热塑性塑料的固化
热塑和热固

热固性塑料,多是以缩聚树脂为基料,加人填料、固化剂以及其他添加剂制取而成。
热塑性塑料,以聚合树脂或缩聚树脂为基料,加人少量的稳定剂、润滑剂或增塑剂,加或不加填料制取而成。
热固性指加热时不能软化和反复塑制,也不在溶剂中溶解的性能,体型聚合物具有这种性能。
热塑性是指物质在加热时能发生流动变形,冷却后可以保持一定形状的性质。
热固性塑料,性能特点是:在一定的温度下,经过定时间的加热或加人固化剂后,即可固化成型。
固化后的塑料质地坚硬、性质稳定,不再溶于溶剂中,也不能用加热方法使它再软化,强热则分解、破坏。
优点是:无冷流性、抗蠕变性强,受压不易变形;耐热性较高,即使超过其使用温度极限,也只是在表面产生碳化层而不失去其原有骨架形状。
缺点是:树脂性质较脆、机械强度不高,必须加入填料或增强材料以改善性能,提高强度;成型工艺复杂,大多只能采用模压或层压法,生产效率低。
热塑性,性能特点是:受热软化、熔融,具有可塑性,可塑制成定形状的制品,冷却后坚硬;再热又可软化,塑制成另形状的制品,可以反复重塑,而其基本性能不变。
优点是:成型工艺简便,形式多种多样,生产效率高,可以直接注射或挤压吹塑成所需形状的制品,而且具有一定的物理力学性能。
缺点是:耐热性和刚性都较差,最高使用温度般只有120°C左右,使用时不能超过温度极限,否则就会引起变形。
氟塑料、聚铣亚胺,聚苯并咪嗟各有其突出的性能,如优良的耐腐询、露温高绝缘、低摩擦因数等。
热塑性塑料成型的特性
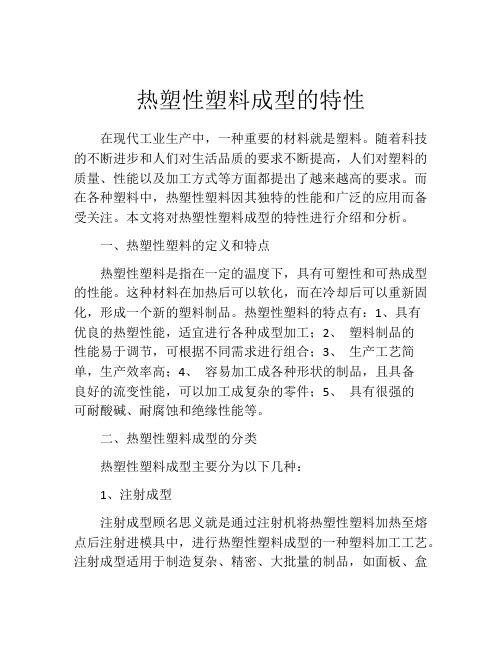
热塑性塑料成型的特性在现代工业生产中,一种重要的材料就是塑料。
随着科技的不断进步和人们对生活品质的要求不断提高,人们对塑料的质量、性能以及加工方式等方面都提出了越来越高的要求。
而在各种塑料中,热塑性塑料因其独特的性能和广泛的应用而备受关注。
本文将对热塑性塑料成型的特性进行介绍和分析。
一、热塑性塑料的定义和特点热塑性塑料是指在一定的温度下,具有可塑性和可热成型的性能。
这种材料在加热后可以软化,而在冷却后可以重新固化,形成一个新的塑料制品。
热塑性塑料的特点有:1、具有优良的热塑性能,适宜进行各种成型加工;2、塑料制品的性能易于调节,可根据不同需求进行组合;3、生产工艺简单,生产效率高;4、容易加工成各种形状的制品,且具备良好的流变性能,可以加工成复杂的零件;5、具有很强的可耐酸碱、耐腐蚀和绝缘性能等。
二、热塑性塑料成型的分类热塑性塑料成型主要分为以下几种:1、注射成型注射成型顾名思义就是通过注射机将热塑性塑料加热至熔点后注射进模具中,进行热塑性塑料成型的一种塑料加工工艺。
注射成型适用于制造复杂、精密、大批量的制品,如面板、盒子、齿轮、模头等。
这种成型方式可以确保制品准确度高,生产效率高。
2、吹塑成型吹塑成型是一种通过将加热到一定温度的热塑性塑料挤出模具进行成型的过程。
与注射成型不同的是,吹塑成型往往用于生产中空制品,如瓶子、桶、塑料球等。
成型效率高,且制品外观漂亮,使用方便。
3、热压成型热压成型是将加热的热塑性塑料放入模具中,然后再进行压力成型。
这种成型方式适用于制造薄膜、牛奶瓶、塑料板等制品。
相对而言,这种成型方式比较简单,成本也相对较低。
三、热塑性塑料成型的成本热塑性塑料成型的成本与各方面因素有关,如生产规模、使用材料、制品的准确度和规格等。
一般而言,生产成本大概会包括材料成本、模具成本和生产成本,其中模具成本占整体成本的比例相对较大。
四、热塑性塑料成型的应用领域热塑性塑料成型具有适应性广泛的特点,所以在许多领域中得到了广泛的应用。
典型的塑料材料各项物理性能
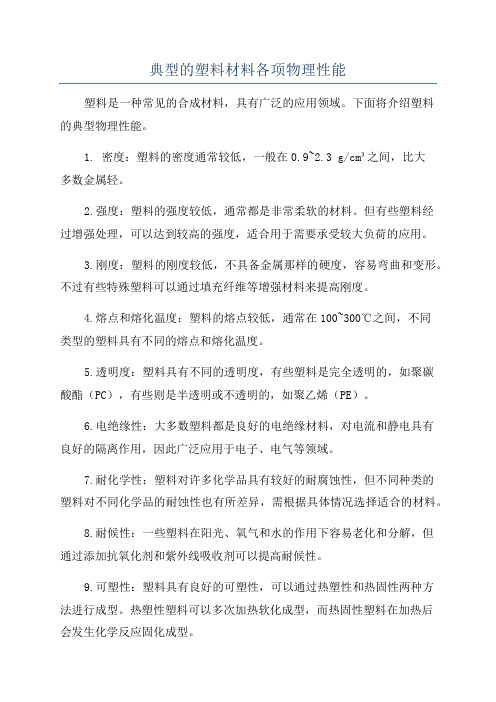
典型的塑料材料各项物理性能塑料是一种常见的合成材料,具有广泛的应用领域。
下面将介绍塑料的典型物理性能。
1. 密度:塑料的密度通常较低,一般在0.9~2.3 g/cm³之间,比大多数金属轻。
2.强度:塑料的强度较低,通常都是非常柔软的材料。
但有些塑料经过增强处理,可以达到较高的强度,适合用于需要承受较大负荷的应用。
3.刚度:塑料的刚度较低,不具备金属那样的硬度,容易弯曲和变形。
不过有些特殊塑料可以通过填充纤维等增强材料来提高刚度。
4.熔点和熔化温度:塑料的熔点较低,通常在100~300℃之间,不同类型的塑料具有不同的熔点和熔化温度。
5.透明度:塑料具有不同的透明度,有些塑料是完全透明的,如聚碳酸酯(PC),有些则是半透明或不透明的,如聚乙烯(PE)。
6.电绝缘性:大多数塑料都是良好的电绝缘材料,对电流和静电具有良好的隔离作用,因此广泛应用于电子、电气等领域。
7.耐化学性:塑料对许多化学品具有较好的耐腐蚀性,但不同种类的塑料对不同化学品的耐蚀性也有所差异,需根据具体情况选择适合的材料。
8.耐候性:一些塑料在阳光、氧气和水的作用下容易老化和分解,但通过添加抗氧化剂和紫外线吸收剂可以提高耐候性。
9.可塑性:塑料具有良好的可塑性,可以通过热塑性和热固性两种方法进行成型。
热塑性塑料可以多次加热软化成型,而热固性塑料在加热后会发生化学反应固化成型。
10.良好的成型性:塑料可通过注塑成型、挤出成型、吹塑成型、压延成型等多种方法进行加工和成型,具有较高的生产效率。
总的来说,塑料具有较低的密度、强度和刚度,较高的可塑性和成型性,良好的电绝缘性和耐化学性。
然而,正是由于这些性质的特点,塑料在现代社会中得到了广泛的应用,用于日常生活用品、建筑材料、电子产品、汽车零部件等众多领域。
注塑工艺分类
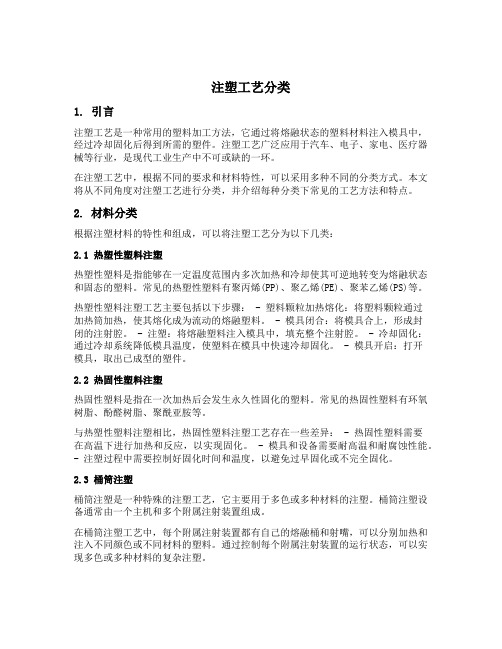
注塑工艺分类1. 引言注塑工艺是一种常用的塑料加工方法,它通过将熔融状态的塑料材料注入模具中,经过冷却固化后得到所需的塑件。
注塑工艺广泛应用于汽车、电子、家电、医疗器械等行业,是现代工业生产中不可或缺的一环。
在注塑工艺中,根据不同的要求和材料特性,可以采用多种不同的分类方式。
本文将从不同角度对注塑工艺进行分类,并介绍每种分类下常见的工艺方法和特点。
2. 材料分类根据注塑材料的特性和组成,可以将注塑工艺分为以下几类:2.1 热塑性塑料注塑热塑性塑料是指能够在一定温度范围内多次加热和冷却使其可逆地转变为熔融状态和固态的塑料。
常见的热塑性塑料有聚丙烯(PP)、聚乙烯(PE)、聚苯乙烯(PS)等。
热塑性塑料注塑工艺主要包括以下步骤: - 塑料颗粒加热熔化:将塑料颗粒通过加热筒加热,使其熔化成为流动的熔融塑料。
- 模具闭合:将模具合上,形成封闭的注射腔。
- 注塑:将熔融塑料注入模具中,填充整个注射腔。
- 冷却固化:通过冷却系统降低模具温度,使塑料在模具中快速冷却固化。
- 模具开启:打开模具,取出已成型的塑件。
2.2 热固性塑料注塑热固性塑料是指在一次加热后会发生永久性固化的塑料。
常见的热固性塑料有环氧树脂、酚醛树脂、聚酰亚胺等。
与热塑性塑料注塑相比,热固性塑料注塑工艺存在一些差异: - 热固性塑料需要在高温下进行加热和反应,以实现固化。
- 模具和设备需要耐高温和耐腐蚀性能。
- 注塑过程中需要控制好固化时间和温度,以避免过早固化或不完全固化。
2.3 桶筒注塑桶筒注塑是一种特殊的注塑工艺,它主要用于多色或多种材料的注塑。
桶筒注塑设备通常由一个主机和多个附属注射装置组成。
在桶筒注塑工艺中,每个附属注射装置都有自己的熔融桶和射嘴,可以分别加热和注入不同颜色或不同材料的塑料。
通过控制每个附属注射装置的运行状态,可以实现多色或多种材料的复杂注塑。
3. 工艺特点不同的注塑工艺具有不同的特点和适用范围,下面将介绍几种常见工艺的特点:3.1 热流道注塑热流道注塑是一种通过加热系统控制熔融塑料流动路径的工艺。
热塑和热固

热塑和热固
热塑和热固是塑料加工过程中两种不同的处理方式。
热塑是指在加热后可软化变形的塑料,通过模具加压成型后冷却固化,制成成品。
热固是指在加热后不可逆转的塑料,通过热固反应使其成型,在固化后无法再次软化变形。
热塑性塑料的特点是加热可软化,制成品后可再次加热变形,可回收再利用。
如聚乙烯、聚丙烯、聚苯乙烯等。
热塑性塑料制成的成品具有柔韧性和良好的韧性,但耐热性和耐腐蚀性相对较差。
热固性塑料则是加热后不可逆转的塑料,制成品后无法再次加热软化变形。
热固性塑料的制成过程需要通过加入固化剂等添加剂,使其在加热过程中发生交联反应,从而固化成型。
如酚醛树脂、环氧树脂、不饱和聚酯等。
热固性塑料制成的成品具有较高的强度、硬度和耐热性,但相对较脆,且不易回收再利用。
选择热塑或热固塑料应根据使用环境和要求来确定,两者各有优劣,需根据实际情况选择适合自己的材料。
- 1 -。
塑料成型工艺流程
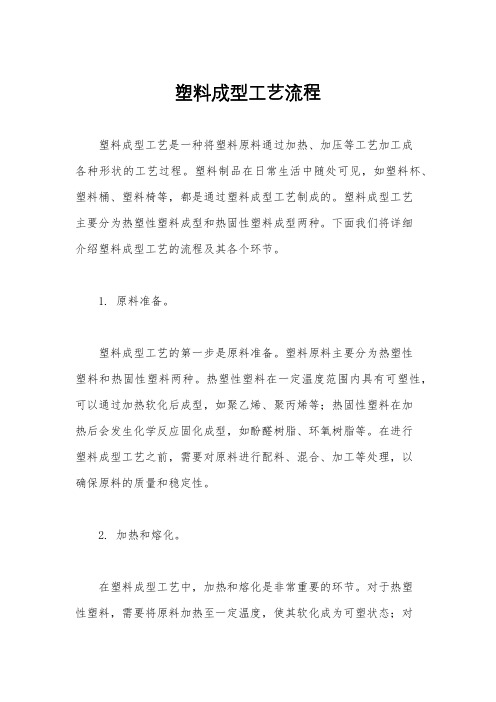
塑料成型工艺流程塑料成型工艺是一种将塑料原料通过加热、加压等工艺加工成各种形状的工艺过程。
塑料制品在日常生活中随处可见,如塑料杯、塑料桶、塑料椅等,都是通过塑料成型工艺制成的。
塑料成型工艺主要分为热塑性塑料成型和热固性塑料成型两种。
下面我们将详细介绍塑料成型工艺的流程及其各个环节。
1. 原料准备。
塑料成型工艺的第一步是原料准备。
塑料原料主要分为热塑性塑料和热固性塑料两种。
热塑性塑料在一定温度范围内具有可塑性,可以通过加热软化后成型,如聚乙烯、聚丙烯等;热固性塑料在加热后会发生化学反应固化成型,如酚醛树脂、环氧树脂等。
在进行塑料成型工艺之前,需要对原料进行配料、混合、加工等处理,以确保原料的质量和稳定性。
2. 加热和熔化。
在塑料成型工艺中,加热和熔化是非常重要的环节。
对于热塑性塑料,需要将原料加热至一定温度,使其软化成为可塑状态;对于热固性塑料,需要将原料加热至一定温度,使其发生化学反应固化成型。
在加热和熔化的过程中,需要控制加热温度、加热时间等参数,以确保原料能够达到适合成型的状态。
3. 成型。
成型是塑料成型工艺的核心环节。
在成型过程中,需要将熔化后的塑料原料注入模具中,并施加一定的压力,使其充分填充模具腔体,并形成所需的产品形状。
成型过程中需要控制注塑压力、注塑速度、注塑时间等参数,以确保成型品质量和生产效率。
4. 冷却。
在成型完成后,需要对产品进行冷却。
冷却过程中,需要控制冷却时间、冷却速度等参数,以确保产品能够充分冷却固化,并保持所需的形状和尺寸稳定。
5. 脱模。
脱模是将成型后的产品从模具中取出的过程。
在脱模过程中,需要注意产品与模具之间的脱模性能,以确保产品能够顺利脱模并保持完整的形状和表面质量。
6. 加工和表面处理。
在脱模后,还需要对产品进行加工和表面处理。
加工包括修整、打磨、去毛刺等工艺,以确保产品的尺寸和表面质量达到要求;表面处理包括喷漆、印刷、镀铬等工艺,以美化产品外观并提高产品的耐磨性和耐腐蚀性。
热塑性与热固性

热固性热固性塑料第一次加热时可以软化流动,加热到一定温度,产生化学反应一交链固化而变硬,这种变化是不可逆的,此后,再次加热时,已不能再变软流动了。
正是借助这种特性进行成型加工,利用第一次加热时的塑化流动,在压力下充满型腔,进而固化成为确定形状和尺寸的制品。
这种材料称为热固性塑料。
热固性塑料的树脂固化前是线型或带支链的,固化后分子链之间形成化学键,成为三度的网状结构,不仅不能再熔触,在溶剂中也不能溶解。
主要用于隔热、耐磨、绝缘、耐高压电等在恶劣环境中使用的塑料,大部分是热固性塑料,最常用的应该是炒锅锅把手和高低压电器。
常用的热固性塑料品种有酚醛树脂、脲醛树脂、三聚氰胺树脂、不饱和聚酯树脂、环氧树脂、有机硅树脂、聚氨酯等。
热塑性thermoplasticity物质在加热时能发生流动变形,冷却后可以保持一定形状的性质。
大多数线型聚合物均表现出热塑性,很容易进行挤出、注射或吹塑等成型加工。
在一定温度范围内,能反复加热软化和冷却硬化的性能,线形或支链型聚合物具有这种性能。
日常生活中,像塑料袋、塑料衣挂等物都具有热塑性。
因此,它们可以通过加热熔化来进行封口、粘合等操作。
最大的区别在于热塑性是线性(梳形)高分子结构,分子间以分子间作用力相结合,另热固性是网状高分子结构,以化学键相结合,表现最明显的是一个可熔(熔化)可溶(溶解),另一个不熔。
只能溶胀不能溶解。
这是有本质区别的。
热固性材料就是thermal set,加工过程中小分子聚合形成网状交联结构,因此在成形后无法再次加工,比如原来的泡沫塑料饭盒。
热塑性材料叫thermal plastic, 加工过程中材料维持在原有的大分子结构下,只是加热熔融后加入粘流态而可以加工。
在冷却进入玻璃态后形状固定。
但是如果需要再次加工,可以通过再次加热熔融本质区别是热塑性塑料在受热成型过程中是不发生化学反应的,热固性塑料在受热或固化剂的作用下发生交联反应,当然是化学反应啦一、热塑性塑料加热时变软以至流动,冷却变硬,这种过程是可逆的,可以反复进行。
塑料的成型工艺
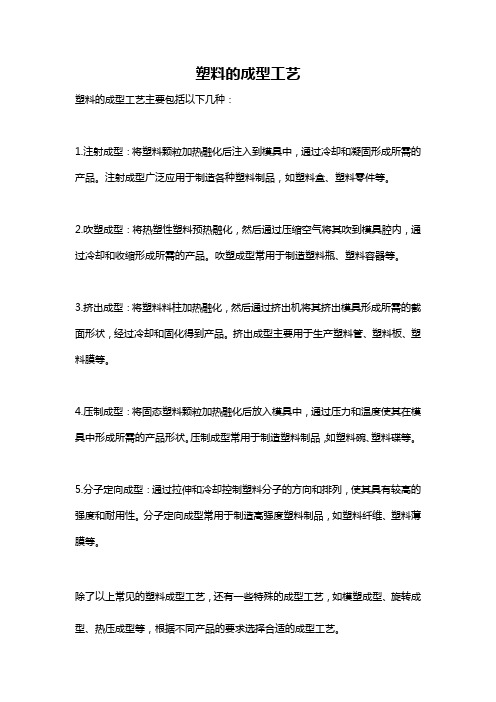
塑料的成型工艺
塑料的成型工艺主要包括以下几种:
1.注射成型:将塑料颗粒加热融化后注入到模具中,通过冷却和凝固形成所需的产品。
注射成型广泛应用于制造各种塑料制品,如塑料盒、塑料零件等。
2.吹塑成型:将热塑性塑料预热融化,然后通过压缩空气将其吹到模具腔内,通过冷却和收缩形成所需的产品。
吹塑成型常用于制造塑料瓶、塑料容器等。
3.挤出成型:将塑料料柱加热融化,然后通过挤出机将其挤出模具形成所需的截面形状,经过冷却和固化得到产品。
挤出成型主要用于生产塑料管、塑料板、塑料膜等。
4.压制成型:将固态塑料颗粒加热融化后放入模具中,通过压力和温度使其在模具中形成所需的产品形状。
压制成型常用于制造塑料制品,如塑料碗、塑料碟等。
5.分子定向成型:通过拉伸和冷却控制塑料分子的方向和排列,使其具有较高的强度和耐用性。
分子定向成型常用于制造高强度塑料制品,如塑料纤维、塑料薄膜等。
除了以上常见的塑料成型工艺,还有一些特殊的成型工艺,如模塑成型、旋转成型、热压成型等,根据不同产品的要求选择合适的成型工艺。
- 1、下载文档前请自行甄别文档内容的完整性,平台不提供额外的编辑、内容补充、找答案等附加服务。
- 2、"仅部分预览"的文档,不可在线预览部分如存在完整性等问题,可反馈申请退款(可完整预览的文档不适用该条件!)。
- 3、如文档侵犯您的权益,请联系客服反馈,我们会尽快为您处理(人工客服工作时间:9:00-18:30)。
热塑性塑料的固化
无定型高分子在液相和固相之间没有尖锐的转变。
无定型热塑性高分子在温度降到低于玻璃化转变温度T g以下时,便呈现玻璃态。
半结晶高分子在熔体和固相之间有明显的转变温度,即熔融温度T m。
一旦冷却到玻璃化转变温度以下,高分子材料就变得硬而脆。
有些半结晶高分子的玻璃化转变温度远低于室温,使得它们的韧性比无定型高分子好。
30﹪~70﹪的分子形成晶体,其余的则保留在无定型态。
由于结晶时释放热量,因此固化制品时必须移走更多的热量;结晶高分子材料收缩量大,故必须采用更长的保压时间和更大的保压压力。
也就是说需要更长的注塑循环时间,制品有更多的收缩。
注射成型中的高冷却速率可降低半结晶高分子材料的结晶度;但是,成型后材料内的无定型区还可能形成结晶,这将引起成品的进一步收缩和翘曲。
对于半结晶聚合物,在熔点T m以下即可认为是固态的。