注塑模具设计
注塑模具设计
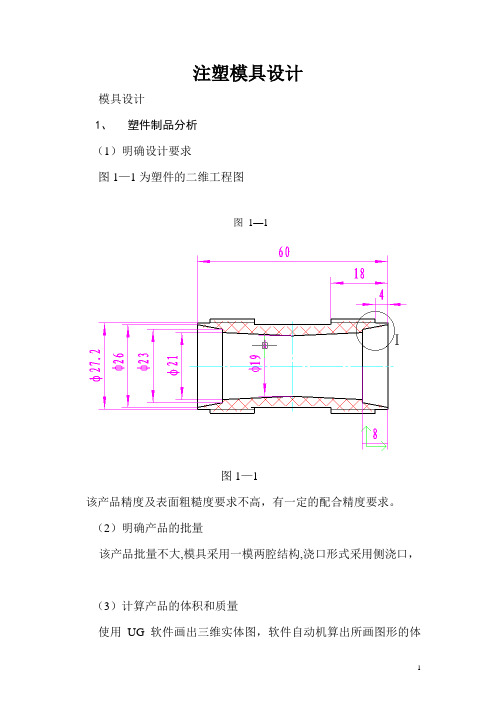
注塑模具设计模具设计1、塑件制品分析(1)明确设计要求图1—1为塑件的二维工程图图1—1图1—1该产品精度及表面粗糙度要求不高,有一定的配合精度要求。
(2)明确产品的批量该产品批量不大,模具采用一模两腔结构,浇口形式采用侧浇口,(3)计算产品的体积和质量使用UG软件画出三维实体图,软件自动机算出所画图形的体积。
通过计算得塑件的体积V塑=13.85cm3塑件的质量M塑=ρV塑=1.04×13.85=14.4g式中ρ---塑料的密度,g/cm3.流道凝料的质量m2还是个未知数,可按塑件质量的0.6倍来估算。
浇注系统的质量M浇=ρV浇=8.6g浇注系统的体积V浇=8.30cm3.故V总= 2×V塑+V浇= 2×13.85cm3 +8.30cm3.= 36cm3 M总=2×M塑+M浇=2×14.4g+8.6g= 43g2.注塑机的确定选择注射机型号 XS—ZY—250主要技术规格如下:螺杆直径:65mm注射容量:250cm3注射压力:1300MPa锁模力:1800kN最大注射面积:500cm3模具厚度:最大350mm最小250mm模板行程:350mm喷嘴:球半径 18mm孔直径4m定位孔直径:125mm顶出:两侧孔径 40mm两侧孔距 280mm3.浇注系统的设计(1)主流道形式浇注系统是指模具从接触注射机喷嘴开始到型腔未知的塑料流动通道,起作用是使塑料熔体平稳且有顺序的填充到型腔中,并在填充和凝固过程中把注射压力充分传递到各个部位,已获得组织机密、外形清晰地塑件。
浇注系统可分为普通浇注系统和无流道凝料系统。
考虑浇注系统设计的基本原则:适应塑料的成型工艺性、利于型腔内气体的排出、尽量减少塑料熔体的热量和压力损失、避免熔料直冲细小型芯、便于修正和不影响塑件外观质量、便于减少塑料损失和减小模具尺寸等。
根据模具主流道与喷嘴的关系: R 2= R 1+(1~2)㎜ D=d+(0.5~1)㎜. 取主流道球面半径R=20㎜, 取主流道小端直径D =Φ5㎜, 球面配合高度h=3-5mm 取h=4 mm主流道长度 有标准模架结合该模具的结构,取L=85mm为了便于将凝料从主流道中拔出,将主流道设计成圆锥形,其斜度为1°~3°d—喷嘴直径 1~5.00+=d d 40=d 5=d2o=α R=10(2)分流道的设计分流道在多型腔模具中是必不可少的,它起连接主浇道和浇口的作用。
注塑模具的设计及制造

注塑模具的设计及制造注塑模具是用于注塑成型的模具,它的设计和制造直接关系到产品质量和生产效率。
本文将从设计和制造两个方面介绍注塑模具的相关知识。
一、注塑模具的设计1.产品设计分析:在进行注塑模具设计之前,首先要对即将生产的产品进行分析。
了解产品的形态尺寸、材料特性、注塑工艺和生产要求等,为模具设计提供依据。
2.模具结构设计:根据产品要求和注塑工艺,设计模具的结构。
包括模具的开合方式、定位方式、注塑道设计和冷却系统设计等。
合理的结构设计可以提高模具使用寿命和生产效率。
3.模具零件设计:根据模具结构设计,对各个零件进行详细设计。
比如模具芯、模具腔、滑块、顶出机构、定位销和定位套等。
零件设计要考虑到材料选择、加工工艺和装配要求等。
4.模具标准件选用:在模具设计过程中,可以选用一些标准件,如模具基础板、导向套和注塑嘴等。
合理选用标准件不仅可以减少设计工作量,还可以提高模具加工精度和降低成本。
5.注塑模具的通气设计:在注塑过程中,模具内会产生大量的气体,如果不能有效排出,会导致产品缺陷。
所以,在模具设计中要合理设置通气孔和排气槽,以确保注塑过程的质量。
二、注塑模具的制造1.模具材料选择:注塑模具常用的材料有优质合金钢和工具钢,比如P20、718、2738等。
材料的选择要根据产品要求、生产批量和制造成本等因素综合考虑。
2.模具加工工艺:注塑模具的加工工艺包括铣削、镗削、磨削、电火花和线切割等。
不同的加工工艺需要选用不同的设备和工装,操作人员要熟悉模具加工过程和技术要求。
3.模具热处理:模具在使用过程中需要经过热处理,以提高材料的硬度和耐磨性。
常见的热处理方法有淬火、回火和表面处理等,要根据模具材料和要求选择适当的热处理方法。
4.模具组装和调试:在模具制造完成后,需要对各个零部件进行组装和调试。
确保模具各部件的精度和配合度,在注塑生产前进行试模和修正,以保证产品质量。
总之,注塑模具的设计和制造对于提高注塑产品的质量和生产效率至关重要。
注塑模具设计岗位职责

注塑模具设计岗位职责注塑模具设计师是制造业中一个非常重要的技术专业。
他们的分工是根据顾客的需求设计并制造高精度、高速、高红利的注塑模具。
注塑模具设计师需对注塑成型设备和工艺有深刻的理解和应用,使生产效率得到提高,并最终生产出符合客户要求的产品。
下面是注塑模具设计岗位职责的范文。
工作职责注塑模具设计师的主要工作职责包括:1. 根据客户需求和订单确定注塑模具的设计规格和参数,包括尺寸、材料、结构等;2. 通过计算机辅助设计软件(CAD)和计算机辅助制造软件(CAM)进行注塑模具的3D设计,标准化和自动化制造;3. 技术支持生产部门,根据自己的经验和理解提供有关工艺、装置、工具的建议;4. 检查交付注塑模具的质量和重要性以确保制品符合客户的规格和需求;5. 对注塑模具的运行、维修和修复所需的材料进行补给,并协助生产和工程师解决技术问题;6. 处理紧急的模具修理请求,确保最小的生产停机时间和客户的质量受到影响;7. 熟悉注塑模具制造工艺,优化模具设计并提高生产效率,以满足客户的要求和时间限制;8. 研究新技术,寻找解决方案,并与客户和生产方案合作开展合作。
技能要求注塑模具设计师需要有以下技能和素质:1. 熟练使用CAD软件,对OEM技术有深入理解;2. 精通注塑模具制造流程,对注塑工艺有充分的了解;3. 执行项目设置和优化技术,可以为客户提供优质的设计服务和技术支持;4. 优秀的良品分析能力,可以在最短的时间内分析出错误的原因;5. 有独立思考分析的能力,以能够明确地表达和解读复杂的制造需求;6. 必须具备想象能力,以便在实际设计中得出最佳的解决方案;7. 需善于沟通和处理人员之间的合作关系,以满足客户质量需求;8. 可以有效组织团队实现目标,并按时交付。
注塑模具设计师是制造业中一个非常关键的专业,对整个行业、对整个社会都有重要的贡献。
因此,注塑模具设计师除了要具备技术能力外,还需要具备责任感和对工作的热情,以实现个人和公司的长足发展。
ug注塑模具设计实例
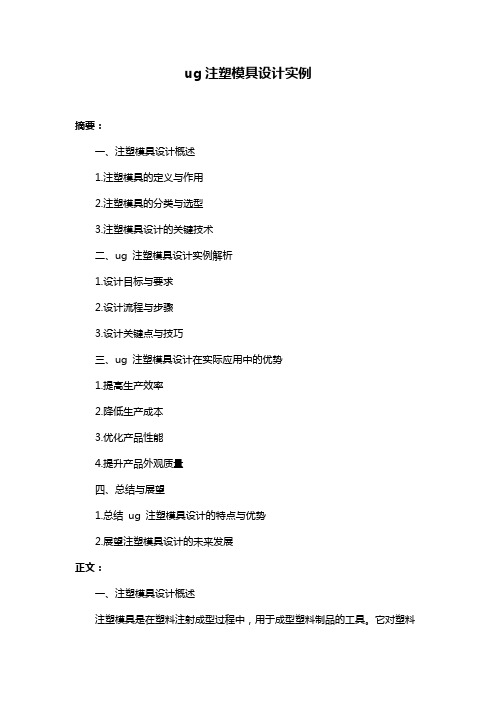
ug注塑模具设计实例摘要:一、注塑模具设计概述1.注塑模具的定义与作用2.注塑模具的分类与选型3.注塑模具设计的关键技术二、ug 注塑模具设计实例解析1.设计目标与要求2.设计流程与步骤3.设计关键点与技巧三、ug 注塑模具设计在实际应用中的优势1.提高生产效率2.降低生产成本3.优化产品性能4.提升产品外观质量四、总结与展望1.总结ug 注塑模具设计的特点与优势2.展望注塑模具设计的未来发展正文:一、注塑模具设计概述注塑模具是在塑料注射成型过程中,用于成型塑料制品的工具。
它对塑料进行准确塑形,保证制品的尺寸、形状、表面质量和物理性能。
注塑模具的设计是注塑成型工艺的关键环节,决定着产品的质量、成本和生产效率。
注塑模具主要分为热流道注塑模具、冷流道注塑模具和双色注塑模具等。
选型时需要根据产品的特点、生产批量和成本要求进行综合考虑。
注塑模具设计的关键技术包括:浇注系统设计、冷却系统设计、脱模机构设计、模具材料选择等。
这些技术影响着模具的性能、使用寿命和生产成本。
二、ug 注塑模具设计实例解析1.设计目标与要求本次设计的目标是制作一个高质量的注塑模具,用于生产一款手机壳。
要求模具具有良好的脱模性能、较长的使用寿命和较低的生产成本。
2.设计流程与步骤设计流程主要包括:分析产品结构、设计模具结构、分型面设计、浇注系统设计、冷却系统设计、脱模机构设计、模具材料选择、模具组装和出图。
3.设计关键点与技巧(1)分析产品结构:了解产品的形状、尺寸、材料和工艺要求,为模具设计提供依据。
(2)设计模具结构:根据产品特点,选择合适的模具类型,如热流道注塑模具。
(3)分型面设计:合理设置分型面,保证制品的质量和成型过程的顺利进行。
(4)浇注系统设计:设计合理的浇注系统,确保塑料充满模具,同时避免产生缺陷。
(5)冷却系统设计:设计高效的冷却系统,保证模具的快速冷却,提高生产效率。
(6)脱模机构设计:设计易于操作、安全的脱模机构,降低生产成本。
注塑模具设计知识与精髓
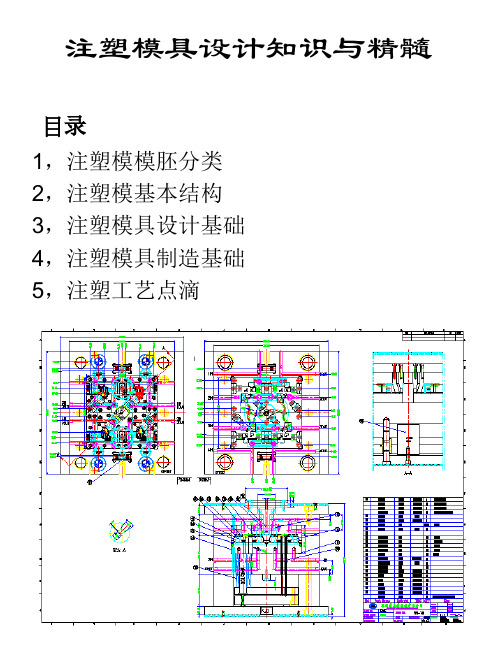
常见塑料的成型收缩率
塑料名称
收缩率(%)
塑料名称
HDPE
1.5~3.5(2.0)*
POM
LDPE
1.5~3.0(1.5)*
PA6
PP
1.0~3.0(1.5)*
PA66
GPPS
0.4~0.8(0.5)*
SPVC
HIPS
0.4~0.6(0.5)*
TPU
ABS
0.4~0.7(0.5)*
PMMA
PC
0.5~0.7(0.5)*
使截面面 积S =πR 2 时应取的 尺寸
0.250D D=2R
热量损失
最小
0.217b
0.250d
0.239D
0.228D
b =1.1D d =0.912D
小
较小
0.250b
0.222D
b =0.886D
较大
0.250d
0.220D
d =0.879D
大
0.153d
0.216D
d =1.414D
更大
其中之规律。
如右图,这是一个传动蜗杆,传动部分要求光滑平整,
入水应放在左端面,产品单件重2g,最大外径φ11.5,
长21.00。
此产品需采用三板模、螺纹抽芯结构。通常以抽芯
机构为圆心,圆状分布。参考抽芯机构标准件,综合加
工、材料的强度,选择四件为一组,产品中心距离125,
如果以这四件组为一模,模胚应为2330大小,注塑机
B,排气方式 a.分 型 面 排 气。 b. 成 型 芯 排 氣。 c.中 心 頂 杆 排 氣 d.頂 針 排 氣
e.側 型 芯 排 氣
流道截面形状
名称
注塑模具设计说明书

注塑模具设计说明书一、引言注塑模具是一种用于制造塑料制品的重要工具。
它具有精密设计和制造的特点,直接影响到注塑成型工艺的质量和效率。
本文档旨在提供一个注塑模具设计的详细说明书,以帮助使用者了解并正确使用注塑模具。
二、设计原则1. 功能性设计:注塑模具设计的首要目标是确保塑料制品的质量和精度。
需要考虑到产品的形状、尺寸、结构等因素,确保模具能够精确地复制产品的形状。
2. 可靠性设计:模具在长时间运行过程中需具有足够的可靠性和稳定性。
设计时应考虑到材料的选择、结构的合理性、工艺性能等因素,以确保模具能够长时间稳定运行。
3. 高效性设计:注塑模具的设计还要考虑到生产效率的提高。
在保证产品质量的前提下,优化流程、减少工序、提高生产速度等都是设计中需要考虑的因素。
三、设计要点1. 产品参数分析:仔细研究产品的形状、尺寸、材料等参数,并根据不同产品的要求进行合理设计。
2. 模具结构设计:根据产品的特点设计合理的模具结构,包括模具的分型面、脱模方式、冷却系统等。
3. 材料选择:根据产品和模具的要求选择合适的材料,考虑材料的韧性、硬度、耐磨性等因素。
4. 流道系统设计:设计合理的流道系统,以保证熔融塑料流动均匀,避免短流、死角等问题,提高注塑成型过程的效率。
5. 冷却系统设计:优化冷却系统的设计,保证塑料在注塑过程中能够迅速冷却固化,提高生产效率并减少翘曲、变形等问题。
6. 模具表面处理:根据产品的表面要求进行合适的模具表面处理,包括抛光、喷涂等,以提高产品的表面质量。
7. 模具装配:模具设计时应考虑装配的便利性和准确性,保证模具能够容易安装和拆卸。
四、注意事项1. 安全操作:在使用注塑模具时,必须严格遵守相关的操作规程和安全要求,保证操作人员的人身安全。
2. 维护保养:定期对模具进行清洁和维护保养,保证模具的正常运行和寿命的延长。
3. 记录维护:对模具的使用情况进行记录,包括使用次数、维修情况等,以便及时调整维修周期和保养计划。
注塑模具设计与制造教程

03
注塑模具结构设计
分型面设计技巧及注意事项
分型面选择原则
确保产品顺利脱模,减少溢料和 飞边,简化模具结构。
分型面设计要点
分型面应位于产品断面轮廓最大 的地方,便于脱模;避免在分型 面上设计小孔或凹槽,防止溢料 和飞边;分型面的设计应便于模
具的加工和装配。
注意事项
分型面的选择应避免影响产品的 外观和性能;对于复杂的产品, 可能需要采用多个分型面进行脱
性能要求
模具材料应具有良好的切削加工性、热处理稳定 性、耐磨性、耐腐蚀性和抗疲劳性等性能。
精度与表面质量要求
精度要求
根据产品精度要求,确定模具的制造 精度和装配精度,保证产品的尺寸精 度和形位公差。
表面质量要求
模具表面应平整、光滑,无裂纹、毛 刺等缺陷;分型面、型腔等重要表面 应达到一定的粗糙度要求,以保证产 品的外观质量和脱模顺畅。
分类
根据模具的结构和使用特点,注塑模具可分为单分型面 注塑模、双分型面注塑模、带有侧向分型与抽芯机构的 注塑模以及热流道注塑模等。
注塑模具结构组成
导向部件
浇注系统
由主流道、分流道、浇口和冷料 穴等组成,用于将熔融的塑料从 注塑机喷嘴引入模具型腔。
包括导柱、导套等,用于保证动 模和定模在合模时的相对位置精 度。
压力调整技巧及常见问题解决方案
压力调整技巧
注射压力、保压压力和背压是注塑成型过程中的关键压力参数。 根据产品的结构、壁厚和塑料的流动性,合理调整这些压力参 数,以确保塑料充分填充模具并补偿收缩。
常见问题解决方案
针对飞边、短射、缩水等常见问题,通过调整注射速度、保压 时间和压力分布等参数,可以有效改善产品质量。
加工工艺流程梳理与规范操作指南
注塑模具设计

这一原则很重要,修改塑件产品图时,必须根据图 纸尺寸公差要求,修改为中间尺寸。尺寸及公差的几种 情况如表2-2所示。 表2-2 尺寸及公差的几种情况
2.2 侧抽芯机构
塑件的侧面常带有孔或凹槽,如图2-9所示。 在这种情况下,必须采用侧向成型芯才能满足塑 件成型上的要求。但是,这种成型芯必须制成活 动件,能在塑件脱模前将其抽出。完成这种活动 成型芯的抽出和复位机构叫抽芯机构。
图2-23 锁紧楔的形式
图2-24 锁紧楔的角度
6) 抽芯时的干涉现象 斜导柱在定模、滑块在动模的该结构形式设计时应注意, 滑块与推杆在合模复位过程中不能发生“干涉”现象,所谓 干涉现象是指滑块的复位先于推杆的复位致使活动型芯与推 杆相碰撞,造成活动型芯或推杆损坏,如图2-25所示。为了 避免上述干涉现象发生,在塑件结构允许的情况下,尽量避 免将推杆设计在活动型芯的水平投影面相重合处,否则,必 须满足条件,如图2-26所示,才能避免干涉现象。
④ 直导套常应用于简单模具或模板较薄的模具;I型带头导 套主要应用于复杂模具或大、中型模具的动定模导向中;II 型带头导套主要用于推出机构的导向中。为有利于减小摩擦, 在导套上也可开设储油槽,或采用自润滑型导套(在钢质导 套的环形槽内设 MoS2、在高强黄铜导套的侧壁孔内设固体 石墨)。 ⑤ 为了确保合模后分型面良好贴合,导柱与导套在分型面处 应设置承屑槽:一般都是削去一个面,或在导套的孔口倒角, 如图2-28所示。 ⑥ 导柱工作部分的长度应比型芯端面高出6-8mm ,如图229所示。
4、斜导柱倾斜角a 倾斜角的大小关系到斜导柱所承受的弯曲 力和实际达到的抽拨力,也关系到斜导柱的工 作长度、抽芯距和开模行程。为保证一定的抽 拔力及斜导柱的强度,取a小于25°,一般在 12°~25°范围内选取。 5、斜导柱直径 根据材料力学可以推导出斜导柱直径计算 公式:
- 1、下载文档前请自行甄别文档内容的完整性,平台不提供额外的编辑、内容补充、找答案等附加服务。
- 2、"仅部分预览"的文档,不可在线预览部分如存在完整性等问题,可反馈申请退款(可完整预览的文档不适用该条件!)。
- 3、如文档侵犯您的权益,请联系客服反馈,我们会尽快为您处理(人工客服工作时间:9:00-18:30)。
课程设计:注塑模具设计设计零件:带螺纹圆桶
设计人:蒙帮爱(254)组员:符祥龙(245)
梁超(250)
1.零件材料以及特点
电绝缘性(尤其高频绝缘性)优良,无色透明,透光率仅次于有机玻璃,着色性耐水性,化学稳定性良好,强度一般,但质脆,易产生应力脆裂,不耐苯.汽油等有机溶剂.适于制作绝缘透明件.装饰件及化学仪器.光学仪器等零件.
成型性能
1.无定形料,吸湿小,不须充分干燥,不易分解,但热膨胀系数大,易产生内
应力.流动性较好,可用螺杆或柱塞式注射机成型.
2.宜用高料温,高模温,低注射压力,延长注射时间有利于降低内应力,防止
缩孔.变形.
3.可用各种形式浇口,浇口与塑件圆弧连接,以免去处浇口时损坏塑件.脱
模斜度大,顶出均匀.塑件壁厚均匀,最好不带镶件,如有镶件应预热。
其密度为1.05g/cm3,伸长长度:3–4%,成型收缩率:0.6-0.8% ,成型温度:170-250℃。
2.零件要求和零件图
要求:塑料制品内壁有凸槽以及外形要求美观,不得有痕迹。
内径为114mm,外径为120mm,长度为130mm,厚度2mm
零件图:proe三维图
3.拟定模具结构
(1)模具结构形式确定
该模型为一模一腔,内斜滑块分型抽芯脱模,产品光滑,深度大,由于带有螺纹,因此使用嵌件制造出外螺纹。
(2)注射机型号
注射量的计算
塑件体积:V=18.2cm3
塑件质量:m=ρV=18.2x1.05=11.41g
浇注系统初步估计
V总=V(1+0.3)=23.66cm3
注射机选择
V注射机=V/0.8=29.58cm3
xs-z30/25
(3)注射机相关参数校核
压力校核
聚苯乙烯的注射压力应视制品的特点、原料情况、模具以及设备条
件等情况综合考虑选择的,大致可在60 ~150MPa 较宽的范围
内选取,大浇口、厚壁制品可低些(约60 ~80M Pa),而薄壁
长流程复杂制品或大面积小浇口制品压力则要求大些(约120M
Pa 以上)。
另外,柱塞式注塑机由于注射压力损失较大,故压力
要求比螺杆式注塑机大得多。
因此,通过综合考虑取p=70MPa,
注射机安全系数k=1.25~1.4,取1.4.
KP=1.4x70=98<116MPa,则该注射机压力满足
锁模力校核
投影面积:A=11304mm2
由于浇注面积不算因此,模具型腔内熔料压力:
F涨=AP模=11304x30=339.12kN(其中,P模取注射压力的
0.2~0.4,即为23.6~47.2MPa)
此外锁模力为F锁模=250kn,安全系数为1.1~1.2,这里取k2=1.2。
则k2F涨=1.2x339.12=406.9>250,因此初定方案不符合。
则另选注射机参数
xs-zy1000/450
由KP=98<120MPa则为合格。
k2F涨=1.2x339.12<4500完全符合
(4)浇注系统设计
由于成型塑件便面要求没有痕迹,采用点浇口进行浇注,使得成型
后脱模容易,以及质量好,下端直径0.4mm,上端为1.2mm,结构
如图所示:
4.模架选取
根据塑件的外形,浇注系统结构,弯销等,根据参考,初步选定DCI5050即500mm×500mm
1.各模板尺寸
(1)定模板
定模板要开腔装入整体嵌入型腔,加上定模板上还要开设有冷却系统,
加之零件体积大小限定,保证一定刚度,选择80mm。
(2)滑块厚度
由塑件外形,要设立两侧分型有滑块作用,保证定位、精度以及刚度,
还要确保分型是滑块稳定,则取30mm厚度
(3)型芯固定板
在此模具中加入型芯固定板,主要起到固定和确保一定刚度,可取其
厚度为30mm
(4)动模板尺寸
动模板的选取主要是其受到注射时候承受的压力而定,在注射塑件时
为了能够承受压力,此外在模具中还承担着导向作用,厚度相对要大
些,取90mm。
(5)模脚尺寸
模脚高度=顶出行程+推板厚度+顶出固定板厚度+5=235mm
由上述综合考虑,初步定出模具高度为550mm,也就是550mm×500mm×525mm。
2.模架校核
1)模具平面尺寸
550mmX500mm<650mmX550mm,得出其合格。
2)模具高度尺寸
300mm<525mm<700mm,校验合格。
3.模具的开模行程
180+130*2+10=450mm<700mm,校验合格。
5.冷却系统设计
为满足塑件需要,在型芯内部装有水套,水通过水套循环进行冷却。
水套和连接杆通过套筒进行配合,水套和套筒过盈配合,而套筒和连接杆则是间隙配合,保证了行程,也保证了工作时精确度,冷却系统结构上满足冷却均匀,水循环呈螺旋流通。
成型温度:170-250℃,则初定成型温度为180℃,冷却温度用水。
如图所示,水套和型芯之间半圆孔就是螺旋形冷却通道。
6. 型芯设计
型芯为圆柱形状,内部有水套以及通过的连接柱,上端为推块并与型芯端面光滑平整,保证塑件成型与精度。
斜度取值8。
,抽芯距为4mm ,则侧型芯顶出距离为28.46mm 。
7. 一些标准件选取
浇口套:基本尺寸25,极限偏差+0.015
+0.002,头部外径30,内径3.2,浇口球面半径19,总长50. 限位钉:选择以下两种
圆柱销:选用长度为25,30,35,50几种规格
圆柱头推杆:两种尺寸
8.总装图
见总装配图
前者主视图,后者俯视图:
模具结构说明(主视图)
1.动模座板
2.卡圈
3.推板
4.动模板
5.型芯固定板
6.滑块
7.弯销
8.型芯
9.水套 10.连接杆 11.衬套 12.定模镶块 13.定模固定板 14推块。