数控铣削加工进刀方式的探讨
数铣
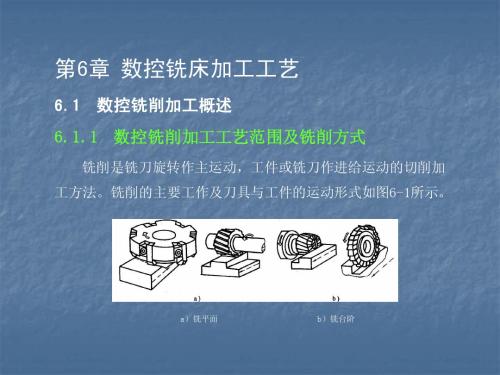
6.3.2
常用数控铣削夹具
(1)机床用平口虎钳 工件在机床用平口虎钳上装夹时应注意:
装夹毛坯面或表面有硬皮时,钳口应加垫铜皮或铜钳口;选择高度适 当、宽度稍小于工件的垫铁,使工件的余量层高出钳口;在粗铣和半 精铣时,希望使铣削力指向固定钳口,因为固定钳口比较牢固。当工 件的定位面和夹持面为非平行平面或是圆柱面时,可采用更换钳口的 方式装夹工件。
(a)硬质合金立铣刀
(b)高速钢立铣刀
立铣刀的圆柱表面和端面上都有切削刃,它们可同时进行切削, 也可单独进行切削,主要用于加工凸轮、台阶面、凹槽和箱口面。
为了能加工较深的沟槽,并保证有足够的备磨量,立铣刀的轴 向长度一般较长。为了改善切屑卷曲情况,增大容屑空间,防止切 屑堵塞,刀齿数比较少,容屑槽圆弧半径则较大。一般粗齿立铣刀 齿数z=3~4,细齿立铣刀齿数z=5~8,套式结构z=10~20。容屑槽 圆弧半径r=2~5mm。 直径较小的立铣刀,一般制成带柄形式。 (3)模具铣刀 模具铣刀由立铣刀发展而成,可分为圆锥形立铣刀、圆柱形球 头立铣刀和圆锥形球头立铣刀三种,其柄部有直柄、削平型直柄和 莫氏锥柄。
a)整体焊接式
b)机夹-焊接式
c)可转位式
面铣刀主要以端齿为主加工各种平面,主偏角为90º的面铣刀 还能同时加工出与平面垂直的直角面,但这个面的高度受到刀片长 度的限制。 面铣刀齿数对铣削生产率和加工质量有直接影响,齿数越多, 同时工作齿数也多,生产率高,铣削过程平稳,加工质量好。可转 位面铣刀的齿数根据直径不同可分为粗齿、细齿、密齿三种(参见 下表)。粗齿铣刀主要用于粗加工;细齿铣刀用于平稳条件下的铣 削加工;密齿铣刀的每齿进给量较小,主要用于薄壁铸铁件加工。
图6-15
弹簧夹头刀柄
图6-16 弹簧夹头结构示图
数铣的对刀方法及参数的设置 -回复
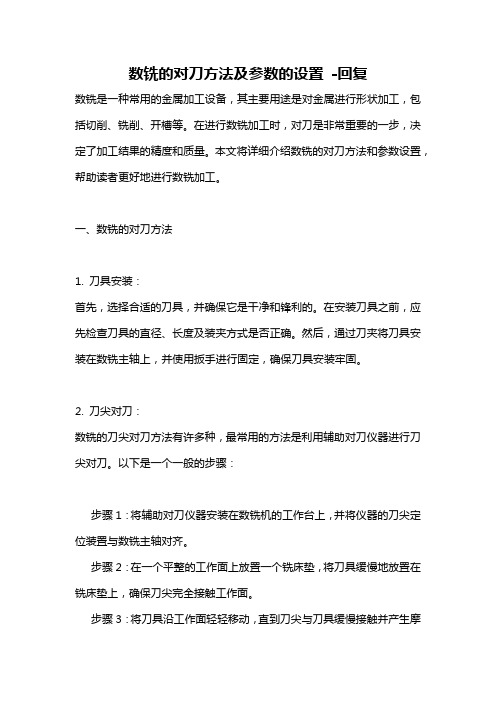
数铣的对刀方法及参数的设置-回复数铣是一种常用的金属加工设备,其主要用途是对金属进行形状加工,包括切削、铣削、开槽等。
在进行数铣加工时,对刀是非常重要的一步,决定了加工结果的精度和质量。
本文将详细介绍数铣的对刀方法和参数设置,帮助读者更好地进行数铣加工。
一、数铣的对刀方法1. 刀具安装:首先,选择合适的刀具,并确保它是干净和锋利的。
在安装刀具之前,应先检查刀具的直径、长度及装夹方式是否正确。
然后,通过刀夹将刀具安装在数铣主轴上,并使用扳手进行固定,确保刀具安装牢固。
2. 刀尖对刀:数铣的刀尖对刀方法有许多种,最常用的方法是利用辅助对刀仪器进行刀尖对刀。
以下是一个一般的步骤:步骤1:将辅助对刀仪器安装在数铣机的工作台上,并将仪器的刀尖定位装置与数铣主轴对齐。
步骤2:在一个平整的工作面上放置一个铣床垫,将刀具缓慢地放置在铣床垫上,确保刀尖完全接触工作面。
步骤3:将刀具沿工作面轻轻移动,直到刀尖与刀具缓慢接触并产生摩擦。
步骤4:在达到刀尖接触的位置时,将辅助对刀仪器的刻度盘归零,然后以相同的刻度读数调整刀夹高度,直到归零位置。
步骤5:再次进行刀具的缓慢移动,以确保刀尖已经对准。
3. 刀具的高度调整:对于切削深度较大的加工,还需要对刀具的高度进行调整。
以下是一个常用的步骤:步骤1:将加工件放置在数铣机的工作台上,并以合适的位置进行固定。
步骤2:根据加工要求,选择合适的进给量和切削深度。
步骤3:使用切削手轮或数控系统,控制刀具沿着加工件的高度进行调整,使刀具与加工件紧密接触。
步骤4:根据实际情况,逐步调整刀具的高度,直到达到理想的切削深度。
二、数铣的参数设置在进行数铣加工时,合理设置切削参数可以提高加工效率和加工质量。
以下是一些常用的数铣参数及其设置方法:1. 主轴转速:主轴转速决定了切削速度,对于不同材料和刀具,主轴转速的要求也不同。
通常,使用硬质合金刀具时,主轴转速较高,而使用HSS刀具时,主轴转速较低。
数控铣床/力口工中心刀具的对刀方法和技巧
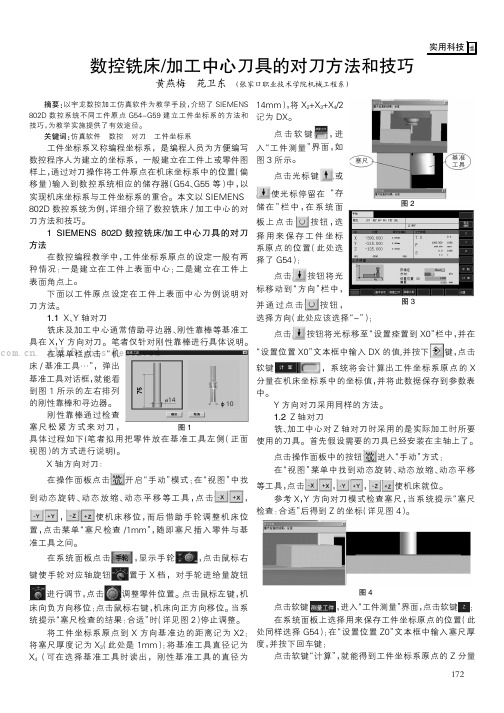
摘要:以宇龙数控加工仿真软件为教学手段,介绍了SIEMENS 802D 数控系统不同工件原点G54-G59建立工件坐标系的方法和技巧,为教学实施提供了有效途径。
关键词:仿真软件数控对刀工件坐标系工件坐标系又称编程坐标系,是编程人员为方便编写数控程序人为建立的坐标系,一般建立在工件上或零件图样上,通过对刀操作将工件原点在机床坐标系中的位置(偏移量)输入到数控系统相应的储存器(G54、G55等)中,以实现机床坐标系与工件坐标系的重合。
本文以SIEMENS802D 数控系统为例,详细介绍了数控铣床/加工中心的对刀方法和技巧。
1SIEMENS 802D 数控铣床/加工中心刀具的对刀方法在数控编程教学中,工件坐标系原点的设定一般有两种情况:一是建立在工件上表面中心;二是建立在工件上表面角点上。
下面以工件原点设定在工件上表面中心为例说明对刀方法。
1.1X、Y 轴对刀铣床及加工中心通常借助寻边器、刚性靠棒等基准工具在X,Y 方向对刀。
笔者仅针对刚性靠棒进行具体说明。
在菜单栏点击“机床/基准工具…”,弹出基准工具对话框,就能看到图1所示的左右排列的刚性靠棒和寻边器。
刚性靠棒通过检查塞尺松紧方式来对刀,具体过程如下(笔者拟用把零件放在基准工具左侧(正面视图)的方式进行说明)。
X 轴方向对刀:在操作面板点击开启“手动”模式;在“视图”中找到动态旋转、动态放缩、动态平移等工具,点击,,使机床移位,而后借助手轮调整机床位置,点击菜单“塞尺检查/1mm”,随即塞尺插入零件与基准工具之间。
在系统面板点击,显示手轮,点击鼠标右键使手轮对应轴旋钮置于X 档,对手轮进给量旋钮进行调节,点击调整零件位置。
点击鼠标左键,机床向负方向移位;点击鼠标右键,机床向正方向移位。
当系统提示“塞尺检查的结果:合适”时(详见图2)停止调整。
将工件坐标系原点到X 方向基准边的距离记为X2;将塞尺厚度记为X 3(此处是1mm );将基准工具直径记为X 4(可在选择基准工具时读出,刚性基准工具的直径为14mm ),将X 2+X 3+X 4/2记为DX。
caxa-数控加工

CAXA数控加工
山东建筑大学 机电学院
进退刀方式示意图:
垂直进刀、 垂直退刀
直线进刀、 圆弧退刀
圆弧进刀、 直线退刀
强制从圆 心进刀、 圆弧退刀
圆弧进刀、 圆弧退刀
CAXA数控加工
山东建筑大学 机电学院
(4)下刀切入方式
指在两个切削层之间刀具从上一层到下一层的切入方 式.
垂直切入
螺旋切入
倾斜切入
数控加工的优点:
1 、提高生产效率; 2、不需熟练的机床操作人员; 3、提高加工精度并且保持加工质量; 4、可以减少工装卡具; 5、可以减少各工序间的周转,原来需要用多道工序完成的工件, 用数控加工可以一次装卡完成,缩短加工周期,提高生产效率。 6、容易进行加工过程管理; 7、可以减少检查工作量; 8、可以降低废、次品率; 9、便于设计变更,加工设定柔性; 10、容易实现操作过程的自动化,一个人可以操作多台机床; 11、操作容易,极大减轻体力劳动强度
刀具
残留高度
行距
加工图形
CAXA数控加工
山东建筑大学 机电学院
(2)切削用量 主轴转速:是切削时机床主轴转动的角速度,(r/min)。 进给速度:正常切削时刀具行进的线速度,(mm/min)。 接近速度:从安全高度切入工件前刀具行进的线速度, (mm/min)。 退刀速度:刀具离开工件回到安全高度时刀具行进的线速 度,(mm/min)。 行间连接速度:用于有往复加工的加工方式,避免在顺逆 铣的变换中,机床的进给方向和吃刀量产生急剧变化,易 对机床、道具造成损坏,此速度一般小于进给速度。
CAXA数控加工
山东建筑大学 机电学院
7.2平面轮廓加工
应用—轨迹生成—平面轮廓加工 平面轮廓加工是生成沿轮廓线切削的两轴刀具轨迹。 它主要用于加工外形和开槽,属于两轴半加工方式。 加工精度:刀具轨迹和实际加工模型的偏 差(最大允许偏差)。 拔模斜度:两轴半加工时轮廓具有的倾斜 度,与拔模基准配合使用。 刀次:生成的刀位的行数。 顶层高度:被加工零件的的要加工的最高 高度。 底层高度:加工完成后,最后一层所在的 高度。 每层下降高度:每加工完一层,加工下一 层时刀具下降的高度,即上一层与下一层 在Z方向上的高度差。
数控铣床(加工中心)对刀方法的研究与实践

数控铣床(加工中心)对刀方法的研究与实践作者:聂小春汪菊英孙晓辉来源:《科技资讯》 2012年第32期聂小春汪菊英孙晓辉(广州工程技术职业学院广东广州 510450)摘要:本文结合使用数控铣床、加工中心(采用FUNAC0i-mate数控系统)的实际经验,控讨了几种常用的数控铣床(加工中心)的对刀方法。
关键词:刀位点工件坐标系对刀方法调刀补中图分类号:TG547 文献标识码:A 文章编号:1672-3791(2012)11(b)-0047-01我们在数控铣床(加工中心)上自动加工零件前,首先一定要确定工件坐标系,这个坐标系是编程人员以工件上的某一点为坐标原点建立的一个坐标系,是用来定义工件形状和刀具相对工件运动的坐标系。
那么如何在机床上确定工件坐标系呢,这就是本文所要探讨的对刀问题。
对刀是数控铣床(加工中心)加工中的主要操作和重要技能,所谓对刀就是使刀具的刀位点与工件坐标系原点重合,也即就是测量工件坐标系原点与机床原点之间的偏移距离(工件坐标系原点在以刀位点为参照的机床坐标系里的坐标值)。
对刀的方法有很多种,本文以数控铣床、加工中心(采用FUNAC0I-mate数控系统)为例介绍几种常用的对刀方法,本文约定以工件坐标系原点在工件上表面中心处为例。
1 用分中棒X、Y方向上的对刀方法(1)在工作台上用平口钳夹好工件,注意装平、装正、装实的六字原则,还需根据零件的加工深度确定好工件伸出平口钳的高度,以免加工中过切平口钳台面。
(2)装夹好分中棒;(分中棒又叫寻边器,是在CNC数控加工中,用于精确确定被加工工件的中心位置的一种检测工具,因为生产的需要分中棒有不同的类型,如光电式偏置式等,比较常用的是偏置式。
应用光电式分中棒分中时,不需要主轴旋转,精度可达±0.005 mm,应用偏置式分中棒分中时,主轴以400~600 RPM的速度转动)。
(3)屏幕上机床坐标切换为相对坐标界面。
1.1 将机床操作模式切换为“手轮模式”,用手轮方式进行对刀1.2 对X轴分中,具体步骤为(1)移动工作台,使分中棒通过调节X轴工作台的移动速度渐渐靠近并接触工件左侧面,如果是偏置式分中棒,就看上下棒体是否同心,如果是电子式分中棒,就会发出警报声及亮警示灯。
浅谈螺纹的数控铣削加工
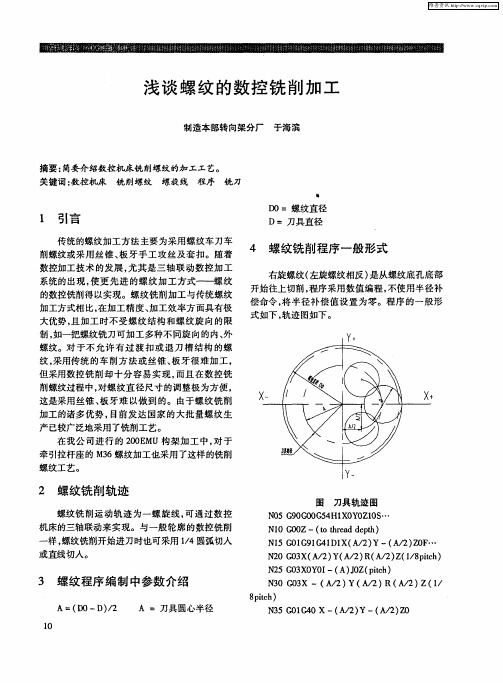
螺纹工 艺 。
2 螺纹 铣 削轨 迹
一
铣刀齿数 Z= , 6 每齿进给量 f 0 0 r 铣刀 = . 1 m, a 进给速度 F为
F =f z×N =0. 01×6×1 6 =6 6 mm/mi 00 3. n
大 优势 , 加工 时 不 受 螺 纹 结 构 和螺 纹旋 向 的 限 且
开始往上切削 , 程序采用数值编程 , 不使用半径补 偿命令, 半径补偿值设置为零。程序 的一 般形 将
式如 下 , 迹 图如下 。 轨
制, 如一把螺纹铣刀可加工多种不同旋 向的内、 外 螺纹 。对 于 不 允 许 有 过 渡 扣 或 退 刀 槽 结 构 的螺 纹, 采用传统 的车削方法或丝 锥、 板牙很难加工 , 但采用数控铣削却 十分 容易实现 , 而且在数控铣 削螺纹过程中, 对螺纹直径尺寸的调整极为方便 , 这是采用丝锥 、 板牙难 以做到 的。由于螺纹铣削
5 深螺纹铣 削程序
螺纹铣削时应尽量选用刀片宽度大于被加工 螺纹长度的铣刀 。 这样, 铣刀只需旋转 3 0 即可完 6。
N1 2 一 0 1 6 M3 0 5 G1 Z 4 S 0 0 F1 0 D N O G1 9 X . Y 一2 2 6 . 2 G 1 2 2 .F3 6 N2 0 x2 2 . U . z . 3 5 5 G 3 . Y2 2 2 2 0 4 7
NI 0 G l 4 DI A 2 Y 一( / ) 0 … 5C 1 9 G 1 X( / ) A 2 ZF N 0C 3 A 2 Y( / ) A 2 Z I8 ih 2 X( / ) A 2 R( / ) (/ pt ) O c N 5C 3 O O 一( JZ pt ) 2 X Y I A)0 ( ih O c N 0C 3 一( / Y( / )R( / ) I 3 X O A 2) A 2 A 2 Z( / 8 i h pt ) c N 5C l 4 3 G 0X一( / ) O A 2 Y一( / ) o A 2z
螺纹数控车削加工几种不同进刀方式

螺纹是机械工程中比较常见的几何特征之一, 应用非常的广泛。
在各种螺纹加工工艺中,数控车削加工是生产单件或小批量螺纹工件的常用方法之一。
但是螺纹的数控车削也存在一定的难度,如加工参与的切削刃较长,容易出现啃刀和扎刀的现象,一般需要多刀切削才能完成;为了保证螺距准确,必须要选择合适的切入和切出长度;再有,螺纹加工的牙型及牙型角基本由刀具形状保证,因此,刀具的形状与正确安装直接影响螺纹牙型的质量;螺纹加工时的进给量与主轴转速必须保持严格的传动比,因此加工时禁止使用恒线速度控制;最后,螺纹切削加工的切削速度一般不高,否则容易出现积屑瘤或造成刀具塑性损坏。
螺纹数控车削的进刀方式:螺纹数控车削必须是多刀切削,其常用的进刀方式有径向进刀、侧向进刀、改进式侧向进刀、左右侧交替进刀以及分层切削式进刀这几种。
径向进刀是一种最基础的进给方式,其优点是编程比较简单,对左、右切削刃后刀面的磨损也比较均匀,牙型与刀头的吻合度高;但缺点是切屑不容易控制,可能会产生振动,刀尖处存在较大的切削力负荷,并且温度也较高。
径向进刀适合用在小螺距螺纹的加工以及螺纹的精加工中。
侧向进刀也是一种较为基础的进刀方式,这种方式有专用的复合固定循环指令编程,可以减小切削力, 便于控制切屑的排出;但这种切削方式使用的是纯单侧刃,因此刀具左、右切削刃的磨损不均匀,一般右侧后刀面磨损较大。
侧向进刀适合用在稍大螺距螺纹的粗加工中。
改进式侧向进刀,只是在侧向进刀的基础上,使进刀方向略微发生变化,这样就可以使右侧切削刃也参与到切削中来,从而抑制了右侧后刀面的磨损,减小了切削热的产生,在一定程度上改善了侧向进刀的不足。
左右侧交替进刀的最大特点是左、右切削刃磨损均匀,对于延长刀具寿命是非常有益的,而且也方便控制切屑的排出;单这种切削方式的不足之处在于编程比其他方式稍微复杂一些。
在编程能力允许的情况下,左右侧交替进刀适合对大牙型、大螺距的螺纹进行加工,甚至可加工梯形螺纹。
铣削加工加工方法
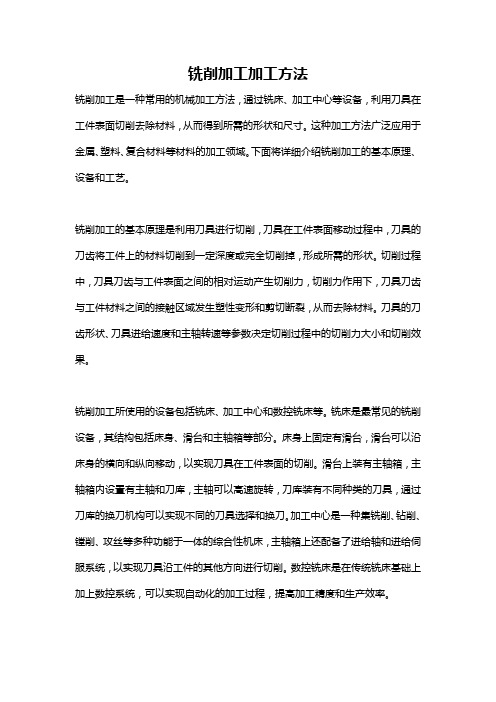
铣削加工加工方法铣削加工是一种常用的机械加工方法,通过铣床、加工中心等设备,利用刀具在工件表面切削去除材料,从而得到所需的形状和尺寸。
这种加工方法广泛应用于金属、塑料、复合材料等材料的加工领域。
下面将详细介绍铣削加工的基本原理、设备和工艺。
铣削加工的基本原理是利用刀具进行切削,刀具在工件表面移动过程中,刀具的刀齿将工件上的材料切削到一定深度或完全切削掉,形成所需的形状。
切削过程中,刀具刀齿与工件表面之间的相对运动产生切削力,切削力作用下,刀具刀齿与工件材料之间的接触区域发生塑性变形和剪切断裂,从而去除材料。
刀具的刀齿形状、刀具进给速度和主轴转速等参数决定切削过程中的切削力大小和切削效果。
铣削加工所使用的设备包括铣床、加工中心和数控铣床等。
铣床是最常见的铣削设备,其结构包括床身、滑台和主轴箱等部分。
床身上固定有滑台,滑台可以沿床身的横向和纵向移动,以实现刀具在工件表面的切削。
滑台上装有主轴箱,主轴箱内设置有主轴和刀库,主轴可以高速旋转,刀库装有不同种类的刀具,通过刀库的换刀机构可以实现不同的刀具选择和换刀。
加工中心是一种集铣削、钻削、镗削、攻丝等多种功能于一体的综合性机床,主轴箱上还配备了进给轴和进给伺服系统,以实现刀具沿工件的其他方向进行切削。
数控铣床是在传统铣床基础上加上数控系统,可以实现自动化的加工过程,提高加工精度和生产效率。
铣削加工的基本工艺包括刀具选择、刀具装夹、工件装夹、刀具路径规划和切削参数设置等。
刀具的选择要根据工件材料和加工要求进行,包括刀具的材料、刀齿形状和刀具直径等。
刀具的装夹要保证刀具牢固固定,以防止在切削过程中的脱落和振动。
工件的装夹要保持工件的稳定位置,以保证加工质量。
刀具路径规划是根据工件形状和加工要求确定刀具的移动轨迹,一般包括顺铣、逆铣和横向铣削等方式。
切削参数的设置是根据工件材料和加工要求确定切削速度、进给速度和切削深度等参数,以保证切削过程中的切削力和加工效果。
- 1、下载文档前请自行甄别文档内容的完整性,平台不提供额外的编辑、内容补充、找答案等附加服务。
- 2、"仅部分预览"的文档,不可在线预览部分如存在完整性等问题,可反馈申请退款(可完整预览的文档不适用该条件!)。
- 3、如文档侵犯您的权益,请联系客服反馈,我们会尽快为您处理(人工客服工作时间:9:00-18:30)。
数控铣削加工进刀方式的探讨
来源:中国幕墙网收集整理
本文对数控铁削加工中的轮廓加工、挖槽和型腔加工等不同加工类型进刀方式的
选择作了有针对性的说明和总结,通过分析各种进刀方式的特点和适用性,给出
了提高加工效率和零件表面质量的措施.对于实际生产具有较强的指导作用。
数控加工对加工工艺有着特殊的要求。数控加工中对工艺问题处理得好坏,
将直接影晌数控加工的质量和效率。国内的一些科研人员对数控加工的工艺进行
了探讨,但对于铣削进刀方式的选择未见单独报道。而在各种型面的数控铣削中,
合理地选择切削加工方向、进刀切入方式是很重要的,因为两者将直接影响零件
的加工精度和加工效率。
本文以数控加工中最常用的自动编程软件CAXA和MasterCAM为例(其他软件
相类似,可做参考),通过分析数控铣削加工中各种进刀方式的特点和适用性,
围绕在自动编程中如何正确选择进刀方式的主题进行探讨,以达到提高加工效
率,改善零件表面质量的目的。
一、轮廓加工中的进刀方式
1.法线进刀和切线进刀
轮廓加工进刀方式一般有两种:法线进刀和切线进刀,如图1所示。由于法
线进刀容易产生刀痕,因此一般只用于粗加工或者表面质量要求不高的工件。法
线进刀的路线较切线进刀短,因而切削时间也就相应较短。
图1 法线进刀与切线进刀方式
在一些表面质量要求较高的轮廓加工中,通常采用加一条进刀引线再圆弧切
入的方式,使圆弧与加工的第一条轮廓线相切,能有效地避免因法线进刀而产生
刀痕,如图2所示。而且在切削毛坯余量较大时离开工件轮廓一段距离下刀再切
入,很好地起到了保护立铣刀的作用。
图2 圆弧切入的方式
需要说明的是:在手工编写轮廓铣削程序时为了编程的方便,或者为了弥补
刀具的磨损,常常采用刀补方式进行编程,即在编程时可以不考虑刀具的半径,
直接按图样尺寸编程,再在加工时输入刀具的半径(或补偿量)至指定的地址进行
加工。但要注意切入圆弧的R值需大于所使用的刀具半径r,否则无法建立补偿
而出现报警,如图3所示。至于进刀引线的长短则要根据实际情况计算,但要注
意减少空刀的行程。
图3 切入与刀补的建立
2.非典型轮廓加工中的进刀方式
在对于一些非典型轮廓的加工,采用切线进退刀的同时,还应沿轮廓走多一
个重叠量L,可以有效避免因进刀点和退刀点在同一位置而产生的刀痕。重叠量
L一般取1~2mm即可,如图4所示。
图4 切削重叠量
二、挖槽和型腔加工中的进刀方式
对于封闭型腔零件的加工,下刀方式主要有垂直下刀、螺旋下刀和斜线下刀
三种,下面就如何选择各下刀方式进行说明。
1.垂直下刀
(1)小面积切削和零件表面粗糙度要求不高的情况
使用键槽铣刀直接垂直下刃并进行切削。虽然键槽铣刀其端部刀刃通过铣刀
中心,有垂直吃刀的能力,但由于键槽铣刀只有两刃切削,加工时的平稳性也就
较差,因而表面粗糙度较n;同时在同等切削条件下,键槽铁刀较立铁刀的每刃
切削量大,因而刀刃的磨损也就较大,在人面积切削中的效率较低。所以,采用
键槽铣刀直接垂直下刀并进行切削的方式,通常只用于小面积切削或被加工零件
表面粗糙度要求不高的情况。
(2)大面积切削和零件表面粗糙度要求较高的情况
大面积的型腔一般采用加工时具有较高的平稳性和较长使用寿命的立铣刀
来加工,但由于立铣刀的底切削刃没有到刀具的中心,所以立铣刀在垂直进刀时
没有较大切深的能力,因此一般先采用键槽铣刀(或钻头)垂直进刀后,再换多刃
立铣刀加工型腔。在利用CAM软件进行编程的时候,一般都会提供指定点下刀的
选项。如图 5所示的CAXA制造工程师里的“区域式粗加工”中的“接近点和返
回点”选项,指的就是从指定点下刀或退刀。在MasterCAM里的“挖槽
(Pocket )”二维加工中虽然没有指定下刀点下刀的选项,但在选择一个指定点
后,再选择加工区域,则系统会自动从选择的指定点下刀;而在曲面粗加工“挖
槽粗加工”方式中,则在粗加工参数(Rough parameters)设置页有相应的选择
项,如图6所示。
图5 CAXA指定点下刀或退刀选项
对于其他方式的曲面粗加工,一般都可以在参数设置中找到相应的选项。
图6 MasterCAM指定点下刀或退刀选项
[an error occurred while processing this directive]
2.螺旋下刀
螺旋下刀方式是现代数控加工应用较为广泛的下刀方式,特别是模具制造行
业中应用最为常见。刀片式合金模具铣刀可以进行高速切削,但和高速钢多刃立
铣刀一样在垂直进刀时没有较大切深的能力。但可以通过螺旋下刃的方式(图7
所示),通过刀片的侧刃和底刃的切削,避开刀具中心无切削刃部分与工件的干
涉,使刃具沿螺旋朝深度方向渐进,从而达到进刀的目的。这样,可以在切削的
平稳性与切削效率之间取得一个较好的平衡点。
图7 螺旋下刀方式
在CAXA中,螺旋下刀方式设置选项主要有4项:半径、螺距、第一及第二层
以后螺旋进刀高度,如图8所示。螺旋半径的大小一般情况下应大于刀具直径的
50%,但螺旋半径过大,进刀的切削路程就越长,下刀耗费的时间也就越长,一
般不超过刀具直径的大小,螺距的数值要根据刀具的吃深能力而定,一般在
0.5~1之间:第二层进刀高度一般等于第一层下刀高度减去慢速下刀的距离即
可。
图8 CAXA螺旋下刀选项
在MasterCAM中,则对螺旋下刀方式作了更人性化和更细致的设定(如图9
所示),如给定一个螺旋半径大小的范围,系统可以根据工件的形状自动去判断
和选择最为合适的土径去下刀;X,Y方向安全距离可以更好地避免下刀时造成的
干涉现象的发生;还有在螺旋下刀时是采用Z向还是水平方向的进刀速率,以及
螺旋下刀失败时是改为垂直进刀还是中断程式等。和CAXA相比,MasterCAM不
是用螺距而是用螺旋升角来设置刀具运动一周后沿Z轴切深的距离的。螺旋升角
选取得太小,螺旋圈数增多,切削路程加长;升角太大,又会产生过大的端刃切
削,一般取3°~10°之间为宜。
图9 MasterCAM螺旋下刀选项
螺旋下刀也有其固有的弱点,比如切削路线较长、在比较狭窄的型腔加工中
往往因为切削范围过小无法实现螺旋下刀等,所以有时需采用较大的下刀进给或
钻下刀孔等方法来弥补,所以选择螺旋下刀方式时要注意灵活运用。
手工编写螺纹下刀程式比较繁琐,在华中21M或22M系统中可利用G02/G03
螺旋进给指令(详见21M世纪星铣削数控装置编程说明书第24页)来实现。但一
般在手工编程过程中不常用螺旋下刀。
3.斜线下刀
斜线下刀时刀具快速下至加工表面上万一个距离后,改为以一个与工件表面
成一角度的方向,以斜线的方式切入工件来达到Z向进刀的目的,如图10所示。
斜线下刀万式作为螺旋下刀方式的一种补充,通常用于因范围的限制而无法实现
螺旋下刀时的长条形的型腔加工。
斜线下刀主要的参数有:斜线下刀的起始高度切入斜线的长度、切入和反向
切入角度。起始高度一般设在加工面上方0.5~1mm之间;切入斜线的长度要视型
腔空间大小及铣削深度来确定,一般是斜线愈长,进刀的切削路程就越长;切入
角度选取得大小,斜线数增多,切削路程加长;角度太大,又会产生不好的端刃
切削的情况,一般选5°~200°之间为宜。通常进刀切入角度和反向进刀切入角
度取相同的值。
图10 切入和反向切入角度
在CAXA中,将斜线下刀方式分解成两种类型:Z字型和倾斜线,如图11所
示。一般一次切深较大的情况下选用Z字型的方式;因为倾斜线下刀方式是通过
下刃距离和角度自动计算出走刀斜线的长度的,所以使用时要特别注意角度值的
设置。
与CAXA斜线下刀方式没置的简洁实用相比,MasterCAM对斜线下刀方式设
置选项突出了人性化的特点(如图12所示),比如限定斜线的长度范围、设置X、
Y方向安全距离避免与加工轮廓的干涉,还有在斜线下刀时是采用Z向还是水平
方向的进刀速率,以及斜线下刀失败时是改为垂直进刀还是中断程式,X、Y 向
角度可自动计算......
图11 CAXA斜线下刀参数设置
图12 MasterCAM斜线下刀参数设置
三、结论
综上所述,正确理解数控铣削加工中各种进刀方式的特点和适用范围,同时
在编程中设置合理的切削参数,对提高加工效率及零件表面质量,如避免接刀痕、
过切等现象的发生以及保护刀具等都有重要的意义。
其他常用自动编程软件,如UG, Cimatron, PowerMILL等,其进刀方式的选
择和进刀切ail参数的设置与本文所厌软件基本相类似,这里就不再赘述了。编
程者可结合铣削的工艺性等问题根据具体情况去选择合适的进刃方式,在生产实
践中加以灵活变通和应用。