未知扰动的影响时,会造成温度的大范围波动,甚至出现高高限报警。
如:由于产品牌号的变化,操作员为保证产品质量而改变催化剂加料量,一不小心就会导致聚合反应的剧烈变化,表现为反应器温度的剧烈波动。
另外,由于循环汽压泵的故障,常会引发循环汽流量的波动,而流量回路由于时间常数小,短时间即可恢复稳定,但由此而导致的反应器温度波动却迟迟不能恢复稳定,有可能会产生振荡。
总的来说,反应器温度控制通道具有大惯性、大滞后、非线性等特征,目前普遍采用的PID控制有不尽如意之处,有待改进。
2、聚合反应器以溶聚丁苯橡胶连续聚合工艺为线索,介绍了我国目前应用于聚合反应生产的反应器。
2.1连续聚合用反应釜采用相向两侧进料的反应釜[2],釜内设有轴向和径向搅拌器,搅拌速度35 0 r/min,4块挡板用来强化混合,适当改善物料在釜内的停留时间分布。
单体和引发剂溶液由湍流区相对两侧的入口管线的3个孔进入体系,从而防止新鲜引发剂直接与高浓度的单体接触,以便减轻挂胶及凝胶的生成;另外要在反应物料中加入适量1,2-丁二烯。
各种物料的组成(质量份)如下:单体溶液中丁二烯100,环己烷475,THF 0.04,1,2-丁二烯0.04;引发剂溶液中正丁基锂0.065,环己烷156。
聚合在126℃下连续进行502 h后,釜内残余的湿聚合物占釜内容积不到1%,将其取出干燥后测其质量仅占产胶量的百万分之一。
然而当进一步提高聚合温度或聚合物相对分子质量时,连续运转周期即明显缩短。
聚合体系物料混合的均匀程度对橡胶的质量有明显的影响,Asahi公司的专利[3]提出,聚合釜搅拌器的线速度与聚合液粘度之比宜控制在0.05以上。
单体溶液也宜由反应器的中部及底部两个部位加入,这样可以改进物料的混合程度,也有利于降低聚合物中嵌段聚苯乙烯的含量。
据专利报道[4],有一种外形为釜,而物料在其中走向为S形的环形反应器。
该反应器中央有一轴向转动的圆桶状搅拌器,单体和催化剂溶液在管道内混合后,进入冷剂环绕的中央管,然后进入转动搅拌器封闭端与热交换外壁之间的区域,在其中搅拌混合,然后依次在环行区下行和上行,最后离开聚合釜。
釜的夹套也通入冷剂。
这种反应器可减少物料的短路和返混,缩短物料在釜内的平均停留时间分布。
这种反应器有两大特点:一是反应速度快,停留时间短;二是传热面积大。
在此反应器中于74~116℃聚合,达到单体转化率92%时所需的物料停留时间只要5 min,此反应速度相当于一般聚合釜的7~8倍;圆桶状搅拌器的转速为787 r/ min。
容积为570 L的这种反应器有近7.4 m2的传热面积,比相同容积反应釜的传热面积大一倍多;在聚合过程中,反应热的25%被冷剂带走,其余靠物料温升平衡。
2.2单釜聚合与闪蒸匹配的系列工艺Firestone公司的专利[5]描述的这种系列工艺的具体过程如下:配比为75/25的丁二烯/己烷溶液(丁二烯含1,2-丁二烯1 000310-6)以及相当于单体质量的0.0 3%的BuLi己烷溶液以约33 m3/ h的流量连续进入反应器,反应温度和进入闪蒸槽的温度分别为121℃和132℃,闪蒸槽的压力为0~0.054 MPa。
闪蒸后反应系统中的聚合物浓度由17%提高到25%,闪蒸溶剂经冷凝后进入缓冲槽,然后经流量控制阀返回进料管线,这样有40%的溶剂不必再进行精制,从而可显著降低后处理过程蒸汽和水的消耗,而且聚合又能在单体浓度较低的条件下进行,有利于反应热的导出和减少交联物及凝胶的形成。
另外,5 0%~70%的未反应的1,2-丁二烯随循环的己烷回收使用并保持极纯的状态,提高了调节聚合物相对分子质量分布的能力。
此外,试验还发现,有将近10%~30%比溶剂轻的杂质以及大部分比溶剂重的杂质可从闪蒸槽流出的聚合物溶液中排出,这对系统维持物料平衡至关重要。
2.3聚合釜与其他类型反应器的结合搅拌式反应釜可与活塞流反应器结合使用,在反应釜中的单体转化率应大于95%,然后在活塞流反应器中完成聚合,以丁二烯负离子封端并完成偶联[6]。
搅拌式反应釜也可与静态混合器相结合。
以静态混合器充当净化器,除去反应物料中的有害毒物,然后送入反应釜[7]。
净化剂可选用碱金属、有机锂及其衍生物等。
净化器中形成的烃不溶物可用某些极性有机物如醛、酮、醚、酯等溶解。
操作中可采用并联的2个净化器切换使用。
采用净化工艺后,可更好地调控聚合物的相对分子质量,也可适当增大1,2-丁二烯的使用量,更好地抑制凝胶及挂胶的形成。
例如,采用2个直径为0.95 cm、长为28 cm的Kenics静态混合器作为净化器,在其后串联一容积为19 L的搅拌式反应釜,将1,2-丁二烯用量由占单体质量的0.05%提高到0.08%,连续聚合575 h,釜内无凝胶形成,所得SSBR的门尼粘度可达90~100。
净化剂为正丁基锂,清理剂用THF,每个净化器的操作周期为72 h,清理时间36~48 h,清理在常温下进行。
2.4管式与环管式聚合在管式聚合工艺中,环管式工艺已成功地应用于制备聚苯乙烯[8],在合成聚二烯烃橡胶方面也有尝试,所得SSBR的相对分子质量分布窄,凝胶含量少。
环管式聚合工艺的循环泵可采用齿轮泵或螺杆泵。
环管周围可设冷却夹套,以保持聚合恒温。
物料在管内的流速10~90 cm/s,物料循环比30~200,相对分子质量分布指数1.5~4.0。
雷诺数的大小则在很大程度上取决于聚合物溶液的粘度,雷诺数过低,易生成凝胶。
环管式反应器前后均安装混合器,以利于提高转化率和均化聚合物门尼粘度。
例如,在容积为16.6 L、内径为4.26 cm的套管式环管反应器内,连续加入丁二烯3.19 kg/h、苯乙烯0.56 kg/h、环己烷15.0 kg/h及正丁基锂0.04份,1,4-二氢苯0.037份、十二烷基苯磺酸钾0.020份(均以100质量份单体为基准),在9 0℃聚合;通过齿轮泵的物料循环量分别为500,1 000,4 000 L/h;聚合连续运转10 d后,单体转化率98%~99%,SSBR的门尼粘度97~99,系统中未发现有凝胶形成。
而采用类似工艺条件,在槽式或无循环物料流的管式反应器中操作,生成凝胶的程度就远比上述情况严重[9]。
环管式反应器所得橡胶的综合性能良好。
管式反应器的应用有很大的局限性,BASF公司的专利[10]述及采用长40 m、直径0. 2 m的反应管,在其前后均装设静态混合器,管的末端装有冷却夹套,以防止聚合物的热终止或热降解;反应管内压力约2 MPa;聚合物相对分子质量分布指数可通过引发剂的分流分点加入予以控制。
该专利报道,将精制的苯乙烯(8份)、丁二烯(16份)、环己烷(64份)、四氢呋喃(2份)混合溶液预热至3 5℃,按500 L/ min的速度加入该反应器中,同时加入仲丁基锂(3.2310-3mol/L),加入速度为0.5 L/min,聚合最高温度为144℃,所得SSBR的相对分子质量为1 623103,产率为5 732kg/(m32h),SSBR的生产能力为7.2 t/h。
在管式聚合中,可采用周期性地改变引发剂与单体比例的方法调节相对分子质量分布指数,但不影响门尼粘度[11]。
2.5螺杆挤出聚合工艺JSR,Bayer及Goodyear等公司均对螺杆挤出聚合工艺有研究,多采用多轴自清理式螺旋挤出反应器,有的在出口与入口之间设有循环装置。
例如,使用由进料、反应、输送和出料4段及冷凝回流装置组成的螺旋式挤出反应器[12],其中反应段的螺旋以具有棱形横截面者为佳,因为它可提供较充足的自由体积,有利于物料的蒸发冷凝回流;反应器内还应设有限流阀,以防止物料的逸出。
2个搅拌轴上下平行排列,用一对锥形止推轴承固定,进入反应段时设有液压油封。
2个长度分别为81 cm和122 cm的轴将反应器分成4个区:第一区为20 cm长的输送区,螺槽较深;第二区为53 cm长的反应区,轴上2.54 cm宽的叶片定向排列,相邻叶片的位差为15°;第三区为7. 6cm长的深槽输送段;第四区为出料段,系长40.6cm,直径5.1 cm的单螺杆,槽深0.23 cm,该螺杆直接连接在下部搅拌轴上。
整个反应器的夹套分为3段,头两段可加热或冷却,出料段的夹套则供冷却用。
反应段的总容积为6 L,其中2 L作为气相空间。
螺杆转速可在29~230 r/min的范围内调节,并用在线电压计监控功率消耗。