圆锥滚子轴承酸洗规程
滚动轴承清洗工艺守则

滚动轴承清洗工艺守则1 适用范围本守则适用于小三相异步电动机及其派生系列电动机用深沟球轴承及短圆滚子轴承(简称普通轴承)的清洗。
2 材料2.1 3#锭子油或20#机油2.2 汽油2.3 00#砂布2.4 白布3 设备及工具3.1 轴承加热油箱3.2 温度计0~200℃3.3 铁丝网3.4 清洗盆3.5 盛放轴承塑料箱4 工艺准备4.1 将3#锭子油倒入油箱中、加热并控制在100~120℃。
4.2 将汽油倒入两个清洗盆中。
5 工艺过程5.1 去除轴承包封用防锈剂,并用目测方法检查轴承内、外圈,保持架及钢球和圆柱的表面有无锈蚀、划痕、烧伤、裂纹等现象,合格方可进行清洗。
5.2 将已去掉外包装的轴承(油质防锈脂)置于3号锭子油中加热约10~15min,待附在轴承上的防锈脂全部溶去后取出。
5.3 将去除防锈剂的轴承置于盛有汽油的清洁盆中清洗,清洗时可使轴承在盆中来回搅动数次。
5.4 再将轴承置于另一只盛有汽油的清洁盆中,用手握住内圈转动外圈,在转动过程中清洗。
5.5 将已经清洗过的轴承置于干净的铁丝网上凉干。
5.6 将已凉干的轴承放入清洁的塑料箱中,用盖盖好,并放在干净的地方。
6 质量检查6.1 清洗后的轴承用手握持轴承内圈,转动外圈,观察其旋转的稳定性及灵活性。
6.2 轴承有轻微锈斑时允许用00#砂纸擦去,并再清洗一次。
7 注意事项7.1 清洗好的轴承不准用棉纱擦拭,以免纤维进入轴承,必要时用白布擦拭。
7.2 一次与二次的清洁盆不得混淆使用。
7.3 清洁干净的轴承不得直接用手或赃物接触,必须戴上干净手套拿放。
7.4 严禁火种,注意安全。
酸洗磷化操作规程

酸洗磷化操作规程
酸洗、磷化、皂化操作规程
工艺:开包整理——酸洗——高压水冲洗——磷化——水清洗——皂化——干燥——吊运堆放
1 .酸洗前的准备:根据生产单,检验原料的批号或炉号、规格和表面质量等,如有异常情况,即通知生产部负责人。
2 .剪断打包带,Ф 10 及以下的 2 吨以上线材必须一开为二,绑上绑腰线。
3 .酸洗:室温下,盐酸池中浸泡约 15 分钟左右,一般先浸低浓度酸,后浸
高浓度酸,粗细钢丝要分别对待,做到无氧化铁皮。
4 .高压水冲洗:尽量冲洗干净钢丝上的附着物,再浸入清水池。
5 .磷化:磷化温度: 7 5 ~ 80 ℃。
磷化时间: 5 ~1 0 分钟(不同材料时间
不同)。
磷化后钢丝表面的颜色为灰色或暗灰色,磷化膜应是牢固、细密。
6 .水清洗:高压水冲洗(特别是下面磷化渣一定要冲掉)再进入清水池,水池的水要保持中偏碱性。
7 .皂化:皂化温度 7 0 ~8 0 ℃,皂化时间:2 ~5 分钟。
皂化后钢丝的表面
为一层乳白色的膜层。
8 .皂化后钢丝要放在吹风机前吹干(特别是Ф 10 及以下的线材),然后分牌号和规格定点堆放或吊运到指定地点。
9 .随时注意调整三池液面的高低,浓度变低时要加料或更换盐酸。
10 .定期打捞磷化池中的沉淀,一般在早晨上班即进行打捞。
关于轴承酸洗的目的、烧伤产生原因和检测方法

关于轴承酸洗的目的、烧伤产生原因、酸洗槽配比成份和检测方法酸洗主要是检测轴承内外圈在磨削时有无烧伤和裂纹,因烧伤是一种热损伤,它使工件表面在高温下产生氧化形成极薄的氧化层,降低了表面硬度,严重的烧伤还会产生龟裂(即与磨削方向垂直的微细裂纹),所以检测烧伤是磨加工的关键检查项目,决不可缺失。
一般磨削烧伤与采用的磨削速比不当、砂轮过硬,使砂轮磨削表面堵塞,冷却润滑不良、砂轮修正不当有关。
GCr15 /440C 酸洗的工艺路线如下:脱脂槽→流动冷水槽→酸洗槽→流动冷水槽→第一明化槽→流动冷水槽→第二明化槽→流动冷水槽→中和槽→流动冷水槽→防锈槽。
1.脱脂槽体积为 0.6×0.6×0.45=0.162m3用料:体积按0.14m3计算(需加热至75℃~85℃)无水碳酸钠 Na2C03 0.14×1.5%=2.1kg磷酸三钠 Na3P04 0.14×1.5%=2.1kg氢氧化钠 NaOH 0.14×10%=1.4kg2.酸洗槽体积为 0.57×0.39×0.35=0.078m3 用料HNO3(硝酸)(室温)溶液体积按0.57×0.39×0.3=0.067m3 0.067×4%=2.68L=3.752kg3.第一明化槽体积为0.57×0.39×0.35=0.078m3(室温)溶液体积按0.57×0.39×0.3=0.067m3 计算:高锰酸钾 KMnO4 0.067×3.5%=2.345kg磷酸三钠 Na3P04 0.067×6.5%=4.355kg氢氧化钠 NaOH 0.067×3.5%=2.345kg4.第二明化槽体积为0.57×0.39×0.35=0.078m3(室温)溶液体积按0.57×0.39×0.3=0.067m3 计算:盐酸 HCL 0.067×12.5%=8.375L=9.88kg二氯化锡SnCl2·2H2O0.067×0.35%=0.2345kg金属颗粒 Sn 0.067×0.1%=0.067kg5.中和槽体积为 0.6×0.6×0.6=0.216m3(室温)溶液体积按 0.6×0.6×0.5=0.18m3无水碳酸钠 Na2C03 0.18×3%=5.4kg6.防锈槽体积同中和槽亚硝酸钠 NaNO2: 0.18×7%=12.6kg无水碳酸钠 Na2C03 0.18×0.4%=0.72kg以上材料可编入轴承零件酸洗规程内,酸洗槽材料陶瓷缸或搪瓷缸,下面有出水口,可按上述尺寸制作,磨削工件时一般每两小时抽查一次,如发现不合格,加大抽查的频率,酸洗后,工件表面呈灰白色,如果在沟道内有轻微烧伤,是呈断续黑色条纹,严重时,呈片状,团状黑斑,按P4级要求,轴承工作表面不允许有烧伤痕迹。
轴承零件冷酸洗检查工艺规程讲解

轴承零件冷酸洗检查工艺规程1.范围本规程适用于ZGCr15.Cr4Mo4V.8CrMo4V.S8Cr4Mo4V.M50钢制轴承零件磨削烧伤的酸洗检查。
本规程规定了采用冷酸洗法检查高温钢制轴承零件烧伤的工艺.各槽溶液成分及配比.操作规程.检查标准与方法等方面的内容。
2. 规范性引用文件下列文件中的条款通过本标准的引用而成为标准的条款,凡是注日期的文件其随后所有的修改单或修订版均不适用于本标准。
凡是不注日期的引用文件其最新版本适用于本标准。
GB/T 639 化学试剂无水碳酸钠GB/T 629 化学试剂氢氧化钠GB/T 626 化学试剂硝酸GB/T 622 化学试剂盐酸GB/T 633 化学试剂亚硝酸钠HC/T 2517 工业磷酸三钠3.人员要求3.1酸洗检查人员应参加公司级(或以上0)组织的学习成绩培训。
并取得相应的上岗证或资格证。
相应证书到期后,酸洗检查人员必须重新进行考核或能力审查,以重新取得相应证书。
3.2酸洗检查人员应具备酸洗溶液的配制.补充和调整,零件目视检查,进行相关测试以及记录工作结果的知识技能。
3.3酸洗检查人员完全熟悉所使用的酸洗检查规程,能够根据工艺规程编写工艺卡。
3.4酸洗检查人员熟悉并能正确执行安全防护规则。
3.5酸洗检查人员在酸洗检查时,严格执行工艺要求,并仔细填写相关记录。
4.设备及校准要求4.1 水槽.中和槽.脱脂槽.防锈槽:材质可用中碳钢或玻璃钢制成,除了流动冷水槽外其余各槽都要求有带把手的盖,盖的材质应与各槽的材质一致。
4.2 酸洗槽.盐酸清洗/明化槽:材质可用玻璃钢.不锈钢.陶瓷材料制成,要求有带把手的盖,盖的材料应与各槽的材质一致。
4.3 钩子.筐:材质用不锈钢制成,筐容积根据实际情况决定,筐以不漏出产品为准孔越大越好。
4.4量杯或量筒.台秤:量杯或量筒可用玻璃或塑料材质制成,含有1000ml的制度;台秤精度为g。
量筒.量杯和台秤均需要定期检定并有证书。
4.5 可显示秒的计时器或电钟:根据实际情况自选。
冷酸洗检验规程
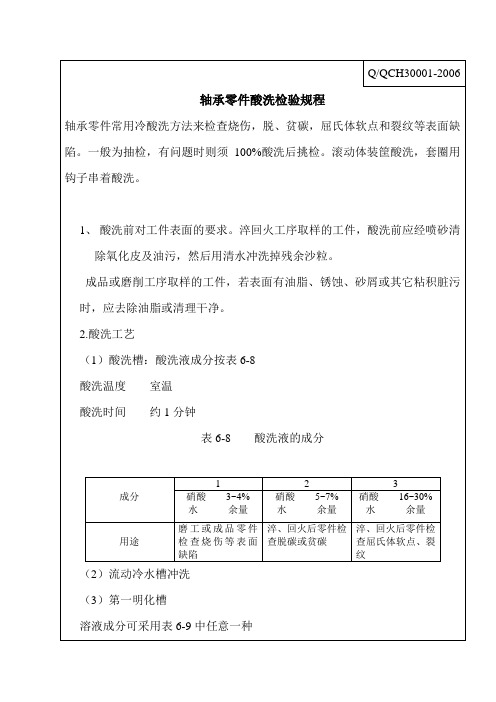
(2)流动冷水槽冲洗
(3)第一明化槽
溶液成分可采用表6-9中任意一种
表6-9第一明化槽溶液成分
名称
1
2
3
铬酐
8~15%
_
_
磷酸(H3PO4)
_
_
10~15%
氢氧化钠(NaOH)
_
3~5%
_
高锰酸钾(KMnO4)
_
3~5%
3~5%
磷酸三钠(Na3PO4)
_
6~9%
_
硫酸(H2SO4)
Q/QCH30001-2006
轴承零件酸洗检验规程
轴承零件常用冷酸洗方法来检查烧伤,脱、贫碳,屈氏体软点和裂纹等表面缺陷。一般为抽检,有问题时则须100%酸洗后挑检。滚动体装筐酸洗,套圈用钩子串着酸洗。
1、酸洗前对工件表面的要求。淬回火工序取样的工件,酸洗前应经喷砂清除氧化皮及油污,然后用清水冲洗掉残余沙粒。
0.3~0.4
_
_
水
余量
余量
余量
温度室温
时间10~20秒
(4)流动冷水槽冲洗
(5)第二明化槽
溶液成分盐酸(比重1.19)10~15%
二氯化锡0.2%
金属锡每槽(约100kg)加100g
水余量
温度室温
时间1~2min
(6)流动冷水槽冲洗
(7)中和槽
溶液成分碳酸钠4~6%
水余量
温度室温
时间约1分钟
(8)流动冷水槽冲洗
成品或磨削工序取样的工件,若表面有油脂、锈蚀、砂屑或其它粘积脏污时,应去除油脂或清理干净。
2.酸洗工艺
(1)酸洗槽:酸洗液成分按表6-8
酸洗温度室温
轴承零件磨削酸洗工艺规程
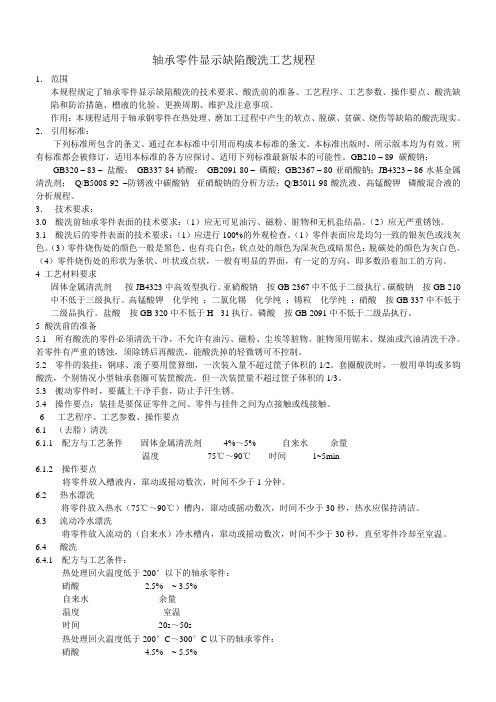
轴承零件显示缺陷酸洗工艺规程1.范围本规程规定了轴承零件显示缺陷酸洗的技术要求、酸洗前的准备、工艺程序、工艺参数、操作要点、酸洗缺陷和防治措施、槽液的化验、更换周期、维护及注意事项。
作用:本规程适用于轴承钢零件在热处理、磨加工过程中产生的软点、脱碳、贫碳、烧伤等缺陷的酸洗现实。
2.引用标准:下列标准所包含的条文、通过在本标准中引用而构成本标准的条文。
本标准出版时,所示版本均为有效。
所有标准都会被修订,适用本标准的各方应探讨、适用下列标准最新版本的可能性。
GB210 – 89 -碳酸钠;GB320 – 83 –盐酸;GB337-84-硝酸;GB2091-80 –磷酸;GB2367 – 80-亚硝酸钠;JB4323 – 86-水基金属清洗剂;Q/B5008-92 –防锈液中碳酸钠- 亚硝酸钠的分析方法;Q/B5011-98-酸洗液、高锰酸钾- 磷酸混合液的分析规程。
3.技术要求:3.0 酸洗前轴承零件表面的技术要求:(1)应无可见油污、磁粉、脏物和无机盐结晶。
(2)应无严重锈蚀。
3.1 酸洗后的零件表面的技术要求:(1)应进行100%的外观检查。
(1)零件表面应是均匀一致的银灰色或浅灰色。
(3)零件烧伤处的颜色一般是黑色、也有亮白色;软点处的颜色为深灰色或暗黑色:脱碳处的颜色为灰白色。
(4)零件烧伤处的形状为条状、叶状或点状,一般有明显的界面,有一定的方向,即多数沿着加工的方向。
4 工艺材料要求固体金属清洗剂按JB4323中高效型执行。
亚硝酸钠按GB 2367中不低于二级执行。
碳酸钠按GB 210中不低于三级执行。
高锰酸钾化学纯;二氯化锡化学纯;锡粒化学纯:硝酸按GB 337中不低于二级品执行。
盐酸按GB 320中不低于H - 31执行。
磷酸按GB 2091中不低于二级品执行。
5 酸洗前的准备5.1 所有酸洗的零件必须清洗干净,不允许有油污、磁粉、尘埃等脏物。
脏物须用锯末、煤油或汽油清洗干净。
若零件有严重的锈蚀,须除锈后再酸洗,能酸洗掉的轻微锈可不控制。
圆锥滚子轴承检验规范

圆锥滚子轴承检验规范 Q/QCHJ30003—20101.本规范规定了圆锥滚子轴承的技术要求及检验规范,适用于本公司成品圆锥滚子轴承的生产检验和外购圆锥滚子轴承的进货检验.2.引用文件GB/T307.1-2005 滚动轴承 向心轴承 公差GB/T307.2-2005 滚动轴承 测量和检验的原则和方法GB/T307.3-2005 滚动轴承 通用技术规则JB/T8921-1999 滚动轴承及其商品零件检验规则JB/T1255-2001 高碳鉻轴承钢滚动轴承零件热处理技术条件3.检验规则3.1公司生产的圆锥滚子轴承成品和外购的圆锥滚子轴承成品按上述标准生产和检查。
按下列要求进行验收。
3.1.1圆锥滚子轴承检查项目及特性分类按表 1下技术要求。
3.2.1 轴承套圈及滚动体热处理标准按JB/T1255-2001 高碳鉻轴承钢滚动轴承零件热处理技术条件执行,同一零件的硬度均匀性应在1HRC以内。
第 2 页 共 4 页3.2.2 套圈在终检前应进行退磁,残磁强度不得超过表3的规定3.2.4.1产品的标识按公司《印字标识规范》执行;用户有要求的按用户要求执行。
3.2.4.2清洗涂油防锈包装按公司《成品轴承清洗涂油包装工艺规程》执行。
用户有要求的按用户要求执行,出厂前检查出的不合格应予更换或重新包装。
3.2.5零件外观要求轴承零件表面不允许有裂纹,锐边,毛刺和锈蚀;不允许有磨伤,划伤,麻点,碰卡伤,棱子等机械损伤。
不允许有氧化皮,黑皮;倒角要亮化处理,不得有阴阳脸,色泽不均匀现象或热处理油污或污渍;零件配合表面不允许有打磨痕迹。
滚道不允许有上道工序加工痕迹,超精加工应纹路均匀一致,不允许有擦伤,碰卡伤,支承印;亮带,砂轮花等。
大、小油沟应深浅均匀一致,位置准确没有偏位现象。
3.2.6轴承装配质量轴承零件配套装配后,应旋转灵活平稳,无阻滞,干涉或异常窜动现象。
保持架不允许有压合伤,变形,错位现象。
不允许有明细错位。
轴承酸洗工艺流程
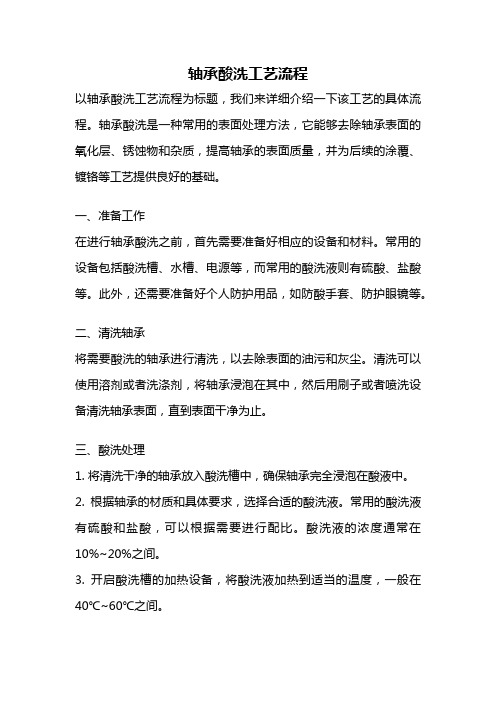
轴承酸洗工艺流程以轴承酸洗工艺流程为标题,我们来详细介绍一下该工艺的具体流程。
轴承酸洗是一种常用的表面处理方法,它能够去除轴承表面的氧化层、锈蚀物和杂质,提高轴承的表面质量,并为后续的涂覆、镀铬等工艺提供良好的基础。
一、准备工作在进行轴承酸洗之前,首先需要准备好相应的设备和材料。
常用的设备包括酸洗槽、水槽、电源等,而常用的酸洗液则有硫酸、盐酸等。
此外,还需要准备好个人防护用品,如防酸手套、防护眼镜等。
二、清洗轴承将需要酸洗的轴承进行清洗,以去除表面的油污和灰尘。
清洗可以使用溶剂或者洗涤剂,将轴承浸泡在其中,然后用刷子或者喷洗设备清洗轴承表面,直到表面干净为止。
三、酸洗处理1. 将清洗干净的轴承放入酸洗槽中,确保轴承完全浸泡在酸液中。
2. 根据轴承的材质和具体要求,选择合适的酸洗液。
常用的酸洗液有硫酸和盐酸,可以根据需要进行配比。
酸洗液的浓度通常在10%~20%之间。
3. 开启酸洗槽的加热设备,将酸洗液加热到适当的温度,一般在40℃~60℃之间。
4. 轴承在酸洗槽中浸泡一段时间,通常为10分钟左右。
酸洗时间的长短可以根据轴承的具体情况和要求进行调整。
5. 酸洗过程中,可以通过搅拌或者气泡冲洗等方式增加酸洗液与轴承表面的接触,提高清洗效果。
6. 酸洗结束后,将轴承取出,并用清水彻底冲洗干净,以去除酸洗液的残留。
7. 最后,将轴承进行干燥处理,可以使用烘箱或者自然风干的方式。
四、检验质量经过酸洗处理的轴承,表面应该干净、光滑,没有氧化层、锈蚀物和杂质的存在。
可以使用目视检查和触摸检查的方式进行质量检验。
此外,还可以使用显微镜等设备进行更加精细的检查。
以上就是轴承酸洗工艺流程的详细介绍。
通过酸洗处理,可以有效提高轴承的表面质量,为后续的涂覆、镀铬等工艺提供良好的基础。
在使用酸洗液和处理过程中,需要注意安全问题,做好个人防护措施,避免酸洗液对人体和环境造成伤害。
同时,也需要根据具体情况和要求,合理选择酸洗液的成分和工艺参数,以达到最佳的酸洗效果。
- 1、下载文档前请自行甄别文档内容的完整性,平台不提供额外的编辑、内容补充、找答案等附加服务。
- 2、"仅部分预览"的文档,不可在线预览部分如存在完整性等问题,可反馈申请退款(可完整预览的文档不适用该条件!)。
- 3、如文档侵犯您的权益,请联系客服反馈,我们会尽快为您处理(人工客服工作时间:9:00-18:30)。
时间(不断抖动,表面显示灰色)1分钟左右
6、清洗:
4号槽流动冷水冲洗,浸渍5-6此,时间1分钟左右。
7、补充明化处理:
补充明化槽成份:
盐酸(HC1比重1.19)10-15%
梁山滚动轴承有限
责任公司
轴承零件烧伤酸洗检查工艺
编号
代替
共5页
第2页
金属锡(Sn)1%
水余量
温度室温
时间(不断抖动,表面显示灰白色)1分钟左右
梁山滚动轴承有限责任公司
轴承零件烧伤酸洗
检查工艺
编制:审核:批准:
二0一一年一月十日
梁山滚动轴承有限
责任公司
轴承零件烧伤酸洗检查工艺
编号
代替
共5页
第4页
六、酸洗液配制及维护:
槽中溶液浓度经分析结果在下列含量范围内为合格
槽号
工序名称
成份名称
含量上限(%)
含量下限(%)
2
酸洗
硝酸(HNO3比重1.43)
梁山滚动轴承有限
责任公司
轴承零件烧伤酸洗检查工艺
编号
代替
共5页
第1页
一、对轴承零件酸洗前的表面要求:
1、热处理后的零件应清除掉氧化皮,结晶盐及油污才能酸洗。
2、凡经过探伤的产品,须将铁粉擦干净后才能酸洗。
3、用防锈油处理过的零件,须吧防锈油清晰干净后才能酸洗
4、有锈产品必须吧锈除干净后才能进行酸洗。
4、零件浸入槽内,操作完毕应立即取出,以防金属溶液解在酸中,削弱酸的作用及弄脏溶液。
5、酸槽要用陶瓷缸或其他耐酸碱的容器。
6、各槽溶液应定期化验,根据化验结果确定调整和更换。
7、必须严格按照控制酸洗温度和时间,随时调节,遵守酸洗工作制度。
8、零件经酸洗后,应立即搬出酸洗室,以免生锈。
9、浓酸、乙醇、汽油等有机物质不可存放在酸洗工作场所,以免发生事故。
10、使用后的废酸未径中和处理不可随意排入下水道,防止环境污染。
8、清洗:
在5号槽中用流动冷水冲洗5-6次,时间1分钟左右。
9、防锈处理:
6号槽溶液成份:
亚硝酸钠(NaNO2)10-15%
水余量
温度室温
时间1分钟
三、注意事项:
1、零件在酸洗、清洗、明化、中和、防锈等槽中都应上下窜动。
2、酸洗槽中硝酸的浓度可以根据零件酸洗后表面黑暗程度及尺寸消耗进行适当调整
3、零件径酸洗后,须立即进行检查,
二、酸洗过程及各槽酸洗液成份:
1、准备工作
把套圈挂入钩上,悬挂数量根据套圈大小而定,保证酸洗时不使零件靠的太近,以保证溶液能浸湿所有表面,滚子则采用带孔小筐,孔的大小根据滚子大小而定,在不使滚子漏出的前提下,越大越好,装的数量不能太多,应恩那个保证酸洗时抖动开,以使溶液很好的浸湿所有表2、减低酸的浓度
梁山滚动轴承有限
责任公司
轴承零件烧伤酸洗检查工艺
编号
代替
共5页
第3页
序号
常见毛病
产生原因
消除方法
3
表面酸洗不够(表面颜色黑暗程度不够)
1、酸的浓度过低
2、酸洗时间过短
1、检查校正酸的浓度。
2、延长酸洗时间
3、重新酸洗。
4
表面酸洗不够(尺寸消耗不均匀或有未酸洗到的痕迹)
6
防锈液
每周分析一次,根据分析结果进行调整更换
梁山滚动轴承有限
责任公司
轴承零件烧伤酸洗检查工艺
编号
代替
共5页
第5页
七、操作注意事项:
1、酸洗、明化和碱液槽配制时须戴上橡胶手套和穿工作服,要注意安全,不要径溶液飞溅道皮肤和衣物上。
2、配酸液时要径酸加在水里,不能将水加在酸里,以防放热剧烈造成溅伤。
3、酸洗室内须安装通风设备,防止有毒气体中毒
四、轴承零件酸洗后的表面质量检查:
酸洗零件表面应当湿润,并在日光灯下用肉眼观察,正常的酸洗表面呈暗灰色。
表面缺陷特征:
1、软点:呈云彩状暗黑色,边界不规则的斑点。
2、脱碳:一般脱碳表面呈灰白色,表面纯铁体脱碳呈亮白色。
3、裂纹:淬火裂纹很细,线条状黑色或中间一条黑色条纹。
4、烧伤:呈现出沿砂轮加工方向的暗黑色斑块、线条、或断续线条。
将准备好的零件浸入1号槽的溶液中,进行脱脂处理。
1号槽溶液成份:
清水
在流动冷水中清晰1分左右。
3、酸洗:
2号槽溶液成份:
硝酸用于显示脱碳软点为10-15%
用于显示表面烧伤为3-4%
水余量
温度室温
时间1分钟
4、流动冷水槽:
用流动冷水冲洗5-6次,时间1分钟左右
5、明化处理:
铬酐(CrO3)8-15%
水余量
1、明化槽成分变质
2、明化市静安不够
3、零件在硝酸中酸洗过强
4、明化后清洗不干净
1、检查校正明化槽溶液成份,不合格的要立即更换
2、遵守明化时间
3、缩短硝酸浸渍市静安
4、冷水槽应流动保持干净
7
酸洗后表面出现锈蚀
1、在水中去酸不够
2、中和不好
3、防锈不好
1、更换清洗槽
2、检查校正中和液
3、检查前后进行调整防锈液成份
合格的零件经检查后,最多不得超过2个小时,应进行清洗和防锈,不合格的应立即送车间返工。
五、酸洗常见毛病及消除方法:
序号
常见毛病
产生原因
消除方法
1
表面出现斑点
(花脸)
1、表面去脂不良
2、1号清水槽水脏
1、延长浸渍时间
2、更换1号槽水
3、将零件重新去脂清洗
2
2
两件表面酸洗过度(尺寸消耗超过公差)
1、酸洗时间过长
1、表面去脂不良。
2、酸洗时零件重叠在一起。
3、表面有气泡,表面未被溶液浸上。
1、检查脱脂槽的浓度。
2、抖动使零件表面不要贴紧
3、使零件间接处的空气排除。
5
表面出现黑黄色雪花状斑点
零件上沾有亚硝酸钠酸洗前没有清洗干净
径粘附在表面的亚硝酸钠结晶消除干净再进行酸洗
6
表面明化不够(酸洗后表面暗黑色或粘附一层暗黑色或黄色物质)
4
3
3
明化(1)
铬酸(Cr2O3)
15
8
4
明化(2)
盐酸(HC1比重1.19)
10
5
5
防锈
亚硝酸钠
15
10
溶液分析与更换周期
槽号
溶液名称
分析与更换周期
1
清水
每周分析一次,根据脏污程度更换
2
硝酸溶液
,每周分析一次,根据零件颜色分析更换
3
铬酐溶液
每周分析一次根据溶液作用能力与分析结果更换
4
盐酸溶液
每周分析一次,根据溶液作用能力与分析结果更换