10外文翻译(1)
超声波加工中英文对照外文翻译文献

超声波加工中英文对照外文翻译文献超声波加工中英文对照外文翻译文献(文档含英文原文和中文翻译)超声波加工综述摘要超声波加工适合切削不导电、脆性材料,例如工程陶瓷。
与其他非传统加工,如激光束、电火花加工等不同,超声波加工不会导致工件表面热损伤或显著的残余应力,这对脆性材料尤其重要。
超声波加工的基本原理,包括材料去除原理,各类操作参数对材料切除率、刀具磨损、工件精确度要求都有叙述,并着重表述了在加工工程陶瓷上的应用,制造复杂的三维立体陶瓷的问题也在叙述当中。
1 概述超声波加工及其应用超声波加工是一种非传统机械切削技术,通常与低材料去除率有关,它并不被加工材料的导电率和化学特性所限制,它用于加工金属和非金属材料,非常适合于脆性大,硬度高于40HRC[6–12]的材料,比如无机玻璃、硅片、镍、钛合金等等 [13–24],有了它,76um 的小孔也能加工,但是被加工的孔深度与直径之比限制在 3 比 1 之内 [8, 12]。
超声波加工的历史可以追溯到 1927 年,R. W. Wood 和 A. L. Loomis 发表的论文,1945年。
有关于超声波的第一项专利给了 L. Balamuth,现在超声波加工已经分化很多领域,超声波钻削、超声波切削、超声波尺寸加工、超声波研磨技术和悬浮液钻孔法,然而,在 20世纪 50 年代初只普遍知道超声波冲磨或 USM[8,25, 28, 30, 31]。
在超声波加工中,高频率的电能通过换能器/增幅器被转变为机械振动,之后通过一个能量集中装置被传送出去, 例如变幅杆/刀具组件[1, 17, 18, 30, 32]。
这导致刀具沿着其纵向轴线以振幅 0-50μm 高频率振动(通常≥20KHz)[16, 33, 34],典型额定功率范围从50~3000W[35]不等,在某些机器上可以达到 4kw。
一个受控静负载被施加于刀具和磨料悬浮液(由研磨材料的混合物组成、例如碳化硅,碳化硼等等,悬浮在水或油中)被泵传送到切削区域,刀具的振动导致磨料颗粒悬浮在刀具和工件表面间,通过微型片冲击工件表面从而去除材料[19]。
外文翻译(英文)
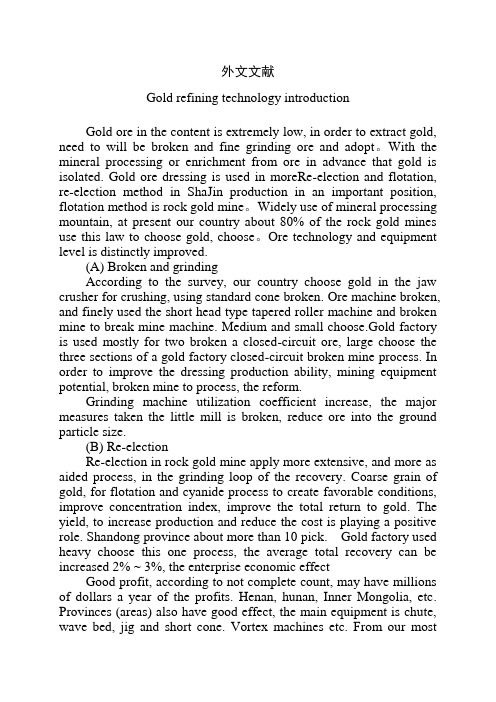
外文文献Gold refining technology introductionGold ore in the content is extremely low, in order to extract gold, need to will be broken and fine grinding ore and adopt。
With the mineral processing or enrichment from ore in advance that gold is isolated. Gold ore dressing is used in moreRe-election and flotation, re-election method in ShaJin production in an important position, flotation method is rock gold mine。
Widely use of mineral processing mountain, at present our country about 80% of the rock gold mines use this law to choose gold, choose。
Ore technology and equipment level is distinctly improved.(A) Broken and grindingAccording to the survey, our country choose gold in the jaw crusher for crushing, using standard cone broken. Ore machine broken, and finely used the short head type tapered roller machine and broken mine to break mine machine. Medium and small choose.Gold factory is used mostly for two broken a closed-circuit ore, large choose the three sections of a gold factory closed-circuit broken mine process. In order to improve the dressing production ability, mining equipment potential, broken mine to process, the reform.Grinding machine utilization coefficient increase, the major measures taken the little mill is broken, reduce ore into the ground particle size.(B) Re-electionRe-election in rock gold mine apply more extensive, and more as aided process, in the grinding loop of the recovery. Coarse grain of gold, for flotation and cyanide process to create favorable conditions, improve concentration index, improve the total return to gold. The yield, to increase production and reduce the cost is playing a positive role. Shandong province about more than 10 pick. Gold factory used heavy choose this one process, the average total recovery can be increased 2% ~ 3%, the enterprise economic effectGood profit, according to not complete count, may have millions of dollars a year of the profits. Henan, hunan, Inner Mongolia, etc. Provinces (areas) also have good effect, the main equipment is chute, wave bed, jig and short cone. Vortex machines etc. From our mostgold mine to see, float-heavy joint process (flotation tailings used heavy Choose) suitable for.(C) FlotationAccording to the survey, 80% of rock in the gold mines flotation method selected gold, the output of the concentrate more. Sent to non-ferrous smelter processing. Because of leaching gold cyanide process of development and enterprise to improve economic efficiency. Good, reduce concentrate transportation loss, in recent years the product structure has experienced a greater change, take more local processing (of course also because of mineral smelting and the contradiction between the problems and valuation, forcing the mine in situ to place Richard) prompted the flotation process have larger development, in the gold production occupies an important position in the. Usually Priority of flotation and mixing floatation two craft. In recent years in the process modification and potions add system .With new progress, flotation recoveries also increased significantly. More than 40 selected according to the national gold factory, flotation work.(D) The choose-leaching gold technology sector1. Mix mercury law of leaching goldMix mercury method of leaching gold process is a kind of old mention gold process, easy, and economic, and is suitable for coarse grains. Monomer recovery of gold. Our country many gold mine still follow the method. Along with the development of the gold production and the progress of science and technology, mix mercury law of leaching gold process is also constantly have improved and perfected. Due to the environment.The increasingly strict requirements, some mining cancelled mix mercury assignments, as heavy choose, the flotation and cyanide process of leaching gold.process replaced. In the gold production, mixed mercury method of leaching gold technology still has its important role in the domestic and foreign are should be with a practical example. At present in zhangjiakou, hebei province, liaoning erdaogou, jilin jiapigou, shandong etc many gold incorporated. Mine the process application. Liaoning erdaogou gold mine was a single flotation process, according to the ore properties instead.2. Of leaching gold cyanide process technologyCyanide process technology of leaching gold from oreconcentrate is modern or extraction of the main method of gold. Cyanide process mention.Gold technologies include: by roasting-cyanide leaching process, leaching of pulp washing filtering, kau liquid or are the cicc pulp.The extraction and the finished product and so on several basic processes of smelting. China's gold mines are the two basic existing factory. Kind of leaching gold process, one kind is dense continuous against washing machine, with zinc powder replacement precipitation back. The gold of so-called ordinary cyanide process of leaching gold process (CCD method and CCF law), the other is without filter washing, the active carbon adsorption in the pulp are directly from the recovery of gold without filter are carbon plasma process (CIP method and CIL law).Ordinary cyanide process of leaching gold process according to the different materials handled and two .(E) Heap leaching process for productionGold resources in China, low grade oxidation of ore has certain proportion, deal with this kind of ore.The routine of leaching gold cyanide process technology not economically viable, and the production process heap leaching, there are economic effect. The victims. Further expand the production scale heap leaching, is increase China's gold production of one of the path.20. At the end of the 70 s, China began to low grade contain gold ore heap leaching oxidation of the production process research, liaoning dandong hushan gold small-scale production trials are successful, successively in henan spirit lake, silver Hole slope, yunnan MoJiang, hebei worship ritual, Inner Mongolia and some of the mine in chifeng application, take more satisfactory economic effect, low grade for the gold ore containing the oxidation of the development and utilization of the opened up.。
外文翻译指导记录怎么写
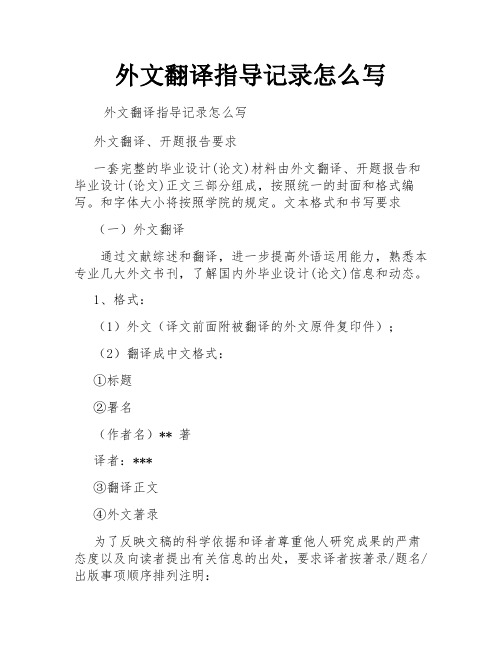
外文翻译指导记录怎么写外文翻译指导记录怎么写外文翻译、开题报告要求一套完整的毕业设计(论文)材料由外文翻译、开题报告和毕业设计(论文)正文三部分组成,按照统一的封面和格式编写。
和字体大小将按照学院的规定。
文本格式和书写要求(一)外文翻译通过文献综述和翻译,进一步提高外语运用能力,熟悉本专业几大外文书刊,了解国内外毕业设计(论文)信息和动态。
1、格式:(1)外文(译文前面附被翻译的外文原件复印件);(2)翻译成中文格式:①标题②署名(作者名)** 著译者:***③翻译正文④外文著录为了反映文稿的科学依据和译者尊重他人研究成果的严肃态度以及向读者提出有关信息的出处,要求译者按著录/题名/出版事项顺序排列注明:期刊——著者,题名,期刊名称,出版年,卷号(期号),起始页码。
书籍——著者,书名、版次(第一版不标注),出版地,出版者,出版年,起始页码。
2、内容要求:(1)阅读每位学生在文献查阅环节中,必须阅读5~10万个印刷符号的外语文献资料(最好阅读与课题或本专业有联系的内容),择其重要的翻译1~2万个印刷符号(约3000汉字)。
(2)翻译①标题应真实地反映出翻译外文的主体内容或原外文标题内容,一般控制在20个汉字以内。
可以用副标题对标题予以补充说明;②标题下方正中为外文作者署名;③外文翻译成中文的内容;④外文著录(二)开题报告1、格式:(1)课题名称;(2)学生、专业、指导教师和教学单位署名;(3)开题报告的正文撰写。
2、内容要求:(1)课题名称要求与毕业设计(论文)正文标题名称一致(一般控制在20个汉字以内,可以用副标题对标题予以补充说明)。
(2)学生、指导教师和教学单位署名:题目下方中间是学生签名,学生签名下方是专业名称,专业名称下方是指导老师签名,指导老师签名下方是教学单位签名(教学单位指学院)。
(3)开题报告的正文撰写要求包括(不少于2500字):①课题来源②研究目的和意义③研究的内容与途径④国内外研究现状与发展趋势通过提问和分析问题,综合前人文献提出的理论和事实,比较各种学术观点,明确所提问题的历史、现状和发展方向。
机械专业毕业设计外文翻译10
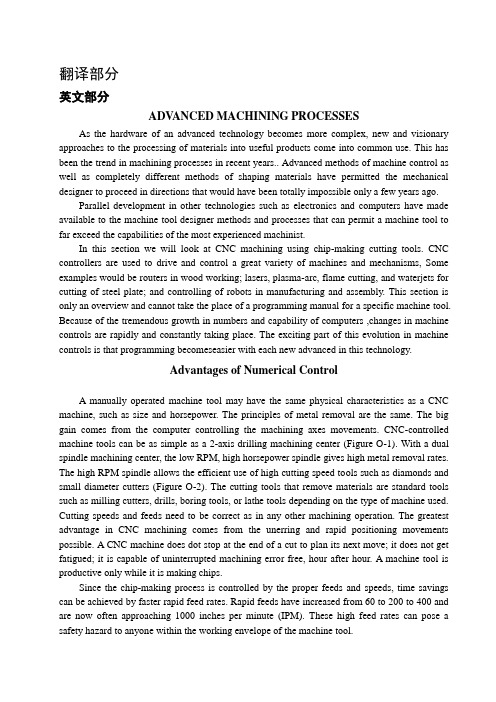
翻译部分英文部分ADV ANCED MACHINING PROCESSESAs the hardware of an advanced technology becomes more complex, new and visionary approaches to the processing of materials into useful products come into common use. This has been the trend in machining processes in recent years.. Advanced methods of machine control as well as completely different methods of shaping materials have permitted the mechanical designer to proceed in directions that would have been totally impossible only a few years ago.Parallel development in other technologies such as electronics and computers have made available to the machine tool designer methods and processes that can permit a machine tool to far exceed the capabilities of the most experienced machinist.In this section we will look at CNC machining using chip-making cutting tools. CNC controllers are used to drive and control a great variety of machines and mechanisms, Some examples would be routers in wood working; lasers, plasma-arc, flame cutting, and waterjets for cutting of steel plate; and controlling of robots in manufacturing and assembly. This section is only an overview and cannot take the place of a programming manual for a specific machine tool. Because of the tremendous growth in numbers and capability of comp uters ,changes in machine controls are rapidly and constantly taking place. The exciting part of this evolution in machine controls is that programming becomeseasier with each new advanced in this technology.Advantages of Numerical ControlA manually operated machine tool may have the same physical characteristics as a CNC machine, such as size and horsepower. The principles of metal removal are the same. The big gain comes from the computer controlling the machining axes movements. CNC-controlled machine tools can be as simple as a 2-axis drilling machining center (Figure O-1). With a dual spindle machining center, the low RPM, high horsepower spindle gives high metal removal rates. The high RPM spindle allows the efficient use of high cutting speed tools such as diamonds and small diameter cutters (Figure O-2). The cutting tools that remove materials are standard tools such as milling cutters, drills, boring tools, or lathe tools depending on the type of machine used. Cutting speeds and feeds need to be correct as in any other machining operation. The greatest advantage in CNC machining comes from the unerring and rapid positioning movements possible. A CNC machine does dot stop at the end of a cut to plan its next move; it does not get fatigued; it is capable of uninterrupted machining error free, hour after hour. A machine tool is productive only while it is making chips.Since the chip-making process is controlled by the proper feeds and speeds, time savings can be achieved by faster rapid feed rates. Rapid feeds have increased from 60 to 200 to 400 and are now often approaching 1000 inches per minute (IPM). These high feed rates can pose a safety hazard to anyone within the working envelope of the machine tool.Complex contoured shapes were extremely difficult to product prior to CNC machining .CNC has made the machining of these shapes economically feasible. Design changes on a part are relatively easy to make by changing the program that directs the machine tool.A CNC machine produces parts with high dimensional accuracy and close tolerances without taking extra time or special precautions, CNC machines generally need less complex work-holding fixtures, which saves time by getting the parts machined sooner. Once a program is ready and production parts, each part will take exactly the same amount of time as the previous one. This repeatability allows for a very precise control of production costs. Another advantage of CNC machining is the elimination of large inventories; parts can be machined as needs .In conventional production often a great number of parts must be made at the same time to be cost effective. With CNC even one piece can be machined economically .In many instances, a CNC machine can perform in one setup the same operations that would require several conventional machines.With modern CNC machine tools a trained machinist can program and product even a single part economically .CNC machine tools are used in small and large machining facilities and range in size from tabletop models to huge machining centers. In a facility with many CNC tools, programming is usually done by CNC programmers away from the CNC tools. The machine control unit (MCU) on the machine is then used mostly for small program changes or corrections. Manufacturing with CNC tools usually requires three categories of persons. The first is the programmer, who is responsible for developing machine-ready code. The next person involved is the setup person, who loads the raw stork into the MCU, checks that the co rrect tools are loaded, and makes the first part. The third person is the machine and unloads the finished parts. In a small company, one person is expected to perform all three of these tasks.CNC controls are generally divided into two basic categories. One uses a ward address format with coded inputs such as G and M codes. The other users a conversational input; conversational input is also called user-friendly or prompted input. Later in this section examples of each of these programming formats in machining applications will be describes.CAM and CNCCAM systems have changed the job of the CNC programmer from one manually producing CNC code to one maximizing the output of CNC machines. Since CNC machine tools are made by a great number of manufacturers, many different CNC control units are in use. Control units from different manufacturers use a variety of program formats and codes. Many CNC code words are identical for different controllers, but a great number vary from one to another.To produce an identical part on CNC machine tools with different controllers such as one by FANCU, OKUMA or DYNAPATH, would require completely different CNC codes. Each manufacturer is constantly improving and updating its CNC controllers. These improvements often include additional code words plus changes in how the existing code works.A CAM systems allows the CNC programmer to concentrate on the creation of an efficient machining process, rather then relearning changed code formats. A CNC programmer looks atthe print of a part and then plans the sequence of machining operations necessary to make it (Figure O-3). This plan includes everything, from the selection of possible CNC machine tools, to which tooling to use, to how the part is held while machining takes place. The CNC programmer has to have a thorough understanding of all the capacities and limitations of the CNC machine tools that a program is to be made for. Machine specifications such as horsepower, maximum spindle speeds, workpiece weight and size limitations, and tool changer capacity are just some of the considerations that affect programming.Another area of major importance to the programmer is the knowledge of machining processes. An example would be the selection of the surface finish requirement specified in the part print. The sequence of machining processes is critical to obtain acceptable results. Cutting tool limitations have to be considered and this requires knowledge of cutting tool materials, tool types, and application recommendations.A good programmer will spend a considerable amount of time in researching the rapidly growing volume of new and improved tools and tool materials. Often the tool that was on the cutting edge of technology just two years ago is now obsolete. Information on new tools can come from catalogs or tool manufacturers' tooling engineers. Help in tool selection or optimum tool working conditions can also be obtained from tool manufacturer software. Examples would be Kennametal's "TOOLPRO", software designed to help select the best tool grade, speed, and feed rates for different work materials in turning application. Another very important feature of "TOOLPRO" is the display of the horsepower requirement for each machining selection. This allow the programmer to select a combination of cutting speed, feed rate, and depth of cut that equals the machine's maximum horsepower for roughing cuts. For a finishing cut, the smallest diameter of the part being machined is selected and then the cutting speed varied until the RPM is equal to the maximum RPM of the machine. This helps in maximizing machining efficiency. Knowing the horsepower requirement for a cut is critical if more than one tool is cutting at the same time.Software for a machining center application would be Ingersoll Tool Company's "Actual Chip Thickness", a program used to calculate the chip thickness in relation to feed-per-tooth for a milling cutter, especially during a shallow finishing cut. Ingersoll's "Rigidity Analysis" software ealculates tool deflection for end mills as a function of tool stiffness and tool force.To this point we looked at some general qualifications that a programmer should possess. Now we examine how a CAM system works. Point Control Company's SmartCam system uses the following approach. First, the programmer makes a mental model of the part to be machined. This includes the kind of machining to be performed-turning or milling. Then the part print is studied to develop a machining sequence, roughing and finishing cuts, drilling, tapping, and boring operations. What work-holding device is to be used, a vise or fixture or clamps? After these considerations, computer input can be started. First comes the creation of a JOBPLAN. This JOBPLAN consists of entries such as inch or metric units, machine type, part ID, type of workpiece material, setup notes, and a description of the required tools.This line of information describes the tool by number, type, and size and includes theappropriate cutting speed and feed rate. After all the selected tools are entered, the file is saved.The second programming step is the making of the part. This represents a graphic modeling of the projected machining operation. After selecting a tool from the prepared JOBPLAN, parameters for the cutting operation are entered. For a drill, once the coordinate location of the hole and the depth are given, a circle appears on that spot. If the location is incorrect, the UNDO command erases this entry and allows you to give new values for this operation. When an end mill is being used, cutting movements (toolpath) are usually defined as lines and arcs. As a line is programmed, the toolpath is graphically displayed and errors can be corrected instantly.At any time during programming, the command SHOWPATH will show the actual toolpath for each of the programmed tools. The tools will be displayed in the sequence in which they will be used during actual machining. If the sequence of a tool movement needs to be changed, a few keystrokes will to that.Sometimes in CAM the programming sequence is different from the actual machining order. An example would be the machining of a pocket in a part. With CAM, the finished pocket outline is programmed first, then this outline is used to define the ro ughing cuts to machine the pocket. The roughing cuts are computer generated from inputs such as depth and width of cut and how much material to leave for the finish cut. Different roughing patterns can be tried out to allow the programmer to select the most efllcient one for the actual machining cuts. Since each tool is represented by a different color, it is easy to observe the toolpath made by each one.A CAM system lets the programmer view the graphics model from varying angles, such as a top, front, side, or isometric view. A toolpath that looks correct from a top view, may show from a front view that the depth of the cutting tool is incorrect. Changes can easily be made and seen immediately.When the toolpath and the sequence of operations are satisfactory, machine ready code has to be made. This is as easy as specifying the CNC machine that is to be used to machine the part. The code generator for that specific CNC machin e during processing accesses four different files. The JOBPLAN file for the tool information and the GRAPHICE file for the toolpath and cutting sequence. It also uses the MACHINE DEFINE file which defines the CNC code words for that specific machine. This file also supplies data for maximum feed rates, RPM, toolchange times, and so on. The fourth file taking part in the code generating process is the TEMPLATE file. This file acts like a ruler that produces the CNC code with all of its parts in the right place and sequence. When the code generation is complete, a projected machining time is displayed. This time is calculated from values such as feed rates and distances traveled, noncutting movements at maximum feed rates between points, tool change times, and so on. The projected machining time can be revised by changing tooling to allow for higher metal removal rates or creating a more efficient toolpath. This display of total time required can also be used to estimate production costs. If more then one CNC machine tool is available to machine this part, making code and comparing the machining time may show that one machine is more efficient than the others.CAD/CAMAnother method of creating toolpath is with the use of a Computer-aided Drafting (CAD) file. Most machine drawings are created using computers with the description and part geometry stored in the computer database. SmartCAM, though its CAM CONNECTION, will read a CAD file and transfer its geometry represents the part profile, holes, and so on. The programmer still needs to prepare a JOBPLAN with all the necessary tools, but instead of programming a profile line by line, now only a tool has to be assigned to an existing profile. Again, using the SHOWPA TH function will display the toolpath for each tool and their sequence. Constant research and developments in CAD/CAM interaction will change how they work with each other. Some CAD and CAM programs, if loaded on the same computer, make it possible to switch between the two with a few keystrokes, designing and programming at the same time.The work area around the machine needs to be kept clean and clear of obstructions to prevent slipping or tripping. Machine surfaces should not be used as worktables. Use proper lifting methods to handle heavy workpieces, fixtures, or heavy cutting tools. Make measurements only when the spindle has come to a complete standstill. Chips should never be handled with bare hands.Before starting the machine make sure that the work-holding device and the workpiece are securely fastened. When changing cutting tools, protect the workpiece being machined from damage, and protect your hands from sharp cutting edges. Use only sharp cutting tools. Check that cutting tools are installed correctly and securely.Do not operate any machine controls unless you understand their function and what the y will do.The Early Development Of Numerically Controlled Machine ToolsThe highly sophisticated CNC machine tools of today, in the vast and diverse range found throughout the field of manufacturing processing, started from very humble beginnings in a number of the major industrialized countries. Some of the earliest research and development work in this field was completed in USA and a mention will be made of the UK's contribution to this numerical control development.A major problem occurred just after the Second World War, in that progress in all areas of military and commercial development had been so rapid that the levels of automation and accuracy required by the modern industrialized world could not be attained from the lab our intensive machines in use at that time. The question was how to overcome the disadvantages of conventional plant and current manning levels. It is generally ackonwledged that the earliest work into numerical control was the study commissioned in 1947 by the US governme nt. The study's conclusion was that the metal cutting industry throughout the entire country could not copy with the demands of the American Air Force, let alone the rest of industry! As a direct result of the survey, the US Air Force contracted the Persons Corporation to see if they could develop a flexible, dynamic, manufacturing system which would maximize productivity. TheMassachusetts Institute of Technology (MIT) was sub-contracted into this research and development by the Parsons Corporation, during the period 1949-1951,and jointly they developed the first control system which could be adapted to a wide range of machine tools. The Cincinnati Machine Tool Company converted one of their standard 28 inch "Hydro-Tel" milling machines or a three-axis automatic milling made use of a servo-mechanism for the drive system on the axes. This machine made use of a servomechanism for the drive system on the axes, which controlled the table positioning, cross-slide and spindle head. The machine cab be classified as the first truly three axis continuous path machine tool and it was able to generate a required shape, or curve, by simultaneous slide way motions, if necessary.At about the same times as these American advances in machine tool control were taking Place, Alfred Herbert Limited in the United Kingdom had their first Mutinous path control system which became available in 1956.Over the next few years in both the USA and Europe, further development work occurred. These early numerical control developments were principally for the aerospace industry, where it was necessary to cut complex geometric shapes such as airframe components and turbine blades. In parallel with this development of sophisticated control systems for aerospace requirements, a point-to-point controller was developed for more general machining applications. These less sophisticated point-to-point machines were considerably cheaper than their more complex continuous path cousins and were used when only positional accuracy was necessary. As an example of point-to-point motion on a machine tool for drilling operations, the typical movement might be fast traverse of the work piece under the drill's position-after drilling the hole, anther rapid move takes place to the next hole's position-after retraction of the drill. Of course, the rapid motion of the slideways could be achieved by each axis in a sequential and independent manner, or simultaneously. If a separate control was utilisec for each axis, the former method of table travel was less esse ntial to avoid any backlash in the system to obtain the required degree of positional accuracy and so it was necessary that the approach direction to the next point was always the same.The earliest examples of these cheaper point-to-point machines usually did not use recalculating ball screws; this meant that the motions would be sluggish, and sliderways would inevitably suffer from backlash, but more will be said about this topic later in the chapter.The early NC machines were, in the main, based upon a modified milling machine with this concept of control being utilized on turning, punching, grinding and a whole host of other machine tools later. Towards the end of the 1950s,hydrostatic slideways were often incorporated for machine tools of highly precision, which to sonic extent overcame the section problem associated with conventional slideway response, whiles averaging-out slideway inaccuracy brought about a much increased preasion in the machine tool and improved their control characteristics allows "concept of the machining center" was the product of this early work, as it allowed the machine to manufacture a range of components using a wide variety of machining processes at a single set-up, without transfer of workpieces to other variety machine tools. A machining center differed conceptually in its design from that of a milling machine, In that thecutting tools could be changed automatically by the transfer machanism, or selector, from the magazine to spindle, or vice versa.In this ductively and the automatic tool changing feature enabled the machining center to productively and efficiently machine a range of components, by replacing old tools for new, or reselecting the next cutter whilst the current machining process is in cycle.In the mid 1960s,a UK company, Molins, introduced their unique "System 24" which was meant represent the ability of a system to machine for 24 hours per day. It could be thought of as a "machining complex" which allowed a series of NC single purpose machine tools to be linked by a computerized conveyor system. This conveyor allowed the work pieces to be palletized and then directed to as machine tool as necessary. This was an early, but admirable, attempt at a form of Flexible manufacturing System concept, but was unfortunately doomed to failure. Its principal weakness was that only a small proportion of component varieties could be machine at any instant and that even fewer work pieces required the same operations to be performed on them. These factors meant that the utilization level was low, coupled to the fact that the machine tools were expensive and allowed frequent production bottlenecks of work-in-progress to arise, which further slowed down the whole operation.The early to mid-1970s was a time of revolutionary in the area of machine tool controller development, when the term computerized numerical control (CNC) became a reality. This new breed of controllers gave a company the ability to change work piece geometries, together with programs, easily with the minimum of development and lead time, allowing it to be economically viable to machine small batches, or even one-off successfully. The dream of allowing a computerized numerical controller the flexibility and ease of program editing in a production environment became a reality when two ralated factors occurred.These were:the development of integrated circuits, which reduces electronics circuit size, giving better maintenance and allowing more standardization of desing; that general purpose computers were reduced in size coupled to the fact that their cost of production had fallen considerably.The multipie benefits of cheaper electorics with greater reliability have result in the CNC fitted to the machine tools today, with the power and sophistication progtessing considerably in the last few years, allowing an almost artificial intelligence(AI) to the latest systems. Over the years, the machine tools builders have produced a large diversity in the range of applications of CNC and just some of those development will be reviewed in V olume Ⅲ。
外文翻译(1)(1)

注:红色字体表示语句不明白的地方,请求学姐帮忙。
聚亚烷基二醇的化学结构和它们在含水环境中的好氧生物降解性之间的关系简要:使用一组聚合流体,其中包括聚乙二醇、聚丙二烯(PPG)、不同EO/PO 比率的环氧乙烷(EO)的无规共聚物和环氧丙烷(PO),对聚亚烷基醇(PAG)的化学结构和它们的生物降解性之间的关系进行研究以及用PAG的醚和酰基部分封端。
被测试的PAG中有一个均分子量范围在350-3600Da,它们的差异是由其聚合物主链的直链(二醇型)或支链(三元醇型)分子。
PAG的最终生物降解能力是根据ISO14593(CO2顶空试验)用非预曝光(如在OECD310试验)和预曝光(改编)接种物来确定。
带有PPG结构和二元醇或三元醇的EO/PO共聚物,均分子量不超过1000沓的PAG,被认为是易于生物降解的。
他们的最终生物降解可超过60%的限制(根据OECD310测试标准)。
具有共聚结构并且MW值在1000-3600之间的PAG不易生物降解,但它们可以被看做是那些固有的最终降解物。
在PAG结构中EO含量的增长和末端羟基的酰化与羧酸基团有利地影响了他们的生物降解性。
含末端醚基团封端的PAG似乎是耐生物降解的。
关键词生物降解、聚亚烷基二醇、PAG、PPG、封顶PAG、ISO14593。
引言:术语中的聚亚烷基二醇-PAG,以及在相关文献中的PAG,例如,聚乙二醇,聚醚和聚(烯化氧)中使用的PAG术语都是带有环氧化物结构烯化氧聚合得到的化合物。
PAG主要是通过使用乙烯和丙烯的氧化物合成的,不常使用丁二醇和更高的烯烃氧化物。
PAG类化合物(不同的分子量,性能和应用)最常用的包括氧化乙烯或丙烯均聚物氧化物以及乙烯和丙烯氧化物的无规或嵌段共聚物。
PAG的分子结构不仅取决于种类和亚烷基氧化物的比例,而且还取决于用于聚合反应的引发剂分子的类型(单-,二-或多官能分子具有2个以上活泼氢原子)。
引发剂影响PAG分子的末端羟基基团和聚合物链的类型,其可以是线性的(单醇及二醇型)或支链的(多元醇的数类型)。
外文翻译英语原文编号01

Vol.25 No.2 PANG Chaoming et al: Methods of Modifying the Brittle (156)DOI 10.1007/s11595-010-1156-yMethods of Modifying the Brittle Behavior ofCementitious CompositesPANG Chaoming1, SUN Wei1, LEUNG Christopher KY2(1.College of Materials Science and Engineering, Southeast University, Jiangsu Key laboratory of Construction Materials, Nanjing 211189,China;2. Department of Civil and Environmental Engineering, Hong Kong University of Science and Technology, Hong Kong, China SAR)Abstract: We put forward effective methods of increasing the tensile strain of cementitiouscomposites with 2% PVA fiber and high fly ash content. The test results show that curing condition hasa significantly effect on the tensile performance. It is approved that the specimens incorporated ap-propriate volume fraction rubber powder and lightweight aggregate greatly increase the tensile strain ofcomposites at medium-term age, but indefinitely at long-term age. To a certain extent, EVA can limitedlyenhance the tensile performance of comentitious composites owing to the formation of polymer membraneand the hindered hydration of cement.Key word: high-ductility cementitious composites (HDCC); tensile properties; high content offly ash; rubber powder; light aggregate; ethylene vinyl alcohol latex powder1 IntroductionCementitious composites are widely used as the majority of structural materials. However, cementitious composites are limited to some special projects due to the inherently brittle behavior. Most efforts have been made to modify the brittle behavior of cementitious composites all along. As a result, the fiber reinforced cementitious composites (FRCC) occurred. In comparison to plain concrete, FRC usually deteriorates the tensile or bending properties by the formation of several cracks and a main crack. In the past two decades, Li, Leung and Wu etc[1-3] investigated the bridging stress of fiber and proposed the theory for high-ductility cementitious composites (here-after abbreviated as HDCCs) or pseudo ductility cemen-titious composites or pseudo strain hardening cementi-tious composites, based on the two nondimensionalized parameters energy absorption rate and normalized flaw size. It has been demonstrated that the ductility behaviors of brittle materials can be achieved by multiple cracks in steady state along the length of the specimen and behave pseudo strain hardening (abbr. PSH). Hereafter, the theories for PSH in the cementitious composites were gradually developed by Li and his co-workers, and the particular theory for “composite design”, based on the micro mechanics parameter, by emphasizing the proper integrant materials and interface was proposed[4,5]. The cementitious composite with high tensile strain capacity of 3%-6%, whose strain capacity is far outperforming conventional cementitious composites, was achieved[6].Recently increasing researchers are interesting to the new type of fiber reinforced cementitious composite. However, it is not easy to achieve PSH in discontinuous random fiber reinforced. Strain due to a little deviation of raw materials occur even if the well-known same mixture proportion of ECC is used due to a little deviation of raw materials. Meanwhile, the design method of existing theory depend on known experimental micro mechanics parameters, such as the fracture toughness, fiber content, fiber strength, fiber distribution, the bridging stress and interface properties between fiber matrix, etc. Moreover, it is very difficult to achieve the accurate fiber distribu-tion and bridging stress due to the randomization and inhomogeneity of the distribution of fiber in composites. But the micromechanical parameters and the ductile be-havior is strongly affected by the bridging stress governed by fiber debonding, fiber bending, fiber rupture, matrix spalling and their coupling[2].The focus in the current study is to discover the ef-ficacious methods to increase the tensile strain of HDCC. It is well know that curing conditions have a significantly©Wuhan University of Technology and Springer-Verlag Berlin Heidelberg 2010 (Received: Jan. 6, 2009; Accepted: Oct. 16, 2009)PANG Chaoming(庞超明): Ph D candidate; E-mail: pangchao@seu. edu. cnJournal of Wuhan University of Technology-Mater. Sci. Ed. Feb.2010157conditions were used for comparison, considering that the structures in practice project are often exposed to different environment and different curing condition are usually applied according to the lab environment in the different researches. For the brittle cementitious com-posites, the matrix cracking strength, which is determined by the matrix toughness and the largest crack or flaw in the stress section of specimen provided that the matrix cracking is controlled by fracture process, does not de-crease unlimitedly but reaches a lower bound at steady state cracking stress with the growing flaw size [7]. Moreover, the discontinuous pre-existing flaw or mi-cro-voids may relax the crack-tip stress triaxiality, dif-fuse the intensity of crack-tip stress singularity and consume more energy. To ensure the formation of multiple cracks, it is desirable to introduce a rtificial flaws in the matrix to reduce its crack tip toughness and increase the crack size due to energy absorption of flaw [8]. Therefore, different materials, such as rubber powder and fine lightweight aggregate, were added to the composites to increase the strain capacity.2 ExperimentalSpecial green island brand P·II 52.5 cement was used. The range of particle size of fly ash is mainly 2-10 μm, and the active index of compressive strength at 7 days, 28 days and 90 days are the 86%, 84% and 96% respectively followed by ASTM C311-04. Polyvinyl alcohol fiber (abbr. PVAF) produced by Japan Kuraray Limited Corporation was used, and its density, length, diameter were 1.3 g/cm 3, 12 mm, 38 μm respectively,also its elastic modulus and rate of elongation is 33 GPaand 6.5% respectively.The particle size of silica fume, silica filler and silica sand used is 1-20 μm, 1-15 μm and 50-200 μm respec-tively. ADVA105 superplastics admixture (abbr. Sp) was %produced by Grace Co.LTD and its solid content is 23. SP4000 (abbr. SP4), which is ethylene vinyl alcohol (abbr. EVA) latex powder and is produced by Japan Kuraray Trading Co.LTD, was used in this study. The particle size of lightweight aggregate (abbr. LA) is between 1 mm and 3 mm, whose specific density is 1 500 kg/m 3, and the loose volume weight is about 780 kg/m 3. Rubber pow-der with the particle size of 0.4 mm was also used.The specimen was demoulded 24 hours after casting, where the temperature and relative humidity was about 20±2 ℃ and (60±5)% respectively, then cured in water at curing room , where the temperature is 27 ℃ (ac-cording to the BS standard). The nominal sizes used for tensile performance and compressive performance are about 350×50×15 mm and 40×40×40 mm respec-tively. The dimensions of the specimen were accurately measured by vernier caliper and all the specimens were polished to smooth surface before testing to obtain ac-curate experimental results, and at least three specimens were tested at each age.The tensile performance was tested under the dis-placement control in the MTS810-25 kN materials test-ing system with the displacement rate of 0.15 mm/min. Linear variable displacement transducer was used to measure the displacement at the gage length of 150 mm for the more accuracy purpose. The first crack strain εfc , the peak strain εp and the maximum strain εm repre-sent to the strain corresponding to the first crack stress σTc when the first crack occurred, peak stress σTp when the stress reaches the peak, and the strain when the stress descends up to 90% σTp , respectively.3 Results3.1 Effect of curing conditions on me-chanical properties of HDCCAccording to previous work, two mix proportions shown in Table 1 were used, i e , SP4 and W1 with high volume fraction fly ash and low ratio of water to binder (cement and fly ash). Table 1 Mix proportion in mass of HDCC No. cement FA SP4 sand water Sp PVAF SP4 1 3.9 0.1 1.0 1.1 0.022 0.090 W1 1 4.0 0 1.0 1.0 0.023 0.096For the purpose of comparing the effect of different curing condition on the tensile performance, four types of curing conditions were applied in mixture SP4 as fol-lowing: full dry curing in room temperature condition after demoulded, which corresponds to symbol D in the denominated title in Table 2, dry curing in room tem-perature condition after 3-day curing in water corre-sponding to symbol W3D, dry curing in room tempera-ture condition after 7-day water curing corresponding to symbol W7D, and 28-day water curing corresponding to symbol W. The only two types of curing conditions wereused in mixture W1: dry curing in room temperature condition after 7 days water curing and full water curing. Table 2 list the test results of the tensile strength and strain and compressive strength on different curing con-ditions at the age of 7-day and 28-day.Vol.25 No.2 PANG Chaoming et al : Methods of Modifying the Brittle …1583.2 Effect of rubber powder on mechanic-al properties of HDCCThe specimen without rubber powder is regarded as control specimen, and two mixtures of HDCCs with the rubber powder were prepared. SR7 and SR11 represent for HDCC of the volume fraction of 7% and 11%, re-spectively. For estimating the long-term performance, the accelerated curing method was conducted, that is, after cured in water for 7 days, at least three specimens were put to the heat curing room for 72 hours, where the temperature and relative humidity are 80 ℃%and 95respectively, the mechanical performance was measured after being cooled down in the room temperature condi-tion. The mix proportion used and test results are sum-marized in Table 3, Table 4 respectively. Heat curing corresponds to symbol HC. Fig.1 shows the tensile stress versus strain curves of SR7 and SR11 at 28 days.3.3 Effect of lightweight aggregate onmechanical properties of HDCC For the purpose of researching the effect of light-weight aggregate on the tensile strain of HDCC with highflyash content, the volume fraction of 3.5% was incor-porated into the mixture, and the mix proportion was listed in Table 5. The specimen FA3 and FA3LA corre-spond to control specimen and specimen with lightweight aggregate, respectively.The test results are shown in Table 6. The condition of heat curing is the same as mentioned above. Fig.2(a) and Fig.2(b) showed the typical stress vs strain curve of FA3 and FA3LA3.5 at different age: 7 days, 28 days and heat curing 3 days.Table 2 Test results of HDCC on different curing conditionsSP4D SP4W3D SP4W7D SP4W W1 7-day 28-day 7-day 28-day 28-day 90-day 7-day 28-day W7 W28 W7DσTfc /MPa 2.68 2.36 2.91 2.54 3.26 3.28 2.70 3.36 2.76 3.65 3.62 εfc /% 0.080 0.069 0.075 0.096 0.080 0.089 0.119 0.060 0.088 0.047 0.128 σTp /MPa 3.30 3.39 3.76 3.14 4.07 3.62 3.17 4.02 3.27 3.81 4.69εp /% 1.53 3.95 2.69 2.56 2.82 2.58 2.78 0.77 1.050.35 2.94 εm /% 1.69 4.28 2.80 2.79 3.54 2.66 2.97 1.81 1.360.54 3.39 σcom /MPa 22.8 27.2 — — — — 23.4 36.0 35.8 58.9 — Table 3 Mix proportion in mass of HDCC with different volume fraction of rubber powder No. Cement FA Filler Sand Rubber Water Sp PVAFControl 1 1.50 0.25 1.00 0 0.63 0.015 0.057 SR7 1 1.50 0.25 0.65 0.163 0.58 0.020 0.055 SR11 1 1.50 0.25 0.40 0.263 0.58 0.020 0.055 Table 4 Test results of HDCCs with different volume fraction of rubber powderControl SR7 SR117-day 28-day 90-day 7-day 28-day HC 7-day 28-day HCσTfc /MPa 3.58 4.61 3.81 2.31 2.60 3.63 2.19 2.31 3.28 εfc /% 0.050 0.042 0.027 0.036 0.022 0.039 0.034 0.051 0.041 σTp/MPa 4.30 5.05 4.53 2.49 3.00 3.81 2.72 3.18 3.57 εp /% 1.33 0.84 0.29 0.31 0.58 0.16 1.04 2.15 0.20 εm/% 1.59 0.98 0.39 0.54 1.07 0.71 1.40 2.49 0.34 σcom /MPa 49.6 66.2 — 29.7 35.7 40.5 24.8 31.4 37.0 Table 5 Mix proportion in mass No. Cement FA LA Sand Water Sp PVAF FA3 1 3 — 1 1 0.025 0.056 FA3LA 1 3 0.16 1 1 0.028 0.056 Table 6 Test results of HDCCs with or without lightweightaggregate FA3 FA3LA 7 d 28 d 90 d HC 7 d 28 d 90 d HCσTfc /MPa 1.42 2.68 3.60 4.38 2.86 3.15 3.25 6.42εfc /% 0.015 0.044 0.031 0.022 0.025 0.045 0.040 0.037 σTp /MPa 2.91 3.46 4.86 4.86 2.86 3.91 3.92 6.49εp /% 0.04 0.58 0.29 0.08 0.03 1.96 0.23 0.04 εm /% 1.16 0.96 0.66 0.31 1.40 2.07 0.54 0.38 σcom/MPa 21.5 44.7 69.5— 19.0 44.2 74.8 —Journal of Wuhan University of Technology-Mater. Sci. Ed. Feb.20101593.4 Effect of EVA powder on mechanicalproperties of HDCCA series of HDCCs specimens with or without EVA powder were also prepared, cured and tested at prescribed age followed by the test procedure. The condition of heat curing is also the same as mentioned above. The mix proportion used is listed in Table 7, and test results of tensile properties are presented in Table 8 and Fig.2(c) respectively. S is the control specimen, and SS4 is representative for HDCC with EVA powder.4 Discussion It can be concluded that the curing conditions have a great effect on the tensile properties from Table 1 and Table 2. The tensile properties exhibit a great difference at 28 days due to different curing condition for mixture SP4 and mixture W1. The HDCC cured in water per-forms better than that in room temperature condition atthe early age, however, as the age increases, the tensileperformance of HDCCs cured in room temperature condition shows an increasing tendency while that curedin the water decreases. The tensile strain of specimensthat of W3D is similar to that of W7D at 28 days, whichtest results also show the ultimate tensile strength has not direct relationship with the tensile strain, and high tensile strain do not mean low tensile strength, and vice versa . That can be explained as follows: curing condi-tion plays a significant influence on microstructure and macroscopical performance of cementitious composites. For fiber reinforced cementitious composites, there exists a distinctive layer of interface zone about 30-50 μm away from the fiber surface [9]. Also the interface will strongly influence the toughness of the compositesand frictional bond [10]. Generally the interface zone is considerable weaker than the matrix due to the large calcium hydroxide crystals and higher porosity for the FRCCs with steel fiber or polypropylene fiber [9], but thePVA fiber is a special organic fiber to the cementitiouscomposites. The majority of fibers used to the cementi-tious composites, such as steel fiber, polypropylenefiber,etc , will not react with the hydration products of cement, but the investigations by Akers show that [11], the PVA fiber performs surprisingly high chemical bonding between the PVA fiber and cement hydrationproducts due to the strong hydrophilic characteristic or hydrogen intermolecular bond induced by the hydroxyl groups, and as the age increase, while there are no evi-dent change in fiber properties, the bonding strengthbetween fiber and cement-based matrix will increase due to an increase in interface bond with age. The re-searches by Kanda T etc also shows that the apparent chemical bonding between PVA fiber and cement ma-,trix independent of the water-to cement ratio of matrix, is relatively stable and up to 30-40 MPa, but the value of friction bond, affected by water to cement ratio, is be-tween 2.2 MPa to 4.4 MPa when the water to cementvaries from 0.62 to 0.27[12]. Through the investigation by Li and his co-workers [3], only the FRCC with the appropriate fracture toughness of matrix and frictional Table 7 Mix proportion with or without EVA in mass No. Cement FA SF SP4 Sand Water Sp PVAF S 1 3.85 0.1 — 1 1.21 0.033 0.096 SS4 1 3.60 0.1 0.1 1 1.21 0.032 0.096 Table 8 Test results of HDCCs with or without EVAS SS47 d 28 d HC 7 d 28 d HCσTfc /MPa 1.15 3.32 4.37 1.86 3.14 3.89 εfc/% 0.021 0.067 0.029 0.057 0.086 0.049 σTp /MPa 1.94 3.43 4.90 2.03 3.42 4.75 εp /% 0.20 1.18 0.33 0.49 1.24 0.60εm /% 0.54 1.63 0.40 1.55 1.73 0.74 σcom /MPa 13.0 33.5 — 13.0 35.4 — (a) FA3 (b) FA3LA (c) S and SS4Fig.2 Stresses vs. Strain curves of FA3, FA3LA, S and SS4 at different ageVol.25 No.2 PANG Chaoming et al: Methods of Modifying the Brittle (160)and high strain capacity of FRCC can dominantly be achieved by using PVA fiber, and the interfacial fric-tional stress for FRCC with PSH behavior show the relative definite requirement and shall preferably be between 0.8 to 2.0 MPa[13], and the value can be achieved by applying oil agent[14]. In the present study, the PVA fiber, which had been coated with the oiling agent by Japan Kuraray Co. LTD, was employed. Ow-ing to low water to binder ratio and high content of fly ash (W/B=0.20, FA/C=4.0), and the specimens were kept only for 0-7 days in water and then longer than 20 days cured in room temperature condition, where there is no enough water for cement hydration, therefore they exhibit relative lower hydration degree and larger shrinkage than those cured in the water in all time. The lower hydration degree and larger shrinkage result in relatively lower frictional bond and weaker interface between PVA fiber and matrix[15]. Therefore, the former forms relatively looser structure and satisfies the re-quirement of low interfacial frictional stress, therefore performs better in strain hardening. Also the failure pat-tern of fiber rupture can be observed in testing process of the latter.In general, the definite range of interfacial fric-tional stress for achieving PSH behavior of FRCC, lower ratio of cement to binder, high fly ash content and PVA fiber properties contribute to the effect of curing condition on the tensile behavior.It can be deduced from Table 4, Table 6, Fig.1 and Fig.2 that the tensile strength of HDCC with rubber powder or light aggregate keep on growing, while the tensile strain also increases as the age increases from 7 days to 28 days, then decreased as the age continually grows up to 90 days or when heat curing was applied. That is because the fiber/matrix bond strength should saturate in a duration of less than 14-28 days, and ma-ture much earlier than matrix properties in cementi-tious[16]. But the high content of fly ash will considera-bly lower the chemical bond and delay the mature due to diluting the metal cation concentration on the fiber surface at early age and as a result the strain increases from 7 days to 28 days[17]. But the friction strength and the facture toughness of matrix continue to develop as age increase to 28 days as the second hydration of fly ash continually develop due to activity effect of fly ash under high temperature or at long age. When the imbal-ance of develop rate occurs, the strain decreases with the continual increasing age.From Table 4 and Table 6, not all the specimens show better tensile performance than the control specimen, only the tensile strain of the specimens with 11% volume fraction rubber powder or 3.5% light-weight aggregate increase comparing to the control specimen at 28 days. The specimens FA3 and FA3LA rapidly reach ultimate strength then crack, and only few cracks develop due to the high fracture toughness of matrix and the low friction between matrix and PVA fiber at 7 days, but the specimen can still maintain the considerable strain after cracking owing to fiber gradu-ally being pulled out. And the SR7 also shows the similar tendency at 28 days. It is possible that the frac-ture toughness of matrix develops faster than the chemical bond and the frictional bond due to the low ratio of water to binder and high content fly ash. However, the specimen with the 11% volume fraction rubber pow-der reaches 2.15% in comparison with only 0.84% for the corresponding control specimen and the ultimate strain of with or without lightweight aggregate varies from 1.96% to 0.58%. The similar test results, i e, pre-existing flaw or micro-voids can modify the brittle behavior of HDCC, were observed in the reference[8] as the pre-existing flaw can relax the crack-tip triaxiality, diffuse the intensity of crack-tip stress and consume more energy, and the lager flaw will not influence the cracking strength but reached a lower bound at a steady state of cracking stress.Table 8 and Fig.2 present that the EVA latex powder show a little positive effect on the tensile strain at different age. It is possible that the EVA as a polymer can form a layer polymer membrane, which hinders the hydration of cementitious materials, but the membrane only influences a little hydration process owing to the lower content, about 1% volume fraction, in compos-ites.In summary, the appropriate fracture toughness of matrix and frictional bond between fiber and matrix is necessary conditions to achieve the PSH behavior or high strain capability. The curing condition emphasize particularly on the influence of friction bond, but the incorporation of rubber powder and lightweight lay particular stress on the fracture toughness of matrix. However the incorporation of rubber powder and lightweight aggregate lower the fracture toughness of matrix and facilitate the crack of matrix, which will possibly lower the effect of curing condition on the tensile properties.Journal of Wuhan University of Technology-Mater. Sci. Ed. Feb.2010 1615 ConclusionsSome methods to modifying the brittle behavior of HDCC with high content fly ash are proposed. It is undoubted that curing condition will strongly influence the microstructure of cementitious composites. The test results show that curing condition has a significant ef-fect on the tensile strain of HDCC with high content fly ash, and dry curing condition will show the clear trend to increase the tensile strain of HDCC with high content fly ash. Not all the specimens but the specimens with appropriate volume fracture rubber powder and light-weight aggregate greatly enhance the tensile strain of HDCC at medium-term age, but indefinitely at long-term age impossibly because disconnected pre-existing flaw or micro-voids may relax the crack-tip, diffuse the intensity of crack-tip stress and significantly consume energy. To a certain extent, EVA can enhance the tensile performance of HDCC owing to the hindered hydration of cement based materials as a result of the formation of polymer membrane. But it is possible that the incorporation of rubber powder and lightweight will lower the effect of curing condition on the tensile per-formance.It also experimentally demonstrates that some specimens rapidly reach ultimate strength and crack, but some specimen can still maintain the considerable strain after cracking owing to fiber gradually being pulled out. The tensile stress keeps increasing, but the tensile strain firstly increases then decreases as the age continually grows because of the imbalance of develop rate between bond strength and matrix properties. References[1]LI V C and LEUNG C K Y. Steady-state and MultipleCracking of Short Random Fiber Composites[J]. Journal ofEngineering Mechanics, 1992, 118(11): 2 246-2 264[2]LEUNG C K Y and LI V C. Effect of Fiber Inclination onCrack Bridging Stress in Fiber Reinforced Brittle MatrixComposites[J]. Journal of Mechanical Physics, 1992, 40(6):1 333-1 362[3]LI V C and WU H C. Conditions for PseudoStrain-Hardening in Fiber Reinforced Brittle MatrixComposites[J]. Applied Mechanics Revolution, 1992, 45(8):390-398[4]LI V C, MISHRA D K and WU H C. Matrix Design forPseudo-Strain-Hardening Fiber Reinforced CementitiousComposites[J]. Materials and Structures, 1995, 28: 586-595 [5]KANDA T, LI V C and Member of ASCE. New Micro-mechanics Design Theory for Pseudostrain Hardness Ce-mentitious Composite[J]. Journal of Engineering Me-chanics, 1999, 125(4): 373-381[6]LI V C, WANG S and WU C. Tensile Strain- HardeningBehavior or Polyvinyl Alcohol Engineered CementitiousComposite (PVA-ECC)[J]. ACI Materials Journal, 2001,98(6): 483-492[7]MAESHALL D B, COX B N and EVANS A G. The Mechan-ics of Matrix Cracking in Brittle Matrix Fiber Composites[J].ACTA Metallurgical, 1985, 33(11): 2 013-2 021[8]WANG S and LI V C. Tailoring of Pre-Existing Flaw inECC Matrix for Saturated Strain Hardening[C]. Proceed-ings of the Fifth International Conference on FractureMechanics of Concrete and Concrete Structures. Colorado:Ia-FraMCos, 2004: 1 005-1 012[9]Li V C, WU H C, and CHAN Y W. Interfacial PropertyTailoring for Pseudo Strain-Hardening Cementitious Composites[C]. Advanced Technology on Design and Fabrication of Composite Materials and Structures. Neth-erlands: Kluwer Acad. Publ., 1995: 261-268[10]SUN W, MANDEL J A and SAID Samir. Studies of theProperties of the Fiber-Matrix Interface in Steel Fiber Re-inforced Mortar[J]. ACI Materials Journal, 1987, 84(12):101-109[11]AKERS S A S. Long Term Durability of PVA ReinforcingFibers in a Cement Matrix[J]. The International Journal ofCement Composite and Lightweight Concrete, 1989, 11:79-91[12]KANDA T and LI V C. Interface Property and ApparentStrength of High-Strength Hydrophilic Fiber in CementMatrix[J]. Journal of Materials in Civil Engineering, 1998,10(1): 5-13[13]LI V C and WANG S. Process for Increasing the Ductilityof High Performance Fiber-Reinforced Brittle Matrix Composites and Composites Produced Thereby[P]. US Patent 7169224. 2007-01-30[14]REDON C. Measuring and Modifying Interface Propertiesof PVA Fibers in ECC Matrix[J]. ASCE J. Materials inCivil Engineering, 2001, 13(6): 399-406[15]CHEN H SUN W and PIET S. Interfacial Transition ZoneBetween Aggregate and Paste in Cementitious Composites(II): Mechanism of Formation and Degradation of Interfa-cial Transition Zone Microstructure and Its Influence Factors[J].Journal of the Cement Ceramic Society, 2004, 32(1): 70-80 [16]CHAN Y W and LI V C. Age Effect on the Characteristicsof Fibre/Cement Interfacial Properties[J]. Journal of Ma-terials Science, 1997, 32: 5 287-5 292[17]WANG S and LI V C. Engineered Cementitious Compos-ites with High-Volume Fly Ash[J]. ACI Materials Journal,2007, 104(3): 233-241。
毕业设计(论文)外文资料翻译(学生用)
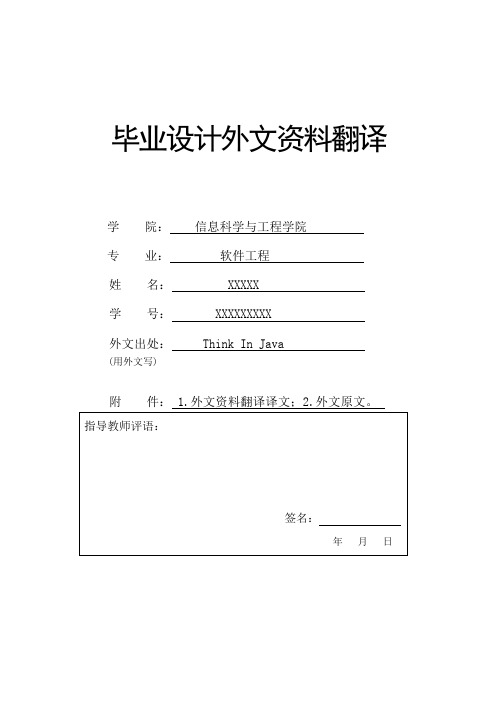
毕业设计外文资料翻译学院:信息科学与工程学院专业:软件工程姓名: XXXXX学号: XXXXXXXXX外文出处: Think In Java (用外文写)附件: 1.外文资料翻译译文;2.外文原文。
附件1:外文资料翻译译文网络编程历史上的网络编程都倾向于困难、复杂,而且极易出错。
程序员必须掌握与网络有关的大量细节,有时甚至要对硬件有深刻的认识。
一般地,我们需要理解连网协议中不同的“层”(Layer)。
而且对于每个连网库,一般都包含了数量众多的函数,分别涉及信息块的连接、打包和拆包;这些块的来回运输;以及握手等等。
这是一项令人痛苦的工作。
但是,连网本身的概念并不是很难。
我们想获得位于其他地方某台机器上的信息,并把它们移到这儿;或者相反。
这与读写文件非常相似,只是文件存在于远程机器上,而且远程机器有权决定如何处理我们请求或者发送的数据。
Java最出色的一个地方就是它的“无痛苦连网”概念。
有关连网的基层细节已被尽可能地提取出去,并隐藏在JVM以及Java的本机安装系统里进行控制。
我们使用的编程模型是一个文件的模型;事实上,网络连接(一个“套接字”)已被封装到系统对象里,所以可象对其他数据流那样采用同样的方法调用。
除此以外,在我们处理另一个连网问题——同时控制多个网络连接——的时候,Java内建的多线程机制也是十分方便的。
本章将用一系列易懂的例子解释Java的连网支持。
15.1 机器的标识当然,为了分辨来自别处的一台机器,以及为了保证自己连接的是希望的那台机器,必须有一种机制能独一无二地标识出网络内的每台机器。
早期网络只解决了如何在本地网络环境中为机器提供唯一的名字。
但Java面向的是整个因特网,这要求用一种机制对来自世界各地的机器进行标识。
为达到这个目的,我们采用了IP(互联网地址)的概念。
IP以两种形式存在着:(1) 大家最熟悉的DNS(域名服务)形式。
我自己的域名是。
所以假定我在自己的域内有一台名为Opus的计算机,它的域名就可以是。
外文翻译
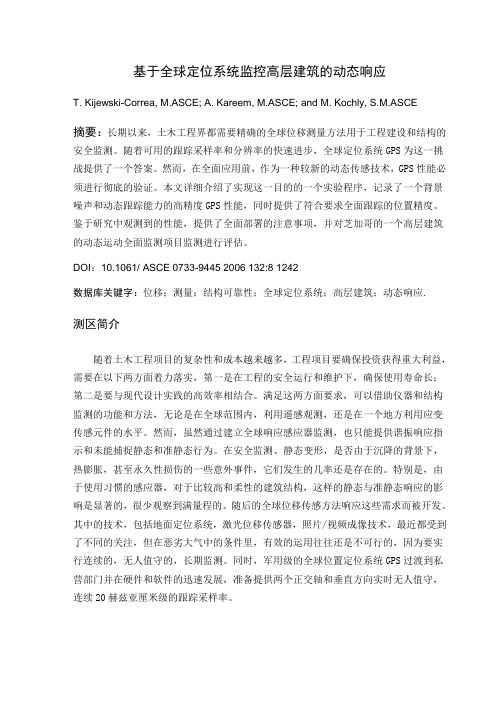
基于全球定位系统监控高层建筑的动态响应T. Kijewski-Correa, M.ASCE; A. Kareem, M.ASCE; and M. Kochly, S.M.ASCE摘要:长期以来,土木工程界都需要精确的全球位移测量方法用于工程建设和结构的安全监测。
随着可用的跟踪采样率和分辨率的快速进步,全球定位系统GPS为这一挑战提供了一个答案。
然而,在全面应用前,作为一种较新的动态传感技术,GPS性能必须进行彻底的验证。
本文详细介绍了实现这一目的的一个实验程序,记录了一个背景噪声和动态跟踪能力的高精度GPS性能,同时提供了符合要求全面跟踪的位置精度。
鉴于研究中观测到的性能,提供了全面部署的注意事项,并对芝加哥的一个高层建筑的动态运动全面监测项目监测进行评估。
DOI:10.1061/ ASCE 0733-9445 2006 132:8 1242数据库关键字:位移;测量;结构可靠性;全球定位系统;高层建筑;动态响应.测区简介随着土木工程项目的复杂性和成本越来越多,工程项目要确保投资获得重大利益,需要在以下两方面着力落实,第一是在工程的安全运行和维护下,确保使用寿命长;第二是要与现代设计实践的高效率相结合。
满足这两方面要求,可以借助仪器和结构监测的功能和方法,无论是在全球范围内,利用遥感观测,还是在一个地方利用应变传感元件的水平。
然而,虽然通过建立全球响应感应器监测,也只能提供谐振响应指示和未能捕捉静态和准静态行为。
在安全监测、静态变形,是否由于沉降的背景下,热膨胀,甚至永久性损伤的一些意外事件,它们发生的几率还是存在的。
特别是,由于使用习惯的感应器,对于比较高和柔性的建筑结构,这样的静态与准静态响应的影响是显著的,很少观察到满量程的。
随后的全球位移传感方法响应这些需求而被开发。
其中的技术,包括地面定位系统,激光位移传感器,照片/视频成像技术,最近都受到了不同的关注,但在恶劣大气中的条件里,有效的运用往往还是不可行的,因为要实行连续的,无人值守的,长期监测。
- 1、下载文档前请自行甄别文档内容的完整性,平台不提供额外的编辑、内容补充、找答案等附加服务。
- 2、"仅部分预览"的文档,不可在线预览部分如存在完整性等问题,可反馈申请退款(可完整预览的文档不适用该条件!)。
- 3、如文档侵犯您的权益,请联系客服反馈,我们会尽快为您处理(人工客服工作时间:9:00-18:30)。
外文资料Ethics and leadership skills in the public serviceAbstractThe deteriorating situation of ethics in public administration–all around the globe–has made it a burning issue. Although ethics cannot be learned, it can be developed. Among various other approaches, improving leadership skills can prove to be effective in promoting ethics. Skilled and committed leadership can set ethical standards. Learning and mastering various technical, conceptual and interpersonal skills and other skills like emotional and social intelligence enable public servants to diffuse and establish core ethical values in the organization. The leadership skills and their role in promoting ethics have been discussed here for a better understanding of the subject.1. IntroductionThe importance of ethics in public administration has long been neglected until recently. The deteriorating situation of ethics in this field –all around the globe– has made it a burning issue. Recent ethical scandals both in the public and private sectors have influenced scholars, national and international organizations to take a deep interest in this matter. Efforts have been made to promote ethical standards of the public servants. Among various other approaches, improving leadership skills can prove to be effective in promoting ethics in public service. Hart (2001) believes ethics cannot be effective without proper leadership. With the increasingly competitive nature of global economy and other surrounding pressures, the array of required leadership skills has also expanded (Montgomery,2003). Leaders guide the members of the organization toward the goals of the organization. It is one of the main responsibilities of a good leader to ensure that the functions of the organization are performed in an ethical manner. This paper discusses the concepts of ethics, leadership and leadership skills and attempts to present the role of leadership skills in enhancing ethics in the public service.2. Ethics in the Public ServiceEthics is a must for public administrators. Public policies have a direct effect on the citizens. Therefore ensuring ethics in the public service is a crucial matter. According to Rosenbloom (1989) ethics can be considered as a form of self-accountability or an “inner check” of the conduct of pub lic administrators. Ethics are statements, written or oral, that prescribe or proscribe certain behaviours under specified conditions (Nigro & Nigro, 1989, p.37). Public service ethics encompasses a broad and widening range of principles and values. According to the United Nations Department of Economic and Social Affairs (1999) these include objectivity, impartiality, fairness, sensitivity, compassion, responsiveness, integrity, accountability, transparency, selfless devotion to duty, protection of public interest. Ethical dilemmas generally take place around administrative discretion, corruption, accountability, nepotism, interest group pressure, informationsecrecy, policy complicacies etc. Skilled leaders can play a significant role in introducing and nurturing the values of ethics and resolving these ethics related quandaries.3. Leadership and Leadership SkillsGenerally, leadership is the process by means of which a person persuades and guides the members of the group or organization towards the achievement of its objectives (Yukl, 1989; Greenburg and Baron, 1997). Norms and values are initiated from the leader, which is then developed and maintained also by the leader (Grosenick & Gibson, 2001). Leaders set examples for ideal behavior which is followed by the organization. They are the trend setters and founders of organizational culture. The success of ethics programs in any organization lies with committed leadership (Lewis, 1999; Hejka-Ekins, 2001). Leadership skills, along with increasing the effectiveness of the administrative leaders, also tend to promote ethics. According to Katz (2009), skills are not innate but they can be learned, developed and are evident in performance.3.1. Technical Skills:Technical skills involve methods, processes, procedures, or techniques which lead to better understanding of and expertise on a particular matter (Katz, 2009). These skills include factual knowledge regarding the rules, structure, management systems, and employee characteristics of the organization. It also includes knowledge concerning the organization‟s products and services like technical specifications, strengths and limitations. Technical skills are gained from an amalgamation of formal education, training and job experience. A good memory and ability to learn helps effective managers to acquire technical skills quickly from various sources of the organization. In order to instruct and guide subordinates and steer the organization in a planned way, the knowledge about products and procedures is a prime requirement (Yukl, 2001; Cook, 1998). These skills lay the foundation for inspiration, innovation and strategic planning.3.2. Conceptual Skills:Conceptual skills include analytical ability, logical thinking, concept formation, inductive and deductive analysis. According to Yukl (2001) conceptual skills involves good judgment, prudence, insight, creativity and the ability to make decisions in complex situations.Conceptual skills have been measured with a variety of different methods, including aptitude test, situational tests, interviews and critical incidents. Conceptual skills are required for effective planning, organizing and problem solving. In order to achieve a proper coordination, administrators need to understand the functioning of various parts of the organization and how they interrelate and interact with each other. “Cognitive complexity” (Yukl, 2001) – the ability to identify complex patterns of relationship and forecast future event from current developments- is required in this case.Managers also need the skill to predict the affects of external environmental changes on the organization. Effective administrative leaders rely on a combination of intuition and conscious reasoning in confronting the various decision making problems of the organization. The ability to learn and adapt to change is a prime requirement forachieving conceptual skills. …Metacognition‟ (Flavell, 1979; Yukl, 2001) is helpful in this case. It refers to the ability to impartially and intricately analyze ones‟ own cogni tive processes and find ways to improve them. These abilities enable leaders to learn from mistakes and alter their assumptions and beliefs.3.3. Interpersonal Skills:Interpersonal skills include knowledge about human behavior and group processes, ability to understand the feelings, attitudes and intentions of others, and ability to clearly and credibly correspond. This category of leadership skills also include …the skills required for coordination of actions of oneself and others (Gillen & Carroll, 1985; Mumford, Marks et al., 2000), and negotiation skills to reconcile differences among employee perspectives and establish mutually satisfying relationships (Copeman, 1971; Mahoney, Jerdee, & Carroll, 1963; Mahoney et al., 1965; Mintzberg, 1973), and persuasion skills to influence others to more effectively accomplish organizational objectives (Katz, 1974; Mintzberg, 1973; Yukl, 1989)‟ (as cited in Mumford et al 2007 p, 157).These skills help to influence people and thereby makes dissemination of views and information easy (Northouse, 2009). This enables the leader to solve problems in a constructive and effective manner.3.4. Emotional Intelligence:Emotions are strong feelings which even after the intensity fades, is likely to linger on as a positive or negative mood. This can sometimes adversely affect leadership behavior. Emotional Intelligence (EI) can help to resolve this situation. EI can be defined as the degree to which people are accustomed to their own feelings and to the feelings of others (Yukl, 2001). It refers to the ability to put together emotions and reasons in such a way that emotions are used to assist cognitive processes and emotions are rationally managed. EI includes skills like self-awareness, communication skills, empathy andself-regulation through which leadership traits can be learned (Goleman, McKee, and Boyatzis, 2002).EI helps leadership role in solving complex problems, better decision making, time management and crisis management. Self awareness enables the leader to be aware of ones own demands and reactions to certain situations. Therefore it assists in the evaluation of alternative solutions. Self-regulation helps to maintain enthusiasm and optimism. Strong social skills which are necessary to develop cooperative interpersonal relationships are regarded as empathy. For example, the ability to listen attentively results in effective communication and conveys appreciation and positive regard.3.5. Social Intelligence:Social intelligence is the ability to determine the requirements for leadership in a particular situation and select an appropriate response. It consists of perceptiveness and behavioral flexibility (Yukl, 2001). Social perceptiveness means the ability to understand the needs, problems and openings of the organization. It also includes the ability to understand the characteristics of the members, social relationships and collective processes that tend to influence the organization (Northouse, 2009). Behavioral flexibilityis the ability and enthusiasm to change one‟s behavior to adjust requirements of new circumstances.4. Leadership Skills and Enhanced Ethics in the Public ServicePublic servants have to exercise administrative discretion while performing their duties. Public trust on the government depends on the manner through which these duties are carried out. Therefore it is crucial to maintain ethical standards in the implementation of government functions. Leadership can have considerable effect on the enhancement of overall ethics in the public service. The administrative leaders should unswervingly take part in all the stages of ethics program - from planning to implementation- sincerely abide by the code of ethics and encourage ethical behavior in the organization by being role models (Hejka-Ekins, 2001). Different leadership skills can escalate the strength of the leader in achieving these purposes. Some of these skills are interrelated and therefore tend to have overlapping results. For example, social skills are essential to develop empathy, which is an integral part of emotional intelligence.Technical skills help the leader to become more efficient and responsive. These skills enable the leaders to independently take technical decisions and thereby detect any attempt of deception related to technical matters. Knowledge and regard forrules-regulations helps to establish rule of law, accountability and transparency. With sound understanding on rules and regulations the leader is more likely to work within the legal ambit. This reduces the risks of unethical behavior. Conceptual skills support the leaders in effective planning, organizing and problem solving. These skills are highly essential to confront ethical dilemmas and conflicts of interest. Skills like these prepare leaders with good judgment and allow the leader to comprehend the consequences of any action beforehand. Thus controversial decisions can be avoided. These skills lead to ethical decisions and reliability. Interpersonal skills and social intelligence make the transmission of ethical values in the organization smoother. They engender compassion and sensitivity which are favorable to the augmentation of ethics. Leaders possessing these skills can easily diffuse the core ethical values among the members of the organization. The leader can also motivate the officials to earnestly take up these values so that they become embedded in the culture of the organization. The practice of various interpersonal and social skills creates an open and friendly environment that motivates employees to expose wrong doings without fear. Emotional intelligence prevents the executive from taking emotionally biased unethical decisions. Hence it facilitates in maintaining impartiality and protection of public interest. Integrity can be intensified by means of self regulation and self awareness. A leader with high emotional and social intelligence can competently select the appropriate and rational decision in critical situations. These skills allow the administrative leader to promptly response to new and diverse ethical issues.5. ConclusionLeadership skills facilitate the administrative leader to distinguish between ethical and unethical acts. Effects of some skills overlap others. Technical, conceptual,interpersonal skills along with emotional and social intelligence contribute to proper understanding of ethical dilemmas, ethical decision making and dissemination and establishment of ethical values. Leaders enriched with these skills can show the way towards enhanced ethics oriented public service.From: Sonia Haq. Micro-blogging: Ethics and leadership skills in the public service[J]. Procedia Social and Behavioral Sciences 2011(15) , 2792–2796.译文公共服务的道德和领导技能摘要伦理在公共行政–全球–已经燃烧的问题恶化的情况。