硫磺装置概况(九江石化)(DOC)
浅谈新硫磺装置(九江石化)
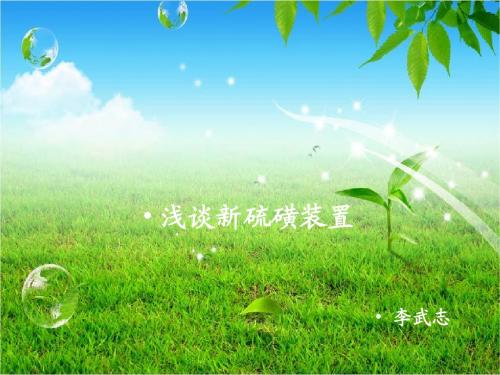
目录
1 2 3
环境保护的重要性
企业发展的需要
√
新硫磺置简介
企业发展的需要
• 随着产品质量升级和产品精制能力的提高、环境 保护要求的严格、加工原油硫含量的增加,九江 分公司现有硫回收装置能力(3万吨/年)不能满 足要求,需要增加环境保护设施。 800万吨油品质量升级改造工程原油加工量为800 万吨/年,加工原油为仪-长管输混合原油,混合 原油按胜利原油:阿曼类原油=4:6,硫含量为 1.16(w)%,API为28.04,酸值0.92 mgKOH/g。
企业发展的需要
原油中的硫 800万吨硫含量按1.16w%, 带入硫量为9.304万吨/年, 煤制氢装置 掺石油焦所带硫 按掺焦20% -58% ,带入硫
硫磺回收 8.87~9.26万吨/年 硫回收率为88.919% 89.343%
量为0.667 -1.06万吨/年
目录
1 2 3
环境保护的重要性
企业发展的需要
新硫磺装置主要特点
制硫部分
酸性气燃烧炉废热锅炉产生4.4MPa中压蒸汽 CLAUS过程气加热方式采用自产中压蒸汽加热
尾气部分
采用低温型CLAUS尾气加氢催化剂 尾气采用装置自产中压蒸汽加热升温 焚烧炉出口设置蒸汽过热器及焚烧炉废热锅炉
THANK YOU
新硫磺装置简介
√
新硫磺装置简介
• 硫磺回收装置设计规模为7+7万吨/年,操作弹性 为30-120%,年开工时数8400小时。由硫磺回收、 尾气处理、溶剂再生三部分组成。 • 硫磺回收、尾气处理为双系列,两系列尾气处理 的富液共用一套溶剂再生。 • 硫磺回收采用部分燃烧、两级转化CLAUS(克劳斯) 制硫工艺。 • 尾气采用热焚烧后经120米烟囱排空,排空烟气中 SO2 量为17.8kg/h、浓度为405mg/m3(标),满 足国家大气污染物综合排放标准。
硫磺装置的主要工艺是

硫磺装置的主要工艺是
硫磺装置的主要工艺是磺化工艺。
磺化工艺通常包括以下步骤:
1. 运输硫磺:原始硫磺经过初步的熔化和过滤处理后,被泵送或输送到硫磺装置的储存罐中。
2. 熔化:将固态硫磺通过加热,使其熔化为液态。
3. 变硫:将液态硫磺通过加热和催化剂反应,将其转化为硫磺蒸汽。
4. 焦炉燃烧:将燃料(通常是天然气或重油)在焦炉中燃烧,产生高温高压的火焰,用于加热反应器和炉内。
5. 高温烟气净化:将焦炉燃烧产生的高温烟气经过冷却和洗涤处理,去除其中的硫化物、蒽等有害物质。
6. 硫磺蒸汽制备:将硫磺蒸汽和氨气通过催化剂反应,生成硫磺蒜味,再经过冷却和净化步骤将其中的杂质去除。
7. 低温净化:将硫磺蒸汽经过洗涤、冷却等过程,去除其中的硫酸、杂质等。
8. 硫磺液态存储:将蒸汽冷却成液态硫磺,存储在储罐中。
9. 贮存和出口:对液态硫磺进行贮存和包装,准备出口销售或用于其他用途。
以上是一般硫磺装置的主要工艺流程,具体的工艺步骤和细节可能会因不同厂家和操作条件而有所不同。
第十四章硫磺回收装置

第⼗四章硫磺回收装置第⼗四章硫磺回收装置第⼀节装置概况及特点⼀、装置概况硫磺回收装置是环保装置,它是洛阳分公司500万吨/年炼油⼯程主体⽣产装置之⼀。
该装置主要处理液态烃、⼲⽓脱硫酸性⽓及含硫污⽔汽提酸性⽓等,其产品是国标优等品⼯业硫磺。
⼆、装置组成及规模硫磺回收(Ⅰ)设计⽣产能⼒为3000t/a,1987年8⽉开⼯,2001年4⽉扩能改造⾄1.0×104t/a;硫磺回收(Ⅱ)设计⽣产能⼒为5650t/a,1997年9⽉开⼯,2000年3⽉扩能⾄1.0×104t/a。
三、⼯艺流程特点两套硫磺回收装置均采⽤常规克劳斯⼯艺,采⽤部分燃烧法,即将全部酸性⽓引⼊酸性⽓燃烧炉,按烃类完全燃烧和1/3硫化氢完全燃烧⽣成⼆氧化硫进⾏配风。
过程⽓采⽤⾼温外掺合、⼆级转化、三级冷凝、三级捕集,最终硫回收率达到93%以上。
尾⽓中硫化物及硫经尾⽓焚烧炉焚烧,70m烟囱排放。
第⼆节⼯艺原理及流程说明⼀、⼯艺原理常⽤制硫⽅法中根据酸性⽓浓度不同,分别采⽤直接氧化法、分流法和部分燃烧法。
本装置采⽤的是部分燃烧法,即将全部酸性⽓引⼊燃烧炉,按烃类完全燃烧和1/3硫化氢完全燃烧⽣成⼆氧化硫进⾏配风。
对于硫化氢来说,反应结果炉内约有65%的硫化氢转化为硫,余下35%的硫化氢中有1/3燃烧⽣成⼆氧化硫,2/3保持不变。
炉内反应剩余的硫化氢、⼆氧化硫在转化器内催化剂作⽤下发⽣反应,进⼀步⽣成硫,其主要反应如下:主要反应:燃烧炉内:H2S+3/2O2=H2O+SO2+Q 2H2S+ SO2= 2H2O+3/2S2+QH2S+CO2=COS+ H2O+Q 2H2S+CO2=CS2+2 H2O+Q反应器内:2H2S+SO2=H2O+3/nSOn+Q COS+ H2O = H2S+CO2-QCS2+ 2H2O=2H2S+CO2-Q为获得最⼤转化率,必须严格控制转化后过程⽓中硫化氢与⼆氧化硫的摩尔⽐为2:1。
⼆、⼯艺流程说明来⾃液态烃、⼲⽓脱硫装置酸性⽓及含硫污⽔汽提酸性⽓,压⼒0.05Mpa(表),温度40℃左右,硫化氢浓度30~90%(V),烃含量⼩于4%(V),在酸性⽓分液罐V101分液后进⾏⼊酸性⽓焚烧炉F101,所需空⽓由风机C101供给。
Szorb催化汽油吸附脱硫装置简介
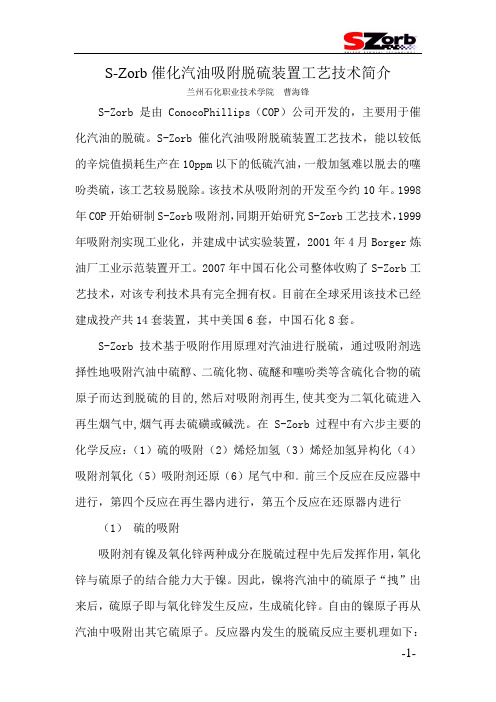
S-Zorb催化汽油吸附脱硫装置工艺技术简介兰州石化职业技术学院曹海锋S-Zorb 是由ConocoPhillips(COP)公司开发的,主要用于催化汽油的脱硫。
S-Zorb催化汽油吸附脱硫装置工艺技术,能以较低的辛烷值损耗生产在10ppm以下的低硫汽油,一般加氢难以脱去的噻吩类硫,该工艺较易脱除。
该技术从吸附剂的开发至今约10年。
1998年COP开始研制S-Zorb吸附剂,同期开始研究S-Zorb工艺技术,1999年吸附剂实现工业化,并建成中试实验装置,2001年4月Borger炼油厂工业示范装置开工。
2007年中国石化公司整体收购了S-Zorb工艺技术,对该专利技术具有完全拥有权。
目前在全球采用该技术已经建成投产共14套装置,其中美国6套,中国石化8套。
S-Zorb技术基于吸附作用原理对汽油进行脱硫,通过吸附剂选择性地吸附汽油中硫醇、二硫化物、硫醚和噻吩类等含硫化合物的硫原子而达到脱硫的目的,然后对吸附剂再生,使其变为二氧化硫进入再生烟气中,烟气再去硫磺或碱洗。
在S-Zorb 过程中有六步主要的化学反应:(1)硫的吸附(2)烯烃加氢(3)烯烃加氢异构化(4)吸附剂氧化(5)吸附剂还原(6)尾气中和。
前三个反应在反应器中进行,第四个反应在再生器内进行,第五个反应在还原器内进行(1)硫的吸附吸附剂有镍及氧化锌两种成分在脱硫过程中先后发挥作用,氧化锌与硫原子的结合能力大于镍。
因此,镍将汽油中的硫原子“拽”出来后,硫原子即与氧化锌发生反应,生成硫化锌。
自由的镍原子再从汽油中吸附出其它硫原子。
反应器内发生的脱硫反应主要机理如下:R-S + Ni + H 2 -------→ R-2H+ NiS + H2ONiS + ZnO + H 2 -------→ Ni + H2O+ZnS该反应需在气态氢存在的条件下进行。
(2)发生在再生器内的氧化反应氧化反应可以脱除吸附剂上的硫,同时使吸附剂上的镍和锌转变成氧化物的形式。
磺化装置工艺原理
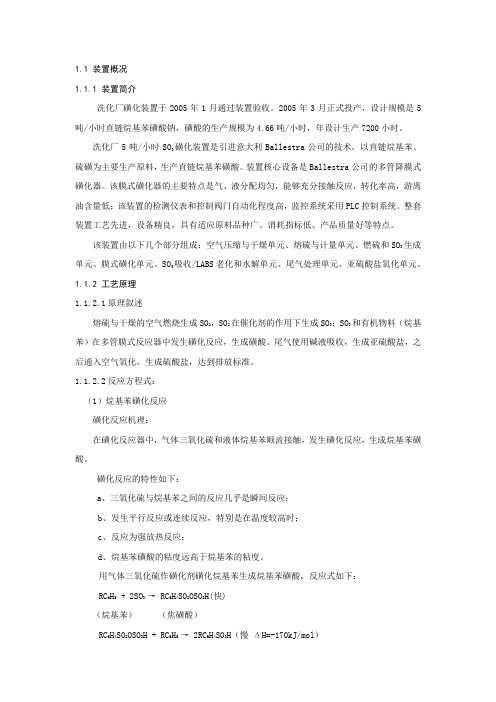
1.1 装置概况1.1.1 装置简介洗化厂磺化装置于2005年1月通过装置验收。
2005年3月正式投产,设计规模是5吨/小时直链烷基苯磺酸钠,磺酸的生产规模为4.66吨/小时,年设计生产7200小时。
洗化厂5吨/小时SO3磺化装置是引进意大利Ballestra公司的技术,以直链烷基苯、硫磺为主要生产原料,生产直链烷基苯磺酸。
装置核心设备是Ballestra公司的多管降膜式磺化器。
该膜式磺化器的主要特点是气、液分配均匀,能够充分接触反应,转化率高,游离油含量低;该装置的检测仪表和控制阀门自动化程度高,监控系统采用PLC控制系统。
整套装置工艺先进,设备精良,具有适应原料品种广、消耗指标低、产品质量好等特点。
该装置由以下几个部分组成:空气压缩与干燥单元、熔硫与计量单元、燃硫和SO3生成单元、膜式磺化单元、SO3吸收/LABS老化和水解单元、尾气处理单元、亚硫酸盐氧化单元。
1.1.2 工艺原理1.1.2.1原理叙述熔硫与干燥的空气燃烧生成SO2,SO2在催化剂的作用下生成SO3;SO3和有机物料(烷基苯)在多管膜式反应器中发生磺化反应,生成磺酸。
尾气使用碱液吸收,生成亚硫酸盐,之后通入空气氧化,生成硫酸盐,达到排放标准。
1.1.2.2反应方程式:(1)烷基苯磺化反应磺化反应机理:在磺化反应器中,气体三氧化硫和液体烷基苯顺流接触,发生磺化反应,生成烷基苯磺酸。
磺化反应的特性如下:a、三氧化硫与烷基苯之间的反应几乎是瞬间反应;b、发生平行反应或连续反应,特别是在温度较高时;c、反应为强放热反应;d、烷基苯磺酸的粘度远高于烷基苯的粘度。
用气体三氧化硫作磺化剂磺化烷基苯生成烷基苯磺酸,反应式如下:RC6H5 + 2SO3 → RC6H4SO2OSO3H(快)(烷基苯)(焦磺酸)RC6H4SO2OSO3H + RC6H5 → 2RC6H4SO3H(慢ΔH=-170kJ/mol)(焦磺酸)(磺酸)磺化反应器中还存在着两种副反应,形成磺酸酐和砜。
九江分公司Ⅱ套催化MIP—CGP装置连续运行超3年
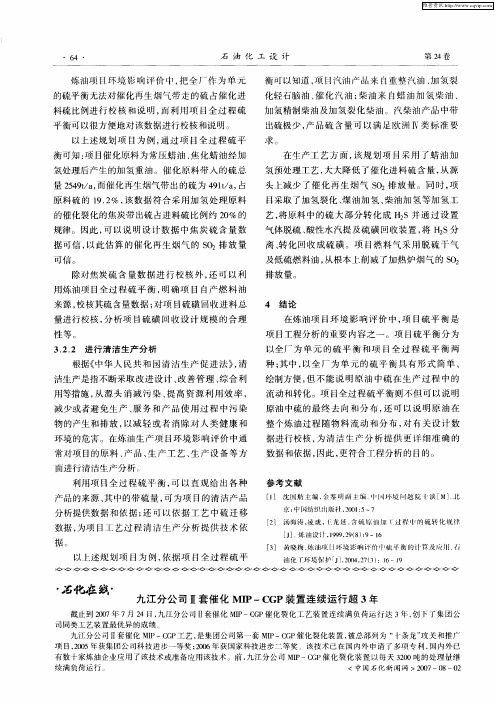
据 可 信 , 此估 算 的催 化 再 生 烟气 的 s 2 放 量 以 o排
可信。
除对 焦炭 硫 含 量 数 据 进 行 校 核 外 , 可 以利 还 用 炼油 项 目全过 程 硫 平 衡 , 确项 目 自产 燃 料 油 明
来 源 , 核其硫 含量 数据 ; 项 目硫 磺 回收 进 料 总 校 对 量进行 校核 , 析 项 目硫 磺 回 收设 计 规 模 的合 理 分 性等 。
衡 叮以知道 , 目汽油 产 品来 自重整 汽油 、 氢裂 项 加
化轻 石脑 油 、 化 汽 油 ; 油 来 自蜡 油 加 氢 柴 油 、 催 柴 加氢 精制 柴油 及加氢 裂 化 柴油 。汽 柴油 产 品 中带
出硫 极少 , 品 硫 含量 可 以满 足 欧洲 Ⅳ类 标 准要 产
求。
在生 产工 艺 方 面 , 该规 划 项 目采 用 了蜡 油 加
参考 文献
[ ] 沈国舫 主编 , 鉴 u 副主编 .{ 上 境 M题院 1谈 [ . I 金 』 ] I : I 1 M]北
京 : 田 纺织 版 礼 .0 15 7 中 20 :
利用 项 目全 过 程 硫 平 衡 , 以直 观 给 出各 种 可
产 品 的来 源 、 中的带 硫 量 , 为项 目的清 洁产 品 其 可 分析提供 数 据 和依 据 ; 可 以 依 据 工艺 中 硫迁 移 还 数据 , 为项 目工 艺 过 程 清 洁 生 产 分 析 提供 技 术 依
环境 的危 害 。在炼 油 生产 项 目环 境 影响 评 价 中通 常对项 目的 原 料 、 品 、 产 工 艺 、 产设 备 等 方 产 生 生 面进行 清洁生 产分析 。
据进行 校核 , 清 洁 生 产 分 析 提 供 更 详 细 准 确 的 为 数据 和依据 , 因此 , 更符 合 工程分析 的 目的 。
磺化装置工艺概述

磺化装置工艺概述1.熔硫系统熔硫槽装在地平以下便于投料,硫磺采用人工投料的方式,通过硫磺液下泵将液体硫磺引入液硫高位槽,液体硫磺的计量使用柱塞计量泵。
液体硫磺采用蒸汽伴管或套管保温,冷凝水集中回收。
熔硫槽内蒸汽伴管压力采用气动调节阀控制蒸汽压力,保证了硫磺合适的熔点温度,提高硫磺的流动性。
2.空气干燥系统反应系统的工艺空气由罗茨风机产生,该风机出口压力由气动调节阀自动调节。
工艺空气由罗茨风机加压后先经过循环水冷却系统,再经过乙二醇冷却系统,然后进入硅胶干燥系统。
干燥过的工艺空气露点达到-60℃以下。
循环水冷却器和乙二醇冷却器与乙二醇储罐设置在一起。
硅胶干燥器采用两个分体式床层切换使用,切换采用气动阀自动控制。
硅胶通过热风或蒸汽加热再生。
乙二醇的温度由制冷机系统控制。
空气干燥单元不仅要求干燥空气有较低的露点,而且要求干燥空气露点稳定从而保证SO3同烷基苯摩尔比稳定,使磺化产物有稳定的中和值及稳定的产品质量。
为此我们5T/h磺化装置的设计中提高空气冷却器的换热面积,二级冷却器的换热面积达1000m2,另外加大空气干燥罐容积,使干燥吸附工作时段内露点稳定,最为关键的是,干燥剂再生后吹冷温度要低从而保证切换后干燥剂初始工作温度低,避免干燥罐切换后由于干燥剂温度高而造成吸附能力急剧下降、露点明显升高而造成不稳定,我们在工艺上采用适当增大冷冻机组制冷量,使一部分冷冻水用于再生后的冷却,使干燥剂冷却温度显著下降。
干燥剂的选用上考虑生产成本80%用硅胶20%可采用分子筛或进口硅胶,再生温度要求达到200℃,因此SO3冷却器空气冷却部分采用串联冷却,提高再生温度,适应分子筛需要较高的再生温度。
3.SO2系统液体硫磺通过硫磺计量泵定量输送至燃硫炉内燃烧,点火采用电点火装置,点燃后自动断电避免由于人为因素造成点火器损坏。
我们在SO2/ SO3气体发生单元设计上考虑到硫磺充分燃烧,我们在燃硫炉内设置了多孔弧形分布盘,分布盘为耐高温高铝陶瓷,让液体硫磺进入燃硫炉内分布均匀,在燃硫炉进口位置由顶部改为侧面,使未充分燃烧的硫磺不会带入到SO2冷却器内燃烧。
硫磺回收装置工艺流程
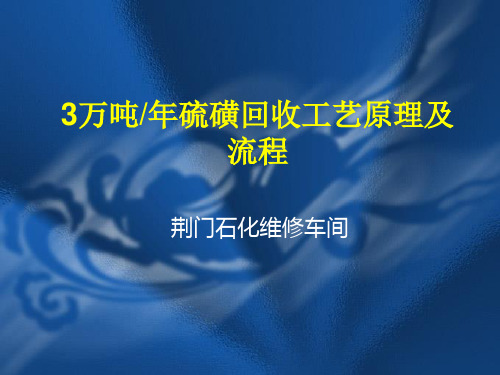
本装置溶剂再生部分来的贫胺液(25%MDEA 溶液)进 入尾气吸收塔(C-412)上部,与尾气急冷塔来的尾气逆 流接触,尾气中的 H2S 被吸收。吸收了 H2S 的富胺液, 经富液泵(P-412A/B)升压后返回溶剂再生部分。 自尾气吸收塔(C-412)塔顶出来的净化尾气,进入尾 气焚烧炉(F-411),在 600℃高温下,将净化尾气中残 留的硫化物焚烧生成 SO2,剩余的 H2 和烃类燃烧成 H2O和CO2,焚烧后的高温烟气先经过蒸汽过热器(E413),然后再经尾气加热器(E-411)回收热量,烟气温 度降至 300℃左右由烟囱(ST-411)排入大气。
三、相关流程图
2、尾气处理部分工艺原理
从硫磺回收部分排出的制硫尾气,仍含有少量的 H2S、SO2、COS、Sx等有害物质,直接焚烧后排 放达不到国家规定的环保要求。 加氢还原吸收工艺是将硫回收尾气中的元素S、 SO2、COS和CS2等,在很小的氢分压和很低的操 作压力下,用特殊的尾气处理专用加氢催化剂,将 其还原和水解为H2S,再用醇胺溶液吸收,再生后 的醇胺溶液循环使用;吸收了H2S的富液经再生处 理,富含H2S气体返回上游硫回收部分,经吸收处 理后的净化气中的总硫<300ppm。 加氢还原吸收尾气处理是目前世界上公认的最彻底 的制硫尾气处理工艺,“SSR”工艺的原理是尾气加 氢还原吸收。
二、流程简述
1、硫磺回收及尾气处理部分工艺流程简述
再生和催化等装置来的酸性气经酸性气分液罐(D401)脱液后,与来自酸性水汽提装置的酸性气混合 进入制硫燃烧炉(F-401)的火嘴。根据制硫反应需 氧量,通过比值调节严格控制进炉空气量,经燃烧 将酸性气中的烃类等有机物全部分解。燃烧时所需 空气由制硫炉鼓风机(K-401A/B)供给。制硫燃烧 炉(F-401)的配风量是关键,为此,在制硫尾气管 道上安装了一台 H2S/SO2 在线比值分析仪,随机分 析尾气中 H2S/SO2 比率,并通过反馈信号调节供风 管道上的微调阀,使过程气中的 H2S/SO2 比率始终 趋近 2:1,从而获得最高的 Claus 转化率。
- 1、下载文档前请自行甄别文档内容的完整性,平台不提供额外的编辑、内容补充、找答案等附加服务。
- 2、"仅部分预览"的文档,不可在线预览部分如存在完整性等问题,可反馈申请退款(可完整预览的文档不适用该条件!)。
- 3、如文档侵犯您的权益,请联系客服反馈,我们会尽快为您处理(人工客服工作时间:9:00-18:30)。
溶脱车间硫磺装置1、装置概况硫磺装置由山东三维公司设计,装置包括一套设计处理量为3万吨/年硫磺回收,与4万吨/年硫磺回收配套的尾气处理部分及溶剂再生等三部分。
于2006年3月中旬建成中交。
原料主要是Ⅰ/Ⅱ催化脱硫酸性气,Ⅰ/Ⅱ催化污水汽提酸性气,加氢脱硫酸性气以及150万吨/年柴油加氢与焦化胺液再生酸性气。
采用中石化自主开发的“SSR”无在线炉硫回收工艺,溶剂再生单元采用热处理技术,配套有DCS集散控制系统、以及一套SIS系统,将制硫燃烧炉的自动点火、进料、停车、吹扫、停车保护以及尾气焚烧炉的自动点火、停车、吹扫、停电保护等安全连锁引入SIS,提高装置运行的安全性能和自动化水平。
为优化操作,降低烟道气二氧化硫的排放浓度,装置配备了硫化氢与二氧化硫在线比值分析仪,通过比值分析优化燃烧炉配风,从而提高硫的转化率。
3、工艺原理酸性气原料经过分液罐分液后与空气进入制硫燃烧炉燃烧,过程气经换热器以及高温掺合阀后,进入一级转化器、二级转化器发生水解反应和岐化反应生成硫单质,尾气经焚烧炉后部加热与氢气混合进入加氢反应器,硫化物在反应器内发生还原反应生成硫化氢,经急冷塔冷却后进入吸收塔,吸收塔采用N-甲基二乙醇胺(MDEA)在低温下吸收,塔顶部出来的净化尾气进入焚烧炉焚烧后排烟囱,塔底富液经换热进入再生塔蒸汽加热再生,再生塔顶气经分液与外来酸性气混合,塔底再生贫液经换热至贫液罐,供本装置和焦化及柴油加氢装置使用。
鉴于燃烧炉控制配风使65%酸性气转化为单质硫,余下的35%酸性气中的1/3转化为二氧化硫,从而使进入一、二级转化器的过程气中硫化氢与二氧化硫的比值接近2:1,从而该工艺称为部分燃烧法。
4、装置主要设备单元1急冷塔及吸收塔:直径2200mm ,1 2总塔高33502mm,急冷塔与吸收塔层叠放置节省占地面积。
急冷塔为填料塔主要对还原后尾气进行冷却,吸收塔为板式塔是提供MDEA吸收硫化氢的场所。
2再生塔:采取热再生处理,进料为闪蒸后富液,以0.3MPa蒸汽作为塔底重沸器的热源,将硫化氢与贫液分离,硫化氢进入制硫系统,贫液送至贫液罐供循环使用。
重沸器蒸汽耗量为装置主要能耗。
3制硫燃烧炉:为主要的反应炉,主要发生硫化氢的部分燃烧氧化,为后面转化器提供合适的原料,余热经废热锅炉产3.5MPa蒸汽经过热处理并网。
4焚烧炉:以瓦斯作为燃料,主要目的焚烧吸收塔塔顶出来的净化尾气以及炼油尾气,焚烧达到一定的排烟温度后直接烟囱排入大气,瓦斯实时耗量一般在0.08t/h左右。
345一、二级转化器:直径3400mm,发生的主要反应为有机硫的水解反应与硫化氢和二氧化硫的岐化反应。
反应器温升一级转化器为70-80℃,二级转化器为20-30℃。
转化器内装载的催化剂为LS-300和LS-971。
6加氢反应器:尺寸大小为Φ2800×6908mm,主要发生有机硫和二氧化硫的加氢还原反应以及有机硫的水解反应。
原料为两级转化器出来的尾气经加热后与氢气混合,反应器内装载的催化剂为CT6-5。
567 成型库房75、流程示意图6、物料平衡(以下数据为设计数据)6.1、制硫部分物料平衡入 方出 方 组 成 kg/h kg /d t/a 组 成 kg/h kg /d t/a 外来酸性气 4867 116808 40883 硫 磺 3579 85896 30064 再生酸性气 2235 53640 18772 制硫尾气13181 316344 110720 空 气 9658 231792 81127合 计16760402240140784合 计16760402240 1407846.2、尾气处理部分物料平衡入 方出 方组 成 kg/h t/d t/a 组 成 kg/h t/d t/a 制硫尾气13181烟 气20709E-33E-32E-23制硫燃烧炉酸性气在炉内与空气混合部分燃烧,65%转化成单质硫,余下的1/3转化二氧化硫,酸性气含有的杂质如烃完全燃烧酸性气原料空气自制硫风机来一级转化器焚烧炉净化尾气及炼油尾气焚烧合格后经烟囱直接排入大气酸性气分液罐瓦斯尾气分液罐二级转化器加氢反应器急冷塔吸收塔炼油尾气与闪蒸烃烟囱再生酸性气全回流贫液循环再生塔主要发生有机硫的水解反应以及少量的硫化氢与二氧化硫反应生成单质硫主要是硫化氢与二氧化硫发生的Claus 反应,少量水解反应尾气在氢气的作用下,有机硫、二氧化硫被还原为硫化氢,并释放大量的热量贫液吸收尾气中的硫化氢,塔顶为净化尾气,塔底为富液在一定温度下,硫化氢发生解析,从富液中分离出来由塔顶进入制硫系统,贫液由塔底进行循环使用急冷水将尾气冷却至42℃左右尾气处理部分物料平衡(续表)入方出方组成kg/h t/d t/a 组成kg/h t/d t/a 老硫磺尾气4394燃料气188 酸性气1702氢气43 再生酸性气2235空气6840合计24646 合计246467、技经指标7.1、能耗指标设计处理量3万吨/年;全年综合能耗为370.9035×104kgEo,折合每吨硫磺能耗为123.6345kgEo/t。
附:能耗数据序号项目年消耗量能耗指标能耗×104kgEo 单位数量单位数量1 循环冷水×104t 285.6 MJ/t 4.19 28.58182 除盐水×104t 0.0084 MJ/t 10.47 0.00213 除氧水×104t 12.44712 MJ/t 385.19 114.51484 新鲜水×104t 1.26 MJ/t 7.12 0.21435 污水×104t 2.9316 MJ/t 33.49 2.34506 电×104kw.h 465.1967 MJ/KWh 11.84 131.55467 3.5MPA蒸汽×104t -6.73848 MJ/t 3684 -592.92448 1.0 MPA蒸汽×104t 7.99512 MJ/t 3182 607.63529 凝结水×104t -12.1716 MJ/t 320.3 -93.115610 燃料气×104t 0.15792 MJ/t 41868 157.920011 净化风×104Nm3134.4 MJ/Nm3 1.59 5.104012 氮气×104Nm360.48 MJ/Nm3 6.28 9.0717合计370.9035名称单位指标管理部门备注循环水温度:4 月1 日- 10月15日℃≯32 调度处10月16日- 3月31日℃≯28 调度处循环水压力MPa ≮0.3 调度处新鲜水压力MPa ≮0.3 调度处低压除氧水压力MPa ≮1.0 调度处中压除氧水压力MPa ≮4.0 调度处除盐水压力MPa ≮0.4 调度处氮气压力MPa ≮0.5 调度处中压蒸汽压力MPa ≮0.9 调度处7.3、其它指标名称指标计算方法名称指标计算方法工艺防腐合格率≮94.5%含硫污水中亚铁离子采样合格次数与采样次数之比静密封泄漏率≯0.4‰泄露密封点密封点总数之比汽水品质合格率≮90%炉水磷酸根采样合格次数与采样次数之比设备完好率≮96%损坏设备数量与所有设备总数之比循环水质量合格率≮90%循环水浓倍和浊度采样合格次数与采样次数之比非计划停工计划外停工次数8.1、原料性质名称单位指标管理部门备注S浓度%>40 技术处酸性气中H2酸性气中烃含量%<1 技术处瓦斯压力MPa >0.3 车间8.2、关键工艺操作指标名称位号单位指标管理部门备注D-101液位LIA-0101 % <60 溶脱联合车间H2S/SO2AIC-0601 比值0~5:1 溶脱联合车间炉F-101炉膛后部温度TIS-0302 ℃1020~1270 机动处酸性气炉前压力PI-0301 MPa <0.06 生产调度处ER-101汽包压力PICA-0401 MPa 3.4~4.0 机动处ER-101过程气出口温度TI-0401 ℃280~360 溶脱联合车间E-101壳程蒸汽压力PIC-0601 MPa <0.4 溶脱联合车间E-101管程出口温度TI-0602 ℃140~170 溶脱联合车间E-103壳程蒸汽压力PIC-0602 MPa <0.4 溶脱联合车间R-101床层温度TI-0504B ℃300~350 生产调度处R-102床层温度TI-0507B ℃210~260 生产调度处R-201入口温度TIC-0701 ℃280~300 溶脱联合车间R-201床层温度TI-0803B ℃300~350 生产调度处E-202壳程蒸汽压力PIC-0801 MPa <0.4 溶脱联合车间E-103管程出口温度TI-0603 ℃140~170 溶脱联合车间C-201塔顶过程气温度TIC-0901 ℃<42 溶脱联合车间D-301底部温度TI-1601 ℃<42 溶脱联合车间炉F-201炉膛温度TIC-1201 ℃<800 机动处C-201急冷水PH值AI-1001 >7 溶脱联合车间C-301顶部温度TIC-2001 ℃105~115 溶脱联合车间C-301顶部压力PI-2003 MPa 0.09~0.11 溶脱联合车间C-201顶过程气H2含量AIC-0901 % 3~5 溶脱联合车间E-203蒸汽并网温度TIC-0702 ℃380~460 溶脱联合车间E-203烟气温度TI-0706 ℃≯500 溶脱联合车间ER-101汽包液位LIC-0401 % 30~60 溶脱联合车间E-101壳程液位LIC-0601 % 40~60 溶脱联合车间E-103壳程液位LIC-0603 % 40~60 溶脱联合车间E-202壳程液位LIC-0801 % 40~60 溶脱联合车间C-201底部液位LIC-0901 % 40~60 溶脱联合车间C-202塔底液位LIC-0902 % 40~60 溶脱联合车间C-301底部液位LIC-2001 % 40~60 溶脱联合车间D-302液位LIC-2101 % 40~60 溶脱联合车间D-305液位LIC-1801 % 40~60 溶脱联合车间D-305压力PIC1801 MPa ≯0.25 溶脱联合车间D-303液位LIC-2002 % 40~60 溶脱联合车间D-304液位LI-1901 % <50 溶脱联合车间D-106液位LIC-1501 % 40~60 溶脱联合车间炉F-201烟囱排烟温度TI-0705 ℃250~380 溶脱联合车间ER-101炉水指标:PH值PH 9~11 机动处磷酸根mg/l 5~15 机动处总碱度ug/l ≤50 机动处ER-101蒸汽指标:Na+ug/l <15 机动处SiO2 ug/l ≤20 机动处9、产品质量指标名称单位指标(优等/一等/合格)管理部门备注工业硫磺(GB2449-92)硫磺含量% ≮99.9 /99.5 /99.0 质管中心硫磺灰份含量% ≯0.03 /0.10 /0.20 质管中心酸度(以H2SO4计)% ≯0.003 /0.005 /0.02 质管中心砷含量% ≯0.0001 /0.01 /0.05 质管中心铁含量% ≯0.003 /0.005 /-- 质管中心有机物含量% ≯0.03 /0.30 /0.80 质管中心水份% ≯0.10 /0.50 /1.0 质管中心10、环保指标名称单位指标管理部门备注硫回收尾气SO2排放速率kg/h ≯110 安环处硫回收尾气SO2排放浓度mg/m3≯600 安环处11、“比学赶帮超”竞赛溶脱车间在运行班开展以“降低瓦斯单耗”、“提高工艺防腐合格率”、“提高炉水合格率”、“硫磺产品等级品率”、“贫液合格率”、“烟道气二氧化硫排放浓度”、“交接班日志及记录评比”、“巡检合格率竞赛”以及“SMES录入竞赛”等内容的工艺劳动竞赛,以提高在总部同类装置中的水平。