叉车阀介绍资料
叉车阀地原理介绍资料

叉车比例多路阀一、目前国内小吨位叉车的现状:目前国内各叉车主机厂生产的小吨位叉车所使用的叉车多路阀基本上都是CDB系列,属于普通换向阀加齿轮定量泵组合模式,从能源的利用率上来讲比较浪费,与当前节能、减排、低碳的大背景格格不入。
而从整车自身运转所浪费的能量而言,通过提升配套件性能来改善能量利用率从而达到节能减排的确是条可行的路。
二、现有配置状况及我们的完整解决方案:1.现有配置模式:目前国内主流配置的叉车多路阀如下图所示,属CDB系列,该技术已有二十几年,一直沿用至今而未作改进。
该类型的阀属于普通换向阀,在操纵过程中流量会随着负载的变化而变化,在不做门架动作时,搭配的定量齿轮泵排出液压油都是在浪费能量,而且供给转向机的油路一直在供油(12L/min左右)。
2.我们完整的解决方案包括:性能优越的变量柱塞泵(负荷传感+压力切断),流量与负载无关的LUDV比例阀,控制阀,控制器,手柄,面向集成控制以及客户定制的相关软件。
3.我们的解决方案具备优点:我们的比例阀如下图所示1.此阀属于LUDV比例阀,流量大小不受负载影响;2.在不做门架动作以及转向动作时,变量泵的排量可以达到最小,使功耗降到最低;3.转向油路不是常供型,只有在做转向动作时,阀的转向阀芯对转向机产生的压力做出反馈后给再给转向机供油,此功能在发动机怠速状态下大大提高工作效率;4.在完整解决方案之外还有多种组合模式,比例阀有手动型、液控型和电控型,三者之间的外型除了在控制端不同之外几乎无差别,以及对应的控制阀不一样,它们可以和变量泵、齿轮泵,普通型转向机、负载反馈型转向机等进行任意组合(用两种转向机的效果相同);5.我们提供的方案中包括有安全模块。
三、传统叉车多路阀台架试验数据:试验条件:系统流量80L/min1.主溢流阀及转向溢流阀的压力测试:主溢流阀20MPa(17MPa已微开启),转向溢流阀12MPa,这两个压力可调2.中位流阻测试:中位P→T的流阻30bar3.各A、B工作油口的流量测定:Q A1=68L/min,Q A2=57L/min,Q B2=65L/min4.A、B工作油口加载185bar时,在T口的泄漏量测定:A1=2ml/min A2=2ml/min (行业内部要求泄漏量低于7ml/min)5.阀芯打到A1口出油的机能位,堵住A1口,P口加载150bar,在T口的泄漏量测定:测得的泄漏量为33ml/min(行业内部要求低于240ml/min)6.PF口的流量测定:Q PF=12.3L/min四、我们的叉车比例多路阀台架试验数据:试验条件:系统流量80L/min1.主溢流阀及转向溢流阀的压力测试:主溢流阀20MPa(19MPa微开启),转向溢流阀13MPa,这两个压力可调2.中位流阻测试:中位P→T的流阻22bar3.各A、B工作油口的流量测定:Q A1=68L/min,Q A2=34L/min,Q B2=39L/min,(A2,B2是倾斜联,考虑原来流量过大,动作会太猛,故调整到这个流量)Q A3=57L/min,Q B3=57L/min,Q A4=56L/min,Q B4=53L/min,4.A、B工作油口加载185bar时,在T口的泄漏量测定:A1=3.5ml/min A2=1.5ml/min A3=3.8ml/minB3=3.9ml/min A4=5.8ml/min B4=4ml/min(行业内部要求泄漏量低于7ml/min)5.阀芯打到A1口出油的机能位,堵住A1口,P口加载150bar,在T口的泄漏量测定:测得的泄漏量为48ml/min(行业内部要求低于240ml/min)6. PF口及LS1的流量测定:当PF口堵住时,LS1口的流量为360ml/min(丹佛斯的流量大于1L/min)当LS1口堵住,PF口的负载达到16bar时,PF口开始出油,达到23bar时,PF口的流量达到最大,最大流量为11.5L/min(LS1口为转向负载口,用普通型转向机时,将此口堵住)7.一次压力输出口的流量测定:P口流量80L/min时,一次压力输出P1口在中位时的输出流量为3L/min8.各控制油口的控制压力检测:各控制油口的控制压力Px=6bar~16bar五、台架试验的控制压力—流量曲线:以下为各工作油口的控制压力—流量曲线图,据图可发现该阀的操纵新很高六、案例对比分析:如上图所示,从左自右分别是CDB 系列叉车阀配定量泵、我厂叉车阀配定量泵、我厂叉车阀配变量泵时各种叉车多路阀的能量利用图(阴影部分的面积大小加以区分,总的框架是泵提供的功率,只是定性的表示一下),反过来说就是可以降低发动机的功率。
叉车调速阀浅析

压力差( 1 P ) P 一 L产生 的液压力与定差减压阀 阀芯左端的弹簧力 F 以及液 流作用于阀芯 的稳态液动力 F 相平衡 , t 定差减压阀的阀芯 就处于某一平衡位置。在节流 阀开 口不变的
条件下 , 果 调 速 阀进 出 口压力 差 ( 0 L 如 P 一P ) 由于外 界原 因发 生 变 化 , 如 出 口压 力 P 譬 因
也可 以 串联 在节 流 阀之后 即后 置式 ( 图 2— 如
2。 )
目 前国内大多数内燃型叉车甚至一些 电 动叉车采用的调速阀仍是 比较简单的管式单 向节流阀。这种调速 阀结构简单 , 其流量不
随 阀进 出 口之 间 的压 力 差 而 变化 , 即调 定 的
目前 叉 车 使 用 的 调 速 阀 阀 芯 属 同 心 结 构, 阀体 多 采 用 嵌 套 结 构 。这 种 结 构 降 低 了 加工 难 度 , 阀体 、 阀套 孔 均 为 通孔 , 于 加 工 利 且精 度容 易保证 。但 是叉 车 调速 阀在 设 计 加 工 中 , 虑到成本 等 原 因 , 结构 上 与 上述 调 考 在
力补偿 , 均可 以使 节流阀前后压力差基本保 持不变。即调速阀的流量在 负载变化时仍能 保持稳定 。如图 4 2 调 速阀与节流阀的流 — (
量特性 比较 ) 示 , 节 流 口过 流 截 面 A 相 所 在 U 同的条件 下 , 速 阀 与 节 流 阀 的 流量 特 性 不 调 相 同。 只 有 当 调 速 阀 进 出 口 压 力 差 小 于
二者呈线性关系, 因此灵敏度相对较高) 。
2 工 作原 理
调速 阀主要 用 于定 量 泵 液压 系统 中 。 目
前 叉 车用 调 速 阀多 为 前 置 式 , 速 阀 正 向过 调 油直 通 时 的 区 别 在 上 述 结 构 介 绍 中 已 有 说
叉车起升油缸安全阀的设计

叉车起升油缸安全阀的设计安全阀是叉车起升油缸的重要部分,保证了叉车升降货物过程中,发生管路失效时,货物不因迅速下降而导致货物与操作人员的伤害。
该文主要对如何对起升油缸安全阀设计与试验进行总结,以期对叉车安全性的提高起到积极推动作用。
引言叉车起升油缸一般为单作用油缸,靠油液作用于无杆腔活塞实现提升功能;下降则靠活塞杆、活塞和负载的重力作用,下降时限速阀控制活塞下降速度。
在叉车升降货物过程中,若起升油缸管路发生暴裂失效,货物受重力作用迅速下落,会导致货物摔坏,危及操作者和周边工作人员的人身安全。
1、安全阀工作原理在起升油缸缸头内设置一个安全阀(如1 所示),该安全阀功能相当于单向节流阀。
当油液从接头流入油缸大腔时,该安全阀不起作用;当起升油缸管路暴裂时,阀芯两侧压差迅速增大,将阀芯推至油口处,油液只能从阀芯上的节流孔流出,减小回油流量,从而降低货物下降速度,起到保护的作用。
2、安全阀设计计算2.1、已知条件缸径、活塞行程、负载、限速阀流量、起升油缸管路发生暴裂时重物下落时间。
限速阀流量作为安全阀匹配计算时的已知条件。
1-阀芯2-弹簧3-阀芯大孔4-阀芯小孔5-起升油缸缸头6-起升油缸缸头油腔7-起升油缸过渡接头1 起升油缸缸头与安全阀装配3、安全阀的试验方法3.1、性能试验依据叉车起升油缸的实际工况,确立基本试验条件。
将安全阀装入叉车起升油缸中,按4 在液压试验台上连接好各管路;控制电磁换向阀7 让油缸自然伸缩3 次,确保无卡死或漏油现象。
使油缸活塞杆伸出最长,关闭电磁阀,给油缸小腔加与负载相应的压力,真空技术网(http://.chvacuumxx/)认为当小腔压力达到预定压力时,打开电磁阀,保持小腔压力基本不变,活塞杆向内收回,记录油缸活塞杆收回整个过程的有杆腔与无杆腔的压力、油缸油口流量、活塞杆收回的时间。
活塞杆收回的时间至少为10s 以上。
3.2、整机试验整机试验时应完成以下3 种工况试验。
叉车比例多路阀介绍

叉车比例多路阀一、目前国内小吨位叉车的现状:目前国内各叉车主机厂生产的小吨位叉车所使用的叉车多路阀基本上都是CDB系列,属于普通换向阀加齿轮定量泵组合模式,从能源的利用率上来讲比较浪费,与当前节能、减排、低碳的大背景格格不入。
而从整车自身运转所浪费的能量而言,通过提升配套件性能来改善能量利用率从而达到节能减排的确是条可行的路。
二、现有配置状况及我们的完整解决方案:1.现有配置模式:目前国内主流配置的叉车多路阀如下图所示,属CDB系列,该技术已有二十几年,一直沿用至今而未作改进。
该类型的阀属于普通换向阀,在操纵过程中流量会随着负载的变化而变化,在不做门架动作时,搭配的定量齿轮泵排出液压油都是在浪费能量,而且供给转向机的油路一直在供油(12L/min左右)。
2.我们完整的解决方案包括:性能优越的变量柱塞泵(负荷传感+压力切断),流量与负载无关的LUDV比例阀,控制阀,控制器,手柄,面向集成控制以及客户定制的相关软件。
3.我们的解决方案具备优点:我们的比例阀如下图所示1.此阀属于LUDV比例阀,流量大小不受负载影响;2.在不做门架动作以及转向动作时,变量泵的排量可以达到最小,使功耗降到最低;3.转向油路不是常供型,只有在做转向动作时,阀的转向阀芯对转向机产生的压力做出反馈后给再给转向机供油,此功能在发动机怠速状态下大大提高工作效率;4.在完整解决方案之外还有多种组合模式,比例阀有手动型、液控型和电控型,三者之间的外型除了在控制端不同之外几乎无差别,以及对应的控制阀不一样,它们可以和变量泵、齿轮泵,普通型转向机、负载反馈型转向机等进行任意组合(用两种转向机的效果相同);5.我们提供的方案中包括有安全模块。
三、传统叉车多路阀台架试验数据:试验条件:系统流量80L/min1.主溢流阀及转向溢流阀的压力测试:主溢流阀20MPa(17MPa已微开启),转向溢流阀12MPa,这两个压力可调2.中位流阻测试:中位P→T的流阻30bar3.各A、B工作油口的流量测定:Q A1=68L/min,Q A2=57L/min,Q B2=65L/min4.A、B工作油口加载185bar时,在T口的泄漏量测定:A1=2ml/min A2=2ml/min (行业内部要求泄漏量低于7ml/min)5.阀芯打到A1口出油的机能位,堵住A1口,P口加载150bar,在T口的泄漏量测定:测得的泄漏量为33ml/min(行业内部要求低于240ml/min)6.PF口的流量测定:Q PF=12.3L/min四、我们的叉车比例多路阀台架试验数据:试验条件:系统流量80L/min1.主溢流阀及转向溢流阀的压力测试:主溢流阀20MPa(19MPa微开启),转向溢流阀13MPa,这两个压力可调2.中位流阻测试:中位P→T的流阻22bar3.各A、B工作油口的流量测定:Q A1=68L/min,Q A2=34L/min,Q B2=39L/min,(A2,B2是倾斜联,考虑原来流量过大,动作会太猛,故调整到这个流量)Q A3=57L/min,Q B3=57L/min,Q A4=56L/min,Q B4=53L/min,4.A、B工作油口加载185bar时,在T口的泄漏量测定:A1=3.5ml/min A2=1.5ml/min A3=3.8ml/minB3=3.9ml/min A4=5.8ml/min B4=4ml/min(行业内部要求泄漏量低于7ml/min)5.阀芯打到A1口出油的机能位,堵住A1口,P口加载150bar,在T口的泄漏量测定:测得的泄漏量为48ml/min(行业内部要求低于240ml/min)6. PF口及LS1的流量测定:当PF口堵住时,LS1口的流量为360ml/min(丹佛斯的流量大于1L/min)当LS1口堵住,PF口的负载达到16bar时,PF口开始出油,达到23bar时,PF口的流量达到最大,最大流量为11.5L/min(LS1口为转向负载口,用普通型转向机时,将此口堵住)7.一次压力输出口的流量测定:P口流量80L/min时,一次压力输出P1口在中位时的输出流量为3L/min8.各控制油口的控制压力检测:各控制油口的控制压力Px=6bar~16bar五、台架试验的控制压力—流量曲线:以下为各工作油口的控制压力—流量曲线图,据图可发现该阀的操纵新很高六、案例对比分析:如上图所示,从左自右分别是CDB 系列叉车阀配定量泵、我厂叉车阀配定量泵、我厂叉车阀配变量泵时各种叉车多路阀的能量利用图(阴影部分的面积大小加以区分,总的框架是泵提供的功率,只是定性的表示一下),反过来说就是可以降低发动机的功率。
叉车阀的介绍资料全

叉车比例多路阀一、目前国内小吨位叉车的现状:目前国内各叉车主机厂生产的小吨位叉车所使用的叉车多路阀基本上都是CDB系列,属于普通换向阀加齿轮定量泵组合模式,从能源的利用率上来讲比较浪费,与当前节能、减排、低碳的大背景格格不入。
而从整车自身运转所浪费的能量而言,通过提升配套件性能来改善能量利用率从而达到节能减排的确是条可行的路。
二、现有配置状况及我们的完整解决方案:1.现有配置模式:目前国内主流配置的叉车多路阀如下图所示,属CDB系列,该技术已有二十几年,一直沿用至今而未作改进。
该类型的阀属于普通换向阀,在操纵过程中流量会随着负载的变化而变化,在不做门架动作时,搭配的定量齿轮泵排出液压油都是在浪费能量,而且供给转向机的油路一直在供油(12L/min左右)。
2.我们完整的解决方案包括:性能优越的变量柱塞泵(负荷传感+压力切断),流量与负载无关的LUDV比例阀,控制阀,控制器,手柄,面向集成控制以及客户定制的相关软件。
3.我们的解决方案具备优点:我们的比例阀如下图所示1.此阀属于LUDV比例阀,流量大小不受负载影响;2.在不做门架动作以及转向动作时,变量泵的排量可以达到最小,使功耗降到最低;3.转向油路不是常供型,只有在做转向动作时,阀的转向阀芯对转向机产生的压力做出反馈后给再给转向机供油,此功能在发动机怠速状态下大大提高工作效率;4.在完整解决方案之外还有多种组合模式,比例阀有手动型、液控型和电控型,三者之间的外型除了在控制端不同之外几乎无差别,以及对应的控制阀不一样,它们可以和变量泵、齿轮泵,普通型转向机、负载反馈型转向机等进行任意组合(用两种转向机的效果相同);5.我们提供的方案中包括有安全模块。
三、传统叉车多路阀台架试验数据:试验条件:系统流量80L/min1.主溢流阀及转向溢流阀的压力测试:主溢流阀20MPa(17MPa已微开启),转向溢流阀12MPa,这两个压力可调2.中位流阻测试:中位P→T的流阻30bar3.各A、B工作油口的流量测定:Q A1=68L/min,Q A2=57L/min,Q B2=65L/min4.A、B工作油口加载185bar时,在T口的泄漏量测定:A1=2ml/min A2=2ml/min (行业内部要求泄漏量低于7ml/min)5.阀芯打到A1口出油的机能位,堵住A1口,P口加载150bar,在T口的泄漏量测定:测得的泄漏量为33ml/min(行业内部要求低于240ml/min)6.PF口的流量测定:Q PF=12.3L/min四、我们的叉车比例多路阀台架试验数据:试验条件:系统流量80L/min1.主溢流阀及转向溢流阀的压力测试:主溢流阀20MPa(19MPa微开启),转向溢流阀13MPa,这两个压力可调2.中位流阻测试:中位P→T的流阻22bar3.各A、B工作油口的流量测定:Q A1=68L/min,Q A2=34L/min,Q B2=39L/min,(A2,B2是倾斜联,考虑原来流量过大,动作会太猛,故调整到这个流量)Q A3=57L/min,Q B3=57L/min,Q A4=56L/min,Q B4=53L/min,4.A、B工作油口加载185bar时,在T口的泄漏量测定:A1=3.5ml/min A2=1.5ml/min A3=3.8ml/minB3=3.9ml/min A4=5.8ml/min B4=4ml/min(行业内部要求泄漏量低于7ml/min)5.阀芯打到A1口出油的机能位,堵住A1口,P口加载150bar,在T口的泄漏量测定:测得的泄漏量为48ml/min(行业内部要求低于240ml/min)6. PF口及LS1的流量测定:当PF口堵住时,LS1口的流量为360ml/min(丹佛斯的流量大于1L/min)当LS1口堵住,PF口的负载达到16bar时,PF口开始出油,达到23bar时,PF口的流量达到最大,最大流量为11.5L/min(LS1口为转向负载口,用普通型转向机时,将此口堵住)7.一次压力输出口的流量测定:P口流量80L/min时,一次压力输出P1口在中位时的输出流量为3L/min8.各控制油口的控制压力检测:各控制油口的控制压力Px=6bar~16bar五、台架试验的控制压力—流量曲线:以下为各工作油口的控制压力—流量曲线图,据图可发现该阀的操纵新很高六、案例对比分析:如上图所示,从左自右分别是CDB 系列叉车阀配定量泵、我厂叉车阀配定量泵、我厂叉车阀配变量泵时各种叉车多路阀的能量利用图(阴影部分的面积大小加以区分,总的框架是泵提供的功率,只是定性的表示一下),反过来说就是可以降低发动机的功率。
叉车多路阀维修及原理
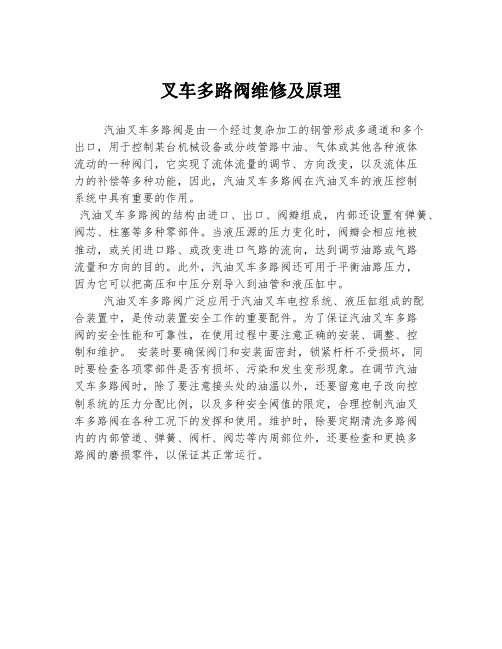
叉车多路阀维修及原理
汽油叉车多路阀是由一个经过复杂加工的钢管形成多通道和多个
出口,用于控制某台机械设备或分歧管路中油、气体或其他各种液体
流动的一种阀门,它实现了流体流量的调节、方向改变,以及流体压
力的补偿等多种功能,因此,汽油叉车多路阀在汽油叉车的液压控制
系统中具有重要的作用。
汽油叉车多路阀的结构由进口、出口、阀瓣组成,内部还设置有弹簧、阀芯、柱塞等多种零部件。
当液压源的压力变化时,阀瓣会相应地被
推动,或关闭进口路、或改变进口气路的流向,达到调节油路或气路
流量和方向的目的。
此外,汽油叉车多路阀还可用于平衡油路压力,
因为它可以把高压和中压分别导入到油管和液压缸中。
汽油叉车多路阀广泛应用于汽油叉车电控系统、液压缸组成的配
合装置中,是传动装置安全工作的重要配件。
为了保证汽油叉车多路
阀的安全性能和可靠性,在使用过程中要注意正确的安装、调整、控
制和维护。
安装时要确保阀门和安装面密封,锁紧杆杆不受损坏,同
时要检查各项零部件是否有损坏、污染和发生变形现象。
在调节汽油
叉车多路阀时,除了要注意接头处的油温以外,还要留意电子改向控
制系统的压力分配比例,以及多种安全阈值的限定,合理控制汽油叉
车多路阀在各种工况下的发挥和使用。
维护时,除要定期清洗多路阀
内的内部管道、弹簧、阀杆、阀芯等内周部位外,还要检查和更换多
路阀的磨损零件,以保证其正常运行。
叉车多路阀工作原理
叉车多路阀工作原理
叉车多路阀是叉车液压系统中的一个重要部件,它的工作原理如下:
1. 液压油进入多路阀的供油口,经过内部的通道进入阀体。
2. 控制手柄操作时,通过操纵杆和阀体内的机构(如弹簧、活塞等)使得相应的阀门打开或关闭,从而控制液压油的流向和压力。
3. 当控制手柄处于中间位置时,多路阀处于中立状态,液压系统中的液压油停止流动。
4. 当控制手柄向前或向后操作时,阀体内的相应阀门会打开或关闭,使得液压油流向液压缸或其他执行元件。
5. 通过多路阀的控制,可以实现叉车的升降、前后倾斜、侧向位移等运动。
需要注意的是,多路阀的工作原理可以根据不同的型号和设计有所差异,以上仅为一般情况下的工作原理。
具体使用时,应根据实际情况选择合适的多路阀,并根据其技术手册进行正确的操作和维护。
叉车电磁阀工作原理
叉车电磁阀工作原理
叉车电磁阀是控制叉车液压系统中液压油流的重要元件,其工作原理如下:
1. 结构组成:叉车电磁阀通常由电磁线圈、阀体和阀芯组成。
2. 原理说明:当电磁阀接通电源时,电磁线圈受电磁激励后产生磁场。
磁场的作用下,阀芯被吸引,与阀座之间的密封被打开。
此时,液压油可以通过阀芯与阀座之间的通道流过。
3. 控制液压油流:叉车电磁阀通常有两种工作状态,分别是“开”和“关”。
当电磁阀通电时,阀芯被吸引,阀门处于开启状态,液压油流经阀门进入液压系统。
当电磁阀断电时,阀芯恢复原位,阀门关闭,停止液压油流的流动。
4. 简单控制系统:在典型的叉车液压系统中,电磁阀往往与其他元件配合使用,如油泵、液压缸等。
通过控制电磁阀的通电和断电,可以实现对液压油流的调节和控制,进而控制叉车的动作。
总的来说,叉车电磁阀的工作原理是通过电磁激励产生磁场,使阀芯被吸引或恢复原位,实现对液压油流的控制,从而控制叉车的运动。
这种简单而可靠的工作原理使得叉车电磁阀成为叉车液压系统中不可或缺的重要部件。
叉车多路阀工作原理
叉车多路阀工作原理叉车多路阀是叉车液压系统中的重要组成部分,它承担着控制液压系统流向、压力和流量的重要作用。
了解叉车多路阀的工作原理对于提高叉车的工作效率和安全性具有重要意义。
首先,我们来了解一下叉车多路阀的结构。
叉车多路阀通常由阀体、阀芯、控制杆、弹簧等部件组成。
阀芯是多路阀的核心部件,它通过控制杆的移动来改变阀的通道,从而实现对液压系统的控制。
弹簧则起到了稳定阀芯位置的作用,保证阀芯在不受外力作用时能够保持在规定的位置。
其次,叉车多路阀的工作原理主要包括液压控制和机械控制两个方面。
液压控制是指通过液压力来控制阀芯的移动,从而改变阀的通道,实现对液压系统的控制。
机械控制则是指通过操纵控制杆来改变阀芯的位置,从而达到控制液压系统的目的。
叉车多路阀的工作原理可以简单概括为,当控制杆移动时,通过机械控制使阀芯位置发生变化,从而改变阀的通道,控制液压系统的流向、压力和流量。
液压控制则是通过液压力来辅助机械控制,使阀芯能够更加灵活地移动,实现对液压系统的精确控制。
叉车多路阀的工作原理决定了其在叉车液压系统中的重要作用。
它能够实现叉车液压系统的各种功能,如提升、倾斜、侧移等操作。
同时,叉车多路阀的工作原理也决定了其对叉车工作效率和安全性的影响。
只有深入了解叉车多路阀的工作原理,才能更好地进行维护和保养,确保叉车的正常运行。
总之,了解叉车多路阀的工作原理对于提高叉车的工作效率和安全性具有重要意义。
只有深入了解其结构和工作原理,才能更好地发挥其在叉车液压系统中的作用,确保叉车的正常运行。
希望本文能够帮助大家更好地了解叉车多路阀的工作原理,为叉车的维护和保养提供帮助。
叉车安全阀的工作原理
叉车安全阀的工作原理
叉车安全阀是一种防止叉车液压系统压力超过设定值的装置。
其工作原理如下:
1. 压力调节阀:安全阀内部设有压力调节阀,用于设置叉车液压系统的最大工作压力。
当系统压力超过设定值时,压力调节阀会自动打开,释放过多的液压油。
2. 弹簧机构:压力调节阀通过弹簧机构实现压力调节。
弹簧机构会根据设定的压力值来控制阀门的开启和关闭。
当系统压力增加到设定值时,弹簧受到压力的作用,会将阀门打开,使液压油流出,从而保持系统的正常工作压力。
3. 密封结构:叉车安全阀内部的密封结构可以防止过多的液压油从阀门处泄漏出来。
它可以确保叉车液压系统在设定的压力范围内工作,同时防止系统压力过高而引发故障或危险。
总的来说,叉车安全阀通过压力调节阀和弹簧机构,监控和控制叉车液压系统的压力,确保系统在安全范围内运行。
一旦系统压力超过设定值,安全阀会自动打开,释放过多的液压油,以确保系统不会受到过高的压力影响。
- 1、下载文档前请自行甄别文档内容的完整性,平台不提供额外的编辑、内容补充、找答案等附加服务。
- 2、"仅部分预览"的文档,不可在线预览部分如存在完整性等问题,可反馈申请退款(可完整预览的文档不适用该条件!)。
- 3、如文档侵犯您的权益,请联系客服反馈,我们会尽快为您处理(人工客服工作时间:9:00-18:30)。
叉车比例多路阀
一、目前国内小吨位叉车的现状:
目前国内各叉车主机厂生产的小吨位叉车所使用的叉车多路阀基本上都是CDB系列,属于普通换向阀加齿轮定量泵组合模式,从能源的利用率上来讲比较浪费,与当前节能、减排、低碳的大背景格格不入。
而从整车自身运转所浪费的能量而言,通过提升配套件性能来改善能量利用率从而达到节能减排的确是条可行的路。
二、现有配置状况及我们的完整解决方案:
1.现有配置模式:
目前国内主流配置的叉车多路阀如下图所示,属CDB系列,该技术已有二十几年,一直沿用至今而未作改进。
该类型的阀属于普通换向阀,在操纵过程中流量会随着负载的变化而变化,在不做门架动作时,搭配的定量齿轮泵排出液压油都是在浪费能量,而且供给转向机的油路一直在供油(12L/min左右)。
2.我们完整的解决方案包括:
性能优越的变量柱塞泵(负荷传感+压力切断),流量与负载无关的LUDV比例阀,控制阀,控制器,手柄,面向集成控制以及客户定制的相关软件。
3.我们的解决方案具备优点:
我们的比例阀如下图所示
1.此阀属于LUDV比例阀,流量大小不受负载影响;
2.在不做门架动作以及转向动作时,变量泵的排量可以达到最小,使功耗
降到最低;
3.转向油路不是常供型,只有在做转向动作时,阀的转向阀芯对转向机产
生的压力做出反馈后给再给转向机供油,此功能在发动机怠速状态下大大提高工作效率;
4.在完整解决方案之外还有多种组合模式,比例阀有手动型、液控型和电
控型,三者之间的外型除了在控制端不同之外几乎无差别,以及对应的控制阀不一样,它们可以和变量泵、齿轮泵,普通型转向机、负载反馈型转向机等进行任意组合(用两种转向机的效果相同);
5.我们提供的方案中包括有安全模块。
三、传统叉车多路阀台架试验数据:
试验条件:系统流量80L/min
1.主溢流阀及转向溢流阀的压力测试:
主溢流阀20MPa(17MPa已微开启),转向溢流阀12MPa,这两个压力可调2.中位流阻测试:
中位P→T的流阻30bar
3.各A、B工作油口的流量测定:
Q A1=68L/min,Q A2=57L/min,Q B2=65L/min
4.A、B工作油口加载185bar时,在T口的泄漏量测定:
A1=2ml/min A2=2ml/min (行业内部要求泄漏量低于7ml/min)
5.阀芯打到A1口出油的机能位,堵住A1口,P口加载150bar,在T口的泄漏量测定:
测得的泄漏量为33ml/min(行业内部要求低于240ml/min)
6.PF口的流量测定:
Q PF=12.3L/min
四、我们的叉车比例多路阀台架试验数据:
试验条件:系统流量80L/min
1.主溢流阀及转向溢流阀的压力测试:
主溢流阀20MPa(19MPa微开启),转向溢流阀13MPa,这两个压力可调
2.中位流阻测试:
中位P→T的流阻22bar
3.各A、B工作油口的流量测定:
Q A1=68L/min,Q A2=34L/min,Q B2=39L/min,(A2,B2是倾斜联,考虑原来流量过大,动作会太猛,故调整到这个流量)
Q A3=57L/min,Q B3=57L/min,Q A4=56L/min,Q B4=53L/min,
4.A、B工作油口加载185bar时,在T口的泄漏量测定:
A1=3.5ml/min A2=1.5ml/min A3=3.8ml/min
B3=3.9ml/min A4=5.8ml/min B4=4ml/min
(行业内部要求泄漏量低于7ml/min)
5.阀芯打到A1口出油的机能位,堵住A1口,P口加载150bar,在T口的泄漏量测定:
测得的泄漏量为48ml/min(行业内部要求低于240ml/min)
6. PF口及LS1的流量测定:
当PF口堵住时,LS1口的流量为360ml/min(丹佛斯的流量大于1L/min)当LS1口堵住,PF口的负载达到16bar时,PF口开始出油,达到23bar时,PF口的流量达到最大,最大流量为11.5L/min(LS1口为转向负载口,用普通型转向机时,将此口堵住)
7.一次压力输出口的流量测定:
P口流量80L/min时,一次压力输出P1口在中位时的输出流量为3L/min
8.各控制油口的控制压力检测:
各控制油口的控制压力Px=6bar~16bar
五、台架试验的控制压力—流量曲线:
以下为各工作油口的控制压力—流量曲线图,据图可发现该阀的操纵新很高
六、案例对比分析:
如上图所示,从左自右分别是CDB 系列叉车阀配定量泵、我厂叉车阀配定量泵、我厂叉车阀配变量泵时各种叉车多路阀的能量利用图(阴影部分的面积大小加以区分,总的框架是泵提供的功率,只是定性的表示一下),反过来说就是可以降低发动机的功率。
从而实现在满足相同工作要求情况下,减少排放量,降低叉车的使用成本。
以下举例说明,对比条件如下:
1.两者都用28ml/r 的泵,一个是定量泵,一个是变量泵
2.执行机构高速工作流量65L/min ,工作压力为170bar ,发动机怠速800r/min ,此时流量可以达到22L/min
3.要求执行机构的流量达到30L/min (在相同工作效率下做对比),转向不工作时老阀的转向流量12L/min ,新阀1L/min ,工作时都为12L/min ,转向工作压力100bar ,不工作压力为10bar
4.两者的中位压力都定为22bar
5.假定发动机全速工作、执行机构流量30L/min 工作以及待命的时间比是:4:4:2,另外在工作状态时,货叉的动作时间和行走时间各占一半
那么新阀对比老阀的能耗比:
另外,在怠速状态时,油泵的流量最大为22.4L/min ,老阀转向待命需要12L/min ,新阀只需要1L/min ,那么他们供执行机构的流量分别为10.4L/min 和
879
.02
1222212100230222121023017021210026522212102651702
12221210021102301702121002110265170=⨯⨯+⨯⨯+⨯⨯+⨯⨯+⨯⨯+⨯⨯+⨯⨯+⨯⨯+⨯⨯⨯⨯+⨯⨯+⨯⨯+⨯⨯+⨯⨯+⨯⨯+⨯⨯
21.4L/min,那么新阀的工作效率将会是老阀的205.7%
七、技术参数及原理:
1.额定流量80L/min
2.额定压力20MPa
3.转向流量11.5L/min
4.转向额定压力13MPa
5.控制压力6bar~16bar。