钣金加工工艺流程
钣金生产流程及工艺
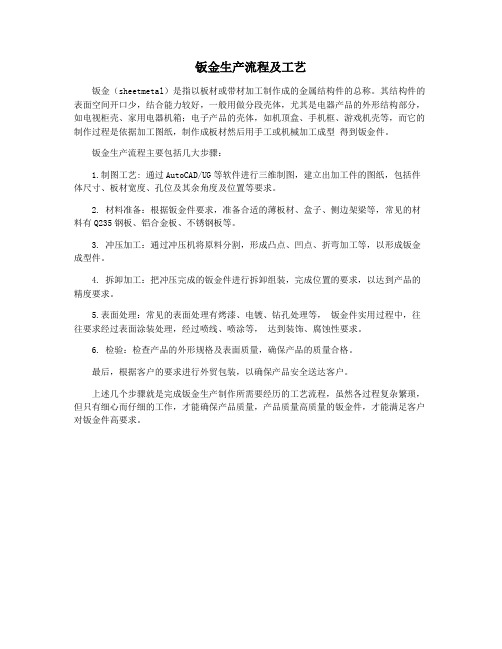
钣金生产流程及工艺
钣金(sheetmetal)是指以板材或带材加工制作成的金属结构件的总称。
其结构件的表面空间开口少,结合能力较好,一般用做分段壳体,尤其是电器产品的外形结构部分,如电视柜壳、家用电器机箱;电子产品的壳体,如机顶盒、手机框、游戏机壳等,而它的制作过程是依据加工图纸,制作成板材然后用手工或机械加工成型得到钣金件。
钣金生产流程主要包括几大步骤:
1.制图工艺: 通过AutoCAD/UG等软件进行三维制图,建立出加工件的图纸,包括件体尺寸、板材宽度、孔位及其余角度及位置等要求。
2. 材料准备:根据钣金件要求,准备合适的薄板材、盒子、侧边架梁等,常见的材料有Q235钢板、铝合金板、不锈钢板等。
3. 冲压加工:通过冲压机将原料分割,形成凸点、凹点、折弯加工等,以形成钣金成型件。
4. 拆卸加工:把冲压完成的钣金件进行拆卸组装,完成位置的要求,以达到产品的精度要求。
5.表面处理:常见的表面处理有烤漆、电镀、钻孔处理等,钣金件实用过程中,往往要求经过表面涂装处理,经过喷线、喷涂等,达到装饰、腐蚀性要求。
6. 检验:检查产品的外形规格及表面质量,确保产品的质量合格。
最后,根据客户的要求进行外贸包装,以确保产品安全送达客户。
上述几个步骤就是完成钣金生产制作所需要经历的工艺流程,虽然各过程复杂繁琐,但只有细心而仔细的工作,才能确保产品质量,产品质量高质量的钣金件,才能满足客户对钣金件高要求。
钣金车间工艺流程

钣金车间工艺流程钣金车间是指进行钣金加工的车间,主要用于制作各种金属板材的加工和成型。
钣金车间工艺流程通常包括以下几个步骤。
第一步,材料准备。
在进行钣金加工之前,需要准备所需的金属板材和其他零部件。
根据具体的产品要求,选择合适的材料,并将其切割成所需的尺寸和形状。
第二步,设计和绘图。
根据客户的要求和产品设计,使用计算机辅助设计软件进行零件的设计和绘图。
在绘图过程中,需要考虑到材料的强度、加工难度等因素,合理设计零件的结构。
第三步,切割和冲孔。
根据设计图纸,使用切割机和冲床将金属板材进行切割和冲孔。
这一步骤的目的是将材料切割成所需的形状,并在其中进行冲孔加工,以便后续加工和组装。
第四步,折弯和成型。
根据产品的要求,使用折弯机将金属板材折弯成所需的形状。
通过对金属板材进行多次折弯和成型操作,使其达到设计要求的形状和尺寸。
第五步,焊接和组装。
将已经折弯和成型好的金属板材进行焊接和组装。
使用焊接机器和其他工具将零部件进行焊接和连接,以形成最终的产品。
第六步,打磨和表面处理。
对已经焊接和组装好的产品进行打磨和表面处理。
通过打磨去除焊接痕迹和毛刺,并对表面进行喷漆、镀铬等处理,使产品的外观更加美观。
第七步,检验和质量控制。
对加工好的产品进行检验和质量控制。
通过对产品进行尺寸、外观等方面的检查,确保产品达到设计要求和质量标准。
第八步,包装和发货。
对通过检验的产品进行包装和标识,并安排发货。
根据客户的要求,选择合适的包装材料和方式,保证产品在运输过程中不受损坏。
以上就是钣金车间工艺流程的基本步骤。
在实际生产中,还会根据不同的产品和要求进行调整和改进。
钣金加工是一项技术要求较高的加工工艺,需要有经验丰富的工人和先进的设备来保证产品质量和生产效率。
随着科技的不断进步,钣金车间的工艺流程也在不断创新和改进,以满足客户日益多样化的需求。
钣金加工工艺流程问题汇总

钣金加工工艺流程问题汇总
1.钣金加工的步骤有哪些?
钣金加工工艺通常由以下步骤组成:
(1)抗锯齿处理:处理锯齿边及贴合面,以达到更柔和和美观的效果;
(2)剪切加工:根据需要,使用不同的方法,以确保材料的准确性和高效性;
(3)焊接:使用激光焊接、TIG焊接、MIG/MAG焊接等技术,使零件完整性;
(4)冲压加工:使用专业的冲压设备,将金属材料冲压成所需的复杂形状;
(5)喷涂装饰:采用专业的喷涂设备,为零件表面涂上底漆、有机硅等涂层,使其具有防腐、耐磨、耐擦的特性;
(6)组装:将加工好的零件组装起来,使其具有完整的功能和结构。
;。
钣金加工工艺流程详解

钣金加工工艺流程详解钣金加工是一种常见的制造工艺,广泛应用于各行各业,包括汽车制造、机械加工、建筑等领域。
在本文中,我们将详细介绍钣金加工的工艺流程与相关注意事项。
一、材料准备与切割钣金加工的第一步是准备材料。
通常使用的材料有不锈钢、铝合金、碳钢等。
接下来,根据设计要求,对材料进行切割。
切割常用的方法有剪切、冲压、激光切割等。
切割后需要进行精确的尺寸测量,以确保后续加工的准确性。
二、钣金折弯与成形在进行折弯与成形之前,需要对材料进行弯曲性能测试,以确定适合的加工方法。
常见的折弯工艺包括V型折弯和U型折弯。
通过使用折弯机械设备,将材料准确地折弯成所需的形状。
需要注意的是,在进行钣金折弯时,应确保折弯角度和尺寸的准确性,以及避免出现折皱或破裂等缺陷。
三、冲孔与切割在冲孔过程中,常用的方法有机械冲孔和数控冲孔。
通过钣金冲床的操作,将设计好的孔型、凹槽等形状冲压到钣金材料上。
切割过程中,可以通过激光切割、火焰切割或者等离子切割等方法,将材料进行精确的切割。
四、焊接与拼接焊接与拼接是钣金加工中常见的工艺之一。
通过焊接来将多个钣金构件拼接在一起,以形成所需的结构或产品。
常用的焊接方法有点焊、氩弧焊、激光焊接等。
在进行焊接之前,要确保工件表面的清洁,以保证焊接质量。
五、涂装与表面处理为了提高钣金制品的表面质量和耐腐蚀能力,通常需要进行涂装和表面处理。
涂装可以采用喷涂、粉末涂装等方式,以增加产品的美观性和防护性。
表面处理包括酸洗、电镀、阳极氧化等,用以改善表面的附着力和硬度。
六、总装与检验在钣金加工的最后阶段,将各个零件进行总装,组装成最终的产品。
同时,进行严格的质量检验,以确保产品的准确性和质量。
主要检验内容包括尺寸、外观、焊接质量、涂装质量等。
总结:钣金加工工艺流程包括材料准备与切割、钣金折弯与成形、冲孔与切割、焊接与拼接、涂装与表面处理、总装与检验等阶段。
每个阶段都要注意操作技巧和质量控制,以确保最终产品符合要求。
常见钣金件加工的工艺流程

常見鈑金件加工的工藝流程一、材料的選用鈑金加一般用到的材料有冷軋板(SPCC )、熱軋板(SHCC )、鍍鋅板(SEC C 、SGCC ),銅(CU )黃銅、紫銅、鈹銅,鋁板(6061 、6063 、硬鋁等),鋁型材,不銹鋼(鏡面、拉絲面、霧面),根據產品作用不同,選用材料不同,一般需從產品其用途及成本上來考慮。
1.冷軋板SPCC,主要用電鍍和烤漆件,成本低,易成型,材料厚度< 3.2mm <2.熱軋板SHCC,材料T >3.0mm ,也是用電鍍,烤漆件,成本低,但難成型,主要用平板件。
3.鍍鋅板SECC 、SGCC 。
SECC 電解板分N 料、P 料,N 料主要不作表面處理,成本高,P 料用於噴塗件。
4.銅;主要用導電作用料件,其表面處理是鍍鎳、鍍鉻,或不作處理,成本高。
5.鋁板;一般用表面鉻酸鹽(J11-A ),氧化(導電氧化,化學氧化),成本高,有鍍銀,鍍鎳。
6.鋁型材;截面結構複雜的料件,大量用於各種插箱中。
表面處理同鋁板。
7.不銹鋼;主要用不作任何表面處理,、成本高。
二、圖面審核要編寫零件的工藝流程,首先要知道零件圖的各種技術要求;則圖面審核是對零件工藝流程編寫的最重要環節。
1.檢查圖面是否齊全。
2.圖面視圖關係,標注是否清楚,齊全,標注尺寸單位。
3•裝配關係,裝配要求重點尺寸。
4.新舊版圖面區別。
5•外文圖的翻譯。
6.表處代號轉換。
7•圖面問題回饋與處埋。
8.材料9.品質要求與工藝要求10 .正式發行圖面,須加蓋品質控制章。
三、展開注意事項展開圖是依據零件圖(3D )展開的平面圖(2D)1•展開方式要合,要便利節省材料及加工性2•合理選擇問隙及包邊方式,T=2.0以下問隙0.2 , T=2-3問隙0.5,包邊方式採用長邊包短邊(門板類)3•合理考慮公差外形尺寸:負差走到底,正差走一半;孔形尺寸:正差走到底,負差走一半。
4.毛刺方向5 •抽牙、壓鉚、撕裂、沖凸點(包),等位置方向,畫出剖視圖6•核對材質,板厚,以板厚公差7•特殊角度,折彎角內半徑(一般R=0.5 )要試折而定展開8•有易出錯(相似不對稱)的地方應重點提示9•尺寸較多的地方要加放大圖10・需噴塗保護地方須表示四、板金加工的工藝流程根據鈑金件結構的差異,工藝流程可各不相同,但總的不超過以下幾點。
钣金车间生产流程图

钣金车间生产流程图一、任务描述:本文将详细描述钣金车间的生产流程图,包括原材料采购、工艺流程、生产设备和质量控制等内容。
二、原材料采购:1. 钣金车间的原材料采购主要包括钢板、铝板、不锈钢板等金属材料。
2. 采购部门负责与供应商进行谈判、签订合同,并确保原材料的质量和数量符合要求。
3. 采购部门将原材料送至仓库,并进行入库管理,确保原材料的安全和追溯。
三、工艺流程:1. 下料:根据产品要求,将原材料进行切割、剪裁,得到所需尺寸的零部件。
2. 折弯:使用折弯机对零部件进行折弯,使其形成所需的形状。
3. 冲孔:使用冲床对零部件进行冲孔,以便后续的连接或装配。
4. 焊接:采用焊接工艺将零部件进行焊接,形成整体结构。
5. 打磨:对焊接后的零部件进行打磨,使其表面光滑。
6. 表面处理:根据产品要求,对零部件进行喷涂、电镀等表面处理工艺。
7. 组装:将各个零部件按照设计要求进行组装,形成成品。
四、生产设备:1. 切割设备:包括剪板机、激光切割机等,用于将原材料进行切割。
2. 折弯设备:包括折弯机、数控折弯机等,用于将零部件进行折弯。
3. 冲床设备:用于对零部件进行冲孔,常见的有液压冲床、机械冲床等。
4. 焊接设备:包括手工焊接、自动焊接等设备,用于将零部件进行焊接。
5. 打磨设备:包括手工打磨、砂带机等设备,用于对零部件进行打磨。
6. 表面处理设备:包括喷涂设备、电镀设备等,用于对零部件进行表面处理。
7. 组装设备:包括螺丝刀、扳手等工具,用于将零部件进行组装。
五、质量控制:1. 原材料检验:采购部门对进货的原材料进行检验,确保质量符合要求。
2. 在线检测:在生产过程中,设置检测点对零部件进行尺寸、外观等方面的检测。
3. 试装检验:对组装好的产品进行试装,确保各个零部件的匹配程度。
4. 成品检验:对最终成品进行全面检验,包括外观、功能等方面的检测。
5. 不良品处理:对不合格的产品进行分类、记录和处理,以确保产品质量和安全。
汽车钣金工艺流程

汽车钣金工艺流程一、设计与制定方案在汽车钣金工艺流程中的第一步是对车身进行设计与测量,以确保钣金件的尺寸精确。
然后根据设计和测量结果,制定出特定的加工方案,确定具体的钣金工艺流程。
二、材料准备在进行钣金加工之前,需要准备好所需的材料,包括钣金板、焊接材料、胶水等。
材料的选择应符合汽车钣金件的要求,一般来说,钣金板通常使用镀锌钢、铝合金等材料。
三、切割与冲压根据制定的方案,对钣金板进行切割和冲压。
切割是指根据设计要求,将钣金板切割成所需要的形状和尺寸。
冲压是通过压力对钣金板进行加工,使其得到特定的形状和结构。
四、折弯与成型在进行钣金加工时,常常需要使用折弯和成型技术。
折弯是指对钣金板进行弯曲,使其得到一定的角度和曲线。
成型则是将钣金板通过拉伸、压制等方式,使其得到所需要的立体形状。
五、焊接与连接在钣金加工的过程中,往往需要对不同的钣金件进行焊接和连接。
焊接是将两个或多个钣金件通过热熔的方式进行连接,常用的焊接方法有点焊和气焊等。
连接则是通过螺栓、胶水等方式将钣金件进行连接。
六、修复与涂装在汽车维修过程中,有时会遇到车身钣金件的损坏或变形,需要进行修复。
修复包括清理、砂光、填补、抛光等工作,以恢复钣金件的原貌。
修复完成后,还需要进行涂装,通过喷涂等方式给钣金件上色。
七、装配与调整在汽车钣金工艺流程的最后阶段,需要将钣金件进行装配和调整。
装配是指将不同的钣金件组合在一起,形成完整的车身结构。
调整则是对装配完成的钣金件进行微调,以确保各个部件之间的合理配合。
八、质量检验与测试在汽车钣金工艺流程的每个阶段,都需要对钣金件进行质量检验和测试。
质量检验包括外观质量、尺寸精度、表面光洁度等方面的评估。
测试则是通过试车等方式对汽车钣金件的性能进行评估。
九、成品出厂经过以上一系列的工艺步骤,最终得到的是经过修复、加工和调整的汽车钣金件。
这些成品将经过最后的检验和测试,并进行包装,最终出厂交付给汽车制造商或汽车维修企业。
钣金与喷漆工艺流程详解

钣金与喷漆工艺流程详解钣金和喷漆是汽车制造和修复过程中非常重要的技术环节。
钣金工艺主要涉及锯切、钻孔、涂装、焊接等步骤,而喷漆工艺则包括准备、喷涂、烤漆等过程。
一、钣金工艺流程1. 材料准备钣金加工的第一步是选取合适的材料。
一般来说,常用的钣金材料有铝板、镀锌板和不锈钢板等。
根据需要,工人会事先将这些材料剪切成适当的尺寸和形状。
2. CAD设计在进行钣金加工之前,往往需要进行CAD设计,以确定所需零部件的精确尺寸和形状。
设计完成后,将设计图纸传输到数控机床上。
3. 加工数控机床按照CAD图纸上的要求进行自动化加工。
这是一个自动化的过程,可以大大提高加工效率和精度。
4. 锯切和钻孔根据设计图纸,通过机床的锯切和钻孔功能,将加工后的零件切割成所需形状,并进行孔洞的加工。
5. 折弯和成型将锯切和钻孔加工好的零件放到机床上进行折弯和成型。
一般采用数控折弯机进行折弯操作,以确保零件达到所需的角度和形状。
6. 涂装完成折弯和成型后的钣金零部件需要进行涂装。
这个过程包括喷涂底漆、干燥、打磨、清洁等几个步骤,以确保涂层均匀、光洁。
二、喷漆工艺流程1. 准备工作喷漆前需要对车身进行准备工作,包括去除油污、旧漆和氧化层等。
这个步骤通常会使用化学药剂进行清洁,确保车身表面干净,以便涂层附着。
2. 喷涂底漆在车身准备完毕后,首先要喷涂底漆。
底漆可以提供更好的涂层附着力和耐久性,同时也可以填充表面不平整的细小瑕疵。
3. 干燥底漆喷涂完毕后,需要让车身在干燥室中进行适当的时间干燥。
这个过程中,温度、湿度和通风等因素都需要严格控制,以确保涂层能够均匀干燥。
4. 打磨干燥完毕后,需要对车身进行打磨以去除表面的不平整和瑕疵。
这一步骤非常关键,需要使用适当的砂纸和打磨工具,确保车身表面光洁平滑。
5. 擦拭和清洁打磨完毕后,车身需要进行擦拭和清洁,以去除打磨过程中产生的粉尘和杂质。
这一步骤通常使用干净的布料和专用清洁剂进行。
6. 喷涂面漆最后一步是喷涂面漆,也被称为面层漆。
- 1、下载文档前请自行甄别文档内容的完整性,平台不提供额外的编辑、内容补充、找答案等附加服务。
- 2、"仅部分预览"的文档,不可在线预览部分如存在完整性等问题,可反馈申请退款(可完整预览的文档不适用该条件!)。
- 3、如文档侵犯您的权益,请联系客服反馈,我们会尽快为您处理(人工客服工作时间:9:00-18:30)。
钣金加工工艺流程1简介 1.1 简介按钣金件的基本加工方式,如下料、折弯、拉伸、成型、焊接。
方式所要注意的工艺要求。
1.2 关键词钣金、下料、折弯、拉伸、成形、排样、最小弯曲半径、毛边、回弹、打死边、焊接下料下料根据加工方式的不同,可分为普冲、数冲、剪床开料、激光切割、风割,由于加工方法的数冲是用数控冲床加工,板材厚度加工范围为冷扎板、热扎板小于或等于3.0mm,冲孔最小尺寸与孔的形状、材料机械性能和材料厚度有关。
图 2.2.1冲孔形状示例材料 圆孔直径b矩形孔短边宽b高碳钢 1.3t 1.0t 低碳钢、黄铜1.0t 0.7t 铝0.8t 0.5t*t 为材料厚度,冲孔最小尺寸一般不小于1mm*高碳钢、低碳钢对应的公司常用材料牌号列表见第7章附录A 。
表1冲孔最小尺寸列表2.3数冲的孔间距与孔边距零件的冲孔边缘离外形的最小距离随零件与孔的形状不同有一定的限制,见图不同, 下料的加工工艺性也有所不同。
钣金下料方式主要为数冲和激光切割本规范阐述每一种加工2.1 铝板 小于或等于4.0mm 不锈钢小于或等于2.0mm2.2 冲孔有最小尺寸要求2.3.1。
当冲孔t ;平行时,应不小于1.5t 。
2.4折弯件及拉深件冲孔时,其孔壁与直壁之间应保持一定的距离2.4.1)2.5螺钉、螺栓的过孔和沉头座螺钉、螺栓过孔和沉头座的结构尺寸按下表选取取。
对于沉头螺钉的沉头座,如果 板材太薄难以同时保证过孔d 2和沉孔D ,应优先保证过孔d 2。
表2用于螺钉、螺栓的过孔di M2 M2.5 M5 M 斗 M5M6 M8M10d2 竝.2 0Z 呂 砧5 叽5 05.5蚣0们1.1]边缘与零件外形边缘不平行时,该最小距离应不小于材料厚度 折弯件或拉深件冲孔时,其孔壁与工件直壁之间应保持一定的距离(图d*要求钣材厚度t > ho表3用于沉头螺钉的沉头座及过孔*要求钣材厚度t > h o表4用于沉头铆钉的沉头座及过孔2.6激光切割是用激光机飞行切割加工,板材厚度加工范围为冷扎板热扎板小于或等于20.0mm,不锈钢 小于10.0mm 。
其优点是加工板材厚度大,切割工件外形速度快,加 工灵活.缺点是无法加工成形,网孔件不宜用此方式加工,加工成本高!3折弯3.1 折弯件的最小弯曲半径材料弯曲时,其圆角区上,外层收到拉伸,内层则受到压缩。
当材料厚度一定时,内 料的拉伸和压缩就越严重;当外层圆角的拉伸应力超过材料的极限强度时,就会产生裂缝和折断,因此,弯曲零件的结构设计,应避免过小的弯曲圆角半径。
公司常用材料的最小弯曲半径见下表。
序号材 料 最小弯曲半径108、08F 、10、10F 、DX2 SPCC E1-T52、0Cr18Ni9、1Cr18Ni9、 1Cr18Ni9Ti 、1100-H24、T20.4t2 15、20、Q235 Q235A 15F 0.5t3 25、30、Q2550.6t 4 1Cr13、H62(M Y 、Y2、冷轧) 0.8t 5 45、50 1.0t 6 55、601.5t 765Mn 60SiMn 、1Cr17Ni7、1Cr17Ni7-Y 、1Cr17Ni7-DY 、SUS3012.0tdi M2 W25 M3 M4 M5d2 0Z2 02.8«.5 04”5 05.5D04.0 阪5 06,5 09.0 010.0h1.2151.652,72J90*di 02®Z503 04 05 d2 02J02.6MJ 05」 D0505.507.209 h11,11,2 1.5290*r 越小,材 廿d2D弯曲半径是指弯曲件的内侧半径 ,t 是材料的壁厚。
t 为材料壁厚,M 为退火状态,丫为硬状态,丫2为1/2硬状态。
表5公司常用金属材料最小折弯半径列表3.2弯曲件的直边高度3.2.1 一般情况下的最小直边高度要求弯曲件的直边高度不宜太小,最小高度按(图 4.2.1 )要求:h > 2t 。
图4.2.1.1图弯1曲件勺直边高度最小值3.2.2特殊要求的直边高度如果设计需要弯曲件的直边高度h < 2t,,则首先要加大弯边高度,弯好后再加工到需要尺寸;或者在弯曲变形区内加工浅槽后,再折弯(如下图所示)。
(图 1.11 )图4.2.2.1 特殊情况下的直边高度要求3.2.3 弯边侧边带有斜角的直边高度当弯边侧边带有斜角的弯曲件时(图 4.2.3 ),侧面的最小高度为:h= (2〜4) t > 3mm图423.1 弯边侧边带有斜角的直边高度3.3 折弯件上的孔边距—1 —1 1I- 屮■—0Cr18Ni9、SUS302=% 压槽孔边距:先冲孔后折弯,孔的位置应处于弯曲变形区外,避免弯曲时孔会产生变形。
弯边的距离见表下表。
表6折弯件上的孔边距3.4局部弯曲的工艺切口3.4.1折弯件的弯曲线应避开尺寸突变的位置局部弯曲某一段边缘时,为了防止尖角处应力集中产生弯裂,可将弯曲线移动一定距离,以离开尺寸突变处(图441.1 a),或开工艺槽(图441.1 b),或冲工艺孔(图441.1 c)意图中的尺寸要求:S> R ;槽宽k> t ;槽深L> t+R+k/2 。
3.4.2当孔位于折弯变形区内,所采取的切口形式孔壁至^25s^2t+r金t+『>23^ 1. &t+r>50。
注■■细工艺孔图441.1精选文库当孔在折弯变形区内时,采用的切口形式示例(图 442.1 )6弯曲线图442.1 (图形式示)3.5带斜边的折弯边应避开变形区图4.5.1带斜边的折弯边应避开变形区3.6打死边的设计要求打死边的死边长度与材料的厚度有关。
如下图所示,一般死边最小长度 其中t 为材料壁厚,R 为打死边前道工序(如下图右所示)的最小内折弯半径。
3.7设计时添加的工艺定位孔为保证毛坯在模具中准确定位,防止弯曲时毛坯偏移而产生废品,应预先在设计时添加工艺定亠厂./ 1f 、.) 1Z-十T支駆城L > 3.5t+R 。
图 4.6.1 死边的最小长度L位孔,如下图所示。
特别是多次弯曲成形的零件,均必须以工艺孔为定位基准, 保证产品质量。
(图 )图4.7.1多次折弯时添加的工艺定位孔3.8标注弯曲件相关尺寸时,要考虑工艺性图4.8.1弯曲件标注示例如上图所示所示,a )先冲孔后折弯,L 尺寸精度容易保证,加工方便。
b )和C )如果尺寸L精度要求高,则需要先折弯后加工孔,加工麻烦(图1.19)3.9 弯曲件的回弹影响回弹的因素很多,包括:材料的机械性能、壁厚、弯曲半径以及弯曲时的正压力等。
3.9.1折弯件的内圆角半径与板厚之比越大,回弹就越大。
3.9.2从设计上抑制回弹的方法示例设计上改进某些结构促使回弹角简少如下图所示: 在弯曲区压制加强筋, 不仅可以提高工件的刚度,也有利于抑制回弹。
弯曲件的回弹,目前主要是由生产厂家在模具设计时, 采取一定的措施进行规避。
同时,从以减少累计误差,工艺孔b:4拉伸如下图所示,拉伸件底部与直壁之间的圆角半径应大于板厚,即■般取r1=(3~5)t ,最大圆角半径应小于或等于板厚的8倍,即r1 < 8t 。
「D rd1 、£、k 八■■ T/n拉伸件凸缘与壁之间的圆角半径应大于板厚的2倍,即r2 >2t ,为了使拉伸进行得更顺利,般取r2=(5~10)t ,最大凸缘半径应小于或等于板厚的8倍,即r2 < 8t 。
(参见图5.1.1 )圆形拉伸件的内腔直径应取 D > d+10t ,以便在拉伸时压板压紧不致起皱。
(参见图 5.1.1 )矩形拉伸件相邻两壁间的圆角半径—/ z A\ / r,b~-y£'' fq O;-¥ } kW丿八丨/ ■- \ X'-■X .J /■\/ X■ .-• 二—-■■丿图 5.1.1"图伸件圆角半径大小二一戋图492.1设计上抑制回弹的方法示例4.1 拉伸件底部与直壁之间的圆角半径大小要求r i >t 。
为了使拉伸进行得更顺利, 4.2 拉伸件凸缘与壁之间的圆角半径4.3 圆形拉伸件的内腔直径4.4矩形拉伸件相邻两壁间的圆角半径应取r3 > 3t,为了减少拉伸次数应尽可能取r3 > H/5,以便一次拉出来。
/. 一■齐.(图 1.21)图5.4.1矩形拉伸件相邻两壁间的圆角半径4.5圆形无凸缘拉伸件一次成形时,其高度与直径的尺寸关系要求圆形无凸缘拉伸件一次成形时,高度H和直径d之比应小于或等于0.4,即H/d < 0.4,如下图所示。
图5.5.1圆形无凸缘拉伸件一次成形时,高度与直径的尺寸关系4.6拉伸件设计图纸上尺寸标注的注意事项拉伸件由于各处所受应力大小各不相同,使拉伸后的材料厚度发生变化。
一般来说,底部中央保持原来的厚度,底部圆角处材料变薄,顶部靠近凸缘处材料变厚,矩形拉伸件四周圆角处材料变厚。
4.6.1拉伸件产品尺寸的标准方法在设计拉伸产品时,对产品图上的尺寸应明确注明必须保证外部尺寸或内部尺寸,不能同时标注内外尺寸。
4.6.2拉伸件尺寸公差的标注方法拉伸件凹凸圆弧的内半径以及一次成形的圆筒形拉伸件的高度尺寸公差为双面对称偏差,其偏差值为国标(GB)16级精度公差绝对值的一半,并冠以±号。
5成形 5.1加强筋在板状金属零件上压筋,有助于增加结构刚性,加强筋结构及其尺寸选择参见表表7 加强筋结构及尺寸选择5.2打凸间距和凸边距的极限尺寸打凸间距和凸边距的极限尺寸按下表选取。
表8打凸间距和凸边距的极限尺寸5.3百叶窗百叶窗通常用于各种罩壳或机壳上起通风散热作用,其成型方法是借凸模的一边刃口将材料切 开,而凸模的其余部分将材料同时作拉伸变形,形成一边开口的起伏形状。
百叶窗的典型结构参见图6.3.1。
6。
<7-ion打凸01,5〉七C05-1.5H15-3CDL 16 5 106 e 吕1375 10.591J闵11152?1S34引44G65J30竝药48405545(>■©图6.3.1(图百叶5的结构百叶窗尺寸要求:a> 4t; b> 6t ; hw 5t ; L> 24t ; r > 0.5t。
5.4孔翻边孔翻边型式较多,本规范只关注要加工螺纹的内孔翻边,如图rr图6.4.1带螺图孔覘内孔翻边结构示意图螺纹材料厚度t 翻边内孔D 翻边外孔d2 凸缘高度h 预冲孔直径D b 凸缘圆角半径RM3 0.82.553.38 1.6 1.9 0.6 13.25 1.6 2.20.53.38 1.8 1.93.5 2 21.23.38 1.92 20.63.5 2.16 1.51.5 3.52.4 1.7 0.756.4.1所示。