铝合金熔铸能量平衡计算模型
铝合金熔铸过程的数值模拟研究

铝合金熔铸过程的数值模拟研究铝合金是目前汽车、飞机等重工业领域所广泛应用的材料之一。
在其应用中,铝合金的加工成型是非常重要的一步。
而在铝合金的成型加工中,熔铸是不可缺少的一部分。
因此,对铝合金熔铸过程的研究,可以更深层次地了解铝合金在熔铸加工中的性质和规律。
这就需要借助数值模拟技术,对铝合金熔铸过程进行深入的研究。
一、铝合金熔铸工艺铝合金熔铸工艺主要分为铸造和浇注两种方式。
铸造方式主要采用铸造机进行铸造,通常包括压铸、重力铸造、低压铸造等方式。
而浇注方式则需要先将铝合金液态熔体倒入模具中,让其冷却硬化后得到所需制品。
通常情况下,铝合金液态熔体的温度控制在650℃左右。
熔铸后,所得制品需要进行退火处理,提高其机械性能和强度。
二、数值模拟在铝合金熔铸中的应用数值模拟技术可以在铝合金熔铸过程中提供精确的预测。
利用计算流体力学(CFD)方法,可以在铝合金熔铸工艺中分析金属流动、传热和固相变化等多个方面。
尤其是随着计算机技术的不断发展,基于有限元分析(FEA)和CFD分析的计算模型越来越准确,为工艺工程师提供了一个行之有效的工具,以评估铝合金熔铸过程的工艺参数、优化加工工艺并改进产品性能。
三、数值模拟方法数值模拟方法的有效利用需要充分考虑铝合金熔铸过程中的所有物理和化学变化因素。
基于CFD和FEA技术开发的模型通常包括金属的流动、传热和固相变化,而金属的材料特性则与其地理形态、温度历程及成分有关。
有些模型甚至可以考虑金属液态、气态和固态之间的相互作用。
基于计算机模拟的研究可以实现更准确、更先进的铝合金熔铸工艺,并发现、避免或消除可能出现的问题。
例如,通过分析不同浇注参数、铸模和分型材料的性能及影响,可以更好地了解向模具中注入液态铝合金的方法,并预测可能的缺陷和位置。
这种分析可以促进工艺优化,从而提高生产效率和制品质量。
四、数值模拟技术的优势数值模拟技术不仅可用于铝合金熔铸过程中的研究,还可用于铝合金的节能、成型、模具和处理过程等的研究。
铝熔炼炉热平衡测试及节能分析_李世轩
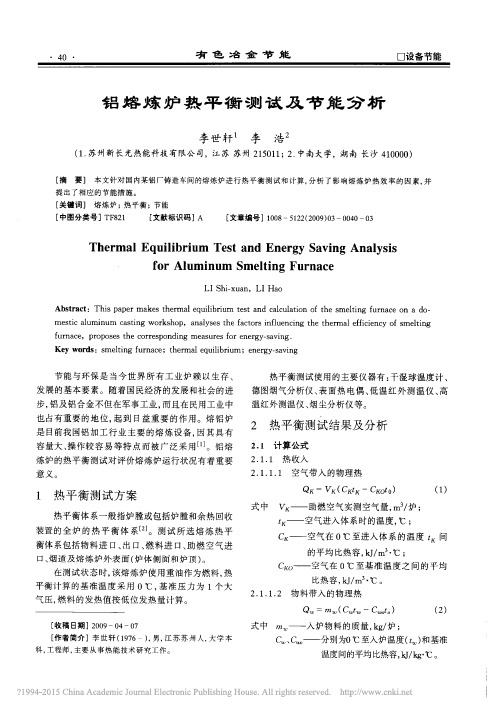
降低 熔 炼 炉 能 耗 的建 议
增 加空 气 带人 的热 空气 的 预 热 温 度 越 高 , 理 论 燃 烧 温 度 也 越 高 。进 入熔 炼 炉 的 空 气 的 温 度 升 高 , 需 要 的 燃 料 量 降低 , 炉子 的 效率 提高 。 在工业 中 , 空 气一 般是 利 用烟 气余 热 通 过 热 交 换 的 方 式 提 高进 炉 空 气 的 温 度。 增 加进 炉物 料 的温 度 加入 熔 炼 炉 的物 料 直 接 来 自电解 槽 的 电解 液 。 当加入 熔 炼炉 的 物 料 温 度 较 低 时 , 物 料 在熔 炼 炉 中 需要摄 入 燃 料燃 烧热 相 反 , 则需 要 的热量 较 小 。 故 在物 料在 加入 熔 炼炉 之前 , 应 保持 其 温度 , 保证 物 料
衬 · ℃
头— 热支出
液体燃料应用基低 位 发热量 ,
每小 时 内炉孔 敞开 时 间 ,
冷材 吸收 热量 冷 材 吸 收 的热 量 包括 冷 材 熔 化 吸 收 的热 量和
烟 气 带走 热量
矶
式中 , 、 , —
, 一 , ,。
℃至烟 气 温度 , 和
熔 化 的冷材 加热 到最 终温 度 吸收 的热量 。 冷 材熔 化 吸收 的热量 牙 乏 ` 了 , 式中 ` — 冷材 的量 , 炉 , — 冷 材 的熔 化热 , 。 冷 材加 热到 最终 温度 吸收 的热 量
分别 为 在
· ℃
基准 温 度 间 的 平 均 比热 容 ,
矶 —
烟气量 , 易 舀
, 炉。 窃一 伽 。
炉 式中
合 金产 品 带走 热量 式中 几— 出炉 铝合 金的质 量 ,
了
窃、 —
,
铝合金熔炼炉热平衡计算与分析

铝合金熔炼炉热平衡计算与分析李雨薇【摘要】对某铝业公司铝合金熔炼炉进行了热平衡测试与分析.结果表明,铝合金熔炼炉烟气带走的热量达56.41%、炉体散热损失达10.27%.提出可通过降低烟气带走的热量、优化配风比例及优化炉体外侧温度均匀性等措施来提高熔炼炉的热效率.【期刊名称】《有色冶金节能》【年(卷),期】2016(032)003【总页数】2页(P44-45)【关键词】铝合金熔炼炉;热平衡计算;节能分析【作者】李雨薇【作者单位】郴州丰越环保科技有限责任公司,湖南郴州423000【正文语种】中文【中图分类】TF061.2随着能源成本的增加、环境要求的逐渐提高,如何提高铝合金熔炼炉的热效率、降低其能耗[1-2],已经成为许多铝合金熔炼企业追求的目标之一。
为了更深入地了解铝合金熔炼炉各项热收入与支出情况,提高铝合金熔炼炉的热效率,降低系统能耗,对我国某铝业公司铝合金熔炼炉进行了热平衡测试与分析。
1.1 热平衡测试基准与条件(1)测试基准。
基准温度按0 ℃,基准压力按1个标准大气压,燃料发热值按低发热值计算。
(2)测试条件。
在设备操作相对稳定,无重大设备以及操作事故下进行。
连续测试三天,每天测试一炉,每炉测试两组数据。
1.2 测量方法此次热平衡计算以测试数据为主,同时结合中控室数据为辅。
若特殊工艺要求,无法获得测试数据时,采用中控室数据。
具体测试参考标准《热设备能量平衡通则》—GB/T2588—2000。
1.3 测试仪器本次热平衡测试所使用的仪器、仪表均在有效检定期内,其测试仪器仪表为毕托管、微压计;高、低温红外测温仪;熔体取样及分析仪器;德图烟气分析仪及配套设备;风速仪;水银温度计;表面热电偶及配套的数字显示表;铠装热电偶及配套的数字显示表。
2.1 测试项目与结果测试项目与结果如表1所示。
2.2 热平衡计算热平衡计算根据能量守恒定律,分别计算铝合金熔炼炉系统热收入与热支出,并计算热量的有效利用率和热量损失比例,以此计算结果作为判断熔炼炉系统热工状况是否正常的依据。
铝熔炼炉热平衡测试及节能分析_李世轩
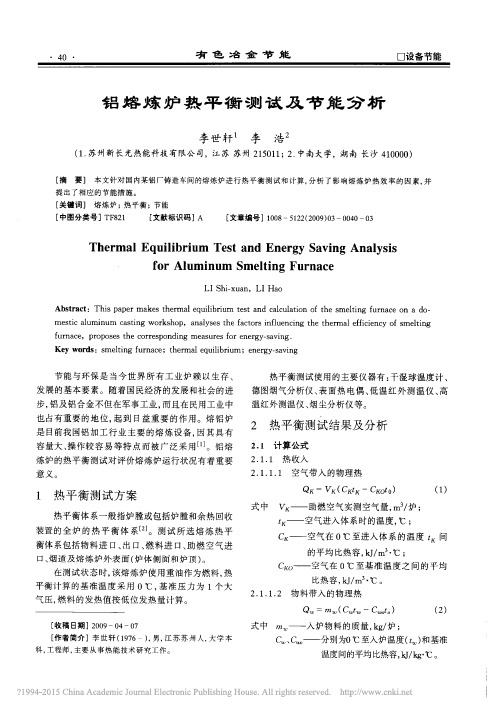
衬 · ℃
头— 热支出
液体燃料应用基低 位 发热量 ,
每小 时 内炉孔 敞开 时 间 ,
冷材 吸收 热量 冷 材 吸 收 的热 量 包括 冷 材 熔 化 吸 收 的热 量和
烟 气 带走 热量
矶
式中 , 、 , —
, 一 , ,。
℃至烟 气 温度 , 和
熔 化 的冷材 加热 到最 终温 度 吸收 的热量 。 冷 材熔 化 吸收 的热量 牙 乏 ` 了 , 式中 ` — 冷材 的量 , 炉 , — 冷 材 的熔 化热 , 。 冷 材加 热到 最终 温度 吸收 的热 量
况 , 因此 应
的热 效率 降低 。 在 所 有 的热 工 炉 窑 中 , 炉 体 表 面 的 散热 是 不可避 免 的 。 熔 炼炉 的炉 体散 热 损失包 括 炉 顶散 热损 失 、炉 侧 散 热 损 失 和 炉 底 散 热损 失 。 在此 熔 炼 炉 热 平 衡 测 试 中 , 炉 体散 热 损 失 的 比例 为 。 由于 每 炉 产 生 的 炉 渣 较 少 , 故 炉 渣 带 走 的 热量 较少 。 冶金 炉漏 气 损 失一般 包括 炉 口及炉 门散热 损 失和 炉 墙砌 砖缝 隙漏 气 损失 。 一 般新 炉子 应 不 存在 缝 隙漏 气 问题 , 但 经 多次 开停 炉后 , 没 有钢 板 外壳 的炉 子 或 多 或 少 都 出现 缝 隙 , 在炉 内外 有 压 差 的情 况 下 , 必 有气 体 漏 出或 吸入 从表 。所测试熔炼 炉 的炉墙 为 钢 板 , 故 只存 在 路 口及 炉 门散 热 损 失 。 可 以看 出 , 漏 气 热 损 失 占 总热 量 收 入 的 比例
结论
本 文 以现场 测试 数据 为 基础 , 利 用 国家 标准 对 铝熔 炼炉 进行 热平 衡 计 算 误 差 为 解 了熔 炼炉 热 量的 流 向和 热 量 的利用 水 平 。 在 热平 衡计 算 的基础 上 , 对铝 熔 炼炉 的热 量 收入 、支 出情 况 进行 了分 析 , 铝熔 炼炉 可 以依 据此 次 热平 衡 测试 数据 及 分 析 结 果 进行 改 造 , 以达 到 降 低 能耗 的 目的 。 〔 参考 文献 〕
铝电解槽能量平衡测试与计算方法
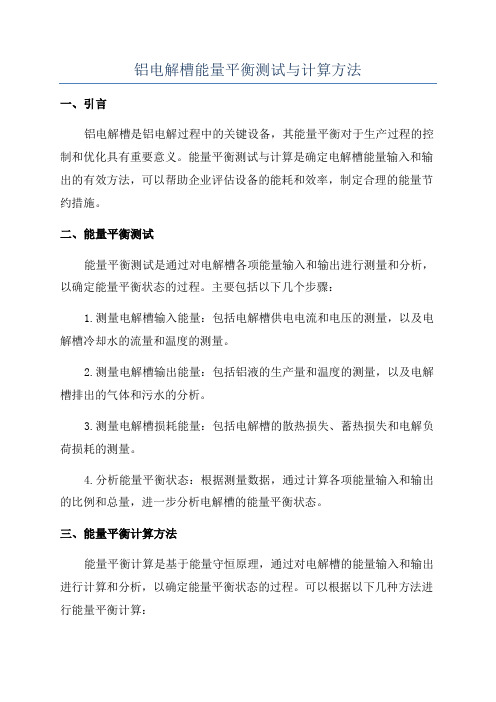
铝电解槽能量平衡测试与计算方法一、引言铝电解槽是铝电解过程中的关键设备,其能量平衡对于生产过程的控制和优化具有重要意义。
能量平衡测试与计算是确定电解槽能量输入和输出的有效方法,可以帮助企业评估设备的能耗和效率,制定合理的能量节约措施。
二、能量平衡测试能量平衡测试是通过对电解槽各项能量输入和输出进行测量和分析,以确定能量平衡状态的过程。
主要包括以下几个步骤:1.测量电解槽输入能量:包括电解槽供电电流和电压的测量,以及电解槽冷却水的流量和温度的测量。
2.测量电解槽输出能量:包括铝液的生产量和温度的测量,以及电解槽排出的气体和污水的分析。
3.测量电解槽损耗能量:包括电解槽的散热损失、蓄热损失和电解负荷损耗的测量。
4.分析能量平衡状态:根据测量数据,通过计算各项能量输入和输出的比例和总量,进一步分析电解槽的能量平衡状态。
三、能量平衡计算方法能量平衡计算是基于能量守恒原理,通过对电解槽的能量输入和输出进行计算和分析,以确定能量平衡状态的过程。
可以根据以下几种方法进行能量平衡计算:1.直接法:直接测量电流、电压、冷却水流量、铝液生产量和温度等参数,通过计算能量输入和输出的总量和比例,得到能量平衡结果。
2.间接法:通过测量电解槽输入能量和铝液生产量的关系,间接计算出其他参数的值,再进行能量平衡计算。
3.统计法:根据历史数据和统计方法,建立能量平衡模型,通过对电解槽供电能量和铝液生产量的统计分析,得到能量平衡结果。
四、能量平衡优化1.降低电解负荷:通过调整电解槽的操作参数,降低电解负荷,减少能量损耗。
2.提高电解效率:改进电解槽的设计和工艺,提高电解效率,减少电解能耗。
3.优化冷却系统:改善电解槽的冷却系统,提高冷却效果,降低散热损耗。
4.节约剂的使用:合理选择和使用节约剂,减少剂量,降低能耗。
5.废热回收:利用废热回收技术,将电解槽散热的废热用于其他生产流程,提高能源利用效率。
总结能量平衡测试与计算是铝电解槽能耗控制和优化的重要手段。
冶金熔体的相平衡图
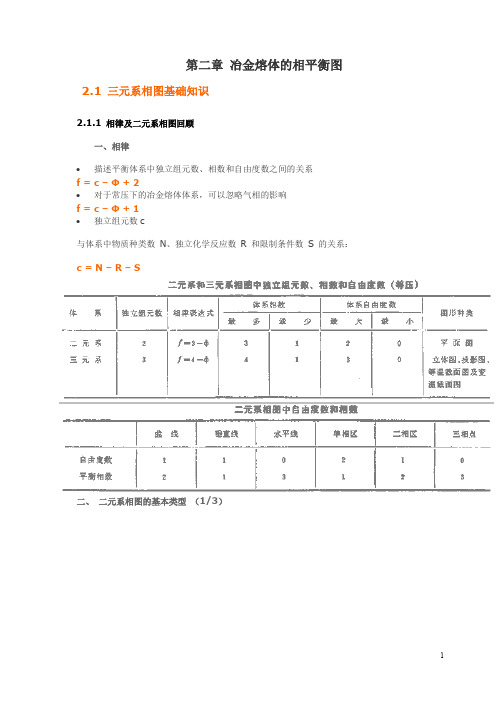
第二章冶金熔体的相平衡图2.1 三元系相图基础知识2.1.1 相律及二元系相图回顾一、相律∙描述平衡体系中独立组元数、相数和自由度数之间的关系f = c –Φ + 2∙对于常压下的冶金熔体体系,可以忽略气相的影响f = c –Φ + 1∙独立组元数c与体系中物质种类数N、独立化学反应数R 和限制条件数S 的关系:c = N – R – S二、二元系相图的基本类型(1/3)(1)有一个低共熔点型(2)生成一个二元一致熔融化合物型(3)有一个化合物在固相分解型(4)生成一个二元不一致熔融化合物型(5)有转熔反应的有限固溶体型(6)有液相分层、固相晶型转变及偏晶反应型(7)形成连续固溶体型(8)有最高点的连续固溶体型(9)有低共熔点的有限固溶体型三、熔体冷却过程分析2.1.2 三元系的组成表示法对于三元熔体体系:f = c –Φ + 1 = 4 –Φ∙三元凝聚体系的自由度数最多为3,即体系的平衡状态决定于温度和两个组元的浓度。
∙要完整地表示三元系的状态,必须采用三维空间图形。
∙在这种立体图中,底面上的两个坐标表示体系的组成,垂直于底面的坐标表示温度。
一、浓度三角形→等腰直角三角形表示法→等边三角形表示法1、等腰直角三角形表示法∙用纵轴表示组元A的浓度,横轴表示组元B的浓度,两轴均分为100等分。
∙组元C的含量→计算法:C% = 100 – A% – B%→图解法:过M点作斜边的平行线交AC、BC边于m2、m1;线段Am2或Bm1的长度表示组元C的含量。
∙→优点:可以用普通直角坐标纸作图→缺点:坐标原点所表示组元的含量的读取欠方便2、等边三角形表示法∙性质:→吉布斯浓度三角形→罗策布浓度三角形→优点:可以直接从图上读出三个组元的百分含量→缺点:必须用等边三角形坐标纸3、双线法确定体系的组成二、浓度三角形的性质1、等含量规则→在浓度三角形△ABC中平行于三角形某一边的任一直线上,其所有体系点中对应顶点组元的浓度相等。
铝铸件 cowper-symonds 模型 公式

铝铸件 cowper-symonds 模型公式铝铸件是指使用铝合金材料进行铸造制造的零件。
铝合金具有优良的机械性能、导热性能和耐腐蚀性能,因此广泛应用于航空、汽车、机械设备等领域。
而铸造是一种常见的金属加工方法,通过将熔融的金属注入到模具中,然后冷却凝固得到所需形状的零件。
在铝铸件的设计和制造过程中,需要考虑到材料的性能、零件的形状和尺寸、模具的设计等因素。
因此,为了更好地预测和优化铝铸件的性能和工艺参数,研究人员提出了各种模型和公式,其中一个著名的模型就是Cowper-Symonds模型。
Cowper-Symonds模型是用来描述铝合金在高温下的流变性能的一种经验模型。
该模型基于实验数据,可以用来预测铝合金在铸造过程中的应力-应变关系。
这对于预测零件的变形、裂纹和缺陷产生的位置和程度非常重要。
Cowper-Symonds模型的公式如下:σ = σ0 + Aε^n其中,σ是应力,σ0是材料的流变应力,A是一个与材料的流变性能有关的常数,ε是应变,n是一个与材料的硬化指数有关的常数。
在这个公式中,σ0可以看作是零应变时的初始应力,A表示材料的流变性能,ε^n表示应变对应的应力增长。
通过调整A和n的值,可以拟合材料的实际流变性能曲线。
根据Cowper-Symonds模型,可以通过实验测量材料的流变性能参数,然后使用公式进行计算,从而预测材料在不同应变下的应力。
这样可以帮助工程师更好地设计模具、优化工艺参数,避免零件变形、裂纹和缺陷的产生。
总之,Cowper-Symonds模型是一种用来描述铝合金铸件在高温下的流变性能的经验模型,可以通过公式预测材料的应力-应变关系。
这对于优化铝铸件的设计和制造具有重要意义,可以提高零件的质量和性能。
10:铝合金熔炼实验有色金属冶金学

10:铝合金熔炼实验有色金属冶金学
铝合金熔炼实验是有色金属冶金学中的一个重要实验,其主要实验步骤包括:
1. 准备铝合金及熔炼设备:选择所需的铝合金材料及熔炼设备,准确称量。
2. 搭建熔炉:选择合适的熔炉,进行熔炼设备的搭建及调试。
3. 加热铝合金:将铝合金放入熔炉中,逐步升温,使其达到熔点。
4. 改善铝合金性质:根据需要,添加相应的元素及合金元素,改变铝合金的物理和化学性质,提高其机械性能。
5. 熔炼铝合金:将铝合金一直熔炼至需要的成分和形态,并控制好其熔炼温度,保证产品质量。
6. 铝合金浇注:将熔融的铝合金倒入模具中,等待其冷却凝固。
7. 检验铝合金品质:根据实验需求,对铝合金成品的金相组织、力学性能等进行检测。
以上就是铝合金熔炼实验的主要步骤。
在实验中,需要注重安全操作,防范液态金属的喷溅等危险情况。
同时,也需要掌握基本的熔炼理论知识和实验技能,以保证实验结果的准确性和可靠性。
- 1、下载文档前请自行甄别文档内容的完整性,平台不提供额外的编辑、内容补充、找答案等附加服务。
- 2、"仅部分预览"的文档,不可在线预览部分如存在完整性等问题,可反馈申请退款(可完整预览的文档不适用该条件!)。
- 3、如文档侵犯您的权益,请联系客服反馈,我们会尽快为您处理(人工客服工作时间:9:00-18:30)。
铝的比热 铝的熔解热 容 J/kg J/(kg· ℃) 880 398000
输入热量: 铝水降温热量Q1+燃气发出热量Q2*热效率η
输出热量: 废料升温到660熔化需要的热量Q3+废料从固态转变为也太 Q4+熔化后的铝水升温需要的热量Q5+单位时间热损失*熔炼
废料温度℃ 废料重量Kg
熔炼
20
铝的比热 铝的熔解 容 热 J/(kg· J/kg 1000 880 398000
熔炼温度 ℃ 770
熔点 ℃ 660
吸收总热量 MJ 1058000000 15.0 27.61
均质
20
1000
880
560
475200000
132 66.00%
出热量Q2*热效率η
的热量Q3+废料从固态转变为也太需要的热量 的热量Q5+单位时间热损失*熔炼时间t
铝水重量 Kg 1000
电解铝温 度 ℃ 1.8371608
天然气热值 J 38320000
天然气数 天然气放 热损失 量 热 M3 J 1 38320000
12.40
3960
51.67%
199.6219 11.6 2.076923 1.657143
高棒60吨炉子,加入1吨冷料,铝水降温20度,相当于冷料比例 1/60,降温20度。 由此经验值计算,铝硅合金生产熔炼温度850度,铸造温度750度, 则需要添加1/12的冷料进行降温。